太阳能电池组件封装工艺研究
组件生产工艺流程简介)
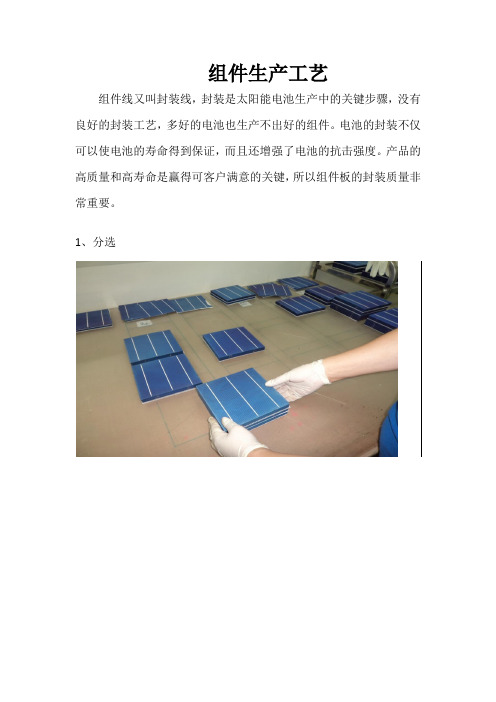
组件生产工艺组件线又叫封装线,封装是太阳能电池生产中的关键步骤,没有良好的封装工艺,多好的电池也生产不出好的组件。
电池的封装不仅可以使电池的寿命得到保证,而且还增强了电池的抗击强度。
产品的高质量和高寿命是赢得可客户满意的关键,所以组件板的封装质量非常重要。
1、分选此为组件的第一道工序,在本道工序中,首先将电池片进行初步筛选,将不符合标准的电池片,如色差片,崩边片,缺胶片,断栅片等等分类放置在一起,将合格的电池片按照机器焊接每打100片的数量清点好。
2、焊接焊接工序采用最先进的德国进口TT1200焊片机。
1200指的时每小时一台机器可以焊接1200片电池片,也就是说老式焊片机3秒焊接一片,新式焊片机2.8秒左右焊接一片。
焊接机采用不接触涂布装置、影响定位系统、红外焊接装置、自动抓取机器人等部分组成。
影响定位系统有效挑选出破片、裂片等装置,有效的保证了焊接品质。
在此工序中由“自动焊片机”将单片电池片和涂锡铜带焊接成一串,再由提取ABB机器人将每串电池串提取到铺设好EVA的玻璃板上。
ABB机器人能够准确按照设置的间距,将电池串排列到好,精确误差在0.5mm以内。
TT焊片机彻底替代了原始的手工焊接,不仅在产量上有了很大的提高,更在质量上有明显的改善。
焊接处理的组件没有杂物、锡渣等。
3,叠层(也称排片)叠层为组件生产过程中的一道关键岗位,这道工序主要将焊接好的电池串连接成电路。
每相邻的电池上都要粘贴2到3条高温胶带,目的是防止电池串发生移位等情况。
之后用烙铁将汇流条焊接在每串的两端,按照正负极的正常方式将组件做成一个完整的导通发电体。
4、隐裂测试在组件半成品做完,需要对组件进行隐裂测试。
做好的本成品组件,可能存在裂纹等情况,用肉眼是无法观察到的。
隐裂测试仪的原理就是将组件通电,通电后组件发出红外光,再利用照相机成像。
隐裂测试能检查到整个组件内部是否存在不合格的电池片如,隐裂片,低效片,黑心片等一系列不符合标准的电池片,一旦发现需要进行返修。
太阳能电池组件的层压工艺(完整版)

环保设备
采用环保型的层压设备,降低生产过程中的环境污染。
06
层压工艺的案例分析
成功案例分享
案例一
案例二
某知名太阳能电池组件制造商通过采用先进 的层压工艺,成功提高了电池组件的效率和 可靠性,从而在市场上获得了显著竞争优势。
某创业公司通过自主研发新型层压工艺,降 低了生产成本并优化了产品结构,在短时间 内实现了快速成长。
04
层压工艺的质量控制
质量标准制定
制定层压工艺的质量标准,确保每个 环节的工艺参数、材料要求、设备精 度等符合标Байду номын сангаас,以确保最终产品的质 量和性能。
根据市场需求和行业标准,不断更新 和完善质量标准,提高产品的竞争力 和可靠性。
质量控制方法
采用统计过程控制(SPC)方法,对 层压工艺过程中的关键参数进行实时 监控和记录,及时发现异常并采取措 施进行调整。
检测设备
用于检测太阳能电池组件的性能参数,如电 压、电流、功率等。
材料与设备的维护与保养
定期检查材料
确保封装材料、背板材料和边框材料无破损、老化等 现象。
设备清洁与保养
定期对层压机、真空泵等设备进行清洁和保养,确保 设备正常运行。
检测与调整
定期对检测设备进行校准和调整,确保检测数据的准 确性和可靠性。
后期处理阶段
冷却与取出
待层压处理完成后,让组件自然冷却, 然后取出。
VS
质量检测
对组件进行外观检测、电性能检测等,确 保符合质量要求。
03
层压工艺的材料与设备
材料选择
太阳能电池片
选择高效、稳定的太阳能电池 片,确保光电转换效率高。
太阳能电池组件封装工艺
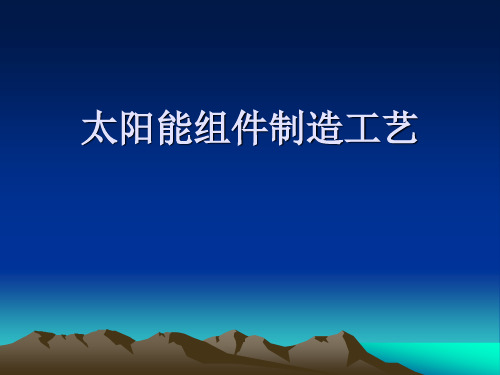
太阳电池组装工艺简介
• 单焊: • 是将汇流带焊接到电池正面(负极)的主 栅线上,汇流带为镀锡的铜带,焊带的长 度约为电池边长的2倍。多出的焊带在背面 焊接时与后面的电池片的背面电极相连。
太阳电池组装工艺简介
• 串焊 • 背面焊接是将N片电池串接在一起形成一个 组件串,电池的定位主要靠一个膜具板, 操作者使用电烙铁和焊锡丝将单片焊接好 的电池的正面电极(负极)焊接到“后面 电池”的背面电极(正极)上,这样依次 将N片串接在一起并在组件串的正负极焊接 出引线。
太阳能组件封装结构图
封装结构图
玻璃
电池片
组件高效和高寿命如何保证:
• 1、 高转换效率、高质量的电池片 ; • 下面是电池的结构示意图: • (1) 金属电极主栅线;(2)金属上电极 细栅线;(3)金属底电极; • (4)减反射膜;(5)顶区层(扩散层); (6)原材料
• • • • 玻璃的质量要求以及来料抽检 4) 不允许有结石,裂纹,缺角的情况发生。 5) 钢化玻璃在可见光波段内透射比不小于90%。 6) 钢化玻璃表面允许每平方米内宽度小于0.1mm,长度 小于15mm的划伤数量不多于2条。每平方米内宽度0.10.5mm长度小于10mm的划伤不超过1条。 • 钢化玻璃不允许有波型弯曲,弓型弯曲不允许超过0.2%. 根据GB/T9963-1998中 4.4,4.5,4.6条款进行试验,在 50mm*50mm的区域内碎片数必须超过40个。
电池组件的主要原材料
• 另一方面,它和玻璃粘合后能提高玻璃的透光率, 起着增透的作用,并对太阳电池组件的输出有增 益作用。 • EVA厚度在0.4mm~0.6mm之间,表面平整,厚 度均匀,内含交联剂,能在140℃固化温度下交 联,采用挤压成型工艺形成稳定胶层。 • EVA主要有两种: ①快速固化 ②常规固化,不 同的EVA层压过程有所不同
晶体硅太阳电池组件封装工艺

性能参数进行 测试 , 测试条件为标准条件, 即: A M1 . 5 、 温度 2 5 ℃、 光 照强度为 1 0 0 0 W/ m , 组 件的测试是 为了组件 的分
3 叠 层
叠层是 指在 电池 背面 串接好且检 验合格后 ,将组 件 串、 玻璃和切割好的 E V A、 背板按照一定的层次铺设好 , 并 引 电极 , 准备层压 。铺设 时保证 电池 串与玻璃等 材料的 相对位 置 , 调 整好 电池 问的距离 , 通 过胶带 固定 电池 串 的
园
也采用手工 焊接 , 电池 的定 位主要 靠一个 焊接 面板 , 上 面
有放 置 电 池 片 的 凹 槽 ,槽 的大 小 和 电 池 的 大 小 相 对 应 , 槽
的位 置预先设 计好 ,不同规格 的组件使 用不 同的模板 , 焊 接 面板 同时还 具有 传热作用 , 可以减少 电池 片的隐裂和虚 焊 。焊接 过程 中 , 操作者使用 电烙 铁将 “ 前 电池” 的正面 电
流, 电压 和输出功率 , 同时保证 晶体 硅太 阳电池 片不受 外 界损坏 , 能 稳定应用 ; 封装方式 是将 一定数 量 的单 片 电池 采用 串 、 并 联 的厅式连 接起来 , 并辅 以钢化 玻璃 、 E V A、 背
2 电池 的 单 焊 和 串焊
晶体硅太阳电池 电池片单焊( 见下 图 2 ) 是将焊带焊接 到 电池正面 ( 负极 ) 的主栅线 E, 焊带 为镀锡 铜带 , 焊带 的
面的 电池片 的背 面电极相 连 , 目前 组件生产厂家有手 『 焊
接 和 自动 化 焊 接两 种 方 式 。
晶体 硅太阳电池 的串焊 ( 见下 2 ) 是指将焊接好 的单 个电池片从背面互相焊接成一 个电池串 , 目前的 艺大 多
太阳能电池组件生产的主要工艺流程
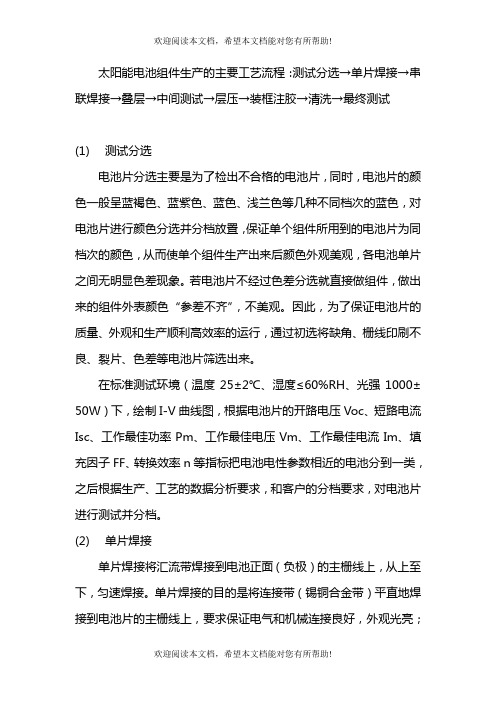
太阳能电池组件生产的主要工艺流程:测试分选→单片焊接→串联焊接→叠层→中间测试→层压→装框注胶→清洗→最终测试(1)测试分选电池片分选主要是为了检出不合格的电池片,同时,电池片的颜色一般呈蓝褐色、蓝紫色、蓝色、浅兰色等几种不同档次的蓝色,对电池片进行颜色分选并分档放置,保证单个组件所用到的电池片为同档次的颜色,从而使单个组件生产出来后颜色外观美观,各电池单片之间无明显色差现象。
若电池片不经过色差分选就直接做组件,做出来的组件外表颜色“参差不齐”,不美观。
因此,为了保证电池片的质量、外观和生产顺利高效率的运行,通过初选将缺角、栅线印刷不良、裂片、色差等电池片筛选出来。
在标准测试环境(温度25±2℃、湿度≤60%RH、光强1000±50W)下,绘制I-V曲线图,根据电池片的开路电压Voc、短路电流Isc、工作最佳功率Pm、工作最佳电压Vm、工作最佳电流Im、填充因子FF、转换效率n等指标把电池电性参数相近的电池分到一类,之后根据生产、工艺的数据分析要求,和客户的分档要求,对电池片进行测试并分档。
(2)单片焊接单片焊接将汇流带焊接到电池正面(负极)的主栅线上,从上至下,匀速焊接。
单片焊接的目的是将连接带(锡铜合金带)平直地焊接到电池片的主栅线上,要求保证电气和机械连接良好,外观光亮;焊带的长度约为电池边长的2倍,多出的焊带在串联焊接时与后面的电池片的背面电极相连。
(3)串联焊接背面焊接是将电池片接在一起形成一个电池片的串组,电池的定位主要靠一个膜具板,上面有放置电池片的凹槽,槽的大小和电池的大小相对应,槽的位置已经是设计好的,不同规格的组件使用不同的模板,操作者使用电烙铁和连接带(锡铜合金带)将单片焊接好的电池片的正面电极(负极)焊接到另一片的背面电极(正极)上,以此类推,依次将电池片串接在一起,并在组件串的正负极焊接出为叠层时准备的引线。
(4)叠层背面串接好且经过检验合格后,将电池片串、钢化玻璃和切割好的EVA 、背板(TPT)按照一定的层次敷设好,玻璃事先涂一层试剂(primer)以增加玻璃和EVA的粘接强度。
电池组件工艺路线

电池组件工艺路线电池组件的制造工艺路线通常包括多个步骤,以下是典型的太阳能光伏电池组件(太阳能电池板)的制造工艺流程:1. 硅片生产:原材料准备:制备高纯度的多晶硅。
拉晶:将高纯度硅熔体拉成硅单晶棒。
切割:切割硅单晶棒,形成硅片。
2. 硅片表面处理:切割:将硅片切割成适当大小的太阳能电池用片。
去除研磨痕迹:对硅片表面进行化学或机械去研磨痕迹的处理。
3. 电池芯片制造(太阳能电池):扩散:在硅片表面扩散掺杂物质,形成p型和n型半导体区域。
光刻:使用光刻技术在硅片表面涂覆光敏胶,然后通过光刻图案形成光刻胶层。
腐蚀:对硅片进行腐蚀,形成电池芯片的金属电极。
沉积金属:在硅片表面沉积金属,形成电池芯片的电极。
4. 电池片组装:打磨和清洗:对电池芯片进行打磨和清洗,去除表面杂质。
串联焊接:将多个电池芯片通过焊接连接成电池串。
组串焊接:将多个电池串组装成电池组件。
5. 电池组件封装:玻璃片涂覆:在电池组件表面涂覆玻璃片,增强电池的结构强度和耐候性。
夹胶:在电池组件上下夹胶,形成密封的夹胶结构。
封边:对夹胶结构进行封边,确保电池组件的密封性。
框架安装:安装电池组件的支架和框架,以便固定和安装。
6. 测试和质量控制:电性能测试:测试电池组件的电性能,包括电压、电流、功率等。
外观检查:对电池组件的外观进行检查,确保没有裂纹、污渍等缺陷。
耐候性测试:对电池组件进行耐候性测试,模拟不同环境条件下的使用情况。
7. 包装和出厂:包装:对测试合格的电池组件进行包装,以防止运输过程中的损坏。
出厂检验:进行最终的出厂检验,确保产品符合质量标准。
这是一个典型的太阳能电池组件的制造工艺流程,实际生产中可能会有一些细节的差异和改进。
随着太阳能技术的发展,工艺流程也在不断优化。
太阳能光伏组件封装工艺
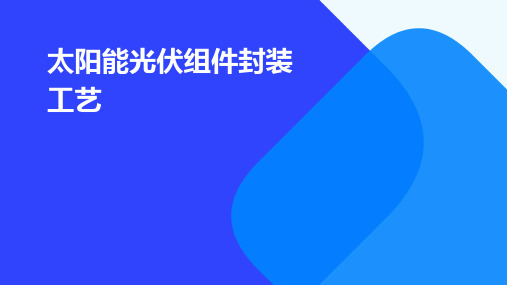
铝合金边框具有强度高、耐腐蚀性好 、美观大方等特点,但成本较高。塑 料边框则具有重量轻、成本低、易于 加工等特点,但耐候性和强度较差。
03
封装工艺流程
清洗
清洗
在太阳能光伏组件的封装过程中, 清洗是第一步,其目的是去除硅 片表面的污垢和杂质,确保硅片 的清洁度,为后续的封装工艺提
供良好的基础。
清洗方法
常用的清洗方法包括机械清洗、 化学清洗和超声波清洗等。根据 硅片表面的污染程度和性质,选
择合适的清洗方法和清洗剂。
清洗设备
清洗设备包括清洗槽、喷淋装置、 传送带等,这些设备能够确保硅 片在清洗过程中得到均匀的清洗
效果,并提高清洗效率。
叠层
叠层
叠层工艺
在清洗完成后,硅片需要进行叠层, 即将多个硅片按照一定的顺序叠放在 一起,形成一个太阳能电池组件。
封装工艺的分类
根据材料
可以分为晶体硅光伏组件封装工艺和非晶硅光伏 组件封装工艺。
根据结构
可以分为层压式封装工艺和盒式封装工艺。
根据功能
可以分为普通封装工艺和特种封装工艺。
02
封装材料
盖板材料
盖板材料是光伏组件最外层的保护层, Nhomakorabea要作用是保护电池 片不受外界环境的影响,如紫外线、水分等。常见的盖板材 料有玻璃和聚合物薄膜等。
接线盒安装
接线盒安装
在切割完成后,需要在每个独立 的电池片上安装接线盒,以便将 电池片连接起来形成太阳能电池 板。
接线盒类型
常用的接线盒类型包括嵌入式和 粘贴式等,嵌入式接线盒能够与 电池片紧密结合在一起,具有较 高的机械强度和稳定性;粘贴式 接线盒则具有较低的成本和较快 的生产速度。
太阳能电池组件封装工艺

太阳能电池组件封装工艺太阳能电池组件的制造过程中主要有以下一些步骤:激光划片—光焊(将电池片焊接成串)—手工焊(焊接汇流条)—层叠(玻璃—EVA—电池—EVA—TPT)—中测—层压—固化—装边框、接线盒—终测。
1、激光划片:太阳能电池每片工作电压0.4-0.5V左右(开路电压约0.6V),将一片切成两片后,每片电压不变;太阳电池的功率与电池板的面积成正比(同样转化率下)。
根据组件所需电压、功率,可以计算出所需电池片的面积及电池片片数,由于单体电池(未切割前)尺寸一定(有几种标准),面积通常不能满足组件需要,因此,在焊接前,一般有激光划片这套工序,切割前,应设计好切割路线,画好草图,要尽量利用切割剩余的电池片,提高电池片的利用率。
切片时的具体要求:1.1、切片时,切痕深度一般要控制在电池片厚度的1/2—2/3,这主要通过调节激光划片机的工作电流来控制。
如果工作电流太大,功率输出大,激光束强,可以将电池片直接划断,容易造成电池正负极短路。
反之,当工作电流太小,划痕深度不够,在沿着划痕用手将电池折断时,容易将电池片弄碎。
1.2、太阳电池片价格较贵,为减少电池片在切割中的损耗,在正式切割前,应先用与待切电池片型号相同的碎电池片做试验,测试出该类电池片切割时激光划片机合适的工作电流I0,这样正常样品的切割中划片机按照电流I0工作,可以减少由于工作电流太大或太小而造成损耗。
1.3、激光划片机激光束进行路线是通过计算机设置XY坐标来确定的,设置坐标时,一个小数点和坐标轴的差错会使激光束路线完会改变,因此,在电池片切割前,先用小工作电流(使激光能被看清光斑即可)让激光束沿庙宇的路线走一遍,确认路线正确后,再调大电流进行切片。
1.4、一般来说,激光划片机只能沿XY轴方向进行切割,切方形电池片较方便。
当电池片切成三角形等形状时,切割前一定要计算好角度,摆好电池方位,使需要切割的线路沿X或Y方向。
1.5、在切割不同电池片时,如果两次厚度差别较大,调整工作电流的同时,注意调整焦距。
钙钛矿太阳能电池材料制备、器件组装及性能测试综合实验设计

钙钛矿太阳能电池材料制备、器件组装及性能测试综合实验设计一、本文概述随着可再生能源需求的不断增长,钙钛矿太阳能电池作为一种高效、低成本的光伏技术,正受到全球研究者的广泛关注。
本文旨在提供一个综合实验设计,涵盖钙钛矿太阳能电池的材料制备、器件组装以及性能测试等方面,以期为相关领域的研究者提供一套系统的实验方法和策略。
本文将首先介绍钙钛矿太阳能电池的基本原理和发展现状,以便读者对该技术有一个全面的了解。
随后,将详细介绍钙钛矿材料的制备过程,包括前驱体溶液的配置、薄膜的制备和退火处理等关键步骤。
在此基础上,本文将进一步阐述器件的组装过程,包括电极的制备、钙钛矿层的沉积以及封装等步骤。
在完成器件组装后,本文将介绍如何进行性能测试,包括光电转换效率、稳定性等关键指标的测量和评估。
本文还将探讨影响钙钛矿太阳能电池性能的各种因素,如材料组成、制备工艺和器件结构等,并提出相应的优化策略。
通过本文的实验设计,读者可以深入了解钙钛矿太阳能电池的制备和性能测试过程,掌握关键技术和方法,为进一步提高钙钛矿太阳能电池的性能和应用奠定基础。
二、钙钛矿太阳能电池材料制备钙钛矿太阳能电池的材料制备是构建高效、稳定器件的关键步骤。
该过程主要包括前驱体溶液的配制、薄膜的制备、退火处理等步骤。
前驱体溶液的配制:需要精确称取适量的钙钛矿材料(如MAPbIFAPbI3等)以及溶剂(如二甲基亚砜、二甲基甲酰胺等)。
在手套箱或氮气环境下,将这些材料按照一定的摩尔比例混合,并进行充分的搅拌,以得到均匀的前驱体溶液。
此过程中,对溶液的浓度、搅拌速度和时间等参数需进行严格控制,以确保溶液的稳定性和均一性。
薄膜的制备:将配制好的前驱体溶液通过旋涂、刮涂或喷涂等方法涂覆在基底(如ITO玻璃、FTO玻璃等)上。
旋涂过程中,需要控制旋涂速度、时间和溶液滴加量等参数,以获得均匀、光滑且无针孔的钙钛矿薄膜。
为了进一步提高薄膜的质量,还可在旋涂过程中引入退火、溶剂工程等技术手段。
简述太阳能电池组件封装的生产工艺流程

简述太阳能电池组件封装的生产工艺流程Solar photovoltaic (PV) module encapsulation is a crucial step in the production process of solar panels. It involves sealing and protecting the PV cells from external environmental factors such as moisture, dust, and mechanical stress. Let's take a closer look at the production process of solar module encapsulation.太阳能光伏电池组件封装是太阳能电池板生产过程中的重要环节。
它涉及封闭和保护光伏电池,防止外部环境因素如潮湿、灰尘和机械应力对其造成的影响。
让我们更详细地了解太阳能模块封装的生产过程。
1. Laminate Cutting:The first step in the encapsulation process involvescutting the backsheet, which serves as a protective layer on the backside of the solar panel. Automatic cutting machines are used to cut the backsheets into desired sizes according to specific module dimensions.1. 切割背板:封装过程的第一步是切割背板,背板作为太阳能电池板的背面保护层存在。
自动切割机根据具体模块尺寸将背板切割成所需大小。
2. Busbar Soldering:After obtaining appropriately sized backsheets, the next step is busbar soldering. The busbars are thin metal strips that collect electric current generated by the solar cells. Automated soldering machines apply solder paste to connect multiple busbars on each cell precisely.2. 母线焊接:在获得适当尺寸的背板之后,下一步是母线焊接。
光伏组件制造工艺分析(光伏电池制造工艺课程设计)
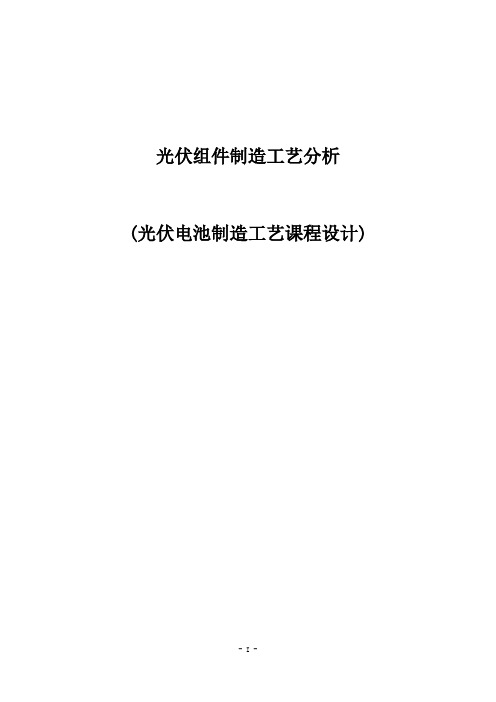
光伏组件制造工艺分析(光伏电池制造工艺课程设计)目录第1章光伏组件概述 (4)1.1 光伏组件 (4)1.2 光伏组件电池的发电原理 (4)1.3 光伏组件中光伏电池的发展历史 (6)1.4 光伏组件分类 (6)第2章光伏组件制造工艺 (8)2.1 电池片检测与分选 (8)2.1.1 太阳能电池片外观检测 (8)2.1.2单片分选仪简介 (8)2.1.3 电池片分类 (9)2.2 组件制造其他材料准备 (9)2.2.1焊带、汇流条的裁剪与浸泡 (9)2.2.2 裁剪EV A与背板 (10)2.2.3 工作结束 (11)2.2.4其他一些材料的准备与材料准备记录单 (11)2.3 电池片焊接 (11)2.3.1 电池片的单片焊接 (11)2.3.2 电池片的串焊 (12)2.3.3 焊片质量检测 (12)2.3.4焊接作业记录单 (13)2.4 电池片层压 (13)2.4.1 电池片叠层 (13)2.4.2 叠层作业记录单 (14)2.5 层压前EL检测 (14)2.6 层压 (14)2.6.1 层压机原理 (15)2.6.2 层压质量检测 (16)2.6.3层压机的使用以及日常维护 (19)2.6.4 层压作业记录单 (21)2.7 修边与外观检测 (21)2.7.1 修边与外观检测 (21)2.7.2修边与外观检测作业记录单 (21)2.8装框与安装接线盒 (21)2.8.1装框 (21)2.8.2接线盒 (23)2.8.3装框与安装接线盒作业记录单 (23)2.9清洗与检测 (23)2.9.1电池组件清洗 (24)2.9.2组件检验标准 (25)2.9.3包装检验 (26)2.9.4清洗与包装作业记录单 (26)第3章滴胶组件 (26)3.1 滴胶组件简介 (26)3.2 1.5W/5V滴胶组件设计 (26)3.2.1尺寸与布局设计 (26)3.2互联条设计 (28)第1章光伏组件概述1.1 光伏组件单体太阳电池不能直接做电源使用。
光伏组件封装技术大全
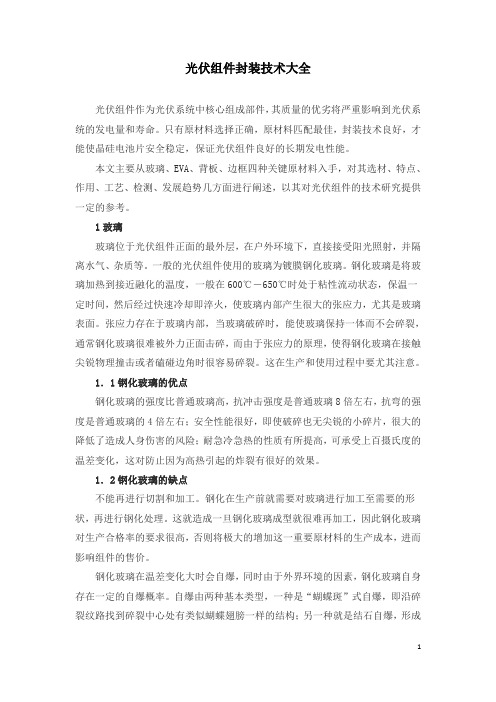
光伏组件封装技术大全光伏组件作为光伏系统中核心组成部件,其质量的优劣将严重影响到光伏系统的发电量和寿命。
只有原材料选择正确,原材料匹配最佳,封装技术良好,才能使晶硅电池片安全稳定,保证光伏组件良好的长期发电性能。
本文主要从玻璃、EVA、背板、边框四种关键原材料入手,对其选材、特点、作用、工艺、检测、发展趋势几方面进行阐述,以其对光伏组件的技术研究提供一定的参考。
1玻璃玻璃位于光伏组件正面的最外层,在户外环境下,直接接受阳光照射,并隔离水气、杂质等。
一般的光伏组件使用的玻璃为镀膜钢化玻璃。
钢化玻璃是将玻璃加热到接近融化的温度,一般在600℃-650℃时处于粘性流动状态,保温一定时间,然后经过快速冷却即淬火,使玻璃内部产生很大的张应力,尤其是玻璃表面。
张应力存在于玻璃内部,当玻璃破碎时,能使玻璃保持一体而不会碎裂,通常钢化玻璃很难被外力正面击碎,而由于张应力的原理,使得钢化玻璃在接触尖锐物理撞击或者磕碰边角时很容易碎裂。
这在生产和使用过程中要尤其注意。
1.1钢化玻璃的优点钢化玻璃的强度比普通玻璃高,抗冲击强度是普通玻璃8倍左右,抗弯的强度是普通玻璃的4倍左右;安全性能很好,即使破碎也无尖锐的小碎片,很大的降低了造成人身伤害的风险;耐急冷急热的性质有所提高,可承受上百摄氏度的温差变化,这对防止因为高热引起的炸裂有很好的效果。
1.2钢化玻璃的缺点不能再进行切割和加工。
钢化在生产前就需要对玻璃进行加工至需要的形状,再进行钢化处理。
这就造成一旦钢化玻璃成型就很难再加工,因此钢化玻璃对生产合格率的要求很高,否则将极大的增加这一重要原材料的生产成本,进而影响组件的售价。
钢化玻璃在温差变化大时会自爆,同时由于外界环境的因素,钢化玻璃自身存在一定的自爆概率。
自爆由两种基本类型,一种是“蝴蝶斑”式自爆,即沿碎裂纹路找到碎裂中心处有类似蝴蝶翅膀一样的结构;另一种就是结石自爆,形成内部向外爆裂开来的圆孔装中心结构。
给予以上两点外观特征,就可以判定钢化玻璃是自爆还是外力引起的。
太阳能电池组件工艺流程

太阳能电池组件工艺流程一、前期准备在进行太阳能电池组件的制造之前,需要进行一系列的前期准备工作。
首先,需要准备太阳能电池的原材料,包括硅片、导电背板、封装材料等。
同时,还需要准备生产设备和工具,如切割机、清洗设备、薄膜涂布机等。
二、硅片切割硅片是太阳能电池的核心部件,需要将大尺寸的硅片切割成适合电池组件的尺寸。
切割过程中需要使用切割机,将硅片切割成薄片。
切割后的硅片需要进行清洗,以去除表面的杂质和污染物。
三、表面处理经过硅片切割后,需要对硅片的表面进行处理,以提高其光吸收能力和光电转换效率。
常见的表面处理方法包括酸洗、碱洗和氧化等。
酸洗可以去除硅片表面的氧化层,碱洗可以去除硅片表面的有机物,而氧化可以形成一层二氧化硅薄膜,增加硅片的光吸收能力。
四、背板制备背板是太阳能电池组件的支撑材料,需要具备良好的导电性和耐候性。
常见的背板材料包括铝板和不锈钢板。
背板制备的过程包括切割、清洗和涂覆导电层等步骤。
涂覆导电层可以提高背板的导电性能,确保电流的顺利传输。
五、电池片制备电池片是太阳能电池组件的核心部件,需要将硅片与导电背板进行连接。
首先,将经过表面处理的硅片放置在导电背板上,然后使用导电胶水将其固定在一起。
接下来,需要进行焊接,将硅片与导电背板之间的电流连接起来。
焊接完成后,还需要进行电池片的测试,以确保其质量和性能达到要求。
六、封装与测试电池片制备完成后,需要进行封装和测试。
封装是将电池片与玻璃、背板等材料进行固定和密封,以保护电池片免受外界环境的影响。
封装过程中需要使用封装材料和封装设备,确保电池组件的稳定性和耐久性。
完成封装后,还需要进行电池组件的测试,包括电流测试、电压测试和功率测试等,以验证其性能是否符合要求。
七、包装与出厂最后一步是对太阳能电池组件进行包装和出厂。
包装是将电池组件进行包装和标识,以便运输和销售。
常见的包装材料包括纸箱和泡沫塑料等。
包装完成后,太阳能电池组件可以出厂,交付给客户使用。
太阳能电池组件生产工艺技术
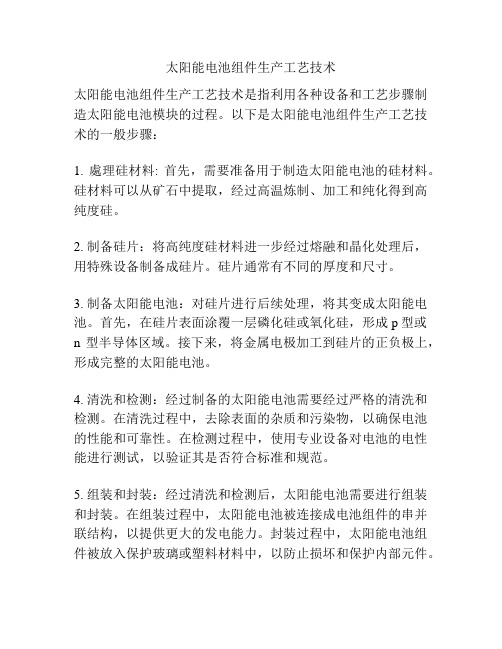
太阳能电池组件生产工艺技术太阳能电池组件生产工艺技术是指利用各种设备和工艺步骤制造太阳能电池模块的过程。
以下是太阳能电池组件生产工艺技术的一般步骤:1. 處理硅材料: 首先,需要准备用于制造太阳能电池的硅材料。
硅材料可以从矿石中提取,经过高温炼制、加工和纯化得到高纯度硅。
2. 制备硅片:将高纯度硅材料进一步经过熔融和晶化处理后,用特殊设备制备成硅片。
硅片通常有不同的厚度和尺寸。
3. 制备太阳能电池:对硅片进行后续处理,将其变成太阳能电池。
首先,在硅片表面涂覆一层磷化硅或氧化硅,形成p型或n型半导体区域。
接下来,将金属电极加工到硅片的正负极上,形成完整的太阳能电池。
4. 清洗和检测:经过制备的太阳能电池需要经过严格的清洗和检测。
在清洗过程中,去除表面的杂质和污染物,以确保电池的性能和可靠性。
在检测过程中,使用专业设备对电池的电性能进行测试,以验证其是否符合标准和规范。
5. 组装和封装:经过清洗和检测后,太阳能电池需要进行组装和封装。
在组装过程中,太阳能电池被连接成电池组件的串并联结构,以提供更大的发电能力。
封装过程中,太阳能电池组件被放入保护玻璃或塑料材料中,以防止损坏和保护内部元件。
6. 特殊处理:有时候,太阳能电池组件还需要进行特殊处理,以增加其性能和耐久性。
例如,可以添加特殊的涂层或涂料来增强电池的光吸收能力和耐候性。
在太阳能电池组件生产工艺技术的每个步骤中,高效的设备和精确的操作都是至关重要的。
同时,生产工艺技术还需要注意环境保护和能源节约,以降低生产成本和对环境的影响。
通过不断改进和创新,太阳能电池组件的生产工艺技术不断提高,为太阳能发电产业的发展做出了重要贡献。
太阳能电池组件生产工艺技术在近年来发展迅猛,随着太阳能发电市场的快速增长,生产工艺技术也变得更加成熟和先进。
下面将进一步详细介绍太阳能电池组件生产工艺技术的相关内容。
7. 硅材料:在太阳能电池组件生产中,硅材料起着核心的作用。
制备高纯度硅是制造高效太阳能电池的关键一步。
太阳能光伏电池芯片封装技术研究
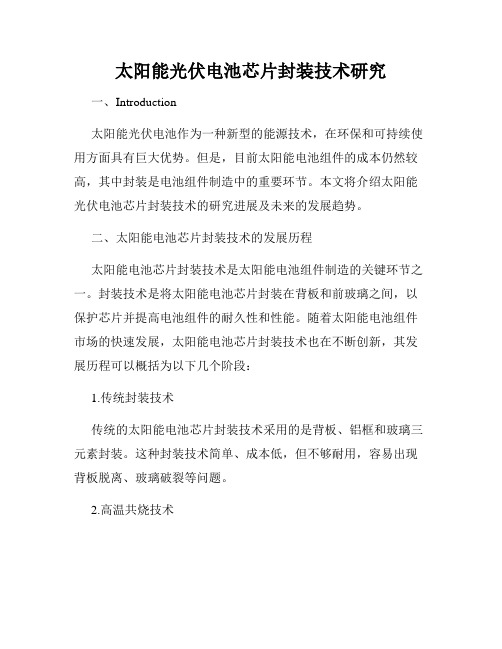
太阳能光伏电池芯片封装技术研究一、Introduction太阳能光伏电池作为一种新型的能源技术,在环保和可持续使用方面具有巨大优势。
但是,目前太阳能电池组件的成本仍然较高,其中封装是电池组件制造中的重要环节。
本文将介绍太阳能光伏电池芯片封装技术的研究进展及未来的发展趋势。
二、太阳能电池芯片封装技术的发展历程太阳能电池芯片封装技术是太阳能电池组件制造的关键环节之一。
封装技术是将太阳能电池芯片封装在背板和前玻璃之间,以保护芯片并提高电池组件的耐久性和性能。
随着太阳能电池组件市场的快速发展,太阳能电池芯片封装技术也在不断创新,其发展历程可以概括为以下几个阶段:1.传统封装技术传统的太阳能电池芯片封装技术采用的是背板、铝框和玻璃三元素封装。
这种封装技术简单、成本低,但不够耐用,容易出现背板脱离、玻璃破裂等问题。
2.高温共烧技术高温共烧技术是传统封装技术的改良版本。
该技术使用玻璃陶瓷、熔融背板和氧化铝等高温材料进行封装,具有较高的耐久性和较好的耐温性能。
3.铜薄膜封装技术铜薄膜封装技术采用铜箔作为电池芯片表面的保护层,减少了电池芯片封装过程中的压力,同时也可以提高电池的输出功率和效率。
4.柔性封装技术柔性封装技术可以将电池芯片封装在柔性材料上,如聚酰亚胺(PI)或聚乙烯醇(PVA),使电池组件更加轻薄、柔韧、透明。
这种封装技术可用于大面积薄膜太阳能电池组件的制造。
三、太阳能电池芯片封装技术存在的问题及未来发展趋势太阳能电池芯片封装技术虽然不断发展,但目前仍存在一些问题需要解决。
1.成本问题目前太阳能电池组件的封装成本仍然较高,封装技术需要进一步降低成本,以实现太阳能光伏发电的商业化。
2.耐久性问题虽然高温共烧技术和铜薄膜封装技术等封装技术已经使电池组件封装更加耐用,但仍需要进一步加强电池组件的耐久性,加大电池组件的使用寿命。
3.技术缺陷问题目前封装技术存在一些技术缺陷,如柔性封装技术中的柔性材料膨胀和收缩问题,以及铜薄膜封装技术中铜膜氧化和腐蚀问题。
太阳能电池组件封装工艺研究

定下来,有效保证产品质量;
(5)分析了胶水固化的温度和时间关系,建立了组件大小与固
化温度和固化时间的对应关系;
(6)针对26个工艺环节进行详细工艺分析和改进,并形成作业
指导书,以便固定工艺,增强可靠性;
(7)形成各环节工艺的技术指导书(附件一);
(8)形成太阳能组件大小、固化温度和时间对应关系表(见7.9
附表一);
关键词:组件、封胶、太阳能电池片ABSTRACT
Abstraet:ThestudyhasanaimtoresearchontheProcessesinsolar
eellePoxyresinPouringsealantmanufacturingintermsofProduetion
3.4.3注意事项........................................................................................................……19
第四章太阳能电池片切割方法””....…”””..“”””“”一”..””””“””…””一“一”..........一”:.”..….20
3.2.1太阳能电池片保存...................................................··..·.··...··.·········……”······……16
3.2.2太阳能电池片的拿放方法..............................……“················……”··············……16
powCf.
钙钛矿太阳能电池封装技术

钙钛矿太阳能电池封装技术嘿,咱今儿就来唠唠钙钛矿太阳能电池封装技术!这可真是个厉害的玩意儿啊!你想想,那钙钛矿太阳能电池就像个小太阳,源源不断地产生能量呢!可要是没有好的封装技术,那不就像个没穿好衣服的小孩子,容易受到各种伤害呀!封装技术就好比给它穿上了一层坚固的铠甲,保护它不受外界的干扰和侵害。
这封装技术可不简单呐!它就像是个神奇的魔法师,要把各种材料和工艺巧妙地结合起来。
首先呢,得选择合适的封装材料,这就像是给小太阳选一件合身又舒服的衣服,既要能挡住风雨,又不能影响它发光发热。
然后呢,还得有精湛的工艺,把这些材料完美地贴合在电池上,不能有一丝缝隙,不然那些捣乱的家伙可就趁机钻进去啦!咱可以类比一下哈,就好像盖房子,封装材料就是那砖头、瓦片啥的,工艺呢就是怎么把这些砖头瓦片砌得结结实实的。
要是材料不好,那房子不牢固;要是工艺不行,那房子也盖不起来呀!钙钛矿太阳能电池封装技术不也是这样嘛!封装好了有啥好处呢?那可多了去啦!它能延长电池的使用寿命啊,让它能更长时间地为我们服务。
还能提高电池的稳定性和可靠性呢,就像一个可靠的伙伴,一直陪着我们。
而且呀,好的封装技术还能让电池在各种恶劣环境下都能正常工作,不管是大热天还是大冷天,它都能稳稳当当的。
你说这封装技术是不是很重要?这可不是随便就能搞定的事儿啊!得有专业的知识和技术,还得有耐心和细心。
就像一个大厨做菜一样,得精心挑选食材,用心烹饪,才能做出美味的佳肴。
这钙钛矿太阳能电池封装技术也是一样,得用心去钻研,去实践,才能让它发挥出最大的作用。
那怎么才能做好这个封装技术呢?这可得下一番功夫呢!得不断地学习,掌握最新的技术和材料。
还得不断地尝试,找到最适合的方法和工艺。
这可不是一蹴而就的事儿啊,得慢慢来,一步一个脚印地走。
你想想,要是我们能把这个封装技术做得越来越好,那钙钛矿太阳能电池不就能发挥更大的作用了吗?我们的生活不也会变得更加美好吗?这难道不是一件超级棒的事情吗?所以啊,我们可得重视这个钙钛矿太阳能电池封装技术,让它为我们的未来添砖加瓦!。
太阳能组件工艺及常见问题

太阳能组件工艺及常见问题(上)黄飞飞陈焜编制中节能太阳能科技(镇江)有限公司二0一二年八月前言近年来,中国光伏企业的综合竞争力在不断提高,整个光伏产业链呈现快速发展态势。
中国已经形成了包括多晶硅生产、太阳能电池及组件制造、光伏系统安装及相关配套产业在内的较完整的太阳能光伏产业链。
在2009年全球太阳电池产量10.7GWp中,我国为5.2GWp,占世界产量的48.7%;2010年全球太阳电池产量15.8GWp,中国光伏太阳能电池产量更是达到8GWp,占世界生产总量的50%;2011年全球太阳电池产量23GW,而我国光伏组件产量达到11GW,在全球光伏市场低迷、欧债危机和美国“双反”的不利国际环境下,依然占据了近50%的份额,且取得了37%的年增幅。
在市场没有启动的情况下,这不能不说是我国光伏产业的骄傲。
但是,光环之下也笼罩着阴影。
虽然目前中国太阳能光伏产业规模居全球第一,但产业链发展不协调,且产业整体技术薄弱。
作为中国第一批专业学习光电知识的本科生,我们感觉到理论知识和实际的应用之间还隔着很宽的一条河。
所以我们把大部分业余时间放在了光伏产品的实际应用中,在应用中发挥我们的专业特长,希望为中国光伏技术行业的进步付出一点点的努力。
暑假也许是很多学生在家里陪家人的时间,但我们光电专业的四名同学经过不断的努力,顺利进入中国节能太阳能科技(镇江)有限公司实习。
在实习的过程中,我们发现公司对新员工的培养很重视,每当有新员工进入公司,公司都会安排专门的指导老师,跟踪指导新员工的学习。
作为新员工入职都要经历一个学习成长过程。
所以我们写这本书来总结一下技术人员或其他相关人员进入公司所要学习的一些技术活,以此来帮助新员工更快的掌握这些知识,熟悉日常工作的内容。
同时也方便光伏组件企业更快的培养一个合格的技术人员。
本书共分为十三个章节,这十三个章节是按照光伏组件的工艺流程展开,每个流程为一个章节。
在每个章节的开始都会简单的介绍一个这个工艺流程的大概情况,以供新员工能够了解相关的行业知识,更加方便的接受工艺技术。
柔性太阳能电池封装工艺简介

柔性衬底材料
• 金属及其合金 • 金属与合金柔性材料用于薄膜太阳能电池衬底,可以使用 较高的衬底温度沉积电池薄膜材料。金属类衬底主要有不 锈钢、钛、铝、镍、锌、钼、铬、Inconel合金( 61%Ni,22%Cr,9% Mo,5% Fe)等[ 5]。不锈钢具有耐高温、耐腐蚀、导电性能优越、延展 性好及成本低廉等优点,不锈钢成为薄膜太阳能电池柔性 衬底的首选材料。以不锈钢作为薄膜太阳能电池衬底,有 利于实现柔性电池卷对卷(roll-torol1)的 生产工艺,对电池的大面积连续生产更具有经济价值。
柔性太阳能电池组件封装方法
CIGS柔性电池组件封装方法:
• 电池片切割:将整块电池切成所需要的尺寸 • 电池片直接的链接:超声焊接机 • 层封:将做好的电池衬底(帆布料)经卷压封装机与 Tedlar层压封装 • 安装接线头或接线盒:接线盒主要是用来连出导线的,盒 内有装反向二极管,防止太阳能电池片串与串之间电流的 ,再一个也要和太阳能电池相搭配,既美观又实用,接线 方便。
• • • • • • 引线键合基本要求有: (1)首先要对焊盘进行等离子清洗; (2)注意焊盘的大小,选择合适的引线直径; (3)键合时要选好键合点的位置; (4)键合时要注意键合时成球的形状和键合强度; (5)键合时要调整好键合引线的高度和跳线的成线 弧度。
键合工艺
• 常用的引线键合设备有热压键合、超声键合和热 超声键合。 • 引线键合工艺有球键合工艺和楔键合工艺两种。 • 球键合一般采用D75μm以下的细Au丝。主要是 因为其在高温受压状态下容易变形、抗氧化性能 好、成球性好。球键合一般用于焊盘间距大于 100μm的情况下。目前也有用于50μm焊盘间距 的例子。
封装工艺概述
⑷ 钢化玻璃/EVA/电池/EVA/普通玻璃
- 1、下载文档前请自行甄别文档内容的完整性,平台不提供额外的编辑、内容补充、找答案等附加服务。
- 2、"仅部分预览"的文档,不可在线预览部分如存在完整性等问题,可反馈申请退款(可完整预览的文档不适用该条件!)。
- 3、如文档侵犯您的权益,请联系客服反馈,我们会尽快为您处理(人工客服工作时间:9:00-18:30)。
太阳能电池组件封装工艺研究
太阳能电池组件封装工艺研究
摘要:太阳能电池组件线又叫封装线,封装是太阳能电池生产中的关键步骤,没有良好的封装工艺,多好的电池也生产不出好的组件板。
电池的封装不仅可以使电池的寿命得到保证,而且还增强了电池的抗击强度。
产品的高质量和高寿命是赢得可客户满意的关键,所以组件板的封装质量非常重要。
关键词:太阳能;电池组件;封装工艺
中图分类号:TK511文献标识码:A文章编号:
引言:
太阳能发电是一种新型能源,具有环保、节能、取之不尽、用之不竭等特点,在当前世界范围资源紧缺的环境下,太阳能发电以其固有的特点赢得了多数使用者的青睐。
太阳能电池组件是太阳能发电系统中的核心部分,也是太阳能发电系统中价值最高的部分,其作用是将太阳能转化为电能,在推广及普及太阳能发电过程中必不可少。
太阳能电池组件在生产过程中需要将太阳能电池片夹在保护背板和表面透明材料之间,并保持牢固密封的状态,以达到隔离空气、保护电池片、增加透光率、延长寿命的目的。
随着技术的不断进步,太阳能电池组件的封装工艺不断的推陈出新,逐渐走向成熟,本文重点探讨一种新的太阳能电池封装工艺。
1.封装损失的分析
常规晶体硅太阳电池组件的封装结构如图一所示,自上而下的顺序分别是钢化玻璃-密封胶-晶体硅太阳电池-密封胶-背板;封装之前的单焊、串焊工艺将电池片通过涂锡焊带连接;组件层压封装好后,再组装上接线盒、边缘密封胶和边框。
因此,造成组件封装损失的可能因素无外乎是太阳电池和组件的封装材料。
我们把封装损失的原因按照属性不同分为两大类:光学损失、电学损失。
下面详细讨论这两类中的各种影响因素。
2.现有技术
太阳能电池组件封装按照玻璃、EVA、电池串、EVA、背板的顺序敷设,通过层压机抽真空加热使EVA熔化,将玻璃、电池串及背板封装在一起。
在加热使EVA熔化过程中,随着EVA流动及层压机施加的压力会使太阳能电池片偏离预定位置,可能造成电池片之间彼此接触,不仅影响外观,还会发生短路现象,影响太阳能电池组件的正常使用。
同时太阳能电池在上述生产过程后还要使用专用设备,消耗大量铝材对其进行装配边框工作,铝边框装配完毕后还需要专门工序粘接接线盒,组装过程工序多、消耗时间长,工作效率相对较低。
现在太阳能电池组件已经得到大范围的应用,生产厂家在生产出了大量优质的太阳能电池组件的前提下,也不可避免地在生产过程中产生的大量待处理的残次废品,同时根据太阳能电池组件的平均使用寿命为二十五年的情况,随着太阳能电池组件的寿命日益临近,对它们的回收处理及综合利用等问题摆在了人们面前。
若干年后,达到使用寿命年限后废弃的太阳能电池组件将形成大量的工业垃圾,如果处理不当,会造成危害自然环境的严重问题,给人类社会带来沉重的负担。
同时,废弃太阳能电池组件问题如果不能够很好的回收解决,太阳能源的综合利用亦不会成为终身清洁能源,对我们新能源发展战略存在不利影响。
3.新工艺研究
为了改善传统太阳能电池封装工艺的缺点,降低成本,同时便于后期回收,本研究利用热致性耐高温改性液晶高分子聚合物LCP优异的物理、化学和电气性能经过注塑成型工艺,加工成太阳能电池组件专用底板,替代传统太阳能电池组件的背板、接线盒、铝边框等使用材料,实现太阳能电池封装的一种工艺。
3.1设计方案。
本设计在专用底板结构设计上综合了常规太阳能电池组件的背板、接线盒与边框的功能,同时特别增加了电池片固定槽和保护支撑架,电池片固定槽和保护支撑架同时保证了与太阳能
电池组件表面封装钢化玻璃的间隙刚好容纳电池片和焊带的厚度,全面保护电池片与焊带不会被进行层压工序时产生的真空负压损坏。
本设计主要由电池片固定槽、保护支撑架、汇流带线槽、EVA容纳槽、边框、接线盒等几部分组成。
电池片固定槽用来放置电池片,和四周保护支撑架配合,固定电池片,电池片固定槽的尺寸可根据要放置的电池片的大小尺寸进行不同规格的生产。
保护支撑架将表面封装玻璃支撑起来在,在抽真空产生负压的情况下保护电池片不被损坏。
汇流带线槽是汇流带及焊带的走线槽,防止因汇流带或焊带的不平影响封装效果。
经容量计算的EVA容纳槽用来放置EVA胶条,同时约束EVA 高温熔化后的流向,确保使用最少量的EVA达到最佳的密封效果。
边框用来和使用设备相连,固定本太阳能电池组件。
接线盒为电源的引出线位置。
3.2生产流程。
根据要制作太阳能电池组的图纸用LCP材料注塑成为太阳能电池组件用底板,将串接好的太阳能电池串放置到LCP底板电池片固定槽及汇流带线槽内,在EVA容纳槽内敷设EVA胶条,在正面盖上封装玻璃。
在层压机内抽真空加热,高温使EVA熔化,完成太阳能电池组件的封装,经过检测合格后即可入库。
3.3新工艺优点。
本研究通过改变使用材料,改善结构设计,和现有工艺相比有较明显优势。
(1)新材料优势。
新型太阳能电池封装工艺采用改性液晶高分子聚合物LCP注塑加工成型,综合接线盒、边框与底板功能,生产周期短,自动化程度高;LCP材料具有优良的电绝缘性能,可使太阳能电池组件免装接地线。
其介电强度比一般工程塑料高,耐电弧性良好。
在连续使用温度200—300℃,其电性能不受影响。
间断使用温度可316℃左右;LCP材料具有自增强性:具有异常规整的纤维状结构特点,因而不增强的液晶塑料即可达到甚至超过普通工程塑料用百分之几十玻璃纤维增强后的机械强度及其模量的水平;LCP材料具有优良的热稳定性、耐热性及耐化学药品性,对大多数塑料存在的蠕变特点,液晶材料可以忽略不计,而且耐磨、减磨性均优异;LCP材料的耐气候性、耐辐射性良好,具有优异的阻燃性,能熄灭火焰而不再继续进行燃烧。
其燃烧等级达到UL94V—0级水平;LCP材料具有突出的耐腐蚀性能,LCP制品在浓度为90%酸及
浓度为50%碱存在下不会受到侵蚀,对于工业溶剂、燃料油、洗涤剂及热水,接触后不会被溶解,也不会引起应力开裂,完全适应太阳能电池组件的户外环境使用要求。
(2)节约材料、降低成本。
新工艺设计可减少95%EVA的使用,同时不再使用背板材料,节省原材料,降低成产成本;不再使用铝型材边框和接线盒,省掉装配铝边框工序和安装接线盒工序,节省了生产时间,提高了工作效率(3)提高成品率、利于回收。
利用电池片固定槽周边的凸起支撑全面保护电池片与焊带不会被真空负压损坏,同时防止太阳能电池片移动,提高了太阳能电池组件的成品率;因为EVA的用量及密封面积很小,只需加热到150度,破坏真空即可将玻璃与底板轻易分离,同时暴露出太阳能电池片、汇流带等,所有材料均可较为容易的分离后回收再利用。
4.结束语
一种新型的太阳能电池封装工艺,通过采用液晶高分子聚合物注塑底板,通过特殊的结构设计提高产品的成品率,且较易于回收重新利用,保护环境,具有较大的发展前景。
参考文献:
[1]施永明,赵高凌,沈鸽,张溪文,翁文剑,杜丕一,韩高荣;染料敏化纳米薄膜太阳能电池的研究进展[J];材料科学与工程;2002年01期.
[2]倪萌;LEUNG Michael;;染料敏化太阳电池纳米结构对输出特性的影响[J];电源技术;2006年09期.
------------最新【精品】范文。