橡胶配方设计第二章章节资料文档
橡胶配方设计综合实验内容及操作步骤(doc 9页)

橡胶配方设计综合实验内容及操作步骤(doc 9页)高分子材料与工程专业实验橡胶配方设计综合实验实验报告班级: 08030342班硬脂酸SA 工业品0.8~1.2高耐磨炭黑HAF 工业品5~30N-芳基-N-烷基对苯二胺4010NA工业品1~32、实验用仪器及设备(1)开放式炼塑机(SK-160B)辊筒工作直径=160mm,辊筒工作长度=320mm,前辊转速=24.0r.p.m,后辊转速=17.8r.p.m,最大辊间距=4.5mm,最小压片厚度=0.2mm。
一次加料量=100~200g,辊筒最高加热温度≤200℃(2)平板硫化机(XKLB-25D)额定表压=145kg/cm²,油缸活塞直径D=160mm,电热板面积=360*360mm,模板最大加热温度≤200℃。
(3)密炼机混炼设备(HL-200型)(4)橡胶硬度计(5)万能拉伸测试仪一、实验工艺条件的预定1、材料配方的确定一原料名称简称成分质量/g丁腈橡胶NR 200邻苯二甲酸二辛酯DOP 10硫磺S 4四甲基秋兰姆二硫化物TMTD 1氧化锌ZnO 10硬脂酸SA 2高耐磨炭黑HAF 10N-芳基-N-烷基对苯二胺4010NA4二原料名称简称成分质量/g 丁腈橡胶NR 200 邻苯二甲酸二辛酯DOP 10硫磺S 4 四甲基秋兰姆二硫化物TMTD 1 氧化锌ZnO 10 硬脂酸SA 2 高耐磨炭黑HAF 20N-芳基-N-烷基对苯二胺4010NA4三原料名称简称成分质量/g 丁腈橡胶NR 200 邻苯二甲酸二辛酯DOP 10 硫磺S 4 四甲基秋兰姆二硫化物TMTD 1 氧化锌ZnO 10硬脂酸SA 2 高耐磨炭黑HAF 30N-芳基-N-烷基对苯二胺4010NA4四原料名称简称成分质量/g丁腈橡胶NR 200邻苯二甲酸二辛酯DOP 10硫磺S 4四甲基秋兰姆二硫化物TMTD 1氧化锌ZnO 10硬脂酸SA 2高耐磨炭黑HAF 40N-芳基-N-烷基对苯二胺4010NA4五原料名称简称成分质量/g 丁腈橡胶NR 200 邻苯二甲酸二辛酯DOP 10 硫磺S 4 四甲基秋兰TMTD 1姆二硫化物氧化锌ZnO 10 硬脂酸SA 2 高耐磨炭黑HAF 50N-芳基-N-烷基对苯二胺4010NA42、塑炼工艺条件的确定塑炼温度: 80℃。
橡胶配方设计整理
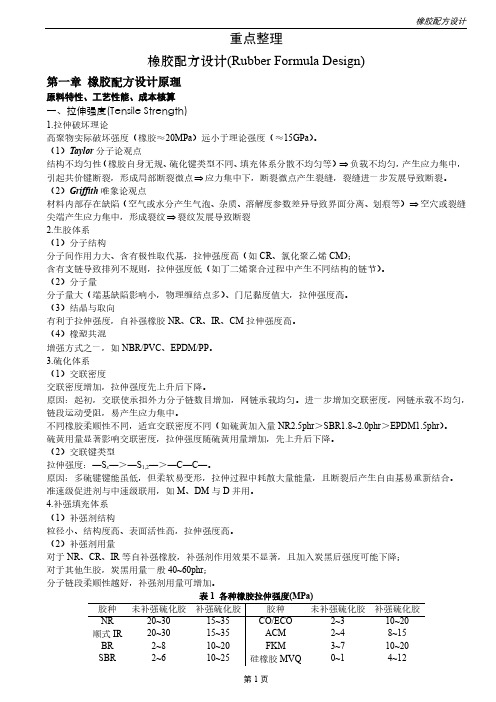
重点整理橡胶配方设计(Rubber Formula Design)第一章橡胶配方设计原理原料特性、工艺性能、成本核算一、拉伸强度(Tensile Strength)1.拉伸破坏理论高聚物实际破坏强度(橡胶≈20MPa)远小于理论强度(≈15GPa)。
(1)Taylor分子论观点结构不均匀性(橡胶自身无规、硫化键类型不同、填充体系分散不均匀等)⇒负载不均匀,产生应力集中,引起共价键断裂,形成局部断裂微点⇒应力集中下,断裂微点产生裂缝,裂缝进一步发展导致断裂。
(2)Griffith唯象论观点材料内部存在缺陷(空气或水分产生气泡、杂质、溶解度参数差异导致界面分离、划痕等)⇒空穴或裂缝尖端产生应力集中,形成裂纹⇒裂纹发展导致断裂2.生胶体系(1)分子结构分子间作用力大、含有极性取代基,拉伸强度高(如CR、氯化聚乙烯CM);含有支链导致排列不规则,拉伸强度低(如丁二烯聚合过程中产生不同结构的链节)。
(2)分子量分子量大(端基缺陷影响小,物理缠结点多)、门尼黏度值大,拉伸强度高。
(3)结晶与取向有利于拉伸强度,自补强橡胶NR、CR、IR、CM拉伸强度高。
(4)橡塑共混增强方式之一,如NBR/PVC、EPDM/PP。
3.硫化体系(1)交联密度交联密度增加,拉伸强度先上升后下降。
原因:起初,交联使承担外力分子链数目增加,网链承载均匀。
进一步增加交联密度,网链承载不均匀,链段运动受阻,易产生应力集中。
不同橡胶柔顺性不同,适宜交联密度不同(如硫黄加入量NR2.5phr>SBR1.8~2.0phr>EPDM1.5phr)。
硫黄用量显著影响交联密度,拉伸强度随硫黄用量增加,先上升后下降。
(2)交联键类型拉伸强度:—S x—>—S1,2—>—C—C—。
原因:多硫键键能虽低,但柔软易变形,拉伸过程中耗散大量能量,且断裂后产生自由基易重新结合。
准速级促进剂与中速级联用,如M、DM与D并用。
4.补强填充体系(1)补强剂结构粒径小、结构度高、表面活性高,拉伸强度高。
橡胶配方资料大全(doc 25页)

合计161 100.00 100.00 80.5 天然橡胶(NR)基础配方原材料名称NBC标准试样编号质量份原材料名称NBC标准试样编号质量份NR 氧化锌硬脂酸—37037210052防老剂PBN促进剂DM硫磺377373371112.5注:硫化时间为140℃×10min,20min,40min,80min。
NBS为美国国家标准局编写丁苯橡胶(SBR)基础配方原材料名称NBC标准试样编号非充油SBR配方充油SBR配方充油量25phr充油量37.5phr充油量50phr充油量62.5phr充油量75phr非充油SBR 充油SBR氧化锌硬脂酸硫磺炉法炭黑促进剂NS ——370372371378384100—311.75501—1253.751.252.1962.501.25—137.54.121.382.4268.751.38—1504.51.52.63751.5—162.54.881.632.8581.251.63—1755.251.753.0687.51.75Phr指每百质量份橡胶的分量数注:硫化时间为145℃×25min,35min,50min 氯丁橡胶(CR)基础配方原材料名称NBC标准试样编号纯胶配方半补强炉黑(SRF)配方CR(W型) 氧化镁硬脂酸SRF氧化锌—37637238237010040.5—510041295促进剂NA-22 防老剂D —3770.3520.52注:硫化时间为150℃×15min,30min,60min 丁基橡胶(IIR)基础配方原材料名称NBC标准试样编号纯胶配方槽黑配方高耐磨炭黑(HAF)配方IIR氧化锌硫磺硬脂酸促进剂DM 促进剂TMTD 槽发炭黑HAF —37037137237337437537810052——1——1005230.5150—10031.751—1—50注:硫化时间为150℃×20min,40min,80min;150℃×25min,50min,100min丁腈橡胶(NBR)基础配方原材料名称NBC标准试样编号瓦斯炭黑配方NBR氧化锌硬脂酸硫磺促进剂DM 瓦斯炭黑—370372371373382100511.5140注:硫化时间为150℃×10min,20min,80min顺丁橡胶(BR)基础配方原材料名称NBC标准试样编号HAF配方BR氧化锌硫磺硬脂酸促进剂NS —37037137238410031.520.9HAF ASTM型103油378—6015注:硫化时间为145℃×25min,35min,50min异戊橡胶(IR)基础配方原材料名称NBC标准试样编号HAF配方IR氧化锌硫磺硬脂酸促进剂NSHAF —37037137238437810052.2520.735注:硫化时间为15℃×20min,30min,40min,60min。
NBR橡胶的配方设计精选文档

N B R橡胶的配方设计精选文档TTMS system office room 【TTMS16H-TTMS2A-TTMS8Q8-NBR密封件配方设计一、常用橡胶用途及性能:1051 丙烯晴含量 41% ML75 SG 稍污染型1052 丙烯晴含量 33% ML50 SG 非污染型1053 丙烯晴含量 29% ML60 SG 非污染型1052M30丙烯晴含量33% ML30 SG 非污染型DN223丙烯晴含量 33%ML 35 SG非污染型丙烯晴含量 50% ML75 SG非污染型1965 丙烯晴含量 19% ML65 SG 非污染型DN401丙烯晴含量 18% ML78 SG 非污染型1043丙烯晴含量 29%ML 80 SG稍污染型N230SL丙烯晴含量 35% ML42 SG 非污染型N260S丙烯晴含量 15% ML62 SG 非污染型1052M40丙烯晴含量 33% ML40 SG 非污染型特性:1、ACN↑耐油性好,非极性或弱极性矿物油,植物油,液体燃料和有较高的稳定性。
2、耐热性优于NR SBR CR 可在120℃下长期使用。
3、属半导体材半料。
4、耐油与压缩永久变形平衡,耐油性与电性能平衡。
5、丙烯晴含量对NBR分类:ACN% 43%以上极高ACN%NBR36-42%以上高31-35% 中高25-30 中24%以下低总结:ACN%越高,耐油性愈好耐热性改善,但TG差,ACN%越低,低温性好,但耐油偏差。
且ML会升高,压缩永久变形好。
一般ACN%在29%可过F17.过F19 须用1965或DN401生胶。
二、共聚物组成(ACN含量)对NBR的影响.项目ACN含量特点密度低→→→高大加工性(流动性)低→→→高良好硫化速度低→→→高快定伸应力、拉伸强度低→→→高大硬度低→→→高大耐磨性低→→→高良好永久变形低→→→高大耐油性低→→→高良好耐化学药品性低→→→高良好耐热性低→→→高良好和极性聚合物的相容低→→→高大弹性低→→→高小耐寒性低→→→高差透气性低→→→高差和增塑剂操作油的相容低→→→高差三、硫化体系一般NBR配方采用半有效硫化体系,例如:TT/CZ,这种硫化体系,具有耐热性较好的效果,SUL/TS压缩歪和焦烧最优。
橡胶配方设计--02-1

硬度测定:邵尔A 7.硬度测定:邵尔A型 磨耗测定: 8.磨耗测定: 磨耗体积
0-100度 100度
)/ρ, 61Km Km, V=(m前-m后)/ρ,cm3/1.61Km,
滚筒磨耗
磨耗指数= 磨耗指数=V标/V试
阿克隆磨耗
疲劳的测试: 9.疲劳的测试: 压缩疲劳: (1)压缩疲劳:1)温升 2)变形 屈挠龟裂: (2)屈挠龟裂:裂口大小及 出现裂口的时间 拉伸疲劳: (3)拉伸疲劳:疲劳寿命计算 10. 10.压缩永久变形 )]*100 100% K=[(h0-h2)/(h0-h1)]*100% 11. 11.粘弹性 (1)摆锤式回弹仪 (2)蠕变 (3)应力松弛 动态粘弹性能(DMA) 动态模量及tgδ (DMA)、 (4)动态粘弹性能(DMA)、动态模量及tgδ
硫化橡胶的性能测试
P/bh, 1.拉伸强度 σ=P/bh,Mpa 定伸应力, 2.定伸应力,Mpa 100% 300% 100%,300%,Mpa 3.扯断伸长率 ,% є=[(L1-L0)/L0]*100% = ]*100 100% 扯断永久变形: 4.扯断永久变形: S=(L2- L0)/ L0 ,% 撕裂强度: 5.撕裂强度: P/h, Φ=P/h,KN/m 6.有效弹性和滞后损失
橡胶配方设计原理及工艺
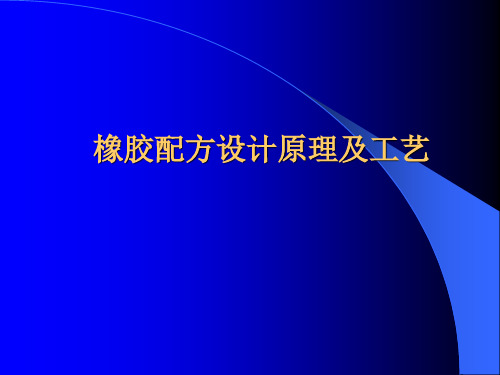
3制定基本配方和性能试验项目 制定基本配方步骤如下: 1确定生胶的品种和用量; 根据主要性能指标确定主体胶料品种;用量与含胶率有关。 2)确定硫化体系。根据生胶的类型和品种,硫化工艺及产品性能要求来确定。 3)确定补强剂品种和用量。根据胶料性能 比重及成本确定。 4)确定软化剂品种和用量。根据生胶及填料种类,胶料性能及加工条件确定。 5)确定防老剂品种和用量。根据产品使用环境的条件来确定。 6)确定其它专用配合剂的品种和用量。如着色剂,发泡剂等)
20˚C
75˚C
150˚C
偏差加大:包容胶活动性增强所致;
Ef/Eg
胶种
纯胶基本硬度
填料品种
估算硬度
NBR
44
FEF,HAF
+1/2份数
CR
44
ISAF
+1/2份数+2
NR
40
SAF
+1/2份数+4
SBR
40
SRF
+1/3份数
IIR
35
陶土
+1/4份数
碳酸钙
+1/7份数
油
-1/2份数
填料与硬度的关系
一 配方设计定义 橡胶材料是生胶与多种配合剂构成的多相体系; 橡胶制品的性能取决于橡胶分子本身;以及各种配合剂性质及它们之间的相互作用关系。 定义:根据产品的性能要求及工艺条件,合理选用原材料,制订各种原材料的用量配比关系的设计方法。 配方设计决定着产品质量、成本和加工性能。
现代橡胶配方设计

2、基本原则
(1)在不降低产品质量的情况下降低成本
(2)在保持成本不变的情况下提高产品的性能
3、一般原则
(1)满足制品的性能要求;(2)设计的配方易于加工
(3)原材料价廉易得; (4)重点设计主要性能
(5)充分考虑交互作用; (6)配方成本低,能耗低
(7)201配9/1方1/18尽可能简化
(8)符合环保与卫生要求
②体积分数配方计算:Vi%=mi/ρ i×[100/∑(mi/ ρi)]
③生产配方计算:Mi=mi×(Q/ ∑mi)
2019/11/18
含配合剂母胶的配方计算:
例如:促进剂M母胶配方
NR
100
促进剂M 20
ZnO
5
合计
125
X促M母=1/(20/125)=6.25份 母胶中: XNR=6.25×(100/125)=5份 XZnO=6.25× (5/125)=0.25份
1. 质量份数表示(mi): 以生胶分数为100份,其余配合剂相应质量份数表示。
2. 质量百分数( mi % ):= mi /∑mi ×100% 以胶料总质量为100,生胶和配合剂质量所占比例数来 表示,主要用于计算原材料质量成本和含胶率。
3. 体积百分数表示(Vi% ): = Vi /∑Vi ×100% 以胶料总体积为100,生胶和配合剂体积所占比例数来 表示,主要用于计算原材料体积成本。
配方1的炼胶成本:P炼胶1=1.2×1.2=1.44(元) 配方1硫化成本:P硫化1=(4/60)×10=0.67(元) 总成本:P总1= P胶1+ P炼胶1+ P硫化1=19.32(元) 2每019件/11制/18 品的利润:R1=P价格—P总1= 21.6-19.32=2.28(元)
橡胶配方设计
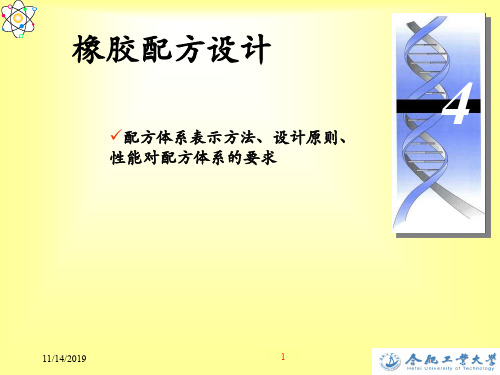
11/14/2019
20
4.2.2 配合体系与撕裂强度的关系
指将带有切口的试片撕裂时所需的最大力,其单位为N/m。 ⑴ 橡胶品种
天然橡胶、氯丁橡胶等结晶性橡胶的撕裂性较好。几种橡胶的抗 撕裂性强弱顺序是:NR>CR>SBR>NBR ⑵ 硫化体系 多硫键具有较高的撕裂强度。 ⑶ 填充体系 粒子细、活性大的炭黑、白炭黑补强时,撕裂强度明显改善;炭 黑用量一般在50~60phr时可获得最高撕裂强度。但用量过大时撕 裂强度反而下降。 ⑷ 增塑体系 适当加入增塑剂有助于撕裂强度的提高,主要是一些树脂类如古 马隆树脂、酚醛树脂等。
炼性主要取决于配合剂与橡胶之间的浸润性。 疏水性填充剂,如炭黑容易被橡胶所浸润,混炼性能较好;亲水
性填充剂,如碳酸钙、陶土、白炭黑等,不易被橡胶浸润,混炼 性能较差。可通过化学改性,或加入表面活性剂加以改进。 增塑剂与橡胶的相容性一般较好,易于分散。
11/14/2019
31
3 配合体系对包辊性能的影响 胶料的包辊性能主要取决于生胶的强度和粘着性能。 影响生胶强度的因素包括生胶的分子量及其拉伸结晶性能。天
所谓配方设计就是如何确定这种比例关系,是橡胶制品生产 过程中的关键环节。
11/14/2019
2
4. 1.1 橡胶配方设计的原则
橡胶配方设计的任务是力求使橡胶制品在性能、成本和工艺可行 性三个方面取得最佳的综合平衡。通常,要遵循以下几条原则:
⑴ 充分了解制品的性能要求、使用条件;半成品的性能一般应 高于成品指标的15%。
然橡胶具有最好的包辊性能,乳聚合成橡胶次之,溶聚的,特别 是分子量分布较宽的橡胶包辊性能较差。改善的途径有以下几种 ⑴ 通过加入活性、结构性高的填充剂,如炭黑、白炭黑等增加生 胶的强度,进而提高胶料地包辊性能。 ⑵ 加入增粘性增塑剂 如高芳烃操作油、松焦油、古马隆树脂、 酚醛树脂等。 ⑶ 与少量天然橡胶并用。
橡胶配方设计基础-2+3+4+5+6+7+8
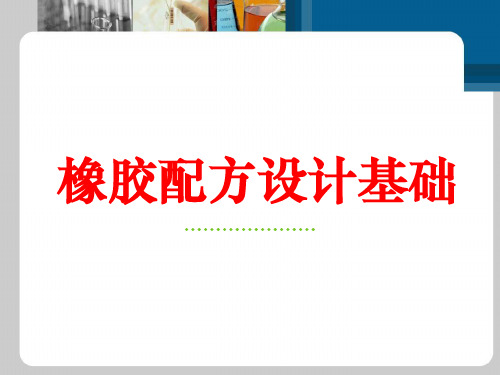
Vi% = Vi /∑Vi ×100%
2. 配方的表示形式
4. 生产配方(Mi ):
取胶料的总质量等于炼胶机的装胶量
Q,各组分以实际用量表示。
M i = Q× m i / ∑ m i
配方换算
①质量分数配方计算:mi=mi/∑mi ②体积分数配方计算:
Vi=mi/ρi[∑(mi/ρi)]
③生产配方计算:Mi=Qi×(m/∑mi)
胶的粘度,改善加工工艺性能。
硫化:
“硫化”因最初的天然橡胶制品用 硫磺作交联剂进行交联而得名,随 着橡胶工业的发展,现在可以用多
种非硫磺交联剂进行交联。
硫化:
因此硫化的更科学的意义应是“交
联”或“架桥”,即线性高分子通
过交联作用而形成的网状高分子的
工艺过程。
硫化过程:分为四个阶段:
硫化过程:
橡胶配方设计基础
1、概 述
橡胶配方设计:根据橡胶产品的
性能要求和工艺条件,合理地选用
原材料,并确定各种原材料的用量 配比关系,使得胶料的物性、工艺
性和成本三者取得最佳平衡。
橡胶配方:生胶和多种配合剂按照
一定比例的一种组合。
五大体系:
生胶体系 ( 高聚物单用或并用 ) :母
体材料或基体材料
橡胶配方的表示形式
原材料名称, (g/cm3) NR 0.92 硫磺 2.05 促进剂M 1.42 ZnO 5.57 St 0.92 C.B. 1.80 合计 基本配 体积分 质量分数 生产配 方,质量 数配方 配方/% 方,kg 份 /% 100 62.20 76.70 50.0 3 1.86 1.03 1.5 1 0.60 0.50 0.5 5 3.10 0.63 2.5 2 1.24 1.54 1.0 50 31.00 19.60 25.0 161 100 100 80.5
橡胶配方设
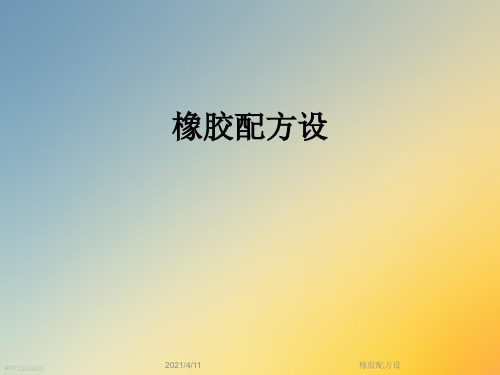
3.拉断伸长率 ,%
є=[(L1-L0)/L0]*100% 4.扯断永久变形:
S=(L2- L0)/ L0 ,% 5.撕裂强度:
Φ=P/h,KN/m
PPT文档演模板
橡胶配方设
6.有效弹性和滞后损失
PPT文档演模板
橡胶配方设
7.硬度测定:邵尔A型 0-100度 8.磨耗测定:
磨耗体积 V=(m前-m后)/ρ, cm3/1.61Km,
抗静电 106~10Ω·cm
高分子导电、导电填料
18.扩散与渗透性能
1)透气性:内胎、瓶塞
2)透湿性和透水性:防水卷材、水坝、房屋
3)油扩散:密封件
PPT文档演模板
橡胶配方设
19.耐液体:耐油、耐化学溶剂、耐酸碱 体积、质量变化率及物理性质的变化率
体积变化百分数△V(%)按下式计算:
△V=
×100
PPT文档演模板
橡胶配方设
四、橡胶配方的组成及表示方法
橡胶配方简单地说,就是表示生胶和配合剂用量 配比表。表示方法:
1. 质量份数表示:以生胶分数为100,其余配合剂相 应质量份数表示。
2. 质量百分数:以混炼胶料总质量为100,生胶和配 合剂所占比例数来表示。
3. 体积百分数表示:即以胶料的总体积为100%,将 基本配方中生胶及各种配合剂的重量分数分别除以各 自的相对密度,求出体积份数。
橡胶配方设
五、橡胶配方设计影响因素
• 原材料应用 • 加工工艺 • 使用性能 • 产品结构
PPT文档演模板
橡胶配方设
1、 原材料应用
生胶(高聚物单用或并用):母体材料或基体材料
硫化体系:与橡胶大分子起化学作用,使橡胶由线 型大分子变为三维网状结构,提高橡胶性能、 稳定形态的体系。
橡胶的配方设计
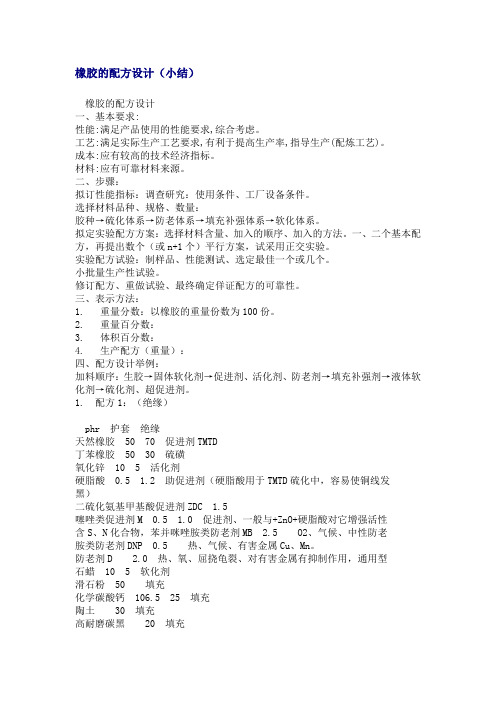
橡胶的配方设计(小结)橡胶的配方设计一、基本要求:性能:满足产品使用的性能要求,综合考虑。
工艺:满足实际生产工艺要求,有利于提高生产率,指导生产(配炼工艺)。
成本:应有较高的技术经济指标。
材料:应有可靠材料来源。
二、步骤:拟订性能指标:调查研究:使用条件、工厂设备条件。
选择材料品种、规格、数量:胶种→硫化体系→防老体系→填充补强体系→软化体系。
拟定实验配方方案:选择材料含量、加入的顺序、加入的方法。
一、二个基本配方,再提出数个(或n+1个)平行方案,试采用正交实验。
实验配方试验:制样品、性能测试、选定最佳一个或几个。
小批量生产性试验。
修订配方、重做试验、最终确定佯证配方的可靠性。
三、表示方法:1. 重量分数:以橡胶的重量份数为100份。
2. 重量百分数:3. 体积百分数:4. 生产配方(重量):四、配方设计举例:加料顺序:生胶→固体软化剂→促进剂、活化剂、防老剂→填充补强剂→液体软化剂→硫化剂、超促进剂。
1. 配方1:(绝缘)phr 护套绝缘天然橡胶 50 70 促进剂TMTD丁苯橡胶 50 30 硫磺氧化锌 10 5 活化剂硬脂酸 0.5 1.2 助促进剂(硬脂酸用于TMTD硫化中,容易使铜线发黑)二硫化氨基甲基酸促进剂ZDC 1.5噻唑类促进剂M 0.5 1.0 促进剂、一般与+ZnO+硬脂酸对它增强活性含S、N化合物,苯并咪唑胺类防老剂MB 2.5 O2、气候、中性防老胺类防老剂DNP 0.5 热、气候、有害金属Cu、Mn。
防老剂D 2.0 热、氧、屈挠龟裂、对有害金属有抑制作用,通用型石蜡 10 5 软化剂滑石粉 50 填充化学碳酸钙 106.5 25 填充陶土 30 填充高耐磨碳黑 20 填充配方2:材料配比/phrCR232 100 氯丁橡胶氧化镁(特级) 4 硫化剂FEF碳黑 25 快压出炉黑SRF碳黑 15 半补强炉黑陶土 50 填充剂氢氧化铝 30 阻然剂氧化锌 5 硫化剂NA—22 1.2 硫脲类促进剂DM 0.5 硫化延迟剂、促进剂DM石蜡 3 软化剂硬脂酸 0.5 软化剂DOP 10 增塑剂、临苯二甲酸二辛脂防老剂ODA 4 防老剂OD、胺类防老剂、P396手册。
阻燃硅橡胶的配方设计

阻燃硅橡胶的配方设(陕理工材料科学与工程学院高分子081班,陕西汉中 723003)指导教师:王铎[摘要]: 硅橡胶具有许多优异的性能,例如具有耐高、低温性能、疏水性、具有适当的透气性等。
尤其是氧指数较以碳为主链的橡胶高, 在燃烧时热释放速率低,火焰传播速度慢, 无滴落,且纯硅橡胶燃烧时几乎不生成有毒气体, 在燃烧后会在表面形成陶瓷化的碳硅层,能阻止热、氧的交换和内部可燃物向外扩散与热、氧接触。
但其但耐密闭老化特别在有湿气条件下的老化性能不够好;机械强度在橡胶材料中是最差的,而且存在可燃的缺陷,特别是其容易阴燃,存在潜在的燃烧风险。
向硅橡胶中掺入阻燃剂, 即可赋予硅橡胶难燃或自熄特性和较强的拉伸撕裂等性能.通过多次实验讨论三氧化二锑、氢氧化铝等辅料用量对硅橡胶自熄时间,续燃性能的影响情况,设计出阻燃硅橡胶的最优配方,由此制造出具备较好的阻燃效果和较强的拉伸撕裂等性能的硅橡胶,增加其应用范围。
结果表明:当100份硅橡胶中氢氧化铝的用量为80份时,硅橡胶的燃烧氧指数( OI 值) 可达30%, 但力学性能却受到严重损害, 发烟量为B 级; 氢氧化铝/ 三氧化二锑并用时,HTV 硅橡胶的性能较理想;当(氢氧化铝+三氧化二锑)用量为50份时,硅橡胶的OI值为31%、拉伸强度为613MPa、扯断伸长率为660%、撕裂强度为2317 kN/ m、邵尔A 硬度为57 度,但发烟量为C级;关键词:硅橡胶;阻燃;氢氧化铝;三氧化二锑Study on the link of aluminium alloy die-forgingtechnologyZhao Ming(Grade03,Class1,Major control materials,Material Institute,Shaanxi University of Technology,Hanzhong 723003,Shaanxi)Tutor: Zhang Hui,Ma ZhenlongAbstract:Aluminum alloy with low density, good processing properties, corrosion resistance, strength and stiffness higher than the merits, to a greater degree of material savings and reduce weight, in forging hammer, screw press, upended aircraft and aircraft bore forged various forging equipment. Based on the analysis of the aluminum alloy forging features easy forging process and the deficiencies should be noted,under the open-die forging parts theory and linkage map, combining link forged aluminum alloy technology and features, bicycle link on the forging process for a specific analysis, determine a reasonable link alloy forging technology and forging process parameters. Drawing rough calculation section map, decide on the size and material blocking step of the process and equipment, rational design of the processes and mapping die mold map. Forging the same time that the process should pay attention to the issue and the relevant preventive measures.Key words:aluminium alloy; link; forge technology; die design目录中文摘要Abstract1 引言 ......................................................................................................................... 错误!未定义书签。
第2章橡胶的硫化
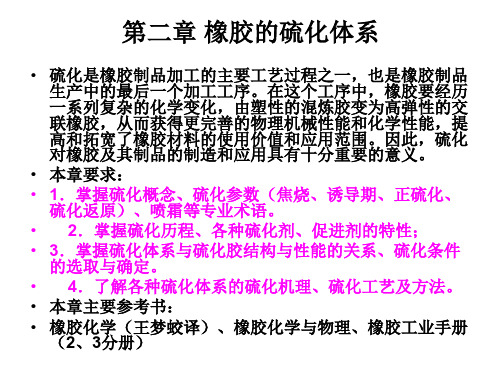
• 二.硫黄的裂解和活性 • 硫在自然界中主要以菱形硫(Sα-硫)和单斜晶硫
(Sβ-硫)的形式存在,前者作为硫化剂使用。硫 的元素形式为S8,一个分子中有8个硫,形成一种 叠环,这种环状的硫黄分子的稳定性较高,不易 反应,为使硫易于反应,必须使硫环裂解,硫环 获得能量后分解,裂解的方式可能是均裂成自由 基,也可能是异裂成离子。
• 这一阶段的长短取决于所用配合剂,特别 是促进剂的种类。
• 另外,不同的硫化方法和制品对焦烧时间 的长短亦有不同要求
二 .欠硫阶段(又称预硫阶段)
• 硫化起步与正硫化之间的阶段称为欠硫阶 段。
• 在此阶段,由于交联度低,橡胶制品应具 备的性能大多还不明显。尤其是此阶段初 期,胶料的交联度很低,其性能变化甚微, 制品没有实用意义。但到了此阶段的后期, 制品轻微欠硫时,尽管制品的抗张强度, 弹性,伸长率等尚未达到预想水平,但其 抗撕烈性,耐磨性和抗动态裂口性等则优 于硫化胶料。因此,如果着重要求后几种 性能时,制品可以轻微欠硫。
(2)对某些需要塑炼的胶种,塑炼未达要求,可塑性太 低,胶质过硬,导致炼胶时急剧升温。炼胶机或其它 辊筒装置(如返炼机、压延机)辊温太高,冷却不够, 也可能导致现场焦烧。
(3)混炼胶卸料时出片太厚,散热不佳,或未经冷却,即仓 促堆积存放,加上库房通风不良、气温过高等因素,造 成热量积累,这样也会引发焦烧。
SxH
C H 3 C H 2 CC HC H 2
C H 3 C H 2 CC HC H
橡胶分子与硫化剂及其他配合剂之间发生的一系列化学反 应以及在形成网状结构时伴随发生的各种副反应。可分为 三个阶段: • 1.诱导阶段 硫化剂、活性剂、促进剂之间的反应,生 成活性中间化合物,然后进一步引发橡胶分子链,产生可 交联的自由基或离子。 • 2.交联反应阶段 可交联的自由基或离子与橡胶分子链之 间产生连锁反应,生成交联键。 • 3.网构形成阶段 交联键的重排、短化,主链改性、裂解。
橡胶配方设计第二章.ppt
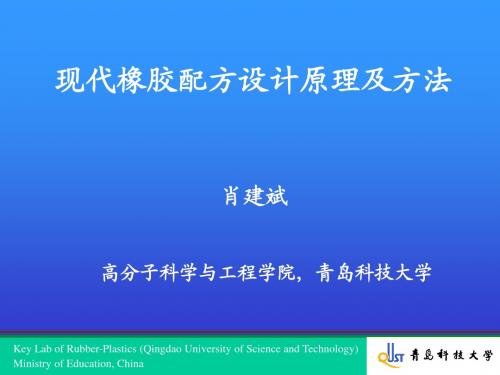
光滑路面:
卷曲、疲劳磨耗
I=K[KμE/σ0]t[P/E]1+βt
由上式可知:磨耗性从本质上说取决于它的
拉伸强度、弹性模量,疲劳性和摩擦特性等。
具体情况具体分析:两种磨耗情况同时考虑,
如定伸应力或硬度的影响。
1、生胶与耐磨性的关系:
(1)PU最耐磨,并且强度高 在多数场合,高压且要求耐磨性时考虑PU 1)浇铸轮胎 2)鞋底 (2)BR:玻璃化转变温度低,摩擦系数低,动 态模量高,耐磨性好;增加1,4结构含量,拉伸 强度和弹性都增加,磨耗体积减小。后期老化后 反而降低了磨耗性,“抗掉块能力差”。 措施:增加BR中CB用量和降低硫化程度 (3)SBR:共轭体系存在时提高耐磨性 (4) NBR: 优良的 抗湿滑性及耐磨性 (5)TPI的耐磨性优于NR
在周期形变中不可逆形变产生的滞后损失 转化为热,亦促进了橡胶的疲劳破坏过程。
氧及臭氧的侵蚀
以断裂力学为基础研究橡胶的疲劳性能
Rivlin和Thomas提出:dc/dn = BGβ
G=2KCW0,W0 =E/2(λ2+2/λ-3)
可以通过积分式得到: LogN=-β[logf(λ)+log(λ2+2/λ-3)] +[logG-log(β-1)-(β-1)logC0-βlogE] 得到疲劳寿命与橡胶裂纹增长特性、形变幅 度、初始裂纹或缺陷的尺寸的定量关系。
4.软化体系
少量填加软化剂能改善胶料的拉伸形变,有 利于撕裂; 用量较多时,降低分子链间作用力,撕裂强 度降低。
三、 拉断伸长率(elongation at break)
1、橡胶分子链柔顺性好、生胶强度高、弹性变形 能力大,胶料的拉断伸长率高。 NR、CR、IR、IIR 2、硫化体系: 1) 拉断伸长率随交联密度增加而降低,降低交联 剂的用量或通过交联不足来达到高的伸长率。 2) C-SX-C> C-S2-C> C-S-C>C-C 3.补强填充体系 选用粒径大,结构度低的CB,伸长大; 用量越多,拉断伸长率越低 填料选用亲和力好的,或采用偶联剂改性 4.增加软化剂用量,显著提高硫化胶的拉断伸长率
特种橡胶配方设计方案(PPT 53页)

第五节 导电橡胶
定义:一般把体积电阻率小于105Ω·cm的 橡胶称为导电橡胶。体积电阻率小于 1Ω·cm的橡胶称为超导电橡胶。
②纤维素类 纤维素-丙烯腈接枝聚合物,羧甲 基纤维素的交联产物等
③聚乙烯醇类 PVA的交联产物,丙烯腈-乙酸 乙烯酯的共聚物的皂化产物
④丙烯酸类 聚丙烯酸盐,甲基丙烯酸甲酯-乙 酸乙烯酯的共聚物的皂化产物
⑤聚亚烷基醚类 聚乙二醇与二丙烯酯交联的产 物
⑥马来酸酐类 异丁烯-马来酸酐的交替共聚物
对吸水树脂的技术要求:
CaCO3 陶土
1.522
S
MgCO3
光折射率(n) 1.56~1.59 1.90 1.55 1.51~1.60 1.53 1.59~224 1.50~1.525
常用透明填料是白炭黑和MgCO3
ZnO对R的遮盖力大,可选透明ZnO, (碳酸锌)用量1.5-3份。
3、硫化体系 S用量<2份,否则颜色暗,可用过氧化物 促进剂:主促进剂为M,副促进剂H 4、软化体系
CPE
21-23
PS
17-18
PVC
45-60
聚合物 聚酰胺 聚酰亚胺 EPDM CSM CR SiR PTFE
OI 22-28 36.5 21.9 25.1 26.3 26-39 795
各类橡胶的氧指数
橡胶名称
天然橡胶 顺丁橡胶 丁苯橡胶 丁基橡胶 丁腈橡胶 氯丁橡胶 氯磺化聚乙烯橡胶 乙丙橡胶
具有阻燃性的橡胶和塑料:
含氯材料-如CR、CSM、FKM、PVC、CPE、 ECO、SiR
2、填充体系 填料一般不采用炭黑、而采用硅酸盐等
浅色填料。
3、软化增塑体系 软化增塑剂一般易燃、在阻燃橡胶中应
- 1、下载文档前请自行甄别文档内容的完整性,平台不提供额外的编辑、内容补充、找答案等附加服务。
- 2、"仅部分预览"的文档,不可在线预览部分如存在完整性等问题,可反馈申请退款(可完整预览的文档不适用该条件!)。
- 3、如文档侵犯您的权益,请联系客服反馈,我们会尽快为您处理(人工客服工作时间:9:00-18:30)。
物性的要求
工艺条件分析 成本合算
加工性能 效益
第一节 配方设计与硫化橡胶物性的关系
一.拉伸强度(tensile strength)
高聚物理论强度=5×1014根分子链/cm2×3×10-9N/键 =15×105N/cm2=15×103N/mm2=15GPa
硫化胶实际强度为20MPa左右
1.拉伸破坏理论: 1) Taylor理论,分子论的观点:分为三个阶段:
由于结构的不均一性,负载分布不均匀,结果导 致共价键上应力集中,形成局部断裂微点(破坏核);
破坏核的进一步应力集中影响导致亚微裂缝; 亚微裂缝聚集成大的主裂缝,从而最终断裂。 2) Griffith理论:唯象论的观点
由于在材料的表面和结构中存在某些缺陷(气泡, 杂质,界面分离,划痕等),容易造成空穴和裂缝, 使应力集中于裂缝的尖端处,裂缝扩展导致断裂。
2. Tensile Strength与橡胶结构的关系
(1) 分子间作用力大,拉伸强度高: 主链上有极性取代基 CR、 CM
(2) 分子量大,门尼值大,Tensile 高 (3) 微观结构对Tensile的影响:CH2=CH-CH=CH2
支链导致排列不规则 (4) 结晶与取向对Tensile的影响
现代橡胶配方设计原理及方法
肖建斌
高分子科学与工程学院, 青岛科技大学
Key Lab of Rubber-Plastics (Qingdao University of Science and Technology) Ministry of Education, China
第二章 橡胶配方设计原理
原材料特性
(1) 交联密度
随交联密度增加,网链能够均匀承载, 强度上升(理想网络)。
继续增加交联度,(2) 交联类型
C-SX-C>C-S-C>C-C 促进剂选用M, DM与D并用较好
4.Tensile Strength与补强填充体系
1) 粒径越小,表面活性越大,结构性越高,补强效果 好
5.Tensile Strength与软化体系的关系
一般加入软化剂主要是改善加工性能,
但降低硫化胶的拉伸强度。
高粘度油类对拉伸强度有利:
芳烃油 SBR、NR、BR
直链烷烃 EPDM
PIB
IIR
DOP
NBR、CR
二、撕裂强度(tear strength)
撕裂强度为胶料单位厚度上的撕裂能,包括 材料的表面能 塑性形变损耗的能量 不可逆形变损耗的能量。
交联密度越大,定伸应力和硬度也随之增加 (2) 交联类型
C-C>C-S-C>C-SX-C(应力松弛倾向大) 3.定伸应力与填充体系 (1) 种类:
粒径小,结构度高,活性大 SAF>ISAF>HAF>FEF>GPF>SRF 白炭黑>滑石粉>陶土>CaCO3 (2) 用量:用量越多,定伸应力和硬度也随之增加
4.软化体系 少量填加软化剂能改善胶料的拉伸形变,有
利于撕裂; 用量较多时,降低分子链间作用力,撕裂强
度降低。
三、 拉断伸长率(elongation at break)
1、橡胶分子链柔顺性好、生胶强度高、弹性变形 能力大,胶料的拉断伸长率高。 NR、CR、IR、IIR
2、硫化体系: 1) 拉断伸长率随交联密度增加而降低,降低交联 剂的用量或通过交联不足来达到高的伸长率。 2) C-SX-C> C-S2-C> C-S-C>C-C
2) 对于NR 、CR、IR自补强(应力诱导结晶)橡胶, 补强剂的补强效果不明显;
3) 其它生胶: 一般炭黑用量为40~60phr
4) 加入白炭黑后,与炭黑补强胶料的力学性能相比有 所降低,加工性能也变差,在偶联剂的作用下,胶 料的加工性能及物性均有改善。
5) 补强树脂包括固马隆和酚醛树脂
6) 加入填充剂后,胶料的物理机械性能均呈现下降趋 势。
SBR 2~6 10~25 MVQ ~1
4~12
CR 10~30 10~30 CSM 4~10 10~24
IIR 8~20 8~23 CPE 4~10 10~25
EPDM 2~7 10~25 聚氨酯 20~50 20~60
NBR 3~7 10~30 HNBR 5~10 20~50
3.Tensile Strength与硫化体系的关系
(1) 分子量和分子量分布的影响 分子量越高,定伸应力和硬度越大, 分子量分布宽,定伸和硬度下降,
(2) 分子化学结构与定伸应力的关系 分子链有侧基或刚性,分子间作用力大
如 CR NBR PU ACM等极性橡胶适合制 作高定伸制品。另外定伸应力和硬度:SBR>BR
2.定伸应力与硫化体系 (1) 交联密度
3.补强填充体系 选用粒径大,结构度低的CB,伸长大; 用量越多,拉断伸长率越低 填料选用亲和力好的,或采用偶联剂改性
4.增加软化剂用量,显著提高硫化胶的拉断伸长率
四、定伸应力和硬度(modulus and hardness)
两者都表征产生一定形变(拉伸形变和压缩 形变)所需要的力 1.定伸应力与橡胶分子结构的关系
4.软化体系的粘度及用量可用来调整定伸及硬度
5.other methods
(1) 选 用 能 参 与 硫 化 反 应 或 与 大 分 子 产 生 某 种 化 学作用的添加剂, 丙烯酸类齐聚酯、甲基丙烯 酸盐较高的硬度、耐磨性、高强度、好的弹 性及粘合性。加工过程中是“临时增塑剂”,在过 氧化物引发下,齐聚酯接枝聚合。
1.生胶分子量大,结晶,内耗大的胶料, 如 NR CR IIR PU 撕裂强度高。
2.硫化体系: C-SX-C>C-S-C>C-C
传统S用量为2.0~3.0份为宜
3.补强体系: 1) 炭黑粒径小,抗撕裂强度增加 2) 使用各向同性的填料:CB,白炭黑,立德粉, ZnO,不宜用各向异性的填料:MgCO3 陶土 3) 使用表面改性剂或偶联剂
如NR 、CR、IR自补强(应力诱导结晶 (5) 橡塑共混 NBR/PVC EPDM/PP
各种橡胶的拉伸强度, MPa
胶种
未补强 补强硫 胶种 硫化胶 化胶
未补强 补强硫 硫化胶 化胶
NR
20~30 15~35 CO/ECO 2~3 10~20
IR
20~30 15~35 ACM 2~4 8~15
BR 2~8 10~20 FKM 3~7 10~20