注射成型模具
模具成型分类
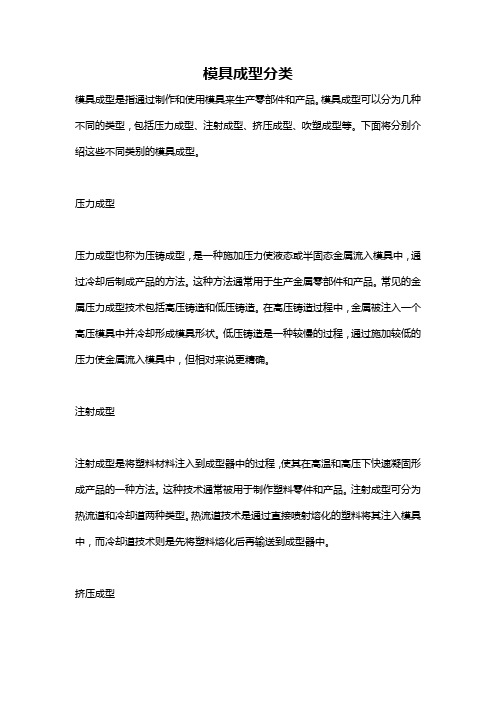
模具成型分类模具成型是指通过制作和使用模具来生产零部件和产品。
模具成型可以分为几种不同的类型,包括压力成型、注射成型、挤压成型、吹塑成型等。
下面将分别介绍这些不同类别的模具成型。
压力成型压力成型也称为压铸成型,是一种施加压力使液态或半固态金属流入模具中,通过冷却后制成产品的方法。
这种方法通常用于生产金属零部件和产品。
常见的金属压力成型技术包括高压铸造和低压铸造。
在高压铸造过程中,金属被注入一个高压模具中并冷却形成模具形状。
低压铸造是一种较慢的过程,通过施加较低的压力使金属流入模具中,但相对来说更精确。
注射成型注射成型是将塑料材料注入到成型器中的过程,使其在高温和高压下快速凝固形成产品的一种方法。
这种技术通常被用于制作塑料零件和产品。
注射成型可分为热流道和冷却道两种类型。
热流道技术是通过直接喷射熔化的塑料将其注入模具中,而冷却道技术则是先将塑料熔化后再输送到成型器中。
挤压成型挤压成型是一种通过将塑料材料推入模具中使其形成产品的方法。
这种技术通常被用于制作管状和长形塑料零件。
挤压成型可以分为单层挤压和多层挤压。
单层挤压是一种将熔化后的塑料材料输送至模具中的过程。
而多层挤压则是将多种材料层叠在一起,以使其形成更耐用的材料。
吹塑成型吹塑成型是通过在成型器中灌入熔化的塑料,然后用压缩空气将其吹成形状的方法。
这种技术常用于生产塑料瓶和其他小型塑料制品。
吹塑成型可以分为一次吹塑和两次吹塑。
一次吹塑是通过将新鲜塑料材料灌入到预定的形状中并加热使其膨胀。
两次吹塑是一种在预定形状和一些细节被制成后再次吹气的方法,以使产品完全形成所需形状。
总结模具成型是制造塑料、金属等各种材料制品的重要工艺之一,模具成型可分为压力成型、注射成型、挤压成型、吹塑成型等不同种类。
了解不同的成型方式有助于在选择制造工艺上做到更好的选择,避免错误选择而导致不必要的损失。
塑料注射模具知识点总结

概述塑料注射模具是用于制造塑料制品的一种装置,由模具基板、模具芯、注射系统、冷却系统、脱模系统等部分组成。
塑料注射模具制造是一项相对复杂的工艺,需要对材料、工艺、设计、加工等方面具有深入的了解和掌握。
本文将从材料、设计、加工、维护等方面综合介绍塑料注射模具的知识点。
一、塑料注射模具的材料1.1 模具基板材料模具基板是塑料注射模具的主要承载部分,需要具有高强度、耐磨损、耐腐蚀等特性。
常见的模具基板材料有P20、718、2738等。
P20材料具有良好的硬度和耐磨损性能,适合制作中小型模具;718材料具有高强度和硬度,适合制作大型模具;2738材料具有高镍合金特性,适合制作高精度模具。
1.2 模具芯材料模具芯是用于塑料制品内部结构的部分,需要具有高硬度、高精度、耐磨损等特性。
常见的模具芯材料有SKD61、S136等。
SKD61材料具有良好的热稳定性和硬度,适合制作高品质的模具芯;S136材料具有良好的耐腐蚀性和耐磨损性,适合制作高精度的模具芯。
1.3 注射系统材料注射系统是用于将熔融塑料材料注入模具腔内的部分,需要具有耐高温、耐腐蚀、高流动性等特性。
常见的注射系统材料有H13、H13W等。
H13材料具有良好的耐热性和抗氧化性,适合制作注射系统组件;H13W材料具有更高的硬度和耐磨损性,适合制作高性能的注射系统组件。
1.4 冷却系统材料冷却系统是用于控制模具温度的部分,需要具有良好的传热性能、耐腐蚀、高耐压等特性。
常见的冷却系统材料有铜合金、铝合金、不锈钢等。
铜合金具有良好的导热性和抗腐蚀性,适合制作冷却系统管道;铝合金具有较轻的重量和较高的导热性,适合制作冷却系统散热器;不锈钢具有较高的耐腐蚀性和耐压性,适合制作高性能的冷却系统组件。
1.5 脱模系统材料脱模系统是用于将成型塑料制品从模具中脱离的部分,需要具有良好的脱模性能、耐磨损、易维护等特性。
常见的脱模系统材料有冷作钢、硬质合金等。
冷作钢具有良好的硬度和耐磨损性,适合制作脱模系统零部件;硬质合金具有更高的硬度和耐磨损性,适合制作高性能的脱模系统零部件。
注射模具总结

注射模具总结引言注塑模具是注塑成型过程中的关键工具之一,其质量直接影响到产品的成型质量和生产效率。
本文将对注射模具进行总结,包括模具的定义、分类、制造工艺等方面,以帮助读者更好地了解注射模具。
何为注射模具注射模具是用于塑料注塑成型的专用模具,也称为注塑模具。
它由模具座(支架)、模具芯(浇注孔)、模具腔(成形孔)等部件组成。
注塑模具能够将熔化的塑料通过注射机注入到模具腔中,经过冷却固化后,得到所需形状的产品。
注射模具的分类根据注塑模具的结构和应用领域,可以将其分为以下几类:1.直线副模具:该类模具结构简单,适用于生产平面形状的产品。
2.斜线副模具:模具芯、模具腔的结构为斜面,多用于生产壁厚不均匀的产品。
3.寄生副模具:模具芯出现在模具腔的内部,通过模具座插入模具腔内注射成型,适用于细长形状的产品。
4.双色模具:该类模具可实现一次注塑成型,生产出颜色不同的产品。
5.复合模具:模具腔形状较复杂,需要多个注射机同时工作,用于生产多组件结构的产品。
6.热流道模具:通过热嘴将熔融塑料永远保持在熔融状态,可用于生产高要求的产品,如透明产品。
注射模具的制造工艺注射模具的制造工艺主要包括以下几个步骤:1.设计:根据产品的要求,设计注射模具的结构、尺寸和形状。
2.制作模具芯和模具腔:根据设计图纸,选用适当的材料,并通过数控机床进行切削加工,制作出模具芯和模具腔。
3.组装与调试:将模具芯和模具腔进行组装,并进行必要的调试工作,以保证模具正常使用。
4.热处理:对模具进行热处理,提高其硬度和耐磨性,以延长模具的使用寿命。
5.表面处理:对模具表面进行精细加工,以提高产品的光洁度和精度。
6.模具试模:在注射机上进行试模,调整模具腔和模具芯的位置和尺寸,以达到产品质量标准。
7.修整和保养:对模具进行定期的修整和保养工作,以保证模具的使用效果和寿命。
注射模具的优势和挑战注射模具作为一种关键工具,在塑料加工行业具有以下优势:•生产效率高:注射模具可以实现高速连续生产,提高生产效率。
注塑模具原理及过程

注塑模具原理及过程
注塑模具是一种用于注塑成型的工具,它的原理和过程如下:
原理:
注塑模具的原理是利用高压将熔化的塑料注入模具腔内,经过
冷却凝固后形成所需的塑料制品。
注塑模具通常由上模和下模组成,上模和下模之间的空腔就是所需塑料制品的形状。
在注塑过程中,
塑料粒子被加热熔化后,通过注射装置将熔化的塑料注入模具腔内,然后进行冷却,最终取出成型的塑料制品。
过程:
注塑成型的过程包括模具闭合、射料、压料、冷却、开模、脱
模等步骤。
首先,模具闭合,上模和下模合拢形成封闭的模腔。
然后,将塑料颗粒加热熔化,通过射料装置将熔化的塑料注入模具腔内。
接着,施加高压使塑料充填模具腔并保持一定的压力,以确保
塑料充分填充模具腔并排除气泡。
随后,进行冷却,让熔化的塑料
在模具内快速冷却凝固,形成所需的塑料制品。
最后,开模,取出
成型的塑料制品,进行脱模处理,清理模具,为下一次注塑做准备。
除了以上基本原理和过程外,注塑模具的设计、材料选择、加工工艺等方面也对注塑成型起着重要作用。
注塑模具的设计需要考虑产品的结构、形状、尺寸等因素,以及塑料材料的流动特性、收缩率等因素,保证成型品质。
模具材料通常选用优质的钢材或合金材料,以确保模具具有足够的硬度和耐磨性。
加工工艺包括数控加工、电火花加工、线切割加工等,以获得精密的模具零部件。
综上所述,注塑模具的原理和过程涉及多个方面的知识和技术,需要综合考虑各种因素,以确保注塑成型的高质量和高效率。
注射模具成型零件的设计

第四节 成型零件尺寸的确定
一、影响塑件尺寸的因素 成型收缩率的选择和成型收缩的波动引起的尺寸误差 成型零件的制造误差、组装误差及相对移动引起的误差; 成型零件脱模斜度引起的误差 成型零件磨损及化学腐蚀引起的误差 二、确定成型零件尺寸的原则
1.综合考虑以下因素,确定合适的塑料收缩率 塑件壁厚、形状及嵌件:壁厚较大、形状较复杂或有时嵌件取偏小值 熔料流向:与进料方向平行的尺寸取偏小值 浇口截面积:浇口截面积小的比大的收缩率大,应取偏大值 与浇口的距离:近的部位比远的部位收缩率小,应选较小值 型腔尺寸取小于平均收缩率的值,型芯尺寸取大于平均收缩率的值 2.据成型零件的性质决定各部分成型尺寸:图5-17 3.脱模斜度的取向:型腔尺寸以大端为准,脱模斜度向缩小方向取得;型
二、型腔壁厚和底板厚度的计算
1.注射过程中型腔所受的力
合模时的压应力;注射压力;保压压力;开模时的拉应力
2. 型腔壁厚和底板厚度计算的必要性:图5-7.8.9.10
型腔刚度不足时会产生弹性变形,型腔向外膨胀,影响塑件质量和尺寸 精度,并产生溢料、飞边
型腔强度不足时会产生塑型变形,可引起型腔永久变形甚至破裂
S刚
22.8 57 98.7 131 145 195 249
S强
35 71 106 131 141 177 212
结论
当圆形型腔内半径r=86mm和矩形型腔的长边L1=370mm时,按刚度和 强度分别算得的侧壁厚度相等。故取r=86mm和L1=370mm为临界值, 当小于该值时按强度计算,大于该值时按刚度计算
塑件螺纹为M20x2-6H/5g,6g,塑料收缩率为0.6%,计算螺纹型环和型芯的各部
分尺寸。
五、小直径螺纹型芯安装形式图5-24
注射成型工艺注射模成型零部件设计

05
注射模成型零部件设计优 化建议与展望
优化建议
优化浇口设计
选择合适的浇口位置和类型,以减少 浇口凝料和压力损失,提高成型效率
。
提高模具温度调控能力
采用高效冷却系统,控制模具温度 ,以减小成型周期和能耗。
优化模具排气设计
合理设计排气通道,避免气体滞留 和困气,确保成型过程顺利进行。
优化成型工艺参数
注射成型工艺可以实现大规模生 产,提高生产效率,降低生产成 本。
02
注射模成型零部件设计
注射模成型零部件材料选择
塑料材料
塑料是注射成型最常用的材料之一,具有成本低、易加 工、重量轻等优点。常见的塑料材料包括聚乙烯、聚丙 烯、聚氯乙烯等。
金属材料
金属材料在某些情况下也用于注射成型,例如精密零件 或高强度要求的应用。常见的金属材料包括铝、钢和成型的工艺,适用于制造连续性、长型材等产品。挤 出成型的工艺参数包括挤出压力、模具温度等。
03
注射模成型零部件性能要 求与检测方法
注射模成型零部件性能要求
强度要求
零部件必须能够承受一定的 压力和温度变化,以确保在 使用过程中不发生破裂或变 形。
耐腐蚀性要求
注塑机
注射成型工艺需要使用注塑机,注塑机是一种能够提供高温 、高压条件的塑料加工设备,能够将塑料原料熔融并注入模 具中。
注射成型工艺流程
原料准备
选择合适的塑料原 料,并进行干燥处 理,以保证制品的 质量。
模具准备
根据制品的要求, 设计并制造模具, 以保证制品的形状 和尺寸符合要求。
注射成型
将熔融的塑料原料 注入模具中,并保 压一定时间,以使 塑料原料充分填充 模具并形成制品。
复合材料
注射模具的基本结构与分类

三、带活动镶件的注射模
1-定模板 2-导柱 3活动镶件 4-型芯 5动模板 6-动模垫板 7-垫板 8-弹簧 9-推 杆 10-推杆固定板 11-推板 12-动模座板
四、带有侧向抽芯的注射模
1-楔紧块 2-斜导柱 3-侧型芯滑块 4-型 芯 5-型芯固定板 6动模垫板 7-垫块 8动模座板 9-推板 10-推杆固定板 11推杆 12-拉料杆 13导柱 14-动模板 15浇口套 16-定模座板 17定位圈
四、自动脱螺纹的注射模
1-螺纹型芯 2-模脚 3动模垫板 4-定距螺钉 5-动模板 6-衬套 7定 模板 8-注射机开合模 丝杠
工作原理:
塑件带有内螺纹或外螺纹须自动脱模时,在 模具中需要设置可以旋转的螺纹型芯或者型环。 通过注射机的往复运动或旋转运动,或者设置专 门的驱动(如电动机或液压马达等)和传动机构, 带动螺纹型芯者型环转动,使塑件脱出。 开模时,A-A面先分开,同时,螺纹型芯1在 随着注射机开合模丝杆8的后退中自动旋转,此时, 螺纹塑件由于定模板7的止转作用并不移动,仍留 在型腔内。当A-A面分开一段距离,即螺纹型芯1 在塑件内还有最后一牙时,定距螺钉4拉动动模板 5,使模具沿B-B打开,此时,塑件随型芯一道离 开定模型腔,然后从B-B分型面两侧的空间取出。
六、推出机构设在定模一侧的注射模
1-动模座板 2-垫板 3-定模垫板 4-成型 镶件 5、7-螺钉 6动 模板 8-脱模板 9-拉 板 10-定模板 11-定 模座板 12型芯 13导 柱
工作原理:
为便于注射机锁模系统的顶出装置工作,模 具开模后,塑件一般留在动模一侧,模具脱模机 构也设置在动模一侧。有时由于塑件的特殊要求 或者形状的限制,开模后塑件可能留在定模一侧, 这时就需要在定模一侧设置脱模机构。定模一侧 的脱模机构一般是采用拉板、拉杆或者链条与动 模相连。。 开模后,塑件紧包在凸模11 上,塑件留在了 定模一侧,当动模左移一定距离,拉板8 通过定 距螺钉6 带动推件板7 将塑件从凸模中脱出。
项目7 注射模具结构类型
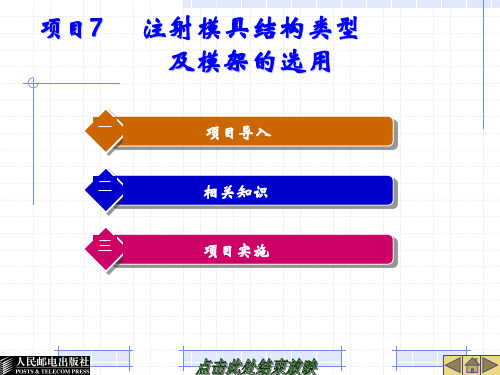
单分型面注射模、双分型面注射模、带侧向分型与抽芯机构的注射模、单 单分型面注射模、双分型面注射模、带侧向分型与抽芯机构的注射模、 多型腔注射模、 型腔注射模 、多型腔注射模、自动卸螺纹注射模 、无流道注射模等
1.注射模具的分类
按浇注系统结构形式可分: (3 )按浇注系统结构形式可分:
普通浇注系统注射模、 普通浇注系统注射模、热流道浇注系统注射模
(三)标准模架的选用
注射模具由成型零部件和结构零部件组成。 注射模具由成型零部件和结构零部件组成。结构零部件部分包括注射 成型零部件和结构零部件组成 模的标准模架、注射模的合模导向机构、支承零部件等。 模的标准模架、注射模的合模导向机构、支承零部件等。
我国已颁布和实施的塑料模国家标准有以下几种:
① ② ③ ④ ⑤ ⑥ ⑦ 塑料注射模具零件GB 4169—1984; 塑料注射模具零件技术条件 GB 4170—1984; 塑料成型模具术语 GB 8846—1988; 塑料注射模具技术条件 GB/T 12554—1990; 塑料注射模大型模架 GB/T12555—1990; 塑料注射模中小型模架及技术条件 GB/T12556—1990 ; 塑料注射模模架及技术条件 GB/T12556—2006 。
(4) 按塑料性质可分为: ) 按塑料性质可分为:
塑料成型模具分类及特点

置于中空制品吹塑模 ↓
管坯中心通压缩空气 ↓
吹胀(贴紧模具吹塑
六、真空或压缩空气成型 热塑性片材的热成型
用压缩空气吹成或用真空吸 成盘状制件或浅凹壳体容器
预制片材压紧在模具周边上 ↓
加热软化 ↓
在靠近模具的一面抽成真空 或反面施加压缩空气 ↓ 成型
七、其它
热塑件塑料:模具需同时具有加热和冷却两种功能 塑料加入型腔→逐渐加热、施压→融化充模→冷却至热 变形温度以下→开模取件(成型周期长,只适于对制品 有特殊要求的场合)
2.特点
优点: (1)易成型,操作方便 (2)模具和设备比注射成型投资少 (3)用于加工纤维塑料,塑件的强度高,特别适用于流
动性差的塑料和大型制品
Bakelite (also called catalin, Patent No. 942,699) is a dense synthetic polymer (a phenolic resin) that was used to make jewelry, game pieces, engine parts, radio boxes, switches, and many, many other objects. Bakelite was the first industrial thermoset plastic (a material that does not change its shape after being mixed and heated). Bakelite plastic is made from carbolic acid (phenol) and formaldehyde, which are mixed, heated, and then either molded or extruded into the desired shape. The Nobel Prize winning German chemist Adolf von Baeyer had experimented with this material in 1872, but did not complete its development or see its potential.
注射成型生产工艺过程
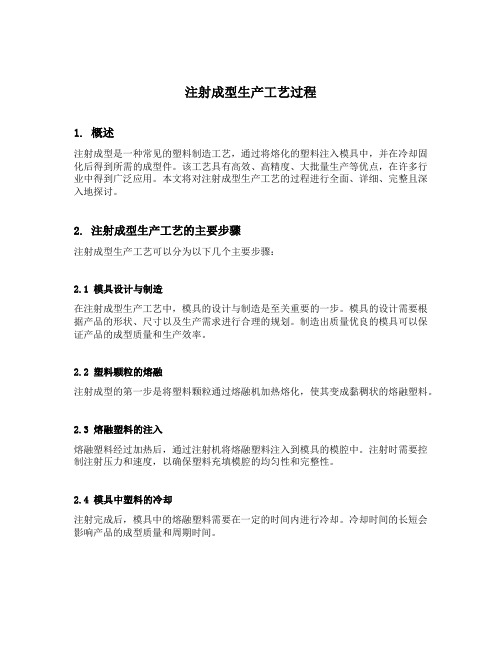
注射成型生产工艺过程1. 概述注射成型是一种常见的塑料制造工艺,通过将熔化的塑料注入模具中,并在冷却固化后得到所需的成型件。
该工艺具有高效、高精度、大批量生产等优点,在许多行业中得到广泛应用。
本文将对注射成型生产工艺的过程进行全面、详细、完整且深入地探讨。
2. 注射成型生产工艺的主要步骤注射成型生产工艺可以分为以下几个主要步骤:2.1 模具设计与制造在注射成型生产工艺中,模具的设计与制造是至关重要的一步。
模具的设计需要根据产品的形状、尺寸以及生产需求进行合理的规划。
制造出质量优良的模具可以保证产品的成型质量和生产效率。
2.2 塑料颗粒的熔融注射成型的第一步是将塑料颗粒通过熔融机加热熔化,使其变成黏稠状的熔融塑料。
2.3 熔融塑料的注入熔融塑料经过加热后,通过注射机将熔融塑料注入到模具的模腔中。
注射时需要控制注射压力和速度,以确保塑料充填模腔的均匀性和完整性。
2.4 模具中塑料的冷却注射完成后,模具中的熔融塑料需要在一定的时间内进行冷却。
冷却时间的长短会影响产品的成型质量和周期时间。
2.5 成品的脱模与后处理冷却后的塑料成型件需要从模具中脱模。
脱模过程需要小心操作,以防止产品损坏。
脱模完成后,还需要对产品进行后处理,如去除余边、修整表面等。
3. 注射成型生产工艺的关键技术和要点在注射成型生产工艺中,有一些关键技术和要点需要特别注意,以确保产品质量和生产效率。
3.1 模具设计和制造技术模具设计应根据产品的形状、尺寸和需求进行合理规划,模具材料选择应具备一定的硬度和耐磨性能。
注射成型模具制造还需要采用先进的加工设备和工艺,以提高模具的精度和寿命。
3.2 塑料材料的选择不同的塑料材料具有不同的性能和特点,选择合适的塑料材料对产品的质量有着至关重要的影响。
需要考虑塑料的耐热性、流动性、收缩率等因素。
3.3 注射工艺参数的控制在注射成型过程中,需要合理控制注射压力、注射速度、注射时间等参数,以保证塑料充填模腔的均匀性和完整性。
注射成型原理
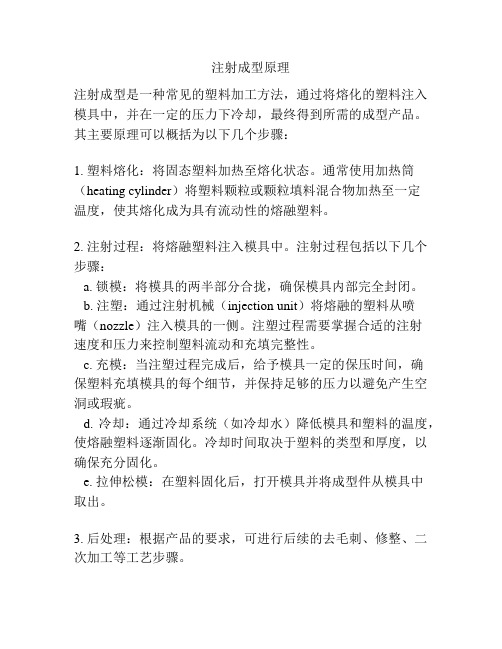
注射成型原理
注射成型是一种常见的塑料加工方法,通过将熔化的塑料注入模具中,并在一定的压力下冷却,最终得到所需的成型产品。
其主要原理可以概括为以下几个步骤:
1. 塑料熔化:将固态塑料加热至熔化状态。
通常使用加热筒(heating cylinder)将塑料颗粒或颗粒填料混合物加热至一定
温度,使其熔化成为具有流动性的熔融塑料。
2. 注射过程:将熔融塑料注入模具中。
注射过程包括以下几个步骤:
a. 锁模:将模具的两半部分合拢,确保模具内部完全封闭。
b. 注塑:通过注射机械(injection unit)将熔融的塑料从喷
嘴(nozzle)注入模具的一侧。
注塑过程需要掌握合适的注射
速度和压力来控制塑料流动和充填完整性。
c. 充模:当注塑过程完成后,给予模具一定的保压时间,确
保塑料充填模具的每个细节,并保持足够的压力以避免产生空洞或瑕疵。
d. 冷却:通过冷却系统(如冷却水)降低模具和塑料的温度,使熔融塑料逐渐固化。
冷却时间取决于塑料的类型和厚度,以确保充分固化。
e. 拉伸松模:在塑料固化后,打开模具并将成型件从模具中
取出。
3. 后处理:根据产品的要求,可进行后续的去毛刺、修整、二次加工等工艺步骤。
总的来说,注射成型原理是通过将熔融塑料注入模具中,利用模具的形状和压力来实现塑料的充填、冷却和固化,从而得到所需的成型产品。
注射成型技术广泛应用于塑料制品的生产,具有生产效率高、成型精度高等优点。
塑料模具拆装实验与注射成型实验
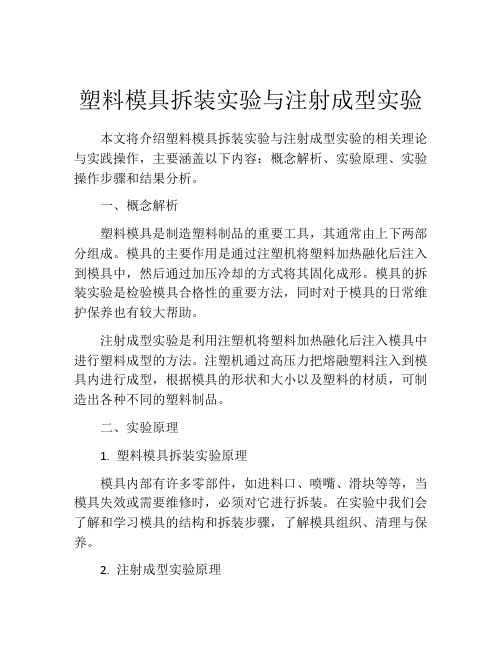
塑料模具拆装实验与注射成型实验本文将介绍塑料模具拆装实验与注射成型实验的相关理论与实践操作,主要涵盖以下内容:概念解析、实验原理、实验操作步骤和结果分析。
一、概念解析塑料模具是制造塑料制品的重要工具,其通常由上下两部分组成。
模具的主要作用是通过注塑机将塑料加热融化后注入到模具中,然后通过加压冷却的方式将其固化成形。
模具的拆装实验是检验模具合格性的重要方法,同时对于模具的日常维护保养也有较大帮助。
注射成型实验是利用注塑机将塑料加热融化后注入模具中进行塑料成型的方法。
注塑机通过高压力把熔融塑料注入到模具内进行成型,根据模具的形状和大小以及塑料的材质,可制造出各种不同的塑料制品。
二、实验原理1. 塑料模具拆装实验原理模具内部有许多零部件,如进料口、喷嘴、滑块等等,当模具失效或需要维修时,必须对它进行拆装。
在实验中我们会了解和学习模具的结构和拆装步骤,了解模具组织、清理与保养。
2. 注射成型实验原理在注射成型实验中,需要将制定好的工艺参数输入注塑机中,并进行调试。
当注塑机加热器加热完毕,热塑性塑料在模具的加压作用下形成形态、大小等各方面都比较准确的产品。
实验主要考察注塑机的操作技能和对成品质量的要求,包括温度调节、注射速度调节、压力调节、第一件试产检查、尺寸测量等操作,根据实验结果分析问题,并及时解决。
三、实验步骤1. 塑料模具拆装实验步骤第一步:对模具进行查看,保证模具无任何堵塞、老化、损坏等缺陷。
第二步:清除模具内残留的塑料,确保全部清理干净。
第三步:取消固定螺钉,拆下模具的活动部分。
第四步:对模具内部零部件进行清理,如滚筒、喷嘴等。
第五步:检查模具贯通性,在必要的地方进行打磨加工。
第六步:进行模具组合,之后再测试使用效果。
2. 注射成型实验步骤第一步:检查注塑机的安全保护装置。
第二步:调节注塑机的加热器,确定合适温度。
第三步:确认注塑机的压力、速度、时间等参数。
第四步:将塑料制品放入料斗中。
第五步:调节注塑机的操作手柄,开始成型。
注塑模具种类及概述

<一> 二板模具(一 次分型模具)的特点:
一般是在分型面处分开 成定模板和动模板。
六角螺丝 顶夹板
导套
型腔板 导向锁(导柱) 型芯板
回锁(弹弓) 隔片 卸器保护板 卸板 底夹板 六角螺丝
1、 成型后将注塑件和浇口切断并进行加工(如:边浇口、直 浇口);
2、 结构简单,便于使用; 3、 适合于产品自动落下(潜伏式浇口,不需后加工); 4、 故障少,价格便宜。
是指为满足模具结构上的要求而设置的零件(如: 固定板、动/定模板、撑头、支承板及连接螺钉等)。
A、二板模具(侧浇口)
结构图
胶件顶出图
三板模具(针孔型浇口)
结构图
胶件顶出图
结构图 出图
胶件顶
斜导柱模具(边浇口、推板顶出)
D、绞牙抽芯模具(直浇口)
结构图 胶件顶出图
三、注塑模具的分类
注塑模的分类方法很多,按其所用注塑机的类型 可分为卧式注塑机用注塑模、立式注塑机用注塑 模、角式注塑机用注塑模及双色注塑机用注塑模 等;按模具的型腔数目可分为单型腔和多型腔注 塑模;按分型面的数量可分为单分型面和双分型 面或多分型面注塑模;按浇注系统的形式可分为 普通浇注系统和热流道浇注系统注塑模;另外还 有气辅注塑模具、蒸汽模具、重叠式模具(叠 模)。
6、模温调节系统 ★
为了满足注射成型工艺对模具温度的要求,需要有模 温调节系统(如:冷却水、热水、热油、蒸汽、冷风及 电热系统等)对模具温度进行调节的装置。
7、排气系统
为了将模腔内的气体顺利排出,常在模具分型面处开 设排气槽,许多模具的推杆或其它活动部件(如:滑块) 之间的板
导套
流道板 导向锁 型腔板 型芯板 回锁(弹弓) 隔片 卸器保护板 卸板 底夹板
注射成型工艺
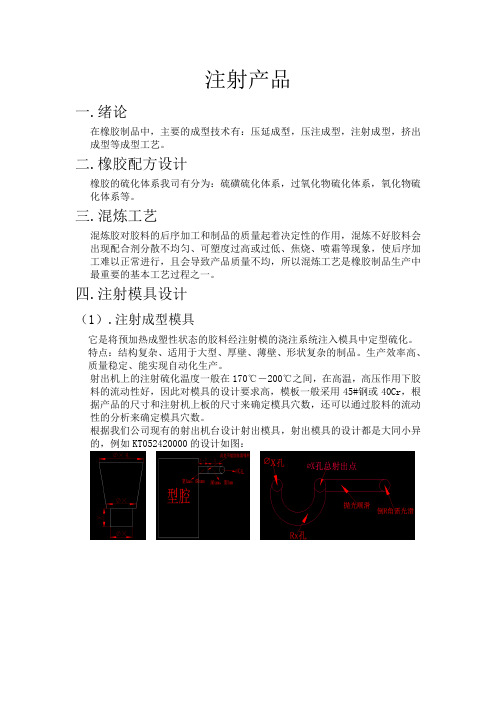
注射产品一.绪论在橡胶制品中,主要的成型技术有:压延成型,压注成型,注射成型,挤出成型等成型工艺。
二.橡胶配方设计橡胶的硫化体系我司有分为:硫磺硫化体系,过氧化物硫化体系,氧化物硫化体系等。
三.混炼工艺混炼胶对胶料的后序加工和制品的质量起着决定性的作用,混炼不好胶料会出现配合剂分散不均匀、可塑度过高或过低、焦烧、喷霜等现象,使后序加工难以正常进行,且会导致产品质量不均,所以混炼工艺是橡胶制品生产中最重要的基本工艺过程之一。
四.注射模具设计(1).注射成型模具它是将预加热成塑性状态的胶料经注射模的浇注系统注入模具中定型硫化。
特点:结构复杂、适用于大型、厚壁、薄壁、形状复杂的制品。
生产效率高、质量稳定、能实现自动化生产。
射出机上的注射硫化温度一般在170℃-200℃之间,在高温,高压作用下胶料的流动性好,因此对模具的设计要求高,模板一般采用45#钢或40Cr ,根据产品的尺寸和注射机上板的尺寸来确定模具穴数,还可以通过胶料的流动性的分析来确定模具穴数。
根据我们公司现有的射出机台设计射出模具,射出模具的设计都是大同小异的,例如KT052420000的设计如图:(2).胶料收缩率1.硫化温度越高(超过正硫化温度),收缩率越大。
在一般情况下,温度每升高10°C,其收缩率就增加0.1%~0.2%。
2.半成品胶料量越多,制成品致密度越高,其收缩率越小。
3.胶料的可塑性越大,收缩率越小;胶料的硬度越高,收缩率越小。
(高硬度例外,据实验测定,胶料硬度超过邵氏90度以上,其收缩率有上升的趋势)4.填充剂用量越多,收缩率越小;含胶量越高,收缩率越大。
5.多型腔模具中,中间模腔压出制品的收缩率比边沿模腔制品的收缩率略小。
6.注射法制品比模压法制品的收缩率小。
7.薄形制品(断面厚度小于3mm)比厚制品(10mm以上)的收缩率大0.2%~0.6%等。
五.注射硫化工艺橡胶注射成型工艺是一种把胶料直接从机筒注入模性硫化的生产方法,注射硫化特点是胶料温度比较均匀一致,硫化速度快,刻加工大多数的模压产品。
注射成型模具结构与注射机.ppt
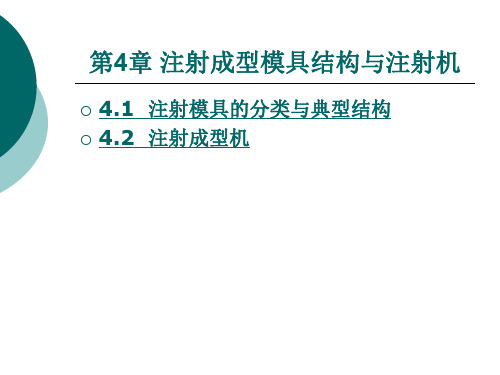
上一页 下一页 返回
4.2 注射成型机
2.合模装置 合模装置的作用主要有以下三个方面: 实现模具的可靠开合动作和必要的行程; 在注射和保压时,提供足够的锁模力; 开模时,提供顶出制件的顶出力及相应的行程。 合模装置主要由定模固定板、动模固定板、移动模板、液压
下一页 返回
4.1 注射模具的分类与典型结构
4.1.2 注射模的典型结构
根据模具中各个部件的不同作用,一副注射模可以分成以下 8个部分,模具中各零部件的作用如下。
(1)成型零部件赋予成型材料形状和尺寸的零件。通常由型 芯、凹模或型腔以及螺纹型芯或型环、镶块等构成。
(2)浇注系统将塑料熔体由注射机喷嘴引向闭合的模腔的通 道。通常由主流道、分流道、浇口和冷料井组成。
程时,注射装置所能给出的最大注出量,它是注射机的主要 参数之一,单位为g或cm3。注射量标志厂注射机的注射能 力,反映厂机器能生产制件的最大质量或体积。 注射量有两种表示法,一种是以加工PS原料为标准(密度为 1.05g/cm3,用注射出熔体的质量(g)表示。加工其他物 料时,应进行密度换算;另一种方法是采用注射容量表示, 即用一次注出熔体的容积(cm3 )表示。
(8)其他零部件如支撑、固定零件,定位或限位零件等。
上一页 返回
4.2 注射成型机
4.2.1 结构组成
注射成型机通常由注射装置、合模装置、液压传动系统、电 器控制系统等组成,如图4-2所示。注射装置能使塑料均匀 地塑化成熔融状态,并以足够的速度和压力将一定量的熔体 注射进模具型腔。合模装置也称锁模装置,用于保证注射模 具可靠闭合,实现模具开、合动作以及顶出制件。液压和电 器控制系统保证注射机按预定工艺过程的要求(如压力、温度、 速度和时间)和动作程序准确、有效地工作。
注塑模的工作原理
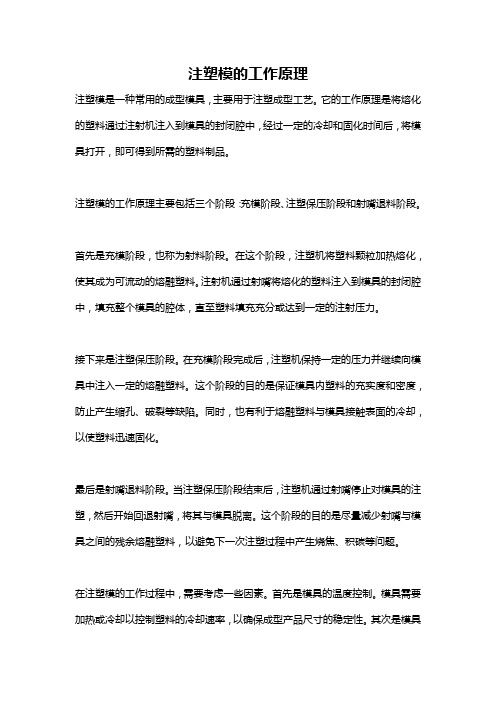
注塑模的工作原理注塑模是一种常用的成型模具,主要用于注塑成型工艺。
它的工作原理是将熔化的塑料通过注射机注入到模具的封闭腔中,经过一定的冷却和固化时间后,将模具打开,即可得到所需的塑料制品。
注塑模的工作原理主要包括三个阶段:充模阶段、注塑保压阶段和射嘴退料阶段。
首先是充模阶段,也称为射料阶段。
在这个阶段,注塑机将塑料颗粒加热熔化,使其成为可流动的熔融塑料。
注射机通过射嘴将熔化的塑料注入到模具的封闭腔中,填充整个模具的腔体,直至塑料填充充分或达到一定的注射压力。
接下来是注塑保压阶段。
在充模阶段完成后,注塑机保持一定的压力并继续向模具中注入一定的熔融塑料。
这个阶段的目的是保证模具内塑料的充实度和密度,防止产生缩孔、破裂等缺陷。
同时,也有利于熔融塑料与模具接触表面的冷却,以使塑料迅速固化。
最后是射嘴退料阶段。
当注塑保压阶段结束后,注塑机通过射嘴停止对模具的注塑,然后开始回退射嘴,将其与模具脱离。
这个阶段的目的是尽量减少射嘴与模具之间的残余熔融塑料,以避免下一次注塑过程中产生烧焦、积碳等问题。
在注塑模的工作过程中,需要考虑一些因素。
首先是模具的温度控制。
模具需要加热或冷却以控制塑料的冷却速率,以确保成型产品尺寸的稳定性。
其次是模具的设计和精度要求。
模具的设计应根据产品的形状和尺寸要求进行合理布置,同时也需要注意模具的加工精度和表面质量,以确保成品的质量。
最后是模具的选材。
模具需要选择具有良好热传导性能、高硬度、耐磨损等特性的材料,以提高模具的使用寿命和成型效果。
总之,注塑模是利用注射机将熔化的塑料注入到模具的封闭腔中,经过冷却和固化,最后取出模具得到所需的塑料制品的一种成型模具。
它的工作原理包括充模阶段、注塑保压阶段和射嘴退料阶段。
在模具的选择、设计和加工过程中需要考虑多种因素,以确保成品的质量和模具的使用寿命。
- 1、下载文档前请自行甄别文档内容的完整性,平台不提供额外的编辑、内容补充、找答案等附加服务。
- 2、"仅部分预览"的文档,不可在线预览部分如存在完整性等问题,可反馈申请退款(可完整预览的文档不适用该条件!)。
- 3、如文档侵犯您的权益,请联系客服反馈,我们会尽快为您处理(人工客服工作时间:9:00-18:30)。
➢ 其它时间则与生产过程是否连续化和自动化以及连续化 和自动化的程度等有关。
资料仅供参考,不当之处,请联系改正。
8.1注射成型原理及工艺特点
压力
➢ 注塑过程中压力包括塑化压力和注射压力两种, 并直接影响塑料的塑化和制品质量。 1、塑化压力:(背压)采用螺杆式注射机时, 螺杆顶部熔料在螺杆转动后退时所受到的压力 称为塑化压力,亦称背压。这种压力的大小是 可以通过液压系统中的溢流阀来调整的。
重点
资料仅供参考,不当之处,请联系改正。
典型注射模具的结构组成 不同类型的注射模具结构特点 浇注系统的设计原则 分型面的选取 型腔尺寸的计算 推出机构的类型及动作原理 推出结构的设计原则 抽芯机构的结构、设计原则和动作原理 冷却水道的结构设计和计算 注射模具设计程序
资料仅供参考,不当之处,请联系改正。
资料仅供参考,不当之处,请联系改正。
8.1注射成型原理及工艺特点
时间(成形周期)
➢ 完成一次注射模塑过程所需的时间称成型周期, 也称模塑周期。
➢ 成型周期直接影响劳动生产率和设备利用率。 因此,在生产过程中,应在保证质量的前提下,尽 量缩短成型周期中各个有关时间
资料仅供参考,不当之处,请联系改正。
资料仅供参考,不当之处,请联系改正。
8.2注射成型模具的分类及结构组成
资料仅供参考,不当之处,请联系改正。
注射成型模具的基本结构
1、浇注系统 2、成型部件 3、导向及定位部件 4、推出系统
5、温控系统 6、排气系统 7、侧抽芯机构 8、模架
资料仅供参考,不当之处,请联系改正。
注射成型模具的基本类型
➢ 温度分布一般遵循前高后低的原则,即料筒后 端温度最低,喷嘴处前端温度最高。
资料仅供参考,不当之处,请联系改正。
8.1注射成型原理及工艺特点
(2)喷嘴温度
➢ 喷嘴温度通常是略低于料筒最高温度的,这是 为了防止熔料在直通式喷嘴可能发生的"流涎 现象"。喷嘴温度也不能过低,否则将会造成 熔料的早凝而将喷嘴堵塞,或者由于早凝料注 入模腔而影响制品的性能
8.1注射成型原理及工艺特点
注射成型原理
➢ 又称为注塑成型 ➢ 塑化:成型时,粒状的塑料被连续输入到注射
成型机料筒中受热并逐渐熔融,称为黏性流动 状态; ➢ 注射充模:料筒中的螺杆或柱塞将塑料熔体推 到料筒端部,通过料筒端部的喷嘴和模具的浇 注系统注入闭合的模具型腔中; ➢ 充满后经过保压、冷却,固化成型; ➢ 然后开模并由模具推出装置推出制件。
➢ 一般操作中,塑化压力的决定应在保证制品质 量优良的前提下越低越好,其具体数值是随所 用的塑料的品种而异的,但通常很少超过 20MPa。
资料仅供参考,不当之处,请联系改正。
8.1注射成型原理及工艺特点
压力
➢ 2、注射压力:在当前生产中,几乎所有的注 射机的注射压力都是以柱塞或螺杆顶部对塑料 所施的压力(由油路压力换算来的)为准的。 注射压力在注塑成型中所起的作用是,克服塑 料从料筒流向型腔的流动阻力,给予熔料充模 的速率以及对熔料进行压实。
资料仅供参考,不当之处,请联系改正。
资料仅供参考,不当之处,请联系改正。
8.1注射成型原理及工艺特点
注射成型工艺条件
➢温度 ➢压力 ➢作用时间
资料仅供参考,不当之处,请联系改正。
8.1注射成型原理及工艺特点
温度
➢ 注射模塑过程需要控制的温度有料筒温度,喷 嘴温度和模具温度等。前两种温度主要影响塑 料的塑化和流动,而后一种温度主要是影响塑 料的流动和冷却。
主要内容
资料仅供参考,不当之处,请联系改正。
注射成形原理及工艺特点 注射模的分类及结构组成 分型面 浇注系统 成形零件的设计 机构设计 注射模的典型结构 注射模设计
资料仅供参考,不当之处,请联系改正。
基本要求与基本知识点
掌握注射模类型与结构组成。 掌握分型面的选取原则。 掌握普通浇注系统的设计。 掌握成型零部件的设计。 掌握推出机构的设计。 掌握侧向分型与抽芯机构的设计。 掌握顺序脱模机构的设计。 掌握冷却系统的设计。
8.1注射成型原理及工艺特点
时间(成形周期)
➢ 型周期
➢ 注射时间
➢ 模内冷却时 间
➢ 充模时间 ➢ 保压时间
➢ 其他时间
8.1注射成型原理及工艺特点 资料仅供参考,不当之处,请联系改正。
时间(成形周期)
➢ 充模时间反比于充模速率, 一般约为3-5秒。
➢ 保压时间就是对型腔内塑料的压力时间, 所占的比例较大, 一般约为20-120秒(特厚制件可高达5~10分钟)。保压时 间依赖于料温,模温以及主流道和浇口的大小。如果主流 道和浇口的尺寸以及工艺条件都是正常的,通常以得出制 品收缩率波动范围最小的压力值为准。
资料仅供参考,不当之处,请联系改正。
8.1注射成型原理及工艺特点
(1)料筒温度
➢ 每一种塑料都具有不同的流动温度,同一种塑 料,由于来源或牌号不同,其流动温度及分解 温度是有差别的,这是由于平均分子量和分子 量分布不同所致,塑料在不同类型的注射机内 的塑化过程也是不同的,因而选择料筒温度也 不相同。
▪ 按所成型的塑料制品材料分,可分为热塑性塑料 注射模和热固性塑料注射模。
▪ 按注射模的整体结构分,可分为单分型面注射模、 双分型面注射模、多分型面注射模、垂直分型面 注射模、有侧面分型和抽芯结构的注射模、定模 有定距推板结构的注射模、直角注射成型机上用 的专用注射模、有活动镶件的注射模等。
资料仅供参考,不当之处,请联系改正。
8.1注射成型原理及工艺特点
(3)模具温度
➢ 模具温度对制品的内在性能和表观质量影响很 大。模具温度的高,塑料的流动性就好,塑件 的密度和结晶度就会提高,但塑件的收缩率和 塑件脱模后翘曲变形会增加,塑件的冷却时间 会,生产率下降。
➢ 模具温度的高低决定于塑料结晶性的有无、制 品的尺寸与结构、性能要求,以及其它工艺条 件(熔料温度、注射速度及注射压力、模塑周 期等)。