0711维码器说明书
维码门禁一体机说明书模板

二维码一体机说明书1注意事项1)设备供电为弱电,请勿接25V以上的直流电或强电。
2)安装接线时,应先将设备断电后,再接线,不可带电接线。
3)电源延长线,使用1.0或以上多股铜丝细线。
电源延长线不能超过30米,若超过30米,应适当调高电压及加粗电源线。
设备接线处做好绝缘保护,不需要使用到的线,逐根用电工胶布包好,不能多根包在一起。
4)若使用WIFI组网,WiFiAP距离设备尽可能保证无遮挡直线5M以内,若超过10米将无法保证通讯质量;若使用4G移动网络,请用手机测试对应运营商信号,以观看直播无卡顿、延时为准;若使用有线以太网,建议使用超五类网线以上、50米内的网线。
5)设备供电为6-25V,由于二维码一体机功率比普通刷卡读卡器高,建议设备取电从开关电源处取。
推荐使用符合3C安全规范的电源。
6)继电器电流最大负载为1A,如控制电插锁、磁力锁、阴极锁、双锁等功率较大的设备,建议采用门禁专用电源,使用门禁专用电源的继电器来控制电锁;若不能用门禁专用电源,则建议增加中转继电器(5A或以上的继电器)。
7)设备安装尽量避免强光直射或爆晒,会影响扫码效果及加速设备老化;如要安装在室外,建议在设备上加一个遮阳罩并保持面板干净,可以避免设备反射阳光导致难以扫码并避免设备暴晒发烫,如有保护膜需先撕去保护膜。
(设备的工作温度:-20°C~60°C)8)本设备防水等级为IPX5,但室外使用时,建议在设备外面加一个防水罩,避免雨水滴落到设备摄像头上影响扫码。
2常见问题1)配置不生效a)配置工具的设备密码不正确,设备默认出厂密码都是666666;2)设备与后台服务连接不成功a)检查设备网络是否能与后台服务通讯。
通常安全性较高的局域网,需要联系网管授权设备联网;b)检查后台服务心跳接口是否按照要求实现;c)可使用配置工具,让设备恢复出厂,设备自动连接我司默认后台服务,以检测网络是否可正常连外网;3)刷卡或扫码提示连接超时问题a)检查设备网络是否正常,可用同一局域网内的电脑连续PING设备IP,如果出现大延时或超时,请检查网线或无线信号;b)检查服务器到设备的网络延时,可用同一局域网内的电脑使用Postman软件测试接口性能;c)使用配置工具网络配置页面,适当加大连接超时时间;4)4G无法拨号成功a)检查4G是否插入卡槽;b)检查卡流量是否超出套餐,流量是否不允许跨省,物联网卡则咨询当地运营商政策,信号是否支持4G。
§7 激光打码机软件使用手册 - 宁波唯尔激光科技有限公司

飞行激光打码机软件使用手册1电路控制板卡接线结构电路控制主板卡电路控制DA 板光电开关 激光驱动信号 手编器,USB ,网络接口 编码器接口15V 电源接口DA 板接口2激光打码机软件介绍及使用说明F1打开控制面板主菜单F2打开文件管理保存标刻的参数和内容1时间设定设定系统时间和日期2字符属性字高:改变字体的大小字间距:改变字间距行间距:改变文本行与行之间的距离X坐标,Y坐标:每次打码中心点的位置镜像:使标刻对象镜像旋转:将对象围着其中心点进行旋转英文字体,汉字字体:字体的选择3加工参数(1)加工速度(mm/s):振镜标刻的速度开光延迟(us):每次标刻初始处停留时间参数设置过大时:每次标刻的初始处会出现烧伤的斑点或者标刻过深参数设置太小时:每次标刻的初始处会出现缺损关光延迟(us):每次标刻末尾相连处停留时间参数设置过大时:每次标刻的末尾处会出现烧伤的斑点或者标刻过深参数设置太小时:每次标刻的末尾处会出现缺损结束延迟(us):每次标刻在末尾结合处停留时间拐角延迟(us):每次标刻在拐弯处停留时间4加工参数(2)跳转速度(mm/s):标刻过程中,激光器不出光时振镜移动的(空走)速度跳转延迟(us):标刻过程中,从上一次标刻结束到下一次标刻开始所需停留的时间末点补偿(mm):每次标刻末尾处的补偿距离加速距离(mm):设定每次标刻前振镜的加速距离打点时间(us):每次标刻一个点所用的时间5 PWM,功率标刻频率(KHZ):激光器输出激光的频率标刻占空比(%):激光器输出激光的功率占其满功率的百分比预电离频率(KHZ):激光器处于待出光状态下的PWM输出频率预电离宽度(us):激光器处于待出光状态下的PWM输出宽度激光功率(%):IPG激光机才起作用6 Q驱参数输出脉冲反转:Q开关驱动电源才起作用首脉抑制时间(us):Q开关驱动电源才起作用关电开关触发延时(ms):触发激光器输出激光所需要的时间,最长延迟10秒7模式设置激光器类型:选择激光器的类型,包括三种激光器类型:YAG; IPG; CO2操作模式:选择标刻模式,可选择两种模式:正常模式;跳号模式飞动模式:选择飞动模式,可选择两种模式:编码器;指定速度。
电磁阀监视控制器LSB-7系列使用说明书

Instruction and OperatingManualValve Monitoring ControllerLSB-7 Series< LSB-7 > < LSB-7S >Power-Genex Ltd.C o n t e n t s1. Safety Instructions and Precautions 22. Overview of Structure 63. Specifications 74. Description on Nameplate 75. Part Numbering System (Order Code) 96. Specifications of Switchesand Proximity Sensors6.1. Mechanical Switches6.1.1. SPDT, SZM-V16-2FA-61(made by STARION)6.1.2. DPDT, DZ-10G (made by OMRON) 6.2. Proximity Sensors6.2.1. NJ2-V3-N(made by Pepperl & Fuchs)6.2.2. NJ2-12GM-N(made by Pepperl & Fuchs) 9 107. Specifications of Position Transmitter 108. Operating Principle of Solenoid Valve 118.1 Manual Button on Solenoid Valve9. Installation 1210. Electrical Connections 1311. Setting of Cams and Switches12. Dimensions 16 17Safety Instructions 1These safety instructions are intended to prevent hazardous situations and/or equipment damage. These instructions indicate the level of potential hazard with the labels of “Caution,” “Warning” or “Danger.” They are all important notes for safety and must be followed in addition to International Standards (IEC) Note 1) and other safety regulations.Note 1) IEC 60079-0: 2007, IEC 60079-1: 2007Caution Caution indicates a hazard with a low level of risk which, if not avoided, could resultin minor or moderate injury.Warning Warning indicates a hazard with a medium level of risk which, if not avoided, couldresult in death or serious injury.Danger Danger indicates a hazard with a high level of risk which, if not avoided, will resultin death or serious injury.Warning1. The compatibility of the product is the responsibility of the person who designs the equipment ordecides its specifications.Since the product specified here is used under various operating conditions, its compatibility withspecific equipment must be decided by the person who designs the equipment or decides itsspecifications based on necessary analysis and test results. The expected performance and safetyassurance of the equipment will be the responsibility of the person who has determined itscompatibility with the product. This person should also continuously review all specifications of the product referring to its latest catalogue information, with a view to giving due consideration to any possibility of equipment failure when configuring the equipment.2. Only personnel with appropriate training should operate machinery and equipment. The productspecified here may become unsafe if handled incorrectly.The assembly, operation and maintenance of machines or equipment including our products must be performed by an operator who is appropriately trained and experienced.3. Do not service or attempt to remove product and machinery/equipment until safety is confirmed.1. The inspection and maintenance of machinery/equipment should only be performed after measuresto prevent falling or runaway of the driven objects have been confirmed.2. When the product is to be removed, confirm that the safety measures as mentioned above areimplemented and the power from any appropriate source is cut, and read and understand the specific product precautions of all relevant products carefully.3. Before machinery/equipment is restarted, take measures to prevent unexpected operation andmalfunction.4. Contact POWER-GENEX beforehand and take special consideration of safety measures if theproduct is to be used in any of the following conditions.1. Conditions and environments outside of the given specifications, or use outdoors or in a placeexposed to direct sunlight.2. Installation on equipment in conjunction with atomic energy, railways, air navigation, space, shipping,vehicles, military, medical treatment, combustion and recreation, or equipment in contact with food and beverages, emergency stop circuits, clutch and brake circuits in press applications, safety equipment or other applications unsuitable for the standard specifications described in the product catalogue.3. An application which could have negative effects on people, property, or animals requiring specialsafety analysis.4. Use in an interlock circuit, which requires the provision of double interlock for possible failure byusing a mechanical protective function, and periodical checks to confirm proper operation.5. Do not open when an explosive gas and dust atmosphere may be present6. Do not touch the visual indicator in electrostatic hazardous areas.Safety Instructions 2Caution1. The product is provided for use in manufacturing industries.The product herein described is basically provided for peaceful use in manufacturing industries. Ifconsidering using the product in other industries consult POWER-GENEX beforehand and exchange specifications or a contract if necessary. If anything is unclear, contact your nearest sales branch.Limited warranty and Disclaimer/Compliance RequirementsThe product used is subject to the following “Limited warranty and Disclaimer” and “Compliance Requirements”. Read and accept them before using the product.Limited warranty and Disclaimer1. The warranty period of the product is 1 year in service or 1.5 years after the product is delivered.Note 2)Also, the product may have specified durability, running distance or replacement parts. Please consult your nearest sales branch.2. For any failure or damage reported within the warranty period which is clearly our responsibility, areplacement product or necessary parts will be provided. This limited warranty applies only to our product independently, and not to any other damage incurred due to the failure of the product.3. Prior to using POWER-GENEX products, please read and understand the warranty terms anddisclaimers noted in the specified catalogue for the particular products.Compliance Requirements1. The use of POWER-GENEX products with production equipment for the manufacture of weapons ofmass destruction (WMD) or any other weapon is strictly prohibited.2. The exports of POWER-GENEX products or technology from one country to another are governedby the relevant security laws and regulations of the countries involved in the transaction. Prior to the shipment of a POWER-GENEX product to another country, assure that all local rules governing that export are known and followed.Precautions 1Be sure to read before handling.OperationWarning1. Do not operate the valve monitoring controller outside the specified range as this may cause problems. (Refer to the specifications.)2. Design the system to include a safety circuit to avoid the risk of danger should the valve monitoring controller suffer failure.3. Be sure that exterior lead-in wiring to the terminal box is based on the guidelines for explosion-protection of manufactory electric equipment when being used as a flame proof, explosion proof construction.4. Do not remove terminal cover in a hazardous location while the power is on.5. Covers for the terminal and body should be in place while operating.6. When using as an intrinsically safe explosion-proof product, do not wire in a hazardous location while the power is on.Caution1. Do not touch the actuator or valve's oscillating section when supply pressure has been added, as this is dangerous.2. Make sure fingers do not get caught when mounting and aligning the cam.Cut off the pressure supply and always release the compressed air inside the valve monitoring controller and actuator before performing this work.3. Always use with the body cover unit mounted.Moreover, the valve monitoring controller may not meet degrees of protection IP66 depending on the body cover mounting conditions. In order to meet degrees of protection IP66, tighten threads using the proper tightening torques (2.8 to 3.0 N·m).4. Always flush the pipe's inside before piping to ensure foreign objects such as machining chips do not enter the positioner.5. The actuator opening may become unstable when using the booster relay.6. Always use a ground connection to prevent noise from the input current and to prevent damage because of static electricity.For usersCaution1. Assemble, operate and maintain the valve monitoring controller after reading the operation manual thoroughly and understanding the content.Precautions 2Be sure to read before handling.HandlingCaution1. Avoid excessive vibration or impact to the valve monitoring controller body and any excessive force to the armature, as these actions may cause damage to the product. Handle carefully while transporting and operating.2. If being used in a place where vibration occurs, using a binding band is recommended to prevent broken wires because of the vibration.3. When exposed to possible moisture invasion, please take the necessary measures. For example, if the valve monitoring controller is left onsite for long periods, a plug should be put in the piping port and a body cover unit fitted to avoid water penetration.Take measures to avoid dew condensation inside the valve monitoring controller if exposed to high temperature and humidity. Take enough measures against condensation especially when packing for export.4. Keep magnetic field off the valve monitoring controller, as this affects its characteristics.Air SupplyCaution1. Use only dehumidified and dust extracted clean compressed air as the air supply.2. Use only dehumidified and dust extracted clean compressed clean air as the valve monitoring controller contains extra fine spool and nozzle.Do not use a lubricator.3. Do not use compressed air containing chemicals, organic solvents, salinity or corrosive gases, as this may cause malfunction.4. When operating below the freezing point, protect the positioner from freezing.Operating EnvironmentCaution1. Do not operate in locations with an atmosphere of corrosive gases, chemicals, sea water, or where these substances will adhere to the regulator.2. Do not operate out of the indicated operation temperature range as this may cause damage to electronic parts and seal materials to deteriorate.3. Do not operate in locations where excessive vibration or impact occurs.4. If the body cover is being installed in a place where the body cover is exposed to direct sunlight, the use of a standard body cover is recommended.2. Overview of Structure3. SpecificationsLSB - 7 LSB – 7S Explosion proof / protection class Ex d IIB+H2 T6Solenoid ValveOperating Air PressureSingle Acting 1.5 ~ 9.9 kgf/㎠Double Acting 1.0 ~ 9.9 kgf/㎠ Max. Supply Air Pressure 15 kgf/㎠Supply Voltage 24VDC / 220VAC / 110VACCurrent AC : 4.9VA(60Hz) / DC : 2.5W Auto/Manual Mode Button-push typeResponse Time Below 25msCoil Insulation Class F – Class (Made in Germany / Nass) Max. Operating Frequency 5 cycle / secondAmbient Temperature -30℃ ~ +75 ℃Electrical connections G 3/4, G 1/2, G 1, NPT 3/4, NPT 1/2, NPT 1, M20x1.5 Pneumatic connections Rc 1/4 or NPT 1/4Body material / paintingAluminum diecast /powder coatingSUS 316 Weight 3 kg 5.8 kg4. Description on Nameplateᆢ MODEL NUMBERModel number and options are described.ᆢ Switch Type : Mechanical switches / Proximity sensors typeᆢ Voltage Ratings : switche / sensor voltage ratingsᆢ Serial No : A serial number and a manufacturing date for tracking are described. ᆢ Solenoid Voltage Rating : Solenoid voltage(220VAC, 110VAC, 24VDC)ᆢ Certificate NoCE XXXX / INERIS ATEX XXXX / IECEx KTL 11.0021X / 11-KB2BO-XXXXᆢ Code : Ex d IIC T6 (Tamb. -30 to +75℃)ᆢ WARNING1. Potential electrostatic charging hazard2. Do not open when an explosive gas and dust atmosphere may be present3. See instruction5. Part Numbering System (order code)LSB — 7x x x—x—x x— x x x —x x Body M aterial Aluminum diecast .SUS316sSwitch Type Mechanical switches 0Proximity switches 1Switch / Sensor None NMechanical switches 2 x SPDT 0 4 x SPDT 2 2 x DPDT 4Proximity Sensors 2 x NJ2-V3-N / P&F 6 4 x NJ2-V3-N / P&F 7 2 x NJ2-12GK-N / P&F8 4 x NJ2-12GK-N / P&F9PositionTransmitterNone N4 ~ 20mA output signal OCoil Type None NSingle coil type SDouble coil type DCoil Power None N220VAC A110VAC B24VDC C Indicator Option 2 – way (standard) N3 – way L-port L3 – way T-port T Electrical 2 x PF 1/2 AConnections 2 x NPT 1/2 B2 x M20 C2 x PF 3/4 E2 x NPT 3/4 F2 x PF 1 H2 x NPT 1 IPneumatic Rc1/4 R Connections NPT1/4 N Feedback Shaft Fork lever F NAMUR shaft (direct mounting) N Mounting Bracket None N Multi-size bracket for VDI/VDE3845 (IEC60534-6-2) R6. Specifications of Switches and Proximity Sensors 6.1 Mechanical Switches6.1.1 SPDT, SZM-V16-2FA-61 (made by STARION)< SPDT Mechanical Switch >TypeNon-inductive load Inductive loadResistive Lamp Inductive Motor Rating250VAC8VDC30VDC125VDC250VDC16A16A10A0.6A0.3A2A4A4A0.1A0.05A10A10A10A0.6A0.3A3A6A4A0.1A0.05A<Wiring>OperatingTemperature-20℃ ~ +105℃6.1.2 DPDT, DZ-10G (made by OMRON)< DPDT Mechanical Switch >TypeNon-inductive load Inductive loadResistive Lamp Inductive MotorNO NC NO NC NO NC NO NC Rating125VAC250VAC8VDC14VDC30VDC125VDC250VDC10A10A10A10A10A0.5A0.25A2A1.5A3A3A3A0.5A0.25A1A0.7A1.5A1.5A1.5A0.5A0.25A6A4A6A6A 4A0.05A0.03A3A2A5A5A3A0.05A0.03A1.5A1A2.5A2.5A1.5A0.05A0.03A<Wiring> OperatingTemperature-20℃ ~ +80℃6.2 Proximity Sensors6.2.1 NJ2-V3-N (made by Pepperl & Fuchs)< Proximity Sensor >General SpecifiactionsSwitching element functionRated operating distanceInstallationOutput polarityAssured operating distanceNAMUR NC2mmembeddableNAMUR0 ~ 1.62 mm Nomial RatingsNominal voltageSwitching frequencyHysteresisCurrent consumptionMesasuring plate not detectedMeasuring plate detected8.2 VDC0 ~ 1000 Hz0.01 ~ 0.1 mm> 3mA< 1mA<Wiring>Mechanical SpecificationsConnection typeCore cross-sectionHousing materialSensing faceProtection degreeCable PCV, 130 mm0.14 mmPBTPBTIP67Operating Temperature-25℃ ~ +100℃6.2.2 NJ2-12GK-N (made by Pepperl & Fuchs)< Proximity Sensor >General SpecificationsSwitching element function Rated operating distance InstallationOutput polarityAssured operating distanceNAMUR NC 4mmNot embeddable NAMUR0 ~ 3.24 mm Nominal Ratings Nominal voltage Switching frequency HysteresisCurrent consumptionMesasuring plate not detected Measuring plate detected8.2 VDC0 ~ 1500 Hz 3%> 3mA < 1mA<Wiring>Mechanical Specifications Connection type Core cross-section Housing material Sensing faceProtection degree Cable PCV, 2 m 0.34 mmPBT PBTIP66Operating Temperature-25℃ ~ +100℃7. Specifications of Position TransmitterGeneral Specifications Current Output Signal Power Supply Range Span Adjustable Angle4 ~ 20mA , 2-wire12 ~ 30VDC (24VDC recommendable) 0 ~ 120°Nominal Ratings Linearity Repeatability HysteresisWithin ± 1.0% F.S. Within ± 0.25% F.S. Within ± 1.0% F.S. Operating Temperature-20℃ ~ +70℃<with mA calibrator><with mA tester>8. Operating Principle of Solenoid Valve1) If the rated voltage/current is supplied to the solenoid valve, the magnetic force around coils is generated.2) According to the magnetic force, the armature core (1) reaches the vent body (2) and blocks the vent air line.3) The supply air (P) pushes the spool through the orifice body (3) and vents out from A. 4) If the solenoid valve is powered off, the magnetic force around coils vanishes.5) Air from the orifice body (3) is blocked by the spring between the armature seat (4) and the armature core.6) The supply air pushes the spool (5) from the bottom of the solenoid valve through the air line located at the center of the spool, and the remaining air inside of the orifice body (3) vents out from the vent body (2).8.1 Manual Button on Solenoid ValveWhile air is supplied, the solenoid valve can be operated manually with a button. If the Auto / Manual button is pushed, the output port A becomes open.Note that the Auto/Manual button is not available while a power is supplied<Power On / Action><Power Off / Normal>9. InstallationLH10. Electrical Connections2 x DPDT, single coil①Be sure to supply the rated voltage and current stated on this manual. Otherwise, it may cause a serious damage or malfunctions.② Check polarity of + and – exactly and connect wires.③When it is necessary to open the positioner cover at a humid place, more attention is required. It may cause a serious damage or malfunctions.IECEx explosion-proof constructionLSB-7 becomes explosion proof, as certified by IECEx, according to the model selected. The explosion-proof grade has the following approval : Ex d IIB+H2 T6. Take extra care when handling the LSB-7 as explosion-proof equipment To use as Ex d IIB+H2 T6 A) Pressure-proof packing.As shown below in the chart, use "Cable gland" B) Metal Piping.Attach the sealant fitting bracket near the cable port.(For details, refer to "The guideline on electric equipment explosion proof" published by the• 2 x P&F NJ2-V3-N, single coil • 2 x P&F NJ2-12GK-N, single coil- Position Transmitter Option<2 x SPDT single coil + Position transmitter>a) With mA loop calibratorb) With multi-meterc) Setting10.1 EarthingThe Postioner must be connected to a good quality earth. The units are provided with internal and① It is necessary to set Zero and Span of position transmitter manually. ② The power supply of 12 – 30VDC should be supplied.- Install the LSB-7 properly before setting the position transmitter. - Check the proper position of the RA/DA switch before setting. 1. Turn the Zero screw until the output signal reaches 4mA. 2. Turn the Span screw until the output signal reaches 20mA.3. Repeat the above procedure until the output signals reach 4mA and 20mA.4. Operate the valve and check if the output signals are transmitted properly.11. Setting of Cams and Switchesa) Push up the red cam if it is necessary to set the position of the red cam.b) Turn the red cam until it touches the limit switch. And put down and fix it with a wrench bolt.c) Do the same procedure for setting of the blue cam. But push it down to move.12. DimensionsPower-Genex Ltd. 44B9L, 434-9, Nonhyun-dong, Namdong-gu, Incheon 405-849 Korea Tel : +82-32-812-6644Fax : +82-32-812-6645Website : E-mail : ********************Subject to change without prior notice。
WCS Installation(编码器使用说明)

读码器本体红色报警灯常亮; 错误代码“Err 1”; 位置值异常示灯; 反馈错误代码“Err 1”; 位置值异常,不正确。
1000
5000 编码递升方向
18
WCS Position Encoding System
WCS
绝对位置定位系统 线性绝对值编码器
2
WCS 简介
WCS线性绝对值编码系统
读码器采用短距离红外对射方式读取编码尺,无机械接触(无磨损),特别 适合重载移动物体的高精度定位。
32
固定圆弧段编码尺
2)然后取一段和圆弧部分一样长的稳定导轨,把它装入支架;
33
固定圆弧段编码尺
2)然后取一段和圆弧部分一样长的稳定导轨,把它装入支架,并剪掉多余部分;
34
精度可达0.8mm 最高速度可达 12.5 m/s; 轨道长度314.5米 单轨道上多个移动装置的精确定位 直形、圆弧、分岔轨道
3
工作原理
线性绝对值编码器
读码器本体不包含位置数据
位置数据经过特殊编码和 穿孔工艺,制作在编码尺 上
4
工作原理
线性绝对值编码器
读码器本体不包含位置信息。 读码器采用红外对射方式读取编码尺,从而获得绝对位置信息。 位置数据经过特殊编码和穿孔工艺,制作在塑压和不锈钢编码尺上。 总长314 m的编码尺上每处位置数据都是唯一的。
5
系列
WCS系统有两大系列:
WCS3B系统 读码器的底部槽宽为31 mm,槽高为55 mm。
4)拧紧2个螺栓(M6 X 12),两片金属薄片加紧编码尺,只要正确安装,加紧力就 足够防止编码尺滑落。 备注:除了夹紧固定,还可以直接用螺丝钉把编码尺固定在基座上,螺丝钉连接 处就产生了一个位于编码尺和基座之间参考点。
WERMA信号技术产品说明书

CONTENTSIntroduction P age 4 - 5 Bene ts / ApplicationsPage 6 - 7The system P age 8 - 13Experience Smart MONITORP age 14 - 15EU R O P E ‘S L E A D E R I N S I G N AL L I N GSmart MONITOR is the smart MDC alternative for industrial companies looking for a way to quickly and easily gather reliable data to optimise their manufacturing processes. Smart MONITOR provides all of the relevant data for machines, systems and manual workstations easily at the touch of a button. Unlike conventional,complex MDC systems, Smart MONITOR is a simple, wireless-based retrofit solution for signalling and analysing your entire production facility - at a glance.Christian Höhler, Research & Development DirectorEVERYTHING UNDER CONTROL WITH Smart MONITORWith signal devices, the control station module or a messageon your smartphone you can shorten your response times and optimiseyour manufacturing process, with the guarantee that you will nevermiss a critical situation.Everything is documented and the reports also show you how topermanently improve your processes and productivity.Smart MONITORWith Smart MONITOR we help to make processes faster, leaner, better and more efficient - simply at the push of a button. The simple, wireless-based retrofit solution for signalling and analysing your entire production area ensures further growth and that you are always a step ahead of your competitors.THE SYSTEMSmart MONITOR from WERMA consists of a wireless transmitter, a wireless receiver and the software. The robust and proven wireless network for the production environment intelligently searches for the best connection and thereby ensures the simplest integration into your production process. The included software already has integrated analysis and reporting tools.TRANSMITTERWIRELESS DATA MONITORING• Can be integrated into the signal tower as an additional element • M onitors the status and counts the output of up to 50 machines or workstations• Data transferred wirelessly to the receiver • Initiates processes, starts and stops machinesRECEIVERSECURE DATA COLLECTION• R eceives all the data sent by the transmitters in the network• T ransfers and saves the data to a Microsoft SQL databaseSOFTWARECENTRAL CONTROL STATION• C ontrol station offers an overview of all machines, equipment and workstations • Retrospective analysis of data • Process optimisation• React quickly to production disruptions • Produce reportsINTUITIVE AND CLEAR –THE WIN SOFTWAREThe software supplied with the system is easy to install and leads the userthrough a series of steps to establish an individual network. It displays thestatus condition of signal lights installed in the system, enables the user toanalyse runtimes, identify causes of disruption in operations and thereforeimprove efficiency.KEEP UP TO DATE WITH CHANGESMESSAGING SERVICEReact quickly regardless of your current location. If the status of a machine or workstationchanges an Email can be automatically sent to a PC or Smartphone of the personresponsible. You can select to whom and after which time interval of the statuschange the Email is to be sent.OBTAIN TRANSPARENCYRUNTIME MODULEThe Runtime Module enables you to check the operation and down-times of your machines or workstations. This allows you to compareDOCUMENT PROBLEMSERROR ANALYSISeliminated.SIMPLY CLEVER REFERENCESA large number of customers already rely on WERMA technology - and thereby make their production safer, better and more e cient. You can nd references and customer applications at:HOTLINE:Smart MONITORP hone + 49 74 24 95 57- 153Fax+ 49 74 24 95 57- 44**********************EXPERIENCEYOUR POSSIBILITIES FOR YOURSELFLive demonstration. Lean Factory.Visit one of our numerous roadshows throughout Germany. Register at:EXPERIMENT WITH THE PRODUCT INFind out more by ordering our test box – without any obligation - at:***********************This offer may not be available in all markets/smartmonitorYOUR FACILITY TEST BOX*WERMA Signaltechnik GmbH + Co. KG Dürbheimer Str. 15D - 78604 Rietheim - W eilheim Phone + 49 74 24 95 57- 0Fax + 49 74 24 95 57- 44**************WERMA Signaltechnik Niederlassung Neuhausen am Rhf. Rheingoldstrasse 508212 Neuhausen am Rheinfall SwitzerlandPhone + 41 52 674 00 60Fax + 41 52 674 00 66www.werma.ch*************WERMA SARL56, Rue Colière69780 MionsFrancePhone + 33 4 72 22 37 37Fax + 33 4 72 22 37 64www.werma.fr*************WERMA BENELUX Poortakkerstraat 41C9051 Sint-Denijs-WestremBelgiumPhone + 32 9 220 31 11********************* WERMA (UK) Ltd.11 Regent Park37 Booth DrivePark Farm Industrial Estate Wellingborough NN8 6GRGreat BritainPhone + 44 15 36 48 69 30Fax + 44 15 36 51 48 10****************.ukWERMA USA Inc.6731 Collamer RoadEast Syracuse, NY 13057 USA Phone + 1 315 414 0200Fax + 1 315 414 0201*****************WERMA (Shanghai) Co., Ltd.No. 8, High Technology Zone, No. 503, Meinengda Road, Songjiang, Shanghai, P. R. C201613 ChinaPhone + 86 21 57 74 - 00 22Fax + 86 21 57 74 - 66 01**************.cnPart Numbers Smart MONITORWIN slaveOrder no. 860 640 02WIN transmitterOrder no. 860 640 05WIN slave performanceOrder no. 860 640 12WIN transmitter performanceOrder no. 860 640 15WIN slave controlOrder no. 860 640 22WIN transmitter controlOrder no. 860 640 25WIN ethernet master Order no. 860 000 06WIN ethernet receiver Order no. 860 000 07COUNTING MODULEThis hardware monitors up to six different statuses and counts a quantity pulse. This information is transmitted to the receiver.CONTROLLING A SIGNAL TOWERIn combination with the software, this hardware allows the actuation of a signal tower or an external application (start machine, stop machine etc.).STATUS MONITORINGThis hardware monitors up to eight different statuses and transmits them to the receiver.1. WIRELESS NETWORKINGT R A N S M I T T E RR E C E I V E RTerminal elementOrder no. 640 800 00Terminal element + Base with integrated tubeOrder no. 640 810 00 +975 840 10Terminal element + Bracket for base mounting Order no.640 800 00 + 960 000 02BuzzerOrder no. 645 800 752 tone sirenOrder no. 645 870 75LED Permanent light red Order no. 644 100 75LED Permanent light green Order no. 644 200 75LED Permanent light yellow Order no. 644 300 75LED Permanent light clear Order no. 644 400 75LED Permanent light blue Order no. 644 500 75Twin LIGHT redOrder no. 647 110 75Twin LIGHT yellowOrder no. 647 310 75Twin LIGHT greenOrder no. 647 210 75Twin LIGHT clearOrder no. 647 430 75Twin LIGHT blueOrder no. 647 510 75LED Permanent lightOrder no. 649 240 02LED Permanent lightOrder no. 649 240 04Twin LIGHT Order no. 649 000 01LED Permanent lightOrder no. 649 240 05LED Permanent lightOrder no. 649 240 06Twin LIGHT Order no. 649 000 022. SIGNAL TOWERPRE-ASSEMBLED SIGNAL TOWER SIGNAL ELEMENTS (UP TO A MAXIMUM OF 4)Base mounting Base mountingTube mounting Tube mountingBracket mounting06/17 ∙ 990.223.02 ∙ E。
维纳斯立体观察系统操作说明和维修手册说明书
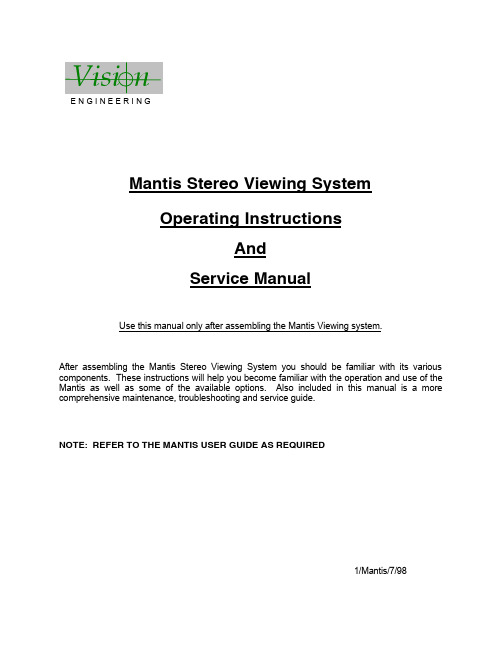
E N G I N E E R I N GMantis Stereo Viewing SystemOperating InstructionsAndService ManualUse this manual only after assembling the Mantis Viewing system.After assembling the Mantis Stereo Viewing System you should be familiar with its various components. These instructions will help you become familiar with the operation and use of the Mantis as well as some of the available options. Also included in this manual is a more comprehensive maintenance, troubleshooting and service guide.NOTE: REFER TO THE MANTIS USER GUIDE AS REQUIRED1/Mantis/7/98CONTENTS Page1) System Diagrams (2)M antis Universal Boom Mount (3)M antis FX Bench Mount (4)1) The Basic Systems (5)1) Objective Specifications (7)1) Using the Mantis (9)T urning the Power “ON” (10)F ocusing (10)A djusting the Lighting .................................... (10)C hanging the Magnification (11)A djusting the Eye Spacing (11)5) Options (12)L ens Protective Covers (13)6)Maintenance (14)Lamp Replacement (15)Lens Cleaning (15)Moisture Control (15)Optical Path Alignment (15)Fan (15)7)Troubleshooting (16)Mantis has No Power (17)Optical View ............... (17)8)Service (18)C leaning the Mirrors (19)F an Replacement (20)R epairing Eye Spacing Adjustment (21)M irror Removal (22)9)Warranty (23)10) Information (25)SYSTEM DIAGRAMSSYSTEM DIAGRAMMANTIS UNIVERSAL BOOM MOUNTE N G I N E E R I N GDescription User Guide Des.Part No.1. Yaw Bolt Cover Cover Plate 187-A-00792. Yaw Bolt Assembly Yaw Spigot YB-A-0013. Anti-glare Shield Anti-glare Shield 187-B-00904. Adj. Friction Handle Height Friction Clamp HAN-05675. Table Mount Base Universal Mount 187-C-02586. C Clamp Assembly G ClampHDW-10927. Power Switch SWI-01228. Switch Cover 187-A-01119. Fan Cover Assembly 187-A-021110. Desiccant(10 pack)Desiccant CartridgeM00611. Grommet HDW-103012. Turret Assembly 187-A-020813. Filter Tray - Left 187-C-007614. Filter Tray - Right 187-C-007515. Lamp Diffuser 187-A-011516. Lamp Diffuser(Blue)187-A-0115A 17. Lamp, 12volt, 20wattLAM-13001241314151617101139128756MANTIS FX BENCH STANDVisi nE N G I N E E R I N GDescription User Guide Des.Part No.1. Yaw Bolt Cover Cover Plate 187-A-00792. Yaw Bolt Assembly Yaw Spigot YB-A-0013. Anti-glare Shield Anti-glare Shield187-B-00904. Focusing Thumbwheel 5. Focusing Platform 187-D-292*6. Surface Lighting Switch7. Substage Lighting Switch8. FX Base187-C-03109. Fan Cover Assembly 187-A-021110. Desiccant(10 pack)Desiccant CartridgeM00611. Grommet HDW-103012. Turret Assembly 187-A-020813. Filter Tray - Left 187-C-007614. Filter Tray - Right 187-C-007515. Lamp Diffuser 187-A-011516. Lamp Diffuser(Blue)187-A-0115A 17. Lamp, 12volt, 20wattLAM-1300*Requires Sub-Assembly187-B-3071231011121314151617956784SYSTEM DIAGRAMThe Basic Systems2) The Basic SystemsThe Mantis Stereo Viewing System is a powerful optical inspection system. The patented optical technology provides a bright, crystal clear overhead image in a fatigue free viewing environment. Long working distance offers ample room for rework and part rotation.Mantis systems are available in two versions. One version is the boom mount (refer to page 3 of this manual) which can be mounted on almost any table surface. This is good for general inspection, viewing and rework, especially in a production environment. The other version is the Mantis FX (refer to page 4 of this manual). This version has a portable stand that resembles a traditional microscope stand. This version is better suited to off-line inspection.Each Mantis system can be equipped with any two of the objective lenses listed below. It is common to use a lower magnification lens (such as 2X or 4X) for general inspection and a higher magnification lens (such as 8X or 10X) for closer inspection of possible defects.Mantis - Boom MountDescription Vision Engineering Inc. Part No.1) Mantis viewing head M0012) Mantis Boom Mount M003Mantis FX - Bench StandDescription Vision Engineering Inc. Part No.1) Mantis viewing head M0012) FX Bench Stand M002Objectives - For use with either systemDescription Vision Engineering Inc. Part No.1) 2X Magnification Lens M2222) 4X Magnification Lens M4443) 6X Magnification Lens M0044) 8X Magnification Lens M0085) 10X Magnification Lens M0096) 6X SLWD Magnification Lens M013The 6X SLWD magnification lens has a much longer working distance than the standard 6X magnification lens. It is specifically designed for rework applications.Objective Specifications 3)Objective SpecificationsThe Mantis objectives provide different levels of magnification ranging from 2X to 10X. As magnification changes, working distance (the distance between the objective lens and the subject when properly focused), field of view (the area of subject that is visible in the viewing screen at any one time) and depth of field (the maximum subject height variation that will remain in focus) also change. The chart below shows the characteristics of each lens.Lens Working Distance Field of View Depth of Field2X171 mm ~ 6.7 in.56 mm ~ 2.2 in. 25 mm ~ 1.0 in.4X 86 mm ~ 3.4 in.28 mm ~ 1.1 in. 11 mm ~ 0.4 in.6X 55 mm ~ 2.2 in.20 mm ~ 0.8 in. 5 mm ~ 0.2 in.6X SLWD112 mm ~ 4.4 in.20 mm ~ 0.8 in. 5 mm ~ 0.2 in.8X 41 mm ~ 1.6 in.15 mm ~ 0.6 in. 3 mm ~ 0.1 in.10X 41 mm ~ 1.6 in.12 mm ~ 0.5 in. 2.5 mm ~ 0.1 in.Using the Mantis 4) Using the MantisTurning the Power “ON”Boom Mount (refer to page 3 of this manual)There is one power switch for the Mantis boom mount system. It is located on the front panel of the vertical support column. Flip the switch to energize the Mantis illuminatorFX Bench Stand (refer to page 4 of this manual)There are three power switches for the Mantis FX bench stand system. The first is the main power switch. It is located on the back of the bench stand vertical support. When energized the switch is illuminated. The remaining power switches are on the front of the bench stand vertical support. The upper switch powers the main illuminator incorporated in the Mantis viewing head. The lower switch powers the substage illuminator built into the focusing platform.FocusingAll of the Mantis objective lenses (except 2X) are parfocal. This means that the image stays in focus when switching between objectives without re-focusing. For best results always focus with the highest magnification lens, then switch to the lower magnification.Boom Mount (refer to page 3 of this manual)To focus the boom mount Mantis system move the Mantis viewing head “UP” or “DOWN”. (Before moving the Mantis head always loosen the boom friction clamp lever located on the right side of the boom mount pivot). To facilitate focusing there are 4 plastic lugs located on the underside of the Mantis head. Hold one of the lugs between your thumb and index finger and gently move the head until proper focus is obtained. Tighten the boom friction clamp.FX Bench Stand (refer to page 4 of this manual)To focus the FX bench stand locate the focus adjustment wheel on the front, right hand corner of the bench stand base plate. Turning this wheel will move the focusing platform “UP” or “DOWN”. With a subject on the focusing platform look into the viewing screen and turn the focus adjustment wheel until a clear image is obtained.Adjusting the LightingThe main illuminator built into the Mantis viewing head features an adjustment to optimize lighting for different applications. The illumination adjustment is a horizontal disc on the right side of the Mantis viewing head. Rotate the disc while looking into the viewing screen until optimal lighting is achieved.4) Using the Mantis (con’t)Changing the Magnification (refer to pages 3 or 4 of this manual)Both Mantis systems use a turret assembly to allow the user to select between two different magnification levels. Objective lenses are screwed onto the threaded turret underneath the Mantis viewing head.After two objectives have been selected and screwed into place on the Mantis turret, they can be switched using the objective selection lever. The lever is located on the left side of the Mantis viewing head. The objective selection lever can be moved into two positions. Each position corresponds to a different objective lens being activated. Select the position that provides the magnification required for your application.Adjusting the Eye Spacing (IPD)The Mantis has an adjustment for different eye spacing. The Inter-pupilary Distance (IPD) must be adjusted to obtain a comfortable view. The IPD adjustment is located on the right side of the Mantis viewing head. While looking in the viewing screen rotate the adjustment knob (the left side optical path will move “LEFT” or “RIGHT”) until a comfortable view is achieved.Note: This adjustment is very important to comfortable and effective inspection. It must be re-adjusted for every individual using the Mantis.Options5) OptionsLens Protective coversAll mantis objectives can be fitted with a replaceable, clear plastic protective cap. These inexpensive caps protect the objective lens from damage and are especially useful when using the Mantis for rework operations. Choose from the chart below.Lens Vision Engineering Part No.2X, 4X, 6X, 8X M0106X SLWD M01610X M011Maintenance6)MaintenanceLamp Replacement (refer to pages 3 or 4 of this manual)Replace the lamps using the following procedure.1) Remove the Mantis viewing head by removing the Yaw Spigot nut.2) Turn the Mantis viewing head upside down.3) Remove the lamp cover (filter tray) by sliding it away from the Mantis head. Do not allow thediffuser lens to drop when removing the lamp covers.4) Pull the lamp out by holding it between your thumb and index finger.5) Replace lamp.6) Reassemble by reversing previous steps.Lens CleaningClean the objective lens using a lint free cloth. An anti-static cleaner may be used to reduce static charging.If frequent contamination is experienced it is recommended to use the optional Protective Lens Covers.Moisture Control (refer to pages 3 or 4 of this manual)The Mantis head is equipped with a blue desiccant cartridge for moisture control. This should be checked regularly. When the desiccant turns pink it is ready for replacement.To replace the cartridge remove the rubber plug under the Mantis viewing head, pull out the desiccant cartridge, replace and re-install the rubber plug.Replace with Desiccant 10 pack, Part No. M006.Optical Path AlignmentIt is a good idea to periodically check the Optical Path Alignment of the Mantis stereo view. Look into the viewing screen from a distance of 12”. The view will appear as two illuminated circles. These two circles must be horizontally aligned within 2/3 of their diameter of each other. Improper alignment will cause imaging problems.If the illuminated circles are out of alignment then they can be adjusted. Locate the large Phillips screw head on the back of the Mantis viewing head (this screw head is locked in place with black silicon). While still looking at the viewing screen from a 12” distance, adjust the screw until the two paths are in acceptable alignment.Fan (refer to pages 3 or 4 of this manual)Blow out the fan assembly with CLEAN, DRY AIR (up to 100 PSI) at least once a month to prevent excessive particulate build-up. This will maximize fan life.Troubleshooting7) TroubleshootingMantis has no powerIf the Mantis head has no power and the illuminator will not come “ON” then check the following items:•Is the Mantis power cord plugged in?•Is the wall outlet functioning properly and supplying sufficient voltage?•Is the fuse in the Mantis support column in good working condition?Optical ViewIf over time the optical view of the Mantis has degraded, check for the following:Are the objectives dirty or damaged?•Dirty or damaged lenses will cause an inferior image.Are both lighting lamps functioning properly?•Both lights must be working to supply sufficient light.Is the Eye Spacing control properly adjusted?•The eye spacing adjustment must be set correctly to obtain a comfortable view.Has the lighting adjustment been used to optimize the lighting?•Optimized lighting is important to maintaining a clear image.Have the Mirrors within the Mantis head become dirty?•Mirrors contaminated with particulate will impede image performance.Is the viewing screen dirty?•Clean the viewing screen regularly to prevent dirt build-up from degrading the image.Has the Optical Path alignment been checked?•Proper Optical path alignment will greatly improve viewing ease.Service 8) ServiceShould the Mantis stereo viewing system require service the unit may be returned to Vision Engineering Inc. Some of the simpler repair procedures are discussed here to prevent excessive downtime.Cleaning the mirrorsThe mirrors within the Mantis viewing head can be cleaned. These mirrors are very delicate and can only be blown off with clean, dry air. Never wipe the mirrors with any type of cloth. Required Tools:Small Phillips screwdriverMedium Phillips screwdriver (magnetic preferred)Work in a dust free environment1. Remove the Mantis viewing head from its support by removing the Yaw bolt.2. Rest the viewing head upside down (objective turret facing “UP”)3. Remove the two screws on the rear of the viewing head.4. Remove both filter trays to gain access to the lamps. Do not allow the diffuser lens to dropwhen removing the lamp covers.5. Remove the screw located in each lamp socket.6. The lower viewing head assembly (black lower section) should now be removable7. Turn the lower viewing head assembly over to prevent dust accumulation on the mirror.8. Without Touching the Mirrors, blow off mirrors with CLEAN, DRY AIR while holding unitupright. Ensure that any dust falls out of the viewing head.9. If any contaminant is on the beam splitter, it can be gently wiped with a soft cloth.10. Reassemble by reversing the disassembly instructions.8)Service (con’t)Fan ReplacementRequired Tools:Small Phillips screwdriverMedium Phillips screwdriverWork in a dust free environment1. Remove the objective lenses.2. Remove the Mantis viewing head from its support by removing the Yaw bolt.3. Rest the Mantis viewing head upside down (turret facing “UP”)4. Remove the three screws from the turret.5. Remove the two screws on the infinity lens.6. Remove the two screws holding the fan assembly in place.7. Remove the two screws on the rear of the Mantis viewing head.8. Remove both filter trays providing access to the lamps. Be careful not to allow the diffuserlens to drop when removing the filter tray.9. Remove the single screw in each lamp socket.10. The lower viewing head assembly (black lower section) now lifts off.11. Gently turn over the viewing head assembly to reduce the risk of the mirror collecting dust.12. Disconnect fan wires from P.C. board and remove old fan. Pay close attention to the wireconnection orientation on the P.C. board.13. Install new fan. Feed new fan wires through grommet one at a time. Connect the wires tothe P.C. board being careful to follow the same orientation as the prior fan.14. Reassemble by reversing disassembly steps.8)Service (con’t)Repairing Eye Spacing Control (IPD)Required Tools:Small Phillips screwdriverMedium Phillips screwdriver (magnetic preferred)Work in a dust free environment1. Remove the magnification objectives2. Remove the Mantis viewing head from its support by removing the Yaw bolt.3. Remove the eye spacing adjustment knob.4. Rest the Mantis head upside down (turret facing “UP”).5. Remove the two screws on the rear of the viewing head.6. Remove both filter trays providing access to the lamps. Be careful not to allow the diffuserlens to drop when removing filter tray.7. Remove the single screw from each lamp socket.8. The lower viewing head assembly (lower black section) can now be removed.9. Gently turn over the viewing head assembly to reduce the chance of dust collecting on themirror.10. Without Touching the Mirrors, replace the detached pin through the viewing head and intothe narrow groove on the eye spacing control knob.11. If necessary, blow off the mirrors with CLEAN, DRY AIR while holding the unit upright.Ensure that any dust falls out of the viewing head.12. Reassemble by reversing the disassembly steps.8)Service (con’t)Remove Mirror from Mantis HeadIn the event that a mirror become dislodged within the Mantis viewing head it may be possible to reattach it by following these steps. If a repair cannot be made then follow these steps toremove the loose mirror. Removing the loose mirror will prevent any internal damage during shipping when returning the unit for service. The mirror can now be packed separately and both units sent back to the factory for service.Required Tools:Small Phillips head screwdriverMedium Phillips head screwdriver (magnetic preferred)Work in a dust free environment1. Remove the Mantis viewing head from its support by removing the Yaw bolt.2. Rest the viewing head upside down (turret facing “UP”).3. Remove the two screws on the rear of the viewing head.4. Remove both filter trays providing access to the lamps. Be careful not to let the diffuser lensdrop when removing the filter trays.5. Remove the single screw in each lamp socket.6. The lower viewing head assembly (lower black section) can now be removed.7. Without Touching the Mirror, remove the mirror or reattach if required.8. Reassemble by reversing the disassembly steps.Warranty9) WarrantyThis product is warranted to be free from defects in material and workmanship for a period of one year from the date of invoice to the original purchaser.If, during the warranty period the product is found to be defective, it will be repaired or replaced at facilities of Vision Engineering Inc. or elsewhere, all at the option of Vision Engineering Inc. However, Vision Engineering Inc. reserves the right to refund the purchase price if it is unable to provide replacement, and repair is not commercially practicable or cannot be timely made. Parts not of Vision Engineering Inc. manufacture carry only the warranty of their manufacturer. Expendable components such as lamps and fuses carry no warranty.This warranty does not cover damage caused in transit, damage caused by misuse, neglect, or carelessness, or damage resulting from either improper servicing or modification by other than Vision Engineering Inc. approved service personnel. Further this warranty does not cover any routine maintenance work which is reasonably expected to be performed by the purchaser.No responsibility is assumed for unsatisfactory operating performance due to environmental conditions such as humidity, dust, corrosive chemicals, deposition of oil or other foreign matter, spillage, or other conditions beyond the control of Vision Engineering Inc..Except as stated herein, Vision Engineering Inc. MAKES NO OTHER WARRANTIES, EXPRESS OR IMPLIED BY LAW, WHETHER OR MERCHANTABILITY, FITNESS FOR A PARTICULAR PURPOSE OR OTHERWISE. Further, Vision Engineering Inc. shall not under any circumstances be liable for incidental, consequential or other damages.Information10) InformationVision Engineering Inc. is committed to providing top quality optical inspection systems. We employ a staff of trained Sales and Service engineers and have a network of Authorized distributors to assist you. Please call whenever you have questions.For additional information contact your local Vision Engineering Distributor or call:Corporate Headquarters Western Region Sales Office Vision Engineering Inc.Vision Engineering Inc.570 Danbury Road745 W. Taft AvenueNew Milford, CT 06776Orange, CA 92865Phone: (860) 355-3776Phone: (714) 974-6966。
条码检测仪的使用说明

条码检测仪的使用说明第一篇:条码检测仪的使用说明条码检测仪的使用说明通常在使用条码检测仪前要按照说明书,用所提供的校准标板对设备进行校准——在不用的时候要保证校准标板的洁净与不受损害。
有些设备需要根据参考反射率标板手工调节仪器;大多数的检测仪则是自动校准,在使用仪器前,应把校准作为其中的一个使用环节向用户提示。
在任何条件下检测条码符号,条码符号通常应为其最终的状态。
如果需要制样,可采取以下措施:首先把要检测的条码符号放在平整的黑色表面上检测,然后再把它放在明亮的表面上重复检测,取结果中较差的那组作为测量结果。
如果实际中已经知道符号背底所衬的材料类型,检验时条码背底要衬垫的状态应尽量与之一致。
如果需要手工扫描,就要手持光学扫描头从左到右或从右到左穿过符号,要尽量以平稳的方式和不变的速度,不能太快,也不能太慢,如果想要进行多重扫描,就要在符号高度范围内平均放置这些光头,而不要超出符号的顶端或底端。
1、检测仪的校准条码检测参数值都是依据扫描反射率曲线计算得出的,因此检测仪必须能精确地测量反射率,所以确保设备的正确校准是非常重要的工作,校正是保证测量结果正确性和一致性及可重复性的前提条件。
不正确的校准会影响设备的正常运行或者导致测量结果错误。
2、孔径/光源的选择光源应与实际所用的扫描光相匹配、测量孔径应与所检测的符号的X尺寸范围相匹配。
如果光源选择错误,特别是当其峰值波长偏离标准所要求的峰值波长,符号反差的测量值就可能会出现错误(如果条码的颜色不是黑条白空)。
在检验EAN/UPC条码时使用670纳米的可见红光为峰值波长,这是因为这个波长接近于使用激光二极管的激光扫描器和使用发光二极管的CCD扫描器的扫描光束的波长。
测量孔径则要根据具体应用的条码符号的尺寸而定,具体的选择方法见具体的应用标准与规范。
3、条码检测仪的使用对于光笔式检测仪,扫描时笔头应放在条码符号的左侧,笔体应和垂直线保持15度的倾角(或按照仪器说明书作一定角度的倾斜)。
Matrix200中文操作说明书

目录一、安装1、确定安装高度――――――――――――――――――――――――――――――――32、确定倾斜角度――――――――――――――――――――――――――――――――3二、接线―――――――――――――――――――――――――――――――――――41、电源连线――――――――――――――――――――――――――――――――――42、通讯连线――――――――――――――――――――――――――――――――――4三、调试―――――――――――――――――――――――――――――――――――51、打开VisiSet调试软件――――――――――――――――――――――――――――52、连接VisiSet与读码器――――――――――――――――――――――――――――53、调试读码器―――――――――――――――――――――――――――――――――7<1> 进入Continuous模式――――――――――――――――――――――――――――9<2> 确定条码位置――――――――――――――――――――――――――――― 10<3> 设置条码类型―――――――――――――――――――――――――――――10<4> 确定调试标准――――――――――――――――――――――――――――――11<5> 调整读码特性――――――――――――――――――――――――――――――11<6> 改回Phase Mode―――――――――――――――――――――――――――――13<7> 下载参数到读码器――――――――――――――――――――――――――――13<8> 上传和下载参数―――――――――――――――――――――――――――――141、确定安装高度Matrix 200 有四种型号,不同的型号根据其焦距安装高度也有所不同。
SmartQ V7 说明书

SmartQV7请访问智器官方网站 获取产品信息、技术支持和软件升级服务。
注意事项............................................01随配附件............................................02功能特性............................................03硬件规格............................................05认识产品............................................07升级固件............................................08● 开机................................................09● 开机界面.........................................09● 校准触摸屏.....................................09● 弹出右键菜单..................................09● 移动超过屏幕高度的窗口................10● 充电................................................10● 开始菜单.........................................10● 关机和挂起.....................................10● 快速启动栏.....................................10● 软键盘............................................11● 输入中文.........................................11● 音量调节.........................................12● 背光亮度及电源管理.......................12● 时间设置.........................................13● 连接电脑读写SD卡中的文件............14● HDMI 输出和TV-out 输出...............16● BT 下载...........................................17● RSS 订阅.........................................17● 即时通讯.........................................17● 浏览器.. (18)Ubuntu Linux 操作系统部分基本操作............................................08功能说明............................................15● 影音................................................15● 互联网............................................17................● PPS 在线视频播放...........................18● 电子邮件.........................................19● 个人信息管理..................................20● 文字处理.........................................20● 电子书阅读.....................................20● 电子表格.........................................21● 宝石方块.........................................22● 连连看............................................22● PDF 文档浏览..................................23● 图片查看.........................................23● 画图................................................23● 文件管理器.....................................24● 软件包安装.....................................24● 压缩文件管理.................................25● 查找文件及目录..............................25● 电子辞典.........................................26● 终端................................................27● 计算器............................................27● 记事本............................................27● 3G 连接...........................................28● Language ......................................28● 外观设定.........................................28● 无线网络.........................................29● 窗口主题.........................................32● 系统设置.........................................32● 蓝牙................................................33● 办公................................................20● 游戏................................................22● 图像................................................23● 系统工具........................................24● 附件................................................25● 首选项............................................28● 运行................................................38使用技巧及疑难问题解答...................39● 系统设置.........................................45● 安装和运行应用程序.......................46● 触摸屏校验.....................................4647Android 操作系统部分开机与关机........................................42桌面...................................................43按键...................................................44主菜单操作........................................45时间日期设置.....................................WIFI 无线连接操作.............................47网页浏览............................................48音乐播放............................................48............................................Windows CE 操作系统部分开机与关机........................................49按键...................................................50系统设置............................................51● 触摸屏校验.....................................51● 日期与时间设置..............................51● 背光、USB 、WIFI 和蓝牙................52● WIFI 网络连接.................................52● 蓝牙连接.........................................53● 输入面板.........................................53● 软键盘和输入法..............................53● 音量和声音设置..............................54● 电源属性.........................................54● 系统显示设置..................................54● 通过USB 连接PC 机..........................55● 文件浏览程序..................................56● 网络浏览器.....................................56● 音乐播放器.....................................57● 视频播放器.....................................57● QQ 客户端程序................................58应用程序............................................56应用程序安装. (58)注意事项●●●●●●●●●●本产品是高精密电子产品 , 请勿自行拆卸。
德国制造的4位数字数字显示压力传感器说明书

1:4-digit alphanumeric display 2:LEDs3:Programming buttonMade inGermanyProduct characteristics Combined pressure sensor ConnectorProcess connection:G 1A /Aseptoflex Vario Display units:bar,psi,MPa,%of the span Function programmable2-wire connection technology:analogue output3-wire connection technology:2outputsOUT1=switching outputOUT2=switching output or analogue output 4-digit alphanumeric displayMeasuring range:-1.00...10.00bar /-14.5...145.0psi /-0.100...1.000MPa Application Type of pressure:relative pressureHygienic systems,viscous media and liquids with suspended particlesLiquids and gasesApplication5MPa 725psi 50bar Pressure rating 15MPa 2175psi 150bar Bursting pressure min.5MPa725psi50barMAWP (for applications according to CRN)-25...125(145max.1h)Medium temperature [°C]Electrical data 2wires DC /3wires DC PNP/NPNElectrical design 20...32DC (2L)/18...32DC (3L)Operating voltage [V] 3.6...21(2L)/<45(3L)Current consumption [mA]>100(500V DC)Insulation resistance[MΩ]III Protection classyesReverse polarity protection Outputs 2-wire connection technology:analogue output3-wire connection technology:2outputsOUT1=switching outputOUT2=switching output or analogue outputOutput1x normally open /normally closed programmable +1x normally open /normallyclosed programmable or 1x analogue (4...20/20...4mA,scalable)Output function ---(2L)/250(3L)Current rating [mA]---(2L)/<2(3L)Voltage drop[V]pulsed Short-circuit protection yesOverload protection ---(2L)/125(3L)Switching frequency [Hz]I:4...20mA (Ineg:20...4mA)Analogue output 300(2L)/max.(Ub -10V)x 50(3L)Max.load[Ω]Measuring /setting range -0.100...1.000MPa -14.5...145.0psi -1.00...10.00bar Measuring range Setting range -0.098...1.000MPa -14.2...145.0psi -0.98...10.00bar Set point,SP -0.100...0.998MPa -14.5...144.7psi -1.00...9.98bar Reset point,rP-0.100...0.750MPa -14.5...108.7psi -1.00...7.50bar Analogue start point,ASP 0.150...1.000MPa21.8...145.0psi1.50...10.00barAnalogue end point,AEP 0.001MPa0.1psi0.01barin steps of SP1=2.50bar;rP1=2.30bar SP2=7.50bar;rP2=7.30bar ASP =0.00bar;AEP =10.00barFactory settingAccuracy /deviations Accuracy /deviations(in %of the span)Turn down 1:1<±0.2Switch point accuracy <±0.2Characteristics deviation *)<±0.15Linearity <±0.15Hysteresis <±0.1Repeatability **)<±0.1Long-term stability ***)Temperature coefficients (TEMPCO)in the temperature range 0...70°C (in %of the span per 10K)<±0.05Greatest TEMPCO of the zero point <±0.15Greatest TEMPCO of the span Reaction times 1(2L)/0.5(3L)Power-on delay time [s]---(2L)/3(3L)Min.response time switching output[ms]0.00...30.00Damping for the switching output (dAP)[s]0.01...99.99Damping for the analogue output (dAA)[s]45(2L)/7(3L)Step response time analogue output[ms]yesIntegrated watchdog Interfaces IO-Link Device COM2(38.4kBaud)Transfer type 1.0IO-Link revision 157d /00009D hIO-Link Device ID no profile Profiles yes SIO modeA Required master port type 1Process data analogue 2Process data binary 2.3Min.process cycle time [ms]Environment -25...80Ambient temperature [°C]-40...100Storage temperature [°C]IP 67/IP 68/IP 69KProtection Tests /approvals EMCDIN EN 61000-6-2DIN EN 61000-6-3Shock resistance 50g (11ms)DIN EN 60068-2-27:Vibration resistance 20g (10...2000Hz)DIN EN 60068-2-6:160MTTF[Years]Mechanical data G 1A /Aseptoflex VarioProcess connection ceramics (99.9%Al2O3);PTFE;stainless steel 316L /1.4435;surfacecharacteristics:Ra <0.4/Rz 4Materials (wetted parts)stainless steel 316L /1.4404;FPM;PTFE;PBT;PEI;PFAHousing materials 100million Switching cycles min.0.313Weight[kg]Displays /operating elements DisplayLED green Display unit LED yellowSwitching status 4-digit alphanumeric display Function display 4-digit alphanumeric displayMeasured values Electrical connection M12connector;Gold-plated contactsConnection Wiring1connection for2-wire operation2connection for3-wire operation3connection for IO-Link parameter setting(P=communication via IO-Link)RemarksRemarks(2L)=value for2-wire operation(3L)=value for3-wire operation*)linearity,incl.hysteresis and repeatability;(limit value setting to DIN16086)**)with temperature fluctuations<10K***)in%of the span per year1Pack quantity[piece]ifm electronic gmbh•Friedrichstraße1•45128Essen—We reserve the right to make technical alterations without prior notice.—GB—PI2794—16.04.2013。
Renishaw 机器工具探头技术指南说明书

BrochureThe evolution of machine tool probing technologyRenishaw invented the touch-trigger probe for machine tools in the 1970s. The success of this innovation, based on a kinematicresistive principle, has contributed to Renishaw’s status as a world leader in the design, manufacture and support of dimensionalmeasurement products. The basis of this design continues to play a valuable role in part set-up, measurement and process control.Decades of continuous investment in development enables Renishaw to provide high-quality products with leading-edgeperformance. This guide compares probes with RENGAGE™ technology with those of conventional probe design and illustratesRENGAGE technology’s superior performance capabilities based upon ‘real world’ tests.RENGAGE technology delivers exceptional three-dimensional (3D) measurement performance and sub-micron repeatability.Due to their innovative design and outstanding capability, Renishaw probes with RENGAGE technology outperformhigh-accuracy machine tool probes available from other manufacturers.Renishaw probes with RENGAGE technologyoutperform high-accuracy machine toolprobes available from other manufacturers.Conventional probe technologyKinematic resistive probesInside a kinematic resistive probe, three equally-spaced rods rest on six tungsten carbide balls to provide six points of contact in a kinematic location. An electrical current flows between the balls and the rods.A spring-loaded mechanism allows the probe stylus to deflect when it makes contact with the workpiece. Upon making contact with a workpiece, the force translated through the stylus moves the balls and rods apart, reducing the size of the contact patches and increasing their electrical resistance. The probe is triggered when a defined threshold is reached.When the stylus is no longer in contact with the workpiece, the probe mechanism returns to its original position (reseats) to within 1 μm 2σ.Other types of probesSpherical seat or pivoting type probes are common alternative designs. Theory suggests that these designs provide uniform trigger force in the XY plane. However, the reality is very different because this is dependent upon the precision of themanufactured sphere and conical seat surfaces, and the relationship between the two. Therefore, in practice, trigger forces are highly variable.The major drawbacks of this design are:1. The stylus is not uniquely located because the relationship between the sphere and conical seat does not constrain all degrees of freedom. The mechanism can rotate and is not suitable for star-styli.2. The free motion of the mechanism typically results in a significant stylus deflection before the probe triggers.3. A high contact force between the stylus and the workpiece may mark the workpiece.Probe lobingLobing is a characteristic of all probes. It is caused by bending of the stylus and movement of the probe mechanism before the probe registers contact with a surface. It is therefore dependent upon:• Length and stiffness of the stylus • Force required to trigger the probe• Direction of contact with the surface • Design of the probe mechanismAll probes will therefore exhibit some lobing, which when plotted can resemble the irregular shape opposite.For two axis measurement, potential errors are relatively easy to calibrate out. In three axis measurement however, lobing errors are greater and more complex to compensate for, particularly with some conventional probes.These errors are significant and can adversely impact accuracy and repeatability in 3D measurement.The stages in trigger generation for a kinematic resistive probe are shown below. Repeatable electrical triggering andmechanical reseating of the mechanism are fundamental to reliable metrology.Example lobing plot (X-Y only) for conventionalspherical seat type probeTrigger mechanismAll kinematics in contactMachine directionMachine directionContact forceReactive forceMechanism pivotsabout these contactsContacts separate Kinematics reseat to repeatable positionStage 1Stage 2Close up of kinematicsResistance increases as area reducesCurrent flows through kinematicsContact patch reduces as stylus force balances spring forceSection throughkinematicsSpringRod and ballkinematic locationsSection viewAnnular reference surface ReferenceringConical seatSpherical reference surfaceSpherical surface pivots within conical seatAnnular reference surface touches reference ringStylus deflects trigger mechanism plungerFurther pivoting about contact point between reference surfacesFor more information on the Productive Process Pyramid™, see /pyramidBenchmarking RENGAGE™ technologyEngineers at Renishaw take immense pride in the products that are developed for our customers. It is important that our products perform to the highest standard to ensure that customers’ products – inspected by our systems – are also of the highest quality. Engineers at Renishaw take immense pride in the products that are developed for our customers. It is important that our products perform to the highest standard to ensure that customers’ products – inspected by our systems – are also of the highest quality.Renishaw states that the performance of its high-precision machine tool probes with RENGAGE™ technology is “unrivalled”. T ransparency is as central to Renishaw’s culture as the spirit of innovation, so to confirm the accuracyof these claims, Renishaw tested the OMP400 probe alongside five touch-trigger probes from other manufacturers – probes “A”, “B”, “C”, “D” and “E”. These probes are either low force versions of conventional probing systems or specially engineered high-accuracy probes.T o determine a realistic assessment of the performance of each probe, Renishaw ensured that each probe completed a thorough test programme – increasing dwell time and re-running the tests where necessary. This enabled each probe to provide results that can be used to benchmark performance.Testing probe performanceA consistent set of metrics is needed to compare the performance of the probes being tested. 2D form error, 3D form error and repeatability have been chosen, as these performance characteristics are critical in order to produce accurate components.The performance test measures a Ø25 mm calibrated sphere at a variety of angles and feedrates, with different styli, to obtain 2D form error, 3D form error and repeatability.When performing the test, best practice – as defined in the ISO 230-10 standard – was followed. A medium-accuracy, mid-priced, 3-axis vertical machining centre (VMC) with a Siemens 828D control was used to conduct the test.The test comprised the following aspects:With styli of different lengthsEach probe was fitted first with a 50 mm stylus, and then with a 200 mm stylus. Both styli were used to measure the points on the sphere at each feedrate.According to specification documentation, all of the probes being tested can be used with a 50 mm stylus, but only theOMP400 and probe “A” are recommended for use with a 200 mm stylus. 200 mm is the longest stylus that is recommended for use with all machine tool probes with RENGAGE™ technology.In realistic machining conditionsAll of the tests were run in wet conditions. The sphere was lubricated using coolant to represent the conditions found in a realistic machining scenario.2D performanceThe 2D performance is measured by finding the form error of a 2D feature. In this test, the radius of a calibrated sphere was measured by taking points around its equator. The difference between the minimum and the maximum measured radius found by these points is the 2D form error.Given that the dimensions of the sphere are known precisely, the form error must be generated by the probe. The lower the 2D form error of the probe, the better the 2D performance.Points measured on a sphere145 points at 2.5° increments were measured normal to the surface at 0°, 22.5°, 45° and 67.5° during the test. A point was also measured at the pole of the sphere.Points at 0° are used for calculation of 2D form error. When calculating 3D form error, all of the points are used.To measure repeatability, each point was measured 25 times.At a variety of feedratesThe test was run multiple times at 30 mm/min, 600 mm/min and 2000 mm/min.3D performanceWith multi-axis machining now common place, 3D measurement performance is more important than ever.3D performance is measured by finding the form error of a feature with X, Y and Z dimensions. The lower the 3D form error value, the better the probe’s 3D performance.To measure the 3D form error, the test measured the radius of a calibrated sphere by taking points at four different elevations and at the pole.The difference between the minimum and the maximum measured radius is the 3D form error.RepeatabilityIn this test, repeatability is a measure of how well a probe can reproduce a measurement under constant conditions. It is a metric that is frequently quoted on probe datasheets. The lower the value, the better the repeatability. Repeatability is different from accuracy, as accuracy describes how close a measured value is from the true value.A 2D form plotA 3D form plotRepeatable, but not accurate,measurements30 mm/min 600 mm/min 2000 mm/min---0°0°22.5°45°67.5°90°--------------------------------------------------------------------200 mm50 mm 45°----2D form errorO M P 4002D form error comparison at 30 mm/min with a 50 mm stylus 2D form error comparison at 30 mm/min with a 200 mm stylusI n c o m p l e t e t e s t *I n c o m p l e t e t e s t *I n c o m p l e t e t e s t *I n c o m p l e t e t e s t *2D form error comparison at 600 mm/min with a 50 mm stylus 2D form error comparison at 600 mm/min with a 200 mm stylus2D form error comparison at 2000 mm/min with a 50 mm stylus I n c o m p l e t e t e s t *I n c o m p l e t e t e s t *2D form error comparison at 2000 mm/min with a 200 mm stylus* Probes B and D failed to complete the test with a 200 mm stylus. However, neither of these probes are specified to work with a 200 mm stylus.P r o b e AP r o b e BP r o b e CP r o b e DP r o b e EThe Renishaw OMP400 probe with RENGAGE™ technology has the lowest 3D form error at all feedrates with both the 50 mm and 200 mm stylus.0°22.5°45°67.5°90°OMP400Probe A-10 μm -20 μm10 μm 20 μm 30 μm 0°315°270°225°180°135°45°-10 μm-20 μm0 μm 10 μm 20 μm 30 μm 0°315°225°180°135°45°Probe BProbe C-10 μm-20 μm10 μm 20 μm 30 μm 315°270°225°135°45°-10 μm-20 μm0 μm 10 μm 20 μm 30 μm 0°315°225°135°45°Probe DProbe E-10 μm-20 μm 10 μm 20 μm 30 μm 0°315°270°225°135°45°-10 μm -20 μm10 μm20 μm 30 μm 315°225°135°45°0 μm 0 μm 0 μm 0 μm O M P 4003D form error comparison at 30 mm/min with a 50 mm stylus 3D form error comparison at 2000 mm/min with a 50 mm stylus 3D form error3D form error comparison at 30 mm/min with a 200 mm stylus3D form error comparison at 600 mm/min with a 50 mm stylus 3D form error comparison at 600 mm/min with a 200 mm stylus3D form error comparison at 2000 mm/min with a 200 mm stylus* Probes B and D failed to complete the test with a 200 mm stylus. However, neither of these probes are specified to work with a 200 mm stylus.I n c o m p l e t e t e s t *I n c o m p l e t e t e s t *I n c o m p l e t e t e s t *I n c o m p l e t e t e s t *I n c o m p l e t e t e s t *I n c o m p l e t e t e s t *P r o b e AP r o b e BP r o b e CP r o b e DP r o b e EO M P 400Repeatability comparison at 30 mm/min with 50 mm stylus Repeatability comparison at 2000 mm/min with 50 mm stylus Repeatability comparison at 30 mm/min with 200 mm stylusI n c o m p l e t e t e s t *I n c o m p l e t e t e s t *I n c o m p l e t e t e s t *I n c o m p l e t e t e s t *I n c o m p l e t e t e s t *I n c o m p l e t e t e s t *Repeatability comparison at 600 mm/min with 50 mm stylus Repeatability comparison at 600 mm/min with 200 mm stylusRepeatability comparison at 2000 mm/min with 200 mm stylus* Probes B and D failed to complete the test with a 200 mm stylus. However, neither of these probes are specified to work with a 200 mm stylus.RepeatabilityProbing pays with RenishawThe repeatability of the Renishaw OMP400 probe with RENGAGE™ technology is better than or equal to other probes on the market at all feedrates with both the 50 mm and 200 mm stylus.P r o b e AP r o b e BP r o b e CP r o b e DP r o b e EOptimise your cutting processReduce scrap and reworkSave time and money£Ensure parts are machined“right first time”.Set parts up to ten times faster thanwhen using manual methods.Produce more parts reliably and accurately.Meeting current and future performance requirements for our products demands manufacture of ever smaller and more intricate parts that are consistently accurate to within 1 μm. Reliable set-up and measurements are therefore critical to this process and form the basis of our decision to use RENGAGE™ technology.Flann Microwave (UK)T echnical assistanceT rainingWe supply technical assistance to all our global customers.We provide a variety of support agreements bespoke to your individual needs.We offer standard and bespoke training courses to meet your requirements.Buy spares and accessories online or obtain quotes for Renishaw parts 24/7.The Renishaw advantageSupport and upgradesSpares and accessoriesAt Renishaw, we enjoy an excellent reputation for offering strong support to our customers through a network of over 70 service and support offices worldwide.RENISHAW HAS MADE CONSIDERABLE EFFORTS TO ENSURE THE CONTENT OF THIS DOCUMENT IS CORRECT A T THE DATE OFPUBLICATION BUT MAKES NO WARRANTIES OR REPRESENTATIONS REGARDING THE CONTENT . RENISHAW EXCLUDES LIABILITY ,HOWSOEVER ARISING, FOR ANY INACCURACIES IN THIS DOCUMENT .© 2011-2018 Renishaw plc. All rights reserved.Renishaw reserves the right to change specifications without notice.RENISHAW and the probe symbol used in the RENISHAW logo are registered trade marks of Renishaw plc in the United Kingdom and other countries. apply innovation and names and designations of other Renishaw products and technologies are trade marks of Renishaw plc or its subsidiaries.All other brand names and product names used in this document are trade names, trade marks or registered trade marks of their respective owners.About RenishawRenishaw is an established world leader in engineering technologies, with a strong history of innovation in product development and manufacturing. Since its formation in 1973, the company has supplied leading-edge products that increase process productivity, improve product quality and deliver cost-effective automation solutions.A worldwide network of subsidiary companies and distributors provides exceptional service and support for its customers.Products include:• Additive manufacturing and vacuum casting technologies for design, prototyping, and production applications• Dental CAD/CAM scanning systems and supply of dental structures• Encoder systems for high-accuracy linear, angle and rotary position feedback• Fixturing for CMMs (co-ordinate measuring machines) and gauging systems• Gauging systems for comparative measurement of machined parts• High-speed laser measurement and surveying systems for use in extreme environments• Laser and ballbar systems for performance measurement and calibration of machines• Medical devices for neurosurgical applications• Probe systems and software for job set-up, tool setting and inspection on CNC machine tools• Raman spectroscopy systems for non-destructive material analysis• Sensor systems and software for measurement on CMMs• Styli for CMM and machine tool probe applicationsFor worldwide contact details, visit /contactPart no.: H-2000-3537-02-A Issued: 12.2018*H-2000-3537-02*T +44 (0) 1453 524524F +44 (0) 1453 524901E ***************Renishaw plcNew Mills, Wotton-under-EdgeGloucestershire, GL12 8JR United Kingdom。
Veriti操作说明 2

Veriti PCR仪简明操作说明Applied Biosystems触摸屏常用按键说明:操作步骤:1、打开PCR仪的热盖,插入样品管。
盖好热盖。
2、打开PCR仪的电源,仪器程序开始初始化,需等待几分钟。
3、初始化完成后,显示主菜单:4、点“Browse/New Methods”,进入PCR程序列表:5、可以直接点一个PCR程序,选择“Start Run”运行;点右边的符号,可以选择不同的文件夹。
如要新建一个PCR程序,点“New”,出现PCR程序:6、添加一段程序:点中上方的“Stage”位置,该位置变红;再点“Add”,软件将加入一段新的程序。
7、修改循环数、温度、时间:点中循环次数、温度或时间位置,下方出现数字键。
依次点数字键,出现合适数字后,点“Done”确定。
8、增加一个步骤:点“Step”位置,该位置变红;再点“Add”,软件将加入一个新的步骤。
9、删除一个步骤:点“Step”位置,在点“Delete”,软件将该步骤删除。
10、建立梯度模式:1)点中一个步骤,再点“Option”键,出现选项如下2)点“VeriFlex step”,出现梯度创建窗口:输入6个梯度温度,温度下方的“1-2”是指对应的1、2两行加热孔,全部输好后,点“Done”确定。
注意:相邻的两个梯度温度之差最大不能超过5℃!11、建立渐变模式:1)点中一个步骤,再点“Option”键,出现选项如下2)点“Auto Delta”,出现渐变模式创建窗口。
点“Staring Cycle”,输入起始循环数;点“Delta Temperature”,输入温度变化值;点“Delta Time”,输入时间变化值。
渐变模式适用于touchdown PCR,可以提高PCR反应的特异性。
例:输入起始循环数为2,温度变化值为+0.5℃,时间变化值为+5s,则表示从第2个循环开始,每循环一次升温0.5℃,时间增加5s。
12、增加暂停步骤:1)点中一个步骤,再点“Option”键,出现选项如下3)点“Pause”,出现如下窗口。
wiegand门禁说明书

AUTO-DIALER 911微电脑自动求救机CCTV SECURITY ALARM AUTOMATION SYSTEM电气特性:工作电压:DC11V TO 15V静态电流:20mA (MAX)拔号方式:音频/脉冲,跳线选择J1报警方式:N.C.、N.O.和电压信号跳线选择J2、J3录音时间:20秒,掉电后电话号码、语音不丢失储存电话号码:4组电话,每组最长可存入16位数字二级私密码:0-6位私人密码,前三位可用解除报警,整体(六体)密码用于更改设置出厂密码:911外观图:①喇叭②麦克风③7段显示器:输入所要储存之号码时,会同时显示其号码④E4指示灯:设定E4号码时,此灯会亮⑤E1指示灯:设定E1电话或行动电话号码时,此灯会亮⑥E2指示灯:设定E2电话或行动电话号码时,此灯会亮⑦ E3指示灯:设定E3电话或行动电话号码时,此灯会亮若设定密码时,E1、E2、E3及E4指示灯会亮⑧接至电话接头⑨○10接至DC12V电源,桔色线(或红色)接正电压,咖啡色线(或黑色)接负电压○11○12信号触发线,当接到N.C.或N.O.干接点时,不分极性,作为DC12V电压输入时,蓝色线(或黄色)接正电压,绿色线接负电压○13 P按键可作为以下用途:可储存6位数字作为密码当使用于语音自动回报系统之总机时,可作为暂停时间,按1次,两秒;按2次,4秒,以此类推.有此功能,即可自动打到分机○14接并联电话机设定触发信号及电话系统:①打开背盖②可看见印刷电路板上有3个跳线座J1、J2、J3,依序并排。
可根据附图调整触发信号及电话系统③配合电信局设定电话为TONE或PULSE系统将J1设定于“左边”即为TONE系统将J1设定于“右边”即为PULSE系统④触发信号,请根据保全主机或感应器触发后输出接点,选择适当之跳线座组合。
(A)N.C.输入:将J2置于“左边”,J3亦置于“左边”(B)N.O.输入:将J2置于“右边”,J3置于“左边”(C)电压输入:将J2置于“左边”,J3置于“右边”⑤设定完成后,请将背盖盖上微电脑自动求救机AUTO-DIALER操作程序开机后先自检:自检完毕后进入工作状态,七段显示器的右下角小数点闪烁,若已存有信息,则收到报警信号后AUTO-DIALER自动开始报警,如要设置或改变设置,按以下步骤可以储存,检查电话号码,密码及录音、放音1 进入编程状态:先键入0-6位)然后按下注意:出厂密码为911例如:新机器未更改密码时进入编程状态操作如下:⑨①① ENTER如密码输入正确则显示一下□,然后进入编程状态显示5若密码输入错误则显示一下E,退回工作状态,可按上述步骤重新输入2 储存第1组电话号码:在编程状态下,即显示5状态下:例如电话号码为93953399,则操作程序如下:A9○3○5○3○3○99键入时间始储存号码,如显示□,则表示已正确存入,然后返回5状态,如显示一下E,则表示未能正确存入,5 如要清除第1组电话号码时,只需在5 状态下键入B 若先拨至语音自动播报总机,不透过接线员转接,再自动拨到分机,假设分机号码为12,则储存方式如下:9○3○5○3○3○99①②C 每按一次(储存第2、3、4组电话号码方式均与第1组相同)3查询所预存之电话号码:在编程状态下,即显示5状态下,按3键,此时显示匚,表示CHECK,再按所欲查询之E1、E2、E3、E4或PAUSE,显示器开始显示号码,其操作程序如下:或或或显示器开始显示所预存之电4储存及播放求救语音信息:A 本机可储存20秒语音信息,在编程状态下,即5状态下,按1键(此时显示器显示┌表示RECORD),即可直接录音,其操作程序如下:①开始讲话,录音回音嘟响(20秒后录音完毕,即自动停止。
Productivity Inc Makino a71机器人安装前检查列表说明书

15150 25th Avenue North, Minneapolis, MN 55447-1981Phone 763-476-8600 Fax 763-476-4092For Service: MN 763-476-4191 IA 319-632-4288 NE 402-330-2323Visit us at: Productivity is ISO 9001:2000 CertifiedProductivity Inc®Makino a71 PRE-INSTALLATION CHECKLIST – Rev 2/2009Installation of your new Makino a71 can be smooth and rapid if preparations are made prior to the delivery of your machine. Any questions regarding machine installation should be directed to our service department for clarification. We hope this checklist will aid in a rapid installation of your new machine. NOTE: The following must be completed prior to our service technician arriving at your facility to install the new machine.¾Power Requirements for your machine: 240v/3ph/65kVa** 225Amp (Main Circuit Breaker)460v/3ph/65kVa** 125 AmpNOTE: **85kVa (including options) See Makino Installation Manual or contact our Service Department for complete information or questions. Machine is a dual-voltage machine and comes with a transformer.Proper voltage per machine specifications should be ready at machine site. Do NOT power up the machine.¾Customer should furnish and have available the proper supply and types of lubricants required for machine operation. See enclosed Makino Installation Manual for specifics – any questions should be directed to our Service Department at the above locations.TYPEITEM CAPACITY FLUID(may vary with type/size of tankWater Soluble, SyntheticGallonsCoolant 106ordered – check Manual for specifics)You will need to have Coolant on hand at the time of installation. Contact our Service Department with any questions.¾Air lines should be routed to the machine location and operational for proper air pressure.Must have clean, dry air supply with less than 40% relative humidity in line. In-line water trap*****************************;werecommend½”airlinehose.¾Machine location should be planned to allow enough room for access panels to be opened and serviced with ease.A minimum of 36” clearance is required around the machine for operator and maintenance access.¾Weight requirements should be checked to insure that the surface below the machine will have sufficient strength for support and stability. The machine must be set on a solid, sound and stable, steel bar-reinforced concrete slab poured directly on the grade. In general, the 6” concrete floor on industrial buildings is suitable for machineplacement.¾The Makino a71 can be moved with either a forklift or crane***. Upon arrival of your machine, uncrate and immediately check for visible damage. SEE ATTACHED FOR SHIPPING DIMENSIONS.***NOTE: LIFTING EQUIPMENT, ROPES, SHACKLES, LIFTING BARS, LIFTING BEAMS, ETC. ARE OPTIONAL EQUIPMENT AND ARE NOT PROVIDED WITH THE MACHINE. ITEMS MUST BE PURCHASED PRIOR TO MACHINE DELIVERY. CHECK WITH YOUR RIGGER TO SEE IF THEY HAVE ANY OF THESE ITEMS.***¾Remove as much preservative from the machine as possible without having to power up (tables – slides, pulleys, etc.). We recommend mineral spirits to clean. Apply oil when finished to prevent rust.Approximate Machine Shipping Dimensions(Note – they may vary slightly – we will provide you with a Bill of Lading copy with actual dimensions at time of shipment. Refer to your Makino Installation Manual for exact floor space/layout dimensions/requirements on the Chip Conveyor/Tank and any other optional peripherals purchased with your new machine.)Makino a71, 40/60-Tool ATC MachineAPPROX SHIP WEIGHTS, MACHINE/ACCESSORIES APPROXIMATE SHIPPING DIMENSIONS (Note: This will vary depending upon the configuration/options ordered.)31,526# (machine) 183” L x 116” W x 133" H (machine skidded and packed)2,205# (60ATC Unit) 111” L x 57” W x 70” H (60ATC Unit Crated)2,205# (Coolant Tank) 117” L x 92” W x 52” H (Coolant Tank/Chip Conveyor Skidded/Crated) 661# (Accessory Box) 113” L x 44” W x 41” H (Crated/skidded)882# (Accessory Box) 48” L x 39” W x 70” H (crated)727# (transformer) 40” L x 39” W x 32” H (skidded – usually ships separately from Makino) See Makino Installation Manual for floor space/layout dimensions, depending upon your configuration.Makino a71, 97/137-Tool ATC MachineAPPROX SHIP WEIGHTS, MACHINE/ACCESSORIES APPROXIMATE SHIPPING DIMENSIONS (Note: This will vary depending upon the configuration/options ordered.)29,652# (machine) 183” L x 116” W x 133" H (machine skidded and packed)7,937# (97/137ATC) 105” L x 82” W x 134” H (97/137ATC crated)800# (ATC Cover) 107” L x 86” W x 98” H (crated)2,205# (Coolant Tank) 111” L x 57” W x 70” H (Coolant Tank/Chip Conveyor Skidded/Crated) 772# (Air Dryer/Accy) 40” L x 26” W x 91” H (Crated/skidded)882# (pallets/skidded) 53” L x 31” W x 17” H (crated)727# (transformer) 40” L x 39” W x 32” H (skidded – usually ships separately from Makino) See Makino Installation Manual for floor space/layout dimensions, depending upon your configuration.Makino a71, 300-Tool ATC MachineAPPROX SHIP WEIGHTS, MACHINE/ACCESSORIES APPROXIMATE SHIPPING DIMENSIONS (Note: This will vary depending upon the configuration/options ordered.)30,093# (machine) 184” L x 116” W x 131" H (machine skidded and packed)7,937# (300ATC) 105” L x 82” W x 133” H (300ATC crated)800# (ATC Cover) 107” L x 86” W x 98” H (crated)1,800# (Coolant Tank) 102” L x 52” W x 64” H (Coolant Tank/Chip Conveyor Skidded/Crated) 700# (Air Dryer/Accy) 96” L x 45” W x 69” H (Crated/skidded)250# (Accessories) 96” L x 45” W x 69” H (Skid/Crated Box)750# (pallets/skidded) 48” L x 30” W x 16” H (crated)727# (transformer) 40” L x 39” W x 32” H (skidded – usually ships separately from Makino) See Makino Installation Manual for floor space/layout dimensions, depending upon your configuration.PLEASE FORWARD THIS TO THE APPROPRIATE PERSON. THANK YOU.。
霍尼韦尔DC1040中文说明书
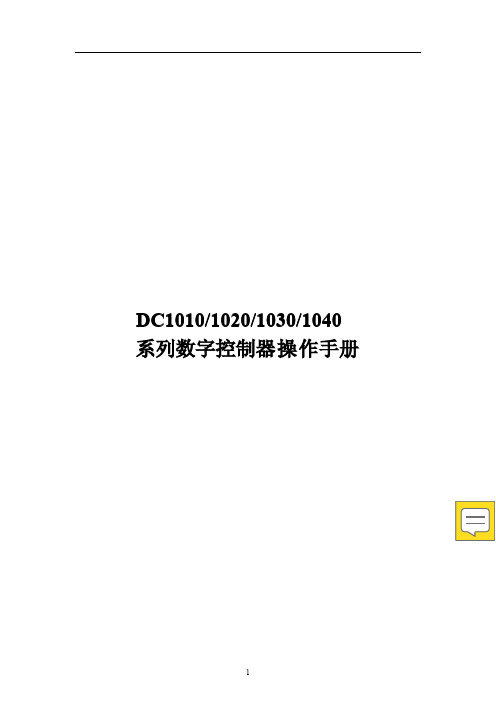
AL2 :第二路报警(Alarm 2),红色灯
AL3 :第三路报警(Alarm 3),红色灯
MAN :手动,黄色灯
*注意:当发生故障(Error)时,MAN 灯亮,输出百分比归零。
1.3 按键
SET :设定键(写入设定值或切换模式)
:移位键(移动设定位数)
:减少键
:增加键 A/M :自动(Auto)/手动(Manual)切换键 2、 自整定功能(AutoTuning) 2.1 将 AT(在 User Leve 中)设定为 YES,启动自整定功能 2.2 ATVL:自整定偏移量(AUTO Tuning offset Vaiue)
子控制输入信号低于下限(INP2)
*
内存(RAM)故障
接口故障
自整定失败
注意:当有“*”标记的故障发生时,请与供应商联系。
4、操作流程
(1):按“SET”键。 (2):按“SET”键持续 5 秒 (3):当 LCK=‘1111’时,按“SET”键和‘ (4):当 LCK=‘0000’时,按“SET”键和‘ 1.1 Level 1
4
4.1.6 输出限幅百分比是“0”时,表示控制器没有输出。
1.2 Level 2
主控制 比例带
主控制 集分时间
主控制 微分时间
主控制 死区时间
主控制 自整定偏移量
主控制 比例循环
主控制 迟滞
子控制 比例带
子控制 集分时间
子控制 微分时间
子控制 比例循环
子控制 迟滞
主控制 间隙 (第一路输出)
子控制 输出间隙(第二路输出)
与 ALT1 相同
范围: 00~19
与 ALT1 相同
范围: 0~1000
维萨拉湿度和温度传感器产品说明书

OrdererOrder no.MMT317 Moisture and Temperature Transmitter1234567891011121314151617 Vaisala HUMICAP® Moisture and Temperature Transmitter for Oil MMT310 7A2121. Probe code MMT317small pressure tight probe72. Transmitter type aw+T Faw+T+ppm for mineral transformer oil only M%RS + T + ppm mineral transformer oil only Paw+T+ppm**)specific transformer oil type:__________X3. Mounting Mounting plate (72.5 x 115 mm)54. Power supply no (24 VDC)A5. Signal output Analog output channel (Ch1&Ch2) 4... 20 mA & RS232C1Analog output channel (Ch1&Ch2)0... 20 mA & RS232C2Analog output channel (Ch1&Ch2) 1... 5 V & RS232C JAnalog output channel (Ch1&Ch2)0... 5 V & RS232C4Analog output channel (Ch1&Ch2)0... 10 V & RS232C56. Analog output signals Analog outputs disabled A A7. for Ch1 and Ch2Temperature (choose range in next section)C Caw (0...1)(0...1)T Tppm (0…100)(0…100)U U%RS (0..100)(0..100)W WSPECIAL:Define quantity for CH1:________________CH2:________________X XDefine scale for CH1:________________CH2:________________NOTE:- Choose A for both channels if you don't use analog outputs Ch1Ch28. Analog output range No range Afor temperature -60…+60°C(-76…140°F)B-40...+60°C(-40...+140°F)C-40...+120°C(-40...+248°F)D-40...+180°C(-40...+356°F)E-20...+60°C(-4...+140°F)F-20...+80°C(-4...+176°F)G-20...+120°C(-4...+248°F)HNOTE:0...+60°C(+32...+140°F)J- Choose A when T0...+100°C(+32...+ 212°F)Kis not desired special X9. Output units metric1non-metric210. Interface connection Connector (M12, 8-pin), no plug0Connector (M12, 8 pin) and plug with 5 m cable spare 5 m cable: 2121424Connector (M12, 8 pin) and plug with 10 m cable spare 10 m cable: 210964SP7Connector (M12, 8 pin) and plug with screw terminals511. Operating manual language no manual Aenglish see latest manual online: /mmt310B12. Probe with 0.5 m cable Xwith 2 m cable Pwith 5 m cable Qwith 10 m cable R13. Moisture sensor type special sensor for fluids spare: HUMICAP180L2214. Sensor protection in probe steinless steel grid (for applications with high flow speed, >1 m/s)spare: 220752SP Estainless steel grid (standard)spare: HM47453SP F15. Special features none116. Installation kit Swagelok ISO 1/2"spare: SWG12ISO12KSwagelok NPT 1/2"spare: SWG12NPT12NSwagelok ISO 3/8"spare: SWG12ISO38V 17. Calibration certificate calibration at room temperature standard service calibration: 2169892Selections in bold are included in the prices of the basic versions.Selections in italic are available at an extra price.Options and accessories:Example of order code with typical settings:238607USB Service cable1234567891011121314151617 ASM211103Rain Shield MMT3107F5A1C T K14B P2F1K2End customer:**) Check the availability and special delivery time from your local Vaisala representative.This model is always needed with silicone based transformer oils.OrdererOrder no.MMT318 Moisture and Temperature Transmitter1234567891011121314151617 Vaisala HUMICAP® Moisture and Temperature Transmitter for Oil MMT310 8A2121. Probe code MMT318for pressurized pipelines82. Transmitter type aw+T Faw+T+ppm for mineral transformer oil only M%RS + T + ppm mineral transformer oil only Paw+T+ppm**)specific transformer oil type:__________X3. Mounting Mounting plate (72.5 x 115 mm)54. Power supply no (24 VDC)A5. Signal output Analog output channel (Ch1&Ch2) 4... 20 mA & RS232C1Analog output channel (Ch1&Ch2)0... 20 mA & RS232C2Analog output channel (Ch1&Ch2) 1... 5 V & RS232C JAnalog output channel (Ch1&Ch2)0... 5 V & RS232C4Analog output channel (Ch1&Ch2)0... 10 V & RS232C56. Analog output signals Analog outputs disabled A A7. for Ch1 and Ch2Temperature (choose range in next section)C Caw (0...1)(0...1)T Tppm (0…100)(0…100)U U%RS (0..100)(0..100)W WSPECIAL:Define quantity for CH1:________________CH2:________________X XDefine scale for CH1:________________CH2:________________NOTE:- Choose A for both channels if you don't use analog outputs Ch1Ch28. Analog output range No range Afor temperature -60…+60°C(-76…140°F)B-40...+60°C(-40...+140°F)C-40...+120°C(-40...+248°F)D-40...+180°C(-40...+356°F)E-20...+60°C(-4...+140°F)F-20...+80°C(-4...+176°F)G-20...+120°C(-4...+248°F)HNOTE:0...+60°C(+32...+140°F)J- Choose A when T0...+100°C(+32...+ 212°F)Kis not desired special X9. Output units metric1non-metric210. Interface connection Connector (M12, 8-pin), no plug0Connector (M12, 8 pin) and plug with 5m cable spare 5 m cable: 2121424Connector (M12, 8 pin) and plug with 10 m cable spare 10 m cable: 210964SP7Connector (M12, 8 pin) and plug with screw terminals511. Operating manual language no manual Aenglish see latest manual online: /mmt310B12. Probe type226 mm probe with 2 m cable S226 mm probe with 5 m cable T226 mm probe with 10 m cable U448 mm probe with 2 m cable V448 mm probe with 5 m cable W448 mm probe with 10 m cable Z13. Moisture sensor type special sensor for fluids spare: HUMICAP180L2214. Sensor protection in probe stainless steel grid (for applications with high flow speed, >1 m/s)spare: 220752SP Estainless steel grid (standard)spare: HM47453SP F15. Special features none116. Installation kit ball valve set spare: BALLVALVE-1Efitting body ISO1/2, no leak screw spare: DRW212076SP Gfitting body NPT1/2, no leak screw spare: 212810SP H 17. Calibration certificate calibration at room temperature standard service calibration: 2169892Selections in bold are included in the prices of the basic versions.Selections in italic are available at an extra price.Options and accessories:Example of order code with typical settings:238607USB Service cable1234567891011121314151617 ASM211103Rain Shield MMT3108F5A1C T K14B S2F1E2End customer:**) Check the availability and special delivery time from your local Vaisala representative.This model is always needed with silicone based transformer oils.。
Walker 738 型号微芯片切割机用户操作说明书
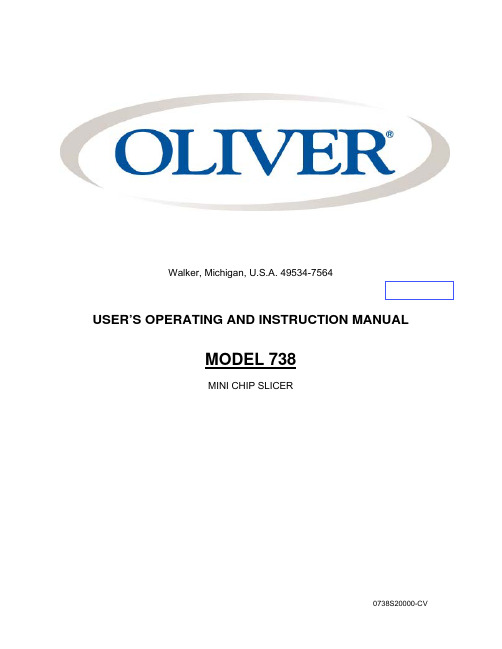
Walker, Michigan, U.S.A. 49534-7564USER’S OPERATING AND INSTRUCTION MANUALMODEL 738MINI CHIP SLICER0738S20000-CVINDEXSection Description Document No.Page No.SAFETY INSTRUCTIONS -------------------------------------- 0738S20002 --------------------------- 1-1 DESCRIPTION/SPECIFICATIONS --------------------------- 0738S20016---------------------------- 2-1 INSTALLATION INSTRUCTIONS ---------------------------- 0738S20004 --------------------------- 3-1 OPERATING INSTRUCTIONS -------------------------------- 0738S20017 --------------------------- 4-1 TROUBLESHOOTING ------------------------------------------- 0758S20006 --------------------------- 5-1 CLEANING AND MAINTENANCE -----------------------------0758S20018 --------------------------- 6-1 Removing the Blade Cartridge------------------------------------------------------------------------- 6-16-4Cleaning---------------------------------------------------------------------------------------------------- Replacing the Blade Frames --------------------------------------------------------------------------- 6-5Changing the Blades ------------------------------------------------------------------------------------- 6-7 ------------------------------------------------------------------------------------------------- 6-8LubricationGeneral Cleaning ------------------------------------------------------------------------------------------ 6-8 REPLACEMENT PARTS SECTIONMAIN FRAME ------------------------------------------------------ 0758S20019 --------------------------- 7-17-2 Drawing------------------------------------------------------------------------------------------------- ELECTRICAL--------------------------------------------------------0758S20020 --------------------------- 8-18-1 -------------------------------------------------------------------------------------------------DrawingParts List ------------------------------------------------------------------------------------------------8-2 DRIVE COMPONENTS-------------------------------------------0758S20021 --------------------------- 9-1 SLICE PARTS/COVERS -----------------------------------------0758S20022---------------------------10-110-1 Drawing----------------------------------------------------------------------------------------------- Parts List ---------------------------------------------------------------------------------------------- 10-2 WIRING DIAGRAM 1-60-120----------------------------------- 0738S20013 -------------------------- 12-1 WARRANTY ------------------------------------------------------- GEN 040225WARRANTY PROCEDURE------------------------------------ GEN 040226RETURNED PARTS POLICY --------------------------------- GEN 040227THIS PAGE WAS INTENTIONALLYLEFT BLANK.SAFETY INSTRUCTIONSWARNINGVARIOUS SAFETY DEVICES AND METHODS OF GUARDING HAVE BEEN PROVIDED ON THIS MACHINE. IT IS ESSENTIAL HOWEVER THAT THE MACHINE OPERATORS AND MAINTENANCE PERSONNEL OBSERVE THE FOLLOWING SAFETY PRECAUTIONS. IMPROPER INSTALLATION, MAINTENANCE, OR OPERATION OF THIS EQUIPMENT COULD CAUSE SERIOUS INJURY OR DEATH.1. Read this manual before attempting to operate your machine. Never allow anuntrained person to operate or service this machine.2. Connect the machine to a properly grounded electrical supply that matches therequirements shown on the electrical specification plate and follow all specifications of local electrical codes.3. Disconnect and lock-out the machine from the power supply before cleaning orservicing.4. Check and secure all guards before starting the machine.5. Observe all caution and warning labels affixed to the machine.6. Use only proper replacement parts.7. Do not wear loose fitting clothing or loose hair when working near this machine.Shirt tails should be tucked in.8. Wear proper, personal, protective, safety equipment.9. Keep Hands away from the moving parts of this machine while it is in operation.10. In addition to these general safety instructions, please follow the more specific safetyinstructions as specified in the operating instruction manual.11. The on/off switch is marked with international symbols for on and off. See below.ON OFFDESCRIPTION/SPECIFICATIONSDescriptionThe Model 738 Mini Chip Slicer is a compact, countertop slicer designed to reprocess shrink - specifically bagels and baguettes - into a marketable bakery/foodservice product. Designed with reciprocating blade technology, the Mini Chip Slicer easily slices through day-old bagels and baguettes.The Model 738 Mini Chip Slicer is constructed of stainless and painted steel. Easy to clean, the Mini Chip Slicer food contact surfaces - infeed cover, pusher, handle, and blade cartridge - can be removed without the use of tools for cleaning and sanitizing in a dishwasher. Blade changes are simple: simply remove the blade cartridge, replacing it with an OEM cartridge. No tools or service company required.SpecificationsSpace Requirements:Model 738 (All Dimensions are Approximate)Product Capacities:Length 6 inchesWidth 6 inches2inchesHeightStandard Electrical Options: (Others consult factory)1 phase, 60 Hz, 120VAC,2 Amps.Shipping Weight:100 lbs. (approximate)Net Weight:80 lbs. (approximate)INSTALLATION INSTRUCTIONSBefore starting the Installation process make sure you observe the following caution notes.CAUTIONTHE SLICER IS HEAVY, USE PROPER TECHNIQUE WHEN LIFTING OR MOVING. Select a location for your slicer which has a substantial mounting surface and which has electrical service compatible with the load the machine will place on it as indicated on the electrical data plate of the machine. Position the machine while it is still in its packaging as close as possible to the desired end location.OPERATING INSTRUCTIONSWARNINGALWAYS USE CARE WHENEVER WORKING NEAR THE CUTTING KNIVES. To operate the slicer, follow these simple steps:1. Power unit on and lift the handle. The unit will automatically shut off.2. Place the product atop the blades towards the front of the cutting area.3. Using the handle, apply slight pressure in a downward motion until the handlecomes to a stop. Repeat steps 1-3.4. When finished, power the unit off.NOTETHE UNIT WILL CONTIUE TO RUN UNLESS THE HANDLE IS LIFTED TO THE STARTING POSITION. PLEASE REMEMBER TO POWER OFF THE UNIT WHENSLICING IS COMPLETE.STEP 1 STEP 2 STEP 3THIS PAGE WAS INTENTIONALLYLEFT BLANK.TROUBLE SHOOTINGWARNINGALWAYS DISCONNECT THE SLICER FROM THE POWER SUPPLY BEFORE ATTEMPTING ANY TYPE OF MAINTENANCE TASK, INCLUDINGTROUBLESHOOTING.Slicer will not start•The machine is not plugged in.•There is no power at the outlet.•The cover is not on correctly. The cover has an interlocking mechanism that allows the unit to operate only if the cover is on.•Broken wire or disconnected terminals.•The switch actuator cam is not contacting the switch. Lift the cover and adjust the screw with a flat head screw driver.Pusher interference when slicing product•Loosen pusher and adjust side to side to make sure there is no interference.•Blade frame is not correctly placed on slide blocks.•Pusher blades are bent or damaged. Contact dealer or factory.Extreme effort needed to slice product•Blades are dull. Contact dealer or factory for replacements.•Product is too stale or old. The slicer is designed to be most efficient with slicing fresh or day old product.CLEANING AND MAINTENANCEWARNINGALWAYS UNPLUG THE SLICER BEFORE PERFORMINGANY TYPE OF MAINTENANCE TASK.To prepare your unit for cleaning please refer to the pictorial below for step by step instructions.REMOVING THE BLADE CARTRIDGE1. Loosen the (2) two thumb screws on the outside of the machine, tip the coverassembly back as shown in figure A. Lift the cover props on each side of the frame securely hold the cover open as shown in figure B.Figure AFigure B2. Loosen and remove the (4) thumbscrews atop the post hold down blocks (Fig. A)and adjust the drive assembly so that the blade frame cartridge is in the closedposition as shown below (Fig. B). This is done by turning the knob on the driveassembly so that the channels on the blade frames are close together.NOTE: The protective blade cover will only fit on the cartridge when it is in the closed configuration. This helps with the cleaning and re-assembly processes.Figure AFigure BCAUTIONUSE CAUTION WHILE ADJUSTING THE DRIVE ASSEMBLY. THE BLADES AREEXPOSED AND VERY SHARP.3. Place the protective blade cover atop the blade cartridge by hooking the coveraround the pin plate near the drive assembly.4. Lay the cover down on top of the blade cartridge and fasten with the thumbscrew to the blade cartridge by threading the thumb screw into the hole provided.5. To remove the protected blade frame cartridge simply grip the front of theassembly and the tab provided on the cover and pull up.WARNINGNEVER REMOVE BLADE FRAME ASSEMBLY WITHOUT PROTECTIVE GUARD.BLADES ARE EXTREMELY SHARP AND IF HANDLED INCORRECTLY MAYRESULT IN SERIOUS INJURY.CLEANINGNow that the blade frames have been safely removed you can now proceed with removing any crumb deposits within the machine. A brush, compressed air, or a vacuum are helpful tools for this task.REPLACING THE BLADE CARTRIDGE6. Make sure that the drive assembly is in the correct position as shown below. NOTE: The blade cartridge will only fit back into the machine with the drive assembly in the correct configuration below. The Bearing holes need to be at the position nearest each other.CORRECTINCORRECT7. With the protective blade guard in place locate the center of the bearings in thedrive assembly with the pin plates attached to the blade cartridge.8. Once the drive assembly has been located, place the blade cartridge posts in thetracks on the base assembly. Apply slight pressure to the front and rear of theblade cartridge to ensure the proper fit in to the drive assembly and slide blocks.You can now replace the post hold down blocks that you set aside in step 5.9. Remove the protective blade cover by loosening the thumb screw and unhookingfrom the pin plate.NOTE: The cover assembly will not fit on the unit if the protective blade cover is left in place.10. Lower the cover assembly by placing one hand on the front of the cover andplacing both of the cover props in their closed position. Gently lower the coverassembly until it stops.11. Lastly, after the cover has been lowered into position firmly tighten all thumbscrews around the perimeter of the unit.CHANGING THE BLADESOliver Packaging and Equipment suggests that blades not be changed in the field due to the potential for injury. We offer a blade frame cartridge exchange program for when blades become dull. Please contact your dealer or the Oliver service department.LUBRICATIONWARNINGALWAYS DISCONNECT THE SLICER FROM THE POWER SUPPLY BEFORE ATTEMPTING ANY TYPE OF MAINTENANCE TASK.Oliver suggests a vegetable based aerosol product be used to gently coat the blades on occasion. Once a month put a drop of a food approved lubricant on the plastic slide blocks on the inside of the unit. This will increase the longevity of the internal parts of your slicer.NOTENEVER OIL OR GREASE THE MOTOR.GENERAL CLEANINGUse a mild detergent solution to clean the exterior surfaces. Periodically remove all covers and brush or blow, (if compressed air is available), all foreign material from all surfaces, especially moving parts.MAIN FRAMEMAIN FRAME PARTS LISTITEM NO PART DESCRIPTION PART NUMBER 001 Base 0738-0002-1 002 Grommet-Rubber 5767-1207 003* Nut-10-24 Stainless Acorn 5832-0585004* Washer-#10 Spring Lock Stainless 5851-9355005 Bumper-Rubber w/ Screw 5902-0035006 Block-Guide 0738-0003-1 007 Screw-10-24 x 3/8 Stainless Truss 5843-5384008 Bracket-RH Cover Attachment 0738-0004-0001 009* Bracket-LH Cover Attachment 0738-0004-0002 010 Screw-10-24 x 1/4 Stainless Truss 5843-5383011 Plate-Prop 0738-0005-1 012 Nut-1/4-20 Stainless Locking 5831-9087013 Washer-1/4 Flat Stainless 5851-9304*Items not shownELECTRICAL PARTSELECTRICAL PARTS LISTITEM NO PART DESCRIPTION PART NUMBER 101 Assembly-Motor Cord 0738-25505K 102 Plate-Motor Mount 0738-0045103 Spacer 0738-0046 106 Screw-5/16-18 x ¾ Stainless Hex 5843-1028107 Screw-5/16-18 x 3 1/2 Stainless Hex 5843-1039108 Screw-8-32 x 5/16 Stainless Pan 5843-5552109 Washer-#8 Shake Proof Stainless 5851-9130110 Washer-5/16 Lock Stainless 5851-9358111 Mount-Switch 0738-0008 112 Screw-8-32 x ¼ Stainless Pan 5843-5551113 Washer-#8 Flat Stainless 5851-8108114 Switch-SM Basic w/ Roller 5757-8002115 Screw-4-40 x 1/2 Stainless Pan 5843-5524116 Washer-#4 Shake Proof Stainless 5851-9127117 Switch-SM Basic 5757-8001 122 Block-Terminal 8 Row 5770-7451131 Strip-Marker 8 Row 5770-7328133 Screw-M3.5 x 16mm Stainless Pan 8843-2265134 Relay 5749-8027135 Switch-Rocker 5757-3314 136 Bushing-Strain Relief 90° 5765-1010137 Nut-PG-11 Plastic Lock 5766-7786 138 Counter-5 Digit Mini 5712-9080139 Screw-6-32 x 1/4 Stainless Truss 5843-5360140 Screw-6-32 x 3/8 Green Grounding 5841-9501142 Washer-#6 Shake Proof Stainless 5851-9129FOR SERVICE PARTS CALL OLIVER PACKAGING & EQUIPMENT @ 800-253-3893THIS PAGE WAS INTENTIONALLYLEFT BLANK.DRIVE COMPONENTSDRIVE COMPONENTS PARTS LISTITEM NO PART DESCRIPTION PART NUMBER 200* Assembly-Drive 0738-25012K 206 Clip-Bearing 0738-0049 207 Bearing-10mm Spherical Flange Mount 5251-3591208 Screw-10-24 x 3/8 Stainless Pan 5843-5384209 Screw-6-32 x 1/4 Stainless Pan 5843-5541210 Washer-#6 Lock Stainless 5851-9353212 Knob 0738-0051 213 Screw-6-32 x 1 ¼ Stainless Pan 5843-5547 Replacements for 200 are ordered assembled with fasteners. Parts may not be substituted within the assembly other than those called out.FOR SERVICE PARTS CALL OLIVER PACKAGING & EQUIPMENT @ 800-253-3893SLICE PARTS/COVERSREV 4-28-15SLICE PARTS/COVERS PARTS LISTITEM NO PART DESCRIPTION PART NUMBER 301 Cartridge-Blade Frame 0738-25XXXK 302 Assembly-Pusher 0738-25XXXK 303 Cover-Blade Frame Safety 0738-0024K 401 Cover-Motor 0738-0033-1 402 Screw-10-24 x 3/8 Stainless Truss 5843-5384403 Washer-#10 Shake Proof Stainless 5851-9394404 Cover-Base 0738-0034-1 406 Knob-1/4-20 4 Prong Plastic 5911-7034407 Block-Top Guide 0738-0052408 Screw-8-32 x 1 Stainless Thumb 0738-25504K 411 Handle Assembly 0738-25037K 413 Block-Handle Hinge 0738-0040414 Screw-10-24 x 3/8 Stainless Truss 5843-5384415 Plate-Pusher Centering 0738-0041416 Screw-10-32 x 1/4 Stainless Truss 5843-5390417 Washer-#10 Fender Stainless 5851-9324418 Plate-LH Cover Cam 0738-0042-0002 419 Plate-RH Cover Cam 0738-0042-0001 420 Screw-8-32 x 1/4 Stainless Round 5843-5232422 Washer-#8 Spring Lock Stainless 5851-9354423 Bumper-Press In 5902-0023*Items 301 and 302 are replaced fully assembled. Specify slice thickness when ordering.**Item 303 is provided with each blade frame assembly and is used for safe handling. Not Shown.FOR SERVICE PARTS CALL OLIVER PACKAGING & EQUIPMENT @ 800-253-3893REV 1-26-18WARRANTYPARTSOliver Packaging & Equipment Company warrants that if any part of the equipment (other than a part not manufactured by Oliver Packaging & Equipment ) proves to be defective (as defined below) within one year after shipment, and if Buyer returns the defective part to Oliver Packaging & Equipment within one year, Freight Prepaid to Oliver Packaging & Equipment plant in Grand Rapids, MI, then Oliver Packaging & Equipment , shall, at Oliver Packaging & Equipment option, either repair or replace the defective part, at Oliver Packaging & Equipment expense.LABOROliver further warrants that equipment properly installed in accordance with our special instructions, which proves to be defective in material or workmanship under normal use within one (1) year from installation or one (1) year and three (3) months from actual shipment date, whichever date comes first, will be repaired by Oliver Packaging & Equipment or an Oliver Packaging & Equipment Authorized Service Dealer, in accordance with Oliver Packaging & Equipment published Service Schedule.For purposes of this warranty, a defective part or defective equipment is a part or equipment which is found by Oliver Packaging & Equipment to have been defective in materials workmanship, if the defect materially impairs the value of the equipment to Buyer. Oliver Packaging & Equipment has no obligation as to parts or components not manufactured by Oliver Packaging & Equipment, but Oliver Packaging & Equipment assigns to Buyer any warranties made to Oliver Packaging & Equipment by the manufacturer thereof.This warranty does not apply to:1. Damage caused by shipping or accident.2. Damage resulting from improper installation or alteration.3. Equipment misused, abused, altered, not maintained on a regular basis, operated carelessly, orused in abnormal conditions.4. Equipment used in conjunction with products of other manufacturers unless such use is approvedby Oliver Packaging & Equipment Company in writing.5. Periodic maintenance of equipment, including but not limited to lubrication, replacement of wearitems, and other adjustments required due to installation, set up, or normal wear.6. Losses or damage resulting from malfunction.The foregoing warranty is in lieu of all other warranties expressed or implied AND OLIVER PACKAGING & EQUIPMENT COMPANY MAKES NO WARRANTY OF MERCHANTABILITY OR FITNESS FOR PURPOSE REGARDING THE EQUIPMENT COVERED BY THIS WARRANTY. Oliver Packaging & Equipment Company neither assumes nor authorizes any person to assume for it any other obligations or liability in connection with said equipment. OLIVER PACKAGING & EQUIPMENT COMPANY SHALL NOT BE LIABLE FOR LOSS OF TIME, INCONVENIENCE, COMMERCIAL LOSS, INCIDENTAL OR CONSEQUENTIAL DAMAGES.WARRANTY PROCEDURE1. If a problem should occur, either the dealer or the end user must contact the Parts andService Department and explain the problem.2. The Parts and Service Manager will determine if the warranty will apply to this particularproblem.3. If the Parts and Service Manager approves, a Work Authorization Number will begenerated, and the appropriate service agency will perform the service.4. The service dealer will then complete an invoice and send it to the Parts and ServiceDepartment at Oliver Packaging & Equipment Company.5. The Parts and Service Manager of Oliver Packaging and Equipment Company willreview the invoice and returned parts, if applicable, and approve for payment.RETURNED PARTS POLICYThis policy applies to all parts returned to the factory whether for warranted credit, replacement, repair or re-stocking.Oliver Packaging and Equipment Company requires that the customer obtain a Return Material Authorization (RMA) number before returning any part. This number should appear on the shipping label and inside the shipping carton as well. All parts are to be returned prepaid. Following this procedure will insure prompt handling of all returned parts.To obtain an RMA number contact the Repair Parts Deptartment toll free at (800) 253-3893. Parts returned for re-stocking are subject to a RE-STOCKING CHARGE.Thank you for your cooperation,Repair Parts ManagerOliver Packaging and Equipment Company。
VERIPOS LD7 快速指南说明书

VOSS : AB-V-MA-00560 Rev A8Reference card for use day to day, to print and use.1. Latch Power Button2. Status LEDs3. Main Antenna Connector4. Aux Antenna Connector5. 1 PPS /Event Connector6. Com 1 Connector7. Power Connector8. Ethernet / USB Connector9. Com2 / Com3 Connector 10.Com4 / Com5 ConnectorCables and adaptors suppliedAntennasSee LD7 Installation manual for more information.Connecting LD7Connect the LD7 making connections as shown in the typical example installation below.When installing the Lemo connectors ensure the red dot on the plug and red mark on the socket line upInitial start-upPress the power switch on the front panel. Allow the unit approximately 120 seconds to start up.Use a Windows 7 or XP PC with browser software (preferably Google Chrome version 30.0.1559.101 or above)Amend the IP address of the PC to a compatible address for the LD7. The default fixed IP address of the LD7 is 192.168.0.126.Connect the LD7 RJ45 lead via an Ethernet hub or directly to the PC. On the PC, open internet browser and enter the default LD7 IP address, 192.168.0.126Enter the unique LD7 User code on front of LD7 unit and press OK. Once connected the main browser page is shown:LD7 Main browser page – default / recommended settings shownBeam selectionOn the LBand page select a V eripos correction satellite beam for yourVOSS : AB-V-MA-00560 Rev A8vessel work area from the drop down options and click Apply:Upon lock to the selected beam the SyncLED should be green.In most locations, more than one beam will be available. Different beams carry corrections for different reference stations. A beam should be selected which has the highest elevations and reference stations mostsuited to the work area.Enabling the LD7 for Veripos ServicesContact the Veripos Helpdesk to request a service enable quoting your Unit ID, Service Access Licence (SAL) number and listingservices required e.g. Veripos Ultra with Standard.Download a Service Notification Form from and use this when contacting the Veripos Helpdesk for an enable.Tel. +44 1224 965900 email:********************The sync indicator must be green in order for the Access code to bereceived.When the unit is enabled the ENBLED should be GreenConfiguring data outputs from the LD7Position and heading data (NMEAa or NMEAb) can be output onCom ports 1 or 2 or via LAN from the LD7.On the Web Browser go to the GNSS Tab and set the NMEAMessages required for output.For serial output, go to the LD7 I/O page and select the data streamsand baud rate required for Com ports 1 and 2.Configuring data outputs from the LD7 (LAN)Position and heading data (NMEAa or NMEAb) is also available foroutput via LAN.To output NMEA messages from the LD7, the IP address of the GNSS receiver should be used. Note that this is different from the IP addressLD7 with Verify QC – LAN outputsConfigure the Verify QC PC network settings to an applicable IP address and Subnet Mask for use with the LD7 (Control Panel/Network Connections).The LD7 processor, GNSS and LBand receivers all have separate IP addresses. Take into account when setting an IP address on the PC. To determine or set the LD7, LBand and GNSS Rx IP Addresses use the LD7 Web Browser.Configure Verify QC inputs for Client Sockets with the following IP Address and LAN ports;LD7 with Verify QC - Serial Port outputsYou can view or amend baud rates, etc. by going to LD7 IO page in the Web Interface.Baud Rates are user configurable. As a result users should check the Baud Rate Settings using the LD7 Web Interface (see Configuring data outputs section of this quick guide).。
- 1、下载文档前请自行甄别文档内容的完整性,平台不提供额外的编辑、内容补充、找答案等附加服务。
- 2、"仅部分预览"的文档,不可在线预览部分如存在完整性等问题,可反馈申请退款(可完整预览的文档不适用该条件!)。
- 3、如文档侵犯您的权益,请联系客服反馈,我们会尽快为您处理(人工客服工作时间:9:00-18:30)。
广州市联承通电子科技有限公司微码器使用手册目录第一章:产品介绍 (2)第一节微码器功能 (2)第二节商品内容 (2)第三节产品图片 (2)第四节脚位图 (3)第二章商家使用步骤指导 (3)第一步开通后台账户 (3)第二步设备绑定 (3)第三步后台添加商品 (3)第四步绑定收款账号 (5)第五步安装设备 (5)第六步WIFI配置(GPRS版不需要配置WIFI,即插即用) (6)第七步操作学习模式 (7)第八步使用设备 (7)第三章:收款账号绑定(多选一) (8)第一节绑定个人微信钱包 (8)绑定方式: (8)到账说明: (10)到账显示示例图: (10)到账个人微信钱包并强制关注公众号 (10)第二节绑定微信公众号 (11)第三节绑定企业支付宝 (12)第四章:后台系统操作说明 (13)第一节登录后台步骤 (13)第二节提现申请 (14)第三节查询订单 (14)第四节重启设备 (14)第五节生成二维码图片 (14)第六节浏览商品 (14)第七节停用设备 (14)第八节手动派币 (15)第九节设备分类管理 (15)第十节启用立即支付(不需要选支付方式) (16)第十一节设置前端支付按钮 (16)第十二节移动设备到其他商家账号(代理账户权限) (17)第十三节启用首单免费 (17)第十四节设置售后电话 (19)第十五节会员卡管理 (19)附录 (22)获取微信公众号资料操作流程 (22)获取企业支付宝资料操作流程 (26)第一章:产品介绍第一节微码器功能微码器是一款新型投币产品,是能够帮助您的机器实现微信、支付宝扫描二维码付款的产品,比传统投币器更简单,便捷,快速。
本产品适用于所有自助投币设备且不需要做任何改造,配套免费后台管理系统,实现有表可查、有帐可对的高效管理。
第二节商品内容1.设备主体2.天线3.投币器转接线4.二维码贴纸5.退奖线两条(部分需要记录退奖的用户)第三节产品图片第四节脚位图第二章商家使用步骤指导第一步开通后台账户由本公司直接为您开通后台账号,如未拿到账号和密码,请联系本公司人员索取第二步设备绑定在本公司购买产品后,我们将会把设备移到您的账号底下,如果后台没有显示此次购买的微码器编号,请联系本公司人员把设备移到您的账号底下第三步后台添加商品首先登陆电脑版系统后台(登陆步骤请参考第四章第一节),在「商品管理」—「商品添加」—填写标题等信息—提交(添加商品分两步,请操作完)如下图:然后到「设备管理」—「批量设置商品」—选择需要添加商品的设备(左方)—选择要添加的商品(右方)—点击「设定—商品列表」注:如果需要设置优惠套餐,如:10元11个币(赠送一个),在添加商品时填写方式如下:第四步绑定收款账号请参照第三章“收款账户绑定”的操作提示绑定收款账户(多选一)(不绑定默认由本公司代收,需要到系统后台申请提现,满500元才能申请,申请提现方式请参考第四章第二节)第五步安装设备第六步WIFI配置(GPRS版不需要配置WIFI,即插即用)1、把微码器SW1 开关第2 位拨下来2、将手机网络连接到场地中投币器欲使用的网络3、然后登陆微信,关注本公司微信公众号“素环珍”,点击进入公众号,点击“微码器”然后选择“配置WIFI”,点击“配置微码器WIFI“,输入WIFI 密码,点击“连接”4、出现下面的页面时表示WIFI 配置成功,请将开关复位第七步操作学习模式传统投币器接J1,通电后,开关SW1-1拨下,用传统投币器投放1-20个币,微码器会自动记录投币参数,学习完成后,将开关SW1-1拨回上方,退出学习模式注:已经投入使用的微码器,如果出现出币不准的情况,可以通过操作此学习模式来改善第八步使用设备第三章:收款账号绑定(多选一)第一节绑定个人微信钱包绑定方式:注:绑定个人微信账户后不需要另外再绑定微信公众号和支付宝(多选一)到账说明:1、到账个人微信账户开通后,微信支付宝款项10分钟到账一次,满2元才转;2、款项直接进入绑定的个人微信钱包(微信—我—钱包—零钱)3、微信非实名用户单日限额2,000元(实名用户20,000元)4、到账个人微信账户手续费为千分之八到账显示示例图:在微信首页会有消息提醒,在“微信支付”里面(10分钟转一次,满2元才转)如下图到账个人微信钱包并强制关注公众号在绑定到账个人微信钱包后,登陆电脑版后台,点击“收款账号”——“微信设置后的编辑“填写资料,点击后面的”保存“按钮,选择你需要顾客关注的公众号,点击”启用“按钮,最多可以添加10个公众号,不建议全部启用,会影响用户体验(获取资料的方式步骤在本操作指南的附录页;此处的”标签“主要用于当您的公众号比较多时进行分类帮助您记忆,不会在其他地方显示)如图:第二节绑定微信公众号1.绑定需要的资料:(获取资料的方法流程请参考本操作指南的附录页)资料:①应用ID②应用密钥③微信支付商户号④ API密钥⑤ API证书密钥⑥公众号原始ID文件:① API证书:cert.zip2.绑定方式:登陆PC端后台—「基本设置」—「收款账号」找到“微信公众号设置”点击“编辑”把资料填写进去,选择“启用”—提交(需要顾客关注您的公众号时,请勾选“强制关注”中的“是”,勾选后顾客扫描二维码会出现弹出一个关注公众号的页面,顾客需要关注后才能购买商品)注:1、绑定微信公众号后需要另外再绑定企业支付宝账户,否则顾客通过支付宝付的款将默认由本公司先代收;不需要另外再绑定个人微信钱包(多选一)2、绑定的公众号需要是能收款的服务号,并且已通过微信认证第三节绑定企业支付宝1.绑定需要的资料:获取资料的方法流程请参考本操作指南的附录页①合作身份者ID:合作身份者ID(partner)。
②商户的私钥:RSA加密,密钥。
③支付宝的公钥:RSA加密,支付宝公钥。
2.绑定方式:登陆PC端后台—「基本设置」—「收款账号」找到“支付宝设置”点击“编辑”把资料填写进去,选择“启用”—提交注:1、绑定企业支付宝后需要另外再绑定企业微信公众号,否则顾客通过微信付的款将默认由本公司先代收;不需要另外再绑定个人微信账户2、如果没有公司的支付宝账号时,可以选择让通过微信支付的款到微信公众号里面,通过支付宝付的款就到个人微信钱包里面,即分开到账(设置方式:在PC端的「收款账号」里面的“支付宝”选项选择不启用,然后开通到账个人微信钱包(开通办法请参考本操作指南中的“绑定个人微信账户”的步骤操作))第四章:后台系统操作说明第一节登录后台步骤电脑登陆:打开本公司官网()点击「登录」—「商家」输入账号,密码手机登陆:关注本公司微信公众号“素环珍”—进入公众号—「微码器」—「商家后台」—输入账号密码—登陆第二节提现申请点击「提现列表」—“申请提现”—提交—代理审核—财务核对收款账号以及联系方式—财务转账第三节查询订单「订单管理」—「订单列表」在下单时间栏选择需要查询的时间或者输入订单号等即可查询到相应的订单,点击相应订单右边的「详情」即可查询到该订单的详细信息第四节重启设备「设备管理」—「设备列表」找到需要重启的设备编号—点击「重启设备」第五节生成二维码图片「设备管理」—「设备列表」找到需要生成的设备编号—点击「点击生成」第六节浏览商品「设备管理」—「设备列表」找到需要浏览的设备编号—点击「浏览商品」第七节停用设备「设备管理」—「设备列表」找到需要停用的设备编号—点击「设备停用」第八节手动派币「设备管理」—「设备派币」—选择设备—填写派币数量—提交第九节设备分类管理「设备管理」—「设备列表」—选择设备—点击编辑在“标签”处填上类别名称分类后在「统计管理」—「运营统计」可以看到各分类设备的营业情况,点击后面的“设备清单”可以看到该分类的设备明细第十节启用立即支付(不需要选支付方式)「设备管理」—「设备列表」—找到您要设置的设备—点击设备名进入—在「资料配置」栏里面的「立即支付启用」里面勾选「是」如下图:注:当商品只有一个的时候,玩家扫描后将直接进入支付页面,不需要选择商品和支付方式;当商品数量为两个或以上的时候需要玩家先选择商品然后进去支付页面,用微信扫描的就用微信支付,用支付宝扫描的就用支付宝支付,不需要再选择支付方式第十一节设置前端支付按钮登陆电脑版系统后台—点击「个人资料」——勾选支付方式——提交第十二节移动设备到其他商家账号(代理账户权限)登陆电脑版系统后台—登陆代理账号—「设备管理」—「设备列表」—输入设备编号—查询—勾选设备编号—选择商家账号—移动(此处的商家账号必须要是由这个代理开出来的账号,如果这个商家不属于这个代理账号底下的商家,设备将不能移动,只能通过总管理后台移动)第十三节启用首单免费「商品管理」—「添加商品」—添加一个首单免费的商品,在“首次免单”处勾选“是”(注:首单免费是针对公众号而言,一个微信号在这个公众号消费过一次后,首单免费会自动失效,再次扫描时“首单免费”这个商品不再显示;没有绑定公众号的默认为本公司公众号)第十四节设置售后电话顾客扫描二维码出现的界面显示商家的售后服务电话登陆电脑后台——「个人资料」处在“服务电话”中填写如售后服务电话保存即可第十五节会员卡管理会员卡说明:会员卡是一张虚拟的卡,用户充值的钱可以在任何时候在此商家底下的所有设备上消费,使用会员卡上面的钱消费不需要再次输入付款密码,使用更便捷商家设置:登陆电脑版后台——找到”收款账号“——点击”钱包支付“后面的编辑按钮(当没有”钱包支付“这个选项时请联系我们给您开放权限)填写充值赠送金额,然后勾选启用——提交用户操作说明:1、充值:扫描机台二维码,点击商品界面左下角的”会员卡“,进入充值页面,填写充值金额;(可在”会员卡使用记录“处查询使用记录)2、使用:扫描机台二维码——选择商品套餐——选择”会员卡支付“即可附录获取微信公众号资料操作流程操作流程(请依照以下教程进行设置,教程中下划线部分为需要提交的资料,请记下)登入微信公众平台(https:///)点击左方菜单「微信支付」点击上方菜单「开发配置」,把「支付授权目录」设置为:点击右上方「公众号设置」点击上方菜单「功能设置」,设置「JS接口安全域名」:点击右方菜单「公众号设置」点击右方菜单「开发者中心」配置项—开发者ID点击「完整显示」取得完整密钥!下方「接口权限表」修改「网页服务—网页账户—网页授权获取用户基本信息」设置授权回调页面域名:登入商户平台—https:///微信支付商户号:127*****(例子)点击右方「账户设置」中的「API安全」「下载证书」,并保存档案cert.zip获取企业支付宝资料操作流程登入商家服务(支付宝商家服务中心:https://)获取“合作身份者ID”如何查询它们需要通过以下操作:第一步:登陆支付宝官方网站()。