4第四章H2S和CO2腐蚀环境和实例P1-15 09.5.21.
硫化氢腐蚀的机理及影响因素.
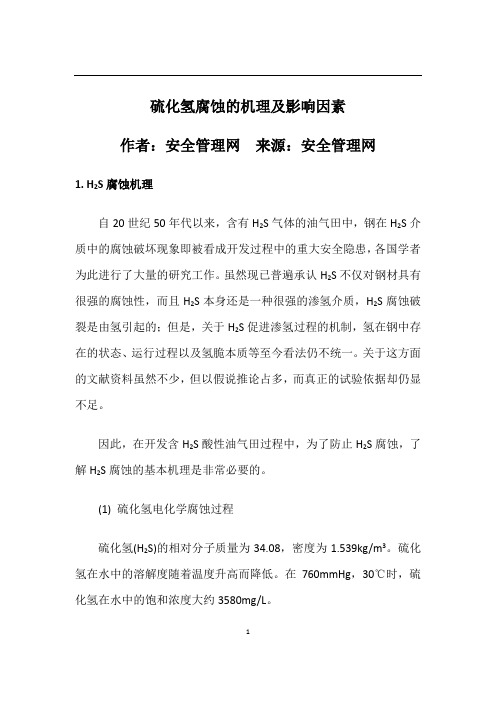
硫化氢腐蚀的机理及影响因素作者:安全管理网来源:安全管理网1. H2S腐蚀机理自20世纪50年代以来,含有H2S气体的油气田中,钢在H2S介质中的腐蚀破坏现象即被看成开发过程中的重大安全隐患,各国学者为此进行了大量的研究工作。
虽然现已普遍承认H2S不仅对钢材具有很强的腐蚀性,而且H2S本身还是一种很强的渗氢介质,H2S腐蚀破裂是由氢引起的;但是,关于H2S促进渗氢过程的机制,氢在钢中存在的状态、运行过程以及氢脆本质等至今看法仍不统一。
关于这方面的文献资料虽然不少,但以假说推论占多,而真正的试验依据却仍显不足。
因此,在开发含H2S酸性油气田过程中,为了防止H2S腐蚀,了解H2S腐蚀的基本机理是非常必要的。
(1) 硫化氢电化学腐蚀过程硫化氢(H2S)的相对分子质量为34.08,密度为1.539kg/m3。
硫化氢在水中的溶解度随着温度升高而降低。
在760mmHg,30℃时,硫化氢在水中的饱和浓度大约3580mg/L。
1在油气工业中,含H2S溶液中钢材的各种腐蚀(包括硫化氢腐蚀、应力腐蚀开裂、氢致开裂)已引起了足够重视,并展开了众多的研究。
其中包括Armstrong和Henderson对电极反应分两步进行的理论描述;Keddamt等提出的H2S04中铁溶解的反应模型;Bai和Conway对一种产物到另一种产物进行的还原反应机理进行了系统的研究。
研究表明,阳极反应是铁作为离子铁进入溶液的,而阴极反应,特别是无氧环境中的阴极反应是源于H2S中的H+的还原反应。
总的腐蚀速率随着pH的降低而增加,这归于金属表面硫化铁活性的不同而产生。
Sardisco,Wright和Greco研究了30℃时H2S-C02-H20系统中碳钢的腐蚀,结果表明,在H2S分压低于0.1Pa时,金属表面会形成包括FeS2,FeS,Fe1-X S在内的具有保护性的硫化物膜。
然而,当H2S分压介于0.1~4Pa时,会形成以Fe1-X S为主的包括FeS,FeS2在内的非保护性膜。
CO2对油气管材的腐蚀及防护

超临界CO2油水介质中腐蚀速率与水含量的关系 90℃,8.27MPa(Tc=31 ℃ , pc=7.38MPa)
因 素
防护措施
缓蚀剂: 较经济,但局部腐蚀和大排量的井 效果差 涂层: 较经济,但适应条件有局限。 如果涂层有局部破坏,将加速局部腐蚀
措 施
合金元素和金相组织改良 发展趋势,成本高 其他
+
+ e → H, 2H →H2
Fe + H2CO3 → FeCO3 + H2
碳 钢 腐 蚀 特 征
基本特征:
局部的点腐、癣状腐蚀、台面腐蚀、垢下腐蚀
原因:腐蚀程度不同的区域之间形成强腐蚀电偶,
特 征
加速局部腐蚀。
νe有时可达7mm/a
油套钢管的CO2腐蚀
特 征
塔里木油田某井油管CO2腐蚀形貌图
因 素
油套钢管的CO2腐蚀
CO2,H2S混合气体的腐蚀速率对比
实验编号 实验 条件 PCO2(ps i) PH2S(psi) 1 304 0 3.540 2 174 0 2.052 3 174 0.28 3.081 4 174 1.5 0.965 5 174 2 0.553 6 174 2.8 0.712
1.油套钢管的CO2腐蚀
特 征
辽河油田某井因CO2所致的油管腐蚀 (失重率:63% ;平均腐蚀速度=4.84 mm/年)
碳 钢腐蚀影 响 因 素
分压 PCO2: <0.021MPa 不腐蚀 0.021~0.21MPa 中等程度 >0.21MPa 严重腐蚀 温度 T: <60℃ 轻度均匀腐蚀 (FeCO3) 100℃左右 局部腐蚀(台状腐蚀或孔蚀) >150℃ 均匀腐蚀,速度下降(FeCO3和Fe3O4) 氯离子Cl- : 低温下 → νe下降 (抑制CO2的溶解度)
4气井中的H2SCO2腐蚀
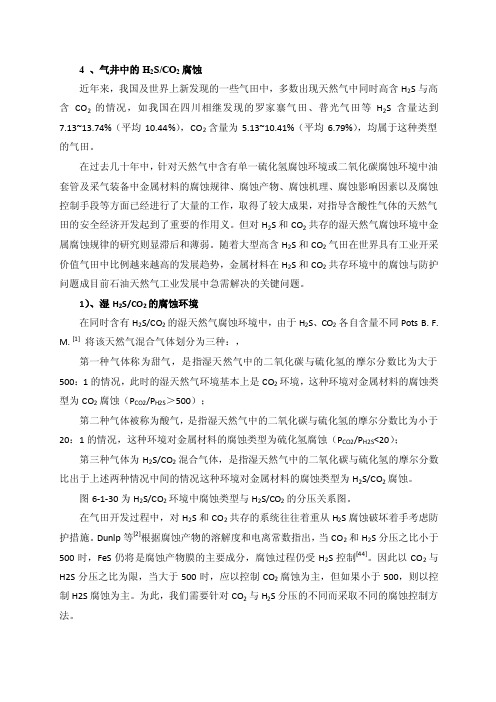
4 、气井中的H2S/CO2腐蚀近年来,我国及世界上新发现的一些气田中,多数出现天然气中同时高含H2S与高含CO2的情况,如我国在四川相继发现的罗家寨气田、普光气田等H2S含量达到7.13~13.74%(平均10.44%),CO2含量为5.13~10.41%(平均6.79%),均属于这种类型的气田。
在过去几十年中,针对天然气中含有单一硫化氢腐蚀环境或二氧化碳腐蚀环境中油套管及采气装备中金属材料的腐蚀规律、腐蚀产物、腐蚀机理、腐蚀影响因素以及腐蚀控制手段等方面已经进行了大量的工作,取得了较大成果,对指导含酸性气体的天然气田的安全经济开发起到了重要的作用义。
但对H2S和CO2共存的湿天然气腐蚀环境中金属腐蚀规律的研究则显滞后和薄弱。
随着大型高含H2S和CO2气田在世界具有工业开采价值气田中比例越来越高的发展趋势,金属材料在H2S和CO2共存环境中的腐蚀与防护问题成目前石油天然气工业发展中急需解决的关键问题。
1)、湿H2S/CO2的腐蚀环境在同时含有H2S/CO2的湿天然气腐蚀环境中,由于H2S、CO2各自含量不同Pots B. F. M. [1]将该天然气混合气体划分为三种:,第一种气体称为甜气,是指湿天然气中的二氧化碳与硫化氢的摩尔分数比为大于500:1的情况,此时的湿天然气环境基本上是CO2环境,这种环境对金属材料的腐蚀类型为CO2腐蚀(P CO2/P H2S>500);第二种气体被称为酸气,是指湿天然气中的二氧化碳与硫化氢的摩尔分数比为小于20:1的情况,这种环境对金属材料的腐蚀类型为硫化氢腐蚀(P CO2/P H2S<20);第三种气体为H2S/CO2混合气体,是指湿天然气中的二氧化碳与硫化氢的摩尔分数比出于上述两种情况中间的情况这种环境对金属材料的腐蚀类型为H2S/CO2腐蚀。
图6-1-30为H2S/CO2环境中腐蚀类型与H2S/CO2的分压关系图。
在气田开发过程中,对H2S和CO2共存的系统往往着重从H2S腐蚀破坏着手考虑防护措施。
硫化氢腐蚀

硫化氢腐蚀
硫化氢腐蚀是指油气管道中含有一定浓度的硫化氢(H2S)和水产生的腐蚀。
硫化氢(H2S)溶于水中后电离呈酸性,使管材受到电化学腐蚀,造成管壁减薄或局部点蚀穿孔。
腐蚀过程中产生的氢原子被钢铁吸收后,在管材冶金缺陷区富集,可能导致钢材脆化,萌生裂纹,导致开裂。
国内外开发含硫化氢(H2S)的酸性油气田的管道和设备曾多次出现突发性的撕裂或脆断、焊接区开裂等事故,多是因为氢致开裂(HIC)和硫化物应力开裂(SSC)引起。
影响硫化氢(H2S)腐蚀的因素有硫化氢浓度、pH值、温度、流速、二氧化碳(C〇2)与氯离子(C1-)的浓度等。
H2S、CO2的腐蚀机理
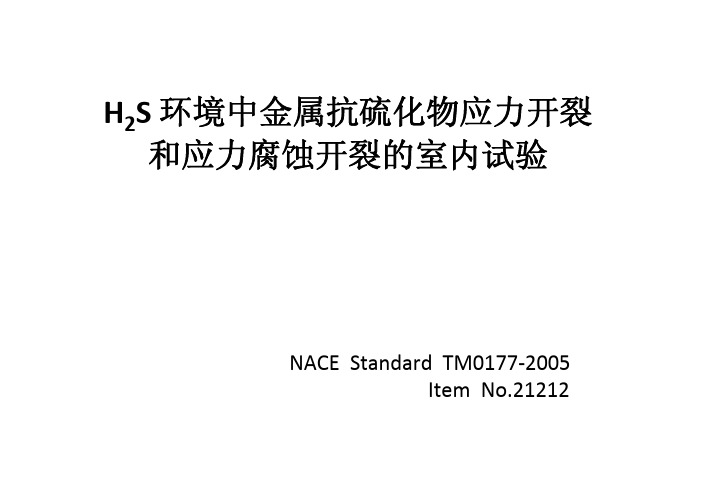
H2S 环境中金属抗硫化物应力开裂和应力腐蚀开裂的室内试验NACE Standard TM0177‐2005Item No.212121总则2试剂及试验溶液3测试试样及材料性能5高温/压力条件下试验6试验方法A‐NACE标准拉伸试验7试验方法B‐NACE标准弯曲试验8试验方法C‐NACE标准C‐环试验1、总则1.1本标准涵盖了在含H2S的低pH值水溶液中,遭受拉伸应力的金属材料抗开裂失效的试验。
碳钢和低合金钢通常在室温下测试EC抗力,在这个温度条件下,它们的SSC敏感性是较高的。
对于其它类型的合金来说,EC敏感性和温度的关系更加复杂。
1.2本标准描述了试剂、检测样品和所用设备,讨论了基本材料和测试试样的性能,接着说明了试验步骤。
本标准介绍了4种试验方法:试验方法A-NACE标准拉伸试验试验方法B-NACE标准弯曲试验试验方法C-NACE标准C-环试验试验方法D-NACE标准双悬臂梁(DCB)试验本标准的第1至5部分给出了用于4种试验方法总的评论。
第6至19部分说明了每一种试样的试验方法。
表明了检测每种样品所需要的检测方法。
在每一种试验方法开始描述之前,给出有助于判定该试验方法适用性的总的指导方针(6-9 部分)。
实验结果报告也被讨论到。
1、总则1.3可在温度和压力下对金属进行抗EC试验,温度和压力可以是室温的(大气条件的),或高温压力条件的。
1.4 该标准可被用作接受或拒绝试验,来保证产品达到EC 抗力的某种最低水平,这由API说明5CT,ISO11960指定,或由使用者或购买者指定。
为了研究或提供信息的目的,该标准可提供产品EC抗力的定量测量。
试验方法A 在720小时内,最高非失效应力。
试验方法B 在720小时内,对50%失效概率,统计基础上的临界应力因子(SC)。
试验方法C 在720小时内,最高非失效应力。
试验方法D 对有效试验来说,重复测试试样的平均KISSC (SSC门槛应力强度系数)。
油管钢的H2S/CO2动态腐蚀行为

, %
试验前 , 1 0 3 0 8 0 10 0 120和 20 0 用 8 ,8 ,0 , 0 , 0 0 号水砂纸逐级打磨试样表面, 然后用清水冲洗试样
前通人高纯氮 2h除氧, 以模拟油井下无氧的实际 情况 。升 温至 预 定 温 度 , 人 C 2 H S至 预 定 通 O 和 2
l 0口井 1 7次发 生 管柱 穿 孔 与断脱 事 故 ; 中国石 油
天然 气股 份有 限公 司 吉林 油 田分 公 司万 五 井 投 产
不到 3年 , 油套 管 即被 C 气 体腐 蚀 , 使 8 0m O 致 0 油管 掉落井 下 , 报废 。 国内其 他一 些主力 油 田 油井 也均 出现 因 H S和 C : 蚀 导 致 油 井 报 废 的事 O 腐 故 。近年来 , 随深层 含油 气藏 的开 发 , 伴 油气 田钻
在着 H S和 C 蚀, O腐 造成 了巨大的经济损失。 美国 的 LteC ek油 田在未 采 取抑 制 H S和 C il re t 2 O 腐蚀措施的油井套管不到 5 个月便腐蚀穿孔 , 腐蚀
速率 高达 l. m/ ; 斯敦 北 Pr nie油气 田 27m a休 es vl o l N 0套管使 用 不 到 一 年 即腐 蚀 穿 孔 , 蚀 速 率 为 8 腐 56mm a . / 。中国石油化工 股 份有 限公 司 中原 油 田 分公 司 19 95年以来 就因 H S和 C : O 腐蚀而造成
研
广
究
C o 化o e t 腐 toc 与 n ty 石ri Pr t工on n e蚀hemialI dus护 os 油 ro 防 r n& ci i P r c
2 1 0 0 , 2 7 ( 6 ) ・ 1 ・ 7
材料在h2s和co2环境中的腐蚀机理和控制研究

材料在h2s和co2环境中的腐蚀机理和控制研究材料在h2s和co2环境中的腐蚀机理和控制研究一、引言在实际工程中,材料腐蚀一直是一个重要的问题。
尤其是在含有H2S 和CO2等腐蚀性气体的环境中,材料的腐蚀问题更加突出。
对材料在H2S和CO2环境中的腐蚀机理和控制研究具有重要的实际意义。
本文将从腐蚀机理、腐蚀控制以及个人观点和理解等方面展开探讨。
二、材料在H2S和CO2环境中的腐蚀机理1. 概述H2S和CO2是常见的腐蚀性气体,它们可以在一定条件下对金属材料进行腐蚀。
在H2S和CO2环境中,腐蚀机理主要包括化学腐蚀和电化学腐蚀两种类型。
2. 化学腐蚀化学腐蚀是指金属材料在H2S和CO2环境中直接与腐蚀性气体发生化学反应,导致金属表面的腐蚀。
在H2S环境中,金属很容易与H2S 气体发生反应生成金属硫化物,从而导致材料的腐蚀。
3. 电化学腐蚀电化学腐蚀是指金属材料在H2S和CO2环境中通过电化学过程引起的腐蚀。
这种腐蚀机理与材料的电化学性质有关,主要包括阳极溶解和阴极还原等过程。
三、材料在H2S和CO2环境中的腐蚀控制1. 表面涂层表面涂层是一种常见的腐蚀控制方法,通过在金属表面涂覆一层具有良好腐蚀性能的材料,来提高材料的抗腐蚀能力。
对电力设备中的金属部件进行漆包处理,可以有效地防止H2S和CO2对金属的腐蚀。
2. 硬质合金涂层硬质合金涂层是一种新型的腐蚀控制技术,它具有高硬度、耐磨损和良好的耐腐蚀性能。
这种涂层可以有效地提高材料在H2S和CO2环境中的抗腐蚀能力。
3. 材料合金设计通过合金设计,可以改变材料的化学成分和微观结构,从而提高材料的抗腐蚀能力。
向铁基材料中加入Cr、Ni等合金元素,可以明显地提高材料在H2S和CO2环境中的抗腐蚀能力。
四、个人观点和理解在我看来,材料在H2S和CO2环境中的腐蚀问题是一个复杂而又重要的课题。
腐蚀是材料科学中的一个长期研究课题,而在含有H2S和CO2等腐蚀性气体的环境中的腐蚀问题更加突出。
H2S及CO2对管道腐蚀机理与防护研究

变 化 。硫化 铁组 成及 结构 均不 相 同 ,其 对腐 蚀过 程
的影 响也 不 相 同 。影 响 H s腐 蚀 的 主 要 因 素 是 :
① H S浓 度 ;②p 值 ;③ 温度 、压 力 。 H
物 质 ,对单 含 C 或 H。 O。 S天然 气 输 送 管 道 的 高 温
2 C 腐 蚀 机 理 O2
天然 气输 送 管 道 在 H: 、c 高 温 高 压 作 用 下 腐 s O 蚀现 象 较 为 普 遍 ,所 以研 究 同 时 含 H。 、C 输 S O
送管 道高 温高 压多相 流环 境 中的腐 蚀行 为 和防护 技 术很 有必要 ,对 我 国油气 开采 具有 重大 的工 程应 用
价值 。
H S是 弱 酸 , 在 溶 液 中 按 下 式 离 解
H 2 — H + HS一 2 S 一 H + S 一 () a
送管道 日益 严 重 的 腐 蚀 问题 ,分 别研 究 了 H2 S和 C 对 管 道 的 腐 蚀 情 况 及 腐 蚀 机 O 的 理 ,对各 自作 用 下的影 响 因素做 了一 定 的分 析 ,进 一步研 究 H: S及 C) ( 2对管道 共 同作 用 机理 ,有针 对性地提 出防护和 管道延寿措施 。 关键 词 :天 然 气 ;H2 ;C 2 S O ;腐 蚀 ;
管 道
H S、 Co 是 最 常 见 和 最 有 害 的 两 种 腐 蚀 管 道
溶液中 S 卜与 F 发 生 以下化 学 反应 e
z Fe + Y S 一 Fe S 。 卜 () b
F 为各 种 结构 硫化 铁 的通 式 。随 着溶 液 中 eS
( ) 反 应 的 进 行 ,溶 液 中 H S含 量 及 p 值 随 之 b H
管道运输对co2中h2s的要求
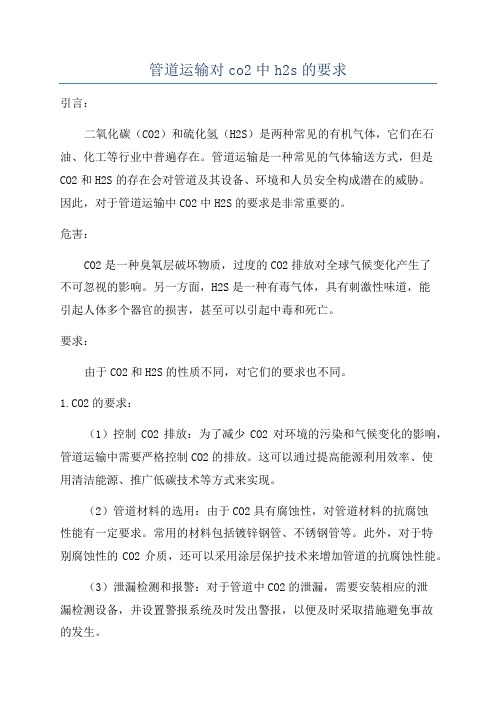
管道运输对co2中h2s的要求引言:二氧化碳(CO2)和硫化氢(H2S)是两种常见的有机气体,它们在石油、化工等行业中普遍存在。
管道运输是一种常见的气体输送方式,但是CO2和H2S的存在会对管道及其设备、环境和人员安全构成潜在的威胁。
因此,对于管道运输中CO2中H2S的要求是非常重要的。
危害:CO2是一种臭氧层破坏物质,过度的CO2排放对全球气候变化产生了不可忽视的影响。
另一方面,H2S是一种有毒气体,具有刺激性味道,能引起人体多个器官的损害,甚至可以引起中毒和死亡。
要求:由于CO2和H2S的性质不同,对它们的要求也不同。
1.CO2的要求:(1)控制CO2排放:为了减少CO2对环境的污染和气候变化的影响,管道运输中需要严格控制CO2的排放。
这可以通过提高能源利用效率、使用清洁能源、推广低碳技术等方式来实现。
(2)管道材料的选用:由于CO2具有腐蚀性,对管道材料的抗腐蚀性能有一定要求。
常用的材料包括镀锌钢管、不锈钢管等。
此外,对于特别腐蚀性的CO2介质,还可以采用涂层保护技术来增加管道的抗腐蚀性能。
(3)泄漏检测和报警:对于管道中CO2的泄漏,需要安装相应的泄漏检测设备,并设置警报系统及时发出警报,以便及时采取措施避免事故的发生。
2.H2S的要求:(1)控制H2S排放:由于H2S是一种有毒气体,对人体和环境都有危害,因此管道运输中要严格控制H2S的排放。
这可以通过对原材料进行预处理、选择低H2S含量的原料、使用H2S去除剂等方式来实现。
(2)材料选择和防腐蚀:与CO2类似,H2S也具有腐蚀性。
因此,在管道材料的选择上,要考虑其抗腐蚀能力。
常用的材料包括不锈钢、合金钢等。
此外,管道的内部和外部还可以进行防腐蚀处理,如涂层、阻隔层等。
(3)监测和保护:管道运输中需要安装H2S监测设备,定期检测管道中H2S的含量。
对于含有高浓度H2S的气体,需要采取相应的措施进行保护,如使用H2S预处理设备、加装气体纯化装置等。
H2S-CO2

分 离 器水 出 口
入 口
一
一 2 6 2 o o o 1 5 8 o o o 4 0 0 . 5 0 0 1 . 5 4
0. 3 5 0 1 . 2 3
0 . 4 2 6 2 1 6 . 2 6 2 6 2 o o o l 5 8 o o o 7 0
B N S管线 钢在 伊 朗北 阿油 田高 硫 高盐 强腐 蚀 介 质 中 的 腐蚀 规 律 尚无 系 统 研 究 。 本 工 作 针 对 该 油 田产 出水 、 注入 水 和 油气 介质 高硫 高 盐 工 况 强腐 蚀 介 质 下 的 腐蚀
特点 , 通过动态模拟试验研究了其均匀腐蚀速率 , 探讨 了温度 、 气 体压 力 和 c l 一 浓 度 对 金 属腐 蚀 速率 的影 响 ,
对伊 朗北 阿 油 田 B N S管线钢 在 温度 、 压力、 C l 一 浓度 变化 下的 腐蚀规 律进 行 了研 究。结 果表 明 : 在H S . C O , 低 分压 下, B N S管线钢 的腐蚀 产 物 为C a C O , 随 着温度 的 升 高 , 腐蚀 速 率先减 小后 增 大 , 随着压 力的增加 , 腐蚀速 率减 小 , 随
表 1 伊 朗 北 阿 油 田工 况 条 件
P( 气相 ) / k P a
测 试 位 置
( mg ‘ L
含盐 C I 一
o FC 力) /
…
m .
.、
1 试
验
井口
。 . …
s . …
z…
s
2 5 -
1 . 1 材 料 及前处 理
清 除其表 面 残屑 , 用含 丙酮 的棉 花球 擦 拭 去 除油 污 ; 蒸
超高温h2-h2s-co2-h2o井下环境渗铝钢的腐蚀及氢损伤机理
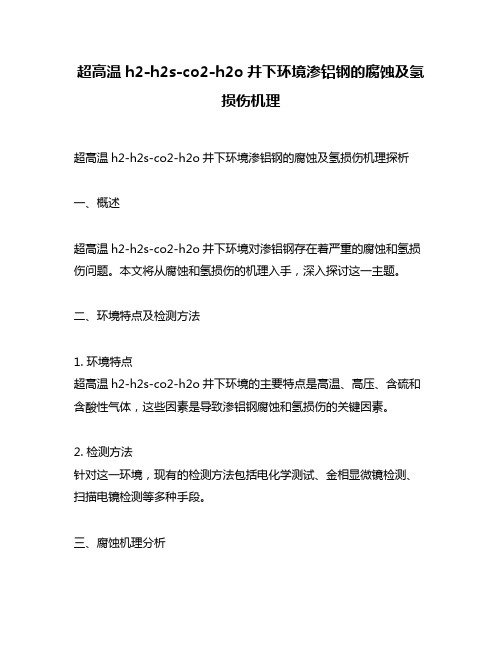
超高温h2-h2s-co2-h2o井下环境渗铝钢的腐蚀及氢损伤机理超高温h2-h2s-co2-h2o井下环境渗铝钢的腐蚀及氢损伤机理探析一、概述超高温h2-h2s-co2-h2o井下环境对渗铝钢存在着严重的腐蚀和氢损伤问题。
本文将从腐蚀和氢损伤的机理入手,深入探讨这一主题。
二、环境特点及检测方法1. 环境特点超高温h2-h2s-co2-h2o井下环境的主要特点是高温、高压、含硫和含酸性气体,这些因素是导致渗铝钢腐蚀和氢损伤的关键因素。
2. 检测方法针对这一环境,现有的检测方法包括电化学测试、金相显微镜检测、扫描电镜检测等多种手段。
三、腐蚀机理分析1. 腐蚀类型根据环境特点,超高温h2-h2s-co2-h2o环境下的腐蚀类型主要包括晶间腐蚀、点蚀和应力腐蚀裂纹等。
2. 腐蚀机理(1)硫化物腐蚀:高温高压下的硫化物腐蚀是导致渗铝钢腐蚀的重要原因之一。
硫化物与金属表面形成复杂的化合物,破坏了金属的表面保护膜,导致腐蚀的加剧。
(2)酸性腐蚀:含酸性气体的环境会导致金属表面发生腐蚀,而在高温高压环境下,其腐蚀速度更是惊人。
四、氢损伤机理探讨1. 引入氢损伤概念及影响因素氢损伤是金属在含氢环境中受到氢的侵入而造成的破坏,超高温h2-h2s-co2-h2o井下环境中氢的存在对渗铝钢的影响极为显著。
2. 氢损伤机理(1)氢脆:在氢气的作用下,渗铝钢易发生氢脆破裂,导致材料强度降低和脆性断裂。
(2)氢致开裂:渗铝钢在超高温高压下,氢会进入晶界和位错处,导致金属的开裂和脆性破坏。
五、个人观点和总结在超高温h2-h2s-co2-h2o井下环境渗铝钢的腐蚀及氢损伤机理分析中,我们能够清晰地看到这些环境因素对于金属材料的破坏性作用。
针对这一问题,我们需要制定相应的材料选型、防腐蚀措施以及监测和维护方案,以最大限度地减少金属材料的腐蚀和氢损伤。
在未来的工程实践中,我们需要不断深入研究腐蚀和氢损伤的机理,提出更加有效的解决方案,保障井下设备的安全和稳定运行。
4第四章H2S和CO2腐蚀环境和实例P1-15 09.5.21.
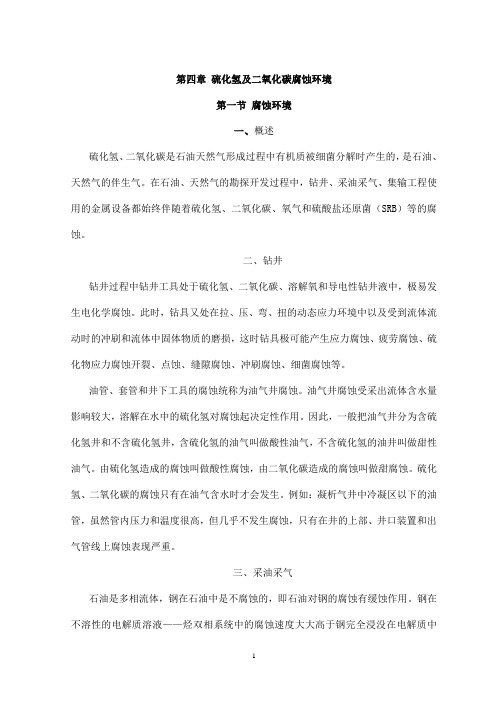
第四章硫化氢及二氧化碳腐蚀环境第一节腐蚀环境一、概述硫化氢、二氧化碳是石油天然气形成过程中有机质被细菌分解时产生的,是石油、天然气的伴生气。
在石油、天然气的勘探开发过程中,钻井、采油采气、集输工程使用的金属设备都始终伴随着硫化氢、二氧化碳、氧气和硫酸盐还原菌(SRB)等的腐蚀。
二、钻井钻井过程中钻井工具处于硫化氢、二氧化碳、溶解氧和导电性钻井液中,极易发生电化学腐蚀。
此时,钻具又处在拉、压、弯、扭的动态应力环境中以及受到流体流动时的冲刷和流体中固体物质的磨损,这时钻具极可能产生应力腐蚀、疲劳腐蚀、硫化物应力腐蚀开裂、点蚀、缝隙腐蚀、冲刷腐蚀、细菌腐蚀等。
油管、套管和井下工具的腐蚀统称为油气井腐蚀。
油气井腐蚀受采出流体含水量影响较大,溶解在水中的硫化氢对腐蚀起决定性作用。
因此,一般把油气井分为含硫化氢井和不含硫化氢井,含硫化氢的油气叫做酸性油气,不含硫化氢的油井叫做甜性油气。
由硫化氢造成的腐蚀叫做酸性腐蚀,由二氧化碳造成的腐蚀叫做甜腐蚀。
硫化氢、二氧化碳的腐蚀只有在油气含水时才会发生。
例如:凝析气井中冷凝区以下的油管,虽然管内压力和温度很高,但几乎不发生腐蚀,只有在井的上部、井口装置和出气管线上腐蚀表现严重。
三、采油采气石油是多相流体,钢在石油中是不腐蚀的,即石油对钢的腐蚀有缓蚀作用。
钢在不溶性的电解质溶液——烃双相系统中的腐蚀速度大大高于钢完全浸没在电解质中的腐蚀速度,当有硫化氢存在时,这一差值更大。
腐蚀一般发生在烃——电解液不混溶的相界面上,迅速受到腐蚀的设备有储存石油和石油产品的容器底部、油气管道、石油破乳装置等。
油气藏的地层水是高矿化度的盐类溶液,主要含有氯化钠、氯化钙,当其中不含硫化氢、二氧化碳或氧气时,对油气田钢质设备只有微弱腐蚀性;当地层水中存在硫化氢、二氧化碳或氧气时,水的腐蚀活性急剧增加。
流速和腐蚀速度成正比,高流速会促进腐蚀加快,而流体中含有固体微粒时,会使磨蚀急剧增加。
四、油气集输油气田集输系统指油气井采出液(气)从井口经单井管线进入计量站,再经计量支干线进入汇管,最后进入油气联合处理站,处理后的原油、天然气进入外输管道长距离外输。
第四讲二氧化碳与硫化氢
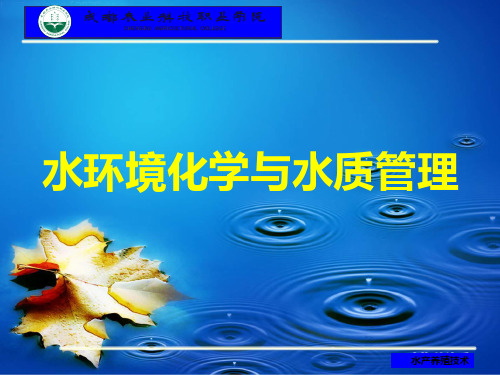
水环境化学与水质管理
水产养殖技术
水中二氧化碳与硫化氢
二氧化碳
一、二氧化碳在养殖水体的作用
1、水生植物光合作用的原料; 2、构成一个复杂的二氧化碳平衡系统, 影响pH值和碱度; 3、高浓度二氧化碳对鱼类有麻痹和毒 害作用。
(5)同化作用
硫是合成蛋白质必须的元素,许多植物、藻类、细 菌可以吸收利用SO42-中的硫合成蛋白质。 H2S不 被吸收,只有某些特殊细菌可以利用H2S进行光合 作用,将H2S转变成S或SO42- ,同时合成有机物, 类似绿色植物的光合作用,只是前者不释放O2。
三、消除水中硫化氢的措施: 1)提高溶氧量,促进水的垂直流动; 2)保持水体pH为中性或者微碱性 3)避免大量含硫酸盐的水体进入; 4) 使用铁剂(红土,黄土---含铁量丰富), 生成无毒的硫化亚铁固定在底泥中.
二氧化碳
一、来源
缺氧条件下,含硫有机物经嫌气细菌分解 产生;或者硫酸盐在硫酸盐细菌作用下生成硫 化物之后生成硫化氢.二者都有毒性,其中硫化 氢毒性最强.一般水体中H2S含量在2.0ug/L时, 对大多数鱼类及其他生物是无害的。
二、硫在水中转化
1、硫在水中存在形态:SO42- 、HS-、H2S、含硫 蛋白质、SO32-、S2O32-、单质硫等。
(1)蛋白质分解作用: 硫在蛋白质中以巯基形 式存在。在微生物作用下,无论有氧或无氧环境, 蛋白质中的硫,首先分解为-2价硫( H2S 、 HS等)。在无游离氧的环境中HS-可稳定存在,在 有游离氧的环境中HS-能迅速被氧化为高价形态。
H2S腐蚀研究进展之欧阳文创编

H2S腐蚀研究进展摘要近年来我国发现的气田均含有硫化氢、二氧化碳等腐蚀性气体,特别是我们四川盆地,含硫化氢天然气分布最广泛。
众所周知,硫化氢腐蚀是井下油套管的主要腐蚀类型之一。
本文简述了硫化氢的物性,研究了硫化氢腐蚀的机理和影响因素,并在此基础上介绍了采用缓蚀剂、涂镀层管材、根据国际标准合理选材、电化学保护等几种国内外常用的防腐措施,并指出了各种方法的优缺点,最后还探讨了硫化氢油气田腐蚀研究的热点问题及发展方向。
关键词:硫化氢腐蚀,腐蚀机理,防腐技术ABSTRACTIn recent years, the gas fields found in our country contain hydrogen sulfide, carbon dioxide and other corrosive gases, especially in the Sichuan basin, with the most extensive distribution of hydrogen sulfide gas. It is well known that the hydrogen sulfide corrosion is one of the main corrosion types of the oil casing in the well. Properties of hydrogen sulfide is described in this paper to study the hydrogen sulfide corrosionmechanism and influencing factors, and on this basis, introduces the corrosion inhibitor, coating tubing, according to international standard and reasonable material and electrochemical protection at home and abroad, several commonly used anti-corrosion measures, and points out the advantages and disadvantages of each method, and finally discusses the hot issues and development direction of the research on oil and gas fields of hydrogen sulfide corrosion by.Key words:hydrogen sulfide corrosion, corrosion mechanism, corrosion protection technology.前言随着各国经济的发展,对石油及天然气需求进一步增加,易开采的油气资源已趋于枯竭,油井的发展趋势向着高技术方向发展,钻探区域势必转移向内陆、沙漠等环境恶劣的地区。
油气生产中的二氧化碳腐蚀ppt课件
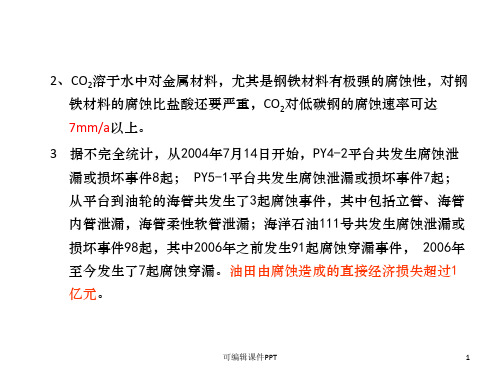
2、CO2溶于水中对金属材料,尤其是钢铁材料有极强的腐蚀性,对钢 铁材料的腐蚀比盐酸还要严重,CO2对低碳钢的腐蚀速率可达 7mm/a以上。
3 据不完全统计,从2004年7月14日开始,PY4-2平台共发生腐蚀泄 漏或损坏事件8起; PY5-1平台共发生腐蚀泄漏或损坏事件7起; 从平台到油轮的海管共发生了3起腐蚀事件,其中包括立管、海管 内管泄漏,海管柔性软管泄漏;海洋石油111号共发生腐蚀泄漏或 损坏事件98起,其中2006年之前发生91起腐蚀穿漏事件, 2006年 至今发生了7起腐蚀穿漏。油田由腐蚀造成的直接经济损失超过1 亿元。
I-
2979.88 672.09 2958.16
0
3.14
Br-
B-
0.5
21.31
K+
Na+
Ca2+
Mg2+
Cu2+
Fe2+
137.5 1954.35 28.57
144.42
0.47
0.28
➢ 油井油套管在油田水中的腐蚀
试验 条件
腐蚀 评价 及试 验结 果
温度:100℃;压力:PCO2=0.03MPa,P0=6.8MPa;液相介质: 离子水;试验周期:144h(不更换溶 液);液相介质速度:2.62m/s;试样位置:液相
反应产物需处理加热 油溶性 水溶性
较低浓度时效果明显
可编辑课件PPT
24
二氧化碳腐蚀防护措施
3、防腐涂层或非金属材料——酚醛涂料、环氧涂料、塑料衬 管、纤维增强塑料、橡胶等
(1)四川石油管理局川西南矿区 威93井、威23井、威35井——聚苯硫醚涂
(2)美国西德克萨斯,为防CO2腐蚀油管通常采用聚乙烯衬 里,油套环空采用防腐剂,防腐剂可将腐蚀速度降到2.5mm/a
- 1、下载文档前请自行甄别文档内容的完整性,平台不提供额外的编辑、内容补充、找答案等附加服务。
- 2、"仅部分预览"的文档,不可在线预览部分如存在完整性等问题,可反馈申请退款(可完整预览的文档不适用该条件!)。
- 3、如文档侵犯您的权益,请联系客服反馈,我们会尽快为您处理(人工客服工作时间:9:00-18:30)。
第四章硫化氢及二氧化碳腐蚀环境第一节腐蚀环境一、概述硫化氢、二氧化碳是石油天然气形成过程中有机质被细菌分解时产生的,是石油、天然气的伴生气。
在石油、天然气的勘探开发过程中,钻井、采油采气、集输工程使用的金属设备都始终伴随着硫化氢、二氧化碳、氧气和硫酸盐还原菌(SRB)等的腐蚀。
二、钻井钻井过程中钻井工具处于硫化氢、二氧化碳、溶解氧和导电性钻井液中,极易发生电化学腐蚀。
此时,钻具又处在拉、压、弯、扭的动态应力环境中以及受到流体流动时的冲刷和流体中固体物质的磨损,这时钻具极可能产生应力腐蚀、疲劳腐蚀、硫化物应力腐蚀开裂、点蚀、缝隙腐蚀、冲刷腐蚀、细菌腐蚀等。
油管、套管和井下工具的腐蚀统称为油气井腐蚀。
油气井腐蚀受采出流体含水量影响较大,溶解在水中的硫化氢对腐蚀起决定性作用。
因此,一般把油气井分为含硫化氢井和不含硫化氢井,含硫化氢的油气叫做酸性油气,不含硫化氢的油井叫做甜性油气。
由硫化氢造成的腐蚀叫做酸性腐蚀,由二氧化碳造成的腐蚀叫做甜腐蚀。
硫化氢、二氧化碳的腐蚀只有在油气含水时才会发生。
例如:凝析气井中冷凝区以下的油管,虽然管内压力和温度很高,但几乎不发生腐蚀,只有在井的上部、井口装置和出气管线上腐蚀表现严重。
三、采油采气石油是多相流体,钢在石油中是不腐蚀的,即石油对钢的腐蚀有缓蚀作用。
钢在不溶性的电解质溶液——烃双相系统中的腐蚀速度大大高于钢完全浸没在电解质中的腐蚀速度,当有硫化氢存在时,这一差值更大。
腐蚀一般发生在烃——电解液不混溶的相界面上,迅速受到腐蚀的设备有储存石油和石油产品的容器底部、油气管道、石油破乳装置等。
油气藏的地层水是高矿化度的盐类溶液,主要含有氯化钠、氯化钙,当其中不含硫化氢、二氧化碳或氧气时,对油气田钢质设备只有微弱腐蚀性;当地层水中存在硫化氢、二氧化碳或氧气时,水的腐蚀活性急剧增加。
流速和腐蚀速度成正比,高流速会促进腐蚀加快,而流体中含有固体微粒时,会使磨蚀急剧增加。
四、油气集输油气田集输系统指油气井采出液(气)从井口经单井管线进入计量站,再经计量支干线进入汇管,最后进入油气联合处理站,处理后的原油、天然气进入外输管道长距离外输。
油气集输系统内腐蚀主要指硫化氢、二氧化碳的腐蚀。
联合处理站是进行油、气、水三相分离的场所,一般分为水区、油区,水区腐蚀严重,油区腐蚀常发生在水相部分和气相部分,如:三相分离器底部、罐底部、罐顶部及污水管道、加热套管等。
注水开发是保持底层压力和油田稳定的重要措施。
注水系统腐蚀主要是油田污水中的硫酸盐还原菌(SRB)、二氧化碳和氯化物共同作用造成的。
稠油注蒸汽开发可提高稠油中二氧化碳的含量、分解稠油中的硫化物放出硫化氢,氧则来自于锅炉水,这些都会对稠油注蒸汽系统造成腐蚀。
稠油注蒸汽开发的压力一般为17MPa、温度280-350℃。
注水管线有可能发生氢腐蚀,这种氢腐蚀有两种表现,一种是碱土金属的氯化物水解酸化引起的氢脆,另一种是水蒸气腐蚀,二者共同特点是反应生成的H进入钢中,与渗碳体(Iron Corrbide,Fe3C)反应生成甲烷CH4导致钢铁脆裂,即氢腐蚀。
第二节硫化氢腐蚀一、概念含有硫化氢的油气称酸性油气,由此引起的腐蚀称酸性腐蚀,也叫硫化氢腐蚀。
石油工业中的硫化氢来源有3个方面:地层流体中原生硫化氢;硫酸盐还原菌(SRB)分解出的硫化氢;添加的含硫化学剂,如磺化高分子化合物降解放出的硫化氢。
硫化氢腐蚀形态有:均匀腐蚀、点蚀、硫化物应力腐蚀开裂(SSCC)和氢致开裂(HIC),氢致开裂常伴着钢表面的氢鼓泡(HB)。
干燥的硫化氢对金属无腐蚀性,当硫化氢溶解在水里变成弱酸时才对金属具有腐蚀性。
二、腐蚀机理1.电化学腐蚀H2S易溶于水,其溶解度与分压和温度有关。
在含硫气井,一旦产层出水,水的酸度会很高,腐蚀严重。
溶解的H2S很快电离,其离解反应为:H2S→HS- + H+HS-→S2- + H+氢离子是强去极化剂,它在钢铁表面夺取电子后还原成氢原子,这一过程称为阴极反应。
失去电子的铁与硫离子反应生成硫化亚铁,这一过程称为阳极反应,铁作为阳极加速溶解反应而导致腐蚀。
其电化学反应可表示为:阳极反应:Fe→Fe2+ + 2e阴极反应:2H+ +2e →2H阳极产物:Fe2+ +S2-→FeS总反应为:Fe + H2S →FeS + 2H上述反应造成的严重后果是:(1)生成氢原子,导致钢铁氢脆。
H2S(s)和或HS-的存在阻止氢原子生成氢分子。
过量氢原子形成氢压,向金属缺陷处渗透和富集。
(2)H2S 分压越高,H+浓度也越高,溶液pH值越低,由此加剧金属的腐蚀。
阴极产物FeS 或FeS2是比较致密的保护膜,它将阻止腐蚀的持续进行。
但是由于腐蚀环境的差异,阳极产物还有其他结构形式的硫化铁,如Fe3S4、Fe9S8等,它们的结构缺陷、对金属的附着力差,甚至作为阴极端面而与钢铁表面形成电位差,产生电偶腐蚀。
在CO2、氯离子、氧共存环境中,硫化铁膜可能被破坏,从而加快电化学腐蚀。
2.钢材在H2S 中的环境断裂行为(1)氢致开裂(HIC,hydrogen-induced cracking)当原子氢扩散进钢铁中并存在缺陷处结合成氢分子(氢气)时,所出现在碳钢和低合金钢中的平面裂纹。
裂纹是由于氢的聚集点压力增大而产生的,氢致开裂的产生不需要施加外部的应力。
能够引起HIC 的聚集点常常发生在钢中杂质水平较高的地方,通常称为陷阱。
富集在陷阱中的氢原子一旦结合成氢分子,积累的氢气压力很高(可达300MPa),促使金属脆化,局部区域发生塑性变形,萌生裂纹导致局部开裂。
(2)硫化物应力开裂(SSC,sulfide stress cracking)在有水和H2S存在的情况下,与腐蚀和应力有关的一种金属开裂。
SSC是氢应力开裂(HSC)的一种形式,它与金属表面的因酸性腐蚀所产生的原子氢引起的金属脆性有关。
在硫化物存在时,会加速氢的吸收。
原子氢能扩散进金属,降低金属的韧性,增加裂纹的敏感性。
高强度金属材料和较硬的焊缝区域易于发生SSC。
(3)氢应力开裂(HSC,hydrogen stress cracking)金属在有氢和拉应力(残余应力和/或工作应力)存在的情况下出现的一种开裂。
HSC描述对SSC不敏感的金属中的一种开裂现象,这种金属作为阴极和另一种易被腐蚀的金属作为阳极形成电偶,在有氢时,金属就可能变脆。
HSC用于描述不锈钢或合金与碳钢或低合金钢连接时,受电偶激发,不锈钢或合金中的组织缺陷聚集氢和变脆的现象和机理。
(4)软区裂纹(soft zone cracking)SZC是SSC的一种形式,当钢中含有屈服强度较低的局部“软区”时,可能会产生SZC。
在操作的载荷作用下,软区会屈服,并且局部塑性应变扩展,这一过程加剧了非SZC材料对SSC的敏感性。
这种软区与碳钢的焊接有关。
(5)应力腐蚀开裂(SCC,stress corrosion cracking)在有水和H2S存在的情况下,与局部腐蚀的阳极过程和拉应力(残余应力和/ 或工作应力)相关的一种金属开裂。
氯化物和/或氧化剂和高温能增加金属产生应力腐蚀开裂的敏感性。
(6)氢致鼓泡(HIB,hydrogen-induced blister)当介质呈酸性时,由于阴离子的大量存在,FeS保护膜被溶解,材料表面处于活性溶解状态,有利于反应过程中产生的氢原子向管材内部渗透。
这些氢原子渗入金属管材内部后,在金属材料的薄弱部位(例如孔穴、非金属夹杂物处)聚集,结合成氢分子。
随着聚集过程的进行,在某些部位,氢气压力可达上百兆帕。
此外,氢原子还能与材料中夹杂的Fe3C反应生成CH4,同样产生气体并聚集。
气体所产生的压力,在材料中形成很高的内应力,致使材料较薄弱面发生塑性变形,造成钢夹层鼓起,即为“鼓泡”。
“鼓泡”也是一种“开裂”,是应力腐蚀析氢所引起的断裂。
“鼓泡”可以在无外部载荷下发生。
三、腐蚀实例目前国内部分油田已进入高含水期开发,有的新油管下井一年后即发生穿孔,3年就得全部更换。
据初步分析,注水井套管的腐蚀速率约为每年0.5-0.6mm,维持费逐年增大,油管、抽油杆、泵等设备的更换,每年约为2.5亿元。
胜利油田已进入特高含水开发期,采出污水中含有溶解氧,SRB,O2, H2S,Cl-,对钢管管材腐蚀相当严重,平均腐蚀速率1-7mm/a,应力作用下的点蚀速率14mm/a。
胜利油田现有地面管线20000km,其中原油集输、污水、注水管线占85%。
钢管年更换率为2.5%,每年至少更换400km,损失达6000万元。
中原油田因水质偏酸性且极不稳定引发腐蚀造成的直接经济损失每年约7000万元,间接经济损失约2亿元。
大庆油田现有地面管线约40000km,平均寿命9年,年更换率12.9%。
油管柱约50000km,平均寿命3年。
四川于1963年左右发现含硫气田。
由于当时对硫化氢的腐蚀缺乏认识,以致从勘探到开发,从井下到地面,从钻杆、套管、油管、采气井口压力表、抽油杆到气田集输管线都发生了多次硫化氢腐蚀破坏。
1966年威远气田开发初期,在短短几个月内,8口井连续发生9次油管断裂事故。
1968年投产的威成输气管道由于输送含有硫化氢和水的天然气冲蚀管壁,使原来8mm的管壁减薄到1.2mm,于1971年1月和5月连续两次发生强烈爆管事故。
九十年代中后期,四川气田生产的天然气中70%以上含H2S和CO2,天然气H2S含量(按体积百分数)大致可分为四种:H2S含量7%-13%,如中坝气田;H2S含量4.7%-7.3%,如卧龙河气田;H2S含量1.22%,如威远气田;H2S含量小于1%,如付家庙气田。
通过多年的研究和生产实践,四川气田摸索了一套防止硫化氢腐蚀的综合技术措施,基本上保证了含硫气田的正常开发。
1976年11月26日华北油田勘探完井的赵二井,试井测试五天,最高产气量10×104m3/d ,H2S含量92%(相当于1400g/m3),井内抗硫油管接触硫化氢仅50h10min ,在井深177.01m处断裂。
此后国内外至今没有单位敢接受该气田的开采任务。
第三节二氧化碳腐蚀一、概念1925年API首次提出二氧化碳腐蚀概念,1943年首次发现Texas油田气井中的油管腐蚀为二氧化碳腐蚀。
二氧化碳溶于水对钢铁具有很强的腐蚀性,由此而引起的材料破坏统称为二氧化碳腐蚀。
油气田二氧化碳来自天然气、油田伴生气、开采石油注入的二氧化碳和采出水中HCO3—减压升温过程中分解出来的二氧化碳。
二氧化碳溶于水形成碳酸(H2CO3),碳酸是一个二元酸,在相同的pH值下,对钢铁的腐蚀比盐酸还严重,低碳钢的二氧化碳腐蚀速度可高达7mm/a,甚至更高,腐蚀产物为FeCO3。
新鲜的FeCO3为黑色,暴露在空气中后会被氧化为氧化铁,颜色由黑变黄。