过程FMEA手册案例
FMEA经典案例48654
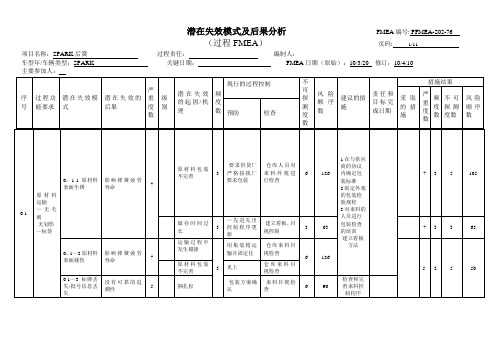
63
清洁
防错图
7
3
3
63
8—2小头朝下,挂弹簧位置超出180度
不能使疲劳寿命最优化
6
悬挂位置不正确
2
-培训
—防错图
100%目视检查
3
72
8-3挂钩未能更换
影响涂层质量
6
没有按时更换
3
-对操作工进行培训
—更换程序检查
每天作检查记录
3
54
9-1清洗
弹簧表面未清洗干净
影响涂层质量
6
温度、时间、喷头压力不恰当
每班检测丸粒比例1次/2H
5-4叶片磨损
强度不够
6
叶片磨损
3
预防性维修
1.喷丸工程师每天检查1次
2.防错图
3
4
54
160
5-5喷丸强度不足
弹簧早期断裂
8
上述参数存在偏差
5
预防性维修
做Allmen试片1次/4H,每次3只弹簧,在不同位置
设备项修后三只弹簧试片饱和度验证
设备科
每次项修后
PPAP阶段采用控制图
2.参数设置偏差
3
-设备预防性维修
—规定拨叉速度并锁定
—生产准备阶段确定
1.操作者点检1次/2h
2.QC检查1次/4h
6
126
5
喷丸1
-提高弹簧的疲劳寿命
-喷丸强度
-喷丸覆盖率
-喷丸时间
-丸粒比例
-丸粒流量
-表面无轧伤
5—3丸粒比例失调
喷丸强度不够
7
1.小丸粒比例过大
2.未及时添加丸粒
3
每班按工艺每60min添加丸粒
FMEA第五版(实例)2023

PFMEA 过程潜在失效模式及影响分析
过程职责: 保密级别:
PMEA 编
页 码:
编制者/日期: 批准/日 期:
版本 号:
第
页, 共
页
结构分析
功能分析
失效分析
风险分析
优化
工 序 编 号
过程项目系 统、子系统 、组件要素 或过程名称
过程步骤
过程影响 因素
注塑机台
过程项目的功能系 统、子系统、组件
要素或过程功能
PFMEA 措施优
先级 (AP)
特 殊 特 性
预防措施
探测 措施
责任 目标 人姓 完成
名 时间
状态
采取 基于 证据 的措
施
实 际 时 间
严 重 度 S
发 生 度 O
探特 测 殊 PFMEA 备注
度 特 AP
D性
工厂:检验来料是 否符合要求
工厂:生产无法使用
针对已制
客户:马达装配
检验来料是 否符合要求
a.作业人员
作业不规范
b.标签打印 包装作业指导
错误\粘贴
书
错误
2
作业员检查
2
L
70
入库储存
储存过程
仓管员
工厂:成品仓储
客户:马达装配 最终用户:车灯转 动
工厂:重复发货增加
将成品放置 规定库位
产品标识与库 位要求是否一
致
工厂成本 客户:影响客户装配
最终用户:无影响
6
a、发货时
发错
b、无法追 现场标识不
2
IQC检验
4
L
最终用户:车灯转
最终用户:影响产品
产
fmea案例
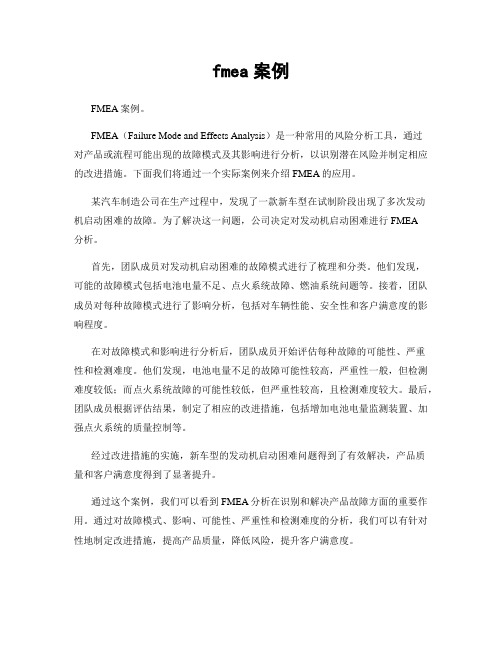
fmea案例FMEA案例。
FMEA(Failure Mode and Effects Analysis)是一种常用的风险分析工具,通过对产品或流程可能出现的故障模式及其影响进行分析,以识别潜在风险并制定相应的改进措施。
下面我们将通过一个实际案例来介绍FMEA的应用。
某汽车制造公司在生产过程中,发现了一款新车型在试制阶段出现了多次发动机启动困难的故障。
为了解决这一问题,公司决定对发动机启动困难进行FMEA分析。
首先,团队成员对发动机启动困难的故障模式进行了梳理和分类。
他们发现,可能的故障模式包括电池电量不足、点火系统故障、燃油系统问题等。
接着,团队成员对每种故障模式进行了影响分析,包括对车辆性能、安全性和客户满意度的影响程度。
在对故障模式和影响进行分析后,团队成员开始评估每种故障的可能性、严重性和检测难度。
他们发现,电池电量不足的故障可能性较高,严重性一般,但检测难度较低;而点火系统故障的可能性较低,但严重性较高,且检测难度较大。
最后,团队成员根据评估结果,制定了相应的改进措施,包括增加电池电量监测装置、加强点火系统的质量控制等。
经过改进措施的实施,新车型的发动机启动困难问题得到了有效解决,产品质量和客户满意度得到了显著提升。
通过这个案例,我们可以看到FMEA分析在识别和解决产品故障方面的重要作用。
通过对故障模式、影响、可能性、严重性和检测难度的分析,我们可以有针对性地制定改进措施,提高产品质量,降低风险,提升客户满意度。
总之,FMEA是一种简单而有效的风险分析工具,可以帮助我们识别和解决潜在风险,提高产品质量,降低成本,增强竞争力。
在实际工作中,我们应该充分发挥FMEA的作用,不断完善和改进产品和流程,为企业的可持续发展提供有力支持。
FMEA新版手册范本

word前言第三版FMEA第三版(QS-9000)是戴姆勒克莱斯勒、福特和通用汽车公司的供方所使用的参考手册,为协助他们在开发设计和过程FMEA提供了指导方向。
本手册意图澄清有关FMEA开发上的技术问题。
本手册符合供方质量要求推动小组 (Supplier Quality Requirement Task Force) 的授权,将戴姆勒克莱斯勒、福特和通用汽车公司在其各自的供方质量体系中应用的参考手册、程序、报告格式和技术术语进展标准化处理。
由于FMEA第三版手册是用来提供给供方的泛用指导,本手册并不规定要求,它意图在设计阶段或过程分析阶段准备FMEA的时候,提供涵盖了一般的概括指导。
本手册等同于SAE J1739为设计和过程FMEA的技术。
然而,他并不包含机械装置的FMEA应用。
对机械装置FMEA方面有兴趣,可参考SAE J1739的相关X例。
供方质量要求工作小组感谢如下每个人,和他们的公司,他们贡献时间和努力开发了FMEA新版手册和较早的版本。
第三版Kevin A. Lange-DaimlerChryslerSteven C. Leggett-General Motors CorporationBeth Baker-AIAG较早版本Howard Riley-DaimlerChrysler Mark T. Wrobbel-- DaimlerChryslerGeorge R. Baumgarther-Ford Motor pany Rebecca French-General MotorsLawrence R. McCullen-General Motors Mary Ann Raymond--BoschRobert A. May-Goodyear William Ireland-Kelsey-HayesTripp Martin-Peterson Spring此外,供方质量要求小组感谢如下在SAE J1739工作小组的个人,他们在这次改版中对技术的变更和改良,有卓越的贡献。
最新FMEA分析经典案例

潜在失效模式及后果分析FMEA编号: PFMEA-S02-76项目名称:富元电子组装线过程责任:装配车间编制人:赵立领车型年/车辆类型:____ 关键日期: FMEA日期(原始):19/4/13 修订:_______主要参加人:1潜在失效模式及后果分析FMEA编号: PFMEA-S02-76项目名称:富元电子组装线过程责任:装配车间编制人:赵立领车型年/车辆类型:____ 关键日期: FMEA日期(原始):19/4/13 修订:_______主要参加人:2潜在失效模式及后果分析FMEA编号: PFMEA-S02-76项目名称:富元电子组装线过程责任:装配车间编制人:赵立领车型年/车辆类型:____ 关键日期: FMEA日期(原始):19/4/13 修订:_______主要参加人:3潜在失效模式及后果分析FMEA编号: PFMEA-S02-76项目名称:富元电子组装线过程责任:装配车间编制人:赵立领车型年/车辆类型:____ 关键日期: FMEA日期(原始):19/4/13 修订:_______主要参加人:4潜在失效模式及后果分析FMEA编号: PFMEA-S02-76项目名称:富元电子组装线过程责任:装配车间编制人:赵立领车型年/车辆类型:____ 关键日期: FMEA日期(原始):19/4/13 修订:_______主要参加人:5潜在失效模式及后果分析FMEA编号: PFMEA-S02-76项目名称:富元电子组装线过程责任:装配车间编制人:赵立领车型年/车辆类型:____ 关键日期: FMEA日期(原始):19/4/13 修订:_______主要参加人:61718191101111121131111611711811912012112212311-规定丸粒流量并锁定-丸粒添加程序1次/80min,每次添加25Kg1.2mm丸粒。
25-设1127128129130113213313411361371139140141142143144145146147148149150。
PFMEA分析案例

项目名称:F507 M31814002电源接插件支架核心小組:项目名称:F507 M31814002电源接插件支架车辆/年度:潜在失效模式及后Failure Mode and Ef(过程F吴为、易军林(技术部);张茂科、漆敏(品质部);谭红军、敖顺洲(生产车辆/年度:Failure Mode and Ef(过程F核心小組:项目名称:F507 M31814002电源接插件支架核心小組:吴为、易军林(技术部);张茂科、漆敏(品质部);谭红军、敖顺洲(生产车辆/年度:Failure Mode and Ef(过程F吴为、易军林(技术部);张茂科、漆敏(品质部);谭红军、敖顺洲(生产项目名称:F507 M31814002电源接插件支架核心小組:车辆/年度:Failure Mode and Ef(过程F吴为、易军林(技术部);张茂科、漆敏(品质部);谭红军、敖顺洲(生产项目名称:F507 M31814002电源接插件支架核心小組:车辆/年度:Failure Mode and Ef(过程F吴为、易军林(技术部);张茂科、漆敏(品质部);谭红军、敖顺洲(生产项目名称:F507 M31814002电源接插件支架核心小組:车辆/年度:Failure Mode and Ef(过程F吴为、易军林(技术部);张茂科、漆敏(品质部);谭红军、敖顺洲(生产47±0.2超差项目名称:F507 M31814002电源接插件支架核心小組:产品成型后尺Failure Mode and Ef(过程F吴为、易军林(技术部);张茂科、漆敏(品质部);谭红军、敖顺洲(生产车辆/年度:FMEA编号:过程责任部门:供销部、品质部关键日期:编制者:FMEA日期:FMEA编号:过程责任部门:生产部冲压二组关键日期:编制者:页码: 第 1 页 共 7 页2015.7.25张茂科式及后果分析d Effect Analasis 过程FMEA)CD/PFMLH-005(生产部);仲伟成(供销部)2015.7.252015.7.25张茂科d Effect Analasis 过程FMEA)CD/PFMLH-005页码: 第 2 页 共 7 页FMEA日期:FMEA编号:过程责任部门:生产部冲压二组关键日期:编制者:FMEA日期:(生产部);仲伟成(供销部)2015.7.25页码: 第 3 页 共 7 页2015.7.25张茂科d Effect Analasis 过程FMEA)CD/PFMLH-005(生产部);仲伟成(供销部)2015.7.25FMEA编号:过程责任部门:生产部加工组关键日期:编制者:FMEA日期:页码: 第 4 页 共 7 页2015.7.25张茂科d Effect Analasis 过程FMEA)CD/PFMLH-0052015.7.25(生产部);仲伟成(供销部)FMEA编号:过程责任部门:生产部冲压二组关键日期:编制者:FMEA日期:页码: 第 5 页 共 7 页2015.7.25张茂科d Effect Analasis 过程FMEA)CD/PFMLH-0052015.7.25(生产部);仲伟成(供销部)FMEA编号:过程责任部门:生产部冲压二组关键日期:编制者:FMEA日期:页码: 第 6 页 共 7 页2015.7.25张茂科d Effect Analasis 过程FMEA)CD/PFMLH-005(生产部);仲伟成(供销部)2015.7.25FMEA编号:过程责任部门:生产部加工组关键日期:编制者:FMEA日期:d Effect Analasis 过程FMEA)CD/PFMLH-005(生产部);仲伟成(供销部)2015.7.25页码: 第 7 页 共 7 页2015.7.25张茂科。
fmea案例

fmea案例FMEA案例。
FMEA(Failure Mode and Effects Analysis)是一种系统性的、前瞻性的方法,用于识别和消除产品或过程中的潜在故障和问题。
通过对可能的故障模式、故障影响和故障原因进行分析,可以预防和减少故障的发生,提高产品的质量和可靠性。
下面我们将通过一个实际案例来介绍FMEA的应用。
案例背景:某汽车制造公司在生产过程中发现,部分车型的发动机在高速行驶时出现了持续性的抖动现象,经过初步调查发现,这一问题导致了不少车辆的质量问题,严重影响了客户的使用体验,因此迫切需要找到问题的根源并解决。
FMEA分析过程:1. 确定分析范围,首先确定分析的范围,包括发动机的设计、生产、装配、使用和维护等环节。
2. 识别故障模式,对发动机可能出现的故障模式进行识别和描述,例如发动机抖动、发动机熄火、发动机失去动力等。
3. 评估故障影响,针对每个故障模式,评估其对产品性能、安全性、可靠性等方面的影响程度,以及对客户的影响。
4. 确定故障原因,分析每个故障模式可能的原因,例如设计缺陷、零部件质量问题、生产工艺不当等。
5. 制定改进措施,针对识别出的故障模式和原因,制定相应的改进措施,包括设计优化、工艺改进、零部件更换等。
6. 实施改进措施,将改进措施落实到实际生产中,并进行跟踪和验证,确保问题得到有效解决。
案例分析结果:经过FMEA分析,发现该汽车发动机抖动的主要原因是由于某零部件的设计不当导致的,该零部件在高速行驶时容易产生共振现象,从而引起发动机抖动。
针对这一问题,制定了更换设计合理的零部件、优化发动机控制系统等改进措施,并在生产中逐步实施。
经过一段时间的跟踪和验证,发现抖动现象得到了明显改善,客户投诉情况也大幅减少。
结论:通过FMEA分析,该汽车制造公司成功地找到了发动机抖动问题的根源,并采取了有效的改进措施,提高了产品质量和客户满意度。
FMEA方法不仅帮助企业预防和解决了具体的质量问题,更重要的是建立了一套系统性的质量管理方法,为企业持续改进提供了有力的工具和支持。
FMEA案例范文
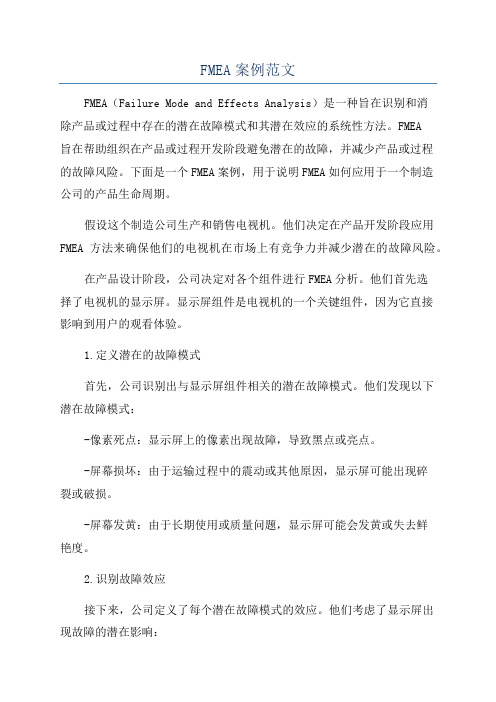
FMEA案例范文FMEA(Failure Mode and Effects Analysis)是一种旨在识别和消除产品或过程中存在的潜在故障模式和其潜在效应的系统性方法。
FMEA旨在帮助组织在产品或过程开发阶段避免潜在的故障,并减少产品或过程的故障风险。
下面是一个FMEA案例,用于说明FMEA如何应用于一个制造公司的产品生命周期。
假设这个制造公司生产和销售电视机。
他们决定在产品开发阶段应用FMEA方法来确保他们的电视机在市场上有竞争力并减少潜在的故障风险。
在产品设计阶段,公司决定对各个组件进行FMEA分析。
他们首先选择了电视机的显示屏。
显示屏组件是电视机的一个关键组件,因为它直接影响到用户的观看体验。
1.定义潜在的故障模式首先,公司识别出与显示屏组件相关的潜在故障模式。
他们发现以下潜在故障模式:-像素死点:显示屏上的像素出现故障,导致黑点或亮点。
-屏幕损坏:由于运输过程中的震动或其他原因,显示屏可能出现碎裂或破损。
-屏幕发黄:由于长期使用或质量问题,显示屏可能会发黄或失去鲜艳度。
2.识别故障效应接下来,公司定义了每个潜在故障模式的效应。
他们考虑了显示屏出现故障的潜在影响:-像素死点:用户在观看电视节目或电影时会被黑点或亮点分散注意力,影响观看体验。
-屏幕损坏:显示屏碎裂或破损可能导致显示效果变差,甚至无法使用。
-屏幕发黄:显示屏发黄或失去鲜艳度会影响图像质量,用户无法获得高质量的观看体验。
3.评估潜在原因和控制措施公司评估了每个潜在故障模式的可能原因,并制定相应的控制措施以减少潜在故障模式的出现概率:-像素死点的可能原因:制造过程中的材料问题,控制措施是选择高质量的材料,进行严格的质量控制。
-屏幕损坏的可能原因:运输过程中的震动,控制措施是加强包装和运输过程中的保护。
-屏幕发黄的可能原因:长期使用,控制措施是使用高品质的材料和组件,以及进行适当的维护和保养。
4.评估风险严重性和优先级公司为每个潜在故障模式评估了风险严重性和优先级,以指导其在产品设计过程中的决策:-像素死点的风险严重性:中等,由于像素死点会影响观看体验,但不会导致电视机无法使用。
过程FMEA范例(工具书标准)

人工插入喷头不够深入
8
每小时进行一次目测检查,每班检查一次喷膜厚度(深度计)和范围
5
280
给喷蜡器加装深度限位器
制造工程
9X 10 15
增加限位器,在线上检查喷枪
7
2
5
70
使喷蜡自动化
制造工程
9X 12 15
由于同一条线上有不同的门,较复杂,因此拒绝该项
7
喷头堵塞
粘度太高
温度太低
压力太低
5
在开始和停机后试验喷雾形状,按照预防维护程序清洗喷头
结合观察和试验验证蜡的上边缘
泰特-车身工程师
9X 01 15
试验结果(1481号试验)表明要求的厚度是合适的。设计试验分析表明规定的厚度变差在25%范围内可以接受
7
2
2
28
7
蜡的配方不当
2
理化实验室实验-报告No.1265
2
28
无
7
混入的空气阻止蜡进入边角部分
5
用功能不良的喷头进行设计辅助调查
8
280
5
70
无
7
喷蜡时间不足
8
按作业指导书进行抽样(每班10个门),检查关键部分喷蜡范围
7
392
安装喷蜡定时器
维修部
9X 09 15
安装了自动喷蜡定时器,操作者打开喷头,定时器控制关闭,控制图显示过程受控
Cpk=2.05
7
1
7
49
示例
潜在失效模式及后果分析
(设计FMEA)
部件01.03/车身密封②设计责任:车身工程部③
车型年/车辆类型199X/狮牌4门/旅行车⑤关键日期:9X年03 01⑥
fmea 案例
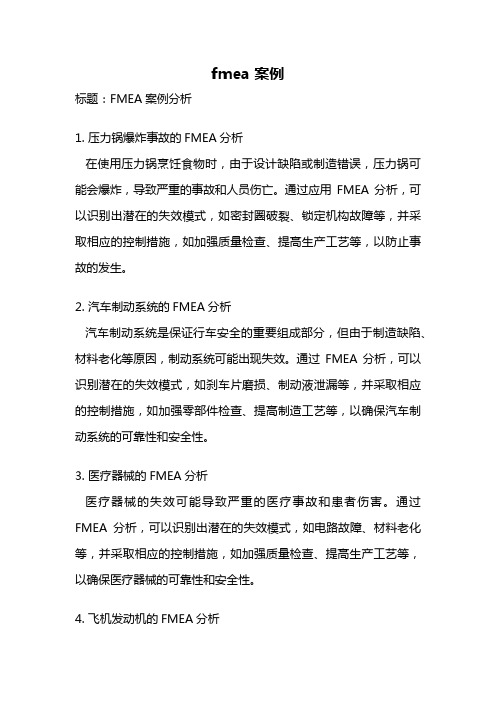
fmea 案例标题:FMEA案例分析1. 压力锅爆炸事故的FMEA分析在使用压力锅烹饪食物时,由于设计缺陷或制造错误,压力锅可能会爆炸,导致严重的事故和人员伤亡。
通过应用FMEA分析,可以识别出潜在的失效模式,如密封圈破裂、锁定机构故障等,并采取相应的控制措施,如加强质量检查、提高生产工艺等,以防止事故的发生。
2. 汽车制动系统的FMEA分析汽车制动系统是保证行车安全的重要组成部分,但由于制造缺陷、材料老化等原因,制动系统可能出现失效。
通过FMEA分析,可以识别潜在的失效模式,如刹车片磨损、制动液泄漏等,并采取相应的控制措施,如加强零部件检查、提高制造工艺等,以确保汽车制动系统的可靠性和安全性。
3. 医疗器械的FMEA分析医疗器械的失效可能导致严重的医疗事故和患者伤害。
通过FMEA分析,可以识别出潜在的失效模式,如电路故障、材料老化等,并采取相应的控制措施,如加强质量检查、提高生产工艺等,以确保医疗器械的可靠性和安全性。
4. 飞机发动机的FMEA分析飞机发动机是飞机正常运行的关键部件,但由于设计缺陷、制造错误等原因,发动机可能出现失效。
通过FMEA分析,可以识别出潜在的失效模式,如涡轮叶片断裂、燃油泄漏等,并采取相应的控制措施,如加强零部件检查、提高制造工艺等,以确保飞机发动机的可靠性和安全性。
5. 电力系统的FMEA分析电力系统的失效可能导致停电、火灾等严重后果。
通过FMEA分析,可以识别出潜在的失效模式,如电缆老化、开关故障等,并采取相应的控制措施,如加强设备维护、提高操作规范等,以确保电力系统的可靠性和安全性。
6. 电子产品的FMEA分析电子产品的失效可能导致设备故障、用户伤害等问题。
通过FMEA分析,可以识别出潜在的失效模式,如电路短路、元器件老化等,并采取相应的控制措施,如加强质量检查、提高生产工艺等,以确保电子产品的可靠性和安全性。
7. 石油化工装置的FMEA分析石油化工装置的失效可能导致爆炸、泄漏等严重事故。
FMEA经典案例(1)(最新整理)
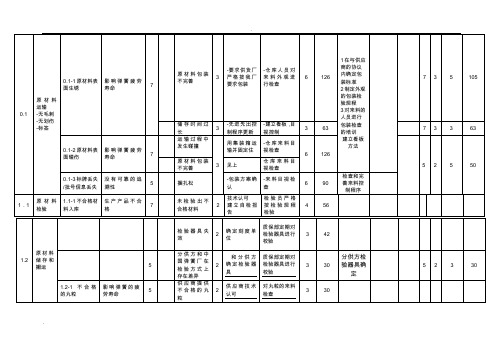
6
HIC
1.设备故障 2. 工 艺 参 数 设置误差
4
-光电开关控 制保证 -设备预防性 维修
光电开关控制 100%
3
72
.
.
6-2 压缩次数不 符合规范
弹簧长度超差
6
HIC
1.参数调整 2.人员
3
对生产线的 调整进行检 查
1.操作者自检 1 次/2h 2.QC 检查 1 次/4h
3
54
6-1 几何尺寸超 10-1 负荷超差,
.
0.1-1 原材料表 影 响 弹 簧 疲 劳
面生锈
寿命
7
原材料 运输 0.1 -无毛刺 -无划伤 -标签
0.1-2 原材料表 影 响 弹 簧 疲 劳
面碰伤
寿命
7
0.1-3 标牌丢失 没 有 可 靠 的 追 /批号信息丢失 溯性
5
1.1
原材料 检验
1.1-1 不合格材 料入库
生产产品不合 格
7
原材料
2
确定检验器 具
检验器具进行 校验
3
存在差异
供应商提供
供 应 商 技 术 对丸粒的来料
不 合 格 的 丸 2 认可
检查
3
粒
1 在与供应
商的协议
126 内确定包 装标准
2 制定外观
的包装检
验规程
3 对来料的
人员进行
63
包装检查 的培训
建立看板
方法
126
检查和完
90
善来料控
制程序
56
42
分供方检 30 验器具确
2. 测 量 所 用 量具不准
3
量具定期校 验
冲压件过程PFMEA案例
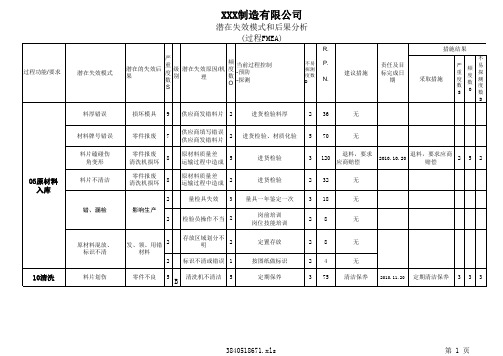
5
进货检验
原材料质量差 运输过程中造成
2
进货检验
5 70
无
3
120
退料,要求 应商赔偿
2010.10.20Βιβλιοθήκη 退料,要求应商 赔偿2
5
2
2 32
无
2
量检具失效 3 量具一年鉴定一次
3 18
无
影响生产
2 检验员操作不当 2
岗前培训 岗位技能培训
28
无
发、领、用错 2 材料
存放区域划分不 明
2
定置存放
28
无
责任及目 标完成日
期
无
措施结果
采取措施
不
严 重 度 数 S
频 度 数 O
易 探 测 度 数
D
材料牌号错误 料片磕碰伤 角变形 料片不清洁
错、漏检
原材料混放、 标识不清
料片划伤
零件报废 7
零件报废 清洗机损坏
8
零件报废 清洗机损坏
8
供应商填写错误 供应商发错料片
2
进货检验、材质化验
原材料质量差 运输过程中造成
孔变形 切边毛刺大 废料未切断 切边排废料不畅, 造成垫废吸入模具内
翻边尺寸超差
翻边开裂 整形不到位 钢印不清楚
零件返修 4
零件返修 7
零件返修 2
零件报废 零件返修
5
6 零件报废
5
零件报废 6 零件报废 5
零件报废 5
模具状态不佳 2
模具质量搞升
模具刀块刃口坏 9 QRK抽检,包装全检
模具刀块刃口坏 3 QRK抽检,包装全检
无
钢印磨损
3
QRK首检,抽检,抽检, 末检
第五版fmea实例

第五版fmea实例FMEA(故障模式与影响分析)是一种系统化的方法,用于识别和评估潜在的故障模式以及它们对产品、过程或系统的影响。
第五版FMEA是指AIAG(汽车行业行动组)和VDA(德国汽车工业协会)共同发布的FMEA手册的第五个版本。
下面是一个关于汽车制造过程的第五版FMEA的实例:1. 识别过程,在这个阶段,需要确定汽车制造过程中的所有关键步骤和子过程。
例如,焊接、喷涂、装配等。
2. 识别潜在故障模式,对于每个识别出来的过程步骤,需要分析可能出现的故障模式。
例如,在焊接过程中,可能出现焊接点质量不良、焊接接头松动等故障模式。
3. 评估故障后果,对于每个故障模式,需要评估其对产品质量和安全性的影响。
例如,焊接点质量不良可能导致焊接接头松动,进而影响汽车结构的强度和稳定性。
4. 评估故障发生概率,对于每个故障模式,需要评估其发生的概率。
这可以基于历史数据、专家意见或其他可用的信息来进行估计。
5. 评估故障检测能力,对于每个故障模式,需要评估当前的故障检测能力。
这涉及到检测方法和设备的有效性和可靠性。
6. 计算风险优先级数(RPN),通过将故障后果、故障发生概率和故障检测能力相乘,可以计算出每个故障模式的风险优先级数。
RPN越高,表示该故障模式对产品质量和安全性的影响越大。
7. 制定改进措施,对于高风险优先级数的故障模式,需要制定相应的改进措施。
例如,改进焊接工艺、加强质量检查等。
8. 实施改进措施,将制定的改进措施付诸实施,并监控其效果。
例如,改进焊接工艺后,进行焊接接头的强度测试。
9. 重新评估风险优先级数,在实施改进措施后,需要重新评估故障模式的风险优先级数,以确定改进措施的有效性。
10. 持续改进,FMEA是一个持续改进的过程,需要定期审查和更新。
随着时间的推移,新的故障模式可能会出现,而旧的故障模式可能会被解决或变得不再重要。
以上是一个关于汽车制造过程的第五版FMEA的实例。
在实际应用中,FMEA可以根据不同行业和领域的需求进行定制和调整。
FMEA手册上的完整案例(DFMEA)

R DP
N 3 30
3 30
3 30
角落设计使得喷 涂设备无法覆盖 所有需喷涂区域
车门板之间空间 不够,容不下喷 头
5 用非功能喷头进 7 175 利用正式量产喷 车身工程部和总 基于试验结果:在 5 1 1 5
行设计辅助调查;
腊设备和特定的 装厂
受影响的区域增加3
整车耐久性试验
标要求不够
(#31268)
T-118(7)
以及最佳实
践
(BP3455)
探R 测P 度N D
建议措施
7 105 增加实验室加速 腐蚀试验
7 105 增加实验室强化 腐蚀试验
对蜡层厚度进行 实验设计(DOE)
蜡的配方规定得 行业标准
不当
MS-1893
2 理化实验室实验- 5 报告NO1265; 整车耐久性试验 T-118(7)
50 无
职责和目标 完成日期
实施结果
采取的措施 完成日期
SO
泰特-车身工程 根据试验结果(4- 5 2
师
484号试验)上边缘
2008-9-03
规范增加125mm。
2008-09-03
泰特-车身工程 试验结果(4-484号 5 2
师
试验)表明要求的
2008-9-03
厚度是充分的。
2008-9-03
J.Smthye 车身 实验设计表明规定 5 2 设计工程师 的厚度变差在25%范 2008-10-18 围内可以接受。
饰板的完整 间,5年 不生锈、 腐蚀
锈,使顾客对 外观不满 ②损害车门内 附Βιβλιοθήκη 件严重 度
分 类
潜在失效原因
S
fmea成功案例

fmea成功案例FMEA(故障模式与影响分析)是一种系统性的方法,用于识别和评估潜在故障模式及其对系统性能的影响。
下面是一些FMEA成功案例的示例。
1. 汽车生产线的FMEA:在汽车生产线上,FMEA被广泛应用于识别和预防潜在的故障模式,以确保高质量和高效率的生产。
通过对每个工作站和关键步骤进行FMEA分析,制造商能够及早发现潜在问题,并采取相应的纠正措施,从而避免生产线停机和产品质量问题。
2. 医疗器械设计的FMEA:在医疗器械设计过程中,FMEA被用于识别和评估潜在的设计缺陷和安全风险。
通过分析每个组件和子系统的潜在故障模式及其对患者安全和治疗效果的影响,设计团队能够及早发现并解决潜在问题,确保医疗器械的安全性和可靠性。
3. 航空航天领域的FMEA:在航空航天领域,FMEA被广泛应用于识别和评估潜在的故障模式,以确保飞机和航天器的安全和可靠性。
通过对每个关键系统和组件进行FMEA分析,工程师能够识别出潜在的故障模式,并采取相应的措施来预防或减轻其对系统性能的影响。
4. 制药行业的FMEA:在制药行业,FMEA被用于识别和评估潜在的制造过程中的风险和质量问题。
通过对每个关键步骤和操作进行FMEA分析,制药公司能够及早发现潜在问题,并采取相应的措施来确保产品质量和符合法规要求。
5. 电子产品设计的FMEA:在电子产品设计过程中,FMEA被用于识别和评估潜在的设计缺陷和可靠性问题。
通过对每个关键功能和组件进行FMEA分析,设计团队能够及早发现潜在问题,并采取相应的措施来提高产品的可靠性和性能。
6. 银行业的FMEA:在银行业,FMEA被用于识别和评估潜在的操作风险和安全问题。
通过对每个关键业务流程和操作进行FMEA分析,银行能够及早发现潜在风险,并采取相应的措施来预防或减轻其对业务运营的影响。
7. 石油和化工行业的FMEA:在石油和化工行业,FMEA被广泛应用于识别和评估潜在的安全和环境风险。
通过对每个关键工艺步骤和设备进行FMEA分析,公司能够及早发现潜在问题,并采取相应的措施来预防事故和减轻对环境的影响。
注塑成型过程FMEA案例
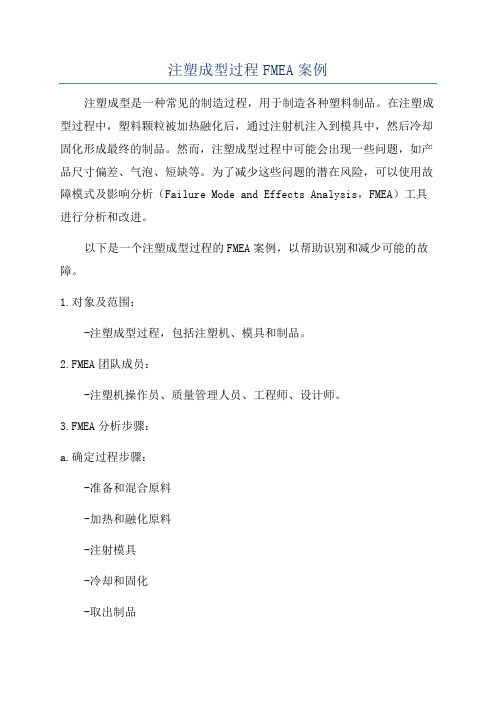
注塑成型过程FMEA案例注塑成型是一种常见的制造过程,用于制造各种塑料制品。
在注塑成型过程中,塑料颗粒被加热融化后,通过注射机注入到模具中,然后冷却固化形成最终的制品。
然而,注塑成型过程中可能会出现一些问题,如产品尺寸偏差、气泡、短缺等。
为了减少这些问题的潜在风险,可以使用故障模式及影响分析(Failure Mode and Effects Analysis,FMEA)工具进行分析和改进。
以下是一个注塑成型过程的FMEA案例,以帮助识别和减少可能的故障。
1.对象及范围:-注塑成型过程,包括注塑机、模具和制品。
2.FMEA团队成员:-注塑机操作员、质量管理人员、工程师、设计师。
3.FMEA分析步骤:a.确定过程步骤:-准备和混合原料-加热和融化原料-注射模具-冷却和固化-取出制品-检查和包装b.识别失败模式:注塑机操作员、质量管理人员和工程师共同讨论并列出每个过程步骤中可能发生的故障模式,如:-原料混合错误-温度控制失效-模具堵塞-冷却时间不足-提取脱模困难-储存和包装时的损坏c.分析失败效果:-尺寸偏差:中度-表面缺陷:轻度-制品破损:重度d.确定潜在原因:分析每个失败模式的可能原因,如:-原料混合错误:操作错误、测量错误-温度控制失效:传感器故障、加热器故障-模具堵塞:模具设计不当、注射速度过快-冷却时间不足:冷却系统故障、注射速度过快-提取脱模困难:模具设计不当、提取工具磨损-储存和包装时的损坏:不恰当的包装、操作错误e.识别当前控制措施:确定当前针对每个故障模式的控制措施,如:-原料混合错误:培训操作员、使用标准测量工具-温度控制失效:定期检查传感器、定期维护加热器-模具堵塞:定期清洗模具、控制注射速度-冷却时间不足:定期维护冷却系统、控制注射速度-提取脱模困难:改进模具设计、定期维护提取工具-储存和包装时的损坏:改进包装方式、进行培训f.确定改进控制措施:识别可能的改进控制措施,以减少或防止故障模式的发生,如:-原料混合错误:使用自动化原料混合系统-温度控制失效:安装备用传感器、增加自动控制功能-模具堵塞:改进模具设计、优化注射速度-冷却时间不足:改进冷却系统、优化注射速度-提取脱模困难:改进模具设计、定期更换提取工具-储存和包装时的损坏:改进包装材料、提供培训4.结论:通过FMEA分析,我们可以识别注塑成型过程中可能出现的故障模式和其潜在原因,并采取相应的控制措施进行改进。
FMEA手册上的标准完整案例(PFMEA)

因撞击使喷头变形 按照预防维 护程序保养 喷头
2 每小时进行一次目 5 测检查,每班检查 一次喷膜厚度(深度 计)和范围
50 无
喷蜡时间不足
8 按作业指导书进行 7 抽样(每班10个 门),检查关键部分 喷蜡范围
280 安装喷蜡定时器
维修部 2009-03-15
试验结果(4-484号试 5 1 5 25 验)表明要求的厚度 是充分的。 2009-04-10
蜡
下层表面涂
规定厚度的
间后生锈,使顾
腊
客对外观不满意
人工插入喷头不够 深入
8 每小时进行一次目 5 测检查,每班检查 一次喷膜厚度(深度 计)和范围
200 给喷蜡器加装深度 制造工程部
限位器
2009-03-15
增加限位器,在线上 5 2 5 50 检查喷枪。 2009-03-15
功能下降
使喷蜡自动化
项目 车型年 度/项目
01.03/左 前 20车 08款门狮 牌 4门/
潜在失效模式及后果分析
(过程FMEA)
过程责任:
制造工程 部
关键日期: 2009/5/20
核心小组:
H.斯蒂文 —制造工
FMEA编号: 页 码:
编 制: 编制日期: 修订日期:
FMEA-5687 第 1页共 1页 斯蒂文—工艺工程 师 2009/1/5
2009/4/19
过程步骤 功能
要求
潜在失效 失效模式 模式 潜在后果
严
重 度
分 类
潜在失效原因
S
控制预防
现行过程
频 度 控制探测 O
探R 测P 度N D
建议措施
职责和目标 完成日期
实施结果
FMEA案例

3
-设备预防性维修
-规定拨叉速度并锁定
-生产准备阶段确定
1.操作者点检1次/2h
2.QC检查1次/4h
6
126
5
喷丸1
-提高弹簧的疲劳寿命
-喷丸强度
-喷丸覆盖率
-喷丸时间
-丸粒比例
-丸粒流量
-表面无轧伤
5-3丸粒比例失调
喷丸强度不够
7
1.小丸粒比例过大
2.未及时添加丸粒
3
每班按工艺每60min添加丸粒
2.降低产品使用寿命
3.改变弹簧几何尺寸
7
HIC
设备故障
2
设备预防性保养计划
-操作工每2小时作自检
-质保部检查1次/4H
3
42
制定详细的设备失效应急计划
7
3
4
84
4
回火
-消除卷簧引起的应力
6
参数设置错误
2
培训
-操作工每2小时作自检
3
42
4-3回火硬度不符合要求
4-4各个炉段的回火温度不符合要求
降低产品疲劳寿命
3
-刀具管理
-100%去毛刺
-.喷丸
目视检查
4
84
刀具管理程序
生产科、设备科
7
3
4
84
4-1.回火间隔小于4h
弹簧使用寿命降低
8
HIC
1.回火设备坏
2.操作者未及时上料
4
-设备预防性维修
-周转箱控制方法
专用周转箱
4
128
1.建立周转箱定制
2.建立周转箱管理程序
8
4
3
96
FMEA培训教材专用案例
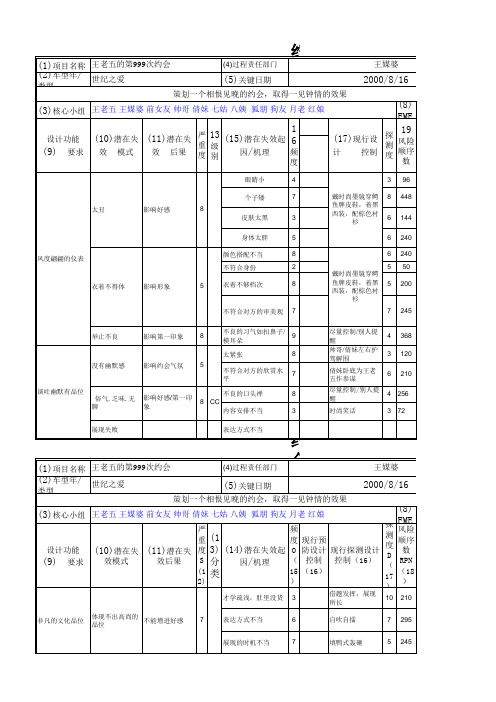
(4)过程责任部门
约会D-FMEA 约会 王媒婆
2000-8-16 (8)FMEA 19 (17)现行设 探 风险 测
控制 度 顺序 数
3 戴时尚墨镜穿鳄 鱼牌皮鞋,着黑 西装,配棕色衬 衫 8 6 6 6 5 戴时尚墨镜穿鳄 鱼牌皮鞋,着黑 西装,配棕色衬 衫 5 96 448 144 240 240 50 200
3 6 7
探 风险 测 顺序 现行预 防设计 现行探测设计 度 数 控制 控制(16) D RPN ( (18 (16) 17 ) 借题发挥,展现 )
所长 自吹自擂 填鸭式轰砸 10 7 5 210 295 245
非凡的文化品位
体现不出高尚的 不能增进好感 品位
7
表达方式不当 展现的时机不当
没有足够住房 经济基础差 影响婚姻成败 9 没有一定数额存款 有保障的经济基 础 经济没有保障 影响婚姻成败 9 没有丰厚的收入 工作没有保障 职业低下(清洁公 司) 油嘴滑舌,有“花心 ”的迹象 举止轻浮,动手动脚 感觉不可靠 值得托付终身的 品质 影响婚姻成败 9 有“前科”记录,有 暴力行为 不学上进,妒忌猜疑 心强 曾吃喝赌谝样样精通 不良习气 影响婚姻成败 7 好吃懒做
(5)关键日期
策划一个相恨见晚的约会,取得一见钟情的效果
(3)核心小组 王老五 王媒婆 前女友 帅哥 倩妹 七姑 八姨 狐朋 狗友 月老 红娘
设计功能 (9) 要求
1 (10)潜在失 (11)潜在失 严 13 (15)潜在失效起 6 重 级 效 模式 效 后果 度 因/机理 频 别
度
4 7 3 5 8 2 8 眼睛小 个子矮 太丑 影响好感 8 皮肤太黑 身体太胖
- 1、下载文档前请自行甄别文档内容的完整性,平台不提供额外的编辑、内容补充、找答案等附加服务。
- 2、"仅部分预览"的文档,不可在线预览部分如存在完整性等问题,可反馈申请退款(可完整预览的文档不适用该条件!)。
- 3、如文档侵犯您的权益,请联系客服反馈,我们会尽快为您处理(人工客服工作时间:9:00-18:30)。
车门寿命下降导致:
·由于漆面经过长时间后生锈,使顾客对外观不满意
·车门内附件功能下降
7
人工插入喷头不够深入
8
每小时或每班进行一次目测检查,查看喷膜厚度(深度仪)和范围
5
280
给喷蜡器加装深度限位器
黄广强—工程部02.11.15
增加限位器,在线上检查喷机
7
2
5
70
使喷蜡自动化
由于同一条线上有不同种门,较复杂,因此拒绝该项
7
1
5
35
因冲击使喷头变形
2
按照预防维护程序保养喷头
每小时或每班进行一次目测检查,查看喷膜厚度(深度仪)和范围
5
70
无
黄广强—工程部
02.11.05
喷蜡时间不足
8
作业指导书及批量抽样(每班10个门),检查关键部分喷蜡范围
7
安装喷蜡定时器
周志德—维修部
02.10.30
安装了自动喷蜡定时器,操作者打开喷头,定时器控制关闭,控制图显示过程受控CPK=2.05
喷头堵塞
粘度太高
温度太低
压力太大
5
在开始和停机后试验喷雾形状,按照预防维护程序清冼喷头
每小时或每班进行一次目测检查,查看喷膜厚度(深度仪)和范围
5
175
对粘度、温度和压力进行实验设计(DOE)分析
黄广强—工程部02.11.15
确定了温度和压力限值,安装了限值控制器,控制图显示过程受控CPK=1.85
过程功能
要求
潜在的
失效模式
潜在的
失效后果
严重程度数
S
级别
潜在失效的起因/机理
频度数
O
现行预防设计控制
现行探测设计控制
不可探测度数
D
风险顺序数
R.P.N
建议措施
责任及目标完成日期
措施结果
采取的措施
严重度数
频度数
不可探测度数
风险顺序数
R.P.N
车门内部人工涂蜡
为覆盖车门内侧,车门下层表面涂以最小厚度的蜡,以延缓腐蚀
潜在的失效模式及后果分析-PFMEA
(过程FMEA)FMEA编号:1450
项目名称:左前门/H8HX-000-X过程责任部门:车身工程部页码:共页第页
车型年/车辆类型:199X/狮牌4门/旅行车关键日期:9X.08.26编制:李富荣-技术部
主要参加人:CFT小组FMEA日期(编制):9X.05.17(修订)9X.11.06
7
1
7
49