刃口尺寸的计算
凸、凹模刃口尺寸的计算
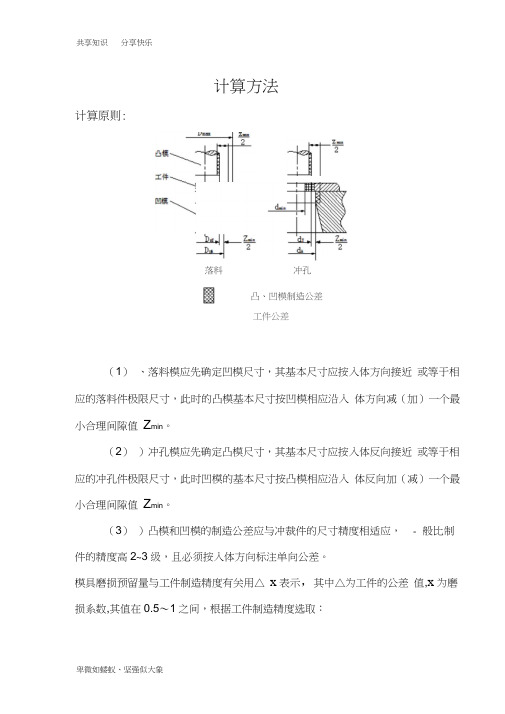
工件公差(1) 、落料模应先确定凹模尺寸,其基本尺寸应按入体方向接近 或等于相应的落料件极限尺寸,此时的凸模基本尺寸按凹模相应沿入 体方向减(加)一个最小合理间隙值 Z min 。
(2) )冲孔模应先确定凸模尺寸,其基本尺寸应按入体反向接近 或等于相应的冲孔件极限尺寸,此时凹模的基本尺寸按凸模相应沿入 体反向加(减)一个最小合理间隙值 Z min 。
(3) )凸模和凹模的制造公差应与冲裁件的尺寸精度相适应, - 般比制件的精度高2~3级,且必须按入体方向标注单向公差。
模具磨损预留量与工件制造精度有关用△ x 表示,其中△为工件的公差 值,x 为磨损系数,其值在0.5〜1之间,根据工件制造精度选取:计算原则:计算方法落料 冲孔凸、凹模制造公差工件精度IT10级以上X =1.0工件精度IT11〜13X =0.75工件精度IT14X =0.5规则形状冲裁模凸模、凹模制造偏差51、分别加工法§凸+ §凹W Z max- Z min落料D凹=(D max - X △0D凸=(D凹-Z min )二凸=(D max - X △Z min )」凸冲孔d凸=(d min + X △) 1凸d凹=(d凸+ Z min ) 0 = ( d min + X△Z min ) 0孔心距孔心距属于磨损后基本不变的尺寸,在同一工步中,在工件上冲出的孔距为L±2/2两个孔时,其凹模型孔心距L d可按下式确定。
L d =L+ —■-8:凸、「•凹一一凸、凹模制造公差,可按IT6〜IT7级来选取,或取、•凸W0.4 ( Z max- Z min ) , '•凹W0.6 ( Z max" Z min )2、单配加工法单配加工法是用凸模和凹模相互单配的方法来保证合理间隙的一种方法。
此方法只需计算基准件(冲孔时为凸模,落料时为凹模)基本尺寸及公差,另一件不需标注尺寸,仅注明“相应尺寸按凸模(或凹模)配做,保证双面间隙在Z max〜Z min之间”即可。
凸凹模刃口尺寸的计算
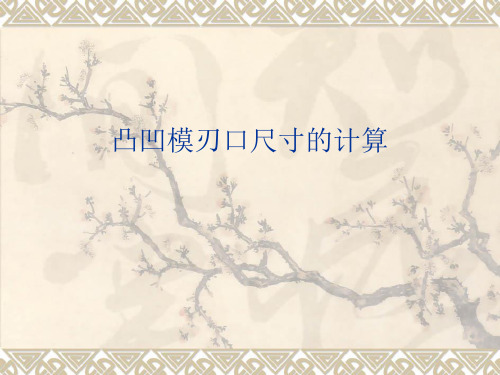
尺寸计算方法
2)落料
尺寸计算方法
dp、dd——别为冲孔凸模和凹模尺寸
Dp、Dd——分别喂落料凸模和凹模尺寸
——共建的迟早公差 D、d——分别为落料件和孔的基本尺寸 Zmin——最小合理间隙(双边) X——磨损系数,与制造精度有关
⊿
尺寸计算方法
凸模与凹模配合加工 适用于形状复杂或薄板料的冲裁件 根据冲裁件结构尺寸的不同类型,分别加以 对待。具体方法如下:
凸凹模刃口尺寸的计算
尺寸计算准则
凸模和凹模刃口尺寸直接决定工件的尺寸和
பைடு நூலகம்
模具间隙的大小,是模具上最重要的尺寸。 1、刃口尺寸计算的基本原则: 1)由于冲孔落料件都是测量其光亮带部分的 尺寸,而冲孔的光亮带是凸模挤入而形成。 落料的光亮带是落料件挤入凹模型孔形成。 故冲孔时孔的尺寸由凸模决定,落料时的外 形尺寸由凹模决定。
尺寸计算方法
第三类:凸模磨损后没有变化的尺寸,分三种 情况: (1)孔尺寸的标注为C+ ⊿时: Cp=(C+0.5 ⊿ )±&p (2)孔尺寸的标注为C+ ⊿时: Cp=(C-0.5 ⊿ )±&p (3)孔尺寸的标注为C ±⊿’时: Cp =C ±&p
2.
落料时应以凹模为基准件来配做凸模,并按
凹模磨损后尺寸变大、变小、不变的规律分 三种类型进行计算。 第一类:当凹模磨损后变大的尺寸 Ad=(A-x⊿) +&d
第二类:当凹模磨损后变小的尺寸,
Bd=(B+x ⊿ )-&d
尺寸计算方法
第三类:当凹模磨损后没有变化的尺寸
(1)冲裁件尺寸标注为C+ ⊿时: Cd=(C+0.5 ⊿ )±&d (2)冲裁件尺寸标注为C+ ⊿时: Cd=(C-0.5 ⊿ )±&d (3)冲裁件尺寸标注为C ±⊿’时: Cd=C ±&d
冲压模具刃口尺寸的计算
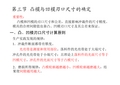
DT = (D A − Z min )−δ t = (35.69 − 0.04) 0 0.016 mm = 35.650 0.016 mm − −
0
校核:0.016 + 0.025 = 0.04 > 0.02(不能满足间隙公差条件) 因此,只有缩小,提高制造精度,才能保证间隙在合理范围内, 由此可取:
计算原则: 1.设计落料模先确定凹模刃口尺寸。以凹模为基准,根据冲模的 磨损规律,凹模基本尺寸应取接近或等于工件的最小极限尺寸; 则与之配合的凸模的基本尺寸为凹模基本尺寸减去Zmin(间隙取 在凸模上,即冲裁间隙通过减小凸模刃口尺寸来取得)。 2. 设计冲孔模先确定凸模刃口尺寸。以凸模为基准,根据冲模 的磨损规律,凸模基本尺寸应取接近或等于工件的最大极限尺 寸;则与之配合的凹模的基本尺寸为凸模基本尺寸加上Zmin(间 隙取在凹模上,冲裁间隙通过增大凹模刃口尺寸来取得)。 3.模具刃口的制造公差,一般根据制件的公差等级进行确定, 通常要比制件的公差等级高出2-4级。常按工件相应部位公差 值的1/4来计算。
Z min = 0.10mm
落料凹模、凸模的尺寸如下图所示。
落料凸、凹模尺寸 a) 落料凹模尺寸 b) 落料凸模尺寸
三、例2
如右图所示的落料件,其中
a = 80
0 − 0.42
mm
b = 40
0 −0.34
mm c = 35
0 − 0 .34
mm
d = 22±0.14mm
e = 15
0 − 0.12
mm
板料厚度t=1mm,材料为10号钢。试计算 冲裁件的凸模、凹模刃口尺寸及制造公差。 解:该冲裁件属落料件,选凹模为设计基准件,只需要计算落 料凹模刃口尺寸及制造公差,凸模刃口尺寸由凹模实际尺寸按 间隙要求配作。 由表查得:
冲裁凸、凹模刃口尺寸计算

2.7.3 冲裁凸、凹模刃口尺寸计算
[例2-1] 用分开制造计算图2-72所示零件的凸凹模 刃口尺寸。
图2-72 零件图
解:1、确定基本工序 内形:冲孔。外形:落料 2、画磨损曲线
2.7.3 冲裁凸、凹模刃口尺寸计算
① 冲孔 画凸模刃口的磨损曲线如图2-73
② 落料 画凹模刃口的磨损曲线。如图2-74
按上(1)、(2)之法可得出: 冲孔磨后变大的公式
δ 凹 a凸 (a max x)0
(2-28) (2-29)
a凹 (a凸 Z min)0 δ 凸
落料磨后变小的公式
δ 凹 B凸 (B凹 Z min)0
(2-30) (2-31)
B凹 (Bmin x)0 δ 凸
0 0.52
2.7.3 冲裁凸、凹模刃口尺寸计算
尺寸Ⅳ、Ⅴ:25( )为落料磨后变大. Δ=0.52→IT14→X=0.5 A凹1 =(A1max-xΔ) =(25-0.5×0.52) =24.74 A凸1=( A凹1- Zmin) =(24.74-0.24) =24.5 尺寸Ⅵ: 7为落料单边磨后变大, Δ=0.2→IT13→X=0.75 A凹2=(A2max-xΔ) =(7-0.750.2)=6.85 A凸2=( A凸2 - )=(6.85-)=(6.85-0.12) =6.73
0.2 0
2.7.3 冲裁凸、凹模刃口尺寸计算
尺寸Ⅳ、Ⅴ:25( )为落料磨后变大. Δ=0.52→IT14→X=0.5 A凹1 =(A1max-xΔ) =(25-0.5×0.52) =24.74 A凸1=( A凹1- Zmin) =(24.74-0.24) =24.5 尺寸Ⅵ: 7为落料单边磨后变大, Δ=0.2→IT13→X=0.75 A凹2=(A2max-xΔ) =(7-0.750.2)=6.85 A凸2=( A凸2 - )=(6.85-)=(6.85-0.12) =6.73
凸、凹模刃口尺寸计算
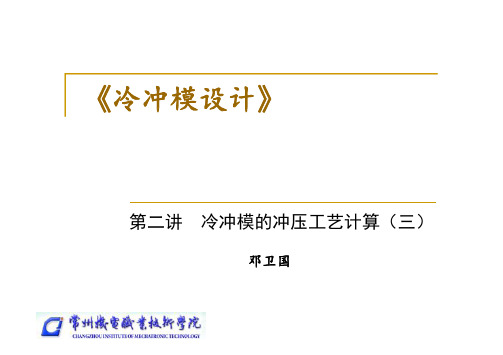
《冷冲模设计》第二讲冷冲模的冲压工艺计算(三)邓卫国第二讲冷冲模的冲压工艺计算(三)第三部分凸、凹模刃口尺寸的确定凹模与凸模的刃口尺寸计算定义:什么叫刃口尺寸:刃口尺寸指在凹模和凸模零件图上分别标注尺寸及公差值,这个值与冲压产品尺寸精度有关。
⏹学习目标☐掌握凸、凹模刃口计算作用☐掌握凸、凹模刃口尺寸计算的依据和原则☐掌握凸、凹模刃口尺寸计算的方法二、冲裁模凸、凹模刃口尺寸的确定1、冲裁模凸、凹模刃口计算的作用冲裁件的尺寸精度主要取决于凸、凹模的刃口部分尺寸。
并且合理的冲裁间隙也靠凸、凹模刃口尺寸保证。
凸模刃口尺寸示意图所以冲裁模刃口设计是冲裁模设计的重点。
凹模刃口尺寸示意图二、冲裁模凸、凹模刃口的确定2、凸、凹模刃口尺寸计算的依据在生产实践中发现:a.由于凸凹模之间存在间隙,冲裁件断面都带有锥度。
依据:①光亮带是冲压件测量和使用部位;②落料件的光亮带,是因凹模刃口挤切材料产生的;③冲孔件的光亮带,是因凸模刃口挤切材料产生的;④落料件的大端(光亮带)尺寸等于凹模尺寸;⑤冲孔件的小端(光亮带)尺寸等于凸模尺寸。
b.凸模轮廓越磨越小,凹模轮廓越磨越大,结果使间隙越用越大。
结论:在计算冲裁模刃口尺寸时,应按落料、冲孔两种情况分别进行计算。
二、冲裁模凸、凹模刃口尺寸确定3、冲裁模凸、凹模刃口计算的原则(一)(1)设计落料模先确定凹模刃口尺寸以凹模为基准,间隙取在凸模上,即冲裁间隙通过减小凸模刃口尺寸来取得;设计冲孔模先确定凸模刃口尺寸以凸模为基准,间隙取在凹模上,冲裁间隙通过增大凹模刃口尺寸来取得。
二、冲裁模凸、凹模刃口尺寸的确定4、冲裁模凸、凹模刃口计算的原则(二)(2)根据冲模在使用过程中的磨损规律:设计落料模时:凹模基本尺寸应取接近或等于零件的最小极限尺寸;设计冲孔模时:凸模基本尺寸则取接近或等于冲件孔的最大极限尺寸。
理由:凸、凹模在磨损到一定程度时,仍能冲出合格的零件。
二、冲裁模凸、凹模刃口尺寸确定5、冲裁模凸、凹模刃口计算的原则(三)(3)凹模和凸模制造公差主要与冲裁件的精度有关①一般冲模精度较零件精度高3~4级;②形状简单的圆形、方形刃口,其制造偏差值可按IT6~IT7级来选取,或查表;③形状复杂的刃口制造偏差可按零件相应部位公差值的1/4来选取;④刃口尺寸磨损后无变化的制造偏差值可取冲件相应部位公差值的l/8并冠(±);⑤若零件没有标注公差,则可按IT14级取值。
冲裁间隙及凸凹模刃口尺寸计算
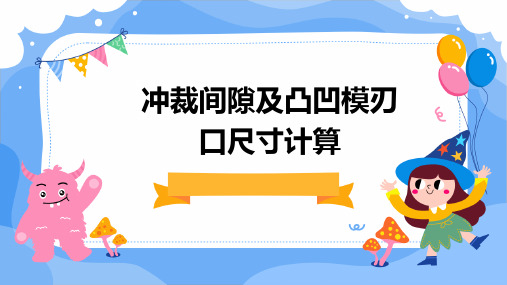
凹模刃口尺寸计算
根据凸模刃口尺寸和冲裁间隙,计算凹模刃口的基本尺寸 。
考虑凹模的磨损和刃磨修正等因素,对刃口尺寸进行修正 。
03
冲裁间隙计算
理论计算方法
弹性变形
考虑材料在冲裁过程中的弹性变 形,通过弹性力学理论计算间隙
值。
塑性变形
基于塑性力学理论,分析材料在冲 裁过程中的流动和应力分布,以确 定合理的间隙值。
冲裁间隙及凸凹模刃 口尺寸计算
目录
• 引言 • 冲裁间隙概述 • 冲裁间隙概述 • 冲裁间隙计算 • 凸凹模刃口尺寸计算 • 实际应用案例 • 结论与展望
01
引言
目的和背景
目的
冲裁间隙及凸凹模刃口尺寸计算 是冲压工艺中的重要环节,其目 的是确保冲裁件的质量和模具的 寿命。
背景
随着制造业的发展,对冲压工艺 的要求越来越高,合理的冲裁间 隙及凸凹模刃口尺寸是实现高效 、高质量冲压的关键。
报告结构
01
本报告将详细介绍冲裁间隙及凸 凹模刃口尺寸的计算方法。
02
报告将分为以下几个部分:冲裁 间隙的概念和作用、凸凹模刃口 尺寸的计算、实际应用案例分析 以及结论。
02
冲裁间隙概述
凸料厚度,计算凸模刃口的基本尺 寸。
考虑凸模的磨损和热处理变形等因素,对刃口尺寸进行修正 。
凹模刃口尺寸计算公式
根据冲裁件的尺寸和公差要求,结合凹模的结构 形式,采用相应的计算公式来确定凹模的刃口尺 寸。
考虑因素
凹模刃口尺寸计算时需考虑冲裁件的形状、尺寸 精度、材料厚度、模具结构等因素。
3
精度要求
凹模刃口尺寸的精度要求较高,一般要求达到 ±0.01mm以内。
刃口尺寸修正
修正原因
加工中心常用计算公式

加工中心常用计算公式加工中心作为一种高精度、高效率的数控机床,广泛应用于航空、汽车、电子、模具、仪器仪表等领域,用于进行零件的精密加工。
在加工中心的加工过程中,有一些常用的计算公式,用于确定刀具的尺寸、工件的位置、加工速度等参数,下面介绍一些常见的加工公式。
一、刀具尺寸计算公式在加工中心的加工过程中,刀具的尺寸是非常关键的,直接影响到加工精度和表面质量。
以下是一些常见的刀具尺寸计算公式:1. 切削深度(a)的计算公式:a = (D1 - D2) × cosα其中,D1为刀具刃口直径,D2为末刃直径,α为刀具倾角。
2.刀具半径(R)的计算公式:R=(D1-D2)/23. 圆柱刀具的公法圆半径(Rc)的计算公式:Rc = R / cos(α/2)其中,α为圆柱刀具的圆锥度。
二、工件位置计算公式在加工中心的加工过程中,确定工件在机床坐标系中的位置是非常重要的。
以下是一些常见的工件位置计算公式:1. 相对初始位置(X,Y,Z)的计算公式:X = X0 + l × cosα × cosβ,Y = Y0 + l × sinα × cosβ,Z = Z0 + l × sinβ其中,(X0,Y0,Z0)为初始位置坐标,l为距离,α为水平方向角度,β为竖直方向角度。
2. 相对初始位置(X,Y)的计算公式(仅在水平加工中使用):X = X0 + l × cosα,Y = Y0 + l × sinα其中,(X0,Y0)为初始位置坐标,l为距离,α为方向角度。
三、进给速度计算公式进给速度是指刀具在加工过程中前进的速度,是保证加工精度和效率的重要参数。
以下是一些常见的进给速度计算公式:1.进给速度(V)的计算公式:V=N×f×z其中,N为主轴转速,f为切削速度,z为刀具刃口数量。
2.切削速度(f)的计算公式:f=π×D×N其中,D为刀具直径,N为主轴转速。
第二章冲裁三.凸、凹模刃口尺寸的计算
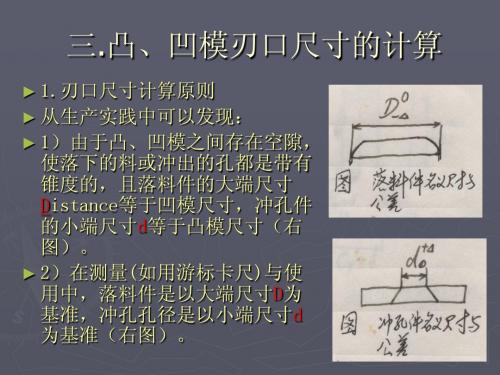
► c.确定刃口公差δ
► 配合加工的公差值要由计算决定(而在分开加工
时要查表):
模具偏差带宽度= 工件偏差带宽度 4 对A类、B类:=
4
1
对C类:需根据工件尺寸的三种可能表示形式确 定,模具也有三种或两种可能表示形式如下: ► 工件: ±Δ 0~+Δ -Δ ~0 ► 模具:
► 3)确定冲裁刃口制造公差时,应考虑制件的
精度Δ 要求。如果对刃口精度δ 要求过高 (即制造公差Δ 过小),会使模具制造困难, 增加成本,延长生产周期;如刃口精度δ 要 求过低(即制造公差Δ 过大),则生产出来 的零件可能不合格,或使模具的寿命降低。 零件精度Δ 与模具制造精度δ 的关系见表2.1 (P11)。若零件没有标注公差(P17)„„
2.刃口尺寸计算方法
(1)凸、凹模分开加工(圆形 或方形工件,且满足不等式) ► ①已知落料件的尺寸与公差如 右图,其尺寸由凹模刃口确定。 先求凹模:因凹模刃口使用磨 损后会变大,所以名义尺寸预先比
►
D取小一些(- Δ )。另外“孔”取正公差+δ d : Dd=(D-xΔ )0+δ d (2.3) 式中xΔ代表磨损量,取孔的偏小值,0.5<x≤1,系数 x查P18表2.7。 再求凸模:Dp=(Dd-Zmin)0 –δ p =(D-xΔ -Zmin)0 –δ p 凸模相当于“轴”取负公差-δ p。 公差δ d和δ p查P18表2.6。
► 3)冲裁时,凸、凹模要与冲裁零件或废料发
生摩擦,凸模愈磨愈小,凹模愈磨愈大,结 果使间隙愈用愈大。
3)冲裁时,凸、凹模要与冲裁零件或废料发生摩 擦,凸模愈磨愈小,凹模愈磨愈大,结果使间隙 愈用愈大。 ► 在决定模具刃口尺寸及其制造公差时,需考虑下述原则: 1)落料制件尺寸由凹模尺寸决定。故设计落料模 时,以凹模为基准,间隙取在凸模上;设计冲孔 模时,以凸模为基准,间隙取在凹模上。 2)考虑到冲裁中凸、凹模的磨损,设计落料模时,凹模基 本尺寸应取工件尺寸公差范围内的较小尺寸;设计冲孔 模时,凸模基本尺寸则应取工件孔的尺寸公差范围内的 较大尺寸。这样,在凸、凹模磨损到一定程度的情况 下,仍能冲出合格零件。凸、凹模间隙则取最小合理间 隙值。
【最新资料】凸、凹模刃口尺寸的计算
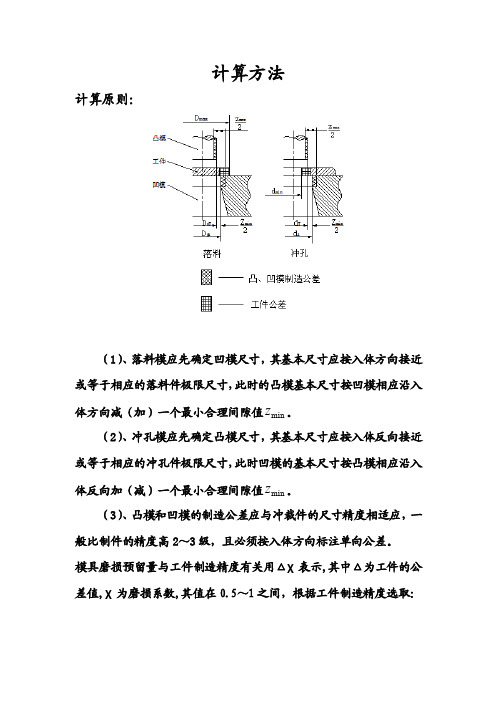
计算方法计算原则:(1)、落料模应先确定凹模尺寸,其基本尺寸应按入体方向接近或等于相应的落料件极限尺寸,此时的凸模基本尺寸按凹模相应沿入z。
体方向减(加)一个最小合理间隙值min(2)、冲孔模应先确定凸模尺寸,其基本尺寸应按入体反向接近或等于相应的冲孔件极限尺寸,此时凹模的基本尺寸按凸模相应沿入z。
体反向加(减)一个最小合理间隙值min(3)、凸模和凹模的制造公差应与冲裁件的尺寸精度相适应,一般比制件的精度高2~3级,且必须按入体方向标注单向公差。
模具磨损预留量与工件制造精度有关用△χ表示,其中△为工件的公差值,χ为磨损系数,其值在0.5~1之间,根据工件制造精度选取:工件精度IT10级以上χ=1.0工件精度IT11~13 χ=0.75工件精度IT14 χ=0.5规则形状冲裁模凸模、凹模制造偏差δ凸模和凹模分别加工时间隙变动范围1、 分别加工法凸δ+凹δ≤max Z -min Z 落料凹D =(max D -χ△)凹δ+0凸D =(凹D -min Z )0凸δ-=(max D -χ△-minZ )0凸δ- 冲孔凸d =(min d +χ△)0凸δ-凹d =(凸d +min Z )凹δ+0=(min d +χ△+min Z )凹δ+0孔心距孔心距属于磨损后基本不变的尺寸,在同一工步中,在工件上冲出的孔距为L ±Δ/2两个孔时,其凹模型孔心距d L 可按下式确定。
d L =L+∆81凸δ、凹δ——凸、凹模制造公差,可按IT6~IT7级来选取,或取 凸δ≤0.4(max Z -min Z ) , 凹δ≤0.6(max Z -min Z )2、 单配加工法单配加工法是用凸模和凹模相互单配的方法来保证合理间隙的一种方法。
此方法只需计算基准件(冲孔时为凸模,落料时为凹模)基本尺寸及公差,另一件不需标注尺寸,仅注明“相应尺寸按凸模(或凹模)配做,保证双面间隙在max Z ~min Z 之间”即可。
在制件上,会同时有三类不同性质的尺寸,需要区别对待, 第一类:凸模(冲孔件)或凹模(落料件)磨损后增大的尺寸;第一类基准尺寸=(冲裁件上该尺寸的最大极限-χ△)4/0∆+第二类:凸模(冲孔件)或凹模(落料件)磨损后减小的尺寸;第二类基准尺寸=(冲裁件上该尺寸的最小极限+χ△)04/∆- 第三类:凸模(冲孔件)或凹模(落料件)磨损后基本不变的尺寸。
刃口尺寸的计算
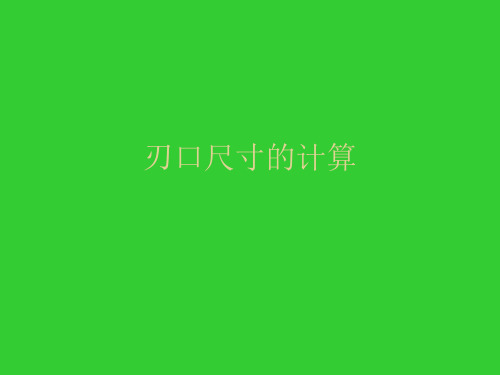
二、凸、凹模刃口尺寸的计算方法(续)
1.按凸模与凹模图样分别加工法(续)
为了保证可能的初始间隙不超过Zmax,即
T A
+Zmin≤Zmax,选取必须满足以下条件: T A ≤ Z max Z min
凸、凹模的制造公差,可按IT6~IT7级来选取,也可 查表2.4.1选取,但需校核。或取
刃口尺寸的计算
一、凸、凹模刃口尺寸计算原则
1.设计落料模先确定凹模刃口尺寸。以凹 模为基准,间隙取在凸模上,即冲裁间隙 通过减小凸模刃口尺寸来取得。 设计冲孔模先确定凸模刃口尺寸。以凸 模为基准,间隙取在凹模上,冲裁间隙通 过增大凹模刃口尺寸来取得。
凸、凹模刃口尺寸计算原则
2.根据冲模在使用过程中的磨损规律,设 计落料模时,凹模基本尺寸应取接近或等 于工件的最小极限尺寸; 设计冲孔模时,凸模基本尺寸则取接近 或等于工件孔的最大极限尺寸。 模具磨损预留量与工件制造精度有关。
A
0 0
DT D A Z min T Dmax x Z min T
(2)冲孔 0 d T d min x T
d A dT Z min 0
1 8
ห้องสมุดไป่ตู้A
d min x Z min 0
A
(3)孔心距
凸、凹模刃口尺寸计算原则
3.冲裁(设计)间隙一般选用最小合理间 隙值(Zmin)。
4.选择模具刃口制造公差时,要考虑工件 精度与模具精度的关系,即要保证工件的 精度要求,又要保证有合理的间隙值。 5.工件尺寸公差与冲模刃口尺寸的制造偏 差原则上都应按“入体”原则标注为单向 公差。但对于磨损后无变化的尺寸,一般 标注双向偏差。
计算凸、凹模刃口尺寸及公差xiugai
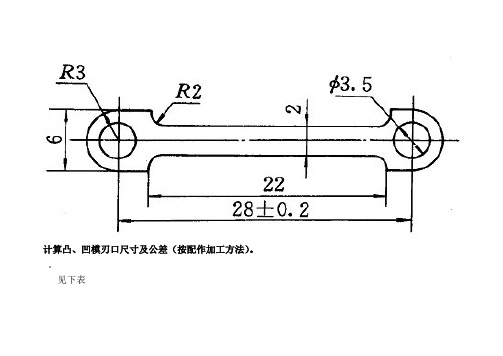
R2
22+0.52
R2+0.25
B凸= (Bmax+x⊿)-⊿/4
0.5
0.5
22.26-0.13
2.13-0.063
随基本刃口磨损而变小(凸模尺寸),
∮3.5
∮3.5+0.3
0.5
与凸模实际刃口配做
3.65-0.075
C类:随基本刃口磨损而不变(凸模的位置尺寸),
28
28+0.2
C凹=C+⊿/8
零件尺寸性质
尺寸分类
公差标注
计算公式
X值取定
凸模刃口
B类,零件尺寸随基本(凸模)刃口磨损而变小
∮3.5
∮3.5+0.3
B凸= (Bmax+x⊿)-⊿/4
0.5
3.65-0.பைடு நூலகம்75
凸凹模刃口尺寸配做,要求保证双面间隙0.05—0.07 mm。
合并以上计算:凹模、凸模图纸尺寸标注尺寸;凸凹模不标注尺寸,只注明配作关系及配作间隙。
计算凸、凹模刃口尺寸及公差(按配作加工方法)。
。
见下表
落料凹模:外形落料,尺寸公差等级皆为IT14级:
零件尺寸性质
尺寸分类
公差标注
计算公式
X值取定
凹模刃口
A类,零件尺寸随基本(凹模)刃口磨损而变大
6
2
R3
6--0.3
2--0.25
A凹= (Amax--x⊿)+⊿/4
0.75
0.75
5.8+0.075
28+0.5
1.81+0.063
2.9+0.038
B类,零件尺寸随基本(凹模)刃口磨损而变小
刀刃刃口尺寸计算公式
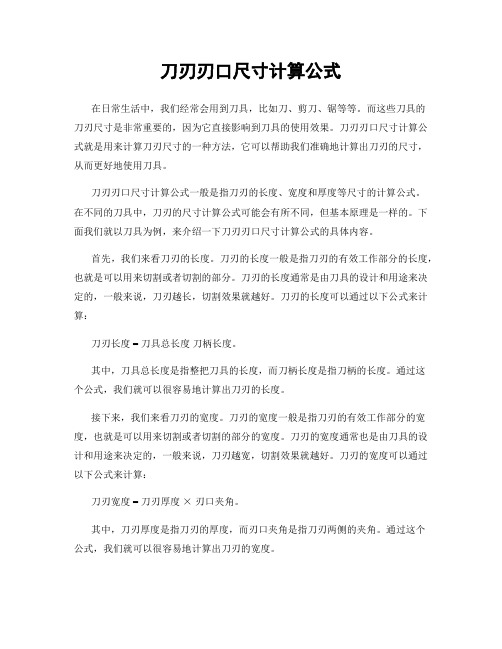
刀刃刃口尺寸计算公式在日常生活中,我们经常会用到刀具,比如刀、剪刀、锯等等。
而这些刀具的刀刃尺寸是非常重要的,因为它直接影响到刀具的使用效果。
刀刃刃口尺寸计算公式就是用来计算刀刃尺寸的一种方法,它可以帮助我们准确地计算出刀刃的尺寸,从而更好地使用刀具。
刀刃刃口尺寸计算公式一般是指刀刃的长度、宽度和厚度等尺寸的计算公式。
在不同的刀具中,刀刃的尺寸计算公式可能会有所不同,但基本原理是一样的。
下面我们就以刀具为例,来介绍一下刀刃刃口尺寸计算公式的具体内容。
首先,我们来看刀刃的长度。
刀刃的长度一般是指刀刃的有效工作部分的长度,也就是可以用来切割或者切割的部分。
刀刃的长度通常是由刀具的设计和用途来决定的,一般来说,刀刃越长,切割效果就越好。
刀刃的长度可以通过以下公式来计算:刀刃长度 = 刀具总长度刀柄长度。
其中,刀具总长度是指整把刀具的长度,而刀柄长度是指刀柄的长度。
通过这个公式,我们就可以很容易地计算出刀刃的长度。
接下来,我们来看刀刃的宽度。
刀刃的宽度一般是指刀刃的有效工作部分的宽度,也就是可以用来切割或者切割的部分的宽度。
刀刃的宽度通常也是由刀具的设计和用途来决定的,一般来说,刀刃越宽,切割效果就越好。
刀刃的宽度可以通过以下公式来计算:刀刃宽度 = 刀刃厚度×刃口夹角。
其中,刀刃厚度是指刀刃的厚度,而刃口夹角是指刀刃两侧的夹角。
通过这个公式,我们就可以很容易地计算出刀刃的宽度。
最后,我们来看刀刃的厚度。
刀刃的厚度一般是指刀刃的有效工作部分的厚度,也就是可以用来切割或者切割的部分的厚度。
刀刃的厚度通常也是由刀具的设计和用途来决定的,一般来说,刀刃越厚,切割效果就越好。
刀刃的厚度可以通过以下公式来计算:刀刃厚度 = 刀刃宽度÷刃口夹角。
通过以上的介绍,我们可以看到,刀刃刃口尺寸计算公式是非常重要的,它可以帮助我们准确地计算出刀刃的尺寸,从而更好地使用刀具。
当我们需要购买刀具或者使用刀具时,可以根据这些计算公式来选择合适的刀具,从而更好地满足我们的需要。
刀刃刃口尺寸计算公式
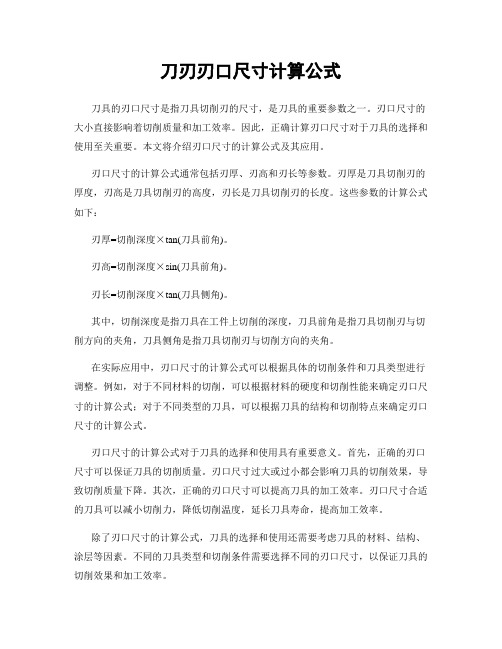
刀刃刃口尺寸计算公式刀具的刃口尺寸是指刀具切削刃的尺寸,是刀具的重要参数之一。
刃口尺寸的大小直接影响着切削质量和加工效率。
因此,正确计算刃口尺寸对于刀具的选择和使用至关重要。
本文将介绍刃口尺寸的计算公式及其应用。
刃口尺寸的计算公式通常包括刃厚、刃高和刃长等参数。
刃厚是刀具切削刃的厚度,刃高是刀具切削刃的高度,刃长是刀具切削刃的长度。
这些参数的计算公式如下:刃厚=切削深度×tan(刀具前角)。
刃高=切削深度×sin(刀具前角)。
刃长=切削深度×tan(刀具侧角)。
其中,切削深度是指刀具在工件上切削的深度,刀具前角是指刀具切削刃与切削方向的夹角,刀具侧角是指刀具切削刃与切削方向的夹角。
在实际应用中,刃口尺寸的计算公式可以根据具体的切削条件和刀具类型进行调整。
例如,对于不同材料的切削,可以根据材料的硬度和切削性能来确定刃口尺寸的计算公式;对于不同类型的刀具,可以根据刀具的结构和切削特点来确定刃口尺寸的计算公式。
刃口尺寸的计算公式对于刀具的选择和使用具有重要意义。
首先,正确的刃口尺寸可以保证刀具的切削质量。
刃口尺寸过大或过小都会影响刀具的切削效果,导致切削质量下降。
其次,正确的刃口尺寸可以提高刀具的加工效率。
刃口尺寸合适的刀具可以减小切削力,降低切削温度,延长刀具寿命,提高加工效率。
除了刃口尺寸的计算公式,刀具的选择和使用还需要考虑刀具的材料、结构、涂层等因素。
不同的刀具类型和切削条件需要选择不同的刃口尺寸,以保证刀具的切削效果和加工效率。
在实际应用中,刃口尺寸的计算可以通过刀具厂家提供的刀具参数表来进行,也可以通过切削力模型和切削仿真软件来进行。
通过这些手段,可以更加准确地确定刃口尺寸,提高刀具的切削效果和加工效率。
总之,刃口尺寸的计算公式是刀具选择和使用的重要参考依据。
正确的刃口尺寸可以保证刀具的切削质量和加工效率,提高加工质量和效率。
因此,刃口尺寸的计算应该引起我们的重视,加强研究和应用。
刃口尺寸计算范文
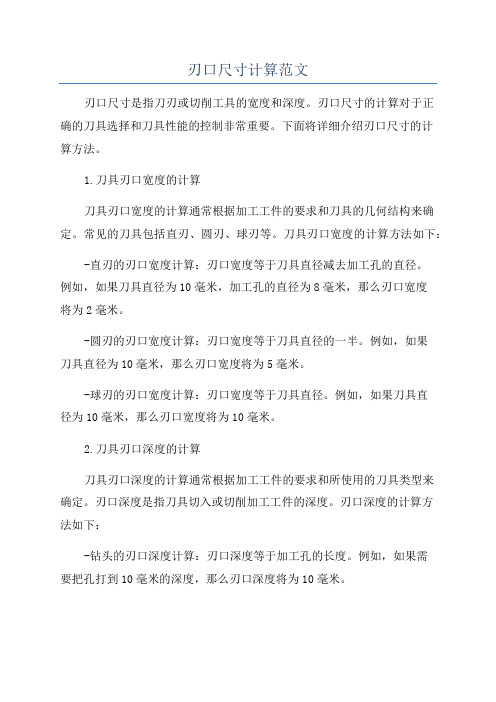
刃口尺寸计算范文刃口尺寸是指刀刃或切削工具的宽度和深度。
刃口尺寸的计算对于正确的刀具选择和刀具性能的控制非常重要。
下面将详细介绍刃口尺寸的计算方法。
1.刀具刃口宽度的计算刀具刃口宽度的计算通常根据加工工件的要求和刀具的几何结构来确定。
常见的刀具包括直刃、圆刃、球刃等。
刀具刃口宽度的计算方法如下:-直刃的刃口宽度计算:刃口宽度等于刀具直径减去加工孔的直径。
例如,如果刀具直径为10毫米,加工孔的直径为8毫米,那么刃口宽度将为2毫米。
-圆刃的刃口宽度计算:刃口宽度等于刀具直径的一半。
例如,如果刀具直径为10毫米,那么刃口宽度将为5毫米。
-球刃的刃口宽度计算:刃口宽度等于刀具直径。
例如,如果刀具直径为10毫米,那么刃口宽度将为10毫米。
2.刀具刃口深度的计算刀具刃口深度的计算通常根据加工工件的要求和所使用的刀具类型来确定。
刃口深度是指刀具切入或切削加工工件的深度。
刃口深度的计算方法如下:-钻头的刃口深度计算:刃口深度等于加工孔的长度。
例如,如果需要把孔打到10毫米的深度,那么刃口深度将为10毫米。
-铣刀的刃口深度计算:刃口深度等于刀具有效切削长度的一半。
有效切削长度是指刀具的刀尖到刀片支撑的部分的长度。
例如,如果刀具的有效切削长度为20毫米,那么刃口深度将为10毫米。
3.刀具磨损对刃口尺寸的影响刀具磨损会使刃口尺寸变大或变小,这可能影响刀具的切削性能和加工结果。
因此,在使用刀具之前和之后,应该对刀具进行检查和测量,以确保刃口尺寸符合要求。
4.提高刃口尺寸的方法有时,需要提高刃口尺寸以满足特定的加工要求。
-使用较大直径的刀具或刀片。
-使用带有刃口扩大器的刀具。
刃口扩大器是一种附件,可以将刀具的刃口尺寸扩大到所需的尺寸。
-进行粗加工后再进行细加工。
通过先使用较大刀具进行粗加工,然后再使用较小刀具进行细加工,可以达到所需的刃口尺寸。
综上所述,刃口尺寸的计算对于正确的刀具选择和刀具性能的控制非常重要。
通过准确计算刃口宽度和深度,可以确保刀具能够满足加工要求,并获得良好的加工效果。
刀具的尺寸量计算公式
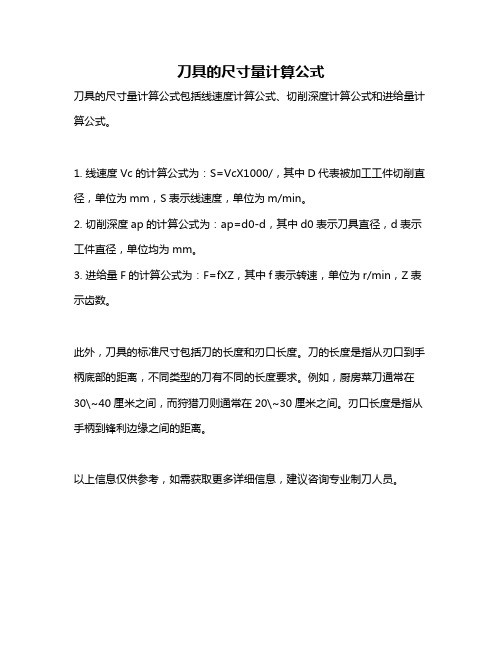
刀具的尺寸量计算公式
刀具的尺寸量计算公式包括线速度计算公式、切削深度计算公式和进给量计算公式。
1. 线速度Vc的计算公式为:S=VcX1000/,其中D代表被加工工件切削直径,单位为mm,S表示线速度,单位为m/min。
2. 切削深度ap的计算公式为:ap=d0-d,其中d0表示刀具直径,d表示工件直径,单位均为mm。
3. 进给量F的计算公式为:F=fXZ,其中f表示转速,单位为r/min,Z表示齿数。
此外,刀具的标准尺寸包括刀的长度和刃口长度。
刀的长度是指从刃口到手柄底部的距离,不同类型的刀有不同的长度要求。
例如,厨房菜刀通常在30\~40厘米之间,而狩猎刀则通常在20\~30厘米之间。
刃口长度是指从手柄到锋利边缘之间的距离。
以上信息仅供参考,如需获取更多详细信息,建议咨询专业制刀人员。
课题十八:刃口尺寸偏差的计算和凸凹模材料(2)
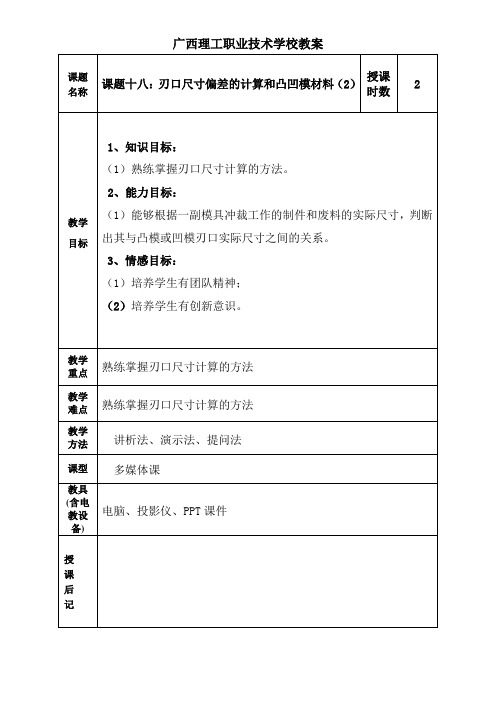
教学过程教学环节及时间分配教学内容及过程教师活动学生活动设计思路组织教学(2分钟)1.检查班级学生出勤及着装情况,集中学生注意力。
2.准备上课。
1.点名,组织学生分组1.课前预习2.准备相关学习工具和资料。
整顿课前纪律,集中学生注意力,调整学生上课状态。
新课导入(5分钟)在前面的课程中我们学习了刃口尺寸计算的基本原则,今天我们就来学习刃口尺寸计算的方法。
导入新课 1. 听讲、思考并回答问题2. 明确本次课任务利用信息化技术创设情境,提高学生的学习兴趣教学过程(70分钟)在标注模具刃口尺寸偏差和制件刃口尺寸偏差时,一般按“入体”原则标注。
所谓“入体”原则,是指标注工件尺寸偏差时应向材料实体方向单向标注。
1)轴尺寸按基轴制标注,上偏差为零,下偏差为负,即d2)孔尺寸按基孔制标注,上偏差为正,下偏差为零,即D3)对于中心距等尺寸标注对称上下标,即A模具刃口尺寸偏差标注对模具制造的实际间隙影响很大。
在实际制造中,为了减少模具刃口制造误差对间隙的影响,有分开加工和配合加工两种加工方法,偏差的计算也不同。
1.凸模与凹模分开加工采用这种方法,是指凸模和凹模分别按图样加工。
要分别标注凸模、凹模刃口基本尺寸制造公差,适用于圆形或形状简单的制件。
模具制造公差一般按IT6~IT8加工,规则形状(圆形、方形)件冲裁时凸模、凹模的制造公差可查表2-5求得。
教师通过PPT 讲解、视频、实物展示、操作演示。
学生认真听讲、思考并回答问题。
模仿练习。
通过讲解新知识和技能、实操演示等手段,帮助学生完成任务。
为了保证初始间隙值小于最大合理间隙 ,必须满足:| |+| |≤ - 在不满足上式时,则取:=0.4( - ) =0.6( - )例2-6 图2-45是图2-1敞开模加工的制件尺寸图,制件材料为10号钢,厚度为1.0mm 。
试求凸模与凹模刃口尺寸。
解: 图2-45 制件尺寸图①、该制件是由落料工序获得,故求刃口尺寸以凹模为基准。
- 1、下载文档前请自行甄别文档内容的完整性,平台不提供额外的编辑、内容补充、找答案等附加服务。
- 2、"仅部分预览"的文档,不可在线预览部分如存在完整性等问题,可反馈申请退款(可完整预览的文档不适用该条件!)。
- 3、如文档侵犯您的权益,请联系客服反馈,我们会尽快为您处理(人工客服工作时间:9:00-18:30)。
DA Zmin
0 T
Dmax x Zmin
0 T
(2)冲孔
dT
ห้องสมุดไป่ตู้d min
x
0 T
dA
dT
Zmin
A 0
dmin x Zmin
A 0
(3)孔心距
Ld
=L±
1 8
二、凸、凹模刃口尺寸的计算方法(续)
1.按凸模与凹模图样分别加工法(续)
为了保证可能的初始间隙不超过Zmax,即 T A +Zmin≤Zmax,选取必须满足以下条件:
(3)刃口制造偏差可按工件相应部位公差值的1/4来选取。对于 刃口尺寸磨损后无变化的制造偏差值可取工件相应部位公差值的 1/8并冠以(±)。
三、例1
冲制图示零件,材料为Q235钢,料厚 t=0.5mm。计算冲裁凸、凹模刃口尺寸及 公差。
解:由图可知,该零件属于无特殊要求 的一般冲孔、落料。
外形
36
DT
DA
Zmin
0 t
(35.69 0.04)00.016 mm 35.6500.016 mm
校核:0.016 + 0.025 = 0.04 > 0.02(不能满足间隙公差条件)
因此,只有缩小,提高制造精度,才能保证间隙在合理范围内, 由此可取:
T ≤ 0.4Zmax Zmin =0.4×0.02=0.008mm
0.008 + 0.012 ≤ 0.06 - 0.04
0.02 = 0.02(满足间隙公差条件)
三、例1(续)
孔距尺寸: Ld =L±=18±0.125×2×0.09 = (18±0.023)mm
落料:
DA
Dmax
x
A 0
(36 0.5 0.62)00.025mm 35.6900.025mm
T A ≤ Z max Z min
凸、凹模的制造公差,可按IT6~IT7级来选取,也可 查表2.4.1选取,但需校核。或取
T ≤ 0.4 Zmax Zmin A ≤ 0.6 Zmax Zmin
二、凸、凹模刃口尺寸的计算方法(续)
2.凸模与凹模配作法 配作法就是先按设计尺寸制出一个基准件(凸模或凹模),
刃口尺寸的计算
一、凸、凹模刃口尺寸计算原则
1.设计落料模先确定凹模刃口尺寸。以凹 模为基准,间隙取在凸模上,即冲裁间隙 通过减小凸模刃口尺寸来取得。 设计冲孔模先确定凸模刃口尺寸。以凸 模为基准,间隙取在凹模上,冲裁间隙通 过增大凹模刃口尺寸来取得。
凸、凹模刃口尺寸计算原则
2.根据冲模在使用过程中的磨损规律,设 计落料模时,凹模基本尺寸应取接近或等 于工件的最小极限尺寸; 设计冲孔模时,凸模基本尺寸则取接近 或等于工件孔的最大极限尺寸。 模具磨损预留量与工件制造精度有关。
0.75;
36
0 0.62
mm为IT14级,取x
=
0.5;
设凸、凹模分别按IT6和IT7级加工制造,则
冲孔:dT
d m in
x
0 T
(6
0.75
0.12)
0 0.008
6.0900.008
dA
dT
Zmin
A 0
(6.09 0.04)00.012 mm 6.1300.012 mm
校核: T A ≤ Z max Z min
A ≤ 0.6 Zmax Zmin =0.6×0.02=0.012mm
三、例1(续)
故:
DA
35
.69
0.012 0
mm
DT
35
.65
0 0.008
mm
三、例2
如图2.4.3所示的落料件,其中 a
80
0 0.42
mm
b
40
0 0.34
mm
c
35
0 0.34
mm
d = 22±0.14mm
e
0 0.62
mm
由落料获得, 2
60.12 0
mm
和18±0.09由冲孔同时获得。查表2.3.3得,
Zmin 0.04mm , Zmax 0.06mm ,则
Zmax Zmin (0.06 0.04)mm 0.02mm
三、例1(续)
由公差表查得:
2
6
0.12 0
mm为IT12级,取x
=
凸、凹模刃口尺寸计算原则
3.冲裁(设计)间隙一般选用最小合理间 隙值(Zmin)。
4.选择模具刃口制造公差时,要考虑工件 精度与模具精度的关系,即要保证工件的 精度要求,又要保证有合理的间隙值。
5.工件尺寸公差与冲模刃口尺寸的制造偏 差原则上都应按“入体”原则标注为单向 公差。但对于磨损后无变化的尺寸,一般 标注双向偏差。
二、凸、凹模刃口尺寸的计算方法
加工方法: 1.分开加工 具有互换性、制造周期短,但Zmin不易保证,
需提高加工精度,增加制造难度。 2.配合加工 Zmin易保证,无互换性、制造周期长。
二、凸、凹模刃口尺寸的计算方法(续)
1.按凸模与凹模图样分别加工法
(1)落料
DA
Dmax
x
A 0
DT
15
0 0.12
mm
板料厚度t=1mm,材料为10号钢。试计算
冲裁件的凸模、凹模刃口尺寸及制造公差。
解:该冲裁件属落料件,选凹模为设计基准件,只需要计算落料 凹模刃口尺寸及制造公差,凸模刃口尺寸由凹模实际尺寸按间隙 要求配作。
由表2.3.3查得: Zmin 0.10mm , Zmax 0.14mm
1 8
0.12mm
14.94
0.015mm
落料凸模的基本尺寸与凹模相同,分别是79.79mm,
39.75mm,34.75mm,22.07mm,14.94mm,不必标注公差,但
要在技术条件中注明:凸模实际刃口尺寸与落料凹模配制,保证
最小双面合理间隙值 Zmin 0.10mm
落料凹模、凸模的尺寸如图2.4.4。
mm
39.7500.085 mm
c凹
(35
0.75
0.34)
0
1 4
0.34
mm
34.7500.085 mm
三、例2(续)
第二类尺寸:磨损后减小的尺寸
d凹
(22
0.14
0.75
0.28)
0
1 4
0.28
mm
22.0700.070 mm
第三类尺寸:磨损后基本不变的尺寸
e凹
(15
0.5
0.12)
然后根据基准件的实际尺寸再按最小合理间隙配制另一件。
特点: 模具的间隙由配制保证,工艺比较简单,不必校核
T A ≤ Zmax Zmin的条件,并且还可放大基准件的制造公差, 使制造容易。
二、凸、凹模刃口尺寸的计算方法(续)
2.凸模与凹模配作法(续)
(1)根据磨损后轮廓变化情况,正确判断出模具刃口尺寸类型: 磨损后变大,变小还是不变。 (2)根据尺寸类型,采用不同计算公式。 磨损后变大的尺寸,采用分开加工时的落料凹模尺寸计算公式。 磨损后变小的尺寸,采用分开加工时的冲孔凸模尺寸计算公式。 磨损后不变的尺寸,采用分开加工时的孔心距尺寸计算公式。
三、例2(续)
由公差表查得:
尺寸80mm,选x = 0.5;尺寸15 mm,选x = 1;其余尺寸均选 x = 0.75。
落料凹模的基本尺寸计算如下:
第一类尺寸:磨损后增大的尺寸
a凹
(80
0.5
0.42)
0
1 4
0.42
mm
79.7900.105 mm
b凹
(40
0.75
0.34)0
1 4
0.34