(完整版)热轧产品缺陷图谱
[分享]钢铁材料常见缺陷(图谱)及产生原因
![[分享]钢铁材料常见缺陷(图谱)及产生原因](https://img.taocdn.com/s3/m/a6654654326c1eb91a37f111f18583d049640f7c.png)
科普知识
钢铁材料常见缺陷(图谱)及产生原因
我们在材料采购、生产加工以及试验检测过程中,经常发现材料中存在这样那样不同程度的缺陷,有的缺陷可能直接影响到使用。
为了进一步了解和识别缺陷成因及其对构件的影响,与大家共同学习,共同提高,
第一部分为“钢铁材料常见缺陷及产生原因”; 第二部分为“缺陷图谱”;“图谱”部分是笔者多年收集、整理、编写而成,供大家参考。
(一)钢铁材料常见缺陷及产生原因
型钢常见缺陷
重轨常见缺陷
线材常见缺陷
中厚板常见缺陷
热轧板(卷)常见缺陷
冷轧板(卷)常见缺陷
镀锌板(卷)常见缺陷
镀锡板(卷)常见缺陷
彩涂板(卷)常见缺陷
硅钢产品常见缺陷
图1-8为弯曲试验缺陷,图9-21为拉伸断口
图1:刮伤 图2:角钢中夹渣分层
图3:角钢夹渣分层 图4:夹杂分层
图5:气泡起层 图6:三分层缺陷
图7:气泡形成三分层图8:角钢上的缩管分层
图9:结晶状断口和星状断口图10:全杯状断口和半杯状断口
图11:菊花状断口和燕尾断口图12:燕尾断口和斜断口
图13:中心增碳和心部增碳图14:心部增碳
图15:表面增碳图16:结晶胎性断口和残余增碳
图17:结晶胎性断口和残余缩孔断口图18:残余缩孔断口和残余缩孔
图19:缩孔断口和缩孔横截面劈开成二半图20:缩孔断口
图21:白点断口和劈开断口。
热轧带钢缺陷图谱(内容清晰)

热轧带钢外观缺陷Visual Defects in Hot Rolled Strip2.1 不规则表面夹杂(夹层)(Irregular Shells)【定义与特征】板带钢表面的薄层折叠,缺陷常呈灰白色,其大小、形状不一,不规则分布于板带钢表面。
【产生原因】板坯表面或皮下有非金属夹杂,这些夹杂在轧制过程中被破碎或暴露而形成夹层状折叠。
【预防与纠正】优化炼钢、精炼工艺,提高钢质纯净度。
【鉴别与判定】肉眼检查,钢板和钢带不得有夹层。
2.2 带状表面夹杂(夹层)(Seams)【定义与特征】板带钢表面的夹杂呈线状或带状不规则地沿轧向分布,有时以点状或舌状逐渐消失。
【产生原因】板坯皮下的夹杂在轧制出现剧烈延伸、破裂而造成。
【预防与纠正】优化炼钢、精炼工艺,提高钢质纯净度。
【鉴别与判定】肉眼检查,钢板和钢带不得有夹层。
2.3 气泡(Blisters)【定义与特征】板带钢表面凸起内有气体,分布无规律,有闭口气泡和开口气泡之分。
【产生原因】板坯由于大量气体在凝固过程中不能逸出,被封闭在内部而形成气体夹杂。
在热轧时,空洞与孔穴被拉长,并随着轧材厚度减薄,被带至产品的表面或边部。
最终,高的气体压力使产品表面或边部出现圆顶状的凸起物或挤出物。
【预防与纠正】优化精炼工艺,保证吹氩时间,使钢水搅拌均匀,避免气体残留;保证中间包烘烤时间;保护渣要符合工艺要求,避免受潮。
【鉴别与判定】肉眼检查,钢板和钢带不得有气泡。
2.4 结疤(重皮)(Scabs)【定义与特征】以不规则的舌状、鱼鳞状、条状或M状的金属薄片分布于带钢表面。
一种与带钢基体相连;另一种与带钢基体不相连,但粘合到表面上,易于脱落,脱落后形成较光滑的凹坑。
【产生原因】由于板坯表面有结疤、毛刺,轧后残留在带钢表面。
或板坯经火焰清理后留有残渣,在轧制中压入表面。
【预防与纠正】加强板坯切口熔渣的清理,合理调整中间坯的切头、切尾量,避免毛刺残留。
【鉴别与判定】肉眼检查,钢板和钢带不得有结疤。
热轧带钢缺陷图谱
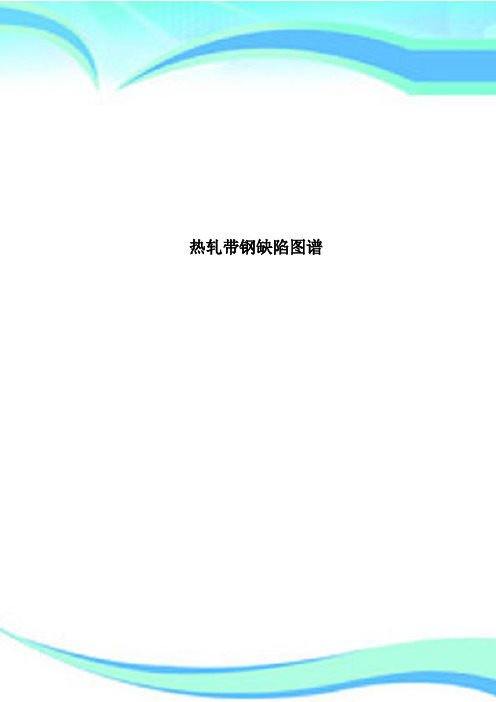
热轧带钢缺陷图谱————————————————————————————————作者: ————————————————————————————————日期:ﻩ热轧带钢外观缺陷Visual Defects inHot Rolled Strip 2.1 不规则表面夹杂(夹层)(IrregularShells)【定义与特征】板带钢表面的薄层折叠,缺陷常呈灰白色,其大小、形状不一,不规则分布于板带钢表面。
【产生原因】板坯表面或皮下有非金属夹杂,这些夹杂在轧制过程中被破碎或暴露而形成夹层状折叠。
【预防与纠正】优化炼钢、精炼工艺,提高钢质纯净度。
【鉴别与判定】肉眼检查,钢板和钢带不得有夹层。
2.2 带状表面夹杂(夹层)(Seams)【定义与特征】板带钢表面的夹杂呈线状或带状不规则地沿轧向分布,有时以点状或舌状逐渐消失。
【产生原因】板坯皮下的夹杂在轧制出现剧烈延伸、破裂而造成。
【预防与纠正】优化炼钢、精炼工艺,提高钢质纯净度。
【鉴别与判定】肉眼检查,钢板和钢带不得有夹层。
2.3 气泡(Blisters)【定义与特征】板带钢表面凸起内有气体,分布无规律,有闭口气泡和开口气泡之分。
【产生原因】板坯由于大量气体在凝固过程中不能逸出,被封闭在内部而形成气体夹杂。
在热轧时,空洞与孔穴被拉长,并随着轧材厚度减薄,被带至产品的表面或边部。
最终,高的气体压力使产品表面或边部出现圆顶状的凸起物或挤出物。
【预防与纠正】优化精炼工艺,保证吹氩时间,使钢水搅拌均匀,避免气体残留;保证中间包烘烤时间;保护渣要符合工艺要求,避免受潮。
【鉴别与判定】肉眼检查,钢板和钢带不得有气泡。
2.4 结疤(重皮)(Scabs)【定义与特征】以不规则的舌状、鱼鳞状、条状或M状的金属薄片分布于带钢表面。
一种与带钢基体相连;另一种与带钢基体不相连,但粘合到表面上,易于脱落,脱落后形成较光滑的凹坑。
【产生原因】由于板坯表面有结疤、毛刺,轧后残留在带钢表面。
攀钢热轧板带表面质量缺陷图谱

精整、成品工序: 7 在搬运钢卷过程中,把有捆带的钢撞倒或地上的硬物压入。——成品 8 生产中异物掉在或将捆带带入钢带表面,压入所致。——精整矫直 9 侧导板立辊磨损严重(起槽) ,将带钢边部刮出飞边压入钢带表面,压入所致。— —机械,精整 3、 预防及消除方法: 轧线: ①检查卷筒扇形板的定位精度。 ②助卷辊严重磨损时,及时更换。 ③检查、修磨卷取机助卷辊、夹送辊辊面。 ④加强卸卷小车托辊表面质量检查和修磨,定期更换托辊。 ⑤定期检查对芯杆顶卷信号杆,出现卡阻,及时处理。 精整线: ⑥发现异物压入钢带表面时,应及时停机处理。 定期更换并合理调整侧导板。 5、检查判断: 用肉眼检查,压痕不得超过有关标准规定深度和范围,否则应予判废。
第 5 页 共 28 页
攀钢热轧板带表面质量缺陷图谱
未按要求除鳞或让头除鳞。——轧钢粗轧、精轧岗位 板坯表面存在严重裂纹(纵裂、横裂等) ,板坯经加热、除鳞后,裂纹处氧化铁皮熔 渣不能完全去除,轧入带钢表面。——连铸 4、预防及消除方法: ①合理控制各钢种的加热制度。 ②合理设定大立辊的侧压。 ③检查高压除鳞水管的水压,保证水压在 15Mpa 以上;水咀角度和堵塞情况。
确保速度运行稳定,速度匹配。
5、检查判断: ①根据缺陷特征用肉眼检查。 ②判定方法与“划伤”相同。
第 10 页 共 28 页
攀钢热轧板带表面质量缺陷图谱
10 折迭(折叠、折皱、折边)
1、 缺陷代码:折跌 QD─02(03)─023 折边 QD─02(04)─036 2、 缺陷特征: 钢板局部性的折合称折迭。沿轧制方向的直线状折迭称顺折;垂直于轧制方向的折迭 称横折;边部折迭称折边。折迭与折印、折皱的区别主要在于缺陷的形状、程度不同而异, 折边与折角根据角度大小不同相区别。横向折迭多发生在薄规格的带钢中。
热轧板带表面缺陷表

1、一次氧化铁皮剥离不净;
2、二次氧化铁皮难以除净而残存
1、检查加热方法;
2、确保适当的轧制温度
不锈钢有一定的区别,尤其是“321”钢。
(冉富整理)
2、板形不佳;
3、开卷时张力辊及压紧辊的压紧力不适当
1、开卷时有效地使用压紧辊;
2、改善板形;
3、降低卷取温度;
4、完全冷却后开卷
异物压入
由于物体从一面被压入,板带上表面呈明显异物压入状
在轧制或精整线上加工时异物落在上面
1、防止异物落入;
2、做好机架间吹扫工作
凹凸块
板带表面出现周期性的凹凸形状的缺陷,上下表面都有可能产生
热轧板带表面缺陷表及由氧化铁皮造成的缺陷表
一、热轧板、带表面缺陷表
缺陷名称
表现形式
产生原因
防止措施
结疤
1、板带上下表面都可能出现;
2、形状呈结疤状
1、板坯裂纹或夹渣;
2、板坯清理不当
1、彻底清理板坯;
2、合理铸造板坯,加强炼钢、连铸工艺质量控制
腰折
1、板带宽度方向上出现的折皱;
2、低碳钢容易出现
1、高温开卷;
1、轧线或精整线各种轧辊粘附上杂物(凹形缺陷);
2、轧线精整辊子掉肉(凸形缺陷)
1、彻底检查各种轧辊;
2、防止轧机带入异物;
3、换辊时注意别碰伤轧辊;
4、清扫导板等,防止异物带入
擦伤
1、不规则、不定形的锐利擦伤;
2、多数是正反两面同时出现;
3、多数是出现在钢卷最外几圈
1、开卷时板卷过松引起擦伤;
2、板卷运输时宽度方向窜动
1、混入炼钢耐火材料;
2、粘附上加热炉耐火材料
热轧钢管产品缺陷一览表

热轧钢管产品缺陷一
缺陷名称产生原因
产生工序
管坯表面砸伤,管坯表面有裂
纹
来料单位轧辊表面有异物穿孔导板材质不好
供货单位导板磨损严重或粘钢穿孔导板的形状和轧辊的形状不吻合
工艺设计导向口或受料槽不光穿孔托辊、抱辊、料钩等表面不光
滑穿孔
内孔刮伤顶头或顶杆上有凸起的部分,
束节不光滑或匹配不当
穿孔钢温偏低司炉顶头冷却水太大穿孔顶头位置过后穿孔管坯剪切斜度过大剪切钢温过低、阴阳面司炉、拔料
顶头偏离中心太多
穿孔模子磨损严重打头职工操作不规范
打头尺寸超差
责任心不够,量具不齐全,取
样不及时
穿孔
壁厚不均
打头不好外折叠
导板印
外表碰划
伤内孔折叠
缺陷一览表
预防措施及解决方法备注
严格检查进厂的管坯质量
修磨轧辊
更换供货厂家,确保导板质量
修磨或更换导板
根据辊形设计导板的尺寸
修磨或更换导向口,受料槽,多
在尾部
修磨或更换
修磨或更换
经常观察仪表,保证炉温
把水开小点
进一点顶头位置
更换剪切刀片(头部)
保证钢温、及时拨料
正确调整抱辊,轧辊左右位
置,保证轧辊中心
堆焊或更换模子
加强锻炼,提高责任心
配备各种量具,加强职工责任
心。
热轧卷缺陷图谱(勿删)
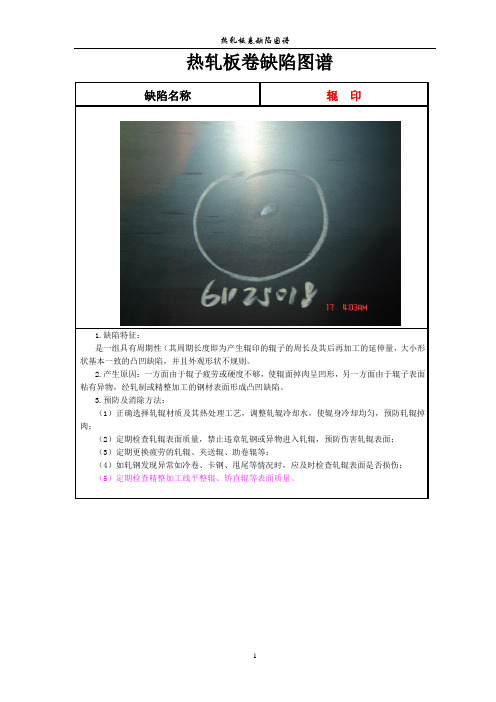
热轧板卷缺陷图谱热轧板卷缺陷图谱缺陷特征:是一组具有周期性(其周期长度即为产生辊印的辊子的周长及其后再加工的延伸量,大小形状基本一致的凸凹缺陷,并且外观形状不规则。
产生原因:一方面由于辊子疲劳或硬度不够,使辊面掉肉呈凹形,另一方面由于辊子表面粘有异物,经轧制或精整加工的钢材表面形成凸凹缺陷。
预防及消除方法:)正确选择轧辊材质及其热处理工艺,调整轧辊冷却水,使辊身冷却均匀,预防轧辊掉)定期检查轧辊表面质量,禁止违章轧钢或异物进入轧辊,预防伤害轧辊表面;)定期更换疲劳的轧辊、夹送辊、助卷辊等;)如轧钢发现异常如冷卷、卡钢、甩尾等情况时,应及时检查轧辊表面是否损伤;)定期检查精整加工线平整辊、矫直辊等表面质量。
缺陷特征:氧化铁皮一般粘附在钢板表面上,分布于板面局部或全部,铁皮有的疏松易脱落;不易脱落。
根据其外观形态不同可分为:红铁皮、线条状铁皮、木纹状铁皮、流线状铁皮、纺锤状铁皮、拖曳状铁皮或散沙状铁皮等。
产生原因:板坯加热制度不合理或加热操作不当生成较厚且较致密的铁皮,除鳞时难以除尽,轧制时被压入钢板表面上;)由于高压除鳞水压力低、水咀堵塞、水咀角度安装不合理或操作不当等原因,使钢坯上的铁皮未除尽,轧制时被压入到钢板表面上。
)氧化铁皮在沸腾钢中发生较多,含硅较高的钢中易产生红铁皮。
缺陷图片缺陷特征:沿钢板的轧制方向呈现高低起伏的波浪形的弯曲。
根据分布的部位不同,分为中间浪、单边浪和双边浪。
产生原因:)辊形曲线不合理,轧辊磨损不均匀;)压下量分配不合理;)轧辊辊缝调整不良或轧件跑偏;缺陷特征:钢卷端部不齐,呈面包状称塔形。
卷边上下错动称卷边错动。
产生原因:)卷取机张力设定不合理;)卷取机前侧导板、夹送辊、助卷辊调整不当;)带钢进卷取机时不对中,带钢跑偏;)带钢存在较大的镰刀弯或板型不良;)卷取机卸卷时将钢卷头部曳出。
缺陷特征:钢卷未卷紧,层与层之间有间隙称松卷。
产生原因:)卷取张力设定不合理;)带钢有严重浪形或因卷取机故障带钢在辊道上温度降低变形;)打捆机故障打捆不紧或吊运过程中断带;)卷取完毕后,因故卷筒反转等。
新钢 mm热轧卷板质量缺陷判定标准及图谱

新钢1580mm生产线热轧卷板质量缺陷判定标准及图谱本标准主要根据表面检测仪上的带钢上下表面缺陷等级和近来热卷质量异议情况来确立判定依据的,并对热卷的质量异议图片、表面检测仪上的图片和现场钢卷图片缺陷组成缺陷图谱,对缺陷的特征、产生的原因、预防措施和检查判定进行了归纳。
本标准主要分以下三大部分。
一、表面检测仪缺陷等级划分;二、钢卷缺陷判定标准;三、热轧卷缺陷图谱。
本标准起草人:唐小勇、朱永宽。
一、表面检测仪缺陷等级划分上下表面仪上表面缺陷等级分为5级:轻微为1,2级——显示为鲜绿色。
一般缺陷为3级——显示为黄色严重缺陷为4级——显示为淡红色极严重缺陷为5级——显示为红色1级的缺陷面积<2mm*2mm2级的缺陷面积在(2mm*2mm——5mm*5mm)之间3级的缺陷面积在(5mm*5mm——10mm*10mm)之间4级的缺陷面积在(10mm*10mm——15mm*15mm)之间5级的缺陷面积>15mm*15mm二、钢卷缺陷判定标准(客户有特殊要求时,按客户特殊要求进行;否则,按以下标准判定。
)表1缺陷类型钢种国内或出口判定标准补充规定结疤或重皮(见缺陷图谱1)冷轧基料和管线钢国内只允许边部10mm以内存在,否则判订单外。
对于只是在带钢头尾存在重皮或结疤,要对其进行切除处理。
出口热轧商品卷国内只允许边部15mm以内存在,否则判订单外。
出口只允许边部10mm以内存在,否则判订单外。
气泡(见缺陷图谱2)冷轧基料和管线钢国内只允许边部15mm以内存在气泡,且在带钢边部的长度方向每米不多于1个,缺陷宽度<6mm、长度<20mm,可放行。
对不符合判定标准的钢卷判订单外,临时封锁,上平整线做第二次判定。
出口只允许边部10mm以内存在气泡,且在带钢边部的长度方向每米不多于1个,缺陷宽度<6mm、长度<20mm,可放行。
热轧商品卷国内①允许边部25mm以内存在气泡,且在带钢边部的长度方向每米不多于1个,缺陷宽度<6mm、长度<20mm,可放行;②对于国内的热轧商品卷,带钢宽度其它部位若出现翘皮,只要在表面缺陷等级≤3级,且相邻两个缺陷沿轧制方向的距离超过3米,可放行。
热轧产品缺陷
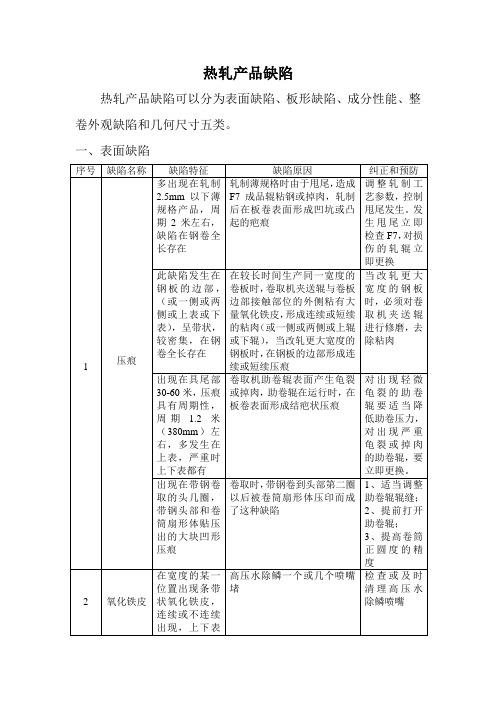
此缺陷发生在钢板的边部,(或一侧或两侧或上表或下表),呈带状,较密集,在钢卷全长存在
在较长时间生产同一宽度的卷板时,卷取机夹送辊与卷板边部接触部位的外侧粘有大量氧化铁皮,形成连续或短续的粘肉(或一侧或两侧或上辊或下辊),当改轧更大宽度的钢板时,在钢板的边部形成连续或短续压痕
1、卷取机前侧导板位置安装不当,使对带钢的导向出现偏差;
2、卷取机卷筒张紧过大,致使卷筒收缩后,卷筒与板卷内圈仍然紧紧接触,卸卷时将内几圈带出,形成塔形
1、定期检查更换侧导板;
2、优化卷取工艺操作。
15
松卷
卷板层与层之间出现较大缝隙,多出现在轧制厚规格产品当中
1、卷取速度、辊道速度的匹配出现偏差;
2、卷取张力出现大的波动;
划伤出现在卷板的下表面,发亮
1、精轧出口与卷取机之间、精整线上个别辊道运转不正常;
2、拆卷时带钢下表与地辊表面摩擦,下表面被划伤。
检查运输辊道的运转情况,及时排除故障
4
啃伤
只发生在拆卷的卷板外层,横向短长条,发亮,上下表均可能发生
主线拆卷时,地辊和压紧辊的作用下,发生层与层之间的错动啃伤。
1、及时更换地辊,保证两个地辊平衡
花纹的基板有明显的凸起与凹陷,呈鱼鳞状,沿板面分布
花纹板在卷取过程中,由于助卷辊压力过大,使内层花纹对外层板面有一个相当大的作用力,导致板面(基板)不平
1、降低卷取温度;
2、降低助卷辊压力,减轻助卷辊对板面饿作用力
三、整卷外观缺陷
序号
缺陷名称
缺陷特征
缺陷原因
纠正和预防
14
塔形
象塔一样的形状,多出现在轧制厚规格产品中
新钢1580mm热轧卷板质量缺陷判定标准及图谱(PDF62页)
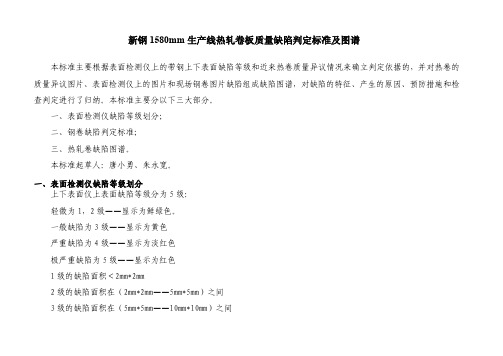
新钢1580mm生产线热轧卷板质量缺陷判定标准及图谱本标准主要根据表面检测仪上的带钢上下表面缺陷等级和近来热卷质量异议情况来确立判定依据的,并对热卷的质量异议图片、表面检测仪上的图片和现场钢卷图片缺陷组成缺陷图谱,对缺陷的特征、产生的原因、预防措施和检查判定进行了归纳。
本标准主要分以下三大部分。
一、表面检测仪缺陷等级划分;二、钢卷缺陷判定标准;三、热轧卷缺陷图谱。
本标准起草人:唐小勇、朱永宽。
一、表面检测仪缺陷等级划分上下表面仪上表面缺陷等级分为5级:轻微为1,2级——显示为鲜绿色。
一般缺陷为3级——显示为黄色严重缺陷为4级——显示为淡红色极严重缺陷为5级——显示为红色1级的缺陷面积<2mm*2mm2级的缺陷面积在(2mm*2mm——5mm*5mm)之间3级的缺陷面积在(5mm*5mm——10mm*10mm)之间4级的缺陷面积在(10mm*10mm——15mm*15mm)之间5级的缺陷面积>15mm*15mm二、钢卷缺陷判定标准(客户有特殊要求时,按客户特殊要求进行;否则,按以下标准判定。
)表1缺陷类型钢种国内或出口判定标准补充规定结疤或重皮(见缺陷图谱1)冷轧基料和管线钢国内只允许边部10mm以内存在,否则判订单外。
对于只是在带钢头尾存在重皮或结疤,要对其进行切除处理。
出口热轧商品卷国内只允许边部15mm以内存在,否则判订单外。
出口只允许边部10mm以内存在,否则判订单外。
气泡(见缺陷图谱2)冷轧基料和管线钢国内只允许边部15mm以内存在气泡,且在带钢边部的长度方向每米不多于1个,缺陷宽度<6mm、长度<20mm,可放行。
对不符合判定标准的钢卷判订单外,临时封锁,上平整线做第二次判定。
出口只允许边部10mm以内存在气泡,且在带钢边部的长度方向每米不多于1个,缺陷宽度<6mm、长度<20mm,可放行。
热轧商品卷国内①允许边部25mm以内存在气泡,且在带钢边部的长度方向每米不多于1个,缺陷宽度<6mm、长度<20mm,可放行;②对于国内的热轧商品卷,带钢宽度其它部位若出现翘皮,只要在表面缺陷等级≤3级,且相邻两个缺陷沿轧制方向的距离超过3米,可放行。
热轧常见缺陷

RAL
5 折迭(折印、折皱、折边、折角) 折迭(折印、折皱、折边、折角)
表现: 钢板局部性的折合称折迭。沿轧制方向的直线状折迭称顺折垂直于轧制方向 的折选称横折,边部折迭称折边。折造与折印、折皱的区别主要在于缺陷的 形状,程度不同而异,折边与折角根据角度大小不同相区别。横向折选多发 生在薄规格的带钢中。含碳量小于0.08的软钢种,因开平机没有安装张力辊易 产生折皱。 (1)板坯缺陷清理的深宽比过大。(2)板坯温度不均匀或精轧轧辊辊型配置不合 理及轧制负荷分配不合理等,轧制中的带钢园不均匀变形成大波浪后被压合。 (3)立辊辊环的挤压或轧件有严重刮伤以及由于粗轧来料有较大的镰w弯,对 中不良等原因,刮框后再次被轧制压合。(4)卷取机前的侧导板严重磨损出现 淘槽,开口度过小,夹送辊缝呈楔形,易使带钢跑偏,在恻导板沟槽处的部 位被夹送辊压。(5)因故没及时卷取,使卷取温度过低或卷取速度设定不台适。 (6)钢卷卷边错动,或因钢卷松动,在用吊车上吊,下降落地时易产生折边(折 角),此时,常发生在厚度较薄的钢卷上。(7)带钢开卷温度过高,或开卷时的 张力及压紧辊的压力设定不合适。
RAL
10 波 浪
带钢板形的产生原因是变形的不均。 热轧 带钢板形的产生原因是变形的不均。 详见板形的设定与控制部分。 详见板形的设定与控制部分。
3 氧化铁皮
表现: 氧化铁皮一般粘附在钢板表面,分布于板 面的局部和全部。铁皮有的疏松易脱落, 有的压入板面不易脱落。根据其外观形状 不同有:红铁皮、线状铁皮、木纹状铁皮、 流星状铁皮、纺锤状铁皮,拖曳状铁皮和 散沙状铁皮等。
(1)板坯加热制度不合理或加热操作不良时产生一次铁皮难以除尽,轧 制时被压人到钢板表面上。 (2)大立辊设定不合理,铁皮未挤松,难以除掉。 (3)由于高压除鳞水管的水压低,水咀堵塞,水咀角度不对及使用不当 等原园,使钢板上的铁皮没有除尽,轧制后被压^引钢板表面上。 (4)氧化铁皮在沸腾钢中发生较多,在含硅较高的钢中易产生红铁皮。
热轧钢板常见表面缺陷浅析

热轧钢板常见表面缺陷浅析董振虎王焱(济南大学控制科学与工程学院,济南 250022)摘要随着热轧板材厚度越来越薄,使其在家用电器、汽车制造、集装箱和建筑工业等方面获得了广泛应用,热轧薄板材在部分行业替代传统的冷轧板材已成为一种发展趋势。
近年来,针对热轧板带产品愈来愈薄以及对板形精度要求越来越高的特点,对热轧钢板的缺陷进行广泛深入的研究也变得尤为重要。
本文对热轧钢板常见表面缺陷进行了详细分类与综述,并且对产生缺陷的影响因素进行了分析。
同时,对如何防止部分缺陷的产生进行了讨论。
关键词热轧钢板表面缺陷缺陷分类Analysis of Common Surface Defects inHot Rolled Steel PlatesDong Zhenhu Wang Yan(School of Control Science and Engineering, University of Jinan, Jinan, 250022)Abstract With the thickness of hot-rolled steel plates getting thinner and thinner,it gained a wide range applications in household appliances,automobile manufacturing,container, and construction industries.Hot-rolled steel plates has become a development trend in some alternative to the traditional cold-rolled sheet metal industry.In recent years,for hot-rolled steel plates getting thinner and thinner and the increasingly high precision of the shape accuracy,it has become particularly important to extensive research for the defects of hot rolled steel sheet.Hot-rolled steel sheet classification of common surface defects are reviewed in detail, and some causes of defects are analyzed. Meanwhile, a number of hot-rolled steel plate to prevent the occurrence of defects are discussed.Key words hot rolled steel plates surface defect defect classification1 引言热连轧钢板、带产品是重要的钢材品种之一,随着热轧板材在各方面的应用和发展,用户对于产品的要求也是越来越严格。
热轧板卷缺陷(精选.)

第七篇热轧板卷缺陷(M)7.1结疤(M01)图7-1-1图7-1-21.缺陷特征附着在钢带表面,形状不规则翘起的金属薄片称结疤。
呈现叶状、羽状、条状、鱼鳞状、舌端状等。
结疤分为两种,一种是与钢的本体相连结,并折合到板面上不易脱落;另一种是与钢的本体没有连结,但粘合到板面上,易于脱落,脱落后形成较光滑的凹坑。
2.产生原因及危害产生原因:①板坯表面原有的结疤、重皮等缺陷未清理干净,轧后残留在钢带表面上;②板坯表面留有火焰清理后的残渣,经轧制压入钢带表面。
危害:导致后序加工使用过程中出现金属剥离或产生孔洞。
3.预防及消除方法加强板坯质量验收,发现板坯表面存在结疤和火焰清理后残渣应清理干净。
4.检查判断用肉眼检查;不允许存在结疤缺陷,对局部结疤缺陷,允许修磨或切除带有结疤部分带钢的方法消除,如结疤已脱落,则比照压痕缺陷处理。
7.2气泡(M02)图7-2-1 闭合气泡图7-2-2 开口气泡图7-2-3 开口气泡1.缺陷特征钢带表面无规律分布的圆形或椭圆形凸包缺陷称气泡。
其外缘较光滑,气泡轧破后,钢带表面出现破裂或起皮。
某些气泡不凸起,经平整后,表面光亮,剪切断面呈分层状。
2.产生原因及危害产生原因:①因脱氧不良、吹氩不当等导致板坯内部聚集过多气体;②板坯在炉时间长,皮下气泡暴露或聚集长大。
危害:可能导致后序加工使用过程中产生分层或焊接不良。
3.预防及消除方法①加强板坯质量验收,不使用气泡缺陷暴露的板坯;②严格按规程加热板坯,避免板坯在炉时间过长。
4.检查判断用肉眼检查;不允许存在气泡缺陷。
7.3表面夹杂(M03)图7-3-1图7-3-21.缺陷特征板坯中的夹杂或夹渣经轧制后在钢带表面暴露的块状或长条状的夹杂缺陷称表面夹杂。
其颜色一般呈棕红色、黄褐色、灰白色或灰黑色。
2.产生原因及危害产生原因:板坯皮下夹杂轧后暴露或板坯原有的表面夹杂轧后残留在带钢表面。
危害:可能导致后序加工过程中产生孔洞、开裂、分层。
3.预防及消除方法加强板坯检查验收,不使用表面存在严重夹杂或夹渣的板坯。
- 1、下载文档前请自行甄别文档内容的完整性,平台不提供额外的编辑、内容补充、找答案等附加服务。
- 2、"仅部分预览"的文档,不可在线预览部分如存在完整性等问题,可反馈申请退款(可完整预览的文档不适用该条件!)。
- 3、如文档侵犯您的权益,请联系客服反馈,我们会尽快为您处理(人工客服工作时间:9:00-18:30)。
目录5.热轧板卷缺陷(M) (2)(M01) 结疤 (3)(M02) 气泡 (5)(M03) 表面夹杂 (7)(M04) 分层 (9)(M05) 中心线缺陷 (10)(M06) 压入氧化铁皮 (11)(M07) 辊印 (14)(M08) 轧烂 (16)(M09) 压痕(压印、压坑) (18)(M10) 塔形 (20)(M11) 松卷 (22)(M12) 扁卷 (23)(M13) 瓢曲 (24)(M14) 波浪(中浪、双边、单边浪) (26)(M15) 镰刀弯 (28)(M16) 横折 (29)(M17) 折迭 (30)(M18) 折边 (32)(M19) 边裂 (33)(M20) 划伤 (35)(M21) 刮伤 (36)(M22) 剪切断面不良 (38)(M23) 纵切交叉卷 (39)(M24) 油污 (41)(M25) 撞伤 (42)(M26) 厚度不合 (44)(M27) 宽度不合 (46)(M28) 长度不合 (47)(M29) 凸度不合 (48)(M30) 楔形 (50)(M31) 切斜 (51)(M32) 冲裂 (52)5.热轧板卷缺陷(M)本章节收录了大量的热轧板卷的缺陷照片,并对每种缺陷的特征、产生原因与危害、预防消除方法、检查方法、判定等作了简要描述。
为我们在实际生产过程中,对于常见产品质量缺陷的判定、成因分析以及治理措施的制定提供一定的指导作用。
(M01) 结疤图5-1-1图5-1-2a)缺陷特征附着在钢带表面,形状不规则翘起的金属薄片称结疤。
呈现叶状、羽状、条状、鱼鳞状、舌端状等。
结疤分为两种,一种是与钢的本体相连结,并折合到板面上不易脱落;另一种是与钢的本体没有连结,但粘合到板面上,易于脱落,脱落后形成较光滑的凹坑。
b)产生原因及危害产生原因:①板坯表面原有的结疤、重皮等缺陷未清理干净,轧后残留在钢带表面上;②板坯表面留有火焰清理后的残渣,经轧制压入钢带表面。
危害:导致后序加工使用过程中出现金属剥离或产生孔洞。
c)预防及消除方法加强板坯质量验收,发现板坯表面存在结疤和火焰清理后残渣应清理干净。
d)检查判断用肉眼检查;不允许存在结疤缺陷,对局部结疤缺陷,允许修磨或切除带有结疤部分带钢的方法消除,如结疤已脱落,则比照压痕缺陷处理。
(M02) 气泡图5-2-1 闭合气泡图5-2-2 开口气泡图5-2-3 开口气泡a)缺陷特征钢带表面无规律分布的圆形或椭圆形凸包缺陷称气泡。
其外缘较光滑,气泡轧破后,钢带表面出现破裂或起皮。
某些气泡不凸起,经平整后,表面光亮,剪切断面呈分层状。
b)产生原因及危害产生原因:①因脱氧不良、吹氩不当等导致板坯内部聚集过多气体;②板坯在炉时间长,皮下气泡暴露或聚集长大。
危害:可能导致后序加工使用过程中产生分层或焊接不良。
c)预防及消除方法①加强板坯质量验收,不使用气泡缺陷暴露的板坯;②严格按规程加热板坯,避免板坯在炉时间过长。
d)检查判断用肉眼检查;不允许存在气泡缺陷。
(M03) 表面夹杂图5-3-1图5-3-2a)缺陷特征板坯中的夹杂或夹渣经轧制后在钢带表面暴露的块状或长条状的夹杂缺陷称表面夹杂。
其颜色一般呈棕红色、黄褐色、灰白色或灰黑色。
b)产生原因及危害产生原因:板坯皮下夹杂轧后暴露或板坯原有的表面夹杂轧后残留在带钢表面。
危害:可能导致后序加工过程中产生孔洞、开裂、分层。
c)预防及消除方法加强板坯检查验收,不使用表面存在严重夹杂或夹渣的板坯。
d)检查判断用肉眼检查;钢带表面不允许存在夹杂缺陷。
对局部夹杂缺陷允许用修磨的方法清除,但不得超过标准规定的深度和范围。
(M04) 分层图5-4-1a)缺陷特征钢带断面出现连续或断续的线条状分离的现象称分层。
b)产生原因及危害产生原因:①板坯内部聚集过多的非金属夹杂或夹渣;②板坯内部存在严重的中心裂纹或中心疏松,经多道次轧制未能焊合。
危害:导致后续加工使用过程中出现分层或焊接不良;在冷轧轧制时可能断带。
c)预防及消除方法①加强炼钢冶炼、浇铸过程控制,提高钢质纯净度;②加强板坯质量验收,不使用存在严重中心裂纹或中心疏松的板坯。
d)检查判断用肉眼检查;不允许存在分层缺陷。
(M05) 中心线缺陷图5-5-1a)缺陷特征在钢带横断面的中心部位出现明显的连续或断续的细线状缺陷称中心线缺陷。
线条较轻,断断续续,肉眼可见的中心线缺陷称中心偏析I级;明显的连续的线条状,但未完全分开的中心线缺陷称中心偏析II级;明显开口状的中心线缺陷称分层。
b)产生原因及危害产生原因:连铸流道质量控制不良或铸坯冷却不良。
危害:可能导致顾客使用过程中出现分层,影响焊接质量。
c)预防及消除方法加强连铸流道质量和铸坯冷却控制。
检查及判断用肉眼检查;中心偏析I级允许存在;有中心偏析II级的产品不能用于汽车大梁等风险产品,但可用于其他产品。
(M06) 压入氧化铁皮图5-6-1 一次(炉生)氧化铁皮(压入)图5-6-2 二次氧化铁皮(轧制过程产生)图5-6-3 二次氧化铁皮(轧辊氧化膜脱落)a)缺陷特征热轧过程中氧化铁皮压入钢带表面形成的一种表面缺陷称压入氧化铁皮。
按其产生原因不同可分为炉生(一次)氧化铁皮、轧制过程中产生的(二次)氧化铁皮或轧辊氧化膜脱落压入带钢表面形成的(二次)氧化铁皮。
b)产生原因及危害产生原因:①板坯表面存在严重纵裂纹;②板坯加热工艺或加热操作不当,导致炉生铁皮难以除尽;③高压除鳞水压力低、喷嘴堵塞等导致轧制过程中产生的氧化铁皮压入带钢表面;④轧制节奏过快、轧辊冷却不良等导致轧辊表面氧化膜脱落压入带钢表面。
危害:影响钢带表面质量和涂装效果。
c)预防及消除方法①加强板坯质量验收,表面存在严重纵裂纹的板坯应清理合格后使用;②合理制订板坯加热工艺,按规程要求加热板坯;③定期检查高压除鳞水系统设备,保证除鳞水压力,避免喷嘴堵塞;④合理控制轧制节奏,确保轧辊冷却效果,防止轧辊表面氧化膜脱落。
d)检查判断用肉眼检查;不允许存在压入氧化铁皮。
(M07) 辊印图5-7-1 前机架轧辊网纹图5-7-2 轧辊网纹a)缺陷特征钢带表面呈周期分布、外观形状不规则的凸凹缺陷称辊印。
b)产生原因及危害产生原因:辊子龟裂、局部掉肉,或表面粘有异物,使局部辊面呈凹、凸状,轧制或精整加工时,压入钢带表面形成凸凹缺陷。
危害:凸辊印可能导致后序轧制过程中产生折迭缺陷;凹辊印可能导致后序轧制过程中产生孔洞。
c)预防及消除方法①定期检查轧辊表面质量,发现辊子掉肉或粘有异物时及时处理;②轧制过程中出现卡钢、甩尾、轧烂等异常情况时,及时检查辊子表面质量,防止辊面损伤或异物粘附;③检查发现轧辊网纹时,立即停机检查轧辊表面质量。
d)检查判断用肉眼检查,根据辊印周期确定责任工序;允许存在轻微辊印,但其深度或高度不得超过标准规定的范围。
(M08) 轧烂图5-8-1图5-8-2a)缺陷特征带钢表面出现多层重叠或轧穿、撕裂等现象称轧烂。
b)产生原因及危害产生原因:①辊缝调整不当或辊型与来料板型配合不良,带钢延伸不均;②板坯局部加热温度不均或轧件温度不均;③精轧侧导板开口度设定不合理;④精轧过程中秒流量不匹配。
危害:轧制过程中断带,存在轧烂缺陷的钢板无法使用。
c)预防及消除方法合理配置轧辊辊型,注意辊缝调整;加强板坯加热温度控制,保证轧件温度均匀;合理设定精轧侧导板开口度;保持连轧过程中秒流量一致。
d)检查判断用肉眼检查;不允许存在轧烂缺陷。
(M09) 压痕(压印、压坑)图5-9-1a)缺陷特征钢带表面无周期性分布的凹凸印迹称压痕。
b)产生原因及危害产生原因:①异物压入,脱落后形成压坑;②卸卷小车托辊表面粘肉;③卷筒、卸卷小车部件松动;④吊运钢卷过程中机械损伤;⑤切边或剪板过程中带钢跑偏,飞边压入钢带。
危害:在后续加工使用过程中可能产生孔洞或断带。
c)预防及消除方法①防止异物压入;②加强卸卷小车托辊表面质量检查和修磨,定期更换托辊;③加强卷筒、卸卷小车点检,防止部件松动;④精心搬运钢卷,防止机械损伤;⑤防止带钢跑偏。
d)检查判断用肉眼检查;允许存在轻微压痕缺陷,但不得超过标准规定深度和范围。
(M10) 塔形图5-10-1图5-10-2 a)缺陷特征钢卷上下端不齐,外观呈塔状称塔形。
b)产生原因及危害产生原因:①助卷辊间隙调整不当;②夹送辊辊缝呈楔形;③带钢进卷取机时对中不良;④卷取张力设定不合理;⑤卷筒传动端磨损严重,回转时有较大的离心差;⑥带钢有较大的镰刀弯、楔形或板形不良。
危害:塔形严重的钢卷无法开卷使用。
c)预防及消除方法①加强助卷辊间隙调整;②保持夹送辊辊缝水平;③合理设定卷取机前侧导板,保持带钢对中;④合理设定卷取张力;⑤定期更换卷筒,防止卷筒严重磨损;⑥加强带钢板形控制。
d)检查判断用肉眼检查,用适当的工具测量塔形高度;允许存在轻微塔形,但塔形高度不得超过标准规定的范围。
图5-11-1a)缺陷特征钢卷未卷紧,层与层之间有明显间隙的现象称松卷。
b)产生原因及危害产生原因:①卷取张力设定不合理、卷取能力不足;②带钢存在严重浪形;③带钢卷取完毕,卷筒反转;④捆带未打紧、断带或卷冷钢。
危害:影响钢带包装和搬运,严重的松卷无法开卷使用。
c)预防及消除方法①合理设定卷取张力;②加强带钢板形控制,防止带钢产生严重浪形;③防止卷筒反转;④选用强度高的捆带。
d)检查判断用肉眼检查,用卷尺测量钢卷外径;允许存在轻微松卷,但钢带外径不得超过标准规定的范围。
图5-12-1a)缺陷特征钢卷呈椭圆形的现象称扁卷。
b)产生原因及危害产生原因:①钢卷在搬运过程中,承受过大的冲击;②钢卷卷取张力偏低,卧卷堆放或多层堆放钢卷。
危害:影响钢卷包装和搬运,严重的扁卷无法开卷使用。
c)预防及消除方法①精心搬运钢卷;②合理设定卷取张力,控制卧卷堆放的层数,必要时采用立卷堆放。
d)检查判断用肉眼检查,用卷尺测量钢卷内、外径;允许存在轻微扁卷,但钢卷最小内径和最大外径不得超过标准规定的范围。
图5-13-1图5-13-2a)缺陷特征钢板的纵横部分同时在同一个方向出现翘起的现象称瓢曲。
b)产生原因及危害产生原因:①带钢轧制过程变形不均;②轧制计划编排不合理,在一个轧辊周期内集中轧制窄规格带钢后又集中轧宽规格带钢;③层流冷却不均;④精整生产时,矫直机压下设定不良或压力辊、矫直辊磨损严重;⑤钢板堆放不当。
危害:影响钢板外观形象,严重时可能导致后工序无法加工使用。
c)预防及消除方法①合理配置辊型,保持带钢变形均匀;②合理编排轧制计划;③控制好层流冷却;④加强矫直机压下设定,定期更换压力辊、矫直辊;⑤钢板堆放应平直。
d)检查判断用肉眼检查,用适当工具测量钢带不平度;允许存在轻微瓢曲,但其不平度不得超过标准规定的范围。
(M14) 波浪(中浪、双边、单边浪)图5-14-1a)缺陷特征沿钢带轧制方向呈现高低起伏的波浪形弯曲现象称浪形。