压力容器铆金工艺文件
压力容器制造铆工工艺制造篇
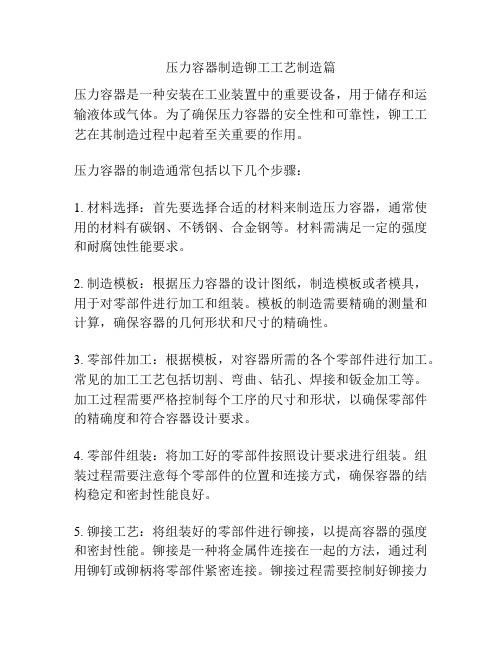
压力容器制造铆工工艺制造篇压力容器是一种安装在工业装置中的重要设备,用于储存和运输液体或气体。
为了确保压力容器的安全性和可靠性,铆工工艺在其制造过程中起着至关重要的作用。
压力容器的制造通常包括以下几个步骤:1. 材料选择:首先要选择合适的材料来制造压力容器,通常使用的材料有碳钢、不锈钢、合金钢等。
材料需满足一定的强度和耐腐蚀性能要求。
2. 制造模板:根据压力容器的设计图纸,制造模板或者模具,用于对零部件进行加工和组装。
模板的制造需要精确的测量和计算,确保容器的几何形状和尺寸的精确性。
3. 零部件加工:根据模板,对容器所需的各个零部件进行加工。
常见的加工工艺包括切割、弯曲、钻孔、焊接和钣金加工等。
加工过程需要严格控制每个工序的尺寸和形状,以确保零部件的精确度和符合容器设计要求。
4. 零部件组装:将加工好的零部件按照设计要求进行组装。
组装过程需要注意每个零部件的位置和连接方式,确保容器的结构稳定和密封性能良好。
5. 铆接工艺:将组装好的零部件进行铆接,以提高容器的强度和密封性能。
铆接是一种将金属件连接在一起的方法,通过利用铆钉或铆柄将零部件紧密连接。
铆接过程需要控制好铆接力度和深度,确保铆接点的牢固和密封性。
6. 焊接工艺:在一些特殊的压力容器制造中,焊接也是必不可少的工艺之一。
焊接通常用于连接大型容器或特殊形状的零部件。
焊接过程需要使用适当的焊接电流和焊材,确保焊接点的强度和密封性。
通过以上的工艺步骤,压力容器的制造可以得到良好的质量和性能。
在整个制造过程中,铆工工艺是一个重要的环节,直接关系到容器的结构强度和安全性能。
因此,制造厂商需要严格遵守相关的制造标准和规范,确保铆接工艺的准确性和可靠性。
同时,对工艺技术人员的培训和技术水平提升也非常重要,以保证压力容器的质量和安全性能。
在压力容器的制造中,铆工工艺起着非常重要的作用。
压力容器铆接是将金属各部分通过铆钉、铆柄或其他形式的连接件进行固定和密封,以保证容器在高压下的工作安全。
压力容器筒体拼接规定(5篇)

压力容器筒体拼接规定为了使锅炉、压力容器上焊缝分布均匀、避免焊接残余应力相互叠加,有关锅炉、压力容器规程中对焊缝的数量和布置做了具体的规定。
(1)筒体拼接时,最短筒节的长度:对于中低压锅炉不应小于300mm,对于高压锅炉不应小于600mm;每节筒体,纵向焊缝的数量:筒体内径Di1800mm时,拼接焊缝不多于2条,Di>1800mm时,拼接焊缝不多于3条;每节筒体两条纵焊缝中心线间的外圆弧长,对于中低压锅炉不应小于300mm,对于高压锅炉不应小于600mm;相邻筒节的纵向焊缝应相互错开,两焊缝中心线间的外圆弧长不得小于钢板厚度的3倍,且不得小于100mm。
(2)封头和管板应尽量用整块钢板制成。
如必须拼接,封头、管板的内径Di2200mm时,拼接焊缝不多于1条,Di>2200mm时,拼接焊缝不多于2条;封头拼接焊缝离封头中心线距离应不超过0.3Di,并不得通过扳边人孔,且不得布置在人孔扳边圆弧上;管板上整条拼接焊缝不得布置在扳边圆弧上,且不得通过扳边孔;由中心圆板和扇形板组成的凸形封头,焊缝的方向只允许是径向和环向的。
径向焊缝之间的最小距离应不小于壁厚的3倍,且不小于100mm。
(3)炉胆拼接焊缝的要求同于筒体。
U形下脚圈的拼接焊缝必须径向布置,两焊缝中心线间最短弧长不应小于300mm。
(4)管子对接焊缝不应布置在管子的弯曲部分。
对于中低压锅炉,受热面管子直段上的对接焊缝的中心线至管子弯曲起点(或锅筒、集箱外壁,或管子支架边缘)的距离。
至少为50mm,对高压锅炉,上述距离至少为70mm;锅炉范围内管道焊缝中心线至管道弯曲起点之间的距离不应小于管道的外径,且不小于100mm;受热面管子直段上,对接焊缝间的距离不得小于150mm。
(5)受压元件主要焊缝及其邻近区域,应避免焊接零件。
如不能避免时,焊接零件的焊缝可穿过主要焊缝,而不要在焊缝及其邻近区域中止。
(6)开孔、焊缝和转角要错开。
开孔边缘与焊缝的距离应不小于开孔处实际壁厚的3倍,且不小于100mm。
铆接工艺标准新版

铆接工艺标准[新版]版本号 A 编号:QCRC-TI-016修改次第 00 QCRC 铆接工艺规范页次/总页数 1/5受控状态:________受控____发放编号:________________生效日期:___2002-09-19__版本号 A 编号:QCRC-TI-016修改次第 00 铆接工艺规范QCRC 页次/总页数 2/5 版本/修改次第更改页次/章节编制审核批准生效日期版本号 A 编号:QCRC-TI-016修改次第 00 铆接工艺规范QCRC 页次/总页数 3/5本规程规定了QCRC铆接工艺要求及质量标准~适用于冷藏箱生产中所有需铆接的零部件及操作人员。
一. 铆钉种类QCRC工厂内所选用的铆钉有半圆头铆钉、扁圆头铆钉、抽芯铆钉、环槽铆钉(哈克钉)等。
二.抽芯铆钉铆接工艺要求1、铆接材料及设备的选用以AVDEL铆钉为例把重要的铆接工艺参数列举如下:铆钉型号铆接厚度钻头大小气压(bar)(mm) (mm)BE61-0509 1.0~3.0 4.1~4.3 80~120BE61-0512 3.0~5.0 4.1~4.3 80~120BE61-0614 3.5~6.0 4.9~5.1 80~120BE61-0618 6.0~8.5 4.9~5.1 80~1202711-0817 4.8~11.1 7.0~7.1 80~1202711-0617 4.8~11.1 4.9~5.1 80~1202774-0613 1.6~6.3 4.9~5.1 80~1202774-0817 4.8~11.1 7 80~1201663-0521 6.4~12.7 4.1~4.2 80~1201663-0613 1.6~6.3 4.9~5.1 80~1201663-0619 4.8~11.1 4.9~5.1 80~1201663-0621 6.4~12.7 4.9~5.1 80~1201663-0631 12.7~19.8 4.9~5.1 80~120 2. 工具的使用每天使用铆枪前检查枪嘴有无碎片,滴几滴润滑油到空气进口里;检查是否有漏气,检查气动枪的气压是否符合说明的最低标准。
铆接操作指导工艺文件

铆接操作指导工艺文件一、前言本工艺文件用于指导铆接操作的步骤和要求,以确保产品质量和生产效率。
操作人员在进行铆接操作前必须仔细阅读和理解本工艺文件,并严格按照要求进行操作,切勿随意修改和变动。
二、操作过程1.准备工作(1)检查所需材料和工具是否齐全,并确保其良好状态。
(2)检查铆接设备的工作状态,如气压、电源等,以确保正常运行。
(3)清理工作区域,确保没有杂物和妨碍操作的障碍物。
(4)佩戴好个人防护装备,包括工作帽、眼镜、手套等。
2.准备工件(1)检查工件的尺寸、材质和表面状态是否符合要求,如有问题应及时报告。
(2)将需要铆接的工件放置在平整、稳定的工作台上,并固定好。
(3)根据工件的特点和要求,选择适当的铆接方法和工具。
3.操作步骤(1)根据工件的形状和尺寸,在合适的位置标记铆孔。
(2)使用钻头或其他工具在标记位置钻孔,确保孔径和深度符合要求。
(3)将铆钉插入铆孔中,并用铆钉锤或其他工具将铆钉固定在工件上。
(4)根据要求和实际情况,对铆钉进行压铆或打磨处理,以确保固定牢固和表面光滑。
(5)对已完成的铆接点进行质量检查,包括外观、强度和尺寸等指标。
(6)记录铆接信息,包括工件编号、铆接日期、操作人员等,以便追溯和质量控制。
4.注意事项(1)严格按照操作要求进行操作,不得随意变动和修改工艺流程。
(2)在操作过程中,应注意安全,确保周围环境整洁、无杂物和障碍物。
(3)对于特殊要求和特殊工件,应根据实际情况进行调整和处理。
(4)操作人员应具备一定的机械和工艺知识,确保能够正确操作设备和工具。
(5)对于出现问题和故障,应及时报告,并配合相关人员进行处理和解决。
三、结束工作1.清理工作区域,将工具和材料归位整理。
2.关闭铆接设备和电源,确保安全。
3.整理并妥善保管铆接文件和记录,以备后续使用和检查。
四、质量控制1.对铆接点进行质量检查,包括外观、强度和尺寸等指标。
2.对于不合格的铆接点,应及时进行整改和处理,并追溯相关责任。
压力容器制造工艺规程(铆工篇)
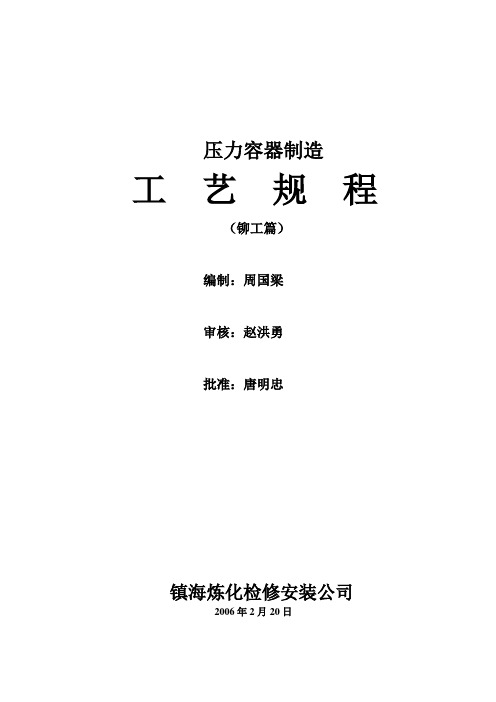
压力容器制造工艺规程(铆工篇)编制:周国梁审核:赵洪勇批准:唐明忠镇海炼化检修安装公司2006年2月20日目录封面---------------------------------------------------------------------------第1页目录------------------------------------------------------------------------ 第2页分片过渡段、封头加工成型(艺01) -------------------------------------第4页筒节下料(艺02)-----------------------------------------------------------第7页筒节滚圆、校圆(艺03)----------------------------------------------- 第9页筒节纵缝组对(艺04)------------------------------------------------第10页筒体环缝组对(艺05)--------------------------------------------------第11页接管/法兰组焊(艺06) ------------------------------------------------第13页换热器管束制作及组装(艺07) ------------------------------------------第16页裙座制作安装(艺08)--------------------------------------------------第20页鞍座制作安装(艺09) --------------------------------------------------第22页腿式支座制座安装(艺10) ------------------------------------------第24页支承式支座制作安装(艺11)--------------------------------------------第26页耳式支座制作安装(艺12) -----------------------------------------------第28页补强圈制作(艺13) -----------------------------------------------------第29页塔顶吊柱制作安装(艺14) -----------------------------------------------第31页吊耳制作安装(艺15) --------------------------------------------------第33页塔盘固定件制作安装(艺16) --------------------------------------------第35页其它内外件制作安装(艺17) --------------------------------------------第38页接管、补强圈安装(艺18)---------------------------------------------第40页空冷器管箱制作(艺19) -----------------------------------------------第45页空冷器附件制作(艺20)--------------------------------------------------第47页空冷器组装(艺21) ------------------------------------------------------第48页绕管换热器管束制作(艺22) --------------------------------------------第50页绕管换热器组装(艺23) ------------------------------------------------第54页水压试验(艺24) --------------------------------------------------------第58页气密性试验(艺25) ------------------------------------------------------第60页气压试验(艺26) --------------------------------------------------------第61页A法氨渗漏(艺27) --------------------------------------------------------第63页B法氨渗漏(艺28) -------------------------------------------------------第64页C法氨渗漏(艺29) -------------------------------------------------------第66页酸洗、钝化(艺30)------------------------------------------------------第67页涂敷(艺31)-----------------------------------------------------------第69页包装、运输(艺32)---------------------------------------------------第71页零部件堆焊(艺33) ---------------------------------------------------第74页 预后热及热处理(艺34) -------------------------------------------------第78页分片过渡段、封头加工成型工艺编号:艺011整体椭圆封头、分片椭圆封头执行JB/T4746-2002标准,旋压封头执行JB/T4746-2002标准,过渡段执行JB/T4746-2002标准, 球形封头执行GB12337-1998《钢制球形储罐》标准,同时应符合GB150-1998《钢制压力容器》、HG20584-1998《钢制化工容器制造技术要求》的有关规定。
压力容器产品工艺文件

压力容器产品工艺文件一、产品概述:本压力容器为一款用于储存和输送压缩气体或液体的设备,由设计、制造、安装、调试和使用五个环节组成。
本文将对这五个环节进行详细描述。
二、设计:1. 根据用户需求和相关标准,确定压力容器的工作压力、温度、材料、几何尺寸等设计参数。
2. 利用计算机辅助设计软件进行压力容器的结构设计,采用有限元分析法进行强度校核。
3. 制定设计文件,包括压力容器的技术规范、设计图纸、材料清单等。
三、制造:1. 购买合格的原材料,包括金属板材、焊接材料、密封材料等。
2. 利用数控剪板机对金属板材进行裁剪,确保尺寸准确。
3. 使用焊接工艺对金属板材进行组装,包括对接焊、角焊、立焊等。
4. 对焊接接头进行无损检测,确保焊缝质量符合要求。
5. 完成焊接后,对压力容器进行喷砂处理,消除焊接残渣和氧化皮。
6. 进行压力试验,验证压力容器的耐压性能。
7. 进行泄漏试验,确保压力容器的密封性。
8. 完成涂装、标识等表面处理工作。
四、安装:1. 根据设计文件要求,选择合适的安装场地。
2. 使用合适的起重设备,将压力容器安装到指定位置。
3. 进行管道连接,确保与其他设备的接口密封可靠。
4. 安装仪表、阀门等附件,确保设备的正常运行。
五、调试及使用:1. 进行系统调试,确保压力容器和相关设备的配合运行。
2. 对压力容器进行定期检查和维护,确保设备的安全可靠。
3. 按照使用说明书规范使用压力容器,防止超负荷使用和操作失误。
六、结束语:本工艺文件详细介绍了压力容器的设计、制造、安装、调试和使用过程。
只有严格按照文件要求执行每个环节,才能保证压力容器的安全运行和长久使用。
七、质量控制:在压力容器的制造过程中,质量控制是非常重要的环节。
以下是一些质量控制措施:1. 原材料检验:在购买原材料时,要求供应商提供相关的质量检验证书,并对关键材料进行验收检查。
检查内容包括材料标识、尺寸、化学成分、力学性能等。
2. 焊接质量控制:焊接是制造过程中最关键的步骤之一,焊接质量的好坏直接影响到压力容器的安全性。
压力容器基本检验标准(铆工)
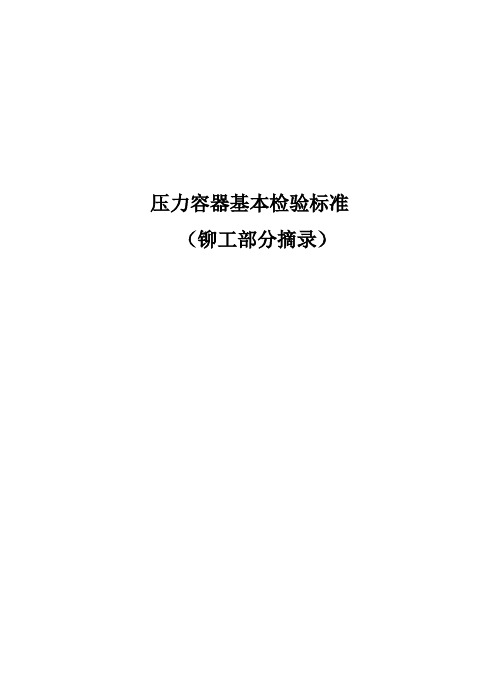
压力容器基本检验标准(铆工部分摘录)XXX公司质量方针:质量第一,科学管理,以质量求效益,以产品的实际使用效果为最终评价,努力生产出用户满意的高质量的压力容器。
设备制作相关技术标准一、《GB150-98钢制压力容器》摘录:10制造、检验与验收10.1.6容器主要受压部分的焊接接头分为A、B、C、D四类。
a)圆筒部分的纵向接头(多层包扎容器层板层纵向接头除外)、球形封头与圆筒连接的环向接头、各类凸形封头中的所有拼焊接头以及嵌入式接管与壳体对接连接的接头,均属A类焊接接头。
b)壳体部分的环向接头,锥形封头小端与接管连接的接头、长颈法兰与接管连接的接头,均属B类焊接接头,但已规定为A、C、D类的焊接接头除外。
c)平盖、管板与圆筒非对接连接的接头,法兰与壳体、接管连接的接头,内封头与圆筒的搭接接头以及多层包扎容器层板层纵向接头,均属C类焊接接头。
d)接管、人孔、凸缘、补强圈等与壳体连接的接头,均属D类焊接接头,但已规定为A、B类的焊接接头除外。
10.1.7凡制造受压元件的材料应有确认标记。
在制造过程中,如原有确认标记被裁掉或材料分成几块,应于切割前完成标记的移植。
确认标记的表达方式由制造单位规定。
对有防腐蚀要求的不锈钢以及复合钢板制容器,不得在防腐蚀面采用硬印作为材料的确认标记。
10.2冷热加工成形10.2.1根据制造工艺确定加工裕量,以确保凸形封头和热卷筒节成形后的厚度不小于该部件的名义厚度减去钢板负偏差。
冷卷筒节投料的钢板厚度δs不得小于其名义厚度减钢板负偏差。
制造中避免钢板表面的机械损伤。
对于尖锐伤痕以及不锈钢容器防腐蚀表面的局部伤痕、刻槽等缺陷应予修磨,修磨范围的斜度至少为1:3。
修磨的深度应大于该部位钢材厚度δs的5%,且不大于2mm,否则予以补焊。
对于复合钢板的成形件,其修磨深度不得大于复层厚度的3%,且不大于1mm,否则应予补焊。
10.2.2坡口表面要求:a)坡口表面不得有裂纹、分层、夹渣等缺陷。
压力容器装配通用工艺规程

压力容器装配通用工艺规程1范围本规程规定了公司压力容器产品装配焊缝布置、装配错边量棱角度不等厚度对接、装配尺寸公差、热处理、无损检测和管箱装配的要求;本规程适用于本公司压力容器产品的装配;非压力容器产品可参照本标准执行;本规程不适用于按ASM规范制造生产的压力容器的装配;2规范性引用文件下列文件中的条款通过本标准的引用而成为本标准的条款;凡是注日期的引用文件, 其随后所有的修改单(不包括勘误的内容)或修订版均不适用于本标准,然而,鼓励根据本标准达成协议的各方研究是否可使用这些文件的最新版本;凡是不注日期的引用文件, 其最新版本适用于本标准;G150 《压力容器》GB151 《管壳式换热器》HG20584 《钢制化工容器制造技术要求》JB4730 《压力容器无损检测》JB/T4750 《制冷装置用压力容器》3总则3.1当本标准与图纸或专用工艺的规定不一致或图纸另有规定时,应以图纸或专用工艺文件规定为准;3.2操作工在操作前应先看图纸和专用工艺文件, 熟悉装配方法、顺序和装配要求;3.3装配时应核对装配零件的P/N号是否与BO一致;受压元件是否有材料标记;上道工序的加工是否合格;是否已经过必要的检验;3.4操作工在本工序完工后应首先自检, 合格后再转下道工序;3.5需经相关检验人员(以下简称检验员)检验的控制点在自检合格后交相关检验员检验;停止点必须经检验员和压力容器体系相关责任人检验确认;3.6不准强力装配;3.7装配时使用的临时拉筋、吊耳等应采用与容器焊接性能相似的材料、焊材及焊接工艺;装配后留下的焊疤应磨平, 打磨后的厚度不应小于设计母材厚度;3.8制造中应避免钢板表面的机械损伤;对尖锐伤痕以及不锈钢容器防腐蚀表面的局部伤痕、刻槽等缺陷应予修磨, 修磨范围的斜度至少为1:3;修磨的深度应不大于该部位钢材厚度的5% S n,且不大于2mm否则应予补焊;对于复合钢板,其修磨深度不得大于复层厚度的3%且不大于1mm 否则应予补焊;钢板的补焊按Q/YWT0204的规定3.9凡被支座、腹板、垫板、补强圈等覆盖的焊缝,均应打磨至母材平齐; 3.10壳体内凡妨碍管束顺利装入或抽出的焊接接头均应打磨至与母材平齐;3.11 容器封闭前(装配封头、管板等)均应对容器内进行清洁检查, 并检查是否有工具或杂物遗留在容器内;3.12容器在生产过程中应对暂时不加工的管口进行封闭, 防止杂物进入容器内;有螺纹的接管在焊接过程中应用闷盖保护, 防止飞溅进入容器或损坏螺纹; 3.13加工过程中如发现标记会被覆盖或加工掉, 则应事先进行标记移植; 4焊缝布置4.1筒节长度一般应不小于300mm相邻筒节间纵缝及筒节纵缝与封头拼缝应错开,焊缝中心错开间距(外圆弧长)应大于名义厚度S n的三倍、且不小于100mm图1);4.2设备内外装配件与壳体相焊接的焊缝,其焊缝边缘应尽量避开筒体焊缝;4.3当装配件与壳体主焊缝交叉时,应在附件上开一槽口,以使连接焊缝跨越主焊缝(图1); 4.4筒体或封头上开孔,以开孔中心为圆心,1.5倍开孔直径为半径的范围内不要布置焊缝 (图1)若不能避开,则在此范围内的A B 类焊缝应全部进行无损检测; 4.5筒体焊缝布置时应尽量不被支座、垫板等覆盖;如被覆盖则按3.9条执行外,还应对被覆盖 部分的焊缝全部进行无损检测;5装配错边量b 、棱角度E 、不等厚对接的要求5.1A 、B 类焊接接头对口错边量b 按表1和图2规定;5.1.1用焊接检验尺检验,当壳体为不等厚钢板时,按薄板计算,且测量时不计入钢板的厚度 差; 5.1.2对于封头压制后接头部分的增厚情况,装配应以外表对齐为准,测量时不计入增厚因素 5.1.3装配时先测量两零件的外周长,计算差值,确定错边量值,以便装配时保证错边量在圆周 方向均匀分布;图2:错边量示意图b表1 A 、 B 类焊接接头的错边量单位:mm对口处钢材厚度S s A 类焊接接头对口错边量b B 类焊接接头对口错边量b< 12 b< 1/4 S s b< 1/4 S s >12~20 b< 3 b< 1/4 S s >20~40 b< 3 b< 5.0 >40~50b< 3b< 1/8 S s > 50b< 1/16,且w 10b< 1/8 S s,且 w 205.2B 类焊接接头在轴向形成的棱角度 EW (0.1 S n+2.0)mm 且不大于5mm 用长度不小于300mm 的直尺或样板测量(图3);图3:棱角度示意图5.3当对接壳体两侧钢板厚度不等时,当薄板厚度大于10mm 两板厚度差超过3mr 时,或当薄板 厚度大于10mm 两板厚度差大于薄板厚度的30%或超过5mr 时,均应按下图4所示的要求单面或 双面削薄厚板边缘,或按同样要求采用堆焊方法将薄板边缘焊成斜面 ;EDdL24 - |r(L1,L2) > 3( S 1—S 2)图4不等厚对接5.4最大最小直径差,壳体上同一截面上最大最小直径差应该不大于该截面内径的1%;如果为换热容器,则壳体上同一截面上最大最小直径差应该不大于该截面内径的0.5 %;当被检断面Eb住J=2ES 2S2”位于开孔中心一倍开孔内径范围内时,则该断面最大内径与最小内径应不大于该断面内径的1%与开孔内径的2%之和;5.5当筒体由几节拼接而成时,拼接后的筒体直线度△ LW L%。
压力容器筒体拼接规定(2篇)
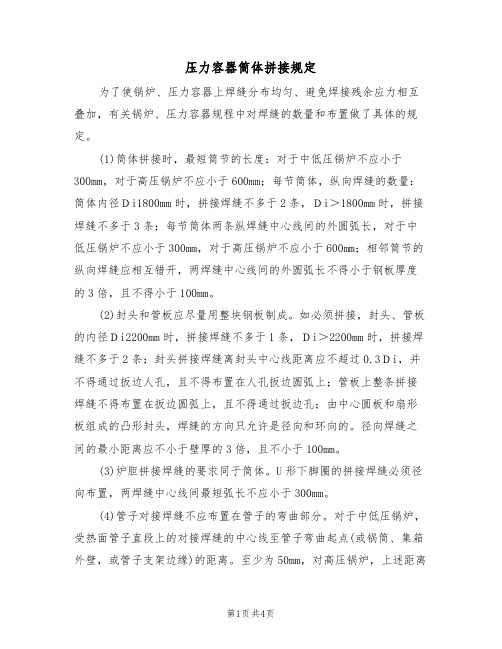
压力容器筒体拼接规定为了使锅炉、压力容器上焊缝分布均匀、避免焊接残余应力相互叠加,有关锅炉、压力容器规程中对焊缝的数量和布置做了具体的规定。
(1)筒体拼接时,最短筒节的长度:对于中低压锅炉不应小于300mm,对于高压锅炉不应小于600mm;每节筒体,纵向焊缝的数量:筒体内径Di1800mm时,拼接焊缝不多于2条,Di>1800mm时,拼接焊缝不多于3条;每节筒体两条纵焊缝中心线间的外圆弧长,对于中低压锅炉不应小于300mm,对于高压锅炉不应小于600mm;相邻筒节的纵向焊缝应相互错开,两焊缝中心线间的外圆弧长不得小于钢板厚度的3倍,且不得小于100mm。
(2)封头和管板应尽量用整块钢板制成。
如必须拼接,封头、管板的内径Di2200mm时,拼接焊缝不多于1条,Di>2200mm时,拼接焊缝不多于2条;封头拼接焊缝离封头中心线距离应不超过0.3Di,并不得通过扳边人孔,且不得布置在人孔扳边圆弧上;管板上整条拼接焊缝不得布置在扳边圆弧上,且不得通过扳边孔;由中心圆板和扇形板组成的凸形封头,焊缝的方向只允许是径向和环向的。
径向焊缝之间的最小距离应不小于壁厚的3倍,且不小于100mm。
(3)炉胆拼接焊缝的要求同于筒体。
U形下脚圈的拼接焊缝必须径向布置,两焊缝中心线间最短弧长不应小于300mm。
(4)管子对接焊缝不应布置在管子的弯曲部分。
对于中低压锅炉,受热面管子直段上的对接焊缝的中心线至管子弯曲起点(或锅筒、集箱外壁,或管子支架边缘)的距离。
至少为50mm,对高压锅炉,上述距离至少为70mm;锅炉范围内管道焊缝中心线至管道弯曲起点之间的距离不应小于管道的外径,且不小于100mm;受热面管子直段上,对接焊缝间的距离不得小于150mm。
(5)受压元件主要焊缝及其邻近区域,应避免焊接零件。
如不能避免时,焊接零件的焊缝可穿过主要焊缝,而不要在焊缝及其邻近区域中止。
(6)开孔、焊缝和转角要错开。
开孔边缘与焊缝的距离应不小于开孔处实际壁厚的3倍,且不小于100mm。
压力容器筒体拼接规定范文(二篇)

压力容器筒体拼接规定范文第一章绪论1.1 研究背景压力容器是指用于储存或运输液体、气体或物质的特殊容器,其内部受到较高的压力。
它广泛应用于石油化工、医药、冶金等行业,承担着重要的工业安全责任。
压力容器的安全性与质量直接关系到工业生产和人员的生命财产安全,因此容器的设计、制造和检验必须遵循一定的标准和规范。
1.2 研究目的本文旨在对压力容器筒体拼接进行规范和标准化,提高容器的安全性和质量,保障工业生产的正常进行。
1.3 研究内容本文将从拼接方法、拼接接头设计、拼接工艺等方面对压力容器筒体拼接进行规定和范文。
第二章拼接方法2.1 拼接方法选择常见的压力容器筒体拼接方法有焊接、铆接和搭接等。
具体选择何种拼接方法应根据容器的材质、尺寸和使用环境等因素综合考虑。
2.2 焊接拼接焊接拼接是最常用的一种方法,可分为手工焊接和自动焊接。
焊接接头的设计应符合相关标准和规范,焊口应做到均匀、充实、无缺陷。
焊接过程中应注意保护气氛和控制焊接温度,从而保证焊缝的质量。
2.3 铆接拼接铆接拼接适用于厚度较薄的容器壁,尤其适用于铝合金容器。
铆接接头的设计应合理,铆钉的选用应符合相关标准和规范。
铆接过程中应注意铆接的力量和位置,保证接头的紧密度和强度。
2.4 搭接拼接搭接拼接是指采用搭接形式将两个或多个薄板连接在一起。
搭接接头应设计合理,接头的搭接量应符合相关标准和规范。
搭接过程中应注意接头的对齐和间隙的控制,保证接头的质量和强度。
第三章拼接接头设计3.1 接头类型选择常见的接头类型有对接接头、角接接头和搭接接头等。
具体选择何种接头类型应根据容器的应力情况、结构形式和使用条件等因素综合考虑。
3.2 接头尺寸设计接头的尺寸设计应根据容器的设计条件和应力计算结果进行确定。
接头的长度、宽度和倾角等参数应符合相关标准和规范要求。
接头的设计应注意考虑焊接变形和残余应力的控制。
3.3 接头强度校核接头的强度校核应根据容器的设计条件和应力状态进行计算和分析。
压力容器筒体拼接规定范文

压力容器筒体拼接规定范文压力容器是工业生产中常见的一种设备,在化工、石化、制药等行业中广泛使用。
为了保证压力容器的安全可靠运行,需要对其筒体的拼接进行规范和标准化。
压力容器筒体拼接具有重要的意义,它涉及到容器的强度和密封性能,需要严格按照相关规定进行操作。
本文将探讨压力容器筒体拼接的规定和范文,以确保压力容器的质量和安全。
以下将详细介绍压力容器筒体拼接的规定和范文。
1. 筒体拼接规定要求压力容器筒体的拼接工艺应严格按照相关规定进行,以确保容器的强度和密封性。
拼接工艺的规定主要包括以下几个方面:1.1 焊接工艺规范焊接是压力容器筒体拼接中常见的一种方法,因此焊接工艺规范是非常重要的。
焊接工艺规范应包括焊缝的准备、焊接参数的选择、焊接方法的选择等方面的要求。
焊缝的准备应包括材料的清洁、焊接面的处理等环节。
焊接参数的选择应根据材料厚度、焊接材料、焊接位置等因素进行合理选择。
焊接方法的选择应根据容器的结构和要求进行综合考虑,包括手工焊、自动焊等方法。
1.2 检查和试验规范拼接完成后,应进行相应的检查和试验,以验证拼接的质量和安全性。
检查和试验规范应包括焊缝的外观检查、焊缝的无损检测、尺寸和形状的检查、压力试验等内容。
外观检查主要用于检查焊缝的表面状况,包括是否有焊缺陷、裂纹等。
无损检测主要用于检测焊缝内部的缺陷,包括超声波检测、射线检测等方法。
尺寸和形状的检查用于检查焊缝的尺寸和形状是否符合要求。
压力试验用于检测容器的密封性和强度。
1.3 质量控制规范质量控制是容器拼接中非常重要的一环,它涉及到整个拼接过程的各个环节。
质量控制规范应包括材料的选择和验收、焊接过程的控制、检查和试验的控制等方面的要求。
材料的选择和验收应根据相应的标准进行,以确保材料的质量和适用性。
焊接过程的控制应包括焊接参数和焊接操作的控制,以确保焊接的质量和稳定性。
检查和试验的控制用于确保检查和试验的准确性和可靠性。
2. 筒体拼接规定范文根据上述的规定要求,以下为压力容器筒体拼接规定的范文:2.1 焊接工艺规范2.1.1 焊缝准备在进行焊接之前,应对焊缝进行准备。
J0701压力容器制造铆工工艺守则汇编

压力容器制造质量管理体系文件QJ/SGZC-Y01-0701-2007 铆工工艺守则汇编受控状态:版号/修改号:A版分发号:编制:唐明金审核:张阳勇批准:康学军2007-07-15发布 2007-07-20实施水电四局水工机械总厂发布前言本工艺守则汇编是依据TSG Z0004-2007《特种设备制造、安装、改造、维修质量保证体系基本要求》、《压力容器安全技术监察规程》和《锅炉压力容器制造许可条件》中有关压力容器制造铆工工艺的要求,并结合本厂ISO9001-2000质量管理体系要求实际情况而编制的。
本工艺守则为本厂规定了与压力容器制造有关的下料通用工艺、筒体制造工艺、喷砂工艺、水压试验工艺、油漆工艺等作出规定,是与本厂压力容器制造有关的铆工工艺汇编性文件,其它的规定或细则等若与本工艺守则汇编有抵触时,应以本工艺守则汇编为准。
本工艺守则汇编由工程管理办提出;本工艺守则汇编由加工中心归口管理并解释;若修改或换版,应由总工程师批准,受控版本应在修改记录中记载。
本工艺守则持有者姓名:受控编号:修改记录目录…………………………………………………4-12 …………………………………………………13-21 …………………………………………………22-24 …………………………………………………25-29 …………………………………………………30-32 ………………………………………………………33-34QJ/SGZC-Y01-0701.1-2007 下料通用工艺守则1总则本工艺守则对压力容器制造下料的准备、下料作业实施、下料工艺参数要求等作出了规定。
适用于压力容器制造过程中的下料作业。
2引用标准JB/T 9168.1-1998《切削加工通用工艺守则总则》JB/T 9168.11-1998《切削加工通用工艺守则下料》JB/T 9168.12-1998《切削加工通用工艺守则划线》国家质量技术监督局压力容器安全技术监察规程锅质检锅[2003]194号锅炉压力容器制造许可条件GB150 钢制压力容器QS/SGZC-Y01-0401-2007《质量管理手册》3 下料前的准备3. 1 施工者认真熟悉施工图纸(含工艺补绘图)和工艺文件要求,看清下料单上的材质、规格、尺寸及数量等,发现问题及时与工艺人员联系,确认无误后方可作业。
压力容器焊接工艺文件(DOC 39页)

压力容器焊接工艺文件(DOC 39页)换热面积(m3)65 √设计使用寿命(年)10 √特殊制造要求酸洗钝化,钝化膜蓝点检查√热处理要求/ √耐压试验要求(MPa)管程:0.55 壳程:1.02 √泄露试验要求(MPa)壳程:0.77 √预防腐蚀要求碳钢部分环氧富锌底漆两遍,环氧面漆两遍√安全附件要求√铭牌位置按图示√包装运输及现场安装按合同√设备设计计算书有√√备注工艺审核日期监检人员签字日期材料审核日期焊接审核日期检验审核日期压力容器施焊焊工明细表产品名称加热箱制造编号R11062 类别Ⅱ类姓名焊工钢印证件编号施焊焊缝代号刘恒辉A145 TS6JSJSW00230F A1-4、B1-3、D8鉴志超H382 TS6JSJW02038F D3-6、C4-5、C7、D9-14、B4-7 郭阿峰H218 TS6JSJSW01811F D1-2、D7-8、C6、C1-3编制日期审核日期C检监员日期压力容器材料明细表第1页共2页产品名称加热箱产品图号容器类别Ⅰ类产品编号序号零件代号零件名称钢号材料规格工件规格下料尺寸件数净数量(Kg)出库数量(Kg)备注1 角铁/ 40X40X4L=95 4 138.12 上板20 δ=15 1974X500 L=1782 5.08 5.363 长侧板Q345RPL125(B)-10RF2 11外购4 下板20ⅡRF700-1.0 1 52.8 外购5 隔板Q345R 见图 1 17.1 详见10图纸6 短侧板Q345R δ=8DN700δ=8L=1112224X1111 15.5 16.97 防护板Q345R δ=8 EHA700X8 φ910 1 36.6 528 加强柱35 M20X140-A 64 18.63外购9 进气口管子8级M20128/外购10 进气口法兰石棉橡胶板700-1.0 1 /外购11 圆螺00Cr17Niφφ108X4 L=99 1 1.02 1.1211母组件14Mo2 108X4 L=9912 出气口法兰00Cr17Ni14Mo2ⅡWN100(B)-25RFS=41 6.5外购13 出气口管子00Cr17Ni14Mo2φ25X2φ25X2L=414L=41422 12.54 12.8414 圆螺母00Cr17Ni14Mo2δ=6 φ695.5X6φ695.55 40 115见图15 抓板00Cr17Ni14Mo2φ12φ12L=2150L=21506 11.5 11.5512编日期审核日期制13石家庄市东明非标设备有限公司共20页第1页焊接工艺指令卡产品名称:加热箱产品编号:R11062图号:SB25-83-1编制:审核:14监检员:15焊接材料汇总表共20页第2页焊接工艺规程母材钢号及规格(mm)焊条电弧焊SMAW 埋弧焊SAW气体保护焊MG/TIG型(牌)号规格(mm)定额(Kg)烘干温度(℃)保温时间(h)型(牌)号规格(mm)定额(Kg)烘干温度(℃)保温时间(h)型(牌)号规格(mm)定额(Kg)纯度(%)00Cr17Ni14Mo2Q235R/A002Φ3.2Φ43.448.171620#δ8、6、3.5~6J50 7Φ3.2Φ41.72.33350 1~2J42 7Φ3.2Φ41.735.31350 1~2A0 42Φ3.2Φ40.04350 1~2压力容器技术特性17部位设计压力MP设计温度℃试验压力MP焊接接头系数容器类别备注壳程0.77 180℃水压1.02气密0.771 Ⅱ类管程0.44 40℃水压0.55 0.8518焊接工艺指令卡20页第4页焊接接头编号焊接工艺卡编号焊接工艺评定编号焊工持证项目无损检测要求A1、A2、B1 DMH-Ⅶ2-1-3-6 2011 HP -12 SMAW -Ⅳ-3G-12-F4RT-100% Ⅱ级合格A3、B2 DMH-Ⅱ-1-3-8 HPSMAW-Ⅱ-1G-6SMAW -Ⅱ-3G-12-F3JRT-20% Ⅲ级合格A4、B3 DMH-Ⅱ-1-3-8 2011 HP -25 SMAW -Ⅱ-3G-12- F3JRT-20% Ⅲ级合格B5、B6、B7、B8 DMH-Ⅶ2-1-5-4 2011 HP -14GTAW -Ⅳ-6G-3/18-02PT-100% Ⅰ级合格C1、C2 DMH-Ⅰ/Ⅱ-2-3-42011 HP -10SMAW -Ⅱ-6FG-9/18-F3J19C3 DMH-Ⅰ/Ⅱ-2-3-42011 HP -05SMAW -Ⅱ-6FG-9/18-F3JD1、D2 DMH-Ⅰ/Ⅱ-2-3-4/82011 HP -102010 HP -08SMAW -Ⅱ-6FG-9/18-F3JD7 DMH-Ⅰ/Ⅱ-2-3-4/82010 HP -132010 HP -08SMAW -Ⅱ-6FG-9/18-F3JD8 DMH-Ⅰ/Ⅱ-2-3-8/302011 HP -102010 HP -08SMAW -Ⅱ-6FG-9/18-F3JMT-100% Ⅰ级合格D11 DMH-Ⅰ/Ⅱ-2-3-8/302010 HP -132010 HP -08SMAW -Ⅱ-6FG-9/18-F3JMT-100% Ⅰ级合格D9、D10 DMH-Ⅶ2-2-3-6/302011 HP -102011 HP -232010 HP -05SMAW -Ⅳ-6FG(K)-9/18-F4PT-100% Ⅰ级合格D3、D4、D5、D6 DMH-Ⅶ2-2-3-4/62011 HP -122010 HP -05SMAW -Ⅱ-6FG-9/18-F3JPT-20% Ⅲ级合格20D17、D18DMH-Ⅶ2-2-5-2.5/302011 HP -15GTAW -Ⅳ-6G-3/18-02D12 DMH-Ⅱ-2-3-10/82011 HP -10SMAW -Ⅱ-6FG-12/18-F3JD13、D14 DMH-Ⅶ2-2-3-6 2011 HP -12SMAW -Ⅳ-6FG(K)-9/18-F4D15、D16 DMH-Ⅰ/Ⅶ2-2-3-3/62011 HP -17SMAW -Ⅳ-6FG(K)-9/18-F4 焊接工艺指令卡2122接头焊接工艺卡共20页第5页焊接层次顺序示意图:母材1 00Cr17Ni14Mo2厚度(mm) 6 焊接工艺卡编号DMH-Ⅶ2-1-3-6母材2 00Cr17Ni14Mo2厚度(mm) 图号SB25-83-1母材3 厚度(mm) 接头名称筒体纵缝、环缝焊接顺序反1、正1、正2 接头型式对接坡口型式V 接头编号A1、A2坡口角度(℃) 60°焊接工艺评定报告编号HP 2011 -12钝边(mm) 1~2 焊缝余高(mm)焊工持证项目SMAW-Ⅳ-3G-12-F4组装间隙(mm) 2~3备注:焊接位置焊接层次焊接方法填充材料焊接电流电弧电压(V)焊接速度(cm/min)气体流量(L/min)线能量KJ/min预热温度(℃)型(牌)号直径(mm)极性电流(A)层间温度(℃) ≤150焊后热处理正1 焊条电弧焊A022 ф3.2 直流反接90~120 20~22 8~9 12~19.8后热正2 焊条电弧焊A022 ф4.0 直流反接160~180 20~22 10~12 16~23.8钨极直径(mm) 反1 焊条电弧焊A022 ф3.2直流反接90~120 20~22 8~9 12~19.823喷嘴直径(mm)气体成份接头焊接工艺卡共20页第6页焊接层次顺序示意图:母材1 Q345R 厚度(mm) 8 焊接工艺卡编号DMH-Ⅱ-1-3-8母材2 Q345R 厚度(mm) 8 图号SB25-83-1母材3 厚度(mm) 接头名称管箱筒体纵缝、与封头环缝焊接顺序正1、正2、正3 接头型式对接坡口型式V 接头编号C1坡口角度(℃) 60°焊接工艺评定报告编号HPSMAW-II-1G-6钝边(mm) 1~2 焊缝余高(mm)焊工持证项目SMAW-II-3 G-12-F3J组装间隙(mm) 2~3备注:焊接位置焊接层次焊接方法填充材料焊接电流电弧电压(V)焊接速度(cm/min)气体流量(L/min)线能量KJ/min预热温度(℃) 型(牌)号直径极性电流(A)24层间温度(℃) ≤150(mm)焊后热处理消除应力正1 焊条焊电弧焊J507 ф3.2 直反90~120 20~22 8~9 12~19.8 后热正2 焊条焊电弧焊J507 ф4.0 直反160~180 20~22 10~12 16~23.8钨极直径(mm)反1 焊条焊电弧焊J507 ф3.2 直反90~120 20~22 8~9 12~19.8 喷嘴直径(mm)气体成份接头焊接工艺卡共20页第7页焊接层次顺序示意图:母材1 Q345R 厚度(mm) 8 焊接工艺卡编号DMH-Ⅱ-1-3-8母材2 Q345R 厚度(mm) 8 图号SB25-83-1母材3 厚度(mm) 接头名称管箱筒体纵缝、与封头环缝焊接顺序正1、正2、正3 接头型式对接坡口型式V 接头编号C2坡口角度(℃) 60°焊接工艺评定报告编号2011HP-2525钝边(mm) 1~2 焊缝余高(mm)焊工持证项目SMAW-II-3 G-12-F3J组装间隙(mm) 2~3备注:焊接位置焊接层次焊接方法填充材料焊接电流电弧电压(V)焊接速度(cm/min)气体流量(L/min)线能量KJ/min预热温度(℃)型(牌)号直径(mm)极性电流(A)层间温度(℃) ≤150焊后热处理正1 焊条焊电弧焊J507 ф3.2 直反90~120 20~22 8~9 12~19.8 后热正2 焊条焊电弧焊J507 ф4.0 直反160~180 20~22 10~12 16~23.8钨极直径(mm)反1 焊条焊电弧焊J507 ф3.2 直反90~120 20~22 8~9 12~19.8 喷嘴直径(mm)气体成份接头焊接工艺卡共20页第8页26焊接层次顺序示意图:母材1 00Cr17Ni14Mo2厚度(mm)焊接工艺卡编号DMH-Ⅶ2-1-5-4母材2 00Cr17Ni14Mo2Ⅱ厚度(mm) 3.5~4.5 图号SB25-83-1母材3 厚度(mm) 接头名称接管与法兰焊接顺序正1、正2 接头型式对接接头坡口型式V 接头编号C3、C4坡口角度(℃) 60 焊接工艺评定报告编号2011 HP -14钝边(mm) 0~2 焊缝余高(mm)焊工持证项目GTAW-IV-6G-3/18-02组装间隙(mm) 2~2.5 备注:焊接位置焊接层次焊接方法填充材料焊接电流电弧电压(V)焊接速度(cm/min)气体流量(L/min)线能量KJ/min预热温度(℃)型(牌)号直径(mm)极性电流(A)层间温度(℃) ≤150焊后热处理正1 钨极氩弧焊ER316Lф2.5 直正80~10012~13 10~13 6~7 4.4~7.8后热正2 钨极氩ER31ф2.5 直正80~10012~13 10~13 6~7 4.4~7.827弧焊6L钨极直径(mm)Φ2.5喷嘴直径(mm)Φ8.0气体成份氩气接头焊接工艺卡共20页第9页焊接层次顺序示意图:母材1 Q345R 厚度(mm) 焊接工艺卡编号DMH-Ⅰ/Ⅱ-2-3-4母材2 20# 厚度(mm) 3.54.5图号SB25-83-1母材3 厚度(mm) 接头名称接管与法兰焊接顺序正1、反1、正2 接头型式角接坡口型式接头编号C5~C12坡口角度(℃) 50°焊接工艺评定报告编号2011 HP -10钝边(mm) 焊缝余高(mm) 4 焊工持证项目SMAW-Ⅱ28-6FG-9/18-F3J组装间隙(mm) 0.5~1备注:焊接位置焊接层次焊接方法填充材料焊接电流电弧电压(V)焊接速度(cm/min)气体流量(L/min)线能量KJ/min预热温度(℃)型(牌)号直径(mm)极性电流(A)层间温度(℃) ≤50焊后热处理消除应力正1 焊条电弧焊J427 ф3.2 直流反接90~120 20~22 8~9 12~19.8后热正2 焊条电弧焊J427 ф3.2 直流反接90~120 20~22 8~9 12~19.8钨极直径(mm) 反1 焊条电弧焊J427 ф3.2直流反接90~120 20~228~9 12~19.8喷嘴直径(mm) 反2 焊条电弧焊J427 ф3.2直流反接90~120 20~228~9 12~19.8气体成份接头焊接工艺卡共20页第10页焊接层次顺序示意图:母材1 Q345R 厚度(mm) 焊接工艺卡编号DMH-Ⅰ/Ⅱ-2-3-4母材2 20# 厚度(mm) 3.54.5图号SB25-83-129母材3 厚度(mm) 接头名称接管与法兰焊接顺序正1、反1、正2 接头型式角接坡口型式接头编号D7、D8坡口角度(℃) 50°焊接工艺评定报告编号2010 HP -05钝边(mm) 焊缝余高(mm) 4 焊工持证项目SMAW-Ⅱ-6FG-9/18-F3J组装间隙(mm) 0.5~1备注:焊接位置焊接层次焊接方法填充材料焊接电流电弧电压(V)焊接速度(cm/min)气体流量(L/min)线能量KJ/min预热温度(℃)型(牌)号直径(mm)极性电流(A)层间温度(℃) ≤50焊后热处理正1 焊条电弧焊J427 ф3.2 直流反接90~120 20~22 8~9 12~19.8后热正2 焊条电弧焊J427 ф3.2 直流反接90~120 20~22 8~9 12~19.8钨极直径(mm) 反1 焊条电弧焊J427 ф3.2直流反接90~120 0~22 8~9 12~19.8喷嘴直径(mm) 反2 焊条电弧焊J427 ф3.2直流反接90~120 0~22 8~9 12~19.8气体成份30接头焊接工艺卡共20页第11页焊接层次顺序示意图:母材1 Q345R 厚度(mm) 8 焊接工艺卡编号DMH-Ⅰ/Ⅱ-2-3-4/8母材2 20# 厚度(mm) 3.54.5图号SB25-83-1母材3 厚度(mm) 接头名称接管与封头焊接顺序正1、正2、正3、反1 接头型式角接坡口型式V 接头编号D6坡口角度(℃) 50±5°焊接工艺评定报告编号2011 HP -102010HP-08钝边(mm) 0.5~1.5 焊缝余高(mm)焊工持证项目SMAW-Ⅱ-6FG-9/18-F3J组装间隙(mm) 2~2.5备注:焊接位置焊接层次焊接方法填充材料焊接电流电弧电压(V)焊接速度(cm/min)气体流量(L/min)线能量KJ/min预热温度(℃)型(牌)号直径(mm)极性电流(A)层间温度(℃) ≤50焊后热处理消除应力正1 焊条电弧焊J427 ф3.2 直流反接90~120 20~22 8~9 12~19.831后热正2、3焊条电弧焊J427 ф4.0直流反接160~180 20~22 10~12 16~23.8钨极直径(mm) 反1 焊条电弧焊J427 ф4.0直流反接160~180 20~22 10~12 16~23.8喷嘴直径(mm)气体成份接头焊接工艺卡共20页第12页焊接层次顺序示意图:母材1 Q345R 厚度(mm) 8 焊接工艺卡编号DMH-Ⅰ/Ⅱ-2-3-4/8母材2 20# 厚度(mm) 3.54.5图号SB25-83-1母材3 厚度(mm) 接头名称接管与封头焊接顺序正1、正2、反1 接头型式角接坡口型式V 接头编号D9坡口角度(℃) 50±5°焊接工艺评定报告编号2010HP-132010HP-08钝边(mm) 0.5~1.5 焊缝余高(mm)焊工持证项目SMAW-Ⅱ32-6FG-9/18-F3J组装间隙(mm) 2~2.5备注:焊接位置焊接层次焊接方法填充材料焊接电流电弧电压(V)焊接速度(cm/min)气体流量(L/min)线能量KJ/min预热温度(℃)型(牌)号直径(mm)极性电流(A)层间温度(℃) ≤50焊后热处理正1 焊条电弧焊J427 ф3.2 直流反接90~120 20~22 8~9 12~19.8后热正2、3焊条电弧焊J427 ф4.0直流反接160~180 20~22 10~12 16~23.8钨极直径(mm) 反1 焊条电弧焊J427 ф4.0直流反接160~180 20~22 10~12 16~23.8喷嘴直径(mm)气体成份接头焊接工艺卡共20页第13页焊接层次顺序示意图:母材1Q345R 厚度(mm) 8 焊接工艺卡编号DMH-Ⅰ/Ⅱ-2-3-8/30母材220#厚度(mm) 图号SB25-83-1母材3厚度(mm) 接头名称设备法兰与筒体33焊接顺序正1、正2、正3、反1、接头型式角接坡口型式V 接头编号D3~D4坡口角度(℃) 50±5°焊接工艺评定报告编号2011HP-102010HP-08钝边(mm) 0.5~1.5 焊缝余高(mm)焊工持证项目SMAW-Ⅱ-6FG-12/18-F3J组装间隙(mm) 2~2.5备注:焊接位置焊接层次焊接方法填充材料焊接电流电弧电压(V)焊接速度(cm/min)气体流量(L/min)线能量KJ/min预热温度(℃)型(牌)号直径(mm)极性电流(A)层间温度(℃) ≤50焊后热处理消除应力正1 焊条电弧焊J427 ф3.2 直流反接90~120 20~22 8~9 12~19.8后热正2 焊条电弧焊J427ф4.0 直流反接160~180 20~22 10~12 16~23.8钨极直径(mm) 正3 焊条电弧焊J427ф4.0直流反接160~180 20~22 10~12 16~23.8喷嘴直径(mm) 正4 焊条电弧焊J427ф4.0直流反接160~180 20~22 10~12 16~23.8气体成份34接头焊接工艺卡共20页第14页焊接层次顺序示意图:母材1 Q345R 厚度(mm) 8 焊接工艺卡编号DMH-Ⅰ/Ⅱ-2-3-8/30母材2 20#厚度(mm) 图号SB25-83-1 母材3 厚度(mm) 接头名称设备法兰与筒体焊接顺序正1、正2、正3、反1、接头型式角接坡口型式V 接头编号D10~17坡口角度(℃) 50±5°焊接工艺评定报告编号2010HP-132010HP-08钝边(mm) 0.5~1.5 焊缝余高(mm)焊工持证项目SMAW-Ⅱ-6FG-12/18-F3J组装间隙(mm) 2~2.5备注:焊接位置焊接层次焊接方法填充材料焊接电流电弧电压(V)焊接速度(cm/min)气体流量(L/min)线能量KJ/min预热温度(℃)型(牌)号直径(mm)极性电流(A)层间温度(℃) ≤5035焊后热处理正1 焊条电弧焊J427 ф3.2 直流反接90~120 20~22 8~9 12~19.8后热正2 焊条电弧焊J427ф4.0 直流反接160~180 20~22 10~12 16~23.8钨极直径(mm) 正3 焊条电弧焊J427ф4.0直流反接160~180 20~22 10~12 16~23.8喷嘴直径(mm) 正4 焊条电弧焊J427ф4.0直流反接160~180 20~22 10~12 16~23.8气体成份接头焊接工艺卡共20页第15页焊接层次顺序示意图:母材1 00Cr17Ni14Mo2厚度(mm) 8焊接工艺卡编号DMH-Ⅶ2-2-3-.6/30母材2 00Cr17Ni14Mo2Ⅱ厚度(mm) 图号SB25-83-1母材3 厚度(mm) 接头名称筒体与管板焊接顺序正1、正2、正3、反1、接头型式角接坡口型式V 接头编号D1、D2坡口角度(℃) 50±5°焊接工艺评定报告编号HP 2011-122011HP-23362010HP-05钝边(mm) 0.5~1.5 焊缝余高(mm)焊工持证项目SMAW-IV-6FG(K)-9/18-F4组装间隙(mm) 2~2.5备注:焊接位置焊接层次焊接方法填充材料焊接电流电弧电压(V)焊接速度(cm/min)气体流量(L/min)线能量KJ/min预热温度(℃)型(牌)号直径(mm)极性电流(A)层间温度(℃) ≤50焊后热处理正1 焊条电弧焊A022 ф3.2 直流反接90~120 20~22 8~9 12~19.8后热正2 焊条电弧焊A022 ф4.0 直流反接160~180 20~22 10~12 16~23.8钨极直径(mm) 正3 焊条电弧焊A022 ф4.0直流反接160~180 20~22 10~12 16~23.8喷嘴直径(mm) 正4 焊条电弧焊A022 ф4.0直流反接160~180 20~22 10~12 16~23.8气体成份接头焊接工艺卡共20页第16页焊接层次顺序示意图:母材1 00Cr17Ni14Mo2厚度(mm) 8 焊接工艺卡编号DMH-Ⅶ2-2-3-4/637母材2 00Cr17Ni14Mo2Ⅱ厚度(mm)3.54图号SB25-83-1母材3 厚度(mm) 接头名称接管与筒体焊接顺序正1、正2、正3、反1 接头型式角接坡口型式V 接头编号D3、D4、D5、D6坡口角度(℃) 50±5°焊接工艺评定报告编号2011 HP-122010HP-05钝边(mm) 0.5~1.5 焊缝余高(mm)焊工持证项目SMAW-Ⅱ-6FG-9/18-F3J组装间隙(mm) 2~2.5备注:焊接位置焊接层次焊接方法填充材料焊接电流电弧电压(V)焊接速度(cm/min)气体流量(L/min)线能量KJ/min预热温度(℃)型(牌)号直径(mm)极性电流(A)层间温度(℃) ≤50焊后热处理正1 焊条电弧焊A022 ф3.2 直流反接90~120 20~22 8~9 12~19.8后热正2、3焊条电弧焊A022 ф4.0直流反接160~180 20~22 10~12 16~23.8钨极直径(mm) 反1 焊条电弧焊A022 ф4.0直流反接160~180 20~22 10~12 16~23.8喷嘴直径(mm)38气体成份接头焊接工艺卡共20页第17页焊接层次顺序示意图:母材1 00Cr17Ni14Mo2厚度(mm) 焊接工艺卡编号DMH-Ⅶ2-2-5-2.5/30母材2 00Cr17Ni14Mo2Ⅱ厚度(mm) 2.5 图号SB25-83-1母材3 厚度(mm) 接头名称换热管与管板焊接顺序正1、正2 接头型式角接坡口型式接头编号D17~18坡口角度(℃) 焊接工艺评定报告编号2011 HP -15钝边(mm) 焊缝余高(mm) 4GTAW-Ⅳ-6FG-3/18-02组装间隙(mm) 备注:焊接位置平位焊接层次焊接方法填充材料焊接电流电弧电压(V)焊接速度(cm/min)气体流量(L/min)线能量KJ/min预热温度(℃)型(牌)号直径(mm)极性电流(A)层间温度(℃) ≤50焊后热处理正1 钨极氩弧焊ER316L ф2.5 直流80~10012~13 10~13 6~7 4.4~7.8正接后热正2 钨极氩弧焊ER316L ф2.5 直流正接80~10012~13 10~13 6~7 4.4~7.8钨极直径(mm)Φ2.5喷嘴直径(mm)Φ8.0气体成份接头焊接工艺卡共20页第18页-焊接层次顺序示意图:母材1 Q345R 厚度(mm) 焊接工艺卡编号DMH-Ⅱ-2-3-10/8母材2 Q345R 厚度(mm) 图号SB25-83-1母材3 厚度(mm) 接头名称隔板与封头焊接顺序1、2、3 接头型式角接坡口型式接头编号D12坡口角度(℃) 焊接工艺评定报告编号2011HP-10钝边(mm) 焊缝余高(mm)焊工持证项目SMAW-Ⅱ40-6FG-12/18-F3J组装间隙(mm) 0~1备注:焊接位置焊接层次焊接方法填充材料焊接电流电弧电压(V)焊接速度(cm/min)气体流量(L/min)线能量KJ/min预热温度(℃)型(牌)号直径(mm)极性电流(A)层间温度(℃) ≤50焊后热处理消除应力 1 焊条电弧焊J507 ф3.2 直流反接90~12020~228~9 14.5~20.8后热 2 焊条电弧焊J507 ф4.0 直流反接160~18020~2210~12 16~23.8钨极直径(mm)喷嘴直径(mm)气体成份接头焊接工艺卡共20页第19页焊接层次顺序示意图:母材1 00Cr17Ni14Mo2厚度(mm) 焊接工艺卡编号DMH-Ⅶ2-2-3-641母材2 00Cr17Ni14Mo2Ⅱ厚度(mm) 图号SB25-83-1母材3 厚度(mm) 接头名称底座板与筒体焊接顺序1、2、3 接头型式角接坡口型式接头编号D13、D14坡口角度(℃) 焊接工艺评定报告编号2011 HP -12钝边(mm) 焊缝余高(mm)焊工持证项目SMAW-IV-6FG(K)-9/18-F4组装间隙(mm) 0~1备注:焊接位置焊接层次焊接方法填充材料焊接电流电弧电压(V)焊接速度(cm/min)气体流量(L/min)线能量KJ/min预热温度(℃)型(牌)号直径(mm)极性电流(A)层间温度(℃) ≤50焊后热处理 1 焊条电弧焊A022 ф3.2 直流反接90~12020~228~9 14.5~20.8后热 2 焊条电弧焊A022 ф4.0 直流反接160~18020~2210~12 16~23.8钨极直径(mm)喷嘴直径(mm)气体成份42接头焊接工艺卡共20页第20页焊接层次顺序示意图:母材1 00Cr17Ni14Mo2厚度(mm) 14 焊接工艺卡编号DMH-Ⅰ/Ⅶ2-2-3-3/6母材2 Q235B 厚度(mm) 3 图号SB25-83-1 母材3 厚度(mm) 接头名称铭牌座与筒体焊接顺序接头型式角接坡口型式接头编号D15、D16坡口角度(℃) 焊接工艺评定报告编号2011 HP -17钝边(mm) 0~1 焊缝余高(mm)焊工持证项目SMAW-Ⅳ-3G-12-F4组装间隙(mm) 0~1 备注:焊接位置焊接层次焊接方法填充材料焊接电流电弧电压(V)焊接速度(cm/min)气体流量(L/min)线能量KJ/min预热温度(℃)型(牌)号直径(mm)极性电流(A)层间温度(℃)焊后热处理焊条电弧焊A042 ф3.2 直流反接70~10020~22 8~9 9.3~16.543后热钨极直径(mm)喷嘴直径(mm)气体成份44产品名称 图 制造编号 产品制造综合卡 使用单位 容器类别 共 2加热箱 SB25-R11062 Ⅱ类 图号或 标准号 件号 名称 件数 材料 定额 工艺线路牌号 名规格单总剪切砂刨机钳锻铆复理外外备SB25-83 1 管 1 / 1313 √ GB/T811-接 2 20 钢φ133X4.5 2.5 5. √ HG/T201-法 2 Q345R 钢PL125(B)- 5.511 √ JB/T4701-法 1 20Ⅱ 锻RF700-1.0 52.52 √ SB25-831-隔 1 Q345R 钢见图 17.17 √ √1-筒 1 Q345R 钢DN700δ15.15 √ √ JB/T4741-封 1 Q345R 钢EHA700X8 36.36 √ √ JB/T470 2 螺635 M20X140-A 0.218 √ GB/T61 3 螺18级 M20 / √ SB25-83 4 垫 1 石棉橡胶 700-1.0 / √5 接 1 00Cr17Ni 钢φ108X4 1.0 1. √ HG/T2056 法 1 00Cr17Ni 锻WN100(B)- 6.5 6. √7 定200Cr17Ni 钢φ25X2 0.512 √ SB25-838 折 5 00Cr17Ni 钢φ695.5X6 8.0 40 √ √ SB25-839 拉 6 00Cr17Ni 圆φ12 1.911. √ √10 筒 1 00Cr17Ni 钢DN700δ2525 √ √ 11 换300Cr17Ni 钢φ25X2 2.897 √ 12 接 2 00Cr17Ni 钢φ45X3.5 0.40. √ HG/T2013 法 2 00Cr17Ni 锻WN40(B)-2 2.0 4. √ JB/T47014 垫 1 石棉橡胶 700-1.0 / √ SB25-8315 管 1 00Cr17Ni 钢φ830X30 78 78 √ JB/T47016 法 1 20Ⅱ 锻RF700-1.0 3.2 3. √17 筒 1 Q345R 钢DN700δ29.29 √ √ JB/T47418 封 1 Q345R 钢EHA736.36 √ √GB/T8119 接 1 20 钢φ0.50. √HG/T2020 法 1 Q345R 钢PL40(B)-1 2.0 2. √ 编制 日期 审核 日期产品名称 图 制造编号 产品制造综合卡 使用单位 容器类共 2加热箱 SB25-R11062 Ⅱ类 图号或 标准号 件号 名称 件数材料 定额 工艺线路牌号 名规格单总剪切砂刨机钳锻铆复理外外备 21 接 1 00Cr17Ni 钢φ89X4 0.80. √ HG/T2022 法 1 00Cr17Ni 锻WN80(B)-2 3.0 3. √23 接 1 0Cr18Ni9 钢70X50X6 0.10. √ JB/T47124 支 1 Q235B/00C B Ⅰ700-S 30 30 √24地 1 Q235B 钢640X150X17.57. √ 24腹 1 Q235B 钢590X375X8 13.13 √ 24筋 2 Q235B 钢120X240X8 1.8 3. √ 24垫 1 00Cr17Ni 钢830X240X6 9.39. √ 25 定8 00Cr17Ni 钢φ25X2 1.19. √ SB25-8326 拉 2 00Cr17Ni φ12 1.5 3. √ √ GB/T41-27 螺15级 M12 / √ JB/T47128 支 1 Q235B/00C B Ⅰ700-F 30 30 √28地 1 Q235B 钢640X150X17.57. √ 28腹 1 Q235B 钢590X375X8 13.13 √ 28筋 2 Q235B 钢120X240X8 1.8 3. √ 28垫 1 00Cr17Ni 钢830X240X6 9.39. √ SB25-8329 管 1 00Cr17Ni φ830X30 78 78 √编制日期审核日期47产品名称图号制造编号封头制造卡件号零件编号第 2 页加热箱SB25-83-1R11062R11062F1共 2 页控制标序号工序工艺内容及技术要求设备工装操作者专检责任师日期监检员日期数检查员1 领料⑴核对材料表面状况,不允许目测超声夹渣、分层等缺陷。
容器铆工工艺守则(参考下)
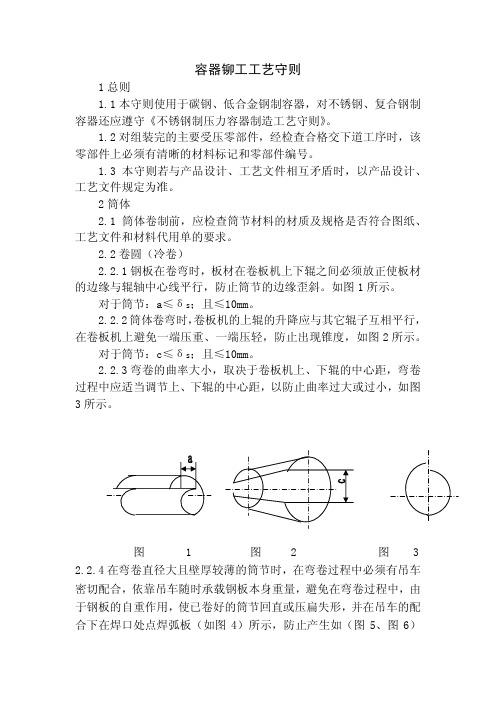
а——弯曲角度°Leabharlann R——弯曲半径mm
3.5.2 根据不同的炜曲方法留装夹量。通常按 4 倍管直径留装夹
筒节直 径
Dimm
类别 无内件容器
塔和有内件容 器
换热器 DN
表2
≤500
500~2000
2000~3000
>3000
≤1%Di 且不大于 25mm
≤0.5%Di
≤0.4%Di
≤0.3%Di
DN≤1200 时,≤0.5%Di 且不大于 5mm DN>1200 时,不大于 7mm
注:对于承受外压及真空容器按现行 GB150-1998 中的有关要求控制壳体的圆
A±ΔA
图
1
3.1.2 划线公差 (1)筒节宽度的划线偏差为±1 毫米; (2)两对角线之差ΔL 见表 2: (3)筒节周长允差ΔA 见表 2;
表2
mm
筒体内径
<800
800~1200
1300~2400
ΔA
±1.5
±2
±3
单位:
>2400 ±3.5
ΔL
1
1.5
2
3
(4)同一筒体相邻筒节间的周长允许偏差见表 3。
一般不留加工余量,当分段时在一边留余量 1.55 毫米,如图 3。
3.4 角钢和槽钢成形如(图 4)、(图 5)。
3.4.1 角钢和槽钢弯曲的展料长计算公式:
热炜 L=π(D±1.5 不)+2W
冷炜 L=π(D±2Z0)+2W
内曲取“-”外曲取“+”
L——展料长度 mm
D——公称外径 mm
Z0——型钢重心距离 mm
W——余量 W=2b 且≮120 毫米 mm
压力容器制造铆工工艺规程

压力容器制造铆工工艺规程Q/XXXXX04.09-2012容器剪切、滚筒、煨曲、冷作工艺规程受控状态:版本号: A发放编号:编制:审核:批准:2012-07-01发布 2012-08-01实施Q/XXXX04.09-2012 版本号:A-0 XXXXX实业有限责任公司XXXX 容器剪切、滚筒、煨曲、冷作工艺规程共3页第1页 1 范围本标准适用于碳素钢、低合金钢、奥氏体不锈钢制焊接压力容器的剪切、滚筒、煨曲、冷作工艺程序。
本标准是产品工艺的通用性文件,当与产品的设计图样及工艺要求有矛盾时,以产品图样为准。
2 引用标准下列文件对于本文件的应用是必不可少的。
凡是注日期的引用文件,仅注日期的版本适用于本文件。
凡是不注日期的引用文件,其最新版本(包括所有的修改单)适用于本文件。
GBl50.1-150.4-2011 压力容器GBl51 管壳式换热器Q,XXXX04.01 容器放样下料工艺规程3内容与方法3(1基本要求3(1(1操作前按Q,XXXX04.01《容器放样下料工艺规程》识别各种号料符号及意义。
对于识别不清的要与号料人员及时联系确认。
3(1(2依据生产计划表明确生产数量。
切料前必须认真检查所切料有无标记移植钢印,无标记移植钢印的材料不得加工。
3(2剪切3(2(1检查剪床设备的完好情况及保养情况,并排除一切杂物。
3(2(2调整好压料装置。
3(2(3根据所切割的板厚、规格,调整好切片的角度和间隙,切片角度一般为3,5度,切薄板时角度应调整小些。
3(2(4上下切片之间的间隙一般为0.6,1.2mm切薄板为0.1,0.5mm。
3(2(5切料3(2(5(1 被切工作表面应清除一切脏物,在切口处两边50mm应彻底清除干净,不得有泥沙等杂物。
3(2(5(2必须严格按剪床的剪刀能力切料,不得切超厚或过硬的材料。
3(2(5(3对切下的第一个工件尺寸必须检查合格后方可继续切料。
3(2(5(4操作时不得用手去取卡在刀刃上的物件或触摸刃口。
压力容器铆金工艺文件

形式
检验
结果
操作者
名称
日期
检验员
签名
日期
设备
型号
工时
工序
准结
操作
一、
机加工
1、材料确认
H
2、领料核对标记。切割下料
H
二、
车
1、管板按图样车外圆,密封面及总厚
W
度。
三、
钳
按图样划264-φ25。25+0。1管孔线,
W
4-M16螺孔线。
四、
钻孔
按图样钻264-φ25。25+0。1管孔,
W
4-M16螺孔。
设计材料
Q345R
入库号
工作令号
2012-21
焊缝
编号
1 A
毛坯
种类
钢板:δ8
L=565
W=2224
工序简图
发放材料
材料代用单号
产品编号
2012-21-0
工序
工序
名称
工序内容
控制
形式
检验
结果
操作者
名称
日期
检验员
签名
日期
设备
型号
工时
工序
准结
操作
一、
铆焊
1、材料确认
H
2、套料划线,对角线允差≤2mm
H
3、标记移植
W
4、切割、按产品“焊卡”坡口形式铣
W
坡口
W
5、压头、卷制、对口、点固
W
6、装点引弧板/(产品试板)/熄弧板
A类焊缝的对口错边量
7、按“焊卡”施焊1A
W
对口处的名义厚度
错边量E
8、割去引弧板/(产品试板)/熄弧板
铆接操作指导工艺文件

目录1适用范围: (1)2操作工艺指导 (1)2.1 拉铆螺母 (1)2.1.1拉铆螺母分类 (1)2.1.1.1 拉铆螺母的螺纹的公称直径; (1)2.1.1.2 拉铆螺母的头型见下表 (1)2.1.1.3 拉铆螺母孔型 (1)2.1.2拉铆螺母作业指导 (1)2.1.2.1 材料准备 (1)2.1.2.2 基材材料板厚和底孔尺寸确认 (1)2.1.2.3 调节铆枪 (2)2.1.2.4 进行铆接 (2)2.1.3检验 (3)2.1.3.1 检测拉铆螺母拉铆后收缩长度(按表2) (3)2.1.3.2 检测拉铆螺母的扭矩(按表3) (3)2.2 压铆螺母 (3)2.2.1压铆螺母材料说明 (3)2.2.2压铆螺母型号说明 (4)2.2.3压铆螺母操作规范 (5)2.2.3.1 确认铆螺母规格 (5)2.2.3.2 底孔尺寸确认 (5)2.2.3.3 调节设备 (5)2.2.3.4 安装压铆螺母 (5)2.2.4检验 (5)2.2.4.1 外观检验 (5)2.2.4.2 扭力检测 (5)2.3 抽芯拉铆钉 (7)2.3.1抽芯拉铆钉分类 (7)2.3.2抽芯拉铆钉规格尺寸 (7)2.3.3铆钉安装步骤 (8)2.3.3.1 安装前准备工作 (8)2.3.3.2 铆钉安装 (8)2.3.3.3 拉铆完成后检测 (8)2.3.4检验 (9)2.3.4.1 外观检测 (9)2.3.4.2 剪切力检测 (9)铆接工艺规范1适用范围:本操作指导适用于产品的铆螺母、压铆螺母、拉铆钉的铆接工序。
2操作工艺指导2.1拉铆螺母又称铆螺母,拉帽,瞬间拉帽,用于各类金属板材、管材等制造工业的紧固领域。
为解决金属薄板、薄管焊接螺母易熔,攻内螺纹易滑牙等缺点而开发,它不需要攻内螺纹,不需要焊接螺母、铆接牢固效率高、使用方便。
2.1.1拉铆螺母分类2.1.1.1拉铆螺母的螺纹的公称直径;如:M3~M122.1.1.2拉铆螺母的头型见下表拉铆螺母头型平头型(f)圆柱头型(C)沉头型(F)2.1.1.3拉铆螺母孔型盲孔通孔2.1.2拉铆螺母作业指导2.1.2.1材料准备在施工前,首先根据图纸要求,对拉铆螺母型号规格进行确认,保证使用正确的拉铆螺母,防止用错规格型号。
铆接工艺标准新版

铆接工艺标准[新版]版本号 A 编号:QCRC-TI-016修改次第 00 QCRC 铆接工艺规范页次/总页数 1/5受控状态:________受控____发放编号:________________生效日期:___2002-09-19__版本号 A 编号:QCRC-TI-016修改次第 00 铆接工艺规范QCRC 页次/总页数 2/5 版本/修改次第更改页次/章节编制审核批准生效日期版本号 A 编号:QCRC-TI-016修改次第 00 铆接工艺规范QCRC 页次/总页数 3/5本规程规定了QCRC铆接工艺要求及质量标准~适用于冷藏箱生产中所有需铆接的零部件及操作人员。
一. 铆钉种类QCRC工厂内所选用的铆钉有半圆头铆钉、扁圆头铆钉、抽芯铆钉、环槽铆钉(哈克钉)等。
二.抽芯铆钉铆接工艺要求1、铆接材料及设备的选用以AVDEL铆钉为例把重要的铆接工艺参数列举如下:铆钉型号铆接厚度钻头大小气压(bar)(mm) (mm)BE61-0509 1.0~3.0 4.1~4.3 80~120BE61-0512 3.0~5.0 4.1~4.3 80~120BE61-0614 3.5~6.0 4.9~5.1 80~120BE61-0618 6.0~8.5 4.9~5.1 80~1202711-0817 4.8~11.1 7.0~7.1 80~1202711-0617 4.8~11.1 4.9~5.1 80~1202774-0613 1.6~6.3 4.9~5.1 80~1202774-0817 4.8~11.1 7 80~1201663-0521 6.4~12.7 4.1~4.2 80~1201663-0613 1.6~6.3 4.9~5.1 80~1201663-0619 4.8~11.1 4.9~5.1 80~1201663-0621 6.4~12.7 4.9~5.1 80~1201663-0631 12.7~19.8 4.9~5.1 80~120 2. 工具的使用每天使用铆枪前检查枪嘴有无碎片,滴几滴润滑油到空气进口里;检查是否有漏气,检查气动枪的气压是否符合说明的最低标准。
- 1、下载文档前请自行甄别文档内容的完整性,平台不提供额外的编辑、内容补充、找答案等附加服务。
- 2、"仅部分预览"的文档,不可在线预览部分如存在完整性等问题,可反馈申请退款(可完整预览的文档不适用该条件!)。
- 3、如文档侵犯您的权益,请联系客服反馈,我们会尽快为您处理(人工客服工作时间:9:00-18:30)。
页
工艺过程、质量控制流转卡
设计材料
发放材料
工序 一、
工序 名称 铆
20
入库号
材料代 用单号
工序内容
1、材料确认 2、领料、核对标记。断料。
产品名称
汽水换热器
工作令号
产品编号
控制 形式
H H
检验 结果
件号
图号
件7 2012-21
焊缝
2012-21-0 操作者
日期 名称
编号 检验员 签名
零件名称 接管φ273*6
期 型号 准结 操作
零件净重
卡片编号
GB9019-88 艺 KⅠ 5
工序简图
A 类焊缝的对口错边量
对口处的名义厚度
错边量 E
≤12mm
≤1/4 S mm
12<S≤50mm
≤3 mm
>50
≤1/16S 且≯10mm
对接 A 类焊缝形成的棱角度 E≤ (S/10+2)且≯5mm;筒体的拼板不 小于 300;筒体高度(长度)应≥300; 相邻的 A 类焊缝的距离不小于筒体厚 度的 3 倍且不小于 100。
W
3、分别装、点各接管。
W
4、焊接 G1-G7D。
W
5、件 19 件 1-3 与件 20 件 1 点固施焊 1C~4C.。
W
三 探伤 1C~.4C.角焊缝磁粉探伤按 JB4730-
W
2005Ⅰ级合格。
四 鉚 将管束与管板及筒体等组装。
C
编制
xxx
审核
xxx
备注
页
数
共 页第
页
工艺过程、质量控制流转卡
W
2005Ⅰ级合格。
编制
xxx
审核
xxx
备注
页
数
共 页第
页
1、材料确认 2、套料划线,对角线允差≤2mm 3、标记移植 4、切割、按产品“焊卡”坡口形式铣 坡口 5、压头、卷制、对口、点固 6、装点引弧板/(产品试板)/熄弧板 7、按“焊卡”施焊 2A 8、割去引弧板/(产品试板)/熄弧板
产品试板必须探伤后才能割下 9、复轧回圆 拼接焊缝作 20%X 射线探伤,按 JB4730-2005 标准( III )合格。
编号 检验员 签名
零件名称 毛刺管φ25*2.0
单台 数量
264
毛坯 L=1800 种类
日 设备 工 时 工序 期 型号 准结 操作 )
零件净重
卡片编号
工序简图
W
C
编制
xxx
审核
xxx
备注
页
数
共 页第
页
工艺过程、质量控制流转卡
设计材料
发放材料
工序 一、
工序 名称 机加 工
Q345R
入库号
材料代 用单号
2012-21 2012-21-0
焊缝 编号
净坯 种类
板 T=44 φ860
控制 形式
检验 操作者
检验员 日 设备 工 时 工序
日期
结果 名 称
签 名 期 型号 准结 操作
工序简图
H
H
二、 车 1、管板按图样车外圆,密封面及总厚 W 度。
三、 四、
五
钳 钻孔 铣
按图样划 264-φ25。25+0。1 管孔线, W
卡片编号
工序简图
H
H
二、 车 1、法兰按图样车内、外圆及总厚度
W
2、标记移植
三、 钳 按图样划 12-φ26 孔线
W
四、 钻孔 按图样钻 12-φ26 孔 .
W
编制
xxx
审核
xxx
备注
页
数
共 页第
页
工艺过程、质量控制流转卡
产品名称 汽水换热器
设计材料
发放材料
工序 一、
工序 名称 铆焊
二、 探伤
Q345R
入库号
材料代 用单号
工序内容
1、材料确认 2、套料划线,对角线允差≤2mm 3、标记移植 4、切割、按产品“焊卡”坡口形式铣 坡口 5、压头、卷制、对口、点固 6、装点引弧板/(产品试板)/熄弧板 7、按“焊卡”施焊 1A 8、割去引弧板/(产品试板)/熄弧板
产品试板必须探伤后才能割下 9、复轧回圆 拼接焊缝作 20%X 射线探伤,按 JB4730-2005 标准( III )合格。
单台 数量
1
毛坯 L=180 种类
日 设备 工 时 工序 期 型号 准结 操作 )
零件净重
卡片编号
工序简图
编制
xxx
审核
xxx
备注
页
数
共 页第
页
工艺过程、质量控制流转卡
设计材料
16Mnli 入库号
发放材料
材料代 用单号
工序 工序
名称
工序内容
机加 一、 工 1、锻件材料确认
2、领料、核对标记。
产品名称
设计材料
16Mnli 入库号
发放材料
材料代 用单号
工序 工序
名称
工序内容
机加 一、 工 1、锻件材料确认
2、领料、核对标记。
产品名称 汽水换热器
工作令号
件号
图号
件 19 件 1-3
EA12011-08
2012-21
焊缝
产品编号
2012-21-0
编号
零件名称 法兰
净坯 种类
单台 数量
共2
T=58 Φ860/ Φ700
零件净重
卡片编号
工序简图
控制 形式
检验 操作者
检验员 日 设备 工 时 工序
日期
结果 名 称
签 名 期 型号 准结 操作
H
H
二、 车 1、法兰按图样车内、外圆及总厚度
W
2、标记移植
三、 钳 按图样划 24-φ27 孔线
W
四、 钻孔 按图样钻 24-φ27 孔 .
W
编制
xxx
审核
xxx
备注
页
数
共 页第
4-M16 螺孔线。
按图样钻 264-φ25。25+0。1 管孔, W
4-M16 螺孔。
铣密封槽。
W
编制
xxx
审核
xxx
备注
页
数
共 页第
页
工艺过程、质量控制流转卡
产品名称 汽水换热器
件号
标准号
零件名称 容器总装
单台 数量
零件净重
卡片编号
设计材料 组合件
入库号
发放材料
材料代 用单号
工序 工序
名称
工序内容
工序 名称 铆焊
Q345R
入库号
材料代 用单号
工序内容
1、材料确认 2、套料划线,标记移植。 3、切割.
二、 外协 外协冷压成形,初检合格。 三、 铆 1、清理表面油污、垃圾。
产品名称
汽水换热器
工作令号
产品编号
控制 形式
H H W
检验 结果
件号 标 准 号
件 20 GB/T25198-201 件 1-1 0
结果 名 称
签 名 期 型号 准结 操作
工序简图
H
H
二、 车 1、管板按图样车外圆,密封面及总厚 W 度。
三、 四、
五
钳 钻孔 铣
按图样划 264-φ25。25+0。1 管孔线, W
。
按图样钻 264-φ25。25+0。1 管孔, W
。
铣密封槽。
W
编制
xxx
审核
xxx
备注
页
数
共 页第
页
工艺过程、质量控制流转卡
期 型号 准结 操作
零件净重
卡片编号
GB9019-88 艺 KⅠ 5
工序简图
A 类焊缝的对口错边量
对口处的名义厚度
错边量 E
≤12mm
≤1/4 S mm
12<S≤50mm
≤3 mm
>50
≤1/16S 且≯10mm
对接 A 类焊缝形成的棱角度 E≤ (S/10+2)且≯5mm;筒体的拼板不 小于 300;筒体高度(长度)应≥300; 相邻的 A 类焊缝的距离不小于筒体厚 度的 3 倍且不小于 100。
工作令号
2012-21
焊缝
产品编号
2012-21-0
编号
控制 形式
检验 操作者
检验员 日 设备 工 时 工序
日期
结果 名 称
签 名 期 型号 准结 操作
工序简图
一、 铆焊 1、设备上所有接管、法兰组装、点固 W
2、施焊 G1C~G4C。
W
二、 铆焊 1、件 12 筒体按图样划各接管。
H
2、经确认后开孔并磨制坡口
页
数
共 页第
页
工艺过程、质量控制流转卡
产品名称 汽水换热器
设计材料
发放材料
工序 一、
工序 名称 铆焊
组合件 入库号
工作令号
材料代 用单号
产品编号
工序内容
控制 形式
检验 结果
1、件 1-3 法兰与管箱筒体,封头组
w
件装配点固。
2.按《焊卡》施焊 1C。
w
3.按图划 a,b,g2,h 接管孔线并开 w
工作令号
产品编号
控制 形式
H H W W W W
检验 结果
W C
W H
编制
xxx
审核
xxx
件号 标 准 号
件 12 2012-21