七大浪费分析与改善培训PPT.
合集下载
如何消除七大浪费PPT课件
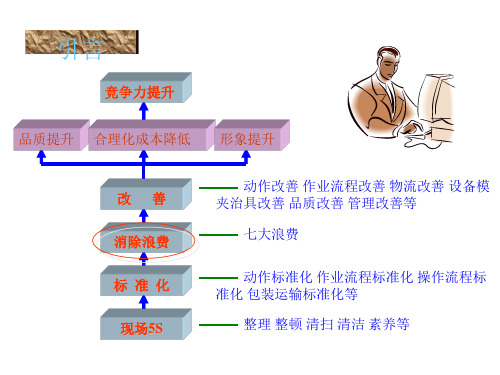
表现形式:
•自动机器操作中;人员的闲视等待 •作业充实度不够的等待 •设备故障 材料不良的等待 •生产安排不当的人员等待 •上下工程间未衍接好造成的工程间的等待
对策:
2 等待的浪费
原因:
•生产线布置不当;物流混乱 •设备配置 保养不当 •生产计划安排不当 •工序生产能力不平衡 •材料未及时到位 •管理控制点数过多 •品质不良
材料不良 加工不良 检查 市场不良 整修工件等
表现形式:
•因作业不熟练所造成的不良 •因不良而修整时所造成的浪费 •因不良造成人员及工程增多的浪费 •材料费增加
7 做出不良的浪费
原因:
•标准作业欠缺 •过分要求品质 •人员技能欠缺 •品质控制点设定错误 •认为可整修而做出不良 •检查方法 基准等不完备 •设备 模夹治具造成的不良
Ⅳ;生产动作研究
动作经济原则共二十二项并归纳为下列三大类
1;关于人体之运用: 2;关于操作场所布置: 3;关于工具设备:
1 关于人体之运用:
1双手应同时开始并同时完成其动作 2除规定时间外;双手不应同时空闲 3双臂的动作应对称;同一方向并同时作业 4手的动作幅度最小并且能得到满意结 果最为妥当
5物体的动量应尽可能利用;但如需用手制止时;应尽可能 用最小的力
对策:
•工程设计适正化 •作业内容的修正 •治具改善及自动化 •标准作业的贯彻 •VA/VE的推进 •设计FMEA的确实推进
注意:
•了解同行的技术发展 •各部门对于改善的共同 参与及持续不断的改善
5 库存的浪费
不良所造成的库存;半成品所造成的 库存;制造过多所造成的库存
材料 零件 组合件等物品的停滞状态;包 括库存及在制品
表现形式:
•不良品存在库房内待修
•自动机器操作中;人员的闲视等待 •作业充实度不够的等待 •设备故障 材料不良的等待 •生产安排不当的人员等待 •上下工程间未衍接好造成的工程间的等待
对策:
2 等待的浪费
原因:
•生产线布置不当;物流混乱 •设备配置 保养不当 •生产计划安排不当 •工序生产能力不平衡 •材料未及时到位 •管理控制点数过多 •品质不良
材料不良 加工不良 检查 市场不良 整修工件等
表现形式:
•因作业不熟练所造成的不良 •因不良而修整时所造成的浪费 •因不良造成人员及工程增多的浪费 •材料费增加
7 做出不良的浪费
原因:
•标准作业欠缺 •过分要求品质 •人员技能欠缺 •品质控制点设定错误 •认为可整修而做出不良 •检查方法 基准等不完备 •设备 模夹治具造成的不良
Ⅳ;生产动作研究
动作经济原则共二十二项并归纳为下列三大类
1;关于人体之运用: 2;关于操作场所布置: 3;关于工具设备:
1 关于人体之运用:
1双手应同时开始并同时完成其动作 2除规定时间外;双手不应同时空闲 3双臂的动作应对称;同一方向并同时作业 4手的动作幅度最小并且能得到满意结 果最为妥当
5物体的动量应尽可能利用;但如需用手制止时;应尽可能 用最小的力
对策:
•工程设计适正化 •作业内容的修正 •治具改善及自动化 •标准作业的贯彻 •VA/VE的推进 •设计FMEA的确实推进
注意:
•了解同行的技术发展 •各部门对于改善的共同 参与及持续不断的改善
5 库存的浪费
不良所造成的库存;半成品所造成的 库存;制造过多所造成的库存
材料 零件 组合件等物品的停滞状态;包 括库存及在制品
表现形式:
•不良品存在库房内待修
七大浪费培训资料ppt课件

定义:存贮产品、材料、零组件等,所有的库存都是浪费 结果: 增加成本、占用资金、瑕疵品隐藏在成品里 掩饰无效率、停工时间过长、生产计划欠妥 员工操作不一致 例子: 过多的设备维修备品库存
你能想到其他的例子吗?
3
动作的浪费 经营者提供商品或者服务有欺诈行为的,应当按照消费者的要求增加赔偿其受到的损失,增加赔偿的金额为消费者购买商品的价款或接受服务的费用
浪费类型 搬运浪费
库存浪费
制造类型 在生产线周围推来推去的搬运车 动线愈长愈浪费
所有原料、零组件、在制品、半(成)品等皆是
非制造类型 文件须靠人力传送 实体文件会签传阅数个部门或人员 办公室动线规划不当或业务相关单位距离太远 寄卖在外的备用设备品 超过一个月或两星期需求的办公室文具用品(A4纸、笔、卫生纸、咖啡
认识浪费:
工厂的七大浪费
T = Transport I = Inventory M = Motion W = Waiting O = Over Production O = Over Processing D = Defects
库存 搬运
动作
MUDA 重工
等待
过 量
生
产
加工
附加价值的时间和工作 经营者提供商品或者服务有欺诈行为的,应当按照消费者的要求增加赔偿其受到的损失,增加赔偿的金额为消费者购买商品的价款或接受服务的费用 附加价值的时间与工作:只占5%
课程目的(Purposes) 经营者提供商品或者服务有欺诈行为的,应当按照消费者的要求增加赔偿其受到的损失,增加赔偿的金额为消费者购买商品的价款或接受服务的费用
➢认识七大浪费的基本概念 ➢找出工作中存在的七大浪费 ➢学习消除七大浪费的方法
课程目标 经营者提供商品或者服务有欺诈行为的,应当按照消费者的要求增加赔偿其受到的损失,增加赔偿的金额为消费者购买商品的价款或接受服务的费用
七大浪费ppt课件

安全第一无工伤 符合技术法规
快速应变 随时满足
精益生产给企业所带来的收益
• 通过精益生产可以实现(一般情况):
– 库存减少 75% – 生产制造周期时间缩减 90% – 生产效率提高 100% – 降低产品缺陷率 – 提高员工主观能动性积极性 – 公司安全管理零事故
一、精益生产概论 二、七大浪费介绍 三、改善提案管理概论
卖方 市场
高价格 少品种 大批量 低质量 长交期
买方 市场
低价格 多品种 少批量 高质量 短交期
按计划生产 大批量制造
精益生产 (紧密联系市场)
精益生产和大批量生产的对比
项目
大批量生产方式
P ( 品 种 ) 少品种
大批量
大批量生产
Q ( 质 量 ) 客户不投诉 不良不可避免
就行了
抽检为中心
C ( 成 本 ) 按成本定价 成本+计划利润
改善提案管理流程
开始
提出改善人填写 《改善提案申请表》
本部门评审 (车间或室)
非改 善提案
向建议提出人 反馈解释(3天内)
是改 善提案
本部门 组织实施
否 按《现场专题注册》申
(部门无法实施) 请专题注册立项
是
将《改善提案申请表》各
①
个部分内容填写完整
月底归口管理部门评 出奖励等级
录入公司OA 管理系统
定义:两个工序或过程不同步时产
生的停顿时间
等待浪费 DV
48
七大浪费解读-等待浪费
表现形式:
停工待料 设备故障 员工缺勤导致停工 计划调整 ……
49
七大浪费解读-等待浪费
等待浪费产生的原因:
零部件供应不及时
消除浪费七大浪费.ppt

17
搬运频繁或是长距离搬运,会增加搬运工与搬 运设备的负担,也会造成产品的损伤,没有充分利 用空间等缺失,结果导致劳动的产能下降。
18
动作的浪费:大抵意指作业人员动作不佳,所 产生的浪费。
※转向 ※反转 ※距离 ※寻找 ※堆叠 ※移动
19
动作的浪费:是 指作业员没有效 率的动作所引发 的浪费。
⑤ 库存的浪费:仓库资金费、搬运费、管理费、折 旧、损耗等库存管理费用,以及物品老化等导致 的损失。
7
⑥ 动作的浪费:步行、把物料或工具拿来却放 在一边、采用不自然的作业姿势,以及因判 断错误导致损失或采用四级、五级动作都计 为浪费等。
⑦ 制造不良的浪费:因员工操作疏忽所造成的 返工、物料原不良在加工时未发现所造成的 物料及人力的浪费。
22
有效消除浪费的方法
做好及时刚好(JIT) 做好目视管理与看板管理 做好5S管理 做好作业改善 做好设备改善 做好生产管理看板 做好一人多机的推行 做好生产线平衡
23
深入改善
工厂的标准化,必须订定许多的规定,例如根据作业 顺序的人员应该如何动作;仓库的材料零件应该如何摆 放,数量该有多少;工作量的指示;为了维护安全及环 境所必须遵守的事项等等。订出规定之后必须执行到底。 在工厂的管理方面,当发现没有按照既定规则的事物时 必须为异常再解决问题,并彻底实施这样的做法。
6
③ 搬运的浪费:超过不要程度的搬运距离、作业到 一半暂时放置、重复搬运、移动堆积物品、应一 次搬运分多次搬运、应使用栈板而未使用造成的 重复搬运、或者是流程布置不顺造成的搬运等。
④ 加工的浪费:作业本身不稳定,或作业人员本身 不熟悉,导致无法以最恰当的速度进行加工或应 一次加工而分成两次以上加工造成的损失。
搬运频繁或是长距离搬运,会增加搬运工与搬 运设备的负担,也会造成产品的损伤,没有充分利 用空间等缺失,结果导致劳动的产能下降。
18
动作的浪费:大抵意指作业人员动作不佳,所 产生的浪费。
※转向 ※反转 ※距离 ※寻找 ※堆叠 ※移动
19
动作的浪费:是 指作业员没有效 率的动作所引发 的浪费。
⑤ 库存的浪费:仓库资金费、搬运费、管理费、折 旧、损耗等库存管理费用,以及物品老化等导致 的损失。
7
⑥ 动作的浪费:步行、把物料或工具拿来却放 在一边、采用不自然的作业姿势,以及因判 断错误导致损失或采用四级、五级动作都计 为浪费等。
⑦ 制造不良的浪费:因员工操作疏忽所造成的 返工、物料原不良在加工时未发现所造成的 物料及人力的浪费。
22
有效消除浪费的方法
做好及时刚好(JIT) 做好目视管理与看板管理 做好5S管理 做好作业改善 做好设备改善 做好生产管理看板 做好一人多机的推行 做好生产线平衡
23
深入改善
工厂的标准化,必须订定许多的规定,例如根据作业 顺序的人员应该如何动作;仓库的材料零件应该如何摆 放,数量该有多少;工作量的指示;为了维护安全及环 境所必须遵守的事项等等。订出规定之后必须执行到底。 在工厂的管理方面,当发现没有按照既定规则的事物时 必须为异常再解决问题,并彻底实施这样的做法。
6
③ 搬运的浪费:超过不要程度的搬运距离、作业到 一半暂时放置、重复搬运、移动堆积物品、应一 次搬运分多次搬运、应使用栈板而未使用造成的 重复搬运、或者是流程布置不顺造成的搬运等。
④ 加工的浪费:作业本身不稳定,或作业人员本身 不熟悉,导致无法以最恰当的速度进行加工或应 一次加工而分成两次以上加工造成的损失。
消除生产现场七大浪费PPT课件

02
利用工业互联网技术实现设备联网、数据采集和分析,优化生
产过程和决策。
学习并借鉴先进企业的经验和技术
03
关注行业发展趋势,学习并借鉴国内外先进企业的经验和技术,
持续改进和优化生产过程。
建立有效的质量管理体系
1 2
制定严格的质量标准和检验流程
确保产品符合客户要求和行业标准,降低不良品 率和返工率。
消除生产现场七大浪费ppt课 件
• 引言 • 生产现场七大浪费 • 消除浪费的方法与策略 • 案例分析 • 结论
01
引言
浪费的定义与影响
浪费定义
在生产现场中,任何超出生产产 品所必需的、不能创造价值的活 动或因素。
浪费影响
降低生产效率、增加成本、降低 产品质量和竞争力。
生产现场浪费的普遍性
普遍存在于各种规模 和类型的企业中。
建立员工建议和改进机制, 鼓励员工提出改进意见, 提高员工的积极性和参与 度。
建立奖励制度
对在消除浪费和改进生产 过程中表现优秀的员工给 予奖励,激发员工的积极 性。
引入先进的生产技术
采用自动化和智能制造技术
01
通过引入自动化设备和智能制造系统,降低人工操作和错误率,
提高生产效率和质量。
应用工业互联网技术
加强质量意识培训
提高员工对质量的认识和重视程度,培养员工自 主质量管理的能力。
3
建立质量信息反馈机制
及时收集和分析质量信息,针对问题采取改进措 施,持续优化产品质量。
04
案例分析
企业A的精益生产实践
总结词:成功实施
详细描述:企业A通过实施精益生产,成功地减少了生产现场的浪费,提高了生 产效率和产品质量。他们在改进生产流程、优化生产线布局和加强员工培训方面 取得了显著成果。
生产中七大浪费PPT课件

总结词
动作浪费是指生产过程中工人的多余动作或 无效动作。
详细描述
动作浪费通常是由于操作流程设计不合理、 工具设备不适用、工人技能水平不足等原因 所导致的。为了减少动作浪费,企业需要对 操作流程进行优化设计,提供合适的工具和 设备,同时加强工人的技能培训和操作指导
,提高生产效率和质量。
制造不良品浪费
运输浪费
总结词
运输浪费是指产品在运输过程中所发生 的额外费用和时间消耗。
VS
详细描述
运输浪费通常是由于运输方式选择不当、 运输路线规划不合理、装卸作业效率低下 等原因所导致的。为了减少运输浪费,企 业需要优化运输方式和路线,提高装卸作 业效率,同时也可以考虑采用第三方物流 等外包方式来降低运输成本。
库存积压
总结词
库存积压是指原材料、在制品和成品等物资在仓库中积压,不能及时被使用或销售。
详细描述
库存积压会导致资金占用、增加仓储成本、降低物资周转率,甚至可能引发物资过期、损坏或贬值的 风险。过多的库存还可能掩盖生产过程中的问题,如设备故障、质量问题等。因此,企业需要定期清 理库存,合理安排生产和销售计划,避免库存积压。
改进措施
企业A应加强生产计划管理,优化物料 采购和库存控制,减少不必要的浪费 。同时,加强员工培训,提高员工的 节约意识和操作技能。
企业B的浪费情况及改进措施
浪费情况
企业B在生产过程中存在大量的时间 浪费,主要表现在设备故障频繁、生 产流程不顺畅以及生产计划安排不合 理等方面。
改进措施
企业B应加强设备维护和保养,减少 设备故障率。同时,优化生产流程, 提高生产效率。加强生产计划管理, 合理安排生产计划,减少等待和闲置 时间。
03
减少浪费的重要性
动作浪费是指生产过程中工人的多余动作或 无效动作。
详细描述
动作浪费通常是由于操作流程设计不合理、 工具设备不适用、工人技能水平不足等原因 所导致的。为了减少动作浪费,企业需要对 操作流程进行优化设计,提供合适的工具和 设备,同时加强工人的技能培训和操作指导
,提高生产效率和质量。
制造不良品浪费
运输浪费
总结词
运输浪费是指产品在运输过程中所发生 的额外费用和时间消耗。
VS
详细描述
运输浪费通常是由于运输方式选择不当、 运输路线规划不合理、装卸作业效率低下 等原因所导致的。为了减少运输浪费,企 业需要优化运输方式和路线,提高装卸作 业效率,同时也可以考虑采用第三方物流 等外包方式来降低运输成本。
库存积压
总结词
库存积压是指原材料、在制品和成品等物资在仓库中积压,不能及时被使用或销售。
详细描述
库存积压会导致资金占用、增加仓储成本、降低物资周转率,甚至可能引发物资过期、损坏或贬值的 风险。过多的库存还可能掩盖生产过程中的问题,如设备故障、质量问题等。因此,企业需要定期清 理库存,合理安排生产和销售计划,避免库存积压。
改进措施
企业A应加强生产计划管理,优化物料 采购和库存控制,减少不必要的浪费 。同时,加强员工培训,提高员工的 节约意识和操作技能。
企业B的浪费情况及改进措施
浪费情况
企业B在生产过程中存在大量的时间 浪费,主要表现在设备故障频繁、生 产流程不顺畅以及生产计划安排不合 理等方面。
改进措施
企业B应加强设备维护和保养,减少 设备故障率。同时,优化生产流程, 提高生产效率。加强生产计划管理, 合理安排生产计划,减少等待和闲置 时间。
03
减少浪费的重要性
七大浪费培训资料ppt课件
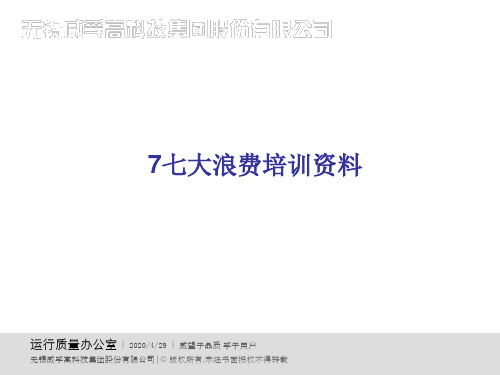
例子: 操作人员等待系统运行完毕
你能想到其他的例子吗?
5 过量生产(最大的浪费源)
定义:生产零组件超过需求或以超过规定的速度生产零组件;必要的 东西在必要的时候,做出必要的数量,除此之外都是浪费
结果: 造成不必要的库存,提早用掉资金,隐藏“等待的浪费"积压在制品
在车间,空间不足,走动困难;搬运,堆积的浪费;增加栈板,周转箱 (纸箱容器)的浪费;库存量增大,管理工时增加;利息负担增加 显示生产能力超过需求 例子: 由于生产方法或设备难以改变而预先生产出大批量的零组件
3 动作的浪费
定义:不能使产品增值之人员动作或机器动作 结果: 增加损坏产品的风险 增加人力需求
例子: 工作区域之间距离太长-如工作站零件盒距离。
你能想到其他的例子吗?
3 动作的浪费
12种动作的浪费:
1、两手空闲 2、举手空闲 3、作业动作停止 4、动作太大 5、左右手交换 6、步行多
7大浪费培训资料 7七大浪费培训资料
运行质量办公室 | 2020/4/29 | 威望于品质 孚于用户
无锡威孚高科技集团股份有限公司|© 版权所有,未经书面授权不得转载
课程目的(Purposes)
➢认识七大浪费的基本概念 ➢找出工作中存在的七大浪费 ➢学习消除七大浪费的方法
课程目标
课程结束后你能够(Deliverable):
7、转身角度大 8、移动中变换“状态" 9、不明技巧 10、伸背动作 11、弯腰动作 12、重复/不必要的动作
4 等待的浪费
定义:操作或事件之间的闲置时间,指断料、作业不平衡,计划 不当造成无事可作的等待
结果: 增加人工成本;工作量变动大,工作量少时,便无所事事;上游工
序发生延误,下游工序没事可做;机器闲置(待料);机器设备时 常发生故障;劳逸不均现象;材料备齐,但无标准品,上下限,工令 单;生产联机品种切换的等待 显示一条不均衡的生产线
你能想到其他的例子吗?
5 过量生产(最大的浪费源)
定义:生产零组件超过需求或以超过规定的速度生产零组件;必要的 东西在必要的时候,做出必要的数量,除此之外都是浪费
结果: 造成不必要的库存,提早用掉资金,隐藏“等待的浪费"积压在制品
在车间,空间不足,走动困难;搬运,堆积的浪费;增加栈板,周转箱 (纸箱容器)的浪费;库存量增大,管理工时增加;利息负担增加 显示生产能力超过需求 例子: 由于生产方法或设备难以改变而预先生产出大批量的零组件
3 动作的浪费
定义:不能使产品增值之人员动作或机器动作 结果: 增加损坏产品的风险 增加人力需求
例子: 工作区域之间距离太长-如工作站零件盒距离。
你能想到其他的例子吗?
3 动作的浪费
12种动作的浪费:
1、两手空闲 2、举手空闲 3、作业动作停止 4、动作太大 5、左右手交换 6、步行多
7大浪费培训资料 7七大浪费培训资料
运行质量办公室 | 2020/4/29 | 威望于品质 孚于用户
无锡威孚高科技集团股份有限公司|© 版权所有,未经书面授权不得转载
课程目的(Purposes)
➢认识七大浪费的基本概念 ➢找出工作中存在的七大浪费 ➢学习消除七大浪费的方法
课程目标
课程结束后你能够(Deliverable):
7、转身角度大 8、移动中变换“状态" 9、不明技巧 10、伸背动作 11、弯腰动作 12、重复/不必要的动作
4 等待的浪费
定义:操作或事件之间的闲置时间,指断料、作业不平衡,计划 不当造成无事可作的等待
结果: 增加人工成本;工作量变动大,工作量少时,便无所事事;上游工
序发生延误,下游工序没事可做;机器闲置(待料);机器设备时 常发生故障;劳逸不均现象;材料备齐,但无标准品,上下限,工令 单;生产联机品种切换的等待 显示一条不均衡的生产线
七大浪费及改善八大步骤ppt课件
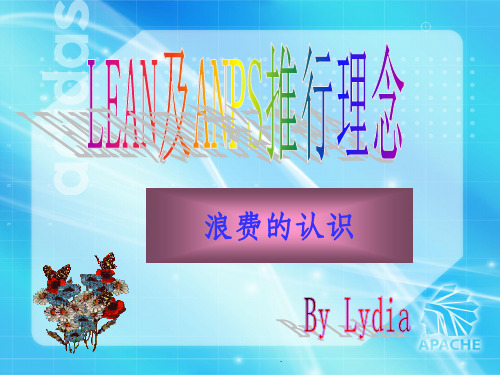
.
七大浪费的认识——P4
六、库存的浪费(为万恶之源):是因传统以来的许 多错误生产观念所造成的。分三种:
1)材料库存:大量采购成本低。 2)在制品库存:不良重修机器故障。 3)成品库存:预测生产与实际需求量不同。 库存所带来的弊端: 1)产生不必要的搬运、堆积、放置、防护处理找寻等浪费; 2)使先进先出作业困难; 3)损失利息及管理费用; 4)物品贬值的风险以及占用空间而引起的投资浪费等。 库存三不原则:不大批量生产;不批量搬运;不大批量采购。 降低库存三要领:回要多;批量要小;交期要快。
.
七大浪费的认识——P5
七、生产过多过早的浪费(最大的浪费):是指生产 出比订单所下的数量更多的产品,或在交货期未到 之前提早生产等待交货之产品。如:订单5000双, 实际生产6000双。
预测生产和提早生产以及过量生产带来的弊端:
1)多做了无用,变成库存从而资金积压以及贬值。
2)过早生产只是提早地用掉了材料费以及人工费, 并把“等待的浪费”隐藏起来——因进度提前,主 管放心,漠视等待的浪费,同样也造成在制品的积 压即库存的浪费,还有搬运的浪费等。
现做,立即现查。 D、比较法:比较最好与最差之状况,协助找出真因。 E、放大法:放大不良品来观察,或将空间扩大并与 其他线别作比较:数据、样品。 F、解剖法:了解不良品之内涵。 G、潜水法:即要不断地、实际地,亲自去寻找问题 的真因。
.
(五)、对策实施: 1. 开展拙速巧迟的改善动作. 2. 要做到五现主义:走入—现场、观察—现
善,分为以下五个方面: 作业的改善:如对作业点的动作改善 流线的改善:即生产线布置、人员安排的改善,注
意前后工序的衔接和不要有离岛式作业 设备的改善:用符合LEAN要求的JIDOKA设备 制度的改善:采购、生管、物管、品管、人力设备
七大浪费的认识——P4
六、库存的浪费(为万恶之源):是因传统以来的许 多错误生产观念所造成的。分三种:
1)材料库存:大量采购成本低。 2)在制品库存:不良重修机器故障。 3)成品库存:预测生产与实际需求量不同。 库存所带来的弊端: 1)产生不必要的搬运、堆积、放置、防护处理找寻等浪费; 2)使先进先出作业困难; 3)损失利息及管理费用; 4)物品贬值的风险以及占用空间而引起的投资浪费等。 库存三不原则:不大批量生产;不批量搬运;不大批量采购。 降低库存三要领:回要多;批量要小;交期要快。
.
七大浪费的认识——P5
七、生产过多过早的浪费(最大的浪费):是指生产 出比订单所下的数量更多的产品,或在交货期未到 之前提早生产等待交货之产品。如:订单5000双, 实际生产6000双。
预测生产和提早生产以及过量生产带来的弊端:
1)多做了无用,变成库存从而资金积压以及贬值。
2)过早生产只是提早地用掉了材料费以及人工费, 并把“等待的浪费”隐藏起来——因进度提前,主 管放心,漠视等待的浪费,同样也造成在制品的积 压即库存的浪费,还有搬运的浪费等。
现做,立即现查。 D、比较法:比较最好与最差之状况,协助找出真因。 E、放大法:放大不良品来观察,或将空间扩大并与 其他线别作比较:数据、样品。 F、解剖法:了解不良品之内涵。 G、潜水法:即要不断地、实际地,亲自去寻找问题 的真因。
.
(五)、对策实施: 1. 开展拙速巧迟的改善动作. 2. 要做到五现主义:走入—现场、观察—现
善,分为以下五个方面: 作业的改善:如对作业点的动作改善 流线的改善:即生产线布置、人员安排的改善,注
意前后工序的衔接和不要有离岛式作业 设备的改善:用符合LEAN要求的JIDOKA设备 制度的改善:采购、生管、物管、品管、人力设备
七大浪费与改善方法ppt课件
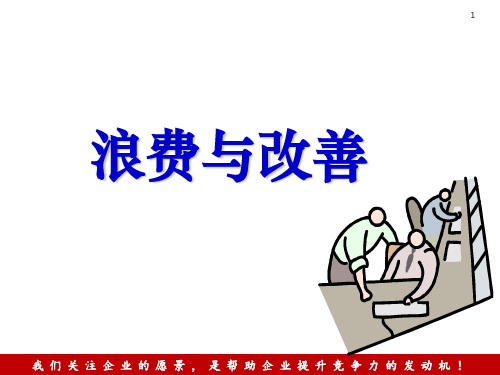
6.过盈生产的 浪费 (过多的生产)
7.做不良的 浪费 (出作业不良)
4M ▶ 8M + 2E
•MAN •MAN+MACHINE+MATERIAL •MAN+MACHINE+MATERIAL •MAN •MAN •MATERIAL •MAN+MATERIAL
我们关注企业的愿景,是帮助企业提升竞争力的发动机!
(
) 同样的事故反复出现
(
) 没有工作欲望
(
) 事故不及时向工厂反映
(
) 紧缺材料到达不及时
(
) 材料取集困难
(
) 作业Error多
(
) 设计图面过于复杂(ຫໍສະໝຸດ ) 不遵守计划日程(
) 不检查材料
(
) 作业没有进行改善
(
) 检查作业不充分
(
) 作业Error发现不及时
(
) 作业没有标准化
(
) 动力系统故障过多
(
) 作业Balance不佳
(
) 没有图纸的情况下进行加工
(
) 不合理的事强行
(
) 设备点检不彻底
(
) 不合理的工作硬要执行
(
) 作业训练不充分
(
) 作业方法不知道
(
) 作业标准改正过慢
(
) 不清楚工厂的纪律
(
) 作业环境恶劣
(
) 作业间信息传达不通畅
(
) 缺少测量仪器
(
) 参加没有效果的会议
(
) 慢性加班过多
我们关注企业的愿景,是帮助企业提升竞争力的发动机!
学习 Ⅰ.浪费
2. 浪费的 种类
9
7.做不良的 浪费 (出作业不良)
4M ▶ 8M + 2E
•MAN •MAN+MACHINE+MATERIAL •MAN+MACHINE+MATERIAL •MAN •MAN •MATERIAL •MAN+MATERIAL
我们关注企业的愿景,是帮助企业提升竞争力的发动机!
(
) 同样的事故反复出现
(
) 没有工作欲望
(
) 事故不及时向工厂反映
(
) 紧缺材料到达不及时
(
) 材料取集困难
(
) 作业Error多
(
) 设计图面过于复杂(ຫໍສະໝຸດ ) 不遵守计划日程(
) 不检查材料
(
) 作业没有进行改善
(
) 检查作业不充分
(
) 作业Error发现不及时
(
) 作业没有标准化
(
) 动力系统故障过多
(
) 作业Balance不佳
(
) 没有图纸的情况下进行加工
(
) 不合理的事强行
(
) 设备点检不彻底
(
) 不合理的工作硬要执行
(
) 作业训练不充分
(
) 作业方法不知道
(
) 作业标准改正过慢
(
) 不清楚工厂的纪律
(
) 作业环境恶劣
(
) 作业间信息传达不通畅
(
) 缺少测量仪器
(
) 参加没有效果的会议
(
) 慢性加班过多
我们关注企业的愿景,是帮助企业提升竞争力的发动机!
学习 Ⅰ.浪费
2. 浪费的 种类
9
七大浪费工业程与制程改善37页PPT
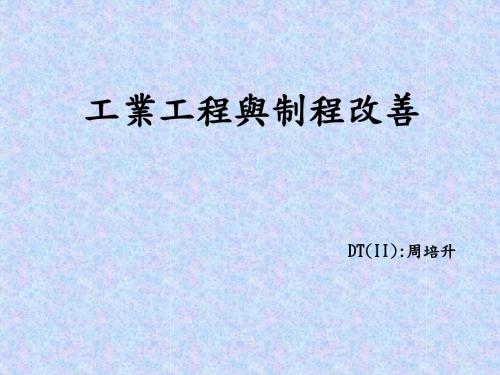
-- 電子工程 -- 核工業 -- 品質工作
-- 工業工程
IE 之概念及工作概要
工業工程 Industrial Engineering 簡稱IE
是對于整個工作系統之人員、物料、設備、 能源,信息等資源, 綜合運用數學、物理 學和社會科學等專業知識和技術,以及工 程分析和設計的原理與方法進行設計,設 置和改進的一門學科. 並對取得的成果進 行確定、預測和評價.
-- 五五法、防呆法、動改法:協助我們 對已知的問題,質問探尋改善的具體方法, 以實現改善的目標.
1. 動 改 法
應用動作經濟原則,評估並改善制程中所
發生的所有動作,以達到減化、省力、省時、 舒適、有效的境界.
動作經濟原則
• 1.兩手同時開始及完成動作. • 2.除休息時間外,兩手不應同時空開. • 3.兩臂之動作應反向同時對稱. • 4.盡可能以最低級動作工作. • 5.盡量利用動量以協助操作人員,如動量需肌肉制止時. • 6.順暢連續曲線動作比方向突變直線運作為佳. • 7.彈道式即自由擺動式比固定或“受控的”動作較快較
(70年代 ~ 現在 ~ 未來)
--- IE部一般組織架構 IE MANAGER
Maintenance
Process Industrial Engineering
Workshop Layout
Maintenance之工作
-- 工場電線,電制之分布設計及安裝. -- 工場電器如冷氣機,空壓機,等安裝及保養 -- 定期檢測工場光亮度,並做計錄. -- 定期檢測產線靜電防護設施,接地性能,靜電帶性能並做計錄. -- 制造生產夾制具及TEST FIXTURE. -- 制造各類自行設計之氣動,手動機械. -- 各類夾治具及設備之調校,維修及保養.
相关主题
- 1、下载文档前请自行甄别文档内容的完整性,平台不提供额外的编辑、内容补充、找答案等附加服务。
- 2、"仅部分预览"的文档,不可在线预览部分如存在完整性等问题,可反馈申请退款(可完整预览的文档不适用该条件!)。
- 3、如文档侵犯您的权益,请联系客服反馈,我们会尽快为您处理(人工客服工作时间:9:00-18:30)。
29
搬运浪费的表现
过多的搬运设备 仓储质量降低
半成品仓 存放 ging
机加 混合
检验 nspection
包装 Packaging 库存 Set-up
原料 Raw
时间 Time = 有附加值的时间
成品
=无附加值的时间(浪费 ) ue
10
用增值和非增值来分析企业制造过程
提高生产能力方式
$
传 统 做 法
时间 me
$
精益生产后的结果
精 益 做 法
27
T:搬运浪费
定义:
任何不为生产过程所必需的物料搬动或信息流转。
&
T:搬运浪费
- 找到、拿起、移动、用手放 - 从手推车移到货板 - 从货仓到工厂 - 从工厂到生产线 - 从生产线到车间 - 从车间到操作工位
搬运浪费指流程中因两点距离远而造成的搬运、走动等浪 费,包括人的浪费和机器的浪费。搬运本身是一种无附加价值 的动作,若分解开来又分为:放置、堆积、移动、整理等动作 浪费。
M6
1.00 1.89 1.80 1.00 1.16 5.26 4.37 1.72 2.55 0.39 2.55 0.48 5.59 1.00 1.00 0.91 2.52 4.40 4.40 1.22 0.91 6.41 5.99
M5 M4 M3 M2 S11 S12 M1
S1
S2
S3
S4
S5
S6
七大浪费分析与改善
主讲人:李富友 2016.1.28
课堂约定
请关闭手机或改为震动
保持空杯的心态
请充分讨论并分享你的观点
请不要吝啬自己的掌声
培训目标
1.认识七大浪费的定义和内容 2.能够掌握七大浪费分析方法识别浪费
精益生产的核心思想
一个流
消除浪费
全员参与 持续改进
4
内容纲要
认识浪费 七大浪费解读
原地打转 没有创造价值
在转动过程中 创造了价值
8
认识增值与非增值
• 某权威机构对企业增值与非增值活动的统计:
增值 (<5%)
制造过 程
非增值 (约95%)
必要非增值(约60%)
不必要非增值(约35%)
思考:物料搬运是属于什么呢?
9
用增值和非增值来分析企业制造过程
原料生产 压铸 运输 Waiting 运输 Transportation
5
什么是浪费?
广义的浪费:
狭义理解:制造业中的浪费
超出增加产品价值所 绝对必须的最少量 的人力、设备、物 料、场地和时间的部分都是浪费。 浪费就是指客户
不愿意为你付钱
6
的那些过程。
认识增值与非增值
• 增值:技术工艺图纸中的所有活动 • 非增值!
7
认识增值与非增值
增值与非增值图解
S7
S8
S9
S10
平衡率:91.2%
26
七大浪费解读
简写
I T D M W O O Inventory Transportation Defects Motion Waiting Over production Over process
英文
中文
过度库存的浪费 搬运的浪费 不良品浪费 动作的浪费 等待的浪费 过量生产的浪费 过度加工的浪费
23
过度库存浪费解决办法
1﹑订单管理模式:根据客户需求生产; 2﹑拉动生产:拉动系统的管理方式;
3﹑节拍平衡:合理的IE手法优化生产线提高平衡率;
4﹑均衡计划:平衡生产计划; 5﹑超市管理:库存警示方法;
过度库存改善案例1
改善前:在生产现场,由于是按工 单来领料,所以堆积了8000多套库 存
不良品浪费
14
七大浪费解读
简写
I T D M W O O Inventory Transportation Defects Motion Waiting Over production Over process
英文
中文
过度库存的浪费 搬运的浪费 不良品浪费 动作的浪费 等待的浪费 过量生产的浪费 过度加工的浪费
合并
合并
M6
0.95 0.91 0.95 1.00 4.40 0.91 2.52 1.22 0.91 6.41 5.99
M5 M4 M3 M2
S13 S14
S1
S2
S3
S4
S5
S6
S7
S8
S9
S10
S11
S12
M1
合并
合并
平衡率:75.3%
改善后
7 6 5 4 3 2 1 0
0.48 0.50 0.96 3.12 0.50 2.61 2.46 0.48
15
I:过度库存的浪费
定义: 由于原材料、在制品或成品的库存超过必需的量, 而造成的浪费。 指除单件流动产品以外所有的物料、半成品、成品。
16
I:过度库存的浪费
资金成本 资金积压 设备投入 场地占用 质量成本 磕碰,变形 难以实现先进先出
管理成本 搬运量、场地、 防护、管理
过度 库存 成本
占用 大量 资金
缓解 供需 矛盾
21
库存产生的内在原因
压 铸 车 间
清 理 车 间
机 加 车 间
提需求 180个
仓 产 储 品
客 户
定单 100个
提需求 150个
300个
提需求 220个
22
库存存在原因解析
孤岛作业的库存
― 以防万一的逻辑; ― 生产线工序间不平衡; ― 生产计划不平衡; ― 供应商不可靠; ― 设备状态良好时连续生产﹔ ― 认为提前生产是高效率表现﹔
变更成本 产品换型、 市场价格变化
17
过度库存的浪费
海
水
礁石
礁石
礁石
礁石
过礁石
质量问题
交货问题
过度库存的浪费
海
水
团队管理
维修问题
效率问题
质量问题
计划管理
交货问题
I:过度库存的浪费
存货管理名言: 库存是必要的恶物
降低了职能部门服务现场的意识 阻碍了现场生产部门改进的意识
改善后:实施物料配送模式,按时 按量将物料配送到生产线上,减 少了库存,提高了效率
25
过度库存改善案例2
改善前
8 7 6 5 4 3 2 1 0
1.00 0.95 1.00 5.55 4.92 1.89 1.80 1.00 0.95 1.00 1.47 5.34 4.37 0.95 1.80 1.83 0.95 0.95 0.91 0.95 5.11 4.98 5.11 5.59
Amount of Time Eliminated
时间 me
节约少量的时间
$
时间 Time
$
11
增值与非增值的管理目标
不必要非增值
消除
减少 提高增值比
必要非增值
增值
12
内容纲要
认识浪费 七大浪费解读
13
七大浪费解读
动作浪费 等待浪费 过度库存浪费
七大浪费
过量生产浪费
搬运浪费
过度加工浪费
搬运浪费的表现
过多的搬运设备 仓储质量降低
半成品仓 存放 ging
机加 混合
检验 nspection
包装 Packaging 库存 Set-up
原料 Raw
时间 Time = 有附加值的时间
成品
=无附加值的时间(浪费 ) ue
10
用增值和非增值来分析企业制造过程
提高生产能力方式
$
传 统 做 法
时间 me
$
精益生产后的结果
精 益 做 法
27
T:搬运浪费
定义:
任何不为生产过程所必需的物料搬动或信息流转。
&
T:搬运浪费
- 找到、拿起、移动、用手放 - 从手推车移到货板 - 从货仓到工厂 - 从工厂到生产线 - 从生产线到车间 - 从车间到操作工位
搬运浪费指流程中因两点距离远而造成的搬运、走动等浪 费,包括人的浪费和机器的浪费。搬运本身是一种无附加价值 的动作,若分解开来又分为:放置、堆积、移动、整理等动作 浪费。
M6
1.00 1.89 1.80 1.00 1.16 5.26 4.37 1.72 2.55 0.39 2.55 0.48 5.59 1.00 1.00 0.91 2.52 4.40 4.40 1.22 0.91 6.41 5.99
M5 M4 M3 M2 S11 S12 M1
S1
S2
S3
S4
S5
S6
七大浪费分析与改善
主讲人:李富友 2016.1.28
课堂约定
请关闭手机或改为震动
保持空杯的心态
请充分讨论并分享你的观点
请不要吝啬自己的掌声
培训目标
1.认识七大浪费的定义和内容 2.能够掌握七大浪费分析方法识别浪费
精益生产的核心思想
一个流
消除浪费
全员参与 持续改进
4
内容纲要
认识浪费 七大浪费解读
原地打转 没有创造价值
在转动过程中 创造了价值
8
认识增值与非增值
• 某权威机构对企业增值与非增值活动的统计:
增值 (<5%)
制造过 程
非增值 (约95%)
必要非增值(约60%)
不必要非增值(约35%)
思考:物料搬运是属于什么呢?
9
用增值和非增值来分析企业制造过程
原料生产 压铸 运输 Waiting 运输 Transportation
5
什么是浪费?
广义的浪费:
狭义理解:制造业中的浪费
超出增加产品价值所 绝对必须的最少量 的人力、设备、物 料、场地和时间的部分都是浪费。 浪费就是指客户
不愿意为你付钱
6
的那些过程。
认识增值与非增值
• 增值:技术工艺图纸中的所有活动 • 非增值!
7
认识增值与非增值
增值与非增值图解
S7
S8
S9
S10
平衡率:91.2%
26
七大浪费解读
简写
I T D M W O O Inventory Transportation Defects Motion Waiting Over production Over process
英文
中文
过度库存的浪费 搬运的浪费 不良品浪费 动作的浪费 等待的浪费 过量生产的浪费 过度加工的浪费
23
过度库存浪费解决办法
1﹑订单管理模式:根据客户需求生产; 2﹑拉动生产:拉动系统的管理方式;
3﹑节拍平衡:合理的IE手法优化生产线提高平衡率;
4﹑均衡计划:平衡生产计划; 5﹑超市管理:库存警示方法;
过度库存改善案例1
改善前:在生产现场,由于是按工 单来领料,所以堆积了8000多套库 存
不良品浪费
14
七大浪费解读
简写
I T D M W O O Inventory Transportation Defects Motion Waiting Over production Over process
英文
中文
过度库存的浪费 搬运的浪费 不良品浪费 动作的浪费 等待的浪费 过量生产的浪费 过度加工的浪费
合并
合并
M6
0.95 0.91 0.95 1.00 4.40 0.91 2.52 1.22 0.91 6.41 5.99
M5 M4 M3 M2
S13 S14
S1
S2
S3
S4
S5
S6
S7
S8
S9
S10
S11
S12
M1
合并
合并
平衡率:75.3%
改善后
7 6 5 4 3 2 1 0
0.48 0.50 0.96 3.12 0.50 2.61 2.46 0.48
15
I:过度库存的浪费
定义: 由于原材料、在制品或成品的库存超过必需的量, 而造成的浪费。 指除单件流动产品以外所有的物料、半成品、成品。
16
I:过度库存的浪费
资金成本 资金积压 设备投入 场地占用 质量成本 磕碰,变形 难以实现先进先出
管理成本 搬运量、场地、 防护、管理
过度 库存 成本
占用 大量 资金
缓解 供需 矛盾
21
库存产生的内在原因
压 铸 车 间
清 理 车 间
机 加 车 间
提需求 180个
仓 产 储 品
客 户
定单 100个
提需求 150个
300个
提需求 220个
22
库存存在原因解析
孤岛作业的库存
― 以防万一的逻辑; ― 生产线工序间不平衡; ― 生产计划不平衡; ― 供应商不可靠; ― 设备状态良好时连续生产﹔ ― 认为提前生产是高效率表现﹔
变更成本 产品换型、 市场价格变化
17
过度库存的浪费
海
水
礁石
礁石
礁石
礁石
过礁石
质量问题
交货问题
过度库存的浪费
海
水
团队管理
维修问题
效率问题
质量问题
计划管理
交货问题
I:过度库存的浪费
存货管理名言: 库存是必要的恶物
降低了职能部门服务现场的意识 阻碍了现场生产部门改进的意识
改善后:实施物料配送模式,按时 按量将物料配送到生产线上,减 少了库存,提高了效率
25
过度库存改善案例2
改善前
8 7 6 5 4 3 2 1 0
1.00 0.95 1.00 5.55 4.92 1.89 1.80 1.00 0.95 1.00 1.47 5.34 4.37 0.95 1.80 1.83 0.95 0.95 0.91 0.95 5.11 4.98 5.11 5.59
Amount of Time Eliminated
时间 me
节约少量的时间
$
时间 Time
$
11
增值与非增值的管理目标
不必要非增值
消除
减少 提高增值比
必要非增值
增值
12
内容纲要
认识浪费 七大浪费解读
13
七大浪费解读
动作浪费 等待浪费 过度库存浪费
七大浪费
过量生产浪费
搬运浪费
过度加工浪费