生产线_异常工时明细纪录表_柏拉图分析
车间不良统计分析图__柏拉图(例)

不良数量
不良数量(根/批次)
4102 35
8
8
8
20
7
6
4
8
8
7
6
4
4
3
32
0
0
A
A
B
C
D
E
F
G
H
B
C
不D良现象
E
F
G
数量 (根/批次)
不良项
累计百分比(%)
从上述统计分析可以看出,目前车间产品质量损失主要集中在封口工序上,表现为封口处钢丝头外露
环与管口边缘不良,给产品造成潜在的质量隐患。那么根据80/20法则,接下来我们要用80%的精力来解
4
3
2
5.48 93.15
4.11 97.26
2.74 100
36
35
12302
车间产柏品拉图不良统计分析图
87.67
93.15
97.26
10208
79.45
93.15
97.26
69.87
87.67
24
79.45
80 58.91 69.87
20
58.91
60
47.95
16
47.95
100
数量 累计百分比(
问题。
制表:李 坤 日 期:2011/ 11/17
合计 73 100
累计百分比(%)
97.26
100 100
90
100
80
70
60
数量 (根/批50次) 累计百分比(%)
40
30
20
2
10
0
H
现为封口处钢丝头外露及封口 们要用80%的精力来解决前两项
完备的不良分析统计图表(柏拉图模版哦)

0 0.00% 53 0.21%
0 0.00% 82 0.29% 20 0.17% 40 0.22% 12 0.09% 207 0.18% 41 0.16%
0 0.00% 99 0.34% 25 0.37% 169 0.87% 13 0.11% 347 0.32%
0 0.00% 0 0.00% 97 0.33% 22 0.11% 119 0.13% 0 0.00% 0 0.00% 43 0.15% 0 0.00% 55 0.25% 0 0.00% 98 0.10% 0 0.00% 127 0.50% 0 0.00% 114 0.60% 15 0.28% 256 0.34% 18 1.30% 2 0.01% 152 0.53% 2 0.02% 46 0.22% 8 0.10% 228 0.27% 56 0.39% 8 0.07% 139 0.46% 0 0.00% 61 0.29% 20 0.20% 284 0.29% 9 0.06% 42 0.33% 0 0.00% 10 0.11% 113 0.59% 45 0.64% 219 0.31% 0 0.00% 0 0.00% 0 0.00% 2 0.02% 32 0.16% 0 0.00% 0 0.00% 34 0.05% 0 0.00% 0 0.00% 2 0.02% 32 0.16% 11 0.07% 45 0.06% 0 0.00%
0 2051
170 658 223 396
0 1447
0 123 1058 343 544
0 2068 1851
91 1645
186 481
0 4254 2026
138 119 178 449
0 2910
334 71
143 133 371
工时异常原因分析与改善表
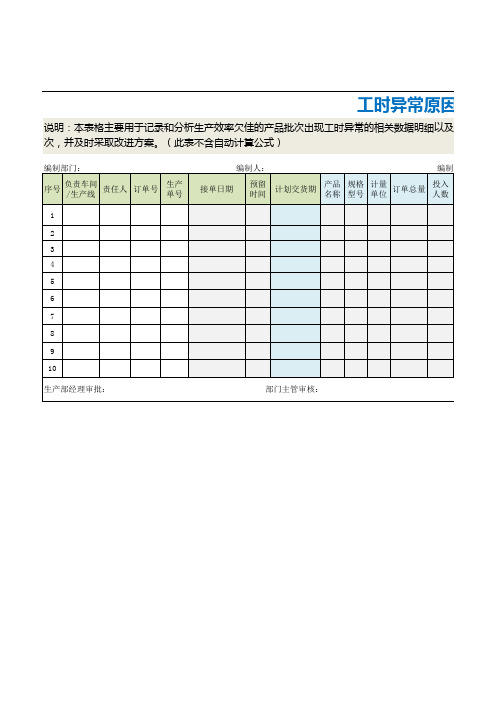
常原因分析与改善表
据明细以及具体原因,并提出相应的改进措施。可以帮助生产管理者集中性的分析生产效率偏低的产品批
编制日期: 标准 标准工时 所需天 实际交货日期 日产能 (H) 数 挡产 实际使用 生产效率 超用工时 时间 工时 超期 天数 差异率
制表:
产效率偏低的产品批原因分析改进措施备注工时异常原因分析与
说明:本表格主要用于记录和分析生产效率欠佳的产品批次出现工时异常的相关数据明细以及具体原因, 次,并及时采取改进方案。(此表不含自动计算公式)
编制部门: 序号 1 2 3 4 5 6 7 8 9 10 生产部经理审批: 部门主管审核: 制表: 负责车间 生产 责任人 订单号 /生产线 单号 接单日期 编制人: 预留 时间 计划交货期 编制日期: 产品 规格 计量 投入 订单总量 名称 型号 单位 人数
生产线异常管理规范(含表格)
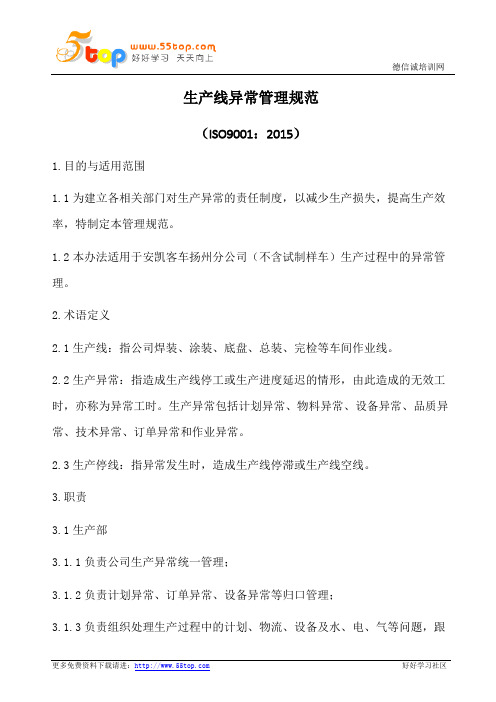
生产线异常管理规范(ISO9001:2015)1.目的与适用范围1.1为建立各相关部门对生产异常的责任制度,以减少生产损失,提高生产效率,特制定本管理规范。
1.2本办法适用于安凯客车扬州分公司(不含试制样车)生产过程中的异常管理。
2.术语定义2.1生产线:指公司焊装、涂装、底盘、总装、完检等车间作业线。
2.2生产异常:指造成生产线停工或生产进度延迟的情形,由此造成的无效工时,亦称为异常工时。
生产异常包括计划异常、物料异常、设备异常、品质异常、技术异常、订单异常和作业异常。
2.3生产停线:指异常发生时,造成生产线停滞或生产线空线。
3.职责3.1生产部3.1.1负责公司生产异常统一管理;3.1.2负责计划异常、订单异常、设备异常等归口管理;3.1.3负责组织处理生产过程中的计划、物流、设备及水、电、气等问题,跟踪闭环3.1.4负责生产、设备等异常责任单位的判定;3.1.5负责异常归口管理单位处理异常,跟踪闭环的责任判定和考核。
3.2技术部3.2.1负责公司技术异常归口管理;3.2.2负责组织处理生产过程中的设计、切换、试装和工艺等问题,跟踪闭环;3.2.3负责技术异常责任单位判定;3.2.4负责及时审核处理异常申报。
3.3质保部3.3.1负责公司品质异常归口管理;3.3.2负责组织处理外购件质量和生产过程检验以及检验信息录入等问题,跟踪闭环。
3.3.3负责品质异常责任单位判定;3.3.4负责及时审核处理异常申报。
3.4采购部3.4.1负责公司物料异常归口管理;3.4.2负责组织处理满足质量要求的物料到位及时性、未与车间办理量产交接等,跟踪闭环;3.4.3负责物料异常责任单位判定;3.4.4负责及时审核处理异常申报;3.5采购部(仓库)3.5.1负责公司常规物料及库管件配送物料(含直送工位件)异常归口管理;3.5.2负责组织处理满足质量要求的常规件(含直送工位件)到位及时性、在原图号进行尺寸和性能提升修改的物料(含直送工位件)未及时到货问题,跟踪闭环;3.5.3负责组织处理库管件配送物料异常、送料维护、及时报缺和首件送检等问题,跟踪闭环;3.5.4负责常规物料及库管件配送物料异常责任单位判定;3.5.5负责及时审核处理异常申报。
生产进度异常分析表(生产线)
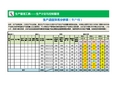
计划实际计划实际计划实际计划80002015/12/20150028000.14001040038040039040040040050012015/12/14150128000.14001040032040039040040040050022015/12/151********.14001040032040041040040040050032015/12/16150328000.14001040032040039040040040050042015/12/17150428000.14001040032040039040040040050052015/12/181********.14001040032040040540040040050062015/12/19150628000.14001040032040039040040040050072015/12/20150728000.1400104003204003904004004004302812028224000.83200803200262032003155320032003200 生产管理工具——生产计划与控制管理12月7日说明:生产进度控制,又称生产作业控制,是在生产计划执行过程中对产品生产的数量和期限的控制。
本表格主要用于统计分析每个星期内各车间或生产进度出现异常现象的产品数量以及主要原因,可以帮助生产管理者定期排查影响生产进度的主要因素,及时进行问题分析并提出改进方案。
(内含自动计算公式,数据为模拟数据,计划与实际出现差异的数据皆设置了自动函数突出显示提醒使用者,包括低于计划的生产数量、交货延迟天数等提醒)生产进度异常分析表(生产线)星期三12月9日生产线本月任务总量编制部门: 编制人: 周期: 编制日期:星期一规格型号本周计划生产数量星期二12月8日星期四12月10日序号车间生产单号接单日期合计标准日产能人员标准配置计划交货期产品编号产品名称本月内已完成数量标准工时(H)生产线生产线2生产线3生产线4生产线5其它461682782版权所有:北京未名潮管理顾问有限公司总经理审批: 生产部门经理: 制表:2.08%生产线2生产线1比例47.92%16.67%8.33%16.67%8.33%46168162800合计原因5(工时数)其它生产线832121生产线7921211生产线6721210生产线5521211生产线4421210生产线352121异常原因原因2(工时数)原因3(工时数)原因4(工时数)7原因1(工时数)212主要异常原因分析:改进措施:62120110等提醒)制表: 2.08%96159200其它合计13121210121310100046 16 8 27 8 2 0 5 10 15 20 25 30 35 40 45 50 生产线1生产线2生产线3生产线4生产线5其它。
异常工时统计表
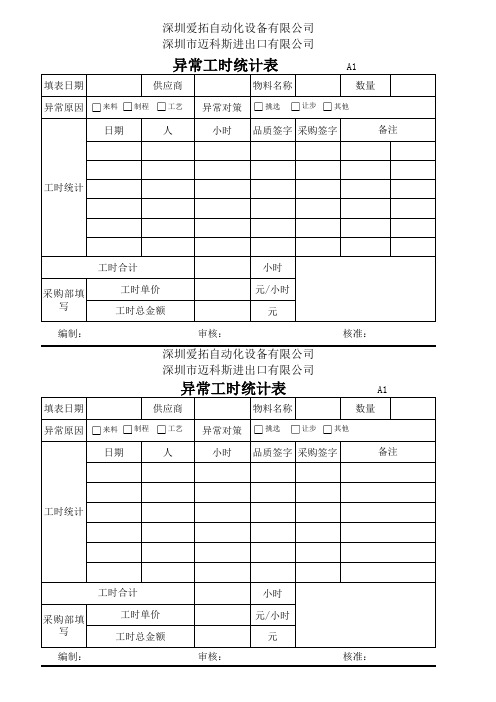
异常工时统计表
填表日期 异常原因
来料 制程
A1 数量
让步 其他
供应商
工艺
物料名称采购签字
备注
工时统计
工时合计 采购部填 写 编制: 工时单价 工时总金额 审核:
小时 元/小时 元 核准:
深圳爱拓自动化设备有限公司 深圳市迈科斯进出口有限公司
异常工时统计表
填表日期 异常原因
来料 制程
A1 数量
让步 其他
供应商
工艺
物料名称 异常对策 小时
挑选
日期
人
品质签字 采购签字
备注
工时统计
工时合计 采购部填 写 编制: 工时单价 工时总金额 审核:
小时 元/小时 元 核准:
深圳爱拓自动化设备有限公司 深圳市迈科斯进出口有限公司
异常工时浪费统计分析图表范例

货/排产需求,重新刷固件;(合计
1
8
50台)
8
销售部50% PMC部50%
PMC部; 4; 1%
合计
253
销售部; 4; 2%
供应商; 245; 97%
1
2
2
供应商
1
1.5
1.5
供应商
1
ห้องสมุดไป่ตู้65
1
48
1
2
1
26
1
35
2
3
1
4
2
5
1
8
1
15
65
供应商
48
供应商
2
供应商
26
供应商
35
供应商
6
供应商
4
供应商
10
供应商
8
供应商
15
供应商
FQC
重新刷固件;
工时浪费 问题点分
责任部门
供应商
PMC部
销售部
合计
浪费工时(H) 245 4 4 253
销售订单与实物固件不一致,满足出
来源 IQC IQC IQC IQC
IQC
IQC
IQC
IQC IQC IQC IQC IQC IQC IQC IQC IQC
XX月份-异常工时浪费-品质部
机型/物料名称
异常描述
加热铝板(华尔康) 孔径偏大,线路反,变形;
0.4喷嘴(几维鸟) 孔径偏小,堵孔; USB转接线B(建军) 万用表测试导通
异常原因 供应商来料问题; 供应商来料问题; 供应商来料问题;
供应商来料问题;
无法调
线材 (深海盛)
线序反,端子坏,端子脱落
车间每日生产异常信息反馈表(2月20日更新)

12013.01.30410A抽屉座料上错(应为有铆钉的,而实际上的是没铆钉的),导致180个抽屉需重做.做好的抽屉用薄膜包好留着以后消化(改为无铆钉后),重做抽屉使用.22013.01.30缺330C金属铰链(实际中午货已到,但物控及物料员均未知晓到货信息,直到下午3:30才领出).换线做其他产品的准备工作32013.01.30330C塑料压脚硬度太硬(昊晟生产),导致装配困难,需要费较大力气才能装入(之前的较软所以好装)、效率低、员工劳动强度增大.已经注塑出来的由产线员工克服生产,并适当进行人员轮换装配.42013.01.30330C压脚拉簧不良率较高(1500个里面有110个不良品,不良率7.3%),不良现象:两端的挂孔不在同一平面上、还有一部分严重变形.产线挑选使用,本批全部生产完毕由产线统计挑选工时提供给采购,由采购将工时费用转稼给供应商.52013.01.31410一体横梁装压脚的卷孔偏小,导致钢丝压脚装入后过紧,转动不灵活(批量性).经技术质量部评估后让步使用,余下的2880个横梁由技术质量部做好检具后确认是否需整形.62013.01.31360钱箱没缝隙、撞前框、锁不牢在线维修、增加人员检测、延长加班时间至23点(需出货).72013.01.31410T钱箱打不开(与360同一条产线生产)锁架整形、在线维修、延长加班时间至23点(需出货).82013.02.01330E铁芯在运行过程中与接杆卡滞,导致回复不顺畅.将连杆角度扳至小于90度92013.02.01330C电磁铁电控击打后,锁片不能通过拉簧自动复位或回复缓慢.将不良铁芯拆下(端部锥度大的),换上端部锥度小的铁芯生产.102013.02.02330C底板有压印(同一部位),数量100块.经技术质量部评估后确认可以让步使用(Ⅲ级标准产品)112013.02.02缺防冻滑轮(低温脂滑轮)临时用普通滑轮代替生产(放到缝纫机油中浸泡后再擦拭使用)122013.02.18供应商提供的4芯及6芯话机插包装数量太大(500个/包,造成数量清点繁琐),且包装凌乱(导致有些芯线头端被挤弯,焊线前需手工整直).产线增加数量清点频率,芯线头端被挤弯的在焊线前先采用手工整直.132013.02.18400D钱箱出不足的问题一直存在,且异常比率均在90%以上,对生产效率影响很大.先将滑轨从罩壳上取下,并将滑轨上原有的油擦掉,然后再加上缝纫机油以后将抽屉反复抽拉磨滑轨.。
工程不良分析(柏拉图-鱼骨图)

作成
年 月份工程不良统计分析(例)
图表一
不良项目 不良次数 不良比率 (%)
冲击
6 40.00% 40.00%
MFR
3 20.00% 60.00%
屈服 2 13.33% 73.33%
灰份 2 13.33% 86.67%
阻燃 2 13.33% 100.00%
合计 15 100.00%
累计不良比率(%)
0.00%
0.00%
0.00%
0.00%
0.00%
0.00%
冲击
阻燃
弯曲
不良次数
屈服
不良累计
灰份
不良比率
MFR
结论:
月份工程不良类别统计图 20 18 16 14 12 10 8 6 4 2 0
100.00% 86.67% 73.33% 60.00%
40.00%
100.00% 90.00% 80.00% 70.00% 60.00% 50.00% 40.00% 30.00% 20.00% 10.00% 0.00%
冲击
不良项目 不良次数 不良比率 (%)
#DIV/0! #DIV/0! #DIV/0! #DIV/0! #DIV/0! #DIV/0! #DIV/0! #DIV/0! #DIV/0! #DIV/0! #DIV/0! #DIV/0!
冲击
阻燃
弯曲
屈服
灰份
MFR
合计 0 100.00%
累计不良比率(%)
----月份工程不良类别统计图 20 18 16 14 12 10 8 6 4 2 0 100.00% 90.00% 80.00% 70.00% 60.00% 50.00% 40.00% 30.00% 20.00% 10.00% 0.00%
- 1、下载文档前请自行甄别文档内容的完整性,平台不提供额外的编辑、内容补充、找答案等附加服务。
- 2、"仅部分预览"的文档,不可在线预览部分如存在完整性等问题,可反馈申请退款(可完整预览的文档不适用该条件!)。
- 3、如文档侵犯您的权益,请联系客服反馈,我们会尽快为您处理(人工客服工作时间:9:00-18:30)。
200 190 180 170 160 150 140 130 120 110 100 90 80 70 60 50 40 30 20 10 0
0 累計不良占有率
39.0% 66.2% 86.1% 100.0%
(材)-材料異常
異常時間
日期
上線機種
問題
異常工時明細
(排)-排 (停)-停 (教)教 (掃)-掃 (新)-新 (搭)-搭 (E)- (試)-試 (測)測 (N (準)-上 (會)-會 (作)-作 (出)-人 程異動 電 育訓練 除 人作業 配異常 ECN/R 產 試NG )NOT 線準備 議 業落後 力調出 D 處理 ES
0 0 0.0%
0 0 0.0%
0 0 0.0%
0 0 0.0%
0 0 0.0%
2 115 27.2%
0 0 0.0%
0 0 0.0%
1 84 19.9%
0 0 0.0%
0 0 0.0%
3 59 13.9%
0 0 0.0%
0 0 0.0%
115
84 59
0
00
00
00
2
00
00
1
00
00
3
00
00
00
3
00
பைடு நூலகம்
00
00
00
異常點內容分析 生產期間 總工時 異常工 異常率 (材)- (搭)- (測)測 時 (會)材料異 搭配異 試NG處 會議 常 常 理
10220
423
16.7%
165
115
84
59
單項異常率 1.61%
1.13%
0.82%
0.58%
不良占有率 39.01% 27.19% 19.86% 13.95%
異常工時
異常點 (換)換 (加)-加 (設)-設 (組)-組 (修)-修 (M)- (品)-品 (缺)-缺 (材)-材 (改)-改 (插)-插 單 線 工不良 備異常 裝不良 改 MES異 質問題 料 料異常 單 常
影響次數 影響工時
0 0
0 0 0.0%
0 0 0.0%
0 0 0.0%
0 0 0.0%
00
00
165
86.1%
115 66.2%
84 39.0%
59
(材)-材料異常
(搭)-搭配異常
(測)測試NG處理
(會)-會議
問題
異常分類
分析
暫時處理方式
(假)人 (發)-發 (備)備 員請假 錯料 料作業 TOTAL
0 0 0.0%
0 0 0.0%
0 0 0.0%
9 423
影響次數 影響工時 占異常工時比例
0 0 0.0%
0 0 0.0%
0 0 0.0%
3 165 39.0%
0 0 0.0%
0 0 0.0%
占異常工時比例 0.0%
工單數 總投入工時 總異常工時 占工時比例
180 160 140 120 100 80 60 40 20 0
61 10220 423 4%
165
00
00
00
00
00
00
00
00
00
100.0%
100.0% 90.0%
80.0% 70.0% 60.0% 50.0% 40.0%
59
30.0% 20.0% 10.0% 0.0%
0.0% 會)-會議
暫時處理方式