穿孔等离子弧焊接技术
等离子弧焊接
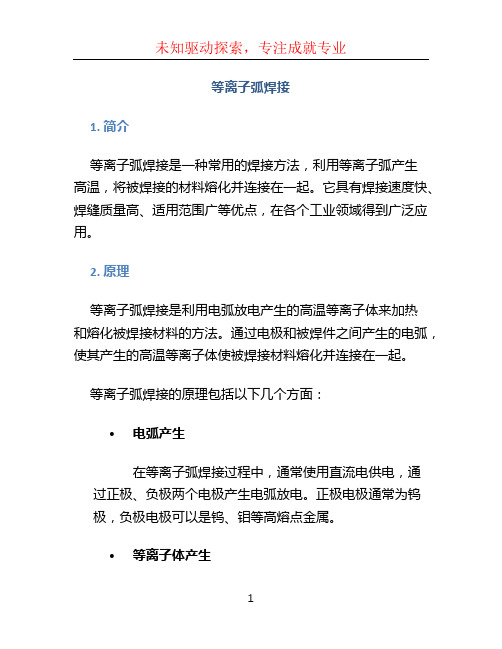
等离子弧焊接1. 简介等离子弧焊接是一种常用的焊接方法,利用等离子弧产生高温,将被焊接的材料熔化并连接在一起。
它具有焊接速度快、焊缝质量高、适用范围广等优点,在各个工业领域得到广泛应用。
2. 原理等离子弧焊接是利用电弧放电产生的高温等离子体来加热和熔化被焊接材料的方法。
通过电极和被焊件之间产生的电弧,使其产生的高温等离子体使被焊接材料熔化并连接在一起。
等离子弧焊接的原理包括以下几个方面:•电弧产生在等离子弧焊接过程中,通常使用直流电供电,通过正极、负极两个电极产生电弧放电。
正极电极通常为钨极,负极电极可以是钨、钼等高熔点金属。
•等离子体产生电弧放电产生的高温会使空气中的原子和分子离子化形成等离子体。
等离子体具有高温、高热量、高电导等特性。
•材料熔化和连接等离子体的高温可使被焊接材料迅速熔化。
通过控制电弧形成的热量和等离子体的速度,可使熔融材料与被焊件接触并融合在一起。
3. 设备和材料•等离子弧焊接设备–电源–控制系统–焊枪–气体供应系统•焊接材料–被焊件–焊条(焊丝)4. 焊接过程等离子弧焊接主要包括以下几个步骤:1.准备焊接材料–清洁被焊件表面,确保无杂质和油污。
–准备好所需的焊条或焊丝。
2.设置焊接参数–根据被焊件的材料和厚度,设置合适的电流和电压。
–设置气体流量和喷嘴的形状。
3.开始焊接–确保焊接区域没有杂散光线和易燃物。
–启动电源,使电极与被焊件接触,产生电弧。
4.控制焊接速度和角度–控制焊接速度,保证焊缝的均匀性。
–调整焊接角度,以获得所需的焊缝形状。
5.完成焊接–在焊接完成后,关闭电源。
–对焊缝进行清理和检查。
5. 应用领域等离子弧焊接在各个领域都有广泛应用,包括但不限于以下几个方面:•金属制造等离子弧焊接可用于焊接各种金属材料,如钢铁、铝合金、不锈钢等。
在汽车制造、造船、航空航天等领域具有重要地位。
•管道焊接等离子弧焊接可用于焊接各种管道,如石油管道、天然气管道、水管等。
它具有速度快、焊缝质量高等优点。
焊接中的等离子焊技术

焊接中的等离子焊技术焊接是与人们生活息息相关的一项技术,在制造业、建筑业等诸多领域都有广泛的应用。
而等离子焊则是焊接技术中非常重要的一种,它广泛应用于金属材料的连接与修复。
本文就从等离子焊的原理、特点、应用等方面入手,较详细地阐述等离子焊技术。
一、等离子焊的原理等离子是指气体分子或原子被能量激发后,电子从原子周层跃迁至中心核,中心核周围的电子云形成一个电离区域,这种电离区域就是等离子体。
在电弧发生时,电极之间的电流使气体分子发生电离,产生等离子体,从而形成电弧。
等离子焊就是利用这种电弧作为热源将工件加热,使其达到熔点,从而完成焊接。
等离子焊的主要特点就是高温、高速和高能量密度。
在等离子焊的过程中,电弧传热效率高,焊接速度快,所以可以用来焊接高导热系数的金属的薄板和薄壁管和其他结构件。
二、等离子焊技术的优势相较于其他焊接方法,等离子焊有很多优势。
1. 等离子焊的焊缝质量高,焊缝强度好。
等离子焊的焊接速度快,从而减少了热输入,焊缝的变形和气孔缺陷少,因此焊接质量比较高。
2. 等离子焊的焊接速度快。
由于等离子焊的热输入大,焊接速度快,从而可以提高工作效率和生产效率。
3. 等离子焊的生产环境整洁。
等离子焊使用气体作为保护气体,不产生明火和焦炭,不会污染环境,因此在生产环境整洁和卫生。
三、等离子焊的应用等离子焊在有色金属、合金材料、不锈钢、钢结构和硬质合金等材料的焊接方面有广泛的应用。
1. 有色金属和合金材料的焊接。
在精密电子仪器、航空航天等领域中,有色金属和合金材料的焊接是一种特殊的焊接方式,一般采用等离子焊。
2. 不锈钢的焊接。
等离子焊在不锈钢中的应用范围非常广泛,尤其在不锈钢的压力容器和管道中应用比较广泛,一般采用氩弧焊和等离子焊。
3. 钢结构焊接。
在钢结构中使用等离子焊,可以实现高速焊接,从而提高了工作效率和生产效率。
4. 硬质合金的焊接。
在硬质合金中使用等离子焊,可以实现高质量焊接,价格较为昂贵,因此一般都使用等离子焊进行连接。
等离子弧焊的工艺方法
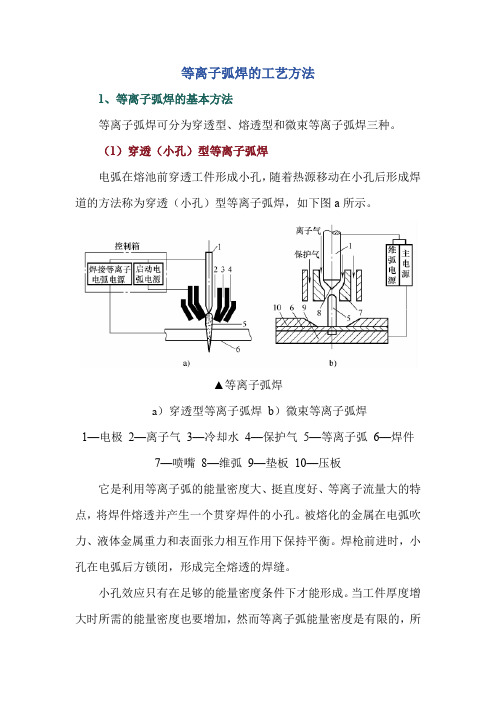
等离子弧焊的工艺方法1、等离子弧焊的基本方法等离子弧焊可分为穿透型、熔透型和微束等离子弧焊三种。
(1)穿透(小孔)型等离子弧焊电弧在熔池前穿透工件形成小孔,随着热源移动在小孔后形成焊道的方法称为穿透(小孔)型等离子弧焊,如下图a所示。
▲等离子弧焊a)穿透型等离子弧焊b)微束等离子弧焊1—电极2—离子气3—冷却水4—保护气5—等离子弧6—焊件7—喷嘴8—维弧9—垫板10—压板它是利用等离子弧的能量密度大、挺直度好、等离子流量大的特点,将焊件熔透并产生一个贯穿焊件的小孔。
被熔化的金属在电弧吹力、液体金属重力和表面张力相互作用下保持平衡。
焊枪前进时,小孔在电弧后方锁闭,形成完全熔透的焊缝。
小孔效应只有在足够的能量密度条件下才能形成。
当工件厚度增大时所需的能量密度也要增加,然而等离子弧能量密度是有限的,所以穿透型等离子弧焊只能在一定的板厚范围内实现。
各种材料一次焊透的厚度见下表。
大电流等离子弧焊一次可焊透厚度穿透型等离子弧焊最适宜焊接厚3~8mm的不锈钢、厚12mm以下的钛合金及铝合金、厚2~8mm的低碳钢或低合金钢,以及铜和铜合金、镍和镍合金的对接焊缝。
(2)熔透型等离子弧焊在焊接过程中只熔透工件而不产生小孔效应的焊接方法称为熔透型等离子弧焊,简称熔透法。
熔透型等离子弧焊是离子气流量较小、弧柱压缩程度较弱时的一种等离子弧焊。
此种方法基本上与钨极氩弧焊相似,随着焊枪向前移动,熔池金属凝固成焊缝。
它适用于板厚小于3mm的薄板I形坡口、不加衬垫单面焊双面成形,厚板开V形坡口多层焊。
其优点是焊接速度比钨极氩弧焊快。
(3)微束等离子弧焊利用小电流(通常在30A以下)进行焊接的等离子弧焊,通常称为微束等离子弧焊,又称为针状等离子弧焊,如上图b所示。
它是采用ф0.6~ф1.2mm的小孔径压缩喷嘴及联合型弧,当焊接电流小于1A时,仍有较好的稳定性。
微束等离子弧焊特别适合于薄板和细丝的焊接。
焊接不锈钢时,最小厚度可以达到0.025mm。
等离子弧焊接使用要点 (一)

等离子弧焊接使用要点(一)一、等离子弧焊(割)炬喷嘴孔径不宜过大等离子弧是一种压缩电弧,其压缩作用来自于喷嘴的机械作用、热收缩和磁收缩等。
通常焊(割)炬的喷嘴孔径应根据电流和离子气流量来确定。
在一定条件下,喷嘴的孔径越大,对等离子弧的压缩作用越小。
如果喷嘴孔径过大,就会丧失压缩作用,等离子弧也就建立不起来。
通常喷嘴的孔道比l/d应大于3,如图所示。
等离子弧喷嘴的孔道比1—钨棒2—喷嘴3—等离子弧及扩散角二、等离子弧焊时不应存在双弧正常的转移型等离子弧应该稳定“燃烧”在钨极和工件之间,当另有电弧“燃烧”于钨极—喷嘴—工件之间时,即形成双弧,如图所示。
此时主弧电流将降低,正常的焊接或切割过程被破坏,严重时将导致喷嘴烧毁或离子弧过程中断。
等离子弧焊喷嘴内的“双弧”三、等离子弧焊接和切割电源不能通用等离子弧焊接和切割电源一般都采用陡降外特性直流电源。
但切割用电源输出的空载电压一般大于150V,压缩空气等离子弧切割电源空载电压可高达600V。
等离子弧焊接电源输出的空载电压一般在80V左右,两者不能通用(下图)。
等离子弧焊接与切割的电源外特性a)焊接电源外特性b)切割电源外特性四、不导电的工件不能建立转移电弧产生于钨极和工件之间的等离子弧称为转移电弧,转移电弧是由非转移电弧(产生于钨极和喷嘴间的电弧)过渡转移产生的。
当工件不导电(或不通电)时,转移电弧不能产生。
因此非金属加工只能利用非转移电弧形成的等离子弧,如图所示。
转移电弧与非转移电弧1—转移电弧电源2—非转移电弧电源3—金属4—非金属5—非转移电弧五、微束等离子弧焊不宜采用单电源供电大电流等离子弧都采用转移电弧,在转移电弧产生后非转移电弧随即切断,因此转移电弧和非转移电弧可合用一个电源。
微束等离子弧焊是采用联合型弧,由于焊接过程中需要同时保持非转移电弧和转移电弧,故要采用两个独立电源,如图所示。
等离子弧焊的供电形式a)大电流等离子弧焊b)微束等离子弧焊6—转移电弧1—焊接电源2—维弧电源R—限流电阻S—转换开关六、大电流工作不宜采用小锥角电极为了便于引弧和增加电弧的稳定性,电极端部可磨成20°~60°的夹角。
等离子焊接工艺
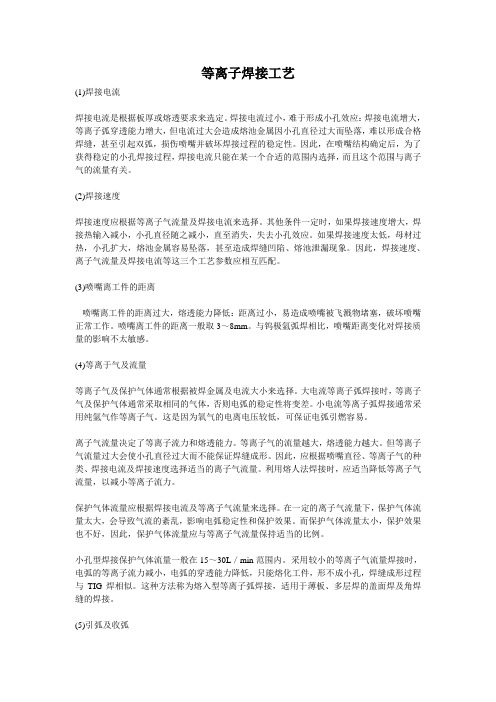
等离子焊接工艺(1)焊接电流焊接电流是根据板厚或熔透要求来选定。
焊接电流过小,难于形成小孔效应:焊接电流增大,等离子弧穿透能力增大,但电流过大会造成熔池金属因小孔直径过大而坠落,难以形成合格焊缝,甚至引起双弧,损伤喷嘴并破坏焊接过程的稳定性。
因此,在喷嘴结构确定后,为了获得稳定的小孔焊接过程,焊接电流只能在某一个合适的范围内选择,而且这个范围与离子气的流量有关。
(2)焊接速度焊接速度应根据等离子气流量及焊接电流来选择。
其他条件一定时,如果焊接速度增大,焊接热输入减小,小孔直径随之减小,直至消失,失去小孔效应。
如果焊接速度太低,母材过热,小孔扩大,熔池金属容易坠落,甚至造成焊缝凹陷、熔池泄漏现象。
因此,焊接速度、离子气流量及焊接电流等这三个工艺参数应相互匹配。
(3)喷嘴离工件的距离·喷嘴离工件的距离过大,熔透能力降低:距离过小,易造成喷嘴被飞溅物堵塞,破坏喷嘴正常工作。
喷嘴离工件的距离一般取3~8mm。
与钨极氩弧焊相比,喷嘴距离变化对焊接质量的影响不太敏感。
(4)等离于气及流量等离子气及保护气体通常根据被焊金属及电流大小来选择。
大电流等离子弧焊接时,等离子气及保护气体通常采取相同的气体,否则电弧的稳定性将变差。
小电流等离子弧焊接通常采用纯氩气作等离子气。
这是因为氧气的电离电压较低,可保证电弧引燃容易。
离子气流量决定了等离子流力和熔透能力。
等离子气的流量越大,熔透能力越大。
但等离子气流量过大会使小孔直径过大而不能保证焊缝成形。
因此,应根据喷嘴直径、等离子气的种类、焊接电流及焊接速度选择适当的离子气流量。
利用熔人法焊接时,应适当降低等离子气流量,以减小等离子流力。
保护气体流量应根据焊接电流及等离子气流量来选择。
在一定的离子气流量下,保护气体流量太大,会导致气流的紊乱,影响电弧稳定性和保护效果。
而保护气体流量太小,保护效果也不好,因此,保护气体流量应与等离子气流量保持适当的比例。
小孔型焊接保护气体流量一般在15~30L/min范围内。
等离子弧焊工艺概述

等离子弧焊工艺概述等离子弧焊,是一种高能量密度焊接工艺,常被应用于合金材料的焊接和切割工作。
本文将对等离子弧焊的工艺、特点和应用进行概述,帮助读者更好地了解该焊接工艺。
一、等离子弧焊工艺简介等离子弧焊是一种高温高压气体电弧焊接工艺,它利用弧焊发电机产生的电弧加热气体,使气体达到高温高能状态,形成等离子体。
等离子体具有很高的能量密度和局部热效应,能够快速加热和熔化焊接部件,实现焊接连接。
等离子弧焊可以分为直流等离子弧焊和交流等离子弧焊两种形式,具体选择根据焊接材料和要求来确定。
二、等离子弧焊的特点1. 高能量密度:等离子弧焊的能量密度较高,能够快速加热焊接部件,减少焊接时间和热影响区域,提高焊接效率。
2. 局部加热效应好:由于等离子体产生的高温高能状态,其加热范围非常局限,降低了对焊接部件周边材料的热影响。
3. 适用于合金材料焊接:等离子弧焊适用于焊接具有高熔点、难焊接的合金材料,如不锈钢、钨、钼等。
4. 焊缝质量高:等离子弧焊焊接质量好,焊缝均匀、致密,抗拉强度高。
三、等离子弧焊的应用领域1. 汽车工业:等离子弧焊在汽车制造领域有广泛应用,可以用于焊接车身零部件、燃油箱及排气管等。
2. 航空航天工业:等离子弧焊可以用于航空航天领域的部件焊接,如飞机结构、气动外壳等。
3. 石油化工工业:等离子弧焊可以用于石油化工设备的制造,如高压容器、石油储罐等。
4. 电子电器行业:等离子弧焊可以用于焊接电子电器行业的零部件,如电路板、连接器等。
综上所述,等离子弧焊是一种高能量密度焊接工艺,具有高能量密度、局部加热效应好、适用于合金材料焊接等特点。
在汽车工业、航空航天工业、石油化工工业和电子电器行业等领域有广泛的应用。
随着科学技术的发展,等离子弧焊技术将不断完善和创新,为各行各业的焊接需求提供更好的解决方案。
等离子弧焊与切割及其他焊接技术
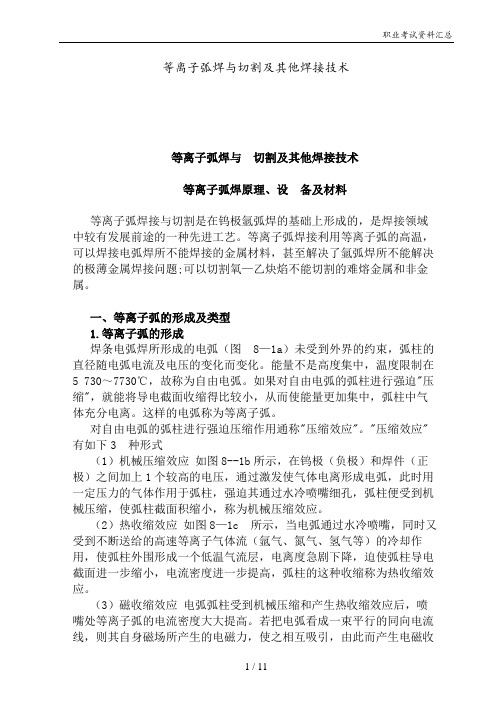
等离子弧焊与切割及其他焊接技术等离子弧焊与切割及其他焊接技术等离子弧焊原理、设备及材料等离子弧焊接与切割是在钨极氩弧焊的基础上形成的,是焊接领域中较有发展前途的一种先进工艺。
等离子弧焊接利用等离子弧的高温,可以焊接电弧焊所不能焊接的金属材料,甚至解决了氩弧焊所不能解决的极薄金属焊接问题;可以切割氧—乙炔焰不能切割的难熔金属和非金属。
一、等离子弧的形成及类型1.等离子弧的形成焊条电弧焊所形成的电弧(图8—1a)未受到外界的约束,弧柱的直径随电弧电流及电压的变化而变化。
能量不是高度集中,温度限制在5 730~7730℃,故称为自由电弧。
如果对自由电弧的弧柱进行强迫"压缩",就能将导电截面收缩得比较小,从而使能量更加集中,弧柱中气体充分电离。
这样的电弧称为等离子弧。
对自由电弧的弧柱进行强迫压缩作用通称"压缩效应"。
"压缩效应"有如下3 种形式(1)机械压缩效应如图8--1b所示,在钨极(负极)和焊件(正极)之间加上1个较高的电压,通过激发使气体电离形成电弧,此时用一定压力的气体作用于弧柱,强迫其通过水冷喷嘴细孔,弧柱便受到机械压缩,使弧柱截面积缩小,称为机械压缩效应。
(2)热收缩效应如图8—1c 所示,当电弧通过水冷喷嘴,同时又受到不断送给的高速等离子气体流(氩气、氮气、氢气等)的冷却作用,使弧柱外围形成一个低温气流层,电离度急剧下降,迫使弧柱导电截面进一步缩小,电流密度进一步提高,弧柱的这种收缩称为热收缩效应。
(3)磁收缩效应电弧弧柱受到机械压缩和产生热收缩效应后,喷嘴处等离子弧的电流密度大大提高。
若把电弧看成一束平行的同向电流线,则其自身磁场所产生的电磁力,使之相互吸引,由此而产生电磁收缩力,这种磁收缩作用迫使电弧更进一步的受到压缩,如图8—1d所示。
在以上3 种效应的作用下,弧柱被压缩到很细的程度,弧柱内气体也得到了高度的电离,温度高达16000~33000℃,能量密度剧增,而且电弧挺度好,具有很强的机械冲刷力,形成高能束的等离子弧。
等离子弧焊接的名词解释

等离子弧焊接的名词解释等离子弧焊接是一种常见的金属材料连接技术,它利用弧焊的原理和等离子体的特性来实现焊接。
1. 弧焊基本原理弧焊是一种利用焊接电弧热量将金属材料熔化并通过填充材料形成焊缝的方法。
在等离子弧焊接中,焊工通过两电极间的电弧放电,使气体或气体混合物在高温电弧热作用下形成等离子体,然后利用等离子体的高温和大能量来熔化金属材料并完成焊接过程。
2. 等离子体的特性等离子体是带电的气体,它的特点是高温、高能量、导电性强以及能在电磁场中受力等。
这些特性使得等离子体在焊接过程中发挥重要作用。
等离子弧焊接中,通过控制等离子体的形成和行为,可以实现高效率、高质量的焊接。
3. 等离子弧焊接的设备等离子弧焊接需要特殊的设备来产生和控制焊接过程中的等离子体。
主要设备包括焊接电源、焊接电极、等离子弧焊枪和保护气体供给系统等。
焊接电源负责提供适当的电流和电压来维持电弧的稳定,并为电弧供能。
焊接电极是产生电弧的工具,常见的有钨极、钼极等。
等离子弧焊枪通过控制电弧的形成和维持,将电弧聚焦在焊接区域。
保护气体供给系统则提供保护气体,从而保护电弧、熔化金属和熔化池免受空气中的氧气和其他杂质的污染。
4. 等离子弧焊接的应用等离子弧焊接广泛应用于各个领域,特别是在航空航天、汽车制造、石油化工、核工程等重要领域中,具有重要的地位。
其应用范围包括焊接厚板、薄板、管道、容器等各种结构件,能够满足不同材料(如碳钢、不锈钢、铝合金等)的焊接需求。
5. 等离子弧焊接的优点等离子弧焊接具有以下优点:(1)焊接速度快,高效率;(2)焊接质量高,焊缝质量好;(3)可焊接不同材料的金属;(4)操作简单、易学易用。
总结等离子弧焊接是一种常见的金属材料连接技术,通过利用等离子体的特性和弧焊的原理来实现焊接。
它具有广泛的应用领域和重要的地位,能够满足不同材料的焊接需求。
通过控制等离子体的形成和行为,等离子弧焊接能够实现高效率、高质量的焊接。
等离子弧焊
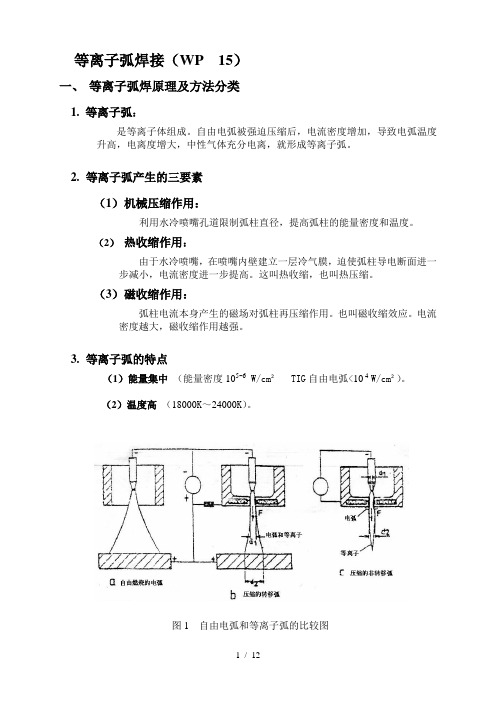
等离子弧焊接(WP 15)一、等离子弧焊原理及方法分类1. 等离子弧:是等离子体组成。
自由电弧被强迫压缩后,电流密度增加,导致电弧温度升高,电离度增大,中性气体充分电离,就形成等离子弧。
2.等离子弧产生的三要素(1)机械压缩作用:利用水冷喷嘴孔道限制弧柱直径,提高弧柱的能量密度和温度。
(2)热收缩作用:由于水冷喷嘴,在喷嘴内壁建立一层冷气膜,迫使弧柱导电断面进一步减小,电流密度进一步提高。
这叫热收缩,也叫热压缩。
(3)磁收缩作用:弧柱电流本身产生的磁场对弧柱再压缩作用。
也叫磁收缩效应。
电流密度越大,磁收缩作用越强。
3.等离子弧的特点(1)能量集中(能量密度105~6 W/cm²TIG自由电弧<10 4W/cm²)。
(2)温度高(18000K~24000K)。
图1 自由电弧和等离子弧的比较图4.等离子弧的三种基本形式(1)非转移型等离子弧钨极为负,喷嘴为正,钨极与喷嘴之间产生等离子弧。
(等离子束焊接)图2 非转移型等离子弧示意图(2)转移型等离子弧钨极为负,工件为正,钨极与喷嘴之间先引弧后,转移到钨极与工件之间产生等离子弧。
(等离子弧焊接)图3 转移型等离子弧示意(3)联合型等离子弧非转移型和转移型弧同时并存。
主要用于微束等离子弧焊、粉末堆焊等方面。
图4 联合型等离子弧示意图5.等离子弧焊基本方法(1)小孔型等离子弧焊(穿孔、锁孔、穿透焊)利用能量密度大和等离子流力大的特点,将工件完全熔透并产生一个贯穿工件的小孔,熔化金属被排挤在小孔的周围,沿着电弧周围的熔池壁向熔池后方移动,使小孔跟着等离子弧向前移动,形成完全熔透的焊缝。
一般大电流等离子弧(100~300安培)时采用该方法。
图5 小孔型等离子弧焊焊缝成形原理(2)熔透型等离子弧焊特点:离子气流量小,弧柱压缩程度较弱时,工件只熔化而不产生小孔效应。
用途:薄板单面焊双面成形,厚板多层焊。
图6 熔透型等离子弧焊焊缝成形原理(3)微弧(束)等离子弧焊30安培以下熔透型焊接方法为微弧(束)等离子弧焊。
等离子弧焊接工艺及设备
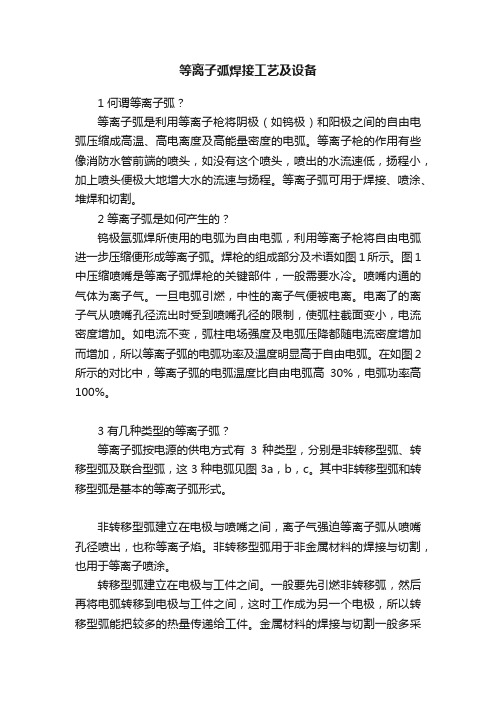
等离子弧焊接工艺及设备1 何谓等离子弧?等离子弧是利用等离子枪将阴极(如钨极)和阳极之间的自由电弧压缩成高温、高电离度及高能量密度的电弧。
等离子枪的作用有些像消防水管前端的喷头,如没有这个喷头,喷出的水流速低,扬程小,加上喷头便极大地增大水的流速与扬程。
等离子弧可用于焊接、喷涂、堆焊和切割。
2 等离子弧是如何产生的?钨极氩弧焊所使用的电弧为自由电弧,利用等离子枪将自由电弧进一步压缩便形成等离子弧。
焊枪的组成部分及术语如图1所示。
图1中压缩喷嘴是等离子弧焊枪的关键部件,一般需要水冷。
喷嘴内通的气体为离子气。
一旦电弧引燃,中性的离子气便被电离。
电离了的离子气从喷嘴孔径流出时受到喷嘴孔径的限制,使弧柱截面变小,电流密度增加。
如电流不变,弧柱电场强度及电弧压降都随电流密度增加而增加,所以等离子弧的电弧功率及温度明显高于自由电弧。
在如图2所示的对比中,等离子弧的电弧温度比自由电弧高30%,电弧功率高100%。
3 有几种类型的等离子弧?等离子弧按电源的供电方式有3种类型,分别是非转移型弧、转移型弧及联合型弧,这3种电弧见图3a,b,c。
其中非转移型弧和转移型弧是基本的等离子弧形式。
非转移型弧建立在电极与喷嘴之间,离子气强迫等离子弧从喷嘴孔径喷出,也称等离子焰。
非转移型弧用于非金属材料的焊接与切割,也用于等离子喷涂。
转移型弧建立在电极与工件之间。
一般要先引燃非转移弧,然后再将电弧转移到电极与工件之间,这时工作成为另一个电极,所以转移型弧能把较多的热量传递给工件。
金属材料的焊接与切割一般多采用转移型弧。
非转移型弧与转移型弧同时存在的等离子弧称联合型弧。
联合型弧需用两个独立电源供电,主要用于30A以下的微束等离子弧焊接。
4 有几种等离子弧焊接方法?按焊缝成形原理,等离子弧有两种基本焊接方法:穿透型等离子弧焊及熔透型等离子弧焊,其中30A以下的熔透型等离子弧焊又可称为微束等离子弧焊,穿透型等离子弧焊也称小孔型等离子弧焊。
穿孔等离子弧焊接热效率的选取及应用

Ke r s ls r ed n wed n h r le ce c a c p y ia t o y wo d :pa ma a c w li g; l i g te ma f in y; r h s l i c me h d
焊接热 过程 模 拟是 焊 接 数 值模 拟 的一 个 主 要 方面, 焊接 热源 物 理模 型 的确 立 是其 中关 键 , 主要
中图 分 类 号 : G 4 T 45 文献 标 志 码 :A 文 章 编 号 : 6 3— 87 2 1 )6— 59—0 17 4 0 (0 10 0 4 4
S l ci n a d a p ia in o h r a f ce c u i g ee t n p l t ft e m le in y d rn o c o i
ke ho e pl s a a c wed g y l a m r l i
H igin Wa gXal, n ah i uQnx , n i iWagY nu a o
( rvni e a fA vne ligTc nlg , i guUnvri f cec n eh o g , h ni gJ ns 10 3, hn ) Poica K yLbo dacdWedn eh o y J n s iesyo i eadTc nl y Z ej n i gu2 20 C ia l o a t S n o a a
穿孔法等离子弧立焊焊缝成形机理

穿孔法等离子弧立焊焊缝成形机理通过对立焊穿孔熔池的受力状态的分析,初步揭示了穿孔法等离子弧立焊焊缝成形机理,从而发现焊接工艺参数对焊缝成形影响的规律,为进一步研究穿孔法等离子弧立焊焊缝成形机理奠定了基础。
理论分析和试验结果均表明,穿孔能否连续稳定存在是焊缝成形的前提,而穿孔熔池液面金属的受力及流动则对焊缝正反面的成形起着重要作用。
在此基础上指出,焊接电流和离子气流量过大时会因穿孔熔池下半部的收缩能力小于上半部的扩张速度而形成切割,反之,过小的焊接电流和离子气流量会形成未焊透。
控制焊接电流的大小和喷嘴到工件的距离均可有效地实现对焊缝正反面增高量及宽度的控制。
穿孔法等离子弧立焊与平焊相比较,由于它改变了熔融金属的受力状态,使得这种方法除具有一般等离子弧平焊焊接特点之外,还具有工艺稳定性好,焊接质量高,一次可焊厚度大,可实现无气孔焊接等特点,是一种很有发展前途的焊接新方法。
在对铝合金穿孔法等离子弧立焊的开发试验过程中,发现焊缝正、反面的成形对焊枪喷嘴到工件的距离较敏感,当距离稍大时,焊缝背面出现凹陷,而平焊时这种现象则不易发生。
为此,认为穿孔熔池的受力状态对焊缝成形有较大的影响。
1 立焊穿孔熔池形状等离子弧由于有强烈的电磁收缩力和等离子流力,对熔池表面将产生很大压力,在这种电弧压力的作用下,熔池液态金属被排开而形成穿孔。
由于等离子弧的压力和温度在轴向上存在压力梯度和温度梯度,加之工件散热的影响。
使得穿孔熔池的垂直截面呈喇叭口形,靠近背面的液态金属在表面张力的作用下,也呈现小喇叭口形。
这样,穿孔熔池则为一个“双喇叭口”形的熔池,如图1所示。
图1 立焊穿孔熔池断面示意图Fig。
1 Cross section of the keyhole pool withvertical position welding2 立焊穿孔熔池受力及成形规律立焊焊缝成形如图2所示。
为了便于分析穿孔熔池的成形过程及成形条件,首先对穿孔熔池受等离子弧作用而形成的受力情况进行分析,如图3所示。
穿孔型等离子弧焊接研究现状

3 莱芜钢铁 集 团银 山型钢 有 限公 司板 带厂 , 东 莱芜 . 山 2 10 ) 7 14
摘要 : 穿孔 型等 离子弧 焊接 作 为一种 高能量 密度焊接 方 法 , 够对 中厚 板 不开坡 口一 次焊 能
透, 具有适 应性 强 、 对接 头装 配精度要 求低 的特 点 , 低 成本 、 属 高效 焊接 工 艺 , 有 很 大 的应 用 具
接工 艺广泛 应用 于结构 钢 、 车 、 汽 飞机 、 火箭 、 太空 飞 船和 空间焊 接等 。
归类 为高能 量密 度焊 接 , 泛 应 用 于 中厚板 金 属 材 广 料 的焊接加 工 。这 三类 热 源 因其 功 率 密度 高 , 接 焊 时在熔 池 中产生 小孔 , 因而 能 一 次性 单 道焊 透 中厚
工业 中的大 量应 用 。与 激 光 焊和 电子束 焊 相 比 , 虽 然等 离子弧 的能量 密度 较低 、 小孔 尺寸较 大 , 但其 作 为 电弧焊具 有适应 性 强 、 接 头装 配精 度要 求 低 的 对
p o e s s,c n f l e e r t h r ic so d l h c n s t i g e p s rc se a ul p n tae te wok p e e fmi d e t ik e swih sn l a s,S h ti i o y Ot a t sp -
等离子弧焊接
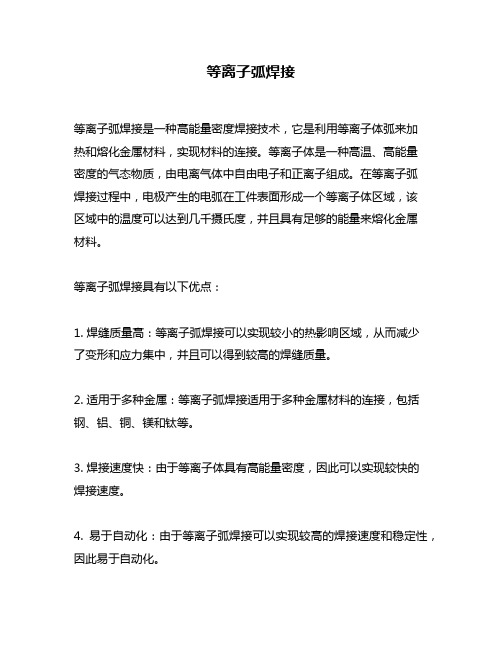
等离子弧焊接
等离子弧焊接是一种高能量密度焊接技术,它是利用等离子体弧来加
热和熔化金属材料,实现材料的连接。
等离子体是一种高温、高能量
密度的气态物质,由电离气体中自由电子和正离子组成。
在等离子弧
焊接过程中,电极产生的电弧在工件表面形成一个等离子体区域,该
区域中的温度可以达到几千摄氏度,并且具有足够的能量来熔化金属
材料。
等离子弧焊接具有以下优点:
1. 焊缝质量高:等离子弧焊接可以实现较小的热影响区域,从而减少
了变形和应力集中,并且可以得到较高的焊缝质量。
2. 适用于多种金属:等离子弧焊接适用于多种金属材料的连接,包括钢、铝、铜、镁和钛等。
3. 焊接速度快:由于等离子体具有高能量密度,因此可以实现较快的
焊接速度。
4. 易于自动化:由于等离子弧焊接可以实现较高的焊接速度和稳定性,因此易于自动化。
等离子弧焊接的缺点包括:
1. 设备成本高:等离子弧焊接设备成本较高,需要专门的设备和技术。
2. 操作难度大:由于等离子弧焊接需要精确控制电弧和等离子体的位
置和形状,因此操作难度较大。
3. 对环境要求高:等离子弧焊接过程中会产生大量的气体、光线和热量,对环境要求较高。
总之,等离子弧焊接是一种高能量密度、高质量、适用于多种金属材
料的连接技术。
虽然它具有一些缺点,但在某些情况下仍然是最优选择。
等离子弧焊工作方式及过程特点

等离子弧焊工作方式及过程特点等离子弧焊是利用等离子弧作为热源的焊接方法。
气体由电弧加热产生离解,在高速通过水冷喷嘴时受到压缩,增大能量密度和离解度,形成等离子弧。
它的稳定性、发热量和温度都高于一般电弧,因而具有较大的熔透力和焊接速度。
形成等离子弧的气体和它周围的保护气体一般用氩。
根据各种工件的材料性质,也有使用氦或氩氦、氩氢等混合气体的。
等离子弧有两种工作方式。
一种是“非转移弧”,电弧在钨极与喷嘴之间燃烧,主要用於等离子喷镀或加热非导电材料;另一种是“转移弧”,电弧由辅助电极高频引弧后,电弧燃烧在钨极与工件之间,用於焊接。
形成焊缝的方式有熔透式和穿孔式两种。
前一种形式的等离子弧只熔透母材,形成焊接熔池,多用於0.8~3毫米厚的板材焊接;后一种形式的等离子弧只熔穿板材,形成钥匙孔形的熔池,多用於3~12毫米厚的板材焊接。
此外,还有小电流的微束等离子弧焊,特别适合於0.02~1.5毫米的薄板焊接。
等离子弧焊接属于高质量焊接方法。
焊缝的深/宽比大,热影响区窄,工件变形小,可焊材料种类多。
特别是脉冲电流等离子弧焊和熔化极等离子弧焊的发展,更扩大了等离子弧焊的使用范围。
等离子弧焊与TIG焊十分相似,它们的电弧都是在尖头的钨电极和工件之间形成的。
但是,通过在焊炬中安置电极,能将等离子弧从保护气体的气囊中分离出来,随后推动等离子通过孔型良好的铜喷管将弧压缩。
通过改变孔的直径和等离子气流速度,可以实现三种操作方式:1、微束等离子:0.1~15A在很低的焊接电流下,材苁褂梦⑹?壤胱踊<词乖诨〕け浠?怀??0mm 时,柱状弧仍能保持稳定。
2、中等电流:15~200A在较大的15~200A电流下,等离子弧的过程特点与TIG弧相似,但由于等离子被压缩过,弧更加挺直。
虽然可提高等离子气流速度来增加焊接熔池的度深,但会造成在紊乱的保护气流中,混入空气和保护气体的风险。
3、小孔型等离子:大于100A通过增加焊接电流和等离子气流速度,可产生强有力的等离子束,与激光或电子束焊接一样,它能够在材料上形成充分的熔深。
等离子弧焊接
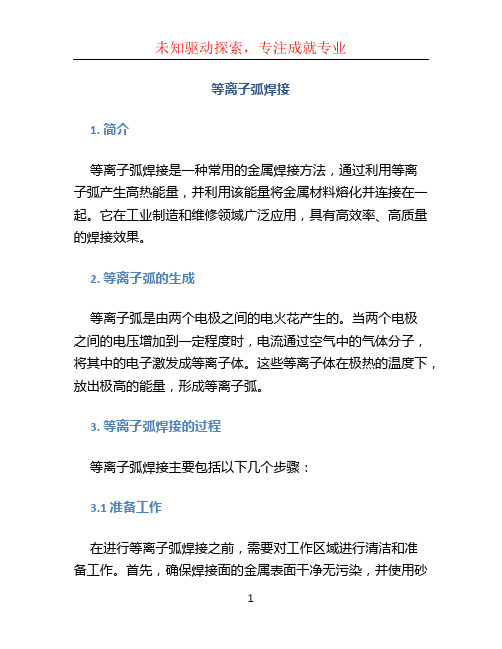
等离子弧焊接1. 简介等离子弧焊接是一种常用的金属焊接方法,通过利用等离子弧产生高热能量,并利用该能量将金属材料熔化并连接在一起。
它在工业制造和维修领域广泛应用,具有高效率、高质量的焊接效果。
2. 等离子弧的生成等离子弧是由两个电极之间的电火花产生的。
当两个电极之间的电压增加到一定程度时,电流通过空气中的气体分子,将其中的电子激发成等离子体。
这些等离子体在极热的温度下,放出极高的能量,形成等离子弧。
3. 等离子弧焊接的过程等离子弧焊接主要包括以下几个步骤:3.1 准备工作在进行等离子弧焊接之前,需要对工作区域进行清洁和准备工作。
首先,确保焊接面的金属表面干净无污染,并使用砂纸或钢丝刷将其清除。
其次,确定焊接电极和工件的位置和角度,并调整焊接设备的电流和电压设置。
3.2 弧焊接等离子弧焊接的焊接过程类似于其他电弧焊接方法。
在焊接之前,将焊接电极放置在待焊接的工件上,并确保其与工件之间的距离合适。
接下来,通过开启电源,产生弧光和电弧。
焊接电极在高温下熔化,并从中释放出等离子弧能量。
这种高温能量熔化金属表面并形成焊接点。
同时,焊接电极材料也会融化并与工件融合在一起。
焊接完成后,关闭电源,等离子弧消失。
焊接点逐渐冷却,形成强固的焊缝。
4. 等离子弧焊接的优势等离子弧焊接具有以下几个优势:•高效率:等离子弧焊接产生的高热能量可以迅速熔化金属,从而提高焊接速度和效率。
•高质量:由于等离子弧焊接的高热能量,焊接点通常具有较高的强度和质量。
•适用范围广:等离子弧焊接适用于各种金属材料的焊接,包括钢、铝、铜等。
•灵活性:等离子弧焊接可用于焊接不同形状和尺寸的工件,具有较高的适应性。
5. 应用领域等离子弧焊接在以下领域得到广泛应用:•车辆制造:汽车、火车等车辆的焊接加工。
•石油化工:石油、化工设备的焊接和修复。
•船舶制造:船舶的焊接、补焊和维修。
•金属结构:建筑结构、桥梁等金属结构的焊接。
6. 结论等离子弧焊接是一种高效率、高质量的金属焊接方法,通过利用等离子弧产生的高热能量,将金属材料熔化并连接在一起。
等离子弧焊接及切割的安全操作技术(二篇)

等离子弧焊接及切割的安全操作技术1.等离子弧焊接和切割用电源的空载电压较高,尤其在乎操作时,有电击妁危险。
因此:(1)电源在使用时必须可靠接地。
(2)焊枪枪体或割枪枪体与手触摸部分必须可靠绝缘。
(3)可以采用较低电压引燃非转移弧后再接通较高电压的转移弧回路。
(4)如果起动开关装在手把上,必须对外露开关套上绝缘橡胶管,避免手直接接触开关。
(5)等离子弧焊接和切割用喷嘴及电极的寿命相对较短,要经常更换,更换时要保证电源处于断开状态。
2.防电弧光辐射等离子弧较其他电弧的光辐射强度更大,尤其是紫外线强度,故对皮肤损伤严重,操作者在焊接和切割时必须戴上良好的面罩、手套,颈部也要保护。
面罩上除具有黑色目镜外,最好加上吸收紫外线的镜片。
自动操作时,可在操作者与操作区之间设置防护屏。
等离子弧切割时,可采用水下切割方法,利用水来吸收光辐射。
3.防高频和射线等离子弧焊接和切割都采用高频振荡器引弧,但高频对人体有一定的危害。
引弧频率选择在20~60kHz较为合适,还要求工件接地可靠,转移弧引弧后,立即可靠地切断高频振荡器电源。
等离子弧焊接和切割采用钍钨极时,同钨极氩弧焊一样,要注意射线的危害。
4.防灰尘和烟气等离子弧焊接和切割过程中伴随有大量气化的金属蒸气、臭氧、氮氧化物等。
尤其切割时,由于气体流量大,致使工作场地上的灰尘大量扬起,这些烟气和灰尘对操作工人的呼吸道、肺等产生严重影响。
因此要求工作场地必须配罩良好的通风设备措施。
切割时,在栅格工作台下方还可安置排风装置,也可以采取水中切割方法。
5.防噪声等离子弧会产生高强度、高频率的噪声,尤其采用大功率等离子弧切割时,其噪声更大,这对操作者的听觉系统和神经系统非常有害。
要求操作者必须戴耳塞,或可能的话,尽量采用自动化切割,使操作者在隔音良好的操作室内工作,也可以采取水中切割方法,利用水来吸收噪声。
等离子弧焊接及切割的安全操作技术(二)等离子弧焊接和切割是一种常用于金属加工的技术,在操作中需要遵循一系列安全操作技术,以确保操作者的人身安全和设备的正常运行。
- 1、下载文档前请自行甄别文档内容的完整性,平台不提供额外的编辑、内容补充、找答案等附加服务。
- 2、"仅部分预览"的文档,不可在线预览部分如存在完整性等问题,可反馈申请退款(可完整预览的文档不适用该条件!)。
- 3、如文档侵犯您的权益,请联系客服反馈,我们会尽快为您处理(人工客服工作时间:9:00-18:30)。
穿孔等离子弧焊接技术研究* 中航一集团625所 朱轶峰 张 慧 董春林 邵亦陈 文摘论述了等离子弧焊接的新进展,介绍一脉一孔的等离子弧焊接工艺、正面弧光传感器、焊接质量模糊控制系统以及采用该系统进行的焊接质量控制的初步试验结果。
研究表明在不锈钢等离子弧焊接过程中,采用该系统可以提高等离子弧焊接焊缝的质量。
主题词等离子弧焊一脉一孔弧光传感模糊控制1 引言进入21世纪,航空航天制造业对焊接技术提出了更高要求,人们在追求低成本高强度的焊接结构时对穿孔等离子弧焊接产生了新的兴趣。
等离子弧能量密度高、射流速度大、等离子流力强 [1],穿孔等离子弧焊接(K-PAW)时等离子弧穿透工件形成小孔,随着小孔的弥合形成焊缝。
对于国防工业中常用金属材料如高强钢、高温合金、钛合金、不锈钢等,在中厚度(3∼10mm)范围与钨极氩弧焊相比,PAW具有更佳的工艺焊接性,接头内部缺陷率降低、焊件变形减小、焊接效率提高。
“单面焊接双面成形”是K-PAW的典型特征,特别适合密闭容器、小直径管焊缝等背面难于施焊的结构件焊接。
但是穿孔等离子弧焊接过程的稳定性及焊接工艺参数的再现性始终是摆在焊接科研人员面前的难题,制约着等离子弧焊接技术的工程应用。
本研究通过采用优化工艺参数、脉冲焊接工艺方式以及增加质量控制的手段提高等离子弧焊接的工艺裕度、提高离子弧焊接过程的稳定性。
2 试验系统建立一个能够满足焊接试验、参数实时采集、实时控制的完整的试验系统,是本研究课题的基础。
2.1 焊接电源目前国内使用的等离子弧焊接电源中,以晶体管、可控硅电源为主,新型的IGBT电源还处于研究阶段,电源输出的稳定性难以保证,成为影响焊接质量稳定性的因素之一。
同时考虑到逆变电源的控制响应时间较快等因素,选用进口的等离子焊接电源及焊枪,逆变频率可达 32kHz,能够提供较好的输出特性,便于实现自动焊。
2.2 焊接夹具自动等离子弧焊接工艺对焊接夹具的压紧均匀性、焊缝对中有一定要求,为此我们自行设计研制了具有琴键式压紧纵缝、机械对中装置的LCAW-2型纵缝和环缝自动焊机。
2.3 焊接质量模糊控制单元利用具有内置模糊控制模块的可编程控制器,开发了外围数字接口电路,结合奔腾133计算机,再加上我们开发的模糊控制规则表,形成了质量模糊控制单元。
模糊控制系统执行机构为焊接电流控制器与焊接速度控制器。
尽管影响等离子焊接焊缝成型质量的参数有很多,考虑到焊接电流和焊接速度对等离子焊接熔池的体积、温度及弧柱压力均有收稿日期:2001-12-04*本课题被评为2000年度国防科技进步二等奖2223比较明显的影响,且信号响应惯性小,因此系统的控制对象选择为焊接电流和焊接速度两个参量,这样的控制系统响应速度快。
3 试验方案 首先通过工艺试验确定加脉冲的时间及脉冲电流的大小、维持时间,达到“一脉一孔”断续穿孔焊的效果,并与数值计算结合进行理论分析,确定工艺参数及控制模型,建立一套脉冲等离子弧焊适应控制系统。
3.1 传感器的选择熔池小孔行为的传感方法有多种,如尾焰导电法、尾焰光电法、背面麦克风声频信号检测法,均可以准确地反映出小孔的有无,并在生产中得到一定范围的应用,但也存在相同的局限性,即传感元件需要放置在焊件背面。
正面弧光传感,体积小、结构简单、信号响应速度快、抗干扰能力强,颇具工程应用潜力。
在穿孔等离子弧焊过程中,小孔的形成、闭合及尺寸变化都将改变等离子弧的物理状态和性能参数,如宏观形态、电弧弧长、能量密度、射流速度等,电弧辐射作为电弧能量传递重要方式之一,直观地表达了等离子弧能量与质量的微观输运机制。
3.2 控制方案的确定由于焊接过程通常表现为一些复杂的非线性系统,难以建立准确的数学模型,因此已不能采用传统的控制方法进行控制。
模糊控制技术是运用模糊集合理论中的推理规则,对工程技术的各种参量实施控制的一种方法。
由于它基于熟练操作者的经验知识库进行控制,且不需要建立数学模型,因此在等离子焊接的过程中采用模糊控制技术对焊缝成型质量进行控制就更显其优越性。
等离子焊接的模糊控制系统主要由模糊控制器、弧光传感器及信号处理器、D/A 转换电路、A/D 转换电路、执行机构、“给定”值设定等七部分组成。
工作原理是:根据不同的焊接对象(焊接材料和焊接厚度等)经通讯面板来 “给定”信号,并利用通讯面板监视控制过程的状态,利用弧光传感器对等离子焊接的正面弧光信号进行检测,其检测信号经过二次信号处理后通过A/D 转换器送至模糊控制器进行处理,模糊控制器的输出通过D/A 转换器送至执行机构进行驱动控制。
控制信号通过控制面板输入到S7300系统,动作命令信号送至执行机构,从而形成一套完整的实时控制系统(图1)进行在线检测和控制,来控制等离子焊接的焊缝成型质量。
4 研究过程 4.1 脉冲等离子弧焊接工艺对于穿孔等离子弧焊接,有利于熔池金属平衡的条件有两个:一是匙孔直径尽可能小;二是焊缝根部与熔池上部凝固时间与空间的偏差尽可能大。
而影响匙孔直径的因素有:焊嘴的孔道比、钨极直径与钨极尖端形状、钨极内缩量、焊接电流、离子气与保护气流量等。
影响焊缝根部与熔池上部凝固时间与空间的偏差的因素有:工件的冷却条件、电弧输入工件的能量控制。
而控制热输入量的最有效途径就是采用脉冲焊方式。
脉冲等离子弧焊的热输入线能量公式为: ()vT T I T I U Q b b p p ×⋅+⋅×=其中:I p 为脉冲电流,是保证焊透和焊缝成形的主要参数之一,T p 为脉冲持续时间,I b图1 等离子焊接模糊控制系统的组成24 为基值电流,直接影响焊缝的熔宽及焊缝的截面积,T b 为基值电流持续时间,T 为脉冲周期。
脉冲等离子弧焊的工艺规范参数还有通断比λt 、脉冲频率f 。
通断比增大时,热输入量增加,熔宽及焊缝截面增大;通断比减小时,热输入量减少,一般所用的通断比为 0.5~1.2 之间。
脉冲频率f ,对焊缝成形尺寸影响不大,脉冲频率一般随焊接速度的增加作相应的增加,以保证相邻两个脉冲所形成的熔池连续。
脉冲频率过低,焊缝的连续性差,焊缝表面的鱼鳞粗糙;脉冲频率过高,则近于普通等离子弧焊,生产中一般采用f =1~5Hz 。
脉冲等离子弧焊接的特点:a.输入功率可精确控制;b.线能量减少,工件变形小,适于对热敏感材料的焊接;c.电流脉冲功能可以充分搅拌熔池,有利于氧化膜的破碎及焊缝气体的逸出;d.有效克服双弧,使焊接过程稳定。
连续穿孔焊时要求焊接全过程中匙孔持续存在,电弧输入熔池的热输入量较大,熔池根部熔宽过大;而采用“一脉一孔”的脉冲等离子弧焊接工艺,可以限制熔池根部熔宽, 提高根部基体金属对熔池的约束作用,使熔池稳定。
所谓“一脉一孔”,就是在每一个脉冲周期内,焊接电弧作用于待焊接头金属处形成的匙孔出现并闭合一次,即在峰值电流期间形成匙孔属于穿孔焊,在基值电流期间匙孔闭合属于熔化焊。
其技术难点在于如何选择恰当的电流参数及合理匹配通断比(T p /T b )。
利用优化焊接参数进行了脉冲等离子弧焊接试验。
图2是检测的焊接过程中匙孔的形成、闭合时同步采集的尾焰电压与焊接电流对应关系。
从图中可以看出,在穿孔型脉冲等离子弧焊接过程中,焊接电弧的尾焰电压在焊接电流峰值达到最大,说明此时匙孔径最大;在焊接电流基值尾焰电压为零,说明匙孔闭合。
在每一个脉冲焊接周期内,匙孔各产生与闭合一次,实现了“一脉一孔”的脉冲等离子焊接工艺。
[2] 4.2 弧光传感的研究弧光传感器是一种接收弧光并将弧光辐射信息转化为电信号的装置。
4.2.1 弧光传感的物理模型弧光传感的物理本质在于从光电器件接收的源于焊接电弧的辐射信息中获取表征熔池小孔行为的信号。
将焊接电弧看作为辐射源,光电器件的接收面看作为探测器的接收面,并分别简化为平面,这样可以将弧光传感过程简化为自辐射源(电弧)到探测器接收平面(光电器件)光能的传输与转换过程,如图3所示。
图中:L λ —— 辐射源单位面积元光谱辐射亮度;θS —— 辐射源面积元dA S 法线n 与两面积元中心连线OO'的夹角;d Ω —— 自辐射源看接收单位面积元dA D 所张单位立体角;θD —— 探测器接收平面单位面积元法线n'与中心连线OO'的夹角;r —— 中心连线 OO'之间的距离。
尾焰电压/V焊接电压/V焊接电流/A采 样 点 数图2 尾焰电压检测焊接过程匙孔的行为 图3 弧光传感过程示意图 25传感的物理模型可表示为:λλλθαλλλλλd L K K r S K U m m D )()(cos 2120∫∆+∆−⋅⋅⋅= 该式定性地表达了等离子弧的光谱辐射亮度L λ与光电器件输出电压U 0之间的关系。
通常,光电器件的光谱响应特性修正因子K 2(λ)、干涉滤光镜片的主要参数等固定不变,则随着等离子弧的光谱辐射亮度L λ的升高,辐射源面积S 加大,辐射源与接收探头之间的距离r 降低,弧光传感器输出信号U 0升高。
[4]4.2.2 熔池小孔特征行为的弧光传感穿孔等离子弧焊焊接过程包括小孔的形成、小孔尺寸的稳定保持、闭合。
借助于光谱分析测试系统,研究焊接过程中当熔池小孔发生特征变化时,等离子弧发射光谱的变化规律;随后,利用研制的弧光传感系统,获取弧光辐射信号,分析其特征及特征信号形成机制。
通常恒流等离子弧焊接过程分为三个阶段:起弧、焊接、收弧。
在起弧阶段,小孔建立,此时焊接电流和离子气流量不断升高;在焊接阶段,小孔保持稳定状态;在收弧阶段,小孔闭合,焊接电流和离子气流量缓降。
显然,在小孔形成与闭合阶段,等离子弧辐射强度的变化必然包含着焊接规范参数的影响作用因素。
穿孔等离子弧焊所面临的主要问题在于焊接过程的不稳定性,电弧的稳定性和焊缝成形的稳定性易于受到破坏。
而影响焊接过程稳定性的因素包括焊接规范参数,及如工件散热条件的变化、材料不均质的影响、网压波动等等。
实际生产时,纵缝穿孔等离子弧焊在起、收弧板上开始或结束焊接程序。
因而,在焊接阶段,测试并分析小孔发生特征变化时的电弧辐射强度信号,对保证焊接质量具有更加重要的意义。
上图为4mm 厚1Cr18Ni9Ti 不锈钢平板铺焊时获得的试验结果。
焊接速度为300mm/min ,离子气流量为1.4LPM ,正面保护气流量为6.0LPM ,均为工业纯氩。
在前32秒,从焊接起弧阶段进入到焊接阶段,小孔建立并保持稳定,焊接过程也比较稳定,之后小孔突然消失,间隔约5秒后,小孔再度建立。
在焊接过程中并未人为改变焊接规范参数,也未调整焊枪,却出现了小孔突然闭合的现象,显示了穿孔等离子弧焊焊接过程不稳定性。
小孔稳定存在时,等离子弧发射光谱辐射强度信号比较平稳,而当小孔闭合以及间隔约5秒后小孔重新建立时,光谱测试系统检测得到的谱线相对辐射强度信号发生了负脉冲式的显著跃变,与发生在焊接起弧阶段和收弧阶段的谱线辐射强度信号的负脉冲跃变特征相同。