下料问题的优化设计复习进程
下料问题的逐级优化方法
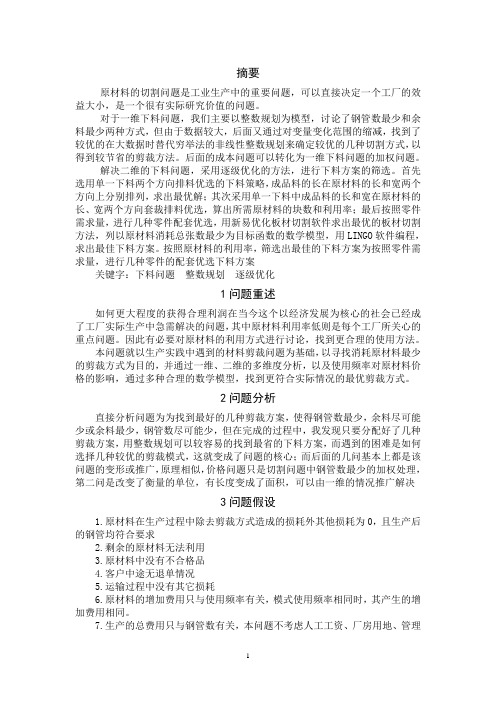
摘要原材料的切割问题是工业生产中的重要问题,可以直接决定一个工厂的效益大小,是一个很有实际研究价值的问题。
对于一维下料问题,我们主要以整数规划为模型,讨论了钢管数最少和余料最少两种方式,但由于数据较大,后面又通过对变量变化范围的缩减,找到了较优的在大数据时替代穷举法的非线性整数规划来确定较优的几种切割方式,以得到较节省的剪裁方法。
后面的成本问题可以转化为一维下料问题的加权问题。
解决二维的下料问题,采用逐级优化的方法,进行下料方案的筛选。
首先选用单一下料两个方向排料优选的下料策略,成品料的长在原材料的长和宽两个方向上分别排列,求出最优解;其次采用单一下料中成品料的长和宽在原材料的长、宽两个方向套裁排料优选,算出所需原材料的块数和利用率;最后按照零件需求量,进行几种零件配套优选,用新易优化板材切割软件求出最优的板材切割方法,列以原材料消耗总张数最少为目标函数的数学模型,用LINGO软件编程,求出最佳下料方案。
按照原材料的利用率,筛选出最佳的下料方案为按照零件需求量,进行几种零件的配套优选下料方案关键字:下料问题整数规划逐级优化1问题重述如何更大程度的获得合理利润在当今这个以经济发展为核心的社会已经成了工厂实际生产中急需解决的问题,其中原材料利用率低则是每个工厂所关心的重点问题。
因此有必要对原材料的利用方式进行讨论,找到更合理的使用方法。
本问题就以生产实践中遇到的材料剪裁问题为基础,以寻找消耗原材料最少的剪裁方式为目的,并通过一维、二维的多维度分析,以及使用频率对原材料价格的影响,通过多种合理的数学模型,找到更符合实际情况的最优剪裁方式。
2问题分析直接分析问题为为找到最好的几种剪裁方案,使得钢管数最少,余料尽可能少或余料最少,钢管数尽可能少,但在完成的过程中,我发现只要分配好了几种剪裁方案,用整数规划可以较容易的找到最省的下料方案,而遇到的困难是如何选择几种较优的剪裁模式,这就变成了问题的核心;而后面的几问基本上都是该问题的变形或推广,原理相似,价格问题只是切割问题中钢管数最少的加权处理,第二问是改变了衡量的单位,有长度变成了面积,可以由一维的情况推广解决3问题假设1.原材料在生产过程中除去剪裁方式造成的损耗外其他损耗为0,且生产后的钢管均符合要求2.剩余的原材料无法利用3.原材料中没有不合格品4.客户中途无退单情况5.运输过程中没有其它损耗6.原材料的增加费用只与使用频率有关,模式使用频率相同时,其产生的增加费用相同。
下料问题的优化设计
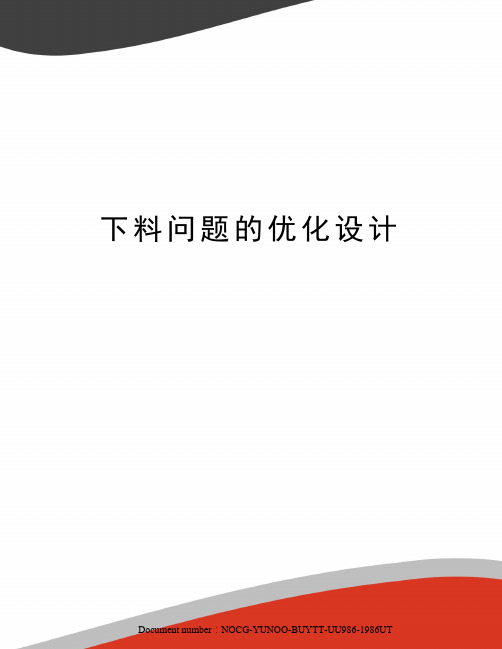
下料问题的优化设计 Document number:NOCG-YUNOO-BUYTT-UU986-1986UT题1、[下料问题的优化设计]某车间有一大批长130cm的棒料,根据加工零件的要求,需要从这批棒料中成套截取70cm长的毛坯不少于100根,32cm 长的毛坯不少于100根,35cm长的毛坯不大于100根。
要求合理设计下料方案,使剩下的边角料总长最短。
根据题目意义,运用优化设计理论和方法,完成设计全过程;工程问题分析:数学模型建立及特征分析:优化方法选择;优化程序设计(解析优化);计算结果分析;结论及体会。
基于MATLAB一维优化下料问题分析0 前言生产中常会通过切割、剪裁、冲压等手段,将原材料加工成所需大小零件,这种工艺过程,称为原料下料问题。
在生产实践中,毛坯下料是中小企业的一个重要工序。
怎样减少剩余料头损失是节约钢材、降低产品成本、提高企业经济效益的一个重要途径。
在毛坯下料中我们常会遇到毛坯种类多、数量大的情况,如不进行周密计算则因料头而造成的钢材损失是相当可观的。
为使料头造成的钢材损失减少到最小程度,我们可依据预定的目标和限制条件统筹安排,以最少的材料完成生产任务。
1 一维优化下料问题的具体模型分析设原材料长度为L,数量充足。
需要切割成n(n≥0)种不同规格的零件,根据既省材料容易操作的原则,人们已经设计好了n种不同的下料方式,设第j种下料方式中可下得第i种零件ij a个,又已知第i种零件得需要量为i b个, j x表示第B种下料方式所消耗得零件数目, j c表示第j B种下料方式所得余料(j=1, j2 , , n, j x∈ Z)。
满足条件的切割方案有很多种,现在要求既满足需要又使所用原材料数量最少,即最优下料方案满足:μp=min (∑j c j x)约束条件:∑ij a j x=i b,j x∈Z。
线性规划数学模型根据线性规划算法,约束条件包括两部分:一是等式约束条件,二是变量的非负性。
一类优化下料数学模型存在的问题及对策

一类优化下料数学模型存在的问题及对策优化下料是传统制造行业最为实用的算法之一,随着技术的进步,已被广泛地应用到工厂中,在其中,一类优化下料数学模型(CO-Packing)特别被广泛采用,其目的在于最小化原材料的废弃,减少产品成本,并且能够满足客户的要求。
然而,目前一类优化下料数学模型也存在着许多问题,损害了其在行业的应用。
首先,由于一类优化下料数学模型的求解过程极其耗费时间,无法在实际生产过程中得到及时的解决,从而导致产品的滞后性问题,给企业造成不良的影响。
其次,一类优化下料数学模型不具备良好的扩展性,不能有效解决更复杂的问题,也限制了其应用范围。
最后,由于一类优化下料数学模型不能实时响应产品的变化,在实际应用时,容易出现产品设计缺陷带来的质量问题,无法满足客户的需求。
针对上述存在的问题,应采取一系列对策,以最大化CO-Packing 模型的运用。
首先,采用智能计算技术,消除一类优化下料数学模型的求解耗费的时间,使其能够更快的响应生产需求,提高产品质量。
其次,采用可扩展的算法,可以有效求解复杂问题,增加CO-Packing 模型的应用范围。
最后,通过实时监测数据,快速调整CO-Packing模型,实现系统的最优化,提高产品的质量,满足客户的要求。
综上,一类优化下料数学模型CO-Packing是一类非常重要的技术,用于简化任务的复杂度,为企业带来更多的利润。
然而,它也存在许多问题,需要采取一系列的对策以解决。
可以采用智能计算技术以及可扩展的算法,通过实时数据监测调整CO-Packing模型,使其能够更加及时、有效地响应生产需求,达到最佳结果。
只有实施这些措施,才能充分发挥一类优化下料数学模型CO-Packing的优势,使其在企业中得到更广泛的应用。
下料问题的解法

有交货时间限制的大规模实用下料问题朱珠,王辉,张志敏指导老师:鲁习文(华东理工大学理学院数学系,上海200237)摘要:本文讨论了有交货时间限制的大规模单一原材料下料问题。
对于一维下料问题,本文提出一种新的算法:DP 贪婪算法。
在一维的基础上建立了二维的求解模型,运用降维思想结合一维的DP 贪婪算法,给出解决该模型的算法。
数值计算结果表明该算法对大规模下料问题是有效的。
关键词:下料问题,DP ,贪婪算法 1、问题描述单一原材料下料问题. 设这种原材料呈长方形,长度为L ,宽度为W ,现在需要将一批这种长方形原料分割成m 种规格的零件, 所有零件的厚度均与原材料一致,但长度和宽度分别为),(,),,(11m m w l w l ,其中m i W w L l w i i i ,,1,, =<<<。
m 种零件的需求量分别为m n n ,,1 。
下料时,零件的边必须分别和原材料的边平行。
这类问题在工程上通常简称为二维下料问题。
特别当所有零件的宽度均与原材料相等,即m i W w i ,,1, ==,则问题称为一维下料问题。
一个好的下料方案是在生产能力容许的条件下,以最少数量的原材料,尽可能按时完成需求任务, 同时下料方式数也尽量地小.2、一维下料问题2.1 模型假设在充分了解并分析了实际情况后,我们对一维下料问题提出如下假设:(1)每天下料的数量受到企业生产能力的限制,在未完成需求任务前,每天下料的数量等于最大下料能力。
(2)每个切割点处由于锯缝所产生的损耗不可忽略。
(3)增加一种下料方式大致相当于使原材料总损耗增加%08.0。
(4)每种零件有各自的交货时间,若某零件无交货时间,则记该零件交货时间为无穷大。
2.2 一维单一原材料实用下料问题的模型根据公司要求,目标是既要所用材料最少,也要下料方式少。
记m :零件种类总数,i x :第i 种下料方式下料的根数,k :下料方式的种类数,:i δ第i 种下料方式的余料。
作业3: 钢筋下料最优化原理分析(配图222)
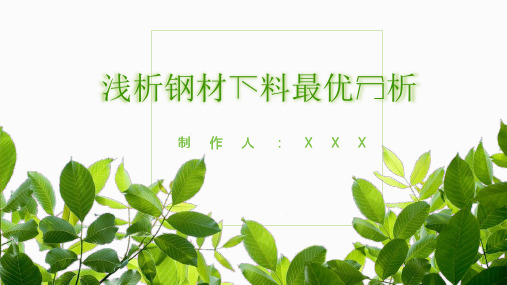
2
钢筋下料最优化原理的数学模型
2、钢筋下料最优化原理的数学模型
数学规划模型是运筹学的重要内容,它的研究对象是在管理工作中有关安排和 估值的问题,解决的主要问题是在给定条件下,按照某一衡量指标来寻求安排的最 优方案⑶.它的主要研究内容是如何在有限的人力、物力和财力等资源条件下,合 理地分配和有效地使用资源,得到问题的最优方案(如产品的产量最多、生产成本 最小、产品收益最高、消耗资源最少等)的优化方法.数学规划模型的一般形式为
2、钢筋下料最优化原理的数学模型 其中x = ( x1,x2,…,x n) T是决策变量向量,f( x) 称为目标函数,符号opt 表示 对函数f( x) 求最优化结果. 如果要求f( x) 的最大值,则opt f( x) 记为max f( x) ; 如果要 求f( x) 的最小值,则opt f( x) 记为min f( x) .gi( x) 和hj( x) 称为约束函数. 符号 s. t. 是受约束于m 个不等式约束gi( x) ≤0( i = 1,2,……,m) ,以及l个等式约束 hj( x) = 0( j = 1,2,……,l) .
浅析钢材下料最优分析
制 作 人 : X X X
一、钢筋下料最优化问题的提出ຫໍສະໝຸດ 目录Content
又 是 一 年 蝉 鸣 时
二、钢筋下料最优化原理的数学模型
三、钢筋下料最优化原理算例及路线选择
1
钢筋下料最优化问题的提出
1.1、钢筋下料最优化问题的意义 钢筋混凝土结构在建筑工程中被广泛应 用.钢筋由于具有强韧性和可弯曲的特点, 无法被其它的材料所替代,在建筑结构中发 挥着重要的作用.随着建筑规模的不断扩大, 钢筋成为建筑结构的核心组成部分,并推动 建筑结构不断向深度、高度、广度发展.同 时,施工企业承包的工程项目能否获得利润, 在很大程度上取决于是否对工程的成本进 行了有效的控制.由于钢筋的单位成本较高, 且用量大,钢筋造价在土建中大约占总成 本的30% -40%左右,是建筑施工管理过程中 成本控制的主要环节,也是决定一个项目能 否获得经济效益的关键因素。
下料问题的基本建模方法
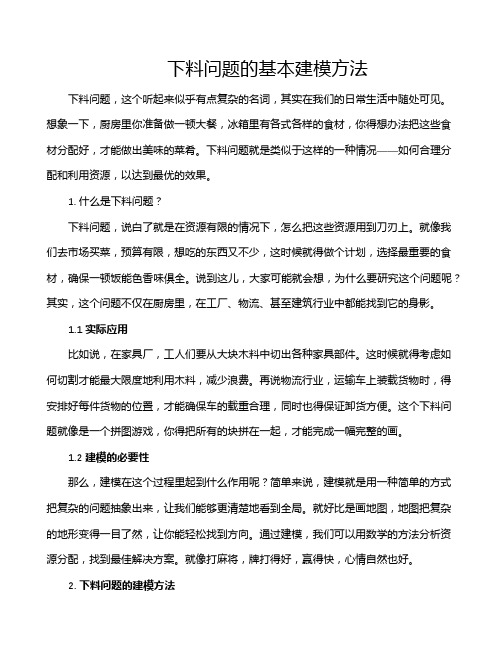
下料问题的基本建模方法下料问题,这个听起来似乎有点复杂的名词,其实在我们的日常生活中随处可见。
想象一下,厨房里你准备做一顿大餐,冰箱里有各式各样的食材,你得想办法把这些食材分配好,才能做出美味的菜肴。
下料问题就是类似于这样的一种情况——如何合理分配和利用资源,以达到最优的效果。
1. 什么是下料问题?下料问题,说白了就是在资源有限的情况下,怎么把这些资源用到刀刃上。
就像我们去市场买菜,预算有限,想吃的东西又不少,这时候就得做个计划,选择最重要的食材,确保一顿饭能色香味俱全。
说到这儿,大家可能就会想,为什么要研究这个问题呢?其实,这个问题不仅在厨房里,在工厂、物流、甚至建筑行业中都能找到它的身影。
1.1 实际应用比如说,在家具厂,工人们要从大块木料中切出各种家具部件。
这时候就得考虑如何切割才能最大限度地利用木料,减少浪费。
再说物流行业,运输车上装载货物时,得安排好每件货物的位置,才能确保车的载重合理,同时也得保证卸货方便。
这个下料问题就像是一个拼图游戏,你得把所有的块拼在一起,才能完成一幅完整的画。
1.2 建模的必要性那么,建模在这个过程里起到什么作用呢?简单来说,建模就是用一种简单的方式把复杂的问题抽象出来,让我们能够更清楚地看到全局。
就好比是画地图,地图把复杂的地形变得一目了然,让你能轻松找到方向。
通过建模,我们可以用数学的方法分析资源分配,找到最佳解决方案。
就像打麻将,牌打得好,赢得快,心情自然也好。
2. 下料问题的建模方法下料问题的建模方法其实有很多,常见的有线性规划、动态规划等。
听起来像是数学课上那些让人头疼的公式,但其实它们都能帮助我们找到最佳的解决方案。
2.1 线性规划先说线性规划吧。
这是一个非常经典的建模方法。
简单地说,线性规划就是把我们的资源和需求用数学式子表示出来,然后通过求解这些方程,找出最优解。
就像是给自己定了一个目标,要在最短的时间内把所有的食材都切好。
只要好好规划,你就能把厨房变成一个高效的“生产线”。
钢管下料优化方案
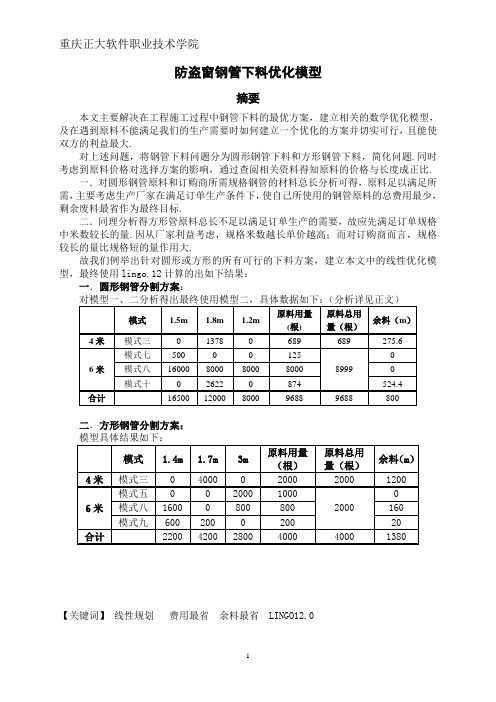
防盗窗钢管下料优化模型摘要本文主要解决在工程施工过程中钢管下料的最优方案,建立相关的数学优化模型,及在遇到原料不能满足我们的生产需要时如何建立一个优化的方案并切实可行,且能使双方的利益最大.对上述问题,将钢管下料问题分为圆形钢管下料和方形钢管下料,简化问题.同时考虑到原料价格对选择方案的影响,通过查阅相关资料得知原料的价格与长度成正比.一.对圆形钢管原料和订购商所需规格钢管的材料总长分析可得,原料足以满足所需,主要考虑生产厂家在满足订单生产条件下,使自己所使用的钢管原料的总费用最少,剩余废料最省作为最终目标.二.同理分析得方形管原料总长不足以满足订单生产的需要,故应先满足订单规格中米数较长的量.因从厂家利益考虑,规格米数越长单价越高;而对订购商而言,规格较长的量比规格短的量作用大.故我们例举出针对圆形或方形的所有可行的下料方案,建立本文中的线性优化模型,最终使用lingo.12计算的出如下结果:一.圆形钢管分割方案:对模型一、二分析得出最终使用模型二,具体数据如下:(分析详见正文)模式 1.5m 1.8m 1.2m 原料用量(根)原料总用量(根)余料(m)4米模式三0 1378 0 689 689 275.66米模式七500 0 0 12589990 模式八16000 8000 8000 8000 0 模式十0 2622 0 874 524.4合计16500 12000 8000 9688 9688 800二.方形钢管分割方案:模型具体结果如下:模式 1.4m 1.7m 3m 原料用量(根)原料总用量(根)余料(m)4米模式三0 4000 0 2000 2000 12006米模式五0 0 2000 100020000 模式八1600 0 800 800 160 模式九600 200 0 200 20合计2200 4200 2800 4000 4000 1380 【关键词】线性规划费用最省余料最省 LINGO12.0一.问题的提出某不锈钢装饰公司承接了一住宅小区的防盗窗安装工程,为此购进了一批型号为304的不锈钢钢管,分为方形管和圆形管两种,具体数据如下表:表1-1规格长4m 长6m方形管25×25×1.2(mm) 5000根9000根圆形管Φ19×1.2(mm) 2000根2000根根据小区的实际情况,需要截取钢管的规格与数量如下:表1-2圆形管规格 1.5m 1.8m 1.2m 方形管规格 1.4m 1.7m 3m 数量(根)16500 12000 8000数量(根)6000 4200 2800根据上述的实际情况建立数学模型,寻找经济效果最优的下料方案,使得厂家在满足订购商的订单需要的同时还能节约原料.二.问题的分析通过题目可知,要求我们在题目所给定的条件下,找寻最佳下料方案,使满足各种需要的前提下所使用的原材料的费用、所使用的量和所剩的余料最省.圆形钢管原材料的总长:()45000+69000=74000 m⨯⨯,订单产品的总长:()1.516500+1 .812000+1.28000=55950m⨯⨯⨯.方形钢管原材料的总长:()42000+ 62000=20000m⨯⨯,订单产品的总长:()1.46000+1.74200+32800=23940m⨯⨯⨯.通过计算,分析得出问题中的圆形钢管原料足够多,在使用时主要考虑所使用的原材料的费用、使用量和切割之后的余料最少;而方形管的原材料明显不能满足生产需要,此时应首先考虑切割不同长度的钢管的优先问题.通过查阅网络资料可得网络上对于304不锈钢钢管的单价是50元/公斤,而相应的不锈钢管重量公式:⨯⨯外径-壁厚)壁厚]0.0249每米的重量(千克/米)[(=又因为在我们的原材料中,规格都为Φ19×1.2(mm),所以可得每米的重量都是一定的,故我们可以得到每根钢管的单价与原材料的长度成正比,比例系数为k,即6米管的单价是6k,4米的单价是4k,所以6米管的单价是4米管的6k/4k=1.5倍.因此在处理这个问题时对于生产厂家而言,应考虑所生产的成品规格越长利益越大;对于订购商而言,规格长度越大材料的使用性越大.通过上诉分析可得,应该在原有材料使用完的情况下先满足规格为3米的钢管,其次是1.7米的钢管,再次生产1.4米的钢管.然而此类问题属于数学中最优解的求解问题,这是典型的线性优化,故该问题可以建立线性优化方程解决.三.模型假设1.假设钢管切割过程中无原料损耗或损坏;2.假设所生产的各种规格的钢管不能通过焊接产生;3.假设同种钢管采用的切割模式数量不限;4.假设每种钢管的单价相同且与长度成正比.四.符号说明x表示采用第i种模式下切割的钢管数id表示第i中模式下的第j种规格下的根数ijc表示第i种模式下的余料ia表示第j种规格的需求量jy表示使用4米的原料所以使用的根数1y表示使用6米的原料所以使用的根数2y表示生产规格为1.5米的钢管总数3y表示生产规格为1.8米的钢管总数4y表示生产规格为1.2米的钢管总数5y为满足生产需求产生的余料总和6k表示单位长度或者单位公斤数钢管原料的价格五.模型的建立与求解针对题目的要求我们将钢管下料方案分为圆形钢管和方形钢管两类,简化问题,并建立相关数学模型.首先根据题目已知条件可得要先给4米和6米不同规格的原材料进行分割,因此产生了不同的切割模式,选取最佳切割模式才是所要求的下料方案.其中切割所剩的余料必须小于所需切割的最小长度,在条件满足的不同组合的情况下,得知圆形管的切割方案有17种;方形钢管的切割方案有11种,具体切割方案如下:5.1 圆形钢管5.1.1圆形钢管的切割方案表5-1模式 1.5m 1.8m 1.2m 余料(m) 圆形`4 米 切 割 模 式模式一 0 0 3 0.4 模式二 2 0 0 1 模式三 0 2 0 0.4 模式四 0 1 1 1 模式五 1 0 2 0.1 模式六 1 1 0 0.7 6 米 切 割 模 式模式七 4 0 0 0 模式八 2 1 1 0 模式九0 0 5 0 模式十 0 3 0 0.6 模式十一 0 1 3 0.6 模式十二 1 0 3 0.9 模式十三 1 2 0 0.9 模式十四 0 2 2 0 模式十五 3 0 1 0.3 模式十六 2 0 2 0.6 模式十七1120.35.1.2圆形钢管的下料模型建立针对圆形管的切割方案,我们假设原材料采用模式i 切割的数量为x i (x i 必须为大于1的正整数),那么目标函数即为使生产厂家在完成订单需要的情况下所使用的原材料最少,同时所使用的原料的费用最少,且又因6米管的原料单价是4米管的1.5倍,所以目标函数是:min z (4)+1.5(6)k k =⨯⨯原料中米的总根数原料中米的总根数又由已知条件可得,所生产的量必须满足订购商的需要,即1.5m 圆管16500根,1.8m 圆管12000根,1.2m 圆管8000根,因此产生以下三个目标函数的约束条件:≤生产规格中所有的1.5米的总根数16500 ≤生产规格中所有的1.8米的总根数12000 8000≤生产规格中所有的1.2米的总根数因此可得如下数学模型:617176117717117311min k 1.550009000..0()i ii i i i i i i ii ij i j i j z x k x x x S T x x d x a ========+⎧≤⎪⎪⎪≤⎪⎪⎨⎪≥⎪⎪⎪≥⎪⎩∑∑∑∑∑∑∑为整数 利用lingo12.0编程运算得出最终结果如下表:(程序代码详见附录1)表5-2模式 1.5 1.8 1.2 原料用量 原料总用量 余料 4米模式三 0 1378 0 689 689275.6 6米模式七500 0 0 125 8999 0 模式八 16000 8000 8000 8000 0 模式十0 2622 0 874 524.4 合计1650012000800096889688 800且对于模型中钢管每米的单价k 进行不同程度改变,得知k 的值不会影响生产过程中我们对模式的选择,只会相应的改变原料成本,影响相应的利润.通过对上表的结果进行分析得,该模型已经满足生产不同规格钢管的需要,且没有多余的生产量,但该模型只考虑到所用的原料费用最省,不一定满足所要求的生产订单过后的余料最省,也就是不一定满足原料的使用率最大,故我们对模型进一步优化检验,把目标函数变为:min z 4(4)+6(6=⨯⨯⨯原料中米的总根数原料中米的总根数) -(订单中所有规格长)(订单中相应规格的根数)最终可得模型如下:617176117717117311min 465595050009000..0()i i i i i i i i i ii ij i j i j z x x x x s t x x d x a ========+-⎧≤⎪⎪⎪≤⎪⎪⎨⎪≥⎪⎪⎪≥⎪⎩∑∑∑∑∑∑∑为整数同样用lingo12.0编程运算得出结果如下:(程序代码详见附录2)表5-3模式 1.5m 1.8m 1.2m 原料用量(根) 原料总用量(根) 余料(m ) 4米模式三 0 1378 0 689 689275.6 6米模式七500 0 0 125 8999 0 模式八 16000 8000 8000 8000 0 模式十0 2622 0 874 524.4 合计1650012000800096889688 800从表一和表二相应结果可得,两张表结果一模一样.相应的证明了该切割方案是最优的切割方案,同时也满足最初的假设,即生产厂家在完成订购商的订单需要的情况下,原材料的使用最少,所产生的费用最少,并在生产过程种产生的废料最少,废料的总和才800米,同时也满足原料的使用率最大.故最佳的切割方案是使用用689根4米的原材料采用模式三进行切割,125根6米的原材料采用模式七进行切割,8000根6米的原材料采用模式八进行切割,874根6米的原材料采用模式十进行切割.5.2 方形钢管5.2.1方形钢管的切割方案表5-4模式 1.4m 1.7m 3m 余料(m)方形管4米切割模式模式一0 0 1 1模式二 2 0 0 1.2模式三0 2 0 0.6模式四 1 1 0 0.96米切割模式模式五0 0 2 0模式六 4 0 0 0.4模式七0 3 0 0.9模式八 2 0 1 0.2模式九 3 1 0 0.1模式十 1 2 0 1.2模式十一0 1 1 1.35.2.1方形钢管余料最少由于方型钢管所能提供的原材料远远不能满足生产所需,该情况下,如果还继续限制所用的材料,那么我们就无法满足生产方管的订单需要.根据问题分析中原材料的单价与它的长度成正比,并对于生产厂家而言,成品规格越长利益越大;对于订购商而言,规格长度越大材料的使用性越大.又因为:方管的总量为:42000+62000=20000m⨯⨯(),方管中的规格为1.7米和3米的钢管总长为:1.74200+32800=15540m⨯⨯().所以得出方管足以满足生产规格为3米和1.7米的钢管,即严格要求生产规格为3米和1.7米的钢管,对于规格为1.4米的钢管实在无法满足需要,只限制它的量必须大于0即可.故可得:3=2800生产出的规格为米的总根数1.7=4200生产出的规格为米的总根数1.4生产出的规格为米的总根数>0又因为总量本身不够生产,所以要求方管的所有材料必须用于生产,所以可得:=原料方管中所使用的4米的总根数2000综上分析可得关于余量最省的优化数学模型如下:()1114111511111312111111min 20002000..00i ii i i i i i i ij i j i j i i i x c x x S T x d x a d x a a ========⎧=⎪⎪⎪=⎪⎪⎪⎪≥⎨⎪⎪=⎪⎪⎪⎪≥=⎪⎩∑∑∑∑∑∑∑同样使用lingo12.0软件编程运算得出如下结果:(程序代码详见附录3) 表5-5模式 1.4m 1.7m 3m原料用量(根) 原料总用量(根) 余料(m )4米 模式三0 4000 0 2000 20001200 6米 模式五0 2000 1000 2000 0 模式八 16000 800 800 160 模式九600 200 0 200 20 合计22004200280040004000 1380对模型结果分析可得,该切割方案已是最优,没有成品钢管的浪费,又能满足生产厂家利润最大,同时还能满足订购商的长料利用率较大.并且在生产过程中总共产生1380米废弃材料.因此最优切割方案是用2000根4米的原材料采用模式三进行切割,1000根6米的原材料采用模式五进行切割,800根6米的原材料采用模式八进行切割,200根6米的原材料采用模式九进行切割.六.模型的分析与推广通过线性规划的应用,可以更好的求解一定约束条件下的最优值的求解问题,能够得出最佳合理的答案.同时线性规划对实际问题的分析与应用较为普遍,容易查找相关资料,同时可见其适于现实问题的求解,例如:对水管的下料,钢材的切割,电线的切割等,优化之后还能解决玻璃的切割问题等等.同时枚举法的运用是问题的求解思路更清晰的呈现,此为该模型的优点.但是切割模式较多,枚举法加大了运算量同时导致问题的解答相对繁杂,也是该模型的明显缺点.参考文献:[1] 颜文勇,数学建模,高等教育出版社,2011.6[2] 谢金星、薛毅,优化建模与LINDO/LINGO软件,北京,清华大学出版社,2009.12[3] /view/1266775.htm(钢管每米重量计算公式)附录附录1:MODEL:MIN=k*(X1+X2+X3+X4+X5+X6)+1.5*k*(X7+X8+X9+X10+X11+X12+X13+X14+X15+X16+X17);k=50;2*X2+X5+X6+4*X7+2*X8+X12+X13+X17>=16500;2*X3+X4+X6+X8+3*X10+X11+2*X13+2*X14+X17>=12000;X4+2*X5+X8+5*X9+3*X11+3*X12+X15+2*X16+2*X17>=8000; X1+X2+X3+X4+X5+X6<=5000;X7+X8+X9+X10+X11+X12+X13+X14+X15+X17<=9000;y1=x1+x2+x3+x4+x5+x6; !y1是使用4米长的原料所用的根数;y2=x7+x8+x9+x10+x11+x12+x13+x14+x15+x17; !y2是使用6米长的原料所用的根数;y3=2*x2+x5+x6+4*x7+2*x8+x12+x13+3*15+2*16+x17; !y3是切得规格为1.5米钢管的总数;y4=2*x3+x4+x6+x8+3*x10+x11+2*x13+2*x14+x17;!y4是切得规格为1.8米钢管的总数;y5=x4+2*x5+x8+5*x9+3*x12+3*x11+2*14+x15+2*x16+2*x17;!y5是切得规格为1.2米钢管的总数;y6=x1*0.4+x2+x3*0.4+x4+x5*0.1+x6*0.7+x7*0+x8*0+x9*0+x10*0.6+x11*0.6+x12*0.9+x13*0.9+x14*0+x15*0.3+x16*0.6+x17*0.3;!为满足生产需求产生的余料总和;@GIN( X1); @GIN( X2); @GIN( X3); @GIN( X4); @GIN( X5); @GIN( X6); @GIN( X7);@GIN( X8); @GIN( X9); @GIN( X10); @GIN( X11); @GIN( X12); @GIN( X13);@GIN( X14); @GIN( X15); @GIN( X16); @GIN( X17);END附录2:MODEL:MIN=4*X1+4*X2+4*X3+4*X4+4*X5+4*X6+6*X7+6*X8+6*X9+6*X10+6*X11+6*X12+6*X13+6*X14+6*X15+6*X16+6*X17-55950; 2*X2+X5+X6+4*X7+2*X8+X12+X13+X17>=16500;2*X3+X4+X6+X8+3*X10+X11+2*X13+2*X14+X17>=12000;X4+2*X5+X8+5*X9+3*X11+3*X12+X15+2*X16+2*X17>=8000; X1+X2+X3+X4+X5+X6<=5000;X7+X8+X9+X10+X11+X12+X13+X14+X15+X17<=9000;y1=x1+x2+x3+x4+x5+x6; !y1是使用4米长的原料所用的根数;y2=x7+x8+x9+x10+x11+x12+x13+x14+x15+x17; !y2是使用6米长的原料所用的根数;y3=2*x2+x5+x6+4*x7+2*x8+x12+x13+3*15+2*16+x17; !y3是切得规格为1.5米钢管的总数;y4=2*x3+x4+x6+x8+3*x10+x11+2*x13+2*x14+x17;!y4是切得规格为1.8米钢管的总数;y5=x4+2*x5+x8+5*x9+3*x12+3*x11+2*14+x15+2*x16+2*x17;!y5是切得规格为1.2米钢管的总数;y6=x1*0.4+x2+x3*0.4+x4+x5*0.1+x6*0.7+x7*0+x8*0+x9*0+x10*0.6+x11*0.6+x12*0.9+x13*0.9+x14*0+x15*0.3+x16*0.6+x17*0.3;!为满足生产需求产生的余料总和;@GIN( X1); @GIN( X2); @GIN( X3); @GIN( X4); @GIN( X5); @GIN( X6); @GIN( X7);重庆正大软件职业技术学院@GIN( X8); @GIN( X9); @GIN( X10); @GIN( X11); @GIN( X12); @GIN( X13);@GIN( X14); @GIN( X15); @GIN( X16); @GIN( X17);END附录3:MODEL:MIN=4*X1+4*X2+4*X3+4*X4+4*X5+4*X6+6*X7+6*X8+6*X9+6*X10+6*X11+6*X12+6*X13+6*X14+6*X15+6*X16+6*X17-55950; 2*X2+X5+X6+4*X7+2*X8+X12+X13+X17>=16500;2*X3+X4+X6+X8+3*X10+X11+2*X13+2*X14+X17>=12000;X4+2*X5+X8+5*X9+3*X11+3*X12+X15+2*X16+2*X17>=8000; X1+X2+X3+X4+X5+X6<=5000;X7+X8+X9+X10+X11+X12+X13+X14+X15+X17<=9000;y1=x1+x2+x3+x4+x5+x6; !y1是使用4米长的原料所用的根数;y2=x7+x8+x9+x10+x11+x12+x13+x14+x15+x17; !y2是使用6米长的原料所用的根数;y3=2*x2+x5+x6+4*x7+2*x8+x12+x13+3*15+2*16+x17; !y3是切得规格为1.5米钢管的总数;y4=2*x3+x4+x6+x8+3*x10+x11+2*x13+2*x14+x17;!y4是切得规格为1.8米钢管的总数;y5=x4+2*x5+x8+5*x9+3*x12+3*x11+2*14+x15+2*x16+2*x17;!y5是切得规格为1.2米钢管的总数;y6=x1*0.4+x2+x3*0.4+x4+x5*0.1+x6*0.7+x7*0+x8*0+x9*0+x10*0.6+x11*0.6+x12*0.9+x13*0.9+x14*0+x15*0.3+x16*0.6+x17*0.3;!为满足生产需求产生的余料总和;@GIN( X1); @GIN( X2); @GIN( X3); @GIN( X4); @GIN( X5); @GIN( X6); @GIN( X7);@GIN( X8); @GIN( X9); @GIN( X10); @GIN( X11); @GIN( X12); @GIN( X13);@GIN( X14); @GIN( X15); @GIN( X16); @GIN( X17);END11。
优化设计复习题

优化设计复习题优化设计复习题在学习过程中,复习是非常重要的一环。
对于设计专业的学生来说,复习设计题目更是必不可少的一部分。
通过复习设计题目,可以巩固知识,提高设计能力,为将来的实践打下坚实的基础。
然而,如何优化设计复习题,使其更加有效,更加有针对性,成为了一个值得探讨的问题。
首先,设计复习题的内容应该全面而有深度。
设计专业的知识点众多,涵盖面广,因此在设计复习题的编写上,应该尽量涵盖各个方面的知识点。
例如,可以包括色彩搭配、构图原则、材料选择等方面的题目。
同时,对于每个知识点,也应该有不同难度的题目,既有基础题目用于巩固基础知识,也有拓展题目用于提高思维能力和创造能力。
其次,设计复习题的难度应该适中。
设计专业的学生在复习过程中,需要既能够巩固基础知识,又能够有所拓展。
因此,在设计复习题的编写上,应该注意难度的控制。
过于简单的题目可能无法起到巩固知识的作用,过于复杂的题目可能会让学生望而却步。
因此,应该根据学生的实际情况,合理设置题目的难度,使学生既能够轻松应对,又能够有所收获。
另外,设计复习题的形式应该多样化。
设计复习题不仅仅是纸上的文字题目,还可以包括图片题、实践题等形式。
通过多样化的形式,可以更好地激发学生的学习兴趣,提高学习效果。
例如,可以设计一些图片题目,要求学生根据给定的图片进行设计,从而锻炼学生的观察力和设计能力。
同时,还可以设计一些实践题目,要求学生亲自动手完成设计,从而将理论知识与实践能力相结合。
此外,设计复习题的答案应该详细解析。
对于设计复习题,仅仅提供答案是远远不够的。
学生在做题的过程中,可能会遇到一些困惑和疑问,需要有详细的解析来指导学生。
因此,在设计复习题的编写上,应该提供详细的答案解析,解释每个选项的含义和正确与否的原因。
这样,学生在做题的过程中,不仅能够得到正确答案,还能够理解答案的原因,加深对知识点的理解。
最后,设计复习题的数量应该适度。
设计专业的学生在复习过程中,需要花费大量的时间和精力进行实践和创作。
复杂下料问题的优化模型及求解方法研究

复杂下料问题的优化模型及求解方法研究xx年xx月xx日CATALOGUE目录•引言•复杂下料问题的数学模型•优化求解方法•实验与验证•结论与展望•参考文献01引言随着制造业的快速发展,下料问题已成为制约企业生产效率提高的关键因素之一。
在生产实践中,由于材料种类繁多、尺寸差异大、切割方式各异等因素,导致下料问题变得异常复杂和困难。
因此,研究复杂下料问题的优化模型及求解方法具有重要的现实意义。
意义阐述通过对复杂下料问题的深入研究,可以为企业提供更加精准的下料方案,提高原材料的利用率和生产效率,降低生产成本,同时也有助于推动制造业的数字化、智能化发展。
背景介绍研究背景与意义VS研究现状与问题现状概述目前,国内外学者已对下料问题进行了广泛的研究,提出了许多不同的优化模型和求解方法。
然而,在实际应用中,这些方法往往难以取得理想的效果,特别是在处理复杂下料问题时,存在着求解速度慢、求解精度低、鲁棒性差等问题。
存在的问题现有的优化模型和求解方法在下料问题中的主要问题包括:1)模型建立不够精确,导致求解结果与实际生产需求存在较大偏差;2)求解算法效率低下,无法在短时间内得出优化结果;3)对于复杂下料问题的处理能力不足,难以满足实际生产中的多样化需求。
本研究旨在解决复杂下料问题的优化模型及求解方法,主要研究内容包括:1)建立精确的数学模型,以提高模型的预测能力和鲁棒性;2)设计高效的求解算法,以提高求解速度和精度;3)结合实际生产需求,对模型和算法进行实验验证和性能评估。
本研究将采用理论分析和实验验证相结合的方法,具体包括:1)对复杂下料问题进行数学建模,建立相应的优化模型;2)设计相应的求解算法,包括遗传算法、模拟退火算法、蚁群算法等;3)通过实验验证和性能评估,对模型和算法进行优化和改进。
研究内容研究方法研究内容与方法02复杂下料问题的数学模型复杂下料问题是在满足一系列限制条件下,从给定的物料清单中选择最优的切割方案,以达到成本最低、材料浪费最少的目标。
《下料作业设计方案-2023-2024学年高中通用技术地质版》

《下料》作业设计方案一、教学目标:1. 理解下料的观点和作用;2. 掌握下料的基本原则和方法;3. 能够熟练进行下料的计算和实际操作;4. 提高学生的动手能力和实践能力。
二、教学内容:1. 下料的观点和作用;2. 下料的基本原则和方法;3. 下料的计算公式和实际操作技巧。
三、教学重点:1. 下料的基本原则和方法;2. 下料的计算公式和实际操作技巧。
四、教学难点:1. 下料的实际操作技巧;2. 下料计算公式的灵活运用。
五、教学方法:1. 讲授相结合的教学方法;2. 实例分析的教学方法;3. 教室讨论的教学方法;4. 实践操作的教学方法。
六、教学过程:1. 导入:通过展示一些实际工程中的下料案例,引导学生了解下料的重要性和作用;2. 观点讲解:介绍下料的观点和基本原则,让学生明白下料的基本原则是什么;3. 方法讲解:详细讲解下料的方法和计算公式,让学生掌握下料的基本技巧;4. 实例分析:通过实际案例分析,让学生了解如何应用下料的方法和原则进行计算;5. 练习操作:让学生进行实际的下料操作,提高他们的动手能力和实践能力;6. 总结反思:对本节课的内容进行总结和反思,帮助学生稳固所学知识。
七、教学资源:1. 教材《机械设计基础》;2. PowerPoint课件;3. 下料实例案例。
八、作业设计:1. 课后作业:让学生完成一些下料计算题目,稳固所学知识;2. 实践作业:让学生选择一个实际工程案例,进行下料计算和实际操作。
九、评判方式:1. 教室表现评判:根据学生在教室上的表现和回答问题的情况进行评判;2. 作业评判:根据学生完成的作业情况进行评判;3. 实践评判:根据学生的实际操作情况进行评判。
十、延伸拓展:1. 鼓励学生参与相关比赛和实践活动,提高他们的动手能力和实践能力;2. 组织学生参观一些工程实践现场,让他们了解下料在实际工程中的应用。
通过本节课的进修,置信学生们能够掌握下料的基本原则和方法,提高他们的动手能力和实践能力,为将来的工程实践打下坚实的基础。
一种输送带转载漏斗下料系统优化方案

一种输送带转载漏斗下料系统优化方案何晓涛㊀惠刚刚㊀肖龙飞广州港集团有限公司㊀㊀摘㊀要:针对输送带转载漏斗下料系统存在的物料拥堵㊁物料对设备冲击过大等问题,应用离散元仿真方法模拟系统的物理过程和运行状态,并依据仿真实验结果提出一种优化方案,对输送带头部漏斗㊁三通分料器㊁落煤溜管㊁开口处承接匙等开展优化设计㊂应用表明,该优化方案可提高系统的生产效率与稳定性,对提高输送带转载漏斗下料系统的整体性能具有技术参考价值㊂㊀㊀关键词:离散元仿真;输送带;漏斗Optimization Scheme for Feeding System of Conveyor Belt Transfer FunnelHe Xiaotao㊀Hui Ganggang㊀Xiao LongfeiGuangzhou Port Group Co.,Ltd.㊀㊀Abstract:Based on the problems of material congestion and excessive impact of materials on equipment in the feeding system of the conveyor belt transfer funnel,the discrete element simulation method is applied to simulate the physical process and operation state of the system.Based on the simulation experiment results,an optimization plan is proposed to optimize the design of the conveyor belt head funnel,tee distributor,coal chute,and opening receiving key.The application shows that this optimization scheme can improve the production efficiency and stability of the system,and has technical reference value for improving the overall performance of the conveyor belt transfer funnel feeding system.㊀㊀Key words:discrete element simulation;conveyor belt;funnel1㊀引言输送带转载漏斗下料系统作为一种常见的固体散货物料输送手段,广泛应用于物流㊁矿山㊁化工等领域㊂输送带转载漏斗连接流程上下游的输送带,实现物料的转向和分流㊂由于散货物料作业工况的复杂性㊁漏斗下料系统设计不合理等原因,在作业过程中,漏斗往往会存在物料拥堵㊁物料对设备冲击过大等问题,导致生产流程故障停止㊁物料洒漏㊁生产效率降低,装卸成本增加㊂因此需要对输送带转载漏斗下料系统进行优化设计㊂2㊀优化方案2.1㊀问题分析某港口煤矿装卸系统转载房漏斗为2个一通二分叉结构,给料输送带和受料输送带之间落差达到7.2m㊂原漏斗下料系统设计存在的主要问题表现为:在煤炭下落过程中,物料直接冲击漏斗面,导致漏斗衬板磨损加剧;给料输送带头部漏斗为方形结构,在锥角部位容易粘黏较湿的煤炭,继而缩小漏斗通径,导致漏斗物料拥堵甚至完全阻塞;下料溜管为方形直筒,物料通过溜管垂直落入受料输送带上,对受料输送带及其托辊承受强大而持续的冲击,加剧输送带跑偏和托辊的损坏,并在受料输送带上产生大量扬尘,煤炭颗粒因高坠产生剧烈弹跳现象,导致煤粒从输送带尾部洒漏,增加了人工清理量㊂2.2㊀优化目标与优化步骤(1)优化目标根据煤炭的颗粒特性,优化系统构造,以控制物料流动的方向和速度,使漏斗在使用过程中保持畅通,避免漏斗体和受料输送带承受剧烈冲击㊂(2)优化步骤①对煤炭物料的颗粒特性进行测验㊂②对漏斗新的下料系统进行3D建模㊂③将煤炭物料颗粒模型数据㊁输送带参数㊁漏斗下料系统3D模型输入EDEM仿真软件,动态模拟漏斗下料系统的物料传送过程㊂④根据模拟仿真结果,对下料系统3D模型进一步修改优化㊂⑤进行漏斗的制作㊁安装和调试㊂41Port Operation㊀2024.No.2(Serial No.275)2.3㊀煤炭颗粒物料的材料模型测验为更好地进行EDEM 仿真模拟,需对煤炭颗粒的材料模型进行测验,如对煤炭颗粒堆积休止角进行测验,用于控制颗粒的堆积方式,从而模拟真实的煤炭堆积情况,反映散体颗粒群综合作用的宏观特征[1]㊂材料模型主要包括煤炭颗粒的密度㊁煤粒堆积角㊁含水量等对物料运动规律影响的参数㊂通过煤炭堆积密度测验㊁干燥箱含水率测试㊁振动式筛分仪尺寸分布测验㊁静动安息角测验等,得到煤炭颗粒的参数(见表1)㊂表1㊀煤炭颗粒的参数表参数名称煤炭颗粒参数堆积密度/(kg ㊃L -1)0.8~0.9静堆积角/ʎ45动堆积角/ʎ20含水量/%8~12粒度/m3~202.4㊀漏斗下料系统设计2.4.1㊀漏斗下料系统整体设计根据物料下落的抛物线特性使用曲面型漏斗设计方案㊂煤炭颗粒在曲面型漏斗的引导下,能够形成更为流畅的运动轨迹,避免物料在漏斗内堵塞和滞留,保证物料的连续输送,减轻物料对漏斗体和受料输送带的冲击负荷,有助于延长设备的使用寿命㊂曲面型漏斗具有较好的适应性,可以适用于多种煤炭颗粒的输送㊂对于不同颗粒大小和物理特性的煤炭物料,可通过调整曲面形状和角度来满足不同的需求㊂漏斗下料系统整体设计见图1㊂1.导液挡板㊀2.头部护罩㊀3.头部漏斗㊀4.三通㊀5.曲线落料管6.曲线落料管-纠偏箱㊀7.曲线落料管-纠偏卸料罩㊀8.承接匙图1㊀漏斗下料系统整体设计2.4.2㊀头部漏斗曲面导流挡板设计在给料输送带头部漏斗中安装曲面导流挡板,改变传统的漏斗衬板直接受冲击的方式,合理改变物料流的方向㊂新设计的导流挡板为3D 曲面结构,采用非常小的冲击角度调整物料运动轨迹,曲面结构能够收拢分散的物料,无锥角的设计可避免因煤颗粒粘黏而发生堵煤现象(见图2)㊂图2㊀3D 曲面导流挡板结构2.4.3㊀曲线溜管设计使用3D 曲线溜管设计,能有效控制煤炭物料流动速度和形态(见图3)㊂在溜管下端设置纠偏箱和调料挡板,可对末端料流进行方向调整,使之能够准确落在出口处的承接匙中㊂出口处3D 曲面物料承接匙的设计,确保将物料以较小冲击角度和速度差卸载到受料输送带上,并使煤炭的冲击方向与受料输送机运行方向相同,有效减少粉尘和冲击的产生,避免洒漏㊂下料过程中,不同落料高度会出现不同程度的落料不均匀现象,需将出料口落料高度设计在1m 以内[2]㊂3D 曲面溜管和承接匙设计能有效减少对受料输送机及其下方缓冲托辊的冲击,提升输送机的整体寿命㊂1.3D 曲线溜管㊀2.出口处3D 曲面承接匙图3㊀曲线溜管-出口承接匙设计2.5㊀仿真验证本方案中,使用ROCKY 三维离散单元法仿真软件,根据煤炭物料测验参数,模拟煤炭粒子组在输送机漏斗下料系统特定边界条件下的流动状况,包括物料的速度㊁轨迹和分布情况㊂该分析有助于识别潜在的问题,如物料堵塞㊁剧烈冲击㊁洒漏和粉尘生成等㊂通过仿真结果,可以评估漏斗下料系统的(下转第29页)51港口装卸㊀2024年第2期(总第275期)图7㊀传感器数据界面4㊀结语通过开发港口起重机运行状态监测平台,模拟起重机堆场作业流程,对起重机运行状态进行实时监测,评估起重机重要结构的健康状态,可提升码头工作人员的管理水平和管理效率㊂参考文献[1]㊀李娜,刘关四,王志杰,等.港口起重机械运行状态监测数据集成分析系统开发及应用[J].中国特种设备安全,2022,38(9):1-4+30.[2]㊀李毅,陈松.基于PLC 的起重机安监管理系统设计[J].电气时代,2021(7):24-27.[3]㊀李益波,肖炳林,何威誉,等.大数据驱动的港口机械状态监测平台研究[J].港口装卸,2020(1):1-5+48.唐现琼:411105,湖南省湘潭市雨湖区湘潭大学机械工程与力学学院收稿日期:2024-03-07DOI:10.3963/j.issn.1000-8969.2024.02.010(上接第15页)性能,并针对存在的问题进行优化设计,例如调整漏斗的形状㊁角度和尺寸,以改善物料的流动性和分布均匀性,优化溜管的设计,以减少物料的冲击和磨损,降低设备的维护量㊂将物料模型数据㊁优化设计的漏斗三维模型㊁输送带参数输入仿真软件并进行模拟验证,结果见图4㊁5㊂图4㊀BC34下BC36/BC37漏斗物料颗粒运动模拟仿真情况图5㊀BC33下BC36/BC37漏斗物料颗粒运动模拟仿真情况从图4和图5可以看出,煤炭物料以3.15m /s的速度均匀下料,正中落于承接匙中,并平缓进入受料输送带,漏斗下料系统的模型设计满足设计要求,表现出良好的性能特点㊂(1)物料在冲击点的表现符合设计目标,冲击角小于20ʎ,没有出现剧烈冲击或煤炭颗粒的严重反弹现象,可以有效地降低扬尘和洒漏,同时减轻漏斗体的磨损㊂(2)落料点与下方的受料输送机实现了对中,使得物料能够轻冲击地送料到受料输送带上,避免了落料不正和皮带跑偏的问题㊂(3)解决了锥角积料问题㊂通过3D 曲面挡板和溜管的设计,有效地避免了锥角粘黏煤炭颗粒继而缩小下料系统通径的问题,避免了堵料问题的发生㊂根据仿真验证得到最佳漏斗下料系统模型后,重新制作和安装了新的漏斗系统㊂重载调试结果显示,重建后下料系统的运行效果良好㊂漏斗下料系统溜管内㊁出口处的受料输送带受煤的冲击力减小,落料点集中在输送带中间无跑偏,洒漏量和粉尘也显著减少㊂3㊀结语优化后的输送带转载漏斗采用曲线下料系统设计,解决了漏斗易堵塞和设备承受剧烈冲击的问题,保证了装卸系统设备的平稳运行,减少了粉尘和洒漏的产生,提高了煤炭输送设备的寿命,在港口㊁矿场等行业具有推广意义㊂参考文献[1]㊀李艳洁,徐泳.用离散元模拟颗粒堆积问题[J].农机化研究,2005(2):57-59.[2]㊀许强.皮带输送机安装维护对跑偏问题的影响及处理措施[J].机械管理开发,2023(7):253-254.何晓涛:510100,广东省广州市越秀区东山口沿江东路406号收稿日期:2024-01-18DOI:10.3963/j.issn.1000-8969.2024.02.00692港口装卸㊀2024年第2期(总第275期)。
优化模型 下料问题
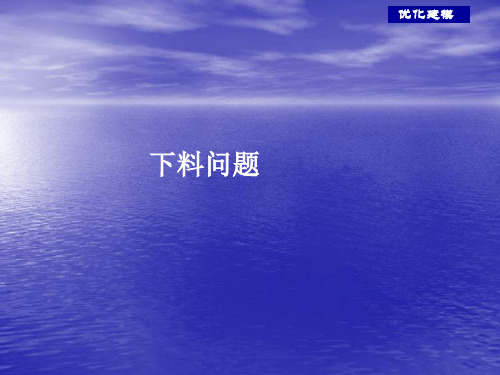
Reduced Cost 1.000000 1.000000 1.000000 0.000000 0.000000 0.000000 0.000000 0.000000 0.000000 0.000000 0.000000 0.000000 0.000000 0.000000 0.000000
优化建模
优化建模
模型求解
1. 将(32),(34)~(36)构成的整数线性规划模型 (加上整数约束)输入LINDO如下: Title 钢管下料 - 最小化余量 Min 3x1 + x2 + 3x3 + 3x4 + x5 + x6 + 3x7 s.t. 4x1 + 3x2 + 2x3 + x4 + x5 >= 50 x2 + 2x4 + x5 + 3x6 >= 20 x3 + x5 + 2x7 >= 15 end gin 7
优化建模
表5-3 钢管下料的合理切割模式
4米钢管根数 6米钢管根数 8米钢管根数 余料(米) 4 0 0 3 3 1 0 1 2 0 1 3
模式1 模式2 模式3 模式4 模式5 模式6 模式7
1 1 0 0
2 1 3 0
0 1 0 2
3 1 1 3
优化建模
问题化为在满足客户需要的条件下,按照哪些种合 理的模式,切割多少根原料钢管,最为节省。而 所谓节省,可以有两种标准,一是切割后剩余的 总余料量最小,二是切割原料钢管的总根数最少。 下面将对这两个目标分别讨论。
优化建模
Variable Value X1 10.00000 X2 10.00000 X3 8.000000 R11 2.000000 R12 3.000000 R13 0.000000 R21 1.000000 R22 0.000000 R23 0.000000 R31 1.000000 R32 1.000000 R33 0.000000 R41 0.000000 R42 0.000000 R43 2.000000
优化设计复习资料有答案
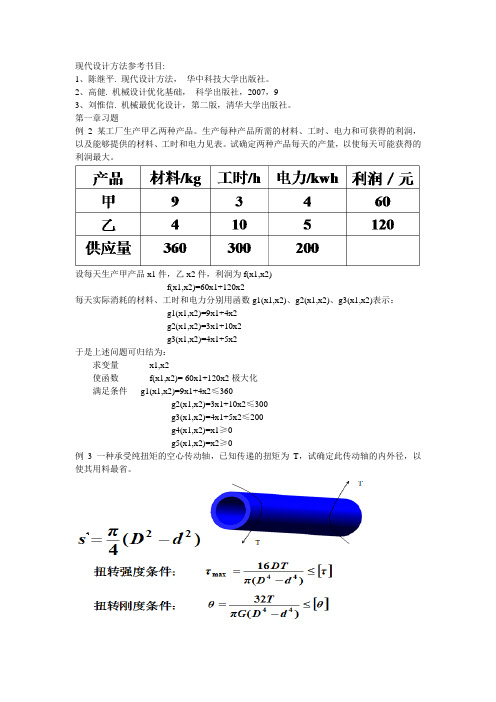
现代设计方法参考书目:1、陈继平. 现代设计方法,华中科技大学出版社。
2、高健. 机械设计优化基础,科学出版社,2007,93、刘惟信. 机械最优化设计,第二版,清华大学出版社。
第一章习题例2 某工厂生产甲乙两种产品。
生产每种产品所需的材料、工时、电力和可获得的利润,以及能够提供的材料、工时和电力见表。
试确定两种产品每天的产量,以使每天可能获得的利润最大。
设每天生产甲产品x1件,乙x2件,利润为f(x1,x2)f(x1,x2)=60x1+120x2每天实际消耗的材料、工时和电力分别用函数g1(x1,x2)、g2(x1,x2)、g3(x1,x2)表示:g1(x1,x2)=9x1+4x2g2(x1,x2)=3x1+10x2g3(x1,x2)=4x1+5x2于是上述问题可归结为:求变量x1,x2使函数f(x1,x2)= 60x1+120x2极大化满足条件g1(x1,x2)=9x1+4x2≤360g2(x1,x2)=3x1+10x2≤300g3(x1,x2)=4x1+5x2≤200g4(x1,x2)=x1≥0g5(x1,x2)=x2≥0例3 一种承受纯扭矩的空心传动轴,已知传递的扭矩为T,试确定此传动轴的内外径,以使其用料最省。
例: 求下列非线性规划优化问题优化设计的迭代算法1、下降迭代算法的基本格式 迭代公式基本原理:从某一初始设计开始,沿某个搜索方向以适当步长得到新的可行的设计,如此反复迭代,直到满足设计要求,迭代终止。
k k k SX X k 1α+=+S(k)——第k步的搜索方向,是一个向量; αk ——第k 步的步长因子,是一个数,它决定在方向S(k)上所取的步长大小。
简单的说:是一个搜索、迭代、逼近的过程。
最关键的是搜索的方向和步长。
迭代算法的基本步骤:1,选定初始点X(0),令k=0;2、在X(k)处选定下降方向S(k);,3、从X(k)出发沿S(k)一维搜索,找到X(k+1)=X(k)+αkS(k), 使得f(X(k+1))<f(X(k)); 令k=k+1,转(2)。
工程学问题下料最佳方案

工程学问题下料最佳方案工程学中的下料指的是将原材料按照设计要求进行切割、裁剪、加工等操作,以便制造出符合产品要求的零部件或产品。
下料的质量和效率直接影响着整个生产流程的顺利进行,因此如何选择最佳的下料方案成为工程学中的重要问题。
在选择下料方案时,需要考虑原材料的特性、产品的设计要求、生产设备的性能以及生产效率等因素。
本文将针对下料过程中的材料选择、下料方式、下料工艺和下料设备等方面进行探讨,以寻找最佳的下料方案。
一、材料选择1. 材料特性在下料过程中,材料的特性是影响下料方案选择的重要因素。
首先需要考虑材料的硬度、韧性、厚度、形状以及表面粗糙度等特性。
不同材料的特性会影响切割前的处理方式、切割工具的选择以及下料过程中的加工参数设定。
此外,材料的成本、可供性和环保性也需要考虑在内。
在选择下料方案时,需要综合考虑材料的特性和成本,以便为下料过程提供最佳的原材料选择。
2. 材料类型根据材料的类型不同,下料方案也会有所差异。
常见的材料类型包括金属材料、塑料材料、木材等。
不同类型的材料需要采用不同的下料工艺和设备,以确保下料过程的质量和效率。
在选择下料方案时,需要根据产品设计要求和生产设备的性能,综合考虑材料的类型,以寻找最佳的下料方案。
二、下料方式1. 切割方式在下料过程中,常见的切割方式包括火焰切割、等离子切割、激光切割、水切割、机械切割等。
不同的切割方式适用于不同类型的材料和产品,具有不同的优势和局限性。
火焰切割适用于钢铁等金属材料,具有成本低、加工速度快的优势;等离子切割适用于不锈钢、铝合金等特殊材料,具有高速切割和高精度的优势;激光切割适用于各种类型的材料,具有非接触式加工、高精度和高效率的优势;水切割适用于石材、陶瓷等非金属材料,具有无热变形、无污染和高精度的优势;机械切割适用于木材、塑料等材料,具有成本低、操作简单的优势。
在选择下料方式时,需要综合考虑材料的特性、产品的设计要求以及生产设备的性能,以寻找最佳的切割方式。
钢构件地优化排料问题

实用标准文档钢构件的优化排料问题1、问题的重述1.1 背景在当今激烈的市场竞争中, 降低生产成本、提高生产效率和增强对市场的应变能力, 是企业保持竞争力的主要实现手段。
在钢构件制造产品的生产过程中,依照产品零件尺寸从板料中截取大小适当的零件过程称之为排料,也称之为下料。
排料是钢构件制造的第一道工序。
在这道工序中,不同的排料方案具有不同的材料利用率,而原材料的利用率直接影响产品的成本。
材料费用是制造企业主要的生产成本, 一般占总成本的 60% ~ 80% , 在大批量生产中, 材料的利用率即使提高 1% , 所创造的经济效益也相当可观。
据调查,优化下料后,制造企业材料利用率可平均提高 5%~ 10%。
另外由于切割工艺的要求,切割只能实行“一刀切”的工艺(在整料或余料中,从一边的某点到另外一边某点的连线一次切割,但可以在切割下来的板料中再次切割)。
板材的利用率就是所有零件面积之和与在一刀切工艺后继续切割的那部分板材面积的比值。
1.2 问题对于第一问,对1张板料和若干规则形状零件,求如何在板料中摆放零件使其板料的利用率最高。
规则形状零件即指矩形零件。
其描述一般只需用矩形的长和宽。
规则形状零件的排料问题的实质是研究如何组合零件摆放问题,使得在整个原料上摆放大量的不同长和宽的零件产生的废料最少、整料和余料的利用率最高。
排放时,其零件间的搭接关系的处理相对容易,只需考虑长、宽两个因素(含预留的损耗量)。
板材大小:2350*900【1张】。
表1是九个规则形状零件的具体规格。
对于第二问,对1张板料和若干不规则形状零件,如何在板料中摆放零件使其板料的利用率最高。
与第一问类似,但是此时需要切割出来的零件不具有矩形般对边平行的条件,切割较为麻烦,同时可能会造成更多边角料的产生,降低板料的利用率。
图1和表2是题目要求的两种不规则零件的具体形状和规格。
板材大小:2380*1630 【1张】。
表2零件一二个数14 14图1零件一零件二对于第三问,考虑到实际的切割过程中,一张板料并不能满足所有零件的生产需求,故而要求设计对2张板料和若干规则形状零件,如何在板料中摆放零件使其板料的利用率最高。
- 1、下载文档前请自行甄别文档内容的完整性,平台不提供额外的编辑、内容补充、找答案等附加服务。
- 2、"仅部分预览"的文档,不可在线预览部分如存在完整性等问题,可反馈申请退款(可完整预览的文档不适用该条件!)。
- 3、如文档侵犯您的权益,请联系客服反馈,我们会尽快为您处理(人工客服工作时间:9:00-18:30)。
精品文档
题1、[下料问题的优化设计]某车间有一大批长130cm的棒料,根据加工零件的要求,需要从这批棒料中成套截取70cm长的毛坯不少于100根,32cm 长的毛坯不少于100根,35cm长的毛坯不大于100根。
要求合理设计下料方案,使剩下的边角料总长最短。
根据题目意义,运用优化设计理论和方法,完成设计全过程;工程问题分析:数学模型建立及特征分析:优化方法选择;优化程序设计(解析优化);计算结果分析;结论及体会。
基于MATLAB一维优化下料问题分析
0 前言
生产中常会通过切割、剪裁、冲压等手段,将原材料加工成所需大小零件,这种工艺过程,称为原料下料问题。
在生产实践中,毛坯下料是中小企业的一个重要工序。
怎样减少剩余料头损失是节约钢材、降低产品成本、提高企业经济效益的一个重要途径。
在毛坯下料中我们常会遇到毛坯种类多、数量大的情况,如不进行周密计算则因料头而造成的钢材损失是相当可观的。
为使料头造成的钢材损失减少到最小程度,我们可依据预定的目标和限制条件统筹安排,以最少的材料完成生产任务。
精品文档
+
+
1 一维优化下料问题的具体模型分析
设原材料长度为L,数量充足。
需要切割成n (n≥0)种不同规格的零件,根据既省材料容易操作的原则,人们已经设计好了n 种不同的下料方式,设第j 种下料方式中可下得第i 种零件
ij
a 个,又已知第i 种零件得需要量为i
b 个, j x
表示第
j
B 种下料方式所消耗得零件数目, j c
表示第
j
B 种下料方式所得余料(j=1, 2 ,
⋯, n, j x
∈ Z)。
满足条件的切割方案有很多种,现在要求既满足需要又使所用原材料数量最少,即最优下料方案满足:μp=min (∑j c j
x )约束条
件:∑
ij a j x =i
b ,j x
∈Z 。
1.2 线性规划数学模型
根据线性规划算法,约束条件包括两部分:一是等式约束条件,二是变量的非负性。
出变量的非负要求外,还有其他不等式约束条件,可通过引入松弛变量将不等式约束化成等式约束形式。
如果是求最大值的,则松弛模型最优解对应的目标函数值必大于或等于整数规划最优解对应的目标函数值;如果问题是求最小值,则松弛模型最优解对应的目标函数值必于或等于整数规划最优解对应的目标函数值。
因此对于最优下料方案模型为:
[]()1
1
min 1n
p j j
j n
ij j j
j j f c x a x b x z μ==+⎧
==⎪⎪⎪=⎨⎪⎪∈⎪⎩∑∑
由式(1)的线性规划(LP)引入松弛变量
()20][m i n
1
1
⎪⎪⎪⎪⎩
⎪⎪⎪⎪⎨⎧
>===∑∑==j n
j i
j ij n
j j
j p x b x a x c f μ 如果得到的最优解是整数,则求解结束。
该最优解也是式(1)的最优解。
否则,得到的最优解只是式(1)的最优解的一个下界。
这样可以把式(1)划分为两个子问题。
再对式(3)和式(4)继续上述过程。
若在某一时刻得到了一个全整数解xm,则xm 为式(1)的一个上界。
此时 ,若打算从子问题k 开始分支,而这一问题的下界为xk>xm,则这一分支不必再考虑了,因为在这一分支中不会找到小于xm 的解。
如果xk<xm,则分支过程还要继续 。
1.3 MATLAB 一维优化算法
求解整数线性规划MATLAB程序 :
function [ x, y] = ILp ( f, G, h, Geq, heq, lb, ub, x, id, options) global upper op t c x0 A b Aeq beq ID options;
if nargin < 10, options = optimset( { } ) ; options. Disp lay = ’off’; op tions. LargeScale = ’off’; end
if nargin < 9, id = ones( size ( f) ) ; end
if nargin < 8, x = [ ] ; end
if nargin < 7 | isemp ty( ub) , ub = inf*ones( size ( f) ) ; end
if nargin < 6 | isempty( lb) , lb = zeros( size ( f) ) ; end
if nargin < 5, heq = [ ] ; end
if nargin < 4, Geq = [ ] ; end
upper = inf; c = f; x0 = x; A = G; b = h; Aeq = Geq; beq = heq; ID = id;
ftemp = ILP ( lb ( : ) , ub ( : ) ) ;
x = opt; y = upper;
function ftemp = ILP ( vlb, vub)
global upper op t c x0 A b Aeq beq ID options;
[ x, ftemp, how ] = linp rog ( c, A, b, Aeq, beq, vlb, vub, x0, op- tions) ;
if how < = 0
return;
end;
if ftemp - upper > 0. 00005 % in order to avoid error
return;
end;
ifmax( abs( x*ID - round ( x*ID) ) ) < 0. 00005
if upper - ftemp > 0. 00005 % in order to avoid error
op t = x’; upper = ftemp;
return;
else
op t = [ op t; x’] ;
return;
end;
end;
notintx = find ( abs( x - round ( x) ) > = 0. 00005) ; % in order to avoid error
intx = fix( x) ; tempvlb = vlb; tempvub = vub;
if vub ( notintx(1, 1) , 1) > = intx( notintx(1, 1) , 1) + 1; tempvlb (notintx(1, 1) , 1) = intx( notintx(1, 1) , 1) + 1;
ftemp = IntLP ( tempvlb, vub) ;
end;
if vlb ( notintx(1, 1) , 1) < = intx( notintx(1, 1) , 1)
tempvub ( notintx(1, 1) , 1) = intx( notintx(1, 1) , 1) ; ftemp = IntLP ( vlb, tempvub) ; end;
2 线性规划实例分析
某车间有一大批长130cm 的棒料,根据加工零件的要求,需要从这批棒料中成套截取70cm 长的毛坯不少于100根,32cm 长的毛坯不少于100根,35cm 长的毛坯不大于100根。
要求合理设计下料方案,使剩下的边角料总长最短。
分析:对于一维下料问题都可以用组合最优化的方法给出合理的下料方式。
该题要求剩余边角料总长最短,可以转化为求使用原材料的量最少。
设x1, x2, x3分别表示所需3种不同长度的棒料零件数,则70x1+32x2+35x3≤130(xi ∈Z+,i=1, 2, 3)。
其中x1≤1 ,表1给出下料方案。
表1 下料方案
由表1可列出目标函数及其约束条件
()1234561213452
34
min 2825283122510024100
52100
(1,2,3,4,5,6)j f x x x x x x x x x x x x x x x x z j +⎧=+++++⎪
+≥⎪⎪
+++≥⎨⎪++≤⎪⎪∈=⎩
用上面的MATLAB程序求解方程组(5)
> > c = [ 28, 25, 28, 31, 2,25];
> >A = [1, 1, 0, 0, 0;1,0, 1, 2, 4; 0,1,2,1,0;0,0,3];
> > b = [ 100; 100; 100 ];
> > [ x, f ] = ILp ( c, [ ] , [ ] , A, b, [ 0, 0, 0, 0, 0,0, ] ,
[ inf, inf, inf, inf, inf, inf,] ) ;
x =[ 0 100 0 0 25 0]
由此可知按B2方式下100根,B5方式下25根,其余方式都不用,按这种方式下料最高。
3 结论及体会
通过用MATLAB软件按照一维下料问题优化进行分析,优化下料要求最大限度地节约原材料,提高原材料的利用率。
本次设计又加深了对机械优化设计的认识,提高了自己分析问题、解决实际问题的能力;利用软件可以快速、简洁的解决问题。