螺纹钢切分轧制有限元分析
Φ16mm螺纹钢筋三切分轧制技术应用分析

q 5 mm× 一 穿水 冷一 2号 飞 剪一 精 轧  ̄30 m× b 0 3 2 5m 6 穿 水冷一 3号倍 尺 飞 剪一 步 进 齿 条 式 冷 床一 冷 一 飞剪一 检验一 收 集一 打包一 入库 。
收 稿 日期 :0 1 0 2 2 1 — 2 5 作 者 简 介 : 玉坤 ( 9 1 , , 西 萍 乡人 , 理工 程 师 , 事 技 术 开 发 管 理 工 作 。 张 18 一) 女 江 助 从
K e o d  ̄ 1 mm ;ib d b ;he l ;ol g y W r s: 6 r e a tresi rln b r t i
式 轧机 ,1~1 轧 机 为短 应 力 线轧 机 。粗 轧 6道 1 8号
1 工 艺概 况
江西萍 钢实 业股 份有 限公 司二 轧钢 厂棒 材生 产 线于 20 0 3年 6月 动 工 兴建 ,0 4年 8月建 成 投 产 。 20 20 0 9年 4月 , 轧 制  ̄1 m 螺 纹 钢 筋 进 行 了相 关 对 6m
智 能控 制 , 机 和电机均 为 国产 , 轧 末机 架最 高速 率 为
1.m s 8 5 / 。坯 料 规 格 为 1 0 7 mm ×10 m ×9 0 m 7m 0 0 m,
技术 改造 , 将原 来 的二 切分 轧 制 技 术 改造 成 三切 分 轧制技 术 , 实现 了提 高产 量 、 降低 生 产成 本 和节 能减
张 玉坤 。 刘建 萍
( 江西 萍 钢 实 业 股 份 有 限公 司 , 江西 萍 乡 371 ) 30 9
摘
要 : 为提高产量、 降低生产成本和实现节能减排 , 萍钢通过技术改造, 1m 将 6 m螺纹钢筋由原来的二切分
轧制改造成三切分轧制 , 取得 了较好 的经济效益 。
Φ12mm螺纹钢四切分轧制工艺优化

钢等 ,平均每班故 障时间 4 0 m i n 左右 ,严重地
制 约 了生产 的正 常进行 。为此 ,展开 攻关 ,实 施
Te mp e r a t u r e
1 2 mm Re i n f o r c e d B a r ; Ro l l i n g ; F o u r - s t r a n d S p l i t t i n g ; P r o i f l e ; P a s s ; G u i d e ;
陆文韬等 : l 2 m I I l 螺纹钢 四切分轧制工艺优化
停 机 必 须 检查 K 2孔 型 的磨 损 情 况 ,发 现 缺 陷 , 及 时 换 孔 ;修 改 K 3出 口导 卫 双 刃 切 分 轮 角度 ,
( 3 )轧辊 、导卫方面。轧辊 4线磨损不均 造成后续机架堆钢 ,崩孔引起堆钢 ,K 2 磨损造
LU we n t a o ZHANG Bi n b i n
( B a r a n d S e c t i o n P l a n t )
Ab s t r ac t : The b r a i n s t o r m c o u n t e r me a s u r e s i mpl e me n t e d f o r t he f o u r - s t r a n d s pl i t t i n g r o l l i ng p r o c e s s f o r
中1 2 mm r e i n f o r c e d b a r p r o d u c t i o n w e r e i n t r o d u c e d i n r e s p e c t s o f p r o i f l e o p t i mi z a t i o n , g u i d e i mp r o v e me n t , r o l l e r p a s s r e f o r ma t i o n a n d t e mp e r a t u r e c e n c e t h e r e a c h a b i l i t y o f d e s i g n c a p a c i t y w a s >9 0 %, t h e r o l l i n g s c r a p r a t e w a s r e d u c e d t o 0 . 0 8 % a n d t h e r o l l i n g y i e l d wa s 1 0 3 . 1 %. Ke y W o r d s :
Ф10mm螺纹钢的五切分轧制新工艺开发

Ф10mm螺纹钢的五切分轧制新工艺开发文章简述五切分轧制工艺情况,结合萍钢公司轧厂高棒车间Ф10mm螺纹钢筋五切分轧制的生产实践,分析五切分轧制工艺在生产中遇到的主要问题及解决方案。
标签:五切分;轧制;工艺1 公司轧厂五切分工艺发展简述萍钢公司轧厂高棒车间先后开发了Ф16mm、Ф18mm、Ф20mm三种规格的二切分轧制工艺,进而开发了Ф14mm的三切分轧制工艺,在此基础上又开发了Ф12mm的四切分轧制工艺。
公司轧钢厂本着永不停步的精神,在四切分生产工艺成熟稳定的基础上,又向Ф10mm五切分轧制工艺这一世界先行技术进行探索,经过一段时期的工艺探索和生产实践,五切分轧制生产逐步稳定,工艺日趋成熟。
目前公司轧厂Ф10mm五切分最高班产达到950吨,最高日产超过2700吨。
2 车间工艺布置萍钢公司轧钢厂棒材车间于2003年6月动工兴建,2004年8月建成投产。
采用全连续式平立交替无扭轧制,控轧、控冷等先进工艺,自动化程度高。
设计轧制坯料为规格为170×170×9000mm,可生产规格为Φ10~Φ32mm螺纹钢及圆钢,年设计生产能力为80万吨。
高棒车间生产工艺流程坯料验收→排钢→加热→出钢→出磷→粗轧→1#飞剪→中轧→预水冷→2#飞剪→精轧→穿水冷→倍尺减切→上冷床→定尺冷切→收集→打包→检验→称量→入库3 Ф10mm螺纹钢筋五切分工艺简述3.1 精轧孔型图(图1)3.2 中轧来料为平椭料型,精轧15~18#机架采用水平布置。
13#机架为平棍,14#机架料型为矩形,15#机架为预切分机架,16#机架为切分机架,17#、18#机架轧制与常规机架相同。
公司轧厂五切分轧制采用切分轮法,其中16#机架为整个五切分轧制工艺控制的核心,切分辊将轧件切分成五根并联的由很薄连接带连成的轧件,切分导卫中的前后两排切分轮先后将轧件撕开,切分刀片将轧件完全切开后通过导槽将五根轧件分开导出,实现了五切分。
4 Ф10mm螺纹钢筋五切分生产中遇到的问题及改进措施自2007年5月份试轧五切分以来,在实际生产中主要遇到了如下一些问题:(1)精轧16#出口导卫冲钢工艺故障;(2)精轧18#出口导卫冲跑钢工艺故障;(3)轧制五线差不稳定;(4)上冷床湾钢。
二切分轧钢生产

切分轧制生产实践摘要:本文对轧厂切分轧制技术做了总结,对生产操作中孔型设计、导卫装置等做了详细分析,为提高产品的成材率及各种规格质量进行了深入探讨。
关键词:螺纹钢生产;二切分;轧制技术要求1 前言轧钢厂2002年引进的小型棒材轧机,对Ф12、Φ14、Φ16mm三种规格带肋钢筋采用二切分轧制,轧机小时产量达到70t,接近其它规格平均85t的水平,且与其它产品共用150mm方连铸坯,经Ф500×1/Ф400×2/Ф350×4/Ф300×6十三架轧机15道次轧出成品。
粗轧和中轧道次孔型具有共用性,缩短更换规格停机时间,提高了轧机作业率。
目前,轧厂φ16mm以下规格的建筑用带肋钢筋都采用切分工艺轧制,既保证了轧制小规格具备的条件,又保证了产品质量和产量,更好地满足市场的要求,取得了明显的经济效益。
2切分轧制技术特点切分轧制是国家推广的新技术,也是今后发展方向。
据不完全统计,在小型棒材的产品中,直径小于φ16mm规格的钢筋约占总量的60%。
而棒材生产率随产品直径的减小而降低,因此要使各种规格产品的生产率基本相等,必须采用切分轧制,从而导致了棒材切分轧制技术的广泛应用。
切分轧制的技术关键在于切分设备的可靠性、孔型设计的合理性、切分后轧件形状的正确性以及产品质量的稳定性。
切分轧制具有以下明显的技术特点:2.1 均衡不同规格产品的生产能力使现有加热炉、轧机、冷床及其它辅助设备的生产能力有效利用和充分发挥。
因此,减少了厂房面积,减少了设备投资。
2.2 大幅度提高轧制小规格产品的机时产量采用切分轧制由于缩短了轧件长度,从而缩短了轧制周期,提高了轧机生产率。
2.3 节约能源、降低成本采用切分轧制变形量小,电机负荷分配均衡,电机效率趋于最佳状态,电量消耗趋于最低。
节约大量能源,且由于轧制成品长度减短,钢坯的出炉温度可适当降低。
但切分轧制也存在一些问题,主要表现在:棒材切分带容易产生毛刺,如调整不当有可能形成折叠,影响产品质量;对坯料的质量要求较严格,切分后坯料中心部位的缩孔、疏松等易暴露在轧件表面;对导卫、切分装置精度要求很高,在操作上应调整好进、出口导卫及切分轮间距,确保轧件对称地切分。
Ф12mm螺纹钢三切分轧制工艺开发与应用

摘 要 : 钢 公 司 在 中 、 轧 水平 轧 机 上 开 发 中 1 螺 纹 钢 三 切 分 轧 制 , 过 设 备 改 进 及 工 艺 优 化 , 宣 精 2mm 通 解 决 了折 叠 、 线 尺 寸 控 制 不 稳 定 、 三 切偏 头 等 问题 , 均 日产 量 比 原 来 的 双 线 切 分 轧 制 提 高 1 % 。在 产 量 平 9 增 加 的 同时 , 钢 电 耗 、 气 单 耗 均 有 一 定 程 度 降 低 , 品 速 度 由双 线 切 分 的 1 / 吨 煤 成 5m s降低 至 1 / , 3m s实
大冷 坯加热 能 力 1 0th 4 / 。全 线 共 有 1 8架 轧 机 , 其 中, 轧机 组 由 粗 4 0 mm × 5 2高 刚 度 闭 口式 轧 机组 成 , 4架 5 0 8 mm 轧 机平 立交替 布置 , 2架 4 0 mm 轧机 水平 布 5 置; 中轧机组 由 4 0mm × 3 6高刚度 闭 口式 轧机 组 成 , 水平 布置 。精轧 机组 由 3 0mm × 全 2 6短应 力 线轧 机组成 , 水平 布置 。冷床 为步进 齿条 式 , 全 尺寸 为 8 n×8 9i , 1I . n 冷剪 机为 6 0 t 5 固定剪 。
( e t n Se lR ln Mi ,Xu n u rn a d Se lC mp n S ci te ol l o i l a h aIo n te o a y,He e rn a d Se lGru b iIo n te o p,Xu n u ,He aha —
i s ng orz ntl olig fnihi h i o a r ln m il i Xua Ste . W i ls n n e1 t mpr v m e t f qupm e t a d p i ia in f h i o e n o e i n s n o tm z to o
敬业集团轧钢厂(一、二车间)概况
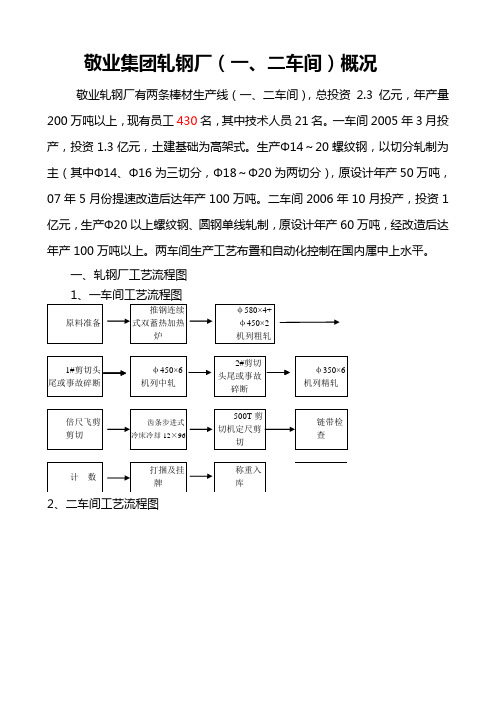
敬业集团轧钢厂(一、二车间)概况敬业轧钢厂有两条棒材生产线(一、二车间),总投资2.3亿元,年产量200万吨以上,现有员工430名,其中技术人员21名。
一车间2005年3月投产,投资1.3亿元,土建基础为高架式。
生产Φ14~20螺纹钢,以切分轧制为主(其中Φ14、Φ16为三切分,Φ18~Φ20为两切分),原设计年产50万吨,07年5月份提速改造后达年产100万吨。
二车间2006年10月投产,投资1亿元,生产Φ20以上螺纹钢、圆钢单线轧制,原设计年产60万吨,经改造后达年产100万吨以上。
两车间生产工艺布置和自动化控制在国内属中上水平。
一、轧钢厂工艺流程图2、二车间工艺流程图二、轧线主要工艺设备及性能:1、两车间加热炉均为端进侧出蓄热式加热炉,一车间加热炉有效尺寸为21 m ×10.6 m ,加热能力120t /h (冷坯),二车间加热炉有效尺寸为29m ×10.6 m ,加热能力150t /h (冷坯)。
燃料是本集团炼铁厂供应的副产品高炉煤气,坯料为150方×10米,由本集团炼钢厂热送。
蓄热式加热和钢坯热送热装两项技术在提高加热质量的同时,又具有显著的经济、节能、减排、环保特色。
2、主轧机:一车间轧机共18架,二车间轧机共16架,均为全平立交替布置。
两车间粗中轧轧机均为Ф580×4+Ф450×8二辊闭口式轧机,一车间精轧机为Ф350×6短应力线轧机,设有5个立活套,二车间精轧机为Ф350×4短应力线轧机,设有3个立活套。
平立交替和活套可实现无扭无张轧制。
3、飞剪:一车间共3台飞剪,1#剪、2#剪分别位于粗、中轧机组之后,用以切头尾或事故碎断,3#剪是倍尺飞剪,位于精轧机组之后;二车间共2台飞剪,1#剪位于粗轧8架之后,用以切头尾或事故碎断,2#剪是倍尺飞剪,位于精轧机组之后4、精整系统由冷床系统、冷剪定尺系统、分捡打捆包装系统及称重标识系统组成。
φ14mm螺纹钢切分工艺设计与轧制

降低成本 ,决定采用切分轧制技术。据有关资料介 绍 ,切分轧制与单线轧制相比 ,可提高生产率3% 0
以 上 ,降 低 燃 耗 5 6% , 电耗 l%- 0 ,辊 耗 %- 5 -% 2
(1 座 j段连续7t 5h /
l%,上述因素可使单位产品成本降低1o- 0 5 0o2 %, /- '
.
til ln l c o dn l ov d tep e s lni rv d tepei n r rd cn a a i r d r ‘ l gwf a c rigys le ,h me s a o c ,h rl ar i o s p mp miayp o u igc p cI f me yo
(邯郸钢 铁公司 四轧钢厂 ,河北 邮郸 0 6 1 5 0 5) 摘 要 :介绍 了邯 钢四轧棒材 连轧机组根据本厂 的 艺特点 ,采用 双线 切分轧制 中 1rm螺纹 钢的 I艺设 4 a : 计 案。对试轧过程中 出现 的一 系列 题进行 了针 对性 的解决 ,使 【 艺 案得到完善 ,初步形成 f产能
维普资讯
总 幕 I7 2 期 20 年 幂 I 02 期
河 北 墙4- -
HEBE1M E TALLURGY
TO a l ll 27
2 02, N a e 0 mb r
1 rm螺 纹 钢 切 分 工 艺设 计 与 轧 制 4 a
贯 硕 磊
近 几 年 ,用 切 分 轧 制 l艺 生 产 中 lr ~ 线 切分经 过五 次轧制 , l 已 日趋 正常 .可 以转 入 : 4m a : 艺 0 1 01 中 lrm螺 纹钢 在我 国普 遍 受 到重 视 ,并将 其 视 为 生产 。20 年 l) 进 行 了 首 次批 量生 产。 本 文对 6 a
我厂二切分轧制生产实践

我厂二切分轧制生产实践陈爱平卢平安钟海清杨世平何水金(新余钢铁有限责任公司棒材厂江西新余338001)摘要:本文主要介绍了我厂切分轧制工艺生产的过程及生产过程中出现的一些问题和改进效果。
关键词:二切分,轧制,生产,问题,改进效果1 前言新余钢铁有限责任公司棒材厂是一条年设计能力为40万吨的棒材半连续生产线,它是在利用现行可靠工艺技术和生产设备设施的基础上建成投产的。
原料:124方、130方、150方主要产品规格:螺纹钢:Φ12—36园钢:Φ16--Φ36其中:Φ12- Φ14螺纹钢轧制总量占20%左右。
由于Φ12- Φ14若单线生产产量太低,能耗高,机架数目多,场地受限,而采用切分轧制,产量可提高至少50%,且能耗低,机架数量少,因而决定Φ12- Φ14采用二切分轧制。
2 切分轧制工艺概述2.1 设备简介我厂是一条半连轧生产线,全线共布置13架水平轧机。
其中粗轧是一架530三辊开坯机,中轧为6架Φ400×4+Φ350×2闭式水平轧机,精轧为6架Φ300×6闭式水平轧机,K7-K2间均设立式活套,K1,K2间不起套。
Φ12,Φ14切分轧制均不甩机架,采用切分轮法。
精轧孔型使用如下:K6为菱形孔,K5为弧边方孔,K4为哑铃预切孔型,K2为椭圆孔,K1为成品孔。
2.2工艺平面布置图3 切分轧轧制生产情况3.1 生产准备3.1.1 车削预切分孔,切分孔轧辊车削精度要高,成品孔,成品前孔轧槽配辊两线间的中心距要保证。
3.1.2 导卫1)导卫安装首先要求检查导卫备件的质量,尺寸公差,表面质量是否符合工艺要求,禁止不合格品进行安装,导卫的开口度每架次用专用样棒进行安装与检测,确保导卫安装质量,即导卫的内腔尺寸,导轮的开口度尺寸符合要求。
2)K6出口DU65为带扭转的滚动导卫,K6轧件进K5孔能自动找正,K5进口导轮尺寸不要将K6轧件夹持很紧,K5出口CTR45度扭转。
3)K4轧件的形状控制对切分轧制的顺利很关键,2个亚铃形的面积要基本一样,防止切分不均匀,K4、K3进口为0930B四辊滚动导卫,导轮间距要合适,以防止料形发生扭转,K4出口为滑动导卫,滑动导板的头部一定要与亚铃形孔相吻合。
螺纹钢切分轧制孔型系统探讨

螺纹钢切分轧制孔型系统探讨【摘要】切分轧制孔型系统在轧件加工过程中占有重要的地位。
本文对切分轧制技术进行了简单的介绍,着重探讨和分析了几种常用的切分轧制孔型系统。
【关键词】螺纹钢;切分轧制;孔型系统引言切分轧制技术早在19世纪就已经被用于旧钢轨加工中,但是此后发展比较缓慢。
直到最近几年,切分轧制技术发展才得到了快速的发展,加工技术也更加成熟,在各种型材和棒材的加工中应用十分广泛。
该工艺具有生产率高、能耗和生产成本低等优点,但在也存在切分孔型磨损严重以及产品质量不稳定等问题。
加工企业需要重视切分轧制技术中存在的问题,优化该加工技术。
螺纹钢的切分轧制孔型系统发展也比较迅速,从最初的二切分孔型系统发展为三切分、四切分孔型系统,螺纹钢的加工效率得到了极大的提升。
本文先对切分轧制技术进行介绍,再重点对螺纹钢切分轧制孔型系统进行探讨。
1 切分轧制概述切分轧制就是沿纵线方向将轧件切成两线或多线的技术,它主要通过轧辊孔型、切分轮或其它切分装置实现的。
它的加工原理就是利用孔型系统对初步加工后的坯料加工成并联轧件,然后沿纵向将并联轧件切分为多个独立轧件。
根据加工方法的不同,切分方法主要有切分轮法、辊切法、圆盘剪切分法以及火焰切分法。
根据切分后轧件数量的不同,切分轧制一般可分为两线切分、三线切分以及四线切分等。
切分轧制具有很多优点,主要可以分为以下几点:第一,切分轧制极大的提高了轧件的生产效率,降低了生产成本。
第二,在单一轧件机器上可以实现多种规格轧件的生产,既扩大了生产的产品范围,又减少了原料的种类。
第三,对于加工同样的轧件,切分轧制的变形率要比单线轧制低,产品质量更高。
第四,切分轧制技术适用性高,对于不同的连轧机,主要的工艺设备不需要变更,生产工艺只需要进行局部变动。
第五,切分轧制技术可以降低轧件的初步加工要求,能够减少燃料和电量的消耗,降低环境污染,实现生产节能减排。
但是切分轧制也存在一些缺点,比如切分时对料型要求更严格;切分部位不规则,容易形成毛刺,处理不适当容易形成折叠,影响产品质量。
螺纹钢质量分析

螺纹钢产品质量简要分析提高产品质量对国家是兴国之道,对企业就是效益和竞争力。
轧钢工序深刻认识到作为终端产品的生产单位,对质量的严格管理,对质量意识的增强显得尤为重要。
尤其是目前钢铁企业在生产经营上遇到前所未有的困难,生产节奏放缓的情况下,轧钢工序把加强过程控制,增强职工的质量意识,提高产品质量水平作为严格控制风险、增强市场竞争力,提高企业效益的头等大事来抓。
轧钢工序生产是一个从加热——轧制——精整——成品入库等工艺过程。
每一道工序出现问题都有可能影响到产品质量的提高,为此工序认真分析了影响产品质量的各环节各因素,对每个环节严格控制,做到了有检查、有落实、有考核;对每一起质量缺陷都要组织班组从我做起,进行认真分析原因,制定措施,班组之间进行交流培训教育,提高全员质量意识和职工处理事故的能力;建立和不断完善两条生产线的质量管理体系并保持有效的运行和持续改进,绝大多数质量缺陷都得到了有效的解决,广大职工都能够认识到“质量安全,我们共同的责任”。
针对2008年11月20日夜班28罗纹轧制过程中产生表面结疤缺陷的质量问题,工序特制定以下措施来教育职工提高质量意识,杜绝因轧钢原因产生类似质量缺陷。
具体措施如下:1 、从轧钢生产各个环节入手,不断优化生产工艺。
2、不断完善工艺纪律,从轧钢的红坯尺寸检查入手,加强执行监督管理。
3、完善质量缺陷产生的原因分析和处理办法,组织每位职工学习、培训、现场指导,从源头杜绝可能产生质量缺陷的因素。
4、不断进行轧钢理论培训,每月进行一次成品表面7 种质量缺陷产生原因的培训,提高职工分析解决问题能力。
5、严肃考核制度,对每起质量缺陷都要组织分析和考核,真正意义上增强职工的质量意识。
下面就轧钢成品易出现的质量缺陷分析如下:一、成品缺陷的种类及其措施1、折叠:折叠是指在钢材表面沿轧制方向近似纵裂的缺陷,有一定的倾斜角,一般呈直线状,内附氧化铁皮。
原因分析:1)成品孔前产生耳子、凸起(轧槽磨损或切分导卫磨损)或严重划痕。
螺纹加工有限元分析

螺纹加工的有限元分析ee(ee)指导教师:ee[摘要]传统的螺纹加工方法不仅加工效率低,而且切断了金属材料的纤维流向,严重降低了内螺纹的质量,难以满足生产中对螺纹连接件高精度、高强度的要求,而冷挤压成形是一种无屑加工方法,大大提高了螺纹的抗拉强度和抗疲劳性能。
本文利用DEFORM软件对螺纹加工过程进行了仿真分析,实现了一般挤压攻丝过程和振动挤压攻丝过程的有效模拟。
在一般攻丝过程中,分析了挤压速度对螺纹加工中丝锥所受应力,应变以及扭矩的影响,底孔直径对螺纹加工过程中应力应变以及扭矩的影响。
并且完成了轴向振动攻丝与一般挤压攻丝的比较,发现振动攻丝过程中丝锥所受扭矩、应力、温度明显减小。
[关键词]:内螺纹冷挤压挤压丝锥振动攻丝有限元分析Finite Element Analysis of Thread Processingee(ee )Tutor:ee[Abstract] The traditional thread processing method is not only low the processing efficiency, and cut off the flow of metal materials fiber, seriously reduce the quality of the internal thread, difficult to meet the requirements of the production of threaded connection high-precision, high-intensity, cold extrusion is a scrap processing methods, greatly improved the tensile strength and fatigue resistance of the thread. In this paper, utilize the DEFORM software to achieve simulation analysis of thread processing, achieved effective simulation of the general extrusion process and the extrusion process of vibration. In the process of general tapping, analysis the effect of the extrusion speed for the stress、the strain and the torque to the tap. the effect of the bottom outlet diameter for the stress 、the strain and the torque to the tap, and compare circle vibration tapping with the general squeeze tapping. Found in the process of vibration tapping tap the torque, stress, temperature significantly reduced.[Key words]: internal thread, cold extrusion, extrusion tap, vibration tapping, Finite Element Analysis目录1绪论 (1)1.1 内螺纹冷挤压成形技术概述 (1)1.2 内螺纹的主要加工技术 (1)1.2.1.传统的内螺纹加工技术 (1)1.2.2.内螺纹加工的新技术 (1)1.3 国内外冷挤压技术的研究现状 (2)1.4 本文的研究内容及研究目的 (3)2. 螺纹冷挤压成形工艺 .................... 错误!未定义书签。
螺纹钢四切分轧制工艺优化

螺纹钢四切分轧制工艺优化郑 虎,李 坤,王文辉(唐山钢铁集团有限责任公司二钢轧厂,河北 唐山 063000)摘 要:本文通过研究对四切分轧制工艺的改良,采取如料型优化、导卫改进、轧辊孔型修改、缩小开轧温度控制范围等措施,达到班产提升、成材率提高的目的。
以此来更好地推进我国钢铁行业的进一步发展。
关键词:Φ12mm 螺纹钢筋 ;轧制 ;四切分 ;料型温度中图分类号:TG335 文献标识码:A 文章编号:11-5004(2020)01-0105-2收稿日期:2020-01作者简介:郑虎,男,生于1985年,安徽颍上人,本科,中级工程师,研究方向:炼钢。
在建筑业迅猛发展的今天,钢材需求量剧增,现有的四切分轧制工艺已无法满足市场的紧迫需求。
所谓四切分轧制工艺,首先要将坯料进行加热,制作成扁坯后,再利用孔型系统将其加工成4个断面相同的并联轧件,且这4个断面尺寸要相同。
然而该工艺被推广应用后出现了诸多的弊病,如生产不稳定,班产量波动等问题发生,严重影响到了正常的生产。
为此,本文展开研究,试图找出解决问题瓶颈的策略。
1 精轧堆钢1.1 原因分析温度影响:一棒精轧机由于采取的是水平布置的方式,且高宽比例差异性大,两侧温度相对较低,因此在经过K3机架切分后头部会出现不规则变形现象,进而会造成堆钢事故的发生。
图1 堆钢现场实拍料型问题:精轧预切分、切分道次的压下量所分配的比例一定要保证均衡,否则一棒精轧机孔型槽底及侧壁位置不能充满。
此外,整个精轧机架轧制线调整也非常关键,如果调整不好,很有可能会因此造成堆钢现象的出现。
轧辊、导卫方面:轧辊4线轧槽磨损程度不同,也会造成堆钢现象出现;K2磨损严重,与K1不能匹配也会造成堆钢;K3出口导卫存在问题引起堆钢。
K3切分导卫设计不合理,切分后4线轧件不能顺利穿过出口导槽,总是会刮碰到导轮侧壁,时间一久便会使其头部变形。
1.2 工艺优化温度调整规范化:由于一棒加热炉开轧温度控制范围较大,进一步缩小了控制范围,由1000℃~1100℃缩小至1020℃~1080℃。
Φ12螺纹钢五切分技术浅析

2)双预切孔型系统。精轧 13#轧机孔型,16#轧机为切分孔型,17# 轧机为椭圆孔型,18#轧机为成品孔型。
1)切分位置选择。采用 13#一预切、15#二预切、16#切分的 切分方式,切分后的五线轧件经 17#扭转、18#轧制后,经圆管引 导进入加速 辊 道、飞 剪 剪 切;随 后,经 变 频 辊 道 上 冷 床,完 成 卸钢。
2)切分方式。基本原理:利用 16#出口切分导卫前切分轮 切开成“1+3+1”线并联轧件,然后通过后切分轮把“1+3+1” 线并联轧件,切成“1+1+1+1+1”五根单个轧件模式。 2.2 双预切轧制工艺及孔型系统
基础研究[D].北京:北京科技大学,2017.
172
技术应用
TECHNOLOGY AND MARKET Vol.26,No.3,2019
Φ12螺纹钢五切分技术浅析
南书刚
(安钢集团信阳钢铁有限责任公司 炼轧厂,河南 信阳 464194)
摘 要:通过对 Φ12×5双预切工艺的开发、实施,大大提升了机时产量、质量等各项经济技术指标。 关键词:五切分;双预切;技术改造 doi:10.3969/j.issn.1006-8554.2019.03.096
3)切分孔:变形需稳定,延伸系数在 1.0~1.2。孔型充满 度要好,充满度不好,会导致 16#出口切分导卫的切分刀片因负 荷过大破裂。孔型号 1660。
4)立箱孔:立箱孔型延伸系数应较小,基本无宽展,起到轧 件微调平整规范料形的作用,①12#立箱要保证槽底充满度,料 形规范,确保稳定进入一预切道次。②12#立箱压下量不得过 大,不得产生扭转、料转等现象。③12#、13#、15#、16#孔型样板 及五切孔型图表,对上线轧辊进行逐一核对,确保轧辊孔型正 确。 五切分线差调整
Φ12螺纹钢四切分轧制技术在棒材厂的应用与改进

Φ12螺纹钢四切分轧制技术在棒材厂的应用与改进摘要:本文叙述了棒材厂φ12螺纹钢生产的工艺选择、试轧时出现的问题和工艺改进以及对切分技术的成果分析和切分技术的展望。
关键词:螺纹钢四切分轧制孔型系统导卫1 前言切分轧制是在轧机上利用特殊的轧辊孔型和导卫或者其他切分装置,将原来的一根坯料纵向切成两根以上的轧件,进而轧制多根成品或中间坯的轧制工艺。
采用切分轧制技术可缩短轧制节奏,提高机时产量,显著提高生产效率,降低能耗和成本。
目前棒材φ12mm螺采用三切分轧制工艺,终轧速度为15米/秒,其最高小时产量为57.4支/小时,平均小时产量为50支/小时,平均日产为2380吨/天,与其他规格的平均日产2903—3189吨/天存在较大的差异。
为了更好的发挥切分轧制的经济效益,结合市场对小规格螺纹钢需求量较大的实际,棒材厂决定开展φ12螺纹钢四切分生产工艺改造。
这将大幅度提高小规格产能和生产效率,降低生产成本,提高经济效益。
2 主要设备概况2.1 加热炉加热炉为步进式加热炉,最大加热能力为11Ot/h。
采用钢坯尺寸为150mm ×150mm ×12000mm,重约2075kg。
2.2 轧机一棒轧线上共有20架轧机,粗轧6架550轧机(1-6架)、中轧6架420轧机(7-12架),精轧8架350轧机(7-20架,其中17、18架轧机为平立转换轧机);二棒轧线上共有18架轧机,粗轧6架550轧机(1-6架)、中轧6架420轧机(7-12架),精轧6架350轧机(7-18架),一棒采用平立交替布置,粗、中轧为无扭微张力轧制,精轧采用活套无张力轧制,粗中轧、中精轧之间各有一台飞剪,精轧后设有一台倍尺飞剪。
2.3 冷床冷床为126米齿条步进式冷床,可收集和冷却剪成倍尺的棒材。
2.4 冷剪冷剪剪切能力为850T,可将成排棒材按定尺剪切,剪切范围6~12米。
3 四切分技术的应用与改进四切分轧制,即在轧制过程中通过孔型,将1根轧件轧成具有4个相同形状的并联轧件,再通过切分导卫及孔型将并联轧件沿纵向切分成4个单根轧件。
Ф20mm螺纹钢筋三切分新工艺开发

车辆工程技术87机械电子0 前言螺纹钢筋广泛应用在建筑工程中,为了进一步降低Φ20螺纹钢筋成本、提升产量,安源轧钢厂对高棒生产设备进行论证和改造升级,在不大规模改变高棒现有设备的前提下,对Φ20螺纹钢筋两切分工艺进行工艺设计,经过几次试生产,通过对生产工艺的不断优化,目前安源轧钢厂高棒生产的Φ20螺纹钢三切分产品质量性能符合GB/ T1499.2-2007标准,从而提高了企业的竞争力。
1 工艺装备安源轧钢厂高棒车间于2003年6月动工兴建,2004年8月建成投产。
采用全连续式平立交替无扭轧制、控轧、控冷等先进工艺,自动化程度较高。
2015年2月对加热炉进行改造后,轧制坯料规格为170×170×9800mm,产品生产规格为Φ10~Φ28 mm螺纹钢及圆钢,年设计生产能力为130万吨。
其工艺流程如下:连铸坯料→编组→称重→排钢→加热炉加热→出钢→粗轧6机架轧制(平立交替)→1#飞剪切头→中轧6机架轧制(平立交替)→预水冷→2#飞剪切头尾→精轧→穿水冷→3#飞剪切头及倍尺剪切→冷床冷却→冷飞剪定尺剪切→成品及短尺收集区、检验→挑钢、点数(短尺经鳄鱼剪二次定尺)→打包→称重→挂牌、入库2 开发内容2.1 孔型设计设计思路:粗中轧1-9#轧机、18#成品架次孔型共用现有孔型,并在相应的孔型基础上对料型进行重新分配,确保工艺参数不产生大的变动,11#、12#两架次空过,10#轧机及后续孔型重新设计。
2.2 孔型修改的过程(1)第1次试生产,成品料型出现两边未充满,中间过充满现象,针对这一现象,对15#、16#孔型进行修订,从而使得三线差减小。
(2)针对第1次生产出现的问题对15#、16#孔型进行修订,生产过程中第1线和第3线差还是不能够满足产品国标尺寸的要求,需进行二次修订,其修订的方向是对14#架的孔型进行适当的修订,同时对15#架次的孔型进行微调。
(3)通过修订第2次孔型后,精轧部分的孔型基本能够满足该规格生产的国标要求,但是生产过程中可调整的工艺范围不合理,根据生产的实际情况,同时结合其他规格产品的生产情况,修订孔型(10#孔型由B10-15B10-02,增加11#孔型B11-14),通过此次调整后进行第3次生产,生产出来的产品各项工艺指标均满足国标要求,可以进行批量生产。
螺纹钢14四切分问题汇总

螺纹钢?14四切分经验总结螺纹钢?14四切分工艺难度大,在开发阶段精轧机组跑钢频繁,现将开发过程中遇到的问题以及解决方案整理如下:一、存在问题:17#冲出口(架次K3)原因:1、K3、K4料型不规范,K3、K4料型不稳定,中轧来料不规范2、导卫安装不规范。
3、导卫或导卫梁紧固不牢,在钢的冲击下导卫发生轻微的摆动或扭动,导致冲出口。
4、K4(16#)进口导卫梁导卫座太窄,过钢时头部冲击力大,进口导卫不稳定容易晃动。
解决方法:1、K3、K4不能错辊、窜辊。
2、K3、K4划料必须均匀,不能有毛边。
3、中轧圆料头尾不能带耳朵,以确保K3、K4料型头尾规范。
4、必须确保中轧不能拉钢。
5、养成K4试小样的习惯,以确认进出口导卫是否在一条直线上。
6、安装K3切分导卫时切分刀、切分轮、轧辊切分尖必须在一条直线上。
7、K3、K4导卫、导卫梁上的锁紧螺栓、螺母,必须紧固好。
8、与导卫厂家协商,导卫梁导卫座加宽,导卫锁紧改成中轧锁紧样式。
二、存在的问题:K3掉块现象比较严重原因:1、K3、K4压下量分配不合理,K3机架的电流应为K4电流的一半,而我厂K3、K4电流几乎一样(设计原因)。
2、K3、K4轧槽缺水(其他架次也存在同样的问题)。
解决方法:1、尝试修改K4孔型,增加K4压下量,减少K3负荷。
三、存在的问题:K1冲出口原因:1、导卫或导卫梁紧固不牢,在钢的冲击下导卫发生轻微的摆动或扭动,导致冲出口。
2、钢头弯顶出口导板,主要原因是K3切分出的料型不好(头部一侧尖),经18#扭转导卫扭转后尖头在上或下,尖头必然先碰到轧辊(K1);尖头先碰到上辊,成品钢头就朝上弯;尖头先碰到下辊,成品钢头就朝下弯。
解决方法:1、导卫、导卫梁上的锁紧螺栓、螺母,必须紧固好。
2、新换K4轧辊或槽,开轧之前试小样,确保K3、K4料型。
四、存在的问题:K3出口导卫切分刀、出口导卫下铲嘴粘钢。
可能原因:1、正常过钢时K3切分尖磨损较快,导致撕裂带太厚。
螺纹钢切分轧制哑铃孔中轧件充满程度的有限元模拟

螺纹钢切分轧制哑铃孔中轧件充满程度的有限元模拟
曹杰;阎军;章静
【期刊名称】《钢铁研究学报》
【年(卷),期】2005(17)2
【摘要】为分析螺纹钢二切分轧制哑铃孔中轧件充满程度,优化孔型形状,笔者借助有限元分析软件 MARC/Au toforge,对哑铃孔中轧件的变形进行了模拟。
结果表明,改变哑铃孔的基本结构尺寸、调整来料尺寸可增加轧件的宽展并改善哑铃孔的充满程度;但会使轧制压力增加、切分楔磨损严重,所以哑铃孔的设计应同时考虑轧件充满程度和轧辊的磨损程度。
【总页数】4页(P34-37)
【关键词】切分轧制;孔型;充满程度;轧制力;有限元法
【作者】曹杰;阎军;章静
【作者单位】安徽工业大学冶金与材料学院
【正文语种】中文
【中图分类】TG335.4
【相关文献】
1.螺纹钢切分轧制弧边方孔中轧件变形有限元分析 [J], 曹杰;阎军;章静
2.螺纹钢三切分轧制轧件尺寸影响因素的分析 [J], 曹杰;阎军;章静
3.螺纹钢切分轧制有限元分析 [J], 曹杰;阎军;章静
4.切分孔形状对轧件变形影响的有限元分析 [J], 阎军;鹿守理;陈希克
因版权原因,仅展示原文概要,查看原文内容请购买。
Φ16规格螺纹钢四切分轧制技术的开发与实现
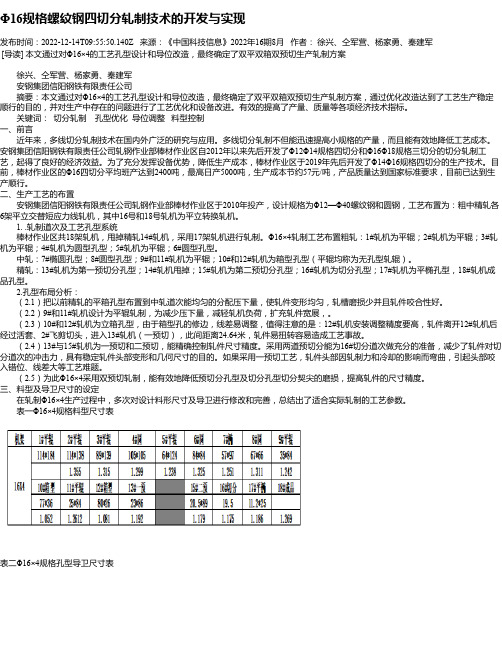
Φ16规格螺纹钢四切分轧制技术的开发与实现发布时间:2022-12-14T09:55:50.140Z 来源:《中国科技信息》2022年16期8月作者:徐兴、仝军营、杨家勇、秦建军[导读] 本文通过对Φ16×4的工艺孔型设计和导位改造,最终确定了双平双箱双预切生产轧制方案徐兴、仝军营、杨家勇、秦建军安钢集团信阳钢铁有限责任公司摘要:本文通过对Φ16×4的工艺孔型设计和导位改造,最终确定了双平双箱双预切生产轧制方案,通过优化改造达到了工艺生产稳定顺行的目的,并对生产中存在的问题进行了工艺优化和设备改进。
有效的提高了产量、质量等各项经济技术指标。
关键词:切分轧制孔型优化导位调整料型控制一、前言近年来,多线切分轧制技术在国内外广泛的研究与应用。
多线切分轧制不但能迅速提高小规格的产量,而且能有效地降低工艺成本。
安钢集团信阳钢铁有限责任公司轧钢作业部棒材作业区自2012年以来先后开发了Φ12Φ14规格四切分和Φ16Φ18规格三切分的切分轧制工艺,起得了良好的经济效益。
为了充分发挥设备优势,降低生产成本,棒材作业区于2019年先后开发了Φ14Φ16规格四切分的生产技术。
目前,棒材作业区的Φ16四切分平均班产达到2400吨,最高日产5000吨,生产成本节约57元/吨,产品质量达到国家标准要求,目前已达到生产顺行。
二、生产工艺的布置安钢集团信阳钢铁有限责任公司轧钢作业部棒材作业区于2010年投产,设计规格为Φ12—Φ40螺纹钢和圆钢,工艺布置为:粗中精轧各6架平立交替短应力线轧机,其中16号和18号轧机为平立转换轧机。
1. .轧制道次及工艺孔型系统棒材作业区共18架轧机,甩掉精轧14#轧机,采用17架轧机进行轧制。
Φ16×4轧制工艺布置粗轧:1#轧机为平辊;2#轧机为平辊;3#轧机为平辊;4#轧机为圆型孔型;5#轧机为平辊;6#圆型孔型。
中轧:7#椭圆孔型;8#圆型孔型;9#和11#轧机为平辊;10#和12#轧机为箱型孔型(平辊均称为无孔型轧辊)。
φ12mm螺纹钢三切分工艺中成品中间线折叠的产生原因及消除方法的分析

φ12mm螺纹钢三切分工艺中成品中间线折叠的产生原因及消除方法的分析φ12mm螺纹钢三切分工艺中成品中间线折叠的产生原因及消除方法的分析摘要:介绍了柳钢棒线厂第二棒材生产线φ12mm螺纹钢三切分轧制的生产现状、工艺流程、技术方案,并对轧制过程中成品中间线产生的折叠进行原因以及消除方法的分析。
关键词:三切分孔型料型折叠1 前言柳钢棒线厂于2004年建成投产第二棒材生产线,最初设计年产量60万吨,设计最高速度为18m/s,生产工艺流程为:原料准备—〉加热—〉粗轧—〉1#飞剪—〉中轧—〉2#飞剪—〉精轧—〉穿水冷却—〉3#飞剪—〉裙板—〉冷床—〉冷剪—〉成品收集—〉打捆—〉称重—〉检验—〉入库发货。
经过技术集成与优化,目前已具备年产100万吨的生产能力。
主要产品为φ12—φ25螺纹钢,2012年前主要以两线切分工艺为主,两切分技术在此生产线已经非常成熟。
由于市场形势的需要,φ12螺纹钢在市场上比较畅销,但两切分的机时产量较低,生产线的能力得不到充分发挥,为满足市场需求,落实“优质增效”,实现效益最大化,今年开发三切分轧制工艺生产φ12螺纹钢。
2 成品中间线产生折叠原因的分析在初试φ12mm螺纹钢三切分时,成品出现了横肋及内径折叠等表面缺陷,中间线尤为明显,有的是断续的,有的是通条的,造成了大量的成品判废,对产量以及其它技术经济指标产生了较大的影响。
通过分析认为二棒轧机机架间距较短,扭转导卫不易安装,轧件出K3后中间线较难实现扭转,经过取样观察分析,发现经K3出来的轧件在切分轨迹上有二次甚至三次切痕(如图1所示),此切痕为成品表面缺陷产生的根本原因。
由于K6和K4以及K3的切分轨迹不重合,K3切分带没有沿着K4及K6的轨迹来切分,加上K3出口刀片的作用,造成了中间线两侧表面切痕,而中间线很难实现扭转,于是在横肋上出现了折叠的现象,严重的时候则会在内径上出现折叠。
图1 经K3切分过的实物图分析认为产生二次切痕的原因有:①切分带、孔槽磨损②K3、K4、K5出来的轧件切分轨迹不重合,产生重复切痕。
- 1、下载文档前请自行甄别文档内容的完整性,平台不提供额外的编辑、内容补充、找答案等附加服务。
- 2、"仅部分预览"的文档,不可在线预览部分如存在完整性等问题,可反馈申请退款(可完整预览的文档不适用该条件!)。
- 3、如文档侵犯您的权益,请联系客服反馈,我们会尽快为您处理(人工客服工作时间:9:00-18:30)。
64塑性上程学报宽高相差较大。
K5孔轧出的轧件翻转45。
后,其上
F左右的对称性较差。
采用对称性差的弧边方轧件进K4孔进行轧制,轧件容易切偏或发牛扭转,不利于轧制过程的顺利进行。
如果增加K6扎的来料尺寸,采用十44mm的坯料,K6孔轧出的轧件尺寸为63×24(mm),K6孔的充满度为93%。
以K6孔轧出的轧件在K5孔继续轧制,轧出的轧件尺寸为36.6×38.8(mm),轧件基本对称。
因此,通过控制上游道次的坯料尺寸可以在一定程度上控制K6、K5孔的宽展大小,从而获得形状规整的弧边方轧件。
鬻酞黧|||篱慧除嚣||;瞪霆扩澎、>
¨.T94/、{…时制W,fj黧i船在溢卫
图3等效塑性应变在轧件断面上的分布Fig.3DistributionofequivaI曲tplasticstraIn1nthe
transversesectionsofrolllngstocks
图4轧件边部节点宽展情况
Fig.4Spread。
fthesidenodeofstocb
由图5可以看出轧件在K4、K3孔中轧制后的形状与充满情况。
采用对称性良好的弧边方形轧件在K4孔中轧制,所得轧件最大宽度为17.omm,上下对称面处的宽度为14.5mm,弧边的深度由最初的3,1mm减小到2.5nⅡn。
弧边的深度在K3孔进一步减小,由K4孔的2.5mm降到1‘6mm。
可以看出,弧边方轧件经过K4、K3两道次的轧制
目
u
越
惺
扯
霹
轧件宽度(衄)
第10卷
图5轧制后轧件的宽度
Fig.5
WidthofstochafterrollI“g
后,弧边没有完全消除,轧件边部存在有“月缺”现象。
实际牛产中,K5~K3孔轧出轧件的断面形状如图6所示。
由图6可以看出,实际生产与模拟结果基本一致。
通过轧机调整,K5可轧出基本对称的弧边方轧件。
采用基本对称的弧边方轧件,经过K4、K3两道次的轧制后,弧边没有完全消除。
弧边的存在对产品的质量不利。
首先,弧边影响了轧件的断面形状与尺寸精度;其次,有可能造成产品的折叠缺陷。
因此,弧边要在K4、K3道次尽量消除。
图6K5~K3轧件取样断面形状
Fig.6
Cmss_sectionsofs哪plesofpassK5~哟为消除“月缺”现象,孤边方轧件的弧边不能太深,在保证轧件能对中的条件下,弧边要尽可能平缓;另外,K4、K3孔的设汁应有利于轧件水平对称面处的宽展。
4结论
1)轧件在哑铃形孔、切分孔内变形量很大,但变形局限在切分区内,其它地方变形量较小,因此切分轧制存在严重的不均匀变形。
2)通过调整圆坯尺寸大小来控制轧件在K6孔的宽展大小,在K5孔可基本袄得形状规整的弧边方形轧件,但通过控制K6孔宽展大小调整弧边方轧件的形状有一定限度。
3)弧边方轧件的弧边在K4、K3孔中不易消
螺纹钢切分轧制有限元分析
作者:曹杰, 阎军, 章静
作者单位:安徽工业大学,冶金与材料学院,马鞍山,243002
刊名:
塑性工程学报
英文刊名:JOURNAL OF PLASTICITY ENGINEERING
年,卷(期):2003,10(3)
被引用次数:3次
参考文献(3条)
1.陈火红Marc有限元实例分析教程 2002
2.阎军;鹿守理;陈希克切分孔形状对轧件变形影响的有限元分析[期刊论文]-钢铁研究学报 2000(02)
3.黄武军水平连轧机组应用切分轧制技术的探讨[期刊论文]-轧钢 2001(04)
本文读者也读过(10条)
1.孙建林.许宝才.康永林.杨进航棒材切分轧制过程中三维弹塑性有限元模拟[期刊论文]-青海大学学报(自然科学版)2004,22(1)
2.廉宏亮.张军霞全连轧棒材线自动化控制系统设计与实现[会议论文]-2004
3.曹杰.阎军.章静螺纹钢切分轧制弧边方孔中轧件变形有限元分析[期刊论文]-安徽工业大学学报(自然科学版) 2003,20(3)
4.杨乾慧金属市场螺纹钢质量问题及管理对策[期刊论文]-实用测试技术2001,27(3)
5.傅强勇.陈军.辛赣宁.FU Qiang-yong.CHEN Jun.XIN Gan-ning活套控制分析与改进[期刊论文]-江西冶金2005,25(6)
6.王薇.王小林.张娜CCR轧机应用于高合金棒材轧制的优势分析[会议论文]-2010
7.陈炳生.刘宝瑛棒、线材及螺纹钢截面形状在线测量技术[期刊论文]-激光与光电子学进展2008,45(2)
8.高伟三线切分时影响棒材张开角的几个因素[期刊论文]-钢铁2003,38(5)
9.刘建萍.LIU Jian-ping萍钢五切分轧制技术的研发[期刊论文]-江西冶金2008,28(2)
10.宁銮凤.赵彦来.王军加热炉高效燃烧控制技术应用[会议论文]-2005
引证文献(3条)
1.蔡长生.李沁怡.陈其伟.胡睿角钢热连轧过程的温度场有限元分析[期刊论文]-安徽冶金科技职业学院学报2013(2)
2.曹淑敏.陈其伟.朱国辉.完卫国20MnSi钢筋热连轧温度场的热力耦合分析[期刊论文]-安徽工业大学学报(自然科学版) 2011(4)
3.胡睿.隋凤利.奚铁.吴结才.陈其伟张力对连轧角钢轧制变形影响的有限元分析[期刊论文]-安徽工业大学学报(自然科学版) 2012(2)
本文链接:/Periodical_sxgcxb200303015.aspx。