零件结构及工艺性设计——冲压零件
冲压工艺过程设计-实验
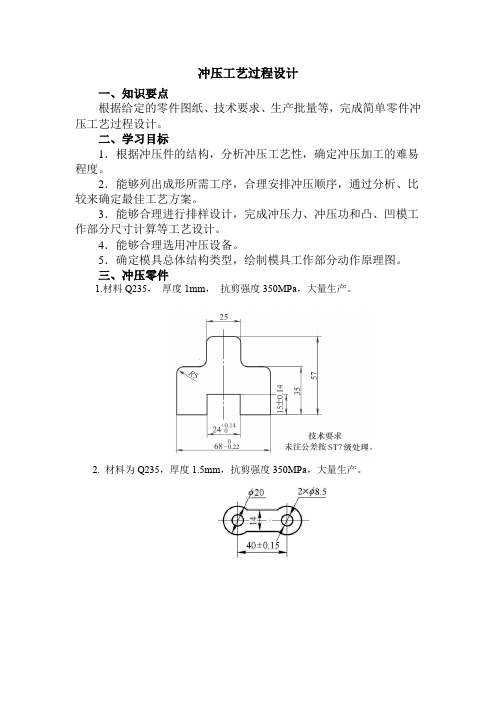
冲压工艺过程设计
一、知识要点
根据给定的零件图纸、技术要求、生产批量等,完成简单零件冲压工艺过程设计。
二、学习目标
1.根据冲压件的结构,分析冲压工艺性,确定冲压加工的难易程度。
2.能够列出成形所需工序,合理安排冲压顺序,通过分析、比较来确定最佳工艺方案。
3.能够合理进行排样设计,完成冲压力、冲压功和凸、凹模工作部分尺寸计算等工艺设计。
4.能够合理选用冲压设备。
5.确定模具总体结构类型,绘制模具工作部分动作原理图。
三、冲压零件
1.材料Q235,厚度1mm,抗剪强度350MPa,大量生产。
2. 材料为Q235,厚度1.5mm,抗剪强度350MPa,大量生产。
3.
4.
5.
6.中批量生产
7.
8.中批量生产
9.材料Q235,料厚2mm
10.材料为Q235钢,料厚t=1.5mm,中批量生产。
11.材料为Q235钢,料厚t=2mm,中批量生产。
13.材料为Q235钢,料厚t=2mm
14.材料为Q235钢,料厚t=2mm
15.材料为Q235钢,料厚t=1.2mm,所有尺寸公差取ST7级,大批量生产。
16.材料为Q235钢,料厚t=1.5mm,中批量生产。
18.材料为10钢,料厚t=0.5mm,中批量生产。
19.材料为08钢
20.
四、实验报告内容
1.冲压件的工艺性分析
2.分析工艺方案,选择最佳工艺方案
3.冲压工艺计算(排样及材料利用率,冲压力,工作零件尺寸计算)
4.模具结构类型(总体设计:送料方式,定位方式,卸料方式,出件方式,导向方式)
5.冲压设备的选择。
冲压工艺及模具设计
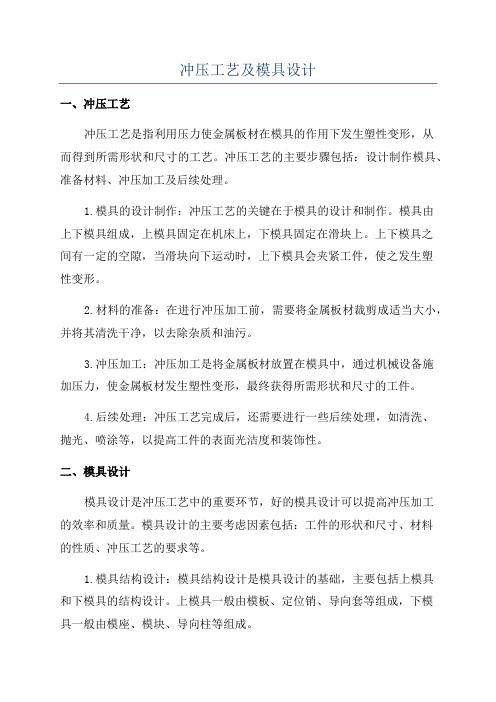
冲压工艺及模具设计一、冲压工艺冲压工艺是指利用压力使金属板材在模具的作用下发生塑性变形,从而得到所需形状和尺寸的工艺。
冲压工艺的主要步骤包括:设计制作模具、准备材料、冲压加工及后续处理。
1.模具的设计制作:冲压工艺的关键在于模具的设计和制作。
模具由上下模具组成,上模具固定在机床上,下模具固定在滑块上。
上下模具之间有一定的空隙,当滑块向下运动时,上下模具会夹紧工件,使之发生塑性变形。
2.材料的准备:在进行冲压加工前,需要将金属板材裁剪成适当大小,并将其清洗干净,以去除杂质和油污。
3.冲压加工:冲压加工是将金属板材放置在模具中,通过机械设备施加压力,使金属板材发生塑性变形,最终获得所需形状和尺寸的工件。
4.后续处理:冲压工艺完成后,还需要进行一些后续处理,如清洗、抛光、喷涂等,以提高工件的表面光洁度和装饰性。
二、模具设计模具设计是冲压工艺中的重要环节,好的模具设计可以提高冲压加工的效率和质量。
模具设计的主要考虑因素包括:工件的形状和尺寸、材料的性质、冲压工艺的要求等。
1.模具结构设计:模具结构设计是模具设计的基础,主要包括上模具和下模具的结构设计。
上模具一般由模板、定位销、导向套等组成,下模具一般由模座、模块、导向柱等组成。
2.模具材料选择:模具的材料选择直接影响到模具的使用寿命和加工质量。
一般情况下,模具材料应具有高硬度、高强度、良好的热导性和耐磨性等特性。
3.模具零件设计:模具零件的设计应考虑到工件的形状和尺寸,以及冲压工艺的要求。
模具零件的设计应尽量简化,减少加工难度,提高生产效率。
4.模具配合设计:模具零件之间的配合关系直接影响到模具的精度和稳定性。
模具配合设计应确保零件的定位准确、运动平稳,并充分考虑到热膨胀等因素。
综上所述,冲压工艺及模具设计是一项复杂的工程,它涉及到材料、结构、流程等多个方面。
通过合理的冲压工艺和精心的模具设计,可以实现高效、高质量的冲压加工,为生产制造提供有力支持。
汽车冲压零件的设计及制造

汽车冲压零件的设计及制造摘要:在冲压塑料加工模具领域,通常都会使用一个产品的技术质量水平来直接衡量整个冲击冲压加工模具行业的技术发展创新水平。
冲压加工模具的结构设计的合理与否以及产品加工精细与否直接的会影响着整个冲压加工部件的生产质量。
关键词:冲压加工;冲压模具;冲压部件1 汽车冲压模具的设计分析在立体模型设计图纸的加工设计绘制过程中,应对设计技术上的切入点以及实际应用需求情况做出全面的分析考量,以此对立体模具的制造工艺设计排样和立体模具成型进行十分合理的加工设计。
以上几个步骤直接就会影响着最终产品批量生产最终设计得到的立体冲压成型模具产品质量。
1.1设定目标尺寸在最初确定最终设计一款产品冲头模具成型外形尺寸图纸的整个操作过程中,第一步就首先需要在对一款成型产品冲头模具外形图的各种外形尺寸公差设计量值分析的基本认识上和基础之上,对最终确定能够设计得到一款成型产品的模具外形尺寸设计量值公差进行正确性的设定。
具体一点说来在最终确定一款产品模具外形尺寸公差后的尺寸量值允许的测量精度要求范围之内,以一款产品模具冲头、凹模的美观外形以及磨损尺寸变化速度趋向等的情况来作为主要测量依据,决定最终的能够得到一款产品冲头凹模模具外形尺寸的一款产品设计量值。
1.2排样图设计以及力学计算产品力学测量计算与应用冲压工具模型最终产品能否安全完成批量生产,在最终客户自行使用产品生产工艺过程中产品主体压力能否完全正确承受力与使用冲压机械机的内部压力之间应该有着直接的密切相互联系,因此最终产品冲压力学模型测量综合计算的技术重要性和应用意义不言而喻。
1.3模具总装图绘制模具设备总装图的总体绘制设计过程一般应当以格式排样的绘图形式作为设计基准,在此基础之上不再进行总体设计绘制工作。
除此之外,需要详细结合各种冲压送料设备的需要合模高度、设备的需要安装模具尺寸以及各种送料加工装置的合模高度,最终可以绘制设计出各种冲压设备模具的详细总体结构。
冲压工艺与模具设计:冲裁模的主要零部件结构设计

凹模厚(高)度
H=kb (≥15)
k见表2.22 凹模壁厚 C=(
1.5~2)H
(≥30~40)
计算值:
靠用标准,选择模架的依据。
2 工作零 件3.凸凹模
复合模中同时具有落料凸模和冲孔凹模作用的工作零件。
凸凹模的最小壁厚: 正装复合模,内孔不积存废料,胀力小,最小壁厚可以小些; 倒装复合模,若内孔为直筒形刃口形式,且采用下出料方式, 则内孔积存废料,胀力大,故最小壁厚应大些。
导料板的厚度:见表2.24
导料板结构
3 定位零件(续)
2)侧压装置
设置目的:若条料公差较大,为避免条料在导料板中偏摆,使最 小搭边得到保证。
结构形式:①弹簧式侧压装置 ②簧片式侧压装置 ③簧片压块式侧压装置 ④板式侧压装置
不宜设置侧压装置的场合:①板料厚度在0.3mm以下的薄板; ②辊轴自动送料装置的模具。
谢谢!
特殊侧刃:既可定距,又可冲裁零件的部分轮廓 宽度b
侧刃断面尺寸 其他尺寸按标准规定
侧刃凹模按侧刃实际尺寸配制,留单边间隙。
侧刃数量: 一个或两个 侧刃布置: 并列布置、对角布置
侧刃定位误差比较
1-导料板 2-侧刃挡块 3-侧刃 4-条料
尖 角 形 侧 刃
特殊侧刃
3 定位零件(续)
5)导正销
使用目的: 消除送进导向和送料定距或定位板等粗定位的误差。 主要用于: 级进模
1)导料销、导料板 导料销:两个,位于条料的同侧, 从右向左送料时,导料销装在后侧; 从前向后送料时,导料销装在左侧。 结构形式: 固定式、活动式
3 定位零件(续) 1)导料销、导料板(续) 导料板:设在条料两侧 结构形式:一种是标准结构,它与卸料板(或导板)分开制造 一种是与卸料板制成整体的结构。
冲压件

表 3(材料厚度 t)
材料 纸胶板、布胶 板 软铝
t ≤1 t>1~2 t>2~3 0.03t ~ 0.04t~0.06t 0.05t 0.04t ~ 0.05t ~ 0.06t ~ 0.06t 0.07t 0.08t 铜,软黄铜,硅 0.05t ~ 0.06t ~ 0.07t ~ 钢 片 , 软 钢 0.07t 0.08t 0.09t (0.08 ~ 0.20%C) 硬铝,硬黄铜, 0.06t ~ 0.07t ~ 0.08t ~ 硬青铜 0.08t 0.09t 0.10t 中硬钢(0.3~ 0.4%C) 硬 钢 (0.5 ~ 0.07t ~ 0.0t8 ~ 0.09t ~ 0.7%C) 0.09t 0.10t 0.10t
常用冲压件非金属材料机械性能见表
材料名称 纸胶板 布胶板 石棉板 橡皮 有机玻璃、聚氯乙烯
抗弯强度г (MPa) 用管状凸模裁切时 用普通凸模冲裁时 100~130 140~200 90~100 120~180 40~50 ----1~6 20~80 70~80 100~130
三、冲压件的设计
• 冲压件应按经规定程序批准的图纸及相 关技术文件制造、验收,并应符合国家、 行业的相关标准,以及本标准的规定。 冲压件材料应具有良好的冲压性能,选用 屈强比(б s/б b)小、弹性模数(E)大、塑性 指数高、厚向异性指数大、板平面内各 向异性指数小的材料有利于冲压的各种 塑性变形。
(一)冲裁件设计的工艺性:
• 1、 冲裁件形状尽可能设计成简单、对称,使排样时废料最少。 • 2、 冲裁件的外形或内孔应避免减角在各直线或曲线连接初宜有 适当圆角其半径最小的R值见附表1。 • 3、 冲裁件突出旋臂和凹槽的最小宽度对于普通软钢取1.2t ;硬 钢为2.0t以上。 • 4、 冲孔时,孔径不宜过小,其最小孔径与孔的形状、材料的机 械性能、厚度有关,见附表2。冲裁件最小孔边距为2t以上,并不小 于3-4mm。 5、 在拉深或弯曲件上冲孔时,其孔壁与工件直壁应保持一定 距离,孔不能在变形区内。
冲压件工艺性分析

一、止动件冲压件工艺性分析1、零件材料:为Q235-A钢,具有良好的冲压性能,适合冲裁;2、零件结构:相对简单,有2个© 20mn t勺孔;孑L与孔、孔与边缘之间的距离也满足要求,最小壁厚为14mm(© 20mn的孔与边框之间的壁厚)3、零件精度:全部为自由公差,可看作IT14级,尺寸精度较低,普通冲裁完全能满足要求。
查表得各零件尺寸公差为:外形尺寸:130°1、48°).62、60_°.74、R403、R60』%内型尺寸:2000.052孔中心距:60± 0.37二、冲压工艺方案的确定完成该零件的冲压加工所需要的冲压基本性质的工序只有落料、冲孔两道工序。
从工序可能的集中与分散、工序间的组合可能来看,该零件的冲压可以有以下几种方案。
方案一:落料-冲孔复合冲压。
采用复合模生产。
方案二:冲孔-落料级进冲压。
采用级进模生产。
方案一只需一副模具,工件的精度及生产效率都较高,工件最小壁厚14mn 大于凸凹模许用最小壁厚3.6mm--4.0mm模具强度好,制造难度中等,并且冲压后成品件可通过卸料板卸下,清理方便,冲压模具设计0用川和屠”口匚JkTJIDliiftL 2闻1坤丘貝5「1「节操作简单。
方案二也只需一副模具,生产效率高,操作方便,工件精度也能满足要求,但是模具结构复杂,制造加工,模具成本较高。
结论:采用方案一为佳三、模具总体设计(1)模具类型的选择由冲压工艺分析可知,采用复合模冲压,所以模具类型为复合模。
(2)定位方式的选择因为该模具采用的是条料,控制条料的送进方向采用导料板,无侧压装置。
控制条料的送进步距采用挡料销定距。
而第一件的冲压位置因为条料长度有一定余量,可以靠操作工目测来定。
(3)卸料、出件方式的选择因为工件料厚为1.5mm相对较薄,卸料力也比较小,故可采用弹性卸料。
又因为是倒装式复合模生产,所以采用上出件比较便于操作与提高生产效率。
冲压零件质量控制

冲压零件质量控制一、引言冲压零件广泛应用于各种行业,如汽车制造、电子设备制造、家具制造等。
随着科技的发展和市场竞争的加剧,对冲压零件的质量控制要求越来越高。
本文将探讨如何进行有效的冲压零件质量控制。
二、质量控制的重要性冲压零件的质量直接影响到产品的性能、安全和使用寿命。
质量控制可以确保冲压零件符合设计要求,提高产品的整体质量,降低生产成本,增强企业的竞争力。
三、质量控制策略1、优化产品设计:在设计阶段,应考虑冲压零件的可制造性和可检查性。
这包括选择合适的材料、设计合理的结构、制定可行的加工工艺等。
2、强化原材料控制:选择优质的原材料,如钢材,是保证冲压零件质量的关键。
应定期对原材料进行质量检查,确保其符合生产要求。
3、严格的生产过程控制:制定和执行明确的冲压生产流程,包括模具准备、材料成型、零件加工等。
每个环节都需要严格的质量监控,以确保生产出符合要求的零件。
4、重视员工培训:定期对员工进行质量管理培训,提高他们的质量意识和技术水平,是保证冲压零件质量的重要措施。
5、建立完善的质量检测体系:通过建立和完善质量检测体系,可以有效地保证冲压零件的质量稳定和持续改进。
这包括使用先进的检测设备和制定科学的质量检测流程。
6、应用统计过程控制(SPC):通过应用SPC,可以实时监控生产过程,发现异常并采取相应的措施,避免不合格品的产生。
7、持续改进:通过对生产过程中出现的问题进行深入分析,找出问题的根本原因,并采取有效的改进措施,不断提高生产效率和产品质量。
四、结论冲压零件的质量控制是保证产品质量和安全的关键。
通过优化产品设计、强化原材料控制、严格的生产过程控制、重视员工培训、建立完善的质量检测体系、应用统计过程控制以及持续改进等措施,可以有效地提高冲压零件的质量水平,满足市场需求。
在未来的发展中,随着科技的进步和市场竞争的加剧,冲压零件的质量控制将更加重要。
企业应不断更新质量控制理念和方法,加强技术创新和人才培养,以适应市场的变化和满足客户的需求。
冲压工艺及冲压件介绍

冲压工艺及冲压件介绍一、基本介绍二、五金冲压件应用领域三、冲压模具各部件在设计上的要求四、冲压件冲压工艺规程五、冲压件成本控制六、冲压件的检验手法七、冲压件材质选取需注意的的问题八、冲压件模具的保养与维护九、冲压模具爆裂原因分析十、金属冲压件的常见问题十一、冲压件凹凸的原因深入解析一、基本介绍冲压是五金加工里面用的最多的一种加工手段,五金冲压件指的是在室温条件下,钢或者有色金属等板材用模具,由压力机提供加工所需压力而成形为指定形状。
1、根据材料总的变形性质,冲压工序分为两大类:A、分离工序:材料在外力作用下,变形部份的应力超过了材料的强度极限板料断裂而分离。
B、塑性变形工序:板料在外力作用下,变形部份的应力超过了材料的屈服极限,但未达到强度极限时,仅产生塑性变表而得到一定形状与尺寸。
2、冲压工序的五种变形A、立体压制:将体积作重新分配并将材料作一定转移以改变坯料外形或高度厚度。
B、弯曲:将平的板料变成弯曲件,使弯曲件形状作进一步改变。
有弯、卷边扭曲等。
C、压延:将平的坯料冲压成所需形状的空心件,或使空心件的尺寸作进一步改变。
D、成型:用各种性质的局部变形平改变制件或坯料的形状。
属于成型变形的有起伏成型、翻边、缩颈、凸肚、卷圆、整形。
E、剪裁、冲裁:没封闭或不封闭使材料的部份与另一部份分离。
属于此类方式有落料、冲孔、切边、切断、剖切、切口等。
二、五金冲压件应用领域:1、汽车行业的冲压。
以拉深为主。
在我国这部份主要集中在汽车厂、拖拉机厂、飞机制造厂等大厂,独立的大型冲压拉深厂还未几见。
2、汽车等行业零部件类冲压。
主要是冲剪成形。
这部门的企业有很多都归在尺度件厂,也有一些独立的冲压厂,目前一些汽车厂或拖拉机厂的附近都有很多这样的小厂。
3、电器件冲压厂。
这类厂是一个新的工业,跟着电器的发展而发展起来,这部门厂主要集中在南方。
4、糊口日用品冲压厂。
做一些工艺品,餐具等,这些厂近几年也有大的发展。
5、家用电器部件冲压厂。
DIN 6932-2011冲压零件结构工艺性
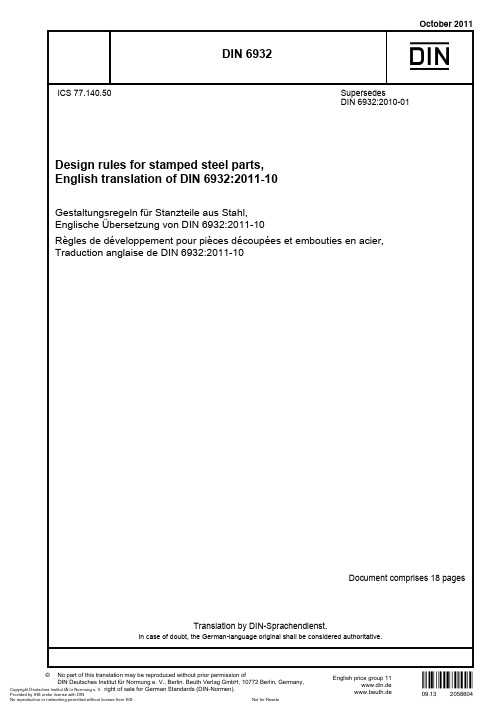
DIN 6932
ICS 77.140.50
D
Supersedes DIN 6932:2010-01
Design rules for stamped steel parts, English translation of DIN 6932:2011-10
Gestaltungsregeln für Stanzteile aus Stahl, Englische Übersetzung von DIN 6932:2011-10 Règles de développement pour pièces découpées et embouties en acier, Traduction anglaise de DIN 6932:2011-10
Document comprises 18 pages
Translation by DIN-Sprachendienst.
In case of doubt, the German-language original shall be considered authoritative.
No part of this translation may be reproduced without prior permission of DIN Deutsches Institut für Normung e. V., Berlin. Beuth Verlag GmbH, 10772 Berlin, Germany, Copyright Deutsches Institut für Normung e. V. right of sale for German Standards (DIN-Normen). has the exclusive
冲压零件各工序工艺要求

冲压零件各工序的工艺性要求一、冲裁件的形状和尺寸:1.冲裁件应尽量设计成简单、对称,使排样时产生废料最少。
2.冲裁件的外形或内形应避免产生尖锐的棱角,应有适当的圆角。
R通常需要大于t,或R2以上,具体情况据α的大小来确定;大中型零件的切边轮廓交角在没有特殊要求时,取R6以上能有利于模具。
3.冲裁件的凸出悬臂和凹槽宽度不宜过小;以上为资料值,供参考;一般设计时,B取5mm以上为宜。
4.冲孔孔径不宜过小,最小孔径与孔的形状、材料机械性能、材料厚度有关。
圆孔直径d和方孔边长a的数值最小为1.3 t,通常d和a的值大于2 t,能不用小数值时就不用小数值。
5.拉延件切边的槽,为了方便卸废料,两侧应设计大于5°的斜度。
6.冲裁件孔边与轮廓的距离不应过小,孔之间的距离也不应过小。
以上为资料值,仅供参考。
设计一般取C为5mm以上。
7.拉延件或成形件切边时,切边线应沿垂直棱线方向通过圆角;(特殊例外)切边线应与斜面和水平面交线的垂直方向,通过斜面;此条不是绝对的,特殊需要时需分析刃口角度。
8.冲孔和工艺缺口不要在与冲压方向小于75°的斜面上,必要时采用侧冲。
如果可以改变冲孔方向,可以局部做出凸台改变方向。
9.拉延以后冲孔时,孔边到侧壁的距离,模具厂家希望B≥5mm,且孔边到圆角边缘的距离应保证大于2 t。
二、弯曲件的工艺性:1.最小弯曲半径:r min=(1-2)t(材质、料厚、退火状态、有否纤维方向的影响)2.弯曲件的直边高度:当弯曲角度为90°时,弯曲直边高度最小为:H≥2 t3.弯曲件孔边距离:如果空在弯曲变形区域附近,弯曲时孔会发生变形,应使孔尽量远离变形区域。
以上数据为资料参考数据,使用时应比极限值大一些为好。
4.增加工艺孔、槽和转移弯曲线:5.定位工艺孔:对于形状复杂或需要多次弯曲的零件,为防止废品,应加工艺孔进行定位。
6.对称工件圆角半径的设置:7.伸长翻边(内凹轮廓)和压缩翻边(外凸轮廓)时,应在圆弧区域适当降低翻边高度,保持含料厚5mm即可。
冲压设计说明书配图纸

课程设计说明书目录1 冲压工艺分析 (3)1.1 冲裁件的结构工艺性 (3)1.2 零件尺寸精度与表面粗糙度分析 (3)1.3 零件材料分析 (4)1.4 冲压加工的工艺分析 (4)3 工艺尺寸计算 (5)3.1排样、计算条料宽度及确定步距 (5)3.2 冲裁力的计算 (7)3.3 压力中心的计算 (8)3.4 刃口尺寸的计算 (10)4 模具零件设计 (11)4.1 卸料板的设计 (11)4.2 弹性元件橡胶的设计 (11)4.3 落料凹模 (12)4.4 模架的选择 (13)4.5 凸凹模固定板,凸模固定板厚度 (14)4.6 凸模的设计 (15)4.7 凸凹模的设计 (16)5 参考资料 (17)6 附录: (17)课题材料08钢,料厚2mm,生产批量,小批量图1—零件尺寸1 冲压工艺分析1.1 冲裁件的结构工艺性由零件图可知,该零件结构简单,呈T行,上下对称,可采用少废料排样。
零件内部有两个较大直径的孔,零件外形存在清角。
无悬臂和窄槽。
两孔的尺寸d>1.0t,两孔之间的间距d1>1.5t,两圆孔的孔边距k>1.5t。
符合工艺性。
、图2—两件尺寸1.2 零件尺寸精度与表面粗糙度分析工件为图一冲孔落料件,材料厚度为2毫米,冲裁件尺寸较大。
零件图上所有尺寸均未标注公差,属自由公差,可按IT14级确定工件尺寸的公差。
通过普通冲裁即可达到零件精度要求。
1.3 零件材料分析材料为08钢,厚度t=2mm材质为极软的碳素钢,。
抗拉强度σb (MPa):≥325,屈服强度σs (MPa):≥195,抗剪切强度τ(MPa)≥260。
其强度、硬度较低,而韧性、塑性却较高,适合冲裁。
图3—材料性能1.4 冲压加工的工艺分析根据工件的形状、尺寸、精度分析,孔的直径寸,孔边距等,都能满足冲裁加工工艺要求。
但为了提高模具寿命,建议将所有90°清角改为R1的圆角。
结论:综合以上材料性能、零件结构、尺寸精度的分析,该零件可以采用普通冲裁的方法获得。
冲压件工艺分析
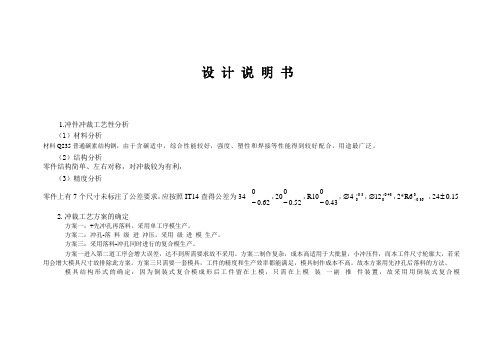
设 计 说 明 书1.冲件冲裁工艺性分析 (1)材料分析材料Q235普通碳素结构钢,由于含碳适中,综合性能较好,强度、塑性和焊接等性能得到较好配合,用途最广泛。
(2)结构分析零件结构简单、左右对称,对冲裁较为有利,(3)精度分析零件上有7个尺寸未标注了公差要求,应按照IT14查得公差为34.00-,2052.00-,R1043.00-,4∅3.00+,43.0012+∅,2*R6036.0- ,2415.0± 2.冲裁工艺方案的确定方案一:+先冲孔再落料。
采用单工序模生产。
方案二:冲孔-落 料 级 进 冲压。
采用 级 进 模 生产。
方案三:采用落料-冲孔同时进行的复合模生产。
方案一进入第二道工序会增大误差,达不到所需要求故不采用。
方案二制作复杂,成本高适用于大批量,小冲压件,而本工件尺寸轮廓大,若采用会增大模具尺寸故排除此方案。
方案三只需要一套模具,工件的精度和生产效率都能满足,模具制作成本不高。
故本方案用先冲孔后落料的方法。
模具结构形式的确定:因为倒装式复合模成形后工件留在上模,只需在上模 装 一副 推 件装置,故采用用倒装式复合模材料Q235 t=2一、 冲裁工艺计算 (一)凸、凹模刃口尺寸计算查表得Z min=0.246,Zmax=0.36, Z max-Z min=0.074.落料件 :3462.00-,2052.00-,R1043.00-. ,R6036.0- ,X=0.5 (3462.00-) : D A =(D max – x △)A0δ+=33.690.030+D T =( D A –Z min) 0T δ-= 33.44400.02- (2052.00-): D A =19.75025.00+ , D T =19.50402.00+(1043.00-):D A =9.68502.00+ , D T =9.439002.0-(R6036.0-) :D A =5.98202.00+ , D T =5.736002.0-冲孔件,4∅3.00+,43.0012+∅,3.0012+∅ : d T =(d min + x △) 0T δ-= 12.21500.02-dA = (d min + x△+ Z min) Aδ+=12.46102.0+4∅43 .0+: dT =4.1500.02-,dA=4.39602.0+孔中心距2415.0±LA=(Lmin+0.5△)±△/8= 25±0.0375排样分析零件形状,应采用单直排的排样方式,零件可能的排样方式有下图所示的两种。
简单冲压模具设计
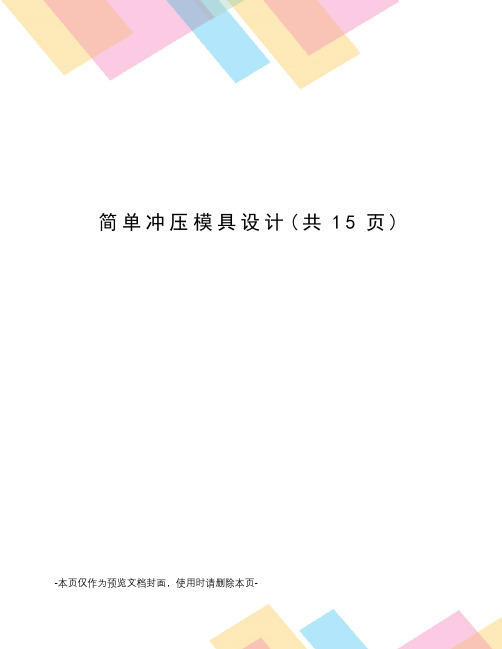
简单冲压模具设计(共15页) -本页仅作为预览文档封面,使用时请删除本页-内容摘要目录第一章零件工艺性分析........................................ 错误!未定义书签。
1.1材料分析 .................................................. 错误!未定义书签。
1. 2结构分析 .................................................... 错误!未定义书签。
1. 3精度分析 .................................................... 错误!未定义书签。
第二章冲裁工艺方案的确定 ................................ 错误!未定义书签。
第三章冲裁工艺方案的确定 ................................ 错误!未定义书签。
刃口尺寸计算原则............................................ 错误!未定义书签。
刃口尺寸计算.................................................... 错误!未定义书签。
排样计算 ........................................................... 错误!未定义书签。
冲压力计算 ....................................................... 错误!未定义书签。
第四章冲压设备的选用........................................ 错误!未定义书签。
第五章模具零部件结构的确定 ............................ 错误!未定义书签。
标准模架的选用................................................ 错误!未定义书签。
钣金件冲压工艺及零件设计规范

冲压工艺及零件设计规范一、钣金件的冲压工艺钣金件的工艺性是指零件在冲切、弯曲、拉伸等加工过程中的难易程度。
良好的工艺应保证材料消耗少,工序数目少,模具结构简单,使用寿命高,产品质量稳定。
在一般情况下,对钣金件工艺性影响最大的是材料的性能、零件的几何形状、尺寸和精度要求。
下面通过一个实例来说明制件的工艺性。
如图6—14所示为摩托车侧盖前支承,材料为Q235钢,厚度1.5mm,要求编制该零件的冲压工艺方案。
一、冲压件的工艺性分析(一)根据零件的使用条件和技术要求进行工艺性分析(二)如图6—14 所示该零件为摩托车侧盖前支承板,以2-φ5.9凸包定位,且焊接组合在车架的电气元件支架上,腰圆孔用于侧盖的装配,故腰圆孔位置是该零件需要保证的重点。
(二)根据零件形状、尺寸和要求进行工艺性分析(1)该零件端部四角为尖角,若采用落料工艺,则工艺性较差,根据该零件的装配使用情况,为了改善落料的工艺性,故将四角修改为圆角,取圆角半径为2mm;(2)该零件的“腿”较长,若能有效地利用过弯曲和校正弯曲来控制倒弹,则可以得到形状和尺寸比较准确的零件;(3)腰圆孔边至弯曲半径R中心的距离为2.5mm,大于材料厚度(1.5mm),从而腰圆孔位于变形区之外,弯曲时不会引起孔变形,故该孔可在弯形前冲出。
二、确定工艺方案(一)冲压工序类型和工序顺序的选择冲压该零件需要的基本工序和顺序有剪切或落料、冲腰圆孔、一次弯曲、二次弯曲和冲凸包。
(二)工序组合及其方案比较如图6--15 弯曲的方法(a)一副模具成形;(b)、(c)两副模具成形。
1、弯曲变形的方法及比较该零件弯曲变形的方法可采用如图6—15所示中的任何一种。
第一种方法(见图6—15a)的优点是用一副模具成形,可以提高生产率,减少所需设备和操作人员。
缺点是毛坯的整个面积几乎都参与激烈的变形,零件表面擦伤严重,且擦伤面积大,零件的形状与尺寸都不精确,弯曲处变薄严重,这些缺点将随零件“腿”长的增加和“脚”长的减小而愈加明显。
冲压件工艺性(3篇)

第1篇一、引言冲压件是机械制造领域中广泛使用的一种零件,其生产工艺性对产品的质量和成本有着重要的影响。
本文将围绕冲压件工艺性展开讨论,分析其特点、影响因素及优化措施。
二、冲压件工艺性特点1. 高精度:冲压件具有很高的尺寸精度和形状精度,可实现复杂形状的零件制造。
2. 高效率:冲压工艺自动化程度高,生产效率高,可实现大批量生产。
3. 低成本:冲压件生产过程中,材料利用率高,加工设备简单,降低了生产成本。
4. 易于实现多样化:冲压件可加工成各种形状和尺寸,适应性强。
5. 易于实现表面处理:冲压件表面光滑,易于进行表面处理,如镀锌、喷漆等。
三、冲压件工艺性影响因素1. 材料性能:材料的选择对冲压件的工艺性有很大影响。
常用的冲压材料有低碳钢、合金钢、不锈钢等。
不同材料具有不同的强度、塑性和硬度,需根据产品要求选择合适的材料。
2. 冲压模具:模具是冲压件生产的关键,其设计、制造和选用对冲压件的工艺性有直接影响。
模具的精度、刚度和磨损程度都会影响冲压件的尺寸精度和形状精度。
3. 冲压设备:冲压设备包括压力机、模具安装设备等。
设备的性能、精度和稳定性对冲压件的工艺性有重要影响。
4. 工艺参数:冲压工艺参数包括冲压速度、压力、温度等。
合理的工艺参数可以保证冲压件的尺寸精度、形状精度和表面质量。
5. 操作人员技能:操作人员的技能水平直接影响冲压件的生产质量和效率。
四、冲压件工艺性优化措施1. 优化材料选择:根据产品要求,选择合适的材料,提高材料的塑性和可冲压性。
2. 优化模具设计:采用先进的模具设计方法,提高模具的精度和寿命。
合理设计模具结构,降低生产成本。
3. 选用高性能冲压设备:提高设备的性能、精度和稳定性,确保冲压件的质量。
4. 优化工艺参数:根据产品要求,合理设置冲压速度、压力和温度等工艺参数,保证冲压件的尺寸精度、形状精度和表面质量。
5. 提高操作人员技能:加强操作人员培训,提高其技能水平,确保生产过程中的产品质量。
冲压模具设计和制造实例

冲压模具设计与制造实例例:图1所示冲裁件,材料为A3,厚度为2mm,大批量生产.试制定工件冲压工艺规程、设计其模具、编制模具零件的加工工艺规程. 零件名称:止动件 生产批量:大批 材料:A3 材料厚度:t=2mm一、 冲压工艺与模具设计1.冲压件工艺分析①材料:该冲裁件的材料A3钢是普通碳素钢,具有较好的可冲压性能. ②零件结构:该冲裁件结构简单,并在转角有四处R2圆角,比较适合冲裁. ③尺寸精度:零件图上所有未注公差的尺寸,属自由尺寸,可按IT14级确定工件尺寸的公差.孔边距12mm 的公差为,属11级精度.查公差表可得各尺寸公差为:零件外形:65 mm 24 mm 30 mm R30 mm R2 mm零件内形:10 mm孔心距:37±0.31mm 结论:适合冲裁. 2.工艺方案及模具结构类型该零件包括落料、冲孔两个工序,可以采用以下三种工艺方案:+①先落料,再冲孔,采用单工序模生产.②落料-冲孔复合冲压,采用复合模生产.③冲孔-落料连续冲压,采用级进模生产.方案①模具结构简单,但需要两道工序、两套模具才能完成零件的加工,生产效率较低,难以满足零件大批量生产的需求.由于零件结构简单,为提高生产效率,主要应采用复合冲裁或级进冲裁方式.由于孔边距尺寸12 mm有公差要求,为了更好地保证此尺寸精度,最后确定用复合冲裁方式进行生产.工件尺寸可知,凸凹模壁厚大于最小壁厚,为便于操作,所以复合模结构采用倒装复合模及弹性卸料和定位钉定位方式.3.排样设计查冲压模具设计与制造表 2.5.2,确定搭边值:两工件间的搭边:a=2.2mm工件边缘搭边:a1=2.5mm步距为:32.2mm条料宽度B=D+2a1=65+2=70确定后排样图如2所示一个步距内的材料利用率η为:η=A/BS×100%=1550÷70××100%=%查板材标准,宜选900mm×1000mm的钢板,每张钢板可剪裁为14张条料70mm×1000mm,每张条料可冲378个工件,则η为:η=nA1/LB×100%=378×1550/900×1000×100%=%即每张板材的材料利用率为%4.冲压力与压力中心计算⑴冲压力落料力 F总=τ=××2×450=KN其中τ按非退火A3钢板计算.冲孔力 F冲=τ=×2π×10×2×450=KN其中:d 为冲孔直径,2πd为两个圆周长之和.卸料力 F卸=K卸F卸=×=KN推件力 F推=nK推F推=6××=KN其中 n=6 是因有两个孔.总冲压力:F总= F落+ F冲+ F卸+ F推=+++=KN⑵压力中心如图3所示:由于工件X方向对称,故压力中心x0=32.5mm=13.0mm其中:L1=24mm y1=12mmL2=60mm y2=0mmL3=24mm y1=12mmL4=60mm y4=24mmL5=60mm y5=27.96mmL6=60mm y6=24mmL7=60mm y7=12mmL8=60mm y8=12mm计算时,忽略边缘4-R2圆角.由以上计算可知冲压件压力中心的坐标为,135.工作零件刃口尺寸计算落料部分以落料凹模为基准计算,落料凸模按间隙值配制;冲孔部分以冲孔凸模为基准计算,冲孔凹模按间隙值配制.即以落料凹模、冲孔凸模为基准,凸凹模按间隙值配制.刃口尺寸计算见表16.工作零件结构尺寸落料凹模板尺寸:凹模厚度:H=kb≥15mmH=×凹模边壁厚:c≥~2H=~2×=~mm 实取c=30mm凹模板边长:L=b+2c=65+2×30=125mm查标准JB/T :凹模板宽B=125mm故确定凹模板外形为:125×125×18mm.将凹模板作成薄型形式并加空心垫板后实取为:125×125×14mm.凸凹模尺寸:凸凹模长度:L=h1+h2+h=16+10+24=50mm其中:h1-凸凹模固定板厚度h2-弹性卸料板厚度h-增加长度包括凸模进入凹模深度,弹性元件安装高度等凸凹模内外刃口间壁厚校核:根据冲裁件结构凸凹模内外刃口最小壁厚为7mm,根据强度要求查冲压模具设计与制造表2.9.6知,该壁厚为4.9mm即可,故该凸凹模侧壁强度足够.冲孔凸模尺寸:凸模长度:L凸= h1+h2+h3=14+12+1440mm其中:h1-凸模固定板厚 h2-空心垫板厚 h3-凹模板厚凸模强度校核:该凸模不属于细长杆,强度足够.7.其它模具零件结构尺寸根据倒装复合模形式特点:凹模板尺寸并查标准JB/,确定其它模具模板尺寸列于表2:根据模具零件结构尺寸,查标准GB/选取后侧导柱125×25标准模架一副.8.冲床选用根据总冲压力 F总=352KN,模具闭合高度,冲床工作台面尺寸等,并结合现有设备,选用J23-63开式双柱可倾冲床,并在工作台面上备制垫块.其主要工艺参数如下:公称压力:63KN滑块行程:130mm行程次数:50次/分最大闭合高度:360mm连杆调节长度:80mm工作台尺寸前后×左右:480mm×710mm二、模具制造1、主要模具零件加工工艺过程制件:柴油机飞轮锁片材料:Q235料厚:1.2mm该制件为大批量生产,制品图如下:一冲裁件的工艺分析1、冲裁件为Q235号钢,是普通碳素钢,有较好的冲压性能,由设计书查得τ=350Mpa.2、该工作外形简单,规则,适合冲压加工.3、所有未标注公差尺寸,都按IT14级制造.4、结论:工艺性较好,可以冲裁.方案选择:方案一:采用单工序模.方案二:采用级进模.方案三:采用复合模.单工序模的分析单工序模又称简单模,是压力机在一次行程内只完成一个工序的冲裁模.工件属大批量生产,为提高生产效率,不宜采用单工序模,而且单工序模定位精度不是很高,所以采用级进模或复合模.级进模的分析级进模是在压力机一次行程中,在一副模具上依次在几个不同的位置同时完成多道工序的冲模.因为冲裁是依次在几个不同的位置逐步冲出的,因此要控制冲裁件的孔与外形的相对位置精度就必须严格控制送料步距,为此,级进模有两种基本结构类型:用导正销定距的级进模和用侧刃定距的级进模.另外级进模有多个工序所以比复合模效率低.复合模的分析复合模是在压力机一次工作行程中,在模具同一位置同时完成多道工序的冲模.它不存在冲压时的定位误差.特点:结构紧凑,生产率高,精度高,孔与外形的位置精度容易保证,用于生产批量大.复合模还分为倒装和正装两种,各有优缺点.倒装复合模但采用直刃壁凹模洞口凸凹模内有积存废料账力较大,正装复合模的优点是:就软就薄的冲裁件,冲出的工件比较平整,平直度高,凸凹模内不积存废料减小孔内废料的胀力,有利于凸凹模减小最小壁厚.经比较分析,该制件的模具制造选用导料销加固定挡料销定位的弹性卸料及上出件的正装复合模.二排样图设计及冲压力和压力中心的计算由3-6,3-8表可查得:a1=,a=,△=查书391.料宽计算: B=D+2a=62+2=64mm2.步距:A=D=a1=62+=62.8mm3.材料利用率计算:η=A/BS×100%=πR2-πR2+12/64=312-+/64×100%=%其中a是搭边值,a1是工作间隙,D是平行于送料方向冲材件的宽度,S是一个步距内制件的实际面积,A是步距,B是料宽,R1是大圆半径,R2是小圆半径,12×是方孔的面积,η为一个步距内的材料的利用率4.冲裁总压力的确定:L=231+2+12+2=周边总长计算冲裁力:F=KLtτ查设计指导书得τ=350MpaF=350≈180KN落料力:F落=τ=231350=卸料力:F卸=kF落==冲孔力:F冲=τ+12+2350=顶件力:F顶=-k2F落==冲裁总压力:F∑=F落+F卸+F冲+F顶=+++=F压=~F∑=246KN说明:K为安全系数,一般取;k为卸料力系数,其值为~,在上式中取值为;k2为顶件力系数,其值为~,式中取值为5.压力机的初步选用:根据制件的冲裁的公称压力,选用开式双柱可倾式压力机,公称压力为350k N 形号为J23-35 满足:F压≥F∑。
冲压工艺及模具设计(3篇)

第1篇一、引言冲压工艺是一种常见的金属成形工艺,广泛应用于汽车、家电、电子、航空等行业。
冲压工艺具有生产效率高、成本低、精度高、尺寸稳定性好等优点。
模具是冲压工艺中的关键设备,其设计质量直接影响到冲压产品的质量和生产效率。
本文将对冲压工艺及模具设计进行简要介绍。
二、冲压工艺概述1. 冲压工艺原理冲压工艺是利用模具对金属板材施加压力,使其产生塑性变形,从而获得所需形状、尺寸和性能的零件。
冲压工艺的基本原理是金属的塑性变形,即金属在受到外力作用时,产生塑性变形而不破坏其连续性的过程。
2. 冲压工艺分类(1)拉深:将平板金属沿模具凹模形状变形,形成空心或实心零件的过程。
(2)成形:将平板金属沿模具凸模形状变形,形成具有一定形状的零件的过程。
(3)剪切:将平板金属沿剪切线剪切成一定形状和尺寸的零件的过程。
(4)弯曲:将平板金属沿模具凸模形状弯曲,形成具有一定角度的零件的过程。
三、模具设计概述1. 模具设计原则(1)满足产品精度和尺寸要求:模具设计应保证冲压产品具有高精度和尺寸稳定性。
(2)提高生产效率:模具设计应优化工艺流程,减少不必要的加工步骤,提高生产效率。
(3)降低生产成本:模具设计应选用合适的材料,降低模具成本。
(4)确保模具寿命:模具设计应考虑模具的耐磨性、耐腐蚀性等性能,延长模具使用寿命。
2. 模具设计步骤(1)产品分析:分析产品的形状、尺寸、材料等,确定模具设计的基本要求。
(2)工艺分析:根据产品形状和尺寸,确定冲压工艺类型,如拉深、成形、剪切、弯曲等。
(3)模具结构设计:根据工艺要求,设计模具结构,包括凸模、凹模、导向装置、压边装置等。
(4)模具零件设计:根据模具结构,设计模具零件,如凸模、凹模、导向装置、压边装置等。
(5)模具加工:根据模具零件设计,进行模具加工。
(6)模具调试:完成模具加工后,进行模具调试,确保模具性能符合要求。
四、冲压工艺及模具设计要点1. 冲压工艺要点(1)合理选择材料:根据产品形状、尺寸、性能要求,选择合适的金属材料。
冲压模具设计方法与步骤

冲压模具设计的方法与步骤1、冲压零件的冲压工艺性分析冲压零件必须具有良好的冲压工艺性,才能以最简单、最经济的方法制造出合格的冲压零件,可以按照以下的方法完成冲压件的工艺性分析:a.读懂零件图;除零件形状尺寸外,重点要了解零件精度和表面粗糙度的要求。
b.分析零件的结构和形状是否适合冲压加工。
c.分析零件的基准选择及尺寸标注是否合理,尺寸、位置和形状精度是否适合冲压加工。
d.冲裁件断面的表面粗糙度要求是否过高。
e.是否有足够大的生产批量。
如果零件的工艺性太差,应与设计人员协商,提出修改设计的方案。
如果生产批量太小,应考虑采用其它的生产方法进行加工。
2、冲压工艺方案设计及最佳工艺规程设计:a.根据冲压零件的形状尺寸,初步确定冲压工序的性质,如:冲裁、弯曲、拉深、胀形、扩孔。
b.核算各冲压成形方法的变形程度,若变形成度超过极限变形程度,应计算该工序的冲压次数。
c.根据各工序的变形特点和质量要求,安排合理的冲压顺序。
要注意确保每道工序的变形区都是弱区,已经成形的部分(含已经冲制出的孔或外形)在以后的工序中不得再参与变形,多角弯曲件要先弯外后弯内,要安排必要的辅助工序和整形、校平、热处理等工序。
d.在保证制件精度的前提下,根据生产批量和毛坯定位与出料要求。
确定合理的工序组合方式。
e.要设计两个以上的工艺方案,并从质量、成本、生产率、模具的刃磨与维修、模具寿命及操作安全性等各个方面进行比较,从中选定一个最佳的工艺方案。
f.初步确定各个工序的冲压设备。
3、冲压零件毛坯设计及排样图设计:a.按冲压件性质尺寸,计算毛坯尺寸,绘制毛坯图。
b.按毛坯性质尺寸,设计排样图,进行材料利用率计算。
要设计多种排样方案,经过比较选择其中的最佳方案。
4、冲压模具设计:a.确定冲压加工各工序的模具结构形式,并绘制模具简图。
b.对指定的1—2个工序的模具进行详细的结构设计,并绘制模具工作图。
设计方法如下:※确定模具的种类:简单模、连续模还是复合模。
锻造和冲压零件的结构设计

(1)避免锻件横 截面面积相差过大, 避免模锻件上有薄 壁、高肋及直径过 大的凸缘。
(a)
(b)
图7-38 模锻件结构工艺性示例1
(a)
(b)
图7-39 模锻件结构工艺性示例2
(2)对于形状复杂的锻件可考虑采用锻焊组合结构,如图7-40所示。 (3)为保证锻件易于从锻模模膛中取出,锻件必须具有一个合理的分模 面。 (4)在零件结构允许的情况下,尽量避免有深孔或多孔结构。当孔径小 于30 mm或孔深大于直径两倍时,不能直接冲出通孔,只能先压凹。
(一)对落料件和冲孔件的要求
在设计落料件和冲孔件时,应考虑以下原则。
(1)零件外形力求简单、对称。零件应尽可能采用圆形、矩形等规则 的形状,这样可以在排样时将废料减少到最低的程度,如图7-41所示。
(2)零件应尽量避免槽与细长悬臂结构,否则模具制造困难、寿命低。
(a)材料利用率高
(b)材料利用率低
图7-42 冲压件尺寸与厚度的关系
(二)对弯曲件的要求
(1)为了防止弯曲破裂,弯曲时应考虑纤维组织的方向,并且弯曲半 径R不能小于材料弯曲半径的最小许可值。常用材料的弯曲半径最小许可值 如表7-8所示。
材料
08 钢,10 钢 20 钢,30 钢,45 钢
黄铜、铝 硬铝
表7-8 弯曲半径最小许可值
弯曲半径最小许可值
圆柱体与圆柱体交接处的锻造很
2
困难,应改为平面与圆柱体交接,
或平面与平面交接
序号
不合理
3
表7-6(续)
合理
说明
加强肋与表面凸合等结构是难以 用自由锻方法获得,应避免这种设 计;椭圆形或工字形截面、弧线及 曲线形表面,也应尽量避免
(二)模锻件的结构工艺性
- 1、下载文档前请自行甄别文档内容的完整性,平台不提供额外的编辑、内容补充、找答案等附加服务。
- 2、"仅部分预览"的文档,不可在线预览部分如存在完整性等问题,可反馈申请退款(可完整预览的文档不适用该条件!)。
- 3、如文档侵犯您的权益,请联系客服反馈,我们会尽快为您处理(人工客服工作时间:9:00-18:30)。
沖裁件:
1. 不同曲線連接處需加适當的圓角;不同材料有 不同的要求,選取方法如下: (如圖示)
a> 落料: 線段夾角>=90°時, 圓角 值:018t~0.35t mm MIN; :018t~0.35t MIN;合金鋼取大值,鋁及類似材料 , 取小值; 線段夾角<90°時, 圓角值:0.35~0.70mm MIN; 合金鋼取大值,鋁及類似材料取小值; b> 沖孔: 線段夾角>=90°時, 圓角值:0.20t~0.45t mm MIN;合金鋼取大值,鋁及類似材料取小值; 線段夾 角<90°時, 圓角值:0.40~0.90mm MIN;合金鋼取大值, 鋁及類似材料取小值.
零件結构及工藝性:
五金沖壓零件:(ATT/BKT/CSP/STH/WSH…) 注塑零件:(ATT/BKT/CBP/CPE/FAN/FNH/SPC…)
鑄鋅/鋁零件(包括鑄鋁轉子)(ATT/BKT/DCR…)
五金沖壓零件:
沖裁件(ATT/AML/BKT/STL/TML/WSH): (包含所有與沖孔/落料有關形狀的零件); 彎 曲 件 (ATT/BKT/FAN/SLB/TML): ( 包 含所有與彎曲有關形狀的零件) ; 拉深件(BKT/RSE/FAN): (包含所有與拉 深有關形狀的零件) .
角>=2t mm ,最好取 5t~10t mm ; b> 矩形件: 圓角>=3t mm ,盡可能取拉深高度的至少1/5.
2. 3.
拉深件的凸緣寬度盡可能保持一致; 在零件的平面部分,尤其是在距邊緣較遠處, 局部凹坑的深度與突起的高度不宜過大.
寸標注方法:
依據零件的結构特點,盡可能在同一視 圖上表達同一形狀的所有的尺寸,且直觀明 瞭.同時要注意尺寸的相互關系,明確零件的 基准要素.力求測量基準,工藝基準與設計基 準重合.因此在尺寸標注需留意以下幾點:
彎曲件:
5. 對稱規格之彎曲件,左右彎曲半徑應一致. 不合理 合理
彎曲件:
6. 7. 必要時設計工芑孔定位. 切口和彎曲同時進行時,切口部分需帶有斜度. 不合理 合理
拉深件(BKT/RSE/FAN): (包含所有 與拉深有關形狀的零件)
1. 拉深件側壁與底面或凸緣連接處的圓角應盡 可能放大,取值方法如下: a> 圓形件: 底部圓角>=t mm ,最好取 3t~5t mm ; 凸緣圓
尺寸標注方法:
1.1 尺寸對應之形狀的可測性; 1.2 尺寸標注與成形工芑的一致性: 1.2.1 對於五金件成形工芑,標注內腔或深度尺寸及公差;如確 需標注外形或包含材料厚度之尺寸,必須考慮材料厚度之公 差;對於拉深件及類似形狀不允許標注外圓角. 1.2.2 對於壓注成型之零件(塑膠及鋁/鋅合金零件),因有出模 斜度,尺寸標注方法為”軸”類形狀標注大端尺寸; 為”孔” 類形狀標注小端尺寸. 1.3 其它要求參考國標:GB4458.4-84.
尺寸精度---五金沖壓零件:
沖裁件的精度:
精度等級 零件 尺寸 形狀 外形 <10 內孔 外形 10~50 內孔 外形 50~150 內孔 外形 <10 內孔 外形 10~50 內孔 外形 50~150 內孔 <1.0 0.12 0.08 0.16 0.10 0.22 0.12 0.03 0.025 0.04 0.04 0.06 0.05 材料厚度 (mm) 1.0~2.0 0.18 0.10 0.22 0.12 0.30 0.16 0.04 0.03 0.06 0.05 0.08 0.06 2.0~4.0 0.24 0.12 0.28 0.20 0.40 0.20 0.06 0.04 0.08 0.06 0.10 0.08
經濟級
精密級
尺寸精度---五金沖壓零件:
沖裁件的披鋒:
材料抗拉強度 ab/ M Pa 材料厚度 (mm) <250 (鋁/銅板) 正常 <=0.35 0.35~0.65 0.65~1.0 1.0~1.5 1.5~2.5 2.5~3.8 0.10 0.15 0.23 0.34 0.50 0.72 較高要求 0.07 0.11 0.17 0.25 0.37 0.54 250~400(普通碳鋼) 正常 0.07 0.10 0.17 0.24 0.35 0.50 較高要求 0.05 0.07 0.13 0.18 0.26 0.37 400~630(合金鋼) 正常 0.05 0.07 0.10 0.15 0.22 0.40 較高要求 0.04 0.05 0.07 0.11 0.13 0.30 >630 和硅鋼 正常 0.03 0.04 0.05 0.08 0.12 0.18 較高要求 0.02 0.03 0.04 0.06 0.09 0.13
垂直纖維方向 0.5 t 0.5 t 1.0 t 2.0 t 1.0 t 0..35 t 0.5 t 0.5 t 0.3 t 1.5 t 3.0 t
平行纖維方向 1.0 t 1.0 t 1.7 t 3.0 t 2.0 t 0.8 t 1.2 t 1.0 t 0.8 t 2.5 t 4.0 t
注明: 上述取值指披鋒在彎角的內層;如披鋒在彎角外層時,應放大彎曲半徑 .
彎曲件/拉深件的精度及彎曲件的 角度公差:
彎曲件/拉深件的精度:
材料厚度
成形與模 有關尺寸 成形與材料 厚度有關之 尺寸 自然形成或且與 材料厚度有關 成形與 模有關 尺寸 成形與材料 厚度有關之 尺寸 自然形成或且與 材料厚度有關之 尺寸
經濟級 <=1.0 >1.0~4.0 IT13 IT14 IT15 IT16 IT16 IT17 IT11彎曲件:
1. 過渡圓角: 板/帶料彎曲件的過渡圓角不宜小於最小彎 曲半徑,以免零件產生裂紋;但也不宜過大,否則彎曲角度 及圓角半徑的精度不能保証.最小彎曲半徑受材料的材質 及方向影響,取值如下: (t為材料厚度) 不合理 合理
材料名稱 08AL/10#/Q195 15#/20#/Q235-A 45#/50#/Q275 60Mn/T8 純銅 軟黃銅 黃銅(半硬型) 磷銅 鋁 半硬鋁 硬鋁
機械零件結构及工藝性設計
---沖壓零件
Xu Ming Engineering Department January,2004
前言
1.
2. 3.
4.
使大家對零件結构及工芑結構有進一步的認 識与提高; 對零件結构與模具的關系有初步的認識; 將一些工藝結構要求有效地運用到具体的工 作中去; 在真正意義上達到零件設計規範化,標準化.
彎曲件:
2. 彎曲件的彎邊:不宜過小,其值應大於R+2t mm.彎邊較 小時不能得到准確的形狀. 不合理 合理
彎曲件:
3. 寬度突變: 彎曲線不應在零件寬度突變處,如必須在 突變處,應事先設計工芑孔或工藝槽. 不合理 合理
彎曲件:
4. 在有孔的毛坯件上彎曲時,如使孔或槽不變形,應使其位 置分布于變形區域之外,其孔或槽邊到彎曲半徑中心的距 離為: 當t<2mm時,距離>=t mm; 當t>=2mm時,距離 >=2t mm. 不合理 合理
3.
沖裁件:
4. 孔與孔之間,孔與邊緣之間的距離不宜太 小,主要會影響模具強度及零件品質,通常 該距離會取>=2t mm,但不得小于3~4mm. 必要時可取1t~1.5tmm,但會降低模具壽命 或增加模具結構複雜程度. (如圖示)
不合理
合理
沖裁件
5. 在彎曲件或拉深件上沖孔時,其孔壁与工件最 近壁之間的距離不宜過小.取值如下: (如圖示) a> 彎曲件: 距離值: R+0.5t mm MIN(內側與外 側距離值一樣); b> 拉深件: 距離值: R+0.5t mm MIN(內側與外 側距離值一樣).
不合理
合理
沖裁件 :
2. 零件凸出部分或凹入部分寬度不宜太小, 並應盡量避免過長的懸臂和狹槽.(如圖示) a> 材料為高碳鋼時寬度取2t; b>材料為黃銅/鋁/軟鋼時寬度取1.5t. 注 明:t<1mm時,按t=1mm計算.
不合理
合理
沖裁件:
沖孔時孔的尺寸不宜過小,其大小與孔的形狀,材料的 材質/厚度有關.選取方法如下: (下述值均為最小值) a> 硬鋼: 圓形時, 孔徑值:1.3t mm ; 矩形時, 孔徑值:1.0t mm ; b> 軟鋼及黃銅: 圓形時, 孔徑值:1.0t mm ; 矩形時, 孔徑 值:0.7t mm ; c> 鋁: 圓形時, 孔徑值:0.8t mm ; 矩形時, 孔徑值:0.5t mm ; d> 酚醛層布(紙)板: 圓形時, 孔徑值:0.4 t mm ; 矩形時, 孔 徑值:0.35t mm .
主要內容介紹:
目的和期望達到的效果; 幾种不同生產工芑之零件的結构及工藝 性要點介紹; ; 零件的尺寸標注方法; 尺寸精度.
目的和期望:
通過此教材使大家對零件結构及工芑性設 計的重要性有進一步的認識与提高,對零件與 模具的關系有初步的認識,並能有效地運用到 具体的工作中去,從真正意義上達到零件設計 規範化,標準化.
精密級 IT13 IT13~IT14 IT13 IT13~IT14
彎曲件的角度公差:
彎角短邊尺寸 經濟級 精密級 >1~6 ±1°30`~3° ±1° >6~10 ±1°30`~3° ±1° >10~25 ±50`~3° ±30` >25~63 ±50`~3° ±30` >63~160 ±25`~3° ±20`