基于MBD的三维数字化制造技术应用体系 MBD功能 2
基于MBD的三维数字化装配工艺设计及现场可视化技术应用

基于MBD的三维数字化装配工艺设计及现场可视化技术应用基于MBD的三维数字化装配工艺设计技术是现代航空数字化制造中的一门新兴学科,也是未来飞机三维装配工艺设计的发展趋势。
本文介绍了该技术主要通过对DELMIA、3DVIA Composer、CAPP等工艺设计、工艺仿真软件进行客户化定制和多系统集成应用,完成基于MBD三维产品模型的工艺分离面的划分、BOM重构、工艺仿真以及三维装配指令编制等工艺设计工作,并通过生产管理系统将已完成的工艺设计信息传递到生产现场实现可视化装配,打通了基于MBD的产品设计与工艺设计及现场可视化装配的技术路线。
MBD(Model-Based Definition)即基于模型的产品数字化定义,其特点是:产品设计不再发放传统的二维图纸,而是采用三维数字化模型作为飞机零件制造、部件装配的依据。
传统的二维工艺设计模式已经不能适应全三维设计要求。
随着现代计算机技术、网络技术、工艺设计软件技术的发展,以及协同平台的建立,为三维数字化装配工艺设计和并行工程奠定了基础。
1 三维数字化装配工艺设计及现场可视化系统通过采用达索公司三维数字化装配工艺设计平台DELMIA及3DVIA Composer解决方案,构建“数字化装配工艺设计和仿真系统”及“生产现场可视化系统”。
突破DELMIA二次开发及定制技术、3D制造过程仿真验证及优化技术、MBD技术、生产现场可视化技术、Windchill/DELMIA/EPCS/CAPP多系统集成技术等关键技术瓶颈,最终构建符合企业业务需求的“数字化装配工艺设计和仿真系统”及“生产现场可视化系统”。
缩短飞机装配周期,提高装配质量,全面提升飞机的数字化制造能力。
系统流程及集成架构如图1所示。
图1 系统流程及集成框架系统流程及集成工作思路如下:(1)Windchill企业数据管理系统是企业唯一合法的数据来源,管理着各种BOM信息。
通过接口程序,把PBOM以XML的格式输出。
MBD技术在飞机制造中的应用

MBD技术在飞机制造中的应用随着科技的不断发展,MBD(Model-Based Definition)技术以其独特的优势在飞机制造中发挥着越来越重要的作用。
本文将详细介绍MBD技术的概念、发展历程以及在飞机制造中的应用现状和未来发展趋势。
MBD技术是一种基于模型的定义方法,它利用三维模型来定义产品及其制造过程,包括产品设计、制造、检验等多个环节。
MBD技术的出现,使得产品设计不再受限于传统的二维图纸,而是通过三维模型进行定义,提高了设计效率和准确性。
MBD技术的发展历程可以追溯到20世纪90年代,随着计算机辅助设计(CAD)技术的不断发展,MBD 技术逐渐成熟并被广泛应用。
在飞机制造中,MBD技术得到了广泛应用。
以下是MBD技术在飞机制造中的主要应用:飞机设计:利用MBD技术,设计师可以在三维模型中直接进行设计,避免了传统二维图纸设计过程中可能出现的数据不一致、误解等问题,提高了设计效率和准确性。
飞机制造:MBD技术使得制造过程更加精细化、自动化和智能化。
通过MBD模型,可以更加准确地指导生产过程,提高生产效率和质量。
飞机管理:MBD模型可以用于对飞机制造过程中的各种数据进行分析和管理,提高了数据管理的效率和准确性,有利于改进生产过程和提高产品质量。
MBD技术在飞机制造中具有明显的优势,但也存在一些不足。
主要优势包括:提高设计效率和准确性、减少生产过程中的错误、提高生产效率和质量等。
不足之处包括:MBD技术需要较高的技术水平、初始投入成本较高、数据管理难度加大等。
随着技术的不断发展,MBD技术在未来将有更广阔的发展前景。
以下是MBD技术在飞机制造中的未来发展趋势:MBD技术与数字化工厂的结合:未来,MBD技术将更加深入地与数字化工厂相结合,实现从设计到制造、维修等全生命周期的数字化管理,进一步提高生产效率和质量。
MBD技术与仿真技术的结合:利用MBD技术与仿真技术的结合,可以在制造之前对飞机的性能进行全面仿真和优化,提高飞机的性能和可靠性。
《基于MBD的三维装配信息集成技术研究》

《基于MBD的三维装配信息集成技术研究》一、引言随着制造业的快速发展,三维装配技术已成为现代制造过程中的关键环节。
而模型定义(MBD)技术的出现,为三维装配信息集成提供了新的思路和方法。
MBD技术通过将产品信息直接定义在三维模型中,实现了产品信息的全面集成和共享,为三维装配提供了更为高效、准确的信息支持。
本文旨在探讨基于MBD 的三维装配信息集成技术的研究,分析其优势和存在的问题,并针对这些问题提出相应的解决方案。
二、MBD技术的概念及其在三维装配中的应用MBD(Model Based Definition)技术,即基于模型的定义技术,它以数字化产品模型为载体,将产品从设计到制造的整个过程中的信息完整地集成在一起。
这种技术广泛应用于产品设计、工艺规划、制造执行等环节。
在三维装配过程中,MBD技术能够提供详细、准确的产品结构信息、装配顺序、装配工艺等,为装配操作提供全面、有效的信息支持。
三、基于MBD的三维装配信息集成技术(一)研究背景及意义传统的三维装配信息主要通过文本描述或图纸展示,这些方式往往存在信息冗余、表达不直观等问题。
而基于MBD的三维装配信息集成技术,将产品信息直接定义在三维模型中,实现了信息的全面集成和共享。
这种技术能够提高装配效率、降低装配成本,同时还能提高产品的可靠性和稳定性。
因此,研究基于MBD的三维装配信息集成技术具有重要意义。
(二)关键技术分析基于MBD的三维装配信息集成技术主要包括以下几个关键环节:1. 模型构建:通过CAD软件构建产品的三维模型,并确保模型的准确性和完整性。
2. 信息定义:在三维模型中定义产品的结构信息、装配顺序、装配工艺等,实现信息的全面集成。
3. 接口开发:开发与各生产环节的接口,实现与ERP、MES 等系统的数据交互。
4. 集成应用:将集成后的信息应用于实际生产过程中,提高生产效率和产品质量。
(三)研究方法与步骤基于MBD的三维装配信息集成技术的研究主要包括以下几个步骤:1. 分析并总结现有的三维装配技术和MBD技术的应用现状;2. 设计基于MBD的三维装配模型结构,并构建相应的三维模型;3. 在模型中定义产品的结构信息、装配顺序、装配工艺等;4. 开发与各生产环节的接口,实现数据交互;5. 将集成后的信息应用于实际生产过程中,分析其效果并不断优化。
MBD介绍

完成工艺编制; 生成汇总卡片(xls),并允许编辑 将TC中PDF格式的工艺卡片合并成册 发起审签流程
1、手工、自动两种整本工艺生成 2、圈阅问题,通过内置浏览器实现
基于MBD三维工艺设计过程
产品工艺规划 创建工艺、 工序 创建基于 MBD的工艺 模型 填写工艺内 容 生成工艺卡 片 工艺审批
基于MBD三维工艺设计过程
产品工艺规划\分工 创建工艺、 工序 创建基于 MBD的工艺 模型 填写工艺内 容 生成工艺卡 片 工艺审批
确定工艺路线 确定加工方式 确定关键工装夹具 确定新工艺方法 确定工艺分工
基于MBD三维工艺设计过程
产品工艺规划 创建工艺、 工序 创建基于 MBD的工艺 模型 填写工艺内 容 生成工艺卡 片 工艺审批
应用MBD的设计审批
针对基于三维模型的产品研发,审阅工作也需要在三维模型上进行, 需要在三维模型上实现:模型浏览、模型检查、模型测量、模型剖切、 模型比较、模型的会签、模型的干涉检查和模型的批注等。
应用MBD的工艺设计
工艺开发工作将在三维数字化环境下,直接依据三维实体模型展开, 完成工艺方案制定及详细工艺设计,并产生三维数字化工艺,作为生 产现场的操作依据。 三维数字化工艺开发的显著特点是在三维数字化环境下,工艺开发人 员利用各类三维数字化实体模型建立起数字化工艺模型,通过模拟仿 真,确定出合理的、可行的制造工艺。同时生成工艺图解和操作动画 等多媒体工艺数据,编制成三维数字化制造工艺。
应用MBD的产品设计
三维模型要包含产品研制有关的 所有信息:除了包含几何信息、 尺寸信息、公差信息、基准、注 释、剖面和焊接符号等外,还需 要包含产品研制有关的所有信息。 面向生产的产品设计:针对模型 的制造方式,在设计过程中,就 要考虑到产品的工艺性、制造性、 装配性和检验性,并针对制造要 求进行三维建模、尺寸标注和参 数定义等。
基于MBD的飞机数字化制造技术

基于MBD的飞机数字化制造技术摘要:在航空制造企业中,数字化制造技术是技术进步的重要基础。
波音公司在787项目中推出了全新的数字化定义技术,也就是以MBD为基础的数字化技术,与传统表达形式相比,MBD数据表达形式有所不同,数字化的程度也存在一定的差异性,再加上制造设备对制造依据有着不一样的需求,促使MBD制造协调技术与传统制造协调技术之间的区别较大。
各航空企业纷纷开始应用基于MBD的飞机数字化制造技术。
目前,我国基于MBD的飞机数字化制造技术还处于发展初期,针对基于MBD的飞机数字化制造技术的相关探究意义深远。
关键词:MBD;飞机;数字化制造技术引言MBD技术是由国外引进的一种先进技术,我国对此的研究基础较为薄弱,将这种技术应用到航空航天领域中,不仅有助于飞机设计与制造一体化,还可以促使整个应用体系的科学性与高效性得以提升。
在研究时,工作人员需要深入了解分析MBD技术的内涵、MBD技术在飞机数字化制造中的应用与优势,剖析基于MBD的飞机数字化制造技术的发展情况,才能更好的提高技术应用水平。
一、MBD技术的主要内涵从MBD技术的起源分析,美国在上世纪后期就已经进行了相关研究,这项技术目前已经逐渐发展成熟。
在实际运用MBD技术的过程中,并不是从简单的二维到三维上的延伸,而是进行了全新的三维立体模型的构建。
同时,还要让数据信息、形成的模型的形象化与具体化更加完善,信息的传达与表现形式更加清晰化,让受众对其的了解更加深入。
此外,集成的三维立体模型可以将工艺信息更加清晰、准确的展现与表达出来,实现了对传统信息数据模型形式的颠覆。
在生产制造时,以三维立体模型作为根本数据依据,在传统工程图纸方式的协助下更好的进行三维立体化制造。
二、MBD技术在飞机数字化制造中的应用优势(一)有助于产品特性的提取应用MBD技术进行飞机制造,有助于用户根据自身实际需要提取相关数据,并以此为基础进行之后的数模测量与标注等工作,还可以通过系统中的自定义功能分类与提取飞机制造信息。
基于MBD的三维数字化装配工艺设计及现场可视化技术应用

维数字化装配工艺设计和并行工程奠定了基础。
1 三维数字化装配工艺设计及现场可视化系 统
通过采用达索公司三维数字化装配工艺设计平台 DELMIA 及 3DVIA Composer 解决方案,构建“数字化 装配工艺设计和仿真系统”及“生产现场可视化系统”。 突破 DELMIA 二次开发及定制技术、3D 制造过程仿 真验证及优化技术、MBD 技术、生产现场可视化技术、 Windchill/DELMIA/EPCS/CAPP 多系统集成技术等关键 技术瓶颈,最终构建符合企业业务需求的“数字化装配 工艺设计和仿真系统”及“生产现场可视化系统”。缩 短飞机装配周期,提高装配质量,全面提升飞机的数字 化制造能力。系统流程及集成架构如图 1 所示。
2011 年第 22 期·航空制造技术 81
装配工艺 ASSEMBLY PROCESS
Hale Waihona Puke 把 MBOM 和 AO 信息传递给 ERP 及 MES 系 统,实 现 车 间 现 场 装 配 可 视 化,指导实际生产工作。
2 三维数字化装配工艺设计
三维数字化装配工艺设计是通过 对飞机产品结构进行分析,在企业现 有制造能力 ( 设备、工艺技术能力、人 力资源等 ) 及产量要求的基础上,进 行 组 件 划 分,制 定 装 配 流 程,确 定 装 配方案,并选择各装配环节所需要的 制 造 资 源。 在 三 维 数 字 化 装 配 工 艺 设计系统中,工艺设计用树状结构表 示,主要由产品结构树、工艺结构树、 资源结构树 3 个分支构成,具体结构 特征按企业需求进行工艺模板定制。 基于 MBD 技术的三维数字化装配工 艺设计主要工作流程如图 2 所示。 2.1 数据准备工作
关键词:MBD 三维工艺设计 现场可视化 [ABSTRACT] MBD-based assembly process of three-dimensional digital design is not only an new discipline in aircraft digital manufacture , but also the future aircraft design trends. The technology completes the jobs of division of the three-dimensional process splice surface based on MBD, BOM reconstruction, process simulation and establishment of three-dimensional assembly order by customization and multi-system integration of process design, process simulation software, such as DELMIA, 3DVIA Composer, CAPP, and so on. The technology transfers the completed process design information to production scene by product management system, the technology opens technology roadmap from the MBD-based product design, process design to on-site visualization assembly. Keywords: MBD Three-dimensional design Onsite visualization
Model_based_definition介绍
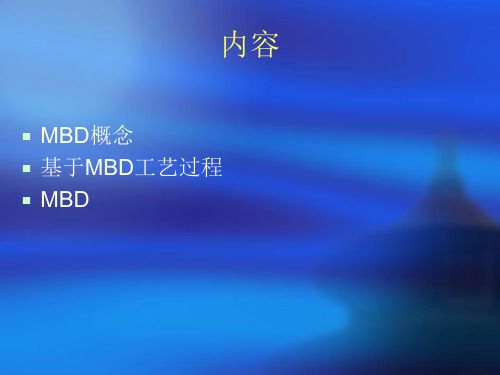
交流,设计、工艺和制造数据不关联,设计数据的更改,工艺、制造 部门需要针对设计更改进行相应的更改,会带来设计、工艺和制造数 据的不一致性问题。
基于MBD的产品设计制造过程
设计部门
三维模型 三维标注
全三维的完整产 品定义信息表达
问题: 插入工序时,工序号如何处理;采用中间序号的方式。 工序顺号,第一次编辑在NX中生成;发布后更改顺号手工填写;
工装申请及返填流程
在NX提交工装申请流程,创建工艺申请单对象, 并记录工装编号。
业务流程按照原业务模式处理,在流程的工装返 填节点,启动NX Manager加载整个工艺,手动 点击刷新按钮,在NX下刷新卡片的工装信息。
设计 批准 添加权限
更改流程
会签
校对 协作工艺会签
审核
材料定额 会签
自动签字
移除权限
发放归档
其他审批流程
业务要求无明显变化 主要功能:
1、审批工艺集合时,优化自动添加对象到目标 的功能; 2、PDF格式卡片签字,先单个工序的PDF签字, 然后再将签字后的问题合并成整本工艺。
3、手动和自动生成整本PDF格式工艺
内容
MBD概念 基于MBD工艺过程 MBD
当前产品设计制造过程
设计部门
二维图纸
基于三维模型的二维 工程图关联设计
生产部门
工艺部门
工艺规程 作业指导书
存在的问题
需要消化二维图纸:工艺、制造部门要花费大量的时间消化二维图样。 数据重复录入:工艺、制造部门需要重新录入数据,以实现工装模具
创建修改 单
工艺变更业务流程
浅谈基于MBD的数字化仿真技术在航天制造企业应用

浅谈基于MBD的数字化仿真技术在航天制造企业应用本文从网络收集而来,上传到平台为了帮到更多的人,如果您需要使用本文档,请点击下载按钮下载本文档(有偿下载),另外祝您生活愉快,工作顺利,万事如意!1引言当前,伴随着三维数字化设计制造技术带来的传统产品研制模式的重大变革,基于模型的定义(ModelBasedDefinition,MBD)技术正向着可以实现产品整个生命周期中各个阶段的数据、过程定义与交换的全数字化方向发展。
近年来我国的航天制造业数字化紧跟现今数字化制造发展方向,在产品的三维数字化协同设计、基于三维产品模型的工艺设计、产品数据和生产过程管理等方面取得了一定的成效,但也应意识到,面向产品全生命周期的数字化尚未实现,全数字化的三维设计制造模式仍未形成,数字化仿真技术对数字化制造的促进效果仍不明显,数字化技术的巨大效能远未发挥。
对于离散型航天制造型企业,应重点从生产系统仿真技术、工艺设计仿真技术、装备设计仿真技术、质量检测仿真技术四方面深入开展数字化仿真技术的探索和应用工作。
现阶段需要着重解决以下几方面的问题:a.如何利用生产系统仿真技术详细验证工厂规划、车间布局方案可行性,降低固定资产投资和技术改进风险;b.如何利用工艺设计仿真技术减少产品研制初期的设计更改、工艺更改和试验件生产,并为产品装配现场提供可视化的三维工艺指导;c.如何通过利用装备设计仿真技术解决大型产品、工装验证成本高,设计周期长的问题;d.如何利用质量检测仿真技术提高产品的尺寸质量,降低产品的生产成本,提高零部件合格率并在产品批产前及时发现质量控制上的潜在隐患。
2生产系统仿真技术生产系统仿真是指利用计算机仿真技术和虚拟现实技术,在虚拟空间内对制造系统元素(包括设备和人)布置的合理性和原材料转化过程(包括加工、流转、装配)的流畅性进行验证和优化,计算各工位产能和物料流动时间并实现最优生产线平衡,以指导工艺布局、工艺物流和生产规划的技术。
基于MBD的产品工艺协同设计关键技术应用
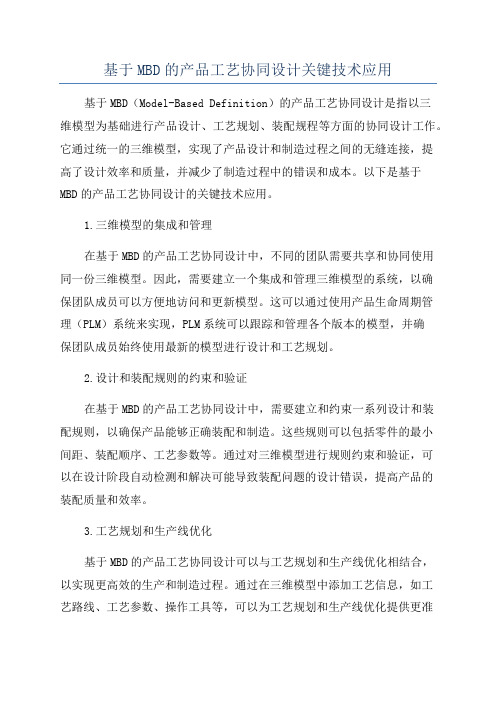
基于MBD的产品工艺协同设计关键技术应用基于MBD(Model-Based Definition)的产品工艺协同设计是指以三维模型为基础进行产品设计、工艺规划、装配规程等方面的协同设计工作。
它通过统一的三维模型,实现了产品设计和制造过程之间的无缝连接,提高了设计效率和质量,并减少了制造过程中的错误和成本。
以下是基于MBD的产品工艺协同设计的关键技术应用。
1.三维模型的集成和管理在基于MBD的产品工艺协同设计中,不同的团队需要共享和协同使用同一份三维模型。
因此,需要建立一个集成和管理三维模型的系统,以确保团队成员可以方便地访问和更新模型。
这可以通过使用产品生命周期管理(PLM)系统来实现,PLM系统可以跟踪和管理各个版本的模型,并确保团队成员始终使用最新的模型进行设计和工艺规划。
2.设计和装配规则的约束和验证在基于MBD的产品工艺协同设计中,需要建立和约束一系列设计和装配规则,以确保产品能够正确装配和制造。
这些规则可以包括零件的最小间距、装配顺序、工艺参数等。
通过对三维模型进行规则约束和验证,可以在设计阶段自动检测和解决可能导致装配问题的设计错误,提高产品的装配质量和效率。
3.工艺规划和生产线优化基于MBD的产品工艺协同设计可以与工艺规划和生产线优化相结合,以实现更高效的生产和制造过程。
通过在三维模型中添加工艺信息,如工艺路线、工艺参数、操作工具等,可以为工艺规划和生产线优化提供更准确的数据。
这有助于减少制造过程中的浪费和错误,并提高生产效率和质量。
4.CAD/CAM集成5.虚拟装配和碰撞检测在基于MBD的产品工艺协同设计中,可以使用虚拟装配和碰撞检测技术来帮助设计师和工艺规划师进行优化设计和规划。
虚拟装配技术可以在三维模型中模拟真实的装配过程,帮助发现和解决可能导致装配问题的设计错误。
碰撞检测技术可以在三维模型中检测到零件之间的碰撞,提前发现并解决可能存在的碰撞问题,避免在实际装配过程中出现故障和损失。
基于MBD技术的航天复杂产品全三维设计应用实践

基于MBD技术的航天复杂产品全三维设计应用实践导读本文结合MBD技术在国内外应用现状,通过基于PDM系统的三维模型技术状态管理、基于模型的知识产权保护管理、基于MBD的数字化设计工具集、基于PDM系统的MBD模型检查、基于PDM系统的基础资源库及三维货架产品库、基于MBD的数字化标准体系等方面阐述了湖北航天技术研究院总体设计所基于MBD技术的航天复杂产品全三维设计应用实践过程中的具体做法。
前言MBD(Model Based Definition)技术,即基于模型定义技术,MBD是产品数字化定义的先进方法,它是指产品定义的各类信息按照模型的方式组织,其核心内容是产品的几何模型,所有相关的工艺描述信息、属性信息、管理信息等都附着在产品的三维模型上中,一般情况下不再有二维工程图纸。
MBD技术改变了传统的由三维实体模型来描述几何信息,而用二维工程图纸来定义尺寸、公差和工艺信息的产品定义方法,MBD技术使三维数模作为生产制造过程中的唯一依据,改变了传统的以工程图纸为主,以三维实体模型为辅的制造方法。
航天型号产品在产品设计上具有产品结构复杂、设计更改频繁、零部件数量庞大、材料种类繁多等特点;在产品制造上具有工艺专业种类多、加工/装配工艺复杂、制造流程长、零部件配套关系复杂等特点;在管理上具有工程更改频繁、供应链复杂、协作协同复杂、产品质量要求高、按批次管理等特点,并且航天型号产品在其产品生命周期涉及到多产品、多企业、多部门、多业务之间的复杂协作,而新出现的MBD技术则真正的将这些需求串联起来。
本文结合MBD技术在国内外应用现状,通过基于PDM系统的三维模型技术状态管理、基于MBD的数字化设计工具集、基于PDM系统的MBD模型检查、基于PDM 系统的基础资源库及三维货架产品库、基于MBD的数字化标准体系等方面阐述了湖北航天技术研究院总体设计所(以下简称“设计所”)基于MBD技术的航天复杂产品全三维设计应用实践过程中的具体做法。
基于MBD的飞机数字化制造技术

基于MBD的飞机数字化制造技术摘要:过去,飞机的制造常常是在各部门之间缺乏沟通的情况下进行的,导致缺乏协调、工程延误和提高质量的障碍。
MBD技术的有效应用提高了飞机制造质量,节省了人力和物力资源。
在此基础上,对基于MBD的飞机制造技术的研究审查了MBD在飞机制造领域的技术优势、实际应用和发展前景,同时考虑到其技术内容和目前的发展状况,并为提高飞机安全水平奠定了基础。
关键词:MBD;飞机制造;数字化技术前言基于模型定义的完整三维设计技术(MBD)是一种高级数字产品定义方法,它将产品的所有设计定义、流程说明、属性和管理信息与产品的三维模型相关联。
了解尺寸和公差的3d制造和定义信息也不容易。
事实上,MBD是一套研发系统和标准,包括卓越、并行工程、面向设计的制造、知识工程等研发理念,以优化数字产品开发的价值。
1在飞机制造过程中应用MBD的技术优势1.1有效提取产品特性在飞机制造过程中使用MBD技术可以更好地帮助用户根据实际需要提取相关数据,并在此基础上开展数字测量、标签等后续活动,同时允许使用系统中的用户定义功能对飞机制造信息进行分类和检索。
飞机制造信息主要包括系统组件和车身结构配置。
组件由多个零件和连接器组成。
当装配零件的组成复杂时,必须将其分为不同的区域。
鉴于飞机制造的复杂性,实际工作往往涉及大量复杂的空间部件和结构,这可能影响MBD数字模型中一系列数据的准确性,从而妨碍根据客户的实际需要提供数据。
因此,需要根据客户的实际需求提取数字模型以获得所需信息。
1.2减少装配错误实施基于MBD的装配技术的主要目的是将相关零件装配到预先设计的接口上,并大大提高装配精度。
同时,数字定位系统和检查测量系统在飞机制造过程中发挥了重要作用,使飞机在装配过程中能够更好地实时调整状态。
为确保飞机的大部分部件能有效满足设计要求,可在装配时引入数字装配定位装置,飞机装配操作可由飞机的机器人操作系统优化,即飞机的数字定位应当指出,在飞机制造过程中,网络部件的数字定位技术可进一步提高飞机制造检查的效率,减少飞机部件装配误差,同时有效减少检查困难。
基于MBD的三维工程化设计应用

IM经验· 60 ·基于MBD 的三维工程化设计应用撰文/南车戚墅堰机车有限公司信息管理部 谢利一、引言当前,国内外大型装备制造企业的数字化技术发展迅速,三维数字化设计技术得到了广泛的应用。
基于模型定义(Model-Based Definition,MBD)的数字化设计与制造技术已经成为制造业信息化的发展趋势。
企业为什么要推广MBD 技术进行三维工程化设计呢?以二维工程图作为交付物,向工艺、制造、生产和检查等环节传递产品的几何结构及技术要求的传统研制模式存在如下问题。
(1)设计环节:由于以二维图作为交付物,三维模型不作为交付物,二维图更改后三维模型不及时更新,导致数据不一致。
(2)工艺、制造和检测环节:工艺、制造以二维图为准,增加了从图纸到形状的还原过程,容易出现理解歧义,并增加了出错概率。
同时,工艺模型或图纸重建,增加了无价值劳动。
管路、电缆以二维图为主,造成制造、装配误差较大,且不能形象地指导装配过程,导致现场更改较多。
检测以二维图为准,数据手工录入效率低,准确性无法保证。
(3)检查机制:由于设计以二维图作为交付物,因此没有建立三维模型的检查机制,导致工艺、制造和检测等后续环节得不到准确的三维模型。
(4)标准规范:当前产品研发过程中遵循的标准规范是基于二维模式,缺乏三维工程化应用的标准体系规范,导致三维设计模型质量较差。
MBD 技术采用包含了三维几何模型、尺寸和尺寸工差、形位公差、基准、符号、表面粗糙度、属性、注释等产品制造信息的单一主模型来完整表达产品定义信息,并将其作为产品制造过程中的唯一依据,从而实现设计、工艺、制造和检测等环节的高度集成。
采用MBD 技术实现了单一数据源,彻底改变产品数据定义、生成、授权与传递的模式,消除了传统研发模式中的三维模型与二维图纸之间的信息冲突,减少了创建、存储和追踪的数据量,实现三维数字化产品定义、三维数字化工艺开发和三维数字化数据应用,保证了产品制造信息的正确和快速传递,从而有效地缩短了产品研制周期,减少了重复工作,提高了产品质量和生产效率。
基于MBD的飞机数字化设计技术应用分析

基于MBD的飞机数字化设计技术应用分析目前国外数字化技术的应用又有了新的发展,以波音公司B787飞机的研制为代表,已经全面采用了基于数字模型定义(Model-Based Definition,简称MBD),并取得了成功。
我国的航空工业在新一代飞机研制中也开始应用MBD 技术,并取得了突破性进展。
为了使得各个业务环节充分利用已有的MBD单一数据开展工作,文章针对如何将MBD技术深入地应用到飞机设计环节,从多方面进行分析阐述。
關键词:MBD技术;设计面向制造;数字化样机引言所谓的基于模型定义(MBD)全三维设计技术,是将产品的所有相关设计定义、工艺描述、属性和管理等信息都附着在产品的三维模型中的先进的产品数字化定义方法。
同时不能简单的理解为尺寸和公差、制造信息的三维定义,实际上MBD是一套研发体系和标准,它涵盖了精益思想、并行工程、设计面向制造、知识工程等研发思想,其目的是产品数字化研制的价值最大化。
1 设计环境如何搭建基于模型的企业总体架构是数字化企业的发展前提。
飞机设计中通常选择ENOVIA LCA/VPM Navigate作为统一的数据管理支持环境,并与CATIA (达索公司开发的计算机辅助设计软件)构建了产品并行设计环境,进行数据创建、存储、查询数据之间的关联关系(如空间位置关系、从属关系等)以及数据的导入/导出,记录控制产品整个设计过程中的工程数据集信息,并实现MBD数字化定义产品数据的共享控制。
同时MBD技术应用需要进行二次开发,将企业的设计理念、管理理念贯彻到实际的数据创建/管理过程中,搭建一个科学的现代化设计管理环境平台。
2 设计面向制造MBD数据一次创建多次使用,且模型是设计制造过程中的唯一权威数据,必须保证模型数据的正确性,即满足客户需求且可制造。
其中可制造即创建的MBD模型能够满足制造应用的需求,该MBD模型在后续的生产中可以直接应用(如自动编程)。
因此,在飞机设计的早期活动中,制造部门工与设计部门协调沟通,并将制造需求转变为设计要求写入设计规范手册。
基于MBD技术的数字化样机的建立

基于MBD技术的数字化样机的建立1前言数字化样机(DMU)飞机整机或系统等数字化描述。
主要是基于CATIA创建的产品部件/整机的三维实体模型以及相关的数据集(如属性),反映产品实际特征。
目前在基于MBD技术的数字化设计制造时代,DMU作为唯一的权威的数据源,贯穿整个飞机产品的生命周期,包括产品设计、生产计划、生产准备、产品运输以及售后服务等各个环节。
2数据输入DMU工作启动基于一系列的飞机设计要求。
飞机设计要求的起点是客户需求,这些需求通过顾客、市场部门、制造部门、产品研发部、工作包团队自上而下金字塔式的沟通交流,最终形成技术文件,包括综合设计要求文件、技术要求文件、质量要求文件、制造要求文件、维护要求文件等。
从概念定义阶段开始进行评估、认证、优化,该项活动持续循环进行,直到在初步定义出口阶段达到成熟度要求并最终定稿。
完整的数字样机包含产品部件/全机零部件及其设备的完整数字信息模型,包括结构件、机构件、系统件(含管路、电子部件等)、标准组件、成品件等,满足产品结构和功能要求,可进行工程分析、优化以及数据管理。
数字样机演变贯穿飞机整个生命周期,其设计进展情况按项目设计阶段计划要求进行。
3概念设计3.1DMU的目标概念定义阶段是飞机研发过程中的第一个且非常重要的阶段,是早期的顶层的潜在生命周期活动,预先确定飞机的功能、形式、成本和研发进度。
其主要任务是选择理想的飞机构型方案,以满足设计要求。
此阶段DMU目标是:(1)能够通过可视化和示意图对设计准则和概念演变进行管理;(2)成为连接几何图形与产品结构纽带。
为此,产品结构必须使用最优的产品顶层节点进行初始定义,以便于产品研发过程中不同阶段的平滑过渡。
3.2DMU的成熟度DMU环境中,成熟度评估基于工程数据集定义的完善程度,成熟度低意味着几个设计概念尚未形成一个解决方案,仍可能发生更改;成熟度高意味着已形成一个解决方案,数据可靠且可能不会发生更改。
当DMU达到成熟度最高时意味着数据集已准备发放。
基于MBD技术的三维工艺设计与现场可视化生产

基于MBD技术的三维工艺设计与现场可视化生产导读:飞机研制采用MBD技术推进了飞机研制模式的创新,“三维工艺设计平台+DCE平台+ERP生产管控平台”构成的集成化的综合信息管理平台是企业打通产品数字化制造的工具;“MBD模型+三维指令(AO/FO)+检验计划”是企业产品设计、生产、质量控制等产品实现过程所依赖的机制创新。
作者:拜明星 | 来源:航空制造技术基于模型定义(Model Based Definition,MBD)是一种新的产品数字化定义技术,用集成的三维实体模型来完整表达产品定义信息,详细规定了三维实体模型中产品定义、公差的标注规则和工艺信息的表达方法,三维实体模型成为生产制造过程中的唯一依据。
波音公司787客机采用了“基于模型的产品定义”技术,实现了产品关联设计、通过建立全球协同平台(GCE)实现了与合作伙伴协同研制,这彻底地改变了研制流程、研制方法和飞机研发模式。
新飞机工程全面应用MBD技术,采用多厂所异地协同的研制模式,为航空产业的跨越发展提供了难得的机遇。
飞机研制的工艺设计与生产管理现状飞机研制采用了基于MBD技术,构建了设计制造的协同工作平台(简称DCE平台),解决了产品制造的单一数据源,实现了产品协同设计。
DCE平台通过与企业ERP系统的集成,实现了飞机装配现场“无纸化”,取得了非常显著的效果。
01产品的工艺设计在DCE平台中依据产品数据集(EBOM、MBD模型等),完成工艺规划工作:编制工艺总方案、构建了PBOM、划分装配流程、建立顶层MBOM:开展工艺准备工作,完成零组件交接状态/毛料供应状态、工装申请及其技术条件的签审与控制,二维形式指令AO/FO设计、工程更改贯彻、检验计划编制及其签审等,实现了EBOM/PBOM/MBOM的技术状态管理,实现了产品制造的关联工艺设计。
02产品计划编制与过程控制飞机研制中产品检验检测与过程控制采用了检验计划(检验规程)。
检验汁划规范了检查项目、检查方法、俭测工量具、明确了检验活动的具体要求,是检验人员验收产品的标准文件在DCE平台的工艺指令的编制环境中编制检验计划,DCE平台进行审签流程管理,提高了检验设计工作质量。
MBD技术应用

目前很多新项目(如Boeing787、MRJ和C919等)都采用基于模型定义技术(Model Based Definition,MBD)。
对于飞机设计,以全三维的MBD模型为数据源,传递给下游的工艺、质量和供应商使用;对于飞机制造,由于交付时间压力,大量新工艺的产生,迫使企业采用先进制造技术,引进自动化设备提高装配质量,缩短装配周期,改进生产率。
而这些设备(如数控机床、机器人、柔性工装和激光跟踪仪)基本都是数字驱动的;对于工艺设计,二维工艺规划方法不能直接利用全数字化MBD模型,需要手工维护大量3D到2D转换等不增值环节,缺少工艺验证手段,编程停留在手工阶段。
当工程更改频繁时,难以准确、高效地将MBD模型的数字量传递到数字化设备。
二维工艺规划方法与上游的全三维数字化设计和下游的先进制造工艺与装备已不相适应,逐渐成为数字化制造瓶颈,针对飞机全数字化MBD模型定义,需要一种直接基于几何和特征的工艺规划方法和自动编程工具,能进行工艺验证,提高数字设备程序编制的质量和效率。
本文探讨了基于MBD的飞机数字化工艺规划、验证和执行技术。
首先提出一种基于MBD的数字化制造与生产技术框架,然后建立了支持设计,工艺和质量的MBD模型体系与相应的数字化制造与生产系统,最后分析了基于MBD的数字化工艺规划在方案设计、详细设计和生产研制阶段的一般流程。
希望能为解决基于MBD的数字化制造与生产技术问题提供一些思路。
基于MBD的飞机数字化制造与生产技术框架本文提出了一种飞机数字化制造框架,主要包含数据、工具和流程3个层次,如图1所示。
数据层作为飞机和资源数字化定义的单一数据源,是数字化制造的基础。
其底层是支撑MBD技术体系的基础数据库,如产品标准件库、工装标准件库、紧固件库、工艺参数库等。
中间层是产品、工艺和资源的行业构型库,代表典型的部件结构、工艺流程和工装结构。
顶层是对应于产品研制各个阶段的设计MBD模型、工艺MBD模型和质量MBD模型。
基于MBD的飞机数字化制造技术

基于MBD的飞机数字化制造技术摘要:本文主要介绍了基于MBD(Model Based Definition)的飞机数字化生产技术,包括MBD技术的内涵及其发展状况、采用MBD技术在飞机制造过程中的优势、MBD技术在飞机生产过程中的具体运用、MBD技术在飞机制造业的未来发展等方面。
研究表明,采用MBD技术能够高效获取产品特性、优化检验点设置、促进飞机制造模式创新,而数字化定义方法、工艺装备设计与制造一体化技术、检测和质量管理技术是MBD技术在飞机生产过程中的具体运用。
未来,MBD技术在飞机制造业仍具有广阔的应用前景。
关键字:MBD;飞机制造;数字化技术引言随着数字化技术的快速发展,数字化生产已经成为了现代制造业的重要趋势。
在飞机制造业中,数字化生产技术已经得到广泛的应用,其中基于MBD的飞机数字化生产技术是一种重要的技术手段。
MBD技术是一种以三维模型为基础的数字化定义方法,能够实现产品设计、制造、检验和质量管理的全过程数字化。
本文将对基于MBD的飞机数字化生产技术进行深入探讨。
1.MBD技术的内涵及其发展状况1.1 技术内涵MBD技术是一种基于三维模型的数字化定义方法,它将产品设计、制造、检验和质量管理等全过程数字化,并实现了从CAD到CAM的全数字化闭环。
传统的图纸定义需要通过多次传递和解读,可能会导致产品特性信息的失真和误解,而MBD技术将产品特性信息直接定义在三维模型中,避免了传统图纸定义带来的信息传递误差和理解偏差,提高了产品开发和制造效率。
同时,MBD技术还可以优化制造过程,降低制造成本。
因此,MBD技术是一种高效、准确和可靠的数字化生产技术。
1.2 发展状况MBD技术的发展可以追溯到上世纪八十年代,当时它主要用于汽车工业中的CAD/CAM系统。
随着计算机硬件和软件技术的不断发展,MBD技术得到了广泛的应用,并逐步成为了数字化生产的重要手段。
目前,MBD技术在飞机制造、汽车制造、船舶制造等领域得到了广泛的应用。
- 1、下载文档前请自行甄别文档内容的完整性,平台不提供额外的编辑、内容补充、找答案等附加服务。
- 2、"仅部分预览"的文档,不可在线预览部分如存在完整性等问题,可反馈申请退款(可完整预览的文档不适用该条件!)。
- 3、如文档侵犯您的权益,请联系客服反馈,我们会尽快为您处理(人工客服工作时间:9:00-18:30)。
基于MBD的三维数模在飞机制造过程中的应用当前,我国航空制造业的数字化技术发展迅猛,三维数字化设计技术和数字化样机技术得到了深入应用。
同时,随着计算机和数控加工技术的发展,传统以模拟量传递的实物标工协调法被数字量传递为基础的数字化协调法代替,缩短了型号研制周期,提高了产品质量。
但是,在当前我国的三维数字化模型并没有贯穿于整个飞机数字化制造过程中,二维数字化模型依然是飞机制造过程的主要依据。
因此,在制造过程中需要把三维数字化模型转化为二维数字化模型,并把二
维数字化模型输出形成纸质工程图纸作为指导生产的依据。
因此,学习国外先进的MBD技术成功经验,研究建立适合我国的飞机三维数字化设计制造一体化技术应用体系很有必要。
1、MBD的内涵
美国机械工程师协会于1997年在波音公司的协助下开始了有关MBD 标准的研究和制定工作,并于2003年使之成为美国国家标准。
MBD的主导思想不只是简单地将二维图纸的信息反映到三维数据中,而是充分利用三维模型所具备的表现力,去探索便于用户理解且更具效率的设计信息表达方式。
它用集成的三维数模完整地表达了产品定义信息的方法,详细规定了三维数模中产品尺寸、公差的标注规则和工艺信息的表达方法。
MBD改变了传统用三维数模描述几何形状信息的方法,而用二维工程图纸来定义尺寸、公差和工艺信息的分步产品数字化定义方法。
同时,MBD使三维数模作为生产制造过程中的唯一依据,改变了传统以工程图纸为主、以三维实体模型数模为辅的制造方法。
2、MBD的意义
3、基于MBD的三维数字化制造技术应用体系
MBD使用一个集成化的三维数字化实体模型表达了完整的产品定义信息,
成为制造过程中的唯一依据。
MBD三维数字化产品定义技术不仅使产品的设计方式发生了根本变化,不再需要生成和维护二维工程图纸,而且它对企业管理及设计下游的活动,包括工艺规划、车间生产等产生重大影响,引起了数字化制造技术的重大变革,真正开启了三维数字化制造时代。
采用MBD技术,将彻底改变飞机产品数据定义、生成、授权与传递的制造模式,实现三维数字化产品定义、三维数字化工艺开发和三维数字化数据应用,形成一个完整的、基于MBD的三维数字化制造技术应用体系,如图所示。
基于MBD的飞机数字化制造技术应用体系
在该应用体系中,通过建立基于的数字化协调规范和数字化定义规范,采用三维建模系统进行数字化产定义,建立起满足协调要求的飞机全级三维数字样机和三维工装模型,进行三维数字化预装配。
工艺人员在工艺设计规范的指导下,直接依据三维实体模型开展三维工艺开发工作,改变了以往同时依据二维工程图纸和三维实体模型来设计产品装配工艺和零件加工工艺的做法。
依据数字化装配工艺流程,建立起三维数字化装配工艺模型,通过数字化虚拟装配环境对装配工艺流程进行数字化模拟仿真,在工艺工作进行的同时及飞机产品实物装配之前,进行制造工艺活动的虚拟装配验证,确认工艺操作过程准确无误后再将装配工
艺授权发放,进行现场使用和实物装配。
在数字化装配工艺模拟仿真过程中生成装配操作过程的三维工艺图解和多媒体动画数据,建立起三维数字化工艺数据,为三维数字化工艺现场应用提供数据。
根据产品开发规范和数据组织规范,所有产品工程设计、工艺设计、工装设计制造等开发过程及其产生的工程数据、工艺数据、工装数据通过PLM系统实现全生命周期管理。
基于MBD的数字化制造技术达到了全机100%的三维数字化产品定义、数字化预装配、数字化工装设计,
第2/5页同时使三维工艺设计及三维数据可视化应用成为现实。
4、国外发达航空企业MBD技术的应用现状
近10余年,随着飞机制造技术的发展,以波音、洛·马和空客公司为代表的飞机制造业在数字化技术应用领域取得了巨大的成功。
波音公司在以波音787为代表的新型客机研制过程中,全面采用了MBD技术,将三维产品制造信息(Product Manufacturing Information,PMI)与三维设计信息共同定义到产品的三维数模型中,摒弃二维图样,直接使用三维标注模型作为制造依据,使工程技术人员从百年来的二维文化中解放出来,实现了产品设计(含工艺设计)、工装设计、零件加工、部件装配、零部件检测检验的高度集成、协同和融合,建立了三维数字化设计制造一体化集成应用体系,开创了飞机数字化设计制造的崭新模式,确保了波音787客机的研制周期和质量。
5、基于MBD的数字化制造流程
6、关键应用技术
6.1基于MBD的数字化定义技术
第3/5页数字化产品定义(DPD)是实现数字化制造的基础,它以数字量方式对产品进行准确描述。
采用MBD技术后,数字化产品定义信息必须按MBD 要求进行分类组织管理,完整准确地表达产品零部件本身的几何属性、工艺属性、质量检测属性以及管理属性等信息,满足制造过程各阶段对数据的需求,保证飞机产品设计制造过程中的协调性。
6.2基于MBD的数字化工艺设计与仿真技术
工艺设计与仿真将在三维数字化环境下,依据基于MBD技术的数字化工艺协调制造体系要求,以产品EBOM和三维数字样机为基础,以工艺数字化并行定义为核心,制定工艺总方案,建立三维工艺数字样机,进行飞机数字化三维工艺设计、数字化工艺容差分配、仿真和优化、数字化三维工艺仿真验证。
6.3基于MBD的工艺装备设计制造集成技术
工艺装备设计在三维数字化环境下,以产品数字样机、工艺数字样机为基础,进行工艺技术装备的设计和仿真,逐步形成面向现代航空制造的基于三维的飞机制造技术装备工程体系,实现技术装备数字化、自动化、柔性化。
在工装设计过程中,产品设计数模、工艺数模的版本变化将直接引起工装数模的版本变化。
因此,必须应用三维关联技术和三维在线技术预先开展基于M B D 工艺装备设计与飞机产品、工艺设计及
仿真的数字化协同技术、工艺装备设计与产品设计、工艺设计的关联更改技术、工艺装备三维数字化设计制造一体化集成技术、基于三维数字化工艺装备设计、制造等技术的研究工作。
6.4基于MBD 的数字化检测与质量控制技术
在基于MBD 的产品数字样机和工艺数字样机的基础上,开展三维工艺检验计划的技术研究工作,探讨三维数字图形转换为测量机等数字化设备能够识别的数字信息的技术方法,并以基于MBD 的三维设计数模、工艺数模和检测方案为依据开发检验数据计算程序,建立基于M B D 的三维检验数模,并与产品数字样机和工艺数字样机一起纳入PDM 系统进行管理。
与此同时,在制造产品数据结构(MBOM)的基础上,建立基于质量产品结构(QB OM)的集成质量管理系统。
以P DM 系统的检测计划、三维检测模型为依据,通过集成质量管理系统在生产现场采集飞机检验检测数据,并建立检验检测结果与QBOM的关联关系,纳入集成质量管理系统进行有效的管理,在此基础上形成单架次飞机的质量档案,最终完成单架次飞机质量档案的归档工作。
7、总结
通过基于MBD的各种关键数字化技术的应用,能够有效地缩短产品研制周期,改善生产现场工作环境,提高产品质量和生产效率,真正实现无二维图纸、无纸质工作指令的三维数字化集成制造。
MBD技术的深入应用必将推动我国飞机制造业的迅猛发展。
参考文献
[1]周秋忠,范玉青. MBD技术在飞机制造中的应用. 北京:北京航空航天大学.2008.
[2]邹翼华. 飞机数字化测量辅助装配技术及应用. 航空制造技术. 2009 (24):
第4/5页48-52
[3]许国康.大型飞机自动化装配技术.航空学报.2008(3):737—738。