硝基芳烃催化加氢过程中的催化剂性能和工艺探究
催化加氢技术及催化剂讲解

催化加氢技术及催化剂作者: buffaloli (站内联系TA)发布: 2009-03-03一、意义1.具有绿色化的化学反应,原子经济性。
催化加氢一般生成产物和水,不会生成其它副产物(副反应除外),具有很好的原子经济性。
绿色化学是当今科研和生产的世界潮流,我国已在重大科研项目研究的立项上向这个方向倾斜。
2.产品收率高、质量好,普通的加氢反应副反应很少,因此产品的质量很高。
3.反应条件温和;4.设备通用性二、催化加氢的内容1.加氢催化剂Ni 系催化剂骨架Ni(1)应用最广泛的一类Ni 系加氢催化剂,也称Renay-Ni ,顾名思义,即为Renay 发明。
具有很多微孔,是以多孔金属形态出现的金属催化剂,该类形态已延伸到骨架铜、骨架钴、骨架铁等催化剂,制备骨架形催化剂的主要目的是增加催化剂的表面积,提高催化剂的反应面,即催化剂活性。
(2)具体的制备方法:将Ni 和Al, Mg, Si, Zn 等易溶于碱的金属元素在高温下熔炼成合金,将合金粉碎后,再在一定的条件下,用碱溶至非活性组分,在非活性组分去除后,留下很多孔,成为骨架形的镍系催化剂。
(3)合金的成分对催化剂的结构和性能有很大的影响,镍、铝合金实际上是几种金属化合物,通常所说的固溶体,主要组分为NiAl3, Ni2Al3, NiAl, NiAl2 等,不同的固熔体在碱中的溶解速度有明显差别,一般说,溶解速度快慢是NiAI3 > Ni2AI3 > NiAl > NiAI2 ,其中后二种几乎不溶,因此,前二种组分的多少直接影响骨架Ni 催化剂的活性。
(4)多组分骨架镍催化剂,就是在熔融阶段,加入不溶于碱的第二组分和第三组分金属元素,如添加Sn, Pb, Mn, Cu, Ag, Mo, Cr, Fe, Co 等,这些第二组分元素的加入,一般能增加催化剂的活性,或改善催化剂的选择性和稳定性。
(5)使用骨加镍催化剂需注意:骨架镍具有很大表面,在催化剂的表面吸符有大量的活化氢,并且Ni 本身的活性也很,容易氧化,因此该类催化剂非常容易引起燃烧,一般在使用之前均放在有机溶剂中,如乙醇等。
芳烃硝化反应机理的研究的进展
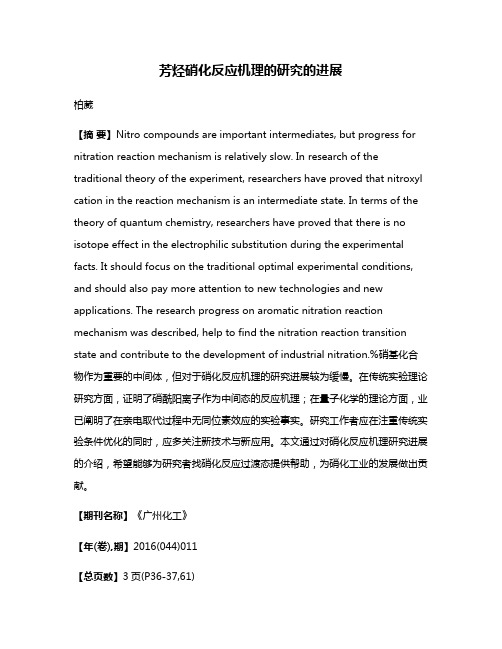
芳烃硝化反应机理的研究的进展柏葳【摘要】Nitro compounds are important intermediates, but progress for nitration reaction mechanism is relatively slow. In research of the traditional theory of the experiment, researchers have proved that nitroxyl cation in the reaction mechanism is an intermediate state. In terms of the theory of quantum chemistry, researchers have proved that there is no isotope effect in the electrophilic substitution during the experimental facts. It should focus on the traditional optimal experimental conditions, and should also pay more attention to new technologies and new applications. The research progress on aromatic nitration reaction mechanism was described, help to find the nitration reaction transition state and contribute to the development of industrial nitration.%硝基化合物作为重要的中间体,但对于硝化反应机理的研究进展较为缓慢。
催化加氢技术及催化剂

一、意义1.具有绿色化的化学反应,原子经济性。
催化加氢一般生成产物和水,不会生成其它副产物(副反应除外),具有很好的原子经济性。
绿色化学是当今科研和生产的世界潮流,我国已在重大科研项目研究的立项上向这个方向倾斜。
2.产品收率高、质量好,普通的加氢反应副反应很少,因此产品的质量很高。
3.反应条件温和;4.设备通用性二、催化加氢的内容1.加氢催化剂Ni系催化剂骨架Ni(1)应用最广泛的一类Ni系加氢催化剂,也称Renay-Ni,顾名思义,即为Renay发明。
具有很多微孔,是以多孔金属形态出现的金属催化剂,该类形态已延伸到骨架铜、骨架钴、骨架铁等催化剂,制备骨架形催化剂的主要目的是增加催化剂的表面积,提高催化剂的反应面,即催化剂活性。
(2)具体的制备方法:将Ni和Al, Mg, Si, Zn等易溶于碱的金属元素在高温下熔炼成合金,将合金粉碎后,再在一定的条件下,用碱溶至非活性组分,在非活性组分去除后,留下很多孔,成为骨架形的镍系催化剂。
(3)合金的成分对催化剂的结构和性能有很大的影响,镍、铝合金实际上是几种金属化合物,通常所说的固溶体,主要组分为NiAl3, Ni2Al3, NiAl, NiAl2等,不同的固熔体在碱中的溶解速度有明显差别,一般说,溶解速度快慢是NiAl3>Ni2Al3>NiAl>NiAl2,其中后二种几乎不溶,因此,前二种组分的多少直接影响骨架Ni催化剂的活性。
(4)多组分骨架镍催化剂,就是在熔融阶段,加入不溶于碱的第二组分和第三组分金属元素,如添加Sn, Pb, Mn, Cu, Ag, Mo, Cr, Fe, Co等,这些第二组分元素的加入,一般能增加催化剂的活性,或改善催化剂的选择性和稳定性。
(5)使用骨加镍催化剂需注意:骨架镍具有很大表面,在催化剂的表面吸符有大量的活化氢,并且Ni本身的活性也很,容易氧化,因此该类催化剂非常容易引起燃烧,一般在使用之前均放在有机溶剂中,如乙醇等。
催化加氢技术及催化剂讲解

催化加氢技术及催化剂作者: buffaloli (站内联系TA) 发布: 2009-03-03一、意义1.具有绿色化的化学反应,原子经济性。
催化加氢一般生成产物和水,不会生成其它副产物(副反应除外),具有很好的原子经济性。
绿色化学是当今科研和生产的世界潮流,我国已在重大科研项目研究的立项上向这个方向倾斜。
2.产品收率高、质量好,普通的加氢反应副反应很少,因此产品的质量很高。
3.反应条件温和;4.设备通用性二、催化加氢的内容1.加氢催化剂Ni系催化剂骨架Ni(1)应用最广泛的一类Ni系加氢催化剂,也称Renay-Ni,顾名思义,即为Renay发明。
具有很多微孔,是以多孔金属形态出现的金属催化剂,该类形态已延伸到骨架铜、骨架钴、骨架铁等催化剂,制备骨架形催化剂的主要目的是增加催化剂的表面积,提高催化剂的反应面,即催化剂活性。
(2)具体的制备方法:将Ni和Al, Mg, Si, Zn等易溶于碱的金属元素在高温下熔炼成合金,将合金粉碎后,再在一定的条件下,用碱溶至非活性组分,在非活性组分去除后,留下很多孔,成为骨架形的镍系催化剂。
(3)合金的成分对催化剂的结构和性能有很大的影响,镍、铝合金实际上是几种金属化合物,通常所说的固溶体,主要组分为NiAl3, Ni2Al3, NiAl, NiAl2等,不同的固熔体在碱中的溶解速度有明显差别,一般说,溶解速度快慢是NiAl3>Ni2Al3>NiAl>NiAl2,其中后二种几乎不溶,因此,前二种组分的多少直接影响骨架Ni催化剂的活性。
(4)多组分骨架镍催化剂,就是在熔融阶段,加入不溶于碱的第二组分和第三组分金属元素,如添加Sn, Pb, Mn, Cu, Ag, Mo, Cr, Fe, Co等,这些第二组分元素的加入,一般能增加催化剂的活性,或改善催化剂的选择性和稳定性。
(5)使用骨加镍催化剂需注意:骨架镍具有很大表面,在催化剂的表面吸符有大量的活化氢,并且Ni本身的活性也很,容易氧化,因此该类催化剂非常容易引起燃烧,一般在使用之前均放在有机溶剂中,如乙醇等。
催化剂在工业生产过程中的应用与优化

催化剂在工业生产过程中的应用与优化催化剂是一种能够促进或改变化学反应速率的物质。
在工业生产过程中,催化剂广泛应用于各种化学合成、石油加工、环境保护等领域。
其作用是通过提供新的反应路径或者降低活化能,加快目标反应的进行,从而提高生产效率和产物纯度。
本文将介绍催化剂在工业生产过程中的应用,并探讨如何优化催化剂的效果。
一、催化剂在化学合成中的应用1. 有机合成催化剂:有机合成是许多化学工业过程的核心。
催化剂在有机合成中起到引发并加速化学反应的重要作用。
例如,铂催化剂常用于合成有机酸和醇,以及氧化反应。
钯催化剂则被广泛应用于有机合成中的氢化和交叉偶联反应。
通过选择合适的催化剂,可以实现高效、高选择性的有机合成过程。
2. 化工合成催化剂:化工合成过程中,催化剂的应用得到了广泛应用。
例如,氧化铝催化剂在异丁烷加氧过程中扮演着重要角色,产生丁酮和丁烯。
另外,催化裂化是石油工业中常见的过程,通过加热和催化剂的作用,将重质石油分解成高级烃。
二、催化剂在石油加工中的应用石油加工是现代工业生产中不可或缺的一部分。
催化剂在石油加工过程中的应用主要包括裂化、重整和加氢。
1. 催化裂化:催化裂化是将原油中的长链烃分解成较短链烃的过程。
这涉及到催化剂的选择和设计,以提高产物的分布和选择性。
常见的催化裂化催化剂包括沸石催化剂和金属催化剂。
沸石催化剂在催化裂化中起到分子筛的作用,帮助控制碳链的长度和产物选择性。
金属催化剂则可以促进裂解反应的进行。
2. 催化重整:催化重整是将低价的烃类转化为高级芳烃和烯烃的过程。
这旨在提高石油产品的质量和附加值。
催化重整过程中常使用铂-铝氧化物催化剂,该催化剂能够促进烃类的分子重排,生成具有较高活性的芳烃和烯烃。
3. 催化加氢:催化加氢是将石油原料中的硫、氮和氧化物还原为对环境和使用设备无害的物质的过程。
通过加氢反应可以大幅度减少有害气体的排放,同时提高石油产品的品质。
常见的催化加氢催化剂包括钼-铝氧化物和镍-硫化物催化剂。
加氢精制催化剂的组成、制备及其性能评价

加氢精制催化剂的组成、制备及其性能评价前言:加氢精制是石油加工的重要过程之一,它主要是通过催化加氢脱除原油和石油产品中的S、N、O以及金属有机化合物等杂质[1]。
加氢精制主要包括加氢脱硫(HDS)、加氢脱氮(HDN)和加氢脱金属(HDM)等工艺,一般在催化加氢过程中是同时进行的。
其具体流程图[1]如下所示:近年来,由于原油的质量逐渐变差以及对重油的加工利用的比例逐渐增大,给加氢精制过程提出了更高的要求。
出于对环保的重视,世界各国普遍制订了严格的环保法规,对汽油、柴油等燃料油中N和S含量作出了严格的限制。
此外,又对汽油中的苯、芳烃、烯烃含量、含氧化合物的加入量以及柴油十六烷值和芳烃含量等也有严格的限制指标。
这些清洁燃料的生产均与加氢技术的发展密切相关[2]。
因而加氢精制技术已成为石油产品改质的一项重要技术,其核心又在于加氢精制催化剂的性能。
一、催化加氢催化剂的组成及其制备方法1.加氢催化剂的组成加氢精制催化剂一般都是负载型的,是有载体浸渍上活性金属组分而制成[3]。
载体一般均是Al2O3。
(1)活性组分其活性组分主要是由钼或钨以及钴或镍的硫化物相结合而成[4]。
目前工业上常用的加氢精制催化剂是以钼或钨的硫化物为主催化剂,以钴或镍的硫化物为助催化剂所组成的。
对于少数特定的较纯净的原料,以加氢饱和为主要目的时,也有选用含镍、铂或钯金属的加氢催化剂的。
钼或钴单独存在时其催化活性都不高,而两者同时存在时互相协合,表现出很高的催化活性。
所以,目前加氢精制的催化剂几乎都是由一种VIB族金属与一种VIII族金属组合的二元活性组分所构成。
(2)载体γ-Al2O3是加氢精制催化剂最常用的载体。
一般加氢精制催化剂要求用比表面积较大的氧化铝,其比表面积达200~400m2/g,孔体积在0.5~1.0cm3/g之间。
[1]氧化铝中包含着大小不同的孔。
不同氧化铝的孔径分布是不同的,这取决于制备的方法和条件。
此外,加氢精制催化剂用的氧化铝载体中有时还加入少量的SiO2,SiO2可抑制γ-Al2O3晶粒的增大,提高载体的热稳定性。
催化加氢还原芳香硝基化合物制备芳胺的技术进展

精
58
细
石
油
化
工
第2卷 第 4 3 期
20 0 6年 7月
S PECI ALI TY ETROCHEM I P CA LS
催 化 加 氢 还 原 芳 香 硝 基 化 合 物 制 备 芳 胺 的 技 术 进 展
徐善 利 陈宏博 李树 德
影响。
用于 催 化 加 氢 反 应 的 催 化 剂 主 要 为 过 渡 金
属, 可分 为贵 金属 系和 一般金 属 系 。贵金属 以铂 、 钯 为主 , 外 还有铑 、 、 等 , 特点是 催化 活性 此 锇 钌 其
高 , 应条 件 温 和 , 反 适用 于 中性 或 酸性 反 应 , 虽然 铂 的活性 最好 , 但其 价格 相对 较 高 , 限制 了它 的应
常用 的催 化 剂 可 以是 金 属 单 质 的 粉末 , 如铂 黑、 钯黑等 , 可直 接 以金属 氧化物 还原制得 ; 或者是 骨架型 , R n yNi 如 ae- 。为了使活性金 属能和原料充
收 稿 日期 :0 6— 3— 9 修 改稿 收 到 日期 : 0 6— 6 9 20 0 0 } 2 0 0 —1 。
作 者 简介 : 善利 (90一 ,男, 士 , 事 染 料 中 间体 合成 的 徐 18 ) 硕 从
研究。
维普资讯
第2 3卷 第 4期
徐 善 利 ,等 . 化 加 氢 还 原 芳 香 硝 基 化 合 物 制 备 芳 胺 的技 术 进 展 催
5 9
分 接触而把金属 载到一定 的载 体上 , 如常见 的 P / d
C、 tC、 d A 。 P/ 。 P / P / l 、 tAl 等催 化 剂 。常见 的载 O O
催化剂及其催化活性的研究

工业上常用单位重量或单位体积的催化剂对反应物转化程度(转化百分数)即用转化率来表示活性。转化率高则活性高,转化率低则活性低。例如用转化率和收率表示催化活性,设反应为aA→pB
则A的转化率为XA= a,p—反应方程式系数项
B的收率为YB= NA0—反应物A的总量
B的选择率为SB= NA—未反应的反应物A的量
空速和接触时间是决定转化率和产率的重要因素。因此工业上又用空时得量(SpacefimeYield简称STV)的数值来表示催化剂的活性。它是指每小时每升催化剂所能生产的产物重量(用公斤计算)的数值。
由上述影响可知,我们在评定催化剂活性好坏时,必须固定温度,空速(或接触时间)时才行,否则就没有意义。
3.2添加物对催化剂活性的影响
助催化剂:人们希望改善催化剂的性能,常常在催化剂中添加适宜的助催化剂。由于助催化剂的种类较多,清况也很复杂,很难把助化剂和载体的作用严格区别开。一般认为助催化剂的用量少,而载体的用量大。即:助催化剂:“在催化剂中加入少量物质(通常<01%)这些物质当单独存在时,活性很小,但添加到催化剂中后,可使催化剂具有更好的活性、稳定性或选择性”。助催化剂有一个最适宜的添加量,此时活性可以达到最大值。助催化剂与主催化剂之间实际上发生复杂的作用。助催化剂具有能改变催化剂的表面积,增加催化剂的活性中心,防止活性中心半熔而增加催化剂的稳定性等作用。助催化剂大体分为:结构助催化剂(Structuralpromoter)、电子助催化剂(Electronicpromoter)、双重作用的助催化剂(DualAdditionpromoter)、晶格缺陷助催化剂(LatticeDefectpromoter)、增界助催化剂(Ad lineationpromoter)、选择性助催化剂(Selectivity promoter)、扩散助催化剂(Diffusion promoter)。
硝基化合物还原方法研究报告

硝基化合物还原方法研究报告芳胺是重要的有机合成中间体和原料,用于合成农药、医药、橡胶助剂、染料和颜料、合成树脂、纺织助剂、表面活性剂、感光材料等多种精细化学品。
芳胺可由相应的芳香硝基化合物还原得到,工业中还原芳香硝基化合物的方法主要有金属(铁粉、锌粉等)还原法、催化加氢还原法和硫化碱还原法,而其他还原方法也多有研究。
最近,针对铁粉还原法制备芳胺的过程中,存在含盐废水的污染问题,还提出了许多绿色,环境友好的还原硝基物制相应芳胺的新方法。
1 金属还原法金属还原法,尤其铁粉还原法适用面广、操作简单、还原效率高、选择性好、产品质量好,尤其对品质有特殊要求的芳胺的制备,仍有优越性。
适宜于采用铁粉还原法生产的胺类有:①容易被水蒸气蒸出的芳胺;②易溶于水,并且可以通过蒸馏分离的芳胺;③能溶于热水的芳胺;④含磺酸基或羧酸基等水溶性基团的芳胺。
近年来,仍有许多关于各种活化铁还原芳香硝基化合物,以适合特殊芳胺制备方法的研究。
Hazlet、孙权一、LIU等分别制成了活化铁,还原各种芳香硝基化合物,相应芳胺的收率很高,对于那些易还原的基团不影响。
除了铁粉外,锌粉也用于还原芳香硝基化合物制芳胺,锡也是一种常用的还原剂。
另外,用镁粉,锰粉,铟、钐以及活性镍等作为还原剂,还原芳香硝基化合物也有研究。
这些金属还原芳香硝基化合物制备相应芳胺,均可获得较高收率的芳胺。
与铁粉相比,这些金属的价格较贵,有些还非常容易氧化。
而且多数反应还需要催化剂或其他条件辅助作用,反应后都会产生含盐的废弃物。
2 催化加氢还原法在催化加氢还原反应过程中,不产生有害副产物,废气、废液排放很少。
由于催化加氢还原硝基苯制苯胺的产量大,产品质量高,对解决环境污染问题有着显著的优越性,目前已经成为工业上生产苯胺的主要方法。
其缺点是对于苯环上有其他易还原取代基的芳香硝基化合物,其催化加氢过程中会发生大量副反应。
为了抑制这些副反应,一种方法是对催化剂进行改性,常用于催化加氢还原硝基物的催化剂有:铂基催化剂心、钯基催化剂、钌基催化剂、金基催化剂、骨架镍催化剂以及非晶态合金催化剂。
化工工艺学第四章4.3催化加氢及脱氢过程课件

(3)影响催化剂性能的主要因素
①化学组成
活性组分、助催化剂、载体
②结构
比表面、孔结构、晶型、表面性质
③制备工艺
共沉淀、浸渍、离子交换、机械混合等
(4)活化与再生
活化
新催化剂在反应器中热处理,以疏松结构,调 整活性物质相互状态,调变活性组分的原子形 态。
①多位吸附:苯在催化剂表面发生多位吸附,然后加氢得产物。 ②单位吸附:苯分子只与催化剂表面一个活性中心发生化学吸附, 形成π–键吸附物,然后把H原子逐步吸附至苯分子上。
多位吸附 单位吸附
(2)动力学方程
k2 双曲线型:
bi:吸附系数 Pi:分压 n:吸附活性中心数 幂指数型:
(3)温度影响 a.对反应速度的影响
还有深度裂解副产物生成
(4)压力的影响
压力的影响视反应的动力学规律而定
※气相加氢,与反应级数有关
①加氢物质的级数为0 1级,PA↑, r ↑ 0级 , PA与 r无关
负值时, PA↑, r ↓
②若产物在催化剂上是强吸附,就会占据一部分催化 剂的活性中心,抑制了加氢反应的进行,产物分压越 高,加氢反应速率就越慢。
, rmax
r
Te :对应转化率x的平衡温度
T
在Top温度下,r达到最大值。
xA
允许温度
最佳温度曲线
T
最佳温度:对于一定的反应物系组成,某一可逆放热反应具 有最大反应速率的温度称为相应于这个组成的最佳温度。 最佳温度曲线:相应于各转化率的最佳温度所组成的曲线, 称为最佳温度曲线。
b.温度对选择性的影响 T↑,S↓,因为副反应的活化能大 如:
从硝基苯催化加氢合成对氨基苯酚的工艺

从硝基苯催化加氢合成对氨基苯酚的工艺1. 引言催化加氢合成对氨基苯酚是一种重要的工业过程,可以通过将硝基苯转化为对氨基苯酚,进而合成其他有机化合物。
本文将介绍从硝基苯催化加氢合成对氨基苯酚的工艺,并探讨其反应机理、催化剂选择和工艺优化等方面的内容。
2. 反应机理硝基苯催化加氢合成对氨基苯酚的反应机理主要包括硝基还原和芳香环氢化两个步骤。
首先,硝基苯在催化剂的作用下发生还原反应,生成亚硝基苯。
然后,亚硝基苯进一步发生芳香环氢化反应,生成对氨基苯酚。
3. 催化剂选择3.1 硝基还原催化剂选择硝基还原的关键是选择一个高效的催化剂。
常用的硝基还原催化剂包括铜、铈和铳基催化剂。
其中,铜是最为常见的催化剂,具有高催化活性和良好的稳定性。
3.2 芳香环氢化催化剂选择芳香环氢化的关键是选择一个具有高选择性的催化剂。
常用的芳香环氢化催化剂包括铂、钯和铑基催化剂。
其中,铂是最为常见的催化剂,具有高选择性和较高的稳定性。
4. 工艺优化4.1 反应条件优化反应条件对于催化加氢合成对氨基苯酚的工艺至关重要。
合适的反应温度和压力可以提高反应速率和产率。
典型的反应条件包括温度在120-150°C,压力在5-10 MPa。
4.2 催化剂用量优化催化剂的用量是影响反应效率和经济性的重要参数。
过低的催化剂用量可能导致反应速率过慢,而过高的催化剂用量则会增加生产成本。
因此,需要通过实验确定合适的催化剂用量。
4.3 反应时间优化合适的反应时间可以使得反应达到最大产率。
过短的反应时间可能导致反应不完全,而过长的反应时间可能导致产物的降解。
因此,需要进行一系列的试验来确定最佳的反应时间。
4.4 副反应的抑制在催化加氢合成对氨基苯酚的过程中,可能还会伴随一些副反应的发生,例如氨基苯酚的进一步氢解和二聚化。
为了抑制这些副反应的发生,可以通过调整反应条件、催化剂选择和添加抑制剂等方式进行。
5. 结论硝基苯催化加氢合成对氨基苯酚是一种重要的工业过程,其工艺涉及硝基还原和芳香环氢化两个步骤。
加氢精制原理及催化剂性能简介

3.1 原料及产品 原料:焦化汽油 主要产品:精制汽油。 副产品:低分瓦斯、塔顶瓦斯、高分排放氢。
3.2 主要操作条件
4 加氢精制催化剂在具体装置的应用
45万加氢目前使用的主催化剂为FH-98改进型 加氢精制催化剂,保护剂、助剂FZC系列、 FHRS-1等。
4.1 本装置催化剂及保护剂等理化性质
45万吨/年汽柴油加氢装置:
于2002年12月建成投产,由中国石化洛阳设计院 设计
使用抚研院FH-98加氢催化剂,固定床加氢反应 器
以焦化汽、柴油、催化柴油混合后为原料,生产 的精制柴油作为成品直接出厂,汽油作为催化重 整原料。为配合公司汽柴油质量升级工作,该装 置于2012年6月进行技术改造,改为纯焦化汽油 加氢装置,主体催化剂未调整。
4.2 催化剂装填
4.3 干燥
由于催化剂载体具有吸湿性,催化剂的吸水量 一般达1~3%,甚至可以到10%,如果湿催化剂 和原料一起升温,易造成催化剂破碎,破坏催化 剂物理结构,增加床层压降。因此,使用前进行 干燥脱水工作。
方式:热氮气循环脱水
温度 ℃
300 250 200
150 100 50
Hg、Cu等)
烃类加氢饱和 少量烃类分子异构化 少量开环、大分子裂化
2.2 主要反应
2.2.1 加氢脱硫反应
硫化物的存在使油品在燃烧过程中生成二氧化 硫从而造成环境污染。
含硫化合物的加氢反应,在加氢精制条件下石 油馏分中的含硫化合物进行氢解,转化成相应的 烃和H2S,从而硫杂原子被脱掉。几种含硫化合 物的加氢精制反应如下:
温度 ℃
350 300 250 200 150 100
50 40 0 0
硫化升温曲线
320
320
炼油厂采用的主流石油加工工艺——催化加氢工艺详解

3、反应空速
空速的大小反映了反应器的处理能力和反应时间。空速越大,装置的 处理能力越大,但原料与催化剂的接触时间则越短,相应的反应时间 也就越短。因此,空速的大小最终影响原料的转化率和反应的深度。
1、加氢处理催化剂 加氢处理催化剂中常用的加氢活性组分有铂、钯、镍等金属和钨、钼、 镍、钴的混合硫化物,它们对各类反应的活性顺序为: 加氢饱和 Pt,Pb﹥Ni﹥W-Ni﹥Mo-Ni﹥Mo-Co﹥W-Co 加氢脱硫 Mo-Co﹥Mo-Ni﹥W-Ni﹥W-Co 加氢脱氮 W-Ni﹥Mo-Ni﹥Mo-Co﹥W-Co 加氢活性主要取决于金属的种类、含量、化合物状态及在载体表面的 分散度等。 活性氧化铝是加氢处理催化剂常用的载体。
目前炼油厂采用的加氢过程主要分为两类:一类是加氢处理,一 类是加氢裂化。
用这种技术的目的在于脱除油品中的硫、氮、氧及金属等杂质, 同时还使烯烃、二烯烃、芳烃和稠环芳烃选择加氢饱和,从而改善原 料的品质和产品的使用性能。此外,加氢裂化的目的在于将大分子裂 化为小分子以提高轻质油收率,同时还除去一些杂志。其特点是轻质 油收率高,产品饱和度高,杂质含量少。 作用机理 吸附在催化剂上的氢分子生成活泼的氢原子与被催化剂削弱了键的 烯、炔加成。烯烃在铂、钯或镍等金属催化剂的存在下,可以与氢加 成而生成烷烃。加氢过程可分为两大类:
4、催化剂再生 国内加氢装置一般采用催化剂器内再生方式,有蒸汽-空气烧焦法和 氮气-空气烧焦法两种。 再生过程包括以下两个阶段: ①再生前的预处理 在反应器烧焦之前,需先进行催化剂脱油与加热炉清焦。 ②烧焦再生 通过逐步提高烧焦温度和降低氧浓度,并控制烧焦过程分三个阶段完 成。
硝基苯液相催化加氢制苯胺技术进展

硝基苯液相催化加氢制苯胺技术进展相关专题:催化剂时间:2008-11-27 13:50苯胺是一种用途十分广泛的有机化工中间体,广泛应用于聚氨酯原料二苯基甲烷二异氰酸酯(MDI)、燃料、医药、橡胶助剂、农药及精细化工中间体的生产。
尤其是作为MDI的生产原料,具有很大的市场潜力。
近年来,随着MDI 生产的不断发展,苯胺生产能力不断扩大,生产装置趋向大型化。
目前苯胺生产工艺路线主要有硝基苯铁粉还原法、苯酚氨化法和硝基苯催化加氢法,分别占苯胺总生产能力的5%、10%和85%,其中硝基苯催化加氢法又分为固定床气相催化加氢、流化床气相催化加氢和液相催化加氢法。
目前我国除山东烟台万华聚氨酯集团公司采用固定床工艺、山西天脊集团公司采用液相加氢工艺外,全部采用流化床气相催化加氢法。
虽然气相加氢取得了流化床和固定床的混合床技术、催化剂体外再生等一些科技成果,使加氢装置有了很大的改进;但是当年产量达到10万t以上时,就遇到了设备体积以及产品质量的巨大挑战。
而国外应运而生的液相法加氢制苯胺技术则成功地解决了这一问题,使苯胺的生产技术有了质的飞跃。
由于液相加氢具有反应温度低、副反应少、催化负荷高、设备生产能力大、总投资低等优点,近年来已引起人们的关注。
本文介绍了硝基苯液相催化加氢技术研究进展,为我国硝基苯催化加氢制苯胺技术提供参考建议。
1 传统硝基苯液相加氢制苯胺工艺为了解决硝基苯气相加氢制苯胺反应温度高等问题,英国IC I、日本三井东亚(Mitsui Toatsu)、美国杜邦(DuPont)公司等相继开发出硝基苯液相催化加氢工艺。
1.1 ICI公司硝基苯液相加氢制苯胺工艺ICI公司在1939年成功开发硝基苯液相加氢制苯胺工艺,采用苯胺作为溶剂,以硅藻土为载体的活性镍为催化剂,载体的粒径为200目,在反应时要及时移走反应中产生的水,防止水浸湿催化剂。
当硝基苯浓度较低时,如当苯胺的摩尔分数大于还原的摩尔分数时,该催化剂具有很好的活性。
硝基加氢还原的操作规程

硝基加氢还原的操作规程硝基加氢还原操作规程一、实验目的:掌握硝基化合物加氢还原的基本操作,了解硝基化合物加氢还原反应的原理和条件。
二、实验原理:硝基化合物(通常指硝基苯类化合物)可以通过加氢还原反应转化为胺化合物。
加氢还原反应是指在适当的条件下,用氢气将硝基官能团还原为氨基官能团的反应。
硝基化合物加氢还原的具体反应途径与条件有关,常常需要选择适当的催化剂、溶剂以及反应温度和压力等操作条件。
三、实验仪器与试剂:1. 氢气气源;2. 反应器;3. 加热器或冷却器;4. 催化剂(如钯/碳催化剂);5. 硝基化合物试样;6. 无水溶剂(如乙醇、二甲基甲酰胺等);7. 氢气压力调节器;8. 水浴或温度控制设备。
四、操作步骤:1. 将所需的催化剂加入反应器中,并加入适量的无水溶剂。
在加入催化剂之前,应事先用气体灼烧法清洗催化剂,以去除表面的有机物和杂质。
2. 将硝基化合物试样加入反应器中。
试样的量应根据反应容器的大小和催化剂的活性而定,一般为一定摩尔比例的试样与催化剂之间的量比。
3. 将反应器密封并连接氢气气源。
调节氢气气源的压力,使其与反应器内部的压力保持恒定,一般为1-3 atm。
4. 启动加热器或冷却器,控制反应温度在适当的范围内。
温度的选择应根据具体的硝基化合物和催化剂而定,一般为50-100°C之间。
5. 反应进行一段时间后,可以根据反应物的消耗情况和产物的生成情况来判断反应的进行程度。
可通过薄层色谱、气相色谱或质谱等方法对反应物和产物进行分析。
6. 反应结束后,关闭氢气气源,并用适当的酸性溶液处理残留的催化剂,以避免环境污染和危险。
7. 将反应溶液进行适当的处理,如浓缩、萃取、分馏等,以获取目标产物。
8. 对产物进行适当的分析和鉴定,如红外光谱、质谱、核磁共振等方法。
五、实验安全注意事项和处理方法:1. 氢气是易燃易爆气体,操作时应注意防止氢气泄漏和积聚。
遇到火源时,应立即采取相应的应急措施,如关闭气源、切断电源,并用湿毛巾或灭火器覆盖火源进行处理。
还原—催化加氢反应类型(有机合成课件)

精精细细有有机机合合成技成术技术
烷基还化原反反应应
醛或酮在酸性催化剂存在下,能与一分子醇发生加 成,生成半缩醛(酮)。半缩醛(酮)很不稳定,一般 很难分离出来,它可与另一分子醇继续缩合,脱水形成 缩醛(acetal)或酮。
精精细细有有机机合合成技成术技术
烷基还化原反反应应
醛加氢时生成的醇会与醛缩合成半缩醛及醛缩醇。
此反应的选择性只能达到70%,有大量的副产物饱和醇生成。
精精细细有有机机合合成技成术技术
烷基还化原反反应应
第二节 催化加氢
如果要得到不饱和醇,应选用金属氧化物催化剂,但
是反应时有可能发生氢转移生成饱和醛,因此必须采用较
为缓和的加氢条件。
不饱和双键与羰基同时加氢比较容易实现。可用金属 或金属氧化物催化剂,反应条件可以较为激烈,只要避免 氢解反应即可。
多烯烃的加氢也有类似过程。即每一个双键可吸收一分子氢,直 至饱和。如果选择合适的催化剂和反应条件,就可以对多烯烃进行部 分加氢,保留一部分双键。
精精细细有有机机合合成技成术技术
烷基还化原反反应应
环烯烃与直链烯烃的加氢反应采用相同的催化剂,双 键上有取代基时可减慢加氢反应速度。另外,环烯烃的加 氢有发生开环副反应的可能,因此要得到环状产物则需要 控制反应条件。通常五元环和六元环较稳定。
因此,苯加氢很难形成分步加氢的中间产物,即苯加氢通常只能得 到环己烷。
苯的同系物加氢速度比苯慢,说明含有取代基会对加氢反应产生活 性降低的影响。
精精细细有有机机合合成技成术技术
烷基还化原反反应应
稠环芳烃在加氢时会分步发生反应。如萘加氢时会有多种中间产物。
芳烃加氢时,也有可能发生氢解,产生侧键或芳环断裂。 工业生产中最常用的芳烃加氢是环己烷的生产。生产环己烷的主要工 艺是苯的催化加氢。
对硝基苯甲醛加氢活化能

对硝基苯甲醛加氢活化能
对硝基苯甲醛加氢活化能的具体数值在公开资料中没有直接给出。
活化能是化学反应中的一个重要参数,它表示反应物转变为产物过程中所需克服的能量障碍。
对于硝基苯甲醛的加氢反应,活化能的大小会受到催化剂种类、反应条件等因素的影响。
目前,研究主要集中在开发高效的催化剂以促进硝基芳烃的选择性加氢,包括贵金属催化剂、非贵金属催化剂和无金属炭催化剂等。
在硝基苯甲醛的加氢反应中,催化剂的选择尤为关键。
例如,Cu3Pt/C催化剂被研究发现具有优异的电子结构,能够有效促进硝基苯分子的吸附和活化。
此外,对于含有其他可还原性基团的硝基化合物,如硝基苯甲醛,选择合适的催化剂以实现只还原硝基而不还原其他基团是一个研究挑战。
需要注意的是,由于具体的活化能数值通常需要通过实验测定,如果需要精确的数据,建议查阅专业的化学文献或进行相应的实验测定。
同时,研究者们也在探索如何通过催化剂设计和反应条件的优化来实现这类化合物的高效和选择性加氢。
硝基加氢催化剂

硝基加氢催化剂
硝基加氢催化剂是一种专门用于硝基加氢反应的催化剂。
这种催化剂的主要特点是活性高,能够保证高选择性,对中间产物羟胺加氢活性更高,更好地抑制副反应。
同时,生成的偶氮副产也会被高活性催化剂催化加氢成氨基。
具体来说,硝基加氢催化剂主要有以下几种类型:
1. 雷尼型催化剂:例如雷尼镍催化剂,它在硝基加氢反应中表现出高活性,尤其在含氯(含卤)硝基物的催化加氢过程中,能够有效抑制脱氯,提高催化剂的选择性。
2. 负载镍催化剂:如粉末负载镍催化剂和固定床负载镍催化剂,主要应用于C5树脂加氢、C9树脂加氢、DCPD树脂加氢、松香及其树脂、PAO聚α烯烃、油品加氢等领域。
3. 贵金属催化剂:如铂、钯等贵金属负载在活性炭或氧化铝上的催化剂,它们主要用于加氢、脱氯、深度脱硫、燃料电池脱硫等领域。
此外,还有一些其他类型的催化剂,如铜/硅系催化剂、钴系催化剂等,它们也在硝基加氢反应中发挥着重要的作用。
这些催化剂的选择和应用,需要根据具体的反应条件、原料特性和产品要求等因素进行综合考虑。
在实际应用中,还需要注意催化剂的活性、选择性、稳定性以及寿命等性能的评价和优化。
硝基加氢还原

硝基加氢还原化学反应中,硝基加氢还原是一种非常常见的还原反应。
所谓硝基,指的是含有硝基官能团 (-NO2) 的有机化合物,而所谓的氢还原则是指加氢反应。
硝基官能团是一种可以在有机化合物中发现的高度活跃、富含氧原子的结合物。
在许多情况下,硝基官能团会与其余的分子相互作用,形成一些相当稳定的共价键。
然而,硝基官能团也可以氢还原,这种反应减少了其与其他分子间的成键,从而导致生成新的化合物。
硝基加氢还原反应,正是简单地为硝基官能团加上氢原子的过程。
这种反应的实施方法得到多种实验室和工业上的应用。
在本文中,我们将详细介绍硝基加氢还原反应的工作原理、过程、应用和反应机制等内容。
硝基的加氢反应是将硝基化合物通过加氢还原,使硝基 (-NO2) 转化为胺基 (-NH2)的反应。
当硝基官能团和氢离子 (或者简称 H+) 反应时,硝基中的 NO2 团子会遭到还原,其中一个氧原子被氢离子置换掉,从而变成了氨基 (-NH2)。
二、硝基加氢还原反应的具体过程1. 游离氢离子(H+)将硝基官能团解离2. 解离出的氮上的两个氧原子有一个原子被游离H+取代3. 氮与H+结合形成NH2基硝基官能团的加氢还原所需的氢离子通常来自于酸性物质,如氢氯酸、硫酸、甲酸等。
此外,反应中也涉及到还原剂,在不同的反应中,还原剂可以是还原金属、氢气或类似的物质。
不过在实际操作中,未被还原的未反应的硝基化合物计量非常重要,因为反应的强度和效果都与其相关。
硝基加氢还原反应在工业生产中得到了广泛应用。
在某些情况下,它是一种相对易于控制和低成本的化学反应,可以产生无毒、可溶性和相对稳定的化合物。
硝基加氢还原反应在生产工艺中最常见的应用之一是制取一些化学品。
硝基官能团可以被还原成胺基,从而制备出处理流体和工艺技术所需的各种化合物。
硝基加氢还原反应也可以用于制备新药和其他特殊化学品。
硝基官能团与还原剂反应,生成自由基R···H这个自由基加入硝基官能团自由基负电荷的电子与硝基原子中的一个氧原子组成了一个负离子中间体还原剂还原反应,去除了负离子中间体中的氧原子五、总结硝基加氢还原反应是一种常见的还原反应,可通过将含有硝基官能团的有机化合物加上氢原子来实现。
- 1、下载文档前请自行甄别文档内容的完整性,平台不提供额外的编辑、内容补充、找答案等附加服务。
- 2、"仅部分预览"的文档,不可在线预览部分如存在完整性等问题,可反馈申请退款(可完整预览的文档不适用该条件!)。
- 3、如文档侵犯您的权益,请联系客服反馈,我们会尽快为您处理(人工客服工作时间:9:00-18:30)。
科研开发2018·09166Chenmical Intermediate当代化工研究硝基芳烃催化加氢过程中的催化剂性能和工艺探究*邱志刚1,2(1.江苏恒祥化学股份有限公司 江苏 226500 2.江苏康恒化工有限公司 江苏 226500)摘要:硝基芳香烃化合物经过催化之后得到的产品被广泛应用于化工、医药等领域,并以催化加氢还原反应为主。
本文根据以往工作经验,对负载型加氢催化剂性能研究进行总结,并从MoS 2/C催化加氢反应过程分析、Mo x N/C催化加氢反应分析、Mo-Co/C催化加氢反应分析、镍系催化剂加氢反应分析四方面,论述了硝基芳烃催化加氢过程中的工艺研究。
关键词:硝基芳烃;催化加氢;催化剂性能;工艺研究中图分类号:O 文献标识码:AStudy on Catalyst Performance and Process in Catalytic HydrogenationProcess of NitroaromaticsQiu Zhigang 1, 2(1.Jiangsu Hengxiang Chemical CO., LTD., Jiangsu, 226500 2.Jiangsu Kangheng Chemical CO., LTD., Jiangsu, 226500)Abstract :The products obtained from the catalysis of nitroaromatics are widely used in the fields of chemical industry and medicine, and mainlyfocus on catalytic hydrogenation reduction reactions. Based on previous work experience, this paper summarizes the research on the performance of supported hydrogenation catalysts, and discusses the technological research in the process of catalytic hydrogenation of nitroaromatics from four aspects: analysis of MoS 2/C catalytic hydrogenation reaction process, analysis of Mo x N/C catalytic hydrogenation reaction, analysis of Mo-Co/C catalytic hydrogenation reaction and analysis of nickel-based catalyst hydrogenation reaction.Key words :nitroaromatics ;catalytic hydrogenation ;catalyst performance ;process research前言硝基芳烃催化加氢过程中所得到的产品在化工、医药等领域中得到了广泛应用,其中还有一部分为重要的还原反应,如芳硝基化合物还原成芳胺的过程,在精细化生产中的作用十分明显。
另外,硝基芳烃催化加氢还原反应之中的关键技术便是对高活性、高选择的催化剂进行制备,在酸性条件下,整个催化剂活性与常用的Pt/Ca相接近,从而进一步提升了反应速率,抑制副产物生成。
1.负载型加氢催化剂的性能研究(1)MoS 2/C 制备性能与表征现阶段,催化剂的制备方式已经日渐成熟,根据相关文献资料记载,人们可以选择浓氨水、蒸馏水以及干燥时间等为考察因素,以硝基苯的转化率为基础,将催化剂的活性考察指标显示出来。
之后采用具体的实验方案对现有条件下的MoS 2/C进行制备,从而对最佳工艺条件进行确定。
硝基苯转化率的计算公式如下:X=转化的硝基苯摩尔数/硝基苯的起始摩尔数通过样本以及催化加氢反应过程,硝基苯的转化率与各种样本的比较过低,并没有将XRD的表征突显出来。
另外,在制备工艺参数的比较过程中,可以将催化活性降到最低,这主要是由于不同反应时间不同,而且很多反应类型也不够全面。
在加氢活化时间中,催化剂只能呈现出部分的还原状态。
而在实验制备上,主要应用的催化剂为二硫化锌,该种催化剂属于非晶体结构,人们可以根据具体的硝基苯转化率,将其催化剂活性展示出来。
由于催化剂的活性不同,最终对硝基苯的转化率带来影响。
(2)Mo x N /C 制备性能与表征在吸取一定量的钼氨酸之后,可以将其放入到500℃的马弗炉之中进行焙烧,焙烧时间为4.5h,在经过长时间高温燃烧之后钼氨酸晶体将会变成浅绿色的MoO 3。
在量取一定量的氨水之后,可以分为两次加入到MoO 3之中,从而形成剧烈反应,该反应属于一个放热且生成气体的过程,第一次的静置时间将会达到5h左右。
第二次加入的氨水所产生的反应不会很强烈,静置时间可以达到0.5h。
之后,将溶液与载体相互混合之后,保持质量比为1:1,并且在100℃的烘箱下干燥1.5h,从而得到一些新的黑色粉末物质。
(3)钼钴二金属催化剂制备性能与表征本文针对该种催化剂的制备和应用进行了深入性研究,首先,为了确保钼酸铵溶液的混合均匀,研究人员需要对其进行焙烧,之后在浸入到硝酸铵溶液之中进行二次焙烧,该样品被称为样品一。
样品二则是利用硝酸钴/氨溶液,对样品进行干燥和焙烧,从而获得最佳的催化效果。
经过数据统计分析,催化剂的活性一般会强于吸附性,如果采用液相硫化方式对MoS 2/C进行制备,所得到的反应物吸附性将会更大。
据XRD分析表明,MoS 2/C属于一种非晶体状态,而在Mo x N/C和二金属催化剂研究上,其状态均属于晶体状态。
2.硝基芳烃催化加氢过程中的工艺研究(1)MoS 2/C 催化加氢反应过程分析科研开发2018·09167Chenmical Intermediate当代化工研究硝基苯催化加氢反应,主要以MoS 2/C催化剂的添加为主,此时加氢反应的起始温度在18.8℃左右,为了方便研究,人们还会将初始压力调整到1.5Mpa。
由于温度、时间等压力变化较大,反应时间也会进一步增加,最长会达到1400min,系统转速为100rpm。
待所有反应结束之后,温度便会进一步降低,最终的终止温度为17.2℃。
想要得到纯净的催化剂,工作人员需要做好产物的过滤工作,最终得到催化剂固体。
另外,在滤液静置分层上,硝基苯也会在分层液之中,并以黄色油状物为主,处于混合溶液的最上层,溶液下层主要以黑色油状液体为主。
站在液体体积对比角度来说,两种溶液的体积比为2:3,称量之后所得到的硝基苯比例占总数的42.7%。
由于催化加氢的作用,当反应温度达到设定温度之后,溶液的反应程度开始变得愈发剧烈。
在此过程中所产生的主要产物包括苯胺、甲基苯胺等。
(2)Mo x N /C 催化加氢反应分析硝基苯的催化加氢反应主要以Mo x N/C催化剂的使用为主,初始温度在23.4摄氏度左右,为了确保反应更加明显,初始压力值应该保持在1.5Mpa。
根据以往工作经验,该项反应的反应时间为600min,尤其是在加热速率之下,整个装置的转速也会进一步提升,速率为100V时,转速也会达到100rpm。
在经过产物过滤之后,便会顺利得到催化剂固体。
另外,本次Mo x N/C催化加氢反应过程中的硝基苯转化率为14.26%, 该数值与充分反应下的数值并不相符,而且要低出很多,主要的反应产物为甲基异喹啉以及苯胺等。
上述产物主要由苯胺深度加氢而获得的,并进一步降低了催化加氢反应的活性。
(3)Mo -Co /C 催化加氢反应分析在硝基苯催化加氢反应过程中,主要以Mo-Co/C作为主要的催化剂类型,反应的初始温度为21.4℃,初始压力值为1.5Mpa。
因此,随着反应温度和压力值的变化,反应时间也会发生改变,当时间增加量为400min时,整个加热速率将会变为100V。
待反应全部结束之后,终止温度为18℃,压力保持在1.2Mpa左右。
另外,研究人员可根据不同状态下的需求,对不同的产物过滤进行有限考虑,最终得到新的催化剂固体。
根据硝基苯顶峰面积和温度等因素之间的关系可知,硝基苯在整个催化反应中的转化率最高,可以达到29.48%,主要生成的产物为苯胺,副产物为喹啉。
如果研究人员能够在此反应中对加氢反应进行控制,催化剂的活性也会得到进一步发挥。
(4)镍系催化剂加氢反应分析首先,在硝基苯催化加氢反应之中,主要以NiO/C的催化剂类型为主,而且加氢反应的起始温度能够达到20℃,初始压力依然保持在0.5Mpa。
等到反应结束之后,反应器内部温度也会开始降低,终止温度为18℃,同样是利用过滤的方式来获得催化剂固体。
在该反应过程中所得到的硝基苯转化率为16.97%,主要产物为苯胺,在副产物喹啉中的含量比较少,而且在加氢效果控制上,也能进一步提升催化剂的活性。
其次,在Ni-Mo/C催化加氢反应过程中,反应的起始温度为20.2℃,初始反应压力值为1.5Mpa。
待反应结束之后,温度会大幅度降低,终止温度为18℃,通过过滤之后得到催化剂固体。
纯物质在发挥过程中的发挥度通常以蒸气压大小来衡量,只有保证蒸气压较高,才能称之为易挥发物质,如果蒸汽压力较低,被称之为难挥发物质。
在混合液挥发度确定上,应该以分压和蒸汽平衡液中的摩尔分数为主。
例如,在AB两种混合液之中,用P(A)和P(B)分别代表两物质的蒸汽分压,利用x代表摩尔分数,经过公式计算之后,以及各种已知的反应条件,便可以得到具体的催化剂反应速率。
3.催化加氢工艺的影响因素(1)表面活性剂用量的影响由于硝基苯催化加氢反应存在水的生成性,人们可以将具体的硝基苯催化加氢反应过程进行有效梳理,即“气-液-液-固”。
因此,在物质强化过程中,需要确保四相反应物质充分接触。
该项加氢过程中的反应速度应该以初始原料为载体,将其与硝基苯的溶解性关系展示出来,只有这样,硝基苯才能真正实现加氢。
催化剂反应条件主要以高温高压要求为主,但由于材料的限制,反应溶剂只能以中性化合物为主。
为了避免反应中的硝基苯出现催化剂,可以在反应表面加入适量的活性物质,将水化、汽化等状态转移出去,在提升有机物溶解度的同时,促使各种相间实现充分接触。
在实际实验情况考虑上,原料价格情况显得十分重要,如果出现过量的分散和转移,便会对反应效果产生影响。
(2)反应温度及压力的影响反应温度对整个催化剂性能的影响十分严重,尤其是在温度较高时,催化剂基层之中便会出现热点,促使反应过程很难被控制。
因此,加氢温度的选择显得十分重要。