车刀刃磨水平的高低直接关系到产品的生产效率
浅谈车工实习中的车刀刃磨

浅谈车工实习中的车刀刃磨作者:高贺来源:《卷宗》2016年第11期摘要:基本的理论知识是刃磨车刀的基础;掌握车刀的类型和合理选择砂轮是正确刃磨车刀的前提;合理的刃磨方法是保证工件加工质量、提高生产效率,延长刀具使用寿命,提高操作技能的有效途径。
文章论述了普通车刀刃磨的方法步骤及注意事项。
关键字:外圆车刀;刃磨方法;砂轮传统的高职院校机械类专业学生对车刀的理论知识是在”金属切削机床”课以课堂教学为主的情况下认知的,而当进行机械加工实训时,学生课堂所学的理论知识又无法直接运用到实际的车刀刃磨上,从而使实训指导老师又要从头讲起。
车刀的刃磨教学是机械加工实习教学中非常重要的一环,学生对车刀刃磨教学存在害怕和恐惧心理,老师怕学生出安全事故,所以目前有部分院校把学生刃磨车刀这一重要的环节删了。
而我们基于长期教学改革实践与探索,研究学生磨刀害怕和恐惧的心理,以学生的角度分析了车刀刃磨的形成,让学生在愉快的心情中进行车刀刃磨技能训练,在此基础上,阐述了车刀的种类及刃磨方法。
我们通过机加工技能实训让学生认识到车刀刃磨的重要性,合理指导学生掌握好典型车刀的刃磨技术,并及时对学生刃磨车刀进行评价检查。
俗话说“磨刀不误砍柴功”,对车削加工来说是“三分技术,七分刀具。
”由此可见磨刀在车工实习中的重要性,车刀的刃磨质量直接影响车削的质量和效率。
但是在实习教学中存在着学生不会磨、不敢磨、不愿意磨刀的问题。
学生还存在着应付心理,对车刀的刃磨要求不高,甚至有的学生都不自己磨刀。
没有好的车刀,就车不出理想的工件。
针对当前实习中存在的问题,迫切需要相应的措施解决。
下面本人从以下几个方面阐述车刀在刃磨过程中需要掌握的刃磨方法。
1 掌握磨刀要领,解决刃磨难题车刀的刃磨要求操作者需要熟悉相关理论知识和刃磨原理,熟练掌握刃磨方法及操作技巧。
为便于初学者尽快熟悉和记忆车刀刃磨的概念、方法与技巧,让学生熟悉下面的要领,磨出好用的车刀。
1.常用车刀种类和材料,砂轮的选用车刀按加工过程中的用途不同,通常把车刀分为外圆车刀、内孔车刀、螺纹车刀和切断刀;车刀刃形分为三种,有直线形、曲线形和复合形;车刀材料种类多,常用的有碳钢氧化铝砂轮和硬质合金碳化硅砂轮,根据车刀材料选用不同的砂轮,氧化铝砂轮多呈白色,它的磨粒韧性好、比较锋利,硬度低,自锐性好,主要用于刃磨高速钢车刀和硬质合金车刀的刀体部分;碳化硅砂轮多呈绿色,其磨粒的硬度高、刃口锋利,但其脆性大,主要用于刃磨硬质合金车刀。
车刀的刃磨实习教学探讨
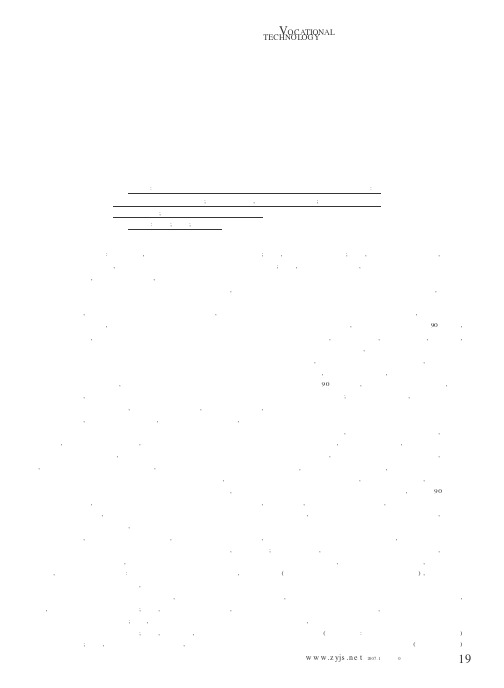
摘要:车刀的刃磨教学是车工实习教学中非常重要的一环。
刃磨教学包括:让学生认识车刀刃磨的重要性;合理设置课题,统筹安排实习进程;指导学生把握好典型车刀的刃磨;及时进行刃磨车刀的评价检查。
关键词:车刀;刃磨;实习教学V OCATIONAL TECHNOLOGY z yj 江苏施亚斌车刀的刃磨实习教学探讨职业技术车削加工有句行话:“三分手艺,七分刀具。
”“七分刀具”是指车刀刃磨的角度非常关键,它直接影响到产品质量的优劣和生产效率的高低。
因此,在车工实习教学中,车刀的刃磨一直是教学中的重点和难点。
但是很多学生一开始并不能正确的理解这句话,因为他们尚未认识到车刀刃磨的重要性。
这样的认识导致了部分学生在实习结束前,仍然不能磨出一把合乎使用要求的车刀,以至于不能顺利完成实习任务,直接影响了学生将来就业后的独立操作。
因此在实习过程中,指导学生顺利完成车刀的刃磨是车工实习教学中非常重要的一环。
一、让学生认识车刀刃磨的重要性车工实习主要包括车床操纵、刀具刃磨、量具使用三方面的内容。
其中刀具刃磨贯穿始终,是学生必须掌握的一项基本技能。
教师在设置课题时,通常将车床操纵与刀具刃磨结合在一起让学生进行练习。
但在练习的过程中,由于砂轮间灰尘较多,刀具刃磨的自动化程度不高,刀具角度不易控制等,学生对磨刀的兴趣不高,有些学生甚至故意逃避这样的练习。
要提高学生对刀具刃磨练习的积极性,克服其怕苦畏难的心理,关键是要让学生认识到车刀刃磨的重要性。
要做到这一点,就需要让学生全面了解车工实习的内容,明确刀具刃磨在车工操作中的地位,在实习中让学生认识到一把好刀在工件车削中的现实意义。
例如在指导学生磨刀之前,有意取一把教师磨的示范刀和一把以前学生磨的不合乎要求的刀,分别演示其切削效果,让学生进行比较。
二、合理设置课题,统筹安排实习进程实习教学与理论教学相比,对实习设备的依赖性较强。
要取得较好的教学效果,要求有足够多的实习设备,让每位学生都有充足的练习机会。
车工考试试题及答案

车工考试试题及答案车工考试试题及答案一、选择题1、下列哪个选项不属于车工操作范围?(答案:D) A. 车削外圆 B. 车削内孔 C. 车削螺纹 D. 铣削加工2、下列哪个刀具适合用于车削加工?(答案:A) A. 硬质合金刀具B. 高速钢刀具C. 陶瓷刀具D. 金刚石刀具3、在进行车削加工时,下列哪个选项不属于切削运动?(答案:D)A. 主运动B. 进给运动C. 横向运动D. 轴向运动4、车削过程中,下列哪个因素主要影响工件的粗糙度?(答案:A)A. 切削速度B. 进给速度C. 切削深度D. 刀具种类二、判断题1、车削加工可以用于加工所有类型的金属材料。
(答案:错)2、在车削加工中,切削速度越快,切削力越小。
(答案:对)3、车削螺纹时,必须保证螺纹的导程与车床的转速成反比。
(答案:对)4、在车削加工中,刀具的硬度必须高于工件的硬度。
(答案:对)三、填空题1、车削加工是指通过______的运动,切除工件材料的加工方法。
(答案:车床主轴)2、车削运动包括主运动、进给运动和______。
(答案:附加运动)3、车削螺纹时,必须保证螺纹的导程与车床的______相互配合。
(答案:转速)4、在车削加工中,工件的粗糙度主要与切削速度、进给速度和______有关。
(答案:切削深度)四、解答题1、请简述车削加工的特点和适用范围。
答:车削加工是一种常用的机械加工方法,主要是利用车床主轴的旋转运动,通过刀具与工件的相对运动,将工件材料切除。
适用于加工各种类型的中、小尺寸的金属材料,包括钢、铸铁、有色金属等。
主要加工外圆、端面、孔、螺纹等。
2、请说明车削加工中切削力的产生和影响。
答:车削加工中,刀具切削工件时会产生切削力。
切削力主要与工件材料、刀具材料、切削用量等因素有关。
切削力的大小直接影响切削过程稳定性和工件表面质量。
过大的切削力会导致刀具磨损、崩刃等问题,甚至损坏机床。
因此,在实际加工过程中,需要根据工件材料和刀具材料选择合适的切削用量,以减小切削力,提高加工质量。
刀主要角度
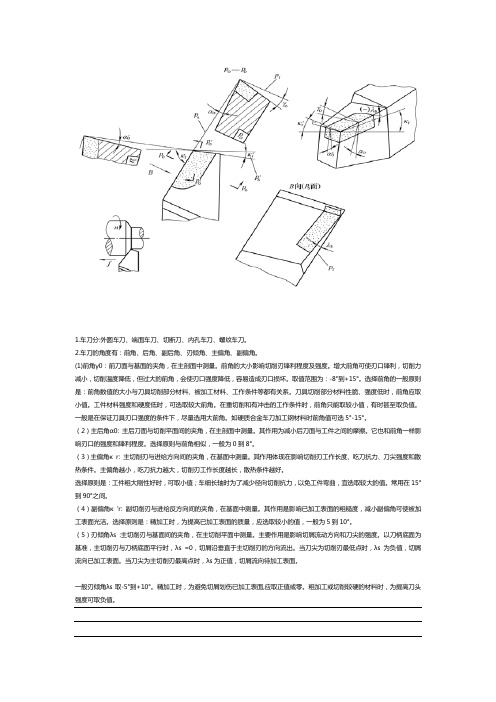
1.车刀分:外圆车刀、端面车刀、切断刀、内孔车刀、螺纹车刀。
2.车刀的角度有:前角、后角、副后角、刃倾角、主偏角、副偏角。
(1)前角γ0:前刀面与基面的夹角,在主剖面中测量。
前角的大小影响切削刃锋利程度及强度。
增大前角可使刃口锋利,切削力减小,切削温度降低,但过大的前角,会使刃口强度降低,容易造成刃口损坏。
取值范围为:-8°到+15°。
选择前角的一般原则是:前角数值的大小与刀具切削部分材料、被加工材料、工作条件等都有关系。
刀具切削部分材料性脆、强度低时,前角应取小值。
工件材料强度和硬度低时,可选取较大前角。
在重切削和有冲击的工作条件时,前角只能取较小值,有时甚至取负值。
一般是在保证刀具刃口强度的条件下,尽量选用大前角。
如硬质合金车刀加工钢材料时前角值可选5°-15°。
(2)主后角α0: 主后刀面与切削平面间的夹角,在主剖面中测量。
其作用为减小后刀面与工件之间的摩擦。
它也和前角一样影响刃口的强度和锋利程度。
选择原则与前角相似,一般为0到8°。
(3)主偏角κr: 主切削刃与进给方向间的夹角,在基面中测量。
其作用体现在影响切削刃工作长度、吃刀抗力、刀尖强度和散热条件。
主偏角越小,吃刀抗力越大,切削刃工作长度越长,散热条件越好。
选择原则是:工件粗大刚性好时,可取小值;车细长轴时为了减少径向切削抗力,以免工件弯曲,宜选取较大的值。
常用在15°到90°之间。
(4)副偏角κ'r: 副切削刃与进给反方向间的夹角,在基面中测量。
其作用是影响已加工表面的粗糙度,减小副偏角可使被加工表面光洁。
选择原则是:精加工时,为提高已加工表面的质量,应选取较小的值,一般为5到10°。
(5)刃倾角λs :主切削刃与基面间的夹角,在主切削平面中测量。
主要作用是影响切屑流动方向和刀尖的强度。
以刀柄底面为基准,主切削刃与刀柄底面平行时,λs =0,切屑沿垂直于主切削刃的方向流出。
关于对车刀几何参数的选择分析

关于对车刀几何参数的选择分析【摘要】刀具的几何参数对切削过程中的金属切削变形、切削力、切削温度、工件的加工质量及刀具的磨损都有显著的影响。
选择合理的刀具几何参数,可使刀具潜在的切削能力得到充分发挥,降低生产成本,提高切削效率。
【关键词】车刀;几何参数;选择车刀刃磨水平的高低直接关系到产品的生产效率、加工质量、设备能耗和产品成本,甚至关系到操作者的人身安全,也反映出操作者对加工主体的特性和切削用量的灵活应变能力。
合理选择车刀的几何参数是决定刃磨质量的关键,其主要体现于对车刀角度和前面形状的合理选择。
两者既相互依赖又相互制约,一把车刀不能只有一个角度,如果只有一个角度选择合理,它的切削效果也不一定理想,操作者必须根据工件材料、车刀材料、切削用量,以及工件、车刀、夹具和车床的刚性等各方面因素,全面分析,找出切削过程中的主要矛盾,合理选择车刀的角度和前面形状。
刀具几何参数包含切削刃的形状、切削区的剖面形式、刀面形式和刀具几何角度四个方面,这里主要讨论刀具几何角度的合理选择,即前角、后角、副后角、主偏角、副偏角及刃倾角的合理选择。
1.前角的选择前角r0是车刀切削部分的一个最主要的角度,车刀是否锋利主要取决于前角的大小。
一般增大前角时可以减小切削变形,减小切屑和前刀面的摩擦,使切削力降低,加工起来很轻快。
增大前角还可以使前刀面上承受切削力的位置后移,改善切削刃受力情况,同时还可以抑制积屑瘤的产生。
减小前角可增强刀尖强度,但切削变形和切削力都会增大。
前角的选择主要遵循以下原则:(1)加工塑性材料时,前角应取较大值;加工脆性材料时,应选用较小的前角;(2)工件材料的强度、硬度较低时,选用较大的前角;反之,选用较小的前角;(3)刀具材料韧性好时,前角应选大些,如高速钢车刀;刀具材料韧性差时,如硬质合金车刀;(4)粗加工和断续切削时应选较小的前角,横加工时应选较大的前角;(5)车床一夹具一工件—刀具系统刚度差时,应选较大的前角。
车刀的刃磨
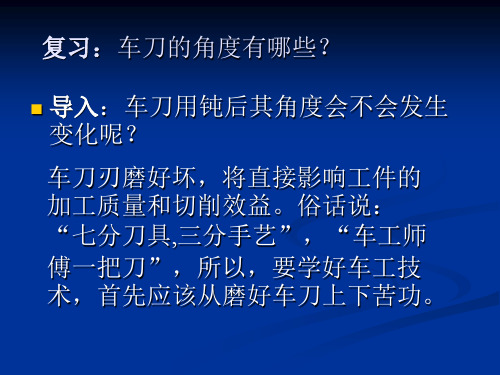
3、刀具刃磨良好的标准
刃磨良好的刀具应达到:刀口平直无崩口; 刀具平整,粗糙度低;角度正确;刀尖无 损伤。其关键要看刀尖、 刀尖附近的刃口、 刀口附近的刀面。因为切削主要是刀尖和 刀尖附近的刀刃来完成的,只要能保证附 近的区域达到上述要求,其他部分不影响 强度、无干涉即可。
磨主后刀面
按主偏角大小,刀杆 向左偏斜 。同时磨 出主偏角和主后角; (如左图)按主后 角大小,刀头向上 翘; 主后刀面自下 而上,接触砂轮。
磨副后刀面,按副 偏角大小,刀杆向
右偏斜,刀头向上 翘;同时磨出副偏 角和副按副后角大 小,(如图)副后 刀面自下而上,接 触砂轮。
2、角度检测的方法
①目测法 观察车刀角度是否合乎切削 要求,刀刃是否锋利,表面是否有裂 痕和其他不符合切削要求的缺陷。
(9)、重新安装砂轮后,要进行检查,经试 转后方可使用。
(10)、结束后,应随手关闭砂轮机来自源。总结作业:车刀刃磨的步骤是什么?
4、刃磨练习注意事项
(1)、车刀刃磨时,不能用力过大,以防打滑伤手。 (2)、车刀高低必须控制在砂轮水平中心,刀头略向上
翘,否则会出现后角过大或负后角等弊端。
(3)、车刀刃磨时应作水平的左右移动,以免砂轮表面 出现凹坑。
(4)、在平形砂轮上磨刀时,尽可能避免磨砂轮侧面。 (5)、砂轮磨削表面须经常修整,使砂轮没有明显的跳
2、砂轮粗细的选择:
粗磨车刀应选用粗砂轮(36#或60#), 精磨车刀应选细砂轮(80#或120#)。
二、刃磨车刀的方法
车刀有机械刃磨和手工刃磨两种 刃磨方法,手工刃磨车刀是车工 的基本功之一。
1、90度外圆车刀的刃磨方法
车刀的刃磨
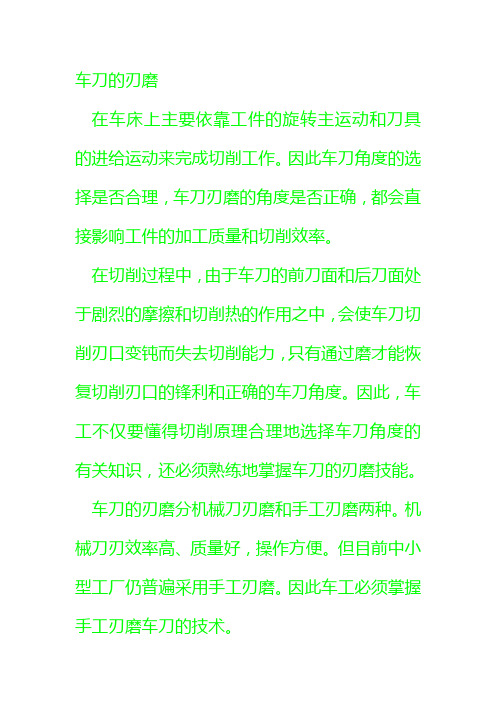
车刀的刃磨在车床上主要依靠工件的旋转主运动和刀具的进给运动来完成切削工作。
因此车刀角度的选择是否合理,车刀刃磨的角度是否正确,都会直接影响工件的加工质量和切削效率。
在切削过程中,由于车刀的前刀面和后刀面处于剧烈的摩擦和切削热的作用之中,会使车刀切削刃口变钝而失去切削能力,只有通过磨才能恢复切削刃口的锋利和正确的车刀角度。
因此,车工不仅要懂得切削原理合理地选择车刀角度的有关知识,还必须熟练地掌握车刀的刃磨技能。
车刀的刃磨分机械刀刃磨和手工刃磨两种。
机械刀刃效率高、质量好,操作方便。
但目前中小型工厂仍普遍采用手工刃磨。
因此车工必须掌握手工刃磨车刀的技术。
1.砂轮的选用目前常用的砂轮有氧化铝和碳化硅两类,刃磨时必须根据刀具材料来决定。
(1)]氧化铝砂轮氧化铝砂轮多呈白色其砂料韬性好,比较锋利,但硬度稍低(指磨料容易从砂轮上脱落),适于刃磨调整钢车刀和硬质合金的刀柄部分。
氧化铝砂轮也不例外称刚玉砂轮。
(2)碳化硅砂轮碳化硅砂轮多呈绿色,其砂料硬度高,切削性能好比较适于刃磨质合金车刀。
砂轮的粗细料度表示。
GB2477-83规定了41个料度号,粗磨时用粗粒度(基本粒尺寸大),精磨时用细粒度(基本粒尺寸小)。
2.车刀刃磨的方法和步骤现以90度硬质合金(YT15)外圆车刀为例,介绍手工刃磨车刀的方法(1)先磨去车刀前面、后面上的焊渣,并将车刀底面磨平。
可选用粒度号为24#到达36#的氧化铝砂轮。
(2)粗磨主后面和副后面的刀柄部分(以形成后隙角)。
刃磨时,在略高于中心的水平位臵处将车刀翘起一个比刀体上的后角大2度到3度的角度,以便再刃磨刀体上的主后角和副后角(如图1—35)。
可选粒度号为24#到达6#、硬度为中软(ZR1、ZR2)的氧化铝砂轮。
(3)粗磨刀体上的主后面磨主后面时,刀柄应与砂轮轴线保持平行,同时刀体底面向砂轮方向倾斜一个比主后角大2度的角度。
刃磨时,先把车刀已磨好的后隙面靠在砂轮的外圆上,以接近砂轮中心的水平位臵为刃磨的起始位臵,然后使刃磨位臵继续向砂轮靠近并作左右缓慢移动。
普通车床考试复习题

普通车床考试复习题一、填空1、工件时头不能离工件太近,以防切屑飞入眼中,为防切屑崩碎飞散,必须戴防护眼镜。
2、凡装卸工件、更换刀具测量加工表面及变换速度时,必须先停车。
3、车床动转时,不得用手去摸工件表面,尤其是加工螺纹时,严禁用手抚摸螺纹面,以免伤手。
严禁用棉纱擦抹转动的工件。
4、毛坯棒料从主轴孔尾端伸出不得太长,并使用料架或挡板,防止甩弯的候伤人。
5、主轴变速必须先停车,变速进给箱手柄要在低速进行。
为保证丝杠的精度,除车削螺纹时,不得使用丝杠进行机动进给。
6、不允许在卡盘及床身导轨上敲击或校直工件,装夹找正较重工件时,应用木板保护床面。
下班时,若工件不能卸下,应用行千顶支撑。
7、按不同的用途可将车刀分为外圆车刀、端面车刀、切断刀、内孔车刀,成形车刀和螺纹车刀等。
8、使工件上多余材料不断的被切除的运动叫进给运动。
9、铸铁是碳量大于2.11%的铁碳合金。
10、将原材料转变为成品的过程称为生产过程。
11、在设计图样上所采用的基准称为设计基准,用以标注尺寸和描述表面相互位置关系。
12、麻花钻的顶角通常为118°13、车孔的关键技术是解决内孔车刀的刚性和排屑问题。
14、通孔车刀采用75°内孔车刀,前排屑。
盲孔则采用90°内孔车刀,后排屑。
15、圆锥大小端直径之差与长度之比叫锥度,基计算公式C=(D-d)/L。
16、车圆锥时,车刀刀尖没有对准工件轴线,车出的圆锥素线不是直线,而是双曲线。
17、螺纹按用途可分为连接螺纹和传动螺纹两大类。
18、三角螺纹按其规格用途不同,一般可分为普通三角螺纹、英制三角形螺纹和管螺纹。
19、车螺纹时,由于受螺旋角的影响,车削时车刀左右两侧后角人产生变化,车刀沿进给方向一侧的后角等于(3-5)+¢;车刀背着进给方向一侧的后角等于(3-5)-¢‘车削左旋时,情况正好相反。
二、判断题。
1、车刀磨损后应及时刃磨,不允许用钝刃车刀继续车削以免增加车床的负荷,损坏车床,影响工件表面的加工质量和生产效率。
刀具磨损和刀具寿命讲解
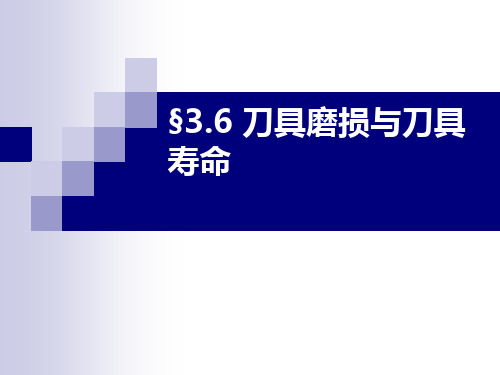
2.塑性破损
在刀具前刀面与切屑、后刀面与工件接触面上, 由于过高的温度和压力的作用,刀具表层材料将 因发生塑性流动而丧失切削能力,这就是刀具的 塑性破损。抗塑性破损能力取决于刀具材料的硬 度和耐热性。硬质合金和陶瓷的耐热性好,一般 不易发生这种破损。相比之下,高速钢耐热性较 差,较易发生塑性破损。
刀具的破损形式分为脆性破损和塑性破损。 1.脆性破损 硬质合金刀具和陶瓷刀具切削时,在机械应力和热应
力冲击作用下经常发生以下几种形态的破损: (1)崩刃 切削刃产生小的缺口。在继续切削中,缺
口会不断扩大, 导致更大的破损。用陶瓷刀具切削及 用硬质合金刀具作断续切削时,常发生这种破损。 (2)碎断 切削刃发生小块碎裂或大块断裂,不能继 续进行切削。用硬质台金刀具和陶瓷刀具作断续切削 时,常发生这种破损。 (3)剥落 在刀具的前、后刀面上出现剥落碎片,经 常与切削刃一起剥落,有时也在离切削刃一小段距离 处剥落。陶瓷刀具端铣时常发生这种破损。 (4)裂纹破损 长时间进行断续切削后,因疲劳而引 起裂纹的一种破损。热冲击和机械冲击均会引发裂纹, 裂纹不断扩展合并就会引起切削刃的碎裂或断裂。
(4)合理选择切削用量 防止出现切削力过大和切 削温度过高的情况。
(5)工艺系统应有较好的刚性 防止因为振动而损 坏刀具。
1.刀具磨损的形式
切削时,刀具的前、后刀面与切屑及已加工表面相接触,产生剧烈摩 擦。在接触区内有相当高的温度和压力。因此在前后刀面上都会发生磨损。 但它们的磨损情况有各自不同的特点,而且相互影响:刀具磨损形式有以 下几种:
前刀面磨损
后刀面磨损
边界磨损
(1)前刀面磨损(月牙洼磨损) 切削塑性材料时,如果切 削速度和切削厚度较大,切屑在前刀向上经常会磨出一个 月牙洼。出现月牙洼的部位就是切削温度最高的部位。月 牙洼和切削刃之间有一条小棱边,月牙洼随着刀具磨损不 断变大,当月才洼扩展到使棱边变得很窄时,切削刃强度 降低,极易导致崩刃。月牙洼磨损量以其深度KT表示 。
对车削加工生产效率提高措施的论述

1 在加工过程中应该关注的事项 1 . 1 车削加工 的困难。在进行车削的加工时, 应该时刻注意工件的部 件是否出现挤裂或者单元切屑 , 一旦在加工 的过程中, 出现挤裂现象 将会对工件的表面按粗糙度增大 ,使得工件的质量达不到要求标准。
数控机床使用的刀具有如下要求 : 1 ) 具有较高的强度 、 较好的刚度和 抗振 眭能 ; 2 ) 高精度 、 高可靠性和较强的适应性 ; 3 ) 能够满足高切削速 度和大进给量的要求 ; 4 ) 刀具耐磨性及刀具的使用寿命长, 刀具材料 和切削参数与被加工件材料之间要适宜 ; 5 )刀片与刀柄要通用化、 规
会对刀尖造成很大的损伤, 并且会让加工 的效率和质量有所降低。刀 1 ) 高速钢。高合金工具钢, 具有 良好 的工艺性 , 能制成复杂的刀 具的寿命跟切削的速度是有根本上的关系的,一旦加快切削的速度 , 具。 高速钢刀具使用前需要使用者 自行刃磨 , 因此 , 适合于特殊需要的 那么刀具的寿命必然会有所降低。 在这方面进给量对于刀具的磨损是 非标准刀具 。 2 ) 硬质合金 。比高速钢硬得多。 允许的切削速度比高速 最小的, 可以控制在—个接受范围内。还有就是切削的深度对于刀具 钢高 4 — 1 0 倍, 切削速度可达 l O O m / mi n以上。国际标准化组织规定 ,
而当出现切屑的情况,将会导致在应力上面超出了工件材料的极限。 格化 、 系列化 、 标准化, 相对主轴要有较高位置精度 , 转位 、 拆装时要求 裂纹贯穿了整个切屑厚度 , 形成 了—个个梯形单元切屑。切削力的波 重复定位精度高 , 安装调整方便。 动更大, 加工表面的粗糙度值也更大。 如果形成崩碎切屑 , 表明切削层 2 . 2 金属切削刀具的主要角度。 车刀的五个基本角度 : 1 ) 前角 o : 是 材料未经塑 眭变形就产生胞 l 生 崩裂 , 形成不规则的碎块状切屑 , 切削 前刀面切削平面之间的夹角, 表示前刀面的倾斜程度。2 ) 后角 O . r o : 是 力波动很大, 并且集中在切削刃上 , 容易损坏刀具。 在加工过程中可以 主后刀面与切削平面之 间的夹角 , 表示主后刀面倾斜的程度 。3 ) 主偏 通过观察切屑形态来判断切削条件是否合适 。同时在加工塑性材料 角 - (一 r : 是 主切削刃在基面上的投影与进给方向之间的夹角 ; 4 ) 副偏 时, 如果出现挤裂或单元切屑 , 则可用改变刀具几何角度 、 切削用量等 角 . c ’ : 是副切削刃在基面上的投影与进给运动方向之间的夹角 ; 5 ) 方法 , 使切屑转化成带状切屑。 精车时不 允{ 午 存在积屑瘤。 积屑瘤会使 刃倾角 0 : 是主切削刃与基面之间的夹角。刀具主要角度的选择原 工件表面粗糙度值增大, 这是精车工件时所不允许的。可 以采取的措 则 : 前角。 增大前角, 切屑易流出, 可使切削力减少 , 切削很轻陕。 但前 施有控制加工时的速度 , 使用很低或很 高的切削速度 , 避开产生积屑 瘤的速度范围; 适当加大刀具前角、 减/ J 、 进给量、 提高刀具表面刃磨质 量、 选用润滑 『 生 能 良好的切削液等 ; 材料塑性太大 的工件 , 切削时塑性 变形大 , 容易产生积屑瘤 。 因此 , 加工前可将材料进行正火或调质处理, 以提高硬度 、 降低 塑性 , 以抑制积屑瘤的产生。 1 - 2 车削加工时的问题。1 ) 合理选择切削用量 : 在进行高级金属切削 加工 的过程中主要的影响因素有被加工材料、切削工具和切削条件。 这些 因素能够对切削产品的寿命和质量起到决定性的作用。 而对于切 削的条件来说也要从多方面来进行考虑,主要有在进行切削时的速 度, 进给量和在切削的过程中对于刀具的损害。在进行切削的加工过 程中, 刀具刀尖会随着加工的延续 自身温度会进行升高 , 这种现象将 角过大 , 刀刃强度降低。 后角。 增大后角可减少刀具后刀面与工件之间 的摩擦。 但后角 x ' 2 , : 3 v , 刀刃强度降低。 主偏角。 在切削深度和进给量不 变的情况下 , 增大主偏角 , 可使切削力沿工件轴向力加大 , 径 向力减 小, 有利于加工细长轴并减小振动。 刃倾角 。 增大刃倾角 有利于承受冲 击。刃倾角为正值时, 切屑向待加工方向流动 ; 刃倾角为负值时, 切屑 向已加工面方向流动。 通常, 精车时取 0 — 4 。; 粗加工时取 一 1 0 ~5 。。 2 - 3 刀具常用材料。刀具切削部分的材料应具备如下性能 :高的硬 度, 足够 的强度和韧 陛, 高的耐磨l 生, 高的耐热眭, 良好的加工工艺性。 刀具材料: 高速钢( 俗称白钢刀条 ) , 硬质合金 , 陶瓷 , 立方氮化硼 ( C B N ) , 聚晶金刚石 ( P C D) 。数控机床上常用高速钢刀具和硬质合金 刀具。材料越硬就越脆 , 越耐磨 , 在使用时需要高速平稳 , 防止冲击和 振动。碳素工具钢和合金工具钢的红硬 差民营 科技 2 0 1 3 年第9 期
车刀的选择和使用

第一节车刀材料的选择车刀的使用寿命和生产效率取决于车刀材料的切削性能。
车刀由刀头和刀杆两部分组成,刀杆一般是用碳素结构钢制成。
由于刀头担任切削工作,因此刀头材料必须具有下列基本性能:1)冷硬性。
车刀在常温时具有较高的硬度,即车刀的耐磨性。
2)红硬性。
车刀在高温下保持切削所需的硬度,该温度的最高值称为"红热硬度"。
3)韧性。
车刀切削部分承受震动和冲击负荷所具有的强度和硬度。
车刀材料的以上三种性能是相互联系、相互制约的,在具体选用时,要根据工件材料的性能和切削要求分析选用,同时还要结合车刀材料在价格、工艺性能方面加以考虑,以便于以较低的成本加工、刃磨和焊接制造车刀。
各种车刀材料的基本性能优劣顺序比较见表4-1。
目前用来作车刀切削部分的材料主要有高速钢、硬质合金和非金属材料,碳素工具钢、合金工具钢多用作钻头、丝锥等工具,用作车刀的较少。
现分别介绍作车刀刀头的两种主要材料:高速钢及硬质合金。
一、高速钢高速钢是一种含钨、铬、钒较多的合金钢,又名锋钢、风钢或白钢。
常用的有Wl8Cr4V及W9Cr4V2两种牌号。
其中用得最多的是Wl8Cr4V高速钢。
它们的化学成分如表4-2所示。
高速钢材料分为带黑皮的高速钢和表面磨光的高速钢两种。
前者是未经热处理的高速钢,后者是经热处理的高速钢。
高速钢硬度较高,具有一定的红热硬性,韧性和加工性能均较好。
高速钢车刀制造简单,刃磨方便,容易磨得锋利。
由于高速钢韧性好,常用于加工一些冲击性较大、形状不规则的零件,它也常用于制作精车刀,但因红硬性不如硬质合金,故不宜用于高速切削。
二、硬质合金硬质合金是由难熔材料的碳化钨、碳化铁和钴的粉末在高压下成形,经l350~1560"(2高温烧结而成的材料,具有极高的硬度,仅次于陶瓷和金刚石。
硬质合金的红硬性很好,在1000℃左右仍能保持良好切削性能;具有较高的使用强度,其抗弯强度可高达1000--1700MPa,但脆性大、韧性差、怕震,以上这些缺点可通过刃磨合理的角度加以克服,因此,硬质合金现已被广泛应用。
如何保证车工实习训练效果

如何保证车工实习训练效果经济飞速发展带来的竞争日趋激烈,如何使学校在竞争中得到长足的发展呢?实习教学效果的保证应该是关键。
车工实习是中职机械专业重要的实习环节之一。
现结合我们近年来的实训教学从以下几方面与大家共同探讨如何抓好车工专业实习,确保教学效果。
一、加强师德、专业理论、专业技能的提升如何使学生把专业理论知识转化为技能、技巧?如何使学生把理论知识应用于实践生产中?这是实习指导教师的首要任务。
如今科技日益发展,教学内容不断更新,新技术、新工艺、新方法的日新月异,都要求教师要适应形式的需要,不断更新自己的知识水平和教学理念。
如果一个实习教师专业知识浅薄,操作水平不高,生产实习中对学生提出的问题无法解答,遇到技术难题就会束手无策。
学生不仅无法掌握好操作技能,更谈不上提高分析问题和解决问题的能力,比如,教师要求学生刃磨出符合加工要求的车刀,教师自己必须先能磨出高质量的车刀,否则又怎能指导好学生呢?二、抓好学生的基础训练1.安全文明生产教育安全文明生产是学生进入生产实习实训基地的第一课,合格的技术工人必须树立牢固的安全文明生产意识。
教学中在对各种机床、砂轮机等的操作示范过程中老师要牢记安全文明生产意识,因为教师每一个操作、每一个举止都在影响着学生,深度体现着身教重于言传。
2.对车床的基本操作要求车床的基本操作包括工件的装夹,刀具的选用,主轴的转速和进给量调整等。
在操作示范时,每个内容的动作要系统、全面、标准,切不可只做一部分,否则好的学生也许没什么,但差的学生就很难了。
在示范动作时,可给学生设置一定的悬念,启发学生思考,培养其积极的思维能力,激发学习的积极性和主动性。
在示范完一个动作后,可以让某个学生再操作一次,纠正其错误及不规范之处。
3.掌握刀具的刃磨方法车削加工有句行话:“三分手艺,七分刀具。
”七分刀具,是指车刀刃磨的角度非常关键,它直接影响到产品质量的优劣和生产效率的高低,因此,在车工实习教学中车刀的刃磨一直是教学中的重点和难点,但是很多学生一开始并不能正确理解这句话。
技能认证车工5级考试(习题卷2)
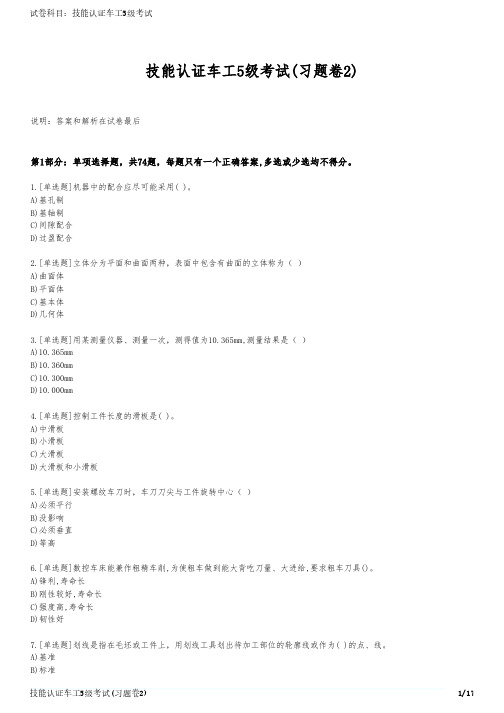
技能认证车工5级考试(习题卷2)说明:答案和解析在试卷最后第1部分:单项选择题,共74题,每题只有一个正确答案,多选或少选均不得分。
1.[单选题]机器中的配合应尽可能采用( )。
A)基孔制B)基轴制C)间隙配合D)过盈配合2.[单选题]立体分为平面和曲面两种,表面中包含有曲面的立体称为( )A)曲面体B)平面体C)基本体D)几何体3.[单选题]用某测量仪器、测量一次,测得值为10.365mm,测量结果是( )A)10.365mmB)10.360mmC)10.300mmD)10.000mm4.[单选题]控制工件长度的滑板是( )。
A)中滑板B)小滑板C)大滑板D)大滑板和小滑板5.[单选题]安装螺纹车刀时,车刀刀尖与工件旋转中心( )A)必须平行B)没影响C)必须垂直D)等高6.[单选题]数控车床能兼作粗精车削,为使粗车做到能大背吃刀量、大进给,要求粗车刀具()。
A)锋利,寿命长B)刚性较好,寿命长C)强度高,寿命长D)韧性好7.[单选题]划线是指在毛坯或工件上,用划线工具划出待加工部位的轮廓线或作为( )的点、线。
C)起点D)终点8.[单选题]同时承受径向力和轴向力的轴承是(A)向心轴承B)推力轴承C)角接触轴承D)滚柱轴承9.[单选题]带电灭火时,( )灭火器是不合适的。
A)1211B)酸碱C)干粉D)泡沫10.[单选题]存在( )的生产经营单位,应当按照有关规定及时申报本单位的职业病危害因素,并定期检测、评价。
A)重大危险隐患B)安全隐患C)劳务派遣工D)职业病危害11.[单选题]刃磨车刀时,车刀的高低必须控制在砂轮的( )。
A)水平中心B)中心偏下C)中心偏上D)任意12.[单选题]球墨铸铁经( )可获得下贝氏体基体组织。
A)正火B)等温淬火C)退火D)淬火13.[单选题]国家标准中,对孔和轴的每一基本尺寸段都规定了( )个基本偏差。
A)26B)28C)30D)3214.[单选题]用硬质合金车刀高速车螺纹时,它的径向前角( )A)-1°B)0°C)1°D)2°15.[单选题]脉冲当量()。
刀具管理知识手册(汇总)

刀具管理知识手册(汇总)一、引言刀具作为工业生产中不可或缺的重要工具,其性能和使用寿命直接影响到产品的质量和生产效率。
为了确保刀具的安全、合理和高效使用,提高生产效益,降低生产成本,本文将介绍刀具管理的相关知识,以供广大生产企业和使用者参考。
二、刀具的分类与选用1.刀具的分类(1)根据加工对象的不同,刀具可分为:车刀、铣刀、钻头、镗刀、铰刀、螺纹刀、齿轮刀具等。
(2)根据制造材料的不同,刀具可分为:高速钢刀具、硬质合金刀具、陶瓷刀具、金刚石刀具等。
(3)根据涂层材料的不同,刀具可分为:无涂层刀具、涂层刀具(如TiN、TiCN、TiAlN等)。
2.刀具的选用(1)根据加工材料:加工高硬度材料时,选用硬质合金或陶瓷刀具;加工低碳钢、不锈钢等易加工材料时,可选用高速钢刀具。
(2)根据加工要求:精度要求高的加工,选用高精度、高刚性刀具;粗加工时,选用强度高、耐用性好的刀具。
(3)根据机床性能:选用与机床主轴、刀柄相匹配的刀具。
三、刀具的安装与调整1.刀具的安装(1)确保刀具与刀柄的连接紧固,防止刀具在加工过程中脱落。
(2)刀具的安装方向应正确,避免加工过程中产生振动。
(3)刀具的安装高度应符合加工要求,保证加工表面质量。
2.刀具的调整(1)调整刀具的切削参数,如切削速度、进给量、切削深度等,以提高加工效率。
(2)调整刀具的径向和轴向位置,保证加工尺寸精度。
(3)调整刀具的切削刃磨状态,确保刀具具有良好的切削性能。
四、刀具的使用与维护1.刀具的使用(1)合理选用切削液,降低切削温度,提高刀具使用寿命。
(2)避免刀具在加工过程中长时间空转,减少刀具磨损。
(3)掌握合理的切削参数,避免刀具过度磨损。
2.刀具的维护(1)定期检查刀具磨损情况,及时更换磨损严重的刀具。
(2)定期对刀具进行清洁和防锈处理,延长刀具使用寿命。
(3)合理存放刀具,避免刀具受到碰撞、变形等损伤。
五、刀具的刃磨与涂层1.刃磨(1)掌握正确的刃磨方法,保证刀具的切削性能。
实训报告车刀的基本知识

一、实训背景随着我国制造业的快速发展,数控车床在机械加工领域的应用越来越广泛。
车刀作为数控车床的切削工具,其性能直接影响着加工质量和生产效率。
为了提高自身对车刀的认识和应用能力,我参加了车刀的基本知识实训。
二、实训内容本次实训主要围绕车刀的组成、结构形式、几何角度及选择等方面展开。
1. 车刀的组成车刀由刀头和刀体两部分组成。
刀头用于切削,刀体用于安装。
刀头一般由三面、两刃、一尖组成。
(1)前刀面:切屑流经过的表面。
(2)主后刀面:与工件切削表面相对的表面。
(3)副后刀面:与工件已加工表面相对的表面。
(4)主切削刃:前刀面与主后刀面的交线,担负主要的切削工作。
(5)副切削刃:前刀面与副后刀面的交线,担负少量的切削工作,起一定的修光作用。
(6)刀尖:主切削刃与副切削刃的相交部分,一般为一小段过渡圆弧。
2. 车刀的结构形式(1)整体车刀:刀头的切削部分是靠刃磨得到的,整体车刀的材料多用高速钢制成,一般用于低速切削。
(2)焊接车刀:将硬质合金刀片焊在刀头部位,不同种类的车刀可使用不同形状的刀片。
焊接的硬质合金车刀,可用于高速切削。
3. 车刀的几何角度及选择(1)切削平面:切于主切削刃某一点并垂直于刀杆底平面的平面。
(2)基面:过主切削刃的某一选定点并垂直于刀杆底平面的平面。
(3)正交平面:垂直于切削平面又垂直于基面的平面。
主要几何角度包括:(1)前角:前刀面与基面之间的夹角。
其中前角又分正前角和负前角。
刀具前刀面在基面之下时为正前角。
刀具前刀面在基面之上时为负刀面。
前角的选择原则:前角的大小主要与刀头的坚固性与锋利性有关系,两者之间是相互矛盾的。
我们应该根据加工的材料和性质来选择前角的大小。
如果加工材料硬度高,则前角应取小值,此时刀头不锋利,适合粗加工。
如果硬度低前角可以取大值,此时刀头锋利,可以进行精加工。
前角一般在-5~25之间选取。
(2)后角:主后刀面与切削平面间的夹角。
需要注意,后角不能为零度或负值,一般在6~12之间选择。
刀主要角度
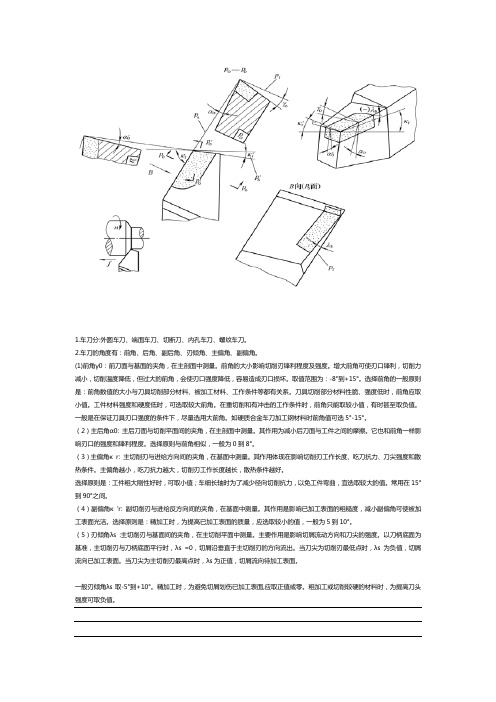
1.车刀分:外圆车刀、端面车刀、切断刀、内孔车刀、螺纹车刀。
2.车刀的角度有:前角、后角、副后角、刃倾角、主偏角、副偏角。
(1)前角γ0:前刀面与基面的夹角,在主剖面中测量。
前角的大小影响切削刃锋利程度及强度。
增大前角可使刃口锋利,切削力减小,切削温度降低,但过大的前角,会使刃口强度降低,容易造成刃口损坏。
取值范围为:-8°到+15°。
选择前角的一般原则是:前角数值的大小与刀具切削部分材料、被加工材料、工作条件等都有关系。
刀具切削部分材料性脆、强度低时,前角应取小值。
工件材料强度和硬度低时,可选取较大前角。
在重切削和有冲击的工作条件时,前角只能取较小值,有时甚至取负值。
一般是在保证刀具刃口强度的条件下,尽量选用大前角。
如硬质合金车刀加工钢材料时前角值可选5°-15°。
(2)主后角α0: 主后刀面与切削平面间的夹角,在主剖面中测量。
其作用为减小后刀面与工件之间的摩擦。
它也和前角一样影响刃口的强度和锋利程度。
选择原则与前角相似,一般为0到8°。
(3)主偏角κr: 主切削刃与进给方向间的夹角,在基面中测量。
其作用体现在影响切削刃工作长度、吃刀抗力、刀尖强度和散热条件。
主偏角越小,吃刀抗力越大,切削刃工作长度越长,散热条件越好。
选择原则是:工件粗大刚性好时,可取小值;车细长轴时为了减少径向切削抗力,以免工件弯曲,宜选取较大的值。
常用在15°到90°之间。
(4)副偏角κ'r: 副切削刃与进给反方向间的夹角,在基面中测量。
其作用是影响已加工表面的粗糙度,减小副偏角可使被加工表面光洁。
选择原则是:精加工时,为提高已加工表面的质量,应选取较小的值,一般为5到10°。
(5)刃倾角λs :主切削刃与基面间的夹角,在主切削平面中测量。
主要作用是影响切屑流动方向和刀尖的强度。
以刀柄底面为基准,主切削刃与刀柄底面平行时,λs =0,切屑沿垂直于主切削刃的方向流出。
机械制造技术基础判断题

1.立式车床车削盘类零件外圆时,其主运动是工件的旋转运动。
(√)2.车削时的切削深度(背吃刀量)等于所切槽的宽度。
(×)3.切削层公称横截面积是在给定瞬间,切削层在切削层尺寸平面里的实际横截面积。
(√)4.切削加工中所使用的刀具材料的硬度必须大于工件材料的硬度。
(√)5.金属的切削过程的实质是一种偏挤压过程。
(√)6.切削塑性材料时,在三个切削变形区中均会产生一定程度的表面变形强化。
(×)7.加工精度指的是实际几何参数相符合的程度。
(√)8.零件表面的残余应力一般都会影响加工精度的稳定性。
(√)9.工步是组成零件工艺过程的基本单元。
(×)10.粗加工阶段和精加工阶段对机床配置的要求相同。
(×)11.车削细长轴,刀具应该选择较小的主偏角。
(×)12.刀具的耐用度和刀具的寿命是同一概念的两种不同描述.(×)13.工件的定位和夹紧统称为工件的安装。
(√)14.只要限制了工件的6个自由度,工件就能够实现定位。
(×)15.过定位和欠定位在加工中都是不允许存在的。
(×)16.车削加工可以保证工件表面之间具有较高的位置精度。
(√)17.在车床上钻孔容易出现轴线偏斜,而在钻床上钻孔则容易产生孔径扩大。
(×)18.铰孔时,由于铰刀和机床是浮动连接,因此不能提高孔的位置精度。
(√)19.顺铣在许多方面都比逆铣好,因此在加工中一般使用顺铣。
(×)20.一般情况下,铣削的生产率高于刨削,但在加工窄长平面时,刨削的生产率则高于铣削。
(√)21.磨削过程的实质是切削、刻划和抛光的综合作用过程。
(√)22.外圆的精密加工主要用来减小形状误差。
(×)23.钻孔是在实体材料上加工孔的唯一切削加工方法。
(√)24.在硬脆的非金属材料上进行雕刻,最好采用激光加工。
(×)25.滚齿加工属于成型法加工齿轮。
(×)26.零件的切削加工工艺性反映的是零件切削加工的难易程度。
- 1、下载文档前请自行甄别文档内容的完整性,平台不提供额外的编辑、内容补充、找答案等附加服务。
- 2、"仅部分预览"的文档,不可在线预览部分如存在完整性等问题,可反馈申请退款(可完整预览的文档不适用该条件!)。
- 3、如文档侵犯您的权益,请联系客服反馈,我们会尽快为您处理(人工客服工作时间:9:00-18:30)。
车刀刃磨水平的高低直接关系到产品的生产效率、加工质量、设备能耗和产品成本,甚至关系到操作者的人身安全,也反映出操作者对加工主体的特性和切削用量的灵活应变能力。
合理选择车刀的几何参数是决定刃磨质量的关键,其主要体现于对车刀角度和前面形状的合理选择。
两者既相互依赖又相互制约,一把车刀不能只有一个角度,如果只有一个角度选择合理,它的切削效果也不一定理想,操作者必须根据工件材料、车刀材料、切削用量,以及工件、车刀、夹具和车床的刚性等各方面因素,全面分析,找出切削过程中的主要矛盾,合理选择车刀的角度和前面形状。
笔者结合多年的教学生产经验及相关理论资料,针对几类车刀的选择和使用情况,论述一下合理选择车刀的几何参数的方法。
1切断刀几何参数的选择在选择切断刀的几何参数时,应首先考虑保证切削刃足够锋利,在此前提下,再认真地维护其具有足够的强度,所以前角应该作为选择的主要参数,一般高速钢切断刀前角应取20。
~25。
左右,硬质合金的钢件切断刀前角应取8o~20。
左右,硬质合金的铸铁件切断刀前角选取5。
~10。
左右。
在维护车刀强度的问题上,应根据不同的工件材料、切削用量等因素,考虑采取以下方法:1.1刀杆部分细而长,所以只能取较小的0.5。
~1.5。
的副偏角和1。
~3。
的副后角,以增加刀杆的强度。
1.2车刀的切削部分深入工件,切削力和热大量集中在刀尖处,应各磨一个过渡刃,以保证刀尖。
1.3切断刀的切削刃一般较宽,且又深入工件里层,在正面切削力和侧面摩擦力作用下,容易引起振动而打坏刀具,所以主后角选取Z。
~5。
左右。
方面环境场中有用、无用的电磁波辐射能相互干扰日趋严重。
另一方面,各种电磁辐射都将影响或污染电磁环境,给人们的生活和健康带来不利因素。
在受污染或干扰的电磁环境中,轻则是电子设备不能正常工作,重则危及电子设备及人们的安全。
例如,当调频收音机本机振荡辐射正好落人民用导航频段,且共辐射超过限额值时,就可能干扰飞机导航,一旦导航有误就有可能造成飞行事故。
又如,生活中因电磁干扰造成的收音机噪声大,电视有“雪花”甚至不能正常收听收看也不足为奇。
电磁辐射与污染众所周知,电磁辐射中的X射线和7射线对人体的危害是较为严重的。
它是一种电离辐射,能使空气中的气体分子游离,穿透力很强。
无线电波波段中的无线电广播、电视、雷达、微波通讯、微波炉、微波理疗机以及工业设备用电磁辐射,属于非电离辐射,辐射的量子能较小,但在一定功率密度和照射时间的条件下,也会对人产生一定程度的危害。
电磁辐射对人体的危害程度,主要决定于电磁辐射的频率,强度和照射时间。
一般来说,电磁辐射能量越大,照射时间越长,对人体的影响也就越大。
当人体长时间受到过量的电磁辐射后,会出现疲劳、头昏、记忆力衰退和视力下降等现象。
作为物理教师,应当使学生在学习物理知识的过程中,逐步懂得科学与环境生活息息相关的问题。
如在指导学生进行有关遥控、遥测及业务无线电通讯等科技活动中,应当教育学生重视电磁环境的保护,遵守当地有关无线电管理部分的管理规定,避免干扰其他无线电波的活动。
对家用电器中的电磁辐射,如彩电的X射线保护,微波炉的微波泄漏防护等常识,也应向学生进行适当的教育,以保护学生的视力、脑力等不受影响。
最后顺便说一句,多吃新鲜蔬菜、水果,对预防和减轻电磁波伤害大有好处。
1.4切断直径较大的工件时,切断刀的切削刃最好磨成大圆弧形。
1.5切断工件时,因受刀具安装误差和进给误差等因素的影响,平头的切断刀往往容易受侧向切削力的作用而歪斜,此时可以做成具有120。
顶角的切断刀使侧向切削力保持平衡来维护刀具稳定。
1.6被切断的材料较硬时,切断刀除了做成120。
顶角外,还应在刀刃上磨出负倒楞,以增强刀刃的强度。
1.7被切断的材料特别硬或进行强力切断时,可将刀杆下面加宽呈鱼肚形,以增强刀杆强度。
2淬硬钢车刀几何参数的选择在选择车削高硬度材料(如淬火钢)的车刀几何参数时,首角应取负值,再配合合适的其它角度,就能顺利地切削了。
一般人们要问,前角是负值,这把车刀还算锋利吗?笔者认为,锋利和强度是刀具的一对矛盾,锋利不能被孤立看待。
如果用前角为10。
~20。
的车刀车削淬硬钢,车刀很快就会磨损变钝或崩刃,所以锋利只有在一定的强固条件下,才能发挥作用。
但是强度高不是最终目的,强度高是为锋利服务的,其目的是为了更好地发挥锋利的作用。
所以必须辩证地看待锋利与强度两者的关系。
被切削材料不同,对刀具强度的要求就不同,衡量车刀锋利的标准也就相应不同。
例如,切削铝件时,车刀前角磨成25。
或30。
仍能保持较好的强度,对切削铝件来说这种车刀是锋利的。
在车削钢件时,假如也选择这样大的前角,就失去了切削所需要的强度,它的锋利就不能有效地发挥作用,此时前角必须取得小一些。
车淬硬钢时,车刀前角应选用负值,为一7。
~一8。
,这样车刀的锋利才能发挥有效作用。
前角决定后,再按以下步骤选择合适的其它切削角度,来进一步增加刀具强度。
2.1刃倾角也取成一7。
~一8。
,以增强刀尖强度。
2.2取较小的后角2。
~3。
,以增大楔角。
3橡胶辊车刀几何参数的选择在车削橡胶辊时,由于切削力很小,同时工件材料的弹性好,切削变形大,所以选择车刀角度时,可较少考虑车刀的强度要求,而着重考虑车刀的锋利,以减少工件的切削变形,保证工件表面的加工质量。
为此,首先应选择较大的前角,若采用硬质合金车刀,前角一般选用40。
~50。
左右。
此外,选择其它角度时,也应紧密配合,立足于增加车刀锋利,其措施如下:3.1加大后角,为8。
~15。
,使楔角减少,进一步增强车刀的锋利,以达到减少切削变形的目的。
3.2加大过渡刃和修光刃,使切削力和切削热不致过分集中,以减少车刀磨损和工件的热烧损,从而提高工件表面质量。
3.3前面做成大前角的平面型式,使切削得以顺利流出排除,避免缠绕在车刀或工件上。
4车刀安装位置和进给运动对车刀工作角度的影响4.1刀具的安装位置对车刀工作角度的影响在安装车刀时,车刀刀尖应尽量对准工件旋转中心,车削外圆时,如果车刀装得太高,则前角增大,后角减小,增大车刀后面的摩擦,降低了刀尖的强度;相反如果车刀装得太低,则后角增大,前角变小,切削不够顺畅,有时甚至会抬起工件,打坏车刀。
车削内孔时,车刀装得高或低,结果恰恰与车外圆时相反。
车刀除了在车无孔端面时,必须对准中心外,一般情况下,尚可略高于中心。
经验认为,车刀安装的高低误差,应小于工件直径的百分之一。
此外,车刀装偏会影响主、副偏角的大小。
4.2进给运动对车刀工作角度的影响在横向进给时,车刀按一定的走刀量向前推进,这时车刀在端面上走过的轨迹不是一个圆圈,而是一条阿基米德螺旋线,车刀越接近中心和走刀量越大,螺旋线越倾斜,从而使车刀切削时的后角变小,前角变大,因此在刃磨时后角应磨得大一些。
在纵向进给时,由于车刀在工件上走出的轨迹是一条螺旋线,这条螺旋线的切线与原切削平面不重合,而是相交一定角度,所以在切削时实际后角是减去这个交角的差值。
在车外圆或内孔时,由于影响很小,可以忽略不计。
在车削螺纹时,这个交角很大,所以在刃磨螺纹刀后角时,要加上这个螺旋角差值,以克服走刀运动的影响。
4.3工件形状对车刀几何参数的影响在加工凸轮类零件时,由于工件形状的变化,也能引起车刀前后角的变化,刃磨时应考虑这个角度的变化。
以上这三个因素在选择刀具的几何参数时必须给予适当考虑。
总之,在选择车刀的几何参数时,应根据工件材料和车刀材料的机械物理性能、切削用量以及工件、车刀、夹具和机床的刚度等等因素,找出切削过程中的主要问题,把车刀的锋利放在第一位,以锋利为前提,适当考虑车刀的强度。
由于车刀的锋利主要取决于前角的大小,所以在选择时首先要抓住切削过程中的主要问题,合理确定前角值,然后选择其它几何角度车刀几何角度是指车刀切削部分各几何要素之间,或它们与参考平面之间构成的两面角和线、面之间的夹角。
它们分别决定着车刀的切削刃和各刀面的空间位置。
根据“一面二角”理论可知,车刀的独立标注角度有六个,它们分别是:确定车刀主切削刃位置的主偏角Kr和刃倾角λs;确定车刀前刀面与后刀面的前角ro和后角ao;确定副切削刃及副后刀面的副偏角Kr′和副后角ao′(附图略)。
这些几何角度对车削过程影响很大,其中尤其以主偏角Kr、前角ro、后角ao和刃倾角λs的影响更为突出,科学合理地选择车刀的几何角度,对车削工艺过程的顺利实施起着决定性作用。
下面就从分析车刀几何角度对切削力、切削热和刀具的耐用度的影响着手,本着合理切削轻便、质量稳定,延长刀具使用寿命的宗旨,来研究确定科学合理的车刀几何角度的一般性原则。
一、车刀几何角度对切削力的影响在金属切削时,刀具切入工件,将多余材料从工件上切除会产生强烈的力的作用,这些力统称为切削力。
切削力主要来源于被加工材料在发生弹性和塑性变形时的抗力和刀具与切屑及工件表面之间的摩擦作用。
根据切削力产生的作用效果的不同,可将切削力分解成三个相互垂直方向的分力。
它们分别是:主切削力Fz,进给抗力Fx和切深抗力Fy,其中Fz是切削总力Fr沿主运动切向分解而得,是计算车刀强度,设计机床零件,确定机床功率的主要依据;Fx也叫轴向力,它是Fr沿工件轴向的分力,是设计进给机构,计算车刀进给功率所必需的;Fy也叫径向力,它是Fr沿着工件径向的分力,它不消耗机床功率,但是机床或工艺系统刚度不足时,容易引起振动。
(一)角度ro对切削力的影响前角ro增大,剪切角Φ随着增大,金属塑性变形减小,变形系数ξ减小,沿前刀面的摩擦力减小,因此切削力减小。
但对于脆性材料而言,前角ro的变化不会对车削力产生较大的影响,这是因为脆性材料在车削时,切屑变形和加工硬化都很小,变形抗力自然会随着减小。
同时,实验还证明,前角ro的增大,对切削分力Fx、Fy的影响程度也不一样,当前角ro的增大,对Fx的影响较明显,而当当前角ro较小时,则对Fy的降低幅度更大些。
(二)主偏角Kr对切削力的影响主偏角Kr的改变,使得切削面积的形状和切削分力Fxy的作用方向改变,从而使切削力也随之变化。
实验证明。
主偏角Kr增大,切削厚度也随之增大,切屑变厚,切削层的变形减小,因此主切削力也随之减小。
但当Kr增大到60°-75°后,Fz又随着Kr的增大而有所回升,这是因为此时刀尖圆弧所占的切削工作比例增大,使切屑变形和排屑阻力增大,从而又使主切削力Fz增大。
根据切削力分解公示:Fy=FxycosKr; Fx= FxysinKr可知,主偏角Kr增大,使Fy减小,Fx增大,这有利于减轻工件的变形和系统的振动。
因此,在工程上我们往往采用较大主偏角的车刀切削细长轴类零件,来减小径向分力Fy。
(三)刃倾角λs对切削力的影响刃倾角λs对切削力Fz影响很小,但对进给抗力Fx和切深抗力Fy的影响较大。