某铜冶炼厂余热利用系统简介
某铜冶炼厂余热利用系统简介
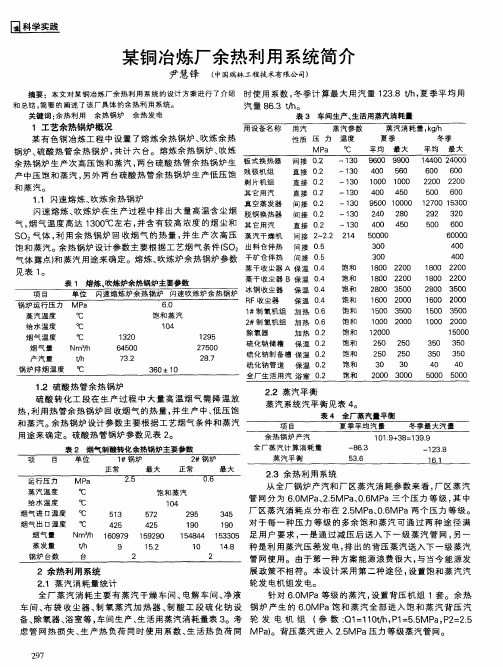
5 0 5 0 0 0 0 0
12 硫酸 热 管余热 锅炉 . 硫酸 转 化 工段 在 生 产过 程 中大 量 高 温烟 气 需 降 温 放 热 , 用 热管 余热 锅炉 回 收烟 气 的热量 , 生产 中 、 压饱 利 并 低
22 蒸 汽平衡 . 蒸汽 系统 汽平衡 见表 4 。
项目
和蒸 汽 。 余热 锅炉 设计 参数 主要根 据工 艺烟气 条件 和蒸 汽 用途 来确 定。 硫酸 热管 锅炉参 数 见表 2 。
表 2 烟气制酸转化余热锅炉 主要参数
表 4 全 厂 蒸 汽 量 平衡 夏 季平 均 汽 量 冬 季 最 大 汽 量
23 余 热利 用 系统 .
从 全厂 锅炉 产汽 和厂 区蒸 汽消 耗参 数来 看 , 区蒸 汽 厂
2 0 5
R F收尘 器 1} 氧 机 组 :制 I
2 #制 氧机 组
保温 0 . 4 加 热 06 .
加 热 O6 .
10 2 0 60 0 0
1 0 35 0 5 0 0 10 2 0 0 0 00 10 0 50
除氧 器
加 热 02 .
饱 和 饱 和
饱 和
某铜冶炼厂余热利用 系统简介
尹慧锋 ( 国 林 程 术 限 司 中 瑞 工 技 有 公 )
摘 要 :本 文 对 某 铜 冶炼 厂余 热 利 用 系统 的设 计 方 案进 行 了 介绍 时使用 系数 , 季计 算最 大用 汽量 1 38 t , 季 平均 用 冬 2. / 夏 h 和 总结 , 要 的 阐 述 了该 广具 体 的余 热利 用 系统 。 简
间接 02 .
直 接 02 . 间接
~
2 2 9 5 0 0
3 0 2 6 0 0 60 0 00 4 0 0 4 0 0
铜冶炼的资源高效利用

铜是一种重要的工业原料,广泛应用 于电气、建筑、交通运输等领域。铜 冶炼是获取铜的关键环节,对于满足 社会经济发展需求具有重要意义。
铜冶炼的工艺流程
铜矿石的采选
通过露天开采或地下开采的方式获取 铜矿石,并进行破碎、磨细、浮选等 物理处理,以获得品位较高的铜精矿 。
火法冶炼
湿法冶炼
将铜精矿中的铜转化为硫酸铜或其他 盐类,再通过电解的方式将铜从溶液 中提取出来。
余热利用
03
利用高效热回收系统,将铜冶炼过程中的余热转化为有用能源
,降低能源消耗。
政策与法规对资源高效利用的影响
1 2 3
政策引导
政府通过制定相关政策,鼓励和支持企业进行资 源高效利用的技术研发和应用,推动产业绿色发 展。
法规约束
严格执行环保法规,促使企业加大环保投入,改 进生产工艺,降低能耗和污染物排放,实现资源 高效利用。
伴生金属回收
在冶炼过程中回收伴生金属,提高 资源综合利用率。
尾矿回收
对尾矿中的有价元素进行回收,减 少资源损失。
降低能耗与排放
节能技术应用
采用先进的节能技术,降低铜冶炼过程中的能 耗。
减排措施
采取有效措施减少污染物排放,降低对环境的 影响。
环保监管
加强环保监管力度,确保企业达标排放。
开发新型冶炼技术
02
CATALOGUE
资源高效利用的策略
优化冶炼工艺
降低能耗
通过改进冶炼工艺,降低 铜冶炼过程中的能耗,提 高能源利用效率。
减少废弃物
优化工艺减少冶炼过程中 产生的废弃物,降低对环 境的影响。
提高金属回收率
改进工艺以提高铜和其他 有价金属的回收率,降低 资源浪费。
奥斯麦特铜冶炼余热发电的应用

7
主要设计技术参数
奥斯麦特 熔 炼 炉 余 热 锅 炉 蒸 发 量 26 & W ’ ; 21 & W ’ ;
" T ! 0UC 饱和蒸汽 奥斯麦特 吹 炼 炉 余 热 锅 炉 蒸 发 量 " T ! 0UC 饱和蒸汽 饱和蒸汽流量 汽轮机入口蒸汽压力 正常: ( 波动) 71 X #" & W ’ 正常: " T ! 0UC 最高: " T " 0UC 汽轮机出口蒸汽压力 正常: ! T + 0UC 72
6
结论
发 ! 利 用 奥 斯 麦 特 铜 冶 炼 废 气 余 热 进 行 发 电, 电后产生的尾气 用 于 铜 电 解 等 生 产 及 生 活 所 需, 冷 凝水也达到循环 利 用, 最大程度地提高余热综合利 用率, 对发展循环经济、 保证经济可持续发展有重要 的战略意义。 对大气 # 整 个 发 电 工 艺 过 程 不 需 要 任 何 燃 料, 环境不增加任何 污 染 物 的 排 放, 而且还可以降低排 气温度, 减轻温 室 效 应 和 降 低 热 污 染, 是 节 约 能 源、 节约资源、 降低企业生产成本极为有效的途径, 对于 保护生态环境具 有 促 进 作 用, 环保效益与节能效益 显著。 在厂区直接并网利 $ 利 用 废 气 余 热 进 行 发 电, 用, 不仅可减缓电力供应紧张的局面, 而且可为企业 创造显著的经济效益。 "
!!!!!!!!!!!!!!!!!!!!!!!!!!!!!!!!!!!!!!!!!!!!!!!!!
草酸脱氢装置获专利
金川集团公司化 工 厂 草 酸 生 产 系 统 始 建 于 !* 年 代, 年 生产能力只有 "***#。 脱 氢 工 序 是 草 酸 生 产 的 关 键 工 序, 而 脱氢器是草酸脱氢 的 核 心 装 置, 原 脱 氢 炉 为 灶 式 炉, 脱氢器 为锅形脱氢器, 受 热 不 均 匀, 导 致 脱 氢 转 化 率 低, 脱氢时间 长, 而且脱氢过程需 加 水 将 物 料 从 脱 氢 器 中 带 走, 脱氢器反 复经过冷热变换, 导致锅形脱氢器易变形, 使用寿命 短, 脱氢 过程不连续, 操作环 境 恶 劣, 还 存 在 严 重 的 安 全 隐 患。 落 后 的脱氢工艺已成为制 约 草 酸 规 模 扩 大 和 生 产 安 全 的 最 大 瓶 颈问题。 为此, 金川公司经过 近 , 年 的 科 技 攻 关, 先后进行无数 次试验, 自主研制开 发 的 新 型 脱 氢 器, 主要技术指标达到国 内先进水平, 应用于生产实际后效果良好。该脱氢器 具 有 加 热效率高、 物料受热 均 匀, 并 能 快 速 升 温、 脱 氢, 脱氢器受热 均匀、 脱氢过程反应完全、 转化率高等优点, 可大大提 高 劳 动 效率, 降低劳动强度, 完成脱氢过程的自动连续化, 安全系数 高。日前获得国家实用新型专利。 [中图分类号]:,*5 + ) [文献标识码]0 (中国有色金属学会)
铜冶炼余热高效利用技术研究

铜冶炼余热高效利用技术研究马晓辉;匡轩毅;赵军生【摘要】通过对铜冶炼厂余热资源状况进行综合分析,遵循能源梯级利用原则,使高品质的余热资源得到充分利用.利用硫酸转化器一段出口温度为580℃的高温烟气余热将底吹炉余热锅炉所产4.2 MPa饱和蒸汽过热为3.82 MPa、450℃过热蒸汽,高温烟气出口温度达503℃,满足硫酸后续工艺生产要求,过热蒸汽进入汽轮发电机组发电.工程实践证明:过热蒸汽发电在铜冶炼生产中应用是成功的,值得进一步推广.【期刊名称】《硫酸工业》【年(卷),期】2017(000)007【总页数】3页(P28-30)【关键词】铜冶炼;烟气;硫酸生产;余热发电;过热蒸汽【作者】马晓辉;匡轩毅;赵军生【作者单位】长沙有色冶金设计研究院有限公司,湖南长沙410000;长沙有色冶金设计研究院有限公司,湖南长沙410000;长沙有色冶金设计研究院有限公司,湖南长沙410000【正文语种】中文【中图分类】TQ111.16;X706铜冶炼余热资源主要集中在冶炼系统和硫酸生产系统。
熔炼炉高温烟气余热一般采用余热锅炉回收,产生饱和蒸汽;硫酸生产系统余热利用方法有3种:①采用省煤器生产热水;②采用热管锅炉生产低压蒸汽[1-3];③采用空冷器将热量排向大气。
虽然目前铜冶炼及制酸余热资源得到利用,但余热利用效率通常不高。
目前国内大部分铜冶炼均采用饱和蒸汽发电[4-5],未考虑采用过热蒸汽发电。
1.1 冶炼与制酸工艺某冶炼厂主要生产工艺流程如下:1)冶炼工艺。
采用炉外分离熔炼工艺,主要流程为:炉外分离底吹熔炼炉—贫化电炉—转炉吹炼—粗铜。
底吹炉配1台余热锅炉,正常运行时产生4.2 MPa的饱和蒸汽12 t/h,最大产蒸汽量达17 t/h,清焦期间不产蒸汽(每天清焦1~2 h),蒸汽除少量用作除氧用汽和生活用汽外,其余均对空排放。
2)制酸工艺。
硫酸装置采用技术先进、成熟的稀酸洗涤净化、二转二吸制酸工艺。
净化工序选择绝热蒸发、稀酸冷却流程,利用稀酸板式换热器移走系统热量。
烧结余热发电系统简介
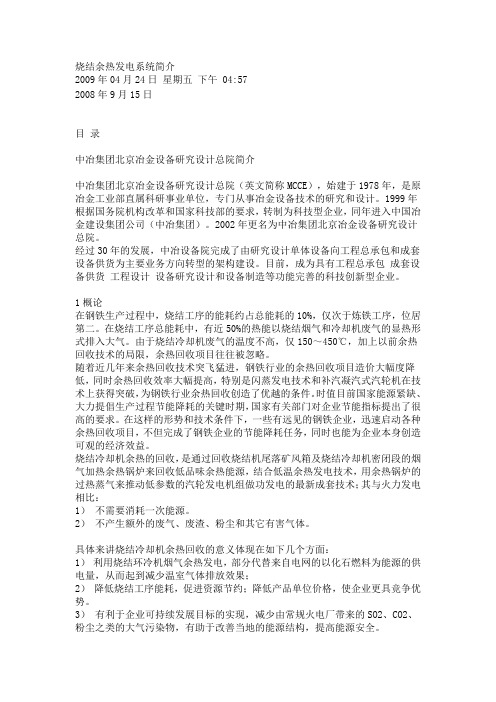
烧结余热发电系统简介2009年04月24日星期五下午 04:572008年9月15日目录中冶集团北京冶金设备研究设计总院简介中冶集团北京冶金设备研究设计总院(英文简称MCCE),始建于1978年,是原冶金工业部直属科研事业单位,专门从事冶金设备技术的研究和设计。
1999年根据国务院机构改革和国家科技部的要求,转制为科技型企业,同年进入中国冶金建设集团公司(中冶集团)。
2002年更名为中冶集团北京冶金设备研究设计总院。
经过30年的发展,中冶设备院完成了由研究设计单体设备向工程总承包和成套设备供货为主要业务方向转型的架构建设。
目前,成为具有工程总承包成套设备供货工程设计设备研究设计和设备制造等功能完善的科技创新型企业。
1概论在钢铁生产过程中,烧结工序的能耗约占总能耗的10%,仅次于炼铁工序,位居第二。
在烧结工序总能耗中,有近50%的热能以烧结烟气和冷却机废气的显热形式排入大气。
由于烧结冷却机废气的温度不高,仅150~450℃,加上以前余热回收技术的局限,余热回收项目往往被忽略。
随着近几年来余热回收技术突飞猛进,钢铁行业的余热回收项目造价大幅度降低,同时余热回收效率大幅提高,特别是闪蒸发电技术和补汽凝汽式汽轮机在技术上获得突破,为钢铁行业余热回收创造了优越的条件。
时值目前国家能源紧缺、大力提倡生产过程节能降耗的关键时期,国家有关部门对企业节能指标提出了很高的要求。
在这样的形势和技术条件下,一些有远见的钢铁企业,迅速启动各种余热回收项目,不但完成了钢铁企业的节能降耗任务,同时也能为企业本身创造可观的经济效益。
烧结冷却机余热的回收,是通过回收烧结机尾落矿风箱及烧结冷却机密闭段的烟气加热余热锅炉来回收低品味余热能源,结合低温余热发电技术,用余热锅炉的过热蒸气来推动低参数的汽轮发电机组做功发电的最新成套技术;其与火力发电相比:1)不需要消耗一次能源。
2)不产生额外的废气、废渣、粉尘和其它有害气体。
具体来讲烧结冷却机余热回收的意义体现在如下几个方面:1)利用烧结环冷机烟气余热发电,部分代替来自电网的以化石燃料为能源的供电量,从而起到减少温室气体排放效果;2)降低烧结工序能耗,促进资源节约;降低产品单位价格,使企业更具竞争优势。
余热发电工艺流程、主机设备工作原理简介(简单)

余热发电工艺流程、主机设备工作原理简介余热发电余热发电是一种通过回收生产过程中产生的工业余热,将其转化为电能的环保型能源利用技术。
它能够有效地提高工业生产过程中的能源利用率,减少大量二氧化碳和其他有害气体的排放,对于推动工业节能和环保发展有着重要的作用。
工艺流程余热发电工艺流程主要包括余热回收、余热蒸汽与受热水循环、加热循环、排气、冷凝等环节。
1.余热回收:利用余热回收装置对工业生产过程中的热量进行回收。
通常,余热回收设备采用高效传热器,将低温余热转化为高温余热。
2.余热蒸汽与受热水循环:余热回收后的高温余热通过传热器传导至工作介质,常用的介质为蒸汽和循环水。
3.加热循环:高温介质在加热器中进一步加热,增加介质的温度和压力。
4.排气:未能转化为电能的高温气体排放至大气中。
5.冷凝:过热蒸汽在冷凝器中冷却,将过热蒸汽转化为高压饱和水,该水通过泵在再次流入传热器,开始新一轮回收。
电能输出余热发电产生的电能主要经过调节和控制后输出,可以用于工厂内部用电和向电网输送电力。
主机设备工作原理简介余热发电主机设备包括涡轮发电机、减速器、发电机控制系统等主要设备。
以下是它们的工作原理简介:涡轮发电机涡轮发电机是余热发电设备中的核心设备之一。
它是将高速旋转的轴承通过机械装置转化为电能的装置。
其工作过程如下:1.涡轮叶片接受高压、高速蒸汽的冲击,启动涡轮的旋转。
2.涡轮的旋转通过轴传动减速器。
3.通过减速器就可以将转速降低到发电机的工作转速。
4.通过发电机控制系统控制输出的电压和频率,即可输出电能。
减速器减速器是涡轮发电机降低转速的一个重要设备,其工作原理如下:1.接收涡轮发电机传来的高速轴,降低转速。
2.转速降低之后,将轴的转速与电机控制系统的要求匹配,实现电能高效输出。
发电机控制系统发电机控制系统是整个余热发电设备的监控和控制中心,其工作原理如下:1.接收来自涡轮发电机的反馈信号,对电压和电流进行监控和调节。
2.通过反馈系统调节发电机的输出功率和工作状态。
浅谈某冶炼厂采暖通风设计
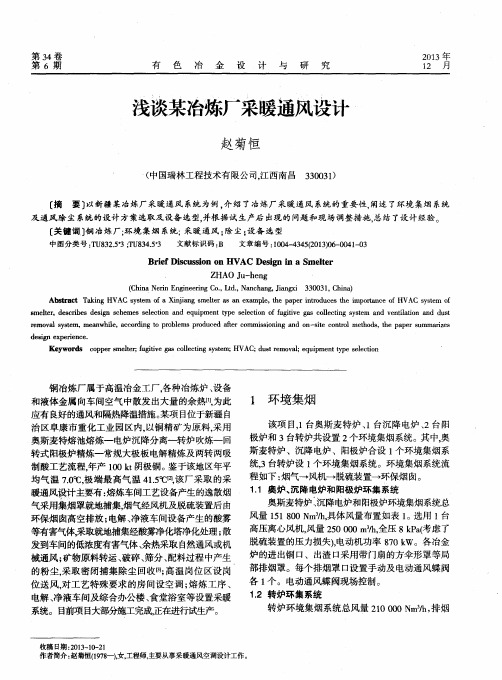
铜冶炼厂属于高温冶金工厂, 各种冶炼炉 、 设备
和液体金属向车间空气 中散发出大量的余热【 1 】 , 为此 应有 良 好的通风和隔热降温措施。 某项 目 位于新疆 自 治 区阜康市重化工业园区内, 以铜精矿为原料, 采用 奥斯麦特熔池熔炼一电炉沉降分离一转炉 吹炼一 回 转式阳极炉精炼一常规大极板电解精炼及两转两吸 制酸工艺流程, 年产 1 0 0 k t 阴极铜。 鉴于该地区年平 均气 温 7 . 0  ̄ C , 极端最高气温 4 1 . 5 o C t 2 1 , 该 厂采取 的采 暖通风设计主要有 : 熔炼车间工艺设备产生的逸散烟 气采用集烟罩就地捕集' 烟气经风机及脱硫装置后由 环保烟 囱高空排放 ; 电解 、 净液车间设备产生的酸雾 等有害气体采 取就地捕集经酸雾净化塔净化处理 ; 散 发到车间的低浓度有害气体、 余热采取 自 然通风或机 械通风 ; 矿物原料转运、 破碎 、 筛分 、 配料过程中产生
1 环境集烟
该项 目, 1 台奥斯麦特炉 、 1 台沉 降电炉 、 2台阳
极炉和 3台转炉共设置 2 个环境集烟系统。其中。 奥 斯麦特炉、沉降电炉、阳极炉合设 1 个环境集烟系 统, 3台转炉设 1 个环境集烟系统。环境集烟系统流 程如下 : 烟气一风机 脱硫装置 环保烟囱。 1 . 1奥炉、 沉降电炉和阳极炉环集 系统 奥斯麦特炉、 沉降电炉和阳极炉环境集烟系统总 风量 1 5 1 8 0 0 N m %。 具体风量布置如表 1 。 选用 1 台 高压离心风机。 风量 2 5 0 0 0 0 m 。 全压 8 k P a f 考虑了 脱硫装置的压力损失1 . 电动机功率 8 7 0 k W。各冶金 炉的进出铜 口、出渣 口采用带门扇的方伞形罩等局 部排烟罩 。每个排烟罩 口设置手动及电动通风蝶阀 各1 个。电动通风蝶阀现场控制 。 1 . 2 转炉环集系统 转炉环境集烟系统总风量 2 1 0 0 0 0 N m 3 ] h , 排烟
余热锅炉系统工作原理及技术特点讲解

余热锅炉系统工作原理及技术特点讲解余热锅炉系统是一种能够回收工业生产中产生的余热,并将其转化为热能供应给其他设备或建筑物使用的设备。
其工作原理主要包括余热回收、传递、转换和利用四个过程。
在工业生产过程中,会产生大量的热能,并且其中有相当一部分是可以回收利用的。
余热锅炉系统可以通过各种方式进行热能的回收,例如烟气余热、废气余热、蒸汽余热等。
在余热回收过程中,首先需要将含有热能的废气或废液传递到余热锅炉系统中。
这一过程可以通过管道、泵或其他输送设备来完成。
传递过程中,需要确保废热源的温度、流量和压力稳定,并且能够满足余热锅炉的工作需求。
余热转换过程主要是指将回收到的废热转化为可用的热能。
最常见的方式是通过余热锅炉将废热转化为蒸汽或热水。
余热锅炉通常由炉体、燃烧器、热交换器等组成。
回收到的废热通过热交换器与余热锅炉内的工质进行热交换,将废热转化为热能。
达到所需温度后,余热锅炉系统将转化后的热能供应给其他设备或建筑物使用。
这一过程可以通过输送管道、热交换器等设备来完成。
在输送过程中,需要确保热能的稳定性,以保证供热设备的正常运行。
1.高效节能:余热锅炉系统能够有效回收和利用工业生产中产生的废热,从而实现能源的高效利用。
通过优化热能转换过程,可以将废热转化为可用能源的比例最大化。
2.环保节能:通过利用余热锅炉系统进行废热回收,可以减少工业生产过程中的能源浪费,并降低对环境的负荷。
这有助于减少温室气体的排放,保护环境。
4.自动控制:余热锅炉系统具有自动化程度高的特点,能够实现对温度、压力、流量等参数的精确调节,从而保证系统的安全稳定运行。
5.可靠性高:余热锅炉系统是由多个部件组成的复杂设备,但其每个部件都经过精心设计和制造,能够满足工业生产的高要求。
同时,余热锅炉系统还具有多重保护措施,如过热保护、低水位保护等,可以有效避免故障和事故的发生。
总之,余热锅炉系统是一种高效、环保、灵活和可靠的废热回收设备。
通过其工作原理和技术特点的讲解,可以更好地理解余热锅炉系统的工作原理和应用价值。
向心式汽轮机在大型铜冶炼厂余热利用系统中的应用
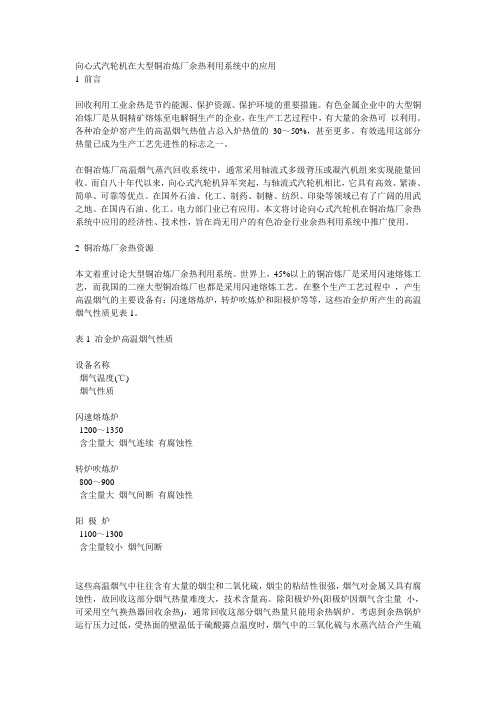
向心式汽轮机在大型铜冶炼厂余热利用系统中的应用-1 前言回收利用工业余热是节约能源、保护资源、保护环境的重要措施。
有色金属企业中的大型铜冶炼厂是从铜精矿熔炼至电解铜生产的企业,在生产工艺过程中,有大量的余热可以利用。
各种冶金炉窑产生的高温烟气热值占总入炉热值的30~50%,甚至更多。
有效选用这部分热量已成为生产工艺先进性的标志之一。
在铜冶炼厂高温烟气蒸汽回收系统中,通常采用轴流式多级背压或凝汽机组来实现能量回收。
而自八十年代以来,向心式汽轮机异军突起,与轴流式汽轮机相比,它具有高效、紧凑、简单、可靠等优点。
在国外石油、化工、制药、制糖、纺织、印染等领域已有了广阔的用武之地。
在国内石油、化工、电力部门业已有应用。
本文将讨论向心式汽轮机在铜冶炼厂余热系统中应用的经济性、技术性,旨在尚无用户的有色冶金行业余热利用系统中推广使用。
2 铜冶炼厂余热资源本文着重讨论大型铜冶炼厂余热利用系统。
世界上,45%以上的铜冶炼厂是采用闪速熔炼工艺,而我国的二座大型铜冶炼厂也都是采用闪速熔炼工艺。
在整个生产工艺过程中,产生高温烟气的主要设备有:闪速熔炼炉,转炉吹炼炉和阳极炉等等,这些冶金炉所产生的高温烟气性质见表1。
表1 冶金炉高温烟气性质设备名称烟气温度(℃)烟气性质闪速熔炼炉1200~1350含尘量大烟气连续有腐蚀性转炉吹炼炉800~900含尘量大烟气间断有腐蚀性阳极炉1100~1300含尘量较小烟气间断这些高温烟气中往往含有大量的烟尘和二氧化硫,烟尘的粘结性很强,烟气对金属又具有腐蚀性,故回收这部分烟气热量难度大,技术含量高。
除阳极炉外(阳极炉因烟气含尘量小,可采用空气换热器回收余热),通常回收这部分烟气热量只能用余热锅炉。
考虑到余热锅炉运行压力过低,受热面的壁温低于硫酸露点温度时,烟气中的三氧化硫与水蒸汽结合产生硫酸凝结在管壁上,使受热面受到腐蚀。
所以在设计余热锅炉时,必须提高锅炉运行压力,使管壁温度高于硫酸露点温度,表2就是国内二家大型铜冶炼厂余热锅炉性能参数表。
余热锅炉系统工作原理及技术特点

余热锅炉系统工作原理及技术特点1.废气收集:余热锅炉系统需要将工业生产过程中产生的废气进行收集,通常是通过管道将废气引入到余热回收装置中。
2.余热回收:余热回收装置是余热锅炉系统的核心部件,它可以将废气中的高温热能转化成水和蒸汽的形式。
通常采用的方法有火管余热锅炉、水管余热锅炉和导热油余热锅炉等。
3.热能利用:经过余热回收装置转化后的热能可以用于发电或供热。
如果是用于发电,通常会将热能转化成蒸汽,然后驱动蒸汽涡轮发电机组产生电能。
如果是用于供热,则可以直接将热能用于加热工业生产或居民生活用水等。
1.高能效:余热锅炉系统能够将工业生产过程中的废气中的余热转化成热能,从而实现能源的高效利用。
这不仅能减少工业生产过程中的能源消耗,还能降低对环境的污染。
2.环保节能:余热锅炉系统通过回收利用废气中的余热,减少了废气的排放量,从而降低了对大气环境的污染。
与传统的锅炉系统相比,余热锅炉系统的能源利用效率更高,能够节约大量的能源资源。
3.应用广泛:余热锅炉系统可以广泛应用于各个行业,例如冶金、化工、石化、电力、纺织、食品等。
只要生产过程中有废气产生,就可以利用余热锅炉系统进行能源回收。
4.系统稳定性高:余热锅炉系统通常由废气收集系统、余热回收系统、能源转换系统和控制系统等组成,具有良好的稳定性和可靠性。
在运行过程中,可以根据工艺需求和能源供应情况进行自动控制和调节。
5.经济效益显著:利用余热锅炉系统将废气中的余热进行回收利用,可以大幅降低工业生产中的能源消耗和成本支出。
在一些能源稀缺的地区,余热锅炉系统具有良好的经济效益和市场前景。
总之,余热锅炉系统是一种能够利用工业生产过程中产生的废气余热进行能源回收的设备。
它的工作原理是通过废气收集、余热回收和热能利用等环节,实现对废气中的余热进行回收利用。
它具有高能效、环保节能、应用广泛、系统稳定性高和经济效益显著等特点,对于能源的稀缺和环境的保护具有重要的意义。
余热发电方案说明

余热发电方案说明余热发电是指利用工业生产中产生的余热作为能源,通过热能转化装置将其转化为电能的一种发电方式。
余热发电具有能够充分利用废热资源、提高能源利用效率和减少环境污染等优点,被广泛应用于许多行业和领域。
本文将从余热发电的原理、应用、技术和前景等方面进行详细的说明。
一、余热发电的原理余热发电的原理是利用工业生产过程中产生的废热,通过热能转化装置将其转化为电能。
工业生产中的许多过程都会产生大量的废热,如冶金、化工、纺织、电力等行业。
这些废热通常以高温的形式存在,如果不进行有效利用就会直接排放到环境中,造成能源浪费和环境污染。
余热发电的主要装置是余热锅炉和汽轮发电机组。
余热锅炉是将废热通过燃料燃烧或者传热的方式转化为蒸汽,然后通过汽轮发电机组将蒸汽产生的动力转化为电能。
余热发电过程中,烟气中的废热被捕获,传导给锅炉中的工质(如水或空气),使其发生相应的温度升高,并将工质蒸发为蒸汽,然后通过汽轮发电机组转化为电能。
这样,就可以将工业生产中的废热转化为可供使用的电能。
二、余热发电的应用余热发电广泛应用于许多行业和领域,尤其是对于高能耗、高温废气、废水的工业企业。
一方面,余热发电可以提高能源的利用效率,降低生产成本。
另一方面,余热发电可以减少废气和废水的排放,减少环境污染,符合环保要求。
以下是几个常见的应用领域:1.钢铁冶炼行业:钢铁冶炼是一个高温高能耗的过程,会产生大量的废热。
利用余热发电技术,可以将冶炼过程中的废热转化为电能,提高能源利用效率,降低生产成本。
2.化工行业:化工行业的许多工艺过程也会产生大量的废热。
通过余热发电技术,可以将废热转化为电能,提高能源利用效率,减少排放,降低生产成本。
3.纺织印染行业:纺织印染过程中需要用大量的热能。
通过余热发电技术,可以将生产过程中产生的废热转化为电能,提高能源利用效率,降低生产成本。
4.电力行业:电力行业是一个庞大的耗能行业,电厂在发电过程中会产生大量废热。
铜冶炼节能技术

The End!
铜精炼电解新工艺
① 永久阴极电解
采用不锈钢板做成阴极代替铜始极片,提高产品质量, 使用较高电流密度和较小极距,进一步提高单位面积的产 能。采用不锈钢作阴极,取消了铜始极片的生产制作,阴极 铜的处理设备多出了剥片过程。 包括不锈钢阴极板、阴极剥片机组、阳极准备机组、残 极洗涤机组、电解专用吊车等,不锈钢永久阴极板包括导电 棒、母板、包边条等部分,阴极板面材质为316L,板最底边 的垂直度控制在5.5min以内,并具有良好平整度和板面质 量。
(3) 设计要点 A) 采取双路供气且保证吹气压力。主气源为N2, 备用气源为压缩空气。 B) 直通定向透气砖气孔 0.6-1.0mm,狭缝定向型 透气砖狭缝宽0.18mm C) 避免透气砖寿命低于炉底寿命而被迫进行大修 D) 倾动炉的转动范围为-29°~+12°,而透气砖 全部安装于炉底,一旦发生渗漏
(4) 技术评价 A) 运用热力学和动力学原理,充分利用粗铜自身 O和S反应,达到脱硫除氧的目的,避免因传统氧 化产生大量Cu2O,减轻还原负担,简化工艺流 程,提高生产效率。 B) 运用高温熔体多相反应热动力学原理和气泡形 成长大析出技术,直接通入混合气(N2+LPG)使熔 体形成沸腾状态,促进[S]、[O]及LPG之间更有效 反应,同时达到脱硫除氧双重目的。
(4) 安全连锁控制
1) 烧嘴熄火时,火焰探 测器给出反馈信号,天然气 和氧气安全控制阀会自动切 断;2) 当天然气压力、氧气 压力、压缩空气压力、仪表 空气压力低于设定值时,天 然气和氧气安全控制阀会自 动切断;3) 烧嘴熄火时,压 缩空气吹扫阀会自动打开吹 扫天然气管路系统;4) 按下 急停按钮,电源切断,燃料 阀和氧气主阀切断。
• 工艺流程 将反射炉进料→熔化工序剥离出来,改由竖炉单 独完成。竖炉连续进料,将铜料熔化成铜水后,再经 过保温溜槽连续流入反射炉。反射炉只需将铜水进一 步氧化、还原后,在炉内铜水液位达到上限前即可浇 铸成阳极板。在阳极板浇铸时,竖炉继续进料熔化, 反射炉继续进铜水并还原。这样,将竖炉、反射炉联 合成一个整体,实现边进料(残极)、边熔化、边还原、 边浇铸,变传统反射炉铜精炼间断作业为连续作业。
一种铜冶炼系统冶炼渣余热回收利用系统及其运行方法

一种铜冶炼系统冶炼渣余热回收利用系统及
其运行方法
铜冶炼系统冶炼渣余热回收利用系统及其运行方法
铜冶炼过程中,产生大量的渣余热能,为了有效利用这些热能资源,设计了一
种铜冶炼系统冶炼渣余热回收利用系统。
该系统主要由两个部分组成:余热回收装置和热能利用装置。
余热回收装置位
于冶炼炉的尾部,通过管道和传热设备连接冶炼炉和热能利用装置。
热能利用装置则将回收的余热转化为可供使用的热能。
在运行方法方面,该系统首先将冶炼炉产生的热能通过余热回收装置引导出来。
余热回收装置利用高效传热设备,将高温废气中的热能传递给能源传导介质(如水和空气),从而使热能得以回收。
传热设备的选择和设计要考虑热能的传导效率和系统的安全性。
之后,回收的热能通过管道输送至热能利用装置。
热能利用装置根据实际需求,可以将热能转化为蒸汽、热水或直接供应给其他生产设备。
例如,可以利用蒸汽发电装置将热能转化为电能,或者将热水输送至加热设备中,用于提供热能。
在运行过程中,需要考虑余热回收装置和热能利用装置之间的连接和协调。
有
效的管道布置和传热设备的选择可以最大限度地提高热能转化效率。
此外,应根据冶炼系统的具体情况,结合工艺参数和产能要求,对余热回收装置和热能利用装置进行优化设计。
综上所述,一种铜冶炼系统冶炼渣余热回收利用系统及其运行方法的设计可以
有效地利用冶炼过程中产生的渣余热能资源。
通过回收和转化这些热能,可以实现能源的节约和环境的保护,并为冶炼生产提供可持续发展的解决方案。
金属冶炼中的资源综合利用

提高经济效益的必要性
01
降低生产成本
通过资源综合利用,可以降低金 属冶炼过程中的原料成本,提高 经济效益。
02
创造就业机会
03
促进产业升级
资源综合利用可以带动相关产业 链的发展,创造更多的就业机会 。
资源综合利用可以推动金属冶炼 行业的产业升级和和智能化技术
随着自动化和智能化技术的不断发展,金属冶炼过程中的资源综合利用
将更加高效和精确。例如,利用AI技术优化生产流程,提高资源利用率
,降低能耗和减少排放。
02
循环经济技术
循环经济技术是实现资源高效利用的重要手段,包括废弃物资源化、能
源回收等技术。未来,这些技术将在金属冶炼中得到广泛应用,实现废
总结词
多元化利用,降低能耗
详细描述
该铜冶炼企业不仅从矿石中提取铜,还将冶炼过程中产生的其他有价元素进行回收。同时,企业采用先进的节能 技术,降低能耗,提高能源利用效率。此外,企业还对生产过程中的余热进行回收利用,用于其他工艺流程。
某铝冶炼企业资源综合利用案例
总结词
全产业链整合,实现循环经济
详细描述
噪声污染
冶炼过程中的机械振动和噪声会对周边居民 产生影响。
02
CATALOGUE
资源综合利用的重要性
资源的有限性
01
02
03
金属资源储量有限
全球金属资源储量有限, 随着工业化进程的加速, 金属需求量不断增加,资 源压力日益增大。
资源开采成本高
金属矿藏开采难度大,成 本高,且品位逐渐下降, 导致采矿成本不断上升。
弃物的减量化和资源化利用。
03
低碳冶炼技术
随着全球气候变化问题日益严重,低碳冶炼技术成为未来金属冶炼的重
余热利用系统设计

余热利用系统设计余热利用系统是指将工业生产过程中产生的废热进行收集、转换和利用的技术系统。
在现代工业生产中,废热是一个宝贵的资源,通过合理利用可以实现能源节约和减排的效果。
下面将从余热利用系统的设计、工艺原理、应用场景和优势等方面进行详细论述。
一、余热利用系统的设计1.废热收集:首先需要在工业生产过程中确定有废热产生的环节,并进行收集。
常见的收集方式包括空气冷却、水冷却和烟气冷凝等。
收集方法的选择需要根据废热的性质和产生环节的具体情况进行评估。
2.废热转换:收集到的废热需要转换成可用的能源形式。
常见的转换方式有蒸汽发生器、热水发生器、热泵和热交换器等。
不同的转换方式适用于不同的能源利用场景,需要根据实际情况选择合适的转换设备。
3.废热利用:转换后的能源可以应用于供暖、供热、电力发电和制冷等方面。
根据实际需求可以将余热利用系统设计成单一能源利用或多种能源利用的复合系统。
二、余热利用系统的工艺原理1.热传导:废热将通过导热介质传导到集热器中,实现热能的收集。
2.热转换:在转换环节,通过传热器、锅炉、蒸汽发生器等设备将废热转换成可用的能源形式。
3.能源利用:转换后的能源可以应用于供暖、供热、电力发电等方面,实现废热的利用和能源的回收。
三、余热利用系统的应用场景1.钢铁行业:钢铁生产过程中会产生大量的高温废热,可以通过蒸汽发生器和热交换器等设备将废热转换为蒸汽或热水,供应给厂区的供暖、供热和发电等系统。
2.化工行业:化工生产中常常会有高温废气和废水,可通过热泵、热交换等技术将废热转换为热水,用于供暖或加热工艺。
3.电力行业:发电过程中会产生大量的余热,可以通过余热发电技术将废热转化为电能,提高发电效率。
4.纸浆纸业:纸浆制造过程中会产生大量的废热,可以通过热交换器将废热转换为热水或蒸汽,用于纸浆干燥和供暖等方面。
四、余热利用系统的优势1.节能减排:废热利用可以降低生产过程中的能耗,减少化石能源的消耗,从而节约能源和降低碳排放。
铜冶炼缓冷余热回收技术应用

铜冶炼缓冷余热回收技术应用摘要:针对铜冶炼渣缓冷过程余热回收利用可行性进行分析探讨,计算余热量及经济性分析。
结果表明在不影响渣包冷却效果的前提下,可以回收大量余热用于发电、冬季供暖等用热需求,具有较好的经济效益。
关键词:铜冶炼;缓冷;热回收;余热发电Application of waste heat recovery technology forslow cooling in copper smeltingAbstract: The feasibility of recovery and utilization of wasteheat in the slow cooling process of copper smelting slag is analyzed and discussed, the calculation of waste heat and economic analysis are carried out. The results show that under the premise of not affecting the cooling effect of the slag bag, a large amount of waste heat canbe recovered for power generation,winter heating and other heat needs, which has good economic benefits.Key words: copper smelting; slow cooling; heat recovery; wasteheat power generation;铜冶炼渣含有大量的有价元素,是重要的二次金属资源。
在铜冶炼渣处理的过程中,使熔融冶炼渣中的铜硫化物和金属铜结晶颗粒长大,有利于对后续浮选法选铜,因而缓冷工艺被广泛应用。
- 1、下载文档前请自行甄别文档内容的完整性,平台不提供额外的编辑、内容补充、找答案等附加服务。
- 2、"仅部分预览"的文档,不可在线预览部分如存在完整性等问题,可反馈申请退款(可完整预览的文档不适用该条件!)。
- 3、如文档侵犯您的权益,请联系客服反馈,我们会尽快为您处理(人工客服工作时间:9:00-18:30)。
某铜冶炼厂余热利用系统简介
摘要:本文对某铜冶炼厂余热利用系统的设计方案进行了介绍和总结,简要的阐述了该厂具体的余热利用系统。
关键词:余热利用余热锅炉余热发电
1 工艺余热锅炉概况
某有色铜冶炼工程中设置了熔炼余热锅炉、吹炼余热锅炉、硫酸热管余热锅炉,共计六台。
熔炼余热锅炉、吹炼余热锅炉生产次高压饱和蒸汽,两台硫酸热管余热锅炉生产中压饱和蒸汽,另外两台硫酸热管余热锅炉生产低压饱和蒸汽。
1.1 闪速熔炼、吹炼余热锅炉
闪速熔炼、吹炼炉在生产过程中排出大量高温含尘烟气,烟气温度高达1300℃左右,并含有较高浓度的烟尘和so2气体,利用余热锅炉回收烟气的热量,并生产次高压饱和蒸汽。
余热锅炉设计参数主要根据工艺烟气条件(so2气体露点)和蒸汽用途来确定。
熔炼、吹炼炉余热锅炉参数见表1。
1.2 硫酸热管余热锅炉
硫酸转化工段在生产过程中大量高温烟气需降温放热,利用热管余热锅炉回收烟气的热量,并生产中、低压饱和蒸汽。
余热锅炉设计参数主要根据工艺烟气条件和蒸汽用途来确定。
硫酸热管锅炉参数见表2。
2 余热利用系统
2.1 蒸汽消耗量统计
全厂蒸汽消耗主要有蒸汽干燥车间、电解车间、净液车间、布袋收尘器、制氧蒸汽加热器、制酸工段硫化钠设备、除氧器、浴室等,车间生产、生活用蒸汽消耗量表3。
考虑管网热损失、生产热负荷同时使用系数、生活热负荷同时使用系数,冬季计算最大用汽量123.8 t/h,夏季平均用汽量86.3 t/h。
2.2 蒸汽平衡
蒸汽系统汽平衡见表4。
2.3 余热利用系统
从全厂锅炉产汽和厂区蒸汽消耗参数来看,厂区蒸汽管网分为6.0mpa、2.5mpa、0.6mpa三个压力等级,其中厂区蒸汽消耗点分布在2.5mpa、0.6mpa两个压力等级。
对于每一种压力等级的多余饱和蒸汽可通过两种途径满足用户要求,一是通过减压后送入下一级蒸汽管网,另一种是利用蒸汽压差发电,排出的背压蒸汽送入下一级蒸汽管网使用。
由于第一种方案能源浪费很大,与当今能源发展政策不相符。
本设计采用第二种途径,设置饱和蒸汽汽轮发电机组发电。
针对6.0mpa等级的蒸汽,设置背压机组1套。
余热锅炉产生的6.0mpa饱和蒸汽全部进入饱和蒸汽背压汽轮发电机组(参
数:q1=110t/h,p1=5.5mpa,p2=2.5 mpa)。
背压蒸汽进入2.5mpa 压力等级蒸汽管网。
针对2.5mpa、0.6mpa等级的蒸汽,设置补汽凝汽机组1套(进汽参数:q1=4~20t/h,p1=2.5mpa,q2=12~60 t/h,p2=0.6mpa)。
2.5mpa
饱和蒸汽供生产和利用汽液全流螺杆动力机拖动动力设备外,剩余蒸汽全部进汽轮机,排出0.6mpa蒸汽进0.6mpa压力等级的管网,0.6mpa管网剩余的饱和蒸汽再接至该机组补汽口,回收凝结水。
考虑余热利用设备事故或检修时,工艺系统不能停产,对汽机设置了事故减压装置作为旁通,同时针对0.6mpa饱和蒸汽设置了蒸汽卸载冷凝器,回收凝结水。
熔炼年修时电解车间用汽,由设置的低压锅炉房提供蒸汽。
余热锅炉的补给水由纯水站提供,经除氧器除氧后由锅炉给水泵送余热锅炉汽包,全厂原则性热力系统见图1。
3 系统及设备特点
3.1 系统的特点
①余热锅炉所产蒸汽得到了充分合理的利用。
②汽轮机进汽量波动范围大,能保证蒸汽首先满足工艺用汽的要求的前提下,多余蒸汽用来发电。
③汽液全流螺杆动力机的应用,既能使多余的高品位蒸汽得到合理利用,又能使其拖动的水泵实现无极变速调解。
④年余热发电约5600万度,经济效益十分可观。
3.2 饱和蒸汽发电机组的特点
①能适应进汽量变化频繁的使用要求;蒸汽波动范围为
5%~100%。
②精密设计,精细加工,应用高档材料,确保汽轮机的使用寿命。
③汽轮机及其所有附属设备的技术是先进的、成熟的。
④进口多阀门调节确保最好性能及部分负载时的操作稳定和高效率。
3.3 汽液全流螺杆动力机的特点
①进口蒸汽压力为1.6mpa~2.0mpa,压力适应范围广,利用蒸汽的压差能量拖动泵,做功后的蒸汽排入0.6 mpa管网系统。
②在全厂停电事故状态下,能利用汽包所蓄热水和蒸汽能量,短时间拖动循环泵为余热锅炉的炉水循环提供动力,保证余热锅炉水循环的可靠性。
③汽液全流螺杆动力机的应用,既能使多余的高品位蒸汽得到合理利用,又能使其拖动的水泵实现无极变速调解。