Hardware support for flexible distributed shared memory
MT3339
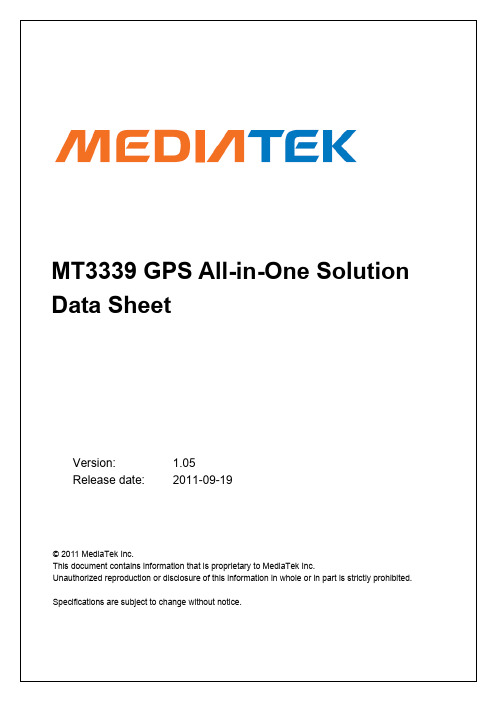
Pin Assignment and Descriptions .............................................................................................. 9 2.1 2.2 Pin assignment (top view) .................................................................................................... 9 Pin descriptions .................................................................................................................... 9
ห้องสมุดไป่ตู้
Description Update TFBGA ball map and pin description Update pin-mux and strap information Update RF part description Update System overview Update RF part electrical characteristics Update analog part electrical characteristics Update RF LDO electrical characteristics Update power scheme Add RTC domain power scheme Modify according to YC Chien’s suggestion Update by JN Yang about UART baud rate and SPI/I2C clock rate Update RF related description Update system overview by Andy Lee Update host interface related description Update power scheme Update block diagram Update crystal frequency range Update external LNA related information Update power scheme diagram and EEPROM I2C interface timing diagram Update power related description Update footprint size Change minimum input power to 2.7V Sync PIN naming of DC characteristic table and change minimum input power to 2.8V Update power scheme and RF information Update description of 32K_OUT pin Add ECLK and SYNC description Add 1.2V IO characteristic for TIMER and 32K_OUT and update serial flash size to 128Mb Remove description about factory testing and internal SRAM size Remove description about strap function tcxo on/off 1. Update RTC leakage information to typ 2. Update package dimensions information Update RF related descriptions 1. Remove Vcc description in 6.3.1 2. Add strap pin tldo_sw_sel description Change MAX of VIH for TIMER and 32K_OUT to 3.6V Change description in 5.20 about CLDO off Add RF LNA MIN of VGA gain and MAX of noise figure © 2011 MediaTek Inc. Page 2 of 37
Seagate GoFlex Desk 外接硬盘说明书

Perfect for when you need to:• S tore or back up photos, movies, music and documents • A ccess your files with both PC and Mac® computers Capacities500GB, 1TB, 2TB, 3TBProtect, store and access files through the interface of your choice with the world’s most versatile drive. The GoFlex™ Desk external drive delivers high-capacity storage and automatic, continuous backup with encryption for all your files with its pre-loaded software. The included plug-and-play USB 2.0 or USB 3.0 adapter makes it easy to connect to your PC or Mac® computer and it displays the drive’s available storage capacity. As the world’s most upgradable external desktop drive, you now have the ability to upgrade your connection interface to suit your needs. Plus, the option to place the drive vertically or horizontally complements any desktop.Access files with the interface of your choice.Available with the standard USB 2.0 interface or the USB 3.0 interface, or upgrade to the FireWire® 800 adapter. Free your files.With the included NTFS driver for Mac®, you can now interchangeably store and access files from PC and Mac computers without reformatting. The NTFS driver is simply installed once on your Mac computer, allowing it to access and store files in a PC compatible format*.SuperSpeed USB 3.0 for Faster PerformanceThe GoFlex Desk drive is available with a USB 3.0 interface that provides up to 10x faster data transfer rates compared to USB 2.0 interfaces. USB 3.0 is backward compatible with USB 2.0 interfaces so you have the flexibility to access files from any PC.* Reformatting to HFS+ required to use backup software for Mac or Time Machine® softwareHighlights• USB 2.0 or USB 3.0 Plug-and-play• Easy-to-use pre-loaded backup software with encryption• World’s most versatile external drive - upgrade to a faster interface with a GoFlex™ Desk desktop adapter• Includes GoFlex Desk USB 2.0 or USB 3.0 adapter with capacity gauge display• Offers both vertical and horizontal drive orientation• 2-year limited warranty© 2010 Seagate Technology LLC. All rights reserved. Seagate, Seagate Technology, the Wave logo, FreeAgent and GoFlex are trademarks or registered trademarks of Seagate Technology LLC or one of its affiliated companies in the United States and/or other countries. All other trademarks or registered trademarks are the property of their respective owners. When referring to drive capacity, one gigabyte, or GB, equals one billion bytes and one terabyte, or TB, equals one thousand billion bytes. Your computer’s operating system may use a different standard of measurement and report a lower capacity. In addition, some of the listed capacity is used for formatting and other functions and will not be available for data storage. The export or re-export of hardware or software containing encryption may be regulated by the U.S. Department of Commerce, Bureau of Industry and Security (for more information, visit ). Actual data rates may vary depending on operating environment and other factors. Seagate reserves the right to change, without notice, product offerings or specifications. DS1709.3 1009-AMERProduct Dimensions 6.22in L x 4.88in W x 1.73in D (158mm x 124mm x 44mm)Weight: 2.38lb (1.08kg)Retail Packaging SpecsBox dimensions: 7.87in L x 9.06in W x 3.54in D (200mm x 230mm x 90mm) Box weight: 2.93lb (1.33kg)Master carton dimensions: 14.96in L x 9.52in W x 8.58in D (372mm x 242mm x 218mm) Master carton weight: 12.44lb (5.66kg)Master carton quantity: 4Master cartons per pallet: 60Pallet dimensions: 43.93in L x 38.11in W x 47.76in D (1,116mm x 968mm x 1,213mm)Pallet weight: 785lb (356.80kg)Pallet layers: 5System Requirements• Windows ® 7, Windows Vista ®, Windows ® XP (32-bit & 64-bit) operating system or • O perating system Max OS X 10.4.6 Tiger or higher, 10.5 Leopard or 10.6 Snow Leopard (the 32-bit kernel). Reformatting for Mac may be required.• USB 2.0 portCompatibility may vary depending on user’s hardware configuration and operating systemInside the Box• GoFlex ™ Desk external drive• Backup and encryption software pre-loaded on drive • NTFS driver for Mac ® pre-loaded on drive*• GoFlex ™ Desk USB 2.0 or USB 3.0 adapter base with capacity gauge • Power supply•5-foot (150cm) USB 2.0 cable or 4-foot (120cm) USB 3.0 cable • Quick start guide• 2-year limited warranty。
电机控制开发套件motorBench 2.25说明书
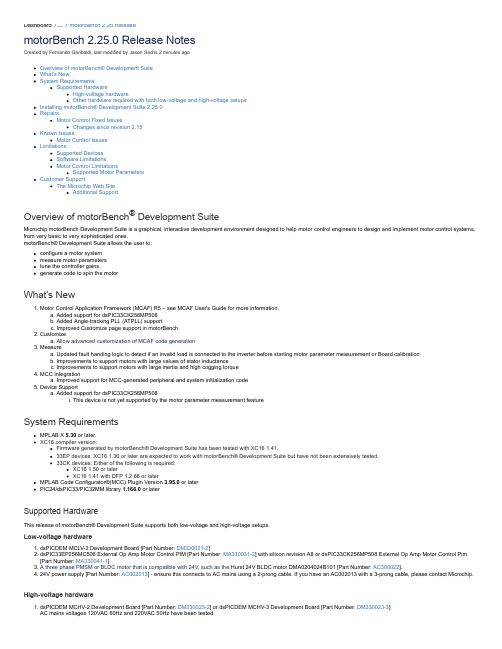
Dashboard/…/motorBench 2.25 ReleasemotorBench 2.25.0 Release NotesCreated by Fernando Garibaldi, last modified by Jason Sachs 2 minutes agoOverview of motorBench® Development SuiteWhat’s NewSystem RequirementsSupported HardwareHigh-voltage hardwareOther hardware required with both low-voltage and high-voltage setupsInstalling motorBench® Development Suite 2.25.0RepairsMotor Control Fixed IssuesChanges since revision 2.15Known IssuesMotor Control IssuesLimitationsSupported DevicesSoftware LimitationsMotor Control LimitationsSupported Motor ParametersCustomer SupportThe Microchip Web SiteAdditional SupportOverview of motorBench® Development SuiteMicrochip motorBench Development Suite is a graphical, interactive development environment designed to help motor control engineers to design and implement motor control systems, from very basic to very sophisticated ones.motorBench® Development Suite allows the user to:configure a motor systemmeasure motor parameterstune the controller gainsgenerate code to spin the motorWhat’s New1. Motor Control Application Framework (MCAF) R5 – see MCAF User's Guide for more information.a. Added support for dsPIC33CK256MP508b. Added Angle-tracking PLL (ATPLL) supportc. Improved Customize page support in motorBench2. Customizea. Allow advanced customization of MCAF code generation3. Measurea. Updated fault handing logic to detect if an invalid load is connected to the inverter before starting motor parameter measurement or Board calibrationb. Improvements to support motors with large values of stator inductancec. Improvements to support motors with large inertia and high cogging torque4. MCC Integrationa. Improved support for MCC-generated peripheral and system initialization code5. Device Supporta. Added support for dsPIC33CK256MP508i. This device is not yet supported by the motor parameter measurement featureSystem RequirementsMPLAB X 5.30 or later.XC16 compiler version:Firmware generated by motorBench® Development Suite has been tested with XC16 1.41.33EP devices: XC16 1.36 or later are expected to work with motorBench®Development Suite but have not been extensively tested.33CK devices: Either of the following is required:XC16 1.50 or laterXC16 1.41 with DFP 1.2.66 or laterMPLAB Code Configurator®(MCC) Plugin Version 3.95.0 or laterPIC24/dsPIC33/PIC32MM library 1.166.0 or laterSupported HardwareThis release of motorBench®Development Suite supports both low-voltage and high-voltage setups.Low-voltage hardware1. dsPICDEM MCLV-2 Development Board [Part Number: DM330021-2]2. dsPIC33EP256MC506 External Op Amp Motor Control PIM [Part Number: MA330031-2] with silicon revision A8 or dsPIC33CK256MP508 External Op Amp Motor Control Pim[Part Number: MA330041-1].3. A three phase PMSM or BLDC motor that is compatible with 24V, such as the Hurst 24V BLDC motor DMA0204024B101 [Part Number: AC300022].4. 24V power supply [Part Number: AC002013] - ensure this connects to AC mains using a 2-prong cable. If you have an AC002013 with a 3-prong cable, please contact Microchip.High-voltage hardware1. dsPICDEM MCHV-2 Development Board [Part Number: DM330023-2] or dsPICDEM MCHV-3 Development Board [Part Number: DM330023-3]AC mains voltages 120VAC 60Hz and 220VAC 50Hz have been tested.2. dsPIC33EP256MC506 External Op Amp Motor Control PIM [Part Number: MA330031-2] with silicon revision A8 or dsPIC33CK256MP508 External Op Amp Motor Control Pim[Part Number: MA330041-1].3. A three phase PMSM or BLDC motor that is compatible with rectified AC mains voltage, such as the Leadshine 400W BLDC motor EL5-M0400-1-24 [Part Number: AC300025].Other hardware required with both low-voltage and high-voltage setups1. A USB-to-logic-level-UART converter from the following list:a. Saelig USB-COM-U or USB-COM-U13b. TRENDnet TU-S9 v2.02. Programming tool - one of the following tools: Real ICE, ICD33. Board calibration load resistors - this is optional, please see motorBench® Development Suite User's Guide document for more detailsInstalling motorBench ® Development Suite 2.25.0To install the MPLAB ® Code Configurator v3.95 Plugin1. In the MPLAB® X IDE, select Plugins from the Tools menu2. Select the Available Plugins tab3. Check the box for the MPLAB® Code Configurator v3, and click on InstallTo install different peripheral library version or motorBench ® Development Suite version when connected to internet1. Create a project with dsPIC33EP256MC506 or dsPIC33CK256MP508, or use the sample project.2. Open MPLAB® Code Configurator3. In the Versions tab under PIC24/dsPIC33/PIC32MM MCUs, find the multiple library versions (loaded version is indicated by the green check mark)4. Right-click on the required version of the library and select Mark for Load5. In the Versions tab under motorBench ® Development Suite find the multiple library versions (loaded version is indicated by the green check mark)6. Right-click on the 2.25.0 version of the library and select Mark for Load7. Click on Load Selected Libraries button to load the marked libraries.To install different peripheral library version or motorBench® Development Suite version when not connected to internet1. In the MPLAB® X IDE, select Options from the Tools menu2. Select Plugins tab3. Click on Install Library4. Add pic24-dspic33-pic32mm_v1.166.mc3lib5. Add motorBench_2.25.0.mc3lib6. Restart MPLAB® X IDERepairsMotor Control Fixed IssuesChanges since revision 2.15The following aspects of motorBench® Development Suite and the Motor Control Application Framework (MCAF) have been updated:MCAF has been updated to R5, includingChanges in R2:Support for DC link compensationSupport for overmodulationSupport for wider range of low-voltage motorsUpdated HAL for future MCHV2 supportUpdated Motor Control LibraryNumerous minor fixesChanges in R3:MCC system module compatibilityMCHV-2 and MCHV-3 supportInverter maximum current now has a 1:1 ratio with the maximum commanded dq-frame current of the drive, operating in FOC (in R2 this incorporated a deratingfactor)Other minor fixesChanges in R4:MCC peripheral supportParameter customizationQuadrature encoder supportAdded new startup method (Weathervane startup)Other minor fixesChanges in R5:Added device support for dsPIC33CK256MP508Added Angle-tracking PLL (ATPLL) sensorless estimatorImproved motorBench Customize page supportOther minor fixesSections in this release notes affected:Other RequirementsLimitationsSupported Motor ParametersKnown IssuesPlease note:We do not recommend using the MCP2200 USB to RS232 Demo Board [Part number: MCP2200EV-VCP ] with this release of motorBench® Development Suite.While testing, we have observed more frequent occurrence of a serial communication timeout issue while running motor parameter measurement using this cable.See Known Issues section of this document for more information (MCGUI-1141)Motor parameter measurement is only supported on dsPIC33EP256MC506 device.Issue Key Summary WorkaroundMBPLAN-673Serial port does not get closed programmatically when MCC exits during motor parametermeasurementIf you exit SC during execution, restart MPLAB X.MBPLAN-932Exception during attempted creation of a runtime properties class No workaround needed, this issue doesn't have an impact on thefunctionality.MBPLAN-984Improve error reporting for SC build errors in the event of a code generation failureMBPLAN-1095Switching projects after loading motorBench erroneously allows motorBench code to generate for new projectMBPLAN-1160"Import Motor" and "Export Motor" buttons can be clicked multiple times, opening multiple dialog boxesMotor Control IssuesIssue Key SummaryDB_MC-411Current calibration happens only once (at part reset) rather than upon entry to MCSM_RESET stateDB_MC-560Speed controller exhibits chattering behavior at voltage saturation hysteresis boundary (MCAF)DB_MC-978"Soft start" gate drive in board_service.c has duty cycle that is too smallDB_MC-1092PLL estimator may not converge into rotor reference frame while using the Classic startup method in MCAFDB_MC-1396PLL calculations in code generation do not allow motor.velocity.nominal to be more than 1250Hz electrical (=20kHz/8/2)DB_MC-1415With some motors and 12V operation, increased velocity margin improves startup but creates unstable estimatorDB_MC-1430Quanum MT4012 unstable in closed-loop operation at 4200 RPM speed and aboveDB_MC-1491With Quanum MT4012, MCAF may not detect stallDB_MC-1492Quanum MT4012 Stalls on pressing 'S3'(reverse) at low speeds and on changes to speed command potentiometerDB_MC-1495Anaheim BLY342D-24V-3000, BLY342D-48V-3200 motors creates hardware over-current during stall-detect testingDB_MC-1521Closed loop speed step response overshoot - MCHV2, Leadshine 400DB_MC-1892Some motors with extreme parameters may produce out-of-range error for stall_detect.group.timerCountsVarianceDetect (detected in Monte Carlo analysis)DB_MC-1920Board service isrCount-based timing is not guaranteedDB_MC-1922LED patterns not displayed when in the TEST_DISABLE or TEST_ENABLE statesDB_MC-2122BLWS232D motor startup in QEI mode causes a false detect for stall-detectionDB_MC-2213Deadtime needs to be changed in both MCC and motorBench to affect codeDB_MC-2275Large current rampup times may not start (STARTUP_TORQUE_RAMPUP_RATE = 0)DB_MC-2309QEI tracking loop Kp and Ki produce out-of-range errors for low-speed motorsDB_MC-2323Weathervane transition state should not have active damping enabledDB_MC-2387DC link voltage measurement may have too much phase delay for MCAF DC link compensation to work effectivelyDB_MC-2606MCC-generated code has incorrect IESO/FNOSC config bits for 33CKDB_MC-2671MCAF_CaptureTimestamp calls incorrect timer function for 33CK devicesDB_MC-2785Current sense signal integrity issue with 33CK during overmodulationLimitationsSupported DevicesmotorBench® Development Suite supports these devices:1. dsPIC33EP256MC5062. dsPIC33CK256MP508Software LimitationsmotorBench® Development Suite is tested for serial communication using Windows 7 and Windows 10 platforms. Other platforms may work with standard baud rates, but this operation has not yet been verified.Motor Control LimitationsFollowing are the known limitations for this release of motorBench® Development Suite:1. One mechanical load - constant load. This represents a mechanical load with constant inertia, viscous damping, and friction. The velocity control loop can generally rejectexternal disturbance torques, within the rated current of the motor and board, and within the bandwidth of the velocity control loop. Mechanical loads with time-varying or angle-varying inertia, viscous damping, and friction, such as a blower, compressor, or pump, are currently not supported.2. One motor type - PMSMMCLV-2:The reference motor is the Nidec Hurst motor DMA0204024B101 (MicrochipDirect part number AC300022). Microchip has also validated motorBench® DevelopmentSuite (including motor parameter measurement) with motors with parameters plotted below. Please also read the following section on Supported Motor Parameters. IfmotorBench® Development Suite is unable to spin a motor successfully, please contact Microchip staff for additional assistance.(Note: Mechanical time constant (2/3)×JR/Ke² represents the time constant of velocity acceleration under an open-loop synchronous-frame voltage step, neglecting the effects of inductance, with J, R, and Ke expressed in canonical metric units. R is expressed as line-neutral resistance = half of line-line resistance, and Ke is expressed as V/(rad/s) line-neutral zero-peak = Vrms/KRPM (line-line) × 0.007796968)MCHV-2/MCHV-3:The reference motor is the Leadshine 400W motor EL5-M0400-1-24 (MicrochipDirect part number: AC300025). Microchip has validated motorBench® DevelopmentSuite (including motor parameter measurement) with motors with parameters plotted below. Please also read the following section on Supported MotorParameters. If motorBench® Development Suite is unable to spin a motor successfully, please contact Microchip staff for additional assistance.3. Boarda. dsPICDEM™ MCLV-2 development board. This release of motorBench® Development Suite is compatible with modifications to the board to alter its rated current orvoltage. Contact your local Microchip office to obtain the document "Using MCLV-2 with motorBench® Development Suite to support alternative current and/or voltageratings", which provides guidance for such modifications. Other modifications may not be compatible.b. dsPICDEM™ MCHV-2 and MCHV-3 development boards. This release of motorBench® Development Suite is compatible with unmodified MCHV-2 and MCHV-3development boards.4. Motors should be well-matched to the board and operating voltage. The nominal DC link voltage of the MCLV-2 board is 24V. This voltage can be changed by cutting jumperJ6 and using an appropriate power supply connected to the appropriate terminals of J7. Use of a mismatched motor (for example, a 12V motor used with a 24V DC link voltage) may cause a hardware over-current fault; in this case motor parameter measurement may fail with the message "Fault Code #10: Undefined Fault". Retry with an appropriate DC link voltage.5. Two PIMs and Two devices - dsPIC33EP256MC506 External OpAmp PIM with silicon revision A8 or dsPIC33CK256MP508 External OpAmp PIM. (Please see the HardwareSetup section of the motorBench User's Guide for important modifications to dsPIC33EP256MC506 External OpAmp PIM for use in MCHV-2 and MCHV-3.)6. One algorithm - FOC7. Estimators - PLL, QEI, ATPLL8. Motor parameter measurement:a. Performance criteria adjustment is not presently supported. This includes adjustment of phase margin and PI phase lag at crossover in the current loop; Microchip hasnot completed validation and documentation of these adjustments.9. Autotuning:a. Performance criteria adjustment of the current loop is not presently supported. This includes adjustment of phase margin and PI phase lag at crossover; Microchiphas not completed validation and documentation of these adjustments.b. Use of performance criteria adjustment of the velocity loop is not fully documented or tested. We recommend not adjusting phase margin or PI phase lag unlessnecessary; cases where this is likely to occur are large inertias where αJ = JR/LK m2 > 10, for which an increase of phase margin is appropriate. Phase margin valuesbetween 70 and 85 degrees are recommended in this case, with larger values providing additional stability at the cost of lower velocity bandwidth.10. Axis management not currently implemented - supports only one axis.11. Code generation:a. PWM switching frequency is fixed at 20kHz and does not reflect the value entered under Board parametersb. Integration with external user-supplied code may involve substantial changes. Some guidelines for this are given in the documentation for the Motor ControlApplication Framework. While it is possible to integrate the code generated from motorBench® Development Suite with external code, it is the responsibility of the end user to validate this combination.12. Required compiler settings:a. Optimization-O1 or greater; -O0 and -Os will both compile without errors but do not execute fast enough to complete within the 50 microsecond ADC ISR. Note: at higheroptimization levels, in-circuit debugging using MPLAB X will behave unreliably with respect to breakpoints and single-stepping through C code.The "Omit frame pointer" and "Unroll loops" settings must be enabled.b. Memory model:Large data model (handles using pointers, not direct addressing, to allow for more than 8K of program variables)Small scalar modelc. Additional options:-Wno-volatile-register-var -finlined. Test harness: In order for the test harness to be enabled, the symbols MCAF_TEST_PROFILING and MCAF_TEST_HARNESS should be defined.13. Recommended compiler settings:a. Additional options:-WundefSupported Motor ParametersSince version 2.15, motorBench®Development Suite supports a wide range of motors, subject to the following notes:Ranges of motor parameters (including rated values and computed metrics) must be within the limits noted in either range-limits-mclv2.html or range-limits-mchv2.html.These ranges were tested to ensure that code generation produced firmware constants that were within bounds.Motor parameter measurement does not need to complete successfully but valid motor parameters are required. Some motors may have too low of an inductance or resistance, and may fail motor parameter measurement.Other particular issues that may cause incompatibility with motorBench®Development Suite includeLarge inertia values – in this case, increasing voltage loop phase margin may prevent stability problems. (See "Autotuning" in the Limitations section of this document.) Rotor magnetic saliency – if there are significant differences between Ld and Lq (>10% difference) then some of the MCAF algorithms may not work optimally. Highermismatch between Ld and Lq is typically found in interior-permanent magnet (IPM) motors, and is an intentional feature of the design. See the MCAF User's Guide for more information.Large back-EMF harmonics – a quasi-sinusoidal back-emf is assumedIssues involving individual motor control algorithms, such as PLL estimator, motor startup, or stall detectionHigh cogging torqueMismatch between motor and drive (namely using a motor with current and/or voltage requirements significantly different from that of the hardware) Microchip cannot guarantee that motorBench®Development Suite will work correctly with all motors. If a particular motor does not work properly, please contact the MCU16 Motor Control Team for further guidance.Customer SupportThe Microchip Web SiteMicrochip provides online support via our web site at . This web site is used as a means to make files and information easily available to customers. Accessible by using your favorite Internet browser, the web site contains the following information:Product Support – Data sheets and errata, application notes and sample programs, design resources, user’s guides and hardware support documents, latest software releases and archived softwareGeneral Technical Support – Frequently Asked Questions (FAQs), technical support requests, online discussion groups/forums (), Microchip consultant program member listingBusiness of Microchip – Product selector and ordering guides, latest Microchip press releases, listing of seminars and events, listings of Microchip sales offices, distributors and factory representativesAdditional SupportUsers of Microchip products can receive assistance through several channels:Distributor or RepresentativeLocal Sales OfficeField Application Engineering (FAE)Technical SupportCustomers should contact their distributor, representative or field application engineer (FAE) for support. Local sales offices are also available to help customers. A listing of sales offices and locations is available on our web site.Technical support is available through the web site at: 。
华为OSN3500设备CES业务高级属性相关参数

本文档介绍华为OSN3500可以配置以及查询CES业务高级属性的相关参数。
表1 配置PW 高级属性的参数说明域值域说明RTP头禁止、使能缺省值:禁止表示配CES业务时,RTP头封装功能是否使能。
RTP头用来装载时钟信号。
对华为OSN3500系统的影响:RTP头使能,系统才支持自适应时钟恢复ACR的功能。
与其它参数的关联关系:修改PW相关参数之前,需要确认PW没有和业务进行绑定;完成修改后,需要将PW和业务进行绑定,然后才能查询该参数是否修改成功。
抖动缓冲时间(us)125~64000缺省值:8000 表示配置业务的抖动缓冲区大小。
配置抖动缓冲时间的主要目的是为了吸收网络侧的抖动。
对华为OSN3500系统的影响:抖动缓冲时间影响业务的时延。
配置抖动缓冲时间之后,需要等待接收了二分之一抖动缓冲时间的数据时,系统才启动下面的操作。
取值建议:设置抖动缓冲时间的步长为125,即取值只能是:125、250、375、500……64000。
与其它参数的关联关系:域值域说明与报文装载时间关系紧密,要求抖动缓冲时间必须大于两倍报文装载时间。
修改PW相关参数之前,需要确认PW没有和业务进行绑定;完成修改后,需要将PW和业务进行绑定,然后才能查询该参数是否修改成功。
报文装载时间(us) 125~5000缺省值:1000 表示每个报文装载的持续时间。
通过设置报文装载时间可以提高封装效率。
对华为OSN3500系统的影响:影响每个报文中封装的E1信号帧数。
取值建议:设置报文装载时间的步长为125,即取值只能是:125、250、375、500……5000。
承载CES业务的每条PW带宽默认为3M,当“报文装载时间”为“125”或“250”,且“RTP头”设置为“使能华为模式RTP”或“使能标准RTP”时,每条PW的带宽为4M。
与其它参数的关联关系:与抖动缓冲时间关系紧密,要求抖动缓冲时间必须大于两倍报文装载时间。
修改PW相关参数之前,需要确认PW没有和业务进行绑定;完域值域说明成修改后,需要将PW和业务进行绑定,然后才能查询该参数是否修改成功。
DIR-890L R AC3200 Ultra Wi-Fi Router 用户手册说明书

AC3200 Ultra Wi-Fi RouterDIR-890L/ROverviewThe AC3200 Ultra Wi-Fi Router delivers premium performance for today’s most demanding tasks: HD streaming, gaming, and multiple device usage. It comes packed with speeds of up to 3.2Gbps 1, a dual-core processor, three bands (one 2.4GHz and two 5GHz), AC SmartBeam technology, Intelligent Quality of Service (QoS) with traffic prioritization, six high-performance external antennas for maximum range, a new user interface, Smart Connect and with a really easy setup. The perfect combination of performance and ease of use.Smarter Wireless AC FeaturesThe AC3200 Ultra Wi-Fi Router creates an incredibly fast and far-reaching home network for all of your connected devices. The DIR-890L with Smart Connect provides Band Steering Technology to prevent your network from being bottlenecked by devices. In other words, Smart Connect Technology will efficiently select the fastest Wi-Fi for every device. SmartConnect will also simplify your Single Home Network, with one SSID (wireless network identifier) and a security key for all of your devices. All that great technology to let you enjoy more of the stuff you love doing the most.Controlling Your Network Just Got EasierControl your network like never before. Using the new user interface, you can monitor internet activity, block unwanted devices, and prioritize (drag and drop) your devices with our intelligent QoS engine, all from our redesigned UI. It’s really easy to use; you can even check on your connected devices’ statistics. Bottom line, fewer clicks to get where you need to go.FeaturesConnectivity• Advanced Wireless AC beamforming dramatically enhances wireless signal strength and throughput • 802.11 a/g/n/ac wireless LAN for a complete range of wireless compatibility • Gigabit WAN and LAN ports for high-speed wired connections• Two USB ports (one 3.0 and one 2.0) to connect storage drives and printers for sharing mydlink R Cloud• Remotely view and manage your network over the Internet• mydlink Lite mobile app helps you access, manage and view your network remotelySmartConnect• Band steering dynamically balances wireless clients among the three wireless bands QoS• Tracks the type of network traffic (HD media streaming, web surfing, online gaming) and decide which applications deserves higher priority Security• WPA & WPA2 wireless encryption protects the network from intruders• Wi-Fi Protected Setup (WPS) securely addsdevices to your network at the push of a buttonAC SmartBeam Gigabit Smarter BandwidthDual-Core ProcessorSpecifications are subject to change without notice. D-Link is a registered trademark of D-Link Corporation and its overseas subsidiaries. All other trademarks belong to their respective owners. ©2014 D-Link Corporation. All rights reserved.U.S.A. | 17595 Mt. Herrmann Street | Fountain Valley, CA 92708 | 800.326.1688 | For more informationUpdated November 6,, 20144 Gigabit LAN Ports Connects up to 4 wiredInternet Port Plug your Internet cable in here USB 2.0 PortShare aprinterWPSButton One buttonsetupUSB 3.0 Port 5Share media from a USB storageSpecifications are subject to change without notice. D-Link is a registered trademark of D-Link Corporation and its overseas subsidiaries. All other trademarks belong to their respective owners. ©2014 D-Link Corporation. All rights reserved.U.S.A. | 17595 Mt. Herrmann Street | Fountain Valley, CA 92708 | 800.326.1688 | For more informationUpdated November 6,, 20141Maximum wireless signal rate derived from IEEE standard 802.11ac specifications which are subject to change. Actual data throughput will vary. Network conditions and environmental factors, including volume of network traffic, building materials and construction, and network overhead, lower actual data throughput rate. Environmental factors will adversely affect wireless signal range.2Compatibility with more devices will be available in the future.3Latest software and documentation are available at .4Software included is not Mac-compatible.5Maximum transfer rate based on USB 3.0 specifications. Actual data throughput will vary. To meet USB3.0 transfer speeds, USB 3.0 hubs, cables and devices are required.61-Year Limited Warranty available only in the USA.。
用于低功耗、非刚性平面应用的柔性AMOLED器件

ห้องสมุดไป่ตู้
文章编号 :0 6 6 6 (o o 1— 0 0 0 10 — 2 g 2 l )1 0 1 —7
用于低 功耗 刚性平 面应 用 的 非 柔 性 AM 件 OL D器 E
r n e o e o u i n r p o t nt sa e b i g c e t d a g f v lt a y o p ru i e r e n r a e . r o i Ke wo d : y r s AM OL D; O —p w e ; l x be d s ly E lW o r f il ip a e
作 者 针 对 P OL D显 示器 展 望 了一 个 五 阶 段 H E 路 线 图 : 1 低 功耗 —— 显示 器 件 仍然 制 备 在 刚性 的 () 玻璃基板上 , 但具 有低 功耗 和 较 薄 的 外形 ;2) ( 非刚 性— — 去 掉 了玻 璃 基板 , 示器 件 更 薄且 不易 破碎 , 显 具 有 有 限 的柔性 ; 3) 弯 曲—— 显 示器 可 弯 曲且 各 ( 可 层 结 构 之间具 有 一 致性 ;4) 卷 曲— — 这 个 阶段 的 ( 可 显 示器 在 某 个 纬 度 非 常 柔 软 , 因此 可 以卷 成 一 卷 ; ( 任 意 形状— — 这 是 柔性 显 示 的终 极 阶段 , 示器 5) 显
文献 标识码 : B
Fe il lxbe AMOL EDsf rL w-P we ,Ru g d Ap l a in o o o r g e pi t s c o
Ruqn iig Ma, k c , n ui . o Mie Ha k a d J l J Br wn e
LT3960 I2C至CAN物理收发器评估电路EVAL-LT3960-AZ 说明书

1Rev. 0DESCRIPTIONLT3960I 2C to CAN-PhysicalTransceiverEvaluation circuit EVAL-LT3960-AZ features the L T ®3960, an I 2C to CAN-Physical transceiver in a 10-lead plastic MSOP package. EVAL-LT3960-AZ consists of two ICs configured in the master and slave mode using selectable jumpers, JP1 and JP3. The board is designed to be easily snapped apart at the center , separating two circuitries.The LT3960 I 2C to CAN-Physical transceiver is used to send and receive I 2C data through harsh or noisy envi-ronments at up to 400kb/s using the CAN-Physical layer for differential signaling over twisted pair connections. The SDA and SCL data lines are converted to differential signals and are shared between devices connected to the bus. This allows for the physical separation of the I 2C source and I 2C receiver .All registered trademarks and trademarks are the property of their respective owners.PERFORMANCE SUMMARYThe first LT3960 is connected to the I 2C master (I 2C-compatible microcontroller). The second LT3960 should be connected to the first LT3960 by two twisted pairs. It regenerates the I 2C bus locally for one or more I 2C slave devices. The LT3960 devices transmit the clock signal in only one direction, from master to slave. Bidirectional communication of the data signal is always permitted.The LT3960 data sheet gives a complete description of the parts, their operation, and application information. The data sheet must be read in conjunction with this user guide for the evaluation circuit EVAL-LT3960-AZ. The LT3960EMSE is assembled in a 10-lead MSOP package.Design files for this circuit board are available .Specifications are at T A = 25°CSYMBOL PARAMETER CONDITIONMIN TYP MAX UNIT V IN Input VoltageV IN Tied to V CC , 3.3V Range (Jumper JP2, JP4: V IN = V CC ) V IN Tied to V CC , 5V Range (Jumper JP2, JP4: V IN = V CC ) V CC Regulated Internally from V IN (Jumper JP2, JP4: V IN ≠ V CC )3 4.5 4 3.3 53.6 5.5 60V V V V MSTR , V SLV , V SHDN EN/MODE VoltageMaster Mode (Jumper JP1, JP3: MASTER) Slave Mode(Jumper JP1, JP3: SLAVE) Low Power Shutdown Mode(Jumper JP1, JP3: OFF)2 0.7 05 2 0.7V V V f CLK Clock Frequency400kHz V CMBus Common Mode Voltage V CC = 3.3VV CC = 5V±25 ±36V VQUICK START PROCEDUREEVAL-LT3960-AZ can be powered by a voltage source between 4V and 60V due to the integrated LDO in the LT3960. The LDO regulates the input from the V IN pin between 4V and 60V to 3.3V on the V CC pin from which the transceivers and bus lines are powered. Alternatively, the EVAL-LT3960-AZ can be powered from a supply volt-age of 3.3V or 5V on VIN, bypassing the LDO by shorting VCC to VIN using jumpers JP2 and JP4.One procedure for using the EVAL-LT3960-AZ is described as follows:1. Launch Arduino IDE.2. Connect two Linduinos to the computer via USB.3. Download the Linduino code from the EVAL-LT3960-AZ webpage.4. Upload the code to the master and slave Linduinosaccordingly.5. Break the EVAL-LT3960-AZ into two separate boardsby applying force to the horizontal scoring line. 6. Use 2 twisted pairs of small wires to connect CANSCLx1and CANSCLx2; CANSDAx1 and CANS-DAx2.7. Connect GND1 and GND2 pins on two boards using asmall wire (optional).8. Connect SLC, SDA, GND pins from the master (slave)Linduino to SLC1, SDA1, GND1 (SLC2, SDA2, GND2) of the EVAL-LT3960-AZ, respectively.9. With input power off, connect the first (second) inputpower supply to VIN1 and GND1 (VIN2 and GND2) of the EVAL-LT3960-AZ.10. Turn on input power supplies.11. Open the serial monitor associated with the slaveLinduino and check the received message.2Rev. 0QUICK START PROCEDUREFigure 1. Quick Start Procedure Setup Drawing for EVAL-LT3960-AZ3Rev. 04Rev. 0PARTS LISTTEST RESULTSFigure 2. Linduino COM Terminal Window of the Slave DeviceITEM QTY REFERENCE PART DESCRIPTIONMANUFACTURER/PART NUMBER Required Circuit Components12C1, C5CAP ., 1µF, X7R, 50V, 10%, 0603YAGEO, CC0603KRX7R9BB10524C2, C4, C7, C8CAP ., 4700pF, X7R, 50V, 10%, 0402MURATA, GRM155R71H472KA01D 32C3, C6CAP ., 2.2µF, X7S, 10V, 10%, 0603, AEC-Q200TDK, CGA3E3X7S1A225K080AB 42R1, R8RES., 10k, 1%, 1/10W, 0603, AEC-Q200VISHAY, CRCW060310K0FKEA 58R2, R4, R6, R7, R9, R12, R13, R14RES., 60.4Ω, 1%, 1/8W, 0805, AEC-Q200PANASONIC, ERJ6ENF60R4V 64R3, R5, R10, R11RES., 4.99k, 1%, 1/10W, 0603, AEC-Q200PANASONIC, ERJ3EKF4991V 72U1, U2IC, 12C TO DUAL CAN TRANSCEIVER, MSOP-10ANALOG DEVICES, LT3960EMSE#PBF Hardware: For Demo Board Only18E1-E8TEST POINT , TURRET , 0.064" MTG. HOLE, PCB 0.062" THK MILL-MAX, 2308-2-00-80-00-00-07-022J1, J3CONN., TERM BLOCK, 5 POS, 2.54mm, ST , THT , SIDE ENTRY, GREEN ON-SHORE TECHNOLOGY, OSTVN05A15032J2, J4CONN., HDR, MALE, 1x2, 2.54mm, VERT , ST , THT WURTH ELEKTRONIK, 6130021112142JP1, JP3CONN., HDR, MALE, 2x3, 2mm, VERT , ST , THT WURTH ELEKTRONIK, 6200062112152JP2, JP4CONN., HDR, MALE, 1x3, 2mm, VERT , ST , THTWURTH ELEKTRONIK, 62000311121618TP1-TP18TEST POINT , 1POS, 0.040" MTG. HOLE, 2.54mm DIA x 4.57mm L, THT , BLACKKEYSTONE, 500174XJP1, XJP2, XJP3, XJP4CONN., SHUNT , FEMALE, 2 POS, 2mmWURTH ELEKTRONIK, 608002134215Rev. 0Information furnished by Analog Devices is believed to be accurate and reliable. However , no responsibility is assumed by Analog Devices for its use, nor for any infringements of patents or other rights of third parties that may result from its use. Specifications subject to change without notice. No license is granted by implication or otherwise under any patent or patent rights of Analog Devices.SCHEMATIC DIAGRAMc o m6Rev. 0ANALOG DEVICES, INC. 202103/21ESD CautionESD (electrostatic discharge) sensitive device. Charged devices and circuit boards can discharge without detection. Although this product features patented or proprietary protection circuitry, damage may occur on devices subjected to high energy ESD. Therefore, proper ESD precautions should be taken to avoid performance degradation or loss of functionality.Legal Terms and ConditionsBy using the evaluation board discussed herein (together with any tools, components documentation or support materials, the “Evaluation Board”), you are agreeing to be bound by the terms and conditions set forth below (“Agreement”) unless you have purchased the Evaluation Board, in which case the Analog Devices Standard Terms and Conditions of Sale shall govern. Do not use the Evaluation Board until you have read and agreed to the Agreement. Your use of the Evaluation Board shall signify your acceptance of the Agreement. This Agreement is made by and between you (“Customer”) and Analog Devices, Inc. (“ADI”), with its principal place of business at One Technology Way, Norwood, MA 02062, USA. Subject to the terms and conditions of the Agreement, ADI hereby grants to Customer a free, limited, personal, temporary, non-exclusive, non-sublicensable, non-transferable license to use the Evaluation Board FOR EVALUATION PURPOSES ONL Y. Customer understands and agrees that the Evaluation Board is provided for the sole and exclusive purpose referenced above, and agrees not to use the Evaluation Board for any other purpose. Furthermore, the license granted is expressly made subject to the following additional limitations: Customer shall not (i) rent, lease, display, sell, transfer , assign, sublicense, or distribute the Evaluation Board; and (ii) permit any Third Party to access the Evaluation Board. As used herein, the term “Third Party” includes any entity other than ADI, Customer , their employees, affiliates and in-house consultants. The Evaluation Board is NOT sold to Customer; all rights not expressly granted herein, including ownership of the Evaluation Board, are reserved by ADI. CONFIDENTIALITY. This Agreement and the Evaluation Board shall all be considered the confidential and proprietary information of ADI. Customer may not disclose or transfer any portion of the Evaluation Board to any other party for any reason. Upon discontinuation of use of the Evaluation Board or termination of this Agreement, Customer agrees to promptly return the Evaluation Board to ADI. ADDITIONAL RESTRICTIONS. Customer may not disassemble, decompile or reverse engineer chips on the Evaluation Board. Customer shall inform ADI of any occurred damages or any modifications or alterations it makes to the Evaluation Board, including but not limited to soldering or any other activity that affects the material content of the Evaluation Board. Modifications to the Evaluation Board must comply with applicable law, including but not limited to the RoHS Directive. TERMINATION. ADI may terminate this Agreement at any time upon giving written notice to Customer . Customer agrees to return to ADI the Evaluation Board at that time. LIMITATION OF LIABILITY. THE EVALUATION BOARD PROVIDED HEREUNDER IS PROVIDED “AS IS” AND ADI MAKES NO WARRANTIES OR REPRESENTATIONS OF ANY KIND WITH RESPECT TO IT . ADI SPECIFICALL Y DISCLAIMS ANY REPRESENTATIONS, ENDORSEMENTS, GUARANTEES, OR WARRANTIES, EXPRESS OR IMPLIED, RELATED TO THE EVALUATION BOARD INCLUDING, BUT NOT LIMITED TO, THE IMPLIED WARRANTY OF MERCHANTABILITY, TITLE, FITNESS FOR A PARTICULAR PURPOSE OR NONINFRINGEMENT OF INTELLECTUAL PROPERTY RIGHTS. IN NO EVENT WILL ADI AND ITS LICENSORS BE LIABLE FOR ANY INCIDENTAL, SPECIAL, INDIRECT , OR CONSEQUENTIAL DAMAGES RESUL TING FROM CUSTOMER’S POSSESSION OR USE OF THE EVALUATION BOARD, INCLUDING BUT NOT LIMITED TO LOST PROFITS, DELAY COSTS, LABOR COSTS OR LOSS OF GOODWILL. ADI’S TOTAL LIABILITY FROM ANY AND ALL CAUSES SHALL BE LIMITED TO THE AMOUNT OF ONE HUNDRED US DOLLARS ($100.00). EXPORT . Customer agrees that it will not directly or indirectly export the Evaluation Board to another country, and that it will comply with all applicable United States federal laws and regulations relating to exports. GOVERNING LAW . This Agreement shall be governed by and construed in accordance with the substantive laws of the Commonwealth of Massachusetts (excluding conflict of law rules). Any legal action regarding this Agreement will be heard in the state or federal courts having jurisdiction in Suffolk County, Massachusetts, and Customer hereby submits to the personal jurisdiction and venue of such courts. The United Nations Convention on Contracts for the International Sale of Goods shall not apply to this Agreement and is expressly disclaimed.。
NVIDIA BOOTH Sl3905 商品展示说明书
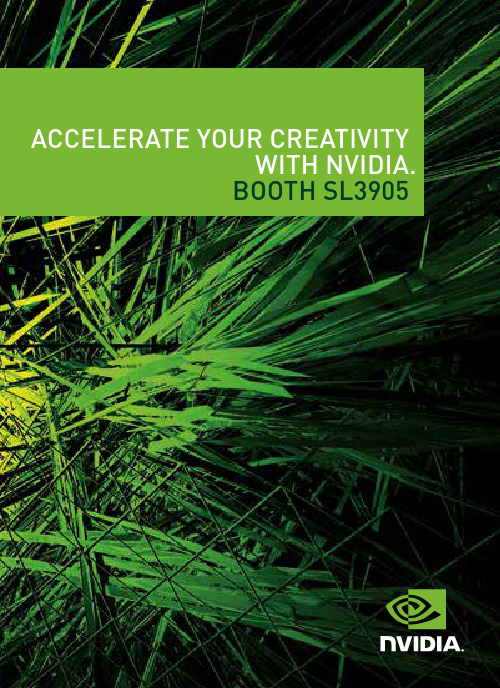
AccElERATE YOuR cREATiviTYWiTH NviDiA.BOOTH Sl3905nVidiA At nAb 2013get faster Animation, simulation, and Rendering.featuring: NVIDIA® Maximus™ technology, including the latest generation of NVIDIA Quadro® GPUs with the powerful newNVIDIA Kepler™ architecture, running:> MAXON CINEMA 4D, Jawset TurbulenceFD, and Dell T7600showcasing particle simulation for 3D animation> OTOY Octane Render and HP Z820 showcasing interactive,globally illuminated renderingfor: Animators and 3D and visual-effect artists to create,simulate, and render simultaneously without interrupting their creative workflowAccelerate Color grading.featuring: DaVinci Resolve running on Mac Pro, powered byNVIDIA Quadro K5000 for Macfor: Colorists, video producers, and digital filmmakers whowant to do state-of-the-art color grading on a MacCreate Video productions with Even greater speed.featuring: Adobe® Premiere® Pro Next with an improved GPU-accelerated Mercury Playback Engine, powered by an NVIDIA Kepler-class of Quadro for mobile workstations.for: Video editors, digital filmmakers and broadcasters whoneed real-time performance to enable creative workflows and fast production turnaroundget Quadro performance on windows, mac, orlinux desktops.featuring: the NVIDIA GRID™ Visual Computing Appliance(VCA). Brand new for NAB 2013, the NVIDIA GRID VCA enablesworkgroups to get the full benefits of top-of-the-line NVIDIAGPU acceleration on their Windows, Mac, or Linux systems. The GRID VCA combines the benefits of remoting, virtualization, and Quadro reliability and performance in a turnkey package. At the booth, NVIDIA will feature a technology demonstration of theGRID VCA running:> Adobe® After Effects®Next and Adobe® Photoshop® CS6 on aLinux system, enabling unprecedented creative power andinteractivity when combined with the power of NVIDIA GPUs.> Autodesk 3ds Max 2014 with full GPU acceleration on aMacBook Pro for 3D modeling, animation, visual effects, andrendering to meet the technology demands of today’smodern pipelines> Autodesk Maya 2014, 3D animation software that offers next-generation display technology, accelerated modelingworkflows, robust systems for handling complex data, andinspiring creative toolsetsfor: Broadcasters, post houses, ad agencies, filmmakers,visual-effects artists, motion-graphic artists, and any media-content creator who wants to deliver GPU-accelerated creative and design applications on demandprovide next-generation Content Experiences.featuring: NVIDIA SHIELD,™ a gaming portable designed forgamers who yearn to play when, where, and how they want. With the advanced processing power of NVIDIA Tegra® 4, a full-sizegame controller, breakthrough Wi-Fi technology, and stunning HD video and audio, SHIELD redefines what gaming can be.for: Content creators and content distributors who areinterested in next-generation platforms for gaming and movieson-AiR gRApHiCsPARTNER BOOTH # AccuWeather SL6816 Broadcast Pix SL6324 ChyronHego SL1010 Compix Media SL5705 Harris Broadcast N2503 Miranda Technologies N2531 NewTek SL4610 Orad Hi-Tec Systems SL5709 Pixel Power N2034 Ross Video N3808 Vizrt SL3305 WASP3D SL6328 WSI/Weather Central SL1710 Editing, Compositing, AnimAtion, REndERing, EffECts, And ColoR mAnAgEmEntPARTNER BOOTH # Adobe Systems SL3910 ASSIMILATE SL12705 Autodesk SL3316 Avid SU902 Binocle C12049 Blackmagic Design SL218 Boris FX SL4327 Brainstorm Multimedia SL10621 Cinnafilm SL9605 (HP) Digital Vision SL14518 EditShare SL9010Editing, Compositing, AnimAtion, REndERing,EffECts, And ColoR mAnAgEmEnt (ContinuEd)PARTNER BOOTH #FilmLight SL3928 GenArts SL4224Grass Valley SL206Lightcraft Technology SL12516Marquise Technologies SL12508Maxon Computer Inc. SL5316MTI Film SL15510NewTek SL4610Quantel SL2109Red Giant SL3728SGO SL10321Sony (Vegas™ Pro) C11001The Foundry SL3324EnCoding, tRAnsCoding, And VidEopRoCEssingPARTNER BOOTH #AmberFin SU8505 Cinegy SL11112Digimetrics N3833Elemental Technologies SU2724Interra Systems SL8006Root6 Technology SL7428Sorenson Media SU6806Telestream SL2605For more information on NVIDIA and its partners, visit /quadro.© 2013 NVIDIA Corporation. All rights reserved. All company and product names are trademarks or registered trademarks of the respective owners with which theyare associated. VidEo i/oPARTNER BOOTH #AJA Video SL3816BlackMagic Design SL218Bluefish444 SL9721Deltacast SL11516DVS, a Rohde & Schwarz company SL6316Matrox Electronic Systems SL4616systEm pRoVidER And HARdwARE pARtnERs PARTNERBOOTH #ARRIC4337Canon USAC4325Hewlett-PackardSL9605RED Digital CinemaSL1516Sony ElectronicsC11001Supermicro SL14510。
Microchip电子产品说明书

TREE 3: POWER MANAGEMENT 2Supervisors & Voltage Detectors Unique Strengths (So What)Broad Portfolio(It's likely we have your part)Small Packages: SOT-23 and SC-70 (Saves space)Industrial Standard Crosses (Replace high priced and poor delivery suppliers)Battery Management Unique Strengths (So What)Wide variety of charging solutions for Li-Ion batteries(We have the solution for you)Small SOT-23, MSOP, DFN and QFN packages (Saves space)DC-DC Converter (So What)Low-voltage operation (Saves Power)PFM/PWM Auto switch mode (PFM at low loads reduces current, saves power)Small SOT-23 packaging (Saves space)Step-down, Step-up (Efficiently increase or decrease voltage) Charge Pumps (So What)Low-voltage operation (Battery operation)Small SOT-23 packaging (Saves space)Step-down, Step-up (Efficiently increase or decrease voltage)Doubling & Inverting (Meets V OUT needs) Low-Frequency capable (Reduces EMI)Low-Current Operation (Saves power)LDO Unique Strengths (So What)Hundreds of voltages, currents, packages (We have a match for the need)0.5% V OUT accuracy (Fills precision need)Up to 1.5A output current(Able to power high load applications)Op Amp Unique Strengths (So What)Low current versus GBWP (Saves power)TC and MCP6XXX devices RR-I/O (Expands usable voltage range)MCP604X 1.4V operation(Two alkaline cells 90% used =1.8V)MCP644X, 450 nA operation (Use the batteries even longer)Comparators Unique Strengths (So What)Low current versus propagation delay (Saves power)Integrated Features (Saves space)1.8V and 1.4V operation (That stuff about the batteries)Programmable Gain Amplifier Unique Strengths (So What)MUX inputWide bandwidth (2 to 12 MHz) (Reduces demand on MCU I/O)System control of gain(Changes easier through software configurable hardware)TREE 5: LINEARTemperature Sensor Unique Strengths (So What)Wide variety of solutions: logic, voltage and digital output products(Multiple sensor needs met)Small packages (Saves space)Low operating current(Saves power, smaller supply)Field or factory programmable (Low cost vs. flexibility)Programmable hysteresis (Stop system cycling)Multi-drop capability (Great for large systems)Beta compensation (Compatible with processor substrate diodes)Resistance error correction (Compensates for measurement error from long PCB traces)Fan Controllers Unique Strengths (So What)Closed loop fan control (Adjust to meet target speed even on aging fans)Integrated temperature sensing (Consolidate thermal management)Multiple temperature measurements drive one fan (Consolidate thermal management)Built-in ramp rate control and spin up alogorithm (Quick time to market, lower acoustic noise)Ability to detect/predict failure of less expensive 2-wire fans (Saves system cost)Unique solutions for extending fan life and reducing acoustic noise(Less power, nuisance and long fan life)TREE 6: MIXED-SIGNALADC Unique Strengths (So What)Low current at max sampling rate (Saves power, system cost)Small SOT-23 and MSOP packages (Saves space)Up to 24-bit resolution(Ideal for precision sensitive designs)Differential & single ended inputs (Able to cover various design needs)Up to 6 ADC per device(Save board space, system cost)DAC Unique Strengths (So What)Low Supply Current (Saves power)Low DNL & INL (Better accuracy)Extended Temperature Range(Suitable for wide temperature applications)Digital Potentiometers Unique Strengths (So What)64/256 tap (6-bit to 8-bit resolution)(Sufficient resolution for most applications)Non-volatile Memory(Remembers last wiper setting on power up)WiperLock™ Technology(Locks NV memory setting-better than OTP)Small SOT-23 and 2 × 3 DFN packages (Saves space)Low CostMOSFET Drivers (So What)4.5V up to 30V Supply voltages (Fills many application needs)Up to 12A Peak output current(Able to meet demanding design needs)Outstanding robustness and latch-upi mmunity (Ours work when the others burn up)Low-FOM MOSFETs(Support high-efficency applications)TREE 4: POWER MANAGEMENT 3LIN Unique Strengths(So What)Compliant with LIN Bus Specs 1.3, 2.0, 2.1 andSAE J2602 (Allows for reliable interoperability)High EMI Low EME (Meets OEM requirements)On-board V REG available(Saves space, allows for MCU V CC flexibility)CAN Unique Strengths(So What)Simple SPI CAN controller is an easy way toadd CAN Ports (Short design cycles)High speed transceiver meets ISO-11898 (Drop inreplacement for industry standard transceivers)Low-cost, easy-to-use development tools(Tools easy to buy/use, quick design)I/O Expanders Unique Strengths(So What)Configurable inputs (interrupt configuration flexibility)Interrupt on pin change, or change fromregister default (interrupt source flexibility)Can disable automatic address incrementingwhen accessing the device(allows continual access to the port)The 16-bit devices can operate in 8-bit or 16-bitmode (easy to interface to 8-bit or 16-bit MCUs)IrDA Unique Strengths (So What)IrDA protocol handler embedded on chip(Complex design issue solved)Low cost developer's kit available to assistInfrared design-in (Quick design cycle)Small, cost-effective way of replacing serial links(No more wires)Enables system to wirelessly communicatewith PDA (Wireless connectivity solution) TREE 8: INTERFACEAnalog & InterfaceQuestion TreesAnalog & Interface Development ToolsDemonstration Boards, Evaluation Kits and AccessoriesAnalog & Interface LiteratureADM00313EV: MCP73830L 2 × 2 TDFN Evaluation BoardADM00352: MCP16301 High Voltage Buck Converter 600 mA Demonstration BoardADM00360: MCP16301 High Voltage Buck Coverter 300 mA D2PAK Demonstration BoardADM00427: MCP16323 Evaluation Board (Supports MCP16321 and MCP16322)ARD00386: MCP1640 12V/50 mA Two Cells Input Boost Converter Reference DesignMCP1252DM-BKLT: MCP1252 Charge Pump Backlight Demonstration BoardMCP1256/7/8/9EV: MCP1256/7/8/9 Charge Pump Evaluation BoardMCP1630RD-LIC1: MCP1630 Li-Ion Multi-Bay Battery Charger Reference DesignMCP1630DM-NMC1: MCP1630 NiMH Battery Charger Demonstration BoardMCP1640EV-SBC: MCP1640 Sync Boost Converter Evaluation BoardMCP1640RD-4ABC: MCP1640 Single Quad-A Battery Boost Converter Reference DesignMCP1650DM-LED1: MCP165X 3W White LED Demonstration BoardMCP1726EV: MCP1726 LDO Evaluation BoardMCP73831EV: MCP73831 Evaluation KitMCP7383XEV: MCP73837/8 AC/USB Dual Input Battery Charger Evaluation BoardMCP7383XRD-PPM: MCP7383X Li-Ion System Power Path Management Reference DesignMCP7384XEV: MCP7384X Li-Ion Battery Chager Evaluation BoardMCP73871EV: MCP73871 Load Sharing Li-Ion Battery Charger Evaluation BoardTC1016/17EV: TC1016/17 LDO Evaluation BoardVSUPEV: SOT-23-3 Voltage Supervisor Evaluation BoardPowerManagementThermalManagementMCP9700DM-PCTL: MCP9700 Thermal Sensor PICtail Demonstration BoardMCP9800DM-PCTL: MCP9800 Thermal Sensor PICtail Demonstration BoardTC72DM-PICTL: TC72 Digital Temperature Sensor PICtail Demonstration BoardTC74DEMO: TC74 Serial Daughter Thermal Sensor Demonstration BoardTC1047ADM-PCTL: TC1047A Temperature-to-Voltage Converter PICtail™ Demonstration BoardSerial GPIODM-KPLCD: GPIO Expander Keypad and LCD Demonstration BoardMCP23X17: MCP23X17 16-bit GPIO Expander Evaluation BoardInterface MCP2515DM-BM: MCP2515 CAN Bus Monitor Demonstration BoardMCP2515DM-PTPLS: MCP2515 PICtail™ Plus Daughter BoardMCP2515DM-PCTL: MCP2515 CAN Controller PICtail Demonstration BoardMCP215XDM: MCP215X/40 Data Logger Demonstration BoardMCP2140DM-TMPSNS: MCP2140 IrDA® Wireless Temp Demonstration BoardLinear ADM00375: MCP6H04 Evaluation BoardARD00354: MCP6N11 Wheatstone Bridge Reference DesignMCP651EV-VOS: MCP651 Input Offset Evaluation BoardMCP661DM-LD: MCP661 Line Driver Demo BoardMCP6S22DM-PCTL: MCP6S22 PGA PICtail Demonstration BoardMCP6S2XEV: MCP6S2X PGA Evaluation BoardMCP6SX2DM-PCTLPD: MCP6SX2 PGA Photodiode PICtail Demonstration BoardMCP6SX2DM-PCTLTH: MCP6SX2-PGA Thermistor PICtail Demonstration BoardMCP6V01RD-TCPL: MCP6V01 Thermocouple Auto-Zero Ref DesignMCP6XXXDM-FLTR: Active Filter Demo BoardPIC16F690DM-PCTLHS: Humidity Sensor PICtail Demonstration BoardMixed-Signal MCP3221 DM-PCTL: MCP3221 12-bit A/D PICtail Demonstration BoardMCP3421DM-BFG: MCP3421 Battery Fuel Gauge Demonstration BoardMCP3551DM-PCTL: MCP3551 PICtail Demonstration BoardMCP355XDM-TAS: MCP355X Tiny Application Sensor Demonstration BoardMCP355XDV-MS1: MCP3551 Sensor Demonstration BoardMCP402XEV: MCP402X Digital Potentiometer Evaluation BoardMCP4725EV: MCP4725, 12-bit Non-Volatile DAC Evaluation Board (Preferred One)MCP4725DM-PTPLS: MCP4725, 12-bit Non-Volatile DAC PICtail Demonstration BoardADM00398: MCP3911 ADC Evaluation Board for 16-bit MicrocontrollersCorporate Microchip Product Line Card - DS00890Brochures Analog and Interface Product Selector Guide - DS21060Low Cost Development Tools Solutions Guide - DS51560Analog and Interface Guide (Volume 1) - DS00924Analog and Interface Guide (Volume 2) - DS21975Cards Analog Highlights Card - DS21972Microchip Op Amp Discovery Card - DS21947Analog & Interface Question Trees - DS21728Mirochip SAR and Delta-Sigma ACD Discovery Card - DS22101Software Tools MAPS - Microchip Advanced Product SelectorAnalog & Interface Treelink Products PresentationDesign Guides Analog-to-Digital Converter Design Guide - DS21841Digital Potentiometers Design Guide - DS22017Programmable Gain Amplifiers (PGAs), Operational Amplifiersand Comparators Design Guide - DS21861Interface Products Design Guide - DS21883Signal Chain Design Guide - DS21825Power Solutions Design Guide - DS21913Temperature Sensor Design Guide - DS21895Voltage Supervisors Design Guide - DS51548DS21728JPowerManagementLDO & SwitchingRegulatorsCharge PumpDC/DC ConvertersPower MOSFETDriversPWM ControllersSystem SupervisorsVoltage DetectorsVoltage ReferencesLi-Ion/Li-PolymerBattery ChargersUSB Port PowerControllersMixed-SignalA/D ConverterFamiliesDigitalPotentiometersD/A ConvertersV/F and F/VConvertersEnergyMeasurement ICsCurrent/DC PowerMeasurement ICsInterfaceCAN PeripheralsInfraredPeripheralsLIN TransceiversSerial PeripheralsEthernet ControllersUSB PeripheralLinearOp AmpsInstrumentationAmpsProgrammableGain AmplifiersComparatorsSafety & SecurityPhotoelectricSmoke DetectorsIonization SmokeDetectorsIonization SmokeDetector Front EndsPiezoelectricHorn DriversThermalManagementTemperatureSensorsFan Control& HarwareManagementMotor DriveStepper and DC3Ф BrushlessDC Motor DriverTREE 7: MOTOR DRIVE Stepper Unique Strenghts(So What)Industrial standard footprint(Footprint compatible to industrial leaders)Perfect PIC® MCU companion chip(Solid field support)Micro-stepping ready(Enhanced performance)Integration protections(Simplify software development)3-Phase BLDC Unique Strengths(So What)Full-wave sinusoidal(Quiet operation, low mechanical vibration)Sensorless operation (Minimum externalcomponents, no software required)Thin form factor(Fits space concerned applications)Information subject to change. The Microchip name and logo, the Microchip logo, dsPIC, PIC are registered trademarks and MiWi, PICtail and ZENA are trademarks ofMicrochip Technology Incorporated in the U.S.A. and other countries. All other trademarks mentioned herein are property of their respective companies.© 2012, Microchip Technology Incorporated. All Rights Reserved.。
KSZ9021RN to KSZ9031RNX Migration Guide
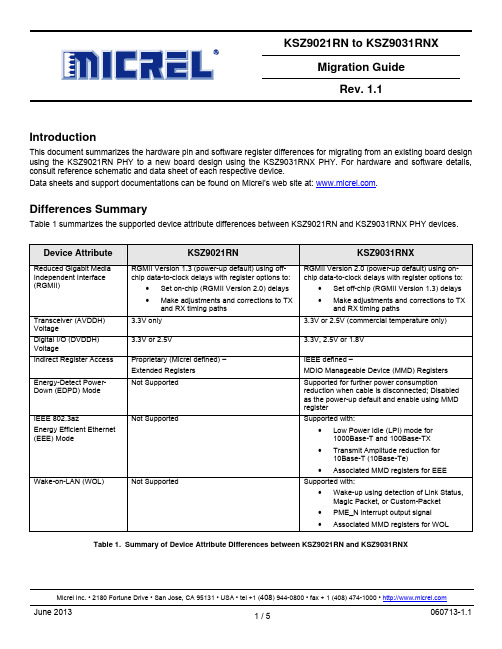
KSZ9021RN to KSZ9031RNXMigration GuideRev. 1.1IntroductionThis document summarizes the hardware pin and software register differences for migrating from an existing board design using the KSZ9021RN PHY to a new board design using the KSZ9031RNX PHY. For hardware and software details, consult reference schematic and data sheet of each respective device.Data sheets and support documentations can be found on Micrel’s web site at: .Differences SummaryTable 1 summarizes the supported device attribute differences between KSZ9021RN and KSZ9031RNX PHY devices.Device Attribute KSZ9021RN KSZ9031RNXReduced Gigabit Media Independent Interface (RGMII) RGMII Version 1.3 (power-up default) using off-chip data-to-clock delays with register options to:•Set on-chip (RGMII Version 2.0) delays•Make adjustments and corrections to TXand RX timing pathsRGMII Version 2.0 (power-up default) using on-chip data-to-clock delays with register options to:•Set off-chip (RGMII Version 1.3) delays•Make adjustments and corrections to TXand RX timing pathsTransceiver (AVDDH)Voltage3.3V only 3.3V or 2.5V (commercial temperature only)Digital I/O (DVDDH)Voltage3.3V or 2.5V 3.3V, 2.5V or 1.8VIndirect Register Access Proprietary (Micrel defined) –Extended Registers IEEE defined –MDIO Manageable Device (MMD) RegistersEnergy-Detect Power-Down (EDPD) Mode Not Supported Supported for further power consumptionreduction when cable is disconnected; Disabledas the power-up default and enable using MMDregisterIEEE 802.3azEnergy Efficient Ethernet (EEE) Mode Not Supported Supported with:•Low Power Idle (LPI) mode for1000Base-T and 100Base-TX•Transmit Amplitude reduction for10Base-T (10Base-Te)•Associated MMD registers for EEEWake-on-LAN (WOL) Not Supported Supported with:•Wake-up using detection of Link Status,Magic Packet, or Custom-Packet•PME_N interrupt output signal•Associated MMD registers for WOL Table 1. Summary of Device Attribute Differences between KSZ9021RN and KSZ9031RNXPin DifferencesTable 2 summarizes the pin differences between KSZ9021RN and KSZ9031RNX PHY devices. Pin #KSZ9021RNKSZ9031RNXPin NameType Pin FunctionPin NameTypePin Function1 AVDDH P 3.3V analog V DD AVDDH P 3.3V/2.5V (commercial temp only) analog V DD 12 AVDDH P 3.3V analog V DD AVDDH P 3.3V/2.5V (commercial temp only) analog V DD 13VSS_PSGndDigital groundNC–No connectThis pin is not bonded and can be connected to digital ground for footprint compatibility with the Micrel KSZ9021RN Gigabit PHY.16 DVDDH P3.3V / 2.5V digital V DD DVDDH P 3.3V, 2.5V, or 1.8V digital V DD_I/O 17 LED1 /PHYAD0I/OLED Output:Programmable LED1 OutputConfig Mode:The pull-up/pull-down value is latched as PHYAD[0] during power-up / reset.LED1 /PHYAD0 /PME_N1I/O LED1 output:Programmable LED1 outputConfig mode:The voltage on this pin issampled and latched during the power-up/reset process to determine the value of PHYAD[0].PME_N output:Programmable PME_N output (pin option 1). This pin function requires an external pull-up resistor to DVDDH (digital V DD_I/O ) in a range from 1.0k Ω to 4.7k Ω. When asserted low, this pin signals that a WOL event has occurred.When WOL is not enabled, this pin function behaves as per the KSZ9021RN pin definition.This pin is not an open-drain for all operating modes.34 DVDDH P3.3V / 2.5V digital V DD DVDDH P 3.3V, 2.5V, or 1.8V digital V DD_I/O38 INT_N O Interrupt OutputThis pin provides aprogrammable interrupt output and requires an external pull-up resistor to DVDDH in the range of 1K to 4.7K ohms for active low assertion.INT_N/O Interrupt OutputThis pin provides aprogrammable interrupt output and requires an external pull-up resistor to DVDDH in the range of 1K to 4.7K ohms for active low assertion.This pin is an open-drain.PME_N2 PME_N output: Programmable PME_N output (pin option 2). When asserted low, this pin signals that a WOL event has occurred.When WOL is not enabled, this pin function behaves as per the KSZ9021RN pin definition. This pin is not an open-drain for all operating modes.40 DVDDH P 3.3V / 2.5V digital V DD DVDDHP3.3V, 2.5V, or 1.8V digitalV DD_I/O47 AVDDH P 3.3V analog V DD NC–NoconnectThis pin is not bonded and canbe connected to AVDDH powerfor footprint compatibility withthe Micrel KSZ9021RN GigabitPHY.48 ISET I/O Set transmit output levelConnect a 4.99KΩ 1%resistor to ground on thispin. ISET I/O Set the transmit output levelConnect a 12.1kΩ 1% resistorto ground on this pin.Table 2. Pin Differences between KSZ9021RN and KSZ9031RNXStrapping Option DifferencesThere is no strapping pin difference between KSZ9021RN and KSZ9031RNX.Register Map DifferencesThe register space within the KSZ9021RN and KSZ9031RNX consists of direct-access registers and indirect-access registers.Direct-access RegistersThe direct-access registers comprise of IEEE-Defined Registers (0h – Fh) and Vendor-Specific Registers (10h – 1Fh). Between the KSZ9021RN and KSZ9031RNX, the direct-access registers and their bits have the same definitions, except for the following registers in Table 3.Direct-access RegisterKSZ9021RN KSZ9031RNXName Description Name Description3h PHYIdentifier2 Bits [15:10] (part of OUI) – same asKSZ9031RNXBits [9:4] (model number) – unique forKSZ9021RNBits [3:0] (revision number) – uniquedepending on chip revision PHY Identifier 2 Bits [15:10] (part of OUI) – same asKSZ9021RNBits [9:4] (model number) – unique forKSZ9031RNXBits [3:0] (revision number) – uniquedepending on chip revisionBh ExtendedRegister –Control Indirect Register AccessSelect read/write control andpage/address of Extended RegisterReserved ReservedDo not change the default value ofthis registerCh ExtendedRegister –Data Write Indirect Register AccessValue to write to Extended RegisterAddressReserved ReservedDo not change the default value ofthis registerDh ExtendedRegister –Data Read Indirect Register AccessValue read from Extended RegisterAddressMMD Access –ControlIndirect Register AccessSelect read/write control and MMDdevice addressEh Reserved ReservedDo not change the default value ofthis register MMD Access –Register/DataIndirect Register AccessValue of register address/data for theselected MMD device address1Fh, bit [1] Software Reset 1 = Reset chip, except all registers0 = Disable resetReserved ReservedTable 3. Direct-access Register Differences between KSZ9021RN and KSZ9031RNXIndirect-access RegistersThe indirect register mapping and read/write access are completely different for the KSZ9021RN (uses Extended Registers) and KSZ9031RNX (uses MMD Registers). Refer to respective devices’ data sheets for details.Indirect registers provide access to the following commonly used functions:•1000Base-T link-up time control (KSZ9031RNX only)• Pin strapping status• Pin strapping override•Skew adjustments for RGMII clocks, control signals, and datao Resolution of skew steps are different between KSZ9021RN and KSZ9031RNX•Energy-Detect Power-Down Mode enable/disable (KSZ9031RNX only)•Energy Efficient Ethernet function (KSZ9031RNX only)•Wake-on-LAN function (KSZ9031RNX only)Revision HistoryRevision Date Summary of ChangesMigration Guide created1.0 12/7/121.1 6/7/13 Indicate PME_N1 (pin 17) for KSZ9031RNX is not an open-drain.Indicate INT_N (pin 38) is an open-drain for KSZ9021RN, but is not an open-drain for KSZ9031RNX.Indicate direct-access register 1Fh, bit [1] difference.。
XRA1403 1405评估板用户手册说明书

REV. 1.0.0 XRA1403/1405 EVALUATION BOARD USER’S MANUAL INTRODUCTIONThis user’s manual is for the XRA1403/1405 16-bit evaluation board. Table 1 shows the different devices and packages that the evaluation board supports. This user’s manual will describe the hardware setup required to operate the different packages.1.0QUICK STARTTo verify communication with the GPIO expander, the following steps are recommended:1.1Connect external +5V power supply to J8 pin 11.2Connect J12 pin 13 and 14 to ground of external power supply1.3Connect to MCU SPI interface for:SPI clock (SCK_SCL signal at J5 pin11)SO (SO_SPI signal at J5 pin17)SI (SI_SPI signal at J5 pin21)CS# (CS#_SPI signal at J5 pin19)1.4From the MCU, write the following registers:GCR1 = 0x00GCR2 = 0x00If the LEDs turn on, the communication with the GPIO expander is successful.To disable connection to LEDs, remove jumpers on J28, J29, J30 and J31. Connect to external inputs or outputs at J3 and J4.2.0HARDWARE SETUP2.1Packages descriptionThe evaluation board supports all 4 packages of the XRA1403 and XRA1405. The ordering part number, package and location on the board is shown below in Table 1. Table 2 lists the evaluation board ordering part numbers.T ABLE 1: P ACKAGE L ISTO RDERING P ART N UMBER P ACKAGE L OCATION XRA1403IL24-F 24-pin QFN U4XRA1403IG24-F 24-pin TSSOP U5XRA1405IL24-F 24-pin QFN U4XRA1405IG24-F 24-pin TSSOP U5T ABLE 2: E VALUATION B OARD O RDERING P ART N UMBERSP ART N UMBERXRA1403IL24-0B-EBXRA1403IG24-0B-EBXRA1405IL24-0B-EBXRA1405IG24-0B-EBXRA1403/1405 EVALUATION BOARD USER’S MANUAL REV. 1.0.0 2.2Jumper Settings2.2.1Common JumpersThe following jumpers apply to all the 4 packages of XRA1403 and XRA1405:T ABLE 3: C OMMON J UMPER S ETTINGSJ UMPERS F UNCTIONS C OMMENTSJ8Selects the supply voltage to generate the +1.8V power supply for the board 1&2 selects +5V (default, Pin 1 -- Test point for external +5V) 2&3 selects +PN OTE: Not installed. Trace between 1 & 2J9Selects the supply voltage to generate the +2.5V power supply for the board 1&2 selects +5V (default)2&3 selects +PN OTE: Not installed. Trace between 1 & 2J13Selects the supply voltage to generate the +3.3V power supply for the board 1&2 selects +5V (default)2&3 selects +PN OTE: Not installed. Trace between 1 & 2J10Selects the supply voltage for +VDDP Used only for the XRA1405Jumper in 1&2 selects +3.3VJumper in 3&4 selects +2.5VJumper in 5&6 selects +1.8VJ11Selects the supply voltage for +VDD Jumper in 1&2 selects +3.3V (default)Jumper in 3&4 selects +2.5VJumper in 5&6 selects +1.8VJ12Not used for XRA140x Installed but not usedJ14Not used for XRA140x Installed but not usedJ6Not used Installed but not usedJ27LEDs N OTE: Not installed. Pin 2 is connected to GND J3Header for testing GPIO[15:8] of bothTSSOP and QFN packageInstalled. Connect to external input/output.J4Header for testing GPIO[7:0] of both TSSOP and QFN package Installed. Connect to external input/output. Remove jumpers on J28, J29, J30 and J31 after test.J2Header for internal test Not installedJ5Header for XRA1403 and XRA1405 sig-nals and spare signalsInstalled. Connect SPI signals from this header to MCU.J7Header for UART signals and spare sig-nals Not installed. Some GPIO signals and spare signals are accessi-ble at this headerREV. 1.0.0 XRA1403/1405 EVALUATION BOARD USER’S MANUAL 2.2.2XRA1403IL24-FThe following jumpers apply to the XRA1403IL24-F:T ABLE 4: J UMPER S ETTINGS F OR XRA1403IL24-FJ UMPERS F UNCTIONS C OMMENTSJ28Header for connecting GPIO[7:0] signals of QFN package Jumper in pin 1 & J29 pin1 connects GPIO0 to LED Jumper in pin 2 & J29 pin 3 connects GPIO1 to LED Jumper in pin 3 & J29 pin 5 connects GPIO2 to LED Jumper in pin 4 & J29 pin 7 connects GPIO3 to LED Jumper in pin 5 & J29 pin 9 connects GPIO4 to LED Jumper in pin 6 & J29 pin 11 connects GPIO5 to LED Jumper in pin 7 & J29 pin 13 connects GPIO6 to LED Jumper in pin 8 & J29 pin 15 connects GPIO7 to LEDJ29Header for connecting GPIO[7:0] signals of TSSOP package to LEDs 1&2 connects GPIO0 to LED - 0 ohm resistor on board3&4 connects GPIO1 to LED - 0 ohm resistor on board5&6 connects GPIO2 to LED - 0 ohm resistor on board7&8 connects GPIO3 to LED - 0 ohm resistor on board9&10 connects GPIO4 to LED - 0 ohm resistor on board 11&12 connects GPIO5 to LED - 0 ohm resistor on board 13&14 connects GPIO6 to LED - 0 ohm resistor on board 15&16 connects GPIO7 to LED - 0 ohm resistor on boardJ30Header for connecting GPIO[15:8] signals of TSSOP package to LEDs 1&2 connects GPIO8 to LED - 0 ohm resistor on board3&4 connects GPIO9 to LED - 0 ohm resistor on board5&6 connects GPIO10 to LED - 0 ohm resistor on board7&8 connects GPIO11 to LED - 0 ohm resistor on board9&10 connects GPIO12 to LED - 0 ohm resistor on board 11&12 connects GPIO13 to LED - 0 ohm resistor on board 13&14 connects GPIO14 to LED - 0 ohm resistor on board 15&16 connects GPIO15 to LED - 0 ohm resistor on boardJ31Header for connecting GPIO[15:8] signals of QFN package Jumper in pin 1 & J30 pin 1 connects GPIO8 to LED Jumper in pin 2 & J30 pin 3 connects GPIO9 to LED Jumper in pin 3 & J30 pin 5 connects GPIO10 to LED Jumper in pin 4 & J30 pin 7 connects GPIO11 to LED Jumper in pin 5 & J30 pin 9 connects GPIO12 to LED Jumper in pin 6 & J30 pin 11 connects GPIO13 to LED Jumper in pin 7 & J30 pin 13 connects GPIO14 to LED Jumper in pin 8 & J30 pin 15 connects GPIO15 to LEDJ81Selects the supply voltage for +VDD for 24-pin QFN packages Jumper in 2&4 selects +VDD (default) Jumper in 1&3 selects +VDD Jumper in 3&5 selects +VDDJ82Selects the corresponding signal for pin18 of 24-pin QFN packageN OTE: Use J87 pin 2 & 3J83Selects the corresponding signal for pin23 of 24-pin QFN package Jumper in 2&4 selects SI signal (default) Jumper in 1&3 selects A1 signal Jumper in 3&5 selects A1 signalJ84Selects the corresponding signal for pin24 of 24-pin QFN package Jumper in 2&4 selects RESET# signal (default) Jumper in 1&3 selects A2 signalJumper in 3&5 selects RESET# signalXRA1403/1405 EVALUATION BOARD USER’S MANUAL REV. 1.0.0J85Selects the corresponding signal for pin20 of 24-pin QFN package Jumper in 2&4 selects SO signal (default) Jumper in 1&3 selects SDA signal Jumper in 3&5 selects SDA signalJ86Selects the supply voltage for +VDDP for 24-pin QFN packages Installed but not used for XRA1403IL24-F Jumper in 1&2 selects +VDDPJumper in 2&3 selects +VDDPJ87Selects the corresponding signal for pin18 of 24-pin QFN package Jumper in 2&3 selects CS# signal (default) Jumper in 1&2 selects A0 signalJ88Selects the corresponding signal for pin23 of 24-pin QFN package Installed but not used for XRA1403IL24-F Jumper in 1&2 selects +VDD signal Jumper in 2&3 selects +VDD signalJ89Selects the corresponding signal for pin24 of 24-pin QFN package Installed but not used for XRA1403IL24-F Jumper in 1&2 selects RESET# signal Jumper in 2&3 selects SI signalJ90Selects the corresponding signal for pin20 of 24-pin QFN package Installed but not used for XRA1403IL24-F Jumper in 1&2 selects SDA signal Jumper in 2&3 selects SO signalJ71, J72, J73, J74, J75, J76, J77, J78, J79, J80Not used for XRA1403IL24-F Not installed.T ABLE 4: J UMPER S ETTINGS F OR XRA1403IL24-FJ UMPERS F UNCTIONS C OMMENTSREV. 1.0.0 XRA1403/1405 EVALUATION BOARD USER’S MANUAL 2.2.3XRA1403IG24-FThe following jumpers apply to the XR1403IG24-F:T ABLE 5: J UMPER S ETTINGS F OR XRA1403IG24-FJ UMPERS F UNCTIONS C OMMENTSJ28Header for connecting GPIO[7:0] signalsof QFN packageInstalled but not usedJ29Header for connecting GPIO[7:0] signals of TSSOP package to LEDs Jumper in 1&2 connects GPIO0 to LED Jumper in 3&4 connects GPIO1 to LED Jumper in 5&6 connects GPIO2 to LED Jumper in 7&8 connects GPIO3 to LED Jumper in 9&10 connects GPIO4 to LED Jumper in 11&12 connects GPIO5 to LED Jumper in 13&14 connects GPIO6 to LED Jumper in 15&16 connects GPIO7 to LEDJ30Header for connecting GPIO[15:8] signals of TSSOP package to LEDs Jumper in 1&2 connects GPIO8 to LED Jumper in 3&4 connects GPIO9 to LED Jumper in 5&6 connects GPIO10 to LED Jumper in 7&8 connects GPIO11 to LED Jumper in 9&10 connects GPIO12 to LED Jumper in 11&12 connects GPIO13 to LED Jumper in 13&14 connects GPIO14 to LED Jumper in 15&16 connects GPIO15 to LEDJ31Header for connecting GPIO[15:8] signalsof QFN packageInstalled but not usedJ71Selects the supply voltage for +VDD for 24-pin TSSOP packages Jumper in 2&4 selects +VDD (default) Jumper in 1&3 selects +VDD Jumper in 3&5 selects +VDDJ72Selects the corresponding signal for pin21 of 24-pin TSSOP packageN OTE: Use J78 pin 2 & 3J73Selects the corresponding signal for pin 2 of 24-pin TSSOP package Jumper in 2&4 selects SI signal (default) Jumper in 1&3 selects A1 signal Jumper in 3&5 selects A1 signalJ74Selects the corresponding signal for pin 3 of 24-pin TSSOP package Jumper in 2&4 selects RESET# signal (default) Jumper in 1&3 selects A2 signalJumper in 3&5 selects RESET# signalJ75Selects the corresponding signal for pin23 of 24-pin TSSOP package Jumper in 2&4 selects SO signal (default) Jumper in 1&3 selects SDA signal Jumper in 3&5 selects SDA signalJ76Selects the supply voltage for +VDDP for 24-pin TSSOP packages Installed but not used for XRA1403IG24-F Jumper in 1&2 selects +VDDPJumper in 2&3 selects +VDDPJ77Selects the corresponding signal for pin 2 of 24-pin TSSOP package Installed but not used for XRA1403IG24-F Jumper in 1&2 selects +VDD signal Jumper in 2&3 selects +VDD signalJ78Selects the corresponding signal for pin21 of 24-pin TSSOP package Jumper in 2&3 selects CS# signal (default) Jumper in 1&2 selects A0 signalXRA1403/1405 EVALUATION BOARD USER’S MANUAL REV. 1.0.0J79Selects the corresponding signal for pin 3 of 24-pin TSSOP package Installed but not used for XRA1403IG24-F Jumper in 1&2 selects RESET# signal Jumper in 2&3 selects SI signalJ80Selects the corresponding signal for pin23 of 24-pin TSSOP package Installed but not used for XRA1403IG24-F Jumper in 1&2 selects SDA signal Jumper in 2&3 selects SO signalJ81, J82, J83, J84, J85, J86, J87, J88, J89, J90Not used for XRA1403IG24-F Not installedT ABLE 5: J UMPER S ETTINGS F OR XRA1403IG24-FJ UMPERS F UNCTIONS C OMMENTSREV. 1.0.0 XRA1403/1405 EVALUATION BOARD USER’S MANUAL 2.2.4XRA1405IL24-FThe following jumpers apply to the XRA1405IL24-F:T ABLE 6: J UMPER S ETTINGS F OR XRA1405IL24-FJ UMPERS F UNCTIONS C OMMENTSJ28Header for connecting GPIO[7:0] signals of QFN package Jumper in pin 1 & J29 pin 1 connects GPIO0 to LED Jumper in pin 2 & J29 pin 3 connects GPIO1 to LED Jumper in pin 3 & J29 pin 5 connects GPIO2 to LED Jumper in pin 4 & J29 pin 7 connects GPIO3 to LED Jumper in pin 5 & J29 pin 9 connects GPIO4 to LED Jumper in pin 6 & J29 pin 11 connects GPIO5 to LED Jumper in pin 7 & J29 pin 13 connects GPIO6 to LED Jumper in pin 8 & J29 pin 15 connects GPIO7 to LEDJ29Header for connecting GPIO[7:0] signals of TSSOP package to LEDs 1&2 connects GPIO0 to LED - 0 ohm resistor on board3&4 connects GPIO1 to LED - 0 ohm resistor on board5&6 connects GPIO2 to LED - 0 ohm resistor on board7&8 connects GPIO3 to LED - 0 ohm resistor on board9&10 connects GPIO4 to LED - 0 ohm resistor on board 11&12 connects GPIO5 to LED - 0 ohm resistor on board 13&14 connects GPIO6 to LED - 0 ohm resistor on board 15&16 connects GPIO7 to LED - 0 ohm resistor on boardJ30Header for connecting GPIO[15:8] signals of TSSOP package to LEDs 1&2 connects GPIO8 to LED - 0 ohm resistor on board3&4 connects GPIO9 to LED - 0 ohm resistor on board5&6 connects GPIO10 to LED - 0 ohm resistor on board7&8 connects GPIO11 to LED - 0 ohm resistor on board9&10 connects GPIO12 to LED - 0 ohm resistor on board 11&12 connects GPIO13 to LED - 0 ohm resistor on board 13&14 connects GPIO14 to LED - 0 ohm resistor on board 15&16 connects GPIO15 to LED - 0 ohm resistor on boardJ31Header for connecting GPIO[15:8] signals of QFN package Jumper in pin 1 & J30 pin 1 connects GPIO8 to LED Jumper in pin 2 & J30 pin 3 connects GPIO9 to LED Jumper in pin 3 & J30 pin 5 connects GPIO10 to LED Jumper in pin 4 & J30 pin 7 connects GPIO11 to LED Jumper in pin 5 & J30 pin 9 connects GPIO12 to LED Jumper in pin 6 & J30 pin 11 connects GPIO13 to LED Jumper in pin 7 & J30 pin 13 connects GPIO14 to LED Jumper in pin 8 & J30 pin 15 connects GPIO15 to LEDJ81Selects the supply voltage for +VDD for 24-pin QFN packages Installed but not used for XRA1405IL24-F Jumper in 1&3 selects +VDDJumper in 3&5 selects +VDDJumper in 2&4 selects +VDDJ82Selects the corresponding signal for pin18 of 24-pin QFN package Installed but not used for XRA1405IL24-F Jumper in 1&3 selects A0 signalJumper in 3&5 selects A0 signalJumper in 2&4 selects CS# signalXRA1403/1405 EVALUATION BOARD USER’S MANUAL REV. 1.0.0J83Selects the corresponding signal for pin23 of 24-pin QFN package Installed but not used for XRA1405IL24-F Jumper in 1&3 selects A1 signalJumper in 3&5 selects A1 signalJumper in 2&4 selects SI signalJ84Selects the corresponding signal for pin24 of 24-pin QFN package Installed but not used for XRA1405IL24-F Jumper in 1&3 selects A2 signal Jumper in 3&5 selects RESET# signal Jumper in 2&4 selects RESET# signalJ85Selects the corresponding signal for pin20 of 24-pin QFN package Installed but not used for XRA1405IL24-F Jumper in 1&3 selects SDA signal Jumper in 3&5 selects SDA signal Jumper in 2&4 selects SO signalJ86Selects the supply voltage for +VDDP for 24-pin QFN packages Jumper in 2&3 selects +VDDP (default) Jumper in 1&2 selects +VDDPJ87Selects the corresponding signal for pin18 of 24-pin QFN package Jumper in 2&3 selects CS# signal (default) Jumper in 1&2 selects A0 signalJ88Selects the corresponding signal for pin23 of 24-pin QFN package Jumper in 2&3 selects +VDD signal (default) Jumper in 1&2 selects +VDD signalJ89Selects the corresponding signal for pin24 of 24-pin QFN package Jumper in 2&3 selects SI signal (default) Jumper in 1&2 selects RESET# signalJ90Selects the corresponding signal for pin20 of 24-pin QFN package Jumper in 2&3 selects SO signal (default) Jumper in 1&2 selects SDA signalJ71, J72, J73, J74, J75, J76, J77, J78, J79, J80Not used for XRA1405IL24-F Not installed.T ABLE 6: J UMPER S ETTINGS F OR XRA1405IL24-FJ UMPERS F UNCTIONS C OMMENTSREV. 1.0.0 XRA1403/1405 EVALUATION BOARD USER’S MANUAL 2.2.5XRA1405IG24-FThe following jumpers apply to the XR1405IG24-F:T ABLE 7: J UMPER S ETTINGS F OR XRA1405IG24-FJ UMPERS F UNCTIONS C OMMENTSJ28Header for connecting GPIO[7:0] signalsof QFN packageInstalled but not usedJ29Header for connecting GPIO[7:0] signals of TSSOP package to LEDs Jumper in 1&2 connects GPIO0 to LED Jumper in 3&4 connects GPIO1 to LED Jumper in 5&6 connects GPIO2 to LED Jumper in 7&8 connects GPIO3 to LED Jumper in 9&10 connects GPIO4 to LED Jumper in 11&12 connects GPIO5 to LED Jumper in 13&14 connects GPIO6 to LED Jumper in 15&16 connects GPIO7 to LEDJ30Header for connecting GPIO[15:8] signals of TSSOP package to LEDs Jumper in 1&2 connects GPIO8 to LED Jumper in 3&4 connects GPIO9 to LED Jumper in 5&6 connects GPIO10 to LED Jumper in 7&8 connects GPIO11 to LED Jumper in 9&10 connects GPIO12 to LED Jumper in 11&12 connects GPIO13 to LED Jumper in 13&14 connects GPIO14 to LED Jumper in 15&16 connects GPIO15 to LEDJ31Header for connecting GPIO[15:8] signalsof QFN packageInstalled but not usedJ71Selects the supply voltage for +VDD for 24-pin TSSOP packages Installed but not used for XRA1405IG24-F Jumper in 1&3 selects +VDDJumper in 3&5 selects +VDDJumper in 2&4 selects +VDDJ72Selects the corresponding signal for pin21 of 24-pin TSSOP package Installed but not used for XRA1405IG24-F Jumper in 1&3 selects A0 signalJumper in 3&5 selects A0 signalJumper in 2&4 selects CS# signalJ73Selects the corresponding signal for pin 2 of 24-pin TSSOP package Installed but not used for XRA1405IG24-F Jumper in 1&3 selects A1 signalJumper in 3&5 selects A1 signalJumper in 2&4 selects SI signalJ74Selects the corresponding signal for pin 3 of 24-pin TSSOP package Installed but not used for XRA1405IG24-F Jumper in 1&3 selects A2 signalJumper in 3&5 selects RESET# signal Jumper in 2&4 selects RESET# signalJ75Selects the corresponding signal for pin23 of 24-pin TSSOP package Installed but not used for XRA1405IG24-F Jumper in 1&3 selects SDA signal Jumper in 3&5 selects SDA signal Jumper in 2&4 selects SO signalJ76Selects the supply voltage for +VDDP for 24-pin TSSOP packages Jumper in 2&3 selects +VDDP (default) Jumper in 1&2 selects +VDDPNOTICEEXAR Corporation reserves the right to make changes to the products contained in this publication in order to improve design, performance or reliability. EXAR Corporation assumes no responsibility for the use of any circuits described herein, conveys no license under any patent or other right, and makes no representation that the circuits are free of patent infringement. Charts and schedules contained here in are only for illustration purposes and may vary depending upon a user’s specific application. While the information in this publication has been carefully checked; no responsibility, however, is assumed for inaccuracies.EXAR Corporation does not recommend the use of any of its products in life support applications where the failure or malfunction of the product can reasonably be expected to cause failure of the life support system or to significantly affect its safety or effectiveness. Products are not authorized for use in such applications unless EXAR Corporation receives, in writing, assurances to its satisfaction that: (a) the risk of injury or damage has been minimized; (b) the user assumes all such risks; (c) potential liability of EXAR Corporation is adequately protected under the circumstances.Copyright 2011 EXAR CorporationDatasheet October 2011.Send your UART technical inquiry with technical details to hotline: ************************.Reproduction, in part or whole, without the prior written consent of EXAR Corporation is prohibited.XRA1403/1405 EVALUATION BOARD USER’S MANUAL REV. 1.0.0 3.0TECHNICAL SUPPORTIf there are any questions, please send an e-mail to ************************.J77Selects the corresponding signal for pin 2 of 24-pin TSSOP package Jumper in 2&3 selects +VDD signal (default)Jumper in 1&2 selects +VDD signal J78Selects the corresponding signal for pin 21 of 24-pin TSSOP package Jumper in 2&3 selects CS# signal (default)Jumper in 1&2 selects A0 signal J79Selects the corresponding signal for pin 3 of 24-pin TSSOP package Jumper in 2&3 selects SI signal (default)Jumper in 1&2 selects RESET# signal J80Selects the corresponding signal for pin23 of 24-pin TSSOP package Jumper in 2&3 selects SO signal (default)Jumper in 1&2 selects SDA signalJ81, J82, J83, J84,J85, J86,J87, J88,J89, J90Not used for XRA1405IG24-FNot installed T ABLE 7: J UMPER S ETTINGS F OR XRA1405IG24-FJ UMPERSF UNCTIONS C OMMENTS。
Power Generation Information Manager (PGIM) 信息管理器说
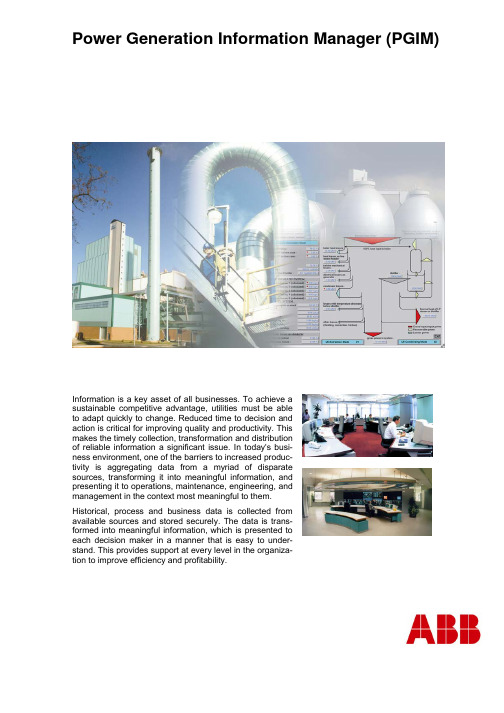
Power Generation Information Manager (PGIM)sustainable competitive advantage, utilities must be ableto adapt quickly to change. Reduced time to decision andaction is critical for improving quality and productivity. Thismakes the timely collection, transformation and distributionof reliable information a significant issue. In today's busi-ness environment, one of the barriers to increased produc-tivity is aggregating data from a myriad of disparate Arraysources, transforming it into meaningful information, andpresenting it to operations, maintenance, engineering, andmanagement in the context most meaningful to them.Historical, process and business data is collected fromavailable sources and stored securely. The data is trans-formed into meaningful information, which is presented toeach decision maker in a manner that is easy to under-stand. This provides support at every level in the organiza-tion to improve efficiency and profitability.The PGIM Clients provide an advanced user interface. Clients retrieve process data from databases, and then offer comprehensive func-tions for evaluating process status information.A True Decision-Taking ToolPower Generation Information Manager (PGIM) offers a company-wide system architec-ture that performs these functions:Center PIMS provides a flexible and scalable structure suitable for building any type of solution; fromsingle computer configurations to large-scale,distributed cross-plant systems.Collecting, archiving and consolidating data from production facilities, control systems.Conducting remote diagnosticson numerous plant components.convenient user interface.Making data available to otherevaluating applications (e.g. foroperation schedule optimization,EXCEL reporting).Delivering process parameters,financial systems.PGIM open client/server architecture.The various elements of the system can run onMicrosoft Windows operating system.Clients can connect to any connected PIMSserver. Protection and access rights are formu-lated in an access protection concept , whichdefines several access levels and signal-specific rights .PGIM is a product of ABB's Industrial IT family,integrated in System 800xA and designed forlong-term protection of asset investment.System StructureThe system is fail-safe thanks to a redundant design database with buffered control system connections. The special design of the PC hardware further enhances the level of safety. The PGIM Scanners collect process data from lower-level control systems, PLCs, or other re-cording systems.The SignalExplorer is a centralized utility de-signed for quick and responsive configuration . An intuitive layout allows you to easily create customized trend displays, dynamic graphical reports, and comprehensive data calculations.The PGIM Server polls the data and stores in-formation, such as:Signal descriptions.Current and historical values. Messages.Detailed status information coming fromsubordinate systems in a process database. All this is accomplished on a millisecond basis over a period of several years.Excel add-ins for reporting purposes enable immediate or programmed initiation of hourly,shift-specific, daily, monthly or yearly reports. In addition, balance and maintenance reports can be generated in a familiar Excel environ-ment. Data from any connected site can becombined and presented in spreadsheet format.Technical calculation tools are available to perform basic arithmetic functions, water/steam chart calculations and other common functions. These tools include a variety of both standard-ized and prepared performance calculation modules.Numerous flexible interfaces enable distrib-uted data collection using most industry stan-dards. Open interfaces are available in the form of OLE/OPC/SQL and native C-DLL APIs. Another powerful feature is performance-based trend representation. You can inte-grate an unlimited number of signals quickly with tools that automate scaling, legends and database functions. Display average, maxi-mum, minimum, differential and integral values. A user-friendly development environment sup-ports simple configuration procedures.PGIM provides a Thin-Web Client to access all relevant information of the PGIM server by standardized web services. The Thin Web Cli-ent can read all configurations made for the normal PGIM clients. It supports graphics, trends, reports and all Event Management func-tions. No extra extra software needs to be installedon your computers.Create High-performance graphic displays to support efficient engineering processes. Logi-cally arranged graphic displays can clearly pre-sent both process parameters and calculated values.The integrated Alarm and Event Manage-ment system allows the storage and retrieval of all Messages from any types of sources to be filtered to match your customized conditions. These messages include items such as prompts for information, links to more informa-tion, or requests to execute programs.Clearly arranged message logs allow you to analyze process disturbances in a comprehen-sive manner.Graphical event statistics help finding distur-bances easier and to optimize the system. The view of messages can be set individually, and can be customized at any time using menu-driven commands. Messages can be viewed in a list format or in an alarm page format.SummaryUse Power Generation Information Manager (PGIM) to:Save costs through company-wide accessto critical information.Accelerate business processes. Detect po-tential bottlenecks quickly. Prevent distur-bances before they become problems.Increase productivity by eliminating activi-ties for conditioning data.Deliver new quality standards by comparingpast and present operational processes. Support decision-taking processes by ex-tending data access to all relevant informa-tion. Make information available to anyone who is interested, at any time.The Industrial IT wordmark and all mentioned product names in the form XXXXXX For continuous monitoring of alarms and events reports such as required by EEMUA 192 can be generated via an easy to use Excel add-in or by using standardized template coming together with PGIM.IT are registered or pending trademarks of ABB.P u b l i c a t i o n n u m b e r : D E A B B 1184 05 EWindows NT ®, Windows 2000®, EXCEL ®, Explorer are registered trademarks of the Microsoft Corporation, USA.ABB AGBusiness Unit Power Generation P.O. Box 10 03 51 68128 Mannheim GERMANYPhone: +49 (0) 6 21 381-30 00 Fax: +49 (0) 6 21 381-26 45 E-mail:****************.com NOTE:We reserve the right to make technical changes or modify the contents of this document without prior notice. With regard to purchase orders, the agreed particulars shall prevail.ABB does not accept any responsibility whatsoever for potential errors or possible lack of information in this document.We reserve all rights in this document and in the subject matter and illustrations contained therein. Any reproduction – in whole or in parts – is forbidden without ABB's prior written consent.。
NI-845x软件和硬件安装指南说明书
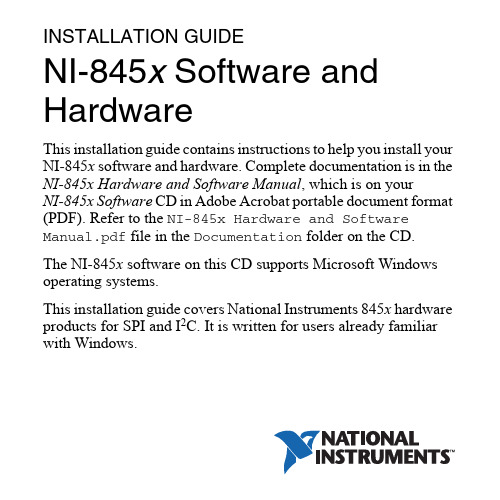
INSTALLATION GUIDENI-845x Software and HardwareThis installation guide contains instructions to help you install your NI-845x software and hardware. Complete documentation is in the NI-845x Hardware and Software Manual, which is on yourNI-845x Software CD in Adobe Acrobat portable document format (PDF). Refer to the NI-845x Hardware and Software Manual.pdf file in the Documentation folder on the CD.The NI-845x software on this CD supports Microsoft Windows operating systems.This installation guide covers National Instruments 845x hardware products for SPI and I2C. It is written for users already familiar with Windows.Install the NI-845x SoftwareBefore installing the NI-845x software, you first must log on as Administrator or as a user with Administrator privileges. The NI-845x software setup program must have Administrator privileges because the program modifies the configuration registry of your system.Complete the following steps to install the NI-845x software. 1.Insert the NI-845x Software CD into your CD-ROM drive. Theinstaller launches if your CD-ROM drive plays data CDsautomatically.If the installer does not launch automatically, navigate to the CD using Windows Explorer and launch the autorun.exefile from your NI-845x Software CD.2.The installation wizard guides you through the necessary stepsto install the NI-845x software. You can go back and change values where appropriate by clicking the Back button. You can exit the setup where appropriate by clicking Cancel.3.When installation is complete, click Finish.2||NI-845x Software and Hardware Installation GuideInstall the HardwareStep 1: Unpack the Devices, Accessories, Cables Your device ships in an antistatic package to prevent electrostatic discharge (ESD) damage to the device. ESD can damage several components on the device.To avoid such damage, take the following precautions:•Ground yourself using a grounding strap or by touching a grounded object.•Touch the antistatic package to a metal part of the computer chassis before removing the device from the package. Remove the device from the package and inspect the device for loose components or any sign of damage. Notify National Instruments if the device appears damaged in any way. Do not install a damaged device into your computer or PXI chassis. Store the device in the antistatic package when not in use.For safety and compliance information, refer to the device documentation packaged with your device.NI-845x Software and Hardware Installation Guide|© National Instruments|3Step 2: Install the Devices, Accessories, and CablesComplete the following steps to install an NI USB device:1.Connect the USB cable from the computer USB port or fromany other hub that provides USB power to the USB port on the device. The following figure shows the USB cable and itsconnectors.2.Power on your computer or PXI chassis. On some Windowssystems, the Found New Hardware wizard opens with a dialog box for every device installed. Click Next or Yes to install the software for each device.3.Install accessories and/or terminal blocks according to theinstructions in their user guides.4||NI-845x Software and Hardware Installation GuideStep 3: Confirm that Y our Device Is Recognized To verify that the USB device is recognized, complete the following steps:1.Double-click the Measurement and Automation icon on thedesktop to open Measurement and Automation Explorer(MAX).2.Expand Devices and Interfaces.3.Verify that the device appears under USB Devices. If thedevice does not appear, press <F5> to refresh the view inMAX. If the device is still not recognized, refer to / support/install for troubleshooting information.NI-845x Software and Hardware Installation Guide|© National Instruments|5Uninstalling the NI-845x SoftwareComplete the following steps to uninstall the NI-845x software: 1.Navigate to the location where the Windows operating systemallows you to uninstall software.2.Find and select National Instruments Software. Click theUninstall/Change button.3.Select NI-845x Software in the list of products and clickRemove.The uninstall program removes all folders, utilities, device drivers, DLLs, and registry entries associated with the NI-845x software. The uninstall program removes only items that the installation program installed.If you have added anything to a directory created by the installation program, the uninstall program cannot delete that directory because it is not empty after the uninstallation. Remove any remaining components manually.6||NI-845x Software and Hardware Installation GuideFurther DocumentationAdditional documentation for the NI-845x software is in theNI-845x Hardware and Software Manual, which is on the NI-845xSoftware CD in Adobe Acrobat portable document format (PDF). The manual includes an overview of the I2C and SPI buses as wellas detailed information on the API. Refer to the NI-845x Hardware and Software Manual.pdf file on your CD or in the NI-845x Software\Documentation folder on your hard drive.Additional documentation for your NI-845x interface is on your CD or in the NI-845x Software\Documentation folder on your hard drive.Worldwide Support and ServicesThe NI website is your complete resource for technical support. At /support you have access to everything from troubleshooting and application development self-help resources to email and phone assistance from NI Application Engineers. Visit /services for NI Factory Installation Services, repairs, extended warranty, and other services.NI-845x Software and Hardware Installation Guide|© National Instruments|7© 2005–2017 National Instruments. All rights reserved.371708D-01Mar17Refer to the NI Trademarks and Logo Guidelines at /trademarks for more information on NI trademarks. Other product and company names mentioned herein are trademarks or trade names of their respective companies. For patents covering NI products/technology, refer to the appropriate location: Help»Patents in your software, the patents.txt file on your media, or the National Instruments Patent Notice at /patents . You can find information about end-user license agreements (EULAs) and third-party legal notices in the readme file for your NI product. Refer to the Export Compliance Information at /legal/export-compliance for the NI global trade compliance policy and how to obtain relevant HTS codes, ECCNs, and other import/export data. NI MAKES NO EXPRESS OR IMPLIED WARRANTIES AS TO THE ACCURACY OF THE INFORMATION CONTAINED HEREIN AND SHALL NOT BE LIABLE FOR ANY ERRORS. U.S. Government Customers: The data contained in this manual was developed at private expense and is subject to the applicable limited rights and restricted data rights as set forth in FAR 52.227-14, DFAR 252.227-7014, and DFAR 252.227-7015.Visit /register to register your NI product. Product registration facilitates technical support and ensures that you receive important information updates from NI.NI corporate headquarters is located at 11500North Mopac Expressway, Austin, Texas, 78759-3504. NI also has offices located around the world. For telephone support in the United States, create your service request at /support or dial 1866ASK MYNI (2756964). For telephone support outside the United States, visit the Worldwide Offices section of /niglobal to access the branch office websites, which provide up-to-date contact information, support phone numbers, email addresses, and current events.。
NXP Semiconductors SAC57D5xx系列多核微控制器外部调节模式和低功耗握手协议
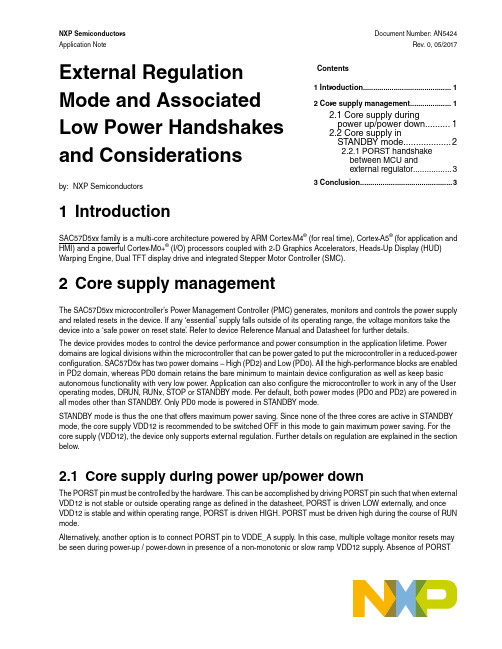
External RegulationMode and AssociatedLow Power Handshakesand Considerationsby:NXP Semiconductors 1IntroductionSAC57D5xx family is a multi-core architecture powered by ARM Cortex-M4® (for real time), Cortex-A5®(for application and HMI) and a powerful Cortex-M0+® (I/O) processors coupled with 2-D Graphics Accelerators, Heads-Up Display (HUD) Warping Engine, Dual TFT display drive and integrated Stepper Motor Controller (SMC).2 Core supply managementThe SAC57D5xx microcontroller’s Power Management Controller (PMC) generates, monitors and controls the power supply and related resets in the device. If any ‘essential’ supply falls outside of its operating range, the voltage monitors take the device into a ‘safe power on reset state’. Refer to device Reference Manual and Datasheet for further details.The device provides modes to control the device performance and power consumption in the application lifetime. Power domains are logical divisions within the microcontroller that can be power gated to put the microcontroller in a reduced-power configuration. SAC57D5x has two power domains – High (PD2) and Low (PD0). All the high-performance blocks are enabled in PD2 domain, whereas PD0 domain retains the bare minimum to maintain device configuration as well as keep basic autonomous functionality with very low power. Application can also configure the microcontroller to work in any of the User operating modes, DRUN, RUNx, STOP or STANDBY mode. Per default, both power modes (PD0 and PD2) are powered in all modes other than ST ANDBY . Only PD0 mode is powered in ST ANDBY mode.STANDBY mode is thus the one that offers maximum power saving. Since none of the three cores are active in ST ANDBY mode, the core supply VDD12 is recommended to be switched OFF in this mode to gain maximum power saving. For the core supply (VDD12), the device only supports external regulation. Further details on regulation are explained in the section below.2.1 Core supply during power up/power downThe PORST pin must be controlled by the hardware. This can be accomplished by driving PORST pin such that when external VDD12 is not stable or outside operating range as defined in the datasheet, PORST is driven LOW externally, and once VDD12 is stable and within operating range, PORST is driven HIGH. PORST must be driven high during the course of RUN mode.Alternatively, another option is to connect PORST pin to VDDE_A supply. In this case, multiple voltage monitor resets may be seen during power-up / power-down in presence of a non-monotonic or slow ramp VDD12 supply. Absence of PORST Contents 1 Introduction...........................................12 Core supply management....................12.1 Core supply during power up/power down..........12.2 Core supply in ST ANDBY mode...................22.2.1 PORST handshake between MCU and external regulator.................33 Conclusion.............................................3NXP SemiconductorsDocument Number: AN5424Application Note Rev. 0, 05/2017handshake may result in multiple interrupts being seen when exiting from ST ANDBY mode. This may also result in device getting stuck in reset in certain mode transition cases from ST ANDBY to DRUN.2.2Core supply in STANDBY modeOnce ST ANDBY mode is entered, it can only be left via a system wakeup. Since the cores are not working in ST ANDBY mode,the VDD12 core supply can be disabled using external regulator control (PE9, PE14 or PM7) pin. External regulator control functionality on PE9, PE14 or PM7 pin can be enabled by configuring UTEST_MISC [EXTn_REG_SUPPL Y]. Polarity of these pins can be further controlled by appropriately configuring UTEST_MISC [EXT_REG_POL]. The timing diagram below describes the required configuration.UT EST _MISC [EXTn_REG_SUPPLY ] = 1, where n can be 0,1,2ResetMODES PHASE1ST AND BY RUNPHASE0PHASE3PHASE2RUN UT EST _MISC [EXT n_REG_POL] = 1, where n can be 0,1,2Reg ulator control PinHi-Z Reg ulator control PinUT EST _MISC [EXT n_REG_POL] = 0, where n can be 0,1,2Hi-Z PORSTUT EST _MISC [PORST _MASK ] = 0PORST EST _MISC [PORST _MASK ] = 1nal receivedFigure 1.External regulator configurationsVDD12 supply is generated externally and can be gated/disabled when in ST ANDBY mode. External regulator control pins can be configured in UTEST_MISC DCF using EXTn_REG_SUPPL Y field (for more details on DCF refer to'UTEST_register_Bits' tab of the DCF sheet attached with device Reference Manual) to enable/disable the supply to the cores. The external regulator control pins can also be used to directly enable/disable the regulator if the external regulator supports such control (usually by means of enable pin). Figure 2. Example hardware block for external regulator control on page 2 shows one of the block level implementation of hardware. The hardware must be designed in such a way that electrical specs stated in the device are followed.SAC57DXXFigure 2.Example hardware block for external regulator controlCore supply managementCore supply in STANDBY modeExternal Regulation Mode and Associated Low Power Handshakes and Considerations , Rev. 0, 05/20172NXP SemiconductorsConclusionCore supply in ST ANDBY mode 2.2.1PORST handshake between MCU and external regulator During ST ANDBY mode, if UTEST_MISC [PORST_MASK] is set to 0 then PORST must be kept high even if VDD12 is supplied externally or not. Pulling PORST pin low in ST ANDBY mode will result in chip getting into RESET.In case UTEST_MISC [PORST_MASK] is set to 1 then PORST pin can be used as a handshake signal between MCU and external regulator to indicate presence/absence of externally supplied VDD12. PORST must be driven low after external regulator control pins indicate ST ANDBY mode has been entered and as soon as the external regulator is disabled. The device will not exit ST ANDBY mode as long as the PORST pin is kept low.3ConclusionPORST signal is recommended to be used for handshake between the Core supply regulator and the MCU in addition to all the recommended hardware design guidelines. For more information refer to AN5265.External Regulation Mode and Associated Low Power Handshakes and Considerations , Rev. 0, 05/2017NXP Semiconductors3How To Reach Us Home Page: Web Support: /support Information in this document is provided solely to enable system and software implementers to use NXP products. There are no express or implied copyright licenses granted hereunder to design or fabricate any integrated circuits based on the information in this document. NXP reserves the right to make changes without further notice to any products herein.NXP makes no warranty, representation, or guarantee regarding the suitability of its products for any particular purpose, nor does NXP assume any liability arising out of the application or use of any product or circuit, and specifically disclaims any and all liability, including without limitation consequential or incidental damages. “Typical” parameters that may be provided in NXP data sheets and/or specifications can and do vary in different applications, and actual performance may vary over time. All operating parameters, including “typicals,” must be validated for each customer application by customer's technical experts. NXP does not convey any license under its patent rights nor the rights of others. NXP sells products pursuant to standard terms and conditions of sale, which can be found at the following address: / SalesTermsandConditions.NXP, the NXP logo, NXP SECURE CONNECTIONS FOR A SMARTER WORLD, COOLFLUX, EMBRACE, GREENCHIP, HITAG, I2C BUS, ICODE, JCOP, LIFE VIBES, MIFARE, MIFARE CLASSIC, MIFARE DESFire, MIFARE PLUS, MIFARE FLEX, MANTIS, MIFARE ULTRALIGHT, MIFARE4MOBILE, MIGLO, NTAG, ROADLINK, SMARTLX, SMARTMX, STARPLUG, TOPFET, TRENCHMOS, UCODE, Freescale, the Freescale logo, AltiVec, C‑5, CodeTEST, CodeWarrior, ColdFire, ColdFire+, C‑Ware, the Energy Efficient Solutions logo, Kinetis, Layerscape, MagniV, mobileGT, PEG, PowerQUICC, Processor Expert, QorIQ, QorIQ Qonverge, Ready Play, SafeAssure, the SafeAssure logo, StarCore, Symphony, VortiQa, Vybrid, Airfast, BeeKit, BeeStack, CoreNet, Flexis, MXC, Platform in a Package, QUICC Engine, SMARTMOS, Tower, T urboLink, and UMEMS are trademarks of NXP B.V. All other product or service names are the property of their respective owners. ARM, AMBA, ARM Powered, Artisan, Cortex, Jazelle, Keil, SecurCore, Thumb, TrustZone, and μVision are registered trademarks of ARM Limited (or its subsidiaries) in the EU and/or elsewhere. ARM7, ARM9, ARM11, big.LITTLE, CoreLink, CoreSight, DesignStart, Mali, mbed, NEON, POP, Sensinode, Socrates, ULINK and Versatile are trademarks of ARM Limited (or its subsidiaries) in the EU and/or elsewhere. All rights reserved. Oracle and Java are registered trademarks of Oracle and/or its affiliates. The Power Architecture and word marks and the Power and logos and related marks are trademarks and service marks licensed by .Ⓒ 2017 NXP B.V.AN5424Rev. 005/2017。
IQAN电子控制系统用户手册说明书
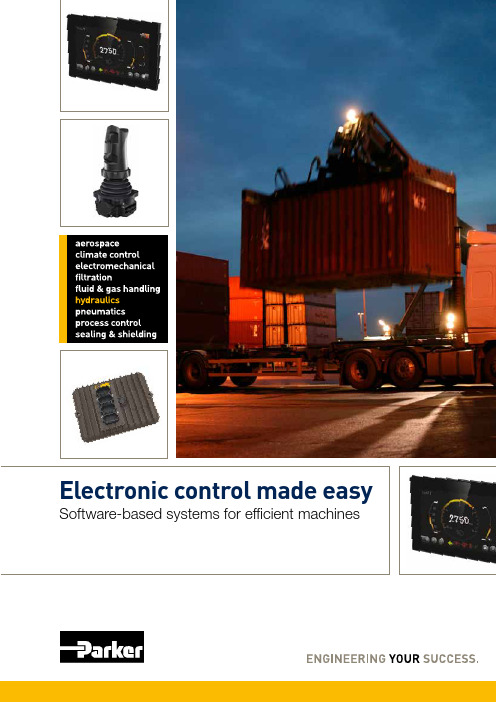
s Dramatically reduced development costsThe wide range of outdoor modules with flexible I/O available with IQAN ensures complete machine manage-ment. The system offers a building-block approach that simplifies component design and installation while also reducing development time and expenses.u Rugged design and excellent ergonomicsIQAN hardware is thoroughly tested for robust operation and compatibility with all kinds of mobile hydraulic equipment. In addition, it meets industry and government standards for operation in severe conditions, including extremely high or low temperatures, vibrations, mechanical impact and electromagnetic interference.Efficiency in focus – throughout the entire machine life cycle Electronic control made easyThe state-of-the-art IQAN systemis a unique, totally electronicapproach that replaces mechani-cal and electromechanical systemsfor controlling and monitoringhydraulics in mobile machines.With Parker’s IQAN, you havecomplete freedom to design cus-tomized software without the needfor advanced programming skills.The flexible functions availablewithin the IQAN system allowsophisticated applications to beprogrammed and optimized veryquickly, enabling huge savings ondevelopment time – and cost.The IQAN software tools cover allphases of a machine’s life cycle,from development through pro-duction to after sales.NTA L E SsEasy installationThe design philosophy behind the IQAN system is based on simplicity in every way. The modular CAN bus structure offers total freedom in machine development – the rugged IQAN units can be placed in any area of the mobile machine, enabling a more compact design and/or minimised wiring, while reducing installation time to an absolute minimum.RO DU C T I O NPsNo programmingskills requiredIQAN is user-programmable via an advanced, highly intuitive graphic design tool, which dramatically simplifies development. Simulation of the control system can be carried out in parallel with the programming of machine functions.u Advanced diagnosticsThe IQAN control units have an advanced built-in diagnostics system that will help to minimize down-time in the case of failure in the field. Problems can be located either by the default system diagnostics delivered with the standardproduct, or by customer designed diagnostics functionality.s Intelligent display/control The IQAN master modules incorp- orates powerful computing capacity with high processing speeds and multiple CAN bus interfaces. These features make the units extremely flexible and adaptable to a variety of applications with a wide range of hydraulic components and input devices such as joysticks, pedals and sensors.s Sensors forevery type of needThe IQAN sensors have been deve-loped specifically for mobile appli-cations and are designed from the ground up to excel in the demanding physical, regulatory and commercial environment of the mobile machine sector.Intelligent software – the way ahead40 years of motion control experience – ready to plug and playParker’s experience in hydraulic motion control is second to none, with over forty years of experience in close collaboration with custo-mers world-wide. What started with basic ergonomic demands from machine operators hasdeveloped into highly advancedelectro-hydraulic machine control knowledge, made accessible to everyone in the IQAN product range. An IQAN system will not only offer shorter development time for the machine manufactu-rer, but also maximum functiona-lity and up-time for the machine owner once it enters the market.Illustration shows possible product applications in an agricultural tractor.-image courtesy of Valtra Inc.u Multi master support Complex machine layouts anddemanding machine functionality can be facilitated easily with a multi mas-ter system design. Major benefits of such a system include distribu-ted functionality and diagnostics, a distributed human machine interface (HMI), extended memory capacity, faster cycle time and additional I/Os. With IQAN, a multi master system will feel like a single master system.u Long-life precision controls At Parker, we know what reliability means for profitability. All IQAN control units are thoroughly tested and builtto withstand many years of use and abuse in the toughest environmentsimaginable, while maintaining theprecision needed for maximum productivity.sRugged 32-bit performance The IQAN control units have been designed with 32-bit performance to meet high computing demands. The rugged design of the IQAN hardware is tested for robust operation and compatibility with mobile hydraulic equipment. In addition, it meets industry and government standards for operation in severe conditions that include extremely high or low tempe-ratures, vibrations, mechanical impact and electromagnetic interference.u SafetyAll IQAN modules are designed with the functional safety requirements of mobile machines in mind.Where there is a need to prove the safety integrity of each implemented safety function; the safety controller IQAN-MC3 can be used.It is designed in accordance with IEC 61508, and can be used to implement safety functions of up to SIL2.When applying EN ISO 138489-1 for safety functions, it can be used as a PLd subsystem.u Create advanced functions – in minutes!IQANdesign is an advanced design tool with an intuitive graphic interface, which simplifies application development for your mobile machine and redu-ces development time. This tool is mainly used for general system layout and machine function design. There is a wide range of predefined building blocks available, such as closed loop control, signal processing, math calculations, communication protocols (e.g. SAE J1939) and system diagnostics.IQANdesign can be used to design systems with multiple masters. Multiple master design work is simplified by use of a project file that contains applica-tions for all IQAN masters in the system.In addition to machine function design, IQANdesign also provides a simple way to accomplish display page programming using a simple drag and drop inter-face. The menu system can also be customized .t Increased productivity andreduced environmental impactWith IQAN Software studios, any OEM can create custom functions that optimize a machine’s energy efficiency – the power can easily be made available when needed, and only then.Easier development...Cut time-to-market by several monthsThe IQAN software studios cover all phases of a machine’s life cycle, from development through pro- duction to after sales. The main philosophy behind the IQAN Soft-ware Studios is that the OEM, with their extensive knowledge of their machine’s life cycle, should be able to create software that makestheir product perform at top level, easy to produce and giving the end user maximum up-time.All this can be achieved without any previous programming expe-rience – anyone who knows what functions are needed can learn to build them in a remarkably shorttime.• 32-bit technology • Outstanding motion control experience • User-friendly• Software-based development• World-wide supportt Endless possibilitiesToday, an OEM’s engineering depart-ment wants to design and prototype new machines or features quickly and easily. The production depart-ment wants to automate, log and trace the delivery status. The service department wants to handle warran-ties, offer proactive maintenance and download machine upgrades. Finally, the machine owner wants a reliable machine with high productivity and low downtime. To meet all of these demands, IQAN Software Studios were designed to fulfill the needs of the machine life cycle model. IQAN tools give an extraordinary value over the product life cycle. A product generation that lives for 5-10 years can be easily be updated to remain competitive until it is replaced by the next product generation.sVirtual simulation speeds up developmentIQANsimulate is a simulation tool, which simplifies function testing andvalidation, reducing development time. It simulates all of the hardware modules in an IQAN application. Software simulation is a safer way to test new app- lications than on an actual machine. Simulation of all input values in your application is easy using the on-screen sliding bar interface. While simulating inputs you can simultaneously measure the resulting output values. T ogether with module and I/O error simulation you will be able to perform machineFMEA (Failure Modes and Effects Analysis). The simulator will behave just like the ‘real thing’, meaning you will be able to look at your display pages,adjust parameters, view logs, test your user interface and much more.p Speed up production Getting a machine design into production is time consuming. Testing equipment and procedures have to be developed and machine start-up and delivery status needs to be recorded. Fortunately, IQAN Software is tailor-made to fulfill all of these demands. Software tools from IQAN can be adapted to feature machine-specific procedures for maintenance, fault finding and web supported machine upgrades, while the machine owner can access spare parts manuals, maintenance videos, service intervals and service sugges-tions by the software.t Fine-tune in the real world During the development phase you can use IQANrun to optimize your machine’s performance with the help of IQANrun’s advanced graphic measuring and machine statistics collection functions. IQANrun also of-fers a convenient way of developing the basic machine settings during theprototyping phase.s Fewer components, easier installationIQANscript allows you to design machine startups with secured and standard-ized procedures. This increases manufacturing productivity and initial machine quality. By creating troubleshooting scripts you can guide both production and service personnel during the fault finding process. This decreases the fault finding time and makes it possible for less trained personnel to find problems that otherwise would require expert knowledge....easier production...Set-up and customise in minutes – not days!With IQANscript you create scripts using simple drag and drop ope-rations. Each script is a sequence of actions that can be executed in IQANrun. A wide range of script actions are available to build scripts for different ing flow control actions such as conditions and loops you can control how the script is executed. With the different measure andotherwise complex operations. Input from the user can also be collected and used by the script. To provide traceability you can include a customized report in the script. When the script is executed the results will be recorded in the report, making it possible to get a good overview as well as saving the report for future use.t Real-time adjustmentsThe user-friendly IQANrun software is makes fine-tuning functions easy. Any changes can be followed on-screen in real-time for maximum control. The result for the end-user is a better performing mobile machine – andperformance means profitability.log actions, information can be re- trieved from the master units to be analyzed by the script or displayed to the user. Setting actions provide full control of the master settings, making it possible to fine tune the machine using a script. IQANs-cript provides powerful building blocks for the script user interface. Using formatted text and imagesthe script user is guided throughThe script concept was developed to help OEM production departments create routines for testing, tuning, setting options, logging, delivery sheets, etc.• Easy to install and set-up quickly• Customize as desired • I ncrease your delivery capacitysUpgrade anywhereFunctions can be easily tweaked to perfection on a laptop computer, and then downloaded to the IQAN master module – in a workshop or out in thefield, in a matter of minutes.t Remote diagnosticsWith a modem connected to the master module, remote diagnostics on a machine out in the field becomes possible. Trouble-shooting and updating of application software can be done remotely. There is no need to get to the machine for a first diagnosis, and if a physical repair is needed, the service technnician is well prepared with advance information and can bring all the necessary spare parts and tools needed to get the machine running quickly....and easier maintenanceCutting down-time with intelligent diagnostics systemsToday, service technicians have a large number of tools and docu- ments to keep track of. Someti-mes, it is hard for them to find the right information and to be sure they use the correct version of a software or document. The cus-tomize feature in IQAN Productive Studio was developed to solve this problem. It allows you to collect all machine software and informa-tion in one user interface and to distribute it to your users quickly and easily via the web. Machine downtime is minimised since the service technicaian have all the information needed in one place and the information is always up to date.IQANcustomize is a tool that enables customization of the IQANrun software functions and appearance to create a unique ser-vice and production tool. This is done by creating one or more pa-ges using the graphical page editor in IQANcustomize. The pages can contain specific information for each machine type and will be displayed when IQANrun is star-ted. Your company logo, graphics, links and information may all be integrated in the user interface of IQANrun. Using IQANcustomize you can also show or hide IQAN-run functions, or make them avai-lable as links on any page, to assist users through a troubleshooting ortuning process.IQAN product range Everything you need for complete controlIQAN by Parker offers a completerange of control products to meetyour needs. No matter what yourneed is, Parker can offer anythingfrom the most basic valve driverapplication to a complete controlsystem for larger, more complica-ted machines.11Your local authorized Parker distributorParker WorldwideE d . 2015-04-21EMEA Product Information Centre Free phone: 00 800 27 27 5374(from AT , BE, CH, CZ, DE, DK, EE, ES, FI, FR, IE, IL, IS, IT , LU, MT , NL, NO, PL, PT , RU, SE, SK, UK, ZA) US Product Information Centre Toll-free number: 1-800-27 27 537Europe, Middle East, AfricaAE – United Arab Emirates, DubaiTel: +971 4 8127100 ********************AT – Austria, Wiener Neustadt Tel: +43 (0)2622 23501-0 *************************AT – Eastern Europe, Wiener NeustadtTel: +43 (0)2622 23501 900 ****************************AZ – Azerbaijan, Baku Tel: +994 50 22 33 458****************************BE/LU – Belgium, Nivelles Tel: +32 (0)67 280 900*************************BG – Bulgaria, Sofia Tel: +359 2 980 1344**************************BY – Belarus, Minsk Tel: +48 (0)22 573 24 00 ************************CH – Switzerland, Etoy Tel: +41 (0)21 821 87 00*****************************CZ – Czech Republic, Klecany Tel: +420 284 083 111*******************************DE – Germany, Kaarst Tel: +49 (0)2131 4016 0*************************DK – Denmark, Ballerup Tel: +45 43 56 04 00*************************ES – Spain, Madrid Tel: +34 902 330 001 ***********************FI – Finland, VantaaTel: +358 (0)20 753 2500 *************************FR – France, Contamine s/Arve Tel: +33 (0)4 50 25 80 25 ************************GR – Greece, Athens Tel: +30 210 933 6450 ************************HU – Hungary, Budaoers Tel: +36 23 885 470*************************IE – Ireland, Dublin Tel: +353 (0)1 466 6370 *************************IT – Italy, Corsico (MI)Tel: +39 02 45 19 21 ***********************KZ – Kazakhstan, Almaty Tel: +7 7273 561 000****************************NL – The Netherlands, Oldenzaal Tel: +31 (0)541 585 000 ********************NO – Norway, Asker Tel: +47 66 75 34 00************************PL – Poland, Warsaw Tel: +48 (0)22 573 24 00 ************************PT – Portugal, Leca da Palmeira Tel: +351 22 999 7360**************************RO – Romania, Bucharest Tel: +40 21 252 1382*************************RU – Russia, Moscow Tel: +7 495 645-2156************************SE – Sweden, Spånga Tel: +46 (0)8 59 79 50 00 ************************SK – Slovakia, Banská Bystrica Tel: +421 484 162 252**************************SL – Slovenia, Novo Mesto Tel: +386 7 337 6650**************************TR – Turkey, Istanbul Tel: +90 216 4997081 ************************UA – Ukraine, KievTel: +48 (0)22 573 24 00 ************************UK – United Kingdom, Warwick Tel: +44 (0)1926 317 878 ********************ZA – South Africa, Kempton Park Tel: +27 (0)11 961 0700*****************************North AmericaCA – Canada, Milton, Ontario Tel: +1 905 693 3000US – USA, Cleveland (industrial)Tel: +1 216 896 3000US – USA, Elk Grove Village (mobile)Tel: +1 847 258 6200Asia PacificAU – Australia, Castle Hill Tel: +61 (0)2-9634 7777CN – China, Shanghai Tel: +86 21 2899 5000HK – Hong Kong Tel: +852 2428 8008ID – Indonesia, Tangerang Tel: +62 21 7588 1906IN – India, MumbaiTel: +91 22 6513 7081-85JP – Japan, Fujisawa Tel: +81 (0)4 6635 3050KR – South Korea, Seoul Tel: +82 2 559 0400MY – Malaysia, Shah Alam Tel: +60 3 7849 0800NZ – New Zealand, Mt Wellington Tel: +64 9 574 1744SG – Singapore Tel: +65 6887 6300TH – Thailand, Bangkok Tel: +662 186 7000TW – Taiwan, New Taipei City Tel: +886 2 2298 8987VN – Vietnam, Ho Chi Minh City Tel: +84 8 3999 1600South AmericaAR – Argentina, Buenos Aires Tel: +54 3327 44 4129BR – Brazil, Cachoeirinha RS Tel: +55 51 3470 9144CL – Chile, Santiago Tel: +56 2 623 1216MX – Mexico, Toluca Tel: +52 72 2275 4200© 2010-2015 Parker Hannifin Corporation. All rights reserved.Bulletin HY33-8368/UK. POD 08/2015 EMDC。
计算机硬件设计中的性能调试与优化方法
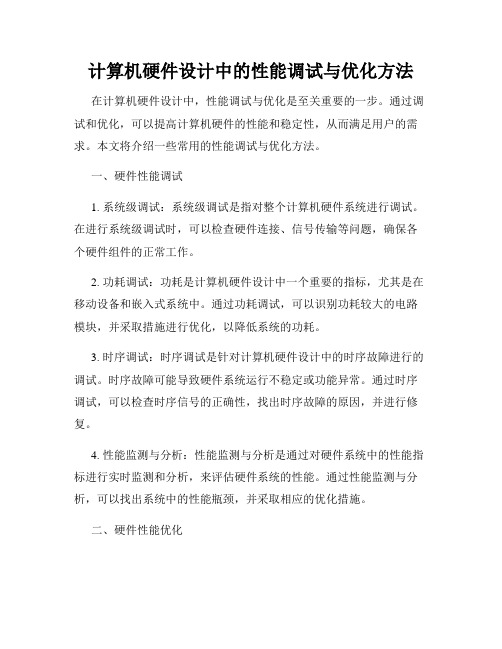
计算机硬件设计中的性能调试与优化方法在计算机硬件设计中,性能调试与优化是至关重要的一步。
通过调试和优化,可以提高计算机硬件的性能和稳定性,从而满足用户的需求。
本文将介绍一些常用的性能调试与优化方法。
一、硬件性能调试1. 系统级调试:系统级调试是指对整个计算机硬件系统进行调试。
在进行系统级调试时,可以检查硬件连接、信号传输等问题,确保各个硬件组件的正常工作。
2. 功耗调试:功耗是计算机硬件设计中一个重要的指标,尤其是在移动设备和嵌入式系统中。
通过功耗调试,可以识别功耗较大的电路模块,并采取措施进行优化,以降低系统的功耗。
3. 时序调试:时序调试是针对计算机硬件设计中的时序故障进行的调试。
时序故障可能导致硬件系统运行不稳定或功能异常。
通过时序调试,可以检查时序信号的正确性,找出时序故障的原因,并进行修复。
4. 性能监测与分析:性能监测与分析是通过对硬件系统中的性能指标进行实时监测和分析,来评估硬件系统的性能。
通过性能监测与分析,可以找出系统中的性能瓶颈,并采取相应的优化措施。
二、硬件性能优化1. 电路优化:电路优化是指对硬件电路进行设计和改进,以提高硬件系统的性能。
通过选择合适的电路元件,调整电路布局和连接方式,可以改善电路的工作性能。
2. 时序优化:时序优化是针对计算机硬件设计中的时序问题进行的优化。
通过对时序逻辑的优化,可以减少时序延迟,提高硬件系统的工作速度和稳定性。
3. 并行计算优化:并行计算优化是指通过合理设计和配置硬件系统中的并行计算单元,以提高硬件系统的并行计算能力。
通过并行计算优化,可以加快计算速度,提高系统的运行效率。
4. 存储器优化:存储器优化是指对硬件系统中的存储器进行优化,以提高存储器的访问速度和容量。
通过合理设计存储器的结构和访问方式,可以改善系统的性能和响应速度。
5. 算法优化:算法优化是指通过改进算法的设计和实现方式,以提高硬件系统的性能。
通过使用更加高效的算法,可以减少计算的复杂度,提高系统的运行效率。
电脑硬件高级调试技巧
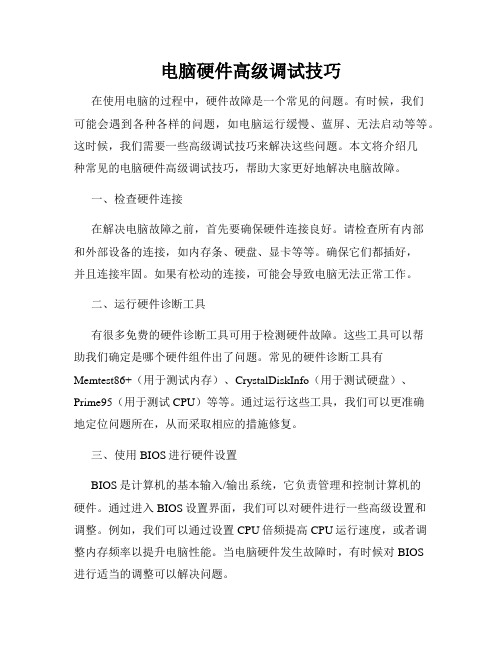
电脑硬件高级调试技巧在使用电脑的过程中,硬件故障是一个常见的问题。
有时候,我们可能会遇到各种各样的问题,如电脑运行缓慢、蓝屏、无法启动等等。
这时候,我们需要一些高级调试技巧来解决这些问题。
本文将介绍几种常见的电脑硬件高级调试技巧,帮助大家更好地解决电脑故障。
一、检查硬件连接在解决电脑故障之前,首先要确保硬件连接良好。
请检查所有内部和外部设备的连接,如内存条、硬盘、显卡等等。
确保它们都插好,并且连接牢固。
如果有松动的连接,可能会导致电脑无法正常工作。
二、运行硬件诊断工具有很多免费的硬件诊断工具可用于检测硬件故障。
这些工具可以帮助我们确定是哪个硬件组件出了问题。
常见的硬件诊断工具有Memtest86+(用于测试内存)、CrystalDiskInfo(用于测试硬盘)、Prime95(用于测试CPU)等等。
通过运行这些工具,我们可以更准确地定位问题所在,从而采取相应的措施修复。
三、使用BIOS进行硬件设置BIOS是计算机的基本输入/输出系统,它负责管理和控制计算机的硬件。
通过进入BIOS设置界面,我们可以对硬件进行一些高级设置和调整。
例如,我们可以通过设置CPU倍频提高CPU运行速度,或者调整内存频率以提升电脑性能。
当电脑硬件发生故障时,有时候对BIOS进行适当的调整可以解决问题。
四、查看系统事件日志Windows系统的事件日志记录了关于硬件和软件故障的信息。
当我们遇到电脑问题时,查看事件日志可以帮助我们找出问题所在。
通过打开“事件查看器”,我们可以查看不同类型的事件,如硬件错误、系统故障等等。
在事件日志中,我们可以找到一些有用的提示,帮助我们解决电脑故障。
五、更新和管理驱动程序驱动程序是连接硬件和操作系统的桥梁。
如果驱动程序过时或者损坏,可能会导致硬件无法正常工作或者出现其他问题。
因此,及时更新和管理驱动程序是非常重要的。
我们可以通过访问硬件制造商的官方网站来获取最新的驱动程序,并按照说明进行安装和更新。
解析电脑显卡的像稳定和防撕裂技术
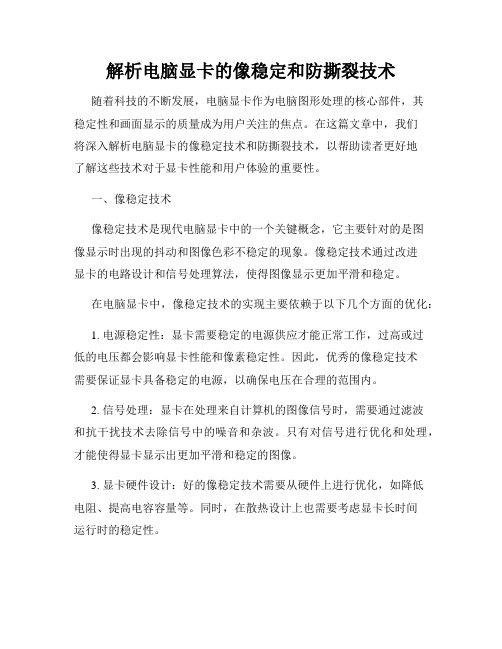
解析电脑显卡的像稳定和防撕裂技术随着科技的不断发展,电脑显卡作为电脑图形处理的核心部件,其稳定性和画面显示的质量成为用户关注的焦点。
在这篇文章中,我们将深入解析电脑显卡的像稳定技术和防撕裂技术,以帮助读者更好地了解这些技术对于显卡性能和用户体验的重要性。
一、像稳定技术像稳定技术是现代电脑显卡中的一个关键概念,它主要针对的是图像显示时出现的抖动和图像色彩不稳定的现象。
像稳定技术通过改进显卡的电路设计和信号处理算法,使得图像显示更加平滑和稳定。
在电脑显卡中,像稳定技术的实现主要依赖于以下几个方面的优化:1. 电源稳定性:显卡需要稳定的电源供应才能正常工作,过高或过低的电压都会影响显卡性能和像素稳定性。
因此,优秀的像稳定技术需要保证显卡具备稳定的电源,以确保电压在合理的范围内。
2. 信号处理:显卡在处理来自计算机的图像信号时,需要通过滤波和抗干扰技术去除信号中的噪音和杂波。
只有对信号进行优化和处理,才能使得显卡显示出更加平滑和稳定的图像。
3. 显卡硬件设计:好的像稳定技术需要从硬件上进行优化,如降低电阻、提高电容容量等。
同时,在散热设计上也需要考虑显卡长时间运行时的稳定性。
总之,像稳定技术对于电脑显卡来说非常重要,它能够提高图像显示的质量,保证用户在游戏或者图形处理时的视觉体验。
二、防撕裂技术防撕裂技术是为了解决显示器刷新率与显卡输出帧率不匹配导致的图像撕裂问题。
在高性能显卡和高刷新率显示器的应用中,由于显卡输出的帧率与显示器的刷新率不同步,会导致图像在水平方向上出现一条或多条不连贯的线条,影响用户的视觉体验。
为了解决这个问题,防撕裂技术应运而生。
主要有以下几种技术实现:1. VSync(垂直同步):VSync技术是一种软件算法,通过使显卡输出帧率与显示器的刷新率保持同步,消除图像撕裂现象。
然而,由于VSync会带来显示延迟,因此在某些对实时性要求较高的场景中并不适用。
2. Adaptive Sync:Adaptive Sync技术是一种硬件和软件结合的技术,它可以根据显卡的输出来动态调整显示器的刷新率,以匹配显卡的帧率,有效地消除图像撕裂。
电脑硬件高级调试
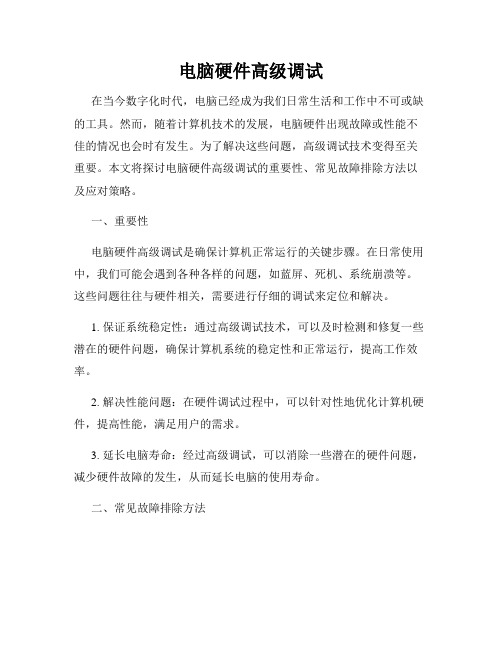
电脑硬件高级调试在当今数字化时代,电脑已经成为我们日常生活和工作中不可或缺的工具。
然而,随着计算机技术的发展,电脑硬件出现故障或性能不佳的情况也会时有发生。
为了解决这些问题,高级调试技术变得至关重要。
本文将探讨电脑硬件高级调试的重要性、常见故障排除方法以及应对策略。
一、重要性电脑硬件高级调试是确保计算机正常运行的关键步骤。
在日常使用中,我们可能会遇到各种各样的问题,如蓝屏、死机、系统崩溃等。
这些问题往往与硬件相关,需要进行仔细的调试来定位和解决。
1. 保证系统稳定性:通过高级调试技术,可以及时检测和修复一些潜在的硬件问题,确保计算机系统的稳定性和正常运行,提高工作效率。
2. 解决性能问题:在硬件调试过程中,可以针对性地优化计算机硬件,提高性能,满足用户的需求。
3. 延长电脑寿命:经过高级调试,可以消除一些潜在的硬件问题,减少硬件故障的发生,从而延长电脑的使用寿命。
二、常见故障排除方法1. 检查硬件设备:首先,需要检查电脑硬件设备是否连接正常,包括电源、内存、硬盘、显卡等。
如果有松动或损坏的情况,应及时修复或更换。
2. 使用硬件诊断工具:借助专业的硬件诊断工具,可以对硬件进行全面的检测,发现可能存在的问题并进行修复。
这些工具能够提供详细的硬件信息,帮助用户更好地了解电脑的状况。
3. 更新驱动程序:驱动程序的更新对于解决硬件问题非常重要。
及时更新最新的驱动程序,可以修复已知的硬件故障,并优化硬件性能。
4. 清理内部灰尘:长时间使用的电脑容易积累灰尘,这些灰尘会影响硬件的散热和运行,导致性能下降或者故障。
定期清理内部灰尘,可以保持电脑良好的工作状态。
三、应对策略1. 寻求专业帮助:如果遇到较为复杂的硬件故障,如主板或处理器故障,建议寻求专业的技术支持或找到经验丰富的技术人员进行修复。
2. 数据备份:在进行高级调试之前,应当先进行数据备份,以防数据丢失或硬件故障导致数据无法恢复。
3. 学习自助修复技巧:掌握一些常用的自助修复技巧,如重装操作系统、重装驱动程序等,可以在遇到简单问题时自行解决,提高效率。
HP Business Desktop Hard Drive SMART IV技术概述说明书
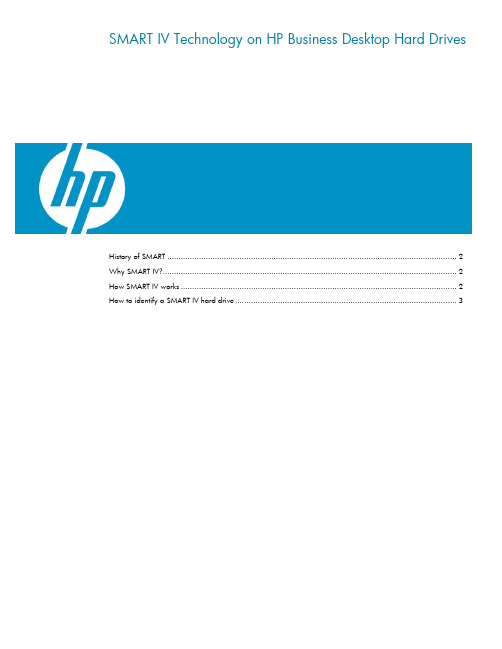
SMART IV Technology on HP Business Desktop Hard DrivesHistory of SMART (2)Why SMART IV? (2)How SMART IV works (2)How to identify a SMART IV hard drive (3)History of SMARTFor the past several years, hard drives have incorporated a feature known as Self-Monitoring Analysis and Reporting Technology (SMART). The advantage of SMART technology is that it provides an early warning system of imminent hard drive failure so that the drive can be replaced before it actually fails. Hard drives equipped with SMART technology automatically monitor certain key parameters for potential drive failure without affecting hard drive performance. If an error is detected, a failure message is displayed on the user’s screen.There are several iterations, or versions of SMART:•SMART: Originally named Drive Failure Prediction (DFP) and invented by Compaq Computer Corporation in 1995, SMART tracks certain drive attributes and parameters during drive activity. If any of these parameters being monitored by the drive exceed certain defined limits, an imminent hard drive failure message is displayed to the user by the BIOS or Client Management Software. •SMART II: Improves upon the reliability of the original SMART technology by adding the capability to use “off-line data collection” to check the hard drive health even during periods of inactivity. •SMART III: Supports SMART I and II. With SMART III, the hard drive does a complete media self-scan every 60 hours. Any questionable sectors can be either validated or remapped. The latest implementation of SMART III includes enforcement of coverage even during heavy-duty cycle usage of the drive.Why SMART IV?Starting in late 2007, new HP business desktops and Workstations will begin incorporating SMART IV technology in hard drives. While the current versions of SMART do a good job monitoring the data on the hard drive media, the ever increasing emphasis on reliability and quality led Hewlett-Packard and hard drive manufacturers to better ensure that the data flow from host interface to media and media to host interface is not compromised. This is done by adding a parity code to every 512 byte block in the data path of the hard drive's Cache RAM. This parity checking, which is called SMART IV by HP, provides more complete error detection coverage of the entire data path between the host and the hard drive. In the hard drive industry, SMART IV is also known as End-to-End Error Detection.How SMART IV works•SMART IV uses a 2 byte parity code to enable it to better detect if data is valid during transfers to and from the data buffer of the hard drive. If the parity data does not match after transferring through the cache RAM data buffer, then depending upon the command, the drive can do abackground retry to get data again or report the error message to the host.•During a disk read, a 2 byte parity code is generated after the data is transferred from the disk.After transfer from the data buffer to the drive interface, the parity data is checked (see Figure 1). •During a disk write, a 2 byte parity code is generated and appended to the data going into the data buffer. The parity code is checked before it goes into the data buffer and before it is written to the disk (see Figure 2).•If an error is detected by the drive and the data cannot be retrieved or sent without failure, a protocol is in place to notify the host operating system of the error. The host operating system can then decide to resend the command or notify the user that a data error may have occurred.•If errors are detected, a SMART attribute called End-to-End Error Detection Count is updated. If the SMART threshold is crossed, an imminent failure error message is reported to the user eitherthrough Client Management Software that has been installed in the operating system or by the HP BIOS on the next reboot. Since all HP BIOS issue the SMART status command, no additionalsoftware is required.How to identify a SMART IV hard driveOpen the Computer Setup (F10) utility in the system BIOS to determine if the system has a SMART IV hard drive.1.Turn on the computer and press the F10 key during boot to access the Computer Setup utility.2.In Computer Setup, select “Device Configuration” from the “Storage” menu. If the hard drivesupports SMART IV technology it will be identified as SMART IV in the description. If the hard drive supports SMART III technology it will be identified as SMART III in the description. Older hard drives prior to SMART III technology will not reference SMART in the description, but all shipping HP business desktop hard drives support prior versions of SMART.3.Select “Ignore Changes and Exit” from the “File” menu to exit Computer Setup.Note:If the drive indicates SMART IV support, it also supports SMART III.© 2007 Hewlett-Packard Development Company, L.P. The information contained herein is subject to change without notice. The only warranties for HP products and services are set forth in the express warranty statements accompanying such products and services. Nothing herein should be construed as constituting an additional warranty. HP shall not be liable for technical or editorial errors or omissions contained herein.Microsoft, Windows, and Windows Vista are either trademarks or registeredtrademarks of Microsoft Corporation in the United States and/or other countries. 458436-001, August 2007。
- 1、下载文档前请自行甄别文档内容的完整性,平台不提供额外的编辑、内容补充、找答案等附加服务。
- 2、"仅部分预览"的文档,不可在线预览部分如存在完整性等问题,可反馈申请退款(可完整预览的文档不适用该条件!)。
- 3、如文档侵犯您的权益,请联系客服反馈,我们会尽快为您处理(人工客服工作时间:9:00-18:30)。
Hardware Support for Flexible Distributed Shared MemorySteven K. Reinhardt,1 Robert W. Pfile,2 and David A. Wood3AbstractWorkstation-based parallel systems are attractive due to their low cost and competitive uniprocessor performance. However, supporting a cache-coherent global address space on these systems involves signifi-cant overheads. We examine two approaches to coping with these overheads. First, DSM-specific hardware can be added to the off-the-shelf component base to reduce overheads. Second, application-specific coher-ence protocols can avoid some overheads by exploiting programmer (or compiler) knowledge of an applica-tion’s communication patterns. To explore the interaction between these approaches, we simulated four designs that add DSM acceleration hardware to a collection of off-the-shelf workstation nodes. Three of the designs support user-level software coherence protocols, enabling application-specific protocol optimiza-tions. To verify the feasibility of our hardware approach, we constructed a prototype of the simplest design.Measured speedups from the prototype match simulation results closely.We find that even with aggressive DSM hardware support, custom protocols can provide significant speedups for some applications. In addition, the custom protocols are generally effective at reducing the impact of other overheads, including those due to less aggressive hardware support and larger network laten-cies. However, for three of our benchmarks, the additional hardware acceleration provided by our most aggressive design avoids the need to develop more efficient custom protocols.Index terms:parallel systems, distributed shared memory, cache coherence protocols, fine-grain cache coher-ence, coherence protocol optimization, workstation clusters.1 IntroductionTechnological and economic trends make it increasingly cost-effective to assemble distributed-memory parallel systems from off-the-shelf workstations and networks [3]. Workstations (or, equivalently, high-end personal computers) use the same high-performance microprocessors found in larger systems—but at a far lower cost per processor, thanks to their much greater market volume. More recently, vendors have begun to advertise high-bandwidth, low-latency switched networks targeted specifically at the cluster market. We expect this trend to continue and for the bandwidth and latency characteristics of cluster networks to approach those of dedicated parallel system interconnects [8, 19].In spite of these trends, custom parallel systems still hold an advantage over off-the-shelf clus-ters of workstations in their ability to provide a low-overhead, globally coherent shared address space. Custom-built distributed shared memory (DSM) systems such as MIT’s Alewife [2], Stan-1. EECS Dept., The University of Michigan, 1301 Beal Ave., Ann Arbor, MI 48109-2122. stever@.2. Yago Systems, 795 Vaqueros Ave., Sunnyvale, CA 94086. pfile@.3. CS Dept., University of Wisconsin–Madison, 1210 W. Dayton St., Madison, WI 53706-1685. david@. Copyright © 1998 IEEE. Published in IEEE Transactions on Computers, vol. 47, no. 10, Oct. 1998. Personal use of this material is permitted.ford’s FLASH [28], and the SGI Origin 2000 [30] integrate the memory and network control and datapaths at each processor–memory node, providing efficient coordination among processor requests, network messages, and DRAM accesses. In contrast, machines assembled from off-the-shelf workstations—even those that add custom hardware to accelerate DSM operations—must build on top of the workstations’ existing memory systems. Nodes attach to the network via adapters that act as pseudo-processors or peripheral devices, as shown in Figure 1, forcing local and remote memory accesses to contend for memory bus bandwidth. These constraints increase the run-time overhead of providing a shared address space relative to a fully custom design.We have explored two approaches to coping with the overheads of workstation-based DSM systems: DSM-specific hardware support and application-specific protocol optimizations. Adding DSM-specific hardware to off-the-shelf components reduces overheads by accelerating common operations. This approach increases performance at the expense of additional hardware design and manufacturing costs. Protocol optimizations avoid overheads by exploiting programmer or compiler knowledge of an application’s communication patterns. For example, moving data pro-actively from producers to consumers both hides the latency of the data transfer and eliminates the overhead of handling the demand misses that would otherwise occur. This approach trades programmer effort for increased performance.This paper discusses both options, focusing on the interaction between them. Can we build hardware that accelerates DSM performance yet provides flexibility to optimize communication?To what extent does hardware support make protocol optimizations unnecessary, and vice versa?We examine these questions in the context of Tempest [44], an interface that lets user-levelNode N-1Node 0Figure 1. Workstation-based DSM system organization.(unprivileged) software manage coherence at a fine granularity within a distributed shared address space. By default, applications use a standard software protocol that provides sequentially consistent shared memory, the consistency model generally preferred by most programmers for its simplicity [24]. However, for performance-critical data structures and execution phases, this default protocol may be replaced with arbitrary, potentially application-specific custom protocols, much like an expert programmer might recode a small performance-critical function in assembly language.1 Although there are many approaches to optimizing shared-memory communication, Tempest uniquely allows programmers and compilers to adapt or reimplement the shared-memory abstraction to match a specific data structure or sharing pattern. This flexibility gives direct mes-sage-level control over communication without abandoning traditional shared-memory features such as pointer-based data structures and dynamic, transparent data replication.Three Tempest-compatible system designs—Typhoon, Typhoon-1, and Typhoon-0—demon-strate one general approach to adding flexible DSM hardware to a cluster of workstations. These designs use logically similar components, but differ in the extent to which these components are integrated and customized for DSM operations. Using simulation, we compare the performance of both standard and custom-protocol versions of our benchmarks on these systems against a baseline hardware-supported DSM design (similar to Simple COMA [21]) that does not allow user protocol customization. While custom protocols provide less relative improvement over stan-dard shared memory on more aggressive hardware, two benchmarks still show dramatic gains—86% and 384%—on the most aggressive Tempest system (Typhoon), outperforming the Simple COMA system by nearly the same amount. Custom protocols also effectively hide the higher overheads of less aggressive hardware; they decrease the performance gap between Typhoon-1 and Typhoon from 222% to 11% and the gap between Typhoon-0 and Typhoon from 427% to 22%. We expand on previous results [44, 45] by examining the effect of network latency and pro-tocol-processor speed; we find that custom protocols are generally effective at reducing perfor-1. Similarly, just as past improvements in compiler technology have reduced the need to code in assembly language for performance, we hope that future compilers will target Tempest to provide similar levels of optimization without expert programmer involvement [11].mance sensitivity to these parameters as well. However, Typhoon executes the standard versions of three of our benchmarks nearly as quickly as the custom-protocol versions, and faster than the custom-protocol versions on the less aggressive systems. In these cases, the additional hardware acceleration avoids the need to develop more efficient custom protocols.To demonstrate the feasibility of our designs, we built a prototype of the simplest system (Typhoon-0). We describe this prototype briefly and report performance measurements. Simula-tion results match measured prototype speedups within 6%.The remainder of the paper is organized as follows. The next section reviews the Tempest model for fine-grain distributed shared memory, then discusses the benchmarks used in this study and the protocol optimizations that were applied to improve their performance. Section3 describes the three Tempest designs, while Section4 reports on their simulated performance. Section5 reports on the Typhoon-0 prototype. Section6 discusses related work, and Section7 summarizes our conclusions and indicates directions for future work.2 The Tempest interfaceThe Tempest interface provides a set of primitive mechanisms that allow user-level software—e.g., compilers and programmers—to construct coherent shared address spaces on distributed-memory systems [44]. Tempest’s flexibility derives from its separation of system-provided mech-anisms from user-provided coherence policies (protocols). Tempest also provides portability by presenting mechanisms in an implementation-independent fashion. This work exploits Tempest’s portability by using optimized applications originally developed for an all-software implementa-tion on a generic message-passing machine [50] to compare the performance of three different hardware-accelerated platforms.Tempest provides four mechanisms—two types of messaging (active messages and virtual channels), virtual memory management, and fine-grain memory access control—to a set of con-ventional processes, one per processor–memory node, executing a common program text. Tem-pest’s active messages, derived from the Berkeley model [55], allow the sender to specify a handler function that executes on arrival at the destination node. This user-supplied handler con-sumes the message’s data—e.g., by depositing it in memory—and (if necessary) signals its arrival. Virtual channels implement memory-to-memory communication, potentially providing higher bandwidth for longer messages. Virtual memory management allows users to manage a portion of their virtual address space on each node. Users achieve global shared addressing by mapping the same virtual page into physical memory on multiple nodes, much like conventional shared virtual memory systems [32]. Fine-grain memory access control helps maintain coherence between these multiple copies by allowing users to tag small (e.g., 32-byte), aligned memory blocks as Invalid, ReadOnly, or Writable. Any memory access that conflicts with the referenced block’s tag—i.e., any access to an Invalid block or a store to a ReadOnly block—suspends the com-putation and invokes a user-level handler function. Users may specify different sets of handlers for different virtual memory pages; thus multiple protocols may coexist peacefully, each manag-ing a distinct set of shared pages. A complete specification of Tempest is available in a technical report [40].2.1 Standard shared memory using TempestTempest’s mechanisms are sufficient to develop protocol software that transparently supports standard shared-memory applications. Stache, the default Tempest protocol included with the standard Tempest run-time library, is an example of such a protocol. The Stache library includes a memory allocation function, a page fault handler, and a set of access fault and active message handlers.The memory allocation function, called directly by the application, allocates shared pages in the user-managed portion of the virtual address space. Stache assigns each page to a home node, which provides physical memory for the page’s primary copy and manages coherence for the page’s blocks. Processors on the home node access the primary copy directly via the global virtual address. Applications can specify a page’s home node explicitly or use a round-robin or first-touch policy. For benchmarks that have an explicit serial initialization phase, the first-touch pol-icy migrates the page to the node that first references it during the parallel phase [33].Non-home nodes allocate memory for shared pages on demand via the page fault handler. Ini-tially, these pages contain no valid data, so all their blocks are tagged Invalid. A reference to one of these Invalid blocks invokes an access fault handler that sends an active message requesting the block’s data to the home node. The message handler on the home node performs any necessary protocol actions, then responds with the data. Finally, the response message’s handler on the requesting node writes the data into the stache page, modifies the access tag, and resumes the local computation.The Stache handlers maintain a sequentially consistent shared-memory model using a single-writer invalidation-based full-map protocol. A compile-time parameter sets the coherence granu-larity, which can be any power-of-two multiple of the target platform’s access control block size. In practice, we maintain several precompiled versions of the Stache library supporting a range of block sizes.2.2 Optimizing communication using TempestThe Stache protocol effectively supports applications written to a standard, sequentially consis-tent shared-memory programming model. However, the real power of Tempest lies in the oppor-tunity to optimize performance using customized coherence protocols tailored to specific data structures and specific phases within an application. Tempest also aids the optimization process itself by enabling extended coherence protocols that collect profiling information [34, 57]. This information drives high-level tools that help programmers identify and understand performance bottlenecks that may benefit from custom protocols. Unlike systems that provide relaxed memory consistency models [1, 18], the effects of these custom protocols are limited to programmer-spec-ified memory regions and execution phases; the remainder of the program sees a conventional sequentially consistent shared memory.At its simplest, Tempest’s flexibility lets users select from a menu of available shared-memory protocols, as in Munin [10]. Programmers or compilers can further optimize performance by developing custom, application-specific protocols that optimize coherence traffic based on knowledge of an application’s synchronization and sharing patterns. For example, a programmer might exploit a producer-consumer pattern in some inner loop, employing a protocol that batchesthe producer’s updates into highly efficient bulk messages. Such protocols can often use applica-tion-specific knowledge to identify updated values without run-time overhead. This optimization does not change the shared-memory view of the data, but only the manner in which the producer and consumer copies are kept coherent. Thus, custom protocols typically do not require non-triv-ial modification of the original shared-memory source code. The custom protocols themselves currently require significant development effort; however, we seek to remedy this situation through software reuse, high-level tools for protocol development [12], and automatic compiler application of optimized protocols [11].Although Tempest custom protocols use message passing to communicate between nodes, they directly support the higher-level shared-memory abstraction. In contrast, other systems that seek to integrate message passing and shared memory treat user-level message passing as a comple-mentary alternative to—rather than a fundamental building block for—shared-memory communi-cation [22, 27, 56]. To optimize communication in these systems, critical portions of the program must be rewritten in a message-passing style. Of course, if desired, Tempest programmers can also dispense with shared memory and use messages directly—for example, to implement syn-chronization primitives.This section briefly describes the Tempest optimizations applied to six scientific benchmarks—Appbt, Barnes, DSMC, EM3D, moldyn, and unstructured—both to indicate typical optimizations and to provide background for following sections where these benchmarks are used to evaluate system designs. In each case, the programmer started with an optimized, standard shared-memory parallel program and further improved its communication behavior by developing custom proto-cols for critical data structures. Again, although these changes were performed manually at the lowest level, we expect future development tools to aid or automate this process. The original papers reporting on these optimizations (Falsafi et al. [16] for Appbt, Barnes, and EM3D, and Mukherjee et al. [37] for DSMC, moldyn, and unstructured) detail the applications and the evolu-tionary optimization process.Appbt is a computational fluid dynamics code from the NAS Parallel Benchmarks [4], parallel-ized by Burger and Mehta [9]. Each processor works on a subcube of a three-dimensional matrix, sharing values along the subcube faces with its neighbors. In the original version, processors spin on counters to determine when each column of a neighbor’s face is available, then fetch the data via demand misses. The Tempest-optimized version combines the communication and synchroni-zation for each column into a single producer-initiated message. Approximately 100 lines of code were added or modified, a small fraction of the roughly 7,000 lines in the original program. Most changes were repetitive replacements of synchronization statements. The custom protocol itself required about 750 lines of C.Barnes, from the SPLASH benchmark suite [51], simulates the evolution of an N-body gravita-tional system in discrete time steps. The primary data structure is an oct-tree whose interior nodes represent regions of three-dimensional space; the leaves are the bodies located in the region repre-sented by their parent node. Computation alternates between two phases: rebuilding the tree to reflect new body positions, and traversing the tree to calculate the forces on each body and update its position. The standard shared-memory version we use incorporates several optimizations not in the original SPLASH code [16]. The Tempest-optimized version splits the body structure into three parts and applies a different protocol to each: read-only fields (e.g., the body’s mass) use the default protocol, fields accessed only by the current owner use a custom migratory protocol, and the read-write position field uses a custom update protocol. Because the sharing pattern is dynamic, the updates are performed indirectly through the home node. Because the body data structure is split into multiple structures, source changes for Barnes were more widespread than for the other applications, making it difficult to quantify their scope.DSMC simulates colliding gas particles in a three-dimensional space. Each processor is respon-sible for the particles within a fixed region of space. When a particle moves between regions, the source processor writes the particle’s data into a buffer associated with the destination processor. Because the original version of the program performs well, we applied only one simple Tempest optimization: processors write particles into the destination processor’s buffer using explicit mes-sages instead of shared-memory writes. In addition to eliminating coherence overhead for thebuffers, the atomic message handlers allow nodes to issue their writes concurrently without barri-ers or locking. This optimization modified only two lines in the original program. The remote-write protocol requires approximately 150 lines of code.EM3D models electromagnetic wave propagation through three-dimensional objects by itera-tively updating the values at each node of a graph as a function of its neighbors’ values [13]. Each processor owns a contiguous subset of the graph nodes and updates only the nodes it owns. Where a graph edge connects nodes owned by different processors, each processor must fetch new values for the non-local nodes on every iteration. The standard shared memory version amortizes this overhead by placing multiple values in a cache block. This optimization modifies the graph node data structure, replacing the embedded value with a pointer into a packed value array. The Tem-pest version uses a custom deferred update protocol: each node sends all of the updated values required by a particular consumer in a single message over a virtual channel. The set of updates is static, but input dependent; the protocol determines the communication pattern by running a mod-ified version of the Stache protocol in the first iteration. Graph nodes are fetched on demand, but the protocol records the addresses and processors involved. The second and subsequent iterations use the optimized protocol. Interfacing this custom protocol to the original program changed five lines of code. The custom protocol itself comprises over 1,000 lines of C. However, this value overstates the protocol’s complexity somewhat; this code represents one of the earliest custom protocols, and was written without the aid of experience or protocol development tools.Moldyn models force interactions between molecules. There are two main computation steps: the first identifies molecule pairs that interact significantly, and the second iterates over these pairs to compute forces and update the involved molecules’ state. Most of the communication occurs in the second step, where each processor may generate a number of updates for a given molecule. The original version accumulates each processor’s updates in a local array, then merges the updates in a synchronous, pipelined reduction phase. The Tempest version takes this optimiza-tion to its logical conclusion, using virtual channels to move array sections from node to node. This optimization changes only one line of the original code. The protocol itself involves less than200 lines of C.Unstructured iterates over a static, input-dependent mesh to calculate forces on a rigid body. The code partitions the mesh nodes across the processors. Unlike EM3D, processors may update as well as examine the values of mesh nodes owned by other processors. As in moldyn, the origi-nal version accumulates each processor’s updates locally, then merges the updates via a separate reduction step. However, this reduction is less efficient than in moldyn because each processor updates a small fraction of the mesh nodes and each update involves only a small amount of com-putation. The custom protocol sets up virtual channels connecting processors that share edges and sends updates across these channels. Each processor then performs the reduction for its nodes locally. This optimization added five lines in the body of the program. The reduction protocol involves just over six hundred lines of C. A second custom protocol, similar to the one used in EM3D, propagates new node values from the owner to the referencing processors. This optimiza-tion modified 12 lines in the body of the program. The protocol itself is less than 600 lines of C.2.3 SummaryBy allowing user-level software to manage coherence, Tempest enables aggressive communi-cation optimization within a shared address space. These optimizations typically require very few changes to the body of the application, because shared global data structures—for example, the pointer-based graph in EM3D—can be left intact.1Unfortunately, the optimizations described here involved significant protocol development effort. We believe that the magnitude of these efforts is due to our lack of experience and the intentionally low level of the Tempest interface, and will be dramatically reduced through software reuse, protocol development tools [12], and compiler support for protocol generation and selection [5, 11, 15]. Nevertheless, because Tempest enables a nearly unlimited spectrum of communication optimizations, it provides a good environ-ment for investigating the interaction of these optimizations with hardware support.3 Hardware support for TempestTo examine the impact of hardware support on both standard and Tempest-optimized shared-1. The leaf structure in Barnes is a notable exception, where the desire to apply different protocols to the structure’s fields conflicts with Tempest’s page-granularity protocol binding.memory applications, we compare the performance of three system designs that add varying lev-els of hardware acceleration to a cluster of workstations. This section describes these three sys-tems briefly. The following section (Section4) analyzes the simulated execution of the benchmarks of Section2.2 on these systems.The three systems we study—Typhoon, Typhoon-1, and Typhoon-0—share the organization depicted in Figure1. The DSM support hardware, represented by the “cloud” in Figure1, consists of three components: logic implementing Tempest’s fine-grain access control, a network inter-face, and a processor to execute protocol code (message and access fault handlers). Tempest’s vir-tual memory management is supported by address translation hardware on the main CPU.All three systems use a custom device at each node to implement some of these components; they differ in the number of components integrated into this device, as depicted by the shaded rectangles in Figure2. Components not included in the custom device are implemented using off-the-shelf parts. These different integration strategies represent different trade-offs between perfor-mance and hardware design simplicity. Integrating a component into a custom device increases the device’s design time and design and manufacturing costs.1 However, separating components into discrete devices significantly increases the overhead of communicating between them. Typhoon provides the highest performance—at the highest cost—by integrating all three compo-nents on a single custom device.2 Typhoon-1 replaces Typhoon’s integrated processor with an off-the-shelf CPU, leaving the network interface and access control logic together in custom hard-ware. Typhoon-0 achieves the simplest design by splitting all three components across separate devices, two of which—the protocol processor and the network interface—can be purchased off the shelf. A relatively simple access control device is Typhoon-0’s only custom component. Typhoon-0’s simplicity allowed us to construct a prototype implementation, which we report on in Section5.1. In sufficient volume, the increase in the custom component’s cost may be offset by the system-level reduction in package count and board space.2. Our focus on workstation-based systems precludes integrating components, such as the memory controller, that are already an integral part of the base workstation system.The rest of this section describes the systems more fully. The first subsection covers common features; following subsections describe Typhoon, Typhoon-1, and Typhoon-0 in turn. Additional details can be found in previous publications [41, 44, 45].3.1 Common featuresTo focus on the impact of the organizational differences in our designs, we assume similar tech-nology for the three common components—the protocol processor, network interface, and access control logic.The protocol processor is a general-purpose CPU. For convenience, the protocol processor uses the same instruction set as the primary (computation) processor. User-level protocol software run-ning on the processor communicates directly with the access control logic and network interface via memory-mapped registers.The network interface is a pair of memory-mapped hardware queues, one in each direction.Sending a message requires writing a header word indicating the destination node and message length, followed by the message data, into the send queue. A message is received by reading words out of the receive queue. A separate signal indicates when a message is waiting at the head of the receive queue. Credit-based flow control prevents deadlock on the hardware queues. To relieve protocol software from dealing with flow control, the run-time library buffers messages in main memory when the network overflows.Tempest’s active messages map directly to the interface: the first word of each message is used for the receive handler’s program counter, and the handler reads the remainder of the message from the hardware queue. The messaging library implements Tempest’s virtual channels in aTyphoonTyphoon-1Typhoon-0Figure 2. Component integration diagram.protocolprocessornetworkinterface access control。