大豆蛋白浓缩加工工艺
大豆浓缩蛋白简介
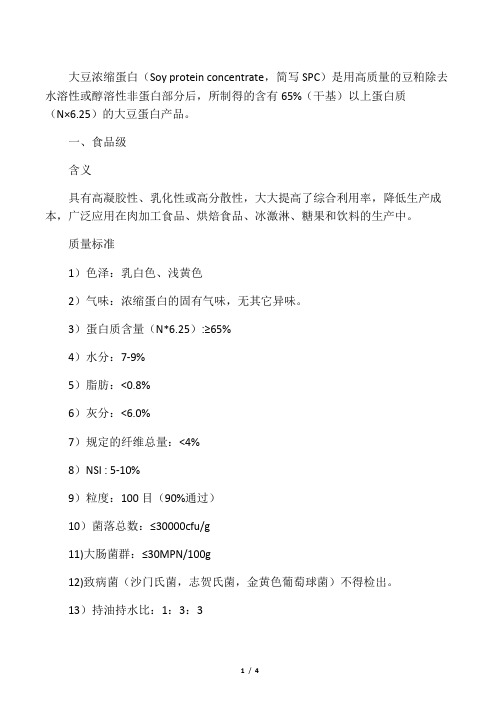
3.营养价值高
蛋白质消化利用率高(类似与脱脂奶粉);氨基酸含量高且组成平衡(理想的植物蛋白原料)。
抗营养因子含量极低(按欧盟检测标准检测);PH值,味道中性(添加到饲料中,对幼小动物的肠道无不利影响)。
大豆浓缩蛋白(Soy protein concentrate,简写SPC)是用高质量的豆粕除去水溶性或醇溶性非蛋白部分后,所制得的含有65%(干基)以上蛋白质(N×6.25)的大豆蛋白产品。
一、食品级
含义
具有高凝胶性、乳化性或高分散性,大大提高了综合利用率,降低生产成本,广泛应用在肉加工食品、烘焙食品、冰激淋、糖果和饮料的生产中。
4、与乳清粉相比较:乳清粉蛋白含量低,货源供应不及时且价格高,小猪食后增长速度慢。
4.不含任何化学添加剂5.制粒性能,流动性好6.耐储存,保存时间长
四、产品应用
乳猪能否顺利产奶是养猪成功的关键。乳猪的消化系统尚未完善,并且在断奶期间又有很强的应激性,需要适口性好,消化吸收率高,品质稳定的蛋白质原料。此时选择好的蛋白质原料对乳猪的顺利成长至关重要。我们的浓缩蛋白作为一种可消化的蛋白含量高,适口性好,抗营养因子和难消化寡糖以及致病菌含量都极低的优秀蛋白原料,它非常适合断奶乳猪的生长需要,是乳崽猪健康生长的理想选择。
水产大豆浓缩蛋白已证实是鱼虾饲料中极好的植物性蛋白源。因为他抗原水平低、灰分、含磷量低,不象鱼粉那样含量高水平的生物胺,同时具有极好的制粒性。适量添加能提高饲养品种的成活率,维持正常生长,同时改善饲料的利用效率。
幼禽由于幼禽肠道短,对动物蛋白利用效率有障碍。该产品应用于幼禽中能有效提高成活率、降低腹泻、促进生长。
大豆蛋白提取技术研究进展
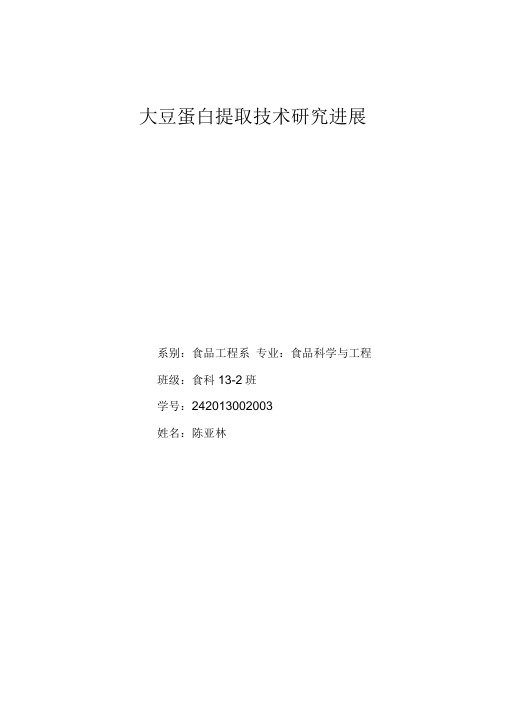
大豆蛋白提取技术研究进展系别:食品工程系专业:食品科学与工程班级:食科13-2班学号:************姓名:***摘要大豆蛋白产品分为三类,即大豆蛋白粉、大豆浓缩蛋白和大豆分离蛋白。
大豆分离蛋白含有人体所必需的八种氨基酸,不含胆固醇,具有许多优良的食品性能,添加在食品中可以改善食品的品质和性能,提高食品营养价值。
是一种重要的植物蛋白,在食品工业中得到了广泛的应用,是近年来的研究重点。
其中,大豆浓缩蛋白的提取方法有稀酸浸提法、酒精浸提法和湿热浸提法。
大豆分离蛋白有碱溶酸沉法、离子交换法、超滤膜分离法等。
本文以研究方向和工艺改进方面为着力点解释大豆浓缩蛋白和分离蛋白这两种主要的提取方法的发展脉络。
关键词大豆浓缩蛋白;大豆分离蛋白;稀酸浸提法;酒精浸提法;碱溶酸沉法;离子交换法;超过滤法;湿热浸提法大豆分离蛋白(soy protein isolate,SPI )是把脱皮大豆中的除蛋白质以外的可能性物质和纤维素、半纤维素物质都除掉,得到的蛋白质含量不低于90% 的制品,又称等电点蛋白。
与大豆浓缩蛋白相比,生产大豆分离蛋白不仅要从低温脱溶豆粕中除去低分子可溶性糖等成分,而且还要去除不溶性纤维素、半纤维素等成分。
其生产方法主要有碱溶酸沉法、超过滤法和离子交换法。
一、碱溶酸沉法1. 提取原理低温豆粕中的蛋白质大部分能溶于稀碱溶液。
将低温豆粕用稀碱溶液浸提后,用离心分离法除去原料中的不溶性物质,然后用酸把浸出物的PH调至4.5左右,蛋白质由于处于等电点状态而凝聚沉淀,经分离可得到蛋白质沉淀,再经洗涤、中和、干燥得到大豆分离蛋白。
2. 提取工艺豆粕的质量直接影响大豆分离蛋白的功能特性和提取率,只有高质量的豆粕才能获得高质量和高得率的大豆分离。
要求原料无霉变,豆皮含量低,残留溶剂少,蛋白质含量高(45沖上),脂肪含量低,NSI高(不低于80%。
豆粕粉碎后过40-60目筛。
首先利用弱碱溶液浸泡低温豆粕,使可溶性蛋白质、糖类等溶解出来,利用离心机除去溶液中不溶性的纤维素和残渣。
大豆蛋白浓缩加工工艺
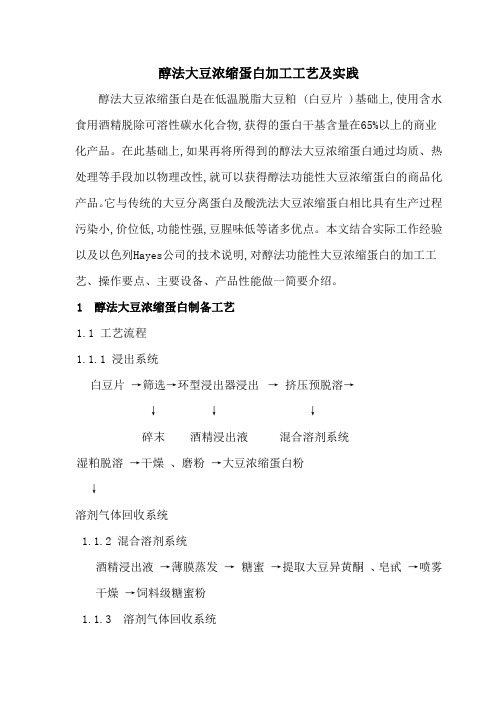
醇法大豆浓缩蛋白加工工艺及实践醇法大豆浓缩蛋白是在低温脱脂大豆粕 (白豆片 )基础上,使用含水食用酒精脱除可溶性碳水化合物,获得的蛋白干基含量在65%以上的商业化产品。
在此基础上,如果再将所得到的醇法大豆浓缩蛋白通过均质、热处理等手段加以物理改性,就可以获得醇法功能性大豆浓缩蛋白的商品化产品。
它与传统的大豆分离蛋白及酸洗法大豆浓缩蛋白相比具有生产过程污染小,价位低,功能性强,豆腥味低等诸多优点。
本文结合实际工作经验以及以色列Hayes公司的技术说明,对醇法功能性大豆浓缩蛋白的加工工艺、操作要点、主要设备、产品性能做一简要介绍。
1 醇法大豆浓缩蛋白制备工艺1.1 工艺流程1.1.1 浸出系统白豆片→筛选→环型浸出器浸出→ 挤压预脱溶→↓↓↓碎末酒精浸出液混合溶剂系统湿粕脱溶→干燥、磨粉→大豆浓缩蛋白粉↓溶剂气体回收系统1.1.2 混合溶剂系统酒精浸出液→薄膜蒸发→ 糖蜜→提取大豆异黄酮、皂甙→喷雾干燥→饲料级糖蜜粉1.1.3 溶剂气体回收系统环型浸出器→冷水冷凝器→冷冻液冷凝器→低压风机平衡罐薄膜蒸发器→冷水冷凝器→冷冻盐水冷凝器→真空泵湿粕脱溶罐→节能器→水冷凝器→冷冻盐水冷凝器→真空泵1.2 工艺说明该工艺流程与溶剂法提取植物油十分相似。
但酒精与水的共沸点(常压下共沸点为78.15℃)高于正己烷(69℃),酒精的蒸发潜热是正己烷的近2.5倍,因此酒精溶剂气体的回收会消耗更大的能量。
考虑到换热器的传热系数,通常所需的加热面积更小,而冷却面积会更大一些。
同时,由于豆粕在含水酒精溶液中会吸水溶胀并且浸出速率相对较低,因此对于同样的浸出能力,用醇洗豆粕方法制备浓缩蛋白所需的浸出器体积要比传统油脂工业用的正己烷萃取豆坯的浸出器大很多倍,造成设备投资相对较大。
在溶剂消耗方面,先进的酒精浸出系统可以使溶剂消耗在30kg/t物料以下,仍高于6号溶剂浸出油脂系统的2kg/t物料以下。
酒精浸出湿粕和含水酒精结合较紧密是造成消耗偏高的主要原因。
大豆蛋白提取方法和工艺流程

大豆蛋白提取方法和工艺流程
大豆蛋白是一种重要的植物蛋白质来源,其提取方法和工艺流程对于高效获得纯度较高的蛋白质产品至关重要。
下面将介绍一种常用的大豆蛋白提取方法和工艺流程。
首先,在大豆蛋白提取过程中,将大豆加工成豆浆是关键步骤之一。
大豆经过清洗后,浸泡在水中,然后经过破碎和热处理,使得大豆中的蛋白质溶解在水中形成豆浆。
接下来,对豆浆进行固液分离,最常用的方式是通过高速离心将固体与液体分离。
离心过程中,大豆渣被分离出来,而含有蛋白质的液体则被留下来。
然后,对蛋白质溶液进行沉淀和过滤。
通过调整pH值和添加适量的盐酸(或盐)等化学物质,使蛋白质在酸性条件下发生沉淀。
接着,通过过滤将沉淀蛋白质分离出来。
这些步骤有助于去除杂质和提高蛋白质的纯度。
最后,对分离出的蛋白质进行干燥和粉碎。
通常使用喷雾干燥或冷冻干燥等方法将蛋白质溶液中的水分去除,得到干燥的蛋白质粉末。
为了得到更细的粒径,粉碎设备常常用于将蛋白质粉碎成所需的颗粒大小。
总结而言,大豆蛋白提取的工艺流程主要包括大豆加工成豆浆、固液分离、沉淀和过滤、干燥和粉碎等步骤。
这些步骤共同作用,可有效提取大豆中的蛋白质,并最大程度地提高蛋白质的纯度,从而满足不同需求的应用场景。
大豆浓缩蛋白工艺流程
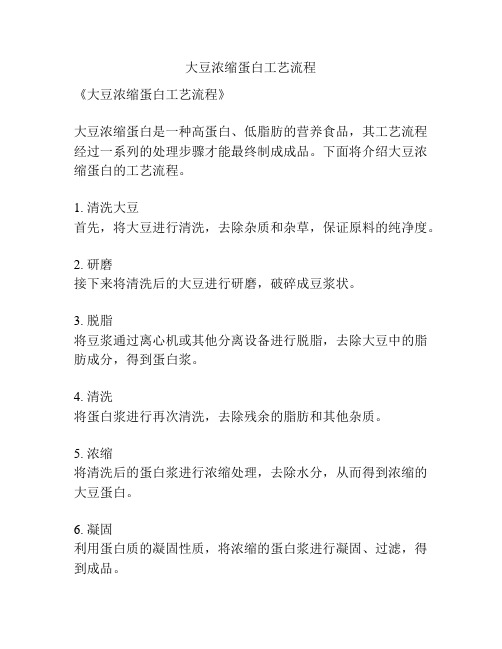
大豆浓缩蛋白工艺流程
《大豆浓缩蛋白工艺流程》
大豆浓缩蛋白是一种高蛋白、低脂肪的营养食品,其工艺流程经过一系列的处理步骤才能最终制成成品。
下面将介绍大豆浓缩蛋白的工艺流程。
1. 清洗大豆
首先,将大豆进行清洗,去除杂质和杂草,保证原料的纯净度。
2. 研磨
接下来将清洗后的大豆进行研磨,破碎成豆浆状。
3. 脱脂
将豆浆通过离心机或其他分离设备进行脱脂,去除大豆中的脂肪成分,得到蛋白浆。
4. 清洗
将蛋白浆进行再次清洗,去除残余的脂肪和其他杂质。
5. 浓缩
将清洗后的蛋白浆进行浓缩处理,去除水分,从而得到浓缩的大豆蛋白。
6. 凝固
利用蛋白质的凝固性质,将浓缩的蛋白浆进行凝固、过滤,得到成品。
7. 干燥
对成品进行干燥处理,使其变成粉末状。
经过以上工艺流程,大豆浓缩蛋白最终制成。
大豆浓缩蛋白在工艺流程中需要精密的操作和严格的控制条件,确保产品的质量和安全。
通过以上流程,大豆浓缩蛋白可以被广泛应用于食品加工、保健品生产等领域,为人们提供了优质的蛋白营养补充。
浓缩大豆蛋白的加工、特性和前景
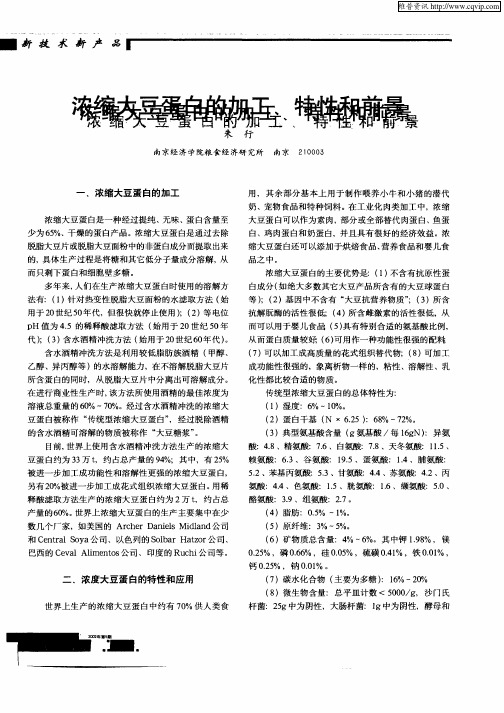
维普资讯
l 新 技 术 新 产 品
…
厘斡
品之 中 。
浓缩大豆蛋 白是一 种经过提纯 、 无味 、 白含量 至 蛋
少为 6 %、 5 干燥 的蛋 白产品。浓缩大 豆蛋 白是通过去 除
脱脂大豆片或脱脂大豆面粉 中的非蛋 白成分 而提取 出来 的, 具体生 产过程是将糖和其它 低分子量成分溶解 , 从
而只剩下蛋 白和细胞壁 多糖 。
法有:( ) 1 针对热变性脱 脂大豆面粉 的水滤取 方法 ( 始 用于 2 世纪 5 年代 ,但很快就停 止使用 ) 2 等 电位 0 0 ;( ) p H值 为 45的稀释酸滤取 方法 ( 用于 2 . 始 0世纪 5 年 0 代 ) 3 含 水酒 精冲洗方法 ( ;( ) 始用于 2 世纪 6 年代 ) 0 0 。 含水酒精冲洗 方法是利用较低脂 肪族酒精 ( 甲醇 、 乙醇 、 丙醇等 )的水溶解 能力,在不溶解脱脂大 豆片 异 所含 蛋 白的 同时,从 脱脂大豆片 中分 离 出可溶解成分 。 在 进行商业性生产 时, 该方法所使 用酒精 的最佳浓度为 溶液总重量 的 6% ~7%。经过含水酒 精冲洗的浓 缩大 0 0
5 . 2、苯基丙氨酸:53、甘氨酸:44、苏氨酸:4 丙 . . . 2、 氨酸 :44、色氨酸 :1 . . 5、胱氨酸:1 . 6、缬氨酸:5 . 0、 酪氨酸 :3 . 9、组氨酸 :27。 .
( )脂肪 :05 ~1 4 . % %。 ( )原纤维 :3 5 %~5 %。
醇法大豆浓缩蛋白的改性技术研究进展.doc
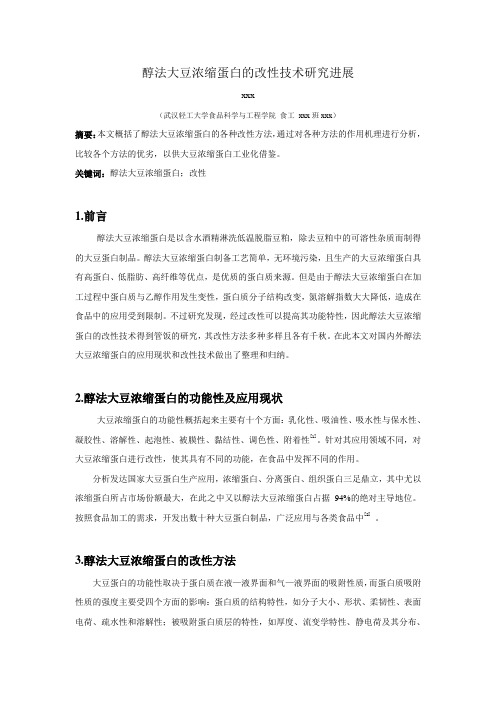
醇法大豆浓缩蛋白的改性技术研究进展xxx(武汉轻工大学食品科学与工程学院食工xxx班xxx)摘要:本文概括了醇法大豆浓缩蛋白的各种改性方法,通过对各种方法的作用机理进行分析,比较各个方法的优劣,以供大豆浓缩蛋白工业化借鉴。
关键词:醇法大豆浓缩蛋白;改性1.前言醇法大豆浓缩蛋白是以含水酒精淋洗低温脱脂豆粕,除去豆粕中的可溶性杂质而制得的大豆蛋白制品。
醇法大豆浓缩蛋白制备工艺简单,无环境污染,且生产的大豆浓缩蛋白具有高蛋白、低脂肪、高纤维等优点,是优质的蛋白质来源。
但是由于醇法大豆浓缩蛋白在加工过程中蛋白质与乙醇作用发生变性,蛋白质分子结构改变,氮溶解指数大大降低,造成在食品中的应用受到限制。
不过研究发现,经过改性可以提高其功能特性,因此醇法大豆浓缩蛋白的改性技术得到管饭的研究,其改性方法多种多样且各有千秋。
在此本文对国内外醇法大豆浓缩蛋白的应用现状和改性技术做出了整理和归纳。
2.醇法大豆浓缩蛋白的功能性及应用现状大豆浓缩蛋白的功能性概括起来主要有十个方面:乳化性、吸油性、吸水性与保水性、凝胶性、溶解性、起泡性、被膜性、黏结性、调色性、附着性[1]。
针对其应用领域不同,对大豆浓缩蛋白进行改性,使其具有不同的功能,在食品中发挥不同的作用。
分析发达国家大豆蛋白生产应用,浓缩蛋白、分离蛋白、组织蛋白三足鼎立,其中尤以浓缩蛋白所占市场份额最大,在此之中又以醇法大豆浓缩蛋白占据94%的绝对主导地位。
按照食品加工的需求,开发出数十种大豆蛋白制品,广泛应用与各类食品中[2]。
3.醇法大豆浓缩蛋白的改性方法大豆蛋白的功能性取决于蛋白质在液—液界面和气—液界面的吸附性质,而蛋白质吸附性质的强度主要受四个方面的影响:蛋白质的结构特性,如分子大小、形状、柔韧性、表面电荷、疏水性和溶解性;被吸附蛋白质层的特性,如厚度、流变学特性、静电荷及其分布、水合程度等;溶液状况,如pH、离子强度、温度等;加工过程的有关参数,如剪切力、温度、相的组成及粘性、液滴大小等[3]。
浓缩大豆蛋白名词解释
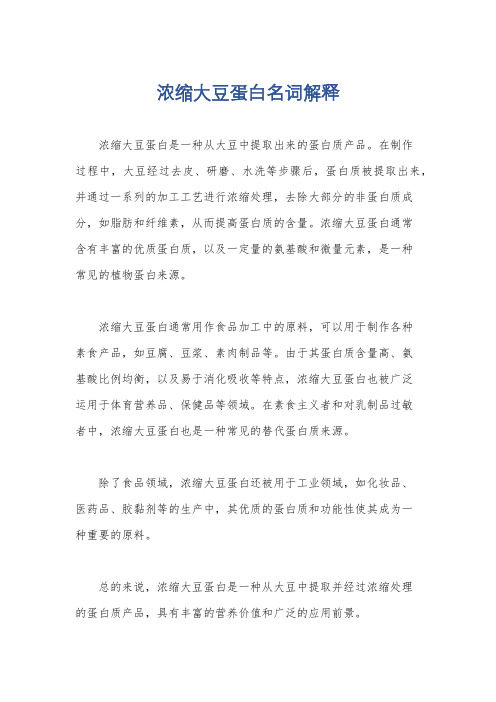
浓缩大豆蛋白名词解释
浓缩大豆蛋白是一种从大豆中提取出来的蛋白质产品。
在制作
过程中,大豆经过去皮、研磨、水洗等步骤后,蛋白质被提取出来,并通过一系列的加工工艺进行浓缩处理,去除大部分的非蛋白质成分,如脂肪和纤维素,从而提高蛋白质的含量。
浓缩大豆蛋白通常
含有丰富的优质蛋白质,以及一定量的氨基酸和微量元素,是一种
常见的植物蛋白来源。
浓缩大豆蛋白通常用作食品加工中的原料,可以用于制作各种
素食产品,如豆腐、豆浆、素肉制品等。
由于其蛋白质含量高、氨
基酸比例均衡,以及易于消化吸收等特点,浓缩大豆蛋白也被广泛
运用于体育营养品、保健品等领域。
在素食主义者和对乳制品过敏
者中,浓缩大豆蛋白也是一种常见的替代蛋白质来源。
除了食品领域,浓缩大豆蛋白还被用于工业领域,如化妆品、
医药品、胶黏剂等的生产中,其优质的蛋白质和功能性使其成为一
种重要的原料。
总的来说,浓缩大豆蛋白是一种从大豆中提取并经过浓缩处理
的蛋白质产品,具有丰富的营养价值和广泛的应用前景。
大豆浓缩蛋白在动物饲料中的营养标准

大豆浓缩蛋白在动物饲料中的营养标准大豆浓缩蛋白是以大豆为原料,经过粉碎、去皮、浸提、分离、洗涤、干燥等加工工艺,去除了大豆中的油脂、低分子可溶性非蛋白组分(主要是可溶性糖、灰分、醇溶蛋白和各种气味物质等)后所得到的大豆深加工产品。
大豆浓缩蛋白的生产工艺主要有4种,即湿热浸提法
大豆浓缩蛋白是以大豆为原料,经过粉碎、去皮、浸提、分离、洗涤、干燥等加工工艺,去除了大豆中的油脂、低分子可溶性非蛋白组分(主要是可溶性糖、灰分、醇溶蛋白和各种气味物质等)后所得到的大豆深加工产品。
大豆浓缩蛋白的生产工艺主要有4种,即湿热浸提法、酸洗涤法、乙醇浸提法和超滤膜法。
由于消除了寡聚糖类胀气因子、胰蛋白酶抑制因子,凝集素和皂甙等抗营养因子,大豆浓缩蛋白中的营养素消化率有一定程度的提高,而且改善了产品风味和品质,这使大豆浓缩蛋白自1959年商业化生产以来就深受食品工业和饲料工业的欢迎。
大豆浓缩蛋白的质量标准和营养特性
1983年1月,美国农业部食品营养学会确定了大豆浓缩蛋白中蛋白质含量大于60%的质量标准。
1987年,国际食品规范委员会、蔬菜蛋白规范委员会在古巴哈瓦那会议上,通过联合国粮农组织/世界卫生组织联合食品标准规程,提出大豆浓缩蛋白中蛋白质含量为65%~90%。
由于大豆浓缩蛋白目前主要用于食品工业,国内外尚无饲料级产品的标准。
湿热浸提法、酸洗涤法和乙醇浸提法三种方法生产的大豆浓缩蛋白产品,其营养价值存在一定的差异,其中以氮溶解指数的差异最明显。
由于一些水溶性低分子蛋白质在浸提过程中也被脱溶,大豆浓缩蛋白与其原料大豆粉氨基酸的组成略有差异。
浓缩蛋白与大豆分离蛋白生产工艺区别
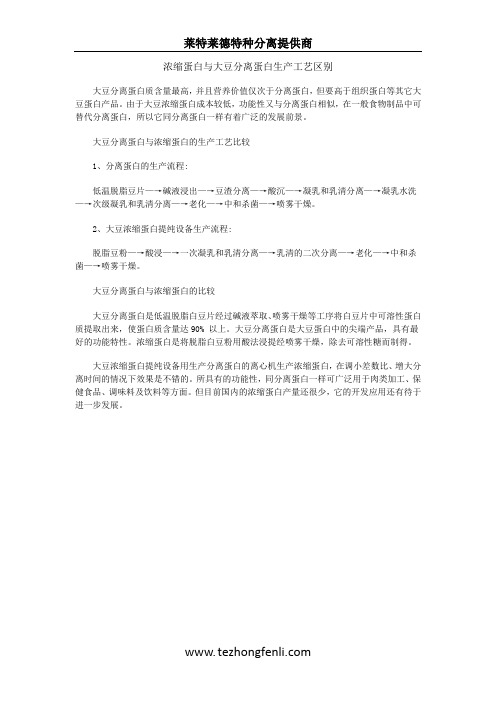
莱特莱德特种分离提供商
浓缩蛋白与大豆分离蛋白生产工艺区别
大豆分离蛋白质含量最高,并且营养价值仅次于分离蛋白,但要高于组织蛋白等其它大豆蛋白产品。
由于大豆浓缩蛋白成本较低,功能性又与分离蛋白相似,在一般食物制品中可替代分离蛋白,所以它同分离蛋白一样有着广泛的发展前景。
大豆分离蛋白与浓缩蛋白的生产工艺比较
1、分离蛋白的生产流程:
低温脱脂豆片—→碱液浸出—→豆渣分离—→酸沉—→凝乳和乳清分离—→凝乳水洗—→次级凝乳和乳清分离—→老化—→中和杀菌—→喷雾干燥。
2、大豆浓缩蛋白提纯设备生产流程:
脱脂豆粉—→酸浸—→一次凝乳和乳清分离—→乳清的二次分离—→老化—→中和杀菌—→喷雾干燥。
大豆分离蛋白与浓缩蛋白的比较
大豆分离蛋白是低温脱脂白豆片经过碱液萃取、喷雾干燥等工序将白豆片中可溶性蛋白质提取出来,使蛋白质含量达90% 以上。
大豆分离蛋白是大豆蛋白中的尖端产品,具有最好的功能特性。
浓缩蛋白是将脱脂白豆粉用酸法浸提经喷雾干燥,除去可溶性糖而制得。
大豆浓缩蛋白提纯设备用生产分离蛋白的离心机生产浓缩蛋白,在调小差数比、增大分离时间的情况下效果是不错的。
所具有的功能性,同分离蛋白一样可广泛用于肉类加工、保健食品、调味料及饮料等方面。
但目前国内的浓缩蛋白产量还很少,它的开发应用还有待于进一步发展。
植物蛋白大豆浓缩蛋白资料
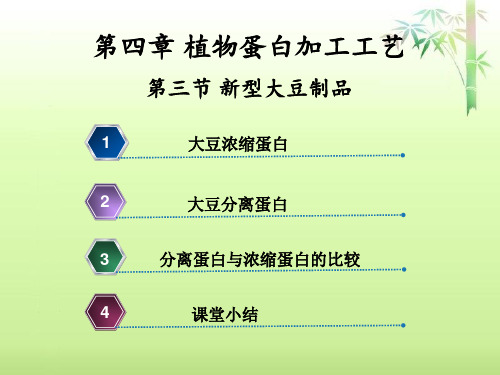
(3)温度—温度的高低对蛋白收率、纯度及色泽有显著影响。浸提温度 过高,会使蛋白变性,而且粘度增加,分离困难,耗能提高。因此,浸 提温度最好控制在30~50℃,等电酸沉温度控制在40~45℃为宜。
(4)时间— 在一定条件下,浸提时间越长,蛋白的溶出率就越高。从 氮溶解指数来看,一般溶解时间延长,蛋白的溶出率提高,当浸提时间 达到50min 时,蛋白质的溶出率区域处于动态平衡状态。综合考虑能源 消耗、生产周期、工艺成本等各种因素,浸提时间不超过40~50min。
第四章 植物蛋白加工工艺
第三节 新型大豆制品
1
大豆浓缩蛋白
2
大豆分离蛋白
3
分离蛋白与浓缩蛋白的比较
4ห้องสมุดไป่ตู้
课堂小结
一、大豆浓缩蛋白
❖ 大豆浓缩蛋白(SPC)通常是以脱皮脱溶豆粕为原料,通 过不同的加工方法,除去其中水溶性糖类、灰分以及 其他水溶性的非蛋白成分,制得蛋白质含量在70% (以 干基计)以上的大豆蛋白制品。
(8)打浆:为进行喷雾干燥需充分打散蛋白质的絮状沉淀,搅拌成匀浆。
( 9)回 调:加入 5%的 NaOH 溶液 中和回调, 使pH达到 6.5~ 7.0,以 85r/min的速度进行搅拌。
(10)杀菌:分离蛋白浆液在90℃加热10min或80℃ 加热15min,不仅可 以起到杀菌的作用,而且可明显提高产品的凝胶性。
•SPC 具有良好的吸水、保水性,在面粉中添加,可使面 包质地柔软,防止面包老化,延长贮存期。饼干中添加, 可提高其蛋白质含量,增加韧性、酥性,还具有保鲜作用。
•大豆浓缩蛋白是产品改善风味,消除胀气现象,糖分含 量低,低抗原性,粗蛋白含量高,使其更适用于禽类和鱼 类的饲料中。
二、大豆分离蛋白
豆制品加工工艺-大豆浓缩蛋白的加工技术
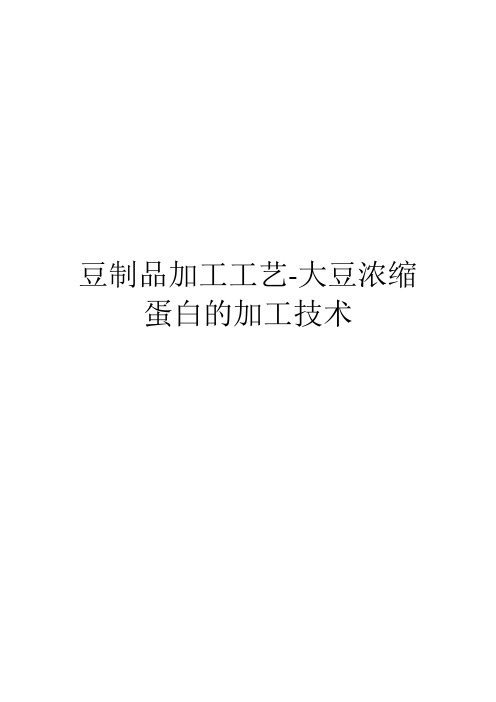
豆制品加工工艺-大豆浓缩蛋白的加工技术
大豆浓缩蛋白又称70%蛋白粉,原料以低温脱溶粕为佳,也可用高温浸出粕,但得率低、质量较差。
生产浓缩蛋白的方法主要有稀酸沉淀法和酒精洗涤法。
①稀酸沉淀法
利用豆粕粉浸出液在等电点(pH4.3~4.5)状态,蛋白质溶解度最低的原理,用离心法将不溶性蛋白质、多糖与可溶性碳水化物、低分子蛋白质分开,然后中和浓缩并进行干燥脱水,即得浓缩蛋白粉。
此法可同时除去大豆的腥味。
稀酸沉淀法生产浓缩蛋白粉,蛋白质水溶性较好(PDI值高),但酸碱耗量较大。
同时排出大量含糖废水,造成后处理困难,产品的风味也不如酒精法。
②酒精洗涤法
利用酒精浓度为60%~65%时可溶性蛋白质溶解度最低的原理,将酒精液与低温脱溶粕混合,洗涤粕中的可溶性糖类、灰分和醇溶蛋白质等。
再过滤分离出醇溶液,并回收酒精和糖,浆液则经干燥得浓缩蛋白粉。
此法生产的蛋白粉,色泽与风味较好,蛋白质损失少。
但由于蛋白质变性和产品中仍含有0.25%~1%的酒精,使食用价值受到一定限制。
此外还有湿热水洗法、酸浸醇洗法和膜分离法等。
其中膜分离法是用超滤膜脱糖获得浓缩蛋白,反渗透膜脱水回收水溶性低分子蛋白质与糖类,生产中不需要废水处理工程,产品氮溶指数(NS)高,因此是一种有前途的方法。
③大豆浓缩蛋白的用途
可应用于代乳粉、蛋白浇注食品、碎肉、乳胶肉末、肉卷、调料、
焙烤食品、婴儿食品、模拟肉等的生产,使用时应根据不同浓缩蛋白的功能特性选择。
大豆浓缩蛋白的生产工艺_营养组成及在动物日粮中的应用

浓缩蛋白在断奶仔猪和水产日粮中的应用
关键词:大豆浓缩蛋白;生产工艺;营养组成;断奶仔猪;水产
doi:10.13302/ki.fi.2015.Z1.009
中图分类号:S816.3
文献标识码:A
文章编号:1001-991X(2015)Z1-0029-04
Technology, nutrition and application of soy protein concentrate in animal diets
成本较高,畜牧行业难以接受
2 大豆浓缩蛋白的营养组成 2.1 大豆浓缩蛋白的常规营养成分
国内外尚无饲料级 SPC 的标准,从美国 ADM 公 司、秦皇岛金海食品工业有限公司、山东三维集团所 属山东长润生物有限公司提供的饲料级 SPC 营养指
29
专题论述
2015 年第 36 卷第 1 期增刊
标数据来看,常规营养指标比较接近:粗蛋白质 65%、 粗纤维 4%、粗灰分 6.5%和脂肪 1%左右,水分低于 9%,可溶性无氮浸出物 1.5%~3%和不溶性无氮浸出 物 15%左右,猪代谢能在 4 000 kcal/kg 左右。ADM 公 司 还 标 明 产 品 菌 落 总 数 ≤50 000 cfu/g 、大 肠 杆 菌 ≤100 cfu/g 和 25 g 样 品 不 得 检 出 沙 门 氏 菌 ,该 公 司 生 产 的 SPC 产 品 已 经 根 据 动 物 品 种 做 了 细 分 , 国内生产企业则尚未做到。 2.2 大豆浓缩蛋白的氨基酸组成
Li Lingui, Xiao Weiwei, Ge Menglan
Abstract:Soy protein concentrate, which is a product from soybean, has high protein and low antinutrition⁃
大豆分离蛋白生产工艺
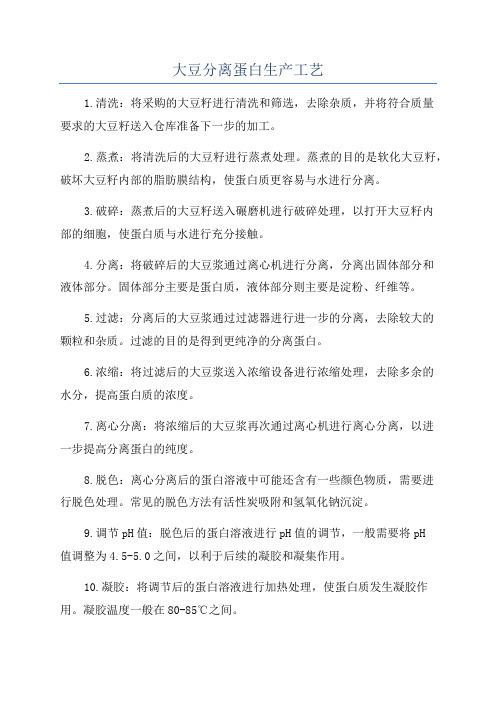
大豆分离蛋白生产工艺1.清洗:将采购的大豆籽进行清洗和筛选,去除杂质,并将符合质量要求的大豆籽送入仓库准备下一步的加工。
2.蒸煮:将清洗后的大豆籽进行蒸煮处理。
蒸煮的目的是软化大豆籽,破坏大豆籽内部的脂肪膜结构,使蛋白质更容易与水进行分离。
3.破碎:蒸煮后的大豆籽送入碾磨机进行破碎处理,以打开大豆籽内部的细胞,使蛋白质与水进行充分接触。
4.分离:将破碎后的大豆浆通过离心机进行分离,分离出固体部分和液体部分。
固体部分主要是蛋白质,液体部分则主要是淀粉、纤维等。
5.过滤:分离后的大豆浆通过过滤器进行进一步的分离,去除较大的颗粒和杂质。
过滤的目的是得到更纯净的分离蛋白。
6.浓缩:将过滤后的大豆浆送入浓缩设备进行浓缩处理,去除多余的水分,提高蛋白质的浓度。
7.离心分离:将浓缩后的大豆浆再次通过离心机进行离心分离,以进一步提高分离蛋白的纯度。
8.脱色:离心分离后的蛋白溶液中可能还含有一些颜色物质,需要进行脱色处理。
常见的脱色方法有活性炭吸附和氢氧化钠沉淀。
9.调节pH值:脱色后的蛋白溶液进行pH值的调节,一般需要将pH值调整为4.5-5.0之间,以利于后续的凝胶和凝集作用。
10.凝胶:将调节后的蛋白溶液进行加热处理,使蛋白质发生凝胶作用。
凝胶温度一般在80-85℃之间。
11.凝集:凝胶后的分离蛋白进行凝集处理,一般采用盐酸、硫酸和醋酸等酸性物质进行凝集。
12.离心:凝集后的蛋白溶液进行离心处理,分离出固体部分和液体部分,固体部分就是经过凝结处理的大豆分离蛋白。
13.干燥:将分离后的大豆蛋白固体进行干燥处理,通常有喷雾干燥、真空干燥、凝固干燥等方法可选。
14.粉碎:干燥后的大豆蛋白固体进行粉碎处理,得到所需的粉状产品。
以上就是大豆分离蛋白的生产工艺。
通过上述工艺,可以得到高纯度的大豆分离蛋白,为食品工业生产提供了重要的原料。
但需要注意的是,生产中需要确保设备的清洁、操作的卫生和原料的质量,以确保最终产品的质量和食品安全。
醇法制备大豆浓缩蛋白工艺
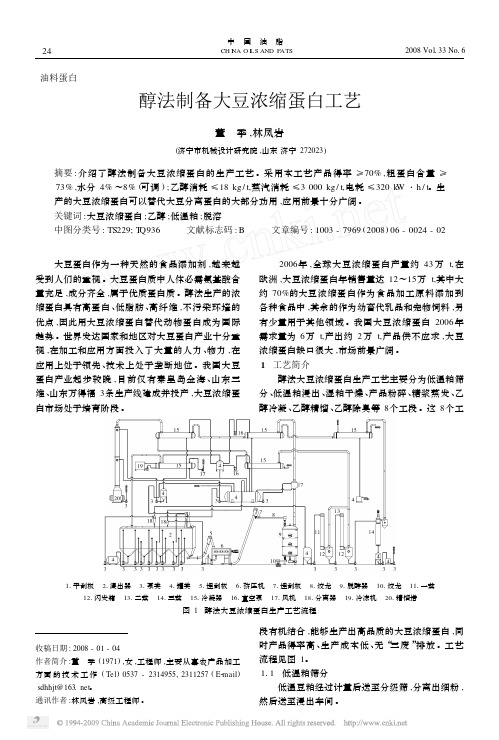
过捕集器捕集粕末 ,再去冷凝器冷凝 ,不凝气体去尾 生产 10 000 t/ a的大豆浓缩蛋白生产线 ,设备和土
气回收系统 。
建总造价不超过 2 000 万元 ,总装机容量为 600 ~
114 成品粉碎
800 kW ,车间大小为 : 26 m ×19 m ×13 m。
成品粕输送至粕库内 , 用超 微粉 碎机 粉碎 成 3 大豆浓缩蛋白与大豆分离蛋白主要消耗指标比
一定比例的 95%的新鲜乙醇水溶液进行喷淋 ,然后 冷凝器出来的不凝气体进入最后冷凝器 ,冷凝
用料溶比为 1∶(3~5)的 65%的新鲜乙醇水溶液进 器使用低温盐水冷却 ,把尾气中的乙醇全部冷凝下
行喷淋 。豆粕中醇溶性成分和水溶性糖浆溶于液体 来 ,不凝气体用风机排出室外 。
中 ,液体向豆粕进料方向流动 ;通过浓度梯度不断增 119 自动控制
2008年第
33卷第
6期
CH中INA 国O IL S油AND 脂FATS
25
112 低温粕浸出
使用 ;精馏过程中在精馏塔 1 /3的位置定期放出一定
送入浸出车间的低温豆粕在浸出器内用乙醇溶 液体 ,把由于长期循环进入产生的臭味物质除掉 。
液浸出 。豆粕和乙醇逆向运动 ,豆粕出浸出器前用 118 尾气回收
粗蛋白 /%
68~75 85~90
水分 /%
≤6 ≤6
残油 粒度 PD I / % (100目 ) / %
≤0. 6 ≥98 ≥10 ≤0. 6 ≥90 ≥90
灰分 致病菌 /%
≤4. 5 未检出 ≤4. 5 未检出
5 结束语 通过以上论述和比较 ,该工艺具有投资少 、见效 快 、得率高 、节约能源 、不污染环境的优点 。生产的
大豆蛋白浓缩加工工艺
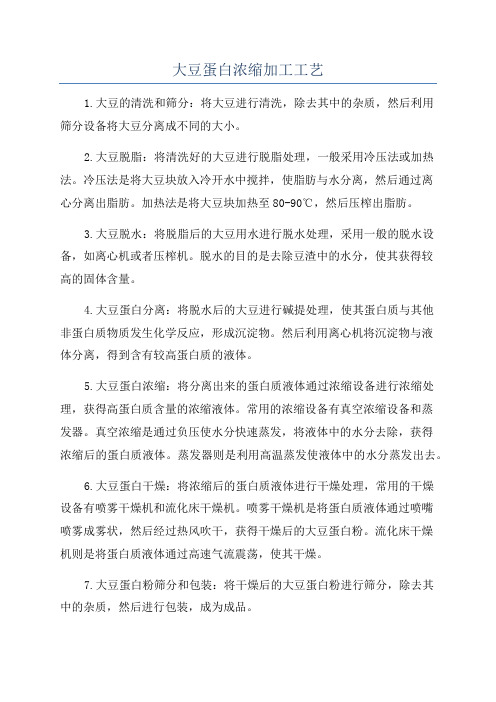
大豆蛋白浓缩加工工艺1.大豆的清洗和筛分:将大豆进行清洗,除去其中的杂质,然后利用筛分设备将大豆分离成不同的大小。
2.大豆脱脂:将清洗好的大豆进行脱脂处理,一般采用冷压法或加热法。
冷压法是将大豆块放入冷开水中搅拌,使脂肪与水分离,然后通过离心分离出脂肪。
加热法是将大豆块加热至80-90℃,然后压榨出脂肪。
3.大豆脱水:将脱脂后的大豆用水进行脱水处理,采用一般的脱水设备,如离心机或者压榨机。
脱水的目的是去除豆渣中的水分,使其获得较高的固体含量。
4.大豆蛋白分离:将脱水后的大豆进行碱提处理,使其蛋白质与其他非蛋白质物质发生化学反应,形成沉淀物。
然后利用离心机将沉淀物与液体分离,得到含有较高蛋白质的液体。
5.大豆蛋白浓缩:将分离出来的蛋白质液体通过浓缩设备进行浓缩处理,获得高蛋白质含量的浓缩液体。
常用的浓缩设备有真空浓缩设备和蒸发器。
真空浓缩是通过负压使水分快速蒸发,将液体中的水分去除,获得浓缩后的蛋白质液体。
蒸发器则是利用高温蒸发使液体中的水分蒸发出去。
6.大豆蛋白干燥:将浓缩后的蛋白质液体进行干燥处理,常用的干燥设备有喷雾干燥机和流化床干燥机。
喷雾干燥机是将蛋白质液体通过喷嘴喷雾成雾状,然后经过热风吹干,获得干燥后的大豆蛋白粉。
流化床干燥机则是将蛋白质液体通过高速气流震荡,使其干燥。
7.大豆蛋白粉筛分和包装:将干燥后的大豆蛋白粉进行筛分,除去其中的杂质,然后进行包装,成为成品。
大豆蛋白浓缩的加工工艺可以根据具体的需求进行调整和优化,以达到不同的蛋白质含量和品质要求。
同时,为了增加产品的营养价值和口感,可以添加一些辅料和调味料进行调整。
大豆蛋白浓缩是一种利用大豆资源进行高蛋白质产品加工的重要工艺,可以广泛用于食品、饮料、保健品等领域。
豆制品加工工艺-大豆蛋白的提取
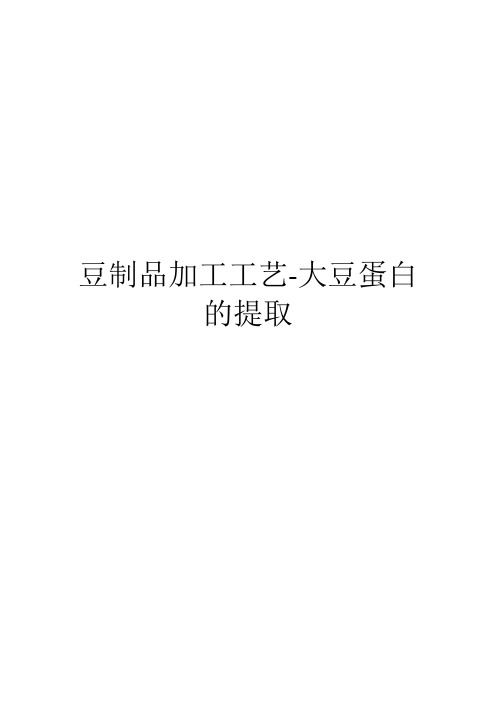
豆制品加工工艺-大豆蛋白
的提取
从大豆中同时分离出油脂和蛋白从而获得大豆蛋白。
采用这种方法所获得的大豆蛋白其含量以干固形物为基准,最低不少于55%,豆油含量以蛋白重量为准为2~32%。
提取方法将洗净和去皮的大豆研磨,然后在过氧化物和水中将研磨产品制成浆状。
通过离心,从浆液中获得提取的蛋白。
把浆液pH 值调到8,以溶解蛋白,去掉不溶成分和游离油脂,再把pH值降到4.5,从浆液中即可获得沉淀蛋白,其蛋白质含量不低于85%。
上述方法稍加更改,提取物中的蛋白和油脂含量可能发生变化,生产出含油提取物,其蛋白含量55%。
实例洗净的大豆70℃预先加热处理,使其水分含量达6%。
然后破碎脱皮,将去皮大豆经ContraplexPin磨研磨。
用美制的70目筛子筛出99%的细粉,用100目的筛子筛出85%的细粉。
再将大豆粉放进60℃的水里,水中约含有0.03的过氧化氢,豆粉与水的比例为1∶12。
然后添加氢氧化钠水溶液,并不断搅拌,添加到pH值为8~9即可,静置30分钟。
水状浆液即可分离成水状“A”、固态“B”和油状或乳状“C”。
将“B”与水以5∶1的比例混合搅拌,按上述方法还可分出离出水状“D”,将“A”和“D”混合,用盐酸将pH调到4.5,蛋白固形物则沉淀。
离心即得固态“G”和乳清状“H”,将“G”喷粉干燥生产出分离蛋白。
上述工序重复多次生产出蛋白提取物,以整个干固形物为基准,其蛋白含量为81~85%,油脂含量为7~9%。
用这种方法所获得提取物比用传统有机溶剂提取的含油的蛋白质延长了货架期。
特别是提取的蛋白,油脂尽管含量不低于2%,其
货架期却延长。
大豆分离蛋白提取方法总结
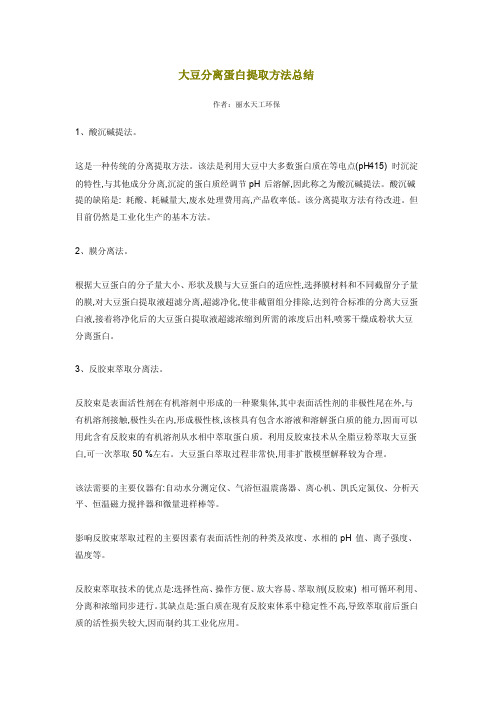
大豆分离蛋白提取方法总结作者:丽水天工环保1、酸沉碱提法。
这是一种传统的分离提取方法。
该法是利用大豆中大多数蛋白质在等电点(pH415) 时沉淀的特性,与其他成分分离,沉淀的蛋白质经调节pH 后溶解,因此称之为酸沉碱提法。
酸沉碱提的缺陷是: 耗酸、耗碱量大,废水处理费用高,产品收率低。
该分离提取方法有待改进。
但目前仍然是工业化生产的基本方法。
2、膜分离法。
根据大豆蛋白的分子量大小、形状及膜与大豆蛋白的适应性,选择膜材料和不同截留分子量的膜,对大豆蛋白提取液超滤分离,超滤净化,使非截留组分排除,达到符合标准的分离大豆蛋白液,接着将净化后的大豆蛋白提取液超滤浓缩到所需的浓度后出料,喷雾干燥成粉状大豆分离蛋白。
3、反胶束萃取分离法。
反胶束是表面活性剂在有机溶剂中形成的一种聚集体,其中表面活性剂的非极性尾在外,与有机溶剂接触,极性头在内,形成极性核,该核具有包含水溶液和溶解蛋白质的能力,因而可以用此含有反胶束的有机溶剂从水相中萃取蛋白质。
利用反胶束技术从全脂豆粉萃取大豆蛋白,可一次萃取50 %左右。
大豆蛋白萃取过程非常快,用非扩散模型解释较为合理。
该法需要的主要仪器有:自动水分测定仪、气浴恒温震荡器、离心机、凯氏定氮仪、分析天平、恒温磁力搅拌器和微量进样棒等。
影响反胶束萃取过程的主要因素有表面活性剂的种类及浓度、水相的pH 值、离子强度、温度等。
反胶束萃取技术的优点是:选择性高、操作方便、放大容易、萃取剂(反胶束) 相可循环利用、分离和浓缩同步进行。
其缺点是:蛋白质在现有反胶束体系中稳定性不高,导致萃取前后蛋白质的活性损失较大,因而制约其工业化应用。
4、反相高效液相色谱法这是对大豆蛋白中7 S 和11 S 球蛋白进行快速分离的一种方法。
在分离条件为40 ℃、流速1mL/ min 的条件下,9 min 可完成相应球蛋白的分离。
具体方法为:(1)试剂与试样。
乙腈(CAN) (HPLC 级) 、三氟乙酸( TFA) (HPLC 级) 、HPLC 级水用于移动相的制备。
大豆蛋白浓缩加工工艺
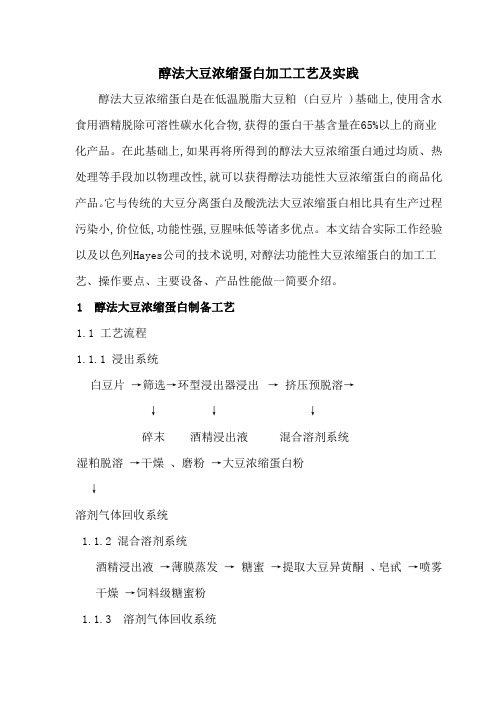
醇法大豆浓缩蛋白加工工艺及实践醇法大豆浓缩蛋白是在低温脱脂大豆粕 (白豆片 )基础上,使用含水食用酒精脱除可溶性碳水化合物,获得的蛋白干基含量在65%以上的商业化产品。
在此基础上,如果再将所得到的醇法大豆浓缩蛋白通过均质、热处理等手段加以物理改性,就可以获得醇法功能性大豆浓缩蛋白的商品化产品。
它与传统的大豆分离蛋白及酸洗法大豆浓缩蛋白相比具有生产过程污染小,价位低,功能性强,豆腥味低等诸多优点。
本文结合实际工作经验以及以色列Hayes公司的技术说明,对醇法功能性大豆浓缩蛋白的加工工艺、操作要点、主要设备、产品性能做一简要介绍。
1 醇法大豆浓缩蛋白制备工艺1.1 工艺流程1.1.1 浸出系统白豆片→筛选→环型浸出器浸出→ 挤压预脱溶→↓↓↓碎末酒精浸出液混合溶剂系统湿粕脱溶→干燥、磨粉→大豆浓缩蛋白粉↓溶剂气体回收系统1.1.2 混合溶剂系统酒精浸出液→薄膜蒸发→ 糖蜜→提取大豆异黄酮、皂甙→喷雾干燥→饲料级糖蜜粉1.1.3 溶剂气体回收系统环型浸出器→冷水冷凝器→冷冻液冷凝器→低压风机平衡罐薄膜蒸发器→冷水冷凝器→冷冻盐水冷凝器→真空泵湿粕脱溶罐→节能器→水冷凝器→冷冻盐水冷凝器→真空泵1.2 工艺说明该工艺流程与溶剂法提取植物油十分相似。
但酒精与水的共沸点(常压下共沸点为78.15℃)高于正己烷(69℃),酒精的蒸发潜热是正己烷的近2.5倍,因此酒精溶剂气体的回收会消耗更大的能量。
考虑到换热器的传热系数,通常所需的加热面积更小,而冷却面积会更大一些。
同时,由于豆粕在含水酒精溶液中会吸水溶胀并且浸出速率相对较低,因此对于同样的浸出能力,用醇洗豆粕方法制备浓缩蛋白所需的浸出器体积要比传统油脂工业用的正己烷萃取豆坯的浸出器大很多倍,造成设备投资相对较大。
在溶剂消耗方面,先进的酒精浸出系统可以使溶剂消耗在30kg/t物料以下,仍高于6号溶剂浸出油脂系统的2kg/t物料以下。
酒精浸出湿粕和含水酒精结合较紧密是造成消耗偏高的主要原因。
- 1、下载文档前请自行甄别文档内容的完整性,平台不提供额外的编辑、内容补充、找答案等附加服务。
- 2、"仅部分预览"的文档,不可在线预览部分如存在完整性等问题,可反馈申请退款(可完整预览的文档不适用该条件!)。
- 3、如文档侵犯您的权益,请联系客服反馈,我们会尽快为您处理(人工客服工作时间:9:00-18:30)。
醇法大豆浓缩蛋白加工工艺及实践醇法大豆浓缩蛋白是在低温脱脂大豆粕 (白豆片 )基础上,使用含水食用酒精脱除可溶性碳水化合物,获得的蛋白干基含量在65%以上的商业化产品。
在此基础上,如果再将所得到的醇法大豆浓缩蛋白通过均质、热处理等手段加以物理改性,就可以获得醇法功能性大豆浓缩蛋白的商品化产品。
它与传统的大豆分离蛋白及酸洗法大豆浓缩蛋白相比具有生产过程污染小,价位低,功能性强,豆腥味低等诸多优点。
本文结合实际工作经验以及以色列Hayes公司的技术说明,对醇法功能性大豆浓缩蛋白的加工工艺、操作要点、主要设备、产品性能做一简要介绍。
1 醇法大豆浓缩蛋白制备工艺1.1 工艺流程1.1.1 浸出系统白豆片→筛选→环型浸出器浸出→ 挤压预脱溶→↓↓↓碎末酒精浸出液混合溶剂系统湿粕脱溶→干燥、磨粉→大豆浓缩蛋白粉↓溶剂气体回收系统1.1.2 混合溶剂系统酒精浸出液→薄膜蒸发→ 糖蜜→提取大豆异黄酮、皂甙→喷雾干燥→饲料级糖蜜粉1.1.3 溶剂气体回收系统环型浸出器→冷水冷凝器→冷冻液冷凝器→低压风机平衡罐薄膜蒸发器→冷水冷凝器→冷冻盐水冷凝器→真空泵湿粕脱溶罐→节能器→水冷凝器→冷冻盐水冷凝器→真空泵1.2 工艺说明该工艺流程与溶剂法提取植物油十分相似。
但酒精与水的共沸点(常压下共沸点为78.15℃)高于正己烷(69℃),酒精的蒸发潜热是正己烷的近2.5倍,因此酒精溶剂气体的回收会消耗更大的能量。
考虑到换热器的传热系数,通常所需的加热面积更小,而冷却面积会更大一些。
同时,由于豆粕在含水酒精溶液中会吸水溶胀并且浸出速率相对较低,因此对于同样的浸出能力,用醇洗豆粕方法制备浓缩蛋白所需的浸出器体积要比传统油脂工业用的正己烷萃取豆坯的浸出器大很多倍,造成设备投资相对较大。
在溶剂消耗方面,先进的酒精浸出系统可以使溶剂消耗在30kg/t物料以下,仍高于6号溶剂浸出油脂系统的2kg/t物料以下。
酒精浸出湿粕和含水酒精结合较紧密是造成消耗偏高的主要原因。
1.3 主要设备1.3.1 浸出器由于使用含水酒精浸出,浸出器最好采用不锈钢制造,碳钢设备内部加涂层也可以有效防锈。
采用H ayes专有技术可以在美国皇冠钢铁公司生产的环形拖链式浸出器技术上稍作改动就可以达到较好的浸出效果。
1.3.2 预脱溶挤压机预脱溶挤压机可以采用Hayes专有技术生产的双螺杆挤压机,通过压榨可将湿粕含溶量由60%~70%降低到45%~50% ,从而减轻后道脱溶工段负荷,缩短脱溶时间,减少溶剂损耗和热变性。
1.3.3 湿粕脱溶罐此设备为关键设备,关系到后续蛋白产品的品质和溶剂回收效率。
Hayes专有技术生产的脱溶罐系立式多层结构,罐上部设计成特殊结构,含溶湿粕进入脱溶罐后在罐下半部分上升溶剂蒸汽和夹套加热共同作用下快速脱除湿粕表面的自由溶剂;罐下部还要通入少量过热水蒸汽,以便脱除残留在豆粕微孔和毛细管中的酒精溶剂,保证豆粕成品的溶剂残留达到规定要求的同时又不至于过度受热变性。
脱溶操作在负压下进行,可以降低酒精溶剂的沸点,避免豆粕热变性。
1.3.4 薄膜蒸发器酒精浸出液在薄膜蒸发器内低温真空回收酒精。
在浓缩的最后阶段,糖蜜浓度较高因而比较黏稠,对设备性能要求较高。
1.4 操作要点1.4.1 选料低温脱脂豆粕的质量直接影响浓缩大豆蛋白成品的蛋白含量及功能特性,只有高质量的豆粕才能得到高质量和高蛋白含量的浓缩蛋白。
所以应选取无霉变,含皮量低,杂质少,蛋白质含量高 (干基含量≥50%),氮溶解指数50%~70%的豆粕作原料。
原料进浸出器前必须筛选除去碎末,以免溶剂渗滤性不好,堵塞浸出器筛板。
残油不能太高,否则影响酒精溶剂的渗透性。
1.4.2 浸出根据成品蛋白含量及最终混合溶剂的浓度,调节料溶比在1∶(5~8),浸出温度保持在55℃左右,浸出时间2~4h。
1.4.3 湿粕脱溶根据出口干粕的脱溶情况和热变性情况调整真空度、干燥温度及罐内的停留时间。
1.4.4 薄膜蒸发含水酒精浸出液的成分十分复杂[3],在进入薄膜蒸发器前必须将大量的粕末及浓缩析出物过滤干净。
1.5 产品质量浓缩蛋白产品要求风味清淡,色泽黄白,重金属含量符合国家相关标准,其主要指标如表1所示。
表1大豆浓缩蛋白成品主要质量指标项目指标项目指标粗蛋白 68%~72% 碳水化合物 16%~20%(N×6.25,干基 )水分 6%~10% 菌落总数 < 5000/g粗脂肪 0.5%~1% 沙门氏菌阴性/25g粗纤维 3%~5% 大肠杆菌阴性/25g灰分 4%~6% 酵母及霉菌 < 100/g2 醇法大豆浓缩蛋白功能改性工艺2.1 工艺流程大豆浓缩蛋白粉→与碱液均匀混合→高压均质→盘管瞬时加热改性并灭菌→真空冷却→喷雾干燥→不同批次产品混合→喷涂磷脂→过筛→包装2.2 工艺说明该工艺流程与大豆分离蛋白的部分生产工艺相似,在实际生产中改性浓缩蛋白和大豆分离蛋白确实可以共线生产。
浓缩蛋白的功能改性(或称“复性”)并非真正意义上的恢复蛋白分子的天然状态 ,而是通过高压均质使物料经历多次剪切、空化作用 ,使醇变性蛋白的次级键断开; 再经过高温短时热处理,使蛋白质分子重排、缔合,转变为大分子量的蛋白质分子聚集物[4]。
目前改性浓缩大豆蛋白粉的蛋白质分散指数(PDI)一般为40~60,与分离蛋白(PD I≥80)相比有不小的差距; 但通过采用在蛋白粉产品表面上喷涂磷脂的方法,可以有效改善产品的润湿性及分散性,在一定程度上克服这一缺陷,并且能起到抑制粉尘,方便使用的目的。
2.3 主要设备2.3.1 混合器该设备保证蛋白粉在稀碱液中按比例均匀混合,有利于后续的均质、热处理及喷雾干燥。
2.3.2 高压均质机要求均质压力不低于300MPa,设备稳定可靠。
2.3.3 瞬时加热盘管该设备直接影响最终产品的性能,是决定改性项目成败的最关键因素,加热时间控制在1min内,应配备自控装置。
2.3.4 喷雾干燥采用压力式喷雾干燥器生产能力大,塔顶及塔壁不易粘附,但是喷嘴容易堵塞及磨损。
2.4 操作要点2.4.1 混合定期检查蛋白溶液的pH及分散情况,调整固液比和加碱量。
2.4.2 均质定期检查均质机的压力及有无漏液情况。
2.4.3 喷雾运行中监控高压泵压力,保证雾化效果,定期检查喷嘴有无堵塞,清扫塔体。
2.4.4 CIP定期用碱液及洗涤剂对所有管线进行CIP清洗,以保证微生物指标不超标。
2.5 产品质量2.5.1 功能性检测由于大豆蛋白功能性检测方法在行业内尚未形成统一标准,因此各个公司的功能检测结果一般只用于内部控制,不对外公开,用户可以根据实际用途判断其功能性好坏。
在这里推荐一种国外大豆蛋白行业普遍采用的简易功能性检测方法[5]。
该方法可以综合衡量蛋白产品的持水、持油、乳化、凝胶强度以及蛋白乳化胶对加热、冷却加工的稳定性: 1份测试蛋白粉,5~7份的精炼油(如玉米油)以及5~7份的水,将全部的精炼油和一半的水以最高转速在真空混合器中混合5min,而后加入测试蛋白粉以及另一半水,持续混合10min, 将所得的蛋白乳化胶迅速加热到90℃,取出后置0~5℃冰箱中冷藏过夜,如果能形成坚硬的乳化胶(凝胶强度可用质构仪检测)并且表面无油、水析出,即可判定该蛋白粉具有高功能性(蛋白/水/油为1∶5∶5) 或非常高的功能性(蛋白/水/油为1∶7∶7) 。
2.5.2 其他质量指标功能性浓缩蛋白产品同样要求风味清淡,色泽黄白,重金属含量符合国家相关标准,表1理化及微生物指标同样适用,添加磷脂的产品油脂含量可能要比表1所列的指标略微偏高。
3 生产工艺改进[5]以上生产工艺基础上适当调整工艺路线或参数,可以进一步提高产品的溶解性、溶液黏度、可分散性、乳化性、吸水性以及持水、持油性等功能特性。
近年来,基于以上工艺的革新包括以下几个方面:改性之前用水进一步脱除非蛋白可溶物以进一步提高蛋白质含量;高温蒸汽处理;增加喷雾干燥前的滞留时间等。
普通功能性大豆浓缩蛋白粉通过适当加工可以进一步加工成为特殊“功能”的浓缩蛋白产品(如完全可溶或超高黏度等产品。
)4 结束语醇法能性大豆浓缩蛋白及改性工艺从20世纪60年代投入商业化运行以来,经过多年的工艺改进,目前已经相当成熟。
但该工艺设备复杂,投资大,使用易燃易爆的乙醇溶剂,工艺及产品质量不易控制。
在目前国内大豆分离蛋白产品产能严重过剩的情况下,如何掌握此项技术并且利用国内大量闲置的油脂浸出设备及大豆分离蛋白生产设备转为大豆浓缩蛋白的生产,是大豆加工行业迫切需要解决的课题。
醇法制备大豆浓缩蛋白工艺大豆蛋白作为一种天然的食品添加剂 ,越来越受到人们的重视。
大豆蛋白质中人体必需氨基酸含量充足,成分齐全,属于优质蛋白质。
醇法生产的浓缩蛋白具有高蛋白、低脂肪、高纤维,不污染环境的优点,因此用大豆浓缩蛋白替代动物蛋白成为国际趋势。
世界发达国家和地区对大豆蛋白产业十分重视,在加工和应用方面投入了大量的人力、物力,在应用上处于领先、技术上处于垄断地位。
我国大豆蛋白产业起步较晚, 目前仅有秦皇岛金海、山东三维、山东万得福3条生产线建成并投产,大豆浓缩蛋白市场处于培育阶段。
2006年,全球大豆浓缩蛋白产量约43万t,在欧洲,大豆浓缩蛋白年销售量达12~15万t,其中大约70%的大豆浓缩蛋白作为食品加工原料添加到各种食品中,其余的作为幼畜代乳品和宠物饲料,另有少量用于其他领域。
我国大豆浓缩蛋白2006年需求量为6万t,产出约2万t,产品供不应求,大豆浓缩蛋白缺口很大,市场前景广阔。
1 工艺简介醇法大豆浓缩蛋白生产工艺主要分为低温粕筛分、低温粕浸出、湿粕干燥、产品粉碎、糖浆蒸发、乙醇冷凝、乙醇精馏、乙醇除臭等 8个工段。
这8个工段有机结合,能够生产出高品质的大豆浓缩蛋白,同时产品得率高、生产成本低、无“三废”排放。
1.1 低温粕筛分低温豆粕经过计量后送至分级筛,分离出细粉,然后送至浸出车间。
1.2 低温粕浸出送入浸出车间的低温豆粕在浸出器内用乙醇溶液浸出。
豆粕和乙醇逆向运动 ,豆粕出浸出器前用一定比例的 95%的新鲜乙醇水溶液进行喷淋 ,然后用料溶比为 1∶ (3~5)的 65%的新鲜乙醇水溶液进行喷淋。
豆粕中醇溶性成分和水溶性糖浆溶于液体中 ,液体向豆粕进料方向流动;通过浓度梯度不断增大的液体的浸泡和喷淋 ,尽可能多的溶解出可溶性糖类 ,形成稀糖浆流出浸出器 ,进入安全罐储存。
1.3 湿粕干燥浸出后的湿粕通过埋刮板进入挤压机 ,通过挤压作用分离出部分液体。
挤压后的湿粕进入真空脱醇器 ,物料在脱醇器内不断地被翻动 ,均匀受热 ,在微负压状态下脱除粕中的乙醇 ,并调整水分至合适范围即为成品粕。
从真空脱醇器抽出来的气体 ,经过捕集器捕集粕末 ,再去冷凝器冷凝 ,不凝气体去尾气回收系统。