推荐 QCC改善报告之降低整机不良率(经典) 精品
QCC改善报告[1]
![QCC改善报告[1]](https://img.taocdn.com/s3/m/4becda5f1fb91a37f111f18583d049649b660eb3.png)
長期目標: 小於 0.483
QCC改善报告[1]
三、活動計劃制定-2
3.2、XXX圈QCC活動計劃表
QCC改善报告[1]
四、特性要因分析(人力工時成本高)
法
人
培訓時間過短
作業手法錯誤
作業熟練度不夠
物料放置
重複作業
作業方法
實作經驗不足
順序錯誤
組裝先後
不正確
重複動作疲勞 作業員心
為
作業時還手頻繁
S/T 115.0 301.5 579.0 87.1
Total Cost 0.0794 0.2081 0.3996 0.0601 0.1650 0.9121
工時成本以每小時$ 2.4845計算,即80NTD,匯率32.2。
QCC改善报告[1]
二、主題選定-2
2.2 、選定理由:
1.S4客戶的 Rockit 系列產品屬於通訊事業處在昆山廠的投入的產品. 2.該機種目標人力工時成本成本為$0.0.483,爾目前為$0.9121 3.在作業程中,存在大量的手動作業,作業強度大, 且一致性較差,品質無 法保證. 4. 測試時間過長, 存在重複不必要測試項目, SFC程式和打印條碼程式 分立同一站需要多次重複掃描同樣SN. 5.提高制程自動化程度,減少人力成本, 簡化測試程式,可以為後續的新 機種導入積累一定的經驗,提前將此類問題消除在萌芽狀態.
1
Remove HDD Device
5
F3 Total
30
3 Test Stations, manpower *3 , Cycle time is 35 S 2 Test Stations, manpower *2 ,cycle time is 35
降低整机生产不良率QCC

降低整机生产不良率QCC1. 引言在整机生产过程中,不良率是一个重要的指标,直接影响产品质量和生产效率。
因此,采取一系列的质量控制措施是至关重要的。
本文将介绍一种质量控制方法,即QCC(Quality Control Circle),旨在帮助企业降低整机生产不良率。
2. QCC概述QCC是一种以小组为单位的员工参与的质量管理方法。
通过成立质量控制小组,通过小组成员的参与和协作,发现并解决生产过程中的问题,从而降低产品不良率。
QCC的核心思想是追求持续改进和全员参与,提高整体生产质量。
3. QCC的实施步骤3.1 小组成立首先,需要成立一个质量控制小组。
小组成员应涵盖生产线上的各个关键环节,包括工人、质检员、技术人员等,并确保小组成员具备相应的培训和技能。
3.2 问题识别与数据收集小组成员应该定期收集和分析整机生产过程中出现的问题和缺陷。
通过数据分析,找出生产过程中存在的主要问题和症结所在。
3.3 问题分析和改进方案制定小组成员应对收集到的问题进行分析,并制定相应的改进方案。
在制定改进方案时,应充分考虑实际操作情况、工艺流程和设备条件等因素。
3.4 实施改进方案小组成员应积极实施制定的改进方案,并跟踪记录改进效果。
在实施改进方案时,需要保持团队合作和沟通,确保改进措施得到有效执行。
3.5 持续改进QCC是一个连续的过程,小组成员应定期评估改进效果,并根据评估结果进行调整和改进。
通过持续改进,不断提高整机生产的质量水平。
4. QCC的优势4.1 全员参与QCC鼓励全员参与,通过集思广益,充分发挥员工的智慧和创造力,能够更全面地发现和解决问题。
此外,全员参与还能增强员工的责任感和归属感,提高整体生产效率。
4.2 快速改进QCC的小组成员具有多种技能和经验,能够快速分析问题并制定相应的改进方案。
由于小组成员紧密合作,能够及时进行实施和跟踪,实现快速改进。
4.3 持续改进QCC强调持续改进的理念,小组成员不断评估和调整改进方案,通过不断地优化和改进,提高整体生产质量。
QCC降低设备故障率

目的和意义
目的
通过实施QCC活动,降低设备故障率,提高生产效率和产品质量,实现企业可 持续发展。
意义
降低设备故障率有助于提高企业的生产效益和竞争力,同时能够减少维修和停 机时间,降低生产成本。此外,QCC活动还有助于培养员工的团队协作和持续 改进意识,促进企业文化的建设。
02 QCC(质量控制圈)介绍
01
QCC成员对设备进行定期检查,及时发现潜在的故障或问题,
确保设备正常运行。
故障诊断与修复
02
QCC成员具备一定程度的设备维修技能,能够快速诊断和修复设备故障,减少停机来自间。预防性维护03
通过分析设备运行数据和故障模式,QCC制定相应的维护计划,
降低设备故障率。
QCC的运作方式
制定计划
制定详细的实施计划,包括目 标、时间安排、人员分工等。
安全事故风险增加
设备故障可能引发安全事 故,给企业员工和财产带 来威胁。
04 QCC降低设备故障率的实 施方案
确定问题并提出解决方案
确定设备故障率高的原因
通过数据收集和分析,确定导致设备故障的主要原因,如设 备老化、操作不规范、维护不足等。
提出解决方案
针对确定的问题,制定相应的解决方案,如更新设备、规范 操作流程、加强维护保养等。
设备故障率定义及影响
设备故障率定义
设备故障率是指设备在运行过程中出现故障的概率,通常以设备故障次数与设备 运行总时间的比值来计算。
设备故障率影响
设备故障率高会增加企业的维修成本、影响生产效率和产品质量,甚至可能引发 安全事故,给企业带来重大损失。
设备故障率高的原因分析
设备老化
设备长时间运行,缺乏必要的维护和保养,导致设备性能下降, 容易发生故障。
品质改善QCC活动成果报告案例
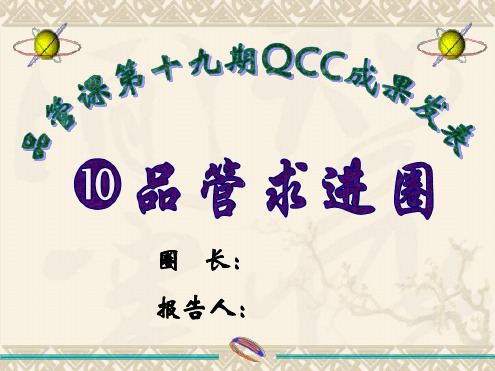
合计 18,247
100
分析:前二项不良率大于80%,故应作为改善重点,马上执行。
伍、现状调查三
(一)改善前数据收集, 5~6月份TR-377 绒布不良数统计 如下表:
收 集 人:张金枝
收集日期: 09.5~09.6
数据来源: 品质异常退料单 物品报废申请单
日期
项目不良数
5/1~5/205/21~6/106/11~6/3合0 计
Z
绒布表面皱折 裁片现场验证叠放层有皱折
要求生产单位设定叠放数15量0P为C,S
36 48 45 129 ○ 五
P
环境因素,风吹起绒布移位(贴生合产时线)机台周边以纸板围起防护
30 35 30 95 ○ 六
绒布毛向错误余料裁片时识别错误,无标识状12态..生 裁产剪线后悬余挂料毛毛向向标标示识绒后布裁样片板
对策实施:包装标准化. 责任人:刘财强 实施日期:09.7.16
舒服 多了!
PD
检讨与标准化:新包装4*4层为一板,另绒 A C 效果确认:从7/26日起所到货全部
布外加纸箱作为保护层.品保作为重点
由新包装纳入,经确认由叠压混放所造成
管控.
的皱折已全面消除.
厂商协谈记录
皱折没了, 漂亮多了!
拾、对策实施三
28 38 35 36 30 167 1
23 19 30 26 24 122 2
分 / 人 解决能力
急迫性 达成能力
圈员了解
评
1 需委外解决
价 方
2 需其它相关部门协助觖决
法
3 自行解决
普通 急
紧急
6~9 个月 3~6 个月 1~3 个月
0~50% 51~75% 76~100%
QCC改善报告
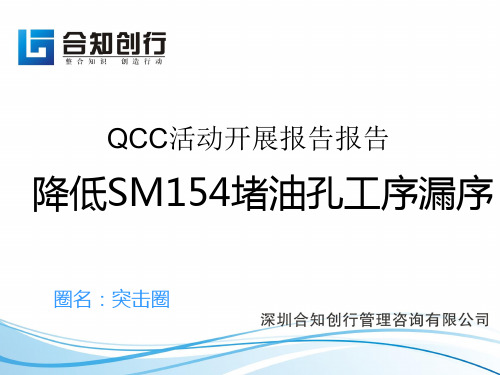
标准
加工前、加工 后标识区分明 确
验证 人
周世恩、 陈小娇
日期
13.8.17
标识不明确
加工状态标识 明确
现场多次抽样确认发现 ,员工在操作时,产品 加工前与加工后的产品 是按照规定区域隔离摆 放,并标识清楚。
Page
16
七、要因确认
7-4、底孔直径大
序 末端因素 确认内容 号
4
照片
姓名: 日期:
用激光感 应开关, 检查到自 动报警 设计一种专用的检查设备
九、对策制定
怎么才能不用 人来保证嘛? 不做就不用 人来保证!
九、对策制定
9-2、 正在讨论得热火朝天、百思不得其解的时候,有个 组员说:怎么才能不用人来保证嘛?不做这个工序就不用人 来保证!对于这一想法,大家心里都觉得滑稽可笑。但主持 人却打断大家的笑声道:我们为什么要堵这个孔?为什么要 钻这个孔?不钻这个孔可不可以? 马上与会的技术人员就进行了回复:钻这个孔的 目的是为了辅助加工斜油孔,在加工完斜油孔后再堵 上。理论上,如果能改变斜油孔的加工方式的话,可 以不用钻这个孔。
作业标准 执行困难
靠员工个 人意识无 法保证现 场质量
100%的 产品靠肉 眼检查, 视觉容易 疲劳
人存在生 理极限
Page
21
九、对策制定
9-1、根据要因制定详细的对策实施表:(5W1H)
序 号 要因 根本原因 对策
WHAT
目标
WHY
措施
H OW
实施 者
WHO
完成 日期
WHE N
1
作业标 准执行 困难
九、对策制定
9-3、 随即会议决定:改变斜油孔加工方式。技术 部立即与主机厂联系,改变斜油孔加工控制程序方案 。 主机厂回复同意该方案。
经典QCC改善报告

4 15000
3853 25.7%
5 15000
2782 18.5%
6 19000
2774 14.6%
7 12800
3660 28.6%
日期
8
9
14000 17400
2225 2490
15.9% 14.3%
11 25900
2334 9.0%
12 21900
3366 15.4%
13 平均不良率
23000
计划在三个月内(9.15-12.15)完成 !
消除三大不良:插板不过,绝缘体残屑,六片变形变曲!7
The first issue
插板不过和六片变形弯曲关系phase1-1
主体来料六片变形
主体来料六片弯曲
装配后保持变形或变曲, 出现
六片弯曲变形/插板不过
8
插板不过和六片变形弯曲鱼骨分析 phase1-1
人力资源
小计:704元+960元=1664元
3 QC筛选员外观检验 基本工资:32元/天×22天=704元;
QC 3人筛选全检
工时节约
加班费:8元/小时×120小时/月=960元 效率提高1/3倍
小计:704元+960元=1664元
5 每年成本节约
(180元+1664元×2)=42,096元
22
QCC第一阶段改善总结phase1
1.SQE/李广 2.IQC/何洪锋 3.SQE(李广)/ IQC(何洪锋)
对不同批次来料主体生产上线时,QC和生产线班长/组 长要关注刚生产时的产品,如有异常及时找生技解决,将 模具调到最佳位置
QC/黄祥成 装配/何春泽 生技/李跃
1.Φ5.13/ Φ 3.51复合检具,保证QC人员在检验上一致性. 1.PIE/王雄飞
推荐 QCC改善报告之降低整机不良率(经典) 精品

137
128
120
116
73.9%
79.0%
81.9%
84.5%
86.6%
88.7% 90.0% 80.0% 70.0%
65.6% 100
60.0%
55.3%
80 71
50.0%
60
38.5%
40 19.9%
20
将前三项 57
40.0%
做为改善 的重点
30.0%
35
20.0%
20
18
15
14
10.0%
3 QC检验员工误 QC检验人员对标准 现场试验及调查
判所致
掌握的程度及对不良
判定的一致性
是否熟练掌握检验 标准,对不良判定 的一致性是否统一
孙振江
8.17--8.24
4 软件与CRT匹 是否匹配存在缺陷 配存在缺陷
与设计师沟通确认 与设计师及供应商 李 强 8.17--8.24 确认判断
5 机芯手插不良 利用Pareto、鱼骨图等分析工具进行进一步的分析
肖 兵 8.17--8.27
6 机芯检焊不良
王贤文 8.17--8.27
7 机心操作不良
何文志 8.17--8.27
我们首先通过Pareto确定部品不良中的主要缺陷:
部品不良Pareto分析图
40 37
35
34 33
37.2%
39.0%
40.8%
45.0% 42.7%
40.0%
35.1%
35.0%
本单位存在的问题是
选定课题
我得想个好办法降低质 量管理成本
1.目前生产不良率与既定的目标存在差距, 造成生产效率降低,生产成本增加; 2.主要客户对目前的质量水平有一定程度的 ,期望提升我司质量控制水平;
品管圈(QCC)活动成果报告书之降低XX科术前准备缺陷率

品管圈(QCC)活动成果报告书圈名:XX圈改善主题:降低XX科术前准备缺陷率活动类别:√护理□医疗□医技□行政后勤活动类型:√问题解决型□课题达成型所属医院:XXXXX医院级别:三级综合医院□三级专科医院□二级医院□企业医院或民营医院所属科室:新生儿科活动时间:2021/1/1-2021/7/30是否参赛:□第一届□第二届□第三届√无目录一、圈的介绍 (4)(一)圈的组成 (4)(二)圈名意义 (4)(三)圈徽意义 (4)二、主题选定 (5)(一)选题过程 (5)(二)本次活动主题 (6)(三)名词定义及衡量指标 (6)(四)选题理由 (6)三、活动计划拟定 (7)四、现状把握 (7)五、目标设定 (8)六、解析 (9)七、对策拟定 (10)八、对策实施与检讨 (11)九、效果确认 (12)(一)有形成果 (12)(二)无形成果 (13)十、标准化 (14)十一、检讨与改进 (15)备注:如果有上期活动,请增加“一、上期活动追踪结果”,其余内容依次下移。
一、圈的介绍(一)圈的组成表1 XX圈简介表(二)讨论圈名、圈徵选定候选圈名圈徵投票结果选定提案人爱心天使圈 2 2 AAA 奋进圈 1 3 BBBXX圈 5 1 CCC理想圈 1 4 DDD注:采用头脑风暴法,共征集4个圈名及圈徽,由9名圈员分别举手表决,票数最高的确定为圈名及圈徽(二)圈名意义XX圈:同心协作、携手并进,用温暖的双手,托起心的希望,同时用我们的爱心、细心、耐心、责任心感动患者,取得配合,促进康复,体现人文关怀,从而实现护理品质的提升,我们对护理前景充满希望。
(三)圈徽意义绿色:代表团结向上红色:代表友爱心,手:一颗心、两只手寓意着用医护人员温暖的双手,呵护患者的身心健康圈口号:医护同心,健康同行!二、主题选定(一)选题过程全体圈员通过头脑风暴法,立足临床实际,以病患满意为向导,按照质量标准,列出基础护理组的突出问题,用权重法和评价法进行主题选定,将“降低XX科术前准备缺陷率”作为本次QCC活动主题。
QCC_降低设备故障率

确定 课题
降低故障率
三、活动计划
为了开展好活动,我们制定了详细的活动计划。
计划与实施进度 项目
计划
完成
采用 手法
三 月
四 月
五 月
六 月
七 月
八 月
九 月
十 月
十一 月
地 点
负责人
可行性分 析 目标确定
调查表 柱状图 排列图 鱼骨图 图 表 车 间
周宁华 吴利祥
P
原因分析 主因确定 制定对策
周宁华 汤静怡
十二、目标值检查
故障率6.5%
故障率5% 故障
故障 运 行
故障率4.9%
故障
运
行 运
行
活动前
目标值 活动后
经济效益
效益测算:通过QC维修小组成员的共同努力,实现故障率降至5%
以下的目标,即提高了有效的生产时间,从而提高产量,稳定质量: 1、年提高产量计算:2、社会效益:减少了随机停机概率,保证订单及 时完成,保障公司信誉。 3、其他:稳定、提高了产品质量,为车间开发多种高附加值产品提供 了坚实的设备保障;保障了设备的安全稳定运行。
检修 保养
1.分解落实 1.极大减少因缺少备件造成的 1.明确包机责任人对所包机设备备件的 统计责任;2.严格对包机人所包设备因 备件计划责 停机故障。 缺少备件造成长时间停机的考核。 任
对因排查不到位造成的设备故障严格考 2.使包机责任人加强设备巡查, 核 及时发现隐患部位
1.对备件型号的正确性把关
二、计划检修、保养不及时
系统相对较为复杂,润滑点众多,液压装备运用广泛,电气、机械系统 运行精度较高,因此检修计划不周全,润滑保养不到位、定期更换不及 时均造成不确定性停机现象频繁出现。
运用PDCA循环降低病区不良事件的发生率
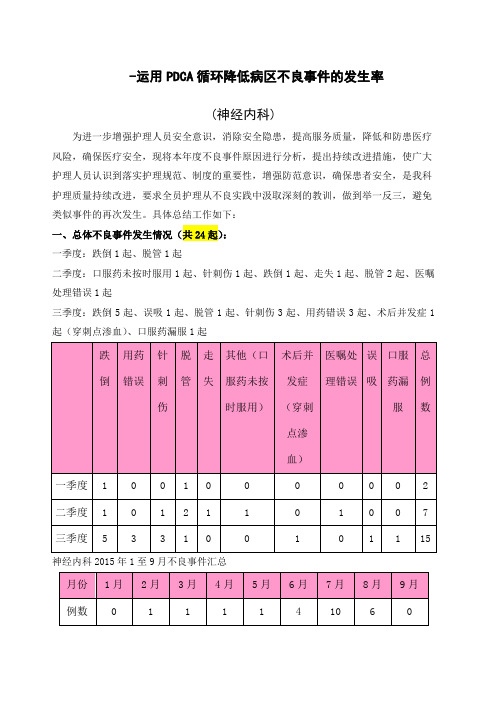
-运用PDCA循环降低病区不良事件的发生率(神经内科)为进一步增强护理人员安全意识,消除安全隐患,提高服务质量,降低和防患医疗风险,确保医疗安全,现将本年度不良事件原因进行分析,提出持续改进措施,使广大护理人员认识到落实护理规范、制度的重要性,增强防范意识,确保患者安全,是我科护理质量持续改进,要求全员护理从不良实践中汲取深刻的教训,做到举一反三,避免类似事件的再次发生。
具体总结工作如下:一、总体不良事件发生情况(共24起):一季度:跌倒1起、脱管1起二季度:口服药未按时服用1起、针刺伤1起、跌倒1起、走失1起、脱管2起、医嘱处理错误1起三季度:跌倒5起、误吸1起、脱管1起、针刺伤3起、用药错误3起、术后并发症1起(穿刺点渗血)、口服药漏服1起跌倒用药错误针刺伤脱管走失其他(口服药未按时服用)术后并发症(穿刺点渗血)医嘱处理错误误吸口服药漏服总例数一季度 1 0 0 1 0 0 0 0 0 0 2 二季度 1 0 1 2 1 1 0 1 0 0 7 三季度 5 3 3 1 0 0 1 0 1 1 15 神经内科2015年1至9月不良事件汇总月份1月2月3月4月5月6月7月8月9月例数0 1 1 1 1 4 10 6 0二、据上表显示7月、8月不良事件总数较前明显增加,原因分析如下:(1)学生刚下临床,对临床护理操作规范不熟。
(2)学生多,带教老师疏于管理,未做到“放手不放眼”。
(3)此阶段病房患者人数较前减少,护士安全意识降低,过于放松,查对及巡视病房力度欠缺。
三、针对上图显示,用药错误、针刺伤、跌倒和脱管分别占12%、17%、17%和29%,为我科1至9月护理不良事件高发类型,列为重点管理对象,PDCA改进措施如下:跌倒P阶段——现状调查2015年1月至8月,神经内科共发生护理不良事件24起,其中跌倒不良事件共7起,占不良事件的比率为29.17%,因此,将跌倒列为2015年整改的重点部分之一,统计分析如下:跌倒不良事件统计表相关内容年龄神志活动时间地点跌倒史视力常需上厕所分类大于等于65岁小于65岁清楚欠清正常无耐力15:~21::~7:其他时间段厕所病房和走廊病房外有无正常不佳是不是0 0 0 0人数 3 4 7 0 6 1 1 1 5 2 3 2 0 7 4 3 2 5经上述统计表可看出神志清楚、活动能力正常、无跌倒史、视力正常、不常需上厕所的患者更易发生跌倒,而往往这类患者又最不易被重视为跌倒高危患者。
推荐 QCC改善案例(超经典) 精品

伟世通在2月份将新产品F3000仪表板在十堰生产、组装,1月份已开始采购新产品原材料(PP粒子)。 为满足陕汽追加的10000辆份的产量,预计3月份F3000项目每日库存将高达100吨。 满足客户需求及降低我司成本与安全风险,改变现在PP粒子的包装方式
【4】
襄樊风神物流有限公司
专业 服务 共创价值
【9】
襄樊风神物流有限公司
专业 服务 共创价值
七、要因确认
序 号
要因
供应商包装 方式
确认过程
供应商到货为散装,必须由人工将货物倒装至我司 托盘后再清点数量入库。
结果
确认人
康启伟、 徐亮
确认时间
10.01.10
1
√ ×
× √
2
无规律到货
多频次,无规律到货造成我司员工重复性工作
王红、 李昌群
10.01.17
改善后
效益
★、无形效益
1.本次改善活动涉及到综合库工作人员,共同参与,出谋划策,增加团队凝聚力。 2. 由叉车作业,我司员工不用登高、上车作业,消除了安全隐患; 3.供应商到货自带托盘、缠绕膜,缓解我司在高产月托盘紧张问题; 4.劳动强度降低,降低了人员流失率; 5.将带缠绕膜的货物堆垛码放提高库房的空间利用率; 6.主机厂高产平稳过渡,得到客户的一致好评!
【15】
襄樊风神物流有限公司
专业 服务 共创价值
十、标准化
《卸货(颗粒)作业》及标准作业书已完成编制修订。
【16】
襄樊风神物流有限公司
专业 服务 共创价值
十一、总结及下一步打算
1)本次活动总结:改善成果
1.本次改善活动在全员共同努力下达成了预期目标。通过与各个部门协调改变包装方式提 高卸货效率。 2.本次改善活动,得到了东风伟世通物流仓储室的大力支持与帮助,通过这次活动加强了 部门与主机厂的协作关系,得到伟世通的赞誉!
QCC改善案例(超经典)
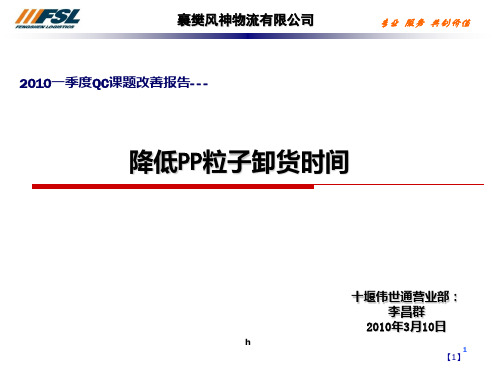
2 康启伟 男 3 李昌群 男 4 徐亮 男
伟世通营业部主管 帐务主管 综合库班长
副组长 组员 组员
5 王德进 男
叉车司机
组员
3.活动时间:
6 李金平 男
DFV物流工程师
组员
2009年12月1日 – 2010年2月20日
7 任菁 男
DFV仓储物流室
组员
8 王红 女
DFV SCM部采购
组员
【5】
三、目标设定
十.标 准 化
十一.总结及下一步计划
专业 服务 共创价值
【2】
一、选题理由
襄樊风神物流有限公司
专业 服务 共创价值
1.F3000新项目 上量,人工卸货 已不能满足正常生产
2.人工卸货,造成 士气低落人员流失率高
3.人工卸货,存在 严重的安全隐患
改善已刻不容缓。
4.人工卸货,成本过高
【3】
一、选题理由
大吨位多频次 的到货,使得 员工劳动强度 高以及卸货不 及时造成供应 商向主机厂投
诉
在倒运过程中 存在严重的安
全隐患
专业 服务 共创价值
累!
【8】
六、要因分析 料
散装
到货包装方式
襄樊风神物流有限公司
法
托盘少
人工卸货 作业方式
设备不够用
机
劳动强度大 士气低落
无规律作业
人
专业 服务 共创价值
PP
粒
子
卸
目标:根据下季度伟世通预估18吨/天的产量,PP粒子卸货效率只有在0.5小时/人·吨,才能满 足客户产能扩张需求,同时成本最小化,达成部门利润指标
【6】
四、活动计划
襄樊风神物流有限公司
QCC成果报告(经典)
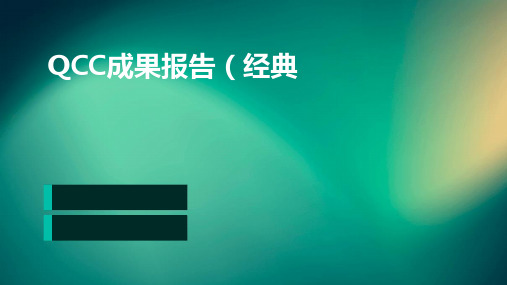
成果四:提升员工士气和凝聚力
总结词
通过QCC活动的实施,员工的工作积极性和凝聚力得到了提高,为企业的发展提供了 有力支持。
详细描述
QCC小组注重员工的参与和成长,鼓励员工提出创新意见和建议,激发了员工的工作 热情和创造力。同时,通过开展团队建设活动和培训课程,提高了员工的技能水平和团 队协作能力,增强了企业的核心竞争力。此外,QCC小组还关注员工福利和工作环境
要点二
详细描述
QCC起源于日本,最初是为了解决生产过程中的品质问题 而自发形成的员工组织。随着日本经济的崛起,QCC的理 念逐渐传播到世界各地,被广泛应用于各种行业和组织。 如今,QCC已经成为一种全球性的品质管理方法,被广大 企业所接受和采纳。随着科技的进步和市场竞争的加剧, QCC也在不断发展演变,以适应新的环境和需求。
QCC成果报告(经典
contents
目录
• QCC活动简介 • QCC成果展示 • QCC实施过程 • QCC成功案例分析 • QCC未来展望
01 QCC活动简介
QCC的定义与特点
总结词
QCC(Quality Control Circle,品质管制圈)是一种员工自发组织的品质改善活动,具有自主性、自下而上、人 人参与的特点。
总结词
通过QCC活动的实施,企业成本得到了有效 控制,提高了经济效益。
详细描述
QCC小组对生产过程中的各个环节进行了成 本分析和控制,优化了原材料采购、库存管 理、生产过程等方面的成本结构。同时,通 过改进工艺和设备,降低了能耗和维修费用, 进一步降低了生产成本。此外,QCC小组还 积极寻求与供应商的合作机会,争取到了更 优惠的价格和更好的采购条件。
改善,为员工创造了一个良好的工作氛围和发展空间。
QC成果报告 降低接管加工一次不合格品率(问题解决型)
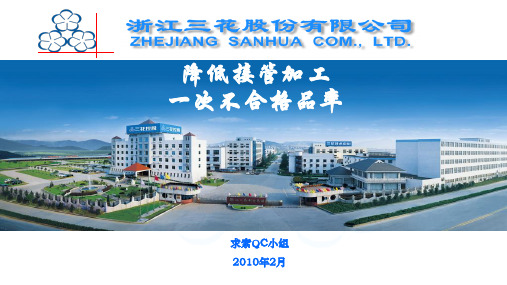
商标、国家重点高新科技企业、中国机械工业百强企业、中国500最具价值品牌、
中国优秀企业、专利示范企业(已拥有311项专利,其中发明专利136项)、国家
重合同守信用企业和浙江省质量奖等多种荣誉称号。
❖ 公司坚持“对内抓现场、对外抓市场、现场服从市场”的经营理念和“生产专业化、产品品牌化、市场国际化"的经营方针,高扬"精
加
工 2.0%
一
次 不
1.5%
合
格 1.0%
品
率 0.5%
接管加工品质对比图
2.39%
1.26%
08年
09年1-3月
从以上统计图表可以发现:从2009年1月开始改用软管后,接管加工一次不合格品率陡然上升,给公司造成了很大的 报废损失。因此,小组成员一致讨论通过以
降低接管加工一次不合格品率
作为本次QC活动的课题。
冲头导向模 原长
加长2mm
批次号
09/04-2136 09/04-2138 09/04-2139 09/04-2141 09/04-2142 09/04-2143
投入数
9864 9986 10011 11242 9839 10021
益求精、追求卓越"的三花精神和'迅速反应、立即行动"的三花作风,继续发扬艰苦创业的精神,与时俱进,开拓创新,努力实现百亿三花、
百强三花、百年三花!
3
产品介绍
四通换向阀
❖ 这是我司的主导产品之一——四通换向阀,销量位居全球第一,市场占有率60%以上。 ❖ 四通换向阀是空调系统三大核心部件之一,主要用于控制制冷、制热的切换。 ❖ 接管主要用于四通换向阀的管路接口,本次QC活动就是围绕它展开的。
18
降低装配工程不良率(QC)
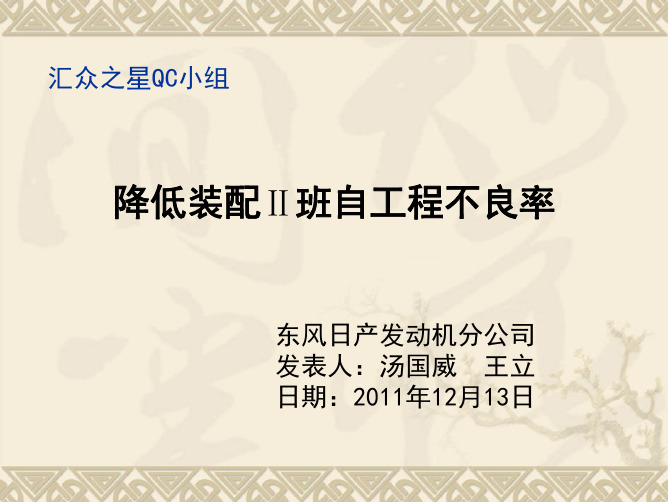
无形效益:
自我评价
QC改善步骤
5 3 活动后 活动前
科长评价
QC改善步骤 5 解决能力度 0 配合性 品质意识 责任感 活动后 活动前 改善意愿
●3月份缸盖气门测漏NG项目统计
(件)
140 120 100 80 60 40 20 0
121 83%
N=146件 作成:李明 作成日期:2011-4-8
100% 80% 60% 40%
15 0
夹异物
8
20%
2
0% 其他
设备堵头破损 座圈压装不到位
<统计结果> 影响气门测漏NG产生的症结是夹异物,占整个不良的83%
手套产生毛线验证内容验证方法验证标准确认手套接触面现场确认手套的磨损程度通过对现场作业者手套的磨损程度进行确认结果发现手套有毛线掉落导致20件缸盖测漏ng结要因验证1小时2小时3小时4小时a班okngngngb班okngngngc班okngngng第一周第二周第三周第四周3件5件8件4件判定序号判定序号换成塑料隔板8否增加托盘清洁的频次8否增加手套更换频次9否19否1换成铁制隔板9否加大支撑块更换频次8否2348否234托盘支撑块磨损掉屑将面纱手套变为点胶手套12要因措施经济性现实性困难度经济性现实性困难度12效果综合评价效果综合评价129912是否采用是否采用将隔板涂一层白色硬纸浆是换成铁制隔板否增加毛刷和自动吹气装置是手套产生毛线是气门隔板掉纸屑缸盖隔板破损掉屑将塑料隔板换为pvc隔板是对策拟定要因措施改善前改善后效果气门隔板掉纸屑在隔层板表面涂一层白色硬纸浆在隔层板表面涂一层白色硬纸浆件对策实施担当人
现状把握(九)
●3月份自工程不良率统计
(%)
0.3 0.25 0.2 0.18 0.15 0.1 0.05 0 11月 12月 1月 2月 3月 0.1 0.1 0.1 0.1 0.16 0.1 0.1 0.17
QC小组报告---提高服务技能,减少服务不良项

提高服务技能,减少服务不良项一.概况1.***科技馆概况:***科技馆是***集团出资兴建的现代化的科技展馆,地处高科园南岭路中段,北临山东省国际会展中心,西依青岛市最大的广场--世纪广场,是青岛新兴旅游景点的黄金地带。
***科技馆是目前国内唯一一家由企业出资兴建的高科技场馆。
她集家电历史、***文化及高科技展示为一体。
现在已被评为全国科普教育基地和青岛市首批科普教育基地,她以展示科技成果为主、兼顾***文化;以展示未来生活为主,寓教于乐,开阔视野,展示了***的科技实力和科技发展的方向。
2.小组成员概况***科技馆接待部QC小组共有6人组成,都是接待骨干,她们熟悉顾客心理,了解科技馆情况,本QC小组2012年以《全组上下齐动员,接待能力创新高》为题的成果获青岛市最佳发表奖,并被青岛市推荐为国优成果。
3.小组概况表注册号:0101制表人:刘利制表时间:2012.11二、选题理由:1. 企业赋与的使命***科技馆作为***集团的窗口,树立良好的企业形象,树立良好的品牌意识,为参观客提供优质满意的服务,是***集团赋予科技馆的使命。
2. 是由***科技馆的主指标决定的***科技馆的方针目标是一切以用户满意度最大化为中心,所以如何不断的提高满意度是***科技馆始终不渝的中心工作.3.现状决定服务不良项在现状中确实存在。
如何能将服务不良项降到最小程度,就成了我们这次活动的主要问题,综上所述,我们将本次活动的选题定为:“提高服务技能,减少服务不良项”三、现状调查:1.人员接待量大,不能全方位满足客人需求。
***科技馆现有讲解员7人,承担着每年20万余人的讲解接待工作,平均每月要接待一万第3 页共12 页六千人,平均每人每天接待近150人,并且客人参观时间不固定,没有专门的培训时间.对服务技巧要求较高。
2.讲解员中实习生占一定比例,基础知识不够扎实,现有7位讲解员中有3位是实习生,她们讲解及服务技能不过硬。
- 1、下载文档前请自行甄别文档内容的完整性,平台不提供额外的编辑、内容补充、找答案等附加服务。
- 2、"仅部分预览"的文档,不可在线预览部分如存在完整性等问题,可反馈申请退款(可完整预览的文档不适用该条件!)。
- 3、如文档侵犯您的权益,请联系客服反馈,我们会尽快为您处理(人工客服工作时间:9:00-18:30)。
56 工程
20.0%
26 设计
25
0.0% 整机操作
2.对故故障类型按照饼型图做进一步的分析:
工厂内部可 控制的不
良,且预计改 善所需时间及 效果会比较显 著
整机操作不良 5%
其他不良 8%
部品不良 31%
涵盖的种类多且 大多符合质量协 议要求,因此我 们只关注批量性 问题
机芯相关不良 31%
部品不良
30
33.0%
26 29.8%
25
30.0%
23.9% 20
25.0%
20.0%
15
16.3%
10 8.5%
5
IC及晶1振4 、 15.0%
声表不良是 9
9
重点
8
8
8
10.0%
5.0%
0 IC201
IC101
1.20%1.70%减去 (-12%)+(0.3%)+(0.1%) =1.18%
机芯相关不良 31%
CRT不良 25%
故障类型 饼型图
部品不良 CRT不良 机芯相关不良 其他不良 整机操作不良
1.我们取09年5月到7月份质量日报按照故障类型制定Pareto,以确认改善方向:
故障类型Pareto
700 647
标
存
软件与CRT匹配存在缺陷
在
机芯手插不良 主要不良 漏插、插反/插错、飞脚
差
距
机芯相关不良
机芯检焊不良 主要不良
虚焊、连焊
仔细分析 认真对待
员工操作不良 主要不良 铜断、断脚、板面异物
1.首先排除小组成员不能改变的供应商来料不良. 2.针对剩下的7条末端因素制定了要因确认计划表,分工负责进行逐一确认.
从10月份开始 增加外观不良
FOR Summary for Philips Model
与09年度目标有 一定的差距
0.60%
Jul-08 FOR 1.92% Target 2.00%
Aug 1.60% 2.00%
Sep 1.36% 2.00%
Oct 1.47% 2.00%
Nov 1.50% 2.00%
Dec 1.76% 2.00%
Jan-09 1.85% 1.50%
Feb 1.81% 1.50%
Mar 1.86% 1.50%
Apr 1.74% 1.50%
May 1.71% 1.50%
Jun 1.68% 1.50%
Jul 1.70% 1.50%
Aug 1.50%
目前FOR 水平为1.70%左右,与既定的目标存在差距;
课题名称
制造总部海外分厂
小 组 名: 雄 鹰 参与部门:质量工程/生产/SQM
小组简介
1、小组名称:啄木鸟小组 2、所属单位:制造总部海外分厂 3、课题类型:现场型
4、活动时间:09.07.01—09.12.31
5、活动次数:15次 6、出席率 :85%
小组成员
组长:王杰
顾问 客 服 部 总 监:张
确定主因计划表
No 项目
确认内容
确认方法
判别标准
负责人 日期
1 员工不良操作 检查操作的规范性 导致
1.作业者是否有相关 1.是否符合公司要求。 谭 强
的资格证明。
2.考核合工装夹具不规 包装或运输生产物料 现场测量调查
范导致
时工装是否符合要求
是否符合工装规格 张繁荣 8.17--8.20 及要求
总
质量工程部经理:莫小荣
生产部 陈远超 肖 兵 何文志
工程部
王贤文 张繁荣
QA/QC 孙振江 谭 强
SQM 李强
• 提高生产员工保留率 (50%)
-3
• 降低整机生产不良率—FOR (30%) - 1
• 提高30%,生产员工工作效率
-2
• 降低生产线转换的时间 (50%)
-4
制造总部的号召各单位开展 QCC改善活动,提升质量管 理水平,降低质量管理成本
CRT不良 机芯相关不良
其他不良
CRT不良 25%
整机操作不良
改善周期长,主 要通过供应商
方面进行改善
3.采用系统图对FOR不良前三项做进一步的分析:
FOR
部品不良
不
良
率
供应商来料不良 员工不良操作导致 工装夹具不规范导致 供应商来料不良
9条末端因素
不可控制因素
与
目
CRT不良
QC检验员工误判所致
可控制因素
我们的目标是将FOR下降30%,即目标设定为由目前的1.70% 降低为1.20%;
2.00%
1.70%
目标设定
目标这么严 格,我们能 达到吗?
1.50%
设定目标
1.00%
1.45% 1.30% 1.20%
0.50%
0.00% 现状
一期目标(Sep) 二期目标(Oct)三期目标(Nov)
整机操作不良 5%
3 QC检验员工误 QC检验人员对标准 现场试验及调查
判所致
掌握的程度及对不良
判定的一致性
是否熟练掌握检验 标准,对不良判定 的一致性是否统一
孙振江
8.17--8.24
4 软件与CRT匹 是否匹配存在缺陷 配存在缺陷
与设计师沟通确认 与设计师及供应商 李 强 8.17--8.24 确认判断
5 机芯手插不良 利用Pareto、鱼骨图等分析工具进行进一步的分析
本单位存在的问题是
选定课题
我得想个好办法降低质 量管理成本
1.目前生产不良率与既定的目标存在差距, 造成生产效率降低,生产成本增加; 2.主要客户对目前的质量水平有一定程度的 ,期望提升我司质量控制水平;
降低整机生产不良率—FOR
--选取产量占总整机产量70%的A产品
2.20% 1.80% 1.40% 1.00%
600 500 400 300
81.8% 517
69.3%
55.2% 299 264
87.8%
91.5%
94.2%
根据质量改善 的二八原则, 这应该是我们
改善的重点
96.8%
98.1%
99.2%100.0% 80.0% 60.0% 40.0%
200
30.7%
100
126 77 57
0 部品 CRT不良 机芯手插 机芯操作 机芯检焊 整机装配 副板
其他不良 8%
部品不良 31%
改进估算
项目 占总 实际 目标 备注 说明 不良 FOR%
1 CRT 25% 0.42% 0.30%•技术相当成熟 彩管
2 •机芯 31% 0.55% 0.25%•出货SKD线不良0.25%
3 部品 31% 0.52% 0.42%降低0.1%是非常有希 望达到的;
达到 == --目标
肖 兵 8.17--8.27
6 机芯检焊不良
王贤文 8.17--8.27
7 机心操作不良
何文志 8.17--8.27
我们首先通过Pareto确定部品不良中的主要缺陷:
部品不良Pareto分析图
40 37
35
34 33
37.2%
39.0%
40.8%
45.0% 42.7%
40.0%
35.1%
35.0%