卡环(焊片)毕业设计
基于UG的汽车焊装夹具三维设计 毕业设计

毕业设计说明书基于UG 的汽车焊装夹具三维设计班 级: 学号: 姓 名:学 院:专指导教师:2014年 6 月软件工程 软件学院基于UG的汽车焊装夹具三维设计摘要汽车夹具是保证车身焊装质量的重要因素,影响整个汽车的制造精度和生产周期。
以某汽车前地板预总成焊装夹具的设计为例介绍了汽车车身焊装夹具的结构特点和基本要求,阐述了基于UG的汽车车身焊装夹具的三维设计方法。
关键词:焊装夹具,设计周期,制造精度Automobile welding fixture three-dimensional design based on UGAbstractauto jig are important factors to ensure the quality of automobile body welding, influence the manufacturing precision of the whole car and production cycle. To advance the floor before the car assembly welding fixture design as an example this paper introduces the structure characteristic and the basic requirement of the automobile body welding jig, elaborated the automobile body welding jig based on UG three-dimensional design method.key words:manufacturing,design cycle,precision welding fixture目录1 绪论 (1)1.1 我国汽车工业近况 (1)1.2 汽车车身焊装夹具综述 (2)1.2.1 车身焊装生产线的组成 (2)1.2.2 焊装夹具在焊接中的作用 (2)1.2.3 焊装夹具 (3)1.3 汽车焊装夹具应该解决的问题 (3)1.4 UG NX 6.0简介 (4)1.4.1 UGNX6.0的优势 (5)1.4.2 UGNX6.0主要功能 (5)2 汽车焊装夹具设计的注意事项 (7)2.1 设计式样书的说明 (7)2.1.1 生产过程 (7)2.1.2 主要控制断面的形状(MCS) (8)2.2 设计中文件管理规定 (10)2.2.1 文件目录命名规则 (10)2.2.2 文件命名规则 (11)2.2.3 图层的设定 (12)2.2.4 文件搜索目录的配置 (12)2.2.5 夹具的具体设计过程 (13)2.2.6 夹具中有关颜色设置的规定 (14)3 WH10汽车焊装夹具的具体设计过程 (15)3.1 导入PNL文件 (18)3.2 截断面 (18)3.3 夹具的整体设计 (20)3.3.1 确定旋转点 (20)3.3.2 确定汽缸安装铰支点的位置 (20)3.3.3 在零件图中进行建模 (22)3.3.4 焊接干涉检查 (24)3.3.5 完成总装图 (24)4 WH10汽车焊装夹具设计的打开状态 (25)4.1 定义连杆LINK (25)4.2 定义构件之间的运动关系JOINT (25)4.3 进行夹具打开过程的模拟仿真 (27)4.4 编辑导出机构的显示 (30)4.5 画车线 (32)5 二维图的生成 (34)5.1 二维图的出图标准 (34)5.2 典型夹具的二维图 (37)5.3 典型零件的装配图 (38)5.4 GA的装配图 (40)6 总结 (42)附录 (43)参考文献 (52)致谢 (53)1.1绪论1.1我国汽车工业近况汽车工业水平可以在很大程度上衡量一个国家的制造业水平。
焊片冲压工艺及模具设计
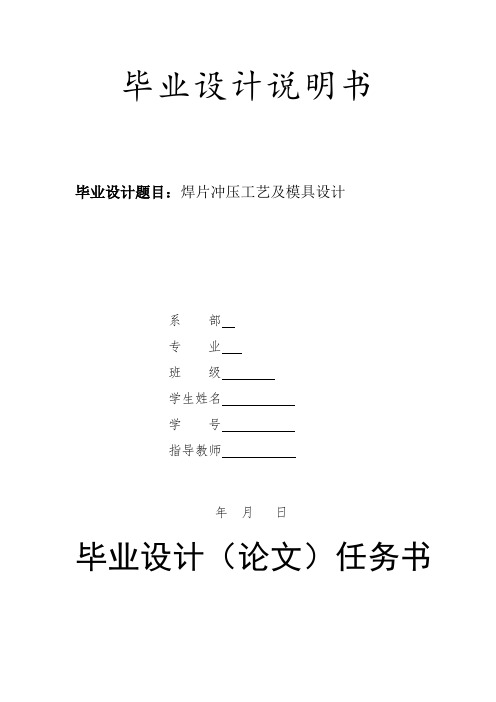
毕业设计说明书毕业设计题目:焊片冲压工艺及模具设计系部专业班级学生姓名学号指导教师年月日毕业设计(论文)任务书系部:企鹅332554595 有删减有CAD图专业:学生姓名:学号:设计(论文)题目:焊片冲压工艺与模具设计起迄日期:指导教师:年月1.本毕业设计(论文)课题来源及应达到的目的:本设计是来源于实际生产,达到能够独立的完成一个冲压模具的过程,在设计期间,能够独立的查阅有关资料,并熟悉设计为以后设计跟复杂的模具积累一定的经验。
2.本毕业设计(论文)课题任务的内容和要求(包括原始数据、技术要求、零件图(1)材料:黄铜板,具有良好的冲压性能。
原始资料:零件件图及其尺寸企鹅332554595 有删减有CAD图见说明书,材料:黄铜生产批量:大批量绪论目前,我国冲压技术与工业发达国家相比还相当的落后,主要原因是我国在冲压基础理论及成形工艺、模具标准化、模具设计、模具制造工艺及设备等方面与工业发达的国家尚有相当大的差距,导致我国模具在寿命、效率、加工精度、生产周期等方面与工业发达国家的模具相比差距相当大。
1.1国内模具的现状和发展趋势1.1.1国内模具的现状我国模具近年来发展很快,据不完全统计,2003年我国模具生产厂点约有2万多家,从业人员约50多万人,2004年模具行业的发展保持良好势头,模具企业总体上订单充足,任务饱满,2004年模具产值530亿元。
进口模具18.13亿美元,出口模具4.91亿美元,分别比2003年增长18%、32.4%和45.9%。
进出口之比2004年为3.69:1,进出口相抵后的进净口达13.2亿美元,为净进口量较大的国家。
在专业模具厂数量增加,能力提高较快;"三资"及私营企业发展迅速;国企股份制改造步伐加快等。
虽然说我国模具业发展迅速,但远远不能适应国民经济发展的需要。
我国尚存在以下几方面的不足:第一,体制不顺,基础薄弱。
“三资”企业虽然已经对中国模具工业的发展起了积极的推动作用,私营企业近年来发展较快,国企改革也在进行之中,但总体来看,体制和机制尚不适应市场经济,再加上国内模具工业基础薄弱,因此,行业发展还不尽如人意,特别是总体水平和高新技术方面。
焊片冲压工艺与模具设计说明书

Keywords:soldering lug
drawing
punching
bending
progressive die
II
河北工程大学毕业设计
目录
摘要 .................................................................................................................................I ABSTRACT ..................................................................................................................II 第1章 绪论 .....................................................................................................程大学毕业设计
4.3 排样设计与计算 ......................................................................................................9 4.3.1 确定是否要开工艺切口并选切口形式 ................................................................9 4.3.2 计算条料宽度 ....................................................................................................9 4.3.3 材料利用率的计算 ...........................................................................................10 4.4 冲压力的计算 ........................................................................................................10 4.4.1 拉深力的计算 .............................................................................................................. 11 4.4.2 弯曲力的计算 .................................................................................................. 11 4.4.3 冲裁力的计算 ..................................................................................................12 4.4.4 卸料力............................................................................................................13 4.4.5 推件力............................................................................................................13 4.4.6 顶件力............................................................................................................13 4.5 计算模具压力中心 ................................................................................................13 4.6 计算凸凹模工作部分尺寸并确定其制造公差 .........................................................15 4.6.1 冲孔(以凸模为基准)...................................................................................15 4.6.2 切口 ...............................................................................................................15 4.6.3 落料 ...............................................................................................................16 4.6.4 弯曲部分 ........................................................................................................16 4.6.5 拉深部分凸、凹模工作部分的尺寸 .................................................................17
焊接夹具的设计思路及案例

(11) 避免细杆受弯曲应力 (12)导轨的驱动力作用点,应作用在 两导轨摩擦力的压力中心上, 使两条导轨摩擦力产生的 力矩互相平衡 (13) 避免导轨受侧推力 (14) 避免螺杆受弯曲应力
10
(15)避免用螺纹件定位 (16)两定位销之间距离应尽可能远 (17)定位销要垂直于接合面
5
(10).满足夹具使用国家或地区的安全 法令法规; (11).形成公司内部产品的系列化和标准化。
6
二:强度和刚度的结构设计原则
(1) 避免受力点与支持点距离太远 (2) 避免悬臂结构或减小悬臂长度
(3) 勿忽略工作载荷可以产生的有利作用 (4) 避免机构中的不平衡力
7
(5) 受冲击载荷零件避免刚度过大
(4) 易损零件必须是可以快速更换的结构, 条件充分时最好不需要使用其它 工具进行;
4
(5).满足夹具在调整或更换过程中重复 定位的可靠性;
(6).尽可能的避免结构复杂、成本昂贵; (7).尽可能选用市场上质量可靠的标准品 作组成零件;
(8).焊接操作的灵活性即焊缝的开创性
(9).便于焊件的装卸,有良好的工艺性
(6) 避免影响强度的局部结构相距太近 (7) 不可以传力的中间零件应尽量避免受力 (8) 尽量避免安装时轴线不中产生的附加力
(9) 对于零件的易磨损表面增加一定的 磨损裕量(最大实体原则)
8
(10)
尽量不采用不符合阿贝原则 的结构方案
注:(阿贝原则是仪器设计中一个非
常重要的设计原则。古典的阿贝原则 是阿贝于1890年提出的一项测量仪设 计的指导性原则。他说:要是测量已 给出精确的测量结果,必须将被测件 布置在基准元件沿运动方向的延长线 上。因此可以称为共线原则。)
白车身焊接夹具的结构设计示例

汽车白车身焊接夹具的结构设计一、焊接夹具的设计方法与步骤1.在设计焊接夹具之前,应首先了解生产纲领、产品结构特征、工艺方法与生产线布置方式,作好充分的准备。
参照国外先进的夹具结构,并结合实际情况确定夹具总体方案。
诸如是固定夹具还是随行夹具,机械化、自动化水平是高是低,几种车型主要夹具是否混型共用等。
要准备好的工艺文件包括工序卡,技术协议,产品数模,夹具式样书,焊点文件。
确定使用那种标准件,那种气动元件以与甲方的特殊要求。
2•根据焊件结构特点与所需焊接设备(焊枪或C02)型号、规格,确定定位与夹紧方式(如果有式样书直接按照式样书上的夹紧定位方式即可);同时根据冲压件的工艺特点与后续装配工艺的需要选择合适的定位点与关键定位点。
大部分厂家已经规定好了零件定位的RPS孔和RPS面,不需要我们在制定定位基准了。
但是大家也一定要了解如何确定定位的基准孔和基准面。
3•主体机构确定后,便可确定辅助装置。
如水、电、气回路,气、液动元件以与覆盖件外部焊点所需保护铜板等。
4•按照确定好的定位点开始3D设计。
定位块要求在定位面的法向有3mm的调整量。
定位销要求在与定位孔中心线垂直的平面上有两个方向的调整量。
5•在进行夹具的具体结构设计时,应尽可能多的采用标准化元件,或提高自身的通用化、系列化程度。
二、焊接夹具的组成、结构与要求汽车焊接夹具通常由夹具地板、定位装置、夹紧机构、测量系统与辅助系统等五大部分组成。
命名规则压抉 定位板姿片—阴给走屮加工善时血名规则川J 己%拆准誓件;■'誣仲11祐仁怜购件-国旅件)的细徇和网能誓同更拒惬凶加工itii 保闱同臥■^P'.ATSW -三、如遇其它耒冷名的却丁1申皆寡盟国标、丰服項耳竇却琴匚由項甘负贾人缆一临时定冥-二-茸余敏也LT 库的名瞬和宦交乐"矚郎1."定枪粧"一一兄书在日第夹具中用王L 座与执行元什上H 的崔也联搖件.2.亍广""卜“卑在动柞'堵构中且一乍固立点迪夷点执衍殖开/閒合柱菱动柞的杠杆.3<iSO*—凡指基本划构之陷用于前后談姑拘XI 的i 惚囲餡,牡‘支崖"一一凡缶在欧羸中基于迪抿面的SR-®定蹩粽接rr5."開SE 扳"一一在日集中左达EASE 祖面的馆梅丛尺寸码里豈片 定也檢一)夹具底板夹具地板是焊接夹具的基础元件,它的精度直接影响定位机构的准确性,因此对工作平面的平面度和表面粗糙度均有严格的要求。
焊接工装卡具设计说明书

焊接工装卡具课程设计说明书学校: 洛阳理工学院系别:机电工程系专业:焊接技术及自动化姓名:陈文杰学号:Z10035419目录序言 .。
..。
..。
.。
.。
....。
.。
.......。
.。
.。
.。
..。
.. 3一、夹具设计任务.。
..。
...。
.。
....。
..。
.。
.....。
.。
..。
...。
..。
31、焊接产品(复合件)“撑杆焊接组合"的产品图。
.。
...。
....。
..。
32、焊接产品“撑杆焊接组合"的重点技术要求分析.。
..。
.。
...。
.。
3二、“撑杆焊接组合”装焊夹具设计方案的确定..。
.........。
...。
.。
.。
. 41、基准面的选择(夹具体方式的确定).。
.。
...。
..。
...。
..。
.. 42、定位方式及元器件选择.。
.。
.。
..。
.。
...。
..。
.。
..。
.。
..。
43、夹紧方式及元器件选择。
..。
..。
..。
.。
.。
..。
..。
..。
(5)4、装焊方案。
.....。
.。
.。
....。
...。
...。
.。
..。
.。
..。
.。
55、装焊夹具结构。
.。
.。
....。
..。
.。
.。
..。
....。
.。
.。
.。
.。
....。
5三、主要零件设计的说明.....。
...。
....。
....。
.。
..。
.。
.。
.。
.。
.。
. 51、夹具体。
..。
..。
.。
......。
.。
.。
.。
.。
.。
.。
.。
.。
.....。
. (5)2、压板..。
.。
..。
.。
..。
..。
...。
.。
..。
.。
..。
.。
.。
..。
.63、插销机构主体。
.。
...。
...。
.。
.。
..。
..。
..。
........。
.。
..。
...。
.. 64、快撤式螺旋夹紧器件。
.。
.。
.。
.。
...。
.。
.。
.....。
.......。
.。
..6四、夹具的装配要求。
.。
.。
.。
.。
...。
...。
..。
.。
.。
.....。
.。
.。
.。
.。
..6五、装焊夹具使用说明...。
.。
....。
..。
....。
冲压模具课程设计卡环
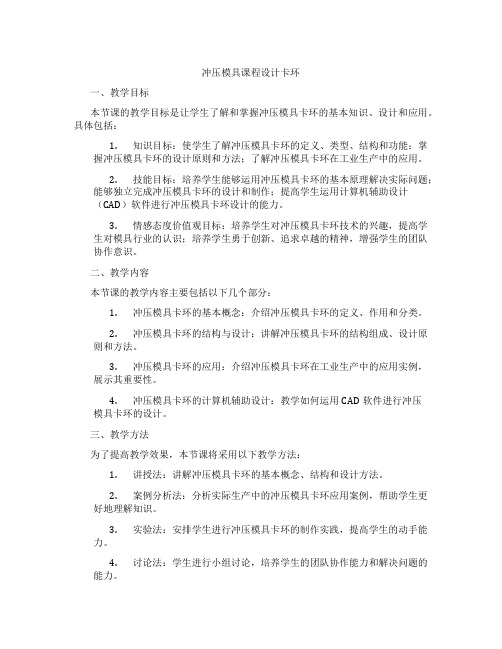
冲压模具课程设计卡环一、教学目标本节课的教学目标是让学生了解和掌握冲压模具卡环的基本知识、设计和应用。
具体包括:1.知识目标:使学生了解冲压模具卡环的定义、类型、结构和功能;掌握冲压模具卡环的设计原则和方法;了解冲压模具卡环在工业生产中的应用。
2.技能目标:培养学生能够运用冲压模具卡环的基本原理解决实际问题;能够独立完成冲压模具卡环的设计和制作;提高学生运用计算机辅助设计(CAD)软件进行冲压模具卡环设计的能力。
3.情感态度价值观目标:培养学生对冲压模具卡环技术的兴趣,提高学生对模具行业的认识;培养学生勇于创新、追求卓越的精神,增强学生的团队协作意识。
二、教学内容本节课的教学内容主要包括以下几个部分:1.冲压模具卡环的基本概念:介绍冲压模具卡环的定义、作用和分类。
2.冲压模具卡环的结构与设计:讲解冲压模具卡环的结构组成、设计原则和方法。
3.冲压模具卡环的应用:介绍冲压模具卡环在工业生产中的应用实例,展示其重要性。
4.冲压模具卡环的计算机辅助设计:教学如何运用CAD软件进行冲压模具卡环的设计。
三、教学方法为了提高教学效果,本节课将采用以下教学方法:1.讲授法:讲解冲压模具卡环的基本概念、结构和设计方法。
2.案例分析法:分析实际生产中的冲压模具卡环应用案例,帮助学生更好地理解知识。
3.实验法:安排学生进行冲压模具卡环的制作实践,提高学生的动手能力。
4.讨论法:学生进行小组讨论,培养学生的团队协作能力和解决问题的能力。
四、教学资源为了支持本节课的教学,将准备以下教学资源:1.教材:选用权威、实用的教材,为学生提供系统的理论知识。
2.参考书:提供相关的参考书籍,丰富学生的知识体系。
3.多媒体资料:制作精美的PPT,直观地展示冲压模具卡环的结构和应用。
4.实验设备:准备冲压模具卡环制作的实验设备,确保学生能够动手实践。
5.网络资源:利用互联网资源,为学生提供更多的学习资料和信息。
五、教学评估本节课的评估方式包括以下几个方面:1.平时表现:评估学生在课堂上的参与程度、提问回答等情况,占总评的30%。
毕业设计(论文)-筒体焊接夹具设计
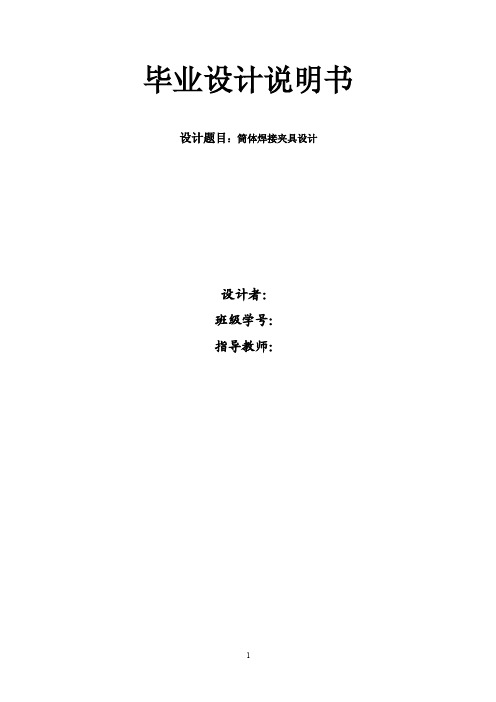
毕业设计说明书设计题目:筒体焊接夹具设计设计者:班级学号:指导教师:诚信承诺我谨在此承诺:本人所写的毕业论文《筒体焊接夹具设计与工艺规程》均系本人独立完成,没有抄袭行为,凡涉及其他作者的观点和材料,均作了注释,若有不实,后果由本人承担。
承诺人(签名):年月日摘要此次设计任务是对筒体的加工工艺、焊接夹具以及定位的设计,该工件由于上端面两小筒体的焊接位置和角度都有位置关系,在大筒体两端和侧面也需要焊接,因此在工序安排上,先两端面端盖,再焊接侧面端盖,最后焊接两小筒体,保证角度和中心距离。
这三步焊接工序采用同一个专用夹具,由于该零件的尺寸大,所需的夹紧力也大,因此都采用自动夹紧,手动脱件的方法,它的机构设计复杂,但能满足要求。
关键词筒体,加工工艺,定位,夹紧,夹具A bstractThe design task is to design and processing of welding fixture and positioning technology, the barrel body, the workpiece as the angle and position on the end face of the two small cylinder welding has welding position, also in the two ends of the cylinder body and side, so in the process arrangement, the first two end surface of the end cover, and the welding of the side cover, finally the welding of two small cylinder, ensure the angle and center distance. The three step of welding process with a special fixture, due to the size of the parts, the clamping force required is large, so the automatic clamping, manual methods of removal of parts, its mechanism is complex, but can meet the requirements of.Keywords:cylinder, processing technology, positioning, clamping, fixture目录摘要 (I)ABSTRACT (II)目录............................................................................................................................ I II 内容提要. (VI)序言 (VI)第一章焊接工装夹具及其在生产中的运用 (IX)第二章夹具设计的目的意义及要求 (X)第三章夹具任务书............................................................................................... X III3.1焊接产品的产品图......................................................................................... X III 3.2.焊接产品“筒体焊接组合”的重点技术要求分析..................................... X III第四章装焊夹具设计方案的确定....................................................................... X IV4.1.基准面的选择(夹具体方式的确定)......................................................... X IV 4.2.定位方式及元器件选择. (XV)4.3.夹紧方式及元器件选择................................................................................. X VI 4.4产品结构要求: ............................................................................................... X VI4.4.1 结构组成分析......................................................................................... X VI4.4.2 焊接结构件焊接性能分析 (XVII)第五章制定焊接结构件的焊接工艺................................................................... X IX5.1焊接方法及焊接规范 .................................................................................. X IX 5.2焊接材料的选择 .......................................................................................... X IX 5.3焊接工序的确定 .......................................................................................... X IX 5.4焊接质量的保证措施.................................................................................... X IX第六章装焊夹具结构 (XX)6.1基准面的选择 (XX)6.2定位器的设计................................................................................................ X XI第七章主要零件设计的说明 (XXIII)7.1夹具体 (XXIII)7.2夹紧装置的设计......................................................................................... X XIV 7.3夹紧材料的设计......................................................................................... X XIV 7.4夹具尺寸公差及粗糙度 (XXV)7.5国家标准件的选择 (XXV)7.6绘制夹具草图 (XXV)第八章夹具的装配要求 (XXVII)第九章夹具体的使用说明 (XXVIII)9.1端盖焊接 (XXVIII)9.2筒体焊接 (XXVIII)9.3夹具使用注意事项、保养及维护 (XXVIII)9.4夹具体的实用性说明................................................................................. X XIX 设计总结.. (XXX)参考文献 (XXXII)致谢................................................................................................................... X XXIV 全套设计请加197216396或401339828内容提要本论文应用本专业所学课程的理论和生产实际知识进行一次机械夹具设计工作的实际训练从而培养和提高学生独立工作能力,巩固与扩充了机械设计基础等课程所学的内容,掌握机械设计方法的方法和步骤,掌握夹具设计的基本的技能懂得了怎样分析零件的工艺性,怎样确定工艺方案,了解了夹具的基本结构,提高了计算能力,绘图能力,熟悉了规范和标准,同时各科相关的课程都有了全面的复习,独立思考的能力也有了提高。
焊装夹具毕业设计方案专业论文
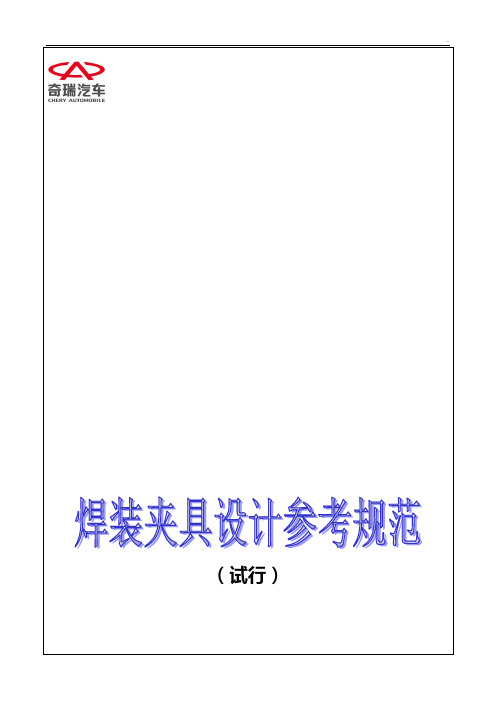
(试行)3.规制块的设计要求规范图1 图23.1.规制块尺寸要求常用规制块有如上(图1、图2和图3)三种结构(两销一钉),根据安装要求的不同,中间孔为M8的螺纹孔或ø9的螺钉过孔,两侧的均为ø8H7的销孔。
其尺寸要求如下(表2)所示:尺寸类型要求尺寸大小(mm)第一系列第二系列加工公差要求L 60 45B1 16 16H 根据板件型面的形状来确定±0.02L1 15 15L2 15 15B2 8 8 ±0.05S1 10 10 ±0.05S2 25 25 ±0.02S3 12.5 12.5表23.2.技术要求3.2.1. 材质要求:规制块的材料要求必须为45#钢并要进行热处理,使规制块工作面的表面硬度达到HRC30~35,工作面的粗糙度为,同时规制块要进行表面发蓝处理。
3.2.2. 在遇到如图4所示的板件结构时(需同时规制板件的两个面),要采用两个单独的规制块分别进行规制,不允许使用如图5所示的结构形式,如特殊情况会签时需经奇瑞公司确认后方可使用。
3.2.3. 规制块设计时原则上要求与板件垂直(图6),若因特殊情况不能保证时,则规制块的压紧方向最大斜角(图7)不大于15°,若大于该角度则需要使用导引挡块(CATCH STOPPER)。
图6 图73.2.4. 第一系列的规制块要优先选用,若设计时的空间不够或选用第一系列无法装配时,可以选用第二系列所规定的规制块,但装配时要便于人员的操作,会签时需经奇瑞公司确认后方可实施。
3.2.5. 规制块压紧时要求每个规制块所能达到的压力F(图8)范围为:25kgf≤F≤30kgf,气缸选用时要依此作为依据。
4.调整垫片的设计要求规范图95.角座的设计要求规范6.BASE板的设计要求规范图136.1.常用尺寸要求如表5所示尺寸类型常用尺寸大小(mm)S(面积:单位m²) S≤0.5 0.5<S≤0.8 0.8<S≤2.0 S>2.0 H1 20 20 22 25H2 15 15 15 15坐标网格线的平行度误差要求:相邻单一间隔距0.10mm/100mm;累积间隔距0.30mm/全长。
汽车座椅骨架的焊接夹具毕业设计说明书1

摘要本文研究的是汽车座椅骨架的焊接夹具设计问题,要求使工件定位迅速,装夹迅速,省力,减轻焊件装配定位和夹紧时的繁重体力劳动。
实现机械化,使焊接条件较差的空间位置焊缝变为焊接条件较好的平焊位置,劳动条件的改善,同时也有利于提高焊缝的质量。
本文首先分析了汽车座椅骨架焊装夹具设计的必要性和可行性;然后围绕座椅骨架焊装夹具设计这一核心,通过对汽车焊装生产线、汽车焊装夹具的结构特点进行分析,归纳了焊装夹具的设计步骤和要点;重点对汽车座椅骨架夹具的设计,包括基准面的选择,定位器的设计,夹具体设计,夹紧装置的设计。
其中,基准面的选择是根据总成件的大小,确定基板的尺寸,然后从标准件库选出合适的基板;定位器的设计是保证焊件在夹具中获得正确装配位置的零件和部件,应利用先装好的零件作为后装配零件某一基面上的定位支撑点,可以减少定位器的数量,提高装配精度;夹具体的设计是通过控制焊件角变形的夹紧力计算和控制焊件弯曲变形的夹紧力计算来确定的,通过公式计算得出拘束角变形所需的单位长度(焊缝)夹紧力q为31720279N,阻挡弯曲变形所需的夹紧力q为208711N,再根据焊件形状、尺寸来完成夹具体的设计。
夹紧装置的设计是本文设计的重中之重,这次设计的主要核心是通过气缸来改善传统手动夹紧的的繁重体力消耗以提高生产效率。
根据要求,设计气缸主要是对工件的夹紧,所以应该选择双作用气缸。
本文通过公式的计算确定一种缸径D为50mm,另一种缸径D为75mm。
合理的气缸选择,合理的气动原理思路,极大地提高了生产效率和产品质量。
关键词:工装; 夹具;汽动;焊接IAbstractThis thesis is to design welding fixture of automobile seat frame,The positioning of the workpiece clamping quickly, quickly, labor saving, reduces the welding assembly positioning and clamping of the heavy manual labor.In order to ensure the weld size, improve the assembly precision and efficiency, to prevent the deformation of the welding fixture.The realization of mechanization, easy to change rapidly, make the space position of welding conditions into a flat position better welding condition, the improvement of working conditions, but also conducive to improve the quality of the weld.including the overall program, positioning fixture, pneumatic clamping part, finally is the specific folder design. Because the welding fixture, some parts need to be rotated. For welding, when welding two pieces of the best and most powerful position, namely the welding positioner, which can solve this problem, easy welding.This paper firstly analyzes the automobile seat frame welding fixture design the necessity and feasibility; then on the seat frame welding fixture design as the core, through the analysis of structural characteristics of the production line, the automobile welding jig, sums up the design of welding fixture and the step points; focus on the automobile seat frame of welding process analysis, study on the seat fixture clamping position and correct positioning design; through the process of seat frame analysis, design of the substrate, mounting plate, positioning device, clamping mechanism. paper firstly analyzes the automobile seat frame welding fixture design the necessity and feasibility; then on the seat frame welding fixture design as the core, through the analysis of structural characteristics of the production line, the automobile welding jig, sums up the design of welding fixture and the step points; focus on the automobile seat frame of welding process analysis, study on the seat fixture clamping position and correct positioning design; through the process of seat frame analysis, design of the substrate, mounting plate, positioning device, clamping mechanism. Reasonable selection of the cylinder, the final completion of the structure design of seat frame welding fixtureKey words: Tooling;fixtures;pneumatic;welding目录摘要 (I)Abstract (II)第1章绪论 (1)1.1 课题的背景及意义 (1)1.2 汽车座椅国内研究现状 (2)1.3 焊装夹具研究概况 (2)1.3.1焊装线发展过程及目前的现状 (2)1.3.2焊装生产线的组成 (4)1.3.3焊装夹具设计基本要求 (4)1.3.4夹具的基本构成 (5)1.3.5夹具的设计步骤 (6)1.4 本课题研究内容及意义 (6)第2章汽车座椅焊接工艺 (7)2.1 汽车座椅的组成 (7)2.2 焊接结构件材料的选择 (7)2.3 焊接方法及焊接工艺 (7)2.4 焊接材料的选择 (8)2.5 焊接缺陷及防止措施 (8)第3章基于座椅骨架夹具的设计 (10)3.1 基准面的选择 (10)3.2 定位器的设计 (11)3.3 夹具体的设计 (12)3.4 夹紧装置的设计 (16)第4章结论 (18)参考文献 (19)致谢 (20)第1章绪论汽车座椅骨架制造是汽车制造业中的一项重要工程,随着我国汽车制造业的飞速发展,对汽车焊装线的需求量巨大,对其质量上的要求也日益提高。
焊片毕业设计说明书
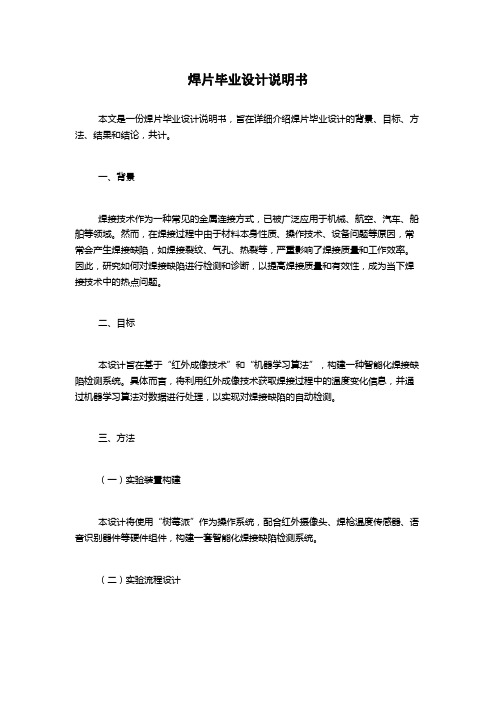
焊片毕业设计说明书本文是一份焊片毕业设计说明书,旨在详细介绍焊片毕业设计的背景、目标、方法、结果和结论,共计。
一、背景焊接技术作为一种常见的金属连接方式,已被广泛应用于机械、航空、汽车、船舶等领域。
然而,在焊接过程中由于材料本身性质、操作技术、设备问题等原因,常常会产生焊接缺陷,如焊接裂纹、气孔、热裂等,严重影响了焊接质量和工作效率。
因此,研究如何对焊接缺陷进行检测和诊断,以提高焊接质量和有效性,成为当下焊接技术中的热点问题。
二、目标本设计旨在基于“红外成像技术”和“机器学习算法”,构建一种智能化焊接缺陷检测系统。
具体而言,将利用红外成像技术获取焊接过程中的温度变化信息,并通过机器学习算法对数据进行处理,以实现对焊接缺陷的自动检测。
三、方法(一)实验装置构建本设计将使用“树莓派”作为操作系统,配合红外摄像头、焊枪温度传感器、语音识别器件等硬件组件,构建一套智能化焊接缺陷检测系统。
(二)实验流程设计利用树莓派控制红外摄像头、焊枪温度传感器,实时采集焊接过程中的温度变化信息。
将数据通过网络传输至云计算平台,通过机器学习算法对数据进行处理,产生相应的诊断结果。
(三)机器学习算法在本设计中,将使用支持向量机(SVM)算法对数据进行分类和识别。
SVM算法是一种常用的监督学习算法,通过对样本数据进行训练,以建立分类器,实现对新样本的分类。
具体而言,将利用SVM算法对焊接过程中的温度变化信息进行分类,将正常焊接数据集和焊接缺陷数据集进行比较,从而实现对焊接缺陷的自动检测。
四、结果与结论该设计基于红外成像技术和机器学习算法,构建了一套智能化焊接缺陷检测系统。
通过对样本数据的训练,系统能够自动识别焊接过程中的正常信息和缺陷信息,并在诊断结果中进行标识。
实验结果表明,该系统具有较高的准确率和稳定性,能够有效地提高焊接质量和工作效率。
因此,本设计的研究成果对于提高焊接技术的智能化水平,加快焊接行业的进步具有重要意义,具有一定的实用价值和推广意义。
卡环的结构和各部分的作用

卡环的结构和各部分的作用直接固位体主要是卡环,是直接卡抱在主要基牙上的金属部分,起固位、稳定和支持作用。
卡环的结构多式多样,以铸造三臂卡环为例,可以将卡环分为卡环臂、卡环体、(牙合)支托3部分。
(1)卡环臂:为卡环的游离部分,具有弹性,环绕基牙颊舌轴面。
其起始部分较坚硬,位于轴面非倒凹区,有稳定作用,可防止义齿侧向移位。
富有弹性的卡环尖位于轴面倒凹区,是卡环产生固位作用的部分,可防止义齿(牙合)向脱位。
卡环臂的形态因所用的材料和制作方法不同而异,常用的有圆形、半圆形和扁平形三种。
铸造方法制作的卡环臂,起始部分宽厚,愈向尖端愈窄而薄,呈逐渐尖削状,以使受力均匀,不易折断。
(2)卡环体:为连接卡环臂和(牙合)支托及小连接体的坚硬部分,无弹性,位于基牙轴面角的非倒凹区,具有稳定和支持作用,可防止义齿侧向或醒向移位。
(3)(牙合)支托:是卡环伸向基牙(牙合)面、产生支持作用的部分,具有防止义齿眼向移位和保持卡环在基牙上位置的作用;若基牙倾斜移位与对(牙合)牙(牙合)接触不良,则可借扩大的(牙合)支托,起恢复咬合接触的作用。
(牙合)支托是最常用的一种支托,此外还有切支托(位于基牙切缘)、舌支托(位于基牙舌隆突上)。
支托除与卡环的其他部分合用外,也可单独使用。
(牙合)支托的设计要求:①(牙合)支托的位置:(牙合)支托一般应放在缺隙两旁的基牙(牙合)面近远中边缘嵴上,如因咬合过紧,不易获得支托位置时,可放在上颌磨牙的颊沟处或放在下颌磨牙的舌沟处。
有时还可把支托放在(牙合)外展隙内。
前牙可放在尖牙舌隆突上或切缘上。
总之(牙合)支托的位置可根据具体情况灵活运用。
②(牙合)支托与基牙的关系:基牙上的(牙合)支托凹底,一般认为应与基牙的长轴垂直。
但是近年来许多学者主张(牙合)支托凹底应与基牙长轴的垂线成200斜面(即与基牙长轴呈700),以使(牙合)支托所承受的(牙合)力,能顺基牙长轴方向传递,不致使基牙倾斜移位。
③(牙合)支托的大小厚薄和形态:应根据制作(牙合)支托的材料和方法决定。
毕业设计(论文)-汽车车身焊装夹具设计[管理资料]
![毕业设计(论文)-汽车车身焊装夹具设计[管理资料]](https://img.taocdn.com/s3/m/c84ee3c6a32d7375a517805a.png)
绪论[摘要]焊接是现代机械制造业中一种必要的工艺方法,在汽车制造中得到广泛的应用,由于点焊、气体保护焊、钎焊具有生产量大,自动化程度高,高速、低耗、焊接变形小、易操作的特点,所以对汽车车身薄板覆盖零部件特别适合,因此,在汽车生产中应用最多。
在投资费用中点焊约占75%,其他焊接方法只占25%。
随着汽车工业的发展,汽车车身焊装生产线也在逐渐向全自动化方向发展,为了赶上国际水平,在提高产量的同时,要求努力提高汽车制造质量。
众所周知,实现自动化的前提是零件的制造精度要很高,希望焊接变形最小,焊接部位外观要清爽,故要求焊接技术越来越高。
我国面临加入WTO的机遇和挑战,焊接方面新技术的推广应用对汽车工业的品牌提升有极其重要的作用。
[关键字] 焊接;焊装生产线;自动化[Summary] The welding is in the modern machine manufacturing industry one essential necessity, getting the extensive application in the automobile manufacture, because of the spot welding , the shielded welding ,the rock drill welding has the product in a big way , the automation degree is high, high speed, low consumption, weld the characteristics of transform the small and easy operation, so overlay zero partses to the automobile carriage lamella special in keeping with, Therefore, applied in automobile produce at most .the spot welding approximately composes 75%,in the investment expenses ,other welding methods only account for 25%.Along with the development of the automobile industry, the automobile body welds installs the production line also at the time of gradually to full-automatically turning the direction development, for the sake of catching up the international level, at raising the yield, request to work hard to raise the automobile manufacturing quantity .It is known to all, the premise that carry out the automation is the manufacturing accuracy of the spare parts and want to be very high, hoping to weld to transform minimum, weld the part external appearance to want the clearness, so request to weld the technique more and more high .The our country faces the opportunity and challenges of join the WTO, the welding aspect new technical expansion application to automobile industry of brand promote to have the very and important function.[Key word] the weld ; the welding installs the production line ;automation第一章汽车工业概况第一节世界汽车工业发展概况从1886年德国人卡尔·奔驰和戈特利布·戴姆勒用四冲程汽油机制成汽车以来,已有一百多年的历史。
卡爪的加工工艺设计 数控加工专业毕业设计论文

3
1) 选择加工设备,选用南通机床厂生产的 XH713A 型加工中心,系统为 FANUC 0i. 2) 选择工艺设备
a) 该零件用平口钳夹紧 b) 刀具选择 Φ3mm 中心钻:钻中心孔 Φ4mm 丝锥:钻螺丝孔 Φ9.8mm 钻头:钻孔 Φ13mm 铰刀:铰孔 Φ10mm 立铣刀:铣台阶、铣槽 c) 量具的选用 分度值为 0.02mm 的游标卡尺 分度值为 0.001 的内径千分尺 5、 线切割加工工序 1) 选择加工设备,电火花数控线切割机床 DK7730。 2) 选择工艺设备 a) 选用压板式定位 b) 无加工刀具,采用电极丝来加工轮廓,本设计选钼丝。 c) 量具选择,分度值为 0.02mm 的游标卡尺。
5
3 执行标准 GB/T699-1999 标准规定的 45 钢推荐热处理制度为 850℃正火、840℃淬火、600℃回火,达 到的性能为屈服强度≥355MPa GB/T699-1999 标准规定 45 钢抗拉强度为 600MPa,屈服强度为 355MPa,伸长率为 16%,断面 收缩率为 40%,冲击功为 39J 4 现货规格 品名 规格/mm 材质 品名 规格/mm 材质 光亮圆棒 3.0-25 45# 热轧钢板 4-10 45# 热轧圆钢 12-50 45# 8-10 45# 热轧圆钢 Ф100-130 45# 12-16 45# 热轧圆钢 Ф140-150 45# 热轧钢板 18-20 45# 热轧圆钢 Ф160-170 45# 热轧钢板 22-28 45# 热轧圆钢 Ф16-40 45# 热轧钢板 30-34 45# 热轧圆钢 Ф16-45 45# 35-75 45# 热轧圆钢 Ф180-200 45# 75-80 45# 热轧圆钢 Ф200-280 45# 锻打钢板 80-100 45# 热轧圆钢 290-500 45# 锻打钢板 100-150 45# 热轧圆钢 500-1500 45# 锻打钢板 150 45# 热轧圆钢 Ф50-70 45# 锻打钢板 160 45# 热轧圆钢 Ф50-90 45# 锻打钢板 170 45# 热轧圆钢 Ф50-95 45# 锻打钢板 180 45# 力学性能 正火:850 ; 淬火:840 ; 回火:600 ; 抗拉强度:不小于 600Mpa ; 屈服强度: 不小于 355Mpa ; 伸长率:16% ; 收缩率:40% ; 冲击功:39J ; 钢材交货状态 硬度:不大于 未热处理:229HBS ; 退火钢:197HBS 5 力学性能 硬度 HRC 48-52 主要成份 Cr Si Mn C 化学成分(%) 0.42-0.50C,0.17-0.37Si,0.50-0.80Mn,0.035P,0.035S,0.25Ni,0.25Cr,0.25Cu 形 态 锭、坯、条、管、板、带 状 态 不热处理、退火、正火、高温回火 抗拉强度 Mpa 600 屈服强度 Mpa 355 伸长率% 16 45 号钢所针对的模具焊材型号为:CMC-E45 它是唯一接合性较好之中硬度钢焊条,适用于空冷钢、铸钢:如 ICD5、7CrSiMnMoV…等 等。汽车板金覆盖件模具及大型五金板金冲压模具之拉延、拉伸部位修补,也可用于硬面制 作。 6 主要用途 轴类零件的功用、结构特点及技术要求 轴类零件是机器中经常遇到的典型零件之一。它主要用来支承传动零 部件,传递扭矩和承受载荷。轴类零件是旋转体零件,其长度大于直径,一般由同心轴的外 圆柱面、圆锥面、内孔和螺纹及相应的端面所组成。根据结构形状的不同,轴类零件可分为
- 1、下载文档前请自行甄别文档内容的完整性,平台不提供额外的编辑、内容补充、找答案等附加服务。
- 2、"仅部分预览"的文档,不可在线预览部分如存在完整性等问题,可反馈申请退款(可完整预览的文档不适用该条件!)。
- 3、如文档侵犯您的权益,请联系客服反馈,我们会尽快为您处理(人工客服工作时间:9:00-18:30)。
1. 摘要1.1 冲模的概念、特点及应用冲模是将材料(金属或非金属)批量加工成所需冲件的专用工具。
所谓冲压是指在常温下利用模具在压力机的作用下,对材料施加压力,将材料分离或变形,从而获得一定形状、尺寸和精度零件的一种加工方法,又可称为冷冲压或板料冲压。
冲压是材料压力加工或塑性加工的主要方法之一,隶属于材料成型工程技术。
与机械加工及塑性加工的其它方法相比,冲压加工无论在技术方面还是经济方面都具有许多独特的优点。
主要表现如下:(1)在压力机的简单冲击下,能得到其它加工方法不能或难以得到的形状复杂、精度一致的制件。
(2)操作简便,劳动强度低,生产效率高,适合批量生产,便于实现机械化和自动化。
(3)尺寸稳定,制件精度高,互换性好。
(4)材料利用率高,制件重量轻、刚性好、强度高,在批量生产条件下成本低。
(5)在生产过程中,材料表面不易遭受破坏,制件表面质量好,通过塑性变形后,还可以使制件的力学性能有所提高。
由于冲压工艺的这些特点,因此其在现代工业生产中,尤其是大批量生产中应用十分广泛。
从精细的电子元件、仪表指针到汽车的覆盖件和大梁、高压容器封头及航空航天器的蒙皮、机身等,均需冲压加工。
目前用冲压工艺所获得的制品,在现代汽车、拖拉机、电机电器、仪器仪表及无线电电子产品和人们日常生活中,都占有十分重要的地位。
1.2 冲压基本工序冲压是机械中常见的一种金属加工方法。
冲压既可以加工金属材料,也可以加工非金属材料。
由于冲压件的形状、尺寸和精度要求不同,因此,冲压加工的方法是多种多样的。
根据材料的变形特点,冲压的基本工序可分为分离工序和变形工序两大类。
(1)分离工序板料在冲压力的作用下,其应力超过材料的强度极限,使之发生剪切而分离的加工工序。
(2)变形工序板料在冲压力的作用下,其应力超过材料的屈服强度,而低于抗拉强度,使之发生塑性变形而成为一定形状的制件的加工工序。
主要冲压工序的分类及特征可见下表1-1。
表1-1 主要冲压工序的分类类别工序名称工序特征分离工序切断用剪刀或模具切断板料,切断线不是封闭的落料用模具沿封闭线冲切板料,冲下的部分为工件冲孔用模具沿封闭线冲切板料,冲下的部分为废料切口用模具将板料局部切开而不全分离,切口部分材料发生弯曲切边用模具将工件边缘多余的材料冲切下来变形工序弯曲用模具使板料弯成一定角度或一定形状拉深用模具将板料压成任意形状的空心件压肋用模具将板料局部拉伸成凸起和凹进的形状翻边用模具将板料上的孔或外缘翻成直壁缩口用模具对空心件口部加由外向内的径向压力,使局部直径缩小胀形用模具对空心件加向外的径向力,使局部直径扩张整形将工件不平的表面压平,将原先弯曲或拉深件压成正确形状1.3 冲压模具1.3.1 冲模的要求冲压模具(简称冲模)是对金属板材进行冲压加工以获得合格产品的工具。
在冲压加工过程中,冲模的凸模与凹模直接接触被加工材料并相对作用使其产生塑性变形达到预期的零件。
因此对冲模的要求:冲模应该具有足够的强度,刚度和相应的形状尺寸精度;冲模主要零件应具有足够的耐磨性和使用寿命;冲模的结构应该确保操作安全,方便,便于管理和维修;冲模应有使材料方便送进,工件方便取出,定位可靠的装置,以保证生产的工件质量稳定;为使冲模上下运动准确,需要有导向装置;冲模零件的加工和装配应该尽可能简单,尽量采用标准件,以缩短模具的制造周期,降低成本;冲模应具有与压力机连接的部位,以适应安装和管理的需要。
1.3.2 冲模的分类冲模按冲压工艺性质分为:冲裁、弯曲、拉深、成形等;按模具的导向方式分为:导柱模、导板模、导筒模和无导向模等;按机械化程度分为:手工操作模、半自动模、自动化模等;按冲模材料分为:钢模、硬质合金模、铸铁模、低熔点合金模、聚氨酯橡胶模等。
1.3.3 冲模基本结构组成主要组成有工作零件,辅助装置,导向装置,支撑零件,紧固零件,其他。
(1)工作零件:冲模的工作零件是凸模和凹模,在复合模中还有凸凹模。
它们成对互相配合,完成对坯料的成形。
他们的形状尺寸,尺寸精度,固定方法决定着冲模的性能,模具成本及使用寿命。
(2)辅助装置:辅助装置是协助凸模,凹模完成工艺成形不可缺少的装置。
(3)导向装置:它是保证上模,下模准确运动的装置,要求工作可靠,导向精度好,有一定的互换性。
(4)支承零件:在上模座和下模座上安装着凸模,凹模及其它所有的零件。
它们和压力机连接,传递并承受着工作压力。
(5)紧固零件:中大型模具大多采用沉头螺栓和销作可卸式连接。
模具的连接可靠,拆卸方便也是冲模设计的一个基本要求。
1.4 冲压技术的现状及发展方向模具工业是国民经济的基础产业,是“百业之母”,是永不衰亡的行业,模具工业的发展水平标志着一个国家工业水平及产品开发能力。
我国模具工业解放后从无到有,在经历了半个多世纪的发展,已有了较大的提高,发展速度十分迅速,目前已初具规模。
近年来,对模具技术的探索和研究取得了可喜的成绩。
我国模具设计与制造技术的发展经历了手工作坊制造阶段、工业化生产阶段和现代化生产阶段。
伴随着计算机技术的快速发展,数字化、信息化模具CAD/CAE/CAM 技术和数控加工机床已普遍采用,模具产业正处于高速发展阶段。
虽然我国模具技术水平正在逐步提高,但与工业较为先进的国家相比,仍存在较大的差距,纵观我国的模具工业,既有高速发展的良好势头,又存在模具品种少、精度低、结构欠合理、寿命短等一系列的不足,无法满足整个工业迅速发展的迫切要求。
随着科学技术的不断进步和工业生产的迅速发展,许多新技术、新工艺、新设备、新材料不断涌现,因而促进了冲压技术的不断革新和发展。
其主要表现和发展方向如下:(1)冲压成形理论及冲压工艺方面冲压成形理论的研究是提高冲压技术的基础。
目前,国内外对冲压成形理论的研究非常重视,在材料冲压性能研究、冲压成形过程应力应变分析、板料变形规律研究及坯料与模具之间的相互作用研究等方面均取得了较大的进展。
特别是随着计算机技术的飞跃发展和塑性变形理论的进一步完善,近年来国内外已开始应用塑性成形过程的计算机模拟技术,即利用有限元(FEM)等有值分析方法模拟金属的塑性成形过程,根据分析结果,设计人员可预测某一工艺方案成形的可行性及可能出现的质量问题,并通过在计算机上选择修改相关参数,可实现工艺及模具的优化设计。
这样既节省了昂贵的试模费用,也缩短了制模具周期。
研究推广能提高生产率及产品质量、降低成本和扩大冲压工艺应用范围的各种冲压工艺,也是冲压技术的发展方向之一。
目前,国内外相继涌现出精密冲压工艺、软模成形工艺、高能高速成形工艺及无模多点成形工艺等精密、高效、经济的冲压新工艺。
其中,精密冲裁是提高冲裁件质量的有效方法,它扩大了冲压加工范围,目前精密冲裁加工零件的厚度可达25mm,精度可达IT16~17级;用液体、橡胶、聚氨酯等作柔性凸模或凹模的软模成形工艺,能加工出用普通加工方法难以加工的材料和复杂形状的零件,在特定生产条件下具有明显的经济效果;采用爆炸等高能效成形方法对于加工各种尺寸在、形状复杂、批量小、强度高和精度要求较高的板料零件,具有很重要的实用意义;利用金属材料的超塑性进行超塑成形,可以用一次成形代替多道普通的冲压成形工序,这对于加工形状复杂和大型板料零件具有突出的优越性;无模多点成形工序是用高度可调的凸模群体代替传统模具进行板料曲面成形的一种先进技术,我国已自主设计制造了具有国际领先水平的无模多点成形设备,解决了多点压机成形法,从而可随意改变变形路径与受力状态,提高了材料的成形极限,同时利用反复成形技术可消除材料内残余应力,实现无回弹成形。
无模多点成形系统以CAD/CAM/CAE技术为主要手段,能快速经济地实现三维曲面的自动化成形。
(2)冲模设计制造方面冲模是实现冲压生产的基本条件在冲模的设计制造上,目前正朝着以下两方面发展:一方面,为了适应高速、自动、精密、安全等大批量现代生产的需要,冲模正向高效率、高精度、高寿命及多工位、多功能方向发展,与此相比适应的新型模具材料及其热处理技术,各种高效、精密、数控自动化的模具加工机床和检测设备以及模具CAD/CAM技术也在迅速发展;另一方面,为了适应产品更新换代和试制或小批量生产的需要,锌基合金冲模、聚氨酯橡胶冲模、薄板冲模、钢带冲模、组合冲模等各种简易冲模及其制造技术也得到了迅速发展。
精密、高效的多工位及多功能级进模和大型复杂的汽车覆盖件冲模代表了现代冲模的技术水平。
目前,50个工位以上的级进模进距精度可达到2微米,多功能级进模不仅可以完成冲压全过程,还可完成焊接、装配等工序。
我国已能自行设计制造出达到国际水平的精度达2~5微米,进距精度2~3微米,总寿命达1亿次。
我国主要汽车模具企业,已能生产成套轿车覆盖件模具,在设计制造方法、手段方面已基本达到了国际水平,但在制造方法手段方面已基本达到了国际水平,模具结构、功能方面也接近国际水平,但在制造质量、精度、制造周期和成本方面与国外相比还存在一定差距。
模具制造技术现代化是模具工业发展的基础。
计算机技术、信息技术、自动化技术等先进技术正在不断向传统制造技术渗透、交叉、融合形成了现代模具制造技术。
其中高速铣削加工、电火花铣削加工、慢走丝切割加工、精密磨削及抛光技术、数控测量等代表了现代冲模制造的技术水平。
高速铣削加工不但具有加工速度高以及良好的加工精度和表面质量(主轴转速一般为15000~40000r/min),加工精度一般可达10微米,最好的表面粗糙度Ra≤1微米),而且与传统切削加工相比具有温升低(工件只升高3摄氏度)、切削力小,因而可加工热敏材料和刚性差的零件,合理选择刀具和切削用量还可实现硬材料(60HRC)加工;电火花铣削加工(又称电火花创成加工)是以高速旋转的简单管状电极作三维或二维轮廓加工(像数控铣一样),因此不再需要制造昂贵的成形电极,如日本三菱公司生产的EDSCAN8E电火花铣削加工机床,配置有电极损耗自动补偿系统、CAD/CAM集成系统、在线自动测量系统和动态仿真系统,体现了当今电火花加工机床的技术水平;慢走丝线切割技术的发展水平已相当高,功能也相当完善,自动化程度已达到无人看管运行的程度,目前切割速度已达到300mm2/min,加工精度可达±1.5微米,表面粗糙度达Ra=0.1~0.2微米;精度磨削及抛光已开始使用数控成形磨床、数控光学曲线磨床、数控连续轨迹坐标磨床及自动抛光等先进设备和技术;模具加工过程中的检测技术也取得了很大的发展,现在三坐标测量机除了能高精度地测量复杂曲面的数据外,其良好的温度补偿装置、可靠的抗振保护能力、严密的除尘措施及简单操作步骤,使得现场自动化检测成为可能。
此外,激光快速成形技术(RPM)与树脂浇注技术在快速经济制模技术中得到了成功的应用。