汽车仪表板电子测试系统的设计与实现
基于VTSystem的汽车电气自动测试系统研制及应用

基于VTSystem的汽车电气自动测试系统研制及应用明星【摘要】汽车电气系统测试除了要测试车身电器基本的功能外,还必须要测试控制器的通信接口和I/O接口在发生故障时的情况。
本文采用Vector公司的CANoe 软件以及VT硬件板卡构建了一个汽车电气自动测试系统,结合装有实车相关电器零部件的Labcar台架,通过自动测试系统的故障自动注入,可以实现对某款轻型客车的仪表(IPK)和车身控制器(BCM)功能的自动测试。
%The controller's communication interface and I/O should be tested as well as the basic functions of electric appliances in the test of vehicle electrical system. An auto-test electrical system based on the CANoe software of Vector company and the VT hardware board card has been set up. It can realize the function auto-test of IPK and BCM on a type of light bus, combining with a Labcar jack horse with related electrical parts and through the fault auto-input of this system.【期刊名称】《汽车电器》【年(卷),期】2012(000)008【总页数】3页(P62-64)【关键词】汽车电气自动测试系统;VT;仪表;车身控制器【作者】明星【作者单位】上海汽车集团股份有限公司商用车技术中心,上海200438【正文语种】中文【中图分类】U467.4仪表(IPK)和车身控制器(BCM)是汽车电器系统中2个重要的控制器,与车身舒适性密切相关,如果某一个控制器在功能上出现一个错误,都很容易被用户感觉出来,从而对品牌造成极其不利的影响。
汽车电子可靠性测试及相关标准

电子设备可靠性测试标准1、ISO国际标准化组织中,ISO/TC22/SC3 负责汽车电气和电子技术领域的标准化工作。
汽车电子产品的应用环境包括电磁环境、电气环境、气候环境、机械环境、化学环境等。
目前ISO 制订的汽车电子标准环境条件和试验标准主要包含如下方面:ISO16750-1:道路车辆-电子电气产品的环境条件和试验:总则ISO16750-2:道路车辆-电子电气产品的环境条件和试验:供电环境ISO16750-3:道路车辆-电子电气产品的环境条件和试验:机械环境ISO16750-4:道路车辆-电子电气产品的环境条件和试验:气候环境ISO16750-5:道路车辆-电子电气产品的环境条件和试验:化学环境ISO20653 汽车电子设备防护外物、水、接触的等级ISO21848 道路车辆-供电电压42V 的电气和电子装备电源环境国内目前汽车电子产品的环境试验标准主要还是按照产品的技术条件来规定。
全国汽车标准化技术委员会(SAC/TC114)正在参照ISO 标准制订相应的国家和行业标准。
ISO 的标准在欧美车系的车厂中得到了广泛采用,而日系车厂的要求相对ISO 标准来说偏离较大。
为了确保达到标准的限值,各汽车车厂的内控的环境条件标准一般比ISO 的要求要苛刻。
2、AEC 系列标准上个世纪九十年代,克莱斯勒、福特和通用汽车为建立一套通用的零件资质及质量系统标准而设立了汽车电子委员会(AEC),AEC 建立了质量控制的标准。
AEC-Q-100 芯片应力测试的认证规范是AEC 的第一个标准。
AEC-Q-100 于1994 年首次发表,由于符合AEC 规范的零部件均可被上述三家车厂同时采用,促进了零部件制造商交换其产品特性数据的意愿,并推动了汽车零件通用性的实施,使得AEC 标准逐渐成为汽车电子零部件的通用测试规范。
经过10 多年的发展,AEC-Q-100 已经成为汽车电子系统的通用标准。
在AEC-Q-100 之后又陆续制定了针对离散组件的AEC-Q-101 和针对被动组件的AEC-Q-200 等规范,以及AEC-Q001/Q002/Q003/Q004 等指导性原则。
整车EMC正向开发及仿真

整车EMC正向开发及仿真整车开发过程一般包括概念设计、产品开发、产品认证、试生产这些阶段,EMC开发工作贯穿于概念设计至产品认证的整个阶段。
由于电子电气系统既与部件本身相关,又与电气互连网络和工作环境相关,因此EMC开发的任务必须同时着眼于零部件和整车两个层面,包括需求开发、整车设计优化、零部件评估及控制、EMC 整改优化、正式测试、实验室认证及管理这几方面工作内容。
经纬恒润经过十余年与国外OEM的合作以及在国内的本地化实施,提供从测试优化到前期正向开发的全过程技术服务。
针对整车EMC性能开发工作,以实际车型开发为主线,为客户完善整车EMC开发体系,将EMC性能评估工作融入到各个重要的开发节点,从而将整车产品的EMC指标控制分解到整个开发过程中,确保整车开发完成后,将EMC风险问题率降到较低水平。
整车EMC正向开发• 新能源 EMC 标准• 零部件 EMC 风险识别及分级• 整车 EMC 设计评估及优化♦整车电气设计 EMC 分析♦整车线束设计 EMC 分析♦整车结构设计 EMC 分析GL Studio 能够输出高清和超高清的显示图形。
这些图形通过定制的UI 开发专为汽车嵌入式硬件进行优化从而实现很小的启动时间。
仪表盘和抬头显应用程序需要顶级的运行时性能、启动时间和功能安全要求。
GL Studio 提供了可靠的运行时库且通过了功能安全认证。
下一代车载信息娱乐系统显示具有复杂的触摸和手势功能。
GL Studio 能让UI 设计师和软件工程师无缝合作,实现快速迭代。
GL Studio 可以复用IVI、仪表和抬头显的设计资源来快速构建后座娱乐系统、平板电脑以及移动应用程序,保证车载HMI 外观和体验的一致性。
•零部件 EMC 性能管控♦零部件需求及设计约束♦零部件 EMC 方案评估♦零部件 EMC 测试计划审核♦零部件 EMC 试验结果评估•新能源高压系统 EMC 开发♦设计评估及优化♦台架试验及整改整车集成分析及优化• 整车 EMC 试验及整改• 整车自兼容试验EMC仿真•电磁发射仿真•抗干扰性能仿真•自兼容仿真• ESD / 瞬态仿真•虚拟 EMC 试验•射频天线系统仿真服务优势• 技术优势:基于国外OEM技术体系,在国内多年成熟运用,拥近超过20项自主知识产权专利• 人才优势:全职工程师近20人,2/3以上具有博士硕士学历和多年行业经验• 积累优势:深入开展EMC正向开发13年、EMC仿真11年、新能源EMC技术10年• 经验优势:已服务汽车、轨交等领域50多个客户的近百个工程项目• 资源优势:依托经纬恒润代理平台与国外厂商密切合作,拥有完善的工具链和外部技术支持• 产品开发优势:每年完成100+各类汽车电子产品项目的EMC开发,产品经验丰富• 集群优势:经纬恒润在整车电气方面有完整的技术体系,可提供整车电气架构、电气开发、网络、整车测试、EMC等方面的服务,可以相互支持配合,确保项目顺利进行。
基于PMU的小型集成电路测试系统实现及性能分析

基于PMU的小型集成电路测试系统实现及性能分析祝新军;纪效礼;何少佳【摘要】文中给出了一种基于精密测量单元的小型集成电路测试系统的设计方法,并对小功率范围进行详细实验验证;该测试系统将电压/电流钳位技术、比较技术、功率扩展技术、恒流源和恒压源技术和四象限驱动技术等多项技术相结合,能够对被测器件(DUT)施加精确地激励值,并准确测量DUT在激励下的响应,该系统同时具备大功率扩展能力满足多种电路测试的需求;系统借助四通道集成仪表放大器电路,结合嵌入式控制器、功率扩展电路以及上位机控制界面共同完成设计,解决了nA级电流无法准确测量的问题,通过优化补偿电路设计,提高电路测试速度;系统性能分析结果表明,文章所设计的小型集成电路测试系统测量精度高、施加激励稳定可靠、响应速度快,相比类似产品节约2/3的硬件设计成本,能够满足集成电路测试中直流参数测试的要求.【期刊名称】《计算机测量与控制》【年(卷),期】2018(026)004【总页数】4页(P52-55)【关键词】集成电路;精密测量单元;直流参数测试;性能分析;嵌入式【作者】祝新军;纪效礼;何少佳【作者单位】绍兴职业技术学院,浙江绍兴312000;桂林电子科技大学机电工程学院,广西桂林541000;桂林电子科技大学机电工程学院,广西桂林541000【正文语种】中文【中图分类】TM1350 引言随着集成电路集成度的不断提高,集成电路的测试难度不断增大。
目前,主要依赖于集成电路自动测试仪(Automatic Test Equipment)完成集成电路测试。
ATE的测试原理是通过对被测器件(Device Under Test)施加激励和收集响应信号,与DUT的技术手册参数进行比对,从而判断DUT是否合格[1]。
集成电路测试仪主要应用在晶圆测试(中测)和成品测试(成测),文章中的集成电路测试系统针对成测中的直流参数测试进行设计。
从半导体技术的发展情况来看,芯片测试技术落后于芯片的制造速率,高性能的测试仪器价格昂贵,大大提高了电路测试的成本[2]。
汽车电路识图实验实训报告(范文)

汽车电路识图实验实训报告汽车电路识图实验实训报告篇一:汽车电路分析实验报告实验一桑塔纳201X乘用车全车电路认知一、实验目的1. 更好的理解、巩固和掌握汽车全车线路组成及工作原理等有关内容。
2.巩固和加强课堂所学知识,培养实践技能和动手能力,提高分析问题和解决问题的能力和技术创新能力。
二、实验设备全车线路试验台 4台三、实验设备组成全车电线束,仪表盘,各种开关、前后灯光分电路、点火线圈、发动机电脑、传感器、继电器、中央线路板、节气组件、电源、收放机、保险等。
四、组成原理汽车总线路的组成:汽车电器与电子设备总线路,包括电源系统、起动系统、点火系统、照明和信号装置、仪表和显示装置、辅助电器设备等电器设备,以及电子燃油喷射系统、防抱死制动系统、安全气囊系统等电子控制系统。
随着汽车技术的发展,汽车电器设备和电子控制系统的应用日益增多。
五、实验方法与步骤1、汽车线路的特点:汽车电路具有单线、直流、低压和并联等基本特点。
(1)汽车电路通常采用单线制和负搭铁,汽车电路的单线制.通常是指汽车电器设备的正极用导线连接(又称为火线),负极与车架或车身金属部分连接,与车架或车身连接的导线又称为搭铁线。
蓄电池负极搭铁的汽车电路,称为负搭铁。
现代汽车普遍采用负搭铁。
同一汽车的所有电器搭铁极性是一致的。
对于某些电器设备,为了保证其工作的可靠性,提高灵敏度,仍然采用双线制连接方式。
例如,发电机与调节器之间的搭铁线、双线电喇叭、电子控制系统的电控单元、传感器等。
(2)汽车电路采用直流电源,汽车用电设备采用与电源电压一致的直流电器设备。
(3)汽车用电都是低压电源一般为12V、24V,目前有的人提出用42V电源。
个别电器工作信号是高压或不同的电压,如点火系统电路中的高压电路,电控系统各传感器的工作电压、输出信号等。
通用汽车仪表自动化测试系统
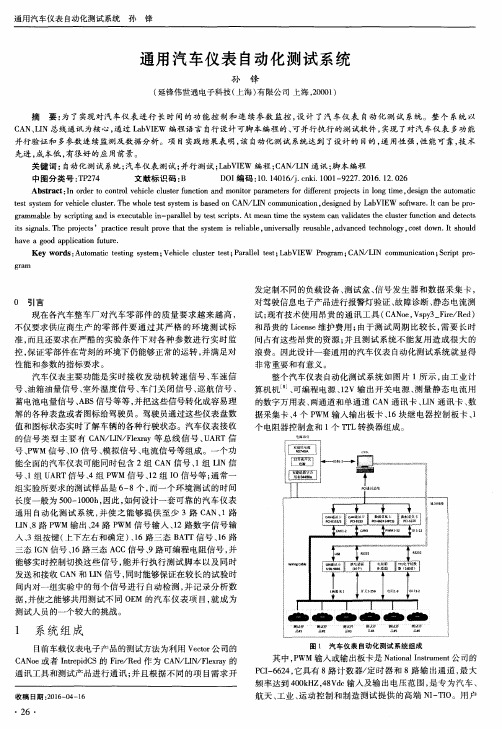
中图分 类号 : T P 2 7 4 文献标 识码 : B D O I 编码 : 1 0 . 1 4 0 1 6 / j . c n k i . 1 0 0 1 — 9 2 2 7 . 2 0 1 6 . 1 2 . 0 2 6
整个 汽 车仪表 自动化 测 试 系统 如 图片 1 所示 , 由工业 计
算机 机 、 可编程 电源 、 1 2 V 输 出开 关 电源 、 测 量 静 态 电 流用
非 常重要 和有 意义 。
现 在各 汽车整 车厂 对 汽 车零 部 件 的质 量 要 求越 来 越 高 , 不仅 要求 供应 商 生 产 的零 部 件 要 通 过 其严 格 的环 境 测 试 标 准, 而且还 要求 在严酷 的实 验条 件 下 对各 种 参 数进 行 实 时 监 控, 保 证零 部件 在苛 刻 的环 境下 仍能够 正 常 的运 转 , 并满 足对 性 能 和参数 的指 标要 求 。 汽车仪表主要功能是实时接收发动机转速信号、 车速信
Ab s t r a c t : I n o r d e r t o c o n t r o l v e h i c l e c l u s t e r f u n c t i o n a n d mo n i t o r p a r a m e t e r s f o r d i f f e r e n t p r o j e c t s i n l o n g t i me , d e s i g n t h e a u t o m a t i c
PLC控制系统在汽车电子仪表中的应用

PLC控制系统在汽车电子仪表中的应用摘要:近年来我国汽车行业的发展速度越来越快,加之电子行业的发展,必须强化电子行业与汽车行业的融合发展。
汽车是由多种不同的仪器设备构成的,其中电子仪表是重要的构成部分。
将汽车技术与电子技术进行集合,有效推动了汽车行业的快速发展。
当前,PLC技术是汽车行业应用最多的电子技术之一。
尤其是电子仪表中。
关键词:PLC控制系统;汽车;电子仪表;应用1PLC介绍PLC是英文ProgrammableLogicController的缩写,其意为可编辑逻辑控制器。
PLC的构成比较复杂,其中主要的部分由CPU、指令及数据内存等。
起初,可编辑逻辑控制只是能够完成简单的编辑逻辑,人们因此为其命名。
近年来人们对可编辑控制器的研究力度在不断增加,使得PLC控制器的功能更加完善,包括逻辑、时序、模拟等模块逐步完善,有效提高了PLC控制器等使用效果。
相比于其他控制器,PLC的抗干扰能力更强,能够适应多种不同的环境,并且还控制器的后期维护与保养比较灵活方便,因此,其应用范围在不断扩大。
2汽车电子仪表分类及功能汽车在设计的过程中使用的电子仪表的种类比较多,其中主要有模拟指针标计、数字表计个综合信息显示表。
结合汽车实际情况选择不同功能属性的电子仪表。
汽车电子仪表在汽车正常使用中发挥着重要的作用,必须在汽车制造的过程中做好电子仪表元器件的设计,从而提高汽车使用的体验感。
3PLC在汽车电子仪表的实践3.1汽车电子仪表的显示随着人们研究力度的提升,汽车仪表的显示功能越来越完善,并且显示的内容正趋于多样化,尤其是汽车的运行状态和汽车运行时各种信息。
这样一来可以为汽车驾驶员提供重要的信息,提高汽车出行的安全性。
数字表是当前汽车仪表的主要原则,这种仪表的数字更新比较快,能够更好的反应汽车的状态。
常用的汽车电子仪表显示单元有很多部分构成中,主要是固定显示部分个可选显示部分。
固定显示仪表主要显示汽车内部水温、油表个转速表等,这些是大部分汽车电子仪表必须的功能。
组合仪表培训讲义

安全注意事项
遵守安全操作规程
在安装和调试组合仪表时,应 遵守相关安全操作规程,确保
人员安全。
断电操作
在进行与电源相关的操作时, 应先断开电源,避免短路或电 击事故。
防震防潮
在安装和调试过程中,应采取 措施防止组合仪表受到剧烈震 动或潮湿环境的影响。
保护线路
在连接线路时,应确保线路不 被挤压或过度弯曲,以防损坏
检查仪表盘的线路是否老化、破损或松动,如有 需要更换或紧固。
更换灯泡
如仪表盘上有灯泡,定期检查并更换损坏的灯泡。
常见故障排除
显示屏不亮
检查线路是否连接良好,灯泡是否损坏,如有问题及时更换。
指针不工作
检查传感器是否正常,线路连接是否牢固,如有问题及时修复。
报警灯常亮
检查报警灯电路是否正常,传感器是否损坏,如有问题及时更换。
THANKS FOR WATCHING
感谢您的观看
5G通信技术
利用5G高速、低延迟的通信特性,实现组合仪表数据的实时传输和 处理。
物联网技术
通过物联网技术,实现组合仪表与车辆其他系统的互联互通,提升信 息共享和协同工作能力。
应用领域拓展
智能交通
组合仪表在智能交通领域的应用,如实时路况显示、交通信号优 化等。
自动驾驶
随着自动驾驶技术的发展,组合仪表将作为人机交互的重要界面, 提供丰富的驾驶信息和辅助决策功能。
工业控制仪表通常包括温度计、压力计、 工业控制仪表的发展趋势是智能化和网
流量计、液位计、振动监测仪等,通过 络化,能够实现远程监控和自动控制,
这些仪表,操作员可以实时了解生产设
提高生产效率和安全性。
备的运行状态和工艺参数。
06 组合仪表的未来展望
汽车智能仪表盘设计

课题介绍.............................................................产品调研.......................................................... 分析研究......................................................... 设计构思........................................................ 设计展开....................................................... 使用说明.......................................................汽车仪表盘是人们日常生活中必不可少的工具。
现在市场上销售的种类多种多样,五花八门。
但是,其中不乏很多不好的设计,更有很多不符合人机工程学。
通过调研,分析,探讨。
实践,我们可以发现汽车仪表设计中存在的各种问题,并找出好的方法将之优化或解决。
汽车智能仪表盘设计摘要:智能仪表日益广泛地应用在工业自动化领域,随着生产自动化要求的不断提高,对智能仪表的设计提出了更高的要求。
从智能仪表的概念及其发展现状出发,分析智能仪表的组成部分,并对智能仪表的设计过程和技术进行探讨。
关键词:智能仪表;技术;设计1.智能仪表的概念及其发展现状工业自动化仪表是用以实现信息的获取、传输、变换、存储、处理与分析,并根据处理结果对生产过程进行控制的重要技术工具。
其中包括检测仪表、分析仪表、执行与控制仪表、记录仪表等几大类,也有将几部分功能集成在一起的仪表,是工业控制领域的基础和核心之一。
微型计算机技术和嵌入式系统的迅速发展,引起了仪器仪表结构的根本性变革,即以微型计算机为主体,代替传统仪表的常规电子线路,成为新一代具有某种智能的灵巧仪表。
乘用车电子组合仪表技术条件

ISO 11452-2-2004道路车辆-窄带辐射电磁能量产生的电骚扰-零部件试验方法-第二部分:电波暗室(Electrical disturbances by narrowband radiated electromagnetic energy – component test methods Part 2-Absorber-lined shielded enclosure)
ISO 11452-4-2005道路车辆-窄带辐射电磁能量产生的电骚扰-零部件试验方法-第四部分:大电流注入(BCI)(Electrical disturbances by narrowband radiated electromagnetic energy – component test methods-Part 4:Bulk current injection (BCI))
对于数字式车速表,当速度平稳变化时其显示应相应变化,数字在跳动过程中的保留时间为1±0.2s,在任意恒定的速度下,车速表显示值的变化不得超过1km/h。
转速表
当转速平稳变化时,电子转速表指针运动应平稳,不得有呆卡或卡滞现象。在恒定转速下,在1400rpm~5600rpm的速度范围内,指针摆动范围应在±70rpm以内,当转速有变化时,指针在1s内指示到新的状态。
g)信号灯点亮时,组合仪表上各种指示信号、符号、图案及颜色应清晰完整,无窜光现象;
h)组合仪表在不工作时,电子车速表、电子转速表、燃油表和发动机温度表指针应位于零分度上;
i)试验后应无明显外观缺陷产生。
故障自诊断系统

• 第四部分为两个数字的组合,是制造厂的原故障 代码。
•
通用故障码与扩展故障码
• 扩展故障码较通用故障码提供的故障信息 更为具体些,诊断的针对性更强些。用于 表示通用型故障码未涵盖的故障及ABS、 ASR等发动机管理系统之外的故障,数据 流也是如此。
•
(1)具有统一的16端子诊断插座 • OBD-Ⅱ标准规定,各种车型的OBD-Ⅱ应具
有统一尺寸和16端子的诊断插座,OBD-Ⅱ 标准对诊断插座中的各个端子也作了相应的 规定,该诊断插座应位于汽车的客舱内并置 于驾驶座上的人伸手可及之处。
•
OBDII诊断
座
• 在16个端子中,其中7个是标准定义的信号端子,其 余9个由生产厂家自行设定,大部分的系统只用7个 端子中的5个具体定义好的端子,第7号和第15号端 子是ISO1994-2标准传送资料的,而第2和第10号脚 是SAEJ-1850标准。
• 数字显示:故障码直接以数字的形式显示 在汽车组合仪表的信息显示屏上(一般在 温度显示屏。
• 外接仪表显示。
•
•4.4.2 第二代故障自诊断系统 (OBD-Ⅱ)
•
•OBD简介
• OBD是On Board Diagnostic的缩写, 即随车故障诊断系统。
• OBD系统的设计初衷是为了监测排气 管废气排放质量,在排放系统有故障 时提示车主注意,使维修技术人员快 速的找到故障来源,减少汽车废气对 大气污染。后来,逐步发展成为用于 进行电控系统故障诊断。
• 例如,发动机水温传感器发生故障时,ECU将启 用代用值固定为80℃;进气温度传感器发生故障 时,可将进气温度设定为22℃。
• 或者,ECU另用与其工作性质相关器件的信号参 数值代用。例如,进气流量传感器损坏后,ECU 则用节气门位置传感器的信号参数值来代用。
第一章 汽车车速表检测

第二篇汽车检测设备及运用技术第一章汽车车速表检测汽车的行驶速度关系到行车安全与运输生产率。
为了提高汽车运输生产率,应发挥车辆性能所能提供的尽量高的车速,但车速过高超过了汽车性能所允许的界限往往会使汽车失去操纵稳定性与制动距离过长,影响行车安全。
此外车辆的行驶速度还受交通情况与道路条件,以及着眼于经济成本的经济车速的限制。
所以在驾驶汽车时合理地运用、准确地掌握行车速度,对行车安全与高效运用车辆有着重要意义。
第一节车速表检验台结构与工作原理一、车速表检验台的结构车速表检验台按有无驱动装置可分标准型与电机驱动型两种。
标准型检验台无驱动装置,它靠被测汽车驱动轮带动滚筒旋转;电机驱动型检验台由电动机驱动滚筒旋转,再由滚筒带动车轮旋转。
此外,还有把车速表检验台与制动检验台或底盘测功机组合在一起的综合式检验台。
目前,检测站使用最多的是标准型滚筒式车速表检验台。
1.标准型车速表检验台该检验台主要由滚筒、举升器、测量装置、显示仪表及辅助装置等几部分组成,主要结构见图2-1-1。
图2-1-1 车速表检验台结构示意图(1)滚筒部分检验台左右各有两根滚筒,用于支撑汽车的驱动轮。
在测试过程中,为防止汽车的差速器起作用而造成左右驱动轮转速不等,前面的两根滚筒是用联轴器联在一起的。
滚筒多为钢制,表面有防滑材料,直径多在175~370mm之间,为了标定时换算方便直径多为176.8mm,这样滚筒转速为1200r/min时,正好对应滚筒表面的线速度为40km/h。
(2)举升器举升器置于前后两根滚筒之间,多为气动装置,也有液压驱动和电机驱动的。
测试时,举升器处于下方,以便滚筒支撑车轮。
测试前,举升器处于上方,以便汽车驶上检验台,测试后,靠气压(或液压、电机)升起举升器,顶起车轮,以便汽车驶离检验台。
(3)测量元件即测量转速的传感器。
其作用是测量滚筒的转动速度。
通过转速传感器将滚筒的速度转变成电信号(模拟信号或脉冲信号),再送到显示仪表。
奥迪A6L车型仪表故障的检测及排除方法
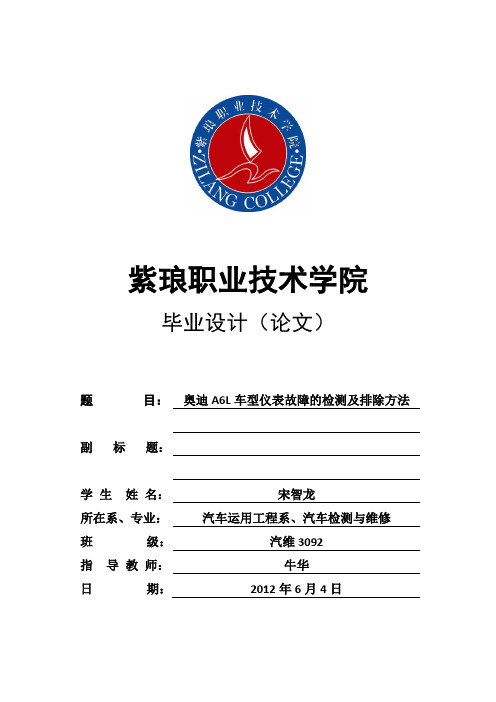
紫琅职业技术学院毕业设计(论文)题目:奥迪A6L车型仪表故障的检测及排除方法副标题:***名:***所在系、专业:汽车运用工程系、汽车检测与维修班级:汽维3092***师:**日期:2012年6月4日自从1999年奥迪A6正式国产以来,奥迪A6便开创了国内中大型车市场的新局面,不到5年的时间里销售达20多万辆,特别是2005推出的全新加长版车型奥迪A6L车型令其拥有了国内中大型车级别的霸主地位。
随着世界电子技术的迅猛发展,奥迪A6L仪表盘智能化、电子化已成为仪表发展的必然趋势。
多功能高灵敏度、高精度、读数直观的电子数字显示及图像显示的仪表已奥迪车系中应用,汽车电子化仪表已取代常规的机电仪表。
关键词:仪表奥迪指示灯电子Since the 1999Audi A6formal domestic since, Audi A6will open up the domestic medium and large car market a new situation, less than 5 years of sales reached about 200000 vehicles, especially the 2005launched a new extended version of Audi A6L models to have the domestic medium and large car level overlord position.With the rapid development of electronic technology, Audi A6L dashboard intelligent electronic instrument, has become the inevitable trend of the development of. Multi function high sensitivity, high precision, visual reading electronic digital display and image display devices have been Audi applications, automotive electronic devices have replaced conventional electrical instrument.Keywords:Instrument;Audi; Indicator lamp; Electronics摘要........................................................................................................ 错误!未定义书签。
基于Labview的汽车仪表模拟实现
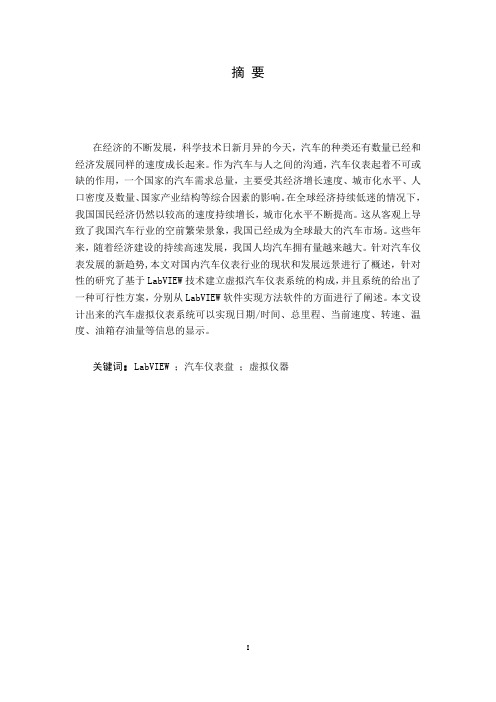
摘要在经济的不断发展,科学技术日新月异的今天,汽车的种类还有数量已经和经济发展同样的速度成长起来。
作为汽车与人之间的沟通,汽车仪表起着不可或缺的作用,一个国家的汽车需求总量,主要受其经济增长速度、城市化水平、人口密度及数量、国家产业结构等综合因素的影响。
在全球经济持续低迷的情况下,我国国民经济仍然以较高的速度持续增长,城市化水平不断提高。
这从客观上导致了我国汽车行业的空前繁荣景象,我国已经成为全球最大的汽车市场。
这些年来,随着经济建设的持续高速发展,我国人均汽车拥有量越来越大。
针对汽车仪表发展的新趋势,本文对国内汽车仪表行业的现状和发展远景进行了概述,针对性的研究了基于LabVIEW技术建立虚拟汽车仪表系统的构成,并且系统的给出了一种可行性方案,分别从LabVIEW软件实现方法软件的方面进行了阐述。
本文设计出来的汽车虚拟仪表系统可以实现日期/时间、总里程、当前速度、转速、温度、油箱存油量等信息的显示。
关键词:LabVIEW ;汽车仪表盘;虚拟仪器ABSTRACTIn the development of economy, science and technology change rapidly today, car type and number and same speed up economic development. As between the car and the human communication, automobile instrument plays an indispensable role, total demand of a country, is mainly influenced by the factors of the economic growth rate, the level of city, population density and the number of national industry structure, etc.. In the global economic downturn, China's national economy continues to grow with high rate, continuously improve the level of city. This led to China's automobile industry an unprecedented prosperity from the objective, China has become the world's largest car market. These years, with the sustained and rapid development of economic construction, China's per capita automobile more and more. The new trend for the development of the automobile instrument, vision status and development of the domestic automobile instrument industry were summarized, based on the establishment of virtual instrument technology LabVIEW system based on the study, and the system provides a feasible scheme, are described respectively, realization method of software LabVIEW software from the aspects of. Virtual instrument system this paper designed can display date / time, mileage, current speed, speed, temperature, fuel oil and other informationKey words LabVIEW;Car dashboard;virtual instrument目录1 引言 (1)2 研究的目的、意义以及主要内容 (2)2.1 研究的目的和意义 (2)2.2 研究的主要内容 (2)3 汽车仪表盘系统功能分析 (3)3.1 车速表 (3)3.2 里程表 (3)3.3 燃油表 (3)3.4 转速表 (3)3.5 温度表 (3)3.6 左右转向灯 (4)3.7 时间 (4)4 车辆虚拟仪表系统 (5)4.1 虚拟仪表系统的优势 (5)4.2 虚拟仪表系统的实现步骤 (5)4.2.1 信号采集与处理 (5)4.2.2 仪表盘输出 (5)5 系统软件介绍 (6)5.1 界面模块 (6)5.2 LabVIEW编程环境 (7)5.3 设计程序构想思路 (8)5.3.2 前面板和程序框图 (8)5.3.3 控件选板 (9)5.3.4 函数选板 (10)5.3.5 设计思路 (10)6 各功能模块程序功能测试 (12)6.1 车速表模块 (12)6.2 发动机转速表模块 (13)6.3 燃油表的模块 (14)6.4 温度表的模块 (15)6.5 时间显示模块 (16)6.6 左右转向灯模块 (16)7 设计总结 (18)7.1 程序调试步骤 (18)7.2 程序结果图见附录B (18)7.3 结果分析 (18)结束语 (19)参考文献 (20)致谢 (22)附录A 前面板图 (23)附录B 程序框图 (24)附录C档位油门提升车速发动机转速提升 (25)附录D右转时档位油门下降车速发动机转速下降 (26)1 引言汽车仪表是驾驶员与汽车进行信息交流的窗口,也是汽车高尖技术的主要部分,各个国家一直在努力开发汽车仪表技术,并不断取得新的进展。
汽车电子产品ECU测试方法
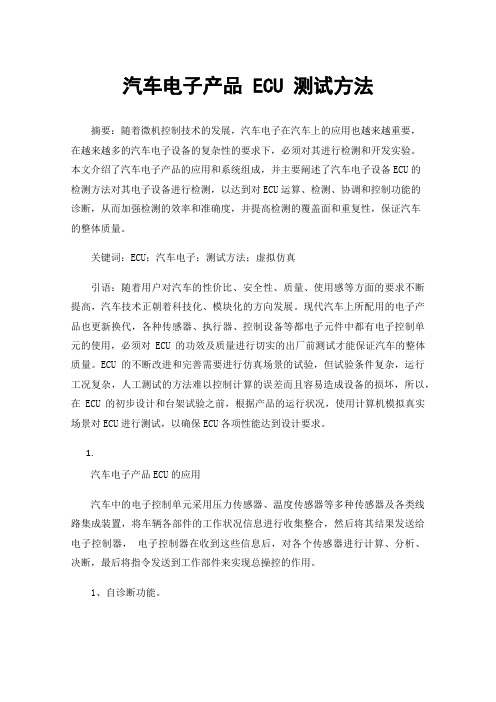
汽车电子产品 ECU 测试方法摘要:随着微机控制技术的发展,汽车电子在汽车上的应用也越来越重要,在越来越多的汽车电子设备的复杂性的要求下,必须对其进行检测和开发实验。
本文介绍了汽车电子产品的应用和系统组成,并主要阐述了汽车电子设备ECU的检测方法对其电子设备进行检测,以达到对ECU运算、检测、协调和控制功能的诊断,从而加强检测的效率和准确度,并提高检测的覆盖面和重复性,保证汽车的整体质量。
关键词:ECU;汽车电子;测试方法;虚拟仿真引语:随着用户对汽车的性价比、安全性、质量、使用感等方面的要求不断提高,汽车技术正朝着科技化、模块化的方向发展。
现代汽车上所配用的电子产品也更新换代,各种传感器、执行器、控制设备等都电子元件中都有电子控制单元的使用,必须对ECU的功效及质量进行切实的出厂前测试才能保证汽车的整体质量。
ECU的不断改进和完善需要进行仿真场景的试验,但试验条件复杂,运行工况复杂,人工测试的方法难以控制计算的误差而且容易造成设备的损坏,所以,在ECU的初步设计和台架试验之前,根据产品的运行状况,使用计算机模拟真实场景对ECU进行测试,以确保ECU各项性能达到设计要求。
1.汽车电子产品ECU的应用汽车中的电子控制单元采用压力传感器、温度传感器等多种传感器及各类线路集成装置,将车辆各部件的工作状况信息进行收集整合,然后将其结果发送给电子控制器,电子控制器在收到这些信息后,对各个传感器进行计算、分析、决断,最后将指令发送到工作部件来实现总操控的作用。
1、自诊断功能。
ECU通常具有故障自诊断与保护的能力,在发生故障时,可以将故障码存入存储器,并通过保护机制,从上面所描述的固有程式中读出替换程式,以保持引擎正常工作。
同时,这些故障信息也会在仪表板上实时显示,让用户能够及时地发现问题并把车送到维修中心,由维修人员通过专用的仪器读取,从而更好地解决问题。
2、自适应功能。
ECU拥有自动学习功能,能够自动检测到驾驶员的驾驶状态,然后根据驾驶员的日常行为进行相应的调整。
中国汽车emc测试标准

中国汽车emc测试标准EMC测试是汽车整车或零部件开发过程中常常涉及到的测试内容,EMC测试的主要目的是确保车辆或零部件在其工作的电磁环境中能够不受影响正常工作,同时也不对其他部件或系统造成电磁干扰。
EMC测试一般可分为电磁骚扰测试EMI(Electro-Magnetic Interference)和电磁抗扰测试EMS (Electro-Magnetic Susceptibility)两大类,前者确保不影响其他设备,后者确保不被其他设备影响。
了解EMC的各项测试最关键的地方就在于确认三要素:干扰源、敏感设备、以及耦合路径。
汽车EMC测试包含哪些方面?都有哪些测试标准?汽车EMC测试是测量汽车及其组件的电磁兼容性(EMC)的过程,从汽车收音机到引擎的每个零件都需要进行测试,以查看其电磁场如何相互作用,并确定是否有任何零件会产生电磁干扰(EMI)。
随着汽车射频设计变得越来越复杂,制造商将4G,WiFi和蓝牙技术集成到汽车中,EMC测试现在比以往任何时候都更加重要,诸如电动汽车和自动驾驶汽车等新兴市场也为这种设计复杂性的增长做出了贡献。
仪表板中充满了活动组件,当它们与控制系统相互通信时,它们会产生RF噪声和辐射以及潜在的EMI源。
符合EMC标准是现代汽车制造的支柱,对乘客安全至关重要。
汽车需要同时进行EMI抗扰度和EMI辐射水平的EMC测试,该测试又分为四个不同的种类:辐射发射,传导发射,辐射抗扰度和传导抗扰度测试。
汽车EMC测试包含哪些方面?一般整车需要做以下测试,跟零部件EMC测试类似,也包括发射测试(EMI)和抗干扰测试(EMS),对于某些整车厂还有主观收音评价测试。
抗扰性测试抗扰性测试将确定有源通信组件(包括安装在控制和娱乐系统中的微处理器)的辐射敏感性和传导敏感性。
电路设计是屏蔽EMI的重要因素之一,并且布线可能直接导致EMI或影响EMC路径。
排放测试汽车排放测试的重点是测量宽带和窄带辐射产生的EMI,宽带EMI 发生在点火组件和其他易于“起弧和火花”的零件中,从而产生宽带辐射,汽车中的有源电子设备(例如电动机)会产生窄带辐射。
汽车电子控制系统检测诊断--汽车电子控制技术

3.3 故障代码
(1) 故障代码的组成
SAE规定OBD—II故障代码有5位组成。
第1个是英文字母,代表测试系统,如: B——车身(BODY); C——底盘(CHASSIS); P——发动机、变速器(POWER TRAIN); U——未定义,由SAE另行发布。 第2个到第5个为数字码。 每一个代码均有特殊含义。例如,故障代码 P1352可表示如下含义: P——代表测试系统,在此表示发动机和变速器; 1——代表汽车制造商; 3——代表SAE定义的故障代码范围; 52——代表原厂故障代码。
当自诊断系统发现某只传感器或执行器发生故障时,电控单元 ECU会将监测到的故障内容以故障代码的形式存储在随机存 储器RAM中。只要存储器电源不被切断,故障代码就会一直 保存在RAM存储器中。
即使是汽车在运行中偶尔出现一次故障,自诊断电路也会及 时检测到并记录下来。在控制系统的电路上,设有一个专用 诊断插座,在诊断排除故障或需要了解控制系统的运行参数 时,使用汽车制造商提供的专用检测仪或通过特定操作方法, 就可通过故障诊断插座将存储器中的故障代码和有关参数读 出,为查找故障部位、了解系统运行情况和改进控制系统设 计提供依据。
将故障检测仪、调码器或跨接线等自诊断测试工具与汽车上的 诊断插座连接后,接通点火开关,即可触发自诊断系统进行诊 断测试。根据读取的故障代码查阅被测车型的《维修手册》, 就可知道故障代码表示的故障内容与故障原因。
诊 断 插 座 ( TDCL ) 是 故 障 诊 断 通 讯 接 口 ( Trouble Diagnostic Communication Link)的简称。在装备电子控 制系统的汽车上,都设有诊断插座,一般安装在熔断器盒上、 仪表盘下方或发动机舱内。
根据发动机运转状态和传输数据的变化情况,即可判断控制系 统的工作状态,将特定工况下的传输数据与标准数据进行比较, 就能准确判断故障类型和故障部位。
汽车检测与诊断-故障自诊断

④用读码器、故障诊断仪、扫描仪、示波器、专用检测
仪等仪器进入故障自诊断系统并读取故障码。
(3)故障码的显示方式(人工读码方法)
1) 脉冲电压显示
利用仪表板上的发动机故障警告灯的闪烁规律显示。 ①找出发动机附近或仪表板下方的故障诊断插座; ②用一根导线跨接故障诊断插孔与接地插孔; ③观察仪表板上的发动机故障警告灯的闪烁规律与次数, 就可以读取故障码。 不同车型的故障诊断插座的形状和插孔位置不同,但读 取方法基本相同。 几乎所有电控汽油喷射发动机均可以故障警告灯的闪烁 规律读取故障码。
自诊断系统都可以显示标准OBD-Ⅱ故障码“P0125”、
“P0204”,分别代表有转速信号时发动机5min内没达到 10℃和4号喷油嘴输出驱动器不正确的响应控制信号。
二、基于OBD—Ⅱ的电子控制汽油喷射系统故障自诊
断方法 1、 OBD—Ⅱ系统的监测机制 OBD—Ⅱ系统以相应的程序管理监测诊断过程,每个 监测过程必须在特定的发动机温度、发动机转速和负荷、节 气门开度、发动机起动后运行时间等运行条件下完成。 诊断管理程序确定故障诊断检测的次序,当正确的运
(3)执行器的故障自诊断工作原理
如果执行器出现了问题,监视程序把故障信息传输给
ECU,ECU做出故障显示、故障存储,并采取应急措施, 确保发动机维持运转。 注意:自诊断系统对于偶尔出现一次的不正常信号, 并不判定为故障,只有不正常信号保持一定时间后才被视
为故障。
3、自诊断测试
(1)自诊断系统的输出接口 ①发动机警告灯、超速档警告灯或ABS指示灯 电控系统利用警告灯或指示灯作为其有无故障的信号灯。 ②电控系统检测插座( CHECK CONNECTOR)
行条件具备时,决定检测的持续时间。
如果条件和时间不满足要求,管理软件将等待时机运行 适当的监测诊断程序。
基于I.MX6的汽车液晶仪表视频模块的设计与实现

第43卷第1期2020年2月电子器件ChineseJournalofElectronDevicesVol 43㊀No 1Feb.2020项目来源:武汉科技大学2018-2019学年度大学生科技创新基金研究项目(18ZZA117)收稿日期:2019-03-13㊀㊀修改日期:2019-06-26DesignandImplementationofAutomotiveLiquidCrystalInstrumentVideoModuleBasedonI.MX6∗GUOJianzhong1ꎬCHENDian1ꎬMINRui2∗ꎬWANGXilin2(1.VehicleEngineeringDepartmentꎬWuhanUniversityofScienceandTechnologyꎬWuhan430065ꎬChinaꎻ2.WuhanBaohuaLCDDisplayTechnologyCo.ꎬLtdꎬWuhan430082ꎬChina)Abstract:Toimprovethereliabilityofvideomoduleinautomobileinstrumentꎬadecodingstrategywasdesignedtopreventparsingfailure.Bydesigningimpedancematchingcircuitandoptimizingdecodingstrategyꎬvideomoduleofautomobileliquidcrystalinstrumentisrealized.Testanalysisshowsthatthedecodingsuccessrateofvideomoduleis100%ꎬwhichimprovesthereliabilityofvideomodule.Theresultsshowthatthemodulecandecodeanddisplaythevideostreamthatcannotbedecodedbytraditionalalgorithmꎬwhichreducestheriskofinstrumentdevelopmentandconformstothemarketdevelopmenttrend.Keywords:automobileliquidcrystalinstrumentꎻvideostreamdecodingꎻdesignandimplementationꎻreliabilityEEACC:7260F㊀㊀㊀㊀doi:10.3969/j.issn.1005-9490.2020.01.023基于I.MX6的汽车液晶仪表视频模块的设计与实现∗郭健忠1ꎬ陈㊀典1ꎬ闵㊀锐2∗ꎬ汪喜林2(1.武汉科技大学汽车与交通工程学院ꎬ武汉430065ꎻ2.武汉保华显示科技有限公司ꎬ武汉430082)摘㊀要:为提高视频模块在汽车仪表中应用的可靠性ꎬ设计了一种防解析失败的解码策略ꎮ通过设计阻抗匹配电路ꎬ优化解码策略ꎬ实现了汽车液晶仪表视频模块ꎮ测试分析发现ꎬ该视频模块的解码成功率100%ꎬ提升了视频模块的可靠性ꎮ结果表明ꎬ该模块可解码显示传统算法无法解码的视频流ꎬ降低了仪表开发的风险ꎬ符合市场发展趋势ꎮ关键词:汽车液晶仪表ꎻ视频模块ꎻ视频流解码ꎻ设计实现ꎻ可靠性中图分类号:TH85㊀㊀㊀㊀文献标识码:A㊀㊀㊀㊀文章编号:1005-9490(2020)01-0114-05㊀㊀汽车电子技术的创新带动了整个汽车行业的快速发展ꎬ汽车对仪表的性能要求越来越高[1]ꎮ液晶仪表作为汽车电子化的集中体现ꎬ是汽车电子系统中的重要节点ꎬ反馈了汽车大部分传感器的运行信息[2-3]ꎮ随着仪表功能需求的提升ꎬ用户希望仪表和中央控制器能够实现互联互控ꎮ要实现这些功能ꎬ势必增加UI资源ꎬ资源的内存占比增加到一定程度后势必会资源溢出ꎬ严重影响仪表的用户体验ꎬ因此ꎬ缩减资源占比势在必行ꎮ视频模块在保证功能实现的前提下ꎬ可大量缩减资源占用的内存ꎬ从而成为仪表研究热点[4-5]ꎮ目前ꎬ仪表视频模块除了支持摄像头实时采集显示外ꎬ还需要支持视频流的解码显示ꎮ视频模块的解码与视频流的格式和解码标识符有关ꎬ实际过程中视频流来源广ꎬ部分视频流格式无法被I.MX6传统解码算法识别ꎬ导致解码失败ꎻ同时ꎬ不同编码算法可能生成相同格式但标识符不同的视频流ꎬ当解码算法与视频流标识符无法成功匹配时ꎬ也会导致解码失败ꎮ这些问题严重影响了系统的可靠性ꎬ因此有必要设计一种稳定的汽车液晶仪表视频模块ꎮ1㊀液晶仪表整体框架汽车液晶仪表遵循模块化开发原则ꎬ系统组成包括CAN模块ꎬMCU模块ꎬ电源模块ꎬ背光及LED模块ꎬGPU图像处理模块等ꎮ基于I.MX6平台的仪表系统硬件拓扑如图1所示ꎬ系统设计了两种不同来源的视频流显示构架ꎬ包括摄像头采集的视频实时显示和仪表共享内存的视频流显示ꎮ当视频流信号输入时ꎬ信号调理电路接收到输入信号ꎬ会触发MCU处理器控制电源模块和背光模块的工作ꎮ第1期郭健忠ꎬ陈㊀典等:基于I.MX6的汽车液晶仪表视频模块的设计与实现㊀㊀图1㊀液晶仪表整体框架示意图2㊀仪表视频模块的硬件设计视频模块硬件主要包括电源模块ꎬ视频接收模块和接口模块ꎮ视频模块正常工作前ꎬ需先确认视频的来源ꎮ视频的来源主要有两种ꎬ一种是摄像头实时采集的视频数据ꎬ完成显示即释放ꎬ无需解码处理ꎻ另一种是仪表内部存储的经压缩编码的视频流ꎬ显示前需解码ꎮ当视频信号通过CVBS接口输入时ꎬ需经ADV7180对接收的视频模数转换ꎬ转换完成后无需解码即可实时显示ꎻ当视频以AVI格式经由MIPI接口输入时ꎬ信号经处理器解码模块解码后显示ꎮ图2㊀仪表系统的视频模块设计图2.1㊀电源模块电源模块由两部分构成:第1部分是集成电源输入电路ꎬ主要由线性调制器稳压电源转换组成[6]ꎮ视频模块电压由外部输入ꎬ采用标准5V电压ꎬ当需要其他低电压时ꎬ通过转换电路将电压转换至3.3Vꎻ第2部分为输入过流保护电路ꎬ仪表内部稳压环路出现故障引起输出过流时ꎬ熔断保护元件ꎬ防止因电流过高损坏仪表后续元件ꎮ由于汽车提供仪表的电压输入电路独立ꎬ视频模块无需担心电压过大ꎬ但仪表上下电时ꎬ可能造成过流损坏仪表ꎮ故设计了过流保护电路如图3所示ꎬ当输入电流过高时ꎬPUSEI管熔断ꎬ阻止电流进入后级电路ꎬ从而保护仪表板ꎮ2.2㊀视频接收模块接收AVI视频流的输入信号时ꎬ系统检测电平信号ꎬ配置视频流源的输入格式[7-9]ꎮ视频流通过MIPI接口传输至处理器ꎬ由GPU处理单元进行图像处理ꎮ图3㊀电源模块电路图接收摄像头采集的视频流源输入信号时ꎬ接收端口获取模拟的视频数据ꎬ通过AIN引脚输入至ADV7180芯片进行模数转换ꎬ模拟信号转换至数字信号后ꎬ由Video_P引脚输出至GPU处理器进行图像处理ꎮ为了提升视频信号质量ꎬ在接收端口处设计如图4所示电阻电路ꎬ通过该电路实现阻抗匹配处理ꎬ保证线上阻抗达到75Ωꎬ以便滤除线材上的反射干扰ꎮ图4㊀阻抗匹配电路图2.3㊀接口模块基于I.MX6平台设计的汽车液晶仪表ꎬ集成ARMA9内核处理器ꎬ支持3D视频投放ꎬ完全兼容H.264ꎬAVꎬMPEG-4等编解码格式ꎬ支持最全高清1920ˑ1080的每秒30帧的图像解码[10]ꎮI.MX6仪表开发平台支持MIPI接口㊁HDMI接口㊁CVBS接口㊁显示接口㊁摄像传感器接口等一系列接口ꎮ目前仪表开发过程中采用MIPI接口实现视频流的传输ꎮ相较511电㊀子㊀器㊀件第43卷HDMI接口ꎬMIPI传输线数少ꎬ支持移动数据处理和低功率高速率传输ꎬ缩减成本的同时可实现视频模块的功能ꎬ故更适合做视频模块的数据传输接口ꎮ针对解码ꎬI.MX6平台提供了API接口ꎬ只需将执行的命令以及数据结构提供给函数ꎬ就能调用VPU解码模块实现视频流的解码ꎮ3㊀仪表视频模块的软件设计基于I.MX6平台搭建的仪表视频模块软件部分主要由视频识别初始化ꎬ仪表及视频流信息设置ꎬ防解析失败解码设置3部分组成ꎮ液晶仪表视频模块的软件流程如图5所示ꎬ视频模块嵌入到仪表系统ꎬ启动软件对系统进行初始化自检ꎬ检测完成后通过引脚高低电平判断视频流的格式ꎬ若视频流通过CVBS接口输入ꎬ经模数转换子模块转换后ꎬ输出到仪表显示ꎻ若视频流通过MIPI接口输入ꎬ需检测视频流的标识IDꎬ调用处理器解码模块ꎬ启动防解析失败解码程序解码视频流ꎬ解码完成后输出到仪表显示ꎮ图5㊀仪表视频模块软件设计流程图3.1㊀视频识别初始化定义无信号输入的状态为video_free状态ꎬ此为默认状态ꎬ输出基础信号ꎮ摄像头采集信号输入的状态为video_in状态ꎬ摄像头采集信号输出的状态为video_run状态ꎮ当VideoMode=0时ꎬ定义视频流格式输入ꎬvideo_free状态切换到video_run状态ꎬ视频流输入完成后ꎬ切换到video_free状态ꎻ当VideoMode=1时ꎬ定义CVBS格式输入ꎬvideo_free状态切换到video_in状态ꎬ对输入模拟信号进行数字信号转换ꎬ转换成功后恢复至初始状态ꎮ3.2㊀仪表及视频流信息设置启动视频模块初始化程序后ꎬ获取IO接口及仪表内核版本信息ꎬ设置仪表属性ꎬ通过mmap函数复制视频流数据到指定地址ꎬ使视频流能被搜索读取ꎻ设置解码物理缓冲区和虚拟缓冲区ꎬ读取仪表固件版本信息ꎬ并对比仪表内核库版本信息ꎬ完成视频模块初始化ꎮ视频流经编码算法处理后生成特定格式标识符ꎬ通过标识符匹配对应解码算法实现视频流的解码ꎮ获取视频流的解码结构后ꎬ将视频流指定到解码空间中ꎬ读取视频流的标识符ꎬ通过decode_open函数获取视频流解码参数ꎬ结合仪表版本信息ꎬ将参数指定给decoder_parse函数ꎬ进行解码参数的配置ꎮ图6㊀传统解码算法流程图3.3㊀防解析失败解码设置若非摄像头采集视频ꎬ共享内存的视频流需要解码才能显示ꎮ支持3D投射的I.MX6仪表对视频要求非常高ꎬ传统的视频流解码算法如图6所示[11-13]ꎮ由于视频流的编解码对算法有要求ꎬ且支持视频流编解码的算法不唯一ꎬ导致视频解码难度增加ꎮ研究测试发现ꎬ传统的解码算法会出现3种情况导致视频流无法解码播放ꎮ视频流的编码格式不在解码程序的解码格式中ꎬ无法进行解码ꎻ视频流解码格式成功匹配ꎬ同时能够成功解析ꎬ但是无法解码播放ꎻ视频流格式成功匹配ꎬ但是视频流编解码算法不一致ꎬ导致视频流解析失败ꎮ为解决以上3种情况可能对仪表造成死机的影响ꎬ设计了如图7所示防解析失败解码策略ꎬ当获取的视频格式无法进行解码ꎬ或者视频流解码成功仍无法显示时ꎬ本算法对视频流进行格式转换ꎬ转换后的视频流可以被算法识别进行解码ꎮ为满足仪表高分高清等技术要求ꎬ将视频流重新编码成AVI格式ꎬ通611第1期郭健忠ꎬ陈㊀典等:基于I.MX6的汽车液晶仪表视频模块的设计与实现㊀㊀过防解析失败解码算法处理的AVI视频流ꎬ能够在仪表中解码显示ꎮ当视频流编解码算法不一致ꎬ导致AVI视频流解析失败无法解码播放时ꎬ通过本解码算法将解析失败的视频流转换成H.264编码的AVI格式视频流ꎬ转换后视频流可以成功地解析解码ꎮ图7㊀视频模块防解析失败解码算法流程图4㊀视频模块功能测试分析及应用为验证视频模块能否进行基于仪表的摄像头实时采集显示以及防解析失败视频解码显示ꎬ能否嵌入I.MX6仪表平台正常实现功能以及相较于传统算法而言防解析失败算法的优势所在ꎬ对视频模块进行了功能测试和分析ꎬ并将其嵌入到了汽车液晶仪表上ꎮ4.1㊀仪表视频模块功能测试连接PCB板并启动内核ꎬ通过SecureCRT工具进行系统操作ꎬ分别对摄像头实时采集显示功能和视频流解码显示功能进行了测试ꎮ对摄像头实时采集显示功能进行测试ꎬ连接摄像头至仪表测试板ꎬ运行可执行程序后ꎬ在外接显示屏上可观察实时显示数据ꎬ如图8(a)所示ꎻ对视频流解码显示功能进行测试ꎬ运行可执行程序ꎬ视频开始自动解码显示ꎬ如图8(b)所示ꎮ对视频流进行了防解析失败测试ꎬ测试视频流包括AVIꎬMP4ꎬMOVꎬMKVꎬFLV等格式ꎬ随机选择视频流后采用传统视频解码算法与防解析失败算法进行解码测试ꎮ如表1所示ꎬ在解码过程中ꎬ传统解码算法出现了四次解码失败ꎬ解码成功率为60%ꎬ而防解析失败算法能够全部解码成功ꎬ成功率为100%ꎮ图8㊀摄像头采集显示和视频流解码显示图表1㊀解码时间对比表随机视频流格式传统解码显示算法/s防解析失败解码算法/sAVI4.9814.980FLVF4.981MKV4.9954.981MOVF4.980MP44.9814.981AVIF4.980MKV4.9954.980MOVF4.980AVI4.9814.981AVI4.9814.9804.2㊀可靠性分析对比传统算法与防解析失败解码算法的视频解码过程ꎬ研究发现:一方面ꎬ传统算法支持的解码格式相对较少ꎬ部分视频流无法识别解码格式导致无法解码ꎬ例如传统解码算法不支持MOV格式的视频流解码ꎬ解码MOV视频流时会出现解码错误ꎻ另一方面ꎬAVI视频流的格式成功匹配后ꎬ由于编码算法多样性导致生成的标识符不同ꎬ可能出现视频流标识符与解码算法标识符无法匹配的情况ꎬ即AVI格式视频流仍可能解码失败ꎮ防解析失败算法对传统解码算法进行了优化ꎬ解决了解码过程中可能出现的问题ꎬ自检时将非H.264算法编码的AVI格式或其他格式视频流转换成H.264的AVI格式视频流储存在共享内存2中ꎬ解码时直接调用ꎬ避免了解析失败或视频流格711电㊀子㊀器㊀件第43卷式无法识别的问题ꎬ解码稳定高效ꎮ进一步研究发现ꎬ独立设计的仪表视频模块ꎬ不会被仪表其他模块干扰ꎬ能够有效保证视频流的解码ꎮ经暴力测试和环境测试ꎬ本算法以非常高的成功率实现了视频流的解码ꎬ规避了解码失败和仪表死机的情况ꎬ证明了本算法可提升仪表的稳定性ꎬ降低开发风险ꎮ4.3㊀视频模块在汽车液晶仪表中的应用将视频模块嵌入到基于I.MX6平台搭建的汽车液晶仪表后ꎬ运行系统程序如图8所示ꎬ在不影响其他模块功能的情况下ꎬ视频能够高清晰度高分辨率的在仪表上显示ꎮ图9㊀仪表视频模块应用实例图5㊀本文创新之处本文以支持3D大屏投射的I.MX6平台为基础ꎬ优化了视频模块的电源电路ꎬ并设计了一种新的视频解码策略ꎮ本文有以下创新点和特色:①设计了新的视频解码算法ꎬ该算法具备防解析失败的优势ꎬ确保不会因视频流格式或标识符无法识别造成仪表死机ꎮ测试可知ꎬ解码成功率100%ꎬ相较于传统解码孙发ꎬ该设计提升了仪表的可靠性和稳定性ꎻ②视频模块应用性强ꎬ实际过程中ꎬ该设计大大节省了仪表的内存ꎬ优化了仪表资源结构ꎬ为后续汽车液晶仪表视频模块的可移植开发提供了经验ꎮ参考文献:[1]㊀TangNꎬZhaoPꎬWuShaoqi.Real ̄TimeVideoImageDehazingSystemBasedonFPGA[J].ComputerEngineering&Designꎬ2016ꎬ37(11):3124-3129ꎬ3141.[2]郭健忠ꎬ吴建立ꎬ谢斌ꎬ等.汽车液晶仪表实车数据测试台开发及数据分析[J].重庆大学学报ꎬ2018ꎬ41(5):37-43.[3]许逸飞ꎬ王闯ꎬ王海鹏ꎬ等.一种车载视频处理模块的设计与实现[J].电子技术ꎬ2014ꎬ43(1):35ꎬ42-43.[4]高俊岭ꎬ陈志飞ꎬ章佩佩.基于FPGA的实时视频图像采集处理系统设计[J].电子技术应用ꎬ2018(2):10-12.[5]张帆ꎬ闫秀秀.基于DFT基的矿井视频监控图像分块压缩感知方法[J].传感技术学报ꎬ2017ꎬ30(1):94-100.[6]向梓豪ꎬ陆安江.基于FPGA的MIPI多模式显示模块设计[J].电子技术应用ꎬ2017ꎬ43(12):48-51.[7]孙宝海ꎬ秦丽ꎬ刘文怡ꎬ等.多接口视频编码方案的设计与实现[J].电子器件ꎬ2018ꎬ41(1):85-89.[8]刘克轩ꎬ李永红ꎬ岳妮ꎬ等.基于FPGA和DSP的音视频采集处理系统设计[J].电子器件ꎬ2016ꎬ39(3):703-708.[9]时旭.基于FPGA的视频图像采集系统的设计[D].长春:吉林大学ꎬ2016.[10]彭玉青ꎬ李木ꎬ高晴晴ꎬ等.基于动态模板匹配的移动机器人目标识别[J].传感技术学报ꎬ2016ꎬ29(1):58-63.[11]聂云.基于FPGA的动态目标跟踪系统设计[D].武汉:武汉轻工大学ꎬ2016.[12]王哲.基于FPGA的图像处理系统设计[D].北京:北京理工大学ꎬ2016.[13]谢荣东.基于以太网AVB技术的音视频编码器设计[J].电子技术与软件工程ꎬ2014(20):30-30.郭健忠(1969-)ꎬ男ꎬ汉族ꎬ湖北武穴人ꎬ武汉科技大学ꎬ副教授ꎬ研究方向为汽车电子与信息技术ꎻ陈㊀典(1994-)ꎬ男ꎬ汉族ꎬ湖北黄冈人ꎬ武汉科技大学ꎬ硕士研究生ꎬ研究方向为汽车液晶仪表技术及开发ꎻ㊀闵㊀锐(1983-)ꎬ男ꎬ汉族ꎬ湖北随州人ꎬ武汉保华显示科技有限公司ꎬ高级工程师ꎬ研究方向为汽车总线技术及嵌入式系统开发ꎮ811。
M车组合仪表国产化设计开发和验证

M车组合仪表国产化设计开发和验证M车组合仪表是一种车载电子仪器,广泛应用于汽车、摩托车等交通工具中。
M车组合仪表的主要功能是记录并展示驾驶员需要关注的行车状态信息,如车速、转速、油量、水温、电量等。
此外,M车组合仪表还可以提供导航、音响、通信等辅助功能,提升驾驶员的驾驶体验和安全性。
在中国市场,M车组合仪表一直依赖进口产品。
然而,随着国内汽车行业的迅速发展和技术水平的提高,越来越多的汽车厂商开始将目光投向了M车组合仪表的国产化设计与开发。
本篇文章将介绍M车组合仪表国产化设计开发和验证的相关内容。
一、M车组合仪表国产化设计开发的关键技术1.硬件方面的设计开发M车组合仪表的硬件设计开发主要针对它的电路板、外壳、屏幕等部件。
其中,电路板的设计是M车组合仪表国产化设计开发的关键。
电路板包括了芯片、德州仪器(TI)的处理器和传感器等元器件。
同时,电路板还要支持车速传感器、转速传感器、燃油传感器、水温传感器等数据的获取和处理。
硬件方面的设计开发由汽车电子厂商负责。
2.软件方面的设计开发M车组合仪表的软件设计开发是基于C语言构建的,并且需要支持多种编程环境。
软件部分主要负责将电路板采集到的数据进行加工、处理和展示,完成汽车驾驶状态显示、音响控制、导航等功能。
软件方面的设计开发由软件开发公司负责。
3.国际认证方面的设计开发除了硬件和软件方面的设计开发,M车组合仪表的国产化设计开发还需要通过一系列的国际认证,如EMC认证、E-Mark认证、E-Typing认证等。
这些认证是保证M车组合仪表质量和安全的标志,可以帮助M车组合仪表顺利进入海外市场。
二、M车组合仪表国产化设计开发的验证1.硬件测试硬件测试主要是针对电路板的功能和性能进行验证,以确保最终的产品可以稳定、可靠地运行。
硬件测试覆盖了电路板的自检、传感器读取、数据传输、显示等方面,有利于发现电路板的设计缺陷并及时纠正。
2.软件测试软件测试主要是对M车组合仪表软件进行功能和性能测试,以验证其是否满足预设的功能和性能指标。
- 1、下载文档前请自行甄别文档内容的完整性,平台不提供额外的编辑、内容补充、找答案等附加服务。
- 2、"仅部分预览"的文档,不可在线预览部分如存在完整性等问题,可反馈申请退款(可完整预览的文档不适用该条件!)。
- 3、如文档侵犯您的权益,请联系客服反馈,我们会尽快为您处理(人工客服工作时间:9:00-18:30)。
汽车仪表板电子测试系统的设计与实现
发表时间:2019-04-04T10:34:50.913Z 来源:《知识-力量》2019年7月上作者:郑伟
[导读] 汽车仪表是最为直观的向人类显示汽车运行情况的仪器。
汽车运行过程中,各系统的工作状态都可以通过多种汽车仪表显示,驾驶员可以及时了解汽车运行的里程、耗油量、车速、有无故障等信息。
(航天科技控股集团股份有限公司,黑龙江省哈尔滨市 150060)
摘要:汽车仪表是最为直观的向人类显示汽车运行情况的仪器。
汽车运行过程中,各系统的工作状态都可以通过多种汽车仪表显示,驾驶员可以及时了解汽车运行的里程、耗油量、车速、有无故障等信息。
现代的汽车仪表,基本都制作精良,外形优美,是众多品牌汽车的标配部件之一。
因此,汽车仪表工作时的可靠性,以及参数传递的准确性,对驾驶员的安全操控至关重要。
关键词:汽车;仪表板;设计
随着汽车工业的发展,现代汽车的各种机构日趋复杂,其附属装置也越来越多。
为了使驾驶员能够更多更迅速的掌握汽车行驶信息,及时有效的采取相应的操作,保证汽车安全正常的工作,汽车仪表板己经成为现代汽车的信息中心。
在汽车仪表大批量生产过程中同时带来另一个问题,那就是生产成品的测试标定问题。
由于电子器件生产工艺的特殊性,造成即使同一类型的电子器件其电气特性也无法完全相同。
因此从同一条生产线上用同样的工艺生产出来的同一型号的仪表,也需要对每一块表进行单独检验标定。
目前国内大部分汽车仪表生产厂家对成型仪表的测试标定都是依照经验采用手工方法标定,严重影响了生产效率。
如何开发出一种能自动测试标定汽车仪表的测试仪表已经成为一项重要而且极富应用意义的课题。
一、概述
作为一种重要的组成部件,汽车组合仪表的性能直接影响到汽车驾驶的安全性。
早在上个世纪七十年代末,显示仪表就已经问世,随着科技的进步,尤其是传感技术、显示技术、软件技术、集成电路技术以及多通道技术的迅速发展,汽车驾驶的安全性和便捷性越来越受到人们关注,而汽车仪表也逐渐向微型化和电子化方向发展。
经过多年的努力,我国汽车仪表已经在前期引进和改造的基础上取得了很大的进步,电热式和电磁式汽车仪表已经相当普及,目前的发展方向是新一代全电子式汽车组合仪表。
尽管如此,国内的众多汽车仪表厂商还不完全具备自主开发的能力,部分仪表制造技术还需依靠国外支持。
此外,仪表制造的整体工艺水平还不够高,创新能力不足,很多企业根本不具备与生产同步的高性能仪表检测设备,这些因素严重影响了我国汽车仪表行业的发展。
在进行仪表指针压装时,还是采用传统的手工或半手工方式,能够使用自动指针压装系统的厂家寥寥无几,而自动标定系统则更是少见,而且标定的精度有待提高。
二、仪表指针压装系统的组成
汽车组合仪表的主要用途是显示汽车行进过程中的各种参数变化,从而判断汽车当前的行驶状态。
现在生产汽车主要配置的组合仪表包括:转速表、里程表、燃油表、压力表、电池电量表等。
由于长期的驾驶习惯,目前的汽车仪表还是采用指针式和数显式相结合的方式,指针式仪表的核心部件包括指针和步进电机。
在进行仪表装配生产时,传统的方法就是采用特制的压装设备,通过手动方式控制气缸驱动多个压装头完成一次多个指针压装。
而现代的压装方式则是采用基于智能微处理器的自动压装系统,这种系统具有较多的优点,例如:可直接接入计算机进行操作,接口丰富,可随时调整流程和参数,抗干扰能力强,性价比高,适应性广等。
这种自动压装系统的结构也较为简单,主要包括微处理器、电机驱动模块、压力检测模块、操作面板、报警电路以及仪表盘支撑和固定机构等。
三、指针压装系统的测试分析
在对指针压装系统进行测试时,本文重点测试两个部分的内容,分别为压装压力测试和压装间隙测试。
影响压装压力的主要因素是压力传感器的性能,因此在测试压装压力时,主要是测试传感器的输出精度、反映速度等指标,同时进行压力校准。
根据之前的分析,在进行仪表指针压装时,压装压力要控制在70-120N 之间,在不同量程下进行了反复多次测试,传感器的输出值经过单片机程序处理。
结果表明,所设计的压装系统能够有效控制下压速度,压装压力大多在90-110N 范围内,检测精度能够达到 0.1N。
在进行压力校准时,利用标准值作为参考,具体结果如表所示。
1、压装间隙的测试分析。
影响压装间隙准确度的主要因素包括压装下压速度、压力检测速度和气缸弹起反应时间等。
理论上来看,在压力检测速度保持不变的情况下,要想保证压装间隙准确,压装下压速度和气缸弹起反应时间都应该越小越好。
在设计压装系统时,我们选取的压装间隙测距光栅尺的分辨率为0.5μm,精度达到±3μm,因此,如果压装下压速度为V =5mm/s,程序扫描时间为T=1ms,那么由单片机程序处理延迟而导致的误差为:
根据式的计算结果,由单片机扫描程序时间所引起的误差很小,基本处在±3μm的光栅尺准确度范围内,因此,影响压装间隙准确度的主要因素应该是气缸弹起反应时间。
在保持压装下压速度为V=5mm/s,气缸压力为30N的条件下,通过反复多次测试,发现气缸弹起反应时间约为0.2s,相应造成的误差约为0.2mm,明显超出了±0.1mm 的精度要求。
在硬件条件无法改变的情况下,为了消除这个误差,在保持气缸压力基本问题的前提下,我们采用在程序中调节处理的办法。
根据压装间隙的检测过程,把压装间隙提高0.3mm,这样在实际压装时可以预先在程序中消除这个延迟误差,从而使压装间隙的精度满足设计要求。
2、指针标定系统的测试分析。
根据标准的规定,在标定汽车仪表等指针式仪表时,主要对示值误差和回程误差进行检测。
(1)示值误差的检定方法。
仪表示值误差需要在正反两个方向上各检定一次,本文设计每隔10个刻度为一个检定点。
在检定时,首先控制步进电机使仪表指针归零,同时控制CCD摄像机提取零刻度时的表盘图像,并保存命名为Image0;然后再控制步进电机使仪表指针按正方向转动10个刻度,达到指定位置后由CCD 摄像机再次提取表盘图像,并保存命名为Image1;最后,利用图像 Image0和Image1以及第四章介绍的表盘示数提取算法,计算出此检定点的表盘示数,并与期望的理论值进行比较得出示值误差。
重复上述过程,直到正方向上所有的检定点都检定完成。
反方向上的检定过程与正方向完全相同,检定条件要保持不变,同时计算各检定点示值误差时的正负号也要保持一致。
每一个检测行程内的示值误差是根据行程中所有检定点的误差求得,而任意 1mm距离内的示值误差则是根据0-1,1-2范围内所得各点的误差求得。
示值误差的计算方法为:如果误差同号,示值误差=最大误差-最小误差;如果误差异号,示值误差=|最大误差|+|最小误差|。
(2)回程误差的检定方法。
由于仪表结构的原因,在正反行程上其示值不可能完全相同,这种误差被称作回程误差。
因此,在检定完示值误差以后,取正反行程内各检定点示值误差的最大值确定回程误差。
(3)检定结果及分析,根据汽车常用仪表的量程,应属于 0 级大量程仪表,国家标准规定的仪表允许误差,在检定开始前,被检仪表的设计精度是已知的,利用本文设计的标定系统对待检仪表进行精度检测,最后根据精度检定结果的对比分析,就可以知晓待检仪表是否合格。
通过工作行程误差 7µm<30µm ,示值误差7µm<12µm,回程误差4.3µm<6µm,因此,设计的仪表标定系统的准确性较好,采用仪表标定系统可以对汽车仪表进行精度检测和标定,实验结果测量准确,检测速度较快,能够满足系统对于实时性的要求。
结论
通过对仪表压装和标定系统进行了简单测试,压装系统测试包括压装压力和电流,以及压装间隙测试;标定系统对汽车仪表的示值误差进行了检定和计算。
测试结果表明,本文设计的仪表压装和标定系统基本满足要求,性能较好。
参考文献
[1]曹旻颖.汽车工艺中仪表板整体优化设计要点分析[J].科技创新与应用,2013(32):95-95.
[2]李慧莲,孙久强. 基于车载网络的汽车数字仪表系统设计[J].应用科技,2013, 40(3)4.
[3]陈美文,丛艺家,赵福全.仪表板的布置设计[J].轻型汽车技术,2012(01):21-24.
[4]卢嘉伟.浅谈汽车电子技术在仪表中的应用[J].黑龙江科技信息,2015,2。