汽车注塑件的设计
27000109_汽车塑料零部件设计技术研究

782022年5月下 第10期 总第382期工艺设计改造及检测检修China Science & Technology Overview1.我国汽车塑料件应用现状分析在汽车行业不断发展过程中,汽车节能减排战略指导下,汽车零部件塑料化成为我国汽车轻量化技术的代表,已经成为汽车节能减排、提升汽车燃烧资源利用率的重要措施,同时也是衡量我国汽车设计水平以及汽车制造水平的重要标准与指标。
当前,一些发达国家平均每辆车的塑料零部件使用量已经达到300kg 以上,我国目前平均每辆车的塑料零部件使用量仅有130kg 左右,可见我国与发达国家相比仍有明显的差距性。
轻量化材料应用是我国汽车工业重要发展策略,汽车轻量化是我国汽车产品实现综合工况燃料消耗量下降的重要发展方向。
我国汽车设计水平与汽车制造水平不断增强,汽车产品对于塑料使用量也将明显提高,所以汽车塑料零部件设计与制造水平要求提高,以塑料材料代替金属材料也是我国汽车轻量化发展目标以及我国汽车零部件行业未来发展趋势。
不仅如此,从我国当前的技术条件来看,汽车动力电池储能受到一定限制,而新能源汽车轻量化建设效果会直接影响汽车续航里程数。
将轻量化技术应用到新能源汽车领域,能够将汽车自重减少10%,电子能源消耗量下降5.5%,汽车续航里程也将增加5.5%。
所以,新能源汽车不断推广形势下,对于轻量化汽车零部件有了更高的要求与需求。
2.我国汽车塑料件发展趋势分析实际上,汽车塑料件是汽车行业的上游行业,同时也是汽车工业发展的基础性条件,而汽车行业下游为整车装配行业以及汽车维修服务行业。
我国汽车塑料件行业的运用和发展与汽车整车装配行业、汽车维修服务行业的发展情况息息相关。
我国最近几年整车消费市场与汽车服务维修市场发展速度非常快,汽车塑料件行业迅猛发展,发展形势也非常好,并且处于转型升级阶段,使汽车塑料件行业逐渐向专业化发展。
从市场竞争角度来说,我国汽车塑料模具行业在中低档模具产品供应方面能够达到自给自足的状态,可是对于精密度比较大、结构比较复杂、寿命比较长模具的高档模具产品主要从国外进口,在目前国内的市场结构中,有40%以上的高档模具都要从国外进口。
汽车方向盘注塑模的设计与制作

毕业设计说明书题目汽车方向盘注塑模的设计与制作学生姓名专业名称模具设计与制造指导教师二0一三年六月五日目录摘要 (IV)引言 (1)第一章产品图 (4)第二章对塑料件的材料与工艺性分析 (5)2.1材料成型的特点分析 (5)2.1.1使用性能 (5)2.1.2成型性能 (5)2.2塑料件的工艺性分析 (6)2.2.1塑件表面质量分析 (6)2.2.2塑件的结构工艺性分析 (6)第三章根据塑件的质量体积确定型腔数目和选择注射机 (7)3.1 ug模型分析 (7)3.2确定型腔数 (7)3.3根据模具型腔能否充满与最大注射量关系计算 (7)3.4注射压力的校核 (8)3.5锁模力的校核 (8)3.6 开模行程的校核 (9)第四章模架的选择 (10)第五章塑料制件在模具中的位置 (11)5.1分型面 (11)5.2成型零件及排列方式 (12)5.2.1型腔 (12)5.2.2型芯 (13)5.2.3 排位方式 (13)第六章浇注系统设计 (15)6.1 主流道的设计 (15)6.2 分流道的设计 (17)6.3 浇口的设计 (18)6.4 泠料穴和拉料杆的设计 (20)第七章合模导向机构设计 (21)7.1导向装置 (21)7.2复位装置 (22)第八章排气系统的设计 (24)第九章冷却系统的设计 (25)第十章推出机构设计 (26)第十一章模具工作原理 (28)第十二章模具草图 (28)参考文献 (29)结论 (30)摘要为了保证成型合格的塑料制品,满足产品的使用要求,保证模塑成型工艺顺利进行,提高劳动生产率,降低成本,必须根据塑料制品的要求和塑料的工艺性能,认真分析制品的工艺性或正确设计塑料制品,正确确定成型方法及成型工艺,正确选择成型工艺条件,正确设计塑料模具及选择合适的成型机械。
在塑料成型工艺和各种塑料模具结构及设计计算的基础上,现扼要叙述一个塑料模设计的实例。
本设计是车模方向盘模具设计。
根据指导老师所给的任务书自己找个零件实物,自己测绘,应用ug软件,创建零件模型图,然后创建分型面,并把模型图停留在动模部分和定模部分。
汽车注塑模具设计全图解教程案例介绍(系统)
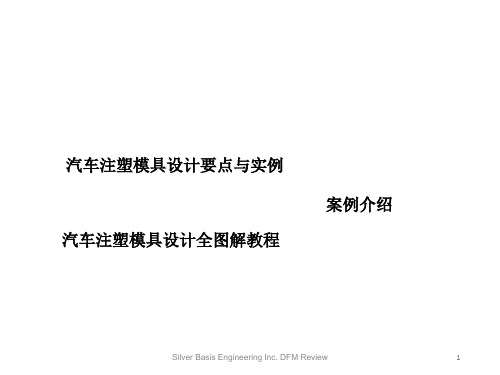
18
内分型核心技术
Silver Basis Engineering Inc. DFM Review
19
如上图所示,为汽车内分型保险杠二次变轨(又称双节变轨)运行轨迹图,共4种 运行轨迹,分别为a,b,c,d四种。下面详细分析4种二次变轨运动轨迹: 图a所示分为3段,分别为L1,L2,L3。 横向斜顶由运动导轨控制其运动,在L1这段距离内,横向斜顶保持不变。 在L2这段距离内,横向斜顶向内拉动制品变形,脱出定模倒扣。
用。
对于汽车保险杠塑件,一般有外分型与内分型两种分型方式。针对所有的汽车 保险杠两侧的大面积倒扣,即可以采用外分型也可以采用内分型。这两种分型方式 的选择主要取决于最终客户汽车主机厂对保险杠的要求,一般欧美汽车大多采用内 分型技术,日系汽车大多采用外分型。两种分型方式各有优缺点,外分型的保险杠 需要处理夹线,增加了加工工序,但外分型保险杠在模具成本与技术难度要低于内 分型保险杠。内分型的保险杠通过二次变轨轨道控制技术,一次性完美的将保险杠 注塑出来,从而保证了保险杠的外观质量,节省了塑件加工工序与加工成本。但缺
接着继续运行,横向斜顶保持不变,制品脱离大斜顶。在L3这段距离内,制品完成 脱模,接着机械手取件。
图b所示分为4段,分别为L1,L2,L3,L4。 1. 横向斜顶由运动导轨控制其运动,在L1这段距离内,横向斜顶保持不变。
2. 在L2这段距离内,横向斜顶在向内拉动制品变形,脱出定模倒扣。 3. 接着继续运行,横向斜顶保持不变,在L3这段距离内,制品脱离大斜顶。
Silver Basis Engineering Inc. DFM Review
图d所示分为4段,分别为L1,L2,L3,L4。
浅谈汽车外饰塑料件设计缺陷
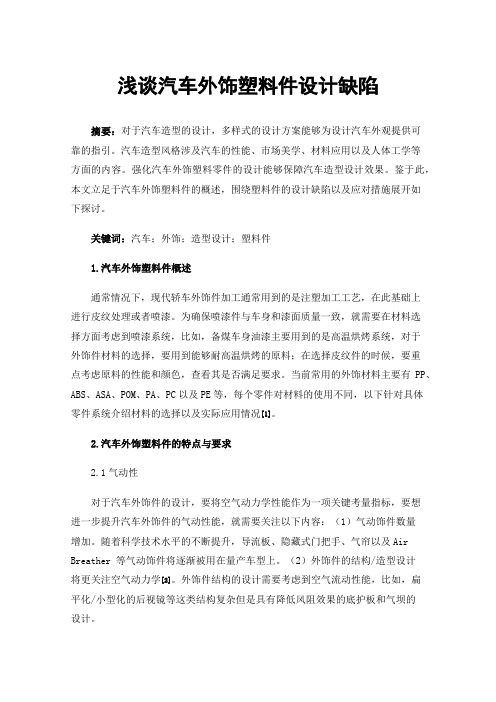
浅谈汽车外饰塑料件设计缺陷摘要:对于汽车造型的设计,多样式的设计方案能够为设计汽车外观提供可靠的指引。
汽车造型风格涉及汽车的性能、市场美学、材料应用以及人体工学等方面的内容。
强化汽车外饰塑料零件的设计能够保障汽车造型设计效果。
鉴于此,本文立足于汽车外饰塑料件的概述,围绕塑料件的设计缺陷以及应对措施展开如下探讨。
关键词:汽车;外饰;造型设计;塑料件1.汽车外饰塑料件概述通常情况下,现代轿车外饰件加工通常用到的是注塑加工工艺,在此基础上进行皮纹处理或者喷漆。
为确保喷漆件与车身和漆面质量一致,就需要在材料选择方面考虑到喷漆系统,比如,备煤车身油漆主要用到的是高温烘烤系统,对于外饰件材料的选择,要用到能够耐高温烘烤的原料;在选择皮纹件的时候,要重点考虑原料的性能和颜色,查看其是否满足要求。
当前常用的外饰材料主要有PP、ABS、ASA、POM、PA、PC以及PE等,每个零件对材料的使用不同,以下针对具体零件系统介绍材料的选择以及实际应用情况[1]。
2.汽车外饰塑料件的特点与要求2.1气动性对于汽车外饰件的设计,要将空气动力学性能作为一项关键考量指标,要想进一步提升汽车外饰件的气动性能,就需要关注以下内容:(1)气动饰件数量增加。
随着科学技术水平的不断提升,导流板、隐藏式门把手、气帘以及Air Breather 等气动饰件将逐渐被用在量产车型上。
(2)外饰件的结构/造型设计将更关注空气动力学[2]。
外饰件结构的设计需要考虑到空气流动性能,比如,扁平化/小型化的后视镜等这类结构复杂但是具有降低风阻效果的底护板和气坝的设计。
2.2装饰性Panoz 与 Feynlab 合作将一种记忆聚合物涂层应用于油漆中,这种材料的使用能够在受热时恢复原始结构,从而将表面划痕除去。
这种涂层通常用来处理漩涡痕迹或者轻微划痕。
车漆自修复技术用到的是一种特殊的涂层保护剂,这种密度较高的透明合成树脂,将其以网状结构涂在汽车油漆外层,能够增强汽车表层抗划伤能力,即便出现划痕,基于超强的网状树脂也能够快速修复划痕。
ts16949注塑件形位标准_解释说明以及概述

ts16949注塑件形位标准解释说明以及概述1. 引言1.1 概述TS16949注塑件形位标准是指在汽车零部件制造过程中,针对注塑件的形位测量和要求而制定的一系列标准规范。
这些标准规定了注塑件在尺寸和位置上的公差范围,以确保注塑件能够正确安装和与其他零部件精确配合。
1.2 文章结构本文主要围绕TS16949注塑件形位标准展开详细说明和解释,并探讨其在质量管理中的应用。
文章分为五个部分:引言、TS16949注塑件形位标准解释说明、形位标准的具体要点解析与示例说明、注塑件形位标准在质量管理中的应用、结论与展望。
1.3 目的本文旨在向读者介绍和解释TS16949注塑件形位标准,包括其定义和背景,作用和重要性,以及分类和要求方面的内容。
同时,我们将对形位标准的具体要点进行深入解析,并提供示例说明。
此外,文章还将探讨注塑件形位标准在质量管理中的应用,并分析其对生产过程、质量检验和评估的影响与控制措施。
最后,我们将总结文章主要观点和研究成果,并展望注塑件形位标准研究的不足之处和未来发展方向。
2. TS16949注塑件形位标准解释说明:2.1 定义和背景:TS16949是汽车行业质量管理体系标准,也是ISO/TS 16949:2009技术规范的简称。
注塑件形位标准是该标准中的一个重要部分,用于规范和约束汽车注塑件在尺寸、位置以及相关要求方面的质量控制。
2.2 形位标准的作用和重要性:注塑件形位标准在汽车零部件制造过程中起着至关重要的作用。
通过明确注塑件尺寸公差、位置公差等要求,可以保证零部件在装配过程中的一致性和互换性。
形位标准可以有效地指导产品设计与制造,并为供应商提供参考,从而提高整个供应链上各环节的生产效率和产品质量。
2.3 注塑件形位标准的分类和要求:注塑件形位标准可以分为两大类:尺寸公差和位置公差。
尺寸公差是指允许零部件实际尺寸与理论尺寸之间的偏差范围;而位置公差则主要描述了零部件之间或其它基准面之间的相对位置关系要求。
汽车塑料件设计要求方案
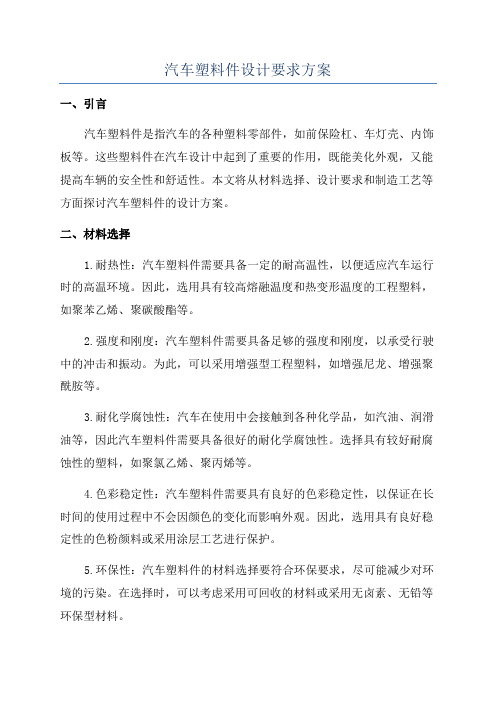
汽车塑料件设计要求方案一、引言汽车塑料件是指汽车的各种塑料零部件,如前保险杠、车灯壳、内饰板等。
这些塑料件在汽车设计中起到了重要的作用,既能美化外观,又能提高车辆的安全性和舒适性。
本文将从材料选择、设计要求和制造工艺等方面探讨汽车塑料件的设计方案。
二、材料选择1.耐热性:汽车塑料件需要具备一定的耐高温性,以便适应汽车运行时的高温环境。
因此,选用具有较高熔融温度和热变形温度的工程塑料,如聚苯乙烯、聚碳酸酯等。
2.强度和刚度:汽车塑料件需要具备足够的强度和刚度,以承受行驶中的冲击和振动。
为此,可以采用增强型工程塑料,如增强尼龙、增强聚酰胺等。
3.耐化学腐蚀性:汽车在使用中会接触到各种化学品,如汽油、润滑油等,因此汽车塑料件需要具备很好的耐化学腐蚀性。
选择具有较好耐腐蚀性的塑料,如聚氯乙烯、聚丙烯等。
4.色彩稳定性:汽车塑料件需要具有良好的色彩稳定性,以保证在长时间的使用过程中不会因颜色的变化而影响外观。
因此,选用具有良好稳定性的色粉颜料或采用涂层工艺进行保护。
5.环保性:汽车塑料件的材料选择要符合环保要求,尽可能减少对环境的污染。
在选择时,可以考虑采用可回收的材料或采用无卤素、无铅等环保型材料。
三、设计要求1.外观设计:汽车塑料件是汽车的重要组成部分,其外观设计要与整车风格相协调。
注重形状的流线化、曲线的柔和、比例的协调等,以提高整体的美观性。
2.强度和刚度:对于需要承受冲击的塑料件,要注重强度和刚度的设计,以确保其在受力时不会发生变形和破裂。
3.安装和拆卸便捷性:汽车塑料件需要便于安装和拆卸,以方便维修和更换。
因此,在设计时要考虑到拆卸和装配的方便性,并采用合适的固定件和连接件。
4.密封性:对于需要防水和密封的汽车塑料件,要注重密封性的设计,以避免水汽渗入和气体泄漏。
5.耐久性:汽车塑料件需要具备一定的耐久性,以承受车辆长期使用带来的磨损和老化。
因此,在设计时要考虑到材料的耐候性和耐磨性,并采取适当的保护措施。
(完整版)汽车研发注塑件工艺流程及参数解析
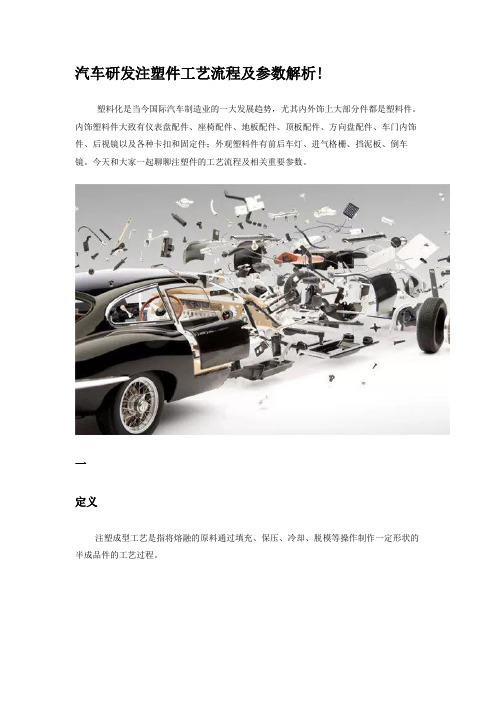
汽车研发注塑件工艺流程及参数解析!塑料化是当今国际汽车制造业的一大发展趋势,尤其内外饰上大部分件都是塑料件。
内饰塑料件大致有仪表盘配件、座椅配件、地板配件、顶板配件、方向盘配件、车门内饰件、后视镜以及各种卡扣和固定件;外观塑料件有前后车灯、进气格栅、挡泥板、倒车镜。
今天和大家一起聊聊注塑件的工艺流程及相关重要参数。
一定义注塑成型工艺是指将熔融的原料通过填充、保压、冷却、脱模等操作制作一定形状的半成品件的工艺过程。
二工艺流程注塑工艺流程图如下:1填充阶段填充是整个注塑循环过程中的第一步,时间从模具闭合开始注塑算起,到模具型腔填充到大约95%为止。
理论上,填充时间越短,成型效率越高。
但是在实际生产中,成型时间(或注塑速度)要受到很多条件的制约。
填充又可分为高速填充和低速填充。
1)高速填充高速填充时剪切率较高,塑料由于剪切变稀的作用而存在粘度下降的情形,使整体流动阻力降低;局部的粘滞加热影响也会使固化层厚度变薄。
因此在流动控制阶段,填充行为往往取决于待填充的体积大小。
即在流动控制阶段,由于高速填充,熔体的剪切变稀效果往往很大,而薄壁的冷却作用并不明显,于是速率的效用占了上风。
2)低速填充热传导控制低速填充时,剪切率较低,局部粘度较高,流动阻力较大。
由于热塑料补充速率较慢,流动较为缓慢,使热传导效应较为明显,热量迅速为冷模壁带走。
加上较少量的粘滞加热现象,固化层厚度较厚,又进一步增加壁部较薄处的流动阻力。
2保压阶段保压阶段的作用是持续施加压力,压实熔体,增加塑料密度(增密),以补偿塑料的收缩行为。
在保压过程中,由于模腔中已经填满塑料,背压较高。
在保压压实过程中,注塑机螺杆仅能慢慢地向前作微小移动,塑料的流动速度也较为缓慢,这时的流动称作保压流动。
由于在保压阶段,塑料受模壁冷却固化加快,熔体粘度增加也很快,因此模具型腔内的阻力很大。
在保压的后期,材料密度持续增大,塑件也逐渐成型,保压阶段要一直持续到浇口固化封口为止,此时保压阶段的模腔压力达到最高值。
汽车门板注塑工艺分析及其注射模设计

汽车门板注塑工艺分析及其注射模设计随着汽车制造技术水平的不断进步,人们对降低汽车能耗提出了越来越高的要求,这为塑料制件在汽车行业的推广应用提供了广阔的发展空间。
近些年来,塑料制件在汽车生产中的应用比例越来越大。
目前汽车的内外饰件已基本实现塑料化,为汽车减轻重量、节约成本和降低油耗发挥着重要作用。
塑料制件需要普及,并提高技术质量,模具作为工业母体必然要先行。
以下以某车型汽车门板为例,阐述其制造工艺及相关注射模具设计要点。
通常汽车拥有前、后两车门,按照门板包皮套分类可分为包皮套和不包皮套,按照门板外形特征,可分为喇叭网和无喇叭网门板。
其中包皮套门板的产品表面质量要求较低,而不包皮套门板的外观件质量要求很高,如产品表面不允许有熔接线、不允许顶白、强度要求高而且无毛刺等。
门板工艺性分析门板作为汽车的内饰件产品,根据车型的不同,尺寸大小有所不同。
图1所示为某车型汽车左前门装饰板,产品最大尺寸为835mm×520mm×90mm ,形状比较复杂,表面有皮纹,其中产品螺丝柱共21处,围绕产品周边一圈分布有7处倒扣,内部所有加强筋模具尺寸为小端0.8mm 、大端1.1mm 。
为防止产品飞边,喇叭网孔全部做在定模上,角度为8°。
图1 产品动模侧平面根据以上工艺性要求,本产品实际生产中材料选用PP-T20,缩水率为1.2%,平均壁厚2.5mm,采用1600t注塑机注射成形。
模流分析根据以上的产品结构及工艺性要求分析,模具设计为一模一穴式结构。
接下来我们采用MOLDFLOW对其注塑工艺性进行仿真分析,根据产品形状和注塑工艺,模具采用3点大水口设计,并配备搭接式侧浇口,流道尺寸直径为14mm,用调结阀控制进浇速度。
浇口详细位置如图2所示。
图2 热流道浇口位置在冷却系统方面,冷却水路(图3)采用直通和水塔式设计,水路直径设置为14mm、水塔为30mm,热嘴附近分布水路,以增强模具冷却效果并调节模具温度,因此极大地缩短了冷却时间和生产周期,提高了生产效率。
汽车内外饰塑料件产品结构设计准则
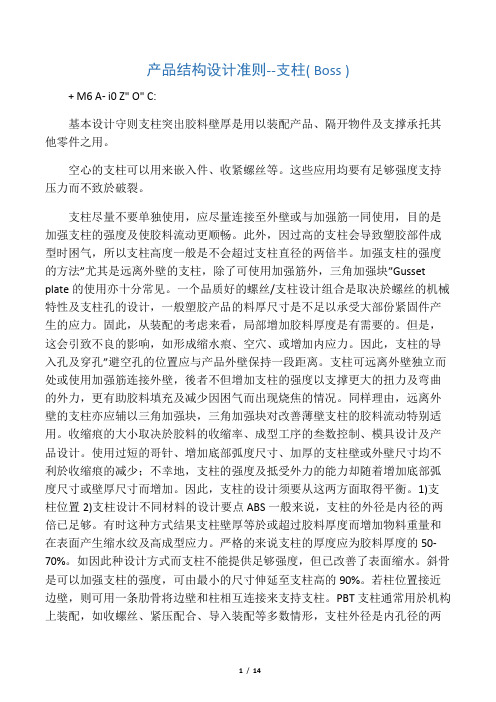
产品结构设计准则--支柱( Boss )+ M6 A- i0 Z" O" C:基本设计守则支柱突出胶料壁厚是用以装配产品、隔开物件及支撑承托其他零件之用。
空心的支柱可以用来嵌入件、收紧螺丝等。
这些应用均要有足够强度支持压力而不致於破裂。
支柱尽量不要单独使用,应尽量连接至外壁或与加强筋一同使用,目的是加强支柱的强度及使胶料流动更顺畅。
此外,因过高的支柱会导致塑胶部件成型时困气,所以支柱高度一般是不会超过支柱直径的两倍半。
加强支柱的强度的方法”尤其是远离外壁的支柱,除了可使用加强筋外,三角加强块”Gusset plate的使用亦十分常见。
一个品质好的螺丝/支柱设计组合是取决於螺丝的机械特性及支柱孔的设计,一般塑胶产品的料厚尺寸是不足以承受大部份紧固件产生的应力。
固此,从装配的考虑来看,局部增加胶料厚度是有需要的。
但是,这会引致不良的影响,如形成缩水痕、空穴、或增加内应力。
因此,支柱的导入孔及穿孔”避空孔的位置应与产品外壁保持一段距离。
支柱可远离外壁独立而处或使用加强筋连接外壁,後者不但增加支柱的强度以支撑更大的扭力及弯曲的外力,更有助胶料填充及减少因困气而出现烧焦的情况。
同样理由,远离外壁的支柱亦应辅以三角加强块,三角加强块对改善薄壁支柱的胶料流动特别适用。
收缩痕的大小取决於胶料的收缩率、成型工序的叁数控制、模具设计及产品设计。
使用过短的哥针、增加底部弧度尺寸、加厚的支柱壁或外壁尺寸均不利於收缩痕的减少;不幸地,支柱的强度及抵受外力的能力却随着增加底部弧度尺寸或壁厚尺寸而增加。
因此,支柱的设计须要从这两方面取得平衡。
1)支柱位置2)支柱设计不同材料的设计要点ABS一般来说,支柱的外径是内径的两倍已足够。
有时这种方式结果支柱壁厚等於或超过胶料厚度而增加物料重量和在表面产生缩水纹及高成型应力。
严格的来说支柱的厚度应为胶料厚度的50-70%。
如因此种设计方式而支柱不能提供足够强度,但已改善了表面缩水。
汽车外饰注塑件的典型缺陷及其规避设计方法探讨

汽车外饰注塑件的典型缺陷及其规避设计方法探讨摘要:在汽车外饰设计时,依据个人经验进行汽车外饰注塑件设计过程中需要分析脱模不良和填充不足,还有毛刺和熔接痕,以及收缩痕和翘曲等缺陷,能够全面提升注塑件的结构设计合理性,才可以更好地进行质量控制。
关键词:汽车外饰;注塑件;典型缺陷;规避设计;方法随着汽车行业的发展,注塑件的应用越来越多,不仅在汽车内饰和外饰上,还应用于保险杠和仪表板等部件,同时许多功能性部件也应用了注塑件。
注塑件优势非常明显,可以进行复杂造型,也可以使汽车轻量化,尤其在节能减排的趋势下,注塑件发挥了重要作用,同时也推进了环保和资源的回收利用。
汽车结构中使用塑料件,大多是注塑方式制成的,因此注塑件的外观会存在各种缺陷,而这些缺陷会给汽车外观质量带来一定影响,严重的还会降低汽车外观品质。
因此,需要分析注塑件的缺陷,并在结构设计时进行有效的控制这些缺陷。
1汽车外饰注塑件缺陷和产生原因分析外饰注塑件常见的缺陷有多种,比如虎皮纹和顶杆,以及镶块印记和银丝,还有水花等缺陷。
这些缺陷形成原因和出现位置,主要有以下几种情况。
1.1脱模不良造成的缺陷和产生原因分析脱模不良主要是因为塑件成品无法从模具当内脱出或者是脱模困难情况,在这样的情况下就会导致塑件成品出现拉白和龟裂等缺陷。
产生这类缺陷是因为结构设计没有在脱模方向上,由于没有根据材料特征设置足够大的脱模斜度,导致无法从模具当中顺利地取出制品,从而所造成了这种缺陷。
1.2填充不足缺陷和产生原因在注塑过程当中,注塑材料如果没有完全填满模具型腔,注塑件就会出现欠胶缺陷,如果产品在成型之前注塑材料冷却固化了,那么制品就会完全成为废品。
在实际操作中填充不足是汽车外饰注塑件的典型缺陷,尤其在孔、柱部位,以及远离浇口的结构和部位,非常容易出现这种缺陷。
出现注塑件充填不足这种情况,主要是因为材料流动性较差和浇口位置设计不合理,以及产品壁厚设计较薄等因素,导致加强筋和产品厚度存在差异,从而引起了滞流现象,因此出现了填充不足问题。
汽车仪表外壳注塑工艺及模具设计

汽车仪表外壳注塑工艺及模具设计摘要:随着经济日益发展,塑料制品越来越多,注塑的、吹塑的、挤压成型的,而对于一些改性塑料的应用,有些塑料甚至可以超越部分合金的硬度,在汽车的应用方面,除了塑料轻的原因之外还有很多优良的特性,一些塑料还用于做防火材料,促使成本大大的降低,使国民经济稳定而高速的增长,在生产力的不断提高,工业技术也渐渐的向国外先进技术靠齐,特别是对于一些出口模具,精度要求都可以到达要求,模具设计的好,模具材料选用的好,加工机床先进的,模具的生产时间可以连续生产10几年。
产品的成型离不开注塑机的生产,生产工艺的调试,为达到更好的产品注塑周期和质量要求。
模具是我们提高生产效率的重要因数,提升模具生产产能是每一位工程师的责任,模具设计的好坏直接反馈到模具是否能稳定长时间的生产和日后生产维修是否方便。
关键词:模具;模具设计;注塑;成型一、汽车仪表概述在普通的汽车当中,仪表会涵盖车速里程表、转速表、水温表和燃油表等。
在现代汽车当中,汽车仪表还要安装了稳压设备,专门对仪表电源的电压进行稳定,压制住了波动产生的幅度,确保仪表能够精准的进行显示[1]。
此外,很多仪表的显示皆来自传感设备,根据监测对象产生的变化,对电阻值进行改变,再利用仪表进行表述。
在仪表板当中,最突出的便是车速里程表,能够将汽车的时速显示出来,车速里程表由2个表组成,分别是车速表和是里程表。
二、模具质量正常而言,客户主要从工期、投入以及质量几个角度对模具进行评估。
这里面质量是客户最为关注的一点,这是由于要做出可靠的产品就必须拥有一个可靠的模具。
因此对于模具生产公司来说,如果想要提高其市场竞争力,就必须增强模具的质量。
增强模具质量应当对其生产的所有流程细节进行严格的把控。
模具制造大致要经过制造与设计两个阶段,前者是通过加工、选材、状态、热处理等各种生产流程方面决定着模具的质量;后者则是通过生产可操作性、细节的精准程度、构造的科学程度等影响模具质量。
汽车研发注塑件工艺流程及参数解析

汽车研发注塑件工艺流程及参数解析!塑料化是当今国际汽车制造业的一大发展趋势,尤其内外饰上大部分件都是塑料件。
内饰塑料件大致有仪表盘配件、座椅配件、地板配件、顶板配件、方向盘配件、车门内饰件、后视镜以及各种卡扣和固定件;外观塑料件有前后车灯、进气格栅、挡泥板、倒车镜。
今天和大家一起聊聊注塑件的工艺流程及相关重要参数。
一定义注塑成型工艺是指将熔融的原料通过填充、保压、冷却、脱模等操作制作一定形状的半成品件的工艺过程。
二工艺流程注塑工艺流程图如下:1填充阶段填充是整个注塑循环过程中的第一步,时间从模具闭合开始注塑算起,到模具型腔填充到大约95%为止。
理论上,填充时间越短,成型效率越高。
但是在实际生产中,成型时间(或注塑速度)要受到很多条件的制约。
填充又可分为高速填充和低速填充。
1)高速填充高速填充时剪切率较高,塑料由于剪切变稀的作用而存在粘度下降的情形,使整体流动阻力降低;局部的粘滞加热影响也会使固化层厚度变薄。
因此在流动控制阶段,填充行为往往取决于待填充的体积大小。
即在流动控制阶段,由于高速填充,熔体的剪切变稀效果往往很大,而薄壁的冷却作用并不明显,于是速率的效用占了上风。
2)低速填充热传导控制低速填充时,剪切率较低,局部粘度较高,流动阻力较大。
由于热塑料补充速率较慢,流动较为缓慢,使热传导效应较为明显,热量迅速为冷模壁带走。
加上较少量的粘滞加热现象,固化层厚度较厚,又进一步增加壁部较薄处的流动阻力。
2保压阶段保压阶段的作用是持续施加压力,压实熔体,增加塑料密度(增密),以补偿塑料的收缩行为。
在保压过程中,由于模腔中已经填满塑料,背压较高。
在保压压实过程中,注塑机螺杆仅能慢慢地向前作微小移动,塑料的流动速度也较为缓慢,这时的流动称作保压流动。
由于在保压阶段,塑料受模壁冷却固化加快,熔体粘度增加也很快,因此模具型腔内的阻力很大。
在保压的后期,材料密度持续增大,塑件也逐渐成型,保压阶段要一直持续到浇口固化封口为止,此时保压阶段的模腔压力达到最高值。
汽车前端模块注塑模具设计要点

2020年30期设计创新科技创新与应用Technology Innovation and Application汽车前端模块注塑模具设计要点王周周(嘉兴信元精密模具科技有限公司,浙江嘉兴314000)引言在汽车零配件中,前端模块一般采用金属冲压件来制造,此部件用塑料件来替代金属件也是国内首次尝试,其优点是强度好、质量轻、成本低;其相关性能通过测试达到了金属件的强度。
1产品简介1.1产品信息(见图1)产品尺寸:1300mm*600mm*378mm摘要:在汽车零配件中,前端模块一般采用金属冲压件来制造,随着塑料产业的不断发展,一些高强度塑料往往可以替代金属件。
近期一款车型前端模块就是采用注塑方式成型的,在成型的过程中也常常会存在一些风险;实际试模后也证实了这一情况,如何更简便有效的解决此问题?文章将给出答案。
关键词:分体式设计方案;排气结构;浮纤现象中图分类号:TQ320文献标志码:A文章编号:2095-2945(2020)30-0077-04Abstract :Among the automotive parts,front-end module is manufactured by metal stamping process.With the continuously de 鄄veloping of the plastic industry,the metal parts can be replaced by some high strength plastic material.Currently,there is the front-end module of one vehicle model which is made by injection process.However,it has risk during injection process normally.This risk is also verified during the actual tryout.Thus,this paper will give a response of solving the problem with simple and effective method.Keywords :split-type design concept;vent structure;fiber emergence作者简介:王周周(1984-),本科,工程师,资深设计工程师,研究方向:汽车外饰模具。
大型汽车工程部件注塑成型实验报告

大型汽车工程部件注塑成型实验报告一、实验目的1、掌握注塑成型工艺中各参数如塑件材料、成型压力、温度、注射速度、浇注系统等因素对其成型质量的影响大小。
2、介绍塑件各种成型瑕疵的构成机理,以及各工艺参数对各种瑕疵构成的影响大小。
3、初步介绍压铸成型分析软件moldflow的各项功能及基本操作。
4、初步介绍ug软件三维建模功能。
5、初步介绍ug软件三维模具设计功能。
二、实验原理1、moldflow压铸成型分析软件的功能十分齐全,具备完备的分析模块,可以分析出来压铸成型工艺中各个参数例如塑件材料、成型压力、温度、口服速度、浇筑系统等因素对成型质量的影响,还可以模拟出成型瑕疵的构成,以及如何改良等等,还可以预测每次成型后的结果。
2、注射成型充填过程属于非牛顿体、非等温、非稳态的流动与传热过程,满足黏性流体力学和基本方程,但方程过于复杂所以引入了层流假设和未压缩流体假设等。
最后通过公式的分析和计算,就可以得出结果。
三、实验器材硬件:计算机、游标卡尺、注塑机、打印机软件:ug软件、moldflow软件四、实验方法与步聚1、ug软件模型创建和模具设计(已省却);2、启动moldflow软件;3、新建一个分析项目;4、输出分析模型文件;5、网格分割和网格修正;6、流道设计;7、冷却水道布置; 8、成型工艺参数设置; 9、运转分析解器; 10、制作分析报告11、用试验模具在注塑机上进行工艺试验(已省去);12、分析演示分析报告(省却与实验结果相比较这一步骤); 13、得出结论五、前置处理相关数据 1.网格处理情况1)展开网格确诊,可以看见网格重合和最小四海比等问题; 2)网格确诊,并依次修正存有的网格问题; 3)修正回去后,再次检查网格情况。
2.材料选择及材料相关参数在在方案任务视窗里双击第四项材料,插入例如图材料挑选窗可直接选常用材料,也可根据制造商、商业名称或全称搜索3. 工艺参数设置双击方案任务视窗里的“成型条件设置”,这里直接用默认值。
浅谈汽车外饰件感观品质设计方法

浅谈汽车外饰件感观品质设计方法摘要:目前我国经济水平和各行业的快速发展,汽车外饰在整车中主要起到美化、防护、安全等作用。
为了追求整车造型美观,像保险杠等外饰件分缝处圆角越来越小,为了满足其他相关部件固定等需求,保险杠不可避免地需要优化一些内部结构,使得外表面不易出现外观缩痕、熔接痕、翘曲变形等外观缺陷。
为了满足整车造型需求,保险杠造型分块越来越多,如何高品质控制好部件间外观匹配已显得尤为重要。
文中结合了以往汽车保险杠的外观问题及实际工作中的经验,主要研究了汽车外饰注塑件感观品质设计方法及要求,通过迭代车型上的应用,有效提升了汽车外饰注塑件的感观品质。
关键词:汽车外饰;结构设计;精度设计引言汽车内、外饰造型一致性认知是客观存在的,且此认知模式中,不但包含造型形态认知的一致性,也包括车型体量认知的一致性。
虽然在普通用户对汽车产品造型的设计意图进行认知解释时,受此认知模式的刺激程度弱于专家(设计师),但是用户之间对于正确答案的选择,并未出现显著性差异。
这表明,此种刺激在用户群体中具有普遍性。
若能探究此认知模式对用户在进行汽车内、外饰造型形态一致性认知时产生的刺激源,则有助于提升用户解读设计师的设计意图的准确率,进而对品牌形象构建产生正向作用。
1外饰产品设计简介汽车外部非金属件一般属于外饰产品,例如前格栅、前后保险杠、尾翼扰流板、侧裙、挡泥板、底护板、立柱外饰板及顶盖饰条等。
外饰产品设计在整车项目开发的预研可研、概念设计、详细设计、设计验证及认证与生产准备的五个大阶段分别对应着如下具体工作:外饰技术方案设计、结构设计、精度设计及设计验证。
本文重点阐述结构设计、精度设计与设计验证,简要阐述方案设计。
2汽车外饰件主要外观缺陷在实际生产制造中,汽车外饰注塑件还存在不少外观缺陷,如填充不足、飞边、缩痕、熔接痕、气泡、翘曲变形等。
其中缩痕、熔接痕、翘曲变形等常见缺陷与产品设计强相关,出现在前后脸、侧面的大型注塑件上就会严重影响整车外观品质。