基于汽车梁类件的回弹计算及补偿系统
汽车轻量化中辊压成形的关键技术

汽车的白车身减重是轻量化的重要内容。
辊压件是白车身的重要构件。
本文介绍了汽车中辊压成形的应用及关键技术,特别是高强钢的辊压成形中的回弹、变形能以及扭曲、侧弯、边波等缺陷的预防和解决办法。
开发了多代保险杠、防撞杆、门槛等辊压件产品。
对于辊压成形国内外先进技术的发展作了介绍。
汽车轻量化中的辊压件为减少能源消耗和环境污染,汽车轻量化成为世界各国汽车制造的新趋势。
白车身作为汽车的重要部件,占到总车重量的40%左右,因此白车身的减重优化成为轻量化设计的重要内容。
目前国际上新车型白车身开发设计,广泛采用先进高强度钢板,其中有相当部分的构件,诸如前后保险杠、门梁、框轨、车顶弓型架、车身的B柱及底盘等构件,都是由辊压成形制造方式完成的。
辊压成形工艺广泛应用于汽车部件的制造,汽车上很多部件是由辊压工艺生产的(图1)。
辊压成形工艺与传统冲压相比,具有高效、节材、环保、成本低等突出优点,成为汽车部件制造工艺方法之一。
据统计采用辊压工艺制造的汽车部件,大约为车重的10%左右。
图1 辊压工艺生产的汽车零件辊压成形是通过顺序配置的多道次成形轧辊,把卷材、带材等金属板带不断地进行弯曲,以制成特定断面的型材。
辊压成形与其他板金属成形的工艺相比,具有以下优点:⑴生产效率高,适合于大批量生产,和冲压、折弯工艺相比提高效率10倍以上,制造成本大幅降低。
⑵加工产品的长度基本不受限制,可以连续生产。
⑶产品的表面质量好,尺寸精度高。
⑷在辊压成形生产线上可以集成其他的加工工艺,如冲孔、焊接、压花等。
⑸与热轧和冲压工艺相比能够节约材料15%~30%。
⑹生产噪声低,无环境污染。
辊压成形工艺加工出来的型材其断面结构合理、品种规格繁多、几何尺寸精确,体现了现代社会对材料轻型化、合理化、功能化的使用要求。
辊压成形是一种高效节能的工艺技术,符合“发展循环经济,创建节约社会”的政策要求。
辊压成形采用先进的高效生产工艺,使成形截面达到最好的力学性能。
高强钢辊压成形的关键技术先进高强度钢AHSS(Advanced High Strength Steel)具有优良的材料性能。
基于AutoForm的回弹补偿

文 章编 号 : 1 0 0 1 — 4 9 3 4 ( 2 0 1 7 ) 0 2 — 0 0 5 0 — 0 4
基 于 Au t o F o r m 的 回 弹 补 偿
成, 数 据之 间访 问能 实现 高度 的 参 数 化 以及 自动 化 , 极 大 地 提 高 了工 艺 回 弹 补 偿 的 效
率, 降低 了生 产 成 本 。 关键 词 :冲 压 模 具 ; 回 弹补 偿 ; Au t o F o r m 中 图 分 类 号 :T G 3 8 6 文献标识码 : B
求模 具 厂 商 进 一 步 压 缩 模 具 制 造 周 期 [ 2 - 3 ] , 而 压 缩 模 具 制 造 周 期 的 关 键 为 控 制 回弹 。若 要 减 少
回弹 整 改 次 数 , 需 在 前 期 制 定 切 实 有 效 的 回 弹 补偿策略 , 才能有效缩短模具制造周期 。
品 缺 陷 需 要 进 行 一 次 又 一 次 的模 具 整 改 , 延 长 了模 具 制 作 周 期 , 增 加 了生 产 成 本 。 当前 汽 车 行 业 竞 争 非 常 激 烈 , 要 求 汽 车 厂
Abs t r a c t:Bas e d on t he a na l y s i s r e s ul t s of Aut oFor m ,t he s pr i ngba c k of t he f i nal pr oc e s s i s c o m par e d wi t h t ha t of t he pr odu c t,a nd t he r e ve r s e c o mp ens a t i on i s ob t ai ne d a c c or di ng t o
基于AutoForm的汽车翼子板冲压回弹仿真及补偿研究

技术聚焦
* '(-% 回弹仿真结果界面
$% ## !" ## )% ##
$" ##
& '($% 优化后的压料板工艺模面 * '()% 优化后的压料板工艺模面 )% ##
+ '()% 回弹仿真结果界面
+ '(,% 优化后的压料板工艺模面 图 优化后的压料板工艺模面
将优化后的工艺模面再次导入 AutoForm求解计
, -./0:拉延
所示。
- -
技术聚焦
'()%
'(*%
'($%
'(+%
回弹
拉 重 压 修 重 压 翻 重 压 翻 拟最
延 力 料 边 力 料 边 力 料 边 检小
& & & &
具夹
冲
整
冲
状持
孔
形
孔
态
模
, 仅计算最终成形工序冲压回弹仿真流程
'()% 回 '(*% 回 '($% 回 '(+% 回弹
选取图 5所示回弹量较大的区域设置测点,分别 记为测点 、、、、、、,并在测点部位进行回弹量
取值,然后与图 6所示回弹量进行对比,对比结果如图
6所示。由图 6可知,两种不同模拟方法的最终回弹趋
势基本一致,翼子板多处回弹远大于制品±0.5mm的
尺寸精度要求,全工序均存在较大的回弹,且 OP10、
2021(3)
20技21术年聚3焦月
设计·创新
基于 %6*/A/.$ 的汽车翼子板 冲压回弹仿真及补偿研究 B
蒋磊 吕中原 王龙 谢蛟龙 马培兵 张雄飞
基于正交试验的车身覆盖件冲压成形回弹分析

( 华东 交通大 学 机 电工程学 院 , 昌 3 0 1 ) 南 3 0 3 Sp ig a k a ay i f t m pn 0 mi g f r h u o o y p e r b c n lss o a n s i g f r n o e a t b d an l t b s d o t o o a s a e n or g n ly t t h i e t
表 1 回弹 正 交试 验 因素 及水 平
有的等效节点力都趋于零时 ,其板料形状即为回弹后板料 的形 状 。由于此方 法无需进 行接触判断 ,故计算 时问较有模法少 。
D nfr y a m软件分析回弹 的方法采用 的是无模法 。其进行回弹过 o 程模拟的计算流程 , 图 2 如 所示。
W ANG n , IZ - u n, HOU Ch n — u Ni g ME i y a Z aggo
(col f caiaadeetnc] nier gE sC ia i tn nvri , acag30 1 ,hn ) Shoo hncl n l r iaE g e n ,at hn a ogU iesyN nhn 30 3 C ia Me ci n i Jo t
图 1等 截 面 直 梁 的纯 弯 曲
都有重要价值 。因此 , 薄板冲压回弹仿真计算及其应用技术不仅
由于采用平截面假定 , 两个横截 面 A1 1 A B B 和 2 2在弯矩 M
是薄板冲压成形领域 的热点问题 , 而且该研究对 回弹仿真的发展 作用下作相对旋转但仍皆垂直于梁的对称平面, 于是凸面 A A 12 和工业应用都具有重要意义。 的纵 向纤维受拉深而凹面 B1 2的纵 向纤维受压缩。 B 在垂直与对
典型汽车高强度钢板冲压产品回弹补偿研究
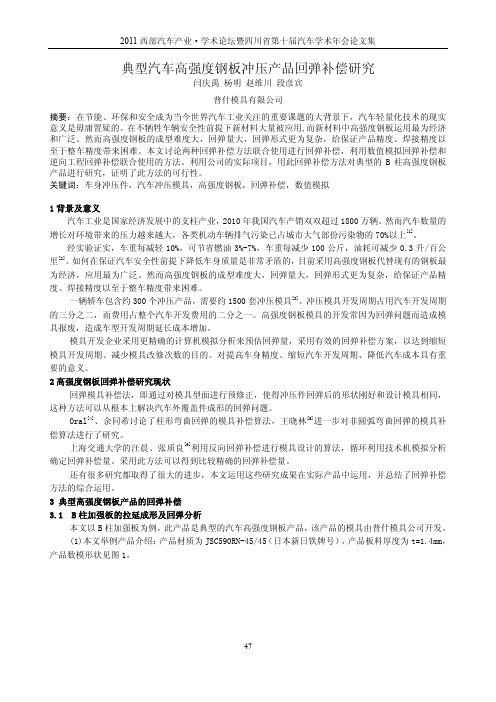
典型汽车高强度钢板冲压产品回弹补偿研究闫庆禹 杨明 赵维川 段彦宾普什模具有限公司摘要:在节能、环保和安全成为当今世界汽车工业关注的重要课题的大背景下,汽车轻量化技术的现实意义是毋庸置疑的。
在不牺牲车辆安全性前提下新材料大量被应用,而新材料中高强度钢板运用最为经济和广泛。
然而高强度钢板的成型难度大,回弹量大,回弹形式更为复杂,给保证产品精度、焊接精度以至于整车精度带来困难。
本文讨论两种回弹补偿方法联合使用进行回弹补偿,利用数值模拟回弹补偿和逆向工程回弹补偿联合使用的方法。
利用公司的实际项目,用此回弹补偿方法对典型的B柱高强度钢板产品进行研究,证明了此方法的可行性。
关键词:车身冲压件,汽车冲压模具,高强度钢板,回弹补偿,数值模拟1背景及意义汽车工业是国家经济发展中的支柱产业,2010年我国汽车产销双双超过1800万辆。
然而汽车数量的增长对环境带来的压力越来越大,各类机动车辆排气污染已占城市大气部份污染物的70%以上[1]。
经实验证实,车重每减轻10%,可节省燃油3%-7%,车重每减少100公斤,油耗可减少0.3升/百公里[2]。
如何在保证汽车安全性前提下降低车身质量是非常矛盾的,目前采用高强度钢板代替现有的钢板最为经济,应用最为广泛。
然而高强度钢板的成型难度大,回弹量大,回弹形式更为复杂,给保证产品精度、焊接精度以至于整车精度带来困难。
一辆轿车包含约300个冲压产品,需要约1500套冲压模具[3]。
冲压模具开发周期占用汽车开发周期的三分之二,而费用占整个汽车开发费用的二分之一。
高强度钢板模具的开发常因为回弹问题而造成模具报废,造成车型开发周期延长成本增加。
模具开发企业采用更精确的计算机模拟分析来预估回弹量,采用有效的回弹补偿方案,以达到缩短模具开发周期、减少模具改修次数的目的。
对提高车身精度、缩短汽车开发周期、降低汽车成本具有重要的意义。
2高强度钢板回弹补偿研究现状回弹模具补偿法,即通过对模具型面进行预修正,使得冲压件回弹后的形状刚好和设计模具相同,这种方法可以从根本上解决汽车外覆盖件成形的回弹问题。
基于仿真误差补偿模型的回弹补偿新方法

0 引言
回弹是薄板冲压成形过程中不可避免的物理 现象 , 是整个成形历史的累积效应 ,与模具几何 形状 、材料特性 、摩擦接触 、润滑状态等诸多因素 密切相关 ,所以回弹问题非常复杂[1] 。
仿真计算的误差 ,假定在冲压工艺条件及仿真参 数不变的情况下 ,回弹仿真误差在模具型面发生 小变形时基本保持不变 ;然后根据该仿真误差在 CAD 模型上进行反向补偿 ,获得仿真误差补偿模 型 ,并以该模型进行回弹仿真迭代计算 ,直到回弹 仿真计算的结果和误差补偿模型一致 。由于新方 法考虑了回弹仿真误差 ,因此可以大幅度地提高 零件的成形精度 。
如果模具没有经过设计补偿 ,则它的型面和 零件的 CAD 型面一致 ,如果经过了设计补偿则 由图 1 的流程可以看到 , 模具型面实际上是由 CAD 型面经过多次回弹仿真计算而来的 ,因此可 以把补偿后的模具型面视为由 CAD 型面经过弹 性变形而来 ,反之亦然 。由于弹性变形只改变形 状而不改变面积 ,所以 CAD 型面 、实际冲压件重 构型面 、回弹仿真型面上的点都应该存在一一对 应的关系 。由于形状发生了变化 ,因构型面进行网格划分也无法保证节点的映射 关系 。
图 3 基于仿真误差补偿模型实现模具补偿的过程
固定其中一个面 , 另一个面通过平移变换找到两 个面的重合点 ,然后围绕重合点通过旋转变换来 找到一个合适的相对位置 。这个相对位置要求整 个面的法向偏差分布比较均匀 , 而且实际冲压件 重构模型的节点和仿真结果模型的节点在位置上 应尽可能地对应 , 以确保法向偏差是在相同的位 置上进行计算的 。重合节点的寻找一般是先计算 出型面的几何中心 , 然后根据几何中心和冲压方 向找到相对应的单元及节点 ; 相对位置的旋转是 一个典型的优化过程 , 优化的参数为绕坐标轴的 三个旋转角度 ,可以采用遗传算法进行计算 ,适应 度函数可以表示为所有对应节点的距离总和 , 总 和越小表明相对位置越好 。 3. 3 曲面强制变形建立节点映射关系
车架纵梁回弹问题的解决

车架纵梁回弹问题的解决杨杰1[摘要]:纵梁在车架结构中,主要通过吸收碰撞动能来为车架承受载荷与冲击,属于最重要的吸能元件。
但其特殊的结构特征、材质以及料厚决定了其成形性差,易产生回弹、扭曲等严重质量问题,影响整车装配。
本文结合纵梁前段冲压工艺的优化过程,重点阐述了通过改变冲压件成形应力状态,使之发生充分塑性变形、以减小回弹的方法。
[关键字]:纵梁前段、回弹、高强钢1 引言车架要具有足够的强度和刚度,以承受汽车的载荷和从车轮和悬架传来的冲击。
车架由纵梁与其他零件共同组装构成。
纵梁是车架的基础件,决定着车身的刚性和耐冲击性。
当汽车发生碰撞的时候,其能量主要由车架的变形来吸收。
在车架前部的吸能结构中,纵梁是最重要的吸能元件,在车辆发生正面碰撞时,纵梁是继保险杠总成压溃失效后产生塑性变形以吸收碰撞动能的主要部件。
所以,纵梁是重要的安全部件①。
所以,对其尺寸精度与质量的严格要求,决定了它在车身结构中的特殊地位。
对于几字型截面冲压件来说,腹面、翼面落差较大,强度高,材料厚,成形困难。
本文结合工艺优化及现场调试,以江淮汽车股份公司某纵梁前段为例,通过对几字型截面纵梁冲压工艺的优化研究,浅析解决类似件回弹与扭曲问题的方法。
2零件工艺分析2.1 产品分析图1是某纵梁前段零件。
零件料厚2.0mm,材料为B410LA,外形尺寸2041 mm×119mm×131mm。
屈服强度σs≥ 420 Mpa,抗拉强度σb≥598 Mpa。
n值0.17,R45值0.71。
该件从端部开始,底面、腹面呈阶梯状变化,落差较大。
腹面及底面开有安装孔及定位过孔。
横截面呈几字型。
腹面高度(X:-307,Z:-70)至(X:267,Z:10)部分沿Z轴负向非均匀收边,高度差80mm。
端头有法兰。
底面内径自(X:-220,Z:-133)处开始,沿X轴,由72mm 收缩至59mm。
翼面有凸台等特征。
该件与多个件搭接,对匹配间隙的要求较高,如不合格,会导致焊点扭曲和强度不够,焊点严重凹陷等问题,最终影响焊接总成精度。
基于AUTOFORM的板料高强度钢零件回弹补偿研究及应用

对每一步增量:
式中为当前时间,T p是总的分析计算时间。
牛顿迭代公式如下:
式中K(i)为当前切向刚度矩阵;F(i)为施加的载荷向(i)为内应力向量。
e
式中σ(i)为当前主应力。
在当前刚度矩阵
力刚度的计算基于等效应。
当假象应力完全去除后,可得到回弹后的零件形状及其相应的残余应力回弹仿真的结果是否正确,还有一个最主要的影响因
会产生变化。
板料在冲压成型之前就有一定的应力应变。
这种情况下,
MPa,N值=0.152。
成型分析参数设置:压边圈行程为100mm,压边力为150T,摩擦系数为0.17,分析模型设置见图2。
成型分析结果如图3所示。
5高强度钢零件的回弹分析及回弹补偿
回弹分析采用静式隐力算法,如图4所示,回弹主要集中在两端和侧壁,最大反弹量有5mm。
从图4可以得出,该零件回弹量较大,达不到所需的品质要求,因此需要对零件进行回弹补偿计算。
由于产品的法兰面用压边圈,同时压边圈也存在较大的反弹量,为了保证产品的相对关系,需要对整个形面进行整体补偿计算。
通过三次迭代补偿后,反弹量控制在1mm以内,再加上对于高强度板的经验数据,需要多补偿2.5-3.0mm。
图1零件形状
图2模型设置图3分析结果图4回弹结果。
回弹补偿

第九章回弹补偿回弹补偿模块(SCP)是eta/DYNAFROM 5.6中新增加的一个用于工具回弹补偿计算的模块。
通过使用诸如铝合金、高强度钢以及超高强度钢之类的高级板料,既减轻了车体的重量,又保证了汽车的安全性能。
随着高级板料被越来越多的应用到车体制造中,金属冲压工业领域也涌现出若干新课题。
其中一个重要的课题就是成形后由于板料弹性回复和不均匀的应力分布导致的回弹现象。
传统上,回弹可以通过过度弯曲、整形等方式在车间解决。
现在在预测钣金零件回弹以及有效地对模具进行回弹补偿方面,冲压CAE软件扮演着一个重要的角色。
用户可以在经过拉延、修边和翻边等一系列工艺过程后采用冲压CAE 软件进行回弹分析。
但是如果要对原始模具曲面进行补偿以解决回弹问题,这就需要使用回弹补偿技术。
几十年来,回弹补偿都是依靠工程师的经验完成的。
如今,随着计算机硬件和软件技术的不断发展,回弹补偿可以方便地在如eta/DYNAFORM之类的CAE软件中得到解决。
在eta/DYNAFORM中,通过进行回弹补偿,可以修正回弹后的零件形状,从而达到所需零件设计的尺寸公差。
如图9.1所示,回弹补偿在一系列成形模拟和回弹分析之后进行。
图 9.1回弹补偿流程示意图在eta/DYNAFORM中,回弹补偿菜单如图9.2所示。
包括回弹补偿模块(COMPENSATION)、补偿结果检查(RESULT CHECK)、网格拓朴结构修复(TOPOLOGY REPAIR)、变形(MORPHING)和曲面映射(SURFACE MAPPING)功能。
下面将对每一个功能进行的详细介绍。
图9.2回弹补偿菜单9.1回弹补偿(COMPENSATION)在进行回弹补偿之前,用户需要分别导入回弹前和回弹后的结果文件(DYNAIN文件)。
同时,用户还需要导入上一步的工具网格(如果是第一次作回弹补偿,导入原始工具网格)。
如果一次补偿不能够得到期望的形状,可以采用多次迭代的方法来进行补偿。
Autoform_V4.1.1_模块介绍

Autoform V4.1.1 模块介绍Autoform为模具制造商和板料成形工业提供软件解决方案。
使用Autoform软件,可以提高工艺规划的可靠性、减少模具调试次数、缩短模具调试的周期,以最大的可信度提高零件和模具设计质量。
另外,也可以减少模具故障而导致压机停机的时间以及降低生产废品率等。
基于实践、工业技术的技巧和板料成形专家的经验,Autoform提供了一套完整的、集成化的系统,为产品开发过程链中的每一个阶段提供分析、审核和优化等高度专业化的功能。
在整个板料成形开发过程链中,Autoform融入了各种解决方案。
可以为小型和中型的公司提供各种独立的模块,也可以为大公司提供集成的多模块系统。
图1. 贯穿整个产品开发过程链的软件解决方案因为Autoform的软件模块完全集成化,这样在产品开发过程早期阶段的方案理念和结果能够容易地并直接地用于后面的阶段。
这就使客户能从同步工程的过程中获益,优化时间、成本和质量,从而使效率和生产率最大化。
PartDesigner零件设计模块这个模块可以帮助用户简单并快速地修改零件。
可成形性分析需要反复地对零件特征进行设计,重新设计的造型也需要反复的评价,直到确定零件成形牢靠。
为了快速并可靠完成可制造的零件设计,零件修改必须在实现上简单快速,可成形性模拟的结果也必须能够快速得到。
然后由设计人员确保最优化的产品造型被鉴定和被确认。
然而,依赖CAD系统并不是一个完成它的有效的方法。
零件设计模块是Autoform一步法模块的一个多方面的、易用的、补充的工具包,它可以实现零件的快速修改,这样就使复杂的设计实例在实际中可以贯彻实现。
OneStep一步法模块这个模块是板金零件可制造性分析的技术。
Autoform一步法模块在产品开发周期里有多个应用范围,涵盖产品可成形性分析,从材料成本优化到早期模具和工艺布局的辅助分析。
应用的多样化和用户的多样化,也就是产品设计人员和工程师、工艺和模具型面设计人员、材料和模具成本评估人员的多样化,由于Autoform一步法模块的易用性,并用相对简单的数据就可以运行一步法进行模拟计算,这是可能的。
汽车厚板料零件冲压成形分析及回弹计算

工 步 -7 4
工步
9 5
时 间 .12 0 + 0e
0 e 0 00 -0 2 2 e 0 00 一0 2 4 e 0 00 -0 2 6 0 00 0 e- 2 8 0 00 0 e- 2 0 0 00 0 e一 2
8 7 3 2 6 5 4 4 2 1 8
■
中国第 一汽车 股份 有 限公 司技术 中心
富 壮
随着 我 国 汽 车 板 料 零 件 设 计 、制 造 水 平 的 不 断
提 高 ,薄板料零件冲压成形C 技术 的应用 已 日趋 AE
成 熟 ,相 关 产 品 的设 计 和 制 造 部 门针 对 不 同软 件 及
1 厚 板料零 件 冲压成形及 其CA 技术 E 的特点
0 0 00 0 e+ 0
4 00 e 0 0 -0 2 32 0 0 2 0 e一 0 2. 0 0 2 40 e一 0 160 e- 0 . 0 02 8. 0 0 3 00 e一 0 0. 0 0 0 00 e+ 0
( ) 通 实体 单元 a 普
( )实体 厚 壳单元 b
工步 .1 时间 1 0 e 0 0 0 + 0 0
2 计算模型建立时需要注意 的问题
2 1 单元 选择 .
MS 软 件 有两种 单 元供 厚板 料零 件 冲压 成 C Mac r 形C E A 分析 时选 用 。一 种是 普通 实体 单 元 ,另 一种 是 实体 厚壳 单 元。 实体厚 壳 单元 是基于 选 择性缩减 积 分和假 定应 变 技术 的 ,由于是 八节 点拓 扑结 构 ,可 以实现 板料 内外
80 0 0 e一0 2 0 7 2 0 00 0 e~ 2
6 4 0 00 0 e- 2 5 60 e 0 0 -0 2 4. 0 0 2 80 e一 0
ThinkDesign_tooling 回弹补偿

© 2010 think3 China
GSM –回弹修改应用
© 2010 think3 China
全局形状建模技术(GSM)
应用GSM功能 修改回弹
© 2010 think3 China
问题:顶盖的修改
• 行业: 交通运输 • 产品: 汽车和摩托车研发CAD • 解决方案:
– Honda已使用ThinkCore垂直开发一些特定的功能,以解决其产品研发过程中的 一些关键问题
• 获益: – 提升产品质量同时,大大减少设计时间 – Thinkcore强大、灵活的特性使得Honda轻松解决之前很多以为极难改善的问题
© 2010 think3 China
交互式建模—ISM
• 允许对实体模型进行直接修改,无论是原生的还是导入的模型 • 解决因为导入的文件缺少历史特征而无法修改的问题 • 不必花费大量的时间去理解零件的建模过程,增强设计的创造力和产出
© 2010 think3 China
ThinkDesign 的解决方案
Step2:应用GSM快速修改。
© 2010 think3 China
ThinkDesign 的解决方案
Step3:结果验证,TD 提供了大量的检查工具,下面我们通过“斑马纹” 和“曲面曲率”来检查修改后的曲面。
• 与Think3合作 – Think3被视为处理关键研发问题的战略合作伙伴 – 与Think3在未来新项目研发方面保持合作 – Think3可以在其软件中使用双方合作的成果 – Honda把Think3的技术视为其独特竞争优势,而不会泄露任何细节给外界
© 2010 think3 China
¾ 世界领先的技术和全球化的研发网络
汽车车门外板全工序回弹分析与补偿的应用

•冲模技术•汽车车门外板全工序回弹分析与补偿的应用杜武昌,唐远柱天津柯麦特模具技术有限公司技术中心(天津300300)【摘要】随着我国的汽车工业不断发展,各车企之间的竞争也在不断加剧,在新车型的开发 过程中,车身外覆盖件外观质量和尺寸精度要求越来越高,从而给汽车模具生产行业也提 出更高的要求,汽车外覆盖件在冲压成形时会产生各种类型的缺陷,其中回弹仍是汽车冲 压行业的一个挑战。
通过一个成功的前车门外板案例,借助Autoform软件阐述一种汽车 外覆盖件全工序回弹分析和补偿的应用。
全工序模拟完全按照模具实际生产现场的边界 条件进行模拟,同时通过稳健性分析以确认各因子的影响,最终保证回弹补偿的准确性,可为汽车外覆盖件回弹补偿提供参考。
关键词:汽车外覆盖件;前车门外板;回弹;补偿;Autoform;全工序模拟中图分类号:TG385.2 文献标识码:BDOI :10.12147/ki.1671-3508.2020.05.008Application of Springback Simulation andCompensation of Automobile Door Outer Panel【Abstract】With the continuous development of the automobile industry in China,the competition between automobile companies is also increasing.In the process of developing new automobile,the quality and size accuracy of automobile panel are increasingly high.Thus to the die production industry also put forward higher requirements,the panel will produce various types of defects during stamping,springback is a challenge for the automobile stamping industry.Through a successful study of the front door outer panel,this paper expound the application of automobile panel process springback simulation and compensation with Autoform software.The full cycle simulation is done according to the boundary conditions of the actual production site of the die.A t the same time,the influence of each affecting factor is confirmed by the sigma simulation,and the accuracy of the springback compensation is finally guaranteed, which can provide reference for the springback compensation of the other automobile parts.Key words:automobile panel;front door otr;springback;compensation;Autoform;full cycle simulationi引言回弹仍是汽车冷冲压生产中最重要的问题,这是 冲压件生产时导致车身零件不合格的重要原因。
Autoform-R8-CAE分析回弹补偿方法
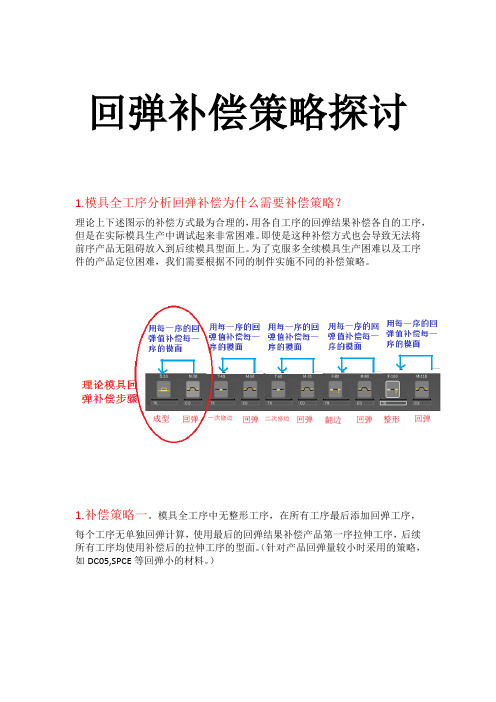
回弹补偿策略探讨1.模具全工序分析回弹补偿为什么需要补偿策略?理论上下述图示的补偿方式最为合理的,用各自工序的回弹结果补偿各自的工序,但是在实际模具生产中调试起来非常困难。
即使是这种补偿方式也会导致无法将前序产品无阻碍放入到后续模具型面上。
为了克服多全续模具生产困难以及工序件的产品定位困难,我们需要根据不同的制件实施不同的补偿策略。
1.补偿策略一。
模具全工序中无整形工序,在所有工序最后添加回弹工序,每个工序无单独回弹计算,使用最后的回弹结果补偿产品第一序拉伸工序,后续所有工序均使用补偿后的拉伸工序的型面。
(针对产品回弹量较小时采用的策略,如DC05,SPCE等回弹小的材料。
)autoform中实现回弹补偿的三种操作方式。
1.回弹补偿设置在模面工程中修改页面的最上方。
这种方式的优点是生成的模面质量高,产品回弹距离较大时,产品与重新生成的补充面以及压边圈能最大程度的还原原始位置关系。
缺点是回弹补偿功能的下方操作要重新生成,一些操作要重新指定点。
2.回弹补偿设置在模面工程中修改页面的最下方。
这种方式的优点是操作简单,无需重新生成修改页面的各项构建补充面操作,缺点是产品回弹距离较大时,产品与重新生成的补充面以及压边圈的还原原始位置关系方面稍差。
3.将模具的整个模面包括产品面,工艺补充,压边圈面全部进行回弹补偿操作。
这种方式前提是将整个模面以导入模具型面的方式,而不是导入产品,从而不激活模面工程。
新生成的回弹补偿工序会产生在产品修改界面中。
这种方式的优点是操作简单,无需重新生成模具型面的任何操作步骤,可生成后续模具相对于前序回弹的结果的反向补偿从而避免回弹后的产品无法放入后续工具体,缺点是产品回弹距离较大时,产品与重新生成的补充面以及压边圈的还原原始位置关系方面较差,此方式不适合在大的回弹时使用,或者可以使用第一种方式对模具进行补偿后,从而避免工具体的大的补偿量后再使用这种方式。
注意;使用此方式时,模具拔模角度处要选择固定角度,压边圈处选择固定不变。
回弹补偿的原理

回弹补偿的原理回弹补偿是指在控制系统中采取一定策略来消除或减小物理系统造成的回弹现象。
在实际的控制系统应用中,回弹补偿是一项重要的技术,它可以提高控制系统的性能和稳定性。
下面将从回弹现象的原因、回弹补偿的作用机制和常用的回弹补偿方法进行详细的阐述。
首先,回弹现象的原因是由于物理系统的惯性和滞后特性造成的。
在实际的物理系统中,由于系统本身的惯性和滞后特性,当输入信号发生变化时,物理系统的输出信号并不会立即跟随变化,而是有一定的滞后和惯性表现出来。
这种滞后和惯性现象导致系统的输出信号在输入信号变化后会出现一定程度的震荡、波动或者超调现象,即回弹现象。
回弹现象会给控制系统带来不稳定性和性能下降的问题,因此需要采取一定的补偿措施来消除或减小回弹现象。
回弹补偿的作用机制主要包括两个方面:一是通过减小系统的惯性和滞后特性来降低回弹现象;二是通过引入额外的控制环节来实现对系统输出信号的调整和修正。
在控制系统中,常用的回弹补偿方法有以下几种:1.比例积分(PI)控制器:PI控制器是最常用的回弹补偿方法之一。
它通过引入积分项来消除系统的滞后特性,从而减小回弹现象。
比例项可以根据系统的特性来调整,并且通过使用积分项可以进一步消除误差。
PI控制器通常用于对速度、位置和温度等变量进行控制。
2.比例积分微分(PID)控制器:PID控制器在PI控制器的基础上增加了微分项,可以更好地抑制系统的惯性特性,进一步减小回弹现象。
通过对系统的积分项和微分项进行调整,可以达到更好的控制效果。
3.自适应控制:自适应控制是一种基于系统反馈信息的控制方法,它通过实时地调整控制器的参数来适应不同的系统工作状态。
自适应控制可以根据系统的反馈信号实时地修正控制器的参数,从而实现对回弹现象的补偿。
4.模糊控制:模糊控制是一种基于模糊逻辑原理的控制方法,在控制系统中应用广泛。
模糊控制通过建立模糊推理规则和模糊控制器的输入输出关系来实现对系统的控制。
模糊控制器可以根据系统的工作状态实时地调整输出信号,从而实现对回弹现象的补偿。
二维截面法在精确预测汽车梁类件回弹上的应用

二维截面法在精确预测汽车梁类件回弹上的应用
聂昕;成艾国;钟志华;申丹凤
【期刊名称】《汽车工程》
【年(卷),期】2007(029)001
【摘要】三维零件回弹结果的精确预测一直是个难题,文中把二维截面法应用到对三维零件回弹的预测和补偿上,离散整个三维零件为各个特征截面,通过二维截面法和有限元软件LS-DYNA精确地对汽车纵梁的回弹和补偿进行了预测计算,实践证明,通过两次的回弹预测和补偿计算,汽车纵梁补偿后的回弹结果和实际产品形状相比,误差在0.5mm以内,有很好的实用价值.
【总页数】5页(P83-86,32)
【作者】聂昕;成艾国;钟志华;申丹凤
【作者单位】湖南大学,汽车车身先进设计制造国家重点实验室,长沙,410082;湖南大学,汽车车身先进设计制造国家重点实验室,长沙,410082;湖南大学,汽车车身先进设计制造国家重点实验室,长沙,410082;湖南大学,汽车车身先进设计制造国家重点实验室,长沙,410082
【正文语种】中文
【中图分类】U4
【相关文献】
1.汽车用梁类零件冲压成形CAE分析及模具设计 [J], 秋艳;范正辉;尤锐
2.高强度梁类件回弹及补偿的二维截面法修正 [J], 聂昕;申丹凤
3.把三维理论应用到二维模型里预测精确的水力压裂范围 [J], Rahim.,Z;王忠
4.几何精确的二维动态压电梁有限元格式 [J], 马军;张雄
5.基于汽车梁类件的回弹计算及补偿系统 [J], 聂昕;成艾国;申丹凤;钟志华
因版权原因,仅展示原文概要,查看原文内容请购买。
汽车铝合金结构件回弹分析

汽车铝合金结构件回弹分析刘新洋;牛忠贺【摘要】根据铝合金板材材料的特殊性能,研究其在塑性成型过程中的变形特点,经分析可知铝合金板材在成型之后会产生回弹、开裂、变薄、起皱等问题,通过对这些问题进行深入研究可知回弹是影响制件尺寸的最大问题,而且也是最难解决的问题,针对不同工序进行回弹补偿是解决问题最直接有效的方法.【期刊名称】《汽车工艺与材料》【年(卷),期】2016(000)007【总页数】5页(P37-41)【关键词】铝制件;结构件;回弹分析【作者】刘新洋;牛忠贺【作者单位】一汽模具制造有限公司,长春130000;一汽模具制造有限公司,长春130000【正文语种】中文【中图分类】TG146.2+1随着科技的进步以及环境改善的迫切需求,如何节省能源已经成为一项世界性的课题。
对于汽车而言,车身轻量化已经成为世界汽车发展的主要趋势,白车身铝合金板材模具工装的开发与使用在整车生产中逐步占有越来越重要的地位。
铝合金材料冲压成型时容易产生较大的回弹变形行为,在冲压过程中易出现尺寸超差、开裂、变薄率超差、起皱等现象。
铝制件这种特殊的材料性能给工艺分析、回弹分析以及调试生产带来了很大的困扰。
主要阐述了通过对制件的回弹分析及回弹补偿,来解决相应的成型问题。
铝合金板材的冲压工艺设计方法是解决铝合金板材制件回弹变形的核心技术,涉及到工艺方法、成型条件、补偿处理等多方面技术内容,需要分析成型过程中的开裂、起皱、回弹、扭曲等多种冲压缺陷产生的位置及原因,并寻找相应的消除办法,具体可以分为以下几个部分。
冲压工艺设计也称工艺方案设计,是根据铝合金板材结构件的产品特点来确认成型区域、补充形状,修边布局及相关的翻边、整形形状等工艺内容,在设计过程中需要详细分析零件成形过程中板料的流动情况及各工序冲压过程的稳定性、成形性等多方面因素,制定相应的工艺过程。
铝合金的延展性较低,制件相应的成型也更加困难,因此,需要考虑更多的成型因素对零件的影响,从而保证制件在冲压工艺设计时能够得到稳定的成型结果。
基于Autoform和Dynaform软件的超高强钢零件仿真对比

基于Autoform和Dynaform软件的超高强钢零件仿真对比牛超;陈新平;崔振祥【摘要】目的研究商用软件Autoform和Dynaform对超高强钢零件的回弹预测精度.方法以某车型前围板中间横梁零件冲压成形过程为例,分别基于Autoform和Dynaform软件建立冲压有限元模型模拟冲压成形和回弹过程,对两种软件成形性和回弹计算结果进行比较和讨论分析.结果Dynaform和Autoform两种软件在成形性计算时结果比较一致,相同位置Autoform计算减薄率为16%,Dynaform为16.2%;Dynaform计算的最大减薄率为18%,比Autoform的16.2%略大;两种软件基本在相同位置预测出了起皱和开裂现象;比较修边后回弹仿真值与实测值,Dynaform计算的偏差满足设定阈值的占51.4%,高出Autoform约20%.结论Dynaform计算的最大减薄率更大一些,对应量产时较高的安全裕度;同时其回弹计算结果与实测回弹值更为接近,回弹预测精度更高.【期刊名称】《精密成形工程》【年(卷),期】2017(009)006【总页数】4页(P53-56)【关键词】Autoform;Dynaform;超高强钢;回弹;成形性【作者】牛超;陈新平;崔振祥【作者单位】宝山钢铁股份有限公司中央研究院,上海 2019002;汽车用钢开发与应用技术国家重点实验室(宝钢),上海 201900;宝山钢铁股份有限公司中央研究院,上海 2019002;汽车用钢开发与应用技术国家重点实验室(宝钢),上海 201900;宝山钢铁股份有限公司中央研究院,上海 2019002;汽车用钢开发与应用技术国家重点实验室(宝钢),上海 201900【正文语种】中文【中图分类】TG386近年来,随着汽车工业对汽车安全性能以及节能环保要求的提高,在开展车身轻量化工作的同时,还要兼顾汽车车身强度,超高强度钢板由于其具有重量较轻和安全性能较高的双重优势,越来越受到汽车企业的青睐,应用日益广泛[1—2]。
- 1、下载文档前请自行甄别文档内容的完整性,平台不提供额外的编辑、内容补充、找答案等附加服务。
- 2、"仅部分预览"的文档,不可在线预览部分如存在完整性等问题,可反馈申请退款(可完整预览的文档不适用该条件!)。
- 3、如文档侵犯您的权益,请联系客服反馈,我们会尽快为您处理(人工客服工作时间:9:00-18:30)。
汽车梁类件的特点是整体结构相对简单,各个 断面形状相似,基本上为类U形断面。零件生产时 常常遇到的问题就是修边后两侧壁的回弹、扭曲, 而且不易解决。
针对汽车梁类件造型的特点,通过利用二维截 面法来计算截面回弹量,再开发截面补偿算法来对 节点进行回弹补偿,最后开发整体型面变形算法来 对补偿型面进行修改来建立一个基于梁类件回弹计 算、回弹补偿及补偿型面修改的整套系统。
results Can be obtained in the system.Secondly,the section nodes Can be compensated by node-offset algorithm and the nodes
information of each section before springback and aRer compensation be call obtained.And thirdlg according to the matching relationship of the section nodes before springback and after compensation,the compensated profile can be obtained by shape global deformation(SGD)algorithm based on the original profile in this system.111is method Can ensue the topology consistency of surface before and after modifications and the quality and smoothness of compensated curved surface.The practice proves that this
回弹计算及补偿系统的关键在于以下三方面: ①回弹计算值的准确性:②根据回弹值,对节点
图2梁类件断面示意图
首先考虑其坐标值。对所有节点中Zl—Zo的绝 对值小于0.1 mm的节点设置一个节点集SETl。 SETl中主要是顶面和两侧面的节点。Zl—zo的绝对
值大于O.1衄的节点设置一个节点集SET2。SET2
45卷第7期 2009年7月
机械工程学报
JOURNAL OF MECHANICAL ENGINEEIUNG
V01.45 Jul.
No.7 2009
DoI:10.3901,JM[E.2009.07.194
基于汽车梁类件的回弹计算及补偿系统木
聂 昕1 成艾国1 申丹凤2钟志华1
(1.湖南大学汽车车身先进设计制造国家重点实验室长沙410082: 2.上海宏旭模具工业有限公司上海20161 1)
Springback Calculation and Compensation System Based on Rail Member Panel
NIE Xinl CHENG Aigu01 SHEN Danfen92 ZHONG Zhihual (1.State Key Laboratory of Advanced Design and Manufacture for Vehicle Body,
图l解决板件回弹问题的系统流程
整个回弹计算及补偿系统的思路是:首先进行 板件的回弹计算,由于梁类件的特殊性,可以采用 二维截面法来进行回弹计算;然后运用节点偏置算 法对各个断面进行节点补偿,保证一一对应关系; 最后根据原始数模型面,采用型面整体变形算法 (Shape global deformation,SGD),对零件进行回弹补 偿面的修改,从而生成精度高、质量好的曲面。
摘要:板件回弹问题一直是学术界和工程界研究的热点,特别是在车身广泛应用高强度钢板之后回弹问题更加明显。针对汽 车梁类件的造型特点,建立基于梁类件的回弹计算、回弹补偿及工艺型面修改的整套分析系统。在此系统中,先利用二维截 面法和有限元软件来计算零件各断面的回弹量,保证其回弹计算的精确性。再通过节点偏置算法来补偿各断面节点的回弹量, 得到各断面回弹前和补偿后的节点信息。最后按照各个断面回弹前和补偿后的节点的一一对应关系,以原始型面为基础,运 用型面整体变形(Shape global deformation,SGD)算法来对零件的工艺型面进行补偿修改。能够保证变形前后的型面整体拓扑 关系的一致性,极大地保证曲面的质量和光顺程度,以便得到更为精确的回弹补偿型面。实践证明,该系统能够很大程度节 省处理回弹问题的时间和精力,并且在补偿型面的修改精度上有较大的提高,回弹补偿更加准确。 关键词:梁类件 回弹计算及补偿系统二维截面法节点偏置算法型面整体变形算法 中图分类号:TGl56
节点坐标为Ⅳl电I’YI,Z1),则xo>xl。所以,回弹补 偿后的节点坐标为Ⅳ2叫,(2Xo—x1)’Yo,2zo—Z1)。
通过以上偏置算法就可以实现节点的偏置,对 断面上的回弹进行补偿。 1.4运用SGD算法对型面进行修改
对各断面节点进行了偏置补偿后,就需要对模 具型面进行修改。以前进行节点的回弹补偿后,需 要手工对型面进行修改,或者通过逆向工程反求曲 面,这样不仅耗时、难度大、曲面质量不高,而且 不能保证光顺性,特别对于曲面质量要求比较高的 零件如车身外观件很难达到要求。
自主开发的节点偏置算法是通过应用二维截 面法得到的各断面节点的回弹量,对各节点进行一 定规律的偏置,从而实现回弹补偿。如图2所示, 由于设定了零件的二维断面属于平面应变问题,所 以在Y轴方向(零件的纵向)是没有回弹的。在此, 又做一个假设,由于在z轴方向(冲压方向)的回弹 主要发生在法向方向为Z轴的两凸缘面上,而两侧 壁z向的回弹相比工向(零件的横向)的回弹比较小, 一般最大也只占x向回弹的5%~8%,也就是说没 有什么上跳。所以,对于两侧壁来说,回弹补偿最 主要的是补偿x向位移。由于一般梁类件的标准公 差是±0.5 mm,为了补偿的简便性,适用于工程实 践,本文也假设忽略了两侧壁在z向的回弹。
SETl:由于是顶面和两侧壁的节点,由上面的
假设分析,Y、Z向的回弹都不考虑。只需考虑X轴 方向的回弹。假设在左侧面,回弹前的节点坐标为
No=(xo,Yo,zo),回弹后的节点坐标为Ⅳl=Ol,Yl,zO, 则xo>xl。所以,回弹补偿后的节点飓气,般2Xo一工1), .蜘,zb)。
SET2:主要是底面两凸缘面和侧壁底部圆角上 的节点,它们的特点是既有z向的回弹,又有X向 的回弹。保持坐标系与原整体坐标系一致。所以, 假设回弹前的节点坐标为So=(xo,Yo,zo),回弹后的
Shape global defonnation(SGD)algorithm
0前言
随着汽车厂商从安全性、轻量化等多方面考
·国家高技术研究发展计划(863计划,007AA042006)、国家重点基础 研究发展计划(973计划。2004CB719402)和“十一五”国家科技支 撑计划(2006BAF02A02)资助项目。20080721收到初稿,20090225收 到修改稿
现在通过自主开发的SGD算法进行回弹补偿 型面的修改。该算法基于最小能原理[5 61,通过建立 一个变形函数实现整体变形,能够保证其变形前后 型面整体拓扑关系一致性,极大地保证其曲面精度 及光顺程度。
SGD算法进行曲面变形修改的过程如下。 (1)导入变形前后的两组特征数据,分属于两 个部件,命名为partA和partB。两组特征数据的数 量必须保持一致。比如有限元计算中回弹前的节点 信息和补偿后的节点信息就属于两个部件,而两个 部件的节点数必须保持一致。 (2)自动搜寻建立从partA到partB的一一对应 的关系。
万方数据
2009年7月
聂听等:基于汽车梁类件的回弹计算及补偿系统
深入,复杂零件的三维回弹分析结果和补偿方法都 不够理想。
对于二维回弹的研究,一直是学术界研究的热 点。其模型简单、特点鲜明,从以前用解析法到现 在用数值模拟来计算二维回弹,都取得了一些不错 的成绩。经过最近lO多年的探索,由一些文献和实 际情况可以看出,二维回弹是能够计算较为准确
system啪save time and cost to a great extent in dealing with springback of rail panel and also a great improvement in
surface-smoothness and more accurate compensation call be achieved. Key words:Rail member panel Springback calculation and compensation system 2D section method Node-offsetalgorithm
Hunan University,Changsha 4 1 0082; 2.Shanghai Horng Shiue Industrial Co.,Ltd.,Shanghai 201611)
Abstract:Springback problem is always a hotspot in automotive industry and academia,especially when the application of high
பைடு நூலகம்
虑,高强度钢板在车身上的应用比例不断增加,板 件的回弹问题越来越成为学术界和工程界研究的热 门课题。近年来,通过国内外学者的大量实践和理 论性的探索,对于回弹量的计算和回弹补偿的方法
取得了一定的成绩,KARAFILLIS掣11在回弹模具
补偿的数值模拟方面做了大量的工作。李延平等【2】 提出了基于RP/RT/RE技术的金属板料冲压成形回 弹误差补偿系统等,但对回弹问题的研究还需更加
万方数据
机械工程学报
第45卷第7期
里面主要是底部两端面和侧面下部圆角上的节点。 其中,Zl代表回弹之后节点的z轴坐标。z0代表回 弹前节点的Z轴坐标。z2代表回弹补偿后节点的z 轴坐标,,为材料系数,与板厚和材料抗拉强度有 关,,为能动控制系数。