风机轴承故障分析及校核
风机常见故障及分析

一,风机的电机或传动件轴承振动、 温度高:
2,电机或轴承箱轴承温度高:风机轴承温度异 常升高的原因有三类:润滑不良、冷却不够、 轴承异常。离心式风机轴承置于风机外,若是 由于轴承疲劳磨损出现脱皮、麻坑、间隙增大 引起的温 度升高,一般可以通过听轴承声音 和测量振动等方法来判断,如是润滑不良、冷 却不够的原因则是较容易判断的。而轴流风机 的轴承集中于轴承箱内,置于进气室的 下方, 当发生轴承温度高时,由于风机在运行,很难 判断是轴承有问题还是润滑、冷却的问题。
一,风机的电机或传动件轴承振动、 温度高:
1,风机轴承振动是运行中常见的故障,风机 的振动会引起轴承和叶片损坏、螺栓松动、 机壳和风道损坏等故障,主要表现为风机 在运行中振动突然上升。这是因为当气体 进入叶轮时,与旋转的叶片工作面存在一 定的角度,根据流体力学原理,气体在叶 片的非工作面一定有旋涡产生,于是气体 中的灰粒由于旋涡作用会慢慢地沉积在非 工作面上。
风机常见故障及分析
风机的常见故障及分析
如何迅速判断风机运行中故障产生的 原因,采取得力措施解决是用户连续安全 运行的保障。 风机是一种将原动机的机械 能转换为输送气体、给予气体能量的机械。 虽然风机的故障类型繁多,原因也很复杂, 但根据调查实际运行中风机故障较多的是: 轴承振动,轴承温度高,保护装置误动, 电机电源缺相等,如能针对不同的现象分 析原因采取恰当的处理办法,往往能起到 事半功倍的效果。
一,风机的电机或传动件轴承振动、 温度高:
3,轴承箱或电机轴承加油是否恰当。应当按 照定期工作的要求给轴承箱加油。轴承加 油后有时也会出现温度高的情况,主要是 加油过多。这时现象为温度持续不断上升, 到达某点后(一般在比正常运行温度高 10℃~15℃左右)就会维持不变,然后会 逐渐下降。
浅谈风力发电机主轴轴承失效分析及解决办法
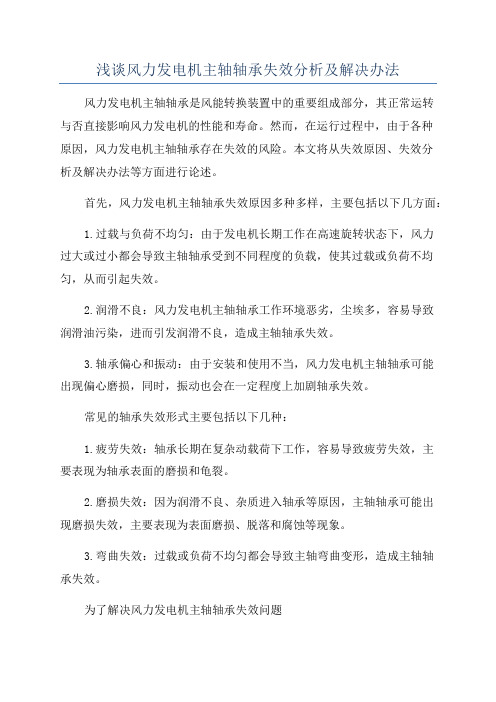
浅谈风力发电机主轴轴承失效分析及解决办法风力发电机主轴轴承是风能转换装置中的重要组成部分,其正常运转与否直接影响风力发电机的性能和寿命。
然而,在运行过程中,由于各种原因,风力发电机主轴轴承存在失效的风险。
本文将从失效原因、失效分析及解决办法等方面进行论述。
首先,风力发电机主轴轴承失效原因多种多样,主要包括以下几方面:1.过载与负荷不均匀:由于发电机长期工作在高速旋转状态下,风力过大或过小都会导致主轴轴承受到不同程度的负载,使其过载或负荷不均匀,从而引起失效。
2.润滑不良:风力发电机主轴轴承工作环境恶劣,尘埃多,容易导致润滑油污染,进而引发润滑不良,造成主轴轴承失效。
3.轴承偏心和振动:由于安装和使用不当,风力发电机主轴轴承可能出现偏心磨损,同时,振动也会在一定程度上加剧轴承失效。
常见的轴承失效形式主要包括以下几种:1.疲劳失效:轴承长期在复杂动载荷下工作,容易导致疲劳失效,主要表现为轴承表面的磨损和龟裂。
2.磨损失效:因为润滑不良、杂质进入轴承等原因,主轴轴承可能出现磨损失效,主要表现为表面磨损、脱落和腐蚀等现象。
3.弯曲失效:过载或负荷不均匀都会导致主轴弯曲变形,造成主轴轴承失效。
为了解决风力发电机主轴轴承失效问题1.加强检查和维护:定期对风力发电机主轴轴承进行检查,确保其润滑状态良好,及时更换磨损严重的轴承。
2.提高轴承负荷承载能力:采用高强度材料制造轴承,增加轴承的负荷承载能力以及寿命。
3.减小振动幅度:通过优化设计和加强安装质量,降低风力发电机的振动幅度,减少对主轴轴承的影响。
4.加强润滑管理:严格控制风力发电机主轴轴承的润滑油品质和污染控制,确保轴承良好润滑,减少摩擦磨损。
总之,风力发电机主轴轴承的失效对风力发电机的性能和寿命具有重要影响。
通过加强检查和维护、提高轴承负荷承载能力、减小振动幅度、加强润滑管理等措施,可以有效预防和解决风力发电机主轴轴承失效问题,提高风力发电机的可靠性和经济性。
风力发电机主轴轴承失效分析

2019年4月下风力发电机主轴轴承失效分析何玉强(新d 绿色能源股份有限公司,河北 石家庄 050000)摘 要:文章结合风力发电场实际运行过程中的各种轴承磨损和故障现象,对双馈异步低温风力发电机组进行现场风机运行数据的统计分析,总结了影响轴承正常运行的因素,希望在技术和经验方面提供参考。
关键词:风力发电机;主轴轴承;失效中图分类号:TM315 文献标志码:A 文章编号:1672-3872(2019)08-0120-02——————————————作者简介: 何玉强(1984—),男,河北石家庄人,本科,工程师,研究方向:机械设计制造及其自动化。
我国风电行业比较严重和普遍存在的问题是大型双馈型风力发电机主轴轴承的磨损,已成为风力发电机组研发和重点排除的故障。
根据目前的情况,导致主轴轴承磨损的主要原因有以下几种:风机组装过程不规范,没有检查润滑油,轴承本身的质量。
文章在风电场实际工作的基础上,详细分析双馈风力发电机前后的轴承磨损情况[1]。
1 主轴轴承在正常情况下失效的主要原因1)兆瓦级风力发电机的主轴轴承用的是双列调心滚子轴承,它必须承受轴向和径向的载荷,所以出现故障次数也比较多。
这是因为具有较大的间隙的双列调心滚子轴承,上风向侧的轴承承受较小的载荷,而下风向轴承要承受很多径向载荷和轴向力,这导致滚子过度滑动,如果润滑不良会导致材料腐蚀并剥落,使座圈,滚子和保持架受力不均出现变形的情况,导致座圈和轴承座之间出现不协调,引起常见故障,如位移和卡住[2]。
2)在设计新的传动系统时,很少使用调心轴承作为主轴轴承。
一般建议使用圆锥滚子轴承,其有很强的径向和轴向承载力,通过预紧可以均匀地加载滚轮,滚轮不易滑动摩擦。
然而,在装置过程,由于安装精度和技术要求,轴承间隙如果调整不当会导致半干滚动摩擦,就会导致轴承失效[3]。
3)用热装法进行轴承装配。
由于加热装置的尺寸限制,只能进行局部加热,这样就会导致加热不均匀,使轴承变形。
风力发电机组轴承的典型故障模式及原因分析
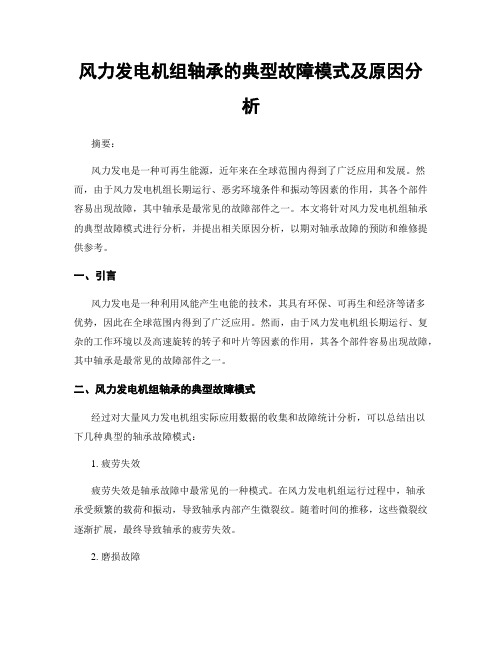
风力发电机组轴承的典型故障模式及原因分析摘要:风力发电是一种可再生能源,近年来在全球范围内得到了广泛应用和发展。
然而,由于风力发电机组长期运行、恶劣环境条件和振动等因素的作用,其各个部件容易出现故障,其中轴承是最常见的故障部件之一。
本文将针对风力发电机组轴承的典型故障模式进行分析,并提出相关原因分析,以期对轴承故障的预防和维修提供参考。
一、引言风力发电是一种利用风能产生电能的技术,其具有环保、可再生和经济等诸多优势,因此在全球范围内得到了广泛应用。
然而,由于风力发电机组长期运行、复杂的工作环境以及高速旋转的转子和叶片等因素的作用,其各个部件容易出现故障,其中轴承是最常见的故障部件之一。
二、风力发电机组轴承的典型故障模式经过对大量风力发电机组实际应用数据的收集和故障统计分析,可以总结出以下几种典型的轴承故障模式:1. 疲劳失效疲劳失效是轴承故障中最常见的一种模式。
在风力发电机组运行过程中,轴承承受频繁的载荷和振动,导致轴承内部产生微裂纹。
随着时间的推移,这些微裂纹逐渐扩展,最终导致轴承的疲劳失效。
2. 磨损故障由于风力发电机组长期运行,轴承表面会因为摩擦而产生磨损。
如果机组的润滑系统不够完善,或者存在润滑油质量不合格等问题,轴承表面的磨损会加剧,最终导致轴承的失效。
3. 弹性变形故障风力发电机组运行过程中,轴承会承受大量的载荷和振动,从而引起轴承的弹性变形。
当弹性变形超出轴承的可承受范围时,轴承会出现形状变形和功能损失,进而导致故障。
4. 渣滓沉积故障风力发电机组运行环境通常存在大量的沙尘和颗粒物,这些物质会随风进入轴承内部,形成渣滓沉积。
过多的渣滓会导致轴承不正常运转,甚至造成卡死等严重故障。
三、风力发电机组轴承故障原因分析针对以上几种典型的轴承故障模式,可以进行如下原因分析:1. 运行时间和振动风力发电机组长时间运行会导致轴承频繁承受载荷和振动,轴承内部可能产生微裂纹,进而引起疲劳失效。
因此,合理控制机组的运行时间和振动水平,可以有效预防轴承故障。
风机主轴轴承故障原因分析和追溯

因轴承故障导致更换轴承,拆卸轴承后需对 主轴进行修复方能再次投入使用。若修复过程处 理不当,甚至可能导致主轴无法再次使用,造成更 大的损失。 1. 3 吊装费用
故障轴承拆下后需吊装至地面,需租用大型 吊车方可完成,将会产生高额费用。
1. 4 主轴轴承及主轴运输费用
因轴承故障导致更换的传动链,需从风场现 场返回机组装配地进行修复,长途运输将产生高 额的运输费用。
No.1 February 2018
《中国重型装备》 CHINA HEAVY EQU11:'MENT
风机主轴轴承故障原因分析和追溯
刘宝金 (东方电气风电有限公司质量管理部,四川618000)
摘要:分析了在风场运行过程中主轴轴承发生故障的原因。通过对风力发电机组主轴轴承的结构特点分 析,得出导致轴承故障的主要因素,,通过实验和分析对各因素进行逐一对比,确认热处理不当是导致该轴承故 障的根本原因"
关键词:主轴轴承;热处理;滚动体;质量损失 中图分类号:TM315 文献标志码:B
Failure Analysis and Tracing of Main Shaft Bearing of .Wind Turbine
Liu Baojin
Abstract:The cause of the failure of spindle bearing during the operation at the wind field has been analyzed in this paper. The main factors that lead to the failure of th~bearing are obtained through the analysis of the structure ~haracteristJcof the spindle bearing of the wind turbine. Each factor is comparedby experimentand anaysis, it is con firmed that the improper heat treatment is the root cause of failure of the bearing.
通风电机轴承维修方案

通风电机轴承维修方案通风电机轴承是通风设备中重要的部件,其正常运转对于设备的性能和寿命具有重要影响。
然而,由于长时间运行或使用条件不佳,轴承往往会出现故障,导致电机无法正常运转。
为了解决轴承故障问题,下面给出一个轴承维修方案。
第一步:故障检测在维修过程中,首先需要对轴承进行故障检测。
可以通过以下方法来判断轴承故障:1. 观察是否有异常噪音:轴承故障时,轴承会发出异常噪音,这是比较直观的判断方法之一。
2. 观察轴承温度:正常情况下,轴承运转时的温度应该是稳定的,如果温度异常升高,则说明有可能存在轴承故障。
3. 观察轴承颜色:轴承故障时,轴承表面可能出现过热的迹象,颜色会变成深红或者黑色。
第二步:轴承更换确定轴承故障后,进行轴承更换工作。
具体步骤如下:1. 停机:首先需要将通风电机停机,并切断电源。
2. 拆卸风扇叶片:将风扇叶片拆卸下来,以便更轻松地进行轴承更换。
3. 拆卸轴承保护盖:使用扳手或螺丝刀拆卸轴承保护盖,注意不要损坏保护盖。
4. 拆卸轴承:将轴承从轴上取下,可以使用专业工具或者敲打轴承外圈边缘进行拆卸。
5. 清洁轴承座:清洁轴承座,并检查座孔是否有磨损或裂纹,如果有,则需要修复或更换座孔。
6. 安装新轴承:取出新轴承,并涂抹适量的润滑油来减少摩擦,然后将轴承安装到轴承座中。
7. 安装保护盖和风扇叶片:将保护盖和风扇叶片安装回原位,并确保紧固牢固。
第三步:测试运行完成轴承更换后,需要进行测试运行,以确保通风电机能够正常运转。
运行时需要注意以下事项:1. 检查轴承温度:运行一段时间后,观察轴承温度是否正常,确保轴承不再过热。
2. 检查噪音:通过听觉来判断电机是否有异常噪音,如果有异常噪音则需要进一步检查。
最后,需要定期进行轴承维护保养工作,包括定期润滑轴承、清洁轴承外壳等,并及时更换老化或故障的轴承,以延长通风电机的使用寿命。
风机轴承故障原因及排除方法

风机轴承故障原因及排除方法风机轴承的故障原因及排除方法爽风有着13年的生产风机的经验,对风机有着自己独到的见解。
对于风机来说,轴承损坏是常见的故障,那么,小编今天就讲一下排除风机轴承的方法。
1、故障原因分析:轮叶两侧用紧定套与轴承座轴承固定配合。
重新试车就发生自由端轴承高温,振动值偏高的故障,拆开轴承匝上盖,手动慢速回转风机,发现处于转轴某一特定位置的轴承滚子,在非负荷区亦有滚动情况.如此可确定轴承运转间隙变动偏高且安装间隙可能不足。
经测量得知,轴承内部间隙仅为0.04mm,转铀偏心达0.08mm;由于左右轴承跨距大,要避免转轴挠曲或轴承安装角度的误差较难,因此,大型风机采用可自动对心调整的球面滚子轴承。
但当轴承内部间隙不足时.轴承内部滚动件因受运动空间的限制,其自动对心的机能受影响,振动值反而会升高。
轴承内部间隙随配合紧度之增大而减小,无法形成润滑曲膜,当轴承运转间隙因温升而降为零时,若轴承运行产生的热量仍大于逸散的热量时,轴承温度即会快速爬升,这时,如不即时停机,轴承终将烧损,轴承内环与轴之配合过紧是本例中轴承运转异常高温的原因。
2、排除方法:处理时,退下紧定套,重新调整轴与内环的配合紧度,更换轴承之后的间隙取0.10mm。
重新安装完毕重新启动风机,轴承振动值及运转温度均恢复正常。
轴承内部间隙太小或机件设计制造精度不佳,均是分机轴承运转温度偏高的主因,为方便风机设备的安装;拆修和维护.一般在设计上多采用紧定套轴承锥孔内环配合之轴承座轴承,然而也易因安装程序上的疏忽而发生问题.尤其是适当间隙的凋整。
轴承内部间隙太小.运转温度急速升高:轴承内环锥孔与紧定套配合太松,轴承易因配合面发生松动而于短期内故障烧损。
浅谈风力发电机主轴轴承失效分析及解决办法

% %
O$ %
% O$
O( %
% O(
':E ':P
=P
=E )O) *$ ,XW))O3 *) ,XW)
轴承的润滑理论中以 !XpWX- 提出的最小油膜厚度公式
应用较为普遍其表述的油膜最小厚度计算公式为
Q !)%0?JA%%1 *%%?3 N G(P%%$(
对于特定轴承而言轴承的尺寸和材料都是固定的公式
现场主要故障形式分析如下
M轴承转动困难 发 热 U 轴 承 产 生 振 动 运 转 发 出 异 响
,内座圈剥落开裂 b 外 座 圈 剥 落 开 裂 [ 轴 承 滚 道 和 滚 动
体产生压痕
'通过对现场考 察 及 对 多 台 失 效 机 组 主 轴 轴 承 进 行 拆 解
通过滚子速度可以计算得到 J油膜厚度与其表面粗糙度
的均方根值的比值决定了轴承的润滑状态即令
4!
Q-
槡N)-$ )N)-)
当 4 R$ 时润滑状态为边界润滑 $ 4 R( 时为混合润
滑 4( ( 时为流体润滑一般情况下 4越大润滑状态越好
轴承的寿命模型可根据损伤理论建立 通过轴承寿命计
关键词风电机组轴承监测与维护
44风力发电机组中主轴连接轮毂和齿轮箱是低速重载轴 承可靠性方面要求较高也极易出现故障 为了解决故障多 发现象需要系统的对现场轴承运转状况及失效形式进行分析 和研究
$轴承失效理论体系 首先建立轴 承 失 效 的 寿 命 分 析 体 系 包 括 轴 承 的 载 荷 分 布润滑油膜建立条件及轴承的润滑状态轴承的寿命计算方 法及影响因素 分析轴承载荷需建立如下传动链几何模型
统通过定期的油脂加注改善轴承内部运转情况
参考文献
风电轴承的失效模式与故障分析
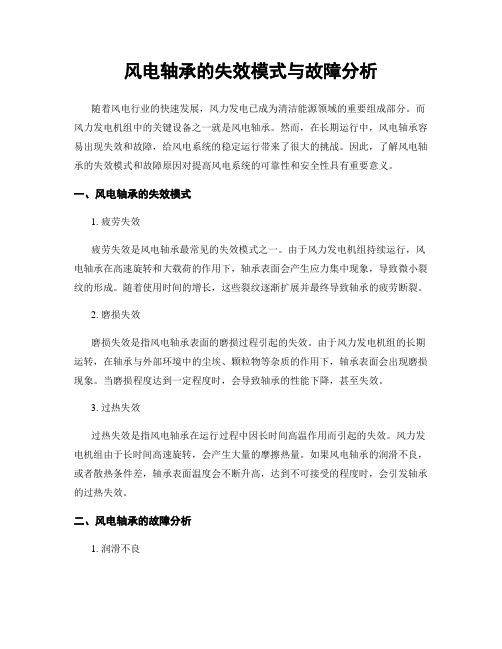
风电轴承的失效模式与故障分析随着风电行业的快速发展,风力发电已成为清洁能源领域的重要组成部分。
而风力发电机组中的关键设备之一就是风电轴承。
然而,在长期运行中,风电轴承容易出现失效和故障,给风电系统的稳定运行带来了很大的挑战。
因此,了解风电轴承的失效模式和故障原因对提高风电系统的可靠性和安全性具有重要意义。
一、风电轴承的失效模式1. 疲劳失效疲劳失效是风电轴承最常见的失效模式之一。
由于风力发电机组持续运行,风电轴承在高速旋转和大载荷的作用下,轴承表面会产生应力集中现象,导致微小裂纹的形成。
随着使用时间的增长,这些裂纹逐渐扩展并最终导致轴承的疲劳断裂。
2. 磨损失效磨损失效是指风电轴承表面的磨损过程引起的失效。
由于风力发电机组的长期运转,在轴承与外部环境中的尘埃、颗粒物等杂质的作用下,轴承表面会出现磨损现象。
当磨损程度达到一定程度时,会导致轴承的性能下降,甚至失效。
3. 过热失效过热失效是指风电轴承在运行过程中因长时间高温作用而引起的失效。
风力发电机组由于长时间高速旋转,会产生大量的摩擦热量。
如果风电轴承的润滑不良,或者散热条件差,轴承表面温度会不断升高,达到不可接受的程度时,会引发轴承的过热失效。
二、风电轴承的故障分析1. 润滑不良润滑不良是导致风电轴承故障的主要原因之一。
风力发电机组长期运行,风电轴承需要保持充足的润滑油膜以减少轴承表面的磨损和摩擦。
如果润滑油不足、质量不佳、污染等原因导致润滑不良,会使轴承失去必要的润滑和冷却,加速了轴承的磨损和失效。
2. 尺寸配合不良风电轴承的尺寸配合不良也是导致轴承故障的常见原因之一。
风力发电机组的工作环境要求风电轴承能够承受大的径向和轴向载荷。
如果轴承的尺寸设计不合理,配合过紧或过松,都会导致轴承在运行过程中受到过大的应力,从而引发故障。
3. 外界环境条件风电轴承的故障还与外界环境条件密切相关。
当风力发电机组运行在恶劣的环境中,如高温、高湿度、腐蚀性气体等,轴承表面容易受到腐蚀和损坏,进而导致轴承失效。
风机常见故障及检修

风机常见故障及检修风机作为工业生产中常见的设备,其运行状态直接影响到生产效率和工作环境。
然而,由于长期使用和各种外部因素的影响,风机也会出现各种故障。
本文将介绍风机常见的故障及其检修方法,以帮助读者更好地了解和维护风机设备。
一、轴承故障。
风机轴承是风机运行中最容易出现故障的部件之一。
常见的轴承故障包括轴承损坏、轴承过热、轴承噪音等。
当出现轴承故障时,首先需要停机检查,查看轴承是否有损坏或过热现象。
如果发现轴承损坏,需要及时更换新的轴承,并在更换轴承前清洁轴承座和轴承安装位置,确保安装时干净整洁。
另外,定期给轴承加注适量的润滑脂,可以有效延长轴承的使用寿命。
二、叶轮故障。
叶轮是风机的关键部件之一,其状态直接影响到风机的风量和风压。
常见的叶轮故障包括叶片损坏、叶轮不平衡等。
当出现叶轮故障时,需要停机检查,查看叶轮是否有损坏或不平衡现象。
如果发现叶轮损坏,需要及时更换新的叶轮,并在更换叶轮前进行动平衡校正,确保叶轮在运行时平衡稳定。
三、电机故障。
风机电机是风机的动力来源,其状态直接影响到风机的运行效率和能耗。
常见的电机故障包括电机过热、电机绕组烧坏等。
当出现电机故障时,需要停机检查,查看电机是否有过热或烧坏现象。
如果发现电机过热,需要检查电机通风是否畅通,及时清理电机周围的杂物和灰尘,确保电机散热良好。
如果发现电机绕组烧坏,需要及时更换新的电机,并在更换电机前检查电机的供电线路和接线端子,确保电机供电正常。
四、风机噪音大。
风机在运行时会产生一定的噪音,但如果噪音过大,则会影响到工作环境和生产效率。
常见的风机噪音大的原因包括叶轮不平衡、轴承损坏、电机故障等。
当出现风机噪音大的情况时,需要停机检查,查找噪音的具体来源。
根据具体情况进行相应的维修和调整,如进行叶轮动平衡校正、更换损坏的轴承、维修或更换故障的电机等。
五、风机振动大。
风机在运行时会产生一定的振动,但如果振动过大,则会影响到风机的安全性和稳定性。
风机运行中常见故障原因分析及其处理
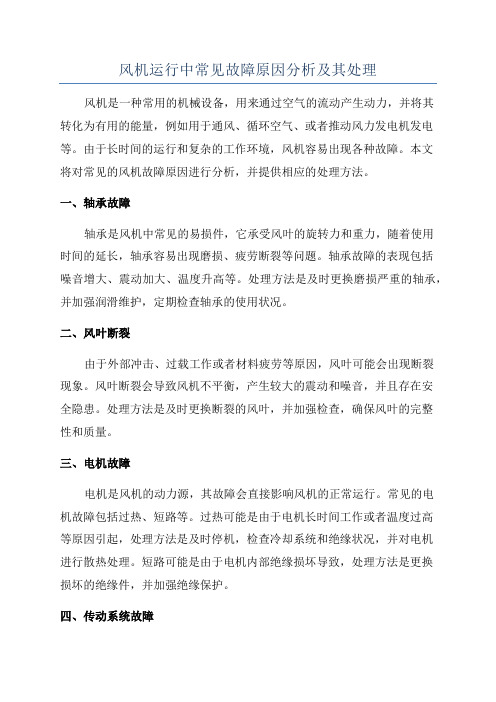
风机运行中常见故障原因分析及其处理风机是一种常用的机械设备,用来通过空气的流动产生动力,并将其转化为有用的能量,例如用于通风、循环空气、或者推动风力发电机发电等。
由于长时间的运行和复杂的工作环境,风机容易出现各种故障。
本文将对常见的风机故障原因进行分析,并提供相应的处理方法。
一、轴承故障轴承是风机中常见的易损件,它承受风叶的旋转力和重力,随着使用时间的延长,轴承容易出现磨损、疲劳断裂等问题。
轴承故障的表现包括噪音增大、震动加大、温度升高等。
处理方法是及时更换磨损严重的轴承,并加强润滑维护,定期检查轴承的使用状况。
二、风叶断裂由于外部冲击、过载工作或者材料疲劳等原因,风叶可能会出现断裂现象。
风叶断裂会导致风机不平衡,产生较大的震动和噪音,并且存在安全隐患。
处理方法是及时更换断裂的风叶,并加强检查,确保风叶的完整性和质量。
三、电机故障电机是风机的动力源,其故障会直接影响风机的正常运行。
常见的电机故障包括过热、短路等。
过热可能是由于电机长时间工作或者温度过高等原因引起,处理方法是及时停机,检查冷却系统和绝缘状况,并对电机进行散热处理。
短路可能是由于电机内部绝缘损坏导致,处理方法是更换损坏的绝缘件,并加强绝缘保护。
四、传动系统故障传动系统是风机实现旋转的重要组成部分,其故障会导致风机无法正常工作。
常见的传动系统故障包括皮带断裂、齿轮磨损等。
处理方法是及时更换磨损严重的皮带或齿轮,并加强润滑维护,定期检查传动系统的状况。
五、控制系统故障控制系统是风机实现自动化运行的关键部分,其故障会导致风机无法正常调节。
常见的控制系统故障包括电路故障、传感器故障等。
处理方法是检查控制系统的电路连接是否良好,更换损坏的传感器,并及时进行维护和调试。
六、其他故障除了以上几种常见的故障原因外,风机还可能出现其他故障,例如风机部件松动、电缆故障等。
处理方法是及时检查和维修,确保风机各部件的正常运行和连接。
总之,风机常见的故障原因涉及轴承、风叶、电机、传动系统、控制系统等多个方面。
风机的常见故障及分析
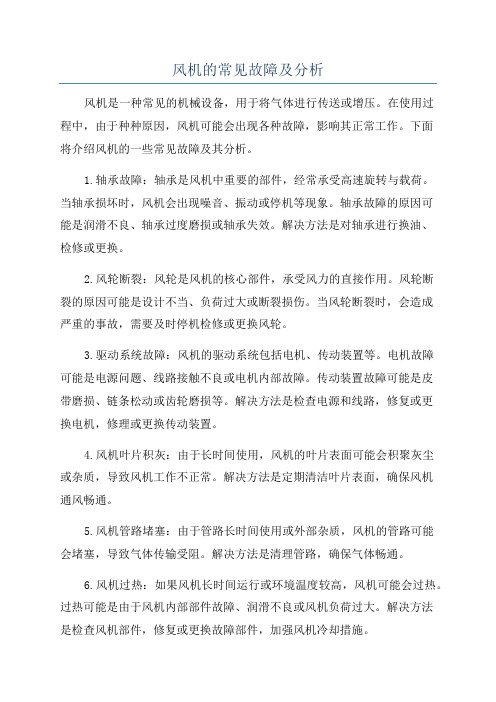
风机的常见故障及分析风机是一种常见的机械设备,用于将气体进行传送或增压。
在使用过程中,由于种种原因,风机可能会出现各种故障,影响其正常工作。
下面将介绍风机的一些常见故障及其分析。
1.轴承故障:轴承是风机中重要的部件,经常承受高速旋转与载荷。
当轴承损坏时,风机会出现噪音、振动或停机等现象。
轴承故障的原因可能是润滑不良、轴承过度磨损或轴承失效。
解决方法是对轴承进行换油、检修或更换。
2.风轮断裂:风轮是风机的核心部件,承受风力的直接作用。
风轮断裂的原因可能是设计不当、负荷过大或断裂损伤。
当风轮断裂时,会造成严重的事故,需要及时停机检修或更换风轮。
3.驱动系统故障:风机的驱动系统包括电机、传动装置等。
电机故障可能是电源问题、线路接触不良或电机内部故障。
传动装置故障可能是皮带磨损、链条松动或齿轮磨损等。
解决方法是检查电源和线路,修复或更换电机,修理或更换传动装置。
4.风机叶片积灰:由于长时间使用,风机的叶片表面可能会积聚灰尘或杂质,导致风机工作不正常。
解决方法是定期清洁叶片表面,确保风机通风畅通。
5.风机管路堵塞:由于管路长时间使用或外部杂质,风机的管路可能会堵塞,导致气体传输受阻。
解决方法是清理管路,确保气体畅通。
6.风机过热:如果风机长时间运行或环境温度较高,风机可能会过热。
过热可能是由于风机内部部件故障、润滑不良或风机负荷过大。
解决方法是检查风机部件,修复或更换故障部件,加强风机冷却措施。
7.风机噪音过大:当风机运行时,可能会产生较大的噪音,影响工作环境。
噪音过大的原因可能是风机内部部件松动、叶片失衡或轴承故障。
解决方法是检查风机部件,进行调整或更换松动部件,平衡叶片或更换轴承。
以上是风机的一些常见故障及分析。
在使用风机时,要定期检查、保养并及时处理故障,以保证风机正常工作。
同时,要注意风机的安全使用,避免因故障而导致事故的发生。
风力发电机主轴轴承失效分析

风力发电机主轴轴承失效分析摘要:近年来,随着我国整体经济建设的快速发展,人们生活水平和生活质量的不断提高,使得我国对于能源的需求越来越大。
我国风电行业比较严重和普遍存在的问题是大型双馈型风力发电机主轴轴承的磨损,已成为风力发电机组研发和重点排除的故障。
关键词:风力发电机;主轴轴承;失效分析引言:时代的进步,科技的发展使我国各行业发展非常迅速,推动我国提前进入现代化发展阶段。
风力发电机组中主轴连接轮毂和齿轮箱,是低速重载轴承,可靠性方面要求较高,也极易出现故障。
为了解决故障多发现象,需要系统的对现场轴承运转状况及失效形式进行分析和研究。
1以双馈异步低温型风电机组为例进行说明以某风电场为例,安装了100套1.5MW双馈异步低温型风电机组,其单机容量为1.5MW,总装机容量为15万kW。
2风电轴承常见问题分析目前问题概况:从风机轴承运行情况来看,各类轴承在运行过程中的问题集中体现在:过载、疲劳导致保持架、内外圈出现断裂或剥落现象;润滑性能不好、游隙不合理导致的滚动体、滚道,出现磨损、擦伤现象;过热导致轴承游隙过小,出现咬死现象;保护、维护不当,导致锈蚀、磕碰等现象,图一。
图一3主轴轴承在正常情况下失效的主要原因1)兆瓦级风力发电机的主轴轴承用的是双列调心滚子轴承,它必须承受轴向和径向的载荷,所以出现故障次数也比较多。
这是因为具有较大的间隙的双列调心滚子轴承,上风向侧的轴承承受较小的载荷,而下风向轴承要承受很多径向载荷和轴向力,这导致滚子过度滑动,如果润滑不良会导致材料腐蚀并剥落,使座圈,滚子和保持架受力不均出现变形的情况,导致座圈和轴承座之间出现不协调,引起常见故障,如位移和卡住。
2)在设计新的传动系统时,很少使用调心轴承作为主轴轴承。
一般建议使用圆锥滚子轴承,其有很强的径向和轴向承载力,通过预紧可以均匀地加载滚轮,滚轮不易滑动摩擦。
然而,在装置过程,由于安装精度和技术要求,轴承间隙如果调整不当会导致半干滚动摩擦,就会导致轴承失效。
风力发电场中风机轴承故障检测方法研究
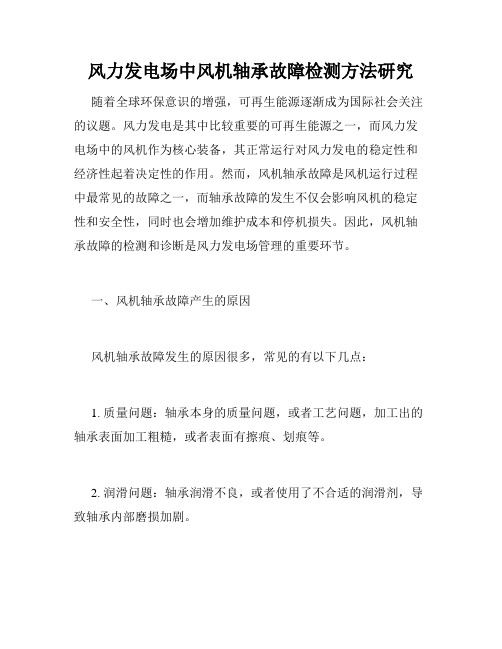
风力发电场中风机轴承故障检测方法研究随着全球环保意识的增强,可再生能源逐渐成为国际社会关注的议题。
风力发电是其中比较重要的可再生能源之一,而风力发电场中的风机作为核心装备,其正常运行对风力发电的稳定性和经济性起着决定性的作用。
然而,风机轴承故障是风机运行过程中最常见的故障之一,而轴承故障的发生不仅会影响风机的稳定性和安全性,同时也会增加维护成本和停机损失。
因此,风机轴承故障的检测和诊断是风力发电场管理的重要环节。
一、风机轴承故障产生的原因风机轴承故障发生的原因很多,常见的有以下几点:1. 质量问题:轴承本身的质量问题,或者工艺问题,加工出的轴承表面加工粗糙,或者表面有擦痕、划痕等。
2. 润滑问题:轴承润滑不良,或者使用了不合适的润滑剂,导致轴承内部磨损加剧。
3. 工作负荷:轴承承受工作负荷过大,或者太小,都会导致轴承内部磨损。
4. 温度问题:轴承温度过高、或者过低,都会影响轴承使用寿命。
二、风机轴承故障的检测方法风机轴承故障的检测方法有很多,目前常用的方法有以下几点:1. 听声法:通过听风机工作时发出的噪音,判断风机运行是否正常。
但该方法的可靠性不够高,而且适用范围窄。
2. 振动法:通过风机振动信号,来判断风机的运行状态。
但该方法需要专业的设备进行检测,成本较高。
3. 温度法:通过测量风机的温度变化来判断轴承的状态。
但该方法对温度波动较为敏感,且对温度测量设备有较高的要求。
4. 油液分析法:通过对润滑油进行分析,来判断轴承的状态。
但该方法需要收集相应的样本进行检测,较为麻烦。
三、基于机器学习的风机轴承故障检测方法随着人工智能的快速发展,机器学习技术在各个领域都有着广泛应用。
风机轴承故障检测也不例外,利用机器学习技术可以快速准确地识别出风机轴承故障,大大提高了故障检测的效率和准确性。
例如,基于机器学习的风机轴承故障检测方法中,可以通过传感器采集数据进行处理和分析。
通过构建适合于轴承故障检测的特征向量,并建立相应的分类器模型,最终可以高效准确地识别轴承故障。
风机主轴轴承座的主要故障
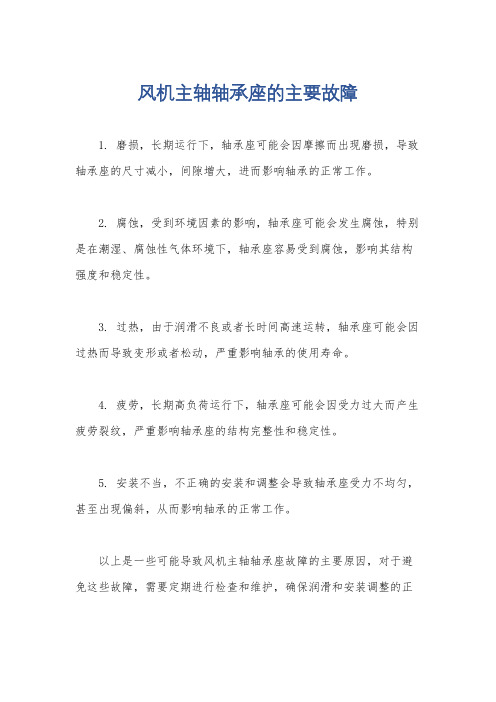
风机主轴轴承座的主要故障
1. 磨损,长期运行下,轴承座可能会因摩擦而出现磨损,导致轴承座的尺寸减小,间隙增大,进而影响轴承的正常工作。
2. 腐蚀,受到环境因素的影响,轴承座可能会发生腐蚀,特别是在潮湿、腐蚀性气体环境下,轴承座容易受到腐蚀,影响其结构强度和稳定性。
3. 过热,由于润滑不良或者长时间高速运转,轴承座可能会因过热而导致变形或者松动,严重影响轴承的使用寿命。
4. 疲劳,长期高负荷运行下,轴承座可能会因受力过大而产生疲劳裂纹,严重影响轴承座的结构完整性和稳定性。
5. 安装不当,不正确的安装和调整会导致轴承座受力不均匀,甚至出现偏斜,从而影响轴承的正常工作。
以上是一些可能导致风机主轴轴承座故障的主要原因,对于避免这些故障,需要定期进行检查和维护,确保润滑和安装调整的正
确性,以及保持良好的工作环境,从而延长轴承座的使用寿命,提高风机的可靠性和稳定性。
低温型风力发电用轴承使用过程中的故障与维修
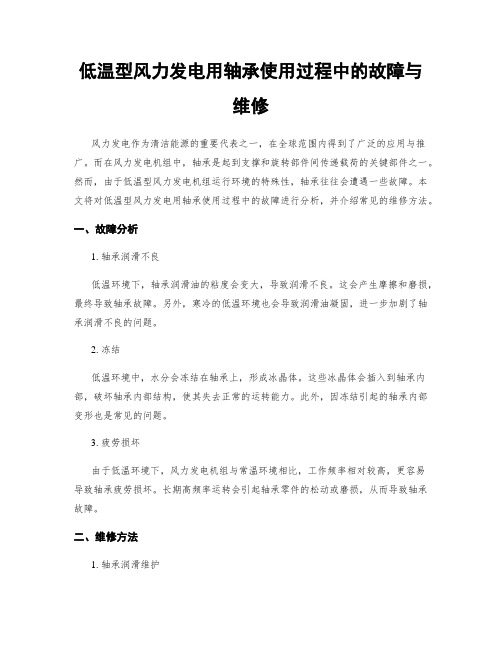
低温型风力发电用轴承使用过程中的故障与维修风力发电作为清洁能源的重要代表之一,在全球范围内得到了广泛的应用与推广。
而在风力发电机组中,轴承是起到支撑和旋转部件间传递载荷的关键部件之一。
然而,由于低温型风力发电机组运行环境的特殊性,轴承往往会遭遇一些故障。
本文将对低温型风力发电用轴承使用过程中的故障进行分析,并介绍常见的维修方法。
一、故障分析1. 轴承润滑不良低温环境下,轴承润滑油的粘度会变大,导致润滑不良。
这会产生摩擦和磨损,最终导致轴承故障。
另外,寒冷的低温环境也会导致润滑油凝固,进一步加剧了轴承润滑不良的问题。
2. 冻结低温环境中,水分会冻结在轴承上,形成冰晶体。
这些冰晶体会插入到轴承内部,破坏轴承内部结构,使其失去正常的运转能力。
此外,因冻结引起的轴承内部变形也是常见的问题。
3. 疲劳损坏由于低温环境下,风力发电机组与常温环境相比,工作频率相对较高,更容易导致轴承疲劳损坏。
长期高频率运转会引起轴承零件的松动或磨损,从而导致轴承故障。
二、维修方法1. 轴承润滑维护为了解决轴承润滑不良的问题,首先需要选择适用于低温环境的润滑油。
这种润滑油应具备较低的粘度,以确保在低温下保持良好的润滑效果。
同时,定期更换润滑油也是必要的,以保持其良好的润滑性能。
2. 防冻措施为了避免冻结现象对轴承的影响,可以在轴承周围设置加热设备或使用加热电缆进行防冻处理。
这样可以有效地防止轴承部位的水分冻结,保持正常的工作状态。
3. 定期检查与维护为了预防轴承故障的发生,应定期对轴承进行检查和维护。
检查内容包括轴承外观、润滑油污染程度、轴承运行状态等方面。
如果发现问题,及时采取维修措施,如紧固螺栓、更换磨损严重的零件等。
定期检查和维护可以及时发现轴承故障的迹象,从而减少故障发生的可能性。
4. 增加轴承寿命为了延长轴承的使用寿命,可以采取一些措施。
首先,合理设置风力发电机组各部件的参数,以减少轴承受力。
其次,增加轴承的径向间隙,提高轴承的抗疲劳能力。
风力发电机主轴承故障分析与诊断
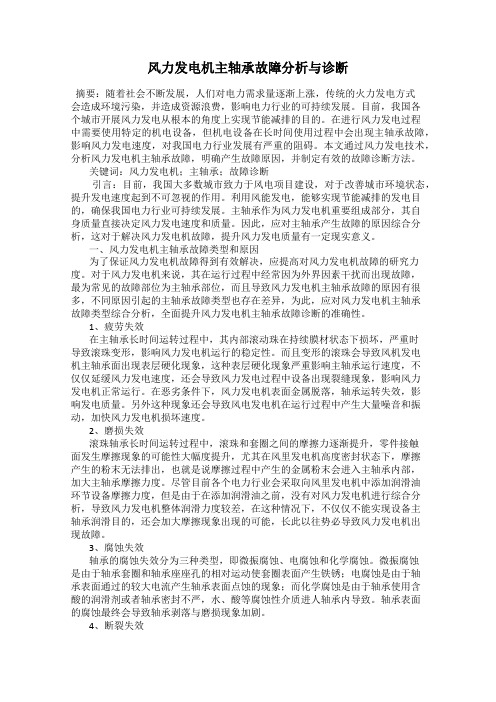
风力发电机主轴承故障分析与诊断摘要:随着社会不断发展,人们对电力需求量逐渐上涨,传统的火力发电方式会造成环境污染,并造成资源浪费,影响电力行业的可持续发展。
目前,我国各个城市开展风力发电从根本的角度上实现节能减排的目的。
在进行风力发电过程中需要使用特定的机电设备,但机电设备在长时间使用过程中会出现主轴承故障,影响风力发电速度,对我国电力行业发展有严重的阻碍。
本文通过风力发电技术,分析风力发电机主轴承故障,明确产生故障原因,并制定有效的故障诊断方法。
关键词:风力发电机;主轴承;故障诊断引言:目前,我国大多数城市致力于风电项目建设,对于改善城市环境状态,提升发电速度起到不可忽视的作用。
利用风能发电,能够实现节能减排的发电目的,确保我国电力行业可持续发展。
主轴承作为风力发电机重要组成部分,其自身质量直接决定风力发电速度和质量。
因此,应对主轴承产生故障的原因综合分析,这对于解决风力发电机故障,提升风力发电质量有一定现实意义。
一、风力发电机主轴承故障类型和原因为了保证风力发电机故障得到有效解决,应提高对风力发电机故障的研究力度。
对于风力发电机来说,其在运行过程中经常因为外界因素干扰而出现故障,最为常见的故障部位为主轴承部位,而且导致风力发电机主轴承故障的原因有很多,不同原因引起的主轴承故障类型也存在差异,为此,应对风力发电机主轴承故障类型综合分析,全面提升风力发电机主轴承故障诊断的准确性。
1、疲劳失效在主轴承长时间运转过程中,其内部滚动珠在持续膜材状态下损坏,严重时导致滚珠变形,影响风力发电机运行的稳定性。
而且变形的滚珠会导致风机发电机主轴承面出现表层硬化现象,这种表层硬化现象严重影响主轴承运行速度,不仅仅延缓风力发电速度,还会导致风力发电过程中设备出现裂缝现象,影响风力发电机正常运行。
在恶劣条件下,风力发电机表面金属脱落,轴承运转失效,影响发电质量。
另外这种现象还会导致风电发电机在运行过程中产生大量噪音和振动,加快风力发电机损坏速度。
风力发电组轴承的常见失效形式及故障分析
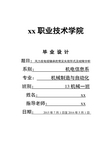
xx职业技术学院毕业设计题目:风力发电组轴承的常见失效形式及故障分析系别:机电信息系专业:机械制造与自动化班别:13机械一班姓名:xx指导老师:xx 日期:2015年7月1日至2016年5月1日内容摘要随着全球经济的发展和人口的增长,人类正面临着能源利用和环境保护两方面的压力,能源问题和环境污染日益突出。
风能作为一种蕴藏量丰富的自然资源,因其使用便捷、可再生、成本低、无污染等特点,在世界范围内得到了较为广泛的使用和迅速发展。
风力发电己成为世界各国更加重视和重点开发的能源之一。
随着大型风力发电机组装机容量的增加,其系统结构也日趋复杂,当机组发生故障时,不仅会造成停电,而且会产生严重的安全事故,造成巨大的经济损失。
本论文先探讨了课题的实际意义以及风力发电机常见的故障模式,在这个基础上对齿轮箱故障这种常见故障做了详尽的阐述,包括引起故障的原因、如何识别和如何改进设计。
通过对常见故障的分析,给风力发电厂技术维护提供故障诊断帮助,同时也给风电设备制造和安装部门提供理论研究依据。
关键词风力发电机;故障模式;齿轮箱;故障诊断Common Faults And Their AnalysisOf The Wind TurbineAbstractWith the global economic development and population growth, humanity is facing with the pressure from two sides of the energy use and environmental protection, the energy problem and environmental pollution has become an increasingly prominent issue. Wind power as a abundant reserves of natural resources, because of its convenient use, renewable, low cost, no pollution, has been more widely used and rapid development in the world. Wind power has been taken as one of the priority development energy sources in the world.The increase of wind power capacity and complicated system structure will not only cause power outage,but also raise serious accidents when the set is at fault.In the beginning, the dissertation introduces the practical significance of project and the common failure mode of wind turbines, then researches and describes the failure of gearbox in detail, including the cause of failure, how to identify and how to improve the design. Based on the analysis of common failures, not only provide assistance for fault diagnosis to the technicalmaintenance of wind power plants, but also provide a theoretical basis to the wind power equipment manufacturing and installation departments.Key WordsWind Turbines; Failure Mode; Gear Box; Fault Diagnosis目录第一章绪论 (1)1.1 风力发电的背景 (1)1.2 风力发电机故障诊断的意义 (2)第二章风力发电机常见故障模式及机理分析 (5)2.1 风力发电机结构 (5)2.2 常见故障模式及机理分析 (7)2.2.1 叶片故障及机理 (7)2.2.2 变流器故障及机理 (8)2.2.3 发电机故障及机理 (10)2.2.4 变桨轴承故障及机理 (13)2.2.5 偏航系统故障及机理 (16)2.3 本章小结 (21)第三章风力发电机齿轮箱故障诊断 (22)3.1 风力发电机齿轮箱常见故障模式及机理分析 (22)3.2 齿轮箱典型故障振动特征与诊断策略 (28)3.3 针对齿轮箱不同故障的改进措施 (32)第四章结论 (36)致谢 (37)参考文献 (38)风力发电机常见故障及其分析第一章绪论1.1 风力发电的背景随着全球人口数量的上升和经济规模的不断增长,世界范围内对能源需求持续增加,化石能源、生物能源等常规能源使用带来的环境问题日益突出。
风机轴承损坏案例分析

风机轴承损坏案例分析一、事故经过原料立磨1327循环风机于2009年11月3日投入生产运行,2010年元月22日,因该风机固定端轴承突然振动大导致跳停,检查发现轴承损坏,由苏州中材进行更换,本次更换的是国产轴承(瓦房店)。
更换后运转至2月2日,轴承出现高温导致风机跳停,检查发现该轴承又一次损坏,由制造分厂自行更换进口轴承(SKF),并对风机与电机进行找正。
之后开机至2月12日因高温导致风机跳停,经检查发现该轴承有一只滚动体、轴承内圈均出现剥离,由制造分厂再一次组织更换进口轴承(SKF)。
结合前期安装情况,对风机与电机进一步找正,包括膜片联轴器的安装间距进行调整、复核。
开机正常。
二、原因分析原料立磨1327循环风机固定端轴承自投入运行以来共损坏三次,经与会人员研讨分析,初步原因如下:第一次轴承损坏的主要原因是:风机整体偏低,运行持续震动,轴承承受的径向载荷过大而导致轴承损坏;第二次和第三次轴承损坏的原因:主要是第一、二次轴承损坏更换后,没有对膜片联轴器之间的间隙(设计为195mm,事后复核为202mm)进行核实,更换轴承后,挪动了电机,认为电机螺栓孔没动,就没有复核联轴器之间的间隙,导致电机开机后,轴承承受轴向力过大,是导致轴承损坏的主要原因。
轴承因受轴向力过大产生热膨胀后轴承游隙变小,出现轴承卡死是轴承损坏的次要原因。
2月12日更换轴承后开机之前,也没有复核膜片联轴器之间的间隙,因此开机2次(第一次运行5分钟后出现跳停、第二次运行15分钟后又出现跳停)后,电机因综保动作无法开启。
经查找图纸结合现场分析,结果发现:联轴器之间的自由间隙为202mm,图纸要求为195mm,相差7mm。
螺栓连接后联轴器之间的间隙为196mm,也就是把电机主轴拉往风机侧6mm;因此风机开机时电机主轴要恢复自身位臵较难,只有拉着风机主轴往电机方向运动,致使风机固定端轴承受到很强的轴向力,这是后三次固定端轴承频繁出现损坏的主要原因。
- 1、下载文档前请自行甄别文档内容的完整性,平台不提供额外的编辑、内容补充、找答案等附加服务。
- 2、"仅部分预览"的文档,不可在线预览部分如存在完整性等问题,可反馈申请退款(可完整预览的文档不适用该条件!)。
- 3、如文档侵犯您的权益,请联系客服反馈,我们会尽快为您处理(人工客服工作时间:9:00-18:30)。
图1 101BJ一段炉风机
风机轴承故障分析及校核
傅德兴
(重庆建峰化工股份有限公司化肥分公司 重庆408601)
摘 要 一段炉风机自原始开车以来多次出现振动高的现象,通过运行监测数据分析进行了处理及轴承校核计算,提出解决风机轴承故障处理措施及建议。
关键词 振动 轴承故障 分析 校核
1 概述
重庆建峰化工股份有限公司化肥分公司第二套化肥年产50万吨合成氨装置采用美国KBR 工艺,于2010年3月建成投产。
101BJ 一段炉风机是单级叶轮双侧进气离心式风机,型号DFY21.5F-C4A ,如图1所示。
风机叶轮直径φ2150mm ,共24个后向机翼型焊接叶片,材质为15MnV 。
主轴材料45#,经过锻造和热处理后精加工而成。
支承轴承为22340CC/W33型调心球面滚子轴承,驱动端为转子固定端,非驱动端是转子自由膨胀端。
风机进口的进气箱采用了防止气流涡旋的结构,进气角度为00。
风机转速780~850RPM ,最高转速990RPM ,转子临界转速为1300RPM ,转子重量12410KG ,轴承支撑距离为6米。
介质为天然气燃烧后的烟气,设计进口温度为
185 ℃。
由EILLOT 公司生产的蒸汽小透平驱动,中间通过减速箱相连,齿轮箱的减速比为5.333。
透平及齿轮箱由机组润滑油系统供油,风机前后轴承采用油浴飞溅润滑的方式。
2 故障现象
一段炉风机在2010年6月的装置原始开车期间,冷态试车一切正常,而投运后的热态开车多次出现振动大、油封冒烟、内部有异响等故障现象,前后端轴承轴向振动在3.5~7 mm/s 波动,最高达17 mm/s ;垂直方向振动在1.5~3 mm/s ,最高达6 mm/s ,而且前后轴承振动与入口温度有相近的变化关系。
7月装置消缺期间对风机进行了一次全面的处理后,轴承各点振动速度均在1.5mm/s 以下。
自2012年投入长期运行,2013年8月2日驱动端轴承开始出现异音且温度逐渐上升,振动在5~13 mm/s 波动,8月7日停车检修,拆卸后发现自动调心轴承的滚子出现严重磨损剥落破坏。
3 故障分析及处理措施
3.1转子动不平衡的影响因素。
根据出厂试验和转子动平衡后的允许偏心距为38μm ,通过计算,转子动平衡精度为G=38*990*2*π/(60*1000)≈
4.0,高于ISO1940/1标准中风机转子的动平衡精度应做到G6.3级的要求。
另外,风机在冷态试车各项参数正常,因此排除了转子动平衡的影响。
3.2轴承座安装偏差影响因素。
根据运行期间的故障现象,分析风机转子运行过程中承受了较大的附加轴向应力。
检查发现非驱动端的轴承与轴承座之间有0.1mm 垫片,存在0.03mm 预紧力。
而非驱动端应是风机转子热态运行的自由滑动端,因此轴承与轴承座之间预紧力,使得转子在热态运行下无法自由膨胀导致风机的振动加剧。
同时通过在转轴上架表,检查了轴承座的垂直度及轴承座与轴的同心度,发现有较大的偏差,如图2所示:
图2 轴承座同心度检测
风机轴承22340CC/W33属调心球面滚子轴承,其最大允许调心角为30,其检测数据计算的偏心角为0.220。
为保证轴承正常使用,对轴承座的同心度进行了精确的调整,同时还保证非驱动端轴承与轴承座之间的0.05~0.07mm 配合间隙,通过对上述安装偏差的调整处理,消除了风机转子振动大的故障现象。
3.3 工艺进气温度影响因素。
图3是风机运行时监测的进气温度与转子轴承的轴向和径向振动变化的关联图。
受原始开车诸多因素影响风机入口温度时有超过185℃的设计温度,当风机的入口温度在200℃以内,风机的振动随温度的变化相对较小,当温度超过200℃甚至更高时,风机的振动受温度的升降影响明显。
分析是由于轴的材料是45#钢,随着温度的升高,所产生的线性膨胀和临时热弯曲越大,轴的刚度发生改变,从而影响转子振动升高,因此通过调整转速和风机进气温度都会使转子的振动降低。
0.4
0.43
0.85
0.7
1.55
0.83
表架在转轴上,表打在轴承端面非驱动端
驱动端
mm mm
图3 工艺气温度与振动趋势
3.4 轴承寿命校核及原因分析
截止2013年8月2日一段炉风机自投用以来累计运
行约500天(12000工作小时),远低于此类轴承
40000~50000h的使用寿命的设计要求。
8月7日拆卸检修
时发现损坏的滚子轴承如图4所示。
风机滚动轴承损坏发生在天气最热的时候,现场环境
温度在450以上,而转子温度在1750左右,通过轴的传热,
轴承箱的实际工作温度在900以上。
分析是因为轴承箱油
浴飞溅润滑未能有效的带走热量导致轴承过热产生过度磨图4 损坏的滚子
损。
从损坏的滚子看,表面发黑且有明显的磨损痕迹,说明轴承工作温度的升高对轴承元件材料产生影响,轴承硬度降低,导致承载能力的下降进而缩短了轴承的使用寿命。
3.4.1轴承寿命选型的校核。
根据轴承产品表和厂家提供数据见表1:
表1 SKF轴承和GB/T288-1994轴承产品表及转子工作参数
当量动负荷:Fa /Fr=0.15≤e, P=Fr+Y1*Fa=83.2 KN
基本额定寿命:L10h=106*(C/P)3.3/(60*N)=1153807(工作小时)
=83.2/2900=0.029和润滑油牌号ISO46根据轴承平均直径(200+420)/2=310m、P/C
等信息,查阅SKF资料表得轴承负荷调整系数fp=1,油粘度调整系数fv=0.95,故在70℃轴承允许转速n perm=Nr*fp*fv=1200*1*0.95=1100rpm。
通过上述计算判断,选用SKF轴承是满足使用要求的。
但若按GB/T288-1994调心滚子轴承提供的计算数据,该轴承的当量动负荷为81.28KN,基本额定使用寿命289067工作小时,极限转速为800rpm,因此若按GB/T288-1994选择此型轴承就不合适宜。
3.4.2轴承润滑方式的复核
轴承润滑方式通常按速度系数dn值的大小和轴承载荷作为设计选择方式(见表2)。
而该风机调心滚子轴承dn值=2(200+420)*850=263500mm.rpm,且属中速重载荷,按表2选择润滑方式应选喷油循环润滑方式更为优化合理。
尤其是22340CC/W33轴承本身是双列调心球面滚子轴承,现有轴承座的型式以及油浴飞溅润滑方式使得轴承中部三个进油孔无法使用,从而难以保证该轴承良好的润滑并带走所产生的热量。
表2 轴承润滑方式选择表
3.4.3喷油循环润滑方式的可行性
计算,润滑油压力0.1~0.5Mpa下供油
0.5~10L/min,取中间值得风机前后轴
承用油量为15L/min。
而齿轮箱所需最
大润滑油量80L/min,透平前后轴承润
滑油量15.2 L/min,润滑油系统油泵的
正常流量为112 L/min,润滑油压1.1bar,图5 喷油循环示意图
因此对现有机组润滑油系统不作改造的情况下,将滚动轴承的油浴飞溅润滑方式改为喷油循环润滑方式是完全可行的,同时须将现有轴封改为梳齿密封形式,如图5所示。
4 下步措施与建议
通过前期故障处理及原因分析,为保障风机长周期的正常运行建议从以下方面加以完善与改进:
①轴承仍沿用油浴润滑方式,每6个月应在线更换一次润滑油,在夏季或缩短换油周期以保证轴承箱内油品质量;
②通过大修期间对轴承座进行必要的技改或换型,采用喷油循环润滑的方式保证轴承充分润滑并带走轴承箱产生的高温热量;
③严格控制轴承座的同心度和垂直度,尽量降低轴承偏心角对轴承运行产生的影响。
④风机运行时应定期使用手持式测振仪和测温仪进行在线监测,加强运行监控。
参考文献
[1]朱向哲贺威袁慧群稳态温度场对转子系统振动特性的影响东北大学学报第29卷第1期 2008年1月。