注射成型模具的设计
注塑模具设计与制造教程

03
注塑模具结构设计
分型面设计技巧及注意事项
分型面选择原则
确保产品顺利脱模,减少溢料和 飞边,简化模具结构。
分型面设计要点
分型面应位于产品断面轮廓最大 的地方,便于脱模;避免在分型 面上设计小孔或凹槽,防止溢料 和飞边;分型面的设计应便于模
具的加工和装配。
注意事项
分型面的选择应避免影响产品的 外观和性能;对于复杂的产品, 可能需要采用多个分型面进行脱
性能要求
模具材料应具有良好的切削加工性、热处理稳定 性、耐磨性、耐腐蚀性和抗疲劳性等性能。
精度与表面质量要求
精度要求
根据产品精度要求,确定模具的制造 精度和装配精度,保证产品的尺寸精 度和形位公差。
表面质量要求
模具表面应平整、光滑,无裂纹、毛 刺等缺陷;分型面、型腔等重要表面 应达到一定的粗糙度要求,以保证产 品的外观质量和脱模顺畅。
分类
根据模具的结构和使用特点,注塑模具可分为单分型面 注塑模、双分型面注塑模、带有侧向分型与抽芯机构的 注塑模以及热流道注塑模等。
注塑模具结构组成
导向部件
浇注系统
由主流道、分流道、浇口和冷料 穴等组成,用于将熔融的塑料从 注塑机喷嘴引入模具型腔。
包括导柱、导套等,用于保证动 模和定模在合模时的相对位置精 度。
压力调整技巧及常见问题解决方案
压力调整技巧
注射压力、保压压力和背压是注塑成型过程中的关键压力参数。 根据产品的结构、壁厚和塑料的流动性,合理调整这些压力参 数,以确保塑料充分填充模具并补偿收缩。
常见问题解决方案
针对飞边、短射、缩水等常见问题,通过调整注射速度、保压 时间和压力分布等参数,可以有效改善产品质量。
加工工艺流程梳理与规范操作指南
塑料成型工艺与注射模具设计 (4)

2
相关知识点
(2)嵌件 的预热
为了满足装配和使用强度的要求,塑件内经常要嵌入金属嵌 件。由于金属和塑料收缩率相差较大,因而在塑件冷却时,嵌 件周围产生较大的内应力,导致嵌件周围塑料层强度下降和出 现裂纹。因此,成型前应对金属嵌件进行预热,以降低它与塑 料熔体的温差,减小内应力。
2
相关知识点
(3)料筒 的清洗
2
相关知识点
螺杆式注射机注射成型工作循环,如图4-3所示。
图4-3
2
相关知识点
与柱塞式注射机注射成型相比 较,螺杆式注射机注射成型由于 螺杆的剪切作用,塑料混合均匀, 塑化效果好,改善了成型工艺, 提高了塑件质量。同时扩大了注 射成型塑料品种的范围和最大注 射量。因此,对于热敏性和流动 性差的塑料和大、中型塑件,一 般可用移动螺杆式注射机成型。
2
相关知识点
当残余压力为正值时,脱模比较困 难,塑件容易被刮伤甚至破裂;当残 余压力为负值时,塑件表面易出现凹 陷或内部有真空泡。因此,只有残余 庄力接近为零时.脱模较顺利,而且 可获得较满意的塑件。 ◆塑件的冷却速率应适中,冷却速率 过快或模温不均匀,都会导致冷却不 均和收缩的不一致,使塑件内部产生 内应力,出现翘曲变形。
2
相关知识点
完整的注射过程包括加料、塑化、 注射、保压、冷却和脱模等几个阶段。 (1)加料 将粉状或粒状的塑料加入注射机料 斗,由柱塞或螺杆带入料筒内加热。 (2)塑化 成型塑料在注射机料筒内经加热、 压实以及混料等作用,由松散的粉状 颗粒或粒状的固态转变为连续的均匀 塑化熔体的过程。对塑化的要求是: 在规定的时间内塑化出足够数量的熔 融塑料;塑料熔体进入模具型腔内之 前应达到规定的成型温度,而且熔体 各点温度应均匀一致,避免局部温度 过低或温度过高。
塑料注射模具课程设计

塑料注射模具课程设计一、课程目标知识目标:1. 学生能理解并掌握塑料注射模具的基本结构及其工作原理;2. 学生能了解并描述塑料注射模具的设计流程和关键参数;3. 学生能掌握相关模具材料的选择和应用。
技能目标:1. 学生能运用CAD软件进行塑料注射模具的设计;2. 学生能运用CAE软件对塑料注射模具进行模拟分析;3. 学生能运用CAM软件进行模具的制造编程。
情感态度价值观目标:1. 学生培养对工程技术专业的热爱和兴趣;2. 学生树立正确的工程观念,注重产品质量,遵循工匠精神;3. 学生培养团队协作意识,提高沟通与表达能力。
分析课程性质、学生特点和教学要求,本课程旨在让学生掌握塑料注射模具设计的基本知识和技能,培养他们解决实际工程问题的能力。
课程目标具体明确,分解为以下具体学习成果:1. 学生完成模具结构设计,并能清晰地展示设计思路和步骤;2. 学生完成模具模拟分析,对分析结果进行合理解释;3. 学生完成模具制造编程,并能对制造过程进行优化;4. 学生在课程实践中,展现出良好的团队协作和沟通能力,以及对工程技术专业的热情。
二、教学内容1. 塑料注射模具基础知识- 模具分类及工作原理- 塑料材料性能与选择- 模具结构及其组成2. 塑料注射模具设计流程- 设计前期准备- 模具结构设计- 模具关键参数确定- 设计验证与优化3. 塑料注射模具CAD/CAE/CAM软件应用- CAD软件进行模具设计- CAE软件进行模拟分析- CAM软件进行制造编程4. 塑料注射模具实践操作- 模具设计与分析案例- 模具制造与调试- 故障分析与解决方案教学内容按照以下进度安排:第一周:塑料注射模具基础知识学习;第二周:塑料注射模具设计流程学习;第三周:CAD/CAE/CAM软件操作学习;第四周:实践操作与案例分析。
教学内容与教材关联紧密,涵盖以下章节:1. 教材第1章:塑料注射成型概述2. 教材第2章:塑料注射模具设计基础3. 教材第3章:塑料注射模具CAD/CAE/CAM技术4. 教材第4章:塑料注射模具实践操作与案例分析教学内容科学系统,确保学生能够循序渐进地掌握塑料注射模具相关知识,为后续课程打下坚实基础。
注塑模具结构及设计-9设计实例改善及细节改进
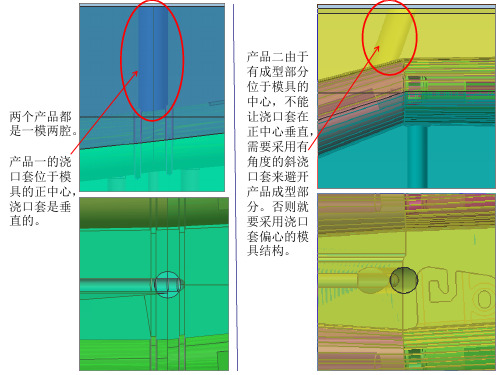
单独的垃圾钉
垃圾钉的位置要考虑顶出板和底板上的各零部件的情况,尽量做到均匀布置,受力平衡。
普通的浇口套的料把经常有拉丝的现象,可以在浇口套的中间加上 一个金属隔片来做成防拉丝的浇口套。
普通的浇口套
防拉丝的浇口套
防拉丝浇口套中间有镶件槽
金属隔片
锁模块
锁模块用在动,定模之间,可以锁紧动, 定模,防止吊装时模具分开产生事故。 通常在模具上是对称布置的。
由于两个滑块的抽芯 距都比较长,当两抽 芯合拢时头部容易产 生错位。
预防措施: 在两个抽 芯的头部 加上锥度 的定位。
两抽芯合拢时因 为有定位的作用, 可以防止错位。
因为有油缸, 所以模具必 须加上长支 腿才能平稳 放置。
支腿的固定 形式采用右 图时,模具 在翻转时螺 钉容易断裂。
支腿的固定 形式改为镶 入式后,模 具在翻转时 产生的剪切 力由镶入部 分承受,螺 钉不容易断 裂。
Z钩形
环槽形
倒锥形
对于型芯的碰穿面要留研配的余量, 尺寸应该标注正公差。
产品
型芯
正公差加在红 色的碰穿面上
从加工方面考虑,顶杆的布置遇到镶拼结构时,一般不允许顶杆 跨越镶拼线,如图1所示。扁顶杆、方顶设计在镶块中间时,成型 制品部分一般要在镶块的一侧。不得跨越两个镶块,如图2所示。
跨越镶拼线不允许
承压片
在模具的动,定模板之间,加上承压片 可以在研配时通过调整承压片的厚度方 便的调整动,定模板之间的间隙和分型 面上所受合模力的大小。 模板上开框
增加承压片
单独的承压片立体图
定模
动模 承压片
单独的带肩螺栓立体图 复位弹簧
带肩螺栓 带肩螺栓用在顶出板上时, 可以利用螺纹部分的拧入 来克服弹簧的预压缩力从 而方便拆装顶出板。
模具毕业设计103注射模的结构设计

模具毕业设计103注射模的结构设计注射模具是工业制造过程中使用最广泛的一种模具,其设计结构直接影响到注射产品的质量和生产效率。
本文将详细介绍注射模具的结构设计,包括模具的结构要求、主要零件设计和结构优化。
一、模具的结构要求1.注射模具的结构要具有良好的刚性和稳定性,以确保模具在注射过程中不发生变形和振动,影响产品的精度和表面质量。
2.注射模具的结构要便于装卸、维修和保养,以提高模具的使用寿命和工作效率。
3.注射模具的结构要尽可能简单,以降低模具的制造成本和维修成本。
二、注射模具的主要零件设计1.模具基座:模具基座是支撑模具的主要部件,其结构要具有足够的刚性和稳定性。
为了方便模具的安装和调整,模具基座通常采用箱式结构,并设置有调整螺栓。
2.模板:模板是注射模具的主要部件,其上安装有注射模具的零件和导向机构。
模板的结构要求平整度高、刚性好,并配有合适的冷却系统,以确保注射过程中的热平衡。
3.滑块和导柱:滑块和导柱是注射模具中重要的导向和定位部件。
滑块通常用于实现中空或复杂形状的注射产品,其结构要求刚性好、耐磨损,并具有良好的导向性能。
导柱负责注射模具的下模板与上模板的定位,其结构要求尺寸精确、表面光洁,并配有合适的润滑系统。
4.模芯和模腔:模芯和模腔是注射模具成型部件的关键零部件,直接决定了注射产品的形状和尺寸。
模芯和模腔的设计要考虑到材料的选用、热处理和表面处理等因素,以提高模具的耐用性和工作精度。
三、注射模具的结构优化为了进一步提高注射模具的生产效率和产品质量,可以采取以下措施进行结构优化:1.采用优质材料:选择适当的模具材料,具有良好的强度和耐磨性,以提高模具的使用寿命和工作精度。
2.优化冷却系统:合理设置注射模具的冷却系统,以提高注射过程中的热平衡,减少产品变形和缩水现象。
3.降低模具重量:通过优化模具结构和采用轻量化材料,来减轻模具的重量,降低模具的惯性和振动,提高注射产品的精度和表面质量。
注射模具设计基础60

1.按料进料(浇口)的形式模架分为哪两大类? 2、模架中需要设计的部分有哪些? 3、默写36种模架.
第六章 注射模的典型结构与注射机
目的与要求: 1.了解注射模结构组成; 2.按结构特征进行分类的几种结构组成、工作原理。 3.掌握注射机最大注射量和锁模力的校核方法。 4.掌握模具与注射机安装部分相关尺寸和开模行 程的校核。60 Nhomakorabea60
70
200
200
285
250×280 250×280 330×440 428×458 598×520 620×520
235×235 235×235 190×300 260×290 448×370 400×300
¢63.5 ¢63.5
¢55
¢100 ¢125 ¢180
SR12 ¢2
SR12 ¢4
SR12 ¢4
SR12 ¢4
SR18 ¢4
SR18 ¢4
顶出形式
两侧顶出 两侧顶出 中心顶出 两侧顶出 两侧顶出 两侧顶出
顶杆中心距 mm
70
170
230
280
280
最大成型面 积
机器外形尺 寸
cm2
mm× mm×
90
90
130
320 550、500
2340×80 234×800 3160×850 3310×75 470×100 530×940 0×1460 ×1460 ×1550 0×1550 0×1815 ×1815
(4)带活动镶件的注射模具 有些塑料制品上虽有侧向的通孔及凹凸形状,但还有更特 殊的要求,模具上需要设置螺纹型芯或螺纹型环等。
开模时,这些活动镶件不能简单地沿开模方向与塑件分离,而是必须在塑件脱模时连 同塑件一起移出模外,然后通过手工或专门的工具将它与塑件分离,在下一次合模注 射之前,再重新将其放入模内。
《注射模设计》
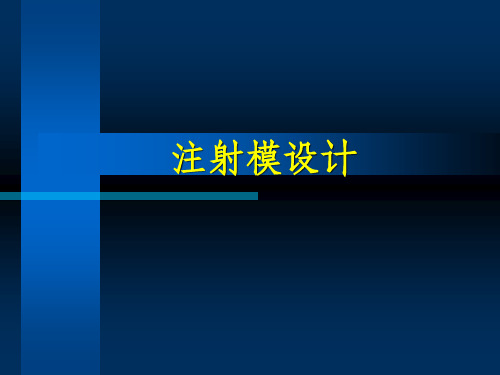
.
39
(二)型腔的布置
1.平衡式浇注系统
分流道到浇口及型腔,其形状、长宽尺寸、圆角、模 壁的冷却条件都完全相同,熔体能以相同的成型压 力和温度同时充满所用型腔。
缺点:流道 总长度要长 些,热量压 力损失大, 模板尺寸大。
.
40
(二)型腔的布置
2.非平衡式浇注系统 由于主流道到各型腔的分流道长度各不相同或 者各型腔形状尺寸不同而使得浇注系统不平衡。
.
16
一、分型面设计 (一)分型面的形式
分型面:是模具上开模时用于取出塑件和(或)浇 注系统冷凝料的可分离的接触表面。
分型面的分类:
1.按其位置与注射机开模运动方向的关系来分类:
垂直于注射机开模运动方向,平行于开模方向,倾 斜于开模方向
2.按分型面的形状来分类 :平面分型面,曲面分型面, 阶梯分型面和斜面分型面
定范围,也不意味浇口浇口越小越好。
.
46
(一)浇注系统流变学
(2)合理的选择剪切速率
在较低的剪切速率范围内,由于剪切速率的微 小变化会引起粘度的巨大变化。这将使注射成型难 以控制,使塑件出现表面不良、充模不匀、密度不 均、内应力高、翘曲以及收缩不均等毛病。所以,
要在ηa ~γ́ 曲线上选取这么一段剪切速率,使它
.
20
(二)选择分型面的原则
使塑件开模时留在动模侧:
.
21
(二)选择分型面的原则
简化模具制造:
.
22
(二)选择分型面的原则
有利于抽芯(活动型芯置于动模):
.
23
(二)选择分型面的原则
有利于抽芯(缩短抽芯距离):
.
24
(二)选择分型面的原则
注射模具成型零件的设计

第四节 成型零件尺寸的确定
一、影响塑件尺寸的因素 成型收缩率的选择和成型收缩的波动引起的尺寸误差 成型零件的制造误差、组装误差及相对移动引起的误差; 成型零件脱模斜度引起的误差 成型零件磨损及化学腐蚀引起的误差 二、确定成型零件尺寸的原则
1.综合考虑以下因素,确定合适的塑料收缩率 塑件壁厚、形状及嵌件:壁厚较大、形状较复杂或有时嵌件取偏小值 熔料流向:与进料方向平行的尺寸取偏小值 浇口截面积:浇口截面积小的比大的收缩率大,应取偏大值 与浇口的距离:近的部位比远的部位收缩率小,应选较小值 型腔尺寸取小于平均收缩率的值,型芯尺寸取大于平均收缩率的值 2.据成型零件的性质决定各部分成型尺寸:图5-17 3.脱模斜度的取向:型腔尺寸以大端为准,脱模斜度向缩小方向取得;型
二、型腔壁厚和底板厚度的计算
1.注射过程中型腔所受的力
合模时的压应力;注射压力;保压压力;开模时的拉应力
2. 型腔壁厚和底板厚度计算的必要性:图5-7.8.9.10
型腔刚度不足时会产生弹性变形,型腔向外膨胀,影响塑件质量和尺寸 精度,并产生溢料、飞边
型腔强度不足时会产生塑型变形,可引起型腔永久变形甚至破裂
S刚
22.8 57 98.7 131 145 195 249
S强
35 71 106 131 141 177 212
结论
当圆形型腔内半径r=86mm和矩形型腔的长边L1=370mm时,按刚度和 强度分别算得的侧壁厚度相等。故取r=86mm和L1=370mm为临界值, 当小于该值时按强度计算,大于该值时按刚度计算
塑件螺纹为M20x2-6H/5g,6g,塑料收缩率为0.6%,计算螺纹型环和型芯的各部
分尺寸。
五、小直径螺纹型芯安装形式图5-24
注射模具设计尺寸计算公式
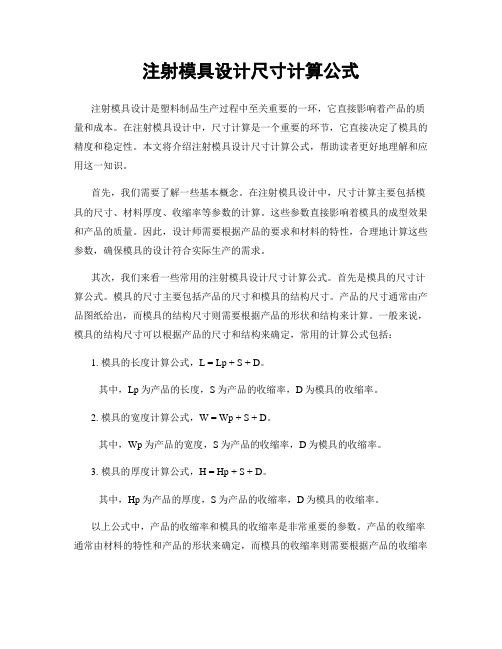
注射模具设计尺寸计算公式注射模具设计是塑料制品生产过程中至关重要的一环,它直接影响着产品的质量和成本。
在注射模具设计中,尺寸计算是一个重要的环节,它直接决定了模具的精度和稳定性。
本文将介绍注射模具设计尺寸计算公式,帮助读者更好地理解和应用这一知识。
首先,我们需要了解一些基本概念。
在注射模具设计中,尺寸计算主要包括模具的尺寸、材料厚度、收缩率等参数的计算。
这些参数直接影响着模具的成型效果和产品的质量。
因此,设计师需要根据产品的要求和材料的特性,合理地计算这些参数,确保模具的设计符合实际生产的需求。
其次,我们来看一些常用的注射模具设计尺寸计算公式。
首先是模具的尺寸计算公式。
模具的尺寸主要包括产品的尺寸和模具的结构尺寸。
产品的尺寸通常由产品图纸给出,而模具的结构尺寸则需要根据产品的形状和结构来计算。
一般来说,模具的结构尺寸可以根据产品的尺寸和结构来确定,常用的计算公式包括:1. 模具的长度计算公式,L = Lp + S + D。
其中,Lp为产品的长度,S为产品的收缩率,D为模具的收缩率。
2. 模具的宽度计算公式,W = Wp + S + D。
其中,Wp为产品的宽度,S为产品的收缩率,D为模具的收缩率。
3. 模具的厚度计算公式,H = Hp + S + D。
其中,Hp为产品的厚度,S为产品的收缩率,D为模具的收缩率。
以上公式中,产品的收缩率和模具的收缩率是非常重要的参数。
产品的收缩率通常由材料的特性和产品的形状来确定,而模具的收缩率则需要根据产品的收缩率和模具材料的特性来确定。
一般来说,模具的收缩率可以通过实验和经验来确定,设计师需要根据实际情况来选择合适的收缩率。
另外,还有一些常用的注射模具设计尺寸计算公式,如材料厚度的计算公式、模具的结构尺寸的计算公式等。
这些公式可以根据具体的产品和模具来确定,设计师需要根据实际情况来选择合适的公式。
最后,需要注意的是,注射模具设计尺寸计算是一个复杂的过程,设计师需要综合考虑产品的要求、材料的特性、模具的结构等多个因素,才能确定合适的尺寸。
第4章 塑料注射模设计 4.16气辅成型(第19讲)

Frozen Layer Gas Channel
塑料滞留区
N2 Gas
《塑料成型工艺与模具设计》
第4章 塑料注射模设计
《塑料成型工艺与模具设计》
第4章 塑料注射模设计
6、气辅成型的应用
3)同时具有薄壁和厚壁的复杂制件:如电视机壳、电脑打 印机外遮光板和汽车部件等。——将几个组装制件集成为单 一结构以降低制造成本。
《塑料成型工艺与模具设计》
第4章 塑料注射模设计
二、气道设计
1、气道设计基本原则 1)制品设计应先确定气体充填的厚壁部分结构,再用气道连 成网络。 管、杆形件:气体最好注入整个制件内部; 片状结构件:用加强筋和增厚通道来内置气道,以增强熔体 流动和提高制品刚度; 厚薄壁共存制品:气道应通过厚壁部分以避免缩痕和缩短冷 却时间。 2)气道尺寸要达到足以引导气 体注入 气道尺寸应明显大于相邻区域 壁厚(2~3倍壁厚)。
直 接 对 模 腔 注 气
第4章 塑料注射模设计
5、气体辅助注射成型(GAIM)的优点
气体辅助射出成型最多可减重50%; 缩短20%成型周期; 降低30%成本; 克服30%凹陷翘曲; 制品设计上可将厚壁及薄壁结合成同一产品中,不必强调 均匀壁厚;模具设计上可避免复杂之滑块机构。
《塑料成型工艺与模具设计》
《塑料成型工艺与模具设计》
Gas Channel
Polymer Melt
第4章 塑料注射模设计
4、气辅成型工艺过程控制
气辅成型工艺过程
保压冷却阶段:型腔充填 结束,保压冷却仍需注入气 体以补缩。 冷却定型阶段:保压冷却 直至定型后,可以减压回收 氮气。
Third Stage : End of Gas Injection
注塑成型工艺与模具设计

注塑成型工艺与模具设计注塑成型工艺是一种常用的塑料制造工艺,它通过将熔化的塑料材料注入模具中,使其冷却固化成型。
在注塑成型过程中,模具设计起着至关重要的作用,决定了最终产品的质量和性能。
本文将深入探讨注塑成型工艺与模具设计的相关内容。
注塑成型工艺包括了几个重要的步骤。
首先是原料的预处理,包括干燥和混合。
塑料材料在加工前需要进行干燥处理,以去除其中的湿气,以免对成型质量产生不良影响。
然后是熔化注塑,将预处理好的塑料材料加热至熔化状态,再通过注射机将熔化的塑料注入模具中。
接下来是冷却固化,注塑模具中的塑料在注射后会迅速冷却固化,形成所需的产品形状。
最后是脱模,将冷却固化的产品从模具中取出。
在注塑成型过程中,模具设计起着决定性的作用。
一个好的模具设计能够保证产品的尺寸精度、表面质量和结构完整性。
首先,模具设计要考虑产品的形状和尺寸要求,合理确定模具的结构和尺寸。
其次,模具设计要考虑产品的注塑工艺特点,确定合适的冷却系统和排气系统,以保证产品的质量和生产效率。
此外,模具设计还要考虑产品的脱模性能,即产品能否顺利脱离模具。
因此,在模具设计中,需要合理选择脱模斜度和表面处理方式,以减少脱模力和提高脱模效果。
注塑成型工艺与模具设计的关键在于如何解决塑料熔体的流动和冷却问题。
在注塑过程中,塑料熔体需要通过射嘴进入模具腔道,充填整个模具腔道,并冷却固化成型。
因此,流道设计是模具设计中的重要环节。
流道的设计要尽可能地短小粗大,以降低熔体的流动阻力和热损失。
同时,流道的位置和形状也要合理选择,以保证熔体在模具中的均匀充填和冷却。
在模具设计中,还需要考虑产品的浇口和排气系统。
浇口是塑料熔体进入模具腔道的通道,其位置和形状直接影响着熔体的充填情况和产品的质量。
排气系统是将模具腔道中的空气排出的通道,其位置和形状决定了空气是否能够有效排除,避免产生气泡和缺陷。
除了流道、浇口和排气系统的设计,模具设计中还需考虑产品的冷却系统。
塑料注射成型工艺及模具设计注射模成型部分的设计PPT课件

成型零部件的设计
❖ 成形零部件是决定塑件几何形状和尺寸的零件,主要包括 凹模、凸模、镶件、成形杆和成形环等
❖ 凹模和凸模的结构设计
整体式凹、凸模结构 组合式凹、凸模结构
➢ 整体嵌入式 ➢ 局部镶嵌式 ➢ 四壁拼合式
小型芯的结构设计
❖ 螺纹型环和螺纹型芯的结构设计
24
名词解释
❖ 凹模:亦称型腔,是成形塑件外表面的主要零件 ❖ 凸模:亦称型芯,是成形塑件内表面的主要零件 ❖ 成形杆:成形塑件上小孔的型芯 ❖ 螺纹型环:成形塑件上的外螺纹 ❖ 螺纹型芯:成形塑件上的内螺纹
这些零件需要运动并传力,因此,要求材料具有良好的机械性能, 有时还与塑料直接接触,还需注意其耐热性
❖ 支撑零部件
是模具中的受力件,要求材料具有足够的强度和刚度
为30~70MPa
❖ 充模时,塑料熔体对模具的冲刷以及脱模时塑料制品对模 具的刮磨,都将导致成形零件表面发生磨损
成形时带有玻璃纤维、玻璃粉、石英粉等硬质填料
❖ 模具在工作过程中,有时还会受到腐蚀作用
在高温下,有些塑料会出现局部分解而产生腐蚀性气体
37
模具常见的失效形式
❖ 塑性变形失效
模具局部产生塑性变形,常见于渗碳钢和碳素工具钢,表现为麻 点、起皱、局部塌陷等,产生的主要原因是成形零部件的强度低, 表面硬化层薄,或工作温度超过了其回火温度
35
塑料注射模具材料的选用
❖ 制造模具零部件的材料直接影响其寿命、加工成本及制品 的质量
❖ 选择模具材料的主要依据是模具的工作条件,结合技术和 经济两方面综合考虑
从经济角度出发,对于大批量生产的塑料制品,关心的是模具的 寿命,总是要选用较好的模具材料,并采取一定的热处理和表面 强化措施;对于小批量生产时,只要能满足成形的质量,可选择 价格低廉的模具材料
「叠层式注射模具设计与应用」

「叠层式注射模具设计与应用」叠层式注射模具是一种新型的注塑模具设计与应用方法,利用多层次叠加的的模具结构,可以同时完成多个零件的注塑成型,提高生产效率和产品质量。
本文将详细介绍叠层式注塑模具的设计原理、制造工艺以及应用领域。
一、叠层式注塑模具的设计原理叠层式注塑模具是将多个注塑模具叠加在一起,利用一个注塑机同时注射多个塑料零件。
每个模腔都独立设计,通过分别控制模温、冷却水路和射胶系统,保证每个零件可以独立成型。
叠层式注塑模具可以分为两种类型:平面叠层和立体叠层。
平面叠层是将多个平面模腔叠加在一起,从而实现多个平面零件的同时成型。
每个平面模腔都有自己独立的注射系统和冷却系统,可以根据零件的要求分别进行控制。
这种设计能够大大提高生产效率,减少生产时间和人力成本。
立体叠层则是将多个立体模腔叠加在一起,实现多个立体零件的同时成型。
每个立体模腔都有自己独立的注射系统和冷却系统,并且需要考虑零件在堆叠时的空间和位置关系。
这种设计在注塑成型中的应用更加广泛,能够满足多种复杂形状零件的要求。
二、叠层式注塑模具的制造工艺制造叠层式注塑模具需要考虑多个模腔的布局和排布,同时还需要设计合适的注射系统和冷却系统。
在制造过程中,需要使用高精度的加工设备和工艺,如数控加工中心、线切割机等。
具体的制造工艺如下:1.模腔布局设计:根据零件的形状和尺寸要求,确定模腔的位置和布局。
同时还需要考虑模腔之间的空间和位置关系,以确保在注塑过程中不会产生干涉和冲突。
2.模腔制造:根据设计要求,使用数控加工中心和线切割机等设备对模腔进行加工制造。
在加工过程中,需要保证模腔的尺寸和表面精度,以确保注塑成型的质量。
3.射胶系统设计:根据零件的形状和尺寸,设计合适的射胶系统。
射胶系统需要考虑注塑机的规格和特点,确保每个模腔都能够获得合适的注塑压力和速度。
4.冷却系统设计:根据零件的材料和尺寸,设计合适的冷却系统。
冷却系统需要保证每个模腔都能够获得均匀的冷却效果,提高注塑成型的效率和质量。
- 1、下载文档前请自行甄别文档内容的完整性,平台不提供额外的编辑、内容补充、找答案等附加服务。
- 2、"仅部分预览"的文档,不可在线预览部分如存在完整性等问题,可反馈申请退款(可完整预览的文档不适用该条件!)。
- 3、如文档侵犯您的权益,请联系客服反馈,我们会尽快为您处理(人工客服工作时间:9:00-18:30)。
注射成型模具的设计
注射成型模具的设计
一、模具设计要点及与注射机的关系。
<一>模具设计要点:
<1>熔体的流动情况:流动阴力,速度,引程,重新融合,排气。
<2>熔体冷却收缩与补缩。
<3>模具的冷却与加热。
<4>模具的相关尺寸与注射机关系。
<5>模具的总体结构与零部件的结构,考虑模具安装与加工强度,精度。
<二>模具与注塑机的关系:
注塑机的技术规范:类型,最大注射量,最大注射压力,最大锁模力、最大成型面积、最大最小模厚、最大开模引程、定注孔尺寸、嘴喷的球面半径、注射机动模板的顶出孔、机床模板安装螺钉孔或丁字槽的位置与尺寸。
1、类型: 卧式、立式、直角式。
2、最大注射量的选择。
注射机一次注射聚本乙烯的最大熔料的重量或容积的量为注射机公称注射量。
塑件十浇注流的总量=0.8 公称注射量
3、注射面积核定。
最大注射面积指模具分型面上允许的塑件最大投影面积. 作用于该面积上的型腔总压力小于注射机允许的锁模力,否则会产出溢料。
4、注射机引程与模具的关系。
Hmin ≤ H ≤ Hmax Hmax = Hmin + L
其中H--模具的闭合高度
Hmin--注射机最小闭合高度
Hmax--注射机最大闭合高度
L--螺杆可调长度
S ≥H1+H2+(5~10)--卧式立式注射机
其中H--脱模距
H--塑件高度(包括浇口长度)
S--注射杨允许开模引程
5、模具安装及顶出形式
可安装模具外形最大尺寸,取决于注射机模板尺寸和拉杆间距。
二、模具的设计程序
<一>塑件的技术要求:
用途,使用情况,工作要求,尺寸精度,粗糙度等小成型工艺性塑件设计原则,模具结构合理性等方面综合分析。
<二>结算塑件重量选择注射机的公称注射量,选择注射机,确定型腔数( 一套模具可成型不同的一套另件)。
<三>分析塑件确定成型方案
分型面,脱模方式,侧凹孔成型方法,浇注紧浇形式. 浇口位置,加热冷却系统及另件的加方法。
<四>绘制模具方案草图
初绘模具方案,并校验选注射机参数。
<五>计算
成型另件工作尺寸计算,受力另部件强度,刚度计算。
<六>画装配图
要求装配图要有尺寸(外形尺寸,特殊尺寸;定位圈尺寸)配合尺寸装配极限尺寸,技术编写时细表。
<七>画另件图
画如图形,注出尺寸,精度,粗糙度要求,,材料度要求.材料及热处理技术条件。
<八>穿核加工。