金属的塑性变形与再结晶(材料第二章)
机械工程材料习题答案

第六章 钢的热处理
2、何谓本质细晶粒钢?本质细晶粒钢的奥氏体晶粒是否一定比本质粗晶粒钢的细?
答: wC0.45%碳钢属于低碳钢,室温平衡组织为F+P,其中F和P相对含量分别为:
wF%0.77 0. 77 0.4542%
硬因度此和,伸该长碳率钢等的性硬能度指为标:符合加w合P法%则。 00..747558%
伸长率为:
H 4 5H PV P % H FV F % 1 8 0 5 8 % 8 4 2 % 1 0 4 .4 3 .3 6 1 0 7 .7 6
增加,材料硬度增加、塑性下降,强度在~ wC0.90% 时最高,之后下降。
因此,Rm( σb): wC0.20%< wC1.20%< wC0.77% HBW: wC0.20%< wC0.77%< wC1.20% A: wC1.20%< wC0.77%< wC0.20%
4、计算碳含量为wC0.20%的碳钢的在室温时珠光体和铁素体的相对含量。
B 将( α+β )II 视为一种组织构成项:
WαI=
W(α+β)II=
61.9-30 61.9-19 30-19 61.9-19
=74.36% =25.64%
WαI= W(α+β)II=
61.9-30 61.9-19 30-19 61.9-19
=74.36% =25.64%
则在( α+β )II中含有多少α和多少β相?
2、试述固溶强化、加工硬化和弥散强化的强化原理,并说明三者的区别。
答: 固溶强化:溶质原子溶入后,要引起溶剂金属的晶格产生畸变,进而位错运动时受到阻力增大。 弥散强化:金属化合物本身有很高的硬度,因此合金中以固溶体为基体再有适量的金属间化合物均 匀细小弥散分布时,会提高合金的强度、硬度及耐磨性。这种用金属间化合物来强化合金的方式为 弥散强化。 加工强化:通过产生塑性变形来增大位错密度,从而增大位错运动阻力,引起塑性变形抗力的增加, 提高合金的强度和硬度。 区别:固溶强化和弥散强化都是利用合金的组成相来强化合金,固溶强化是通过产生晶格畸变,使 位错运动阻力增大来强化合金;弥散强化是利用金属化合物本身的高强度和硬度来强化合金;而加 工强化是通过力的作用产生塑性变形,增大位错密度以增大位错运动阻力来强化合金;三者相比, 通过固溶强化得到的强度、硬度最低,但塑性、韧性最好,加工强化得到的强度、硬度最高,但塑 韧性最差,弥散强化介于两者之间。
实验七 材料的塑性变形和再结晶

滑移变形具有以下特点: ①滑移在切应力作用下产生(图2)。
图 2 晶体在切应力作用下的变形
②滑移沿原子密度最大的晶面和晶 向发生。
滑移常沿晶体 中原子密度最 大的晶面和晶 向发生,因为 原子密度最大 的晶面之间间 距最大,点阵 阻力最小,原 子密度最大晶 向上原子间最 短,结合力最 弱,因此产生 滑移所需切应 力最小。
因此,一般在室温使用的 结构材料都希望获得细小而均 匀的晶粒。因为细晶粒不仅使 材料具有较高的强度、硬度, 而且也使它具有良好的塑性和 韧性,即具有良好的综合力学 性能。故生产中总是尽可能地 细化晶粒。
2.2 冷塑性变形对金属组织和性能的影响
塑性变形后,金属在组织和性能方面发生四个方面的变化: 1)产生纤维组织,性能由各向同性趋于各向异性。
• 变形金属在加热中一般经历三个过程: (1)回复 (2)再结晶 (3)晶粒长大
变形金属加热时组织和性能变化示意图
回复 再结晶
晶粒长大
组 织
变 内应力
化
性
能 变
强度
化
晶粒度 塑性
(1)回复
(2)再结晶
• 由于再结晶后组织的复原,因而金属的强度、硬度下降, 塑性、韧性提高,加工硬化消失。
再结晶温度(T再): 通常指经大变形度(70~80%)的变形后,在规定
图5a为锌的变形孪晶,其形貌特征为薄透镜状。纯铁在低温 下受到冲击时也容易产生变形孪晶,其形貌如图5b所示,在 这种条件下萌生孪晶并长大的速度大大超过了滑移速度。
a 锌的变形孪晶
100
b 铁的变形孪晶
图5 变形孪晶光学显微形貌
100
工业纯铁压缩变形——滑移线
纯锌冲击变形——孪晶
2.多晶体的塑性变形
金属的塑性变形与再结晶

实验名称:金属的塑性变形与再结晶实验类型:一、实验目的和要求(必填)二、实验内容和原理(必填)三、主要仪器设备(必填)四、实验步骤与实验结果(必填)五、讨论、心得(必填)一、实验目的1.了解冷塑性变形对金属材料的内部组织与性能的影响;2.了解变形度对金属再结晶退火后晶粒大小的影响。
二、实验原理金属塑性变形的基本方式有滑移和孪生两种。
在切应力作用下,晶体的一部分沿某一晶面相对于另一部分滑动,这种变形方式称为滑移;在切应力作用下,晶体的一部分沿某一晶面相对另一部分产生剪切变形,且变形部分与未变形部分的位向形成了镜面对称关系,这种变形方式称为孪生。
(一) 冷塑性变形对金属组织与性能的影响若金属在再结晶温度以下进行塑性变形,称为冷塑性变形。
冷塑性变形不仅改变了金属材料的形状与尺寸,而且还将引起金属组织与性能的变化。
金属在发生塑性变形时,随着外形的变化,其内部晶粒形状由原来的等轴晶粒逐渐变为沿变形方向伸长的晶粒,在晶粒内部也出现了滑移带或孪晶带。
当变形程度很大时,晶粒被显著地拉成纤维状,这种组织称为冷加工纤维组织。
同时,随着变形程度的加剧,原来位向不同的各个晶粒会逐渐取得近于一致的位向,而形成了形变织构,使金属材料的性能呈现出明显的各向异性。
金属经冷塑性变形后,会使其强度、硬度提高,而塑性、韧性下降,这种现象称为加工硬化。
(二) 冷塑性变形后金属在加热时组织与性能的变化金属经冷塑性变形后,由于其内部亚结构细化、晶格畸变等原因,处于不稳定状态,具有自发地恢复到稳定状态的趋势。
但在室温下,由于原子活动能力不足,恢复过程不易进行。
若对其加热,因原子活动能力增强,就会使组织与性能发生一系列的变化。
1.回复当加热温度较低时,原子活动能力尚低,故冷变形金属的显微组织无明显变化,仍保持着纤组织的特征。
此时,因晶格畸变已减轻,使残余应力显著下降。
但造成加工硬化的主要原因未消除,故其机械性能变化不大。
2.再结晶当加热温度较高时,将首先在变形晶粒的晶界或滑移带、孪晶带等晶格畸变严重的地带,通过晶核与长大方式进行再结晶。
“金属的塑性变形与再结晶实验”实验报告.docx

金属的塑性变形与再结晶实验”实验报告、实验目的( 1) 了解冷塑性变形对金属材料的内部组织与性能的影响。
( 2) 了解变形度对金属再结晶退火后晶粒大小的影响。
二、实验原理金属材料在外力作用下,当应力大于弹性极限时,不但会产生弹性变形,还会产生塑性变形。
塑性变形的结果不仅改变金属的外形和尺寸,也会改变其内部的组织和性能。
在冷塑性形变过程,随着变形程度的增大,金属内部的亚晶增多,加上滑移面转动趋向硬位向和位错密度增加等原因,金属的强度和硬度升高,塑性和韧性下降,这种现象称为加工硬化。
加工硬化后的金属内能升高,处在不稳定的状态,并有想稳定状态转变的自发趋势。
若对其进行加热,使其内部原子活动能力增大,随着加热温度逐渐升高,金属内部依次发生回复、再结晶和晶粒长大3 个阶段。
冷塑性变形金属经再结晶退火后的晶粒大小,不仅与再结晶退火时的加热温度有关,,而且与再结晶退火前预先冷变形程度有关。
当变形度很小时,由于金属内部晶粒的变形也很小,故晶格畸变也小,晶粒的破碎与位错密度增加甚微,不足以引起再结晶现象发生,故晶粒大小不变。
当变形度在2%~10% 范围内时,由于多晶体变形的特点,金属内部各个晶粒的变形极不均匀(即只有少量晶粒进行变形) ,再结晶是晶核的形成数量很少,且晶粒极易相互并吞长大,形成较粗大的晶粒,这样的变形度称为临界变形度。
大于临界变形度后,随着变形量的增大,金属的各个晶粒的变形逐步均匀化,晶粒破碎程度与位错密度也随着增加,再结晶时晶核形成的数量也增多,所以再结晶退火后晶粒较细小而均匀。
为了观察再结晶退火后铝片的晶粒大小,必须把退火后的铝片放入一定介质中进行浸蚀,由于各个晶粒内原子排列的位向不同,对浸蚀剂的腐蚀不同,因而亮暗程度不同,就能观察到铝片内的晶粒。
三、实验装置及试件工业纯铝片、铝片拉伸机、浸蚀剂( 15%HF+45%HCL+15%HN ??3+25% ??2??组成的混合酸)、HV-120型维氏硬度计、小型实验用箱式炉、钢皮尺、划针、扳手、放大镜。
金属的塑性变形与再结晶

金属的塑性变形与再结晶一、实验目的:1、了解显微镜下滑移线、变形孪晶和退火孪晶特征。
2、了解金属经冷加工变形后显微组织及机械性能的变化。
3、讨论冷加工变形对再结晶晶粒大小的影响。
二、实验内容:1、观察工业纯铁冷变形滑移线,纯锌的变形孪晶,黄铜或纯铜的退火孪晶。
2、观察工业纯铁经冷变形(0%、20%、40%、60%)后的显微组织。
3、用变形度不同的工业纯铝片,退火后测定晶粒大小。
三、实验内容讨论:1、显微镜下的滑移线与变形孪晶:当金属以滑移和孪晶两种方式塑性变形时,可以在显微镜下看到变形结果。
我们之所以能看到滑移线(叫滑移带更符合实际)是因为晶体滑移时,使试样的抛光表面产生高低不一的台阶所致。
滑移线的形状取决于晶体结构和位错运动,有直线形的,有波浪形的,有平行的,有互相交叉的,显示了滑移方式的不同。
变形量越大,滑移线愈多、愈密。
在密排六方结构中,常可看到变形孪晶,这是因为此类金属结构难以进行滑移变形。
孪晶可以看成是滑移的一种特殊对称形式,其结果使晶体的孪生部分相对于晶体的其余部分产生了位向的改变。
由于位向不同,孪晶区与腐蚀剂的作用也不同于其他部分,在显微镜下,孪晶区是一条较浅或较深的带。
在不同的金属中,变形孪晶的形状也不同,例如在变形锌中可看到孪晶变形区域,其特征为竹叶状,α—Fe则为细针状。
除变形孪晶外,有些金属如黄铜在退火时也常常出现以平行直线为边界的孪晶带,这类孪晶称为退火孪晶。
滑移和孪晶的区别:制备滑移线试样时,是试样先经过表面抛光,然后再经过微量塑性变形。
如果变形后再把表面抛光,则滑移线就看不出来了。
制备孪晶试样时,是先经塑性变形,然后再抛光腐蚀,可见:(1)对于滑移线不管样品是否经过腐蚀均可看到,而孪晶只有在磨光腐蚀后才可看见。
(2)滑移线经再次磨光即消失,而孪晶在样品表面磨光腐蚀后仍然保留着。
滑移线和磨痕的区别在于前者是不会穿过晶界的。
2、冷变形后金属的显微组织和机械性能冷加工变形后,晶粒的大小、形状及分布都会发生改变。
第二章 金属材料的塑性变形与性能

9
根据载荷作用性质不同:
a)拉深载荷 --拉力 b)压缩载荷 —压力 c)弯曲载荷 --弯力 d)剪切载荷--剪切力 e)扭转载荷--扭转力
10
2.内力 (1)定义 工件或材料在受到外部载荷作用时,为使其不变形,在 材料内部产生的一种与外力相对抗的力。 (2)大小 内力大小与外力相等。 (3)注意 内力和外力不同于作用力和反作用力。
2
§1.金属材料的损坏与塑性变形
1.常见损坏形式
a)变形
零件在外力作用下形状和尺寸所发生的变化。 (包括:弹性变形和塑性的现象。
c)磨损
因摩擦使得零件形状、尺寸和表面质量发生变化的现象。
3
2.常见塑性变形形式 1)轧制 (板材、线材、棒材、型材、管材)
28
2)应用范围 主要用于:测定铸铁、有色金属及退火、正火、 调质处理后的各种软钢或硬度较低的 材料。 3)优、缺点 优点:压痕直径较大,能比较正确反映材料的平均 性能;适合对毛坯及半成品测定。 缺点:操作时间比较长,不适宜测定硬度高的材料; 压痕较大不适合对成品及薄壁零件的测定。
29
2.洛氏硬度(HR)——生产上应用较广泛 1)定义 采用金刚石压头直接测量压痕深度来表示材料的硬度值。 2)表示方法
11
3.应力 (1)定义 单位面积上所受到的力。 (2)计算公式 σ= F/ S( MPa/mm2 ) 式中: σ——应力; F ——外力; S ——横截面面积。
12
二、金属的变形 金属在外力作用下的变形三阶段: 弹性变形 弹-塑性变形 断裂。 1.特点 弹性变形: 金属弹性变形后其组织和性能不发生变化。 塑性变形: 金属经塑性变形后其组织和性能将发生变化。 2.变形原理 金属在外力作用下,发生塑性变形是由于晶体内部 缺陷—位错运动的结果,宏观表现为外形和尺寸变化。
工程材料与热加工 判断题

判断题专项练习第一章工程材料的力学性能1.用布氏硬度测量硬度时,压头为钢球,用符号HBS表示。
2.用布氏硬度测量硬度时,压头为硬质合金球,用符号HBW表示。
3.金属材料的机械性能可以理解为金属材料的失效抗力。
第二章工程材料结构(一)金属的晶体结构1. 非晶体具有各向异性。
2. 每个体心立方晶胞中实际包含有2个原子。
3. 每个面心立方晶胞中实际包含有4个原子。
4. 晶体具有各向同性。
5. 单晶体具有各向同性,多晶体具有各向异性。
6. 单晶体具有各向异性,多晶体具有各向同性。
7. 不同晶体结构中不同晶面、不同晶向上的原子排列方式相同而排列紧密程度不同。
8. 实际金属内部原子排列是规则的,无缺陷的。
(二)金属的结晶与相图1. 物质从液体状态转变为固体状态的过程称为结晶。
2. 金属结晶后晶体结构不再发生变化。
3. 在金属的结晶中,随着过冷度的增大,晶核的形核率N和长大率G都增大,在N/G增大的情况下晶粒细化。
4. 液态金属结晶时的冷却速度越快,过冷度就越大,形核率和长大率都增大,故晶粒就粗大。
5. 物质从液体状态转变为固体状态的过程称为凝固。
6. 液态金属冷却到结晶温度时,液态金属中立即就有固态金属结晶出来。
7.合金中各组成元素的原子按一定比例相互作用而生成的一种新的具有金属特性的物质称为固溶体。
8.合金元素在固态下彼此相互溶解或部分地溶解,而形成成分和性能均匀的固态合金称为金属化合物。
(三)铁碳合金相图1.铁素体是碳溶解在α-Fe中所形成的置换固溶体。
2.铁素体是碳溶解在γ-Fe中所形成的间隙固溶体。
3.GS线表示由奥氏体冷却时析出铁素体的开始线,通称Acm线。
4.PSK线叫共析线,通称Acm线。
5.奥氏体是碳溶解在γ-Fe中所形成的间隙固溶体。
6.ES线是碳在奥氏体中的溶解度变化曲线,通称Acm线。
7.在Fe-Fe3C相图中的ES线是碳在奥氏体中的溶解度变化曲线,通常称为A3线。
(四)高分子材料与陶瓷1. 高分子材料是良好的绝缘体。
工业纯铝的塑性变形与再结晶实验方案

实验方案金属的塑性变形与再结晶一,实验目的1、观察显微镜下滑移线、变形孪晶的特征;2、了解金属经冷加工变形后显微组织及性能的变化;二、概述1 显微镜下的滑移线与变形挛晶金属受力超过弹性极限后,在金属中特产生塑性变形。
金属单晶体变形机理指出,塑性变形的基本方式为滑移和孪晶两种。
所谓滑移时晶体在切应力作用下借助于金属薄层沿滑移面相对移动实质为位错沿滑移面运动的结果。
滑移后在滑移面两侧的晶体位相保持不变。
把抛光的纯铝试样拉伸,试样表面会有变形台阶出现,一组细小的台阶在显微镜下只能观察到一条黑线,即称为滑移带。
变形后的显微姐织是由许多滑移带所组成。
另一种变形的方式为孪晶。
不易产生滑移的金属,如六方晶系镉、镁、铍、锌等,或某些金属当其滑移发生困难的时候,在切应力的作用下将发生的另一形式的变形,即晶体的—部分以一定的晶面为对称面;与晶体的另一部分发生对称移动,这种变形方式称为孪晶或双晶。
孪晶的结果是孪晶面两侧晶体的位向发生变化,呈镜面对称。
所以孪晶变形后,由于对光的反射能力不同,在显微镜下能看到较宽的变形痕迹——孪晶带或双晶带。
2、变形程度对金属组织和性能的影响变形前金属为等轴晶粒,轻微量变形后晶粒内即有滑移带出现,经过较大的变形后即发现晶粒被拉长,变形程度愈大,晶粒被拉得愈长,当变形程度很大时,则加剧剧了晶粒沿一定方向伸长,晶粒内部被许多的滑移带分割成细小的小块,晶界与滑移带分辨不清,呈纤维状组织。
由于变形的结果,滑移带附近晶粒破碎,产生较严重的晶格歪扭,造成临界切应力提高,使继续变形发生困难,即产生了所谓加工硬化现象。
随变形程度的增加,金属的硬度、强度、矫顽力、电阻增加,而塑性和韧性下降。
3、形变金属在加热后组织和性能的影响变形后的金属在较低温度加热时,金属内部的应力部分消除,歪曲的晶格恢复正常,但显微组织没有变化,原来拉长的晶粒仍然是伸长的。
这个过程是靠原子在一个晶粒范围内的移动来实现的,称为回复。
变形后金属加热到再结晶温度以上时,发生再结晶过程,显微组织发生显著变化。
工程材料第二章知识点
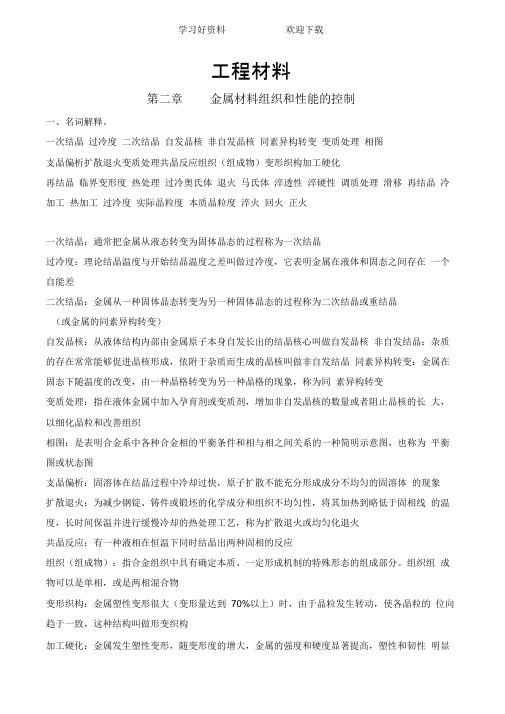
工程材料第二章金属材料组织和性能的控制一、名词解释。
一次结晶过冷度二次结晶自发晶核非自发晶核同素异构转变变质处理相图支晶偏析扩散退火变质处理共晶反应组织(组成物)变形织构加工硬化再结晶临界变形度热处理过冷奥氏体退火马氏体淬透性淬硬性调质处理滑移再结晶冷加工热加工过冷度实际晶粒度本质晶粒度淬火回火正火一次结晶:通常把金属从液态转变为固体晶态的过程称为一次结晶过冷度:理论结晶温度与开始结晶温度之差叫做过冷度,它表明金属在液体和固态之间存在一个自能差二次结晶:金属从一种固体晶态转变为另一种固体晶态的过程称为二次结晶或重结晶(或金属的同素异构转变)自发晶核:从液体结构内部由金属原子本身自发长出的结晶核心叫做自发晶核非自发结晶:杂质的存在常常能够促进晶核形成,依附于杂质而生成的晶核叫做非自发结晶同素异构转变:金属在固态下随温度的改变,由一种晶格转变为另一种晶格的现象,称为同素异构转变变质处理:指在液体金属中加入孕育剂或变质剂,增加非自发晶核的数量或者阻止晶核的长大,以细化晶粒和改善组织相图:是表明合金系中各种合金相的平衡条件和相与相之间关系的一种简明示意图,也称为平衡图或状态图支晶偏析:固溶体在结晶过程中冷却过快,原子扩散不能充分形成成分不均匀的固溶体的现象扩散退火:为减少钢锭、铸件或锻坯的化学成分和组织不均匀性,将其加热到略低于固相线的温度,长时间保温并进行缓慢冷却的热处理工艺,称为扩散退火或均匀化退火共晶反应:有一种液相在恒温下同时结晶出两种固相的反应组织(组成物):指合金组织中具有确定本质、一定形成机制的特殊形态的组成部分。
组织组成物可以是单相,或是两相混合物变形织构:金属塑性变形很大(变形量达到70%以上)时,由于晶粒发生转动,使各晶粒的位向趋于一致,这种结构叫做形变织构加工硬化:金属发生塑性变形,随变形度的增大,金属的强度和硬度显著提高,塑性和韧性明显下降,这种现象称为加工硬化再结晶:变形后的金属在较高温度加热时,由于原子扩散能力增大,被拉成(或压扁)破碎的晶粒通过重新形核和长大变成新的均匀、细小的等轴晶,这个过程称为再结晶临界变形度:再结晶时使晶粒发生异常长大的预先变形度称做临界变形度热处理:是将固态金属或合金在一定介质中加热、保温和冷却,以改变材料整体或表面组织,从而获得所需性能的工艺过冷奥氏体:从铁碳相图可知,当温度在A1(PSK线/共析反应线)以上时奥氏体是稳定的,能长期存在,当温度降到A1以下后,奥氏体即处于过冷状态,这种奥氏体称为过冷奥氏体(过冷A)退火:将组织偏离平衡状态的钢加热到适当温度,保温一定时间,然后缓慢冷却(一般为随炉冷却)热处理工艺叫做退火-马氏体:碳在a —Fe中的过饱和固溶体淬透性:钢接受淬火时形成马氏体的能力叫做钢的淬透性淬硬性:钢淬火后硬度会大幅度提高,能够达到的最高硬度叫钢的淬硬性调质处理:通常把淬火加高温回火称为调质处理滑移:在切应力的作用下,晶体的一部分沿一定的晶面(滑移面)上的一定方向(滑移方向)相对于另一部分发生滑动的过程叫做滑移冷加工:在金属的再结晶温度以下的塑性变形加工称为冷加工热加工:在金属的再结晶温度以上的塑性变形加工称为热加工实际晶粒度:某一具体的热处理或热加工条件下的奥氏体的晶粒度叫做实际晶粒度本质晶粒度:钢加热到(930土10C),保温8h,冷却后测得的晶粒度叫做本质晶粒度淬火:将钢加热到相变温度以上,保温一定时间,然后快速冷却以获得马氏体组织的热处理工艺称为淬火回火:钢件淬火后,为了消除内应力并获得所要求的组织和性能,将其加热到Ac1(PSK线/共析反应线)以下某一温度,保温一定时间,然后冷却到室温的热处理工艺叫做回火正火:钢材或钢件加热到Ac3 (对于亚共析钢)、Ac1 (对于共析钢)和Accm (对于过共析钢)以上30~50C,保温适当时间后,在自由流动的空气中均匀冷却的热处理称为正火一次渗碳体是从液相包晶过程中直接析出二次渗碳体是从奥氏体中析出三次渗碳体是从铁素体中析出珠光体:铁素体+渗碳体高温莱氏体Le(A+Fe3C):奥氏体+渗碳体低温莱氏体Le'(P+Fe3C U +Fe3C):珠光体+二次渗碳体+渗碳体二、填空。
金属的塑性变形与再结晶

等轴晶粒,机械性能完全恢复。
(三)再结晶后晶粒大小与变形量的关系
冷变形金属再结晶后晶粒大小除与加 热温度、保温时间有关外,还与金属的预 先变形量有关。 当变形度很小时,金属不发生再结晶。
晶粒 大小
这是由于晶内储存的畸变能很小,不足以
进行再结晶而保持原来状态,当达到某一 变形度时,再结晶后的晶粒特别粗大,该
2
3 4
低碳钢
低碳钢 低碳钢
压缩58%
压缩45%,550℃退火半小时 压缩58%,550℃退火半小时
伸长的晶粒
部分等轴晶 部分等轴晶
5
6 7 8
低碳钢
低碳钢 低碳钢 低碳钢
压缩45%,650℃退火半小时
压缩58%,650℃退火半小时 压缩45%,700℃退火半小时 压缩58%,700℃退火半小时
完全再结晶
c. 对比分析不同变形量,不同退火温度对晶粒大小的影响。
(二)塑性变形后的回复与再结晶
金属经冷塑性变形后,在热力学上处于不稳定状态,
必有力求恢复到稳定状态的趋势。
但在室温下,由于原子的动能不足,恢复过程不易进 行,加热会提高原子的活动能力,也就促进了这一恢复 过程的进行。 加热温度由低到高,其变化过程大致分为回复、再结 晶和晶粒长大三个阶段,当然这三个阶段并非截然分开。
变形度称之临界变形度。
一般金属的临界变形度在2%~10%范 围内。此后,随着变形度的增加,再结晶
临界变形度
预先变形程度
预先变形程度对晶粒度的影响
后的晶粒度逐渐变细。
三、实验方法
1.实验材料及设备 (1)金相显微镜; (2)低碳钢不同变形量及再结晶状态金相样品一套;
编号 1 材料 低碳钢 处理状态 压缩45% 组织 伸长的晶粒
机械工程材料作业答案

第一章材料的结构与金属的结晶1.解释下列名词:变质处理P28;细晶强化P14;固溶强化P17。
5.为什么单晶体具有各向异性P12,而多晶体在一般情况下不显示各向异性P13?答:因为单晶体内部的原子都按同一规律同一位向排列,即晶格位向完全一致。
而在多晶体的金属中,每个晶粒相当于一个单晶体,具有各项异性,但各个晶粒在整块金属中的空间位向是任意的,整个晶体各个方向上的性能则是大量位向各不相同的晶粒性能的均值。
6.在实际金属中存在哪几种晶体缺陷P13?它们对力学性能有何影响P14?答:点缺陷、线缺陷、面缺陷。
缺陷的存在对金属的力学性能、物理性能和化学性能以及塑性变形、扩散、相变等许多过程都有重要影响。
7.金属结晶的基本规律是什么P25?铸造(或工业)生产中采用哪些措施细化晶粒?举例说明。
P27~P28答:金属结晶过程是个形核、长大的过程。
(1)增大过冷度。
降低金属液的浇筑温度、采用金属模、水冷模、连续浇筑等。
(2)变质处理。
向铝合金中加入钛、锆、硼;在铸铁液中加入硅钙合金等。
(3)振动和搅拌。
如机械振动、超声波振动、电磁搅拌等。
第二章金属的塑性变形与再结晶1.解释下列名词:加工硬化P40;再结晶P43;纤维组织P38。
2.指出下列名词的主要区别:重结晶、再结晶P43答:再结晶转变前后的晶格类型没有发生变化,故称为再结晶;而重结晶时晶格类型发生了变化。
另外,再结晶是对冷塑性变形的金属而言,只有经过冷塑性变形的金属才会发生再结晶,没有经过冷塑性变形的金属不存在再结晶的问题。
5.为什么常温下晶粒越细小,不仅强度、硬度越高,而且塑性、韧性也越好?P38答:晶粒愈细,单位体积内晶粒数就愈多,变形是同样的变形量可分散到更多的晶粒中发生,以产生比较均匀的变形,这样因局部应力集中而引起材料开裂的几率较小,使材料在断裂前就有可能承受较大的塑性变形,得到较大的伸长率和具有较高的冲击载荷抗力。
6.用冷拔铜丝制作导线,冷拔后应如何处理?为什么?P42答:应该利用回复过程对冷拔铜丝进行低温退火。
机材课后答案

第二章金属的塑性变形与再结晶一、名词解释滑移、滑移系、滑移线、滑移带、孪生;软位向、硬位向;回复、再结晶;织构、加工硬化。
二、判断是非1.金属晶体的滑移是在正应力作用下产生的。
2.经塑性变形后,金属的晶粒变细,故金属的强度、硬度升高。
3.室温下铜的塑性比铁好,这是因为铜的滑移系比铁的多。
4.冷变形金属在再结晶过程中会改变其晶体结构。
5.用冷拉紫铜管制造输油管,在冷弯以前应进行去应力退火,以降低硬度、提高塑性,防止弯曲裂纹产生。
6.热加工纤维组织(流线)可以通过热处理方法给予消除。
7.铸件、锻件、冲压件都可以通过再结晶退火,来消除加工硬化,降低硬度。
8.材料的弹性模量E愈大,则材料的塑性愈好。
三、填空1.常见的金属的塑性变形方式有()和()两种类型。
2.铜的多晶体要比单晶体的塑性变形抗力(),这是由于多晶体的()和()阻碍位错运动造成的。
3.金属的晶粒愈细小,则金属的强度、硬度愈()、塑性韧性愈(),这种现象称为()强化。
金属随塑性变形程度的增加,其强度、硬度(),塑性、韧性(),这种现象称为()。
金属经塑性变形以后,金属的晶粒(),亚晶粒(),位错()。
4.金属晶体的滑移是通过()运动来实现的,而不是晶体一部分相对另一部分的刚性滑动,因此实际临界()应力值很小。
5.纯金属结晶后进一步强化的唯一方法是依靠()来实现的,降低纯金属强度的工艺方法通常采用()。
6.塑性金属材料制造的零件,在工作过程中一旦过载,零件不会立即断裂而是发生(),使强度()。
7.多晶体金属经过大量塑性变形后,各晶粒的晶格某些位向趋向一致,这种结构称为(),此时金属呈现明显的()性,这种结构用热处理()消除。
金属再结晶后的晶粒大小与()和()有关。
工业金属不能在()变形度进行变形,否则再结晶后的晶粒(),使机械性能()。
8.铸钢锭经过热轧后,粗大的晶粒会(),缩松、气孔等缺陷会(),并且还会出现()组织。
9.用热轧圆钢通过锻造生产零件毛坯,应力求使流线与零件所受最大拉应力方向(),与切应力或冲击力方向()。
第二章 金属塑性变形的物理基础

26
锻造温度区间的制定
27
2、锻合内部缺陷 3、打碎并改善碳化物和非金属夹杂物在钢 中的分布 4、形成纤维组织 5、改善偏析
28
塑性变形过程中晶粒的变化
29
第三节 金属的超塑性变形
一、超塑性的概念和种类 概念:金属和合金具有的超常的均匀变形 能力。
大伸长率、无颈缩、低流动应力、易成形、无加工硬化
另一个取向,故晶界处原子排列处于过渡状态。
4、晶界不同于晶内性质:
3
一、变形机理
晶内变形 1、滑移 2、孪生 晶间变形 晶粒之间的相互转动和滑动 注意: 晶间变形的情况受温度的影响
4
1、滑移面和滑移方向的确定
确定滑移面:原子排 列密度最大的晶面 确定滑移方向:原子 排列密度最大的方向
5
金属的主要滑移方向、滑移面、滑移系
种类:
细晶超塑性:在一定的恒温下,在应变速率和晶粒度都满 足要求的条件下所呈现出的超塑性。 相变超塑性:具有相变或同素异构转变的金属,在其转变 温度附近以一定的频率反复加热、冷却。在外力的作用下 所呈现出的超塑性。
30
二、细晶超塑性变形的力学特征
无加工硬化
31
三、影响细晶超塑性的主要因素
应变速率
20
21
二、性能的变化 (力学性能) 加工硬化 成因:位错交互作用,难以运动 应用:强化(奥氏体钢) 避免:多次塑性加工中加入退火工序
22
第二节 金属热态下的塑性变形
热塑性变形:再结晶温度以上进行的塑性 变形 一、塑性变形时的软化过程 1、动态回复、动态再结晶 2、静态回复、静态再结晶、亚动钢中的碳和杂质元素的影响 碳 磷 硫 氮 氢 氧
37
2、合金元素对钢的塑性的影响 合金元素的加入,会使钢的塑性降低、变 形抗力提高 原因见课本p43
金属的塑性变形与再结晶材料第二章

第三节 回复与再结晶
一、变形金属在加热时的组织和性能的变化 金属经冷变形后, 组织处于不稳定状态, 有自发恢复
到稳定状态的倾向。但在常温下,原子扩散能力小, 不稳定状态可长时间维持。加热可使原子扩散能力 增加,金属将依次发生回复、再结晶和晶粒长大。
黄 铜
加热温度 ℃
㈠ 回复 回复:是指在加热温度较低
韧性断口
脆性解理断口
塑性变形的形式:滑移和*孪生。 金属常以滑移方式发生塑性变形。 ㈠ 滑移 滑移是指晶体的一部分沿一定的晶
面和晶向相对于另一部分发生滑动 位移的现象。
1、滑移变形的特点 : ⑴ 滑移只能在切应力的作
用下发生。产生滑移的最 小切应力称临界切应力.
⑵ 滑移常沿晶体中原 子密度最大的晶面和 晶向发生。因原子密 度最大的晶面和晶向 之间原子间距最大, 结合力最弱,产生滑 移所需切应力最小。
弥散强化的原因是由于硬的颗粒不易被切变,因而 阻碍了位错的运动,提高了变形抗力。
颗粒钉扎作用的电镜照片
位错切割 第二相粒 子示意图
电 镜 观 察
第二节 塑性变形对组织和性能的影响
一、产生纤维组织 金属发生塑性变形时,不仅外形发生变化,而且其内部的晶粒也
相应地被拉长或压扁。当变形量很大时,晶粒将被拉长为纤维状, 晶界变得模糊不清。 二、产生加工硬化 随着形变量的增大,由于晶粒破碎和位错密度的增加,金属的塑 性变形抗力迅速增大,使硬度和强度升高,塑性和韧性下降。
沿其发生滑移的晶面和晶向分别叫做滑移面和滑移 方向。通常是晶体中的密排面和密排方向。
一个滑移面
和其上的一
个滑移方向
构成一个滑
移系。
三种典型金属晶格的滑移系
晶格
体心立方晶格
吉林大学工程材料第2章 金属的塑性变形和再结晶
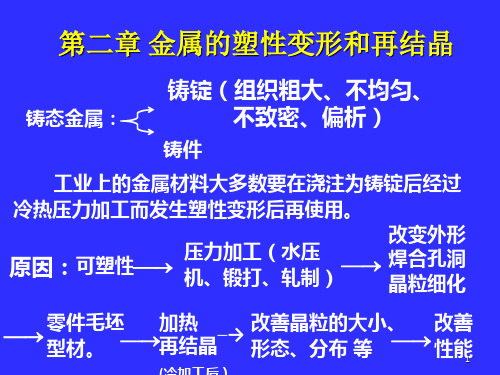
1、晶粒正常长大: 再结晶后的晶粒均匀、稳速地长大的现象。发生在
再结晶晶粒细小且均匀时。(希望的长大方式)
2、晶粒异常长大:
再结晶后的晶粒不均匀,急剧长大的现象。在再结晶 粒大小不均时,大晶粒吞并小晶粒,将得到异常粗大的 晶粒,也称“二次再结晶”。
d晶↑ 晶界面积↓ 能量↓∴晶粒长大是自发的 过程。因为粗晶是弱化,所以要避免晶粒长大,特别要
方向 σb(MPa) σ0.2(MPa) δ(%) ψ(%) αk(KJ/M2)
平行 701 垂直 659
460
17.5 62.8
608
431
10.0 31.0
294
34
四 、热加工的不足
在实际生产中,热加工与冷加工相比也有不足处
(1)热加工需要加热,不如冷加工简单易行。 (2)热加工制品的组织与性能不如冷加工均匀和易 于控制。
目的:1. 消除加工硬化 使、σ、HB↓ δ%、 %、ak↑ 2. 消除内应力,但保留加工硬化,使理化性能↑
对于冷加工后的金属,由于10%的变形能储存在 金属中,在加热时,随着温度的升高,原子活动能力 提高,在变形能的作用下,就要发生组织和性能的变 化,其主要包括三个阶段:回复、再结晶及晶粒长大。
18
底面对角线
1 面×3 方向=3
7
4、滑移机理
临界切应力(c): 能够发生滑移的最小切应
力叫做为)。当切应力()满足 c时滑移才 能发生。
铜的滑移临界切应力:理论计算 1500 Mpa 实际测试 1 MPa
滑移是由于滑移面上的位错运动造成的。
8
位错运动造成滑移示意图
9
10
二、 多晶体金属的塑性变形
700℃
金属塑性成形原理---第二章_金属塑性变形的物理基础
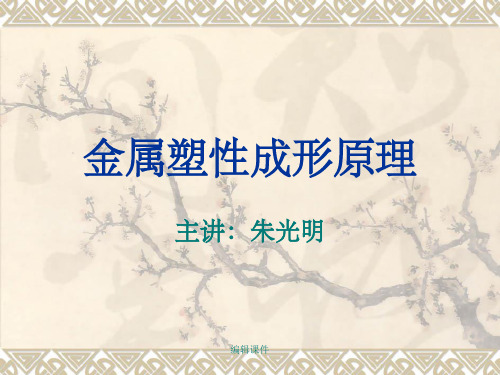
位错的攀移
❖ 螺型位错无攀移
❖ 正攀移——正刃型位错位错线上移
负刃型位错位错线下移
编辑课件
位错的交割
❖ 两根刃型位错线都在各自的滑移面上移动,
则在相遇后交截分别形成各界,形成割阶后
仍分别在各自的平面内运动。
❖ 刃型位错和螺型位错交割时,在各自的位错
线上形成刃型割阶,位错线也能继续滑移。
❖ 螺型位错和螺型位错交割时,相交后形成的
❖ 假设:理想晶体两排原子相距为a,同排原子间距
为b。原子在平衡位置时,能量处于最低的位置。
在外力τ作用下,原子偏离平衡位置时,能量上升,
原子能量随位置的变化为一余弦函数。
❖ 通过计算晶体的临界剪切应力,并与实际的临界
剪切应力进行比较,人们发现,理论计算的剪切
强度比实验所得到的剪切强度要高一千倍以上。
编辑课件
典型的晶胞结构
编辑课件
典型的晶胞结构
编辑课件
三种晶胞的晶格结构
编辑课件
一、塑性变形机理
实际金属的晶体结构
❖ 单晶体:各方向上的原子密度不同——各向
异性
❖ 多晶体:晶粒方向性互相抵消——各向同性
❖ 塑性成形所用的金属材料绝大多数为多晶
体,其变形过程比单晶体复杂的多。
编辑课件
多晶体塑性变形的分类
加工中,会使变形力显著增
加,对成形工件和模具都有
III.抛物线硬化阶段:
一定的损害作用;但利用金
与位错的交滑移过程有关,
θ3
随应变增加而降低,应力应变
属加工硬化的性质,对材料
曲线变为抛物线。
进行预处理,会使其力学性
能提高
编辑课件
2.2 金属热态下的塑性变形
实验二 金属的塑性变形与再结晶

实验二金属的塑性变形与再结晶一、实验目的1、了解工业纯铁经冷塑性变形后,变形量对硬度和显微组织的影响2、研究变形量对工业纯铝再结晶退火后晶粒大小的影响二、实验原理金属在外力作用下,当应力超过其弹性极限时将发生不可恢复的永久变形称为塑性变形。
金属发生塑性变形后,除了外形和尺寸发生改变外,其显微组织与各种性能也发生明显的变化。
经塑性变形后,随着变形量的增加,金属内部晶粒沿变形方向被拉长为偏平晶粒。
变形量越大,晶粒伸长的程度越明显。
变形量很大时,各晶粒将呈现出“纤维状”组织。
同时内部组织结构的变化也将导致机械性能的变化。
即随着变形量的增加,金属的强度、硬度上升,塑性、韧性下降,这种现象称为加工硬化或应变硬化。
在本实验中,首先以工业纯铁为研究对象,了解不同变形量对硬度和显微组织的影响。
冷变形后的金属是不稳定的,在重新加热时会发生回复、再结晶和晶粒长大等过程。
其中再结晶阶段金属内部的晶粒将会由冷变形后的纤维状组织转变为新的无畸变的等轴晶粒,这是一个晶粒形核与长大的过程。
此过程完成后金属的加工硬化现象消失。
金属的力学性能将取决于再结晶后的晶粒大小。
对于给定材料,再结晶退火后的晶粒大小主要取决于塑性变形时的变形量及退火温度等因素。
变形量越大,再结晶后的晶粒越细;金属能进行再结晶的最小变形量通常在2~8%之间,此时再结晶后的晶粒特别粗大,称此变形度为临界变形度。
大于此临界变形度后,随变形量的增加,再结晶后的晶粒逐渐细化。
在本实验中将研究工业纯铝经不同变形量拉伸后在550℃温度再结晶退火后其晶粒大小,从而验证变形量对再结晶晶粒大小的影响。
三、实验设备和材料1、实验设备箱式电阻炉、万能拉伸机、卡尺、低倍4X型金相显微镜、洛氏硬度计等2、实验材料(1)变形度为0%、30%、50%、70%的工业纯铁试样两套,其中一套用于塑性变形后的硬度测定,一套为已制备好的不同变形量下的金相标准试样,用于观察组织(2)工业纯铝试样,尺寸为160mm×20m m×0.5mm,(3)腐蚀液:40mlHNO3+30mlHCl+30mlH2O+5g纯Cu),硝酸溶液四、实验内容及步骤1、测定工业纯铁的硬度(HRB )与变形度的关系,观察不同塑性变形量后工业纯铁的金相显微组织(1)将工业纯铁的试样在万能拉伸实验机上分别进行0%、30%、50%、70%的压缩变形。
第二章_金属塑性变形的物理基础

超塑性的特点
超塑性变形的一般特点: 1、大伸长率 2、无缩颈 3、低流动应力 4、易成形
采用超塑性成形工艺,可获得形状复杂和尺寸精确的锻件, 而变形力大大降低 。
超塑性成形实例
b 弥散强化
位错切过第二相粒子(表面能、错排能、 粒子阻碍位错运动)
四 塑性变形对金属组织和性能的影响
1 对组织结构的影响 (1) 形成纤维组织
晶粒拉长 杂质呈细带状或链状分布
H62黄铜挤压的带状组织
(2) 亚结构
变形量增大 位错缠结 位错胞 (大量位错缠结在胞壁,胞内位错密度低)
(3) 形变织构
四 塑性变形对金属组织和性能的影响
2 对力学性能的影响(加工硬化) (1)加工硬化(形变强化、冷作强化):随变形 量的增加,材料的强度、硬度升高而塑韧性下降 的现象。
2 对力学性能的影响(加工硬化)
强化金属的重要途径
利 提高材料使用安全性
(2)利弊
材料加工成型的保证
弊 变形阻力提高,动力消耗增大
孪生的特点
(1)孪生是一部分晶体沿孪晶面相对于另一部分晶体 作切变,切变时原子移动的距离是孪生方向原子间距的 分数倍;孪生是部分位错运动的结果;孪晶面两侧晶体 的位向不同,呈镜面对称;孪生是一种均匀的切变。
孪生的特点
(2)孪晶的萌生一般需 要较大的应力,但随后长 大所需的应力较小,其拉 伸曲线呈锯齿状。孪晶核 心大多是在晶体局部高应 力区形成。变形孪晶一般 呈片状。变形孪晶经常以 爆发方式形成,生成速率 较快。
位错密度越高,金属的强度、硬度越高。
S:位错线长度,V:体积,ρ:位错密度
02第二章金属塑性变形的物理基础

Fe-C合金(钢铁)
Fe-0.8C
-
Fe-(1.3,1.6,1.9)C -
GCr15
0.42
Fe-1.5C-1.5Cr
-
Fe-1.37C-1.04Mn0.12V
-
AISI01(0.8C)
0.5
52160
0.6
高级合金
901
-
Ti-6Al-4V
0.85
210~250 470 540 1200 817 1200 1220
合金成分(Wt%) 共析合金 Zn-22Al 共晶合金
Zn-5Al
m 延伸率δ(%) 变形温度(℃)
0.5
>1500
200~300
0.48~ 0.5
300
200~360
Al-33Cu Al-Si Cu-Ag
Mg-33Al Sn-38Pb Bi-44Sn
Pb-Cd
0.9 - 0.53 0.85 0.59 - 0.35
一、概念和种类
(一)概念 具有超常的均匀变形能力,伸长率达到百分之几 百~百分之几千。
伸长率:δ>200%;
应变速率敏感性指数:m>0.3;
抗缩颈能力大。
特点:大伸长率、低流动应力、易成形。
(二)种类
1.细晶超塑性(结构超塑性或恒温超塑性) 条件:a.晶粒超细化和等轴长(<10um);
b.恒温条件的下限温度0.5Tm
Al-Zn-Ca Cu基合金 Cu-9.5Al-4Fe Cu-40Zn
0.5 0.43 0.9 0.9
- 0.72 -
0.64 0.64
1800~2000 1310 100 1550 >1000 >600 267
- 1、下载文档前请自行甄别文档内容的完整性,平台不提供额外的编辑、内容补充、找答案等附加服务。
- 2、"仅部分预览"的文档,不可在线预览部分如存在完整性等问题,可反馈申请退款(可完整预览的文档不适用该条件!)。
- 3、如文档侵犯您的权益,请联系客服反馈,我们会尽快为您处理(人工客服工作时间:9:00-18:30)。
σ
σ
铜多晶试样拉伸后形成的滑移带
㈢ 晶粒大小对金属力学性能的影响 金属的晶粒越细,其强度和硬度越高。 金属的晶粒越细,其强度和硬度越高。 因为金属晶粒越 因为金属晶粒越 金属 细,晶界总面积 越大, 越大,位错障碍 越多;需要协调 越多; 的具有不同位向 的晶粒越多, 的晶粒越多,使 金属塑性变形的 抗力越高。 抗力越高。
韧性断口
脆性解理断口
塑性变形的形式:滑移和 孪生 孪生。 塑性变形的形式:滑移和*孪生。 金属常以滑移方式发生塑性变形。 金属常以滑移方式发生塑性变形。 ㈠ 滑移 滑移是指晶体的一部分沿一定的晶 滑移是指晶体的一部分沿一定的晶 面和晶向相对于另一部分发生滑动 位移的现象。 位移的现象。
1、滑移变形的特点 : 、 ⑴ 滑移只能在切应力的作 用下发生。 用下发生。产生滑移的最 小切应力称临界切应力 小切应力称临界切应力. 临界切应力
Cu-Ni合金成分与性能关系 合金成分与性能关系
二、多相合金的塑性变形与弥散强化 当合金的组织由多相混合物组成时, 当合金的组织由多相混合物组成时,合金的塑性变 形除与合金基体的性质 有关外, 有关外,还与第二相的 性质、形态、大小、数 性质、形态、大小、 量和分布有关。 量和分布有关。第二相 可以是纯金属、 可以是纯金属、固溶体 或化合物, 或化合物,工业合金中 第二相多数是化合物。 第二相多数是化合物。
⑵ 滑移常沿晶体中原 子密度最大的晶面和 晶向发生。 晶向发生 。 因原子密 度最大的晶面和晶向 之间原子间距最大, 之间原子间距最大 , 结合力最弱, 结合力最弱 , 产生滑 移所需切应力最小。 移所需切应力最小。 沿其发生滑移的晶面和晶向分别叫做滑移面和 沿其发生滑移的晶面和晶向分别叫做滑移面和滑移 滑移面 方向。通常是晶体中的密排面和密排方向。 方向。通常是晶体中的密排面和密排方向。
孪生示意图
孪晶组织
与滑移相比: 与滑移相比: 孪生使晶格位向发生改变; 孪生使晶格位向发生改变; 所需切应力比滑移大得多, 变形速度极快, 接近声速; 所需切应力比滑移大得多 变形速度极快 接近声速 孪生时相邻原子面的相对位移量小于一个原子间距. 孪生时相邻原子面的相对位移量小于一个原子间距
密排六方晶格金属滑移系少,常以孪生方式变形。 密排六方晶格金属滑移系少,常以孪生方式变形。 体心立方晶格金属只有在低温或冲击作用下才发生 孪生变形。面心立方晶格金属, 孪生变形。面心立方晶格金属,一般不发生孪生变 形,但常发现有孪晶存在,这是由于相变过程中原 但常发现有孪晶存在, 子重新排列时发生错排而产生的, 退火孪晶。 子重新排列时发生错排而产生的,称退火孪晶。
颗粒钉扎作用的电镜照片
位错切割 第二相粒 子示意图
电 镜 观 察
第二节 塑性变形对组织和性能的影响
一、产生纤维组织 金属发生塑性变形时,不仅外形发生变化,而且其内部的晶粒也 金属发生塑性变形时,不仅外形发生变化,而且其内部的晶粒也 相应地被拉长或压扁。当变形量很大时,晶粒将被拉长为纤维状, 相应地被拉长或压扁。当变形量很大时,晶粒将被拉长为纤维状, 晶界变得模糊不清 得模糊不清。 晶界变得模糊不清。 二、产生加工硬化 随着形变量的增大,由于晶粒破碎和位错密度的增加, 随着形变量的增大,由于晶粒破碎和位错密度的增加,金属的塑 性变形抗力迅速增大,使硬度和强度升高,塑性和韧性下降。 性变形抗力迅速增大,使硬度和强度升高,塑性和韧性下降。
工业纯铁在塑性变形前后的组织变化
(a) 正火态
(b) 变形 变形40%
(c) 变形 变形80%
5%冷变形纯铝中的位错网 冷变形纯铝中的位错网
加工硬化:随冷塑性变形量增加,金属的强度、硬度提高, 加工硬化:随冷塑性变形量增加,金属的强度、硬度提高, 塑性、韧性下降的现象称加工硬化。 加工硬化 塑性、韧性下降的现象称加工硬化。
1040钢(0.4%C)
黄铜 黄铜 铜 1040钢 (0.4%C)源自铜冷塑性变形量,%
冷塑性变形量,%
产生加工硬化的原因:金属发生塑性变形时, 产生加工硬化的原因 位错密度增加, 位错间的交互作用增强, 相互 缠结, 造成位错运动阻力的增大, 引起塑性变 形抗力提高。另一方面由于晶粒破碎细化, 使 强度得以提高。在生产中可通过冷轧、冷拔提 高钢板或钢丝的强度。 没有加工硬化, 金属就不会发生均匀塑性变形。 没有加工硬化 金属就不会发生均匀塑性变形。 加工硬化是强化金属的重要手段之一, 加工硬化是强化金属的重要手段之一,对于不 能热处理强化的金属和合金尤为重要。 能热处理强化的金属和合金尤为重要。
当滑移面、滑移方向与外力方向都呈 °角时, 当滑移面、滑移方向与外力方向都呈45°角时,滑移
F
A1
韧性断口
2、滑移的机理 、 把滑移设想为刚性整体滑动所需的 理论临界切应力值比实际测量临界 切应力值大3-4个数量级 切应力值大 个数量级。滑移是通 过滑移面上位错的运动来实现的。 过滑移面上位错的运动来实现的。
应变
脆性 材料 塑性材料
通过细化晶粒来同时 提高金属的强度、 提高金属的强度、硬 度、塑性和韧性的方 法称细晶强化 细晶强化。 法称细晶强化。
*第二节 合金的塑性变形与强化
合金可根据组织分为单相固溶体和多相混合物两种. 合金可根据组织分为单相固溶体和多相混合物两种 单相固溶体 两种 合金元素的存在,使合金的变形与纯金属显著不同 合金元素的存在,使合金的变形与纯金属显著不同.
一个滑移面 和其上的一 个滑移方向 构成一个滑 构成一个滑 移系。 移系。
三种典型金属晶格的滑移系
晶格 滑移面 {110} {110} {111} 滑移 方向 滑移系 体心立方晶格 {111} 面心立方晶格 密排六方晶格
滑移系越多,金属发生滑移的可能性越大, 滑移系越多,金属发生滑移的可能性越大,塑性也 越好,其中滑移方向对塑性的贡献比滑移面更大。 越好,其中滑移方向对塑性的贡献比滑移面更大。 因而金属的塑性,面心立方晶格好于体心立方晶格 因而金属的塑性,面心立方晶格好于体心立方晶格, 体心立方晶格好于密排六方晶格。 体心立方晶格好于密排六方晶格。
切应力作用下的变形和滑移面向外力方向的转动
转动的原因: 转动的原因:晶体滑移后使正应 力分量和切应力分量组成了力偶. 力分量和切应力分量组成了力偶 方向上切应力 最大, 最大,因而最 容易发生滑移. 容易发生滑移 滑移后, 滑移后 滑移 面两侧晶体的 位向关系未发 生变化。 生变化。
F A0 A0
刃位错的运动
*㈡ 孪生 ㈡ 孪生是指晶体的一 孪生是指晶体的一 部分沿一定晶面和 晶向相对于另一部 分所发生的切变。 分所发生的切变。
发生切变的部分称孪生带或孪晶, 发生切变的部分称孪生带或孪晶,沿其发生孪生的 孪生带 晶面称孪生面。 晶面称孪生面。 孪生面 孪生的结果使孪生面两侧的晶体呈镜面对称。 孪生的结果使孪生面两侧的晶体呈镜面对称。
多 脚 虫 的 爬 行
滑移是通过滑移面上位错的运动来实现的
晶体通过位错运动产生滑移时, 晶体通过位错运动产生滑移时,只 在位错中心的少数原子发生移动, 在位错中心的少数原子发生移动, 它们移动的距离远小于一个原子间 距,因而所需临界切应力小,这种 因而所需临界切应力小, 现象称作位错的易动性。 现象称作位错的易动性。 位错的易动性
晶 粒 大 小 与 金 属 强 度 关 系
金属的晶粒越细,其塑性和韧性也越高。 金属的晶粒越细,其塑性和韧性也越高。 因为晶粒越细,单位体积内晶粒数目越多, 因为晶粒越细,单位体积内晶粒数目越多,参与变 晶粒越细 形的晶粒数目也越 多,变形越均匀, 变形越均匀, 使在断裂前发生较 大的塑性变形。强 大的塑性变形。 度和塑性同时增加, 度和塑性同时增加 金属在断裂前消耗 的功也大,因而其 的功也大, 韧性也比较好。 韧性也比较好。
产生固溶强化的原因, 产生固溶强化的原因,是由于溶质原子与位错相互作 用的结果,溶质原子不仅使晶格发生畸变, 用的结果,溶质原子不仅使晶格发生畸变,而且易被 吸附在位错附近形成柯氏气团,使位错被钉扎住, 吸附在位错附近形成柯氏气团,使位错被钉扎住,位 错要脱钉,则必须增加外力,从而使变形抗力提高 错要脱钉,则必须增加外力,从而使变形抗力提高.
固溶体第二相) α+β钛合金 固溶体第二相 β钛合金(固溶体第二相
当在晶界呈网状分布时,对合金的强度和塑性不利; 当在晶界呈网状分布时,对合金的强度和塑性不利; 当在晶内呈片状分布时,可提高强度、硬度, 当在晶内呈片状分布时,可提高强度、硬度,但会 降低塑性和韧性; 降低塑性和韧性;
珠光体
当在晶内呈颗粒状弥散分布时,第二相颗粒越细, 当在晶内呈颗粒状弥散分布时,第二相颗粒越细, 分布越均匀,合金的强度、硬度越高,塑性、 分布越均匀,合金的强度、硬度越高,塑性、韧性 略有下降,这种强化方法称弥散强化或沉淀强化。 略有下降,这种强化方法称弥散强化或沉淀强化。 弥散强化 弥散强化的原因是由于硬的颗粒不易被切变, 弥散强化的原因是由于硬的颗粒不易被切变,因而 是由于硬的颗粒不易被切变 阻碍了位错的运动,提高了变形抗力。 阻碍了位错的运动,提高了变形抗力。
奥氏体
珠光体
一、单相固溶体合金的塑性变形与固溶强化 单相固溶体合金组织与纯金属相同, 单相固溶体合金组织与纯金属相同,其塑性变形过程 也与多晶体纯金属相似。 随溶质含量增加, 也与多晶体纯金属相似。但随溶质含量增加,固溶体 的强度、硬度提高,塑性、韧性下降, 固溶强化。 的强度、硬度提高,塑性、韧性下降,称固溶强化。
晶界对塑性变形的影响
Cu-4.5Al合金晶 合金晶 界的位错塞积
2、晶粒位向的影响 、 由于各相邻晶粒位向不同, 由于各相邻晶粒位向不同,当一个晶粒发生塑性变形 时,为了保持金属的连续性,周围的晶粒若不发生塑 为了保持金属的连续性, 性变形,则必以弹性变形来与之协调。 性变形,则必以弹性变形来与之协调。这种弹性变形 便成为塑性变形晶 粒的变形阻力。由 粒的变形阻力。 于晶粒间的这种相 互约束, 互约束,使得多晶 体金属的塑性变形 抗力提高。 抗力提高。