冲压模具翻边整形l类加工工艺
冲压模具毕业设计 翻边模的设计

基本内容及拟解决的主要问题:
1)设计落料模具
2)设计液压拉深模具
3)设计翻边模具
4)设计卷边模具
落料模具的设计主要是为了得到圆形板料的设计,根据逆向设计和理论要求,确定圆形板料的尺寸,根据圆形板料的尺寸来设计落料模具。在落料模设计的过程中,对板料的利用率进行计算,使其符合经济实用的要求[4]。在对落料模的设计中,根据其它相关类似模具的设计,落料模设计成通用的落料模结构。同时对落料冲压力进行计算来选择相对应的压力机。根据设计的数据,利用Solidworks软件画出三维模型。
Analysis of the complexity of the shade of such a shape, thin-walled parts of the structural characteristics.Easy for die-casting in the formation of cracks, lack of defects in the tensile properties of the process, and in accordance with the requirements of theoretical analysis and data based on the use of Solidworks 3D solid modeling software, and the provisions of unknown size. Then calculated using the three-dimensional entities, the quality of parts, in accordance with Solidworks software to design parts of the quality of the target plate thickness the diameter of the circular blank. According to the original blank diameter to determine the number of dimensions for the design and follow-up to provide a basis for research. At the same time, the use of Solidworks software or other three-dimensional software model of the stamping feasibility analysis and design, use of software related to shade Mold mold design.
冲压模具的基本工艺

压的基本工序:1.冲裁:包括落料和冲孔两个工序。
1)落料:模具沿封闭线冲切板料,冲下的部分为工件,其余部分为废料,设计时尺寸以模仁为准,间隙取在冲子上;2)冲孔:模具沿封闭线冲切板料,冲下的部分是废料,设计时尺寸以冲子为准,间隙取在模仁上。
2.剪切:用模具切断板材,切段线不封闭.3.切口:在坯料上将板材部分切开,切口部分发生弯曲.4.切边:将拉深或成形后的半成品边缘部分的多余材料切掉。
5.剖切:将半成品切开成两个或几个工件,常用于成双冲压。
切口切边剖切6.弯曲:用模具使材料弯曲成一定形状(V型/U型/Z型弯曲)。
7.卷圆:将板料端部卷圆。
8.扭曲:将平板的一部分相对于一部分扭转一个角度。
弯曲卷圆扭曲9.拉深:将板料压制成空心工件,壁厚基本不变。
10.变薄拉深:用减小直径与壁厚,增加工件高度的方法来改变空心件的尺寸,得到要求的底厚,壁薄的工件。
11.孔的翻边:将板料或工件上有孔的边缘翻成竖立边缘。
拉深变薄拉深孔的翻边12.外缘翻边:将工件的外缘翻起圆弧或曲线状的竖立边缘。
13.缩口:将空心件的口部缩小。
14.扩口:将空心件的口部扩大,常用于管子。
外缘翻边缩口扩口15.起伏:在板料或工件上压出筋条,花纹或文字,在起伏处的整个厚度上都有变薄。
16.卷边:将空心件的边缘卷成一定的形状。
17.胀形:将空心件(或管料)的一部分沿径向扩张,呈凸肚形。
起伏卷边胀形18.旋压:利用赶棒或滚轮将板料毛坯赶压成一定形状(分变薄与不变薄两种)。
19.整形:把形状不太准确的工件校正成形。
20.校平:将毛坯或工件不平的面或弯曲予以压平。
旋压整形校平21.压印:改变工件厚度,在表面上压出文字或花纹。
22.正挤压:凹模腔内的金属毛坯在凸模压力的作用下,处于塑性变形状态,使其由凹模孔挤出,金属流动的方向与凸模运动方向相同。
23.反挤压:金属挤压过程中,沿凸模与凹模的间隙塑流,其流动方向与凸模运动方向相反。
24.复合挤压:正挤与反挤的结合。
冲压件工艺过程设计的内容及步骤
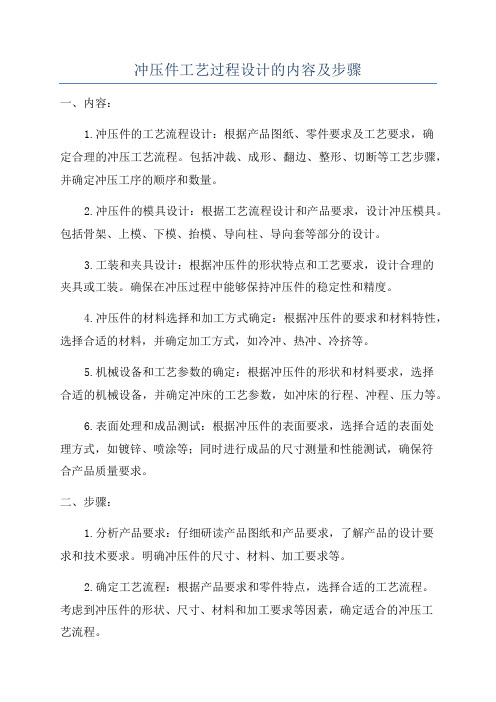
冲压件工艺过程设计的内容及步骤一、内容:1.冲压件的工艺流程设计:根据产品图纸、零件要求及工艺要求,确定合理的冲压工艺流程。
包括冲裁、成形、翻边、整形、切断等工艺步骤,并确定冲压工序的顺序和数量。
2.冲压件的模具设计:根据工艺流程设计和产品要求,设计冲压模具。
包括骨架、上模、下模、抬模、导向柱、导向套等部分的设计。
3.工装和夹具设计:根据冲压件的形状特点和工艺要求,设计合理的夹具或工装。
确保在冲压过程中能够保持冲压件的稳定性和精度。
4.冲压件的材料选择和加工方式确定:根据冲压件的要求和材料特性,选择合适的材料,并确定加工方式,如冷冲、热冲、冷挤等。
5.机械设备和工艺参数的确定:根据冲压件的形状和材料要求,选择合适的机械设备,并确定冲床的工艺参数,如冲床的行程、冲程、压力等。
6.表面处理和成品测试:根据冲压件的表面要求,选择合适的表面处理方式,如镀锌、喷涂等;同时进行成品的尺寸测量和性能测试,确保符合产品质量要求。
二、步骤:1.分析产品要求:仔细研读产品图纸和产品要求,了解产品的设计要求和技术要求。
明确冲压件的尺寸、材料、加工要求等。
2.确定工艺流程:根据产品要求和零件特点,选择合适的工艺流程。
考虑到冲压件的形状、尺寸、材料和加工要求等因素,确定适合的冲压工艺流程。
3.设计模具和工装:根据工艺流程设计和产品要求,设计合理的冲压模具和工装。
包括骨架、上模、下模、抬模、导向柱、导向套等部分的设计,并确保模具和工装的合理性和可行性。
4.选择材料和加工方式:根据冲压件的要求和材料特性,选择合适的材料,考虑材料的强度、硬度、韧性等性能要求。
同时,根据冲压件的形状和材料要求,确定适合的加工方式。
5.确定机械设备和工艺参数:根据冲压件的形状和材料要求,选择合适的机械设备,确定冲床的工艺参数。
包括冲床的行程、冲程、压力等参数。
6.表面处理和成品测试:根据冲压件的表面要求,选择合适的表面处理方式,如镀锌、喷涂等。
同时进行成品的尺寸测量和性能测试,确保冲压件符合产品质量要求。
冲压工艺基础知识

冲压模具基础知识(术语)冲裁冲裁是利用冲模使部分材料或工序件与另一部分材料、工(序)件或废料分离的一种冲压工序。
冲裁是切断、落料、冲孔、冲缺、冲槽、剖切、凿切、切边、切舌、切开、整修等分离工序的总称。
切开切开是将材料沿敞开轮廓局部而不是完全分离的一种冲压工序。
被切开而分离的材料位于或基本位于分离前所处的平面。
切边切边是利用冲模修边成形工序件的边缘,使之具有一定直径、一定高度或一定形状的一种冲压工序。
切舌切舌是将材料沿敞开轮廓局部而不是完全分离的一种冲压工序。
被局部分离的材料,具有工件所要求的一定位置,不再位于分离前所处的平面上。
切断切断切断是将材料沿敞开轮廓分离的一种冲压工序,被分离的材料成为工件或工序件。
扩口扩口是将空心件或管状件敞开处向外扩张的一种冲压工序。
冲孔冲孔是将废料沿封闭轮廓从材料或工序件上分离的一种冲压工序,在材料或工序件上获得需要的孔。
冲缺冲缺是将废料沿敞开轮廓从材料或工序件上分离的一种冲压工序,敞开轮廓形成缺口,其深度不超过宽度。
冲槽冲槽是将废料沿敞开轮廓从材料或工序件上分离的一种冲压工序,敞开轮廓呈槽形,其深度超过宽度。
冲中心孔冲中心孔是在工序件表面形成浅凹中心孔的一种冲压工序,背面材料并无相应凸起。
精冲精冲是光洁冲裁的一种,它利用有带齿压料板的精冲模使冲件整个断面全部或基本全部光洁。
连续模连续模是具有两个或更多工位的冲模,材料随压力机行程逐次送进一工位,从而使冲件逐步成形。
单工序模单工序模是在压力机一次行程中只完成一道工序的冲模。
组合冲模组合冲模是按几何要素(直线、角度、圆弧、孔)逐副逐步形成各种冲件的通用、可调式成套冲模。
平面状冲件的外形轮廓一般需要几副组合冲模分次冲成。
压凸压凸是用凸模挤入工序件一面,迫使材料流入对面凹坑以形成凸起的一种冲压工序。
压花压花是强行局部排挤材料,在工序件表面形成浅凹花纹,图案、文字或符号的一种冲压工序。
被压花表面的背面并无对应于浅凹的凸起。
成形成形是依靠材料流动而不依靠材料分离使工序件改变形状和尺寸的冲压工序的统称。
冲压模具的加工工艺规程

冲压模具的加工工艺规程
摘要:胀形、翻边、缩口的冲压模分工序、分设备进行,工件经历变形—校正过程。
冷精压模主要为平面精压,以矫正工件变形为主。
关键词:分工序分设备校正过程冷精压模矫正工件变形冲压模具加工工艺规程。
胀形、翻边、缩口的冲压模分工序、分设备进行,工件经历变形—校正过程。
冷精压模主要为平面精压,以矫正工件变形为主。
1 胀形
常用的胀形方法有刚模胀形和以液体、气体、橡胶等为施力介质的软模胀形。
2 胀形的变形特点
球头凸模胀形平板毛坯时的胀形变形区及其主应力和主应变图。
图中涂黑部分表示胀形变形区。
2.1 胀形的极限变形程度
胀形极限变形程度主要取决于材料的塑性和变形的均匀性。
压加强筋。
(1)用刚性凸模压制加强筋的变形力按式计算;
4 胀形力
刚模胀形所需压力的计算公式,可根据力的平衡方程式推导得到,其表达式为。
7 缩口
缩口是将预先成形好的圆筒件或管件坯料,通过缩口模具将其口部缩小的一种成形工序。
常见的缩口形式有斜口式、直口式和球面式。
变形区由于受到较大切向压应力的作用易产生切向失稳而起皱,
起传力作用的筒壁区由于受到轴向压应力的作用易产生轴向失稳而起皱,所以失稳起皱是缩口工序的主要障碍。
参考文献
[1] 薛翔.冲压工艺与模具设计实例分析[M].北京:机械工业出版社,2008.
[2] 徐政坤.冲压模具设计与制造[M].北京:化学工业出版社,2009.
[3] 洪慎章.实用冲模设计与制造[M].北京:机械工业出版社,2012.。
模具分种几类型

冲压模具的形式很多,冲模也依工作性质,模具构造,模具材料三方面来分类。
一般可按以下几个主要特征分类:1〃根据工艺性质分类a.冲裁模沿封闭或敞开的轮廓线使材料产生分离的模具。
如落料模、冲孔模、切断模、切口模、切边模、剖切模等。
b.弯曲模使板料毛坯或其他坯料沿着直线(弯曲线)产生弯曲变形,从而获得一定角度和形状的工件的模具。
c.拉深模是把板料毛坯制成开口空心件,或使空心件进一步改变形状和尺寸的模具。
d.成形模是将毛坯或半成品工件按图击、凹模的形状直接复制成形,而材料本身仅产生局部塑性变形的模具。
如胀形模、缩口模、扩口模、起伏成形模、翻边模、整形模等。
2〃根据工序组合程度分类a.单工序模在压力机的一次行程中,只完成一道冲压工序的模具。
b.复合模只有一个工位,在压力机的一次行程中,在同一工位上同时完成两道或两道以上冲压工序的模具。
c.级进模(也称连续模)在毛坯的送进方向上,具有两个或更多的工位,在压力机的一次行程中,在不同的工位上逐次完成两道或两道以上冲压工序的模具。
3、依产品的加工方法分类依产品加工方法的不同,可将模具分成冲剪模具、弯曲模具、抽制模具、成形模具和压缩模具等五大类。
a. 冲剪模具:是以剪切作用完成工作的,常用的形式有剪断冲模、下料冲模、冲孔冲模、修边冲模、整缘冲模、拉孔冲模和冲切模具。
b.弯曲模具:是将平整的毛胚弯成一个角度的形状,视零件的形状、精度及生产量的多寡,乃有多种不同形式的模具,如普通弯曲冲模、击轮弯曲冲模、卷边冲模、圆弧弯曲冲模、折弯冲缝冲模与扭曲冲模等。
c.抽制模具:抽制模具是将平面毛胚制成有底无缝容器。
d.成形模具:指用各种局部变形的方法来改变毛胚的形状,其形式有击张成形冲模、卷缘成形冲模、颈缩成形冲模、孔击缘成形冲模、圆缘成形冲模。
e.压缩模具:是利用强大的压力,使金属毛胚流动变形,成为所需的形状,其种类有挤制冲模、压花冲模、压印冲模、端压冲模。
汽车门槛内板翻边成形复合模冲压工艺设计

状 , 先 考 虑 刀 口 间 隙 和 减 料 边 , 角 起 皱 时 也 应 考 虑 但 转 刀 口间 隙 是 否 太 大 , 是 否 没 地 方 走 , 要 考 虑 减 料 边 料 也
表 面 平 整 光 滑 ,无 翘
是 制 造 这 类 零 件 的 关 键 , 直 接 影 响 产 品 质 量 、 料 利 它 材
用 率 、生 产 效 率 和 制 造 成 本 。 由 于 零 件 表 面 质 量 要 求 高 , 状 复杂 且生 产 批量 大 , 形模 具 结 构 复杂 , 般 形 成 一 不 经 过 多 次 成 形 , 采 用 单 动 ( 双 动 ) 床 一 次 成 形 而 或 压 而 成 。 因 此 , 艺 制 定 的 合 理 与 否 。 接 决 定 材 料 消 耗 工 直 的 多 少 ;翻 边 整 形 之 前 是 否 需 要 设 置 毛 坯 形 状 的修 边 和 预 先 折 弯 的 工 序 , 接 影 响 修 边 、 边 工 序 的 排 列 顺 直 翻 序 和 次 数 多 少 , 以及 完 成 这 些 工 序 的 冲模 复 杂 程 度 和
2 初 步 建 立 零 件 工 艺 补 充数 模
工 艺 补 充 部 分 是 汽 车 门槛 内板 翻 边 整 形 模 具 设 计 的 主 要 内 容 , 该 部 分 的设 计 优 劣 决 定 了最 终 零 件 的 质 量 。 同 时 , 由 于 工 艺 补 充 部 分 在 翻 边 整 形 之 后 必 须 去 掉 , 少 的工艺 补充 能降 低材料 的消耗 。 较
冲压模具毕业设计翻边模设计

刃口尺寸的调整方法:根据冲压件的尺寸和形状,以及冲压机的压力和速度,进行适当的调整
刃口尺寸的确定注意事项:刃口尺寸的确定要符合冲压件的尺寸和形状,以及冲压机的压力和速度,以保证冲压件的质量和生产效率。
刃口尺寸的确定原则:根据冲压件的尺寸和形状,以及冲压机的压力和速度来确定
刃口尺寸的计算方法:根据冲压件的尺寸和形状,以及冲压机的压力和速度,利用公式进行计算
材料处理:对材料进行热处理、表面处理等,提高材料的耐磨性、耐腐蚀性和抗疲劳性
翻边模的工艺参数设计
PART FIVE
冲压工艺方案的确定
确定冲压工艺方案的目的:提高生产效率,降低成本,保证产品质量
冲压工艺方案的选择:根据产品形状、尺寸、材料等因素选择合适的冲压工艺方案
冲压工艺方案的设计:包括模具设计、冲压设备选择、冲压工艺参数设定等
退火:将模具材料加热到一定温度后保温一定时间,消除应力,提高塑性和韧性
调质:将模具材料加热到一定温度后保温一定时间,然后冷却,提高硬度和韧性
渗碳:将模具材料加热到一定温度后渗入碳元素,提高表面硬度和耐磨性
模具材料的选用原则
材料强度:应满足模具的使用寿命要求
材料硬度:应与冲压件的硬度相匹配
材料耐磨性:应具有良好的耐磨性,减少磨损
冲压工艺方案的优化:根据生产实际情况,对冲压工艺方案进行优化和改进,以提高生产效率和产品质量。
冲裁间隙的确定
冲裁间隙的定义:冲裁过程中,冲头和被冲材料之间的最小距离
冲裁间隙的确定方法:经验公式法、试验法、计算机模拟法等
冲裁间隙的确定原则:保证冲裁质量、提高生产效率、降低成本等
冲裁间隙的影响因素:材料性质、冲头形状、冲压速度等
寿命预测的重要性:合理预测模具寿命,有助于优化生产工艺,降低生产成本,提高产品质量。
冲压模具翻遍整形模毕业设计说明书
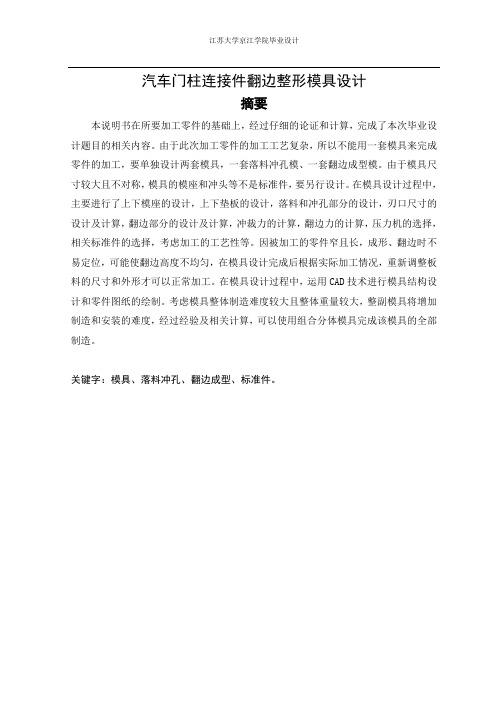
汽车门柱连接件翻边整形模具设计摘要本说明书在所要加工零件的基础上,经过仔细的论证和计算,完成了本次毕业设计题目的相关内容。
由于此次加工零件的加工工艺复杂,所以不能用一套模具来完成零件的加工,要单独设计两套模具,一套落料冲孔模、一套翻边成型模。
由于模具尺寸较大且不对称,模具的模座和冲头等不是标准件,要另行设计。
在模具设计过程中,主要进行了上下模座的设计,上下垫板的设计,落料和冲孔部分的设计,刃口尺寸的设计及计算,翻边部分的设计及计算,冲裁力的计算,翻边力的计算,压力机的选择,相关标准件的选择,考虑加工的工艺性等。
因被加工的零件窄且长,成形、翻边时不易定位,可能使翻边高度不均匀,在模具设计完成后根据实际加工情况,重新调整板料的尺寸和外形才可以正常加工。
在模具设计过程中,运用CAD技术进行模具结构设计和零件图纸的绘制。
考虑模具整体制造难度较大且整体重量较大,整副模具将增加制造和安装的难度,经过经验及相关计算,可以使用组合分体模具完成该模具的全部制造。
关键字:模具、落料冲孔、翻边成型、标准件。
Automotive Connectors post mold design plastic flangeAbstractThis instruction booklet in must process the components in the foundation, after careful proof and computation, has completed this graduation project topic related content. Because this processing components craft is complex, so we can not use a die to complete the processing of this parts, must alone design two sets of dies, a cutting punched hole die, a upsiding down edges die. Because the mold size is big also is asymmetrical, the die base and punch is not a standard hardware, must separate design. In die design process, mainly process project on the punch set, die set, punch pad, die pad, pierce, forming , tool point design and size calculation, upsiding down edgesof the design and calculation, stamping power calculation, upsiding down edges power calculation, hydraulic machine select, Related standards of standard parts atc. Because the components processes is been narrow also is long, bending and upsiding down edges not positioning, In die design based on the actual completion of the processing, readjusts the sheet size and the contour only then may process normally. In die design process, exertion CAD structural design and layout for the parts drawings. Consider a molding tool a whole manufacturing a difficulty bigger and whole weight to compare greatly, the whole molding tool difficulty of increment manufacturing and fixing, through experience and the related calculation, can use a discrete molding tool of combination to complete all manufacturings of this mold tool.Keyword:die, punched hole, upsiding down edges, standard parts目录引言 (1)第1章设计任务书 (2)第2章确定工艺方案 (3)第3章相关计算 (4)3.1内孔翻边的工艺计算 (4)3.1.1翻边件的口部壁厚 (5)3.1.2翻边力P和翻边功A (5)3.1.3翻边间隙和凸、凹模尺寸 (5)3.2内凹外缘翻边的计算 (6)3.3翻边凹模刃部的入模量 (7)第4章初步选定压力机 (9)4.1压力机类型的选择 (9)4.2压力机规格的选择 (9)第5章模具安装 (11)第6章翻边模具主要零件的结构设计与加工工艺 (12)6.1模具材料的选用 (12)6.2模具的总体设计 (12)6.3工作零件的结构设计 (12)6.4 模架、模柄的选择 (14)6.5螺钉的选择 (14)第7章成形模具凸凹模的数控加工工艺分析 (15)7.1 产品分析 (15)7.2 成型零件结构与分析 (15)7.3 工艺分析 (15)7.3.1工艺基准选择 (16)7.3.2装夹方式的选择 (16)7.3.3加工顺序安排 (16)7.4 基于MaterCAM的数控加工工艺过程 (17)7.5 分析与小结 (17)第8章选定设备 (19)总结 (20)参考文献 (22)引言模具是用以限定生产对象的形状和尺寸的装置。
冲压工艺技术介绍

数据工艺编制例子说明
修边线
侧修边线 修边线
翻边线
侧 冲 孔
侧修边线
侧翻边线
侧修边线
数据工艺编制例子说明
3:B12-8402501.CATPart
003
8402501
发盖内板
54 05 10 20 30 40 50 60 檢具
DR
1
TR+CTR
1
FL+CTR+CPI
1
CFL
1
数据工艺编制例子说明
压料面
B
A
ABຫໍສະໝຸດ A分模线分模线
B A
修边线
B
修边线
拉延与成型的区别
1.当零件成形深度大于10MM时最好采用拉延方式,避免出现挤料现象, 小于10的可以考虑用成型.同时成型过程中为避免叠料通常加工艺缺口. 2.拉延一般需要做出完整的工艺补充面及压料面,且是一个封闭的几何形状, 但成型可以只作出局部,无需全部封闭 3.同一零件相同材料牌号,采用拉延或成型工艺得到的产品,在刚性方面前者 比后者强. 4.零件产品接近于封闭的零件最好采用拉延,敞口的可以采用成型
B、提高材料利用率
C、成型前的板料相对于成型后的零件有大面积未参与成型
开卷落料与普通落料的区别
A、产品零件较大,人工操作劳动强度大的零件尽量采用开卷落 料。 B、相对于普通落料模,可以提高材料利用率的零件,采用开卷 落料。 C、毛坯所需要的卷料宽度太小或太宽,无法采用开卷落料的, 需要采用普通落料模式。 D 、零件工艺路线规划在自动化线上生产的零件,其落料模最好 采用开卷落料。
成形工序分:拉延、翻边、整形、翻孔、弯曲等
工序 名称
图示
特点
冲压模具加工工艺流程
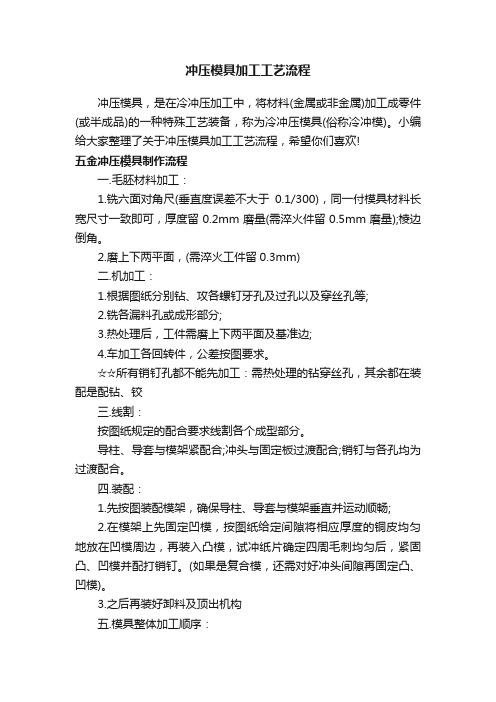
冲压模具加工工艺流程冲压模具,是在冷冲压加工中,将材料(金属或非金属)加工成零件(或半成品)的一种特殊工艺装备,称为冷冲压模具(俗称冷冲模)。
小编给大家整理了关于冲压模具加工工艺流程,希望你们喜欢!五金冲压模具制作流程一.毛胚材料加工:1.铣六面对角尺(垂直度误差不大于0.1/300),同一付模具材料长宽尺寸一致即可,厚度留0.2mm磨量(需淬火件留0.5mm磨量);棱边倒角。
2.磨上下两平面,(需淬火工件留0.3mm)二.机加工:1.根据图纸分别钻、攻各螺钉牙孔及过孔以及穿丝孔等;2.铣各漏料孔或成形部分;3.热处理后,工件需磨上下两平面及基准边;4.车加工各回转件,公差按图要求。
☆☆所有销钉孔都不能先加工:需热处理的钻穿丝孔,其余都在装配是配钻、铰三.线割:按图纸规定的配合要求线割各个成型部分。
导柱、导套与模架紧配合;冲头与固定板过渡配合;销钉与各孔均为过渡配合。
四.装配:1.先按图装配模架,确保导柱、导套与模架垂直并运动顺畅;2.在模架上先固定凹模,按图纸给定间隙将相应厚度的铜皮均匀地放在凹模周边,再装入凸模,试冲纸片确定四周毛刺均匀后,紧固凸、凹模并配打销钉。
(如果是复合模,还需对好冲头间隙再固定凸、凹模)。
3.之后再装好卸料及顶出机构五.模具整体加工顺序:1.优先加工需要热处理的工件2.其次加工.需要线切割的工件3.然后加工模架部件即上托和底座4.再后加工其它部件。
5.装配、试模冲压模具的分类根据工艺性质分类a.冲裁模沿封闭或敞开的轮廓线使材料产生分离的模具。
如落料模、冲孔模、切断模、切口模、切边模、剖切模等。
b.弯曲模使板料毛坯或其他坯料沿着直线(弯曲线)产生弯曲变形,从而获得一定角度和形状的工件的模具。
c.拉深模是把板料毛坯制成开口空心件,或使空心件进一步改变形状和尺寸的模具。
d.成形模是将毛坯或半成品工件按图凸、凹模的形状直接复制成形,而材料本身仅产生局部塑性变形的模具。
如胀形模、缩口模、扩口模、起伏成形模、翻边模、整形模等。
冲压模具工艺基础

1第一章:工艺培训第一节 冲压加工概述1.冲压车间工艺流程原材料(板料和卷料)入库 → 开卷线 → 大件清洗涂油、小件开卷剪切 → (10、20、30、40、50冲压生产线) → 安装模具调试首件合格 → 投入批量生产(自检、专检) → 合格件防锈 → 入库 2.冷冲压的概念及特点 2.1冷冲压的定义冷冲压是指在常温下,利用安装在压力机上的冲模对材料施加压力,使其产生分离或塑性变形,从而获得所需要零件的一种压力加工方法。
2.2冷冲压的特点产品尺寸稳定,精度高,重量轻,刚度好,互换性好,高效低耗,操作简单,易于实现自动化。
3.冷冲压基本工序的分类冷冲压概括起来分两大类:分离工序和成形工序。
3.1 分离工序是板料在外力作用下沿一定的轮廓线分离而获得一定形状、尺寸和切断面质量的成品和半成品。
分离工序分:落料、冲孔、切断、修边等工序名称图示特点落料用冲模沿封闭曲线冲切,冲下部分是零件。
用于制造各种形状的平板零件冲孔用冲模沿封闭曲线冲切,冲下部分是废料。
用于制造各种形状的平板零件2切断用冲模沿不封闭曲线冲切产生分离修边将成形零件的边缘修切整齐或切成一定形状3.2成形工序是坯料在不破裂的条件下产生塑性变形而获得一定形状和尺寸的成品和半成品。
成形工序分:拉延、翻边、整形、翻孔、弯曲等工序名称图示 特点拉延把板料毛坯成形制成各种开口空心零件翻边把板料或半成品的边缘沿一定的曲线按一定的曲率成形成竖立的边缘整形为了提高已成形零件的尺寸精度或获得小的圆角半径而采用的成形方法翻孔在预先冲孔的板料或半成品上或未经冲孔的板料制成竖立的边缘弯曲把板料沿直线弯成各种形状,可以加工形状极为复杂的零件3.3各工序名称及其代号工序名称拉延 修边冲孔整形成形翻边翻孔代号 DR TR PRC RST FO FL BUR工序名称切角 翻口压合落料弯曲切开斜楔冲孔代号 CT BU HEM BL BE SEP CAM-PRC第二节 普通冲裁冲裁,在广义上讲,是分离工序的总称。
冲压模具加工工艺的翻边工艺

冲压模具加工工艺的翻边工艺
冲压模具加工工艺的翻边工艺是在预先加工好或部分孔型的毛料上(有时也可不预先加工孔),依靠材料的拉伸变形沿一定的曲线翻成竖边的冲压方法,分圆孔翻边和外缘翻边。
由于是通过对材料的拉伸成形,故其成形主要受材料延伸率大小的限制。
翻边主要用来铆合、过孔、攻丝等用途。
1、圆孔翻边的模具与计算公式及相关工艺要求数据如下:
公式:d=0.5~0.6T;d的取值与H成反比,d值小时,H值就大。
D=D1+(D-D1)=D1+1.3T;为了保证翻边D的垂直度,在一般情况下D≤D1+1.3T。
H=+0.43R+0.72T;翻边高度H(取决于翻边金属的体积)通常为1.7T~1.9T。
L=+2.5T;M为螺纹规格。
式中
d——预冲孔直径
D1——翻边孔内径、凸模冲子
D2——翻边竖边直径(按中心层计算)
D——翻边孔外径
H——翻边孔高度
R——翻边内半径、凹模外半径
L——翻边孔中心距边距
T——材料厚度
工艺要求:
翻边孔高度≥3P;P为螺纹牙距。
翻边同一平面的孔距公差为≥±0.15
不推荐使用T=1.5mm的不锈钢进行M3翻边,T=2.0的不锈钢进行M4翻边。
铝板翻边攻丝时要考虑螺纹所能承受的力。
2、外缘翻边分外凸轮廓和内凹轮廓翻边两种形式;外凸轮廓的翻边也称压缩类翻边,内凹轮廓的翻边也称伸长类翻边,见下图:
说明:
R——制件翻边后圆角半径
b——翻边前的半径与翻边后的半径之差
R+b、R-b——制件翻边前(毛坯)的圆角半径。
CATIA 翻边整形模(5)
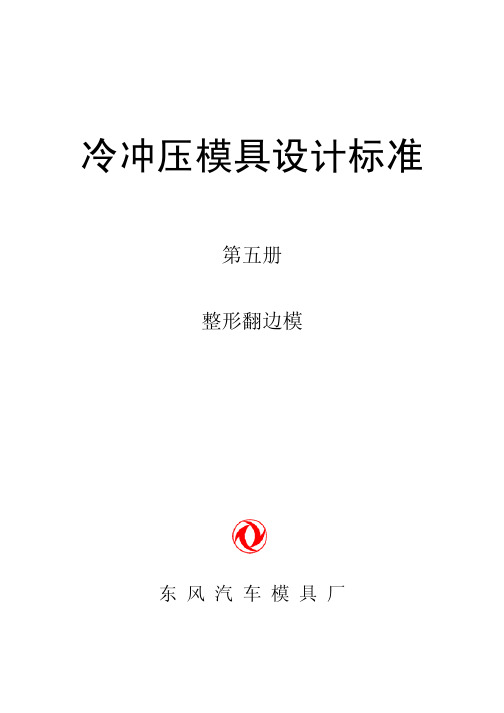
整形翻边模
顶出器
顶出器的导向
17 (1)
适用
○大量生产时 ○顶出力大时
简图
无导板
○少量生产时 ○顶出力小时 (但是,为方便制造时调 整,有时单侧必须用导 板)
使用顶出器限位器部分
○实际使用情况根据技术协议要求决定。
4.2 特殊的导向方法 极少量生产的情况下,采用凹模镶块或导向块来导向。
东风汽车模具厂
l:整形翻边加工长度 P2:平衡用压力(kgf) 2.2 系数 a 值(整圆角时,也按以下要求)见下表。
15 (1)
注:当产品有特殊技术要求时,不按此表,根据不同的产品资料。
东风汽车模具厂
冷冲压模具设计标准 5——3
3 3.1 标准
3.2 注意事项
整形翻边模
顶出器
顶出器工作表面
16 (1)
☆ 零件的工作表面比凸模的工 作表面少 10mm。
钢材镶块
铸钢或球铁
压弯翻边时,顶出器断面强度弱的部分,底面必须与底板接触。
东风汽车模具厂
冷冲压模具设计标准 5——3
6
整形翻边模
顶出器
顶出器与凹模的间隙
19 (1)
顶出器相对与凹模的 间隙为 0.5。
东风汽车模具厂
冷冲压模具设计标准 5——4
1
整形翻边模
翻边退料板
翻边退料板的使用条件
1.1 使用条件 翻边不易退件的部位,必须设置翻边退料板。
冷冲压模具设计标准 5——3
5
5.1 标准厚度 顶出器的厚度以右图为基准。 铸件的情况下,特别是在中间 部位,顶出器的断面面积明显 变小时,应注意其强度。
整形翻边模
顶出器
顶出器的强度
汽车冲压模具狄原整形翻边
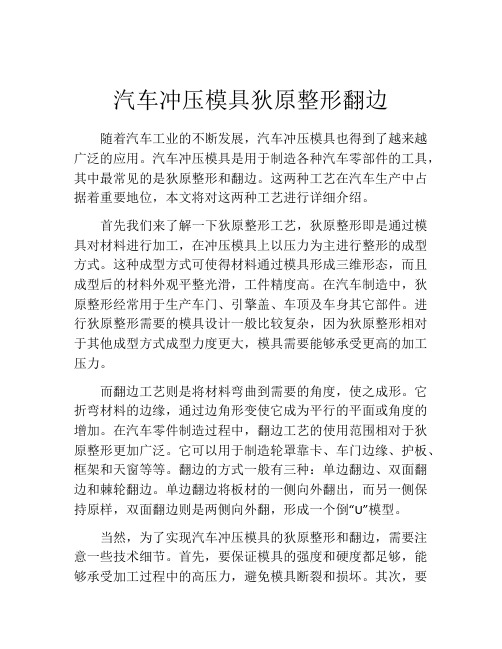
汽车冲压模具狄原整形翻边随着汽车工业的不断发展,汽车冲压模具也得到了越来越广泛的应用。
汽车冲压模具是用于制造各种汽车零部件的工具,其中最常见的是狄原整形和翻边。
这两种工艺在汽车生产中占据着重要地位,本文将对这两种工艺进行详细介绍。
首先我们来了解一下狄原整形工艺,狄原整形即是通过模具对材料进行加工,在冲压模具上以压力为主进行整形的成型方式。
这种成型方式可使得材料通过模具形成三维形态,而且成型后的材料外观平整光滑,工件精度高。
在汽车制造中,狄原整形经常用于生产车门、引擎盖、车顶及车身其它部件。
进行狄原整形需要的模具设计一般比较复杂,因为狄原整形相对于其他成型方式成型力度更大,模具需要能够承受更高的加工压力。
而翻边工艺则是将材料弯曲到需要的角度,使之成形。
它折弯材料的边缘,通过边角形变使它成为平行的平面或角度的增加。
在汽车零件制造过程中,翻边工艺的使用范围相对于狄原整形更加广泛。
它可以用于制造轮罩靠卡、车门边缘、护板、框架和天窗等等。
翻边的方式一般有三种:单边翻边、双面翻边和棘轮翻边。
单边翻边将板材的一侧向外翻出,而另一侧保持原样,双面翻边则是两侧向外翻,形成一个倒“U”模型。
当然,为了实现汽车冲压模具的狄原整形和翻边,需要注意一些技术细节。
首先,要保证模具的强度和硬度都足够,能够承受加工过程中的高压力,避免模具断裂和损坏。
其次,要注意模具表面的平整度和光洁度,这也是保证成品造型平整光滑的关键因素。
最后,模具的设计一定要细致、精准,充分考虑材料弹性、收缩率、伸长率等因素。
这样才能满足高标准的汽车制造要求。
总结一下,汽车冲压模具的狄原整形和翻边工艺都是用于制造汽车零部件的重要工艺,在汽车工业中占有不可替代的地位。
随着技术的不断进步和创新,这些工艺的应用范围也将不断拓展和完善,为汽车制造业的发展提供更强的保障和基础。
模具技术要求

模具技术要求一.模具材料及热处理要求1.拉延、成形类模具●外板件拉延序凸模、凹模及压边圈使用GGG70L铸铁,淬火硬度HRC50-55;内板件凸模、凹摸及压边圈使用MoCr铸铁,淬火硬度HRC50-55.特殊情况下须渗氮或TD处理(模具图纸会签时确认)。
●变形剧烈及高强度钢板(抗拉强度≥350MPa)的制件应采用整体镶Cr12MoV;淬火硬度要达到HRC58—62。
●基体采用HT300。
采用键槽与螺栓链接。
●GGG70L铸件厂:天津虹岗或长城精工或经甲方认可的同等铸造品质铸造厂。
2.冲裁类模具●普通板料零件料厚小于或等于1.2mm的刃口镶块可采用空冷钢(7CrSiMnMoV 或ICD-5),淬火硬度HRC55-60;料厚大于1。
2mm的采用Cr12MoV材料,淬火硬度为HRC58~62。
料厚大于等于1。
4mm的镶块采用波浪刃口.●高强度板的制件采用Cr12MoV材料,淬火硬度为HRC58~62。
●所有凹模镶块、废料刀均采用背托,凹模采用镶块结构,凸模可采用整体结构。
●模具基体采用HT300。
3.翻边、整形类模具●中大型模具凹模镶块原则上应采用侧面固定式以便于调整;小型模具可采用整体式结构,料厚大于1。
4mm的凹模采用镶块式。
●零件料厚小于或等于1。
2mm,材料可选用MoCr/7CrSiMnMoV;零件料厚大于1。
2mm 的采用Cr12MoV或与之相当的材料(应取得甲方工艺认可,具体以会签为准)。
●普通板料的制件凸模可采用合金铸铁,表面淬火硬度不低于HRC50;高强度板的制件采用Cr12MoV材料,淬火硬度为HRC58—62;如采用分体或镶块式基座(底板)可采用HT300的材料。
●对于部分易拉毛部位,必要时需进行TD处理。
4.压料(退料)顶出器可采用铸造结构,但应根据其强度要求,决定用铸铁或球铁或铸钢材料(工艺会签时,甲方根据具体结构决定)。
5.其它部件材质及热处理按国家标准执行。
二.模具结构及技术要求1.模具结构1。
冲压模具工序分类

冲压模具工序分类
冲压加工中为满足冲压零件地形状、尺寸、精度批量、原材料性能等不同方面地要求,所采用地工序也不同.根据材料地变形特点可将冷冲压工序分为分离工序和成形工序两类.
1.分离工序——是指坯料在冲压力作用下,变形部分地应力达到强度极限以后,使坯料发生断裂而产生分离.分离工序又可分为落料、冲孔和剪切等,其目地是在冲压过程中使冲压件与板料沿一定地轮廓线相互分离,见表1.1.1
2.成形工序——是指坯料在冲压力作用下,变形部分地应力达到屈服极限,但未达到强度极限,使坯料产生塑性变形,成为具有一定形状、尺寸与精度冲压件地加工工序.成形工序主要有弯曲、拉深、翻边、旋压、胀形、缩口等,目地是使冲压毛坯在不被破坏地条件下发生塑性变形,并转化成所要求地冲压件形状.有关冲压工序地详细分类与特征,见表1.1. 2.
表1.分离工序分类
修边冲孔工序等.。
- 1、下载文档前请自行甄别文档内容的完整性,平台不提供额外的编辑、内容补充、找答案等附加服务。
- 2、"仅部分预览"的文档,不可在线预览部分如存在完整性等问题,可反馈申请退款(可完整预览的文档不适用该条件!)。
- 3、如文档侵犯您的权益,请联系客服反馈,我们会尽快为您处理(人工客服工作时间:9:00-18:30)。
所有底面冲头让位孔沉头程序单所标的孔位 都必须保留在图纸图档里,好方便以后检查 程序,孔位标注要标注清楚孔径大小、用的 锥钻还是平钻,冲头座让位有无加工颜色都需 加工,让位孔在斜面或毛坯的必须用刀具加 工(如刀具限制,必须铣出平台在点钻孔), 压料板冲头过孔厚度一律保留5~8mm 。
深度大于100mm的侧壁让位,在不影响模具 强度情况下,单边过切1mm加工
2D,3D加工到 位
组立
上模座结构面加工
刀块安装面螺钉孔 只需点孔
万向斜锲导板安装面正向开粗 留1mm,万向精加工到位
上下模配合导板、导 柱(套)开粗留1mm
结构面加工到位,刀块安装面螺钉孔点出,上下模配合导板、导 柱(套)开粗留1mm
此类上下模配合导板 (滑)面开粗留1mm
底面防绕倒滑面、正 面安全螺栓过孔不要 遗漏加工
侧修区域考虑间隙补面正 向加工,局部负角在万向 加工到位
2D、3D中粗留量0.6mm 组装镶块 2D、3D精加工到位
底面留量2mm
2D、3D中粗留 0.6mm
键槽、大头销 孔开粗留1mm
正面无法加工的 螺钉过孔从底面 加工
四处翻转孔大 小一致
镶块安装面螺 钉孔点出
模仁螺钉沉头孔见光铣平台,中心点孔,当深度大 于200mm的需加工深度50mm以上钻头导向孔,模 仁底面有落差的直接加工到位
侧修区域较少时,可 以火前不加工,待精 加工结束后淬火
锥形定位器安装面 开粗留量0.5mm
螺钉底孔必须按中心钻点孔 钻孔 定心钻倒角工艺 加工
如导板安装面挂台让位无加 工颜色要求,厚度大于 15mm的,需按15mm加工。
侧销孔按工艺卡加工,侧销面原则上侧向加工, 如侧向无法加工或太深,可以底面加工到位
上模修边刀块、镶块
型面3D、与压 料板配合处2D 中粗留量0.6mm
翻边、整形模工艺路线
下模 外发 龙铣底面留
座
量2mm
结构面加工到位
组立
下
下模仁 外发 龙铣底面留 量4mm
结构面到位,底面留量 2mm,键槽大头销孔开
组立 钻孔
粗留1mm
2D.3D中粗留 量0.6mm
淬火
底面精 加工
组立
2D,3D 精加 组立
调 试
模
下模镶块 外发 2D.3D留量0.6mm
刀块
结构面到位
此类刀口较尖锐、易崩刃区 域,3D型面需用小刀具局部 精加工到位
此类翻孔凹模套,需按标准 件标准件深度加工到位
凹模套加工需对照材料明细表大小、深度、 翻转销角度,加工深度以加工片体为准(考 虑料厚)最底点高出型面0.2~0.4mm
斜面上凹模套需考虑型面 加工完后,刀口厚度最少 大于4mm,凹模套压料区 域8mm以上。
结构面加工到位,模仁、刀块安装面螺钉孔点出,上下模配合导 板、导柱(套)开粗留1mm
此类上下模配合导板 (滑)面开粗留1mm
顶料器导向销孔 需加工到位
模座上的3D型面中 粗留量0.6mm
锥形定位器安装面 开粗留量0.5mm
下模仁火前加工
火前底面留量2mm,键槽、大头销孔开粗留1mm,其余结构面到位 (包括侧铣万向),2D、3D中粗留量0.6mm ,2D清角至最小,3D清 角至∅12R6.
组立
上模斜锲
结构面加工到位, 上下模配合驱动方 面开粗留量1mm
组立
2D.3D导滑面 精加工到位
组立留 量0.6mm
组立
2D,3D精加
压
外发 结构面加工到
工到位
料
压料板镶
板
块
位,2D,3D中 粗留量0.6mm
组立 研配 钻孔
组立
组立
压料板斜锲
结构面加工 到位
组立 钻孔
淬火 研配 组立
工 凹模
套型
下模斜锲
结构面加工到位上下 模配合驱动方面开粗
2D.3D中粗留 量0.6mm
淬火 组立
面加 工
留量1mm
上模座
外发
龙铣底面留 量2mm
结构面加工 到位
组立
2D,3D精
加工
组立
上 模
上模镶块 外发 刀块
2D、3D留量0.6mm,结 构面到位
组立 钻孔
淬火 组立 研配 2D、3D、导 滑面到位
冲头定心孔与刃口 一起精加工
锥形定位器安装面 精加工到位
刀块、模座、标准件加工钢印槽, 要求平行于刀块方向加工,模座 加工槽:35(总长)X20X0.2 刀 块加工槽:60 (总长) X20X0.2
上下模刀口间隙以凸模为基准, 0.8mm以下板料间隙控制在3%-5% 1.0mm板料取4%-6% (有特殊要求除 外)
外发加工,除废料刀单件加工到位,其余结构面加工到位,2D中粗 留量0.6mm, 3D精加工到位,螺钉沉头、销孔铣平台点孔
此类镶块2处拼 接面需加工到位
凹模套及漏料孔不能 加工
无法加工的冲孔2D需线割 的必须加工线割穿丝孔
螺钉孔、销子孔、起吊孔等 必须是整圆见光中心点孔
下模斜锲结构面加工
上下模配合导板(滑) 面正向开粗留1mm
压板式凹模套孔,先加工 压板槽,在加工凹模孔
此类下模斜锲、镶块必须组合一起精加工
2D、3D精加工刀具需校刀具跳动,跳动 0.03mm以内,3D清角用油漆笔画线接刀,2D、 3D因刀具限制无法加工到位区域需用油漆笔 注明清楚。
下模锥形定位器销孔 需加工到位
压料板结构面加工
除锥形定位器安装面中粗留0.5mm,其余结构面加工到位,镶块 安装位螺钉孔点孔
整形刀块带修边刀块的, 需垫高加工刃口2D
此类刀块先不组装,精加工两端2D轮廓 后,拆下两端刀块后在装上精加工此刀 块2D轮廓
图纸状态为非工作状态
需紧固螺钉后装装到模 座一起精加工2D、3D
下模座结构面加工
模仁、刀块安装面 螺钉孔只需点孔
万向斜锲导板安装面正向开粗 留1mm,万向精加工到位
上下模配合导板、导 柱(套)开粗留1mm
侧冲漏料孔直径大于40mm的加工 到位,小于40mm铣平台点孔
检测,保证最 少余量0.6mm
下模仁火后底面精加工
精加工到位
火后需检测3D余量,确保3D余量最少0.5~0.6mm,多出余量底面 加工,程序单注明,精加工底面、键槽、大头销孔到位
下模修边刀块、镶块火前加工
废料刀单件到位,刀口 按上模检测数据加工
侧修刀块不需淬火
交刀让位单件加工到位, 2D逃料让位加工到位
上模斜锲结构面加工
上下模配合导板(滑) 面正向开粗留1mm
无双向定位基准或安装2块以上 刀块,安装面上的刀块螺钉孔 只需点出
除上下模配合导板(滑)面开粗留1mm,其余结构面加工到位
上模斜锲、刀块组装加工
一起精加工到位
2D刃口与导板(滑)面一起精加工到位
除上下模配合导板(滑)面开粗留1mm,其余结构面加工到位
下模组装精加工
2D轮廓、3D型面精加工到位,刀口检测、标准,公差: ±0.02mm,凹 模套孔、定位孔、CH孔、锥形定位器安装面及销孔、上下模配合导板、 基准孔、等结构面精加工到位
无法加工到位的2D、孔, 需留线割基准,需单件加 工的侧冲、侧修2D留基准
上模、刀块组装精加工
2D轮廓、3D型面精加工到位, 2D轮廓、3D型面精加工到位,刀 口检测、标准,公差: ±0.02mm,锥形定位器安装面、冲头定心 孔、上下模配合导板、基准孔、等结构面精加工到位
需检测废料刀数据,记录
无定位基准镶块2D、3D开粗留量0.6mm 淬火 研配 组装精加工
上下模配合导板(滑)面、 导柱(套)孔与2D、3D一 起精加工到位
外发结构面加工到位,2D中粗留量0.6mm, 3D精加工到位,螺钉沉 头、销孔铣平台点孔
标准斜锲修边刀 块2D、3D单件 加工到位
弹顶销孔淬火 前攻丝
无2个方向定位基准 镶块2D、3D不加工
浮动刀安装面及侧面 导柱孔单件加工到位
浮动刀块结构面加 工到位,2D、3D留 量0.6mm
整形刀块带修边刀块的, 修边刀块刃口2D精加工 留0.3mm
侧销聚胺脂定位销孔先加工沉 头孔,后加工销子孔,销子孔 需点、钻、铰加工
此类顶杆安装销孔让位需 精加工到位,公差: 0.1~0.15mm
压料板侧销深度让位面(黄色),按图纸加 深1~2mm加工
不影响耐磨板安装有效距离及模具强度情况 下,内导板安装面R角放大加工,减少清角时 间。
四处翻转孔大 小一致
侧冲让位正向能加工到位 的必须正向加工
锥形定位器安装面 中粗留量0.5mm
正面结构面只有基准孔、起吊 孔等加工内容较少的待型面一 起加工,减少装夹时间。
压料板镶块加工
镶块底面冲孔让位(正、 万向)加工到位
结构面加工到位,2D、3D中粗留量0.6mm,螺钉沉头、销孔铣平台 点孔
压料板2D、3D粗精加工