提高镀液的阴极极化度
镀锌时ph对镀层的影响

氯化物镀锌时pH对镀层的影响1.PH值对镀液和镀层的影响生产实践表明,PH值对氯化钾镀锌也是至关重要的。
镀液的PH值一般控制在5-6之间,过髙或过低都是不利的。
镀液值的大小会影响镀液性能,诸如阴极电流效率,分散能力和阳极溶解性能等。
值过高时,工艺性能将严重恶化,主要表现为,镀件光亮范围缩小〈即电流密度变窄〉,凹陷处镀层发暗;而髙电流密度处(如边缘和夹角处)容易烧焦,镀层粗糙、不光亮,同时也会影响镀层的韧性和结合力。
如果PH>6.8,并长时间在这样条件下进行电镀将会阻碍阳极溶解,并在阳极表面生成碱式锌盐膜,增加槽电压,还会使镀层局部出现灰黑色或黑色条纹。
这时就要注意镀锌光亮剂的选择。
过髙时,还会造成锌离子以氢氧化锌的形式沉淀,使镀液浑浊,巔终导致无法正常生产。
如果值过低(例如PH<5),则会使阳极溶解加快,镀液中锌离子浓度就增髙,将会降低电流效率和分散能力。
PH值过低时,还会导致镀液中铁杂质不能形成氢氧化铁沉淀,因此,铁杂质会越积越多。
在滚镀时,因有铁杂质的干扰,还容易出现滚桶眼印。
为此,PH值应控制得略比5高一些为好。
此时,铁杂质容易沉到槽底,对镀层干扰较少。
氯化物镀锌出现漏镀的处理方法(1)首先分析镀液的组成,若Zn离子和Cl-离子的浓度,严重失调,则必须稀释镀液以降低离子浓度,同时提髙氯离子浓度,即增加氯化钾。
(2)新的光亮剂在加入镀槽之前,最好在实验室用赫尔槽检验一下它的质量。
然后,按正常量加入。
总电流开1A、若赫尔槽试验片能全光亮,表明光亮剂质量好。
若低端无镀层,表明该光亮剂质量欠隹,应更换另一厂家的镀锌光亮剂。
⑶pH调节值的正确方法,应把浓盐酸稀释1-2倍,一边搅拌镀液,一边加入稀盐酸,并随时用精确的pH试纸测定pH。
当PH= 5.5时,要更小心地加盐酸。
当PH=5时,应停加盐酸。
如PH值太低,可用稀碱溶液(如5%NaOH)来调节。
当碱加入后,也许会出现白色的沉淀物,这是Zn(OH)2此沉淀物在激烈地搅拌下,会慢慢地溶解,而少量的不溶解物会自然地沉淀于槽底,不影响生产。
电镀质量六大影响因素

电镀质量六大影响因素影响电镀质量的因素很多,包括镀液的各种成分以及各种电镀工艺参数,下面讨论其中的主要因素。
(l) pH值的影响镀液中的pH值影响氢的放电电位、碱性夹杂物的沉淀,还影响络合物或水化物的组成以及添加剂的吸附程度。
但是,对各种因素的影响程度一般不可预见。
最佳的pH值往往要通过试验决定。
在含有络合剂离子的镀液中,pH值可能影响存在的各种络合物的平衡,因而必须根据浓度来考虑。
电镀过程中,若pH值增大,则阴极效率比阳极效率高,pH值减小则反之。
通过加入适当的缓冲剂可以将pH值稳定在一定的范围。
(2)添加剂的影响镀液中的光亮剂、整平剂、润湿剂等添加剂能明显改善镀层组织。
这些添加剂有无机和有机之分,无机添加剂在电解液中形成高分散度的氢氧化物或硫化物胶体,吸附在阴极表面阻碍金属析出,提高阴极极化作用。
有机添加剂多为表面活性物质,它们会吸附在阴极表面形成一层吸附膜,阻碍金属析出,因而提高阴极极化作用。
另外,某些有机添加剂在电解液中形成胶体,会与金属离子络合形成胶体一金属离子型络合物,阻碍金属离子放电而提高阴极极化作用。
(3)电流密度的影响任何电镀液都必须有一个能产生正常镀层的电流密度范围。
当电流密度过低时,阴极极化作用较小,镀层结晶粗大,甚至没有镀层。
随着电流密度的增加,阴极极化作用也随着增加,镀层晶粒越来越细。
当电流密度过高,超过极限电流密度时,镀层质量开始恶化,甚至出现海绵体、枝晶状、“烧焦”及发黑等。
电流密度的上限和下限是由电镀液的本性、浓度、温度和搅拌等因素决定的。
一般情况下,主盐浓度增大,镀液温度升高,以及有搅拌的条件下,可以允许采用较大的电流密度。
(4)电流波形的影响电流波形的影响是通过阴极电位和电流密度的变化来影响阴极沉积过程的,它进而影响镀层的组织结构甚至成分,使镀层性能和外观发生变化。
实践证明,三相全波整流和稳压直流相当,对镀层组织几乎没有什么影响,而其他波形则影响较大。
例如,单相半波会使镀铬层产生无光泽的黑灰色;单相全波会使焦磷酸盐镀铜及铜锡合金镀层光亮。
电镀镀液各成分的作用

电镀镀液各成分的作用(1)氧化锌:是提供锌离子的主盐。
锌在电镀镀液中形成两种络合盐:一是锌氰化钠络合盐Naz(Zn(CN)4);另一种是锌酸钠络合盐Na2[Zn(011)4),它们会随游离氰化钠或游离氢氧化钠含量不同而改变它们的含量比率:当锌含量提高会提高电流效率,但镀层粗糙,光亮度降低,若锌含量偏低,镀层均镀能力与深镀能力提高,但镀层不易镀厚,电流效率下降。
因此要控制锌的含量在工艺规定范围,而且还要使氰化钠与氢氧化钠的含量控制在一定范围才能使镀层质量稳定。
(2)氰化钠:是镀液主络合剂。
氰化钠除与锌离子全部络合外,还要存在一定的游离氰化钠才能使镀层结晶细致。
因此,控制全部氰化钠与锌的比值(M比)在一定范围很重要,一般在2一3.2左右,氰化钠偏高,镀层结晶细致深镀能力降低,电流效率也降低,造成大量析氢,氰化钠偏低则镀层粗糙发灰。
(3)氢氧化钠:是辅助络合剂。
除与锌全部络合外,镀液还要保持一定量的游离氢氧化钠,才能使镀层结晶细致,氢氧化钠与锌的比值一般在2 -2.50氢氧化钠能提高导电性,促使锌板溶解,提高电流效率。
当镀液中氢氧化钠含童偏高时,使锌板的化学与电化学溶解加快,锌含量升高,沉积速度也加快,镀层结晶粗糙;若氢氧化钠偏低,则导电性差,电流效率降低,镀层也会粗糙。
氢氧化钠在很多东莞电镀厂里有用到!(4)硫化钠与甘油:硫化钠是镀液中必不可少的成分。
它除了有一定发亮作用外,主要是能除去重金属杂质(如铅、锡等)。
甘油能使镀层平滑细致。
硫化钠若多加的话,它与锌生成絮状硫化锌,使镀液阴极极化作用提高,但镀液混浊,锌的损失大。
一般添加硫化钠不超过3g/L。
(5)洋茉莉醛与钥酸钠:组合使用具有很好的光亮效果。
由于洋茉莉醛不溶于水,因此要用酒精在60℃左右把洋茉莉醛溶解好,在另一容器把重量为洋茉莉醛两倍的重亚硫酸钠溶解成饱和溶液,在不断搅拌下把洋茉莉醛倒人饱和的重亚硫酸钠溶液中即完成磺化反应。
反应产物可溶于水,与钥酸钠一起溶解加入。
电镀处理中的阳极和阴极的选择

电镀处理中的阳极和阴极的选择电镀处理是一种通过电化学方法在金属表面形成一层金属或合金镀层的表面处理技术。
它既能够提高金属表面的耐腐蚀性能,也能够提高金属表面的装饰性能和机械性能。
同时,电镀处理也广泛应用于机械制造、电子、航空等行业,达到了极其重要的作用。
电镀处理中的阳极和阴极的选择是影响电镀效果的重要因素,下面将会详细探讨它们的选择。
一、电镀处理中的阳极1、阳极的作用阳极是电镀液中含有被电极化金属的电极,当电流通过电解槽时,金属阳极被氧化释放出阳离子。
阳离子在液体中游离并在工件的表面沉积,从而形成电镀层。
因此,选择适当的阳极是电镀处理的关键之一。
2、阳极的种类在电镀处理中,广泛采用的阳极有铜阳极、铝阳极、铜-铅阳极、铅阳极等。
其中,铅阳极的工作电压低、电化学性能稳定,不易氧化和腐蚀,因此是较为理想的阳极。
3、选择阳极的原则在选择阳极时,应考虑以下因素:(1)阳极应选择电化学性能稳定的材料。
(2)阳极应压降小、电流分布均匀,不能影响电镀质量。
(3)阳极形状应适应工件的形状。
(4)阳极应考虑成本等综合因素。
二、电镀处理中的阴极1、阴极的作用阴极是电镀液中没有被电极化的装置。
在电镀液中,阴极是电子的接收方,能够为阳离子提供电子,使其在工件表面沉积形成电镀层。
因此,阴极的选择也是影响电镀效果的重要因素之一。
2、阴极的种类在电镀处理中,广泛采用的阴极有铁和不锈钢等。
3、选择阴极的原则在选择阴极时,应考虑以下因素:(1)阴极应选择起电位低、化学性能稳定的材质,不得对电镀液造成污染。
(2)阴极表面应平整,电镀液需要充分接触阴极表面,以保证电流分布均匀。
(3)阴极的面积和位置应适应电解槽和工件的要求。
(4)阴极应考虑成本等综合因素。
三、结论在电镀处理中,选择适当的阳极和阴极是影响电镀效果的重要因素。
针对不同的电镀液,需要选择与之相适应的阳极和阴极。
同时,在选择阳极和阴极的时候,还需要考虑成本和工艺等因素,以达到最佳的电镀效果。
应用电化学习题复习及答案
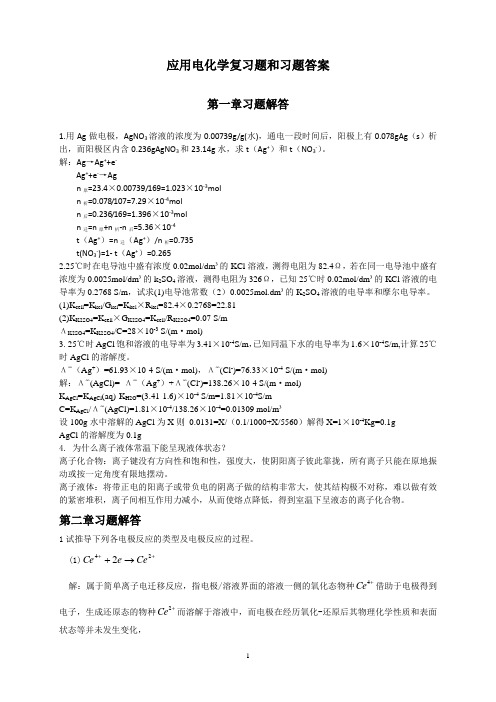
应用电化学复习题和习题答案第一章习题解答1.用Ag 做电极,AgNO 3溶液的浓度为0.00739g/g(水),通电一段时间后,阳极上有0.078gAg (s )析出,而阳极区内含0.236gAgNO 3和23.14g 水,求t (Ag +)和t (NO 3-)。
解:Ag →Ag ++e -Ag ++e -→Agn 原=23.4×0.00739/169=1.023×10-3mol n 析=0.078/107=7.29×10-4mol n 后=0.236/169=1.396×10-3mol n 迁=n 原+n 析-n 后=5.36×10-4t (Ag +)=n 迁(Ag +)/n 析=0.735 t(NO 3-)=1- t (Ag +)=0.2652.25℃时在电导池中盛有浓度0.02mol/dm ³的KCl 溶液,测得电阻为82.4Ω,若在同一电导池中盛有浓度为0.0025mol/dm ³的k 2SO 4溶液,测得电阻为326Ω,已知25℃时0.02mol/dm ³的KCl 溶液的电导率为0.2768 S/m ,试求(1)电导池常数(2)0.0025mol.dm ³的K 2SO 4溶液的电导率和摩尔电导率。
(1)K cell =K kcl /G kcl =K kcl ×R kcl =82.4×0.2768=22.81 (2)K K2SO4=K cell ×G K2SO4=K cell /R K2SO4=0.07 S/m ΛK2SO4=K K2SO4/C=28×10-3 S/(m ·mol)3. 25℃时AgCl 饱和溶液的电导率为3.41×10-4S/m ,已知同温下水的电导率为1.6×10-4S/m,计算25℃时AgCl 的溶解度。
应用电化学测试实验
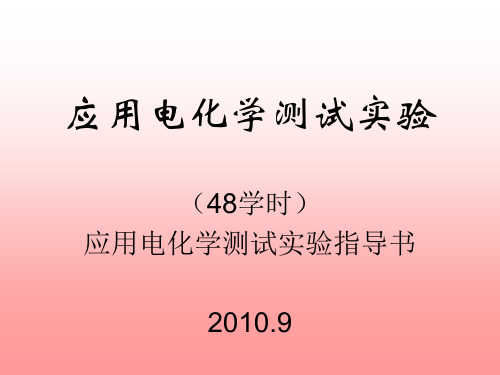
四、 实验结果与讨论
1. 添加剂用量对极化曲线的影响: 不同用量下的极化曲线,分析添加剂的加入对
镀层外观、性能的影响。 将5条曲线叠加对比分析
2. 锌镀层质量与极化曲线的关系: 主要观察表面外观状态对镀层质量的影响,
可通过极化曲线形式来体现
实验四 循环伏安曲线的测定
一、实验目的 1. 掌握电化学工作站测定循环伏安的使用方法; 2. 了解循环伏安法的基本原理及其在电化学研究 中的应用,学会分析循环伏安曲线图; 3. 了解扫描速率和浓度对循环伏安图的影响。
采用工业级原料,称量质量偏上限; 施镀(1A/dm2、10min),获得整片全光亮镀层为合格
2. 用铜库仑计法测定镀锌溶液的阴极电流效率:
➢ 配制400 mL镀锌溶液和400 mL铜库仑计溶液;
➢ 按试验装置图(图4.1)接线;
➢ 将用分析天平(0.1mg感量)称取铜阴极和锌阴极质量;
➢ 按阴极面积计算试验电流,电流密度为2 A/dm2,电镀时间
二、实验原理
电化学法是一种简单而有效的方法。制备时常 采用三电极系统,即工作电极(W)、对电极(C)与 参比电极(R)。工作电极一般用贵金属或碳类 材料制作,铂和甘汞电极可分别作为对电极和参 比电极。制备时可采用不同波型的电压或电流作 为激励信号,可采用循环伏安法、恒电位法和恒 电流法。
三、实验要求
内孔法是采用有内孔的圆管做镀件,用一定的方法 进行电镀,镀完后观察圆管内壁镀层的长度来评定镀 液覆盖能力的优劣。
三、实验内容
1. 酸性氯化钾光亮镀锌液的配制:
按配方的含量范围称取ZnCl2、KC1 并加水溶解(体积控 制在300~400mL) → 另取一烧杯,称取H3BO3,加200 mL水 并加热溶解 → 将完全溶解的H3BO3溶液倒入ZnCl2、KC1混合 液中搅拌均匀 → 加1~2克活性炭颗粒进行加热搅拌,时间 30min → 过滤 → (预留250mL空白液,做实验十四故障分 析实验) → 加入15mL NDZ-1添加剂,加水至1000mL备用。
影响镀层厚度分布均匀性的因素:镀液性能因素-阴极上的电流分布

影响镀层厚度分布均匀性的因素:镀液性能因素-阴极上的电流分布当只考虑几何因素对阴极电流分布的影响时,称为“一次电流分布”;若同时考虑电化学因素的影响,则称为“二次电流分布”。
电流分布不等于金属分布,因为后者还与不同阴极电流密度时的电流效率有关。
在此,先讨论二次电流分布的影响因素,即不考虑阴极电流效率影响的问题。
显然,此时工件上的阴极电流密度分布越均匀,则镀层厚度分布越均匀。
2.2.1 几个概念2.2.1.1 远阴极与近阴极将一个工件装挂于阴极杆上,同一个阴极工件的不同部位到阳极的距离不可能完全相同(与工件装挂方式及其本身形状和复杂程度有关)。
离阳极最近的一点(或线、面)称为“近阴极”,其与阳极的距离以k表示;离阳极最远的一点(或线、面)称为“远阴极”,其与阳极的距离用,抚表示。
2.2.1.2 远近阴极距离差远、近阴极与阳极距离之差,称为远近阴极距离差,以△l表示,则△l=l 远—l近。
2.2.1.3 镀液的电导率镀液为正负离子导电,是第二类导体,它也存在电阻。
镀液单位体积(边长为 1 cm的正方体,即l cm3)的电阻称为镀液的电阻率,以p表示。
电阻的倒数称为电导,电阻率的倒数二则为电导率,单位为“西门子/厘米”(S/cm)。
电流通过电阻时会产生电压降。
平时所说的“槽电压”就是电流通过镀液、阴极杆与挂具、挂具与工件及阳极相关部分总串联电阻的电压降。
镀液的电导率越高,则槽电压越低。
整流器的输出电压要高于槽电压,其差值则为汇流排、汇流排与阴阳极杆接触电阻、汇流排与整流器输出板接触电阻等“外电阻”的电压降。
若汇流排(或软线)面积过小、接头太多或接头接触不良,外电路上发热量大,直流损耗也就大。
当阴阳极杆的截面积过小时,也有压降损失,两个端头测得的槽电压会有差别。
将直流回路上的电压损失尽量降低,是必要的节能措施。
滚镀时,浸入镀液中滚筒孔眼的总表面积为镀液的导电面积。
若滚桶孔眼过小、开孔率过低,该值则很小,槽电压很高,槽液发热快,甚至整流器开至最大,电流也上不去。
电镀镀液各成分的作用
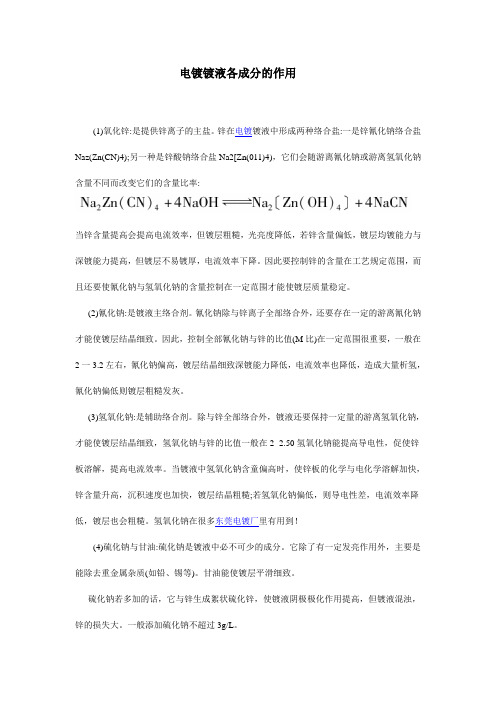
电镀镀液各成分的作用(1)氧化锌:是提供锌离子的主盐。
锌在电镀镀液中形成两种络合盐:一是锌氰化钠络合盐Naz(Zn(CN)4);另一种是锌酸钠络合盐Na2[Zn(011)4),它们会随游离氰化钠或游离氢氧化钠含量不同而改变它们的含量比率:当锌含量提高会提高电流效率,但镀层粗糙,光亮度降低,若锌含量偏低,镀层均镀能力与深镀能力提高,但镀层不易镀厚,电流效率下降。
因此要控制锌的含量在工艺规定范围,而且还要使氰化钠与氢氧化钠的含量控制在一定范围才能使镀层质量稳定。
(2)氰化钠:是镀液主络合剂。
氰化钠除与锌离子全部络合外,还要存在一定的游离氰化钠才能使镀层结晶细致。
因此,控制全部氰化钠与锌的比值(M比)在一定范围很重要,一般在2一3.2左右,氰化钠偏高,镀层结晶细致深镀能力降低,电流效率也降低,造成大量析氢,氰化钠偏低则镀层粗糙发灰。
(3)氢氧化钠:是辅助络合剂。
除与锌全部络合外,镀液还要保持一定量的游离氢氧化钠,才能使镀层结晶细致,氢氧化钠与锌的比值一般在2 -2.50氢氧化钠能提高导电性,促使锌板溶解,提高电流效率。
当镀液中氢氧化钠含童偏高时,使锌板的化学与电化学溶解加快,锌含量升高,沉积速度也加快,镀层结晶粗糙;若氢氧化钠偏低,则导电性差,电流效率降低,镀层也会粗糙。
氢氧化钠在很多东莞电镀厂里有用到!(4)硫化钠与甘油:硫化钠是镀液中必不可少的成分。
它除了有一定发亮作用外,主要是能除去重金属杂质(如铅、锡等)。
甘油能使镀层平滑细致。
硫化钠若多加的话,它与锌生成絮状硫化锌,使镀液阴极极化作用提高,但镀液混浊,锌的损失大。
一般添加硫化钠不超过3g/L。
(5)洋茉莉醛与钥酸钠:组合使用具有很好的光亮效果。
由于洋茉莉醛不溶于水,因此要用酒精在60℃左右把洋茉莉醛溶解好,在另一容器把重量为洋茉莉醛两倍的重亚硫酸钠溶解成饱和溶液,在不断搅拌下把洋茉莉醛倒人饱和的重亚硫酸钠溶液中即完成磺化反应。
反应产物可溶于水,与钥酸钠一起溶解加入。
电镀基础化学知识

电镀基础化学知识1.盐酸有何特征?答:纯净的盐酸是无色透明的液体,一般因含有杂质三氯化铁而呈黄色。
常用浓盐酸中约含37%的氯化氢。
盐酸易挥发,是一种强酸。
在电镀生产中广泛使用盐酸作为浸蚀剂。
2.硫酸有和特征?答:浓度为96%的硫酸溶液,比重为1.84。
浓硫酸具有吸水性,吸水过程中放出大量的热量。
在电镀生产中广泛使用硫酸作为浸蚀剂,由于其挥发性低,所以可利用加热提高浸蚀速度。
3.硝酸有何特征?答:硝酸是一种氧化型的强酸,在见光受热时分解放出氧而使别的物质氧化,所以硝酸应盛在棕色瓶内,电镀生产中广泛使用权有作为浸蚀剂。
4.现有浓盐酸、浓硝酸、浓硫酸各一坛,能凭目测将它们分辨出来吗?答:冒白雾的是盐酸,冒黄烟的是硝酸,无烟雾的是硫酸。
5.如何区别碳酸钠,片碱(NaOH)?答:碳酸钠又名纯碱,又称弱碱,是白色粉末,水溶液呈碱性,电镀中配制去油溶液。
片碱,化学名氢氧化钠,是强碱,又称烧碱,是白色固体或片状体。
与水溶解后放出热量,易灼烧皮肤,电镀中用碱性镀槽、发黑、去油等用处。
6.什么叫溶液、溶剂与溶质?答:一种或数种物质分散到另一种液体物质里形成的均匀、稳定液体叫溶液。
能够溶解其它物质的液体叫溶剂,被溶剂溶解的物质叫溶质。
7.什么叫溶解与溶解度答:溶质在溶剂作用下,以分子状态不断地扩散到溶剂分子间去的过程叫做溶解。
在一定温度和压力下,某溶质在100克溶剂里达到饱和所溶解的克数,叫做该溶质在这种溶剂里的溶解度。
8.什么叫溶液浓度?答:一定量溶液里所含溶质的量叫做溶液的浓度。
溶液浓度的表示方法主要有比例浓度、重量百分浓度、克/升浓度、摩尔浓度与当量浓度等。
9.什么叫比例浓度?答:以溶质与溶剂的重量或体积之比来表示的浓度叫比例浓度。
一般比例浓度中均标明是重量比或是体积比,若不标明,则固体按重量计,液体按体积计。
如配制1:1的盐酸溶液,将1体积的浓盐酸与1体积的水混合即得;又如配制1:5000的高锰酸钾溶液,将1克高锰酸钾溶于5000毫升水中即得。
电镀镍钴合金镀液与操作
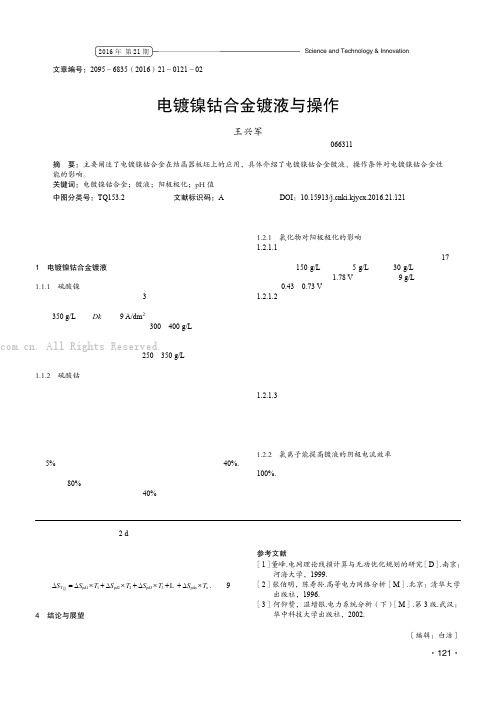
Science and Technology & Innovation ┃科技与创新·121·文章编号:2095-6835(2016)21-0121-02电镀镍钴合金镀液与操作王兴军(河北省秦皇岛市长白结晶器有限责任公司,河北 秦皇岛 066311)摘 要:主要阐述了电镀镍钴合金在结晶器板坯上的应用,具体介绍了电镀镍钴合金镀液、操作条件对电镀镍钴合金性能的影响。
关键词:电镀镍钴合金;镀液;阳极极化;pH 值中图分类号:TQ153.2 文献标识码:A DOI :10.15913/ki.kjycx.2016.21.121近年来,电镀镍钴合金工艺被广泛应用于电镀板坯结晶器铜板。
结晶器板坯是连铸机的重要部件,要求具有耐高温、耐磨损、耐腐蚀性能。
镍钴合金具有较高的硬度,组织致密,耐磨性和耐高温性能都比较好。
在结晶器板坯上,电镀镍钴合金可以满足性能要求。
1 电镀镍钴合金镀液 1.1 电镀镍钴合金主盐 1.1.1 硫酸镍对于硫酸镍,需要注意以下3点:①随着硫酸镍质量浓度的增加,最大电流密度不断提高,光亮度也在增加。
当质量浓度为350 g/L 时,Dk 可达9 A/dm 2。
由此可见,硫酸镍含量高,则光亮度、平整性都好。
其范围在300~400 g/L 为宜,镍离子含量相对稳定,可使用较高电流密度。
②硫酸镍质量浓度增加,阴极极化值下降,低质量浓度的硫酸镍阴极极化较高,镀层结晶细致。
综上所述,选择硫酸镍250~350 g/L 为宜。
③当硫酸镍含量升高时,镀液的分散能力呈线性下降。
1.1.2 硫酸钴为了保证镀层中的钴含量,在施镀的过程中,需要不断地向镀液中补充硫酸钴。
镍与钴的主盐浓度比例的变化直接影响合金镀层镍与钴的比例。
在其他条件不变的情况下,钴的质量浓度比例越高,镀层含钴量越高。
镍钴合金属于异常共沉积合金,电极电位较负的钴优先于镍在阴极上沉积。
由于钴比镍优先在阴极上沉积,所以镀液中钴盐质量浓度的变化对镀层成分影响明显,镀液中钴离子稍有增加,镀层中钴含量就会增加很多。
电镀镍的基本知识

硫酸镍为镍液中的主盐,镍盐主要是提供镀镍所需的镍金属离子并兼起着导电盐的作用。
镀镍液的浓度随供应厂商不同而稍有不同,镍盐允许含量的变化较大。
镍盐含量高,可以使用较高的阴极电流密度,沉积速度快,常用作高速镀厚镍。
但是浓度过高将降低阴极极化,分散能力差,而且镀液的带出损失大。
镍盐含量低沉积速度低,但是分散能力很好,能获得结晶细致光亮镀层。
缓冲剂──硼酸用来作为缓冲剂,使镀镍液的pH值维持在一定的范围内。
实践证明,当镀镍液的pH值过低,将使阴极电流效率下降;而pH值过高时,由于H2的不断析出,使紧靠阴极表面附近液层的pH值迅速升高,导致Ni(OH)2胶体的生成,而Ni(OH)2在镀层中的夹杂,使镀层脆性增加,同时Ni(OH)2胶体在电极表面的吸附,还会造成氢气泡在电极表面的滞留,使镀层孔隙率增加。
硼酸不仅有pH缓冲作用,而且他可提高阴极极化,从而改善镀液性能,减少在高电流密度下的“烧焦”现象。
硼酸的存在还有利于改善镀层的机械性能。
阳极活化剂──除硫酸盐型镀镍液使用不溶性阳极外,其它类型的镀镍工艺均采用可溶性阳极。
而镍阳极在通电过程中极易钝化,为了保证阳极的正常溶解,在镀液中加入一定量的阳极活化剂。
通过试验发现,CI—氯离子是最好的镍阳极活化剂。
在含有氯化镍的镀镍液中,氯化镍除了作为主盐和导电盐外,还起到了阳极活化剂的作用。
在不含氯化镍或其含量较低的电镀镍液中,需根据实际性况添加一定量的氯化钠。
溴化镍或氯化镍还常用来作去应力剂用来保持镀层的内应力,并赋与镀层具有半光亮的外观。
润湿剂——在电镀过程中,阴极上析出氢气是不可避免的,氢气的析出不仅降低了阴极电流效率,而且由于氢气泡在电极表面上的滞留,还将使镀层出现针孔。
镀镍层的孔隙率是比较高的,为了减少或防止针孔的产生,应当向镀液中加入少量的润湿剂,如十二烷基硫酸钠、二乙基已基硫酸钠、正辛基硫酸钠等,它是一种阴离子型的表面活性物质,能吸附在阴极表面上,使电极与溶液间的界面张力降低,氢气泡在电极上的润湿接触角减小,从而使气泡容易离开电极表面,防止或减轻了镀层针孔的产生。
阴极极化
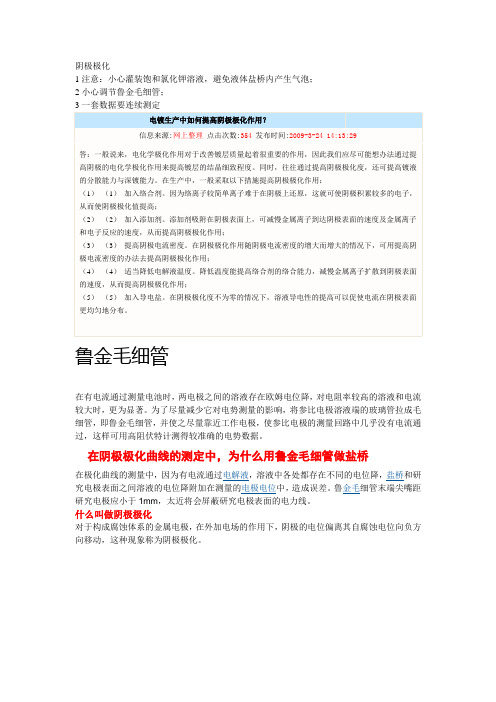
阴极极化
1注意:小心灌装饱和氯化钾溶液,避免液体盐桥内产生气泡;
2小心调节鲁金毛细管;
鲁金毛细管
在有电流通过测量电池时,两电极之间的溶液存在欧姆电位降,对电阻率较高的溶液和电流较大时,更为显著。
为了尽量减少它对电势测量的影响,将参比电极溶液端的玻璃管拉成毛细管,即鲁金毛细管,并使之尽量靠近工作电极,使参比电极的测量回路中几乎没有电流通过,这样可用高阻伏特计测得较准确的电势数据。
在阴极极化曲线的测定中,为什么用鲁金毛细管做盐桥
在极化曲线的测量中,因为有电流通过电解液,溶液中各处都存在不同的电位降,盐桥和研究电极表面之间溶液的电位降附加在测量的电极电位中,造成误差。
鲁金毛细管末端尖嘴距研究电极应小于1mm,太近将会屏蔽研究电极表面的电力线。
什么叫做阴极极化
对于构成腐蚀体系的金属电极,在外加电场的作用下,阴极的电位偏离其自腐蚀电位向负方向移动,这种现象称为阴极极化。
镀铜不均影响因素理论推导

TO :周经理、电镀 Date :2009-10-16 FM :工艺/陈世金Sub : 镀铜均匀性影响因素理论推导一、 目的:(略)二、均匀性数据对比:(略)三、影响因素推导:1.首先了解一下电镀原理:简单来说,电镀指借助外界直流电的作用,在溶液中进行电解反应,使导电体例如金属的表面沉积一金属或合金。
将直流电流的正负极分别用导线连接到镀槽的阴、阳极上,当直流电通过两电极及两极间含金属离子的电解液时,电镀液中的阴、阳离子由于受到电场作用,发生有规则的移动,阴离子移向阳极,阳离子移向阴极,这种现象叫“电迁移”。
此时,金属离子在阴极上还原沉积成镀层,而阳极氧化将金属转移为离子。
当然,离子的移动除电迁移外,还可以通过对流和扩散迁移。
当阴,阳离子到达阳,阴极表面时,就会发生氧化还原反应:C u →Cu 2++2e - (阳极)Cu 2++2e -→C u(阴极)(左图为电镀原理简单示意图)法拉第第一定律:金属在电解时析出的重量与电解液中所通过的电流和时间成正比。
即W=kIt ,(k 为比例常数)该定律知:影响镀层厚度的是电流和通电时间,要保证镀层厚度在通电时间一定的条件下,只与电流强度有关。
再由I=Q/t 知:影响电流是单位时间通过电荷的多少,通过电荷的多少又与电场线的分布直接相关联。
也就是说,电场在阴极上的分布状况直接影响镀层的均匀性。
这一部分是我们需要改善的2.知道影响镀层均匀性是与电流在阴极上的分布有直接关系后,再来找出影响电流分布均匀的因素。
很显然,影响电流分布的只有设备和药液。
将我们设备的构造简单说一下,阳极、阳极钛篮(阳极袋)、飞巴(鞍座)、夹具、挡板、浮架、整流机(火牛线)、喷管(打气)、震动、摇摆、循环泵、过滤器等。
电镀槽的形状、电极形状、尺寸及相对位置等都会影响电流分布的均匀性。
理论上讲,只有阳极与阴极平行并垂直于电极表面时,电流才在阴极表面分布最均匀。
当不能垂直(如相切)或阴极形状复杂时,就会出现边缘效应和尖端效应。
镀液中各主要成分的作用及操作条件的影响
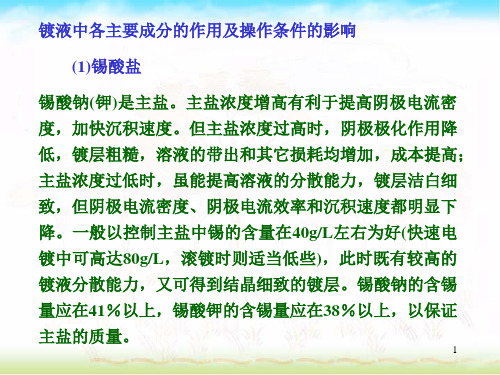
c、抑制空气中二氧化碳的有害影响 镀液中的[Sn(OH)6]2- 络离子能吸收空气中的二氧化碳,按下式分解:
[Sn(OH)6]2-+CO2 → SnO2 +CO32-+3H2O 保持一定量的游离碱可吸收空气中的二氧化碳,生成碳 酸钠(钾),可抑制二氧化碳对主盐的影响。 d、使[Sn(OH)6]2-电离度降低,提高阴极极化。 当游离碱浓度过高时,会使阳极的钝化膜溶解,此时应 加入少量的冰乙酸来调整。含量低时,阳极的表面会结上 一层壳垢,此时应补加一定量的氢氧化物。
3~4 A/dm2
阴极电流密度
8~10A/dm2
阳极
不溶性的镍板或镀镍钢板
化学法
过硼酸钠 0.4g/L
过氧化氢 0.3ml/L
Байду номын сангаас
9
生产中可采取以下方法使锡阳极保持金黄色,以Sn4+形态 正常溶解,防止产生Sn2+的生成:
a、阳极带电入槽,并始终保持阴、阳极面积比,电镀过 程中不能断电。因为,不通电或阳极电流密度小时阳极以 Sn2+形态溶解。因此,当第一槽零件入槽时,应先打开电源, 把零件挂在阴极导电棒上(必须注意不能先挂阳极),再按阴、 阳极面积比立即挂人阳极;零件出槽时,取出一挂时应立即 补充另一挂,交替进行,以便不 降低电流密度,不断电; 最后一槽零件出槽时,应先取出部分锡阳极,然后再相应地 取出零件,逐步地降低电流,直到完全取出零件再切断电源。
镀液中各主要成分的作用及操作条件的影响
(1)锡酸盐
锡酸钠(钾)是主盐。主盐浓度增高有利于提高阴极电流密 度,加快沉积速度。但主盐浓度过高时,阴极极化作用降 低,镀层粗糙,溶液的带出和其它损耗均增加,成本提高; 主盐浓度过低时,虽能提高溶液的分散能力,镀层洁白细 致,但阴极电流密度、阴极电流效率和沉积速度都明显下 降。一般以控制主盐中锡的含量在40g/L左右为好(快速电 镀中可高达80g/L,滚镀时则适当低些),此时既有较高的 镀液分散能力,又可得到结晶细致的镀层。锡酸钠的含锡 量应在41%以上,锡酸钾的含锡量应在38%以上,以保证 主盐的质量。
涂层极化曲线 标准

涂层极化曲线标准
涂层极化曲线标准涉及两个重要的概念:电极电位和极化曲线。
电极电位是指电极表面与溶液接触时,电极与溶液界面之间的电势差。
极化曲线则描述了电流密度与电极电位之间的关系,这种关系可以通过曲线来表达。
在涂层极化曲线的绘制过程中,通常会观察到三个阶段。
第一个阶段是AB 段,主要发生电化学极化,随着电流密度的增加,电极电位偏离平衡电位的程度也增加。
第二个阶段是CD段,主要发生浓差极化,此时电流密度不再上升,而电极电位急剧负移。
第三个阶段是BC段,两种极化混合发生。
涂层极化曲线在镀液性能对比与选择时具有应用价值。
一般来说,阴极极化作用大,镀层结晶细致、光亮,而阴极极化度(极化度即极化曲线的斜率,可近似看作变更单位电流密度时,电极电位相应变化的程度)大,镀液分散能力好,镀层均匀。
此外,涂层极化曲线还可以用于评估金属双极板的耐蚀性。
通过测量腐蚀电流密度和腐蚀电势,可以评估金属双极板的长期稳定性。
较低的腐蚀电流密度和较高的腐蚀电势表明金属双极板具有良好的耐蚀性。
以上内容仅供参考,如需涂层极化曲线的标准,建议查阅相关文献或咨询材料科学专家。
吴晓光-铵盐镀锌[精彩]
![吴晓光-铵盐镀锌[精彩]](https://img.taocdn.com/s3/m/c494d0f7534de518964bcf84b9d528ea81c72f32.png)
铵盐镀锌一、实验目的:1.了解和掌握电镀的基本原理,主要设备和工艺操作过程。
2.了解铵盐镀锌镀液的组成和配制,和主要工艺参数及其对电镀质量的影响。
二、基本原理:将直流电通过电解质溶液,在电极表面发生电化学反应,从而使金属离子在工件(阴极)表面沉积的过程称之为电镀。
铵盐镀锌即是用ZnCl2为主盐,以NH4Cl 为导电盐形成电解质溶液,通过直流电后在阴极工件上获得Zn镀层。
它是目前广泛应用的一种镀锌方法,其优点是镀液成本低,电流效率高,对操作人员危害小,均镀能力和深镀能力均较好。
本实验用酸性氯化铵镀锌液是由适量ZnCl2,NH4Cl,醋酸钠和少量“海鸥”洗涤剂组成。
其中除主盐ZnCl2,,导电盐NH4Cl外,醋酸钠为络合剂。
它使镀液中Zn2+以络离子形式存在,起到提高阴极极化,改善镀液分散能力和覆盖能力以及使镀层结晶细化的作用。
“海鸥”洗涤剂是表面活性剂,它不参与电极反应,但吸附于阴极表面,能使镀层平滑光亮。
除上述镀液成分外,主要的工艺参数还包括pH值,温度和电流密度。
pH值应控制在6~6.4范围,若pH值偏高时,镀液粘度增大,镀层粗糙疏松;pH值偏低,阴极上析氢多。
电流效率低,同时镀层会出现垂直条纹。
电镀过程中,由于阴极上有H2析出,pH将逐渐升高,应随时加以调整。
镀液温度应控制在15~30℃为宜,温度偏低,易使NH4Cl结晶,沉积速度慢,电流效率降低而且电流密度范围变窄;温度偏高,则使镀层粗糙,均镀能力差。
电镀过程中温度会逐渐升高,应注意控制。
阴极电流密度一般控制在1-2毫安/厘米2,最佳的电流密度根据温度、pH 值、锌离子浓度和镀件形状来确定。
在锌离子含量高,温度高及pH低的情况下,电流密度可适当加大,这有助于提高阳极极化作用,但电流密度过大,会使镀层发脆。
镀件的前期处理也是保证镀层质量重要的工艺环节,包括磨光、抛光、除锈、除油等。
三、实验仪器:稳压稳流电源 1台锌电极 1块碳钢试样 2块托盘天平 1台量筒500ml 1个烧杯1000ml 2个温度计100℃ 1支恒温水浴 1个氯化铁、氯化锌、醋酸钠、“海鸥”洗涤剂、水砂纸、pH试纸、丙酮、无水乙醇、脱脂棉等物品。
电镀基础知识100问(下)
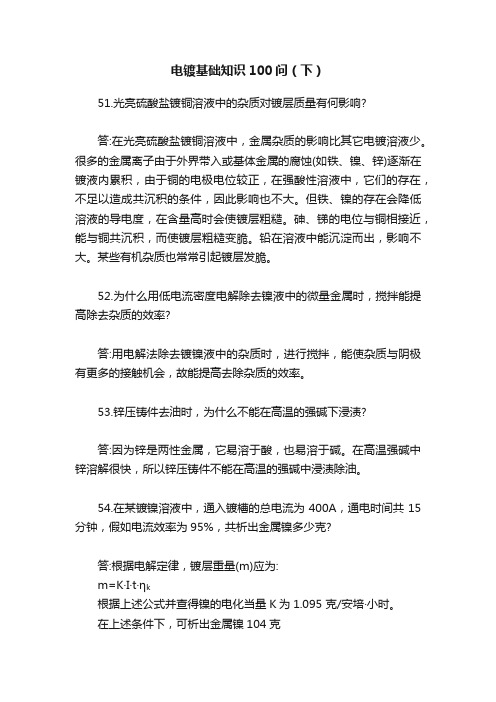
电镀基础知识100问(下)51.光亮硫酸盐镀铜溶液中的杂质对镀层质量有何影响?答:在光亮硫酸盐镀铜溶液中,金属杂质的影响比其它电镀溶液少。
很多的金属离子由于外界带入或基体金属的腐蚀(如铁、镍、锌)逐渐在镀液内累积,由于铜的电极电位较正,在强酸性溶液中,它们的存在,不足以造成共沉积的条件,因此影响也不大。
但铁、镍的存在会降低溶液的导电度,在含量高时会使镀层粗糙。
砷、锑的电位与铜相接近,能与铜共沉积,而使镀层粗糙变脆。
铅在溶液中能沉淀而出,影响不大。
某些有机杂质也常常引起镀层发脆。
52.为什么用低电流密度电解除去镍液中的微量金属时,搅拌能提高除去杂质的效率?答:用电解法除去镀镍液中的杂质时,进行搅拌,能使杂质与阴极有更多的接触机会,故能提高去除杂质的效率。
53.锌压铸件去油时,为什么不能在高温的强碱下浸渍?答:因为锌是两性金属,它易溶于酸,也易溶于碱。
在高温强碱中锌溶解很快,所以锌压铸件不能在高温的强碱中浸渍除油。
54.在某镀镍溶液中,通入镀槽的总电流为400A,通电时间共15分钟,假如电流效率为95%,共析出金属镍多少克?答:根据电解定律,镀层重量(m)应为:m=K·I·t·ηk根据上述公式并查得镍的电化当量K为1.095 克/安培·小时。
在上述条件下,可析出金属镍104克55.测定镀铬溶液的电流效率时,通过电流20A,经2小时在阴极上析出金属铬的重量为1.8克,求该镀铬液的电流效率?答:根据电解定律,镀层重量(m)应为:ηk=K·I·t·m 根据上述公式并查得六价铬的电化当量K为0.324 克/安培·小时。
在上述条件下,该镀铬液的阴极电流效率为13.9%56.重铬酸根在阴极上还原至三价铬的反应,为什么在没有催化阴离子时,一瞬间就停止了?答:镀铬溶液在没有催化阴离子的情况下,接通电流时,阴极上有氢气析出,同时部分还原为三价铬。
- 1、下载文档前请自行甄别文档内容的完整性,平台不提供额外的编辑、内容补充、找答案等附加服务。
- 2、"仅部分预览"的文档,不可在线预览部分如存在完整性等问题,可反馈申请退款(可完整预览的文档不适用该条件!)。
- 3、如文档侵犯您的权益,请联系客服反馈,我们会尽快为您处理(人工客服工作时间:9:00-18:30)。
镀液性能及测试方法
镀液的性能:分散能力、覆盖能力、整平能力 分散能力:(均镀能力)Throwing power
电解液使零件表面镀层厚度均匀分布的能力。
覆盖能力:(深镀能力) Covering power 电解液使零件深凹处沉积金属镀层的能力。
整平作用: Leveling power 电解液使有微观粗糙的金属表面填平的能力。
4.1
镀液性能及测试方法
②远、近阴极与阳极距离之差(△l)
当管件或封底腔盒体, 要求内部镀层良好时, 可借助辅助阳极。
辅助阳极
4.1
镀液性能及测试方法
③阴极与阳极距离(l1)
零件和阳极的距离(l1)增大l倍,K 值就从原来的12/8=1.5减小到 20/16=1.25,从而使分散能力得 到改善。
曲线Ⅲ: 电流效率对镀层分布起“调节” 作用。
4.1
镀液性能及测试方法
使电流和金属在阴极上分布均匀,采用的措施: •选择适当的配位剂和添加剂,提高镀液的阴极极化度; •添加碱金属盐类或其他强电解质,提高镀液的电导率; •尽可能加大零件与阳极间的距离; •采用象形阳极、辅助阴极等使电流分布均匀; •在挂具设计时,使零件主要被镀面对着阳极并与之平行; •零件在电镀槽中应均匀排布,并充满整个镀槽。
为了消除被镀件 某些部位电力线 过于集中,在该 部位附近另加某 种形状的阴极, 用以消除部分电 流,叫辅助阴极, 又称屏蔽阴极。
4.1
①镀槽形状
镀液性能及测试方法
金属在阴极上分布与 电解槽尺寸的关系
使电流分布均匀,应 将阳极和零件均匀地 挂满整个电解槽。
4.1
镀液性能及测试方法
4.1
镀液性能及测试方法
①极化度对电流分布的影响
不同斜率的极化曲线
极化度大的镀液 电流分布更均匀, 分散能力好。
4.1
镀液性能及测试方法
在电镀生产中,一般常选择电流密度的上限, 最大阴极极化作用,使分散能力得到改善。
适当的配位剂和添加剂
较高极化度的电解液
复杂零件均镀
4.1
镀液性能及测试方法
②电解液的电阻率(ρ)
提高导电性Leabharlann 施:降低溶液的电阻率(ρ)或增大溶液的导电性, 提高阴极极化度(△φ/△D)。
4.1
镀液性能及测试方法
1)几何因素 几何因素包括电解槽的形状、电极的形状、尺寸
及其相对位置等。
电力线分布示意图
电力线分布:边缘效应、尖端效应
4.1
镀液性能及测试方法
例如:镀刀尖悬挂方位
4.1
镀液性能及测试方法
如:防止边缘效应应采用辅助阴极或绝缘板。
Dk1 I1 R电液2 Dk2 I2 R电液1
R=ρL/S
∵远、近阴极的截面积S相同,ρ(电阻率)相同, Dk1/Dk2=I1/I2=R电液2/R电液1=l2/l1=Kl1/l1=K
4.1
镀液性能及测试方法
结论: 1、近阴极和远阴极上的电流密度与它们同阳极
的距离l成反比。
2、初次电流分布等于l2/l1,等于常数K, 3、K值越大,电流分布越不均匀。
4.1
镀液性能及测试方法
(2)影响电流及金属在阴极表面分布的因素
φk1:阴极与溶液界面的电位差
当直流电通电解槽时,
U =φA-φk1+I1R1 =φA-φk2 +I2R2
远、近阴极电解槽
l-近阴极; 2-远阴极; 3-阳极;4-绝缘隔板
φA:阳极与溶液界面的电位差
4.1
镀液性能及测试方法
φA-φk 工件表面材质与阳极相同时,
4.1
镀液性能及测试方法
一、镀液的分散能力
(1)镀液分散能力的数学表达式
总阻力:R电极;R电液;R极化
I=U/(R电液+R极化) ∴I1= U1/(R电液1+R极化1);
I2= U2/(R电液2+R极化2)
远、近阴极电解槽
l-近阴极;2-远阴极; 3-阳极;4-绝缘隔板
4.1
镀液性能及测试方法
由于:S1=S2 ,U1=U2
此值一般为0.xV~1V
槽压如升高?
镀液种类
槽体结构与大小
IR
阴阳极板面积
一般不超过1V~2V
极板间距
4.1
镀液性能及测试方法
(2)影响电流及金属在阴极表面分布的因素
当直流电通电解槽时,
U =φA-φk1+I1R1 =φA-φk2 +I2R2
由此得:
I1R1-φk1 = I2R2-φk2
其中: l2= l1+Δl
I1 I2
Dk1 Dk2
R电液2+R极化2 R电液1+R极化1
•R电液与R极化是影响电流在阴极上分布的主要因素。 •电流在阴极不同部位上的分布与电流到达该部位的 总阻力成反比。
4.1
镀液性能及测试方法
1)初次电流分布 (一次电流分布)
假定R极化≈0时,研究电流在阴极各部位的分布。
目的:研究几何因素对电流分布的影响。
I=DS
R=ρl1/S
R=ρl2/S
4.1
镀液性能及测试方法
I1、I2 ——近阴极和远阴极的电流强度; ρ ——电解液的电阻率;
l1——近阳极和阳极之间的距离。 △l ——远阴极和近阴极与阳极距离之差;
△φ/△D ——阴极极化度。
趋于0
4.1
镀液性能及测试方法
措施:缩小远、近阴极与阳极之间的距离差(△l); 尽可能增大零件和阳极之间的距离(l 1);
4.1
镀液性能及测试方法
2) 二次电流分布(实际电流分布) 阴极极化存在时,固定几何条件,研究电流在阴极
各部位的分布。
目的:研究电化学因素对电流分布的影响。
Dk1 Dk2
I1 I2
R电 液2+R极 化2 R电 液1+R极 化1
R极化1>R极化2,使分子与分母的数值趋于接近,
这种补偿使远、近阴极上的电流趋于均布。
0
加入碱、碱土金属盐或铵盐。
•当 ≠0时,增加镀液的导电性,可改善电流 在阴极表面的分布。 •当 →0,增加镀液的导电性能,不可能提高 分散能力。(例:镀铬液)
4.1
镀液性能及测试方法
③电流效率对镀层均布的影响
ηk-Dk关系曲线
曲线I: 电流效率对分散能力没影响。
曲线II: 电流效率使镀层分布更不均匀。
增大极间距时k值的变化
单排电镀时,槽净宽不小于0.8m; 双排电镀时,槽净宽不宜小于1.2m。
4.1
镀液性能及测试方法
④零件在电解槽中的悬挂深度
解决方法: 挂满整个电解液深度。
5cm
零件悬挂深度对镀层分布的影响
15cm
4.1
镀液性能及测试方法
挂镀复杂件镀锌槽
4.1
2)电化学因素
镀液性能及测试方法
②远、近阴极与阳极距离之差(△l)
当△l→0时,有助于电流在阴 极表面均布。 •当阳极为平板时,零件形状 越简单,越接近平面,电流 分布就越均匀。 •在实际生产中采用象形阳极, 使阳极和零件各处的距离相 等,可使电流均布。
象形阳极
4.1
镀液性能及测试方法
4.1
镀液性能及测试方法
例如:发动机气门杆镀硬铬