失效模式与效应分析作业程序
失效模式和效应分析模式预防CCU重症患者失禁相关性皮炎的效果
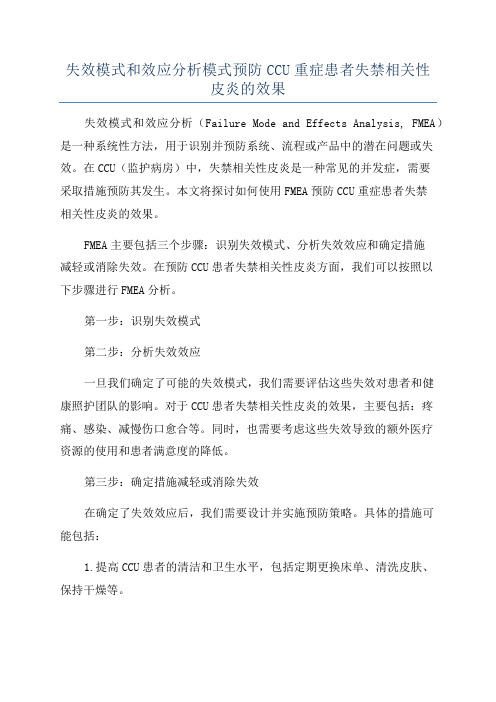
失效模式和效应分析模式预防CCU重症患者失禁相关性皮炎的效果失效模式和效应分析(Failure Mode and Effects Analysis, FMEA)是一种系统性方法,用于识别并预防系统、流程或产品中的潜在问题或失效。
在CCU(监护病房)中,失禁相关性皮炎是一种常见的并发症,需要采取措施预防其发生。
本文将探讨如何使用FMEA预防CCU重症患者失禁相关性皮炎的效果。
FMEA主要包括三个步骤:识别失效模式、分析失效效应和确定措施减轻或消除失效。
在预防CCU患者失禁相关性皮炎方面,我们可以按照以下步骤进行FMEA分析。
第一步:识别失效模式第二步:分析失效效应一旦我们确定了可能的失效模式,我们需要评估这些失效对患者和健康照护团队的影响。
对于CCU患者失禁相关性皮炎的效果,主要包括:疼痛、感染、减慢伤口愈合等。
同时,也需要考虑这些失效导致的额外医疗资源的使用和患者满意度的降低。
第三步:确定措施减轻或消除失效在确定了失效效应后,我们需要设计并实施预防策略。
具体的措施可能包括:1.提高CCU患者的清洁和卫生水平,包括定期更换床单、清洗皮肤、保持干燥等。
2.降低摩擦和剪切力的作用,例如使用垫子、特殊的床垫和床垫覆盖物。
3.尽量减少或消除患者长时间卧床的情况。
可以通过定期帮助患者翻身、进行被动运动等方法来实现。
4.加强患者和护理人员的教育,提高意识,例如正确的清洁和保养皮肤的方法、坐垫使用等。
这些措施的实施需要一个团队的协作,包括护士、医生、患者和家属。
另外,我们还需要监控和评估这些措施的效果。
定期检查患者的皮肤状况、回顾和分析发病率等数据可以帮助我们了解是否需要进一步改进和调整预防策略。
总结起来,采用FMEA方法进行失效模式和效应分析,可以帮助预防CCU重症患者失禁相关性皮炎的发生。
通过识别失效模式、分析失效效应和确定相应措施,我们可以减少失禁相关性皮炎的发病率,提高护理质量和患者满意度。
FMEA失效模式和效应分析

1 of 19項 目:過程責任:生產準備者:部 門:制一部零件號:關鍵日期:FMEA 日期:中心隊員:FMEA 編號: 0606242 of 19項 目:過程責任:生產準備者:部 門:制一部零件號:關鍵日期:FMEA 日期:中心隊員:FMEA 編號: 0606243 of 19項 目:過程責任:生產準備者:部 門:制一部零件號:關鍵日期:FMEA 日期:中心隊員:FMEA 編號: 0606244 of 19項 目:過程責任:生產準備者:部 門:制一部零件號:關鍵日期:FMEA 日期:中心隊員:FMEA 編號: 0606245 of 19項 目:過程責任:生產準備者:部 門:制一部零件號:關鍵日期:FMEA 日期:中心隊員:FMEA 編號: 0606246 of 19項 目:過程責任:生產準備者:部 門:制一部零件號:關鍵日期:FMEA 日期:中心隊員:FMEA 編號: 0606247 of 19項 目:過程責任:生產準備者:部 門:制一部零件號:關鍵日期:FMEA 日期:中心隊員:FMEA 編號: 0606248 of 19項 目:過程責任:生產準備者:部 門:制一部零件號:關鍵日期:FMEA 日期:中心隊員:FMEA 編號: 0606249 of 19項 目:過程責任:生產準備者:部 門:制一部零件號:關鍵日期:FMEA 日期:中心隊員:FMEA 編號: 06062410 of 19項 目:過程責任:生產準備者:部 門:制一部零件號:關鍵日期:FMEA 日期:中心隊員:FMEA 編號: 06062411 of 19項 目:過程責任:生產準備者:部 門:制一部零件號:關鍵日期:FMEA 日期:中心隊員:FMEA 編號: 06062412 of 19項 目:過程責任:生產準備者:部 門:制一部零件號:關鍵日期:FMEA 日期:中心隊員:FMEA 編號: 06062413 of 19項 目:過程責任:生產準備者:部 門:制一部零件號:關鍵日期:FMEA 日期:中心隊員:FMEA 編號: 06062414 of 19項 目:過程責任:生產準備者:部 門:制一部零件號:關鍵日期:FMEA 日期:中心隊員:FMEA 編號: 06062415 of 19項 目:過程責任:生產準備者:部 門:制一部零件號:關鍵日期:FMEA 日期:中心隊員:FMEA 編號: 06062416 of 19項 目:過程責任:生產準備者:部 門:制一部零件號:關鍵日期:FMEA 日期:中心隊員:FMEA 編號: 06062417 of 19項 目:過程責任:生產準備者:部 門:制一部零件號:關鍵日期:FMEA 日期:中心隊員:FMEA 編號: 06062418 of 19項 目:過程責任:生產準備者:部 門:制一部零件號:關鍵日期:FMEA 日期:中心隊員:FMEA 編號: 06062419 of 19項 目:過程責任:生產準備者:部 門:制一部零件號:關鍵日期:FMEA 日期:中心隊員:FMEA 編號: 060624。
失效模式与效应分析程序FMEA资料
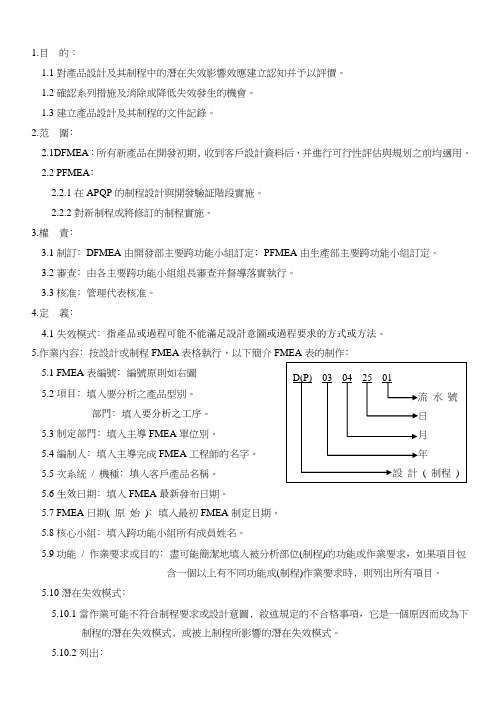
1.目的:1.1對產品設計及其制程中的潛在失效影響效應建立認知并予以評價。
1.2確認系列措施及消除或降低失效發生的機會。
1.3建立產品設計及其制程的文件記錄。
2.范圍﹕2.1DFMEA:所有新產品在開發初期﹐收到客戶設計資料后,并進行可行性評估與規划之前均適用。
2.2 PFMEA﹕2.2.1在APQP的制程設計與開發驗証階段實施。
2.2.2對新制程或將修訂的制程實施。
3.權責﹕3.1制訂﹕DFMEA由開發部主要跨功能小組訂定﹔PFMEA由生產部主要跨功能小組訂定。
3.2審查﹕由各主要跨功能小組組長審查并督導落實執行。
3.3核准﹕管理代表核准。
4.定義﹕4.1失效模式﹕指產品或過程可能不能滿足設計意圖或過程要求的方式或方法。
5.作業內容﹕按設計或制程FMEA表格執行,以下簡介FMEA表的制作﹕5.2項目﹕填入要分析之產品型別。
部門﹕填入要分析之工序。
5.3制定部門﹕填入主導FMEA單位別。
5.4編制人﹕填入主導完成FMEA工程師的名字。
5.5次系統/ 機種﹕填入客戶產品名稱。
5.6生效日期﹕填入FMEA最新發布日期。
5.7 FMEA日期( 原始)﹕填入最初FMEA制定日期。
5.8核心小組﹕填入跨功能小組所有成員姓名。
5.9功能/ 作業要求或目的﹕盡可能簡潔地填入被分析部位(制程)的功能或作業要求,如果項目包含一個以上有不同功能或(制程)作業要求時﹐則列出所有項目。
5.10潛在失效模式﹕5.10.1當作業可能不符合制程要求或設計意圖﹐敘述規定的不合格事項,它是一個原因而成為下制程的潛在失效模式﹐或被上制程所影響的潛在失效模式。
5.10.2列出﹕5.10.2.1每一潛在失效模式假設失效是將發生的﹐但不是必須發生的。
5.10.2.2盡可能敘述失效模式發生于某些作業條件下(如﹕壓力等)和在某些使用條件下(如﹕溫度,高度)。
5.10.2.3一般失效模式含如下各項﹐但不限于此﹕破損、變形、碰傷、錯位、裂紋等。
PFMEA教程(五大工具)
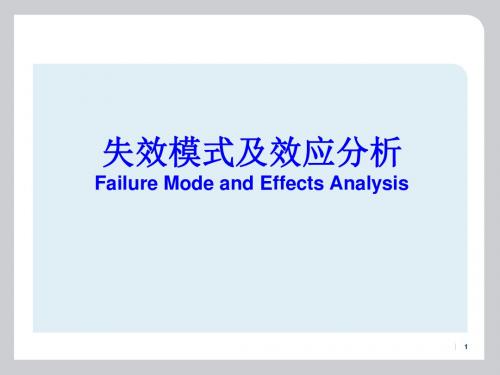
Smiths Interconnect
21
2.4 PFMEA的实施步骤(4)
4.PFMEA的制程项目/功能
•根据流程图简单描述被分析的制程或作业。 •PFMEA小组应当审查适用的作业、材料、制程、环境和安全标准。 •尽可能简单地说明该将被分析制程或作业的目的。 •不同潜在失效模式的作业,独立列出。
Smiths Interconnect
18
2.4 PFMEA的实施步骤(1)
1.PFMEA的开始
• PFMEA的开始列出过程希望做什么?即:过程意图 • PFMEA应该从整個制造过程的流程图开始。 – 流程图应该包括每个作业站有关的产品/过程特性
– 用于PFMEA准备工作的流程图的附件应该随附于PFMEA中。
Smiths Interconnect
24
2.4 PFMEA的实施步骤(7)
7.发生率评价(O)
可能性 很高:持续性失效 发生周期 多于每天一次 发生概率 >30% 分数 10
每3–4天发生一次
每星期发生一次
≤30%
≤ 5% ≤ 1% ≤ 0.03% ≤ 0.01% ≤ 0.006% ≤ 6ppm ≤ connect
22
2.4 PFMEA的实施步骤(5)
5.PFMEA的失效效应和后果讨论填写
潜在失效效应:是指失效模式对顾客的影响。 顾客:是下一个作业、后续的作业,每一个对象均应考虑到。
填写其中最严重 的效应即可
效应一
失效模式
效应二 效应三
Smiths Interconnect
修正 FMEA1 各项未考虑的失效 模式的发现、评审 和更新
修正 FMEA2
时间
各项未考虑的失效 模式的发现、评审 和更新
PFMEA失效模式与效应分析
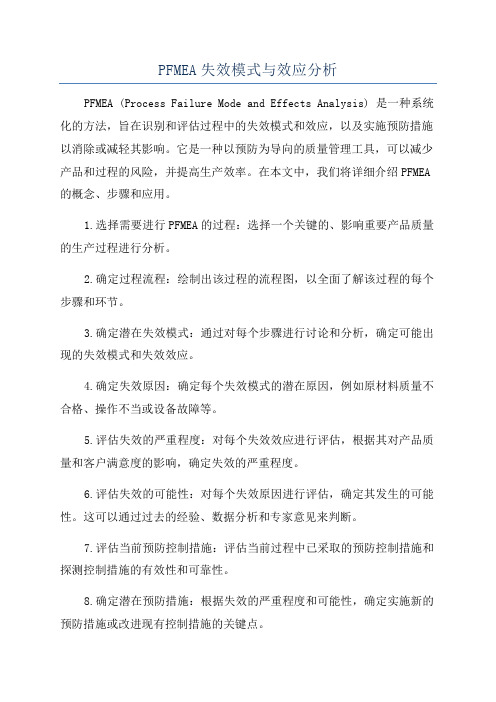
PFMEA失效模式与效应分析PFMEA (Process Failure Mode and Effects Analysis) 是一种系统化的方法,旨在识别和评估过程中的失效模式和效应,以及实施预防措施以消除或减轻其影响。
它是一种以预防为导向的质量管理工具,可以减少产品和过程的风险,并提高生产效率。
在本文中,我们将详细介绍PFMEA 的概念、步骤和应用。
1.选择需要进行PFMEA的过程:选择一个关键的、影响重要产品质量的生产过程进行分析。
2.确定过程流程:绘制出该过程的流程图,以全面了解该过程的每个步骤和环节。
3.确定潜在失效模式:通过对每个步骤进行讨论和分析,确定可能出现的失效模式和失效效应。
4.确定失效原因:确定每个失效模式的潜在原因,例如原材料质量不合格、操作不当或设备故障等。
5.评估失效的严重程度:对每个失效效应进行评估,根据其对产品质量和客户满意度的影响,确定失效的严重程度。
6.评估失效的可能性:对每个失效原因进行评估,确定其发生的可能性。
这可以通过过去的经验、数据分析和专家意见来判断。
7.评估当前预防控制措施:评估当前过程中已采取的预防控制措施和探测控制措施的有效性和可靠性。
8.确定潜在预防措施:根据失效的严重程度和可能性,确定实施新的预防措施或改进现有控制措施的关键点。
9.优先级排序和实施措施:根据失效的严重程度、可能性和控制可靠性,对预防措施进行优先级排序,并制定实施计划。
10.跟踪和监测措施的实施效果:实施预防措施后,跟踪和监测结果,确保措施的有效性和可持续性。
1.产品设计阶段:在产品设计和开发阶段使用PFMEA可以识别潜在的设计缺陷,提前采取措施来确保产品质量和可靠性。
2.工艺优化和改进:通过对生产过程进行PFMEA,可以发现可改进的环节和潜在的问题,从而优化生产效率和质量。
3.新生产线的引入:在引入新的生产线或设备时,使用PFMEA可以帮助识别潜在的问题和风险,确保新工艺的稳定性和可靠性。
91制程失效模式与效应分析作业办法
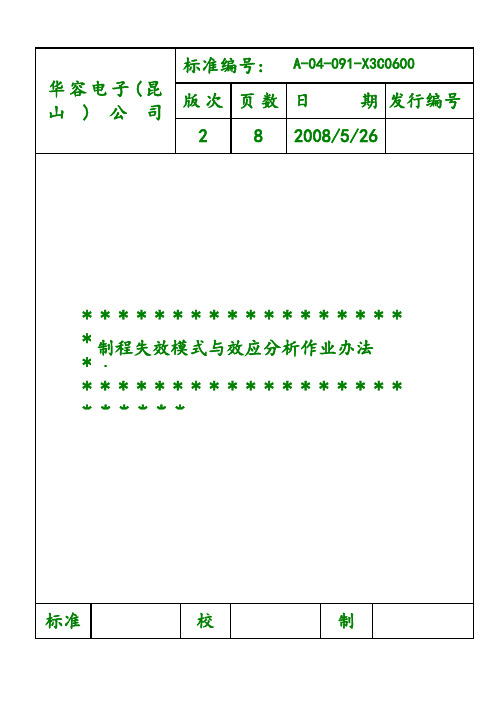
1.目的:1-1.对失效的产品进行分析,找出零组件之失效模式,监定出它的失效原因,研究该项失效模式对系统会产生什么影响1-2.失效分析在于找出零组件或系统的潜在弱点,提供设计、制造、品保等单位采取可行之对策.2.范围:新产品的试制、量产以及客户报怨等各阶段均属之.3.权责:3-1.由品管部QE制订制程FMEA3-2.由该部门主管审查制程FMEA3-3.由厂长核准制程FMEA4.定义:4-1.失效是指在规定条件下(环境、操作、时间)不能完成既定功能,产品之参数值不能维持在规定的上下限之间,产品在工作范围内,导致零组件的破裂、断裂、卡死等损坏现象.4-2.顾客:一般指“最终使用者”,也可以是后续的或下一制造或装配工序,以及服务工作.是“失效模式与效应分析“的英文名称缩写,PFME指制程FMEA5.相关文件:5-1.“失效模式与效应分析”技术手册6.内容:6-1.实施PFMEA的时机,一般在生产工装准备之前,或制程可行性分析之前的作用:a.确定与产品相关的制程潜在失效模式.b.评价失效对顾客的潜在影响.c.确定潜在制造或装配制程失效的起因,确定减少失效发生或找出失效条件的制程控制变量.d.编制潜在失效模式分级表,然后建立考虑纠正措施的优先体系.e.将制造或装配过程的结果编制成文件.编号:a.填入FMEA文件编号,以便可以追踪使用.b.制程FMEA表编号方法:采用7位码,分别表示如下:部门别年月流水号6-4.产品名称:填入将被分析的制程系统,子系统或零件名称和编号.6-5.责任部门:填入责任单位、部门或小组,也包括供应商名称.6-6.页码:本PFMEA共几页,此为第几页.6-7.产品类型:填入将被分析的产品类别和规格.6-8.关键日期:填入初次FMEA预定完成日期,该日期不应超过计划开始生产的日期.6-9.编制:填入负责准备FMEA工作的主管或助理工程师的姓名、电话或公司名称.日期:填入编制FMEA原始稿的日期及最新修订的日期.6-11.主要参加人(即CFT小组成员)列出有权确定和执行任务的责任部门和个人姓名(建议将所有成员姓名、部门、电话、地址等另行列表)6-12.制程功能/要求填入被分析的过程或工序的简单描述.尽可能简单地说明该制程或作业的目的,当制程包括许多具有不同失效模式的作业时,可以将这些作业作为独立的制程处理.6-13.潜在失效模式为制程中可能发生的不满足制程要求或设计意图的模式,是对某具体作业不符合要求的描述.它可能是引起下一个作业的潜在失效模式或者可能是上一道工序潜在失效的后果.无论如何,在FMEA准备中,应假设原材料都是合格的.根据零部件、子系统及系统的工艺特性列出对应特定作业的每一个潜在失效模式.制程工程师或小组要提出并回答下列问题:a.制程或零组件为何不符合规格b.假设不考虑工程规范,顾客(最终使用者、后续工序或服务),会提出什麽异议.注:典型的失效模式可能有下列情况:变形、断裂、开路、短路、粘合、弯曲、灰尘等.6-14.潜在失效效应:a.潜在失效效应是指失效模式对顾客的影响.这里的顾客指下一道工序,后续工序或工位、代理商、或最终用户.在评价潜在失效效应时这些因素都必须考虑.b.应根据顾客可能注意的或经历的情况来描述失效的效应.对最终使用者而言,失效的效应用产品或系统的性能来描述,如:杂音、工作不正常、不起作用、不稳定、外观不良、粗糙费力、异味、工作减弱、间歇性工作等.c.若顾客是下一道工序或后续工序/工位,失效的效应用工艺/工序性能来描述,如:不配合、不连接、不区配、损坏设备、危害操作者、无法加工等.6-15.严重度(severity)严重度是潜在失效模式对顾客的影响后果(效应)的严重程度.严重度仅适用于失效的后果,严重度评估分为“1”到“10”级.评估准则如下表:统的一些特殊制程特性进行分级的.若在制程FMEA中确定了某一分级,应通知设计主管或工程师,因为它可能影响有关确定管制项目标识的工程文件.注:分级方式常用的有:a.关键、一般.b.重要、次要c.特殊、一般d.主要、次要6-17.潜在失效原因潜在失效的原因是指失效是怎麽发生的,并根据可纠正或管制的原则来描述.针对每一个潜在失效模式,在尽可能广的范围内列出每个可以想到的失效原因,/典型的失效原因有:a.不当的扭力,过大或过小.b.焊接不当,电流、时间、压力不正确.c.不精确的量测d.零组件漏装或错装列表时应明确记录具体的错误或误操作情况,不应用一些含糊不清的词语(如:操作者错误、机器工作不正常).6-18.发生率(OCCURRENCE)发生率是指具体的失效原因发生的频率,可分“1”到“10”级来估计发生率的大小,只有导致相应失效模式的发生,才能考虑发生率分级.评估准则如下表:现行制程管制是尽可能预防失效模式的发生,或探测将发生的失效模式的管制的描述,这些管制方法可以类似防错夹具之类的制程管制方法,或者统计制程管制(SPC),也可是制程评价,评价可在目标工序进行,也可在后续工序进行.有三种制程管制方法可考虑:a.预防失效原因或失效模式/效应的发生,或降低其发生率b.查明失效原因,并提出矫正措施c.查明失效模式较好的做法是首先使用上述的a种管制方法,其次使用上述b种方法最后才使用上述c种管制方法.6-20.检出率a.检出率是指在零组件离开制造工序或装配工位之前,用管制方法找出失效原因的可能性的评价指标;或用管制方法找出后序发生的失效模式的可能性的评价指标.b.评价指标分“1”到“10”级,评价准则如下表风险优先数是严重度数(S)、频度数(O)和不易探测度数(D)之乘积 RPN=(S)X(O)X(D)是一项制程风险的指标,RPN取值在“1”到“1000”之间.如果RPN>100时,工程人员应采取纠正措施降低RPN值.在一般实践中,不管RPN的结果如何,当严重度(S)>=9时,就应于以改善.6-22.建议改善措施及优先顺序a.当失效模式依RPN值排列其风险优先次序时,针对最高等级的影响和关键项目采取矫正措施.任何建议措施的目的都是为了减小严重度.b.在任何情况下,若失效模式的效应会危害制程/作业人员,应采取矫正措施,消除或控制失效模式的原因,以阻止其发生;或明确规定适当的作业保护措施.c.下列措施予以考虑:(a).为了减小失效发生可能性,需修改制程或设计(b).只有修改设计或工艺制程,才能减小严重度数(c).为了增加探测失效的可能性,需修改制程或设计.通过改善探测管制方法达到产品品质改善是不经济的且效果较差.增加品质管制检验频率不是良好矫正措施.统计制程管制及制程改善等永久性的矫正措施才是必需的.6-23.责任(对建议措施)及目标完成日期填入负责建议措施的单位和个人以及预计完成的日期.6-24.采取措施实施一项措施,简要记载具体的执行情况和生效日期.的结果将矫正措施实施后,填入简短的执行作业和生效日期、频度、严重度及不易探测度,计算并记录RPN之值.另有必要考虑进一步的措施,只要重复“建议改善措施及优先顺序”到“采取措施”步骤即可.6-26.追踪工程主管工程师应负责所有措施已实施或落实.FMEA是一个不断完善和发展的文件,应时刻体现最新的改善状况及矫正措施的实施情况.7.附件:7-1.制程FMEA表失效模式及效应分析表(制程FMEA) FMEA编号:产品名称: 责任部门: 页码:产品类型: 关键日期: 编制:FMEA日期(编制): (修订):主要参加人:。
潜在的失效模式与效应分析

潜在的失效模式与效应分析潜在的失效模式与效应分析(FMEA)(Failure Mode and Effects Analysis)是一种用于识别和评估潜在失效模式及其对系统或过程性能的影响的方法。
它被广泛应用于各个行业,包括制造业、汽车工业、医疗保健等,用于提前预防潜在的问题和缺陷,减少风险和成本。
FMEA方法通过系统地识别可能的失效模式、评估其严重性、确定其潜在的原因和效应,并制定相应的预防措施和应对措施来提升产品和过程的质量。
具体而言,FMEA步骤包括:1.确定分析对象:确定要进行FMEA分析的系统、产品、流程或部件。
2.建立团队:组建由跨职能团队成员组成的FMEA分析团队,以确保全面的视角和专业知识。
3.描述分析对象:对分析对象进行详细描述,包括功能、特性、运行条件等。
4.列举失效模式:通过头脑风暴或专家判断,列举所有可能的失效模式。
5.评估严重性:评估每个失效模式对系统或过程性能的影响,包括安全性、可靠性、维修性、性能等方面。
6.确定原因:分析每个失效模式的潜在根本原因,通过鱼骨图、5W1H分析等方法找出原因。
7.评估概率:评估每个失效模式发生的可能性,可以借助历史数据、统计分析等方法。
8.制定预防措施:针对每个失效模式,制定预防措施来减少失效概率或降低严重性。
9.制定应对措施:针对每个失效模式,制定应对措施,包括监测、检测、报警、维修等,以减少影响。
10.重新评估:根据预防和应对措施的实施情况,重新评估每个失效模式的概率和严重性,并对措施进行迭代改进。
FMEA方法的优势在于可以提前预防潜在的问题和缺陷,减少风险和成本。
通过系统地分析潜在失效模式和其效应,可以及早采取措施进行风险管理和改进,提高产品和过程的质量。
此外,FMEA还能够改善跨职能团队的沟通和协作,增强问题解决能力和质量意识。
然而,FMEA方法也存在一些潜在的局限性。
首先,FMEA方法无法准确预测未来的潜在失效模式和效应,而只能基于现有的经验和知识进行分析。
IATF16949失效模式和效果分析FMEA控制程序.docx
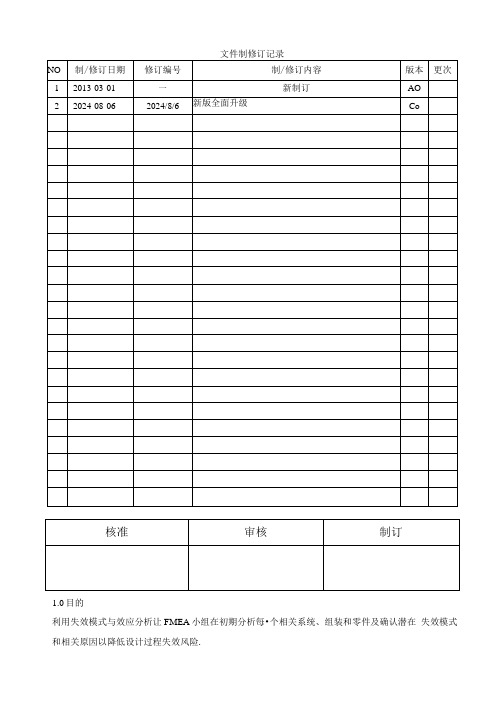
1.0目的利用失效模式与效应分析让FMEA小组在初期分析每•个相关系统、组装和零件及确认潜在失效模式和相关原因以降低设计过程失效风险.2.0适用范圉本公司所有汽车件五金系列新产品及新工艺均适用。
注:非汽车件产品不强制要求执行该程序.3.0权责FMEA小组负责FMEA运作.4.0定义4.1 FMEA:利用工程去分析产品零、组件可能失效的模式及原因,研究失效的模式对系统可能产生的影响及严重程度:4. 2失效4. 2.1在规定条件下(环境、操作、时间等)不能完成既定功能;4. 2. 2在规定条件卜.,产品参数值不能维持在规定的上卜限之间。
4. 2. 3产品在工作范围内,导致零组件如性能失效、重金属超标等正常规范以外之异常现象均属之。
4.3系统:此处专指FMEA之对象物,或为零件之某部位、或为零件、或为组合、或为总成、或为机构…。
4.3.1子系统:系统之构成件,如零件之对组合,组合之对总成等,为上游工程(前制程)状态。
5.0作业内容5.1失效模式与效应分析不是依靠制程管制来克服,是用现有技术或考虑制造及组装过程的限制来减少设计上潜在的问题,如:5.1.1需要的工艺流程图:5.1.2组装的空间或要求的工具:5. 1.3产品材料的限制:5.L 4制程能力或效能。
5.2FMEA 编号:6. 2.1填入FMEA文件编号以便可以追踪使用:7. 2. 2 FMEA表编号,依产品编订.8.3型别:填入要分析设计产品型别.5.4FMEA日期:填入最初FMEA被完成日期,和最新被修订日期。
5.5关键日期:填入FMEA计划完成的日期。
该日期不能超过开始计划生产日期。
5.6项目N0:以流水号厂99方式编入。
同一项目再细分时允许以“一”(允号)方式编号,例4T, 4-2, 4-3。
5.7部位(构成部品)名称:填入被分析之构成部品或工程名称,使用之名词应和预定发行之工程规格上所显示的相符.5. 8机能:尽可能简洁地依设计意图填入被分析部位的机能。
失效模式效应分析作业程序

xxxx 光电有限公司 xxxxxxxx OPTO-ELECTRONIC CO.,LTD.编 号:FDH-QP-RD-7101 版 本:1.1修订日期:2013/07/28 拟案单位:研发部 发 行 章:修订记录一、目的确定设计和生产过程相关的潜在失效模式和潜在制造或装配过程失效的机理/起因,评价潜在失效对顾客产生的后果和影响,采取控制来降低失效产生频度或失效条件探测度的过程变量和能够避免或减少这些潜在失效发生的措施。
二、范围产品开发过程中以及设计和生产过程中的各个过程、工序皆属之。
三、定义3.1 S(Severity):严重度; O(Occurrence):频度; D(Detection):可探测度。
3.2 RPN (Risk Prior Number):风险顺序系数。
3.3 在失效分析中,失效是指:在规定条件下,产品参数值不能维持在规定的上、下限范围内。
3.4 PFMEA:过程潜在失效模式与后果分析。
3.5 DFMEA:设计潜在失效模式与后果分析。
四、权责4.1跨功能小组:负责过程失效模式及后果分析(FMEA)的制定与评审。
4.2研发部:负责主导DFMEA之制定与维护。
4.3工程部:负责主导PFMEA之制定与维护。
五、内容5.1 FMEA作业流程图(续下页)FMEA作业流程图5.2流程说明:5.2.1 建立FMEA表单:根据《潜在失效模式及效应分析》来说明其实施方法。
(1) FMEA编号:填入FMEA文件的编号,以便查询(2) 项目名称:填入所分析的系统,子系统的过程名称。
(3) 过程责任部门:填入产生失效过程之发生部门。
(4) 编制者:填入负责编写FMEA的工作人员姓名。
(5) 关键日期:填入初次FMEA预定完成的日期,DFMEA为设计开发书中设计开发前1~2天;PFMEA为预计生产日期之前的任一日期。
(6) FMEA日期:填入编制FMEA原始稿的日期或最新修订日期,该日期要在关键日期当天或之前。
PFMEA文件
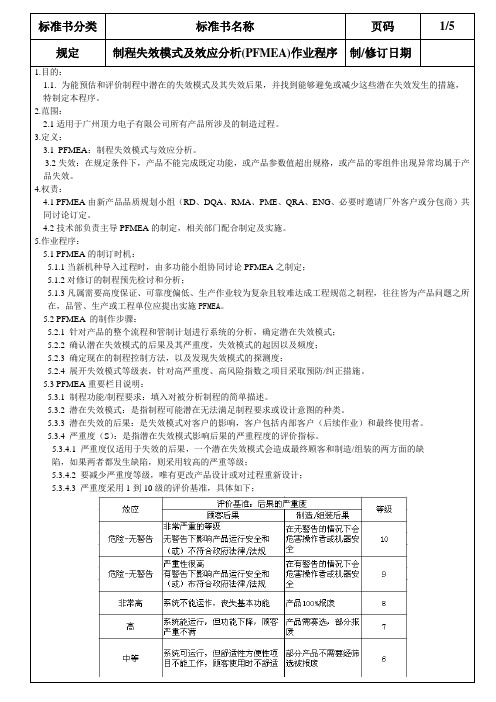
5.3.4.2要减少严重度等级,唯有更改ቤተ መጻሕፍቲ ባይዱ品设计或对过程重新设计;
5.3.4.3严重度采用1到10级的评价基准,具体如下;
标准书分类
标准书名称
页码
1/5
规定
制程失效模式及效应分析(PFMEA)作业程序
制/修订日期
5.3.5.分类:对要求额外制程管制的特殊性进行分类。
5.3.6.潜在失效起因:是指失效是怎么发生的,并按照能被矫正或控制的事情来描述。
5.3.7.频度(O):是指具体的失效起因发生的可能性。频度采用1到10级的评价基准,具体如下表:
5.3.8.现行制程控制:是对尽可能阻止失效模式或失效原因的发生/探测将发生的失效模式或失效原因的控制的描述,制程控制包括以下两种类型:
5.作业程序:
5.1PFMEA的制订时机:
5.1.1当新机种导入过程时,由多功能小组协同讨论PFMEA之制定;
5.1.2对修订的制程预先检讨和分析;
5.1.3凡属需要高度保证、可靠度偏低、生产作业较为复杂且较难达成工程规范之制程,往往皆为产品问题之所在,品管、生产或工程单位应提出实施PFMEA。
5.2PFMEA的制作步骤:
5.3.8.1.预防:预防失效起因或失效模式的出现,或减少它们的出现率。
5.3.8.2.控制:探测失效或失效的起因,并引导至纠正措施。
5.3.9.探测度(D):是指发现失效模式的难易程度,采用1~10级的评价基准:
标准书分类
标准书名称
页码
1/5
规定
制程失效模式及效应分析(PFMEA)作业程序
制/修订日期
5.2.1针对产品的整个流程和管制计划进行系统的分析,确定潜在失效模式;
失效模式与效应分析(failure modes and effects analysis,FMEA)
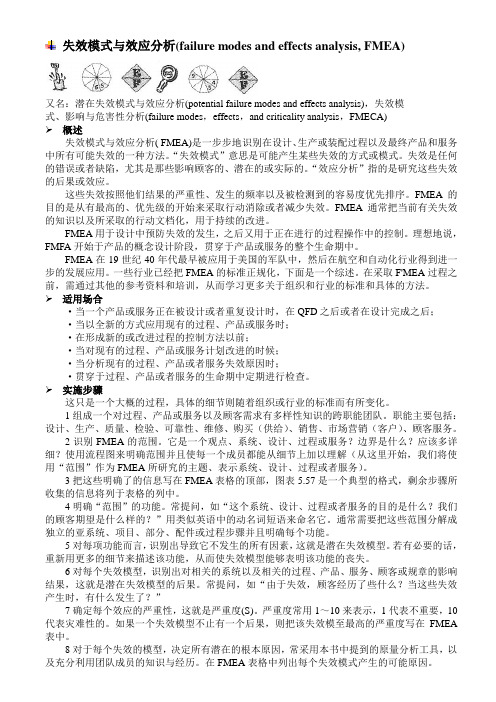
失效模式与效应分析(failure modes and effects analysis, FMEA)又名:潜在失效模式与效应分析(potential failure modes and effects analysis),失效模式、影响与危害性分析(failure modes,effects,and criticality analysis,FMECA)概述失效模式与效应分析( FMEA)是一步步地识别在设计、生产或装配过程以及最终产品和服务中所有可能失效的一种方法。
“失效模式”意思是可能产生某些失效的方式或模式。
失效是任何的错误或者缺陷,尤其是那些影响顾客的、潜在的或实际的。
“效应分析”指的是研究这些失效的后果或效应。
这些失效按照他们结果的严重性、发生的频率以及被检测到的容易度优先排序。
FMEA的目的是从有最高的、优先级的开始来采取行动消除或者减少失效。
FMEA通常把当前有关失效的知识以及所采取的行动文档化,用于持续的改进。
FMEA用于设计中预防失效的发生,之后又用于正在进行的过程操作中的控制。
理想地说,FMFA开始于产品的概念设计阶段,贯穿于产品或服务的整个生命期中。
FMEA在19世纪40年代最早被应用于美国的军队中,然后在航空和自动化行业得到进一步的发展应用。
一些行业已经把FMEA的标准正规化,下面是一个综述。
在采取F'MEA过程之前,需通过其他的参考资料和培训,从而学习更多关于组织和行业的标准和具体的方法。
适用场合·当一个产品或服务正在被设计或者重复设计时,在QFD之后或者在设计完成之后;·当以全新的方式应用现有的过程、产品或服务时;·在形成新的或改进过程的控制方法以前;·当对现有的过程、产品或服务计划改进的时候;·当分析现有的过程、产品或者服务失效原因时;·贯穿于过程、产品或者服务的生命期中定期进行检查。
实施步骤这只是一个大概的过程,具体的细节则随着组织或行业的标准而有所变化。
失效模式与效应分析FMEA作业程序
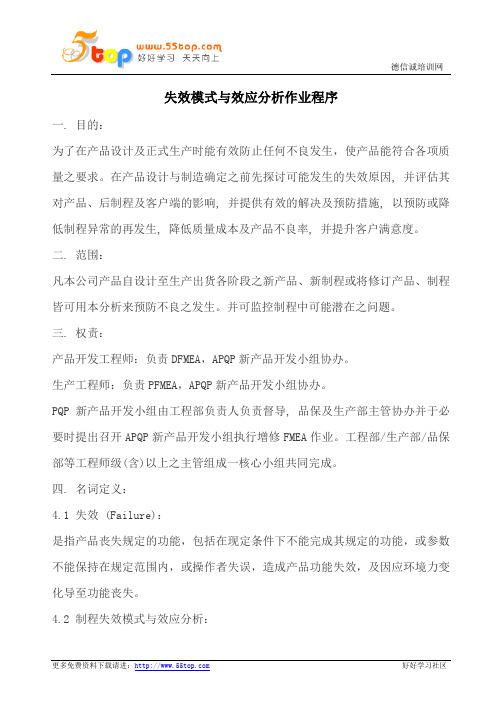
德信诚培训网
失效模式与效应分析作业程序
一. 目的:
为了在产品设计及正式生产时能有效防止任何不良发生,使产品能符合各项质量之要求。
在产品设计与制造确定之前先探讨可能发生的失效原因, 并评估其对产品、后制程及客户端的影响, 并提供有效的解决及预防措施, 以预防或降低制程异常的再发生, 降低质量成本及产品不良率, 并提升客户满意度。
二. 范围:
凡本公司产品自设计至生产出货各阶段之新产品、新制程或将修订产品、制程皆可用本分析来预防不良之发生。
并可监控制程中可能潜在之问题。
三. 权责:
产品开发工程师:负责DFMEA,APQP新产品开发小组协办。
生产工程师:负责PFMEA,APQP新产品开发小组协办。
PQP新产品开发小组由工程部负责人负责督导, 品保及生产部主管协办并于必要时提出召开APQP新产品开发小组执行增修FMEA作业。
工程部/生产部/品保部等工程师级(含)以上之主管组成一核心小组共同完成。
四. 名词定义:
4.1 失效 (Failure):
是指产品丧失规定的功能,包括在现定条件下不能完成其规定的功能,或参数不能保持在规定范围内,或操作者失误,造成产品功能失效,及因应环境力变化导至功能丧失。
4.2 制程失效模式与效应分析:
更多免费资料下载请进:好好学习社区。
PFMEA失效模式与效应流程文件
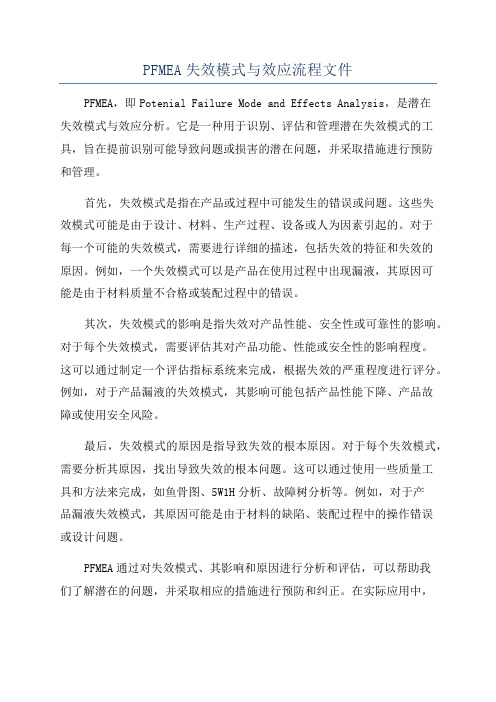
PFMEA失效模式与效应流程文件PFMEA,即Potenial Failure Mode and Effects Analysis,是潜在失效模式与效应分析。
它是一种用于识别、评估和管理潜在失效模式的工具,旨在提前识别可能导致问题或损害的潜在问题,并采取措施进行预防和管理。
首先,失效模式是指在产品或过程中可能发生的错误或问题。
这些失效模式可能是由于设计、材料、生产过程、设备或人为因素引起的。
对于每一个可能的失效模式,需要进行详细的描述,包括失效的特征和失效的原因。
例如,一个失效模式可以是产品在使用过程中出现漏液,其原因可能是由于材料质量不合格或装配过程中的错误。
其次,失效模式的影响是指失效对产品性能、安全性或可靠性的影响。
对于每个失效模式,需要评估其对产品功能、性能或安全性的影响程度。
这可以通过制定一个评估指标系统来完成,根据失效的严重程度进行评分。
例如,对于产品漏液的失效模式,其影响可能包括产品性能下降、产品故障或使用安全风险。
最后,失效模式的原因是指导致失效的根本原因。
对于每个失效模式,需要分析其原因,找出导致失效的根本问题。
这可以通过使用一些质量工具和方法来完成,如鱼骨图、5W1H分析、故障树分析等。
例如,对于产品漏液失效模式,其原因可能是由于材料的缺陷、装配过程中的操作错误或设计问题。
PFMEA通过对失效模式、其影响和原因进行分析和评估,可以帮助我们了解潜在的问题,并采取相应的措施进行预防和纠正。
在实际应用中,PFMEA通常以表格的形式进行编制,包括列出潜在的失效模式、其影响和原因,以及相应的预防和纠正措施。
总之,PFMEA是一种有助于识别、评估和管理潜在失效模式的工具。
通过对失效模式、其影响和原因的分析和评估,可以为产品开发和生产过程提供指导,并帮助我们提高产品的可靠性和质量。
失效模式与效应分析(HFMEA)范例

NO
4、该危害是否很明确,即使 缺乏控制也能轻易察觉?
YES
NOYES
继续进行HFMEA步骤5
stop
忘记取登机牌 该失效模式或步骤是否会造成 系统相当大的危害?(如危害 指数>8)4分
YES
NO
2、该项是否为整体流程中唯一 的一处弱点或关键?(一旦失 效会造成系统失败)
NO
NO
YES
3、是否已有有效Y的ES控制措施 YES
可侦测该失效模式的发生?
NO
4、该危害是否很明确,即使 缺乏控制也能轻易察觉?
YES
NOYES
继续进行HFMEA步骤5
stop
1旅行社将名字填错 该失效模式或步骤是否会造成 系统相当大的危害?(如危害 指数>8)4分
YES
NO
2、该项是否为整体流程中唯一 的一处弱点或关键?(一旦失 效会造成系统失败)
NO
YES
3、是否已有有效Y的ES控制措施 YES
可侦测该失效模式的发生?
NO
4、该危害是否很明确,即使 缺乏控制也能轻易察觉?
YES
NOYES
继续进行HFMEA步骤5
stop
HFMEA执行步
骤 流 失效 潜在原因 风险 分 决策树分析
程 模式
析
过安 有效证件 1、个人疏忽 检 丢失
严 发 危 问题 重 生 害 是否 性 率 指 为关
数 键点
4 14否
有无有 难检度: 是否 效 衡量 能否明显 进行 控制方 看出失效 矫正 法(监 (失败立 视器等) 即处置)
携带禁止 1、个人疏忽 登记的物 2、无乘机时禁
4 14否
品
失效模式以及效应分析(FMEA)作业方法
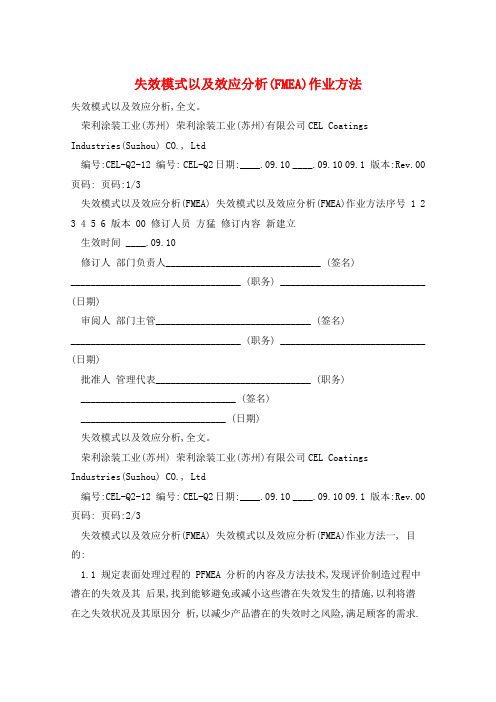
失效模式以及效应分析(FMEA)作业方法失效模式以及效应分析,全文。
荣利涂装工业(苏州) 荣利涂装工业(苏州)有限公司CEL CoatingsIndustries(Suzhou) CO., Ltd编号:CEL-Q2-12 编号: CEL-Q2日期:____.09.10 ____.09.10 09.1 版本:Rev.00 页码: 页码:1/3失效模式以及效应分析(FMEA) 失效模式以及效应分析(FMEA)作业方法序号 1 2 3 4 5 6 版本 00 修订人员方猛修订内容新建立生效时间 ____.09.10修订人部门负责人_______________________________ (签名)__________________________________ (职务) _____________________________ (日期)审阅人部门主管_______________________________ (签名)__________________________________ (职务) _____________________________ (日期)批准人管理代表_______________________________ (职务)_______________________________ (签名)_____________________________ (日期)失效模式以及效应分析,全文。
荣利涂装工业(苏州) 荣利涂装工业(苏州)有限公司CEL CoatingsIndustries(Suzhou) CO., Ltd编号:CEL-Q2-12 编号: CEL-Q2日期:____.09.10 ____.09.10 09.1 版本:Rev.00 页码: 页码:2/3失效模式以及效应分析(FMEA) 失效模式以及效应分析(FMEA)作业方法一, 目的:1.1 规定表面处理过程的 PFMEA 分析的内容及方法技术,发现评价制造过程中潜在的失效及其后果,找到能够避免或减小这些潜在失效发生的措施,以利将潜在之失效状况及其原因分析,以减少产品潜在的失效时之风险,满足顾客的需求.二, 适用范围: 2.1 供应给客户的零件,新过程或产品更改时进行 PFMEA 活动的控制.新零件,新过程等相关流程请参阅《新零件评价的程序》 2.2 若客户需求与本程序有差异,依顾客要求执行. 三, 职责: 3.1 研发部与工程部:负责过程阶段 PFMEA 主导分析. 3.2 APQP 小组:参与 PFMEA 讨论. 3.3 品管部:涉及标准语的 PFMEA 主导分析四, 名词定义: 4.1 本程序采用 ISO/TS16949:____ 品质管理体系术语和定义.` 4.2 FMEA:Failure 五, PFMEA 表格的填写: Mode and Effects Analysis(潜在失效模式及效应分析)5.1 零件编号:输入用以识别 FMEA 文件的字母数字串,用作文件的控制. 5.2 工艺流程:输入受分析零部件的表面处理工艺类别,如三价彩锌钝化. 5.3 审查小组:输入审核 PFMEA 参数与失效风险是否符合要求的人员(R_amp;D 主管与品管主管必填) 5.4 负责人签名/日期:输入拟定 PFMEA 的工程师的姓名与拟定文件的日期. 5.5 修订号:指本文件的修订版本.失效模式以及效应分析,全文。
PFMEA作业程序(含表格)

PFMEA作业程序(IATF16949/ISO9001-2015)1.0目的:在产品品质规划及制造阶段对各工序进行分析,找出潜在的失效模式,并对产品的失效模式及后果进行分析,解决潜在的质量问题,以确保产品品质的可靠性。
2.0范围:本公司产品制造中的潜在失效模式及效应分析。
3.0权责:工程部:负责组织制定PFMEA。
4.0定义:PFMEA:Process Failure Mode and Effects Analysis 制程中潜在失效模式及效应分析。
5.0流程:无。
6.0程序:6.1编写者需按以下要求的格式填制PFMEA表格;6.1.1项目:写明分析的项目名称;6.1.2 责任部门:填入产生失效过程发生的部门;6.1.3编制人:填入负责编写PFMEA工作的人员姓名;6.1.4关键日期:填入初次FMEA预计完成日期,该日期应为预计生产日期之前的任一日;6.1.5 FMEA日期:填入编制FMEA原稿的日期及最新修订日期;6.1.6编号:为便于查询应按以下要求编号:FMEA ×× ××××××年型号顺序号6.1.7制程功能/要求:填入被分析的制程或作业简单的叙述,叙述尽可能与被分析的制程或作业目的一致。
当制程包含多种作业,而有不同的潜在失效模式时,要将不同的作业视为不同的制程处理;6.1.8潜在失效模式:当制程可能不符合制程要求,叙述规定作业的不合格事项,它可能成为下一工程的潜在失效模式;6.1.9潜在失效后果:填入因潜在失效模式之原因所产生不符合制程要求的结果;6.1.10严重度(S)6.1.10.1制程潜在失效模式及效应分析的严重度6.1.11级别:是指此要素关键特性、重要特性;6.1.12潜在失效起因/机理:在尽可能的范围内,列出的有能想象得到的失效原因;6.1.13频度(O):6.2现行制程控制、探测、预防填入现行的制程控制、探测、预防方法,用来预防可能扩大的失效模式和侦查出失效模式的发生,有三种制管制可以考虑。
失效模式与效应分析
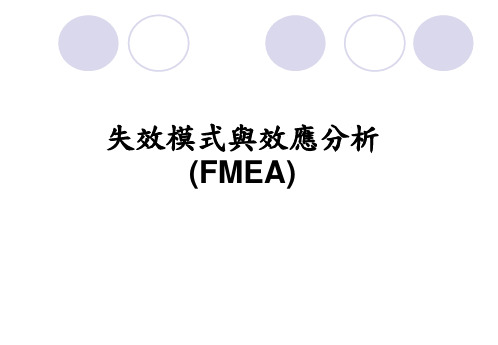
低
6
出貨前
----------------------------------------------------------------------------------------------------------------
非常低
7
客戶尚未收到貨
----------------------------------------------------------------------------------------------------------------
幾乎無法檢出
10
不良發生後知道
21
表格內容介紹及說明-風險優先指數
22
風險優先指數(Risk Priority Number)
定義: 相等於發生率(O)、嚴重度(S)、難檢度(D)三 項數據之乘積,可做為關鍵要因及產品特性之 優先評估依據。
說明: RPN為較高數據之項目代表較高風險,需優先 加以處理,反之則異。 RPN數據較低時亦有特殊狀況需優先處理之。
FMEA 的基本概念
將失效依照其應用的目的或特性加以分類:
1.依失效發生原因分類 2.依失效發生時間情況分類
• 先天性弱點的失效 • 誤用失效
• 突發性失效 • 漸次性失效
3.依失效範圍程度分類 4.依失效根源分類
• 局部性失效 • 全面性失效
• 老化、組件、環境、人員
4
表格內容介紹及說明-失效模式
* 錯誤 * 遺漏 * 沒有或僅有部份動作 * 產生危險 * 有障礙
2
FMEA型式
設計FMEA(DFMEA) 1. 零件 2. 次系統 3. 系統
將系統之失敗效應減 至最低 將系統之品質與可靠 度提昇之最高
失效模式与效应分析FMEA作业规范
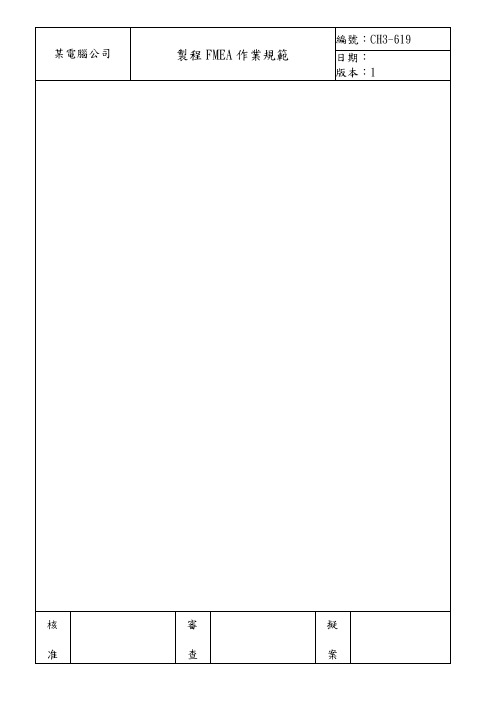
b.製造協助單位(含工程,機構,治具,物管,品保……等單位),協助製造單位依據產品特性及規劃流程,提出可能失敗模式及對應對策確保製造品質。另需對各單位現行作業針對產品及流程作業,提出預測預防措施。
1.目的:
製程FMEA作業的目的為:
1.1確保產品從試做到量產階段每一階段的生產活動與流程管理如EPR (TR)、PPR (FTR)、MP,皆能做到預測預防的動作,實現「第一次就做對」Do It Right the First Time的目的。
在作FMEA作業循環時,需在每一個階段中,分別依據各產品設計、生產及流程等特性,及試產各階段問題點,作FMEA展開與預測預防等檢討的動作。確保可能發生問題點降至最低,使得量產開始動作能達到高生產品質及效率。
為使作業達成品質保證及流程工作順利,FMEA作業需由製造等相關單位一起完成。
5-3.1製程FMEA作業推動應工廠PM或QA為推動單位:
a.負責定期FMEA Review會議召開,整合各單位做法,對於各單位FMEA對策項目加以彙整,確保生產開始就可獲致高生產品質及生產效率。
5-3.2製造等相關單位作業:
5-1-4找出可能失敗的原因。
5-1-5針對可能發生失敗模式問題原因研究可對應的對策。
5-1-6針對不同失敗模式實際導入對策。
5-1-7試產觀察追蹤對策導入效果。
5-1-8對策重修訂及導入。
5-1-9回5-1,挑戰目標持續改善降低失敗機率,增進客戶滿意。
- 1、下载文档前请自行甄别文档内容的完整性,平台不提供额外的编辑、内容补充、找答案等附加服务。
- 2、"仅部分预览"的文档,不可在线预览部分如存在完整性等问题,可反馈申请退款(可完整预览的文档不适用该条件!)。
- 3、如文档侵犯您的权益,请联系客服反馈,我们会尽快为您处理(人工客服工作时间:9:00-18:30)。
作业流程:
流 程 权 责 单 位 相 关 说明 表 单
────── ─────── ──────────── ─────────
┌────┐ DFMEA:研发 失效模式与效应分析作业程序 异常处理单QA-AQA26
│资料准备│ PFMEA:生技 QP-AFA15
└────┘ 制程管制程序QP-AFA04 质量改善会议记录
3
微乎其微
生产线有一点损坏,部份产品不得不在生产中重新加工,但在站内(in-station)合配性、亮度与异音这一项不合要求,敏锐的顾客注意到的缺陷(少于25%)。
2
无
顾客无法发现的缺陷。
1
文件编号
页 版 本
1
文件名称
失效模式与效应分析作业程序
页 次
6/10
级别:本栏用于对产品之尺寸特性或保安特殊等级做明确区别。
│ (制造.品保等其
↓ 他有关单位协办)
↓
┌────┐ 跨功能小组 1.列出该产品应有之功
│召开会议│ 能及不应有之功能 会议记录
└────┘ 2.列出制程特性
│ 3.对每一作业可能出
↓ 错之处加以明定
/\
/ \
/ 是 否 \
\ 增 修 / 跨功能专业小组
\ / (参考 “内容”
\/
│
↓
┌─────┐
FMEA分析表作成:
DFMEA序号:填入DF-□□□可用于追查。
PFMEA序号:填入PF-□□□可用于追查。
项目:填入系统、子系统或零组件的名称和号码(型号)。
制程责任;填入生产部门和组织,OEM部门和组织,也包括供货商姓名。
编制人:填入负责准备FMEA之工程师的姓名。
车型/年份:填入分析零件所装附于客户的型号及年份(将利用和正被分析的设计或制程所影响)。
PFMEA制程功能/要求:描述工程目的,使用之设备。填入对正被分析制程的简单描述
(如:冲压、塑行、组装)尽可能简单地指出正被分析的制程的目的,在制程中有
许多带有不同潜在失效模式的流程,按单独流程列出工序也许是可取的。
潜在失效模式:
DFMEA潜在的失效模式被定义为一种方式,以这种方式,零件可能潜在地无法满足设
工程放行日期/主要生产日期:填入最初工程放行日期与不超过预定的生产开始日期。
FMEA日期:填入原版FMEA制订的日期及最近的修改日期。
文件编号
页 版 本
1
文件名称
失效模式与效应分析作业程序
页 次
4/10
核心(跨功能)小组:列出负责的个人和有权去确认和从事这项任务的部门的名单。
DFMEA零件功能与要求:填入对正被分析零件的简单描述。
4
高
将会侦测出潜在原因/机制和随后的失效模式
现行的控制将检测出失效模式的可能性较高。当场或多重接获准则后续作业侦测。
3
很高
有很高的机会侦测出潜在原因/机制和随后的失效模式
现行的控制几乎可以确定能检测出失效模式。当场自动化侦测。
侦测性
由设计控制所测出的可能性
制程管制减检测出来之可能性
等级
完全不确定性
将不会和 (或)不能侦测潜在的原因/机制和随后的失效模式; 或者根本没有设计控制。
现在没有已知的控制去检测或检查失效模式。
10
极其微乎其微
几乎不可能侦测出潜在原因/机制和随后的失效模式的机会。
现行的控制将检测出失效模式的可能性极其微乎其微,间接或随机检查。
文件编号
页 版 本
1
文件名称
失效模式与效应分析作业程序
页 次
2/10
侦测性(Detection):为在半成品流向后制程前,检出失效原因或失效模式之能力评估指针。
风险优先数(RPN):原文为〞Risk Priority Number" :
由严重性、发生性、侦测性三指数相乘所得,为是否实施对策改善之总评估指标。
潜在失效模式:制程不能满足设计或规格需求时之现象。
失效的潜在效果:失效模式对客户之影响。
严重性(Severity):失效模式发生时, 对客户之影响的严重性之评估指标。
失效的潜在原因与结构:失效如何发生之原因。
发生性(Occurrence):为失效原因发生频率之评估指针。
现行制程管制:为目前已经使用之措施, 以预防失效发生或当失效发生时能被检出。
≧
1
文件编号
IP-AQA01
页 版 本
1
文件名称
失效模式与效应分析作业程序
页 次
7/10
现行设计&制程管制:分为预防&侦测。
现行管制是对要在一定程序上阻止了失效模式出现,如果它出现就测出该失效模式的管制的措述,这些管制的可能是诸如装置器差错防止或制程管制之类的制程管制,或者可能是后制程评估。这评估可以在目标制程发生后或在随后的制程上发生。
文件修订纪录书
QF-ARD01
使用时机:
当生产线导入新产品或新设备、新材料、制程变更、规格变更、制程不稳定、制程能力不足,均需进行或重新研拟制程 FMEA 作业。
跨功能专业小组之编成:
须以技术支持能力及产品特性为考虑,人数不限, 但至少包括品保、工程、制程各一员,其余材料、服务和供货商等部门视需要加入。
四. 名词定义:
失效 (Failure):
是指产品丧失规定的功能,包括在现定条件下不能完成其规定的功能,或参数不能保持在规定范围内,或操作者失误,造成产品功能失效,及因应环境力变化导至功能丧失。
制程失效模式与效应分析:
DFMEA为英文"Design Failure Mode and Effects Analysis" 之缩写, ,系质量规划构想阶段(第一阶段)中将客户期望转换成可靠度,再从产品设计与开发验证阶段(第二阶段)导入。本项分析,系以新产品为对象做系统化检讨及分析;用意在于事先预测、解决或监查制程中之潜在问题。
DFMEA:失效模式功能上所产生的效果
噪音
粗糙
不稳定动作
需要过份努力
不起作用
令人不愉快的气味
不稳定
动作受损
通风
间歇性动作
外观不佳
控制受损
PFMEA:失效模式对顾客所产生的效果,在本文中的顾客是指下一个工程、随后的工程或场所、交易商和(或)最终使用者、当评估一个失效的潜在效果时,每一个都必需被考虑到。
└────┘
│
↓
┌────┐ DFMEA:研发
│效果确认│ 失效模式与效应分析作业程序 FMEA改正后结果
└────┘ PFMEA:品保 QP-AFA15
│ 统计.分析及改善程序
│ QP-AQA11
↓
┌────┐
│标 准 化│ 制造单位 文件与数据管制 文件修订.废止申请表
└────┘ 程序QP-ARD01 QF-ARD03
│执行FMEA │ FMEA
└─────┘
│
↓
┌────┐
│是否采取│ 跨功能专业小组 FMEA RPN 评估
│对 策│
└────┘
│
↓ ©
文件编号
页 版 本
1
文件名称
失效模式与效应分析作业程序
页 次
3/10
│©
↓
┌───┐
│对策拟定│ 权责单位 制程管制程序QP-AFA04 FMEA推荐措施
│执 行│
6
低
造成生产线有一点损坏,100%产品要重新加工,功能能运作,但某些舒适/方便性功能下降,顾客有点不满。
5
甚低
生产线有一点损坏,产品挑拣后,部份要重新加工,合配性、亮度与异音这一项不合要求,大多数顾客注意到了缺陷(多于75%)。
4
很小
生产线有一点损坏,部份产品不得不地重新加工,合配性、亮度与异音这一项不合要求,一般顾客注意到的缺陷(50%)。
失效的潜在原因与结构:
失效的潜在原因定义为失效会如何发生(设计弱点)。按照能被矫正或控制的事情来描述,失效原因必须是可管制或是能改善的。典型失效原因可以包括,但不限于:
DFMEA
塑性
蜕变
疲劳
磨损
材料不稳定
腐蚀
PFMEA
锯带钝化
模具设计不良
零组件遗失或错位
温控器的故障
气压不足
供料不及
涂模剂不剥落
只有特定过失或功能障碍(如:操作员过失、机器功能障碍)不应该被使用。
计意图。
破裂的
黏着
变形的
短路的
松开的
生锈的
渗透的
断裂的
PFMEA假设前工程之半成品零件都是好的,列出本制程中所有可能发生的潜在失效模
式,即使它不一定会发生。
温 度
压 力
孔 位 错
毛 边
变 形
短 路
装 卸 受 损
弄 脏
漏 焊
不适当的结构
工具磨损
失效的潜在效果:
当上述失效发生时,客户会感觉到什么? 后制程性能上会有什么影响?
6
文件编号
页 版 本
1
文件名称
失效模式与效应分析作业程序
页 次
8/10
侦测性
由设计控制所测出的可能性
制程管制减检测出来之可能性
等级
一般
侦测出潜在原因/机制和随后的失效模式的机会有限
现行的控制将检测出失效模式的可能悾中等。计量值/计数值测定。
5
有点高
有机会侦测出潜在原因/机制和随后的失效模式
现行的控制将检测出失效模式的可能性不低。后续作业侦测/作业前准备/首件检查。
PFMEA为英文"Process Failure Mode and Effects Analysis" 之缩写, 其功能为事前鉴别出制程中可能发生之失效模式, 并且加以文件化及数量化之评估, 主要采用归纳法。