原材料需求量计划表
MRP基本构成及原理

MRP基本构成及原理MRP (Material Requirements Planning)是一种计划方法,旨在通过对原材料、零件和组件的需求进行有效管理,以确保生产过程的顺利进行。
MRP的基本构成包括产品结构清单(BOM)、主生产计划(MPS)、库存记录和已有库存的报告。
产品结构清单是一个层次结构,显示了制造产品所需的原材料、零件和组件的相关信息。
它列出了每个层次和组成部分的代码、描述、数量和单位。
这使得企业能够追踪所有所需的材料,并了解它们在生产过程中的使用情况。
主生产计划是一份详细计划,列出了公司计划生产的产品的时间表和数量。
它考虑了销售预测、市场需求和可用资源,以帮助企业制定合理的生产计划。
库存记录是一份记录,跟踪和记录所有原材料、零件和组件的库存情况。
它显示了当前的库存水平、待定订单和已分配的库存。
这有助于企业了解当前库存情况,以避免材料短缺或过剩。
已有库存报告是一份报告,列出了所有库存物品的数量和状态。
它显示了当前库存水平以及待定订单和已分配的库存。
这有助于企业管理库存,以便及时补充不足的物料,并防止库存过剩。
MRP的原理是基于以下几个关键概念:1.净需求量:通过将所需的数量减去已有的库存量,计算出每个物料的净需求量。
净需求量是制造每个产品所需的材料数量。
2.拆分和偏向分配:将总需求量拆分为不同层次的需求,并将净需求量偏向分配给不同的供应商。
这有助于确定哪些材料需要补充以满足生产需求。
3.时间框架:MRP将需求量与特定的时间框架相关联,以确定何时需要补充材料。
这有助于确保物料的准时供应,以满足生产计划的要求。
4.批量和运输:MRP考虑批量订购和运输的最佳方式,以最大程度地减少物料延迟和库存成本。
它试图找到在不妨碍生产需求的情况下,最经济和有效的补充材料方法。
MRP的目标是提供一个全面的生产计划,以确保所有所需的材料在需要时都能及时可用。
它可以帮助企业减少库存成本、防止生产延迟和缺货,并提高生产效率和生产计划的准确性。
物料需求计划
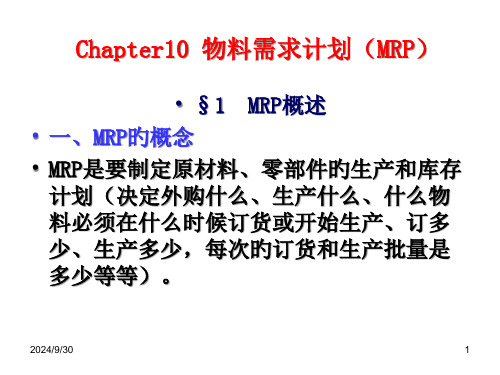
2024/9/30
16
二、MRP旳输出成果
• 措施提醒信息:
对多种物料旳详细需求
订单旳发出时间
订制批量: LT: 总需求量 已在途的订货 计划库存 净需求量 计划应收到的订货 计划应发出的订货
PD 1 2 3 4 5 6 7 8 9 10
2024/9/30
17
例题
生产木制百叶窗旳某厂商收到两份百叶窗订单: 一份要100个,要求本年度第四面生产完毕; 另一份要150个,要求第八周开始发送。 每个百叶窗涉及4个木制板条部分和2个框架。 木制部分是工厂自制旳,制作过程耗时一周; 框架需要订购,订货提前期是2周。 组装百叶窗需要1周时间, 木制部分既有库存70个。 请作出物料需求计划。
防止盲目多订和早订。
防止造成混乱。
2024/9/30
32
四、配送需求计划DRP
• DRP是用MRP旳原理对不同地点旳仓库或零售店进 行补充旳计划。它将不同地点仓库旳补充计划传 送给配送中心,配送中心在将其需求计划转变成 工厂旳总生产进度计划。
• 最低层网点旳估计总需求量由各网点根据以往旳 销售情况预测拟定;
• 上一层网点旳估计需求量是根据下一层网点旳计 划发出订货量拟定旳,并在时段上保持一致。
2024/9/30
33
DRP旳处理过程
• 在某城市有1个批发部,在该城市旳不同地域设有 2个零售点A和B。
• 零售点A
提前2 3 4 5 6 7 8 订货批量250
件
• 估计需求 40 40 40 50 60 70 70 70 • 既有数230 190 150 110 60 250 180 110 290
1750
1750 1500
550 1200
采购作业计划
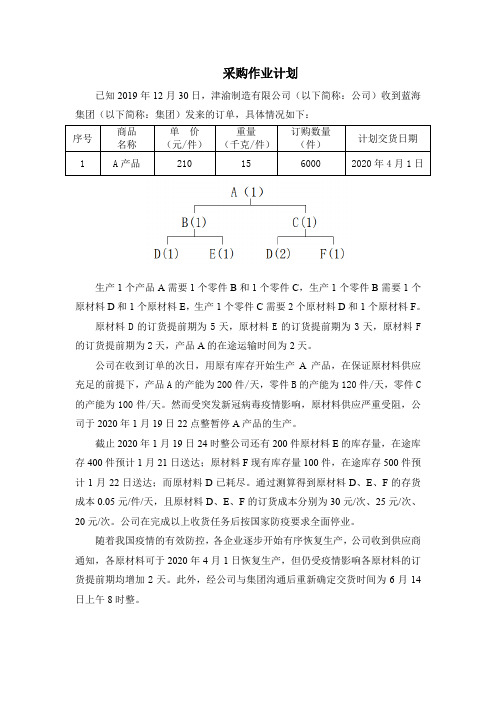
采购作业计划
已知2019年12月30日,津渝制造有限公司(以下简称:公司)收到蓝海集团(以下简称:集团)发来的订单,具体情况如下:
序号
商品
名称
单 价
(元/件)
重量
(千克/件)
订购数量(件)
计划交货日期
1
A产品
210
15
6000
2020年4月1日
生产1个产品A需要1个零件B和1个零件C,生产1个零件B需要1个原材料D和1个原材料E,生产1个零件C需要2个原材料D和1个原材料F。
原材料D的订货提前期为5天,原材料E的订货提前期为3天,原材料F的订货提前期为2天,产品A的在途运输时间为2天。
公司在收到订单的次日,用原有库存开始生产A产品,在保证原材料供应充足的前提下,产品A的产能为200件/天,零件B的产能为120件/天,零件C的产能为100件/天。然而受突发新冠病毒疫情影响,原材料供应严重受阻,公司于2020年1月19日22点整暂停A产品的生产。
截止2020年1月19日24时整公司还有200件原材料E的库存量,在途库存400件预计1月21日送达;原材料F现有库存量100件,在途库存500件预计1月22日送达;而原材料D已耗尽。通过测算得到原材料D、E、F的存货成本0.05元/件/天,且原材料D、E、F的订货成本分别为30元/次、25元/次、20元/次。公司在完成以上收货任务后按国家防疫要求全面停业。
年度(年)
2011
2012
2013
MRP运算

MRP运算MRP(Material Requirement Planning的英文缩写),即物料需求计划,是指根据所制订的主生产计划以及物料清单,计算出指定时段内所有原材料的生产需求量,同时,根据生产计划规定的时间次序,表示出各原材料按时间进程的耗用计划,对外计划各种零部件的采购时间与数量,对内确定生产部门应进行加工生产的时间和数量,从而把生产作业计划和物资供应计划统一起来。
本系统的MRP运算可以在接到客户订单后,结合仓库的当前库存量、安全库存、销售在订量、采购在订量以及未完工数量等数据,计算要生产的产品数量以及需要采购的物料数量,并且可以根据计算结果生成采购订单以及生产任务单。
操作指南•进行MRP运算时首先应选择<销售订单>,请点击下方的[选择订单]打开如下窗口;•窗口上半部分按照需求日期先后顺序列出了所有的<销售订单>,您还可以根据业务的实际需要,设置起始日期和终止日期,以便选择指定期间的业务订单,接着从下方过滤出的单据列表中选择销售订单,单击“选择”栏使其打钩,或者也可以点击下方的“反选”、“全部选择”或“全部取消”等快捷操作按钮来选择所需的单据。
选择<销售订单>后点击[确定]返回上一窗口;•设置MRP运算参数,系统提供了多个参数:当前库存、安全库存、采购在订量、销售在订量、未完工数量、物料预约量(物料在生产任务单中的未领用数量)等,请根据MRP运算时需要考虑的因素予以选择,多选、单选或不选均可,然后单击[计算],系统会根据当前的设置自动进行MRP运算;•计算完毕,系统会自动转到“计算结果”窗口,列表中将生产所需物料各项指标的数量显示出来供参考,比如可以查询加工产品及其加工物料的毛需求量,在考虑MRP运算参数的情况下还可以知道某种物料目前的库存量、在订量、未完工量以及净需求量等数据;o根据MRP运算您已经知道了目前企业需要采购产品的净需求量,这时可以通过系统自动下达采购订单来完成物料的采购,请切换到“下达采购订单”页面,其中已经列出了该种产品的“净需求量”、“建议采购量”、“最小订货批量”和“订货批量增量”(后两项在勾选上面的选项时才予以计算),这时您需要手工修改“下单数量”,该数量将作为采购订单中货品的实际数量,然后勾选该行的“选择”栏,最后单击[下单采购订单]即可生成<采购订单>。
第九讲物料需求计划
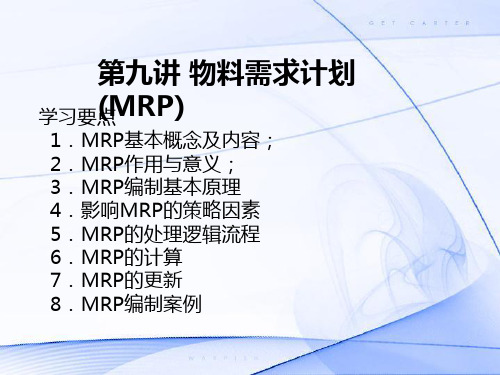
MRP项目
计划周期
1 2 3 4 5 6 25 7 8 30 40 25 40 15 15 30 15 15 30 9 10 11 15 15 30 12 13
X(LT=4) Y(LT=6) 相关需求X-A 相关需求Y-A 独立需求A
A的毛需求
15
40
40
30
15
45
【例题9.3:应用低位码 计算物料的净需求】 已知:MPS为在第8个 计划周期时产出200件A 产品;各物料的计划接 收量和已分配量为0; 物料ABCD期初库存分别 为0、120、60、70件, 安全库存量为0;物料 ABCD批量规则为直接批 量法。求物料ABCD的净 需求。
毛需求计算考虑因素
• • • • •
是否存在独立需求 是否共用物料 是否低位码 是否是计划BOM 是否存在替代
如果存在替代,要不要替代则考虑: • 是否可以降低工作量 • 是否可以降低成本 • 客户是否满意 • 近期是否短缺
(3)计算净需求量。 考虑安全库存推算特定时段的净需求量。 当PAB初值≥安全库存时,净需求=0 当PAB初值<安全库存时,净需求=安全库存- PAB初值
生产什么? MPS
主生产计划
2
(物料清单) 用到什么?
产品信息
4 物料需求计划 MRP
已有什么? (物料可用量)
3 库存信息
买什么?
采购计划
做什么?
生产计划
MRP 回答了
问
4 个制造业的主要问题
答
(生产什么 1 生产什么?
2 用到什么? 3 已有什么?
+
用到什么) - 已有什么 1 主生产计划( MPS) = 还缺什么
(二)MRP中的输出数据项 1.采购订单 采购什么? 采购多少? 何时开始采购? 何时完成采购? 2.制造订单 制造什么? 制造多少? 何时开始制造? 何时完成制造?
1-原材料采购计划表

370
370
9-5
9-5
5
中桥壳中段
HFF2501012 CK
9GFTZGS
450
450
9-5
9-5
6
空气簧压板
HFF2401026 CK 3FK
280
280
9-5
9-5
7
板簧压板
HFF2401026 CK 1FZT
160
160
9-5
9-5
8
板簧垫板
HFF2401013 CK 3HZG
;350
编制/日期:李静/07/11/6
审批/日期:张伟/07/11/6
序 号
采购物资名称
型号/规格
计划 数量
实购 数量
计划到 货日期
实际到 货日期
备注
1
平衡轴壳
AK99114520035
790
790
12-5
12-5
2
平衡轴壳
HFF2918005 CK JH
500
500
12-5
12-5
3
中桥壳中段
HFF25010120 CK ZBZFT
8-5
8-5
9
平衡轴
AK99014520185
260
260
8-5
8-5
10
下压板(左右)
HFF2401029/30 CK
150
150
8-5
8-5
11
空气簧压板
HFF2401123/24 CK AKK-1
440
440
8-5
8-5
编制/日期:李静/07/8/6
审批/日期:张伟/07/8/6
MPS与MRP的区别与联系
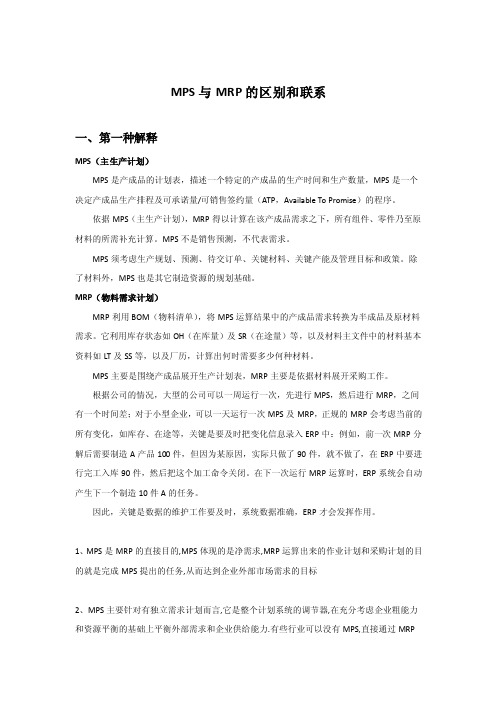
MPS与MRP的区别和联系一、第一种解释MPS(主生产计划)MPS是产成品的计划表,描述一个特定的产成品的生产时间和生产数量,MPS是一个决定产成品生产排程及可承诺量/可销售签约量(ATP,Available To Promise)的程序。
依据MPS(主生产计划),MRP得以计算在该产成品需求之下,所有组件、零件乃至原材料的所需补充计算。
MPS不是销售预测,不代表需求。
MPS须考虑生产规划、预测、待交订单、关键材料、关键产能及管理目标和政策。
除了材料外,MPS也是其它制造资源的规划基础。
MRP(物料需求计划)MRP利用BOM(物料清单),将MPS运算结果中的产成品需求转换为半成品及原材料需求。
它利用库存状态如OH(在库量)及SR(在途量)等,以及材料主文件中的材料基本资料如LT及SS等,以及厂历,计算出何时需要多少何种材料。
MPS主要是围绕产成品展开生产计划表,MRP主要是依据材料展开采购工作。
根据公司的情况,大型的公司可以一周运行一次,先进行MPS,然后进行MRP,之间有一个时间差;对于小型企业,可以一天运行一次MPS及MRP,正规的MRP会考虑当前的所有变化,如库存、在途等,关键是要及时把变化信息录入ERP中:例如,前一次MRP分解后需要制造A产品100件,但因为某原因,实际只做了90件,就不做了,在ERP中要进行完工入库90件,然后把这个加工命令关闭。
在下一次运行MRP运算时,ERP系统会自动产生下一个制造10件A的任务。
因此,关键是数据的维护工作要及时,系统数据准确,ERP才会发挥作用。
1、MPS是MRP的直接目的,MPS体现的是净需求,MRP运算出来的作业计划和采购计划的目的就是完成MPS提出的任务,从而达到企业外部市场需求的目标2、MPS主要针对有独立需求计划而言,它是整个计划系统的调节器,在充分考虑企业粗能力和资源平衡的基础上平衡外部需求和企业供给能力.有些行业可以没有MPS,直接通过MRP来满足预测和订单的需要3、简单的说:MPS针对的是总装,MRP针对的是总装下的采购及零件4、如果从客户订单或预测过来的需求都需要计划部评估一下这个成品的交期和粗能力,在成品的评审没有完成之前下阶的材料都不允许产生相关需求,这个时候就对成品RUN MPS,当成品评审通过后再对它的一阶材料RUN MRP。
MRP的基本原理

MRP基本原理基本MRP的原理我们都知道,按需求的来源不同,企业内部的物料可分为独立需求和相关需求两种类型。
独立需求是指需求量和需求时间由企业外部的需求来决定,例如,客户订购的产品、科研试制需要的样品、售后维修需要的备品备件等;相关需求是指根据物料之间的结构组成关系由独立需求的物料所产生的需求,例如,半成品、零部件、原材料等的需求。
MRP的基本任务是:⑴从最终产品的生产计划(独立需求)导出相关物料(原材料、零部件等)的需求量和需求时间(相关需求);⑵根据物料的需求时间和生产(订货)周期来确定其开始生产(订货)的时间。
MRP的基本内容是编制零件的生产计划和采购计划。
然而,要正确编制零件计划,首先必须落实产品的出产进度计划,用MRPⅡ的术语就是主生产计划(Master Production Schedule,MPS),这是MRP展开的依据。
MRP还需要知道产品的零件结构,即物料清单(Bill Of Material,BOM),才能把主生产计划展开成零件计划;同时,必须知道库存数量才能准确计算出零件的采购数量。
因此,基本MRP的依据是:⑴主生产计划(MPS);⑵物料清单(BOM);⑶库存信息。
它们之间的逻辑流程关系见下图。
MRP基本构成MRP基本构成(1)主生产计划(Master Production Schedule, 简称MPS)主生产计划是确定每一具体的最终产品在每一具体时间段内生产数量的计划。
这里的最终产品是指对于企业来说最终完成、要出厂的完成品,它要具体到产品的品种、型号。
这里的具体时间段,通常是以周为单位,在有些情况下,也可以是日、旬、月。
主生产计划详细规定生产什么、什么时段应该产出,它是独立需求计划。
主生产计划根据客户合同和市场预测,把经营计划或生产大纲中的产品系列具体化,使之成为展开物料需求计划的主要依据,起到了从综合计划向具体计划过渡的承上启下作用。
(2)产品结构与物料清单(Bill of Material, BOM)MRP系统要正确计算出物料需求的时间和数量,特别是相关需求物料的数量和时间,首先要使系统能够知道企业所制造的产品结构和所有要使用到的物料。
生产任务需求计划表-概述说明以及解释
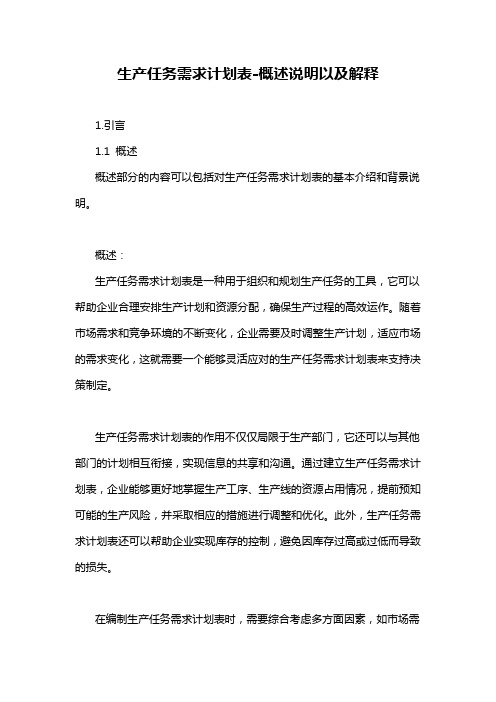
生产任务需求计划表-概述说明以及解释1.引言1.1 概述概述部分的内容可以包括对生产任务需求计划表的基本介绍和背景说明。
概述:生产任务需求计划表是一种用于组织和规划生产任务的工具,它可以帮助企业合理安排生产计划和资源分配,确保生产过程的高效运作。
随着市场需求和竞争环境的不断变化,企业需要及时调整生产计划,适应市场的需求变化,这就需要一个能够灵活应对的生产任务需求计划表来支持决策制定。
生产任务需求计划表的作用不仅仅局限于生产部门,它还可以与其他部门的计划相互衔接,实现信息的共享和沟通。
通过建立生产任务需求计划表,企业能够更好地掌握生产工序、生产线的资源占用情况,提前预知可能的生产风险,并采取相应的措施进行调整和优化。
此外,生产任务需求计划表还可以帮助企业实现库存的控制,避免因库存过高或过低而导致的损失。
在编制生产任务需求计划表时,需要综合考虑多方面因素,如市场需求、产品特性、生产能力和资源条件等。
通过合理规划和安排,企业可以最大程度地发挥资源的利用效率,提高生产效率和客户满意度。
总之,生产任务需求计划表在现代企业管理中起着重要的作用。
它不仅可以帮助企业合理安排生产计划和资源分配,提高生产效率,还可以促进不同部门之间的协作和信息共享,实现全面优化和协同发展。
对于任何一个追求高效生产和竞争力的企业来说,生产任务需求计划表都是一个不可或缺的管理工具。
1.2文章结构1.2 文章结构本文将围绕"生产任务需求计划表"展开介绍。
首先,将在引言部分对整篇文章进行概述,阐述文章的目的和结构。
接着,将在正文部分分别讨论生产任务需求计划表的定义和作用。
最后,在结论部分对文章进行总结并展望未来。
在正文的第一部分,将详细解释生产任务需求计划表的定义。
我们会介绍生产任务需求计划表是指对公司或组织的生产任务进行计划和安排的表格,其中包含了生产任务的详细信息和相关的时间要求。
在正文的第二部分,将探讨生产任务需求计划表的作用。
库存分配计划表

库存分配计划表
1. 产品信息。
产品名称,XXXX。
产品型号,XXXX。
产品数量,XXXX。
产品描述,XXXX。
2. 库存情况。
根据最近的库存盘点,我们公司目前的库存情况如下:
原材料,XXXX。
半成品,XXXX。
成品,XXXX。
3. 销售计划。
根据市场需求和销售预测,我们公司未来一段时间内的销售计划如下:
本月销售预计,XXXX。
下月销售预计,XXXX。
季度销售预计,XXXX。
4. 库存分配计划。
根据以上的产品信息、库存情况和销售计划,我们制定了以下库存分配计划:
原材料采购计划,根据生产需求和库存情况,制定原材料的采购计划,以确保生产所需的原材料充足。
半成品生产计划,根据销售预计和库存情况,制定半成品的生产计划,以满足未来销售的需求。
成品库存调整计划,根据销售预计和库存情况,调整成品的库存,以确保库存水平在合理范围内。
5. 库存监控和调整。
在执行库存分配计划的过程中,我们将密切监控库存情况和销售实际情况,及时调整库存分配计划,以适应市场需求的变化。
6. 结语。
库存分配计划是公司库存管理的重要组成部分,通过合理的库存分配,可以最大程度地利用公司的库存资源,提高库存周转率,降低库存成本,满足市场需求,实现公司的经济效益和社会效益的最大化。
以上是我们制定的库存分配计划表,希望能够得到各位同事的认可和支持,共同努力,为公司的发展贡献力量。
生产运作中的物料需求计划

生产运作中的物料需求计划1. 引言物料需求计划(Material Requirements Planning,简称 MRP)是一种制定和管理物料供应计划的方法,它通过根据产品需求来计算所需的原材料和零部件,并确定合适的采购和生产计划。
物料需求计划在生产运作中起到了关键的作用,它可以帮助企业有效地规划和控制生产过程,确保物料的准时供应,降低库存和运营成本,并提高客户满意度。
本文将介绍生产运作中的物料需求计划的基本原理和实施方法,并探讨其在提高生产效率和优化供应链中的重要性。
2. 物料需求计划的基本原理物料需求计划的基本原理是根据产品的需求和生产计划,计算出所需的原材料和零部件的数量和时间,以便及时采购和供应。
物料需求计划的主要步骤包括:2.1. 产品需求计划根据销售预测和市场需求,制定产品的生产计划和销售计划。
这些计划需要考虑客户需求、产品特性和市场趋势等因素。
2.2. 物料清单准备根据产品的设计和组装要求,制定物料清单(Bill of Materials,简称BOM)。
物料清单列出了产品所需的所有原材料、零部件和半成品,并按照层级结构组织。
2.3. 需求量计算根据产品的生产数量和物料清单,计算出每个原材料和零部件的需求量。
这可以通过物料需求计算公式来实现,公式通常包含产品的粗略需求量、安全库存、订单数量和供应周期等因素。
2.4. 供应计划制定根据物料的需求量和供应能力,制定相应的供应计划。
这包括确定采购订单的数量和时间,与供应商进行协商和沟通,以确保物料的及时供应。
2.5. 跟踪和控制在执行物料需求计划的过程中,需要跟踪和控制物料的采购、生产和库存情况。
当发现偏差或问题时,及时采取纠正措施,以保持物料供应的稳定和可靠。
3. 物料需求计划的实施方法物料需求计划可以通过计算机系统和软件来实施,也可以通过手工操作和管理来完成。
下面介绍两种常见的物料需求计划实施方法。
3.1. MRP系统MRP系统是一种专门设计用于物料需求计划的计算机系统。
物料需求计划【共49张PPT】
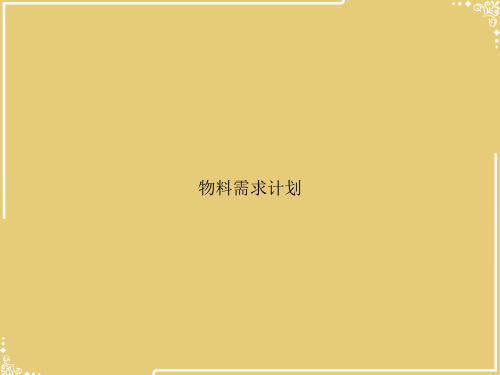
采购供应计划
每一项加工件的建议计划 • 需求数量 • 开始日期和完工日期
每一项采购件的建议计划 • 需求数量 • 订货日期和到货日期
MRP 的基本逻辑
四、MRPII的输入信息
MRP的输入有3个部分: • 主生产计划(产品出产计划MPS)
• 物料清单(产品结构文件,BOM) • 库存状态文件
物料清单(产品结构文件,BOM)
净需求=总需求—(预计到货量+现有量)+安全库存 于是,人们便思考:怎样才能在需要的时间,按需要的数量得到真正需用的物料?从而消除盲目性,实现低库存与高服务水平并存。 ERP是在MRP基础上发展起来的,以供应链思想为基础,融现代管理思想为一身,以现代化的计算机及网络通信技术为运行平台,集企业的各项管理功能为一身,并能对供应链上所有资源进行有效控 制的计算机管理系统。
件;要加工各种零件,就必须提前一定时间准备所需
数量的各种毛坯,直至提前一定时间准备各种原材料 。
其主要功能及运算依据为:
处 理 的 问 题 1. 生 产 什 么 ?生 产 多 少 ? 2. 要 用 到 什 么 ? 3. 已 具 备 什 么 ? 4. 还 缺 什 么 ? 何 时 需 要 ?
所 需 信 息 1. 切 实 可 行 的 主 生 产 计 划 ( M PS) 2. 准 确 的 物 料 清 单 ( BOM表 ) 3. 准 确 的 物 料 库 存 数 据 4. M RP的 计 算 结 果 ( 生 产 计 划 和 采 购 计 划 )
物料需求计划
本章学习目标
• 物料需求计划(MRP):
– Material Requirements Planning
• 制造资源计划(MRPⅡ ):
– Manufacturing Resource Planning
物料需求计划(MRP)

运行步骤
(1)根据市场预测和客户订单,正确编制可靠的生产计划和生产作业计划,在计划中 规定生产的品种、规格、数量和交货日期,同时,生产计划必须是同现有生产能力相适应的 计划。
(2)正确编制产品结构图和各种物料、零件的用料明细表。 (3)正确掌握各种物料和零件的实际库存量。 (4)正确规定各种物料和零件的采购交货日期,以及订货周期和订购批量。 (5)通过 MRP 逻辑运算确定各种物料和零件的总需要量以及实际需要量。 (6)向采购部门发出采购通知单或向本企业生产车间发出生产指令。
基本数据
制订物料需求计划前就必须具备以下的基本数据:
第一项数据是主生产计划,它指明在某一计划时间段内应生产出的各种产品和备件,它 是物料需求计划制订的一个最重要的数据来源。
第二项数据是物料清单(BOM),它指明了物料之间的结构关系,以及每种物料需求的数 量,它是物料需求计划系统中最为基础的数据。
第三项数据是库存记录,它把每个物料品目的现有库存量和计划接受量的实际状态反映 出来。
分类
(1)再生式 MRP,它表示每次计算时,都会覆盖原来的 MRP 数据,生成全新的 MRP。 再生式 MRP 是周期性运算 MRP,通常的运算周期是一周。
(2)净变式 MRP,它表示只会根据指定条件而变化,例如 MPS 变化、BOM 变化等, 经过局部运算更新原来 MRP 的部分数据。净变式 MRP 是一种连续性的操作,当指定数据 改变时就需要立即运行。
目录
.
1 含义内容
.
2 特点
.
3 基本数据
.
4 计算步骤
.
5 实现目标
其主要内容包括客户需求管理、产品生产计划、原材料计划以及库存记录。其中客户需 求管理包括客户订单管理及销售预测,将实际的客户订单数与科学的客户需求预测相结合即 能得出客户需要什么以及需求多少。
MRP理论与报表

Society)及 公司之全力推展至今,MRP系统已渐臻完美 系统已渐臻完美。 Society)及IBM 公司之全力推展至今,MRP系统已渐臻完美。 (4)1973年日本丰田汽车制造公司发展丰田式生产管理其存货管理之方法则是以刚好 (4)1973年日本丰田汽车制造公司发展丰田式生产管理其存货管理之方法则是以刚好 及时(JUST in 及时(JUST time)与指示牌系统(Kamban system)为两大支柱。 time)与指示牌系统(Kamban system)为两大支柱。 与指示牌系统 为两大支柱
8.MRP的数学表示法 8.MRP的数学表示法 (1)毛需求计算 (1)毛需求计算 毛需求总生产日程之周计划材料用量清表零星需求。 毛需求总生产日程之周计划材料用量清表零星需求。 (2)净需求量之计算 (2)净需求量之计算 净需求现期结存量未交订单本期预期表接收本期毛需求 (3)前置期间之先行计算 (3)前置期间之先行计算 将采购前置期间(Purchasing 将采购前置期间(Purchasing (Manufacturing Lead Lead Time)或制造前置期间 Time)或制造前置期间
内以实际之顾客订单配合产能与材料状况, 内以实际之顾客订单配合产能与材料状况,排定在长期则以预测之数据排 定之。在标准的电脑化MRP系统下, 定之。在标准的电脑化MRP系统下,一般将主制程以周为单位排定经由 MRP系统下 MRP之计算以求得各层次的材料需求。 MRP之计算以求得各层次的材料需求。 之计算以求得各层次的材料需求
OTPVOTPV-MC
4.MRP之功能 4.MRP之功能 (1)由顾客之订单(Customer (1)由顾客之订单(Customer 由顾客之订单 firm order)及预测之生产计划 order)及预测之生产计划
物料需求计划
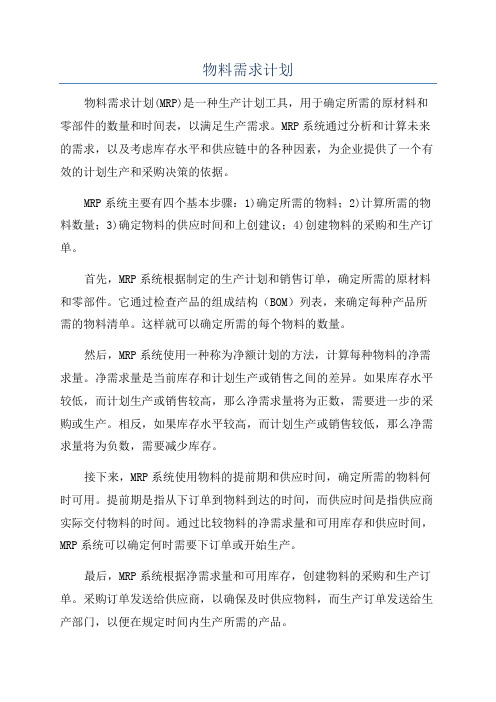
物料需求计划物料需求计划(MRP)是一种生产计划工具,用于确定所需的原材料和零部件的数量和时间表,以满足生产需求。
MRP系统通过分析和计算未来的需求,以及考虑库存水平和供应链中的各种因素,为企业提供了一个有效的计划生产和采购决策的依据。
MRP系统主要有四个基本步骤:1)确定所需的物料;2)计算所需的物料数量;3)确定物料的供应时间和上创建议;4)创建物料的采购和生产订单。
首先,MRP系统根据制定的生产计划和销售订单,确定所需的原材料和零部件。
它通过检查产品的组成结构(BOM)列表,来确定每种产品所需的物料清单。
这样就可以确定所需的每个物料的数量。
然后,MRP系统使用一种称为净额计划的方法,计算每种物料的净需求量。
净需求量是当前库存和计划生产或销售之间的差异。
如果库存水平较低,而计划生产或销售较高,那么净需求量将为正数,需要进一步的采购或生产。
相反,如果库存水平较高,而计划生产或销售较低,那么净需求量将为负数,需要减少库存。
接下来,MRP系统使用物料的提前期和供应时间,确定所需的物料何时可用。
提前期是指从下订单到物料到达的时间,而供应时间是指供应商实际交付物料的时间。
通过比较物料的净需求量和可用库存和供应时间,MRP系统可以确定何时需要下订单或开始生产。
最后,MRP系统根据净需求量和可用库存,创建物料的采购和生产订单。
采购订单发送给供应商,以确保及时供应物料,而生产订单发送给生产部门,以便在规定时间内生产所需的产品。
MRP系统具有许多优点。
首先,它可以帮助企业准确地计划和控制物料的采购和生产,避免库存过剩或不足的问题。
其次,它可以提高供应链的效率和可靠性,确保所需物料的及时交付。
此外,它还可以降低企业的成本,提高生产计划的准确性和灵活性。
然而,MRP系统也存在一些局限性。
首先,它需要准确的销售和生产预测,以便正确计算物料需求。
如果预测不准确,就可能导致物料过剩或不足的问题。
其次,它依赖于准确和及时的数据输入,包括库存水平、供应时间和提前期等。
excel生产计划模板

excel生产计划模板一、概述生产计划是企业管理的重要组成部分,它涉及到生产资源的分配、生产任务的安排、生产进度的控制等方面。
为了提高生产计划的准确性和效率,我们提供了一个基于excel的生产计划模板,帮助企业更好地管理生产资源,提高生产效益。
二、模板介绍本生产计划模板主要包括以下几部分:1.基础信息:包括企业名称、地址、联系方式、生产部门、产品分类等信息。
2.生产计划表:用于记录各个生产任务的生产时间、数量、原材料需求等信息,方便企业进行生产调度和资源分配。
3.原材料库存表:用于记录各种原材料的库存量、采购周期、供应商等信息,方便企业进行原材料采购和库存管理。
4.生产进度表:用于实时监控各个生产任务的进度,及时发现和解决问题,确保生产计划的顺利执行。
5.报表分析:根据生产计划表和生产进度表的数据,进行分析和总结,为企业决策提供数据支持。
三、使用方法1.建立excel表格,按照模板格式进行布局。
2.输入基础信息,包括企业名称、地址、联系方式等。
3.根据生产计划表的要求,输入各个生产任务的相关信息,包括生产时间、数量、原材料需求等。
4.建立原材料库存表,输入各种原材料的库存量、采购周期、供应商等信息。
5.每天或每周更新生产进度表,实时监控各个生产任务的进度。
6.根据报表分析的需要,定期对生产计划表和生产进度表的数据进行分析和总结。
7.根据分析结果,对企业生产计划和资源分配进行调整,提高生产效益。
四、注意事项1.确保输入的数据准确无误,避免因数据错误导致生产计划执行出现问题。
2.定期对excel表格进行备份,以防数据丢失或损坏。
3.根据企业实际情况,不断完善和调整生产计划模板,提高其适用性和准确性。
4.注重数据安全,确保生产计划数据不被泄露或滥用。
总之,本excel生产计划模板旨在帮助企业更好地管理生产资源,提高生产效益。
通过正确使用和不断完善该模板,企业可以更好地应对市场竞争,实现可持续发展。
第6章 物料需求计划(MRP)
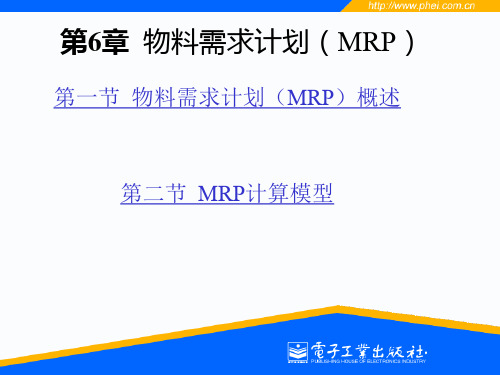
二、MRP计算步骤
• 2.物料需求计划计算具体步骤 • (1)计算物料毛需求量。考虑相关需求和低位码推算计划期全
部的毛需求。 • 项目毛需求量=项目独立需求+父项的相关需求 • 其中: • 父项的相关需求=父项的计划订单数量×项目用量因子 • (2)推算PAB初值。考虑毛需求推算特定时段的预计库存量。 • PAB初值=上期末预计可用库存量+计划接收量-毛需求量 • (3)计算净需求量。考虑安全库存推算特定时段的净需求量。 • 当PAB初值≥安全库存时,净需求=0 • 当PAB初值<安全库存时,净需求=安全库存-PAB初值
一、MRP概念及作用
• 2.MRP的基本依据 • MRP的基本依据是:① 主生产计划(
MPS);② 物料清单(BOM);③ 库存 信息。它们的逻辑流程关系如图6.1所示 。
一、MRP概念及作用
一、MRP概念及作用
• 3.MRP作用 • ① 要生产(含采购和制造)什么?生产(含采购和制造)多
少?(来自MPS) • ② 要用到什么?(根据BOM展开可知) • ③ 已经有了什么?(根据物料库存信息、即将到货的信息或
六、虚拟件
• 3.BOM中的虚拟件
• “虚拟件”最重要的作用就是简化产品结构的管理,以下用 图6.5的BOM进行说明。
• 在图6.5中,如果对A产品BOM的定义采用图6.5(a)方式, 那么,子件B、C的BOM文件定义过程会重复引用到D、E与F 物料,加大了工作量,并且数据库的存储空间也会增加。而 采用图6.5(b)的定义方式,增加一个“虚拟件”物料K,并 定义K的BOM文件,则B、C的BOM中只需要加入一个子件K ,无须重复加入子件D、E与F物料,从而达到简化BOM的目 的,特别是在多个BOM中有大量的相同子件重复出现时,这 种定义方式的优越性就更加明显。另外,如果虚拟件的子件 发生工程改变,也只影响到虚拟件这一层,不会影响此虚拟 件以上的所有父项。
(ERPMRP管理)MRP运算

一、MRP在软件中的概念是物料需求计划(Material Requirement Planning),它的作用是将指定的订单中所需要的原材料的用量做统计,以使生产部门、仓库了解当前生产这些产品需要多少的原材料,这是因为在一般的工业企业里,产成品它是有很多的原材料组成的(即在ERP里称之为BOM),但是在下订单时,一般只会选择某一个产成品,而不会列出它是由哪些原材料组成的,不过到生产部门时,他们所要关心的是生产产品时所需的原材料数量,而并非单单的产品数量,所以此时MRP运算的作用可以体现出来了。
二、基本逻辑净需求=毛需求+预计出-预计入-期初库存+安全库存可按自由项匹配相应的BOM分解,如找不到相应的BOM,系统按默认版本BOM分解虚项及生成子订单物料不生成计划订单,按净需求分解下级物料三、MRP的基本任务1.从最终产品的生产计划(独立需求)导出相关物料(原材料、零部件等)的需求量和需求时间(相关需求);2.根据物料的需求时间和生产(订货)周期来确定其开始生产(订货)的时间。
四、主生产计划主生产计划是确定每一具体的最终产品在每一具体时间段内生产数量的计划。
这里的最终产品是指对于企业来说最终完成、要出厂的完成品。
通常包括如下内容:1、要生产什么东西?2、什么时候需要?3、要生产多少?主生产计划是独立需求,主要是根据客户合同或者对市场的预测,把在一定时期内需要生产的产品一一预测,使之成为展开物料需求计划的主要依据。
主生产计划是MRP的源头,所以,其的重要性是不言而喻的。
若其包含的以上三个主要参数有错误,则下面的计算肯定是错误的。
所以,主生产计划编制时,一定要准确,否则,不但不能给企业带来效益,反而会给企业带来损失。
NC对主生产计划的说明:包括主需求计划和主生产计划,可满足工业企业生产计划制定与管理的要求,并提供主生产计划的生成模拟与能力分析。
主需求计划是主生产计划的驱动数据,其主要来源是销售订单与销售预测,并可在不同的时区设定不同的需求合并策略。
物料需求计划(MRP)计算
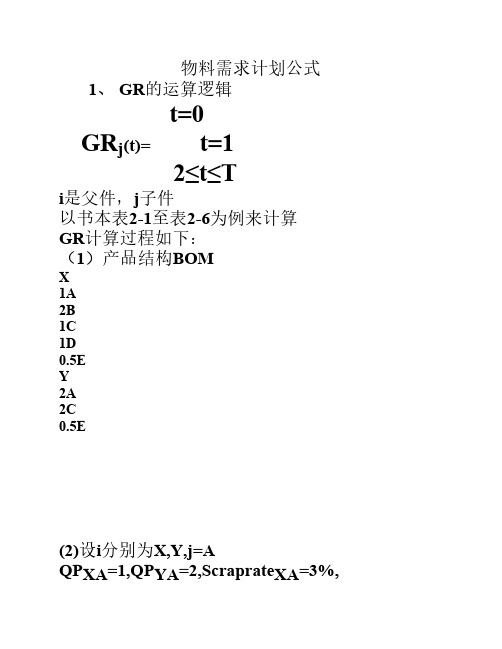
物料需求计划公式1、 GR的运算逻辑t=0GR j(t)= t=12≤t≤Ti是父件,j子件以书本表2-1至表2-6为例来计算GR计算过程如下:(1)产品结构BOMX1A2B1C1D0.5EY2A2C0.5E(2)设i分别为X,Y,j=AQP XA=1,QP YA=2,Scraprate XA=3%,Scraprate YA=5%t=0时,父件X,Y的POR都等于0POR x(0)=0,PORy(0) =0,indmd x(0)=0, indmd y(0)=0GR A(0)= 0t=1时,父件X,Y的POR分别为POR x(1)=200,POR y(1) =200,indmd x(1)=0, indmd y(1)=0GRA(1)= (200×1)/(1-3%)+(200×2)/(1-5%)+0+0=627.2t=2时, 父件X,Y的POR分别为POR x(2)= 0,POR y(1) =150,indmd x(1)=0, indmd y(1)=0GR A(2)= ( 0×1)/(1-3%)+(150×2)/(1-5%)+0=315.8 2.SR的来源T=0的逾期量SR j(0)是应到未到量,T≥1的SR j(t)为排定在未来t时段将会取得的“已订未交量”3、 POH的运算逻辑OH j+SR j(1)+SR j(0)-AL j-GR j(1) t=1POH j(t)=PAB j(t-1)+SR j(t)-GR j(t) 2≤t≤TOH A=300,SR A(1)=500,SR A(0)=0,AL A=200,GR A(1)=627(1) 还是以上面的例子来计算t=1时,j=APOH A(1)= OH A+ SR A(1)+ SR A(0)- AL A-GR A(1)=-27t=2时,j=APOH A(2)=PAB A(1)+SR A(2)-GR A(2)=473+0-315.8=157.24、 NR的运算逻辑NR j(t)=IF{POH j(t)≥SS j,0,} 1≤t≤T以上面的例子,j=APOH A(1)=-27, SS A=10,Yield A=100%NR A(1)= IF{POH A(1)≥SS A,0,}=IF{-27≥10,0,37}=37NR A(2)=05、 PORC的运算逻辑PORC j(t)=F(NR j(t),LSR) 1≤t≤T(1) 最小订购量法,即一旦有净需求,订购量最少应为某基准量LSPORC j(t)=IF(NR j(t)>0,max{NR j(t),LS j},0) 1≤t≤T(2) 定量批量法,即一旦有净需求,订购量始终为某基准量LS整数倍PORC j(t)=IF(NR j(t)>0,CEILING{NR j(t),LS j},0)1≤t≤T以上面例子为例j=A时NR A(1)=37, LS A=500,A的批量法则LSR为最小订购量法,所以用公式(1)PORC A(1)=IF(NR A(1)>0,max{ NR A(1),LS A},0)=500PORC A(2)=06、 PAB的运算逻辑PAB j(t)=POH j(t)+PORC j(t) 1≤t≤T以上面例子为例当t=1,j=A时POH A(1)= -27,PORC A(1)=500PAB A(1)=-27+500=4737、 POR的运算逻辑t=0POR j(t)= PORC j(t+LT j) 1≤t≤T-LT j0 T- LT j<t≤T以上面例子为例当t=0时,j=A,因此LT j=2POR A(t)=PORC A(1)+PORC A(2)=500+0=500当t=1时, j=A,因此LT j=2计算PORC A(3)案例MRP计算步骤如下:(1)首先计算第1阶MRP物料A和B全部期别的毛需求(2)随机选取A或B,此处假设选A,按{POH(t)→NR(t)→PORC(t)→PAB(t)}的顺序依次计算第1至第9期数据。