生料立磨LV选粉机技术改造节能体会
生料立磨系统节能降耗技术改造探讨
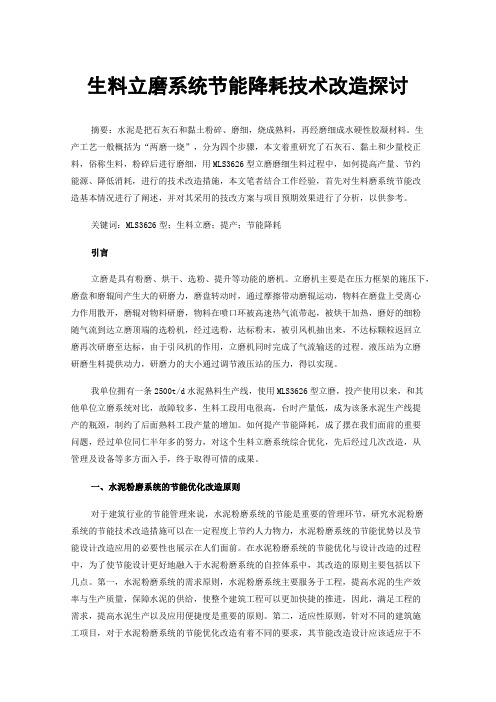
生料立磨系统节能降耗技术改造探讨摘要:水泥是把石灰石和黏土粉碎、磨细,烧成熟料,再经磨细成水硬性胶凝材料。
生产工艺一般概括为“两磨一烧”,分为四个步骤,本文着重研究了石灰石、黏土和少量校正料,俗称生料,粉碎后进行磨细,用MLS3626型立磨磨细生料过程中,如何提高产量、节约能源、降低消耗,进行的技术改造措施,本文笔者结合工作经验,首先对生料磨系统节能改造基本情况进行了阐述,并对其采用的技改方案与项目预期效果进行了分析,以供参考。
关键词:MLS3626型;生料立磨;提产;节能降耗引言立磨是具有粉磨、烘干、选粉、提升等功能的磨机。
立磨机主要是在压力框架的施压下,磨盘和磨辊间产生大的研磨力,磨盘转动时,通过摩擦带动磨辊运动,物料在磨盘上受离心力作用散开,磨辊对物料研磨,物料在喷口环被高速热气流带起,被烘干加热,磨好的细粉随气流到达立磨顶端的选粉机,经过选粉,达标粉末,被引风机抽出来,不达标颗粒返回立磨再次研磨至达标,由于引风机的作用,立磨机同时完成了气流输送的过程。
液压站为立磨研磨生料提供动力,研磨力的大小通过调节液压站的压力,得以实现。
我单位拥有一条2500t/d水泥熟料生产线,使用MLS3626型立磨,投产使用以来,和其他单位立磨系统对比,故障较多,生料工段用电很高,台时产量低,成为该条水泥生产线提产的瓶颈,制约了后面熟料工段产量的增加。
如何提产节能降耗,成了摆在我们面前的重要问题,经过单位同仁半年多的努力,对这个生料立磨系统综合优化,先后经过几次改造,从管理及设备等多方面入手,终于取得可惜的成果。
一、水泥粉磨系统的节能优化改造原则对于建筑行业的节能管理来说,水泥粉磨系统的节能是重要的管理环节,研究水泥粉磨系统的节能技术改造措施可以在一定程度上节约人力物力,水泥粉磨系统的节能优势以及节能设计改造应用的必要性也展示在人们面前。
在水泥粉磨系统的节能优化与设计改造的过程中,为了使节能设计更好地融入于水泥粉磨系统的自控体系中,其改造的原则主要包括以下几点。
立磨助力水泥降本又增效

立磨助力水泥降本又增效第一篇:立磨助力水泥降本又增效立磨助力水泥业降本又增效据悉,在有关部门多方面采取措施化解产能过剩压力的同时,水泥行业开始寻求“自救”。
北京、天津、山东、河北、山西、河南等地的水泥行业协会于2014年12月27日曾在济南发布《泛华北地区水泥企业错峰生产自律公约》,明确表示2015年1月15日至3月15日,上述地区的水泥企业将陆续“停窑”,在两个月的时间里实行错峰生产。
据相关人士介绍,由于北方冬季施工量减少,水泥用量锐减,水泥企业在冬季只生产水泥熟料,俗称“熟料冬储”,到来年春暖施工季节再粉磨水泥销售,这不仅占用了大量的企业生产周转资金,更加剧了冬季北方地区的空气污染。
当前,在东北、华北、西北地区水泥产能总体严重过剩的情况下,市场恶性竞争不断,已经出现企业生产越多,亏损越多的现象。
水泥行业是一个能源大量消耗的行业,而我国水泥消耗量以10%的速度递增,水泥行业是我国节能减排重点行业。
当前我国水泥行业结构性产能过剩问题较为突出,水泥行业的产品结构目前仍是低标号普通水泥占主导地位,中、低档水泥产品过剩,而高档、优化的水泥产品却存在较大的缺口。
目前,我国的水泥生产企业有两大类:一类是传统的小生产企业,这类企业由于采用的生产线设备、技术、工艺和配套环保设备等相对落后,导致水泥跑漏量较大、大气污染物排放量等无法满足当前国家对大气污染物限值排放标准的要求,而这部分小、多、散、弱的落后水泥产能将是国家“十二五”规划中“淘汰落后产能,加快产业整体升级”的重点;另一类是新型的现代化大型水泥集团,这类生产企业主要采用新型干法水泥熟料生产线、余热发电等先进技术,实现了产业技术的升级,其已建、在建和新建的水泥行业生产线需要配臵的除尘设备一直是公司袋式除尘设备的主要目标市场之一。
淘汰落后产能是近年水泥行业政策的重点之一,是国家加快行业结构调整、实现节能减排的重要手段。
根据《水泥工业“十二五”发展规划》,“十二五”期间完成2.5亿吨落后产能(主要指水泥熟料)淘汰任务。
生料立磨系统节能降耗技术改造
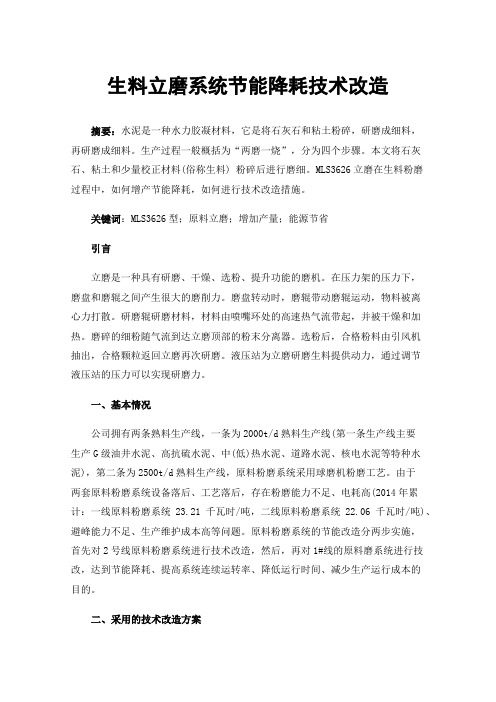
生料立磨系统节能降耗技术改造摘要:水泥是一种水力胶凝材料,它是将石灰石和粘土粉碎,研磨成细料,再研磨成细料。
生产过程一般概括为“两磨一烧”,分为四个步骤。
本文将石灰石、粘土和少量校正材料(俗称生料) 粉碎后进行磨细。
MLS3626立磨在生料粉磨过程中,如何增产节能降耗,如何进行技术改造措施。
关键词:MLS3626型;原料立磨;增加产量;能源节省引言立磨是一种具有研磨、干燥、选粉、提升功能的磨机。
在压力架的压力下,磨盘和磨辊之间产生很大的磨削力。
磨盘转动时,磨辊带动磨辊运动,物料被离心力打散。
研磨辊研磨材料,材料由喷嘴环处的高速热气流带起,并被干燥和加热。
磨碎的细粉随气流到达立磨顶部的粉末分离器。
选粉后,合格粉料由引风机抽出,合格颗粒返回立磨再次研磨。
液压站为立磨研磨生料提供动力,通过调节液压站的压力可以实现研磨力。
一、基本情况公司拥有两条熟料生产线,一条为2000t/d熟料生产线(第一条生产线主要生产G级油井水泥、高抗硫水泥、中(低)热水泥、道路水泥、核电水泥等特种水泥),第二条为2500t/d熟料生产线,原料粉磨系统采用球磨机粉磨工艺。
由于两套原料粉磨系统设备落后、工艺落后,存在粉磨能力不足、电耗高(2014年累计:一线原料粉磨系统23.21千瓦时/吨,二线原料粉磨系统22.06千瓦时/吨)、避峰能力不足、生产维护成本高等问题。
原料粉磨系统的节能改造分两步实施,首先对2号线原料粉磨系统进行技术改造,然后,再对1#线的原料磨系统进行技改,达到节能降耗、提高系统连续运转率、降低运行时间、减少生产运行成本的目的。
二、采用的技术改造方案具体技术改造思路如下:2.1拟在原1#原料磨车间南侧对面的空白场增设一套HFCG160-140辊压机+HFV4000空气分级机+高效分级机组成独立机架,充分利用原球磨机系统中的废气处理设备,组成新的辊压机终磨系统。
根据同利公司提供的原料及配比可磨性试验结果,方案技术改造完成后,原料粉磨系统能力220t/h,单位产品电耗~ 14.0 kwh/t(从原料配料到原料入库);2.2拟在原2#原料磨车间南侧对面的空白场增设一套HFCG160-140辊压机+HFV4000空气分级机组成独立机架,充分利用原球磨机系统中的风道、选粉、废气处理设备及土建设施,组成新的辊压机终磨系统。
水泥厂立磨个人工作总结
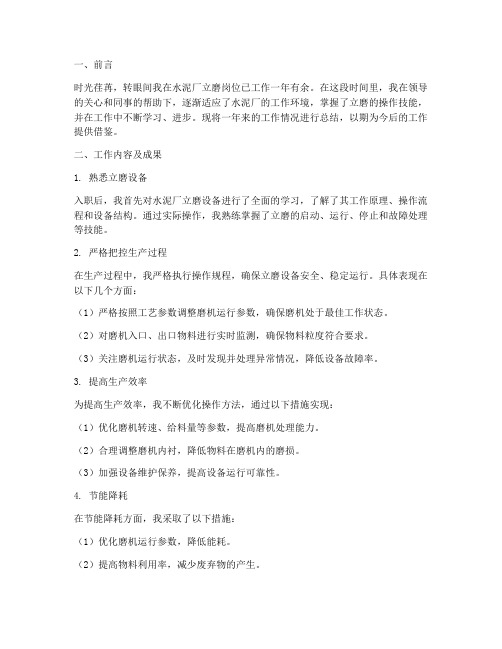
一、前言时光荏苒,转眼间我在水泥厂立磨岗位已工作一年有余。
在这段时间里,我在领导的关心和同事的帮助下,逐渐适应了水泥厂的工作环境,掌握了立磨的操作技能,并在工作中不断学习、进步。
现将一年来的工作情况进行总结,以期为今后的工作提供借鉴。
二、工作内容及成果1. 熟悉立磨设备入职后,我首先对水泥厂立磨设备进行了全面的学习,了解了其工作原理、操作流程和设备结构。
通过实际操作,我熟练掌握了立磨的启动、运行、停止和故障处理等技能。
2. 严格把控生产过程在生产过程中,我严格执行操作规程,确保立磨设备安全、稳定运行。
具体表现在以下几个方面:(1)严格按照工艺参数调整磨机运行参数,确保磨机处于最佳工作状态。
(2)对磨机入口、出口物料进行实时监测,确保物料粒度符合要求。
(3)关注磨机运行状态,及时发现并处理异常情况,降低设备故障率。
3. 提高生产效率为提高生产效率,我不断优化操作方法,通过以下措施实现:(1)优化磨机转速、给料量等参数,提高磨机处理能力。
(2)合理调整磨机内衬,降低物料在磨机内的磨损。
(3)加强设备维护保养,提高设备运行可靠性。
4. 节能降耗在节能降耗方面,我采取了以下措施:(1)优化磨机运行参数,降低能耗。
(2)提高物料利用率,减少废弃物的产生。
(3)加强设备维护,降低设备故障率,降低维修成本。
三、工作不足及改进措施1. 工作经验不足在立磨操作过程中,我发现自己在处理突发事件和复杂问题时,经验不足。
为改进这一问题,我将加强以下方面的学习:(1)参加相关培训,提高自己的专业技能。
(2)多向经验丰富的同事请教,学习他们的操作技巧。
2. 节能降耗意识有待提高在节能降耗方面,我还有很大的提升空间。
为改进这一问题,我将:(1)加强环保意识,从自身做起,节约能源。
(2)关注行业动态,学习先进的节能技术。
四、展望未来在今后的工作中,我将继续努力,提高自己的业务水平,为水泥厂的发展贡献自己的力量。
具体表现在以下方面:1. 深入学习立磨设备知识,提高操作技能。
水泥立磨节能环保 性能电耗均优于球磨机

更多详情参考水泥立式磨机水泥立磨节能环保性能电耗均优于球磨机近年来,新型干法水泥的生产工艺日渐成熟,所使用的水泥粉磨设备和技术也有了较大发展。
原先水泥粉磨生产使用的是球磨机,现在大部分厂家的设备都已经更新换代,变成了立式磨、梯形磨等磨粉机。
但是传统粉磨系统产生的电耗可以占比整个水泥生产综合电耗的65%-70%,对于企业来说,寻求挖掘节能的粉磨设备已成为发展水泥行业的重要方向。
而在各个粉磨系统中,立式磨机的节能效果备受用户厂家的关注和好评。
水泥立磨作为一种新型、高效、节能的粉磨设备,是今后水泥生产中的主流设备,必将得到更大的发展和推广应用。
对于这个观点,中国水泥网高级顾问高长明在《立磨在我国水泥工业的应用历程回顾》文章中表示赞同,他表示,在水泥粉磨方面,立式磨机的节能型、水泥产能、系统设备总重、系统装机容量、单位装机容量等方面的综合优势注定了其必将取代传统球磨机的客观发展规律。
很多传统水泥企业对于水泥立磨的认识不足,认为所谓的立磨水泥,其性能比球磨水泥的“差”,发达国家经研究后发现,实际上,这个问题的实质是因立磨水泥的出现,水泥企业、商品混凝土企业与施工企业之间需要有一个相互协调、磨合适应的过程,属于科技进步中出现的新问题,完全可以妥善解决或承受的。
而根据国外的有关研究试验与大量的生产实践结果表明,对每一台具体的水泥立磨来说,其所生产的水泥与更多详情参考水泥立式磨机更多详情参考水泥立式磨机市场之间相互协调的磨合期,一般约3个月,最多不会超过6个月,所以实际上是一个国外早已发生过而且已经解决了的问题。
国内的水泥行业并不能因为这个误解而就此否定了水泥立磨。
立磨www.momeis 立式磨机www.mo meishe bei.co但是当初引进立磨进入国内市场的时候,虽然国外的使用技术已经相当成熟,国内的立磨使用情况却很不乐观,多数厂家反映效果不好,这其实更多详情参考水泥立式磨机是初期引入仿制的国外设备时未掌握核心技术所致,因而当时很多厂商都弃用立磨,重新用回老机器球磨机。
生料磨的学习心得
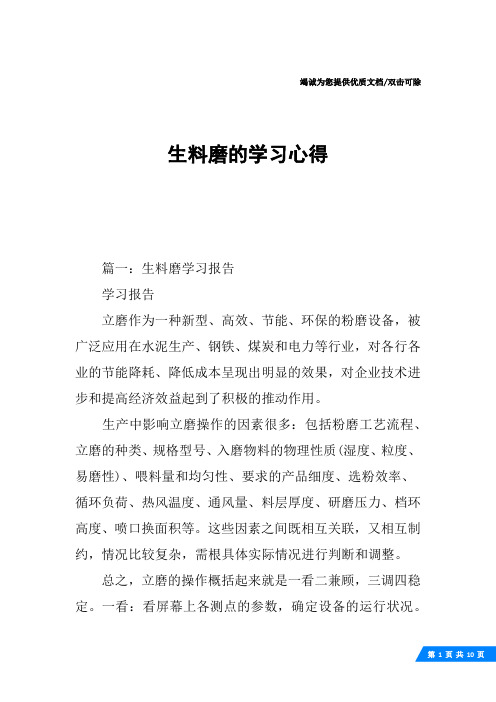
竭诚为您提供优质文档/双击可除生料磨的学习心得篇一:生料磨学习报告学习报告立磨作为一种新型、高效、节能、环保的粉磨设备,被广泛应用在水泥生产、钢铁、煤炭和电力等行业,对各行各业的节能降耗、降低成本呈现出明显的效果,对企业技术进步和提高经济效益起到了积极的推动作用。
生产中影响立磨操作的因素很多:包括粉磨工艺流程、立磨的种类、规格型号、入磨物料的物理性质(湿度、粒度、易磨性)、喂料量和均匀性、要求的产品细度、选粉效率、循环负荷、热风温度、通风量、料层厚度、研磨压力、档环高度、喷口换面积等。
这些因素之间既相互关联,又相互制约,情况比较复杂,需根具体实际情况进行判断和调整。
总之,立磨的操作概括起来就是一看二兼顾,三调四稳定。
一看:看屏幕上各测点的参数,确定设备的运行状况。
二兼顾:窑磨的拉风要兼顾;增湿塔与磨内喷水量要兼顾。
三调:调风(风温的高低,风量的大小);调料(喂料的大小,原料的配比);调研磨压力。
四稳定:稳定料层的厚度;稳定磨机的振动值;稳定磨内的压差;稳定产品的质量。
压差的控制。
压差是立磨操作的核心参数,它直接反应磨内循环物料量的大小,压差稳定标志着入磨物料量和出磨物料量趋于平衡,磨机运转正常。
当压差上升说明入磨物料量大于出磨物料量,内循环量增加,整个系统的通风阻力增大。
当压差下降说明入磨物料量小于出磨物料量,内循环降低,料层厚度变薄。
以上两种情况都是料层不稳定的现象,均可引起磨机振动、主电机电流波动、进出口压力变化。
通常我们以调整喂料量、通风量、选粉机转速、喷水量的方式来控制压差。
料层厚度的控制。
合适的料层厚度、稳定的料床是立磨粉磨的基础,也是立磨操作的关键。
料层的厚度受研磨压力、喂料量、喷水、风量、风速、物料性能等各种参数的影响。
料层厚度较薄时可采取的措施有:(1)增加磨内喷水;(2)降低研磨压力;(3)适当增加喂料量;(4)提高选粉机转数,增加磨内物料循环量。
若料层较厚时,则反之。
研磨压力的控制。
生料粉磨节能降耗实践
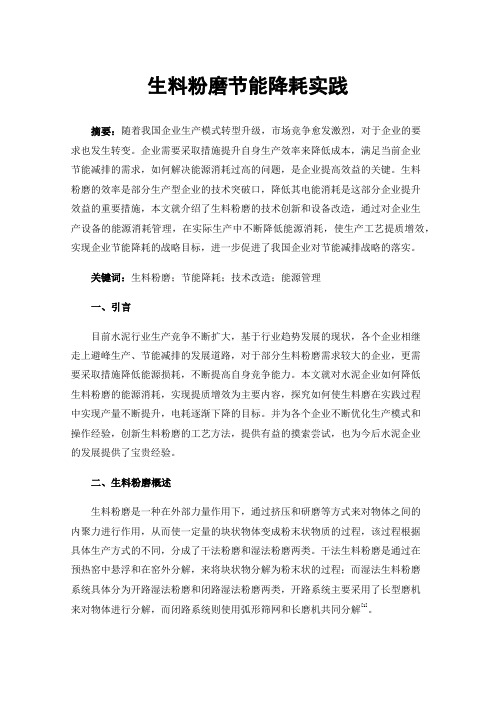
生料粉磨节能降耗实践摘要:随着我国企业生产模式转型升级,市场竞争愈发激烈,对于企业的要求也发生转变。
企业需要采取措施提升自身生产效率来降低成本,满足当前企业节能减排的需求,如何解决能源消耗过高的问题,是企业提高效益的关键。
生料粉磨的效率是部分生产型企业的技术突破口,降低其电能消耗是这部分企业提升效益的重要措施,本文就介绍了生料粉磨的技术创新和设备改造,通过对企业生产设备的能源消耗管理,在实际生产中不断降低能源消耗,使生产工艺提质增效,实现企业节能降耗的战略目标,进一步促进了我国企业对节能减排战略的落实。
关键词:生料粉磨;节能降耗;技术改造;能源管理一、引言目前水泥行业生产竞争不断扩大,基于行业趋势发展的现状,各个企业相继走上避峰生产、节能减排的发展道路,对于部分生料粉磨需求较大的企业,更需要采取措施降低能源损耗,不断提高自身竞争能力。
本文就对水泥企业如何降低生料粉磨的能源消耗,实现提质增效为主要内容,探究如何使生料磨在实践过程中实现产量不断提升,电耗逐渐下降的目标。
并为各个企业不断优化生产模式和操作经验,创新生料粉磨的工艺方法,提供有益的摸索尝试,也为今后水泥企业的发展提供了宝贵经验。
二、生料粉磨概述生料粉磨是一种在外部力量作用下,通过挤压和研磨等方式来对物体之间的内聚力进行作用,从而使一定量的块状物体变成粉末状物质的过程,该过程根据具体生产方式的不同,分成了干法粉磨和湿法粉磨两类。
干法生料粉磨是通过在预热窑中悬浮和在窑外分解,来将块状物分解为粉末状的过程;而湿法生料粉磨系统具体分为开路湿法粉磨和闭路湿法粉磨两类,开路系统主要采用了长型磨机来对物体进行分解,而闭路系统则使用弧形筛网和长磨机共同分解[1]。
根据生料粉磨系统粉末装备的形式可以分为三类系统:辊式粉磨系统、钢球粉磨系统和无介质粉磨系统。
其中,在水泥行业应用较多的是钢球式粉磨系统,其能够更好的应用于水泥介质的分解,而近年来,随着立式磨的不断发展,使得其他两种粉磨应用较少,尤其是对无介质磨的影响较大,使得其应用逐年减少。
生料辊压机终粉磨系统节能技改实践
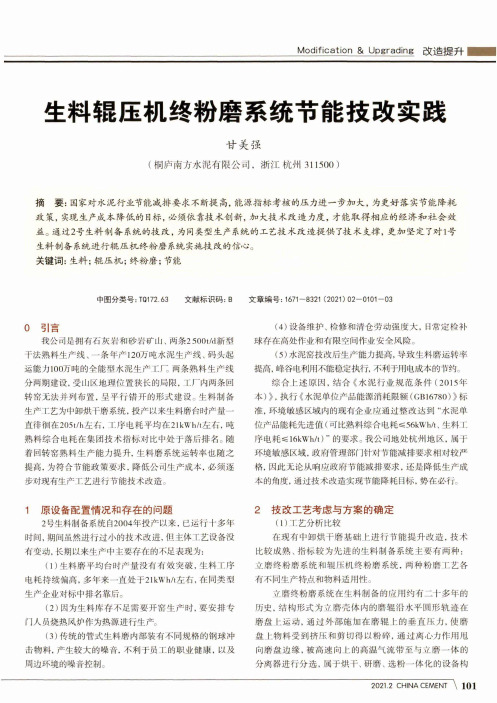
M o d ific a tio n& U pgrading 改造提升霱生料辊压机终粉磨系统节能技改实践甘美强(桐庐南方水泥有限公司,浙江杭州311500 )摘要:国家对水泥行业节能减排要求不断提高,能源指标考核的压力进一步加大,为更好落实节能降耗政策,实现生产成本降低的目标,必须依靠技术创新,加大技术改造力度,才能取得相应的经济和社会效益。
通过2号生料制备系统的技改,为同类型生产系统的工艺技术改造提供了技术支撑,更加坚定了对1号生料制备系统进行辊压机终粉磨系统实施枝改的信心。
关键词:生料;辊压机;终粉磨;节能中图分类号:TQ172.63 文献标识码:B文章编号:1671 —8321 (2021) 02—0101—030引言我公司是拥有石灰岩和砂岩矿山、两条2 500tM新型干法熟料生产线、一条年产120万吨水泥生产线、码头起运能力100万吨的全能型水泥生产工厂。
两条熟料生产线分两期建设,受山区地理位置狭长的局限,工厂内两条回转窑无法并列布置,呈平行错开的形式建设。
生料制备生产工艺为中卸烘干磨系统,投产以来生料磨台时产量一直徘徊在205t/h左右,工序电耗平均在21kWh/t左右,吨熟料综合电耗在集团技术指标对比中处于落后排名。
随着回转窑熟料生产能力提升,生料磨系统运转率也随之提高,为符合节能政策要求,降低公司生产成本,必须逐步对现有生产工艺进行节能技术改造。
1原设备配置情况和存在的问题2号生料制备系统自2004年投产以来,已运行十多年时间,期间虽然进行过小的技术改进,但主体工艺设备没有变动,长期以来生产中主要存在的不足表现为:(1)生料磨平均台时产量没有有效突破,生料工序 电耗持续偏高,多年来一直处于21kWh/t左右,在同类型生产企业对标中排名靠后。
(2)因为生料库存不足需要开窑生产时,要安排专 门人员烧热风炉作为热源进行生产。
(3) 传统的管式生料磨内部装有不同规格的钢球冲 击物料,产生较大的噪音,不利于员工的职业健康,以及周边环境的噪音控制。
生料立磨系统节能降耗技术改造

生料立磨系统节能降耗技术改造广西鱼峰水泥股份有限公司第四条生产线为2 500t/d水泥生产线,在生料制备加工过程中主要采用立磨终粉磨系统,其中主要设备配置是TLM384四辊立磨,在设计阶段需要达到台时产量为210 t/h,实际功率值是2 100 kW,电流为252 A;循环风量为420 000 m3/h,全压是10 000 Pa,电流为188 A。
自2021年建成投产以来,立磨系统运行稳定,但长期存在生料工序电耗高的问题。
影响生料工序电耗的主要设备为循环风机和立磨主电机,因此公司技术人员开始摸索降低立磨主电机电流和循环风机电耗,达到进一步降低生料工序电耗的目的。
1 能耗高的原因(1)生料立磨喂料系统采用三道锁风阀,其液压传动的故障率较高,经常会出现阀板磨损、非传动侧轴承损坏等问题,漏风率较高,需要及时进行拉风,循环风机接近在额定转速下运行,导致系统电能消耗不断加大,情况严重时还会对磨机基本产量造成影响,持续扩大电能消耗。
(2)正常生产时,磨内不同部位因长期受到块状物料磨损和高速气流携带的粉末颗粒的冲蚀磨损,磨盘、磨辊磨损严重,料层厚度相对提高,导致主电机电流上升。
2 技术革新2.1 生料立磨喂料系统改造针对现有立磨喂料系统三道锁风阀锁存在的弊端(如图1所示),磨头锁风决定采用料封方式进行锁风,生料立磨入料口的锁风通过物料自身的锁风实现,喂料设备本身不再考虑锁风,只起到输送物料的作用。
从配料库底输送过来的已经搭配好的物料,先进入一个新设的20 t容量的过渡小仓,过渡小仓内的物料通过仓底新设的板式喂料机喂入生料立磨,取消原来的三道锁风阀喂料装置,过渡小仓仓底至立磨的入料溜子通过一个全封闭罩子连接。
在立磨正常运行的过程中,过渡小仓的仓重与原料库底的配料皮带进行联锁,使过渡小仓内始终留有6~8 t的物料,通过这部分物料实现立磨入料口锁风(如图2所示)。
2.2 挡料圈技改立磨主电机电流主要受研磨压力和料层厚度的影响,而研磨压力主要与原材料易磨性有关,相对不可控,因此考虑通过降低料层厚度减小立磨主电机电流。
水泥粉磨系统节能优化技术改造探讨
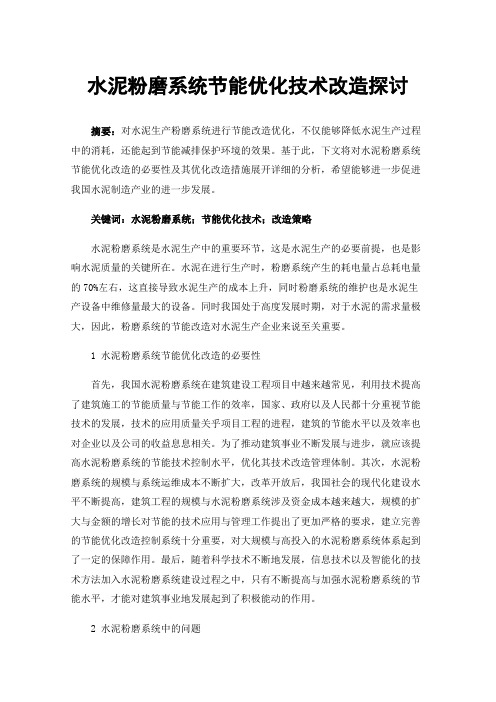
水泥粉磨系统节能优化技术改造探讨摘要:对水泥生产粉磨系统进行节能改造优化,不仅能够降低水泥生产过程中的消耗,还能起到节能减排保护环境的效果。
基于此,下文将对水泥粉磨系统节能优化改造的必要性及其优化改造措施展开详细的分析,希望能够进一步促进我国水泥制造产业的进一步发展。
关键词:水泥粉磨系统;节能优化技术;改造策略水泥粉磨系统是水泥生产中的重要环节,这是水泥生产的必要前提,也是影响水泥质量的关键所在。
水泥在进行生产时,粉磨系统产生的耗电量占总耗电量的70%左右,这直接导致水泥生产的成本上升,同时粉磨系统的维护也是水泥生产设备中维修量最大的设备。
同时我国处于高度发展时期,对于水泥的需求量极大,因此,粉磨系统的节能改造对水泥生产企业来说至关重要。
1 水泥粉磨系统节能优化改造的必要性首先,我国水泥粉磨系统在建筑建设工程项目中越来越常见,利用技术提高了建筑施工的节能质量与节能工作的效率,国家、政府以及人民都十分重视节能技术的发展,技术的应用质量关乎项目工程的进程,建筑的节能水平以及效率也对企业以及公司的收益息息相关。
为了推动建筑事业不断发展与进步,就应该提高水泥粉磨系统的节能技术控制水平,优化其技术改造管理体制。
其次,水泥粉磨系统的规模与系统运维成本不断扩大,改革开放后,我国社会的现代化建设水平不断提高,建筑工程的规模与水泥粉磨系统涉及资金成本越来越大,规模的扩大与金额的增长对节能的技术应用与管理工作提出了更加严格的要求,建立完善的节能优化改造控制系统十分重要,对大规模与高投入的水泥粉磨系统体系起到了一定的保障作用。
最后,随着科学技术不断地发展,信息技术以及智能化的技术方法加入水泥粉磨系统建设过程之中,只有不断提高与加强水泥粉磨系统的节能水平,才能对建筑事业地发展起到了积极能动的作用。
2 水泥粉磨系统中的问题2.1 设备小但是耗能高我国的水泥生产中使用的粉磨系统,其中小型粉磨机占的比例较大,因此水泥生产企业为了满足水泥生产需求,会大量购买相关的粉磨机,但是在实际的生产过程中粉磨机进行的产量远远低于设计产量,这直接造成了能源消耗的上升。
lm60.4生料立磨在生产调试中的体会

lm60.4生料立磨在生产调试中的体会
作为一名机械工程师,我的工作之一就是参与生料立磨的生产调试。
在这个过程中,我学到了很多关于生产调试的技巧和体验,以下是我的心得体验:
1. 做好充分的准备工作是成功调试的关键。
在开始调试前,我们必须对设备进行全面、详细的检查和测试,确保设备良好运作。
这也意味着要准备好所有需要的工具和备件,以避免在调试过程中出现任何不必要的延误。
2. 与其他团队成员紧密合作非常重要。
一个人无法完成生产调试的工作,需要与其他同事紧密协作,共同克服问题和挑战。
这需要开放的沟通和高效的团队合作。
3. 在调试过程中,我们必须非常关注设备的稳定性。
我们的目标是实现最佳的工作效率和品质,但必须确保生料立磨能够在长时间的生产过程中保持稳定和可靠的运行。
4. 所有调试过程中的数据都应该被记录下来。
这些数据可以帮助我们追踪问题和挑战,并帮助我们改进设备。
同时,记录数据也有助于进一步提高设备的效率和生产质量。
5. 我们必须非常小心地进行每一个细节的调试。
生料立磨是一个复杂的机械设备,可能存在多种问题和挑战。
为了确保生产效率和质量,我们必须非常技术性
地调试每一个细节,从而确保整个系统可以高效稳定地运作。
总之,在进行生产调试时,我们必须专注于每一个细节,与同事进行紧密协作,并保持开放的沟通和高度的专注性。
只有这样,我们才能成功完成整个调试过程,为公司的生产贡献自己的力量。
生料粉磨节能降耗技术实践(探讨)
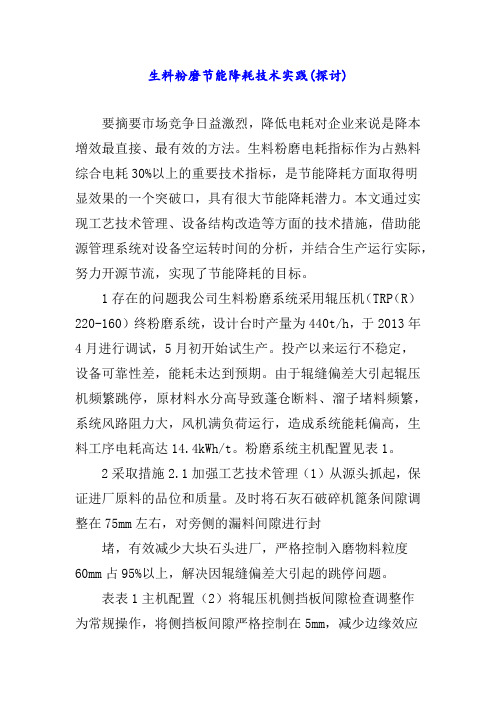
生料粉磨节能降耗技术实践(探讨)要摘要市场竞争日益激烈,降低电耗对企业来说是降本增效最直接、最有效的方法。
生料粉磨电耗指标作为占熟料综合电耗30%以上的重要技术指标,是节能降耗方面取得明显效果的一个突破口,具有很大节能降耗潜力。
本文通过实现工艺技术管理、设备结构改造等方面的技术措施,借助能源管理系统对设备空运转时间的分析,并结合生产运行实际,努力开源节流,实现了节能降耗的目标。
1存在的问题我公司生料粉磨系统采用辊压机(TRP(R)220-160)终粉磨系统,设计台时产量为440t/h,于2013年4月进行调试,5月初开始试生产。
投产以来运行不稳定,设备可靠性差,能耗未达到预期。
由于辊缝偏差大引起辊压机频繁跳停,原材料水分高导致蓬仓断料、溜子堵料频繁,系统风路阻力大,风机满负荷运行,造成系统能耗偏高,生料工序电耗高达14.4kWh/t。
粉磨系统主机配置见表1。
2采取措施2.1加强工艺技术管理(1)从源头抓起,保证进厂原料的品位和质量。
及时将石灰石破碎机篦条间隙调整在75mm左右,对旁侧的漏料间隙进行封堵,有效减少大块石头进厂,严格控制入磨物料粒度60mm占95%以上,解决因辊缝偏差大引起的跳停问题。
表表1主机配置(2)将辊压机侧挡板间隙检查调整作为常规操作,将侧挡板间隙严格控制在5mm,减少边缘效应的影响,防止循环料过多造成提升机能耗上升。
(3)加强密封堵漏,降低风机能耗。
首先,要加强漏风点密封,对增湿塔出口膨胀节、旋风筒下部观察口、动态选粉机检修门等漏风点进行密封,对不再使用的热风炉管道进行盲死,漏风严重的12个窑尾袋收尘器检修门做了更换,旋风筒下部布帘式密封改为布帘式+双翻板阀密封。
其次,要重视管道的耐磨,对所有下料溜子、通风管道作耐磨层,特别是一些非标件,比如入小仓的溜子、入V型选粉机溜子、V型选粉机与动态选粉机的连接管道、动态选粉机粗粉下料管等做耐磨层,保证系统无严重磨损,定期更换磨损的衬板、溜子等,避免堵料、漏料、漏风,影响系统风量平衡。
MLS3626生料立磨提产降耗技改项目总结
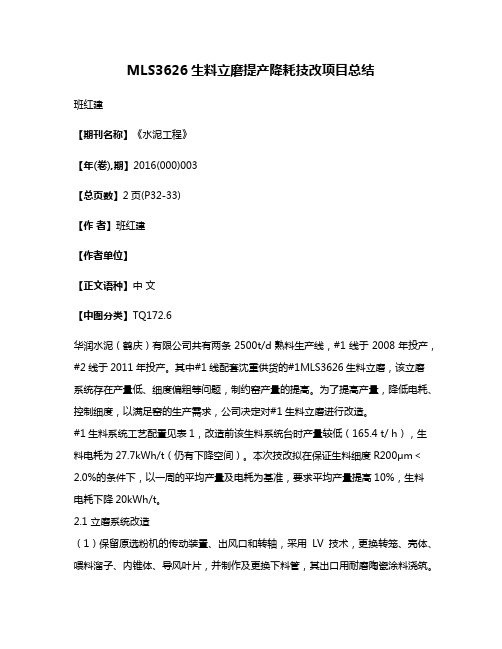
MLS3626生料立磨提产降耗技改项目总结班红建【期刊名称】《水泥工程》【年(卷),期】2016(000)003【总页数】2页(P32-33)【作者】班红建【作者单位】【正文语种】中文【中图分类】TQ172.6华润水泥(鹤庆)有限公司共有两条2500t/d熟料生产线,#1线于2008年投产,#2线于2011年投产。
其中#1线配套沈重供货的#1MLS3626生料立磨,该立磨系统存在产量低、细度偏粗等问题,制约窑产量的提高。
为了提高产量,降低电耗、控制细度,以满足窑的生产需求,公司决定对#1生料立磨进行改造。
#1生料系统工艺配置见表1,改造前该生料系统台时产量较低(165.4 t/ h),生料电耗为27.7kWh/t(仍有下降空间)。
本次技改拟在保证生料细度R200μm<2.0%的条件下,以一周的平均产量及电耗为基准,要求平均产量提高10%,生料电耗下降20kWh/t。
2.1 立磨系统改造(1)保留原选粉机的传动装置、出风口和转轴,采用LV技术,更换转笼、壳体、喂料溜子、内锥体、导风叶片,并制作及更换下料管,其出口用耐磨陶瓷涂料浇筑。
制作与更换喷口环与导风板,将导风角度改为75°,相应工况下风环风速调整为约50m/s,改内循环为外循环,增加外循环量,降低磨内压差。
现场测量制作刮料板,以适应外循环量增加的需要。
改造后转子与壳体密封性能好,以其独特的进风方式,提高了选粉效率。
选粉机改造前后见图1。
(2)根据磨机设计理念,降低喷口环风速,可以减少不合格物料在磨机内部的循环次数,减少选粉机提升这部分物料再将它们返回磨盘上所做的功,从而达到降低磨内循环负荷的目的。
采用生料立磨部分外循环喷口环替代内循环喷口环及相应的刮料板,改造前后结构示意见图2,刮料板结构见图3。
内循环是物料在磨盘上碾压,细粉尘由风道的风吹起来,经选粉机选粉,细度太大的又落到磨盘上,再次粉磨,这个过程在立磨里面进行,称为内循环。
内循环磨机喷口环设计风速为70m/s。
生料磨的学习心得
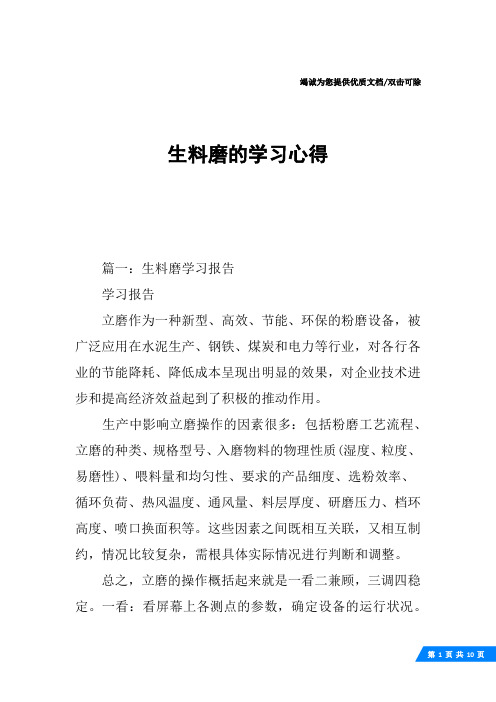
竭诚为您提供优质文档/双击可除生料磨的学习心得篇一:生料磨学习报告学习报告立磨作为一种新型、高效、节能、环保的粉磨设备,被广泛应用在水泥生产、钢铁、煤炭和电力等行业,对各行各业的节能降耗、降低成本呈现出明显的效果,对企业技术进步和提高经济效益起到了积极的推动作用。
生产中影响立磨操作的因素很多:包括粉磨工艺流程、立磨的种类、规格型号、入磨物料的物理性质(湿度、粒度、易磨性)、喂料量和均匀性、要求的产品细度、选粉效率、循环负荷、热风温度、通风量、料层厚度、研磨压力、档环高度、喷口换面积等。
这些因素之间既相互关联,又相互制约,情况比较复杂,需根具体实际情况进行判断和调整。
总之,立磨的操作概括起来就是一看二兼顾,三调四稳定。
一看:看屏幕上各测点的参数,确定设备的运行状况。
二兼顾:窑磨的拉风要兼顾;增湿塔与磨内喷水量要兼顾。
三调:调风(风温的高低,风量的大小);调料(喂料的大小,原料的配比);调研磨压力。
四稳定:稳定料层的厚度;稳定磨机的振动值;稳定磨内的压差;稳定产品的质量。
压差的控制。
压差是立磨操作的核心参数,它直接反应磨内循环物料量的大小,压差稳定标志着入磨物料量和出磨物料量趋于平衡,磨机运转正常。
当压差上升说明入磨物料量大于出磨物料量,内循环量增加,整个系统的通风阻力增大。
当压差下降说明入磨物料量小于出磨物料量,内循环降低,料层厚度变薄。
以上两种情况都是料层不稳定的现象,均可引起磨机振动、主电机电流波动、进出口压力变化。
通常我们以调整喂料量、通风量、选粉机转速、喷水量的方式来控制压差。
料层厚度的控制。
合适的料层厚度、稳定的料床是立磨粉磨的基础,也是立磨操作的关键。
料层的厚度受研磨压力、喂料量、喷水、风量、风速、物料性能等各种参数的影响。
料层厚度较薄时可采取的措施有:(1)增加磨内喷水;(2)降低研磨压力;(3)适当增加喂料量;(4)提高选粉机转数,增加磨内物料循环量。
若料层较厚时,则反之。
研磨压力的控制。
生料立磨LV选粉机技术改造节能体会

生料立磨LV选粉机技术改造节能体会辽阳千山水泥有限责任公司5000吨/日熟料生产线配套生料磨采用沈阳重型机械集团生产MLS4531A立磨。
2008年8月28日正式投产运行,由于公司首次使用立磨生产,生产运行初期不能保证熟料生产线正常的生料供应。
2009年底经过认识与实践上的不断提高,实施LV选粉机技术改造,基本实现水泥窑受生料立磨产量影响吃不饱的现象,实现了良好运行状态。
一、工艺流程简介生料磨设计:生产能力:390t/h(磨损后期);允许入磨物料最大粒度:110mm;允许入磨物料最大水份:12%;出磨生料细度:80μm筛的筛余≤12%;出磨生料最大水份:<0.5%。
原料调配站配备五个原料库,由各自的定量给料机从库中卸出,然后经由胶带输送机、气动推杆三通阀、回转锁风下料器喂入生料磨。
原料通过物料在磨内被研压粉碎、烘干并被选粉机分选,成品生料粉随出磨气体带出立磨。
采用窑尾预热器排出的废气作为立磨烘干的热源。
出磨的高浓度的含尘气体进入旋风收尘器(四个筒)进行料气分离。
收下的成品经回转下料器(四个)卸到生料入库输送系统中的空气输送斜槽(两条),并最终进入生料均化库内。
生料粉磨设置有物料外循环系统。
磨内不能被上升气流带起的大颗粒物料作为外循环物料通过重锤锁风翻板卸料阀、皮带输送机、提升机、带式输送机重新入磨。
带式输送机上设金属探测器,若发现意外产生的铁件,则通过气动三通溜子排入废渣仓。
外循环系统可增加磨机的产量,降低能耗。
生料细度可通过选粉机转子速度调节。
生料磨入磨物料量根据磨机进出口压差调节;磨内通风量根据旋风筒出口流量调节,由磨系统风机转速控制;根据磨机入口负压、废气风机转速控制循环风量;根据磨机出口废气温度控制磨机喷水量。
二、初期与运行情况对比1、立磨投产初期的基本情况。
立磨投产时,台时仅达到280吨/小时,生料质量波动。
日产5000吨熟料,小时入窑生料322吨;日产6000吨熟料,小时入窑生料388吨,生料产量的限制,使熟料台时无法进一步提高,成为熟料生产线达标、达产的主要瓶颈,吨熟料电耗达到75kwh。
生料磨、水泥磨系统节电技术改造

水 泥 助 磨 剂 c me t r d n i e n i igad gn
技 术 应 用
生 料 磨 、水 泥 磨 系统 节 电技 术 改造
徐 州亚隆建材机械有 限公 司 2 0 200 1
文 章 编 号 :2 1- 8 2 ( 0 )0 - 0 7 0 2 9 8 2 1 8 2 8 0 3- 2
和降低 电力 消耗 。
减少电费约 1. 6 12 万元 。
4 项 目总 投资
项 目总投资2 8 8 万元 。
5 2水 泥磨 系统 .
3 4 1 水 泥 磨 机 台 时 产 量 从 改 造 前 的 . mX 1 m
5节 电效果
5 1生料磨系统 .
5 . 7 / 提 高到7 . 2 / ,磨机单位 产品 电耗从改造 7 1 th 3 1th
石灰石粒度 ,可提 高台时产量1% 5 。 0  ̄1%
3 3采用新型 沟槽 衬板 .
在 q3 4 ×1m T 。 m l 水泥 磨的细磨仓 中采用新 型沟 槽 ) 衬 板 ,沟槽 衬板 为高铬 铸 铁材质 ,有 效地 抵抗 了被 磨物料 的侵 入和 磨削 。 同时衬板 的渗 透性好 ,其 金
一
4 . 4 / 提高 到5 . 7 / : 79 t h 4 7 t h 磨机 单位产 品电耗从 改造
前的4 . 2 W / 下降到3 . 9 W / 。2 0 年 实际生产 13 k h t 68kh t 03
8 1 ,全年节约 电量 18 7 万k h 6.8 w 。 3 4 ×7 5 i 8 生料 磨机 台时产量 从改造前的 水泥3 .万 t . m .+ . m
砂浆;
( )0 0 0 0 卜3 5 加 气混 凝土块墙 每 1 m 2 13 4 0 — 8 O
磨粉机的节能与环保改造方案分析
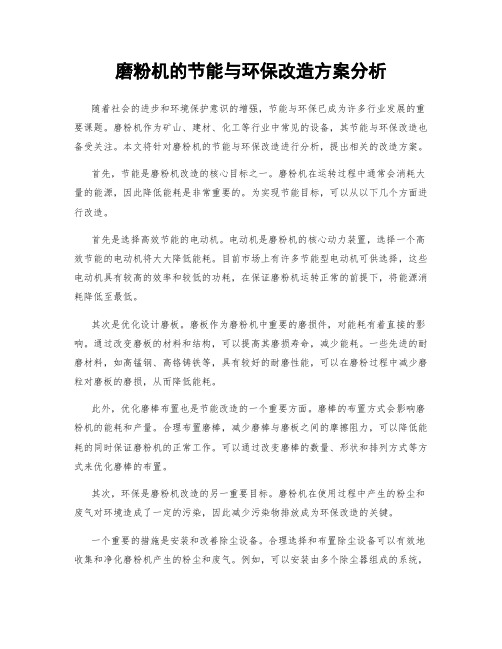
磨粉机的节能与环保改造方案分析随着社会的进步和环境保护意识的增强,节能与环保已成为许多行业发展的重要课题。
磨粉机作为矿山、建材、化工等行业中常见的设备,其节能与环保改造也备受关注。
本文将针对磨粉机的节能与环保改造进行分析,提出相关的改造方案。
首先,节能是磨粉机改造的核心目标之一。
磨粉机在运转过程中通常会消耗大量的能源,因此降低能耗是非常重要的。
为实现节能目标,可以从以下几个方面进行改造。
首先是选择高效节能的电动机。
电动机是磨粉机的核心动力装置,选择一个高效节能的电动机将大大降低能耗。
目前市场上有许多节能型电动机可供选择,这些电动机具有较高的效率和较低的功耗,在保证磨粉机运转正常的前提下,将能源消耗降低至最低。
其次是优化设计磨板。
磨板作为磨粉机中重要的磨损件,对能耗有着直接的影响。
通过改变磨板的材料和结构,可以提高其磨损寿命,减少能耗。
一些先进的耐磨材料,如高锰钢、高铬铸铁等,具有较好的耐磨性能,可以在磨粉过程中减少磨粒对磨板的磨损,从而降低能耗。
此外,优化磨棒布置也是节能改造的一个重要方面。
磨棒的布置方式会影响磨粉机的能耗和产量。
合理布置磨棒,减少磨棒与磨板之间的摩擦阻力,可以降低能耗的同时保证磨粉机的正常工作。
可以通过改变磨棒的数量、形状和排列方式等方式来优化磨棒的布置。
其次,环保是磨粉机改造的另一重要目标。
磨粉机在使用过程中产生的粉尘和废气对环境造成了一定的污染,因此减少污染物排放成为环保改造的关键。
一个重要的措施是安装和改善除尘设备。
合理选择和布置除尘设备可以有效地收集和净化磨粉机产生的粉尘和废气。
例如,可以安装由多个除尘器组成的系统,以提高除尘效果,减少粉尘排放。
此外,还可以优化除尘器的设计,增加过滤面积,提高处理能力,确保粉尘得到有效的过滤和吸附。
另外,选择环保的润滑剂也是改造的重要一环。
磨粉机在工作过程中需要润滑剂来减少摩擦和磨损,但传统润滑剂可能含有有害物质,对环境造成污染。
因此,选择环保型润滑剂可以减少对环境的污染。
原料立磨提产降耗效益显著
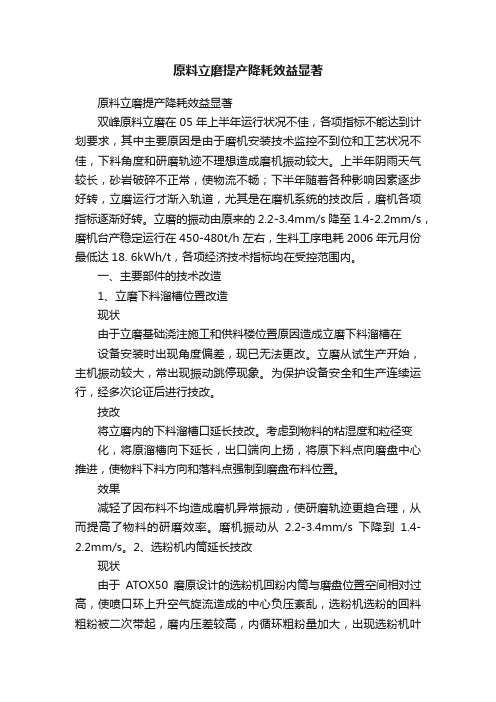
原料立磨提产降耗效益显著原料立磨提产降耗效益显著双峰原料立磨在05年上半年运行状况不佳,各项指标不能达到计划要求,其中主要原因是由于磨机安装技术监控不到位和工艺状况不佳,下料角度和研磨轨迹不理想造成磨机振动较大。
上半年阴雨天气较长,砂岩破碎不正常,使物流不畅;下半年随着各种影响因素逐步好转,立磨运行才渐入轨道,尤其是在磨机系统的技改后,磨机各项指标逐渐好转。
立磨的振动由原来的2.2-3.4mm/s降至1.4-2.2mm/s,磨机台产稳定运行在450-480t/h左右,生料工序电耗2006年元月份最低达18. 6kWh/t,各项经济技术指标均在受控范围内。
一、主要部件的技术改造1、立磨下料溜槽位置改造现状由于立磨基础浇注施工和供料楼位置原因造成立磨下料溜槽在设备安装时出现角度偏差,现已无法更改。
立磨从试生产开始,主机振动较大,常出现振动跳停现象。
为保护设备安全和生产连续运行,经多次论证后进行技改。
技改将立磨内的下料溜槽口延长技改。
考虑到物料的粘湿度和粒径变化,将原溜槽向下延长,出口端向上扬,将原下料点向磨盘中心推进,使物料下料方向和落料点强制到磨盘布料位置。
效果减轻了因布料不均造成磨机异常振动,使研磨轨迹更趋合理,从而提高了物料的研磨效率。
磨机振动从2.2-3.4mm/s下降到1.4-2.2mm/s。
2、选粉机内筒延长技改现状由于ATOX50磨原设计的选粉机回粉内筒与磨盘位置空间相对过高,使喷口环上升空气旋流造成的中心负压紊乱,选粉机选粉的回料粗粉被二次带起,磨内压差较高,内循环粗粉量加大,出现选粉机叶片磨损及磨内过粉磨现象,选粉效率差。
技改为了使内循环粗粉尽可能收集回到磨盘上再次粉磨成合格细粉,减少物料在磨内的循环次数,在原内筒口位置根据磨内实际空间向下加。
效果磨内的差压下降,选粉机转速、电耗均有所下降,磨机台产提高了约20t/h。
3、刮板腔刮板头技改现状立磨吐渣循环量较大,且粒径不均匀,加上铁质原料采用钢渣配料,刮板腔刮板头的磨损十分严重。
生料立磨减阻改造方案及效果
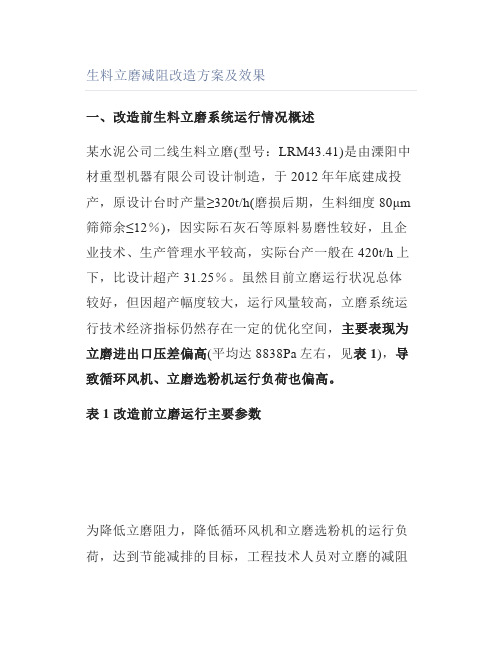
生料立磨减阻改造方案及效果一、改造前生料立磨系统运行情况概述某水泥公司二线生料立磨(型号:LRM43.41)是由溧阳中材重型机器有限公司设计制造,于2012年年底建成投产,原设计台时产量≥320t/h(磨损后期,生料细度80μm 筛筛余≤12%),因实际石灰石等原料易磨性较好,且企业技术、生产管理水平较高,实际台产一般在420t/h上下,比设计超产31.25%。
虽然目前立磨运行状况总体较好,但因超产幅度较大,运行风量较高,立磨系统运行技术经济指标仍然存在一定的优化空间,主要表现为立磨进出口压差偏高(平均达8838Pa左右,见表1),导致循环风机、立磨选粉机运行负荷也偏高。
表1 改造前立磨运行主要参数为降低立磨阻力,降低循环风机和立磨选粉机的运行负荷,达到节能减排的目标,工程技术人员对立磨的减阻改造方案进行了认真的讨论研究,拟对立磨选粉机结构、立磨风环调风板以及立磨下壳体风道等进行技术改造。
二、具体的减阻改造方案2.1立磨选粉机结构改造选粉机运行阻力在整个立磨总阻力中占有很大的比重,减少该部分阻力是关键,主要方法是增大选粉机转子尺寸(壳体、静叶片同步调整),优化各项风速尤其是转子截面风速、转子切向风速、动叶片静态间隙风速。
同时,基于节约成本与有效利旧的原则,对选粉机传动装置、轴系(主轴、轴承等)、上壳体、支撑、油管、温度计管进行充分利用,仅需与上壳体一起拆装就能达到改造目的。
选粉机结构改造总体方案见图1。
图1 选粉机总体改造方案2.1.1选粉机转子叶片改造本次选粉机转子叶片改造采用低阻型转子叶片结构(见图2),同时此叶片宽度较之前宽,既能降低局部阻力,同时对有效控制0.2mm细度指标有利。
图2 选粉机转子叶片改造前后对比2.1.2选粉机静叶片改造选粉机静叶片数量由原来的100片更改为90片,同时宽度由150mm增加至180mm,材质采用6+4复合耐磨板。
基于节约原则,静叶片上部固定之螺栓、紧固件一等不更换;下部紧固件二因固定焊接过,处理难度大,考虑更换,具体见图3。
- 1、下载文档前请自行甄别文档内容的完整性,平台不提供额外的编辑、内容补充、找答案等附加服务。
- 2、"仅部分预览"的文档,不可在线预览部分如存在完整性等问题,可反馈申请退款(可完整预览的文档不适用该条件!)。
- 3、如文档侵犯您的权益,请联系客服反馈,我们会尽快为您处理(人工客服工作时间:9:00-18:30)。
李 豪杰 山水集团辽阳千 山水泥有 限责任公司 辽 宁辽 阳
1 1 1 2 0 1
辽 阳千 山水 泥有 限责任 公司5 0 0 0 吨/ 日熟料生 产 线配 套生料 磨 采 由于熟 料台时提 高, 2 0 0 9 年 与2 0 1 2 年比熟料 电耗下 降2 O %。 5 、 由于生料 粒径范 围的变窄, 增加 0 . 2 筛余对 立磨 台时影 响和质量 用沈阳重 型机 械集 团生产ML S 4 5 3 1 A S  ̄ 磨。 2 0 0 8 年8 月2 8 日正式 投产运 行, 由于公司首次使 用立磨 生产, 生 产运行 初期不 能保证 熟料生 产线 正 影 响的 重要性 , 兼顾 放 宽0 . 0 8 筛余对立 磨 台时 提高 的必要性 , 带来的质 常的生 料供 应 。 2 0 0 9 年底 经过 认识与 实践上 的不 断提高 , 实施 L v 选粉 量 是相对稳 定的。 机技术 改造 , 基本 实现水泥窑 受生料立磨 产量影 响吃不饱 的现象 , 实 现 五、 根据目前基本现状需要解 决问题在挖节能降耗潜力 了良好 运行状 态。 l 、石灰石粒度 的改 进 生料立 磨从投 产至今石灰石 粒度的认识 日 趋加 深 , 由于对磨机 工艺 工 艺流 程 简介 生料 磨设 计 : 生产 能力 : 3 9 0 t / h ( 磨 损后期 ) ; 允 许入 磨物 料 最大 粒 参 数理 解 的不到 位 , 使最初 投料 时对石 灰石粒 度 的控制 采取 的宁 大勿 度: 1 l O mm; 允许入磨 物料 最大 水份 : 1 2 %l 出磨 生料 细度 : 8 0 “ m筛的 筛 小 的原 则, 把石 灰石粒 度控制在7 0 - 1 2 0 mm粒 径 , 如此 大 的粒 径带 来的 余 ≤l 2 %{出磨生 料最大 水份: <0 . 5 %。 负面 影 响, 是 从矿 山使用 设配 到立 磨磨 辊等 一系 列配套 设 配使用寿 命 原料调 配站 配备五个原料库 , 由各 自的定量 给料 机从库 中卸出 , 然 缩 短 , 造成设 备运 转率偏 低 , 电耗 上升而且 质量不 稳定 , 更谈不到 消耗 后经由胶带输 送机 、 气动推杆 三通 阀、 回转锁风下料 器喂入 生料磨。 指 标的优化 。 原料 通 过物 料在 磨 内被研 压粉 碎 、 烘 干并 被选 粉机 分 选 , 成 品生 通 过不 断 地学 习与实践 , 石 灰石 粒度 的重要 性 已是 前期 控制 最关 料 粉随 出磨气体带出立磨 。 键 的因素, 必须 解决 。 采用窑尾预热 器排 出的废气作为立磨 烘干的热 源 。 ( 1 ) 2 0 1 3 年 冬季大修 , 石灰石破碎 采用双转 子单 段锤式 破碎机 , 原 出磨的 高浓度的含尘 气体进入 旋风收尘 器( 四个 筒) 进行 料气分离。 设 计蓖板 蓖缝4 0 am一 r 6 0 a m一 r 8 0 am三个梯度 范围最 大8 r 0 mm, 更 换一 收下的成 品经回转下料 器 ( 四个) 卸到生料 入库输 送系统 中的 空气输送 套 新锤 头及承 击砧 , 锤 头与蓖缝 间隙调整 到2 O mm 一 3 0 mm一 4 0 mm三个 斜槽 ( 两条) , 并 最终进入 生料均化库 内。 梯度范 围, 石灰石平均 粒度2 5 am。 r 生料 粉磨 设置有物 料 外循环 系统 。 磨 内不能 被上 升 气流 带 起的 大 ( 2 ) 石 灰石 粒度 下降 与石灰石 破碎 机台时 产量下 降 , 并 没有 明显 颗粒物 料 作为 外循 环物 料 通过 重锤 锁风 翻板 卸料 阀 、 皮 带输 送机 、 提 的对应 关系 , 不仅要关心石 灰石破碎 电耗 的提 高 , 更要 关心吨 生料 电耗 更要关心石 灰石 粒度下 降带来 的微 粉量增加 , 对立 磨振 值的 升机 、 带 式 输送 机重新 入磨 。 带式 输送机 上设金 属探测 器, 若 发现意 外 是 否下降 , 产生的铁 件 , 则 通过气动 三通溜子 排入废渣仓 。 外循环 系统可增加磨 机 影 响 , 通过摸 索提 出适合 自 身实 际情况的石 灰石粒 度颗粒 分布范 围, 不 仅 严格 控制最 大粒度 , 更要 控制最 小粒度 范围量。 的产量 , 降低能 耗。 生料 细度 可通过 选粉 机转 子速 度调 节。 生料磨入 磨 物料量 根据 磨 ( 3 ) 在 石灰石粒 度 下降过 程 中深 刻认 识到 , 破碎粒 度下 降不 仅是 机进 出 口 压 差调节 ; 磨 内通 风 量根据 旋风筒 出口流 量调节 , 由磨系统 风 吨 生料综 合 电耗下 降的主要 渠道 , 更是 减 少石灰石 离析现象 , 实现 石灰 机转 速控 制 ; 根据磨 机入 口负压 、 废 气凤机 转速 控制循 环风量 ; 根据 磨 石均质稳 定的重要渠 道。 机出口废气温 度控制磨 机喷水 量。 2 、 生 料细度控 制指标 精细 合理 = 初 期 与运 行情 况 对 比 在 水泥生 产工艺中, 生料 细度并没有 受过过 多的关注 , 该 指标 比较 l 、 立 磨投 产初期 的 基本情况 。 立 磨投 产时 , 台 时仅达  ̄ U 2 8 o 吨/ , J 、 容易实现 , 而却对下道 工艺并没有产生 更大的影 响 , 传 统的观 念是体 现 时, 生料 质量波动 。 日 产5 0 0 0 吨熟料 , 小 时入窑 生料3 2 2 吨1 日 产6 0 0 0 吨 在 生料细 度越细 越好, 但从 精细化 角度去分析 , 该指 标 的合理制定 有着 熟料, 小 时入窑生料3 8 8 吨, 生料产量 的限制 , 使 熟料台时 无法进一 步提 积极重要的意 义。 高, 成为 熟料生产 线达标 、 达 产的主要 瓶颈 , 吨熟料 电耗达 到7 5 k wh 。 从 能耗角度分析 , 生料 并非越 细越 好。 直接对 立磨的 电耗 和产量 产 2 、 立 磨达 标 达 产后的 基本 情况 。 通 过L V 改 造 加上 几年 来公 司领 生 显著的影 响, 不 可忽视它 的负面作用。