模具氮化及氮化设备
模具表面离子氮化工艺研究
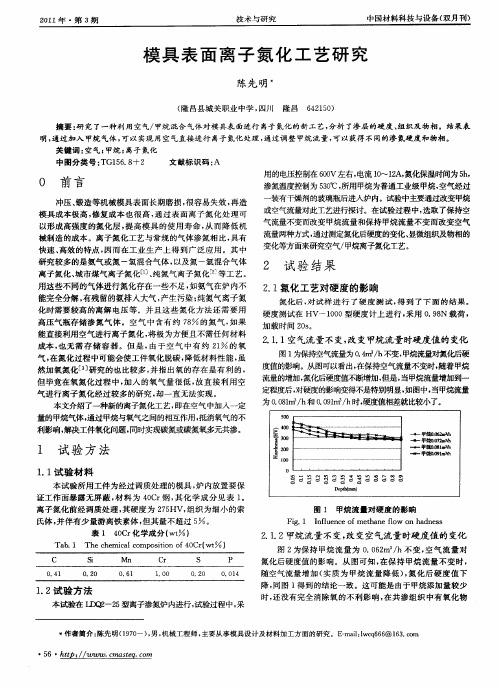
氮化后硬度值的影响 。从 图可知 , 在保 持 甲烷 流量 不变时 , 随 空气 流 量 增 加 ( 质 为 甲 烷 流 量 降 低 )氮 化 后 硬 度 值 下 实 ,
1 2试 验 方 法 .
本 试验在 U3 2 2 Q - 5型离子 渗氮 炉 内进 行 , 验过程 中 , 试 采
降 , 图 1 到 的 结 论一 致 。这 可 能是 由于 甲烷 添加 量 较 少 同 得
关键词 : 气; 空 甲烷 ; 离子 氮化
中 图 分 类 号 : G16 8 T 5 . +2
文献 标 识 码 : A
0 前 言
冲压 、 锻造 等机械模具表面长期磨损 , 很容易失效 , 再造
模 具 成 本 极 高 , 复 成 本 也 很 高 , 过 表 面 离 子 氮 化 处 理 可 修 通
(a :Me b n ta e00 2m 7 / Ai h. n 941 1/ 1 h)
3 结 论
根 据 上 面 的结 果 , 以得 出以 下 结 论 : 可
() 1 在添加一定量 的甲烷后 , 直接利 用空气 进行离 子氮
化 能够 在模 具 表 面 形 成 氮 化层 。 ( ) 着 甲烷流 量 的 改 变 , 化 后 模 具 表 面 的 硬 度 、 微 2随 氮 显 组 织及 物 相 组 成都 将 发 生 改 变 , 随着 甲烷 流 量 增加 , 化 过 程 氮
度值的影响。从图可以看出, 在保持空气流量不变时, 随着 甲烷 流量的增加, 氮化后硬度值不断增加 , 但是, 当甲烷流量增加到一
定程 度后 , 硬度 的影 响变得不是特 别明显 , 图 中, 对 如 当甲烷流量
气进行离子氮化经过较多的研究 , 却一直无法实现。
模具氮化安全操作规程

高科建材(咸阳)铝材科技有限公司模具氮化安全操作规程一、目的:明确氮化操作规定要求,确保模具氮化质量。
二、适用范围:适用于模具的氮化处理。
三、安全操作规程1、操作前设备检查。
1)在氮化前检查冷却水管道、氨分介管道和排气管道是否畅通。
2)检查氨气管道接口,不得有漏气现象。
3)检查电器线路是否正常;密封圈有否弹性,无弹性需更换新2、氮化前工件准备:工件在氮化前需清洗干净,程序为:用铁钩勾销孔放入酸中,时间参看工艺,拿出后用砂纸或刷子边洗边冲干净。
洗净后,在水中浸泡5分钟,出水用布抹干,浸入酒精中,出酒精吹干。
3、装框工件分大小模入框,一般为竖放模具,间隙为≥10mm,注意小心轻放,最上格与最下第二格分别吊上一试样,模具放完后,用铝丝加固,防止模具在吊运中撞落损坏,用吊机把框架吊入炉中,放油阀下炉盖压紧压柄。
4、氮化1)氨气为1~1.5Mpa,开减压阀0.8~0.12Mpa。
2)按工艺要求设置温度,操作仪表键盘见参考说明书。
3)到保温时间后,每半小时测量一次。
4)保持炉内压力在工艺范围内,如果超出应调节进出气阀门。
5)注意氨流量,不能变化太大。
6)整个氮化过程中,一定要保证冷却水供应,遇到停水须向上级部门反映,迅速排除故障。
5、降温:氮化结束关闭升温开关,按工艺减少氨流量及炉内压力,半小时后开鼓风机,注意打开进出风口。
6、出炉:炉内温度降至180℃以下,关氨气总阀,放松压柄,开炉盖,用吊机吊出模框,待冷至50℃以下取下试样,交试验员待检,模具从框中取出,转运模具仓。
四、本管理办法从2018-7-1日起试行。
编制:复核:批准:。
cr12w氮化处理工艺

cr12w氮化处理工艺
以下是CR12W氮化处理的一般工艺流程:
1. 预处理:
- 清洗:首先对CR12W模具钢零件进行彻底清洗,去除表面油脂、杂质和氧化皮,常用的方法包括超声波清洗、碱洗或溶剂清洗。
- 热处理:根据设计要求,可能需要先进行淬火和回火处理,以获得合适的基体硬度和内部组织结构。
2. 氮化处理:
- 装炉:将预处理过的零件放入氮化炉中,确保零件之间适当间距,避免氮化过程中相互影响。
- 升温:慢慢加热至氮化处理温度,一般在450℃至550℃之间,具体温度根据所需的氮化层深度和硬度要求确定。
- 氮化:在保护气氛(氨气或氮气)中,使氮原子渗入零件表面并与之发生化学反应,形成氮化物层,显著提高表面硬度。
- 保温:在氮化温度下保温一段时间,使氮化层充分形成和扩散,保温时间取决于零件尺寸、氮化温度和期望的氮化层深度。
- 冷却:氮化处理结束后,通常采用缓慢冷却的方式降温,以减少热应力和防止氮化层开裂。
3. 检验与后处理:
- 检验:氮化处理后进行硬度测试、金相组织观察、氮化层深度测定等,确保氮化效果达到设计要求。
- 精加工:如果需要,可进行必要的磨削或其他精加工处理,
以达到零件的尺寸精度和表面粗糙度要求。
注意:具体的氮化处理工艺参数(如温度、时间、氨气流量等)应根据实际设备条件和材料特性,并参考相关工艺规范或试验结果来确定。
模具渗氮处理

模具渗氮处理2011-07-04 16:34渗氮常称为氮化,就是将工件放在含氮介质中,加热到较低温度(480~600℃),使氮渗入其表面,形成以氮化物为主的渗层。
有些钢种的氮化层硬度高达1000~1200HV,渗后不必进行提高硬度的淬火处理。
氮化层的高硬度是因高硬度氮化物弥散分布在基体中所造成的,随渗氮温度温度升高,氮化物片厚度增加,与母相的共格关系开始破坏,硬度降低。
氮化层的耐磨性远高于渗碳层,渗氮工件的变形小,处理后不再进行加工就可以使用,高精度的工件也只需要精磨、研磨或抛光。
在渗氮层中形成大的残余压应力,有利于提高零件的疲劳强度。
渗氮温度一般稍代于淬火钢的回火温度范围。
调质状态的结构钢渗氮时,工件心部保持了状态的回火索氏体组织,在得到高硬度表面的同时具有良好的综合力学性能。
氮化层具一定热硬性,在500℃以下能长时期保持高硬度。
在600℃短时间加热,硬度也不降低,而当温度超过600~625℃时,由于高弥散分布的氮化物的聚集,而使氮化层硬度下降。
为了工件心部具有必要的力学性能,渗氮前一般要进行调质处理,获得回火索氏体组织。
渗氮往往是最后一道工序,因而氮化前要求加工到足够的精度,为了消除加工应力和减少渗氮过程的变形,一般在机械加工后要进行1、2次除应力回火。
根据渗氮的目的,可分强化渗氮(硬渗氮)和抗蚀渗氮,对要求表面硬度高、耐磨性好、热处理变形小的高精度工件,多采用强化渗氮,如精密机床的主轴、镗床的镗杆、发动机缸套、液压泵的分配轴等。
为了提高碳钢、合金钢、塑料模具钢及电工钢工件的抗蚀能力,则对其进行抗蚀渗氮。
抗蚀渗氮适用于对抗蚀性要求不太高的小零件,如仪表、打字机、缝纫机的零件。
抗蚀渗氮是在工件表面获得0.015~0.06mm厚的致密的、化学稳定性好的ε相渗氮层。
对潮湿空气、过热空气、海水、气体燃烧产生的气体具有一定耐蚀能力。
抗蚀渗氮温度比强化渗氮的温度高(550~650℃),渗氮后可以快冷。
渗氮用钢中常加入铬、钼、钨、钒、钛、铝等形成稳定氮化物的元素。
模具氮化的作用范文

模具氮化的作用范文模具氮化是指在模具表面通过一定的工艺方法将氮原子渗入模具表面,形成一层氮化物层。
模具氮化的作用主要体现在以下几个方面:1.提高模具表面硬度:模具氮化后,氮化物层具有很高的硬度,其硬度可以达到1000-1200HV。
相比之前的模具材料,氮化后的模具具有更高的耐磨性和耐蚀性,能够在使用过程中减少模具表面的磨损,延长模具的使用寿命。
2.提高模具的耐磨性:模具氮化后,氮化物层具有较高的耐磨性,能够在摩擦和挤压等工作过程中减少摩擦阻力和磨损,提高模具的耐磨性能。
尤其对于需要多次重复的冲击和摩擦工作的模具来说,氮化后的模具能够提供更好的使用效果,并减少维修和更换的频率。
3.改善模具的抗腐蚀能力:模具氮化后,氮化物层具有较高的耐腐蚀性能,能够在潮湿环境、高温环境和化学腐蚀性物质的作用下保持模具表面的完整性和稳定性,延长模具的使用寿命。
特别是对于需要在恶劣环境下工作的模具来说,氮化后的模具能够提供更好的抗腐蚀能力。
4.提高模具的抗疲劳能力:模具在工作过程中经历长时间的冲击和振动,容易出现疲劳断裂。
模具氮化后,氮化物层会改善模具的表面组织和结构,提高模具的抗疲劳性能,减少模具发生疲劳断裂的可能性,保证模具的长时间稳定工作。
5.提高模具的导热性能:模具氮化后,氮化物层具有良好的导热性能,能够更好地分散和传递模具表面的热量,降低工作温度,提高模具的散热效果。
这对于需要进行高温冲击和挤压工作的模具来说尤为重要,可以有效保护模具,并提高工作效率。
总之,模具氮化通过在模具表面形成一层氮化物层,能够提高模具的硬度、耐磨性、耐腐蚀性、抗疲劳性和导热性能,延长模具的使用寿命,提高模具的稳定性和工作效率。
因此,在模具制造和使用过程中,模具氮化是一种非常重要的表面处理方式。
一种铝合金模具氮化废气处理装置的制作方法

一种铝合金模具氮化废气处理装置的制作方
法
铝合金模具氮化技术在现代制造业中得到了广泛应用,但是氮气气体的排放会对环境产生污染,因此需要对废气进行处理。
本文介绍一种制作铝合金模具氮化废气处理装置的方法。
首先,我们需要准备以下材料和工具:一个净化塔、一根塑料管、一台风机、一些耐高温的管道、氮气气箱和电线等。
具体步骤如下:
1. 净化塔的制作:将金属网格捆扎在塔的内部,金属网格中装有碳基吸附剂。
在上部开一个进气口,下部开一个排气口。
2. 制作塑料管:将塑料管直接连接到氮气气箱和净化塔,组成一个管道。
废气从模具中排出并通过管道进入净化塔。
3. 安装风机:安装一台风机在负压方向,将废气吸入管道,并通过净化塔进行净化。
4. 接通电源:通过电线将风机和氮气气箱连接到电源,使其正常运行。
该装置能够有效地净化铝合金模具氮化产生的废气,达到了环保标准。
同时该装置的制作相对简单,成本低廉,可以应用于多种不同的氮化设备中。
氮化基础知识及设备的基本结构
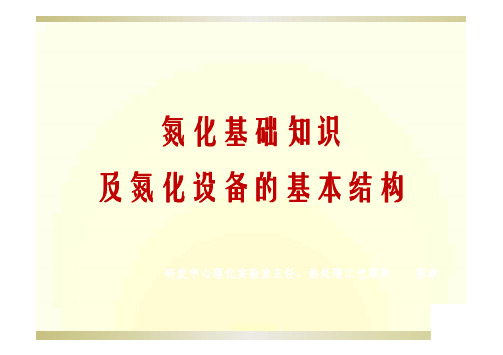
氮化基础知识及氮化设备的基本结构(一)概论①什么叫渗氮?渗氮亦称氮化,是指在一定温度下,在含氮介质中使氮原子渗入模具表层的化学热处理方法。
②氮化优点:模具氮化后具有极高的表面硬度和耐磨性,高的疲劳性和高的耐腐蚀性,加热温度低,变形小。
③氮化缺点:处理的周期较长。
④氮化种类:按目的分类:强化渗氮和抗蚀渗氮按介质分类:气体渗氮、液体渗氮、固体渗氮按设备分类:气体渗氮、离子渗氮、低压脉冲渗氮(二)原理1、气体渗氮基本过程气氛形成、吸附、分解、吸收和扩散五个步骤。
氨气在400℃以上将发生如下反应:2NH3≒3H2+2[N]⑴向炉内不断输入氨气⑵氨分子向金属表面迁移⑶氨分子吸附在金属表面⑷氨分子在相界面上不断分解,形成氮原子和氢原子⑸活性原子复合成分子,经相界面反应的扩散层界,不断从炉内排出⑹表面吸附的氮原子溶解于α-Fe中⑺氮原子由金属表面向内部扩散,并产生相应的浓度梯度⑻当超过α-Fe中的溶解度后,在表面开始形成氮化物⑼氮化物沿金属表面的垂直方向和平行方向长大⑽氮化物层不断增厚⑾从氮化物层向金属内部扩散。
2、合金元素对渗氮过程的影响①碳钢的含碳量越多,氮的扩散系数越小②合金元素的影响a、合金元素与氨的亲和力顺序,依次递增:Ni→Fe→Mn→Cr→Mo→W→Nb→V→Ti→Zr。
与氮的亲和力越强,形成的氮化物愈稳定。
b、H13渗氮时,形成合金氮化物主要由含Cr、Mo、V的碳化物与氮原子相互作用,在化合物层和扩散层形成三种弥散析出的CrN、MoN、VN2合金元素的氮化物,具有高的硬度和熔点,但很脆。
c、合金元素的存在阻碍氮在铁中的扩散。
3、渗氮层的性能特点①模具氮化后具有极高的硬度与耐磨性。
H13可达950HV-1200HV(相当于65.0-72.0HRC),因摩擦系数低,因此具有良好的耐磨性和减磨性②显著提高疲劳强度并降低缺口的敏感性;③可以抵抗水,过热蒸汽及碱性溶液的腐蚀;④渗氮表面白亮层的脆性是气体渗氮的主要问题之一,白亮层的脆性主要取决于它的相组成,主要决定因素是渗氮方法、渗氮规范和材料的化学成分。
浅谈铝型材挤压模气体氮化处理工艺

浅谈铝型材挤压模气体氮化处理工艺【摘要】挤压模在铝型材生产中具有重要地位,近年来,挤压模氮化己成为改善其表面性能的适用方法。
模具经氮化处理后,氮化层有一定的硬度、深度、韧性和耐热性,大大提高模具的抗咬合性和抗磨损性,在生产中的应用效果理想。
良好的氮化工艺可以提高模具氮化质量和使用寿命,降低成本,增强竟争力。
本文介绍了气体氮化的原理,气体渗氮系统的组成,提出了挤压模渗氮工艺方案的选择。
【关键词】挤压模具;氮化处理;工艺控制在铝型材挤压生产中,模具对产品质量、生产成本影响甚大,模具经高温高压使用后,其工作带易磨损而影响铝型材表面质量。
铝合金型材挤压模的工作条件为长时间的高温、高压,承受着强烈的热应力、冲击应力和摩擦磨损。
因此,提高模具表面硬度,延长模具使用寿命对高质量、低成本铝合金型材的生产具有重要意义。
1.气体氮化原理气体氮化的原理是在气体介质中进行的气体渗氮,由于其成本低、操作简单及产品质量稳定等,目前在国内外普遍使用,随着科学技术的发展,渗氮工艺普遍应用于工业领域,并发挥了及其重要的作用。
在氮化过程中,对密封炉通入NH3,当加热达到380一550℃时,N氏发生如下反应:2NH3?葑2[N]+3H2活性[N]原子一部分被模具工件表面吸收,随着时间增长,氮化层厚度加厚,氮原子被钢吸收后所形成的固溶体和氮化物,具有很高的强度、硬度和耐磨性,起到延长模具使用寿命的作用。
2.气体渗氮系统的组成气体渗氮设备一般由氮化炉、供氨系统(液氨罐)、氨分解率测定系统和测温系统等组成,氮化炉有多种形式,如井式电阻炉、多用箱式炉、钟罩式炉,渗氮罐一般用1Cr18Ni9Ti不锈钢制造,该材料表面有一层致密的钝化膜,本身抗氧化性好,不易氮化发脆。
由于钢中的镍的一些化合物对氨的分解率有催化作用,使氨分解率逐渐升高,不易控制,使用一段时间后应进行退氮处理。
而近年来耐热搪瓷渗氮罐的出现解决了这一问题,该罐具有抗氧化性、抗热振性、抗蚀性、耐冲击性与基体的结合性、绝缘性均良好。
软氮化和氮化处理有什么区别
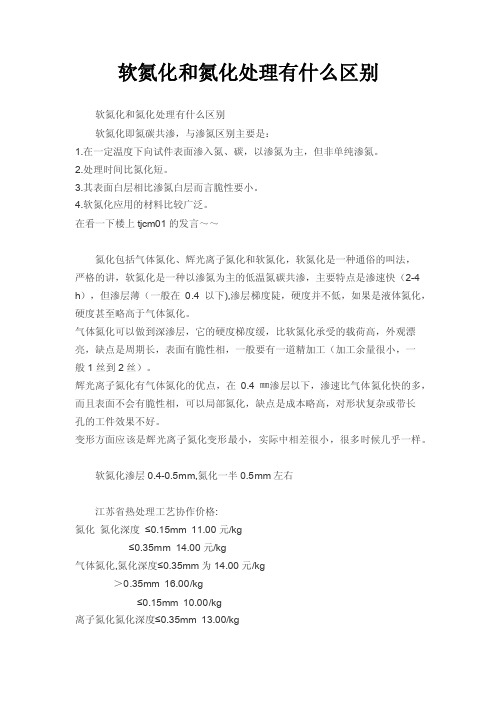
软氮化和氮化处理有什么区别软氮化和氮化处理有什么区别软氮化即氮碳共渗,与渗氮区别主要是:1.在一定温度下向试件表面渗入氮、碳,以渗氮为主,但非单纯渗氮。
2.处理时间比氮化短。
3.其表面白层相比渗氮白层而言脆性要小。
4.软氮化应用的材料比较广泛。
在看一下楼上tjcm01的发言~~氮化包括气体氮化、辉光离子氮化和软氮化,软氮化是一种通俗的叫法,严格的讲,软氮化是一种以渗氮为主的低温氮碳共渗,主要特点是渗速快(2-4 h),但渗层薄(一般在0.4以下),渗层梯度陡,硬度并不低,如果是液体氮化,硬度甚至略高于气体氮化。
气体氮化可以做到深渗层,它的硬度梯度缓,比软氮化承受的载荷高,外观漂亮,缺点是周期长,表面有脆性相,一般要有一道精加工(加工余量很小,一般1丝到2丝)。
辉光离子氮化有气体氮化的优点,在0.4㎜渗层以下,渗速比气体氮化快的多,而且表面不会有脆性相,可以局部氮化,缺点是成本略高,对形状复杂或带长孔的工件效果不好。
变形方面应该是辉光离子氮化变形最小,实际中相差很小,很多时候几乎一样。
软氮化渗层0.4-0.5mm,氮化一半0.5mm左右江苏省热处理工艺协作价格:氮化氮化深度≤0.15mm 11.00元/kg≤0.35mm 14.00元/kg气体氮化,氮化深度≤0.35mm为14.00元/kg>0.35mm 16.00/kg≤0.15mm 10.00/kg离子氮化氮化深度≤0.35mm 13.00/kg>0.35mm 15.00/kg气体氮碳共渗(软氮化) 8.30/kg软氮化即氮碳共渗,氮化是只渗氮.由于软氮化后另件表面的白亮层比氮化后白亮层脆性小,另件的韧性好故称之为"软氮化",软氮化处理后的另件表面硬度有时不比氮化低.对于不同材料软氮化处理后表面硬度在HV500-1200之间.最高硬度接近70HRC渗氮(软氮化)的常见缺陷一、硬度偏低生产实践中,工件渗氮(软氮化)后其表面硬度有时达不到工艺规定的要求,轻者可以返工,重者则造成报废。
江苏模具氮化收费情况汇报
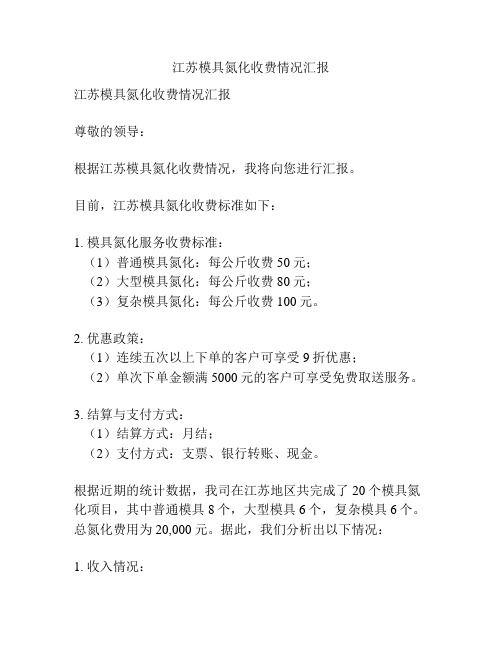
江苏模具氮化收费情况汇报江苏模具氮化收费情况汇报尊敬的领导:根据江苏模具氮化收费情况,我将向您进行汇报。
目前,江苏模具氮化收费标准如下:1. 模具氮化服务收费标准:(1)普通模具氮化:每公斤收费50元;(2)大型模具氮化:每公斤收费80元;(3)复杂模具氮化:每公斤收费100元。
2. 优惠政策:(1)连续五次以上下单的客户可享受9折优惠;(2)单次下单金额满5000元的客户可享受免费取送服务。
3. 结算与支付方式:(1)结算方式:月结;(2)支付方式:支票、银行转账、现金。
根据近期的统计数据,我司在江苏地区共完成了20个模具氮化项目,其中普通模具8个,大型模具6个,复杂模具6个。
总氮化费用为20,000元。
据此,我们分析出以下情况:1. 收入情况:(1)普通模具:收入8,000元;(2)大型模具:收入4,800元;(3)复杂模具:收入6,000元。
2. 优惠情况:据统计,没有客户符合优惠政策的条件。
3. 结算与支付方式:我司采用月结方式进行结算,目前还未向客户发出结算账单。
支付方式根据客户的要求进行选择,绝大多数客户选择了银行转账。
根据以上情况,我们初步评估了江苏模具氮化服务的市场需求和竞争状况。
通过与客户的交流和了解,我们发现当前市场上对模具氮化服务的需求较高,尤其是在大型模具和复杂模具方面。
同时,我们也注意到附近地区有几家竞争对手提供类似的服务,但我们的定价相对较低,且质量和服务上也有竞争优势。
在今后的工作中,我们将进一步推广江苏模具氮化服务,并通过与客户保持良好的反馈沟通,不断优化服务质量和提高客户满意度。
希望能够稳步扩大市场占有率,提高收入情况。
同时,我们也会关注竞争对手的动态,及时做出相应的调整和改进。
以上是对江苏模具氮化收费情况的汇报,如有任何问题或建议,欢迎指导和批评。
谢谢!。
潮州模具表面离子氮化和气体氮液的区别

潮州模具表面离子氮化和气体氮液的区别潮州模具表面离子氮化与气体氮液的区别潮州是中国著名的模具制造中心之一,其制造的模具在各个领域得到广泛的应用。
为了提高模具的硬度和耐磨性,采用离子氮化技术和气体氮液技术对模具表面进行处理,可以使其在工作中拥有更长的使用寿命和更高的性能。
然而,离子氮化与气体氮液在技术原理、成本和效果等方面存在显著的差异。
本文将对这两种技术进行比较分析,旨在帮助潮州模具制造企业选择适合自己的加工方式。
一、技术原理区别离子氮化技术是一种在真空或氮气气氛中利用电子束或离子束对模具表面进行处理的方法。
通过供应一定的电压,产生高速电子束,使模具表面的金属离子与氮离子反应生成氮化物,从而使得模具表面硬度更高、抗腐蚀性更好、耐磨性更强、耐热性更佳等优点。
气体氮液技术则是将模具浸泡在氮气液体中,达到模具表面氮化的效果。
在高压的氮气气闸下,氮气液体会产生巨大的压力和温度,使得模具表面的金属能够和氮气液体接触,而氮气液体的高温和高压可以使得氮气液体中的氮离子与金属离子结合生成氮化物,从而对模具表面进行氮化处理。
两种技术的原理不同,离子氮化主要通过高速电子束直接与模具表面的金属离子相互作用,进而实现氮化处理效果;而气体氮液在温度和压力上给予较大的影响使金属离子和氮离子进行氮化反应。
因此,两种技术在具体处理过程,时间,效果和成本等方面存在差异。
二、处理效果区别离子氮化处理可以使得模具表面硬度提高,摩擦系数降低,耐磨性、抗腐蚀性等性能得到显著提高,氮化层厚度可达几百微米,相对深度较大,常常能够有效延长模具的使用寿命,且还可添加一些其他元素如碳化物来进行复合加工。
然而,离子氮化的设备较大,工艺较为复杂,处理周期较长。
气体氮液技术在比较一些沉积物与离子氮化处理之后也能得到相同的效果,但其一般应用于薄膜、镀层和喷涂等表面处理领域中,适合批量生产、成本控制较低、氮化后表面的保养和维护相对较容易,且制程时间相对短,提高效率。
铝业公司模具氮化工艺操作规程

铝业公司模具氮化工艺操作规程1 主题内容与适用范围1.1 本标准规定了本公司挤压模具氮化各阶段的技术要求。
1.2 本标准适用于本公司挤压车间模具氮化操作工及质量管理部门监督。
2 主要工艺流程:清洗——风干——装炉——烘干——加氨——保温——加催渗剂——保温——停止加热————关闭催渗剂——随炉冷却——关闭氨气——出炉——检验3 主要工序技术要求:3.1模具清洗、装炉:3.1.1把模具放入盛有稀盐酸(10—15%)的塑料盆内浸泡≤15分钟左右后,用流水冲洗,边洗边用耐水砂纸打磨,以除去表面油污、锈迹,特别是工作带、分流孔、导流坑、模具入料口端面应清洁。
取出在干燥无油污的地方风干,烘干的模具在1—2小时内必须入炉。
盐酸溶液和金属清洗液使用几次后,视其模具清洗效果,适当兑入少许盐酸或金属清洗液,以保证溶液去污除锈能力。
必要时重新更换溶液。
3.1.2检查氮化炉及附属设备(如冷却水、料筐、炉子的气密性、气管、阀门、电动葫芦、电源等)是否处于良好状态。
3.1.3开启氮化炉电源,使炉子开始加温,同时微开炉子排气伐。
3.1.4把风干好的模具竖立摆放在模框内。
模具间距>30mm,不能摆得太密,以保证气流通畅,使氮化层均匀。
旧模、大模放在下部,新模放在上部。
在铁杯中放氯化氨≤5克, 将铁杯放在模框底部。
3.1.5关紧炉盖,先启动风机和冷却水泵,再接通氮化炉电源。
当炉温达到200℃,关闭氮化炉电源,打开炉盖,将模具平稳地吊入炉内正中,停放约15分钟,使模具彻底干燥后,再关闭炉盖。
3.2. 氮化工艺过程控制:★3.2.1排气。
加热温度设置为520℃,温升速度控制在200℃/小时,刚升温的0.5小时是排气阶段。
以500L/h的流量通入氨气,氨气压力0.15Mpa,通氨气排空气.调节阀门,使炉内压力保持在80-110mm水柱。
3.2.2氮化。
升温2.5小时使炉温达到设置加热温度520℃,通入氨气,流量1000-1100L/h,此时氨气压力0.2Mpa,氨分解为25-30%,( 适时点燃尾气)保温6小时后,再升温至535±2℃, 保温3小时。
模具氮化工艺操作规程
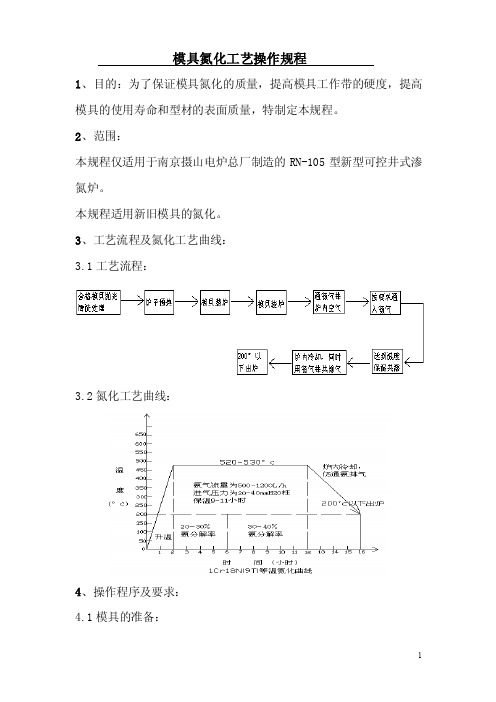
模具氮化工艺操作规程1、目的:为了保证模具氮化的质量,提高模具工作带的硬度,提高模具的使用寿命和型材的表面质量,特制定本规程。
2、范围:本规程仅适用于南京摄山电炉总厂制造的RN-105型新型可控井式渗氮炉。
本规程适用新旧模具的氮化。
3、工艺流程及氮化工艺曲线:3.1工艺流程:3.2氮化工艺曲线:4、操作程序及要求:4.1模具的准备:4.1.1新模具必须经试模合格,模具的型腔内各部位必须抛光,去掉碱垢和尖角,过渡部位要圆滑,未经处理的模具不准氮化。
4.1.2使用过的模具要按4.1.1的要求进行检查,并要重点检查桥位部分和棱角处有无裂纹,确认无误后方能重复氮化处理。
4.1.3模具表面应清洁、无油污、锈蚀和其它脏物,工作带可用酒精或汽油或香蕉水清洗干净,否则不准入炉氮化。
4.2设备气密性检查:氮化前应对加热炉、氮化罐和整个氮化系统的管道接头处进行气密性检查,保证氨气不漏和在管路中畅通无阻。
氨气对人体健康危害极大,空气中氨的含量达10-25%时,遇到火会引起爆炸。
漏气的检查办法时用酚酞试纸浸湿后放在怀疑的漏气处,试纸变红就证明漏气。
4.3炉体和温控系统检查:开炉前必须检查炉体、炉腔、炉盖、升降系统、循环风机、电气控制系统、温控系统、测温系统等是否稳定、可靠、灵活;进气管、出气管、水冷系统、氨气瓶阀门等是否正常完好。
4.4氮化过程的操作:4.4.1将模具吊入氮化罐内,封闭炉盖。
4.4.2把氨气瓶中的液氨经过减压阀,通过氨气干燥柜通入炉内,将炉内的空气排出。
时间为15分钟,氨气的压力为0.2MPα以下。
4.4.3通电升温,炉温升到100℃时,打开冷却水阀。
当炉温升到200-250℃时,保温0.5-1小时,并开动循环风机,将氮化罐和管道中的空气充分排出。
当罐内氨的分解率为零时允许继续升温。
这时可降低氨气流量,保证炉内正压,保证模具不被氧化。
4.4.4当炉温升到450℃左右时,要控制升温速度,同时,应加大氨气流量,使分解率控制在20-30%左右,迅速提高模具表面氮化的浓度。
零件的氮化处理相关知识
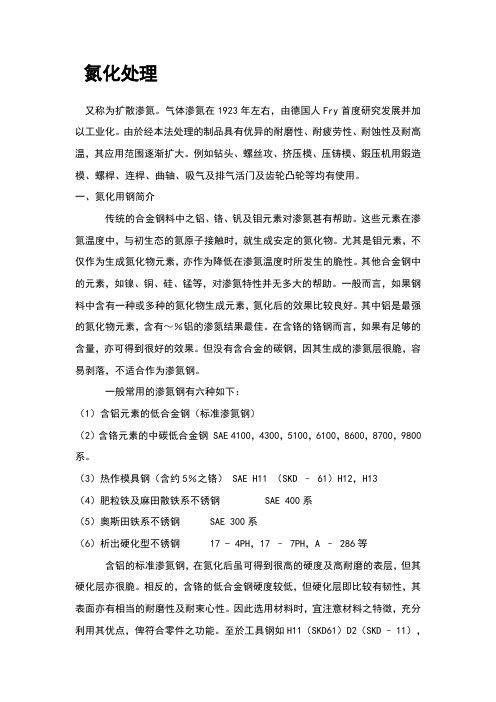
氮化处理又称为扩散渗氮。
气体渗氮在1923年左右,由德国人Fry首度研究发展并加以工业化。
由於经本法处理的制品具有优异的耐磨性、耐疲劳性、耐蚀性及耐高温,其应用范围逐渐扩大。
例如钻头、螺丝攻、挤压模、压铸模、鍜压机用鍜造模、螺桿、连桿、曲轴、吸气及排气活门及齿轮凸轮等均有使用。
一、氮化用钢简介传统的合金钢料中之铝、铬、钒及钼元素对渗氮甚有帮助。
这些元素在渗氮温度中,与初生态的氮原子接触时,就生成安定的氮化物。
尤其是钼元素,不仅作为生成氮化物元素,亦作为降低在渗氮温度时所发生的脆性。
其他合金钢中的元素,如镍、铜、硅、锰等,对渗氮特性并无多大的帮助。
一般而言,如果钢料中含有一种或多种的氮化物生成元素,氮化后的效果比较良好。
其中铝是最强的氮化物元素,含有~%铝的渗氮结果最佳。
在含铬的铬钢而言,如果有足够的含量,亦可得到很好的效果。
但没有含合金的碳钢,因其生成的渗氮层很脆,容易剥落,不适合作为渗氮钢。
一般常用的渗氮钢有六种如下:(1)含铝元素的低合金钢(标准渗氮钢)(2)含铬元素的中碳低合金钢 SAE 4100,4300,5100,6100,8600,8700,9800系。
(3)热作模具钢(含约5%之铬) SAE H11 (SKD – 61)H12,H13(4)肥粒铁及麻田散铁系不锈钢SAE 400系(5)奥斯田铁系不锈钢 SAE 300系(6)析出硬化型不锈钢 17 - 4PH,17 – 7PH,A – 286等含铝的标准渗氮钢,在氮化后虽可得到很高的硬度及高耐磨的表层,但其硬化层亦很脆。
相反的,含铬的低合金钢硬度较低,但硬化层即比较有韧性,其表面亦有相当的耐磨性及耐束心性。
因此选用材料时,宜注意材料之特徵,充分利用其优点,俾符合零件之功能。
至於工具钢如H11(SKD61)D2(SKD –11),即有高表面硬度及高心部强度。
二、氮化处理技术:调质后的零件,在渗氮处理前须澈底清洗乾净,兹将包括清洗的渗氮工作程序分述如下:(1)渗氮前的零件表面清洗大部分零件,可以使用气体去油法去油后立刻渗氮。
模具氮化种类

模具氮化种类一、硼化物氮化模具硼化物氮化模具是目前应用最广泛的模具氮化种类之一。
硼化物氮化模具主要由硼化钛、硼化铝和硼化硅等组成,具有高硬度、高耐磨性、高耐腐蚀性和高热稳定性等特点。
硼化物氮化模具在金属加工、塑料加工、玻璃加工等领域都有广泛的应用。
硼化物氮化模具的硬度通常在2000-3000HV之间,远远高于普通模具材料的硬度。
这使得硼化物氮化模具在高速切削、高温热压、高压注塑等工艺中具有优异的性能。
此外,硼化物氮化模具还具有良好的耐腐蚀性,能够有效抵抗酸碱等腐蚀介质的侵蚀,延长模具的使用寿命。
二、碳化物氮化模具碳化物氮化模具是另一种常见的模具氮化种类。
碳化物氮化模具主要由碳化钨、碳化钛和碳化硅等组成,具有高硬度、高耐磨性和高热稳定性等特点。
碳化物氮化模具广泛应用于金属冲压、塑料注塑、玻璃烧结等工艺中。
碳化物氮化模具的硬度通常在1800-2500HV之间,较普通模具材料硬度高出很多。
这使得碳化物氮化模具在高负荷、高温度、高速度下仍能保持较好的切削性能和耐磨性能。
此外,碳化物氮化模具还具有较高的热稳定性,能够承受高温下的工作环境,不易变形和烧蚀。
三、氮化钨模具氮化钨模具是一种特殊的模具氮化种类。
氮化钨模具主要由氮化钨和钼等组成,具有极高的硬度和耐磨性,是一种理想的切削和塑料加工模具材料。
氮化钨模具广泛应用于航空航天、电子、汽车等高精度领域。
氮化钨模具的硬度通常在2000-3000HV之间,是目前硬度最高的模具材料之一。
这使得氮化钨模具能够在高速切削、高温热压、高压注塑等工艺中保持较好的切削性能和耐磨性能。
此外,氮化钨模具还具有较高的热稳定性和抗氧化性,能够在高温环境下长时间稳定工作。
四、氮化硅模具氮化硅模具是一种高性能模具氮化种类。
氮化硅模具主要由氮化硅和碳化硅等组成,具有高硬度、高耐磨性、高抗腐蚀性和高热稳定性等特点。
氮化硅模具广泛应用于光学、电子、医疗等领域。
氮化硅模具的硬度通常在2000-3000HV之间,具有很高的抗磨性和切削性能。
潮州模具表面离子氮化和气体氮液的区别
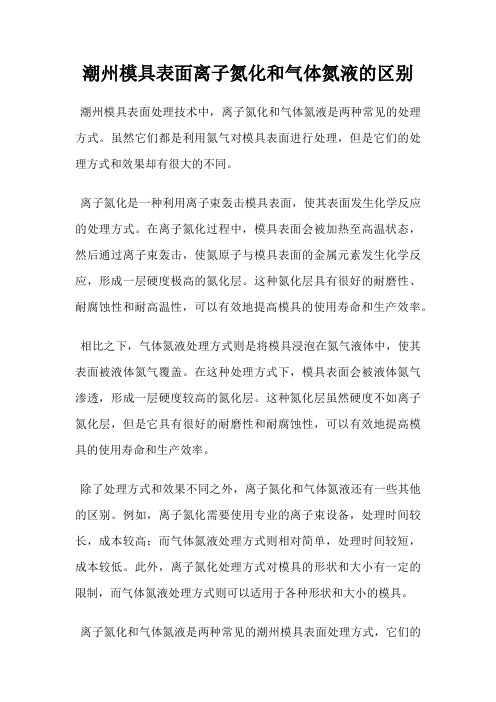
潮州模具表面离子氮化和气体氮液的区别
潮州模具表面处理技术中,离子氮化和气体氮液是两种常见的处理方式。
虽然它们都是利用氮气对模具表面进行处理,但是它们的处理方式和效果却有很大的不同。
离子氮化是一种利用离子束轰击模具表面,使其表面发生化学反应的处理方式。
在离子氮化过程中,模具表面会被加热至高温状态,然后通过离子束轰击,使氮原子与模具表面的金属元素发生化学反应,形成一层硬度极高的氮化层。
这种氮化层具有很好的耐磨性、耐腐蚀性和耐高温性,可以有效地提高模具的使用寿命和生产效率。
相比之下,气体氮液处理方式则是将模具浸泡在氮气液体中,使其表面被液体氮气覆盖。
在这种处理方式下,模具表面会被液体氮气渗透,形成一层硬度较高的氮化层。
这种氮化层虽然硬度不如离子氮化层,但是它具有很好的耐磨性和耐腐蚀性,可以有效地提高模具的使用寿命和生产效率。
除了处理方式和效果不同之外,离子氮化和气体氮液还有一些其他的区别。
例如,离子氮化需要使用专业的离子束设备,处理时间较长,成本较高;而气体氮液处理方式则相对简单,处理时间较短,成本较低。
此外,离子氮化处理方式对模具的形状和大小有一定的限制,而气体氮液处理方式则可以适用于各种形状和大小的模具。
离子氮化和气体氮液是两种常见的潮州模具表面处理方式,它们的
处理方式和效果有很大的不同。
选择哪种处理方式应该根据具体的模具材料、形状和使用环境等因素来进行综合考虑。
模具氮化处理存在的问题及对
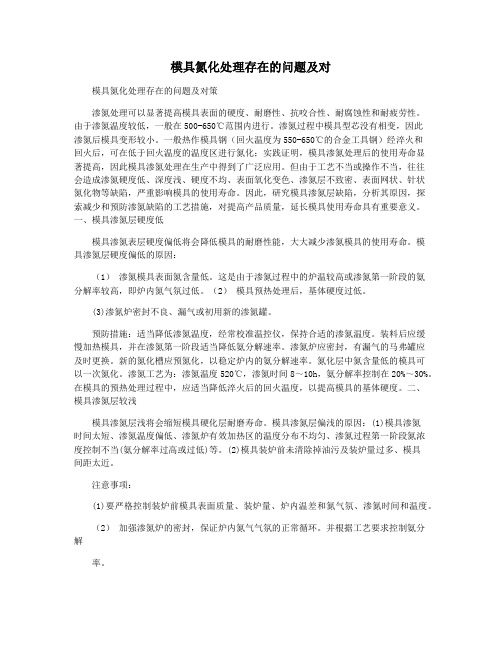
模具氮化处理存在的问题及对模具氮化处理存在的问题及对策渗氮处理可以显著提高模具表面的硬度、耐磨性、抗咬合性、耐腐蚀性和耐疲劳性。
由于渗氮温度较低,一般在500-650℃范围内进行。
渗氮过程中模具型芯没有相变,因此渗氮后模具变形较小。
一般热作模具钢(回火温度为550-650℃的合金工具钢)经淬火和回火后,可在低于回火温度的温度区进行氮化;实践证明,模具渗氮处理后的使用寿命显著提高,因此模具渗氮处理在生产中得到了广泛应用。
但由于工艺不当或操作不当,往往会造成渗氮硬度低、深度浅、硬度不均、表面氧化变色、渗氮层不致密、表面网状、针状氮化物等缺陷,严重影响模具的使用寿命。
因此,研究模具渗氮层缺陷,分析其原因,探索减少和预防渗氮缺陷的工艺措施,对提高产品质量,延长模具使用寿命具有重要意义。
一、模具渗氮层硬度低模具渗氮表层硬度偏低将会降低模具的耐磨性能,大大减少渗氮模具的使用寿命。
模具渗氮层硬度偏低的原因:(1)渗氮模具表面氮含量低。
这是由于渗氮过程中的炉温较高或渗氮第一阶段的氨分解率较高,即炉内氮气氛过低。
(2)模具预热处理后,基体硬度过低。
(3)渗氮炉密封不良、漏气或初用新的渗氮罐。
预防措施:适当降低渗氮温度,经常校准温控仪,保持合适的渗氮温度。
装料后应缓慢加热模具,并在渗氮第一阶段适当降低氨分解速率。
渗氮炉应密封,有漏气的马弗罐应及时更换。
新的氮化槽应预氮化,以稳定炉内的氨分解速率。
氮化层中氮含量低的模具可以一次氮化。
渗氮工艺为:渗氮温度520℃,渗氮时间8~10h,氨分解率控制在20%~30%。
在模具的预热处理过程中,应适当降低淬火后的回火温度,以提高模具的基体硬度。
二、模具渗氮层较浅模具渗氮层浅将会缩短模具硬化层耐磨寿命。
模具渗氮层偏浅的原因:(1)模具渗氮时间太短、渗氮温度偏低、渗氮炉有效加热区的温度分布不均匀、渗氮过程第一阶段氮浓度控制不当(氨分解率过高或过低)等。
(2)模具装炉前未清除掉油污及装炉量过多、模具间距太近。
- 1、下载文档前请自行甄别文档内容的完整性,平台不提供额外的编辑、内容补充、找答案等附加服务。
- 2、"仅部分预览"的文档,不可在线预览部分如存在完整性等问题,可反馈申请退款(可完整预览的文档不适用该条件!)。
- 3、如文档侵犯您的权益,请联系客服反馈,我们会尽快为您处理(人工客服工作时间:9:00-18:30)。
常见问题及预防措施
采用合理的渗氮工艺,避免渗氮层的氮浓度过高,获得 合适的渗氮组织,才能有效提高模具的热疲劳性能。而 不当的渗氮工艺所产生的低劣渗氮层,反而会导致模具 的早期失效。
2、H13模具渗氮层由白色化合物和黑色扩散层组成。 化合物层存在ɛ相,ý相和弥散分布的CrN,Mo2N,VN相。黑 色扩散层存在含氮ý相,脉状氮化物及弥散分布的 CrN,Mo2N,VN相。脉状组织是合金元素和氮原子在原奥氏 体金界偏聚形成合金氮化物。合理控制渗氮时间、温度 和氮势,脉状组织可减少为细小颗粒状。
预防及补救措施
(3)根据工艺试验确定各个阶段的氨分解率,确定 各个阶段保温时间。
常见问题及预防措施
缺陷特征 产生原因
(1)炉温过高,氨含水高 渗氮层出现网状或 波纹状氮化物或针 状鱼骨状氮化物 (2)氨应脱水充分,干燥剂更换或再生 (2)材质晶粒粗大,脱碳层未去除 (3)严控热处理工艺,实行无氧化加热 (3)工件有棱边锐角 (4)避免棱边和锐角 (1)更换氨干燥剂或干燥剂再生 (1)液氨含水量高 (2)表面脱碳层未去除掉 (3)氨分解率过低 (4)退氮处理不当,时间不足 (5)零件表面粗糙有锈蚀 表层脆性过大表面 起泡剥落 (6)原材料带状组织及非金属夹杂物严重 (7)尖角、表层处形成波纹状氮化物或网 状氮化物 (8)白亮层太厚 (9)渗氮层深度不均匀 (2)加大模具加工余量,表面不得有脱碳、贫碳 (3)按技术要求进行退氮处理,降低含氮量 (4)挽救方法:凡不因表面脱碳而引起的脆性可以退氮 处理,允许表面有氧化色,可在空气中冷却,加工余量大 时,可磨掉一些化合物层 (5)将零件清理干净 (6)通过预先热处理,消除原材料缺陷 (7)选用合格原材料 (8)零件尽量采用圆角或倒角 (9)带试样检查,调整工艺参数 (10)保证装炉间隙使炉气畅通、温度均匀
氮化基础知识及氮化设备的基本结构
渗氮原理
(一)概论
1、什么叫渗氮? 渗氮亦称氮化 ,是指在一定温度下,在含氮介质中使氮原子 渗入模具(工件)表层的化学热处理方法。 2、氮化优点: 模具氮化后具有极高的表面硬度和耐磨性,高的疲劳性和高 的耐腐蚀性,加热温度低,变形小。 3、氮化缺点: 生产周期较长。 4、氮化种类: 按目的分类:强化渗氮和抗蚀渗氮。 按介质分类:气体渗氮、液体渗氮、固体渗氮。 按设备分类:气体渗氮、离子渗氮、低压脉冲渗氮。
(二)原理
1、气体渗氮基本过程 气氛形成、吸附、分解、吸收和扩散五个步骤。氨气在400°C以上 将发生如下反应: 2NH3≒3H2+2[N] 2、渗氮过程
1 ):向炉内不断输入氨气 2 ):氨分子向金属表面迁移 3 ):氨分子吸附在金属表面 4 ):氨分子在相界面上不断分解,形成氮原子和氢原子 5 ):活性原子复合成分子,经相界面反应的扩散层界,不断从炉内排出 6 ):表面吸附的氮原子溶解于a-Fe中 7 ):氮原子由金属表面向内部扩散,并产生相应的浓度梯度 8 ):当超过a-Fe中的溶解度后,在表面开始形成氮化物 9) :氮化物沿金属表面的垂直方向和平行方向长大 10):氮气物层不断增厚 11):从氮化物层向金属内部扩散。
一、准备
1、核对模具数量,帐卡物相符。 2、检查模具表面有无缺陷。
3、清理模具表面油污并吹干,两次以上氮化模具最好把 表面氧化皮清理干净。
4、把模具放置料框中,相距大于10mm,允许分层装。
5、把料框装入炉内。
氮化工艺
二、按工艺进行升温、保温、降温。作好记录并巡回检 查。
三、渗氮操作工艺 气体渗氮工艺过程包括升温、保温渗氮和冷却三个阶 段。在渗氮阶段,整个渗氮过程划分为三个时期:强渗 氮、扩散期、强烈扩散期。每个时期的氨分解率是不同 的,可根据氮势需要进行调节。 模具氮化常用 氮化工艺方法有两种:一段式氮化法和 二段式氮化法。采用哪一种工艺要通过检测随炉试样和 模具使用效果决定。 此外,长期使用,炉罐会出现氨分解率增高,影响炉 气氮势控制。如遇此情况,停炉进行脱氮处理。600650℃保温4-6H。
(3)干燥剂失效
(4)管道有积水
渗层不致密 抗蚀性差
(1)表面渗氮浓度低 (2)零件原来有锈斑
(1)氨分解率太高,适当调低 (2)仔细清理工作表面可以重新渗氮
常见问题及预防措施
小结:
1、铝型材热挤压模在工作时由于经受冷热交替的作用, 模具表面易于发生因热疲劳引起的龟裂,导致制品表面 质量不符合要求,模具表面裂纹的扩展还会引起早期失 效。 在模具表面渗氮,以便在模具表面形成压力状态,提 高模具的热疲劳性能,有助于延长模具的工作寿命,这 是一种常用的工艺方法。但是如果渗氮工艺控制不当, 则易于在模具表面形成过厚的白亮层,这层白亮层硬度 高达950-1050HV,脆性较大,对微裂纹很敏感;而在渗 氮层的次表层,还易出现脉状氮化物,脉状氮化物韧性 低,易剥落。因而,渗氮层的质量控制对提高模具表面 的热疲劳性能有很大的影响。
4)、控温系统应保证炉子温度符合工艺要求。
气体渗氮设备
2、渗氮炉结构及其装置
1)、炉体、炉盖 2)、电器、温控系统:热电偶、温度计
3)、风搅拌系统:风机、导风筒
4)、供气及测量系统:气瓶、阀、压力表、分解仪 5)、水循环系统
渗氮装置示意图
图片
图片
氮化常见操作工艺及问题分析
预防及补救措施
(1)严控渗氮温度
常见问题及预防措施
缺陷特征 产生原因 预防及补救措施
(1)常查炉体密封情况,消除管道积水 (1)渗氮罐漏气、退氮处理或降温 时炉内压力低,使冷空气进入 表面出现氧 化色 (2)出炉温度过高 (2)降温或退氮处理时,炉压应大于200pa, 不得出现负压 (3)定期烘烤干燥剂或更换 (4)补救方法: 可以用低压喷砂消除之 再在500~520℃补渗2~4h 通氮炉冷至200℃以下出炉
一段式渗氮法
图片
炉内510-520℃,控制530-550℃
分解率30-50 分解率 70-80
排空 正压
8-10h
1-2h
随炉冷到 200℃以下 出炉空冷
一段氮化法炉内5源自0-530℃ 控制530-550℃
450℃
300℃
分解率 60-
分解率35-50%
正 压
正 0· 5h 压
0· 5h
正 压 8-10h
1-2h
炉冷到 200℃以下 空冷
二段氮化法
500-510℃
炉内510-530℃ 控制540-550℃ 分解率 40-60 分解率 70-90
300℃
分解率 20-30
随炉降温 到200℃ 以下出炉 空冷
正 压
0、5h
正 压
4-5h
4-5h
1-2h
二段氮化法:强渗与扩散两段,可以减缓氮化层梯度,缩短氮化总的时间。
气体渗氮设备
3、氨分解率
渗氮处理时,在排气的气体中,除掉氨气的部分气体 占气体整体容积的百分率。 4、氮势 氮势是反映气体渗氮能力的重要参数指标,气体氮势 越高(氨分解率越低),其渗氮能力越强。
气体渗氮设备
(二)渗氮设备
1、渗氮炉要求符合GB/T9452-2000规定。 1)、有效加热区炉温均匀性不应超过±10℃.(最好 ±5℃) 2)、炉罐应有良好密封。 3)、应设有氨分解率测定装置。
4、渗氮层的性能特点
1)、模具氮化后具有极高的硬度与耐磨性。H13可达950HV1200HV(相当与65.0-72.0HRC),因摩擦系数低,因此具有良好的耐磨 性和减磨性。
2)、显著提高疲劳强度并降低缺口的敏感性;
3)、可以抵抗水,过热蒸汽及碱性溶液的腐蚀; 4)、渗氮表面白亮层的脆性是气体渗氮的主要问题之一,白亮层的
氨分解率测定仪
氨分解率测定仪
2、氨分解率测定仪
气体渗氮的结果主要由氨在炉内的行为来确定。 在平衡状态下,当温度大于500℃时,理论上氨的分 解率已达到99%,远远大于平衡值,也就是说实际分解率 远小于平衡分解时的理论分解率。当炉内存在混合气时, 在炉气中氨含量相同的情况下,混合气含量越高,氨分 解率越低,氨气的流量和压力可通过针形阀进行调节。 罐内压力用U形水压计测量,一般控制在30-50mm水柱。 泡泡瓶内盛水,以观察供氨系统的流通状况。在渗氮工 艺控制技术中,渗氮气氛的“氮势”可定义为PNH3/PH21.5, 可见氨分解率越低(通氨越多),氮势越高。
气体渗氮设备
生产中通常通过调节氨分解率控制渗氮过程。氨分 解率测定仪,是利用氨溶于水而其分解产物不溶于水这 一特性进行测量的。使用时首先将上半部加入适当的水, 然后将炉罐中的废气引入标有刻度的玻璃容器中,通过 泡泡瓶排出,然后依次关闭排气阀、排水阀和进气阀, 打开进水阀,向充满废气的玻璃容器中注水。由于氨溶 于水,水占有的体积即可代表未分解氨的容积,剩余容 积为分解产物占据,从刻度可直接读出氨分解率。近年 来,随着技术的发展,以电信号来反映氨分解率的测量 仪器已投入生产应用,使得渗氮过程计算机控制成为可 能。
2)、铝挤压模具原材料投料前应该进行超声波探伤
(GB/T4162-2008)和金相(NADCA#207-2003)组织检查, 不合格的禁用。热处理后进行100%硬度检查(HRC48-52)
及金相组织抽查按(JB/T8420-2000 标准)2-4级合格才
能出厂。模具内在组织合格是保证氮化质量好坏的前提 条件。
常见问题及预防措施
缺陷特征 产生原因
(1)温度低,保温时间不够。 (2)第一阶段氨分解率过高、过低。 渗氮层深浅度 (3)装炉不当,工作之间距离太小。 (4)新炉罐夹具有未预渗或使用时间太久。 (1)升温速度快,渗氮罐内温差大,氮化温度高。 (1)经常校队炉温、仪表。 (2)中断供氨。 (2)缓慢升温,升温到300、400-450℃保温1h均温。 表面硬度低 (3)第一阶段保温时间短,第二阶段保温时间太长, 氨分解率过高。 (4)装炉量太多,炉气循环不好。 (4)补救措施 (5)零件表面不清洁,有氧化皮。 允许重新渗氮,按原工艺也行。 (6)新渗氮罐和夹具未预渗氮。 (1)炉温不均匀,装炉量多,模具靠在一起或进氨 气管道堵塞。 渗氮层硬度不 均匀有软点 (2)材料夹杂物严重。 (3)表面油污。 (1保证设备炉温均匀±5℃,模具拆开装炉,保证一 定间隙使炉气畅通,循环正常 (2)加强原材料检验。 (3)氮化前将工件清洗干净。 (2)补救:在正常温度下再渗氮数小时 (1)严格工艺纪律,按规定的温度、时间生产。