以可靠性为中心的维修
两种典型维修管理模式介绍

两种典型维修管理模式介绍随着社会和科学技术的发展,设备日益朝着集成化、大型化、连续化、精密化等方向发展。
先进的设备使得企业的设备操作人员不断减少,而维修任务和维修人员的比重不断增加;操作的技术含量逐渐下降,而维修的技术含量不断上升,先进的设备需要先进的维修技术,更需要先进的管理模式。
本文就为大家介绍两种最典型的维修管理方法。
1、以预防为主的维修法与定期维修制长期以来,人们认为机械设备的安全性取决于其可靠性,故认为预防工作做得越多、修理周期越短、机械设备越可靠,这就是我们沿用多年的以定期维修为主的预防性维修方法。
即不论每个具体维修对象的技术状况、使用环境如何,都必须按照统一规定的时间或行驶里程进行强制性维修(如现行规定的一、二、三级保养)与针对性的维修。
定期维修的这种方法对于早期机械设备及零件的维修比较合适,曾对我国机械设备维修起过重要的作用。
早期的定期维修制增加了维修工作量、维修费用及停机时间,其结果是做了很多无效维修,却不能及时排除随机故障和早期故障。
对故障数据的统计分析表明,定期维修对许多故障的控制并不起作用,所进行的分解检查不能提供尚可使用的零件在何时会可能出现故障的真实情况,过多的拆修反而易产生人为故障、增加维修消耗、降低维修效率。
理论证明,对于复杂的机械设备,其故障主要是随机性的,而定期维修不能排除随机故障,因此,20世纪60年代初人们开始对传统的维修方法产生了怀疑。
这时期有的国家开始通过应用可靠性大纲、针对性维修、按需检查和更换等试验性工作进行探索,在统计的基础上初步产生了以可靠性为中心的维修方法。
2、以可靠性为中心的维修法与视情维修制(1)以可靠性为中心的维修是现代维修理论的核心。
系统工程的观点认为,维修对象的研制、设计、制造、使用都是与维修有关的环节,各个环节都围绕着可靠性这个中心进行工作,因此维修对象的可靠性在循环往复中得到不断的改进和提高。
以可靠性为中心的维修方法也是对传统的以预防为主的维修方法的继承和发展,人们对维修的认识由原来的工作—磨损—故障—危及安全演变为采取积极有效的措施,控制机械设备可靠性下降的因素,以保持恢复机械设备的固有可靠性。
以可靠性为中心的维修_RCM_维修科学的发展趋势

以可靠性为中心的维修(RCM )—维修科学的发展趋势3南京航空航天大学 (210016) 孙有朝 樊蔚勋 摘 要 分析了维修科学的发展历程,指出了RCM 的基本问题和主要研究内容,阐述了RCM 将成为维修科学的重要发展方向。
关键词 可靠性 预防维修 设备管理 维修计划 RCM 3获“民航总局自选科研课题基金”资助1 维修观念的更新众所周知,机械设备正向复杂、成套、自控和机电一体化方向发展,在实际运行中,为了保持设备在设计中原有的可靠性和稳定性,设备管理和维修工程已成为系统工程的一个重要分支。
七十年代至今,是维修观念和技术迅速发展、维修由被动排除故障变为主动预防并发展成为一门科学的重要时期。
这一时期对维修的期望值有了较大提高,通过维修要求达到更高的设备可用度和可靠性、更高的安全性、更高的产品质量、更长的设备寿命、更高的成本效益、对环境无危害等等,由此可见,可靠性和可用度已成为关键性因素。
除了提高期望值外,人们对设备工龄期与故障的很多基本看法也发生了重大变化,尤其是大多数复杂设备的运行工龄与设备发生故障可能性之间的联系很明显越来越少(早期的故障观点比较简单,认为设备越陈旧越可能发生故障,人们对“强化试验”的深入认识,逐渐形成了“浴盆”曲线的观点,但根据近期的研究表明,由于具体设备的状态不同,故障模型可达六种之多),同时,还发展了许多新技术(如决策支持手段、状态监测技术等),更加注重了设备的可靠性和可维修性设计,组织中的主要方法朝参与、合作、灵活的方向转变,当今的维修管理人员所面临的主要挑战,不仅是要学习这些新技术,而且要能决定是否值得做,正确的选择是改善设备性能、降低维修费用的关键。
2 以可靠性为中心的维修(RCM)以可靠性为中心的维修(Reliability -Centered 2Maintenance )是近二十年来从众多的维修理论中脱颖而出并逐步被广泛接受的一种全新的维修方法,它是建立在设备的设计特点、运行功能、失效模式和后果分析的基础上,以最大限度提高设备的使用可靠性为目的,应用可得到的安全性和可靠性数据,判别哪些子系统和零部件处于临界状态,哪些需要修复、改进或重新设计,确定维修的必要性和可行性,对维修要求进行评估,最终制订出实用、合理的维修计划或大纲。
什么是以可靠性为中心的维修
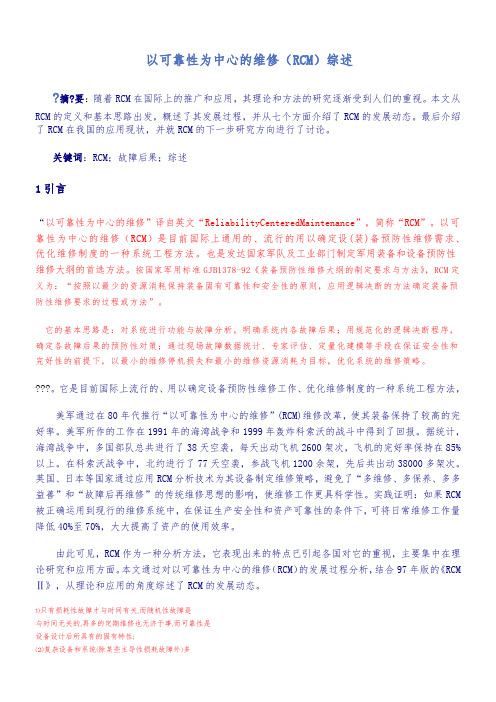
以可靠性为中心的维修(RCM)综述摘?要:随着RCM在国际上的推广和应用,其理论和方法的研究逐渐受到人们的重视。
本文从RCM的定义和基本思路出发,概述了其发展过程,并从七个方面介绍了RCM的发展动态。
最后介绍了RCM在我国的应用现状,并就RCM的下一步研究方向进行了讨论。
关键词:RCM;故障后果;综述1引言“以可靠性为中心的维修”译自英文“ReliabilityCenteredMaintenance”,简称“RCM”。
以可靠性为中心的维修(RCM维修大纲的首选方法。
按国家军用标准定防性维修要求的过程或方法”。
(RCM)维修改革,使其装备保持了较高的完1999年轰炸科索沃的战斗中得到了回报。
据统计,天空袭,每天出动飞机2600架次,飞机的完好率保持在85%77天空袭,参战飞机1200余架,先后共出动38000多架次。
英国、日本等国家通过应用RCM分析技术为其设备制定维修策略,避免了“多维修、多保养、多多益善”和“故障后再维修”的传统维修思想的影响,使维修工作更具科学性。
实践证明:如果RCM 被正确运用到现行的维修系统中,在保证生产安全性和资产可靠性的条件下,可将日常维修工作量降低40%至70%,大大提高了资产的使用效率。
由此可见,RCM作为一种分析方法,它表现出来的特点已引起各国对它的重视,主要集中在理论研究和应用方面。
本文通过对以可靠性为中心的维修(RCM)的发展过程分析,结合97年版的《RCM Ⅱ》,从理论和应用的角度综述了RCM的发展动态。
1)只有损耗性故障才与时间有关,而随机性故障是与时间无关的,再多的定期维修也无济于事,而可靠性是设备设计后所具有的固有特性;(2)复杂设备和系统(除某些主导性损耗故障外)多属于随机性,浴盆曲线对此类产品不适用;以可靠性为中心的维修(ReliabilityCenteredMaintenance,简称RCM)是目前国际上通用的、用以确定资产预防性维修需求、优化维修制度的一种系统工程方法。
以可靠性为中心维修(RCM)简介

苏联: 计划维修(- ) 按计划大、中、小修(我国过去也采用)
美国: 预防维修() 事后维修() 预防维修() 改善维修(- ) 维修预防(- )
定期检修 (减少非计划停车损失→成本较高→过度维修与维
第三代维修模式
(上世纪60年代出现,上世纪80年代至今天广泛使用)
国内
1979年 民航与空军引进了
1992年 “装备预防性维修大纲的制订要求与方法”
的社会基础
1970年
1974年 环境(社会承受能力脆弱)
一系列标准规范 严惩
“美国职业安全与健康法” “健康安全法” 安 全 的 工 作
严重的失效事故,管理人员受到
所有发达国家都有类似的法规
我国更侧重于经济效益,缺乏西方对 的社会需求,但近年
维修与资产完整性管理
基于风险的资产管理()
2 定义
() 以可靠性为中心的维修管理 一种维修的理念,一种维修的策略,一种维修的模式
功能与故障分析
依据 可靠性状况 后果与严重程度
安全
应用 逻辑判断方法 最小的维修资源消耗
维修内容
维修类型
确定维修大纲
维修间隔期 维修级别
→达到优化维修的目的
图3
图4 流程图
图5 故障后果及维修工作分析流程图(第一步)
图6 预防性维修工作类型分析流程(第二步)
3 故障与后果分类及处理原则
故障 设备不能实现预定功能的状态
功能故障 明显功能故障
潜在故障 隐蔽功能故障
故障后果:
安全性和环境后果:人员伤亡与环境污染
隐蔽性故障后果:
暂无直接影响,导致
严重的多重故障后果
可靠性维修为中心(RCM)管理

设备主动性维修、预先维修与以可靠性为中心的维修RCM管理1 引言“以可靠性为中心的维修”译自英文“Reliability Centered Maintenance”,简称“RCM”,它是国内外维修行业已经非常熟悉的一个用词,是受到世界各国普遍承认的科学的维修理论。
在发达国家,RCM的推广应用已经取得了显著成效,并且还在继续扩展。
主动性维修或主动维修,源于Proactive Maintenance (缩写为Promaint或PaM,也可译为“预先维修”),从上世纪90年代开始,在西方国家逐渐发展和应用。
2002年欧洲维修联盟(EFNMS)第16次会议曾将Promaint 作为会议主题。
但是“主动性维修”到底是什么,各国是“仁者见仁,智者见智”,存在不同的理解,就是在Promaint发源地,对其概念、原理和具体技术也有着截然不同的观点。
本文将在分析有代表性的两种主动性维修观点的基础上,研究如何应用主动性维修,丰富和完善现有的RCM理论和方法。
2 两种不同的“主动性维修”(PaM)2.1 狭义的“主动性维修”1992年美国资深的液压系统设计专家E.C.Fitch,在其著作《Proactive Maintenance for Mechanical Systems》[1]中详细论述了Proactive Maintenance的概念、原理和技术。
这种维修在理论和实践上有其重要的意义,它提出了“故障根源”(Boot Causes of Failure)的概念,给出了故障根源的种类(材料变形、超常液体污染、液体泄漏、液体化学不稳定、液体物理不稳定、液体气蚀、液体温度不稳定、严重的磨损状况等),认为通过对可能引起设备产生故障的“故障根源”进行系统化的识别,在系统的性能和材料退化之前采取措施进行维修,可以有效地减少系统的整体维修需求,延长系统的使用寿命。
Fitch的“主动性维修”认为,在实际的维修工作中不但要重视零部件的损伤,还应重视相关介质(如油液等)的“条件性故障”。
什么是可靠性为中心的维修RCM

什么是可靠性为中心的维修RCM?以可靠性为中心的维修管理(英文为Reliability Centered Maintenance,简称RCM),属于第三代维修管理的最具有代表性的模式。
这一设备管理模式强调以设备的可靠性、设备故障后果,作为制定维修策略的主要依据。
按照以可靠性为中心的维修管理模式,首先应对设备的故障后果进行结构性评价、分析并综合出一个有关安全、运行经济性和维修费用节省的维修策略。
另外,在制定维修策略时,自觉地以故障模式的最新探索成果作为依据。
也就是说,以可靠性为中心的维修管理,是综合了故障后果和故障模式的有关信息,以运行经济性为出发点的维修管理模式。
下面介绍一下这一维修体系的基本要点。
1.关于故障后果的评价以可靠性为中心的维修管理,对设备故障后果进行结构性评价。
这种评价是以下面的顺序来排列其重要程度的。
1)潜在故障问题。
目前对设备无直接影响,而故障一旦发生则后果严重。
2)安全故障问题。
故障一旦发生,会造成人身或生命安全。
3)运行故障问题。
故障一旦发生,影响生产运行和修理的直接费用。
4)非运行故障问题。
此故障一般不影响生产运行,但影响修理费用。
按照以可靠性为中心的维修管理策略,如果设备故障后果严重,则应采用预防维修。
否则除日常维护和润滑外,不必进行预防维修。
在评价故障后果以便制定维修策略时,每个设备的所有功能和故障模式都应加以考虑,并进行分析,制定出每一设备的维修方针。
其故障后果与维修策略关系如表1所示。
表1 故障后果与维修策略的选择2.对于故障特性的研究预防维修是根据设备故障特征曲线或浴盆曲线,在设备进入耗损故障期之前安排进行的维修活动。
当今的设备比以往要复杂得多,而且故障模式也有了新的变化。
美国民航在过去30年间,作了大量关于设备可靠性的研究,发现在设备从使用到淘汰(包括无形磨损造成的设备报废),其故障特征曲线呈六种不同形状,如图1所示。
从图中可以看出,模式B开始为恒定或逐渐略增的故障率,最后进入耗损期;模式C 显示了缓慢增长的故障率,但没有明显的耗损故障期;模式D显示了新设备刚出厂时的低故障率现象,很快增长为一个恒定的故障率;模式E在整个寿命周期都保持恒定的故障率;模式F在开始时有较高的初期故障率,很快降低为恒定或增长极为缓慢的故障率。
以可靠性为中心的维修(RCM)

一、什么是以可靠性为中心的维修?以可靠性为中心的维修(RCM)是目前国际上通用的用以确定设(装)备预防性维修需求、优化维修制度的一种系统工程方法。
按国家军用标准GJB1378-92《装备预防性维修大纲的制定要求与方法》,RCM定义为:“按照以最少的资源消耗保持装备固有可靠性和安全性的原则,应用逻辑决断的方法确定装备预防性维修要求的过程或方法”。
它的基本思路是:对系统进行功能与故障分析,明确系统内各故障后果;用规范化的逻辑决断程序,确定各故障后果的预防性对策;通过现场故障数据统计、专家评估、定量化建模等手段在保证安全性和完好性的前提下,以最小的维修停机损失和最小的维修资源消耗为目标,优化系统的维修策略。
[ 转自铁血社区]二、RCM分析的输出是什么?对于民用设备,RCM分析的结果给出的是设备的预防性维修工作项目、具体的维修间隔期、维修工作类型(或方法)和实施维修的机构。
对于军用装备而言,RCM分析的结果是针对于该装备的预防性维修大纲。
装备预防性维修的大纲是规定装备预防性维修要求的汇总文件,是关于该装备预防性维修要求的总的安排。
其主要内容包括:需要进行预防性维修的产品或项目(WHAT);实施的维修工作类型或“方式”(HOW);维修工作的时机即维修期(WHEN);实施维修工作的维修级别(WHERE)。
[ 转自铁血社区]装备预防性维修大纲对于我们的维修管理来说是一个新的术语,它是装备全系统、全寿命维修管理的产物。
按着现代维修工程的要求,装备在研制过程中就要规划其维修保障系统,而维修大纲是规划维修保障系统的顶层文件,是纲目性的资料。
因为只有搞清了装备的维修工作需求才能进一步有针对性地设计和优化维修保障系统。
[NextPage]三、RCM的产生与发展背景RCM的产生与装备维修方式的多样化与人们对维修实践的不断认识有直接的关系。
二十世纪50年代末以前,在各国装备维修中普遍的做法是对装备实行定时翻修,这种做法来自早期对机械事故的认识:机件工作就有磨损,磨损则会引起故障,而故障影响安全,所以,装备的安全性取决于其可靠性,而装备可靠性是随时间增长而下降的,必须经常检查并定时翻修才能恢复其可靠性。
02以可靠性为中心的维修

2 3 4
从可靠性原理及实践寻找或消除隐蔽 故障, 故障,可以预防多重故障的严重后果 预防性维修不能提高固有可靠度 预防性维修难以避免故障的发生,不能改 预防性维修难以避免故障的发生, 变故障的后果。 变故障的后果。 采用不同的维修策略和方式, 采用不同的维修策略和方式 , 可以大大减少维修费用。 可以大大减少维修费用。 完善的预防性维修大纲由使用人 员与维修人员共同加以完善。 员与维修人员共同加以完善。 通过改进使用和维修方式, 通过改进使用和维修方式, 也能 得到一些良好的效果。 得到一些良好的效果。 维修是维持有形资产的功能(质量、 维修是维持有形资产的功能 ( 质量 、 售后 服务、运行效益、操作控制、安全性等) 服务、运行效益、操作控制、安全性等) 首先改变人们的思维方式, 首先改变人们的思维方式,以新观念不 断渗透, 断渗透,其次再解决技术和方法问题。 维修不仅影响可靠度和费用, 维修不仅影响可靠度和费用 , 还有环境保 能源效率、质量和售后服务等风险。 护、能源效率、质量和售后服务等风险。 1-289
2011-1-15 1-289 7
一、以可靠性为中心的维修思想的基本原理: 以可靠性为中心的维修思想的基本原理: 1 、 定时拆修对复杂设备的故障预防几乎不起 作用,但对简单设备的故障预防有作用。 作用,但对简单设备的故障预防有作用。 2 、 提出潜在故障的概念 , 可使设备在不发生 提出潜在故障的概念, 功能故障的前提下得到充分地利用, 达到安全、 功能故障的前提下得到充分地利用 , 达到安全 、 经济的使用目的。 经济的使用目的。 3 、 检查并排除隐蔽功能故障是预防多重故障 严重后果的必要措施。 严重后果的必要措施。 4、有效的预防性维修工作能够以最小的资源
2011-1-15 1-289 13
设备的周检制和以可靠性为中心的维修理念

设备的周检制和以可靠性为中心的维修理念提要:设备的维修与管理的地位愈来愈显得重要,维修的社会化使更多的专业人士潜心于对现代化维修理念和方式的研究与探索。
设备的周检制和以可靠性为中心的维修理念应运而生。
所谓周检是基于状态维修方式中日常点检、定期点检、精密点检的三检基础上,根据设备失效发展过程所确定的一种对设备运行工况进行诊断的方法。
所谓以可靠性为中心的维修管理RCM(Reliabity Centered Maintenance)一种用于确定某一设备在其运行环境下,是否需要维修的一种方法。
推行设备周检制,保证以可靠性为中心的维修模式的实现郭精义卢世忠兰炼设备维修公司随着石油化工企业过程化控制程度的提高和企业对低成本的追求,设备的维修与管理的地位愈来愈显得重要,维修的社会化使更多的专业人士潜心于对现代化维修理念和方式的研究与探索。
设备的周检制和以可靠性为中心的维修理念应运而生。
一、设备周检和以可靠性为中心维修的概念所谓周检是基于状态维修方式中日常点检、定期点检、精密点检的三检基础上,根据设备失效发展过程所确定的一种对设备运行工况进行诊断的方法。
设备故障的发生要经历六个阶段,即机械性能完好、根源性参数异常、材料磨损、性能下降、部分功能损坏、突然完全停止工作。
一台设备由机械性能完好到根源性参数异常,再到最后的突然完全停止工作,与其工作时间是一个函数关系。
周检就是通过定期的检查,确定一台运行的设备处于哪个阶段,然后依据其损坏的后果及形式确定何时对其进行必要的检修。
所谓以可靠性为中心的维修管理RCM(Reliabity Centered Maintenance)一种用于确定某一设备在其运行环境下,是否需要维修的一种方法,RCM方法要不断地对设备提出和回答以下问题:①在现行环境下,设备的功能、标准是什么?②什么情况下,设备无法实现其功能?③引起功能故障的原因是什么?④故障的后果是什么?⑤什么后果的故障最重要?⑥做什么才能预防故障?⑦做这种预防的故障值不值得。
什么是RCM 概述
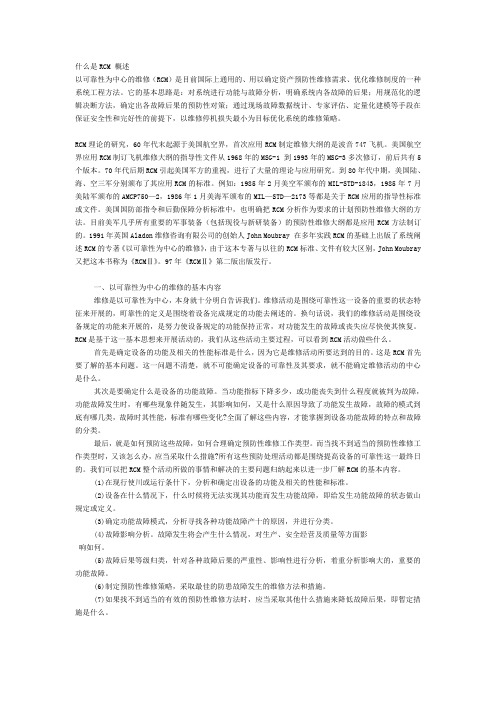
什么是RCM 概述以可靠性为中心的维修(RCM)是目前国际上通用的、用以确定资产预防性维修需求、优化维修制度的一种系统工程方法。
它的基本思路是:对系统进行功能与故障分析,明确系统内各故障的后果;用规范化的逻辑决断方法,确定出各故障后果的预防性对策;通过现场故障数据统计、专家评估、定量化建模等手段在保证安全性和完好性的前提下,以维修停机损失最小为目标优化系统的维修策略。
RCM理论的研究,60年代末起源于美国航空界,首次应用RCM制定维修大纲的是波音747飞机。
美国航空界应用RCM制订飞机维修大纲的指导性文件从1968年的MSG-1 到1993年的MSG-3多次修订,前后共有5个版本。
70年代后期RCM引起美国军方的重视,进行了大量的理论与应用研究。
到80年代中期,美国陆、海、空三军分别颁布了其应用RCM的标准。
例如:1985年2月美空军颁布的MIL-STD-1843,1985年7月美陆军颁布的AMCP750—2,1986年1月美海军颁布的MIL—STD—2173等都是关于RCM应用的指导性标准或文件。
美国国防部指令和后勤保障分析标准中,也明确把RCM分析作为要求的计划预防性维修大纲的方法。
目前美军几乎所有重要的军事装备(包括现役与新研装备)的预防性维修大纲都是应用RCM方法制订的。
1991年英国Aladon维修咨询有限公司的创始人John Moubray 在多年实践RCM的基础上出版了系统阐述RCM的专著《以可靠性为中心的维修》,由于这本专著与以往的RCM标准、文件有较大区别,John Moubray 又把这本书称为《RCMⅡ》。
97年《RCMⅡ》第二版出版发行。
一、以可靠性为中心的维修的基本内容维修是以可靠性为中心,本身就十分明白告诉我们。
维修活动是围绕可靠性这一设备的重要的状态特征来开展的,町靠性的定义是围绕着设备完成规定的功能去阐述的。
换句话说,我们的维修活动是围绕设备规定的功能来开展的,是努力使设备规定的功能保持正常,对功能发生的故障或丧失应尽快使其恢复。
以可靠性为中心的维修(RCM)综述

修计划; ④研究 、 改进R M有关方法 : C 包括研制故障模式 、 影响及危害度分析(M C ) F E A 自动化 软件 ; ⑤改进R M C 决断逻辑 , 改进 “ 机体状况评价” “ 、飞机腐蚀分析评价” 的技术和设备等 ; ⑥更新技术文件, 组织R M C 培训 ; ⑦建立和扩大R M C 数据库 , 加强R M C 数据的利用等。
要内容包括 :①审查修订大修规划 :按 R M原理对现有大修规程进行审定 ,首批审定 4 C 0 个 , 后对 其余 规 程进 行 审定 ; 应 用 R M 制 订现 役 飞行 维修 大 纲 及维 修计 划 , 括 进行 然 ② C 包 故 障模式 、 响及危 害度分析 ; 影 确定 维修项 目、 式 、 方 修理 间 隔 、 要求 等 。现役 主要 机 型( H一 A
1 引言
“ 以可 靠性 为中心 的维修 ” ( ei it C nee ane ac ,R M)是 目前 国际上 流 R l bly e trdM itnn e C a i
行 的 、用 以确 定设 备 预防性 维修工作 、优化维 修制 度 的一种 系统 工程方 法 ,也是 发达 国家
军 队 及工 业 部 门 制定 军用 装 备 和设 备 预 防性 维 修 大 纲 的首 选 方 法 。 随着 RC 技 术 的 发 M 展 ,在 不同 领域其 定义 也不 同 ,但最 主要 、最 基本 的定义仍 属 Jh o ba 教 授 的定义 。 on M u ry R M 是 确定有 形资产 在其使 用背 景下 维修需 求 的一种 过程 。 C
以可靠性为中心的维修(RCM)简介

③ RCM 逻辑分析研究
a.通过失效模式分析,确定给定设备的关键元件; b.对每个关键元件进行 RCM 逻辑判断,选择优化的维修方法, 确定是否需要重新设计或改进; c.确定维修任务、设备和周期,建立维修分析所需数据,过错 成RCM 判断; d.利用可获得的实际设备的可靠性、维修性数据,对维修过程 进行优化。
表2 故障现象分析及维修方法 维修方法 ① ② ③ ④ ⑤ ⑥ ⑦ ⑧ 对叶轮作平衡校正 或清洗叶轮 修理或更换轴承 校直或更换泵轴 检修 检修或更换磨损零件 排除产生气蚀的原因 重新调整 拧紧地脚螺栓
故障现象学 故障产生的原因和机理 (故障模式) 离心泵振动 ① 叶轮磨损不均或流道堵 塞,造成叶轮不平衡 ② 轴承磨损 ③ 泵轴弯曲 ④ 转动部件有摩擦 ⑤ 转动部件松驰或破裂 ⑥ 泵内发生气蚀现象 ⑦ 两联轴器结合不良 ⑧ 地脚螺栓松弛
失效分析阶段 分别在设备、子系统、部件和零件 级的水平上进行失效分析
表1 故障模式的层次表 故障产生的原因和机理
故障现象(故障模式)
离心泵不能正常运转
轴承烧坏 轴承过热
轴承烧坏
轴承过热 润滑 不良、轴承 安装不正 确、轴承磨损等
②
失效模式和影响分析阶段 确定潜在失效模式及其 相应的原因、结果、发生频率和严重性;
8
RCM 技术关键
① 数据的获取 ② 失效模式、机理、原因分析(力学、物理、化学、生物 学机理和人为因素) ③ 鉴定重要项目(故障对设备性能有严重后果的项目)和隐 蔽项目(不易发现因而会成为隐患的项目) ④ RCM 逻辑分析 ⑤ 可靠性、维修性设计与分析
9
① ② ③ ④ ⑤ ⑥ ⑦
RCM 注意的几个问题
以可靠性为中心的维修(RCM) 简介
以可靠性为中心的维修及其在设备维修

三、以可靠性为中心的维修理论的八项基本原理
以可靠性为中心的维修理论认为,一切维修活动,归根 到底是为了保持和恢复设备的固有可靠性。具体地说, 要求根据设备及其机件的可靠性状况,以最少的维修资 源消耗,运用逻辑决断分析方法来确定所需的维修内容、 维修类型、维修间隔期和维修级别,制订出预防维修大 纲,从而达到优化维修的目的。以可靠性为中心的维修 理论的内容可分解为八项基本原理,简称为RCM原理, 它与传统维修的观念有较大的差别。
1980年,西方民航界吸收了RCM方法的优点,将“MSG-2”修 改为“MSG-3”,1988年又修改为“MSG-3修改1”,1993年再次修 改为“MSG-3修改2”。
1990年9月,英国阿兰德公司莫布雷在RCM和“MSG-3修改1” 的基础上,结合民用设备的实际情况,提出了“RCM2”,到1997 年底已在许多国家的钢铁、电力、铁路、汽车、地铁、海洋石油、 核工业、建筑、供水、食品、造纸、卷烟、药品等行业广泛应用。
以可靠性为中心的维修及其在设备维 修
2、系统维修/故障总费用构成图
系统维修/故障费用
元素维修/故障费用
元素故障费用
元素预防维修费用
单一故障费用
多重故障费用
预防பைடு நூலகம்修用材 料、人工费用
元素计划停运造成的损失
故障维修用材 料、人工费用
元素强迫停运造成的损失
机组出力或效率 下降造成的损失
机组强迫停运 造成的损失
修
(五)以可靠性为中心的维修理论的发展
1978年美国联合航空公司诺兰等人受国防部的委托,发表了 《以可靠性为中心的维修》专著,使以可靠性为中心的维修理论 又向前迈进了一大步。从此,人们把制订预防性维修大纲的逻辑 决断分析方法统称为RCM(Reliability-Centered Maintenance)。
保障性分析:5_RCMA
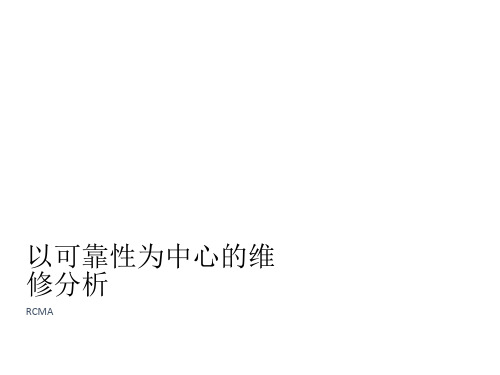
BUAA
4
RCMA的发展
MSG-1 1968 年
EMSG-2 1972 年
Mil-M-5096 1978年
NAUVIR00 1-25-400 1978年
MSG-2 1970 年
AR750-1 1978年
ADAO6657 9
1978年
Mil-Std1843
1985年
Mil-HDBK266
1981年
MSG-3 1978年
BUAA
9
装备的预防性维修大纲的作用
• 维修大纲是确定维修保障任务与所需资源的、制定维修文件的主 要依据(维修工艺卡片、维护规程)
• 分析确定预防性维修要求是维修规划的主要内容,是保障性分析 的重要子过程
• 分析和确定预防性维修要求,制定维修大纲的过程,是发现设计 缺陷,提出更改设计建议以提高产品可靠性、维修性的重要途径
BUAA
10
制定维修大纲的目的
• 通过适当而有效的预防性维修工作,保持和恢复装备固有的安全 性和可靠性水平
• 提出保障系统的功能要求 • 为维修工作分析提供输入 • 提供必要的设计更改所需的信息
BUAA
11
提纲
• 以可靠性为中心的维修(RCMA)简介 • RCMA的基本原理 • 系统与设备RCMA • 结构RCMA • 区域检查 • 维修大纲的综合 • 维修大纲的组织与审核
• 两种情况
• 工作状态的隐蔽功能故障 • 非工作状态的隐蔽功能故障
BUAA
19
潜在故障
• 产品将不能完成规定功能的可鉴别的状态 • 功能故障临近前的产品状态而不是功能故 障前的任何状态
• 产品的这种状态是经观察和检测是可鉴别 的
BUAA
以可靠性为中心的维修
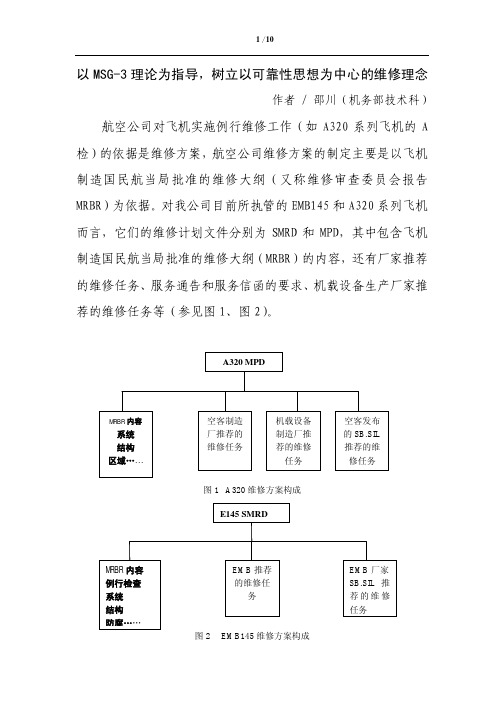
以MSG-3理论为指导,树立以可靠性思想为中心的维修理念作者 / 邵川(机务部技术科)航空公司对飞机实施例行维修工作(如A320系列飞机的A 检)的依据是维修方案,航空公司维修方案的制定主要是以飞机制造国民航当局批准的维修大纲(又称维修审查委员会报告MRBR)为依据。
对我公司目前所执管的EMB145和A320系列飞机而言,它们的维修计划文件分别为SMRD和MPD,其中包含飞机制造国民航当局批准的维修大纲(MRBR)的内容,还有厂家推荐的维修任务、服务通告和服务信函的要求、机载设备生产厂家推荐的维修任务等(参见图1、图2)。
图1 A320维修方案构成航空公司在制定某种机型的维修方案时,必须体现的是MRB (维修审查委员会)的要求,将MRB规定的维修要求以易于航空公司操作和控制的方式体现在维修方案中。
MRBR的制定是以可靠性思想为依据的。
一、以可靠性为中心的维修。
以可靠性为中心的维修是目前国际上通用的用以确定航空器及设备预防性维修需求、优化维修制度的一种系统工程方法。
它的基本目标是以最少的资源消耗保持飞机的可靠性和安全性。
为达到这一目的,需要应用逻辑决断的方法确定航空器及设备预防性维修需求,并力求使方案达到最优。
它的基本做法是:对飞机各个系统进行功能与故障分析,明确系统故障后果;用规范化的逻辑决断程序,确定各故障后果的预防性对策;以最小的维修停机损失和最小的维修资源消耗为目标,优化航空器及各系统的维修策略。
以可靠性为中心的维修思想产生于20世纪60年代。
在此之前,航空界的人们普遍认为:对飞机的预防性维修工作做得越多,翻修周期越短,翻修深度越高,飞机就越可靠、越安全。
想必老一辈的川航机务人对苏制图154飞机的二型定检以上的检查还记忆犹新,那时驾驶舱内的各种仪表几乎全部都拆下来送车间修理,飞机大修的停场时间长达数月。
到了60年代初,美联航通过收集大量的数据并进行分析,得出了两个重要结论,即:对于复杂的飞机系统,除非具有某种支配性的故障模式,否则定时翻修无助于提高其可靠性;对于许多项目,没有一种预防性维修方式是十分有效的。
以可靠性为中心的维修RCM的原理及分析过程

以可靠性为中心的维修RCM的原理及分析过程
一、原理:
以可靠性为中心的维修RCM方法的核心原理是明确设备关键功能的可
靠性要求,并根据设备的实际工作状态和性能指标来制定相应的维修策略。
该方法以设备的关键功能为出发点,通过系统化的分析和决策,实现最佳
的维修方案,以最小化设备故障对生产效率和安全的影响。
二、分析过程:
1.选择分析对象:根据设备的重要性和影响程度,选择需要进行RCM
分析的设备。
2.定义设备功能:明确设备的关键功能,即设备的主要工作任务和性
能要求。
3.确定工作条件:分析设备的使用环境和工作模式,包括工作时间、
工作负荷、工作环境等。
4.收集设备数据:收集设备的历史故障数据、维修记录、维修手册等
相关资料。
5.分析设备故障模式:根据收集到的数据,分析设备的故障模式和原因,确定设备的可能故障模式。
6.评估故障后果:分析设备故障对工作任务和生产效益的影响,评估
故障的后果和风险。
7.制定维修策略:根据故障模式和后果评估结果,制定适当的维修策略,包括预防性维修、修复性维修、替代性维修等。
8.评估维修效果:对采取的维修策略进行实施,并评估维修效果,以验证维修策略的有效性。
9.持续改进:根据维修效果评估的结果,不断进行改进和优化,完善维修策略,提高设备的可靠性和可用性。
通过以上的分析过程,以可靠性为中心的维修RCM方法可以有效提高设备的可靠性和可用性,降低设备故障率和维修成本,提高生产效率和安全性。
同时,该方法还能够提前发现潜在故障模式,预测故障发生的可能性,采取相应的维修措施,避免或减少设备的故障和停机时间。
RCM简介

以时间为基础的维修(TBM-Time Based Maintenance) - 以时间为基础的维修
不管坏与不坏, 不管坏与不坏,修了再说
苏联: 计划维修(PPM-Planning Preventive Maintenance) 苏联: 计划维修 -
按计划大、 我国过去也采用) 按计划大、中、小修(我国过去也采用 小修 我国过去也采用
处理原则: 处理原则:
功能丧失与安全性环境性后果→必须预防维修, 功能丧失与安全性环境性后果 必须预防维修,否则改变设计或流程 必须预防维修 隐蔽性故障对操作人员不是显显而易见的→预防维修为主 隐蔽性故障对操作人员不是显显而易见的 预防维修为主 事后维修(非使用性后果 非使用性后果) 事后维修 非使用性后果 使用性与非使用性→根据效果费用 根据效果费用→决定 使用性与非使用性 根据效果费用 决定 状态维修 预防维修 改进设计
O. 该故障对设备使用 功能是否有严重的不 利影响? 利影响? Y O1. 对有使用性后果 的故障的状态监测工 作是否技术可行? 作是否技术可行? 状态监测<- <-Y 状态监测<- N 状态维修 O2. 定期计划维修工 作是否技术可行的? 作是否技术可行的? 定期计划维修 <-Y <- N
N N1. 对非使用性后果 的故障的状态监测工 作是否技术可行? 作是否技术可行? 状态监测<- <-Y 状态监测<- N 状态维修 N2. 定期计划维修工 作是否技术可靠的? 作是否技术可靠的? 定期计划维修 <-Y <- N
全员生产维修(TPM)(日本 日本) 全员生产维修 日本 全面计划质量维修(TPQM) 全面计划质量维修 适应性维修(AM) 适应性维修 利用率为中心的维修(ACM) 利用率为中心的维修 风险维修(RBM) 风险维修 费用有效性维修(CEM-Cost Effective Maintenance) 费用有效性维修 - 商业关键性维修(CCA-Commercial Criticality Maintenance) 商业关键性维修 -
说说RCM那些事

说说RCM那些事说明:本文是对RCM(以可靠性为中心的维修)的一个科普性的介绍文章,主要介绍其产生背景、进化历史和七步法基本流程,力图正本清源,提供RCM的指导标准。
目录一、什么是RCM?二、RCM的产生历史三、RCM的理念核心四、RCM七步法基本流程一、什么是RCM?这些年RCM这个词越来越得到关注,但是这到底指的是什么呢?说法其实很多,也不大一样。
这个词原文是Reliability Centered Maintenance, 顾名思义,就是以可靠性为中心的维修。
光看这个名称,解释起来可就太宽泛了,和可靠性搭边的都可以往这个词上靠。
实际上,很多培训机构包括论文也的确是这么做的,把很多衍生的臆想的东西都扣了一顶RCM的帽子,感觉立马有点高大上的感觉。
其实人家阿Q就是骂了句脏话而已,除了解读了人性,社会,有人都能解读到太空宇宙去了。
按照维基百科的说法呢, RCM是一套使设备或系统能够满足用户需求的流程。
是不是听起来不像人话,或者说这也太虚了。
好在人家紧跟着说了一句,具体流程定义参见SAE JA1011。
把球踢给了标准,但至少指明了方向,有兴趣的同学可以找来标准仔细学习一下。
我们今天还是慢慢从历史说起吧。
二、RCM的产生历史这话得先从上世纪60年代的美国说起。
那时候美国航空管理局(FAA)和一些商业航空公司针对波音747展开了一些维修理念的研究,主要是针对预防性维护的研究。
到了大约1965年的时候,有了一些发现,研究表明复杂设备的定周期大修对设备的可靠性其实没有什么大的作用或者说作用很小。
如果你是干这一行的,你会知道这个成果其实挺吓人的。
因为到今天为止,大部分设备都还是执行定周期大修管理制度。
而且就是象Solar或GE这样的大牛公司们,他们目前给客户推荐的也还是定周期大修的管理计划。
具体原因咱就不细聊了,还是说RCM的事。
根据这些研究成果,在1967到1968年间,一些航空公司和制造企业组成了一个维修指导委员会(MSG)并发布了他们的第一代指导手册 MSG-1:《维修评估和程序制定手册》,并开始在波音747上实践应用。
- 1、下载文档前请自行甄别文档内容的完整性,平台不提供额外的编辑、内容补充、找答案等附加服务。
- 2、"仅部分预览"的文档,不可在线预览部分如存在完整性等问题,可反馈申请退款(可完整预览的文档不适用该条件!)。
- 3、如文档侵犯您的权益,请联系客服反馈,我们会尽快为您处理(人工客服工作时间:9:00-18:30)。
RCM方法中,所有资产的功能、功能故障以及所有的可能的故障模式都要进行系统的分析和确认。
进而,明确各种可能故障造成的影响以及影响的方式。
一旦收集到这些信息,就可以选择最恰当的资产管理策略。
与其它维修规划方法不同的是,RCM全面考虑了资产维修的各种方式,即:——视情维修工作(on-condition);——计划修复工作;——计划报废工作;——故障检查(探测)(failure-finding);——一次性改变(one-time change)(改变硬件设计,运行程序,人员培训,以及其它非严格意义上的维修工作)。
[编辑]以可靠性为中心的维修的发展历程[1]RCM技术在60年代末起源于美国航空界,首次应用RCM制定维修大纲的是波音747飞机。
70年代中期,RCM引起美国军方的重视,美国防部明确命令在全军推广以可靠性为中心的维修(RCM)。
70年代后期RCM开始在美国陆、海、空三军装备上获得广泛应用。
到80年代中期,美国陆、海、空三军分别就RCM的应用颁布了标准和规范。
例如:1985年2月美空军颁布的MIL-STD-1843,1985年7月美陆军颁布的AMCP750—2,1986年1月美海军颁布的MIL—STD—2173等都是关于RCM应用的指导性标准或文件。
美国国防部指令和后勤保障分析标准中,也明确把RCM分析作为制定预防性维修大纲的方法。
为了更好的应用RCM,美三军除制定明确的指令和标准外,还制定了各自的RCM工作规划。
其中美陆航88-92年的RCM工作规划简要内容包括:①审查修订大修规划:按RCM原理对现有大修规程进行审定,首批审定40个,然后对其余规程进行审定;②应用RCM制订现役飞行维修大纲及维修计划,包括进行故障模式、影响及危害度分析;确定维修项目、方式、修理间隔、要求等。
现役主要机型(AH- 64,UH-60,CH47D,OH-58)均在应用之列;③应用RCM制订在研飞机(LHX)维修大纲及维修计划;④研究、改进RCM有关方法:包括研制故障模式、影响及危害度分析(FMECA)自动化软件;⑤改进RCM决断逻辑,改进“机体状况评价”、“飞机腐蚀分析评价”的技术和设备等;⑥更新技术文件,组织RCM培训;⑦建立和扩大RCM数据库,加强RCM数据的利用等。
结合RCM推广应用的成果,美国陆军实施了多方面的维修改革。
首先是改革陆军战斗车辆(坦克、装甲车辆)的送厂大修规定,改变过去的定程修理规定,实行类似于陆航飞机视情送修的办法。
美陆军规程(AR750-1)《陆军装备维修原则与方针政策》(1978年版)中明确规定:选送“战斗车辆进厂大修的规则只应基于车辆状况,行驶里程不作为确定送修的因素”;“选送的规则应以根据RCM原则确定的因素为依据”。
从美军1977年到1982年实际调查情况看,采用视情送修,比原来定程大修减少送修车辆70%左右,大修费节约是可观的。
陆军维修改革的其它途径还有:采用RCM分析方法审查日常维护保养规定,使维修项目、时间间隔趋于合理,以节约维修人力物力;按RCM原理对大修规程进行修订,改变过去大拆大卸的做法,只进行必需项目、必要深度的修理。
目前美军几乎所有重要的军事装备(包括现役与新研装备)的预防性维修大纲都是应用RCM方法制订的。
RCM不仅被军事领域所重视,而且在商界也具有广泛的应用。
进入90年代后,RCM逐渐在工业发达国家兴起并应用于生产设备的维修管理。
1991年英国Aladon维修咨询有限公司的创始人John Moubray 在多年实践RCM的基础上出版了系统阐述RCM的专著《以可靠性为中心的维修》。
目前美国、英国、日本等国的很多大中型企业都在采用这项技术制定其生产设备的维修策略。
其中英国Aladon维修咨询有限公司,从90年代开始就为40多个国家的1200多家大中型企业成功地进行过RCM的咨询、培训和推广应用工作。
据统计,这些企业中大约25%的高级管理人员受到了RCM初级培训,约10%的企业至少在一个工厂的所有设备上应用了RCM,65%的企业对其所属的部分设备进行过审查,大部分企业计划继续应用RCM来分析其绝大部分的设备。
[编辑]以可靠性为中心的维修的发展动态[1]1、应用范围逐渐扩大RCM 最初应用于飞机及其航空设备,后应用于军用系统与设备,现已广泛用于其它各个行业,如核电企业、电力公司、汽车制造厂等,逐渐扩展到企业的生产设备与民用设施。
为了更准确地反映RCM的应用对象与范围,《RCMⅡ》把RCM定义为:确定有形资产在其使用背景下维修需求的一种过程。
从其定义可以看出RCM的适用对象为有形资产(phsical assets),而不仅仅是传统RCM规定的大型复杂系统或设备。
这里有形资产主要是相对于无形资产(资金或软件)而言,它可以是军用装备、生产设备,也可以是民用设施。
这样的定义使RCM的适用范围大大扩展。
从《RCMⅡ》(97年版)公布的Aladon公司已推广应用RCM的行业清单中可以看出:目前的RCM应用领域已涵盖了航空、武器系统、核设施、铁路、石油化工、生产制造、甚至大众房产等各行各业。
2、用7个基本问题概括RCM分析过程1994年,美军采办政策改革后,美国三军的RCM标准被废止或不再具有强制性,而民用企业领域存在多种RCM版本,承包商使用哪些标准才能代表真正意义上的RCM过程?1999年国际汽车工程师协会(SAE)颁布的RCM标准《以可靠性为中心的维修过程的评审准则》(SAEJA1011)给出了正确的RCM过程应遵循的准则,如果某个大纲制定过程满足这些准则,那么这个过程就可以被称为“RCM过程”。
反之,则不能称之为“RCM过程”。
按照SAEJA1011第五章的规定,只有保证按顺序回答了标准中所规定的七个问题的过程,才能称之为RCM过程。
(1)功能:在具体使用条件下,设备的功能标准是什么?(2)故障模式:什么情况下设备无法实现其功能?(3)故障原因:引起各功能故障的原因是什么?(4)故障影响:各故障发生时,会出现什么情况?(5)故障后果:各故障在什么情况下至关重要?(6)主动故障预防:做什么工作才能预防各故障?(7)非主动故障预防:找不到适当的主动故障预防措施应怎么办?回答上述七个问题,必须对设备的功能、功能故障、故障原因及影响有清楚明确的定义,通过“故障模式及影响分析(FMEA)”对设备进行故障审核,列出其所有的功能及其故障模式和影响,并对故障后果进行分类评估,然后根据故障后果的严重程度,对每一故障式做出“是采取预防性措施、还是不采取预防性措施待其发生故障后再进行修复的”决策。
此外,还应明确如果采取预防性措施,应选择哪种办法。
RCM分析中对故障后果的评估分类和预防办法的选择是依据逻辑决断图进行的。
3、对安全与环境性后果更加重视'RCM认为:故障后果的严重程度影响着我们采取预防性维修工作的决策。
即如果故障有严重后果,就应尽全力设法防止其发生。
反之除了日常的清洁和润滑外,可以不采取任何预防措施。
RCM过程把故障后果分成下列4类:(1)隐蔽性故障后果。
隐蔽性故障没有直接的影响,但它有可能导致严重的、经常是灾难性的多重故障后果;(2)安全性和环境性后果。
如果故障会造成人员伤亡,就具有安全性后果;如果由于故障导致企业违反了行业、地方、国家或国际的环境标准,则故障具有环境性后果;(3)使用性后果。
如果故障影响生产(产量、产品质量、售后服务或除直接维修费用以外的运行费用),就认为具有使用性后果;(4)非使用性后果。
划分到这一类里的是明显功能故障,它们既不影响安全也不影响生产,它只涉及直接维修费用。
环境性后果已成为预防性维修决策的重要因素之一。
将环境性后果引入RCM决策过程是RCMⅡ的重要贡献,也是RCMⅡ与其它RCM版本最显著的区别。
4、预防性维修工作的分类更加科学RCMⅡ把预防性维修工作定义为预防故障后果而不仅仅是故障本身的一种维修工作,这样的定义使预防性维修的范畴大大扩展。
这样划分后RCMⅡ把预防性维修分为两大类,即:4.1 主动性工作为了防止产品达到故障状态,而在故障发生前所采取的工作。
它们包括传统的预计性维修和预防性维修,包括:定期恢复、定期报废和视情维修等;(1)定期恢复与定期报废。
定期恢复要求按一个特定的工龄期限或在工龄期限之前,重新加工一部件或翻修一组件,而不管当时其状态如果。
与此相同,定期报废工作要求按一个特定的工龄期限或在工龄期限之前报废,也不顾其状态;(2)视情维修。
视情维修是通过监控掌握装备的状况,对其可能发生功能故障的项目进行必要的预防维修。
视情维修适用于耗损故障初期有明显劣化症侯的装备,但需要适当的检测手段,如功能检测和先进的技术等。
4.2 非主动性工作当不可能选择有效的主动性工作时,选择非主动性对策处理故障后的状态,它包括故障检查、重新设计和故障后修理。
(1)故障检查。
在RCMⅡ中故障检查工作是指定期地检查隐蔽功能以确定其是否已经发生故障,从预防故障的时机上讲,它是在隐蔽功能发生故障发生后为防止多重故障的后果而进行的一项检查工作。
故障检查工作需要定期地检查隐蔽功能以确定其是否故障(这里基于状态的工作是检查是否已发生故障);(2)重新设计。
重新设计需改变系统的固有能力,它包括硬件的改型和使用操作程序的变化两个方面;(3)无预定维修。
如其名称所指,这种对策对所研究的故障模式不需进行预计或预防,因此只是简单地允许这些故障发生并进行修理,这种对策也称为故障后修理。
5、对RCM逻辑决断图进行改进RCMⅡ的逻辑决断图的基本流程与传统的RCM逻辑断决断图(MSG-3,MIL—STD1843,GJB1378)相比,有了一定的改进,主要体现在以下几点:(1)增加了对环境问题的考虑,把隐蔽性后果与其它后果并列使故障后果有四个分支,即隐蔽性故障后果、安全性和环境性后果、使用性后果和非使用性后果;(2)使用“技术可行性”和“值得做”,代替传统的决断准则用语“适用性”与有效性。
因为RCMⅡ的提出者认为后两个术语的使用方式在维修领域不为人们所熟悉,需要经常做大量的解释;(3)图中增加了各项具体工作的“技术可行性”和“值得做”的详细准则;(4)图中未单独把保养/润滑列为一项预防性维修工作,但RCMⅡ要求对集中润滑系统作完整的RCM分析,把各独立的润滑点看作是单独的故障模式。
(5)把故障检查看作是非主动性工作,排在各项主动性工作之后,而在传统的决断图中故障检查工作排在了定期恢复、定期报废等主动性工作之前。
6、注重RCM实施过程的管理尽管RCM的应用属于技术层面的问题,但它产生的结果对装备的使用以及维修制度产生直接的影响,没有决策部门的支持参与,RCM的推广应用不可能取得理想的结果。
当前在RCM的实施过程中比较注重加强管理,具体表现在:6.1成立RCM指导小组RCM指导小组由熟悉并能对装(设)备维修制度运行产生影响的有关领导、熟悉RCM 原理与分析过程的专家和熟悉装(设)备结构与维修的人员共同组成。