五金冲压模具模具设计开发控制程序
模具设计开发控制程序
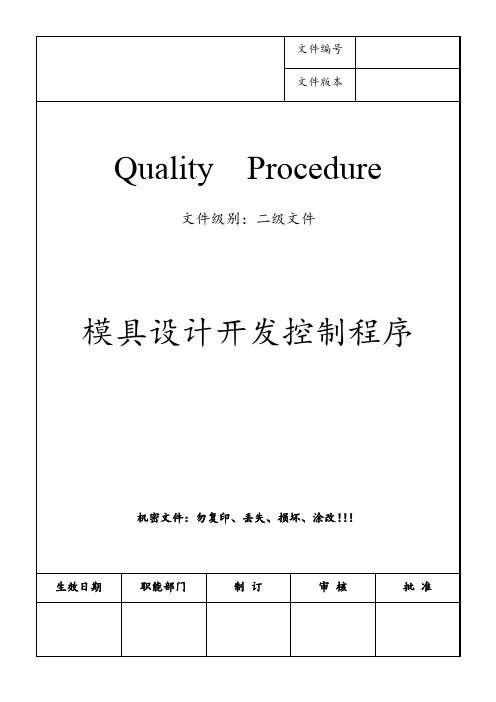
b.凡是不改变模具结构、原理的一般更改会签评审后,由设计部负责跟进直达到预期的改进效果。
4.5.3模具设计和开发技术文件的管理
设计和开发技术文件属受控文件,依据《文件控制程序》及《工程技术文件管理规定》进行管理和控制,其中模具结构图纸及设计文件、工艺文件的发放,必须经设计部经理批准。
4.4模具设计输出
4.4.1模具施工图纸设计
4.4.1.1设计部在初步技术评审的基础上完成全部模具图纸及设计文件,包括模具总图、线割加工图、装嵌施工图、BOM等。
4.4.1.2模具设计工程师对制作完毕的图纸进行技术检查,将检查结果记录于《制模前的图纸设计技术检查表》。
4.4.1.3模具设计工程师按模具结构图对模具的零配件作出详细的《标准件模具零件明细表》交PMC部/采购部实施采购部,对需加工的工件,制作零件加工图(施工图),施工图由设计部主管审核签名由设计部文员按《工程技术文件管理规定》发放工模部签收并记录。
4.4.2.2工模部将做好的工模部件进行组装,同时检查模具组装是否有错漏,及模具吻合程度并对组装好的成品模具进行检测,形成《模具试模前检测》表。
4.4.2.3工模部将制好的模具交试模组安排试模。
4.4.2.4注塑课组织工模部、设计部、品管部按《模具要求》、《试模申请单》要求进行试模,注塑课将试模结果填写于《试模记录表》。
4.5模具设计更改
4.5.1市场部组织客户、设计部、品管部对模具制作结果作最终评价,当模具不能满足客户技术要求时,设计部工程师对模具结构、技术参数进行分析、检讨,把改善方案形成《模具成品改良书》,经设计部主管批准交工模部按《模具制造过程控制程序》、《工程技术文件管理规定》实施模具改良。
五金冲压模具的开发流程详解~

五⾦冲压模具的开发流程详解~⼀:产品导⼊1 精密冲压磨具常规产品导⼊流程1.1产品图→加⼯图→排样图→结构图→组⽴图→模具图纸1.2 连续模具排样图及结构图须审核1.3 单冲模具排样图及结构图须审核1.3 模具图纸须审核签字⽣效,图纸规范清晰2 样品控制流程现场提供样品→⾃检→品管部检测→检测报告→检测报告确认→⼯程部→客户⼆:模具设计1.模具设计流程(1)模具设计流程图(2)此为模具设计基本流程,⼀般情况下,都应遵循该流程的步骤来规划及实施设计⼯作。
对于某些特殊产品的设计,在此流程基础上,可以依实际情况适当变更。
2. 产品图、展开图、加⼯(⼯序)图、料带图的绘制规范(1)产品图开模⽤的产品图或产品(样品)由客户及⽂控中⼼提供。
因产品图均来⾃于各个客户,规范不⼀,且有图⾯不清晰,标注不完善,尺⼨或检测基准混乱,或者⼈为疏忽造成的错误。
故应以原图纸为基础,在忠于原设计的前提下,⾃⾏绘制本⼚⾃⽤的产品图。
对于客户图纸中的⼯艺问题,及时与客户的⼯程师沟通,难以达到的⼯艺或结构要求,可与对⽅⼯程师协商,通过降低⼯艺要求、更改产品结构或者增加⼯艺辅助⼿段的⽅法来解决。
对客户原图纸不得更改,原样保存。
客户提供的样品,⽤各种⼿段准确测绘出样品尺⼨,作成产品图。
客户样品要妥善保存。
给制的产品图需数据准确,要求明了,尺⼨标注完善,公差合理,便于检测。
(2)加⼯图产品图确认后,开始制订加⼯图。
加⼯图的制订要注意以下⼏个要点:A: 产品尺⼨的取值分冲孔与落料两种情况。
冲孔尺⼨是由冲头决定的,落料尺⼨是由凹模决定的。
B: 产品公差的取值以产品图为主,产品图上标有公差的,按图纸执⾏,产品图上未注公差的,以客户惯⽤的公差为准.公差取值⽅向参考图 1-1。
对于冲裁后会变⼤的尺⼨,加⼯图尺⼨为其下偏差的 2/3,对于冲裁后会变⼩的尺⼨,加⼯图尺⼨为其上偏差的 2/3。
对于孔⼼距和孔边距等冲裁后尺⼨基本保持不变的,则按中间公差取值。
五金冲压模具模具设计开发控制程序

五金冲压模具模具设计开发控制程序首先,在模具设计开发过程中,要进行充分的前期准备工作。
这包括对产品的功能需求进行分析和确定,以及对模具的使用环境和条件进行了解。
通过这些准备工作,可以为后续的模具设计和开发提供指导和依据。
其次,在模具设计阶段,需要制定相应的设计准则和标准。
这些标准可以包括模具的使用寿命、制造成本、制造周期等要求。
在设计时要充分考虑到各种因素的影响,如模具的结构设计、材料选择、工艺要求等。
然后,在模具制造阶段,需要建立严格的制造管理程序。
这包括对材料采购、工艺过程、设备使用等方面的管理。
在制造过程中,需要进行严格的质量控制,确保模具的加工质量和尺寸精度符合设计要求。
在模具制造完成后,还需要进行模具试模和调试。
通过试模和调试,可以验证模具的设计和制造是否满足产品的要求,发现和解决可能存在的问题。
最后,在模具使用过程中,需要建立完善的维护和保养程序。
对于长期使用的模具,要定期进行维护,保证其正常使用。
在使用过程中,还要及时记录和反馈模具的使用情况,以便对模具进行优化和改进。
综上所述,五金冲压模具模具设计开发控制程序是一个较为复杂和繁琐的过程,需要从前期准备、设计、制造到使用的各个环节都进行严格的控制和管理。
只有这样,才能保证模具的质量和效率,提高生产效益。
冲压模具开发流程

冲压模具开发流程1.产品需求分析和设计:首先,对于需要冲压的零部件,需要进行需求分析并确定产品的设计要求。
根据产品的形状、尺寸以及数量要求,制定相应的设计方案。
2.模具设计:根据产品设计方案,进行模具的设计。
包括三维模型设计、结构设计、模具零部件设计等。
模具的设计要满足产品要求,并且考虑到材料的选择、加工工艺等因素。
3.模具制造:在完成模具设计后,需要进行模具的制造。
包括模具标准件的采购、非标准件的加工以及模具的组装等。
制造过程中需要进行严格的质量控制和检测,以确保模具的质量。
4.模具调试:在模具制造完成后,需要进行模具的调试。
包括模具零部件的配合检查、模具操作的检验、以及产品的抽样试模等。
通过调试,可以确保模具的正常运行,并达到产品设计要求。
5.试产和修正:在模具调试过程中,进行初步的试产。
通过试产可以发现模具存在的问题,并进行修正。
包括模具结构的改进、零部件的更换等。
通过多次试产和修正,最终达到满足产品质量要求的模具。
6.批量生产:在完成模具的调试和修正后,进行批量生产。
根据客户的需求,进行大批量的产品生产。
生产过程中需要进行质量控制和检测,以确保产品的质量稳定。
7.模具维护和改进:在模具的使用过程中,需要进行定期的维护和保养。
包括模具的清洁、零部件的更换等。
同时,根据客户反馈和产品要求的变化,进行模具的改进和升级。
总结起来,冲压模具开发流程包括产品需求分析和设计、模具设计、模具制造、模具调试、试产和修正、批量生产以及模具维护和改进等环节。
在每个环节中,需要进行严格的质量控制和检测,以确保模具和产品的质量。
冲压模具开发流程的顺利进行,能够为企业提供优质的零部件,提高生产效率和产品质量。
冲压模具设计的一般流程
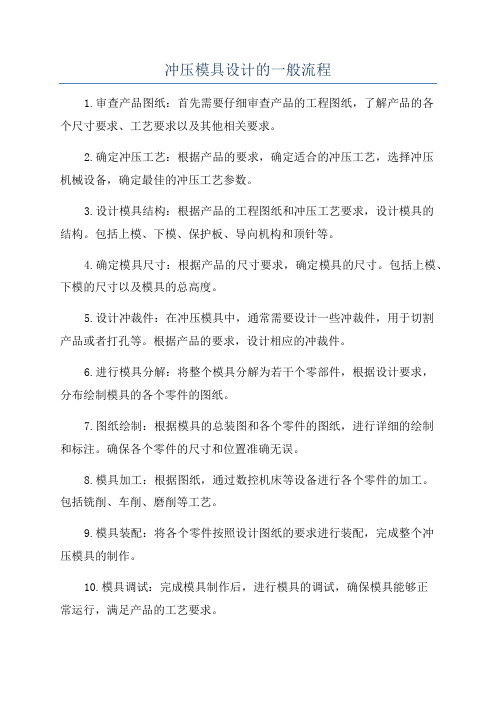
冲压模具设计的一般流程
1.审查产品图纸:首先需要仔细审查产品的工程图纸,了解产品的各
个尺寸要求、工艺要求以及其他相关要求。
2.确定冲压工艺:根据产品的要求,确定适合的冲压工艺,选择冲压
机械设备,确定最佳的冲压工艺参数。
3.设计模具结构:根据产品的工程图纸和冲压工艺要求,设计模具的
结构。
包括上模、下模、保护板、导向机构和顶针等。
4.确定模具尺寸:根据产品的尺寸要求,确定模具的尺寸。
包括上模、下模的尺寸以及模具的总高度。
5.设计冲裁件:在冲压模具中,通常需要设计一些冲裁件,用于切割
产品或者打孔等。
根据产品的要求,设计相应的冲裁件。
6.进行模具分解:将整个模具分解为若干个零部件,根据设计要求,
分布绘制模具的各个零件的图纸。
7.图纸绘制:根据模具的总装图和各个零件的图纸,进行详细的绘制
和标注。
确保各个零件的尺寸和位置准确无误。
8.模具加工:根据图纸,通过数控机床等设备进行各个零件的加工。
包括铣削、车削、磨削等工艺。
9.模具装配:将各个零件按照设计图纸的要求进行装配,完成整个冲
压模具的制作。
10.模具调试:完成模具制作后,进行模具的调试,确保模具能够正
常运行,满足产品的工艺要求。
11.产出产品:经过模具调试后,使用冲压机械设备进行批量生产,产出满足产品要求的冲压件。
12.模具维护和修理:冲压模具在使用过程中,需要进行定期的维护和修理,确保模具长时间稳定运行。
五金冲压模具模具设计程序

頁次
PAGE 3 OF 3
7.7模板繪制
7.8開模組立圖
7.9A、B沖繪制
7.10沖頭零件
7.11異型分層
8、依據設計點檢表繪圖。
9、列出料表費清單。
10、模板分離並注解輸出。
11、線割孔轉路徑。
12、核對“注解輸出”及“料表清單”。
13、出圖。
核准
審核
編制
5.4按內。
5.5頂料銷。
5.6彈簧位置。
5.7側面架構圖。
6、討細節(模具接單檢討要項)。
7、依據模具種類選定規劃檔,繪制正式圖面。
7.1叫規劃檔 (DFG)
7.2間隙設定
7.3模板厚度設定
7.4材料設定
7.5模座設定
7.6存規劃檔
文件編號
TT-QW-TI-09
版本
01
類別
生管組作業規范
制定日期
2005年12月1日
文件編號
TT-QW-TI-09
版本
Hale Waihona Puke 01類別模具設計程序
制定日期
2005年12月1日
操作規範
頁次
PAGE 2 OF 3
1、閱成品圖。
2、據公差及比例修改成品圖至±0尺寸。
3、確定展開系數後展開。
4、檢討排料模式,確定開模方法。
5、繪制草圖。
5.1定模板外形尺寸。
5.2導柱位置
5.3下模(or公模)螺絲及Pin。
模具设计开发控制程序简洁范本

模具设计开发控制程序模具设计开发控制程序1. 简介2. 功能模具设计开发控制程序主要具有以下功能:2.1 模具设计模具设计是整个程序的核心功能。
通过该功能,用户可以进行模具的三维设计和参数设置。
程序提供了丰富的工具和库,方便用户进行模具的设计和修改。
用户可以根据产品的要求和工艺特点,设计出满足需求的模具。
2.2 模具开发模具开发是将设计好的模具进行制造和加工的过程。
在该功能下,用户可以根据设计好的模具进行材料选择、加工工艺设置以及出厂检验等操作。
程序提供了完善的材料库和加工工艺库,方便用户进行选择和设置。
用户也可以随时根据需要对模具进行修改和优化。
2.3 模具控制模具控制是将制造好的模具投入生产使用的过程。
该功能主要包括模具装配、模具调试和模具保养等操作。
用户可以通过程序对模具的使用情况进行实时监控和记录,方便后期的维护和追踪。
2.4 数据统计与分析程序还提供了数据统计与分析功能,用户可以通过该功能对模具设计和开发的各个环节进行数据分析,以求提高设计和开发的效率和质量。
程序会自动各种报表和图表,方便用户进行数据分析和决策。
3. 界面模具设计开发控制程序拥有友好的用户界面,方便用户进行各项操作。
界面采用直观的图形化设计,用户可以通过鼠标和拖拽等简单操作完成各项任务。
4. 技术实现模具设计开发控制程序采用了现代化的软件开发技术,包括三维建模技术、数据库技术、图形化界面设计技术等。
程序使用的编程语言主要是C++和等。
5. 好处与应用模具设计开发控制程序为模具设计和开发提供了全面的管理和控制,可以提高模具的设计、开发和生产效率,降低生产成本,提高产品质量。
该程序广泛应用于各种制造业领域,如汽车制造、家电制造、航空航天等。
6.模具设计开发控制程序是对模具设计和开发的全面管理和控制的软件系统,具有丰富的功能和友好的界面。
该程序可以提高模具的设计、开发和生产效率,降低生产成本,提高产品质量。
它在各种制造业领域都有着广泛的应用前景。
五金冲压工艺流程

五金冲压工艺流程五金冲压工艺是一种通过模具将金属板材加工成所需形状的工艺方法。
它是制造五金制品的重要工艺之一,广泛应用于汽车、电子、家电等行业。
五金冲压工艺流程包括设计模具、选材、冲压加工、表面处理等多个环节,下面将详细介绍五金冲压工艺的流程。
1. 模具设计。
五金冲压工艺的第一步是进行模具设计。
模具是冲压加工的关键工具,直接影响产品的质量和生产效率。
在模具设计阶段,需要根据产品的形状、尺寸和材料特性进行合理设计,确定合适的模具结构和加工工艺。
模具设计师需要具备丰富的经验和专业知识,以确保模具制造的准确性和稳定性。
2. 材料选用。
在模具设计确定后,需要选择合适的金属材料进行冲压加工。
常见的五金冲压材料包括冷轧板、热轧板、不锈钢板等。
不同材料具有不同的强度、硬度和塑性,需要根据产品的要求进行合理选择。
材料的选用直接影响产品的质量和成本,因此需要进行严格的材料筛选和检验。
3. 冲压加工。
冲压加工是五金冲压工艺的核心环节。
在进行冲压加工时,需要根据模具设计和产品要求,将金属板材放置在冲床上,通过模具的压力和动作,使金属板材产生塑性变形,最终得到所需形状的产品。
在冲压加工过程中,需要控制好冲床的压力、速度和位置,以确保产品的精度和表面质量。
4. 表面处理。
冲压加工完成后,产品往往需要进行表面处理,以提高产品的耐腐蚀性和美观度。
常见的表面处理方法包括电镀、喷涂、阳极氧化等。
表面处理的选择需要根据产品的材料和用途进行合理确定,以保证产品的质量和外观要求。
5. 检验包装。
最后,冲压加工完成的产品需要进行严格的检验和包装。
检验包括外观质量、尺寸精度、材料成分等多个方面,以确保产品符合客户的要求。
同时,还需要对产品进行包装,以防止在运输和储存过程中受到损坏。
综上所述,五金冲压工艺流程包括模具设计、材料选用、冲压加工、表面处理和检验包装等多个环节。
每个环节都需要严格控制和管理,以确保产品的质量和生产效率。
五金冲压工艺在现代制造业中具有重要地位,对于提高产品质量和降低生产成本具有重要意义。
五金冲压模具模具设计开发控制程序

目的:舄完善本公司之殴^流程,碓保tzFUffio二、逋用簸圉:逋用於本公司所有模具殴tH乍棠。
三、W M:Jl 模具工作。
四、作H内容:1、和的输入:1.1典祺客签弃丁合同或技ffiBti ,由具【承接模具/工件明条田罩】(殴模通知害)及客户之走品圈^交殴以此舄根掳6!行殴1^和的输入工作;1.2 和^畿的输入要求,雁符合客FtW /合同的要求。
1.3根at市埸^研或分析,提出殴和之建n,条鸳息经理批准彳瓷,:®同相B1背景St料$1交IStm;1.4粽合公司内外反^之信息,以【新品承接梅信#己^】提出^it或技律亍改it之建H,呈^经理批准,签署意见彳瓷,it回2、和1^1的输出;2.1 以输入的要求舄依it, ii行和人封品圈名窟!行检查,5O0B比例、公差、技T M条件及客户之殴要求。
2.2 展^前,雁先按比例和公差整理走品鄙氏,经碓tgmg,再根at具醴情况和客户之特殊要求碓定展^系数后,方可展2.3 之展由雨彳固人分别展|g,且如占圈一致彳如方可it行以下工序。
2.4模具殴方案之制定雁僵先考虑客户之要求,殴^方案(模具工程^0)由殴^人^提出,//经理言牛可,方可it行模具2.5在模具殴tH!程中,殴随畤追跳殴作行情况,填舄【殴度表】。
2.6模具殴th寺,如客户有范则依客范it行,否则依公司内部范it行。
2.7模具俞入资料雁包含:成品圈、模具备&W圈、工序圈、料表清罩、!^田加工圈。
2.8 完成彳瓷,殴填舄【言青膳罩】【五金配件MIW 】交鲍H及批。
【五金配件】先由含康核imt存虽,再由采Wo3、和的言平蕃:3.1 的言平蕃雁由殴和相^罩位it行全面的言平蕃。
3.2富言平H布吉果潇足日寺,则i!行和1^1的勇觥登。
3.3 果不潇足畤,则需畲知备恩经理,it行典客FWBB商参照《客户服将管理程序》4、和1^1 的Mhf:4.1舄了碓保殴^和的结果潇足客户的需求,则由至生走相^罩位it行走品的SB登即^模。
模具设计开发管制程序

适用于本公司冲压模具开发全过程,包括客户产品的开发设计,产品定型及生产过程的技术改进等。
3、职责:
3.1业务部/工程部:客户沟通和传递产品相关的设计和开发的各种信息(如最新图面、功能和性
能要求)。
3.2工程部/模具部:负责模具设计和开发全过程的计划、组织、协调等实施工作,进行设计和开发的策划、确定设计开发的组织和技术接口输入、输出、评审、验证、确认以及设计开发的变更和确定。负责新模具零件外协加工的安排。负责新模具的组装调试并记录试制过程中的各项管控指标。
4.6.3.1当设计和开发的变更对产品的质量和使用无重大影响时,由工程部负责人批准实施
变更。
4.6.3.2当变更涉及到产品的主要性能、功能指标的改变,或人身安全及相关法律法规要
求时,应对变更进行适当验证和确认,经送样客户认可后方可批量生产。
4.6.4设计变更作业参见《工程变更管制程序》。
5.相关文件及表单:
4.3.4模具零件采购作业参见《外协管理程序》。
4.4设计开发的评审
4.4.1工程部应按照策划的要求对设计输出进行系统和综合的评审,评价阶段输出设计文件
是否满足设计开发的要求,及对应的内外部资源的实用性,满足总体设计输入要求的
充分性和程度,识别和预测可能存在的问题,提出纠正措施,以保证最终设计满足客
5.1《设计变更作业规范》
5.2《外协管理程序》
5.3《工程变更管制程序》
5.4.1 :模具进度计划表
5.4.2 :零件加工清单
5.4.3 :请购单
5.4.4 :样品需求通知单
5.4.5 :工程变更申请单
5.4.6 : 设计输出审查记录
5.4.7 :模治具可行性评估表
5.4.8 :模具设计检查表
模具设计开发控制程序
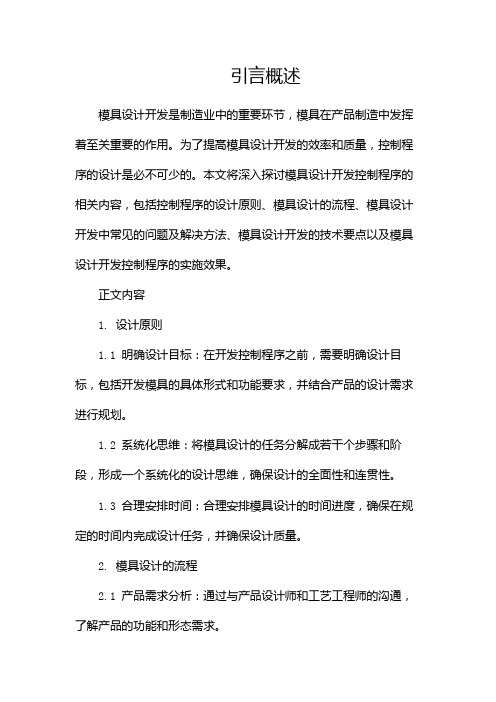
引言概述模具设计开发是制造业中的重要环节,模具在产品制造中发挥着至关重要的作用。
为了提高模具设计开发的效率和质量,控制程序的设计是必不可少的。
本文将深入探讨模具设计开发控制程序的相关内容,包括控制程序的设计原则、模具设计的流程、模具设计开发中常见的问题及解决方法、模具设计开发的技术要点以及模具设计开发控制程序的实施效果。
正文内容1. 设计原则1.1 明确设计目标:在开发控制程序之前,需要明确设计目标,包括开发模具的具体形式和功能要求,并结合产品的设计需求进行规划。
1.2 系统化思维:将模具设计的任务分解成若干个步骤和阶段,形成一个系统化的设计思维,确保设计的全面性和连贯性。
1.3 合理安排时间:合理安排模具设计的时间进度,确保在规定的时间内完成设计任务,并确保设计质量。
2. 模具设计的流程2.1 产品需求分析:通过与产品设计师和工艺工程师的沟通,了解产品的功能和形态需求。
2.2 模具结构设计:根据产品设计要求,设计模具的整体结构和关键部位,包括注塑系统、冷却系统、顶出系统等。
2.3 零件设计与制造:对模具的各个零部件进行详细设计,并制定零部件的制造工艺和加工工艺。
2.4 组装与调试:将模具的零部件进行组装,并进行必要的调试和测试,确保模具的稳定性和可靠性。
2.5 验收和交付:对模具进行全面的验收,确保模具的质量和性能符合设计要求,并进行交付给生产部门。
3. 常见问题及解决方法3.1 模具结构设计不合理:通过优化模具结构,减少冗余部分的设计,提高模具的功能性和性能。
3.2 零件制造精度不高:采用精密加工设备和工艺,确保模具零部件的尺寸和形状精度。
3.3 模具组装不准确:加强对模具组装工艺的控制,确保模具的各个零部件能够正确地配合和协调工作。
3.4 模具使用寿命不长:通过选用高强度材料和优化模具的使用方式,延长模具的使用寿命。
3.5 模具维护保养不到位:建立模具维护保养的规范制度,对模具进行定期检查和维护,延长模具的使用寿命。
冲压模具设计全套步骤和流程总算是弄明白了
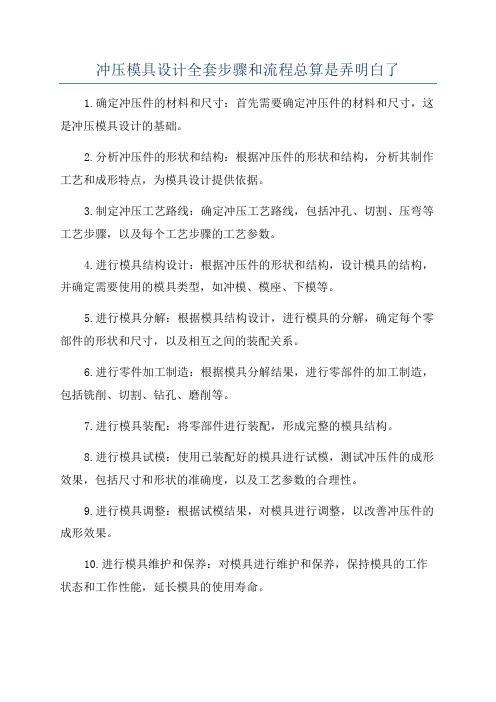
冲压模具设计全套步骤和流程总算是弄明白了
1.确定冲压件的材料和尺寸:首先需要确定冲压件的材料和尺寸,这是冲压模具设计的基础。
2.分析冲压件的形状和结构:根据冲压件的形状和结构,分析其制作工艺和成形特点,为模具设计提供依据。
3.制定冲压工艺路线:确定冲压工艺路线,包括冲孔、切割、压弯等工艺步骤,以及每个工艺步骤的工艺参数。
4.进行模具结构设计:根据冲压件的形状和结构,设计模具的结构,并确定需要使用的模具类型,如冲模、模座、下模等。
5.进行模具分解:根据模具结构设计,进行模具的分解,确定每个零部件的形状和尺寸,以及相互之间的装配关系。
6.进行零件加工制造:根据模具分解结果,进行零部件的加工制造,包括铣削、切割、钻孔、磨削等。
7.进行模具装配:将零部件进行装配,形成完整的模具结构。
8.进行模具试模:使用已装配好的模具进行试模,测试冲压件的成形效果,包括尺寸和形状的准确度,以及工艺参数的合理性。
9.进行模具调整:根据试模结果,对模具进行调整,以改善冲压件的成形效果。
10.进行模具维护和保养:对模具进行维护和保养,保持模具的工作状态和工作性能,延长模具的使用寿命。
以上就是冲压模具设计的全套步骤和流程。
冲压模具设计需要考虑多个方面的因素,包括冲压件的形状和结构、冲压工艺路线、模具结构和装配、模具试模和调整等,通过合理的设计和精确的加工制造,能够提高冲压工艺的质量和效率。
模具产品设计开发控制程序
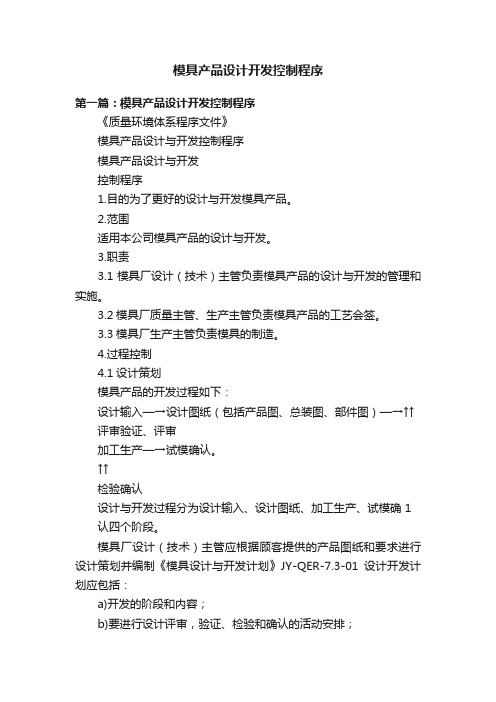
模具产品设计开发控制程序第一篇:模具产品设计开发控制程序《质量环境体系程序文件》模具产品设计与开发控制程序模具产品设计与开发控制程序1.目的为了更好的设计与开发模具产品。
2.范围适用本公司模具产品的设计与开发。
3.职责3.1模具厂设计(技术)主管负责模具产品的设计与开发的管理和实施。
3.2模具厂质量主管、生产主管负责模具产品的工艺会签。
3.3模具厂生产主管负责模具的制造。
4.过程控制4.1设计策划模具产品的开发过程如下:设计输入—→设计图纸(包括产品图、总装图、部件图)—→↑↑评审验证、评审加工生产—→试模确认。
↑↑检验确认设计与开发过程分为设计输入、设计图纸、加工生产、试模确 1 认四个阶段。
模具厂设计(技术)主管应根据顾客提供的产品图纸和要求进行设计策划并编制《模具设计与开发计划》JY-QER-7.3-01设计开发计划应包括:a)开发的阶段和内容;b)要进行设计评审,验证、检验和确认的活动安排;c)进度;d)负责人。
《模具设计与开发计划》经质量和生产主管会签后报厂长批准后实施,并在进展中发生不适宜时及时地进行修改。
4.2设计输入:模具营业主管在接受模具合同前应组织模具设计(技术)主管,质量主管按《产品有关要求确认和评审控制程序》进行评审并由设计(技术)主管制定《设计输入及其评审记录》。
其中内容包括:a)客户的图纸和样件要求,及在合同里提出的有关产品功能和性能的要求;b)本公司关于设计文件的相关规定《加工工艺手册》。
c)对产品适用的有关法律法规的要求;d)其他要求。
如:产品的技术要求和技术规范等。
设计主管拟定完后,应组织质量主管、生产主管进行评审以确保其充分性,报厂长批准。
4.3设计输出:在模具产品设计中,设计输出有:4.3.1模具总装图,零部件图,并注明验收标准;4.3.2采购清单;4.3.3在只有产品样件情况下,应有模拟产品样件的产品图纸。
4.4在设计主管输出总装图、零部件图之后,由技术、质量、生产应对设计结构的合理性和材质的选择进行评审。
五金冲压模具模具设计开发控制程序

一、目的:为完善本公司之设计流程,确保设计质量。
二、适用范围:适用於本公司所有模具设计作业。
三、权责:设计课负责模具设计工作。
四、作业内容:1、设计和开发的输入:1.1与顾客签订合同或技术协议,由业务组开具【承接模具/工件明细单】(设计开模通知书)及客户之产品图转交设计课,设计课以此为根据进行设计和开发的输入工作;1.2设计和开发的输入要求,应符合客户订单/合同的要求。
1.3根据市场调研或分析,业务课提出设计和开发之建议,经总经理批准後,连同相关背景资料转交设计课;1.4综合公司内外反馈之信息,设计课以【新品承接检讨记录】提出开发或技术改进之建议,呈总经理批准,签署意见後,发回设计课。
2、设计和开发的输出;2.1设计课以输入的要求为依据,进行设计和开发,设计人员设计前应对产品图纸进行检查,确认图档比例、公差、技术条件及客户之设计要求。
2.2设计图纸展开前,应先按比例和公差整理产品图纸,经确认无误,再根据具体情况和客户之特殊要求确定展开系数后,方可展开。
2.3设计图纸之展开应由两个人分别展开,且贴图一致後,方可进行以下工序。
2.4模具设计方案之制定应优先考虑客户之要求,设计方案(模具工程总图)由设计人员提出,经组长/课长/经理许可,方可进行模具设计。
2.5在模具设计过程中,设计课长应随时追踪设计动作执行情况,填写【设计进度表】。
2.6模具设计时,如客户有设计规范则依客户设计规范进行,否则依公司内部设计规范进行。
2.7模具设计输入资料应包含:成品图、模具结构图、工序图、料表清单、详细加工图。
2.8设计完成後,设计员填写【请购单】【五金配件订购单】交组长及课长审批。
【五金配件订购单】先由仓库核对库存量,再由采购购买。
3、设计和开发的评审:3.1设计开发的评审应由设计课长和相关单位进行全面的评审。
3.2当评审结果满足时,则进行设计和开发的验证。
3.3当评审结果不满足时,则需会知总经理,进行与客户沟通协商参照《客户服务管理程序》4、设计和开发的验证:4.1为了确保设计和开发的结果满足客户的需求,则由设计课下达图纸至生产相关单位进行产品的验证即试模。
五金冲压模具模具设计开发控制程序

一、目的:為完善本公司之設計流程,確保設計質量。
二、適用範圍:適用於本公司所有模具設計作業。
三、權責:設計課負責模具設計工作。
四、作業內容:1、設計和開發的輸入:與顧客簽訂合同或技術協議,由業務組開具【承接模具/工件明細單】(設計開模通知書)及客戶之產品圖轉交設計課,設計課以此為根據進行設計和開發的輸入工作;設計和開發的輸入要求,應符合客戶訂單/合同的要求。
根據市場調研或分析,業務課提出設計和開發之建議,經總經理批准後,連同相關背景資料轉交設計課;綜合公司內外反饋之信息,設計課以【新品承接檢討記錄】提出開發或技術改進之建議,呈總經理批准,簽署意見後,發回設計課。
2、設計和開發的輸出;設計課以輸入的要求為依據,進行設計和開發,設計人員設計前應對產品圖紙進行檢查,確認圖檔比例、公差、技朮條件及客戶之設計要求。
設計圖紙展開前,應先按比例和公差整理產品圖紙,經確認無誤,再根據具體情況和客戶之特殊要求確定展開系數后,方可展開。
設計圖紙之展開應由兩個人分別展開,且貼圖一致後,方可進行以下工序。
模具設計方案之制定應優先考慮客戶之要求,設計方案(模具工程總圖)由設計人員提出,經組長/課長/經理許可,方可進行模具設計。
在模具設計過程中,設計課長應隨時追蹤設計動作執行情況,填寫【設計進度表】。
模具設計時,如客戶有設計規范則依客戶設計規范進行,否則依公司內部設計規范進行。
模具設計輸入資料應包含:成品圖、模具結構圖、工序圖、料表清單、詳細加工圖。
設計完成後,設計員填寫【請購單】【五金配件訂購單】交組長及課長審批。
【五金配件訂購單】先由倉庫核對庫存量,再由采購購買。
3、設計和開發的評審:設計開發的評審應由設計課長和相關單位進行全面的評審。
當評審結果滿足時,則進行設計和開發的驗證。
當評審結果不滿足時,則需會知總經理,進行與客戶溝通協商參照《客戶服務管理程序》4、設計和開發的驗證:為了確保設計和開發的結果滿足客戶的需求,則由設計課下達圖紙至生產相關單位進行產品的驗證即試模。
冲压模具开发过程及管控要点
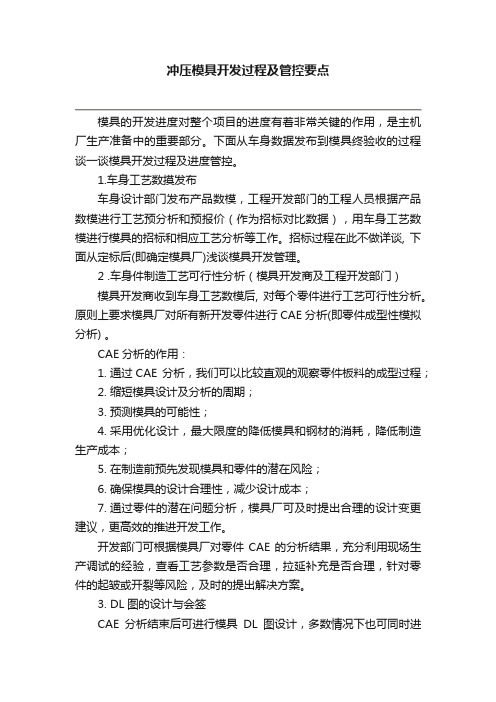
冲压模具开发过程及管控要点模具的开发进度对整个项目的进度有着非常关键的作用,是主机厂生产准备中的重要部分。
下面从车身数据发布到模具终验收的过程谈一谈模具开发过程及进度管控。
1.车身工艺数摸发布车身设计部门发布产品数模,工程开发部门的工程人员根据产品数模进行工艺预分析和预报价(作为招标对比数据),用车身工艺数模进行模具的招标和相应工艺分析等工作。
招标过程在此不做详谈, 下面从定标后(即确定模具厂)浅谈模具开发管理。
2 .车身件制造工艺可行性分析(模具开发商及工程开发部门)模具开发商收到车身工艺数模后, 对每个零件进行工艺可行性分析。
原则上要求模具厂对所有新开发零件进行CAE 分析(即零件成型性模拟分析) 。
CAE分析的作用:1.通过CAE 分析,我们可以比较直观的观察零件板料的成型过程;2.缩短模具设计及分析的周期;3.预测模具的可能性;4.采用优化设计,最大限度的降低模具和钢材的消耗,降低制造生产成本;5.在制造前预先发现模具和零件的潜在风险;6.确保模具的设计合理性,减少设计成本;7.通过零件的潜在问题分析,模具厂可及时提出合理的设计变更建议,更高效的推进开发工作。
开发部门可根据模具厂对零件CAE的分析结果,充分利用现场生产调试的经验,查看工艺参数是否合理,拉延补充是否合理,针对零件的起皱或开裂等风险,及时的提出解决方案。
3. DL图的设计与会签CAE分析结束后可进行模具DL图设计,多数情况下也可同时进行。
DL图设计即design layout—冲压工序分析设计,也可称为模具工艺流程图,包含:零件料片的尺寸、冲压的方向与角度、冲压的工序安排、送料方向、废料刀分布及刃口方向、废料排除方向示意、CH 孔、左右件标识、各工序标注等。
同时,DL图还需体现相关工序的冲压设备、模具高度、模具材质、压边圈或压料板的工作行程、板料的定位方式、完成工序的压力分析等。
DL设计完成后,原则上在模具厂应完成内部审核,内部审核问题整改完成后即可提供给主机厂的开发部门,并进行会签,DL图的会签非常关键,直接导致后期模具的设计,并且对后期模具开发周期也有较大的影响,若DL图后期再更改,则开发周期和成本上都将造成很大的浪费,工程开发部门主要审核零件工艺的合理性、机台参数的正确性、工艺补充的合理性、材料利用率、并结合压机情况审查送料方便性等。
五金冲压模具设计步骤流程详解

五金冲压模具设计步骤流程详解五金冲压模具设计有哪些步骤和流程?为你讲解如下:一.冲压模具分类“冲压模具依构造可分为单工程模、复合模、连续模三大类。
前两类需较多人力不符经济效益,连续模可大量生产效率高。
同样,设计一套高速精密连续冲模,也要对你所生产的产品(包含所有用冲压加工出来的产品,富士康集团主要有端子、电脑机壳以及连接器上用的小五金及目前的手机零件等等)。
设计连续冲模需注意各模组之间的间距、零件加工精度、组立精度、配合精度与干涉问题,以达到连续模自动化大量生产的目的。
二.单元化设计之概念:“冲压模具整体构造可分成二大部分:(1).共通部分(2).依制品而变动的部分。
共通部分可加以标准化或规格化,依制品而变动的部分是难以规格化。
三.模板之构成及规格1.模板之构成“冲压模具之构成将依模具种类及构成及相异,有顺配置型构造与逆配置型构造二大类。
前者是最常使用的构造,後者构造主要用於引伸成形模具或配合特殊模具。
从事的主要工作包括:(1)数字化制图——将三维产品及模具模型转换为常规加工中用的二维工程图;(2)模具的数字化设计——根据产品模型与设计意图,建立相关的模具三维实体模型;(3)模具的数字化分析仿真——根据产品成形工艺条件,进行模具零件的结构分析、热分析、疲劳分析和模具的运动分析;(4)产品成形过程模拟——注塑成形、冲压成形;(5)定制适合本公司模具设计标准件及标准设计过程;(6)模具生产管理。
2.模具之规格(1).模具尺寸与锁紧螺丝“模板之尺寸应大於工作区域,并选择标准模板尺寸。
模板锁紧螺丝之位置配置与模具种类及模板尺寸有关。
其中单工程模具最常使用锁紧螺丝配置於四边角,最标准形式工作区域可广大使用。
长形之模具及连续模具最常使用锁紧螺丝配置於四边角及中间位置。
(2).模板之厚度“模板之厚度选择与模具之构造、冲压加工种类、冲压加工加工力、冲压加工精度等有绝对关系。
依据理论计算决定模具之厚度是困难的,一般上系由经验求得,设计使用的模板厚度种类宜尽量少,配合模具高度及夹紧高度加以标准化以便利采购及库存管理。
- 1、下载文档前请自行甄别文档内容的完整性,平台不提供额外的编辑、内容补充、找答案等附加服务。
- 2、"仅部分预览"的文档,不可在线预览部分如存在完整性等问题,可反馈申请退款(可完整预览的文档不适用该条件!)。
- 3、如文档侵犯您的权益,请联系客服反馈,我们会尽快为您处理(人工客服工作时间:9:00-18:30)。
一、目的:
為完善本公司之設計流程,確保設計質量。
二、適用範圍:
適用於本公司所有模具設計作業。
三、權責:
設計課負責模具設計工作。
四、作業內容:
1、設計和開發的輸入:
1.1與顧客簽訂合同或技術協議,由業務組開具【承接模具/工件明細
單】(設計開模通知書)及客戶之產品圖轉交設計課,設計課以此為根據進行設計和開發的輸入工作;
1.2設計和開發的輸入要求,應符合客戶訂單/合同的要求。
1.3根據市場調研或分析,業務課提出設計和開發之建議,經總經理批
准後,連同相關背景資料轉交設計課;
1.4綜合公司內外反饋之信息,設計課以【新品承接檢討記錄】提出開
發或技術改進之建議,呈總經理批准,簽署意見後,發回設計課。
2、設計和開發的輸出;
2.1設計課以輸入的要求為依據,進行設計和開發,設計人員設計前應
對產品圖紙進行檢查,確認圖檔比例、公差、技朮條件及客戶之設計要求。
2.2設計圖紙展開前,應先按比例和公差整理產品圖紙,經確認無誤,
再根據具體情況和客戶之特殊要求確定展開系數后,方可展開。
2.3設計圖紙之展開應由兩個人分別展開,且貼圖一致後,方可進行以
下工序。
2.4模具設計方案之制定應優先考慮客戶之要求,設計方案(模具工程
總圖)由設計人員提出,經組長/課長/經理許可,方可進行模具設計。
2.5在模具設計過程中,設計課長應隨時追蹤設計動作執行情況,填寫
【設計進度表】。
2.6模具設計時,如客戶有設計規范則依客戶設計規范進行,否則依公
司內部設計規范進行。
2.7模具設計輸入資料應包含:成品圖、模具結構圖、工序圖、料表清
單、詳細加工圖。
2.8設計完成後,設計員填寫【請購單】【五金配件訂購單】交組長及
課長審批。
【五金配件訂購單】先由倉庫核對庫存量,再由采購購買。
3、設計和開發的評審:
3.1設計開發的評審應由設計課長和相關單位進行全面的評審。
3.2當評審結果滿足時,則進行設計和開發的驗證。
3.3當評審結果不滿足時,則需會知總經理,進行與客戶溝通協商參照
《客戶服務管理程序》
4、設計和開發的驗證:
4.1為了確保設計和開發的結果滿足客戶的需求,則由設計課下達圖紙
至生產相關單位進行產品的驗證即試模。
4.2試模之產品需進行檢驗,由品管課進行產品檢驗工作,並將結果記
錄於【產品全尺寸檢驗報告】中,由將結果發至設計及相關單位,由設計及相關單位根據試模之結果判斷設計和開發的驗證結果。
4.3如驗證結果不符合客戶之要求時,由設計課與相關生產單位進行驗
證結果的商討。
需設計課進行圖紙的變更改進或生產相關單位進行工程變更作業,參照《工程變更管理程序》。
4.4如改進之後的試模結果滿足客戶要求時,則由設計課下達最新的設
計圖紙至相關單位進行模具的生產作業,並將試模時之發的圖紙進行通知修改必要時進行回收後發放最新圖紙。
4.5如最終試模的結果不能滿足客戶要求時,則會知總經理,進行與客
戶溝通進行修模參照《工程變更管理程序》
4.6試模的結果需達到能滿足客戶的合同/訂單之要求。
5、設計和開發的確認:
5.1設計和開發進行最後的輸出時,應由業務組將產品發送給客戶,並
由設計課將產品之圖紙電子檔案發送給客戶。
由客戶根據合同/訂單要求進行最終的產品與圖紙的確認工作。
6、設計和開發的更改:
6.1模具圖紙的更改,見《工程變更管理程序》
五、相關文件與資料:
《工程變更管理程序》
《客戶服務管理程序》
六、相關表單與記錄:
承接模具/工件明細單 TT-QR-TE-07 新品承接檢討記錄 TT-QR-TI-02設計進度表 TT-QR-TI-03 請購單 TT-QR-TI-04 五金配件訂購單 TT-QR-TI-05產品全尺寸檢驗報告 TT-QR-TD-03。