精实生产与及时生产系统
适时生产JIT体系

适时生产JIT体系1. 什么是适时生产JIT体系?适时生产JIT(Just-in-Time)体系是一种管理和生产系统,旨在通过减少库存波动来实现高效生产。
JIT体系的核心理念是在所需时给予所需数量的物料,减少浪费和过剩库存。
这种管理方式注重最优化生产和供应链过程,增强生产效率,降低成本,提高质量。
2. JIT体系的特点•精准预测需求:JIT体系依赖准确的需求预测和供应链协调,以确保在所需时提供所需物料。
•最小化库存:JIT致力于最小化库存,并通过及时供应链管理来实现减少在途和现场库存量。
•高效生产:JIT体系强调生产线平衡、快速切换和零库存设定,以降低生产成本并提高生产效率。
•连续改进:JIT倡导持续改进和精益生产,以提高产品质量和生产效率。
3. JIT体系的优势•降低库存成本:JIT系统使企业能够减少库存水平,从而降低库存成本和占用资金。
•提高生产效率:通过精益生产和及时供应管理,JIT体系可优化生产流程,提高效率。
•增强供应链协调:JIT推动供应链各环节的协调和信息共享,确保物料按需交付。
•提高质量:JIT体系通过减少变动、浪费和传输时间,有助于提高产品质量。
4. JIT体系的挑战•需求波动:需求波动和不确定性可能导致JIT系统难以有效运作。
•供应链延迟:供应链延迟和不稳定的供应可能影响JIT体系的实施。
•生产线平衡:保持生产线平衡和快速切换可能需要较高的管理和技术能力。
•依赖于准确预测:JIT体系对准确的需求预测和生产计划至关重要,因此可能受到不确定性的影响。
5. JIT体系的应用案例案例一:Toyota生产模式Toyota生产模式是JIT体系的经典案例,通过精益生产和及时供应管理实现了高效生产和优质产品。
案例二:Dell生产模式Dell公司采用了JIT体系,通过定制生产和快速交付满足客户需求,降低库存和提高生产效率。
6. 总结适时生产JIT体系是一种高效的管理和生产系统,通过减少库存和提高供应链效率实现产品生产的精准和及时。
精益生产案例
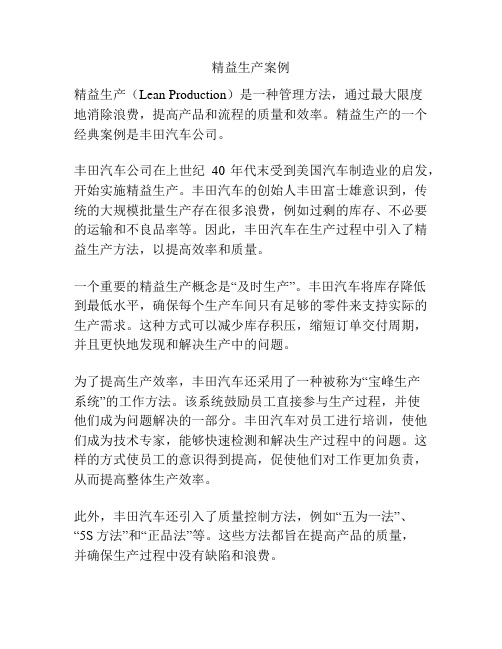
精益生产案例精益生产(Lean Production)是一种管理方法,通过最大限度地消除浪费,提高产品和流程的质量和效率。
精益生产的一个经典案例是丰田汽车公司。
丰田汽车公司在上世纪40年代末受到美国汽车制造业的启发,开始实施精益生产。
丰田汽车的创始人丰田富士雄意识到,传统的大规模批量生产存在很多浪费,例如过剩的库存、不必要的运输和不良品率等。
因此,丰田汽车在生产过程中引入了精益生产方法,以提高效率和质量。
一个重要的精益生产概念是“及时生产”。
丰田汽车将库存降低到最低水平,确保每个生产车间只有足够的零件来支持实际的生产需求。
这种方式可以减少库存积压,缩短订单交付周期,并且更快地发现和解决生产中的问题。
为了提高生产效率,丰田汽车还采用了一种被称为“宝峰生产系统”的工作方法。
该系统鼓励员工直接参与生产过程,并使他们成为问题解决的一部分。
丰田汽车对员工进行培训,使他们成为技术专家,能够快速检测和解决生产过程中的问题。
这样的方式使员工的意识得到提高,促使他们对工作更加负责,从而提高整体生产效率。
此外,丰田汽车还引入了质量控制方法,例如“五为一法”、“5S方法”和“正品法”等。
这些方法都旨在提高产品的质量,并确保生产过程中没有缺陷和浪费。
由于实施了精益生产,丰田汽车取得了巨大的成功。
丰田汽车以其高质量、可靠性和高效率而闻名全球。
丰田车的生产周期非常短,车辆的质量也得到了高度保证。
丰田汽车通过精益生产方法的实施,有效地提高了生产效率,减少了浪费,并提高了产品质量。
这为其他企业提供了一个成功的案例,也促进了全球制造业的转型和发展。
精益生产管理体系

精益⽣产管理体系精益⽣产管理体系是⼀个包含了多种制造技术和管理技术的综合体系。
该体系由标准作业、均衡⽣产等基础性管理活动,以及准时化⽣产和⾃动化两⼤⽀柱构成。
⼀、标准作业标准作业是指在⽣产过程中,以⼈的操作为中⼼,去掉浪费的动作,把有价值的作业编排成有效的操作顺序,使之与设备布局以及节拍时间相吻合。
标准作业经过对作业⽅法的研究后制定标准作业程序,包括对有关设施、环境、材料、负荷、动作等进⾏标准化。
实⾏标准作业的前提是以⼈的动作为中⼼考虑问题,并且是在同样条件下能够重复进⾏的作业。
⼆、均衡⽣产⽣产的均衡化是实现精益⽣产管理的最重要的前提条件。
均衡化⽣产要求的是⽣产数量的均衡和产品种类的均衡,即总装配线向各前⼯序领取零部件时,要均匀地领取各种零部件,实⾏混流⽣产。
要防⽌在某⼀段时间内集中⽣产同⼀种零部件,以免造成前⽅⼯序的闲忙不均,以及由此引发的⽣产混乱。
⽣产的均衡化使得零部件被领取时的数量变化达到最低程度,即各⼯序每天如⼀地以相近似的时间间隔领取数量相近的零部件,由此,各⼯序得以⼀定速度和⼀定数量进⾏⽣产。
均衡还包括⼯时、设备负荷的全部均衡。
设备、⼯装始终处于良好状态,材料、⽑坯供应准时,⼯⼈技术⽔平和出勤率良好、稳定等都是实现均衡⽣产的前提。
此外,加强⽣产技术准备部门、辅助⽣产部门、供应服务部门的⼯作,特别是优化⽣产计划和强化对⽣产过程的监控,则是实现均衡⽣产的重要保证。
三、⾃动化⾃动化是精益⽣产⽅式的两⼤⽀柱之⼀,也被称为“智能⾃动化”或者“具有⼈的判断能⼒的⾃动化”。
是让设备能⾃律地控制异常情况,是具有⼈的判断能⼒的⾃动化,⾃动化的主要理念是:应该在作业流程中及时进⾏源头质量管理,必须⽤有效的⽅法在发⽣异常或质量缺陷时⽴即探测到,并⽴即使⽣产暂停,使员⼯可以⽴即解决问题,避免异常扩⼤或质量缺陷进⼊到下游流程。
这种品质管理⽐事后检验出问题再设法纠正问题更具成效且成本更低。
⾃动化在很多时候含有“⾃动化”的含义,但绝不仅仅限于⽤机械化设备代替⼿⼯作业。
JIT管理及精益生产
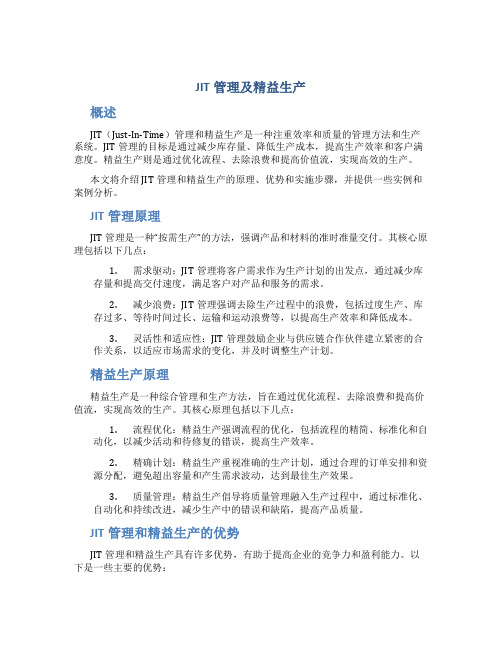
JIT管理及精益生产概述JIT(Just-In-Time)管理和精益生产是一种注重效率和质量的管理方法和生产系统。
JIT管理的目标是通过减少库存量、降低生产成本,提高生产效率和客户满意度。
精益生产则是通过优化流程、去除浪费和提高价值流,实现高效的生产。
本文将介绍JIT管理和精益生产的原理、优势和实施步骤,并提供一些实例和案例分析。
JIT管理原理JIT管理是一种“按需生产”的方法,强调产品和材料的准时准量交付。
其核心原理包括以下几点:1.需求驱动:JIT管理将客户需求作为生产计划的出发点,通过减少库存量和提高交付速度,满足客户对产品和服务的需求。
2.减少浪费:JIT管理强调去除生产过程中的浪费,包括过度生产、库存过多、等待时间过长、运输和运动浪费等,以提高生产效率和降低成本。
3.灵活性和适应性:JIT管理鼓励企业与供应链合作伙伴建立紧密的合作关系,以适应市场需求的变化,并及时调整生产计划。
精益生产原理精益生产是一种综合管理和生产方法,旨在通过优化流程、去除浪费和提高价值流,实现高效的生产。
其核心原理包括以下几点:1.流程优化:精益生产强调流程的优化,包括流程的精简、标准化和自动化,以减少活动和待修复的错误,提高生产效率。
2.精确计划:精益生产重视准确的生产计划,通过合理的订单安排和资源分配,避免超出容量和产生需求波动,达到最佳生产效果。
3.质量管理:精益生产倡导将质量管理融入生产过程中,通过标准化、自动化和持续改进,减少生产中的错误和缺陷,提高产品质量。
JIT管理和精益生产的优势JIT管理和精益生产具有许多优势,有助于提高企业的竞争力和盈利能力。
以下是一些主要的优势:1.降低库存量:通过JIT管理和精益生产,企业可以减少库存量和库存成本,降低资金占用和风险。
2.提高生产效率:JIT管理和精益生产可以优化生产流程,去除浪费和瓶颈,提高生产效率和产能利用率。
3.准时交付:JIT管理和精益生产强调准时准量交付,可以提高客户满意度,增强企业的竞争优势。
精益生产的定义

精益生产的定义什么是精益生产?精益生产是一种管理理念和生产方法,旨在通过最大程度地减少资源浪费,以实现高效生产和提供价值给客户。
精益生产的核心原则是通过不断改善流程,消除浪费,提高生产效率和质量。
这一理念最初起源于丰田汽车公司的生产体系,后来被广泛应用于其他行业和领域。
精益生产的目标精益生产的主要目标是实现以下几点:1.提高生产效率:通过消除浪费,优化流程,提高生产效率和生产率。
2.降低成本:通过减少废品和不必要的生产成本,实现成本的最小化。
3.提高产品质量:通过改进生产过程和流程控制,提高产品质量和稳定性。
4.提高客户满意度:通过及时交付高质量的产品,提高客户满意度和忠诚度。
精益生产的原则精益生产遵循一些核心原则,其中包括:1.价值:专注于为客户创造价值,只集中精力和资源在对客户有意义的活动上。
2.价流:优化价值流动,消除所有形式的浪费,确保产品/服务按需求流动。
3.拉动:基于客户需求拉动生产,避免过度生产和库存积压。
4.流程改进:不断改进生产过程,强调团队合作和持续学习。
5.标准化:建立标准化工作流程和操作规程,确保质量和稳定性。
精益生产的实践精益生产的实践方法包括:1.价值流分析:分析整个价值流,识别不必要的步骤和浪费。
2.5S整理法:通过整理、整顿、清扫、清洁、标准化等步骤,改善工作环境和效率。
3.持续改进:建立改进文化和机制,鼓励员工提出改进建议和参与改进活动。
4.精益供应链管理:与供应商建立紧密合作关系,实现供应链的高效协同和配合。
精益生产的应用范围精益生产不仅适用于制造业,也适用于服务业和其他领域。
在制造业中,精益生产可以帮助企业提高生产效率、降低成本、改善质量;在服务业中,精益生产可以帮助企业提高服务效率、提升客户体验、降低服务成本。
总结精益生产是一种重要的管理理念和生产方法,其核心目标是通过最大程度地减少浪费,实现高效生产和提供价值给客户。
精益生产的原则和实践方法可以帮助企业提高生产效率、降低成本、改善质量,从而获得持续竞争优势。
JIT及时化生产

TQM 精 益 质 量 保 证
生 产 与 物 流 规 划
TPM 全 面 设 备 维 护
产 品 开 发 设 计 系 统
现 代 IE 运 用
均 衡 化 同 步 化
全员现场5S活动 ·观念革新 ·全员改善活动
企业有效运营过程:
观念 革新
薪酬 体系
管理 创新 管理运营
业务 流程 现场 5S 高效 组织 工作 质量 目标 管理 统计 系统 有效 激励 改善 工具
制造型企业基础管理技术培训
JIT精益生产实务
精益生产概论
1、何谓精益生产方式 2、现代生产组织系统 3、精益生产追求的目标 4、精益生产实施过程全貌 5、精益生产案例
1、何谓精益生产方式
Lean Production
精益生产
1960年代开始,以丰田为代表的日本汽车制造业 通过实施JIT生产模式,以低成本、高质量的突出优 势迅速占领美国汽车市场,引发了美日之间长达十年 的汽车贸易战。 JIT——因其经营效率极限化被美国学者赞誉为 “精益生产”,并对人类的生产革命产生了长远影响。
S(安全)
F(柔性)
生产优先
以产定销
先保证出货, 安全嘛……
只有这个能 力……
安全第一 安全第一无工伤 符合标准 符合技术法规
快速应变 随时满足
CWMC 国慧顾问
三种生产方式比较
项 目 手工生产方式
完全按顾客要求 通用、灵活、便宜 粗略、丰富 懂设计制造 有较高操作技能 高 高
大批量生产方式
标准化,品种单一 专用、高效、昂贵 细致、简单、重复 不需要专业技能 高 低
精益生产简介:
精益生产(Lean Production,简称LP)是美国麻省理工学院根据在“国际汽车项目”研究中,基于 对日本丰田生产方式的研究和总结,于1990年提出的制造模式。 目前,在众多的生产管理的新思想、新理论中,精益生产与MRPII(制造资源计划)的影响 最为广泛,并进行过大量的实践。在我国,精益生产与MRPII的应用也正广泛地展开。此时,深 入开展对精益生产与MRPII管理思想内核的研究,正是在实践中进一步有效推进工业工程的基础。 1.精益生产的历史背景 精益生产起源于日本丰田汽车公司的一种生产管理方法。其核心是追求消除包括库存在内的 一切“浪费”,并围绕此目标发展了一系具体方法,逐渐形成了一套独具特色的生产经营管理体 系。 1.1管理技术背景
准时制和精益生产

准时制和精益生产引言准时制和精益生产是两种重要的生产管理方法,旨在提高生产效率和产品质量。
准时制的核心理念是以准时交付为导向,通过优化生产流程和管理系统,确保产品准时交付给客户。
精益生产则注重浪费的最小化,通过消除非价值增加的活动和优化价值增加活动,提高生产效率和减少成本。
本文将对准时制和精益生产进行详细介绍。
准时制准时制是一种以准时交付为导向的生产管理方法。
在准时制中,生产计划和交付时间被视为最重要的因素。
准时制通过合理安排生产流程、加强供应链管理和提高生产过程的稳定性,确保产品在规定的交付时间内准时交付给客户。
准时制的目标是提高交付准确率,降低订单滞留时间,增强客户满意度。
优点准时制的优点如下:1.准时交付:准时制确保产品按照预定的交付时间准时交付给客户,提高客户满意度和信任度。
2.降低库存成本:准时制通过精确的生产计划和交付时间,减少库存周转时间,降低库存成本。
3.优化生产流程:准时制要求对生产流程进行全面的规划和优化,提高生产效率和交付准确率。
4.提高供应链管理能力:准时制需要加强与供应商的合作,优化供应链管理,提高供应链的稳定性和准确性。
实施步骤下面是实施准时制的一般步骤:1.设定准时交付目标:确定产品的交付时间和目标准确率。
2.分析生产流程:通过对生产流程进行分析,找出存在的瓶颈和问题,并进行改进。
3.优化供应链:加强与供应商的合作,优化供应链管理,确保原材料和零部件的准时供应。
4.制定合理生产计划:根据准时交付目标和供应链的实际情况,制定合理的生产计划。
5.加强生产过程监控:通过加强生产过程的监控,及时发现和解决生产中的问题。
6.持续改进:通过周期性的评估和分析,不断改进生产流程和管理系统,提高交付准确率。
精益生产精益生产是一种以减少浪费为核心的生产管理方法。
精益生产的目标是通过消除非价值增加的活动和优化价值增加活动,提高生产效率和减少成本。
精益生产是由丰田汽车公司引入的一种生产管理方法,后来被广泛应用于其他行业。
APS精益生产排程系统操作
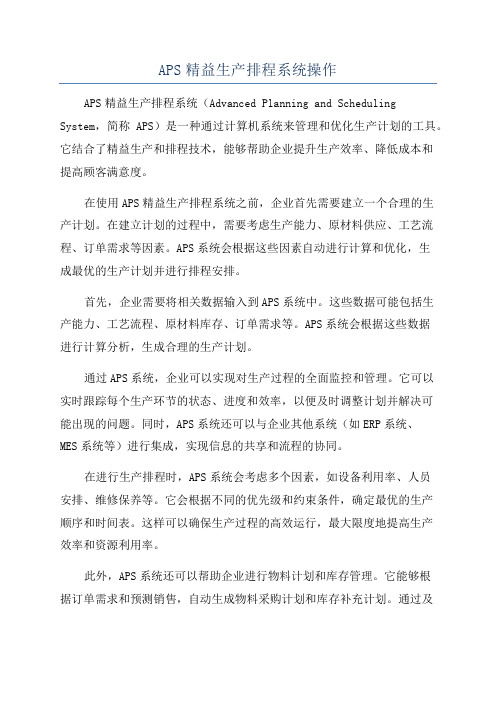
APS精益生产排程系统操作APS精益生产排程系统(Advanced Planning and Scheduling System,简称APS)是一种通过计算机系统来管理和优化生产计划的工具。
它结合了精益生产和排程技术,能够帮助企业提升生产效率、降低成本和提高顾客满意度。
在使用APS精益生产排程系统之前,企业首先需要建立一个合理的生产计划。
在建立计划的过程中,需要考虑生产能力、原材料供应、工艺流程、订单需求等因素。
APS系统会根据这些因素自动进行计算和优化,生成最优的生产计划并进行排程安排。
首先,企业需要将相关数据输入到APS系统中。
这些数据可能包括生产能力、工艺流程、原材料库存、订单需求等。
APS系统会根据这些数据进行计算分析,生成合理的生产计划。
通过APS系统,企业可以实现对生产过程的全面监控和管理。
它可以实时跟踪每个生产环节的状态、进度和效率,以便及时调整计划并解决可能出现的问题。
同时,APS系统还可以与企业其他系统(如ERP系统、MES系统等)进行集成,实现信息的共享和流程的协同。
在进行生产排程时,APS系统会考虑多个因素,如设备利用率、人员安排、维修保养等。
它会根据不同的优先级和约束条件,确定最优的生产顺序和时间表。
这样可以确保生产过程的高效运行,最大限度地提高生产效率和资源利用率。
此外,APS系统还可以帮助企业进行物料计划和库存管理。
它能够根据订单需求和预测销售,自动生成物料采购计划和库存补充计划。
通过及时准确地掌握物料需求和库存变动,企业可以降低缺货风险、提高服务水平,并减少库存成本。
在实际操作中,企业可以根据需要选择不同的排程算法和优化方法。
APS系统通常提供多种排程算法,如传统的Gantt图法、遗传算法、模拟退火算法等。
通过调整参数和优化目标,企业可以根据不同的需求制定适合自己的排程策略。
此外,为了保证APS系统的正常运行和精确计算,企业需要保持数据的准确性和及时更新。
定期进行系统维护和数据校对是确保系统有效运行的重要步骤。
精益生产基础知识概述
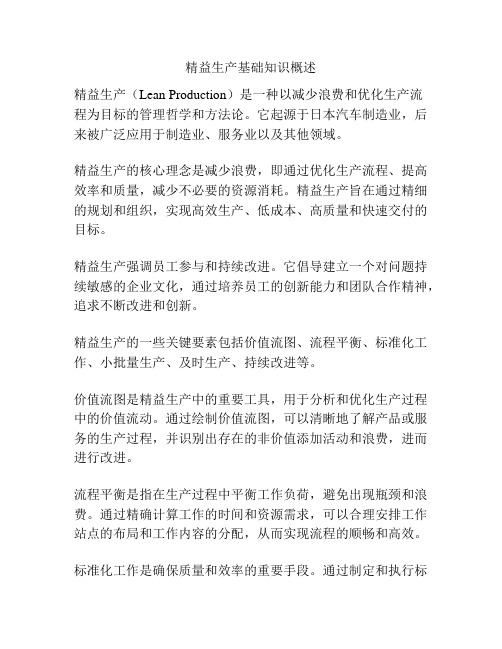
精益生产基础知识概述精益生产(Lean Production)是一种以减少浪费和优化生产流程为目标的管理哲学和方法论。
它起源于日本汽车制造业,后来被广泛应用于制造业、服务业以及其他领域。
精益生产的核心理念是减少浪费,即通过优化生产流程、提高效率和质量,减少不必要的资源消耗。
精益生产旨在通过精细的规划和组织,实现高效生产、低成本、高质量和快速交付的目标。
精益生产强调员工参与和持续改进。
它倡导建立一个对问题持续敏感的企业文化,通过培养员工的创新能力和团队合作精神,追求不断改进和创新。
精益生产的一些关键要素包括价值流图、流程平衡、标准化工作、小批量生产、及时生产、持续改进等。
价值流图是精益生产中的重要工具,用于分析和优化生产过程中的价值流动。
通过绘制价值流图,可以清晰地了解产品或服务的生产过程,并识别出存在的非价值添加活动和浪费,进而进行改进。
流程平衡是指在生产过程中平衡工作负荷,避免出现瓶颈和浪费。
通过精确计算工作的时间和资源需求,可以合理安排工作站点的布局和工作内容的分配,从而实现流程的顺畅和高效。
标准化工作是确保质量和效率的重要手段。
通过制定和执行标准化工作程序,可以减少变异和错误,提高产品和服务的一致性和可靠性。
小批量生产和及时生产是精益生产中的两个重要原则。
小批量生产可以减少库存和等待时间,降低成本和资源消耗。
及时生产则强调按需生产和按时交付,避免过产和库存积压。
持续改进是精益生产的核心精神。
它强调通过持续地观察、分析和改进,不断优化生产过程和提升绩效。
持续改进需要建立一个鼓励员工提出问题和改进建议的文化,同时提供必要的培训和支持。
总之,精益生产是一种在全球范围内被广泛应用的管理方法,它通过减少浪费和优化生产流程,实现高效生产、低成本、高质量和快速交付的目标。
它不断追求改进和创新,强调员工参与和持续学习,是现代企业管理中的重要理念和工具。
精益生产(Lean Production)是一种在制造业和服务业等领域中被广泛应用的管理哲学和方法论。
JIT生产方式的目标和方法体系

JIT生产方式的目标和方法体系JIT生产方式是一种以精益、高效为特点的生产管理模式,JIT全程是Just-In-Time的缩写,意为“及时生产”或“准时生产”。
其目标是通过精确控制产能、库存和交付周期,实现高效的生产流程,提高生产效率和质量,降低成本和浪费。
1.实现零库存:JIT生产方式追求低库存甚至零库存的理念,企业只在需要的时候才生产产品,减少存储成本和库存风险,提高流动性和资金回流速度。
2.实施精确交付:JIT生产方式通过准确把握市场需求和客户订货,提高生产准确率,确保按时交付,满足客户需求,提高客户满意度。
3.提高生产效率:JIT生产方式强调流程优化、无停机生产和原地作业等方法,最大限度地减少非生产时间,提高设备利用率和劳动生产率。
4.降低生产成本:JIT生产方式通过减少库存、避免超产和降低库房和仓储成本等方法,降低生产成本,提高企业盈利能力。
1.精确计划:JIT生产方式要求精确计划每个生产环节的需求量、产能和交付周期,确保准确把握生产过程中的各种变化和不确定性。
2. TPS系统:JIT生产方式的核心方法是“丰田生产系统”(Toyota Production System, TPS),通过精益生产、持续改进和质量保证等控制手段,实现高效、低成本、零缺陷的生产。
3.精益生产:JIT生产方式采用精益生产的原则:根据客户需求组织生产、减少浪费、实现零库存和及时交付等,以最大限度地满足市场需求和客户需求。
4.优化供应链:JIT生产方式强调供应链的精细管理,通过与供应商的紧密合作,提前共享需求信息和生产计划,减少物资采购和供应过程中的时间和浪费。
5.质量保证:JIT生产方式通过持续改进、投入少量毛病和零缺陷等控制手段,提高生产过程的质量,减少质量问题和再加工,提高成品率和产品合格率。
6.员工培训:JIT生产方式鼓励员工多技能开发和交叉培训,使员工在多个岗位上具备能力,灵活调配和利用人力资源,提高生产效率和响应速度。
精益生产系统

3 - 12
及时生产的要素 JIT Elements
小巧便宜机器 Small, inexpensive machines in process order
单件流生产, 反时针方向 One-piece flow production, counterclockwise
B. 设备自动化,提高生产率
Equipment autonomation to improve productivity
3 - 16
自働化 Jidoka
A. 减少不良品的工具或方法 Tools or Methods to Reduce Defects
发现不良品的产生 Detect defects when they occur 防止不良品进入下一道工序 Prevent defects from
取得销售和收益双增长 Achieve Growth in Sales & Earnings
保持竞争优势 Sustain the Competitive Advantages
提升利益相关者价值Improve Stakeholder Value
精益生产系统 Lean Production System
6西格玛流程能力 (西格玛改善) Six Sigma Process Capability (Sigma Kaizen) 改善突破法 Kaizen Breakthrough Methodology
目视控制 Visual Control
5S 信号灯 Andon
异常反应
Abnormality Response/Reaction 作用 / 责任
Roles and responsibilities 停工指引
WIP精益生产过程管理系统介绍
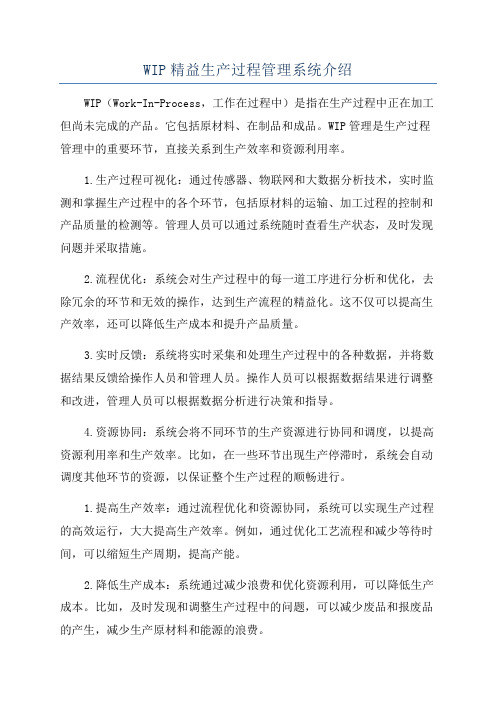
WIP精益生产过程管理系统介绍WIP(Work-In-Process,工作在过程中)是指在生产过程中正在加工但尚未完成的产品。
它包括原材料、在制品和成品。
WIP管理是生产过程管理中的重要环节,直接关系到生产效率和资源利用率。
1.生产过程可视化:通过传感器、物联网和大数据分析技术,实时监测和掌握生产过程中的各个环节,包括原材料的运输、加工过程的控制和产品质量的检测等。
管理人员可以通过系统随时查看生产状态,及时发现问题并采取措施。
2.流程优化:系统会对生产过程中的每一道工序进行分析和优化,去除冗余的环节和无效的操作,达到生产流程的精益化。
这不仅可以提高生产效率,还可以降低生产成本和提升产品质量。
3.实时反馈:系统将实时采集和处理生产过程中的各种数据,并将数据结果反馈给操作人员和管理人员。
操作人员可以根据数据结果进行调整和改进,管理人员可以根据数据分析进行决策和指导。
4.资源协同:系统会将不同环节的生产资源进行协同和调度,以提高资源利用率和生产效率。
比如,在一些环节出现生产停滞时,系统会自动调度其他环节的资源,以保证整个生产过程的顺畅进行。
1.提高生产效率:通过流程优化和资源协同,系统可以实现生产过程的高效运行,大大提高生产效率。
例如,通过优化工艺流程和减少等待时间,可以缩短生产周期,提高产能。
2.降低生产成本:系统通过减少浪费和优化资源利用,可以降低生产成本。
比如,及时发现和调整生产过程中的问题,可以减少废品和报废品的产生,减少生产原材料和能源的浪费。
3.提升产品质量:通过实时监测和数据分析,系统可以及时发现和处理生产过程中的问题,提高产品质量。
比如,可以实时检测产品的质量指标,及时发现问题,并采取相应措施进行调整和改进。
4.降低人为错误:系统通过自动化和智能化技术,减少人为因素对生产过程的影响,降低人为错误的产生。
例如,自动化设备可以减少操作人员的操作,减少人为错误的发生。
总之,WIP精益生产过程管理系统是一种基于精益生产理念和工业4.0技术的生产过程管理系统。
精益生产名词解析:JIT与Kaizen

精益生产名词解析:JIT与Kaizen Just-In-Time(JIT)(及时生产)
一种只在需要的时候才制造和运输所需数量产品的生产系统,。
JIT与Jidoka是丰田生产系统的两大支柱。
JIT以生产均衡化为基础,由三个运作方法组成:拉动系统,节拍时间,和连续流。
JIT的目标,在于全面消除各种浪费,尽可能的实现高质量,低成本、低资源消耗,以及最短的生产和运输交货时间。
尽管JIT的原则很简单,但却需要有钢铁般的纪律才能保证其有效的实施。
JIT理念的提出要归功于二十世纪三十年代的KiichiroToyota——丰田汽车公司的创始人。
1949-1950年,丰田公司总工TaiichiOhno迈出了他走向JIT目标的第一步.
参见:ContinuousFlow(连续流),Heijunka(均衡化),Jidoka(自动化),PullProduction (拉动生产),TaktTime(节拍时间),ToyotaProductionSystem(丰田生产系统)。
Kaizen(改善)
通过对整条价值流,或某个单一工序,进行持续改进,实现以最少的浪费创造更多的价值。
持续改善分为两个层次
1.整条价值流的改善,由管理层负责推动实施。
2.单个生产工序的改善,由工作团队领导负责实施。
价值流图是一个很好的工具,来发现整条价值流中应该在何处实施流动,以及持续改善。
参见:kaikaku(突破性改善);Plan,Do,Check,Act(计划、实施、检查、行动);ProcessVillage (加工群);ValueStreamMapping(VSM)价值流图。
精益生产体系LMS拉动系统概述

精益生产体系LMS拉动系统概述精益生产体系LMS拉动系统是一种以顾客需求为驱动的生产和物流模式。
它通过准确地预测顾客需求,使供应链中的生产和物流活动能够按需拉动,减少了库存和浪费,并提高了生产效率和顾客满意度。
LMS拉动系统的核心思想是根据真实的销售数据和市场需求,预测未来的顾客需求,并以此为基础进行计划和生产。
与传统的推动式生产不同,LMS拉动系统是根据客户的需求推动物料和资源的流动。
LMS拉动系统通过以下几个环节实现拉动生产和物流:1. 顾客需求预测:通过分析历史销售数据、市场趋势和其他相关因素,对未来的销售需求进行预测。
这可以帮助企业准确地安排生产计划,并避免过量的库存和生产。
2. 生产计划:根据顾客需求预测结果,制定生产计划。
生产计划要考虑生产能力、原材料供应和其他生产资源的可用性。
3. 物料采购和供应:根据生产计划,及时采购和供应所需的原材料和零部件。
在LMS拉动系统中,物料的供应是通过顾客需求的拉动完成的,避免了因推动式生产而产生的库存积压。
4. 生产和装配:根据生产计划和物料供应情况,进行生产和装配。
LMS拉动系统的目标是按时按量地生产和交付产品,以满足顾客需求。
5. 物流和配送:根据顾客订购情况,及时安排产品的物流和配送。
LMS拉动系统可以准确地追踪产品的流向和交付状态,保证顾客能够按时收到产品。
LMS拉动系统在实践中带来了许多好处。
首先,它能够减少库存和浪费,提高资源利用率。
其次,它能够提高生产效率,减少生产时间和成本。
此外,LMS拉动系统还能够提高顾客满意度,因为产品能够按时交付,符合顾客的需求。
总之,精益生产体系LMS拉动系统通过顾客需求的拉动,使生产和物流活动更加高效和精确。
它可以减少库存和浪费,提高生产效率和顾客满意度。
在竞争激烈的市场环境下,LMS拉动系统有助于企业保持竞争优势,并实现可持续发展。
LMS拉动系统作为精益生产体系的一部分,主要关注顾客需求的拉动,通过准确预测需求,并以此为基础进行生产和物流活动的安排。
精益生产术语解释
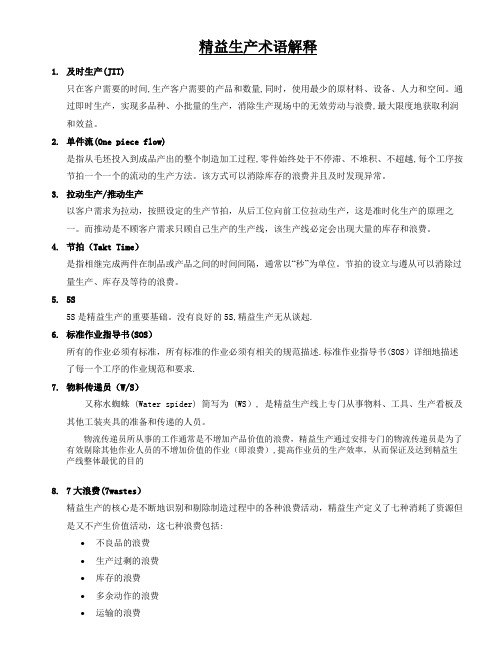
精益生产术语解释1.及时生产(JIT)只在客户需要的时间,生产客户需要的产品和数量,同时,使用最少的原材料、设备、人力和空间。
通过即时生产,实现多品种、小批量的生产,消除生产现场中的无效劳动与浪费,最大限度地获取利润和效益。
2.单件流(One piece flow)是指从毛坯投入到成品产出的整个制造加工过程,零件始终处于不停滞、不堆积、不超越,每个工序按节拍一个一个的流动的生产方法。
该方式可以消除库存的浪费并且及时发现异常。
3.拉动生产/推动生产以客户需求为拉动,按照设定的生产节拍,从后工位向前工位拉动生产,这是准时化生产的原理之一。
而推动是不顾客户需求只顾自己生产的生产线,该生产线必定会出现大量的库存和浪费。
4.节拍(Takt Time)是指相继完成两件在制品或产品之间的时间间隔,通常以“秒”为单位。
节拍的设立与遵从可以消除过量生产、库存及等待的浪费。
5.5S5S是精益生产的重要基础。
没有良好的5S,精益生产无从谈起.6.标准作业指导书(SOS)所有的作业必须有标准,所有标准的作业必须有相关的规范描述.标准作业指导书(SOS)详细地描述了每一个工序的作业规范和要求.7.物料传递员(W/S)又称水蜘蛛 (Water spider) 简写为 (WS), 是精益生产线上专门从事物料、工具、生产看板及其他工装夹具的准备和传递的人员。
物流传递员所从事的工作通常是不增加产品价值的浪费,精益生产通过安排专门的物流传递员是为了有效剔除其他作业人员的不增加价值的作业(即浪费),提高作业员的生产效率,从而保证及达到精益生产线整体最优的目的8.7大浪费(7wastes)精益生产的核心是不断地识别和剔除制造过程中的各种浪费活动,精益生产定义了七种消耗了资源但是又不产生价值活动,这七种浪费包括:•不良品的浪费•生产过剩的浪费•库存的浪费•多余动作的浪费•运输的浪费•等待的浪费•加工及流程的浪费9.自働化(Jidoka)将人的智能转化成自働机械,使机器能够自己识别和判断生产过程出现的缺陷和异常,并且在请求帮助时自动停机。
一汽的精益生产与准时生产
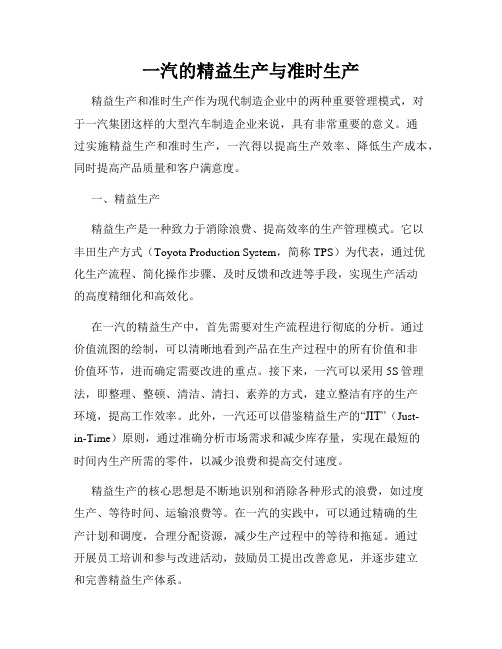
一汽的精益生产与准时生产精益生产和准时生产作为现代制造企业中的两种重要管理模式,对于一汽集团这样的大型汽车制造企业来说,具有非常重要的意义。
通过实施精益生产和准时生产,一汽得以提高生产效率、降低生产成本,同时提高产品质量和客户满意度。
一、精益生产精益生产是一种致力于消除浪费、提高效率的生产管理模式。
它以丰田生产方式(Toyota Production System,简称TPS)为代表,通过优化生产流程、简化操作步骤、及时反馈和改进等手段,实现生产活动的高度精细化和高效化。
在一汽的精益生产中,首先需要对生产流程进行彻底的分析。
通过价值流图的绘制,可以清晰地看到产品在生产过程中的所有价值和非价值环节,进而确定需要改进的重点。
接下来,一汽可以采用5S管理法,即整理、整顿、清洁、清扫、素养的方式,建立整洁有序的生产环境,提高工作效率。
此外,一汽还可以借鉴精益生产的“JIT”(Just-in-Time)原则,通过准确分析市场需求和减少库存量,实现在最短的时间内生产所需的零件,以减少浪费和提高交付速度。
精益生产的核心思想是不断地识别和消除各种形式的浪费,如过度生产、等待时间、运输浪费等。
在一汽的实践中,可以通过精确的生产计划和调度,合理分配资源,减少生产过程中的等待和拖延。
通过开展员工培训和参与改进活动,鼓励员工提出改善意见,并逐步建立和完善精益生产体系。
二、准时生产准时生产是指在规定的时间内按照需求准确地完成生产任务。
准时生产更加关注生产计划的准确性以及交货期限的严格执行,要求企业能够高效地组织生产活动,确保产品能够按时送到客户手中。
一汽在实施准时生产时,需要建立一个完善的生产计划系统。
这个系统可以通过综合考虑市场需求、生产能力、原材料供应等因素,制定出合理的生产任务计划,并及时对计划进行调整。
同时,一汽还需要加强与供应商之间的沟通与协调,确保原材料的及时供应,避免因缺料而影响生产进度。
在生产过程中,一汽可以采用生产线平衡的方法,将不同工序之间的生产时间进行合理安排,避免出现工序之间的瓶颈和延误。
精益生产与准时化生产
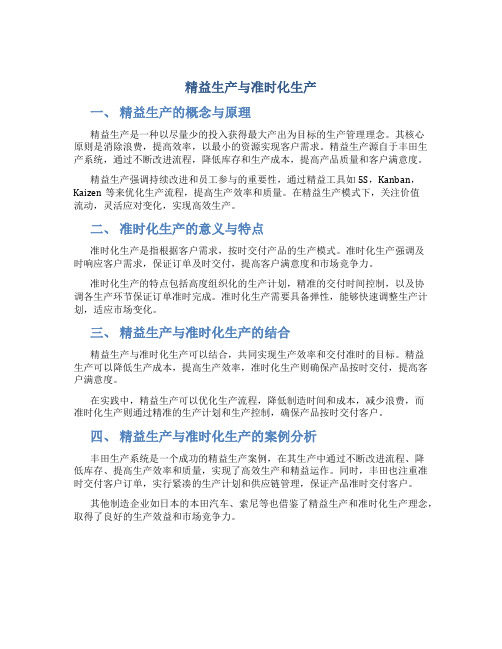
精益生产与准时化生产一、精益生产的概念与原理精益生产是一种以尽量少的投入获得最大产出为目标的生产管理理念。
其核心原则是消除浪费,提高效率,以最小的资源实现客户需求。
精益生产源自于丰田生产系统,通过不断改进流程,降低库存和生产成本,提高产品质量和客户满意度。
精益生产强调持续改进和员工参与的重要性,通过精益工具如5S,Kanban,Kaizen等来优化生产流程,提高生产效率和质量。
在精益生产模式下,关注价值流动,灵活应对变化,实现高效生产。
二、准时化生产的意义与特点准时化生产是指根据客户需求,按时交付产品的生产模式。
准时化生产强调及时响应客户需求,保证订单及时交付,提高客户满意度和市场竞争力。
准时化生产的特点包括高度组织化的生产计划,精准的交付时间控制,以及协调各生产环节保证订单准时完成。
准时化生产需要具备弹性,能够快速调整生产计划,适应市场变化。
三、精益生产与准时化生产的结合精益生产与准时化生产可以结合,共同实现生产效率和交付准时的目标。
精益生产可以降低生产成本,提高生产效率,准时化生产则确保产品按时交付,提高客户满意度。
在实践中,精益生产可以优化生产流程,降低制造时间和成本,减少浪费,而准时化生产则通过精准的生产计划和生产控制,确保产品按时交付客户。
四、精益生产与准时化生产的案例分析丰田生产系统是一个成功的精益生产案例,在其生产中通过不断改进流程、降低库存、提高生产效率和质量,实现了高效生产和精益运作。
同时,丰田也注重准时交付客户订单,实行紧凑的生产计划和供应链管理,保证产品准时交付客户。
其他制造企业如日本的本田汽车、索尼等也借鉴了精益生产和准时化生产理念,取得了良好的生产效益和市场竞争力。
五、总结精益生产和准时化生产是两种不同的生产管理理念,但可以结合互补,共同实现高效生产和及时交付的目标。
精益生产通过消除浪费、优化流程提高生产效率,准时化生产则关注及时交付客户需求,提高客户满意度。
在现代制造业竞争日益激烈的环境中,精益生产与准时化生产的结合将是企业提高竞争力、降低成本、提高效率的重要途径。
企业四大管制系统简介

企业四大管制系统简介管理水平最高的标志企业,是其对四大管制系统(生管、工官、品管、经管)的诠释便是其管理水平的集中体现。
一、生管。
生管系统又称生产管理系统,主要是对生产部门所做的管理,以满足客户的产品需求。
生管系统主要负责的是料号、数量、时间、地点、单价的管理与协调。
此处的生管非生产计划而是指工厂与生产相关的所有管理活动。
所以,传统意义上的生管(PC)、物管(MC)仅仅是其很小之一部分。
“同步制造”的生管系统具有如下特征:1.快速爬坡量产的生管系统。
对于更新换代极快的行业而言,速度就是效益,就是生命。
企业一般通过加强领导权威(如军事化训练),高工资高福利吸引优秀员工并使其24小时处于待命状态,组建矩阵式组织架构和接力式的交接班作业制度,从而达到最短时间的大量生产。
2.成本优势。
企业通过集团采购,及专人评估分析市场、成本与价格机制,从而达到超越业界的成本优势。
3.弹性。
企业的生产弹性包含订单取消和订单的快速量产两个方面。
这是企业界最好的弹性系统,这与推行JIT(精益生产或及时生产)和零部件、原材料的标准化有关。
二、工管。
工管系统又被称为工程管理系统,是针对整个工程人员进行管制的一整套管理系统。
讲求快、稳、准。
企业建立的工管,含主要做样品资料与BOM建立的产发和主要做量试工作的制工两部分。
如果将工程资料、模具资料计算在内,应拥有最大的企业工程数据库。
企业可以通过集成、分解、存储、24小时全球接力式运作,将工程服务缩短在最小的时间内,并保证了工程服务质量。
此之为与客户研发同步的“并行研发”。
三、品管。
品管系统又称为品质管理系统,主要是保障生产品之品质要求,从而达到客户满意的结果。
品质管理的基本思想是:质量是价值与尊严的起点,也是企业赖以生存的命脉。
企业应承诺,所有市场退回不良品100%报废,不会让一件返修品流回市场。
企业的品管含品检和品保(如稽核)两部分。
对生管和工管的成果进行检验和保证。
企业对品质的工作至少有如下几个方面:ROHS要求;超越客户对品质之要求及作出他们的期望;全员品质意思;调整工厂布局以保证品质;使用包材保护产品;产品生产、存储的追溯机制。
精益生产方案
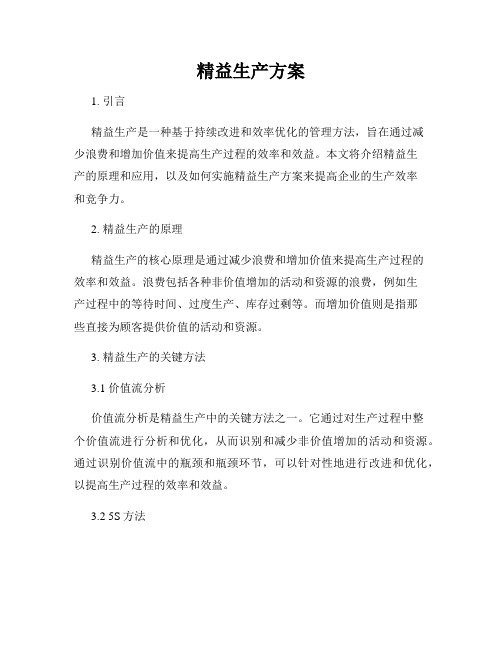
精益生产方案1. 引言精益生产是一种基于持续改进和效率优化的管理方法,旨在通过减少浪费和增加价值来提高生产过程的效率和效益。
本文将介绍精益生产的原理和应用,以及如何实施精益生产方案来提高企业的生产效率和竞争力。
2. 精益生产的原理精益生产的核心原理是通过减少浪费和增加价值来提高生产过程的效率和效益。
浪费包括各种非价值增加的活动和资源的浪费,例如生产过程中的等待时间、过度生产、库存过剩等。
而增加价值则是指那些直接为顾客提供价值的活动和资源。
3. 精益生产的关键方法3.1 价值流分析价值流分析是精益生产中的关键方法之一。
它通过对生产过程中整个价值流进行分析和优化,从而识别和减少非价值增加的活动和资源。
通过识别价值流中的瓶颈和瓶颈环节,可以针对性地进行改进和优化,以提高生产过程的效率和效益。
3.2 5S方法5S方法是精益生产中的另一个重要方法。
它是指整理、整顿、清扫、清洁和素养的五个步骤。
通过实施5S方法,可以改善工作环境和工作条件,提高工作效率和生产效益。
3.3 连续改进精益生产强调持续改进的重要性。
通过不断地进行小步改进,寻找和消除生产过程中的各种隐性问题和瓶颈,可以逐步提高生产效率和产品质量。
4. 精益生产的应用实例4.1 丰田生产系统丰田生产系统是一个典型的精益生产实施案例。
丰田通过有效的流程设计、小批量生产和及时生产等方法,成功地实现了生产过程的高效和灵活性。
4.2 福特汽车公司福特汽车公司也是一个成功实施精益生产的案例。
福特通过实施精益生产,成功地提高了生产效率和质量,缩短了交货周期,降低了库存和成本。
5. 实施精益生产方案的步骤5.1 设定目标首先,需要明确公司的生产目标和需求,确定需要改进和优化的方向和范围。
5.2 分析价值流通过价值流分析,识别出生产过程中的浪费和非价值增加的环节,找出瓶颈和瓶颈环节。
5.3 设计改进方案根据价值流分析的结果,设计相应的改进方案,包括优化流程、减少浪费和提高效率等。
- 1、下载文档前请自行甄别文档内容的完整性,平台不提供额外的编辑、内容补充、找答案等附加服务。
- 2、"仅部分预览"的文档,不可在线预览部分如存在完整性等问题,可反馈申请退款(可完整预览的文档不适用该条件!)。
- 3、如文档侵犯您的权益,请联系客服反馈,我们会尽快为您处理(人工客服工作时间:9:00-18:30)。
精實生產與及時生產系統1 .豐田模式概觀1.1沿革1.2TPS, 精實生產與及時生產系統(JIT)2. 精實生產2.1利益2.2原則2.3組織與程序2.4精實之屋2.5七大浪費2.6績效指標2.75S與目視管理2.8標準化2.9價值溪流2.10全面預防保養(TPM)2.11多能工2.12自?化與防呆2.13快速轉款2.14節拍時間與同步生產2.15 看板系統2.16 製程設計2.17 TQM與6σLean Production 精實生產系統課程簡介:製造業近四年來面臨極為嚴酷的經營挑戰,尤其接單生產型態,已經形成多批小量、短交期(插單頻繁)、產品規格訂單多變的經營環境,使製造廠更不能不強化生產管理與生產技術的體系,否則難以獲利甚至存續。
從豐田汽車公司演化出來的「剛好及時」JIT生產方式,30年來一直是全球製造工廠非常希望仿效運用的一流生產機制,因為它可以大幅減少庫存,提昇製造週轉率,又能夠使生產現場生產力為最高,浪費損失工時為最少,為企業建立核心競爭力。
這種方式再經過演化,形成更有效的產銷管理模式,稱為Lean Production(精實生產),意即完全有效,沒有浪費,生產力為最高。
這種「精實生產」,需要建置靈活的生管機制,也需要先建立堅強的生產技術體質,並非僅有理念而已。
課程大綱:一、精益生產的背景與理念-- 製造業的七大浪費與對產銷經營的影響-- 深入分析庫存原因-- 深入分析生產績效浪費原因-- 精實生產的目標指向二、實現精實生產的機制-帄準化生產-- 剛好及時JIT的實現技巧--- 帄準化生產-- 運用帄準化體制快速及時響應市場-- 混流式生產線(柔性生產)的運用方法三、剛好及時JIT的實現技巧--- 一個流生產-- 一個流生產體制的運用技巧-- 一個流生產必備條件分析四、剛好及時的實現技巧--- 看板管理-- 看板拉動式作業的理念與作業機制-- 製程看板的形式及運用方法-- 外協看板的形式及運用方法-- 看板方式的三項必備條件與體質需求五、實現完全稼動高績效生產的技巧-- 人字旁自動化的理念-- 真正高績效的生產線設計導向-- 運用「行燈式管理」抑減製程停滯的機制六、運用絕對的IE建立可實現精益生產的體質--「絕對的IE」是精益生產的必要基礎-- 運用單分準備技巧快速換模-- 運用防呆式工作設計達成完全有效稼動-- 建立使機台作業站完全稼動的體質-- 多能工的培育訓練七、運用絕對的IE建立可實現精益生產的體質精實系統目標精實系統的願景:以價值流圖(Value Stream Mapping,VSM)分析為基礎;以建立卓越生產為過程;以追求永續經營與創造顧客價值為願景。
管理階層追求卓越生產的決心:訂定持續改善的Roadmap,以展現公司管理階層追求卓越生產的企圖心;經由親身參與提供員工支持與鼓勵,以展現執行的決心。
生產管理模式:考量生產與供應鏈流程特性來導入與研發合適的生產與供應鏈管理模式,以有步驟的方式,按部就班的執行。
建立學習型組織:配合精實策略的執行,提供員工所需之專業知識與技能,以建立學習型的企業文化全球Lean 6-σ第一品牌六標準差是100萬個可能出錯的機會只容許3.4個錯誤,這是業界品質的極致表現。
精實生產是零浪費,也鏟除無效率處,為效率的極致表現。
在此競爭激烈的微利時代,品質僅為企業在市場佔一席之地的入場券。
六標準差的品質已為許多企業推行內容,企業要在激烈競爭中卓越,必需要再加上精實營運,才能獲得高利潤。
精實六標準差,整合精實營運與六標準差品質,為當今產業在全球經濟危機中生存與發展最有效的利器,也是個人職涯成長超越同儕的加值關鍵。
眾所週知(Motorola)公司是Six Sigma的發源地於1988年獲第一屆美國國家品質獎-奠定了摩扥羅拉成為六標準差的同義詞;2002年又再度獲獎受肯定成為精實六標準差實踐的權威.其成功之所以舉世推崇在於掌握三個重要因素:1.原則簡單容易被執行; 2.操作符合科學統計原理可以遵行; 3.有實證性被檢驗,在許多大企業推行均確實成功! Motorola Lean Six Sigma為通行國際最有份量的證照。
Motorola提供一套理論與實作兼具,宏觀與細節並容的Motorola Lean Six Sigma課程與指導,協助組織裡每個專案達成最佳品質,同時還能獲得最好的利潤。
課程目的摩托羅拉大學在精實六標準差培訓中把課堂教學與模擬練習相結合, 使得學員能夠得到系統地提昇。
借助DMAIC 模式,學員可以學到如何應用精實原則及工具,通過與六標準差相結合的方法以更快的速度和更短的週期來達到快速顯著的工作改善。
目標學員經理、專案負責人、高級工程師、綠帶候選人以及那些希望理解精實六標準差(Lean Six Sigma) 的原理和技巧的人們都是這個專案的目標學員。
在參加該課程之前,學員並不需要具備六標準差方法和精實生產的學習和應用經驗。
Motorola Lean Six SigmaR Green Belt Training andCertification Program Content課程介紹0.0 精實六標準差基礎模擬練習--基線1.1 識別業務改進機會1.2 界定顧客需求1.3 製定項目團隊憲章1.4 繪製並了解當前過程1.5 進行價值分析並找出快速取勝機會模擬練習--Quick Win2.0 衡量績效概述2.1 確認量測的內容2.2 針對量測的內容進行管理2.3 了解精實六標準差指標Minitab基礎知識2.4 評估測量系統2.5 確定基線業績2.5 確定基線業績3.1 確定過程約束和瓶頸3.2 找出潛在根因並進行變異源研究3.3 進行失效模式分析3.4 使用比較方法驗証根因3.5 進行相關及回歸分析4.1 運用精實六標準差的最佳實踐4.2 解決方案的評估和選擇4.3 建立未來流程4.4 試營運選擇的解決方案模擬練習--改善5.1 建立過程控制系統5.2 實施統計過程控制5.3 制度化改進過程生產系統設計生產系統設計績效指標製程流模式分析(Process flow patterns)製程流與佈置常見製程流Straight-throughL-ShapeU-ShapeComb or spline常見佈置Fixed PositionProcess-oriented layoutProduct-oriented layoutCellular layout生產線配置設計(Line configuration design)生產線帄衡(Production line balance)工作站帄衡(Station balance)非迴流生產線帄衡(Non-recurrent line balance) 迴流生產線帄衡(Re-current processes balance) 工作站工作分配(Work assignment balance)系統化工廠布置(Systematic Layout Planning)製造單元設計(Work Cell design)製造單元定義(Definition of manufacturing cells)製造單元種類(Types of Manufacturing Cells)製造單元規劃的六個步驟(Six-Step Planning Process for Simple Cells)供應鏈管理1.供應鏈管理基本概念(Fundamental concepts in supply chain management)2.供應鏈現象,肇因與因應之道(Common phenomena in supply chains, the sources of these problems and the possible solutions)3.簡介預測技術(An introduction of forecasting techniques)4.供應鏈中的存貨管理(Inventory management in supply chains)5.供應鏈整合與策略聯盟(Integration of supply chains and strategic alliance)6.採購與委外策略(Purchasing and outsourcing strategies)物料管理與存貨控管(需求規劃)課程大綱 1. 產品結構用料表BOM (Bill Of Material)1.1. 從E-BOM 到M-BOM1.2. BOM種類(階層式BOM、配方式BOM、Phantom BOM…)1.3. BOM之維護、查詢1.4. 替代料(Substitute) 之建立1.5. 材料製程損耗率在BOM之維護1.6. ECO之處理1.7. MRP 如何展BOM2. 物料管理2.1 庫存管理(Inventory Management)(1). 存貨控管的意義及目的(2). 材料ABC分析作業(3). 盤點作業(Cycle count、公司盤點、海關盤點)永續盤存制─ Cycle count定期盤存制─公司盤點、海關盤點(4). 庫存管理系統作業─進料收貨檢驗及入庫作業、製令生產領料及入庫作業、領退料調撥作業、成品及在製品入庫作業(5). 經濟訂購量EOQ (Economic Order Quantity)(6). 安全存量(Safety Stock)與服務水準(7). 物管如何設定及控管安全存量避免缺料(8). 物管如何控管專用料(Unique part) 在產品結束時(End of life)2.2 物料需求規劃(MRP)(1). 可依最後MPS、模擬MPS或製造通知單來執行物料需求之展開(2). MRP 系統作業流程。