铸铁件生产过程铁水特性若干问题的探讨(1)
铸造铸件常见缺陷原因与解决方法分析

铸造铸件常见缺陷原因与解决方法分析前言铸造工艺过程复杂,影响铸件质量的因素很多,往往由于原材料控制不严,工艺方案不合理,生产操作不当,管理制度不完善等原因,会使铸件产生各种铸造缺陷。
常见的铸件缺陷名称、特征和产生的原因,详见下表。
★ 常见铸件缺陷及产生原因★缺陷名称特征产生的主要原因气孔在铸件内部或表面有大小不等的光滑孔洞①炉料不干或含氧化物、杂质多;②浇注工具或炉前添加剂未烘干;③型砂含水过多或起模和修型时刷水过多;④型芯烘干不充分或型芯通气孔被堵塞;⑤春砂过紧,型砂透气性差;⑥浇注温度过低或浇注速度太快等缩孔与缩松缩孔多分布在铸件厚断面处,形状不规则,孔内粗糙①铸件结构设计不合理,如壁厚相差过大,厚壁处未放冒口或冷铁;②浇注系统和冒口的位置不对;③浇注温度太高;④合金化学成分不合格,收缩率过大,冒口太小或太少砂眼在铸件内部或表面有型砂充塞的孔眼①型砂强度太低或砂型和型芯的紧实度不够,故型砂被金属液冲入型腔;②合箱时砂型局部损坏;③浇注系统不合理,内浇口方向不对,金属液冲坏了砂型;④合箱时型腔或浇口内散砂未清理干净粘砂铸件表面粗糙,粘有一层砂粒①原砂耐火度低或颗粒度太大;②型砂含泥量过高,耐火度下降;③浇注温度太高;④湿型铸造时型砂中煤粉含量太少;⑤干型铸造时铸型未刷涂斜或涂料太薄夹砂铸件表面产生的金属片状突起物,在金属片状突起物与铸件之间夹有一层型砂①型砂热湿拉强度低,型腔表面受热烘烤而膨胀开裂;②砂型局部紧实度过高,水分过多,水分烘干后型腔表面开裂;③浇注位置选择不当,型腔表面长时间受高温铁水烘烤而膨胀开裂;④浇注温度过高,浇注速度太慢铸件沿分型面有相对位置错移①模样的上半模和下半模未对准;②合箱时,上下砂箱错位;③上下砂箱错型未夹紧或上箱未加足够压铁,浇注时产生错箱冷隔铸件上有未完全融合的缝隙或洼坑,其交接处是圆滑的①浇注温度太低,合金流动性差;②浇注速度太慢或浇注中有断流;③浇注系统位置开设不当或内浇道横截面积太小;④铸件壁太薄;⑤直浇道(含浇口杯)高度不够;⑥浇注时金属量不够,型腔未充满浇不足铸件未被浇满裂纹铸件开裂,开裂处金属表面有氧化膜①铸件结构设计不合理,壁厚相差太大,冷却不均匀;②砂型和型芯的退让性差,或春砂过紧;③落砂过早;④浇口位置不当,致使铸件各部分收缩不均匀★ 常见铸件缺陷及预防措施★序缺陷名称缺陷特征预防措施1 气孔在铸件内部、表面或近于表面处,有大小不等的光滑孔眼,形状有圆的、长的及不规则的,有单个的,也有聚集成片的。
高强度灰铸铁件典型质量问题探讨

高强度灰铸铁件典型质量问题探讨摘要:铸造生产的困扰是因任何铸件的具体质量问题与缺陷表征及其原因是多种多样又彼此关联甚至相互对立。
当生产高强度(HT300和HT350级)灰铸铁件时更为突出,较难处理的两对主要矛盾是:提高金属强度将引起石墨形态恶化;而材质性能的升高将加大铸件产生缩松的倾向并降低铁水流动性。
本文拟就此进行分析并相应地探讨一些调解措施,冀期能有助于拟订调试工艺方案和分析问题时参考。
关键词:冶金因素凝固与结晶形核能力过冷和过冷组织缩松1.问题的由来考察机械制造的动态可知,机械——尤其是行走机械,其研发重点内容之一是提高金属强度以减轻自重和提高使用寿命。
灰铸铁件生产较易、价格低廉且耐磨、抗压性好,故迄今仍占各类铸件重量的首位(约占50~55%)。
至于在汽车制造业,灰铸铁也是重量居第一位的铸造合金。
灰铸铁之所以仍具有竞争力,在于克服其固有的最大弱点——强度相对较低导致工件较重这方面不断地取得进展的缘故。
例如,有的高强度灰铸铁轿车缸体自重己降至40公斤以下,最薄断面壁厚不及3毫米。
如果孤立地仅就金属强度而言,要提高灰铸铁强度并非难事,因为只要降低灰铸铁的碳硅量,即可减少所形成的片状石墨(相对于金属而言,石墨的硬度和强度可以视为零),同时加入合金元素强化基体,就能达到这一目的。
但是,碳量(碳当量)的降低将加剧两大质量问题,一是石墨形态的恶化,二是铸件易于产生缩松缺陷。
可见,为生产高强度灰铸铁件需要解决好这些突出矛盾,而这将涉及一系列理论和实践方面的问题。
2.影响灰铁性能的因素早年的一致认识是:灰铁材质性能取决于它的化学成份及冷却速率。
对于给定形状、重量和壁厚的铸件,如果铸型介质和浇注温度不变,冷却速率也是不变的,因而影响到金属性能的将主要是化学成份,对于灰铸铁来说,基本成份中的锰、磷、硫三元素对性能的影响较小且可供调控和实际变化的范围又很窄,显然,决定灰铁材质性能的最重要因素是碳和硅的含量(合金元素影响作为另类问题对待),如果找出该两元素含量(还可以将两元素合二为一地用碳当量代表)与表征灰铁材质性能的强度和硬度之间的数学关系,这不仅给试验研究带来便捷同时也将对生产者具有实用价值。
球墨铸铁件常见缺陷的分析与对策(1)
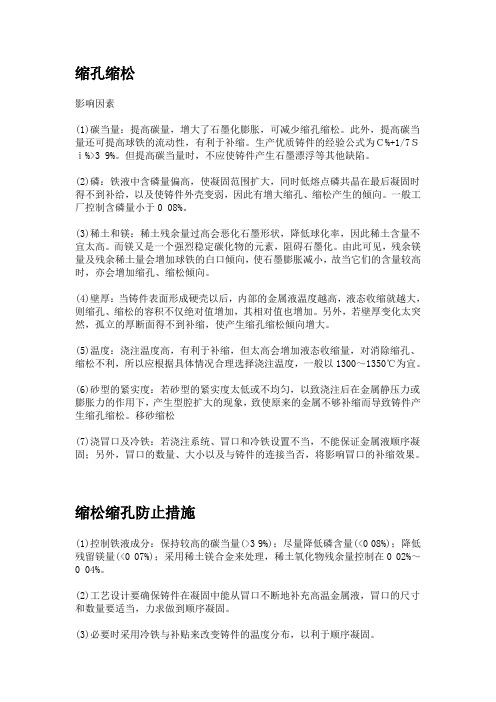
缩孔缩松影响因素(1)碳当量:提高碳量,增大了石墨化膨胀,可减少缩孔缩松。
此外,提高碳当量还可提高球铁的流动性,有利于补缩。
生产优质铸件的经验公式为C%+1/7Si%>3 9%。
但提高碳当量时,不应使铸件产生石墨漂浮等其他缺陷。
(2)磷:铁液中含磷量偏高,使凝固范围扩大,同时低熔点磷共晶在最后凝固时得不到补给,以及使铸件外壳变弱,因此有增大缩孔、缩松产生的倾向。
一般工厂控制含磷量小于0 08%。
(3)稀土和镁:稀土残余量过高会恶化石墨形状,降低球化率,因此稀土含量不宜太高。
而镁又是一个强烈稳定碳化物的元素,阻碍石墨化。
由此可见,残余镁量及残余稀土量会增加球铁的白口倾向,使石墨膨胀减小,故当它们的含量较高时,亦会增加缩孔、缩松倾向。
(4)壁厚:当铸件表面形成硬壳以后,内部的金属液温度越高,液态收缩就越大,则缩孔、缩松的容积不仅绝对值增加,其相对值也增加。
另外,若壁厚变化太突然,孤立的厚断面得不到补缩,使产生缩孔缩松倾向增大。
(5)温度:浇注温度高,有利于补缩,但太高会增加液态收缩量,对消除缩孔、缩松不利,所以应根据具体情况合理选择浇注温度,一般以1300~1350℃为宜。
(6)砂型的紧实度:若砂型的紧实度太低或不均匀,以致浇注后在金属静压力或膨胀力的作用下,产生型腔扩大的现象,致使原来的金属不够补缩而导致铸件产生缩孔缩松。
移砂缩松(7)浇冒口及冷铁:若浇注系统、冒口和冷铁设置不当,不能保证金属液顺序凝固;另外,冒口的数量、大小以及与铸件的连接当否,将影响冒口的补缩效果。
缩松缩孔防止措施(1)控制铁液成分:保持较高的碳当量(>3 9%);尽量降低磷含量(<0 08%);降低残留镁量(<0 07%);采用稀土镁合金来处理,稀土氧化物残余量控制在0 02%~0 04%。
(2)工艺设计要确保铸件在凝固中能从冒口不断地补充高温金属液,冒口的尺寸和数量要适当,力求做到顺序凝固。
(3)必要时采用冷铁与补贴来改变铸件的温度分布,以利于顺序凝固。
铸铁件性能差异原因及如何提升铸件质量,熔炼工艺和化学成分是关键

铸铁件性能差异原因及如何提升铸件质量,熔炼工艺和化学成分是关键展开全文1、前言铁液的化学成分相同,熔炼工艺不同,获得铸铁的性能差异很大。
铸造工厂采取铁液过热、孕育处理、改变炉料配比、添加微量或合金元素等方法,提高铸铁的冶金质量和铸造性能,同时使力学性能和加工性能得到较大提高。
感应电炉熔炼铁液,可以有效地控制铁液温度,精确的调整化学成分,元素烧损少,硫、磷含量低,对于生产球墨铸铁、蠕墨铸铁和高强度灰铸铁非常有利。
但是感应电炉熔炼铁液的形核率减少,白口倾向大,易于产生过冷石墨,虽然强度和硬度有所增加,但铸铁的冶金质量并不高。
上世纪八十年代,出国考察学习的我国工程师,看到国外铸造厂电炉熔炼时加入黑色碎玻璃状物体,经过询问得知这是碳化硅。
国内的日资铸造企业也长期大量使用碳化硅作添加剂。
冲天炉或电炉熔炼铁液,加入预处理剂SiC的优点很多。
碳化硅有磨料级和冶金级之分,前者纯度高价格贵,后者价格低廉。
加入熔炉内的碳化硅转化成铸铁的碳和硅,一是提高碳当量;二是加强了铁液的还原性,[2]大大减轻锈蚀炉料的不利作用。
加入碳化硅可以防止碳化物析出,增加铁素体量,使铸铁组织致密,显著提高加工性能并使切削面光洁。
增加球墨铸铁单位面积石墨球数,提高球化率。
对于减少非金属夹杂物和熔渣,消除缩松,消除皮下气孔也有良好的作用。
2、预处理的作用2.1 形核的原理在Fe-C共晶系中,灰铸铁在共晶凝固阶段由于石墨的熔点高,是共晶体的领先相,奥氏体借助石墨析出。
以每个石墨核心为中心所形成的石墨+奥氏体两相共生共长的晶粒称共晶团。
存在于铸铁熔液中的亚微观石墨聚集体、未熔的石墨微粒、某些高熔点硫化物、氧化物、碳化物、氮化物颗粒等,都可能成为石墨的非均质晶核。
球墨铸铁的形核与灰铸铁形核没有本质区别,只是核心物质中增加有镁的氧化物和硫化物。
铁液中石墨的析出必须经历形核和生长两个过程。
石墨的形核有均质形核和非均质形核两种方式。
均质形核亦称自生晶核。
铸件十大不良现象及原因

铸件十大不良现象及原因一、冷隔:1.现象:铸件主体不完整的位置多呈现冷硬的圆弧面,外观较为光洁。
2.成因: 1)铁水浇注温度太低或浇注不足(浇不足)2)模型设计中,如水口太小,入水慢。
3)浇注之铁水压力不足,薄壁处或拐角处铁水不易成形。
4)浇注分层,多次浇注。
冷隔二、砂(渣)眼:1.现象:在铸件表面上出现分布不均匀的小空洞,通常呈现不规整,深浅不一且内部较不光洁,无冷口现象。
2.成因:1)铁水不干净,浇注时夹渣混入。
2)滤渣片下放时铲砂。
3)铸型中残余小砂粒随铁水冲入型腔。
4)合模时,铸型之间或铸型与砂芯之间挤压造成砂粒脱落。
5)型砂性能不良(如:水分低,强度低等)6)方案设计时入水太快易造成冲砂。
砂眼三、掉砂:1.现象:铸件洗砂后,出现少量铸件多肉,面积大小不一(一般比砂眼大),有时多肉之处的砂子在其他部位形成大的孔洞。
2.成因:1)造型压力不够。
2)铸型湿度不良。
3)模型拔模不良。
4)凹槽,内孔处射砂不实。
掉砂四、粘板:1.现象:铸件出现大量之多肉,且同一模具位置较为一致,多在拐角不易拔模处。
2.成因:1)造型时,模板未预热。
2)分型液喷洒不良(或不适量)3)模型拔模不良4)铸砂稳定性不够,一般在较干时易粘板粘板五、押入(挤砂):1.现象:铸件表面上呈现落沉现象,边缘明显。
2.成因:1)合模压力过大,造成铸型破裂,裂成的表面移动。
2)造模之参数选定不良等。
3)浇注后,不良异物重压铸件(铁水尚未凝固时) 4)砂芯位置跑偏或芯头与型腔配合不好。
押入押入1.现象:铸件之分型部位出现不吻合,或上下或左右移动。
2.成因:1)正反板模型位置不统一。
2)DISA跑偏。
3)砂型跑偏(漏铁水时常见)错模七、粘砂:1.现象:铸件表面参差不齐,粗糙。
2.成因:1)铸砂性能不良。
2)离型液喷洒不良。
3)模板温度低于型砂温度。
粘砂错模1.现象:铸件表面呈现数量不等的小孔洞,比砂眼小且深孔洞一般比砂眼较为圆整。
2.成因:1)型砂的透气型不好。
铸造可能遇到的问题和解决方案

铸造可能遇到的问题和解决方案标题,铸造中常见问题及解决方案。
在铸造过程中,常常会遇到一些问题,这些问题可能会影响产品的质量和生产效率。
以下是一些铸造中常见的问题以及可能的解决方案。
1. 气孔和气泡。
气孔和气泡是铸造中常见的质量问题,可能会导致产品强度不足或者外观质量不佳。
这可能是由于熔融金属中的气体未能完全排除所致。
解决方案,采取适当的浇注系统设计,确保熔融金属能够充分充填模具,同时使用合适的除气剂和浇口设计来减少气孔和气泡的产生。
2. 热裂纹。
热裂纹是由于金属在冷却过程中产生的应力超过了其承受能力
而引起的。
这可能会导致产品在使用过程中出现裂纹。
解决方案,通过合理的冷却控制和合适的金属合金选择,可以减少热裂纹的发生。
此外,预热模具和采用合适的退火工艺也可以有效减少热裂纹的产生。
3. 金属收缩。
金属在冷却过程中会收缩,如果不加以控制,可能会导致产品尺寸不准确甚至变形。
解决方案,通过合理的浇注系统设计和冷却控制,可以减少金属收缩对产品质量的影响。
此外,采用合适的模具设计和金属合金选择也可以减少金属收缩带来的问题。
总之,铸造过程中可能会遇到各种质量问题,但通过合理的工艺控制和技术手段,这些问题是可以得到解决的。
只有不断改进工艺和技术,才能确保铸造产品的质量和稳定性。
球墨铸铁件常见缺陷的分析与对策
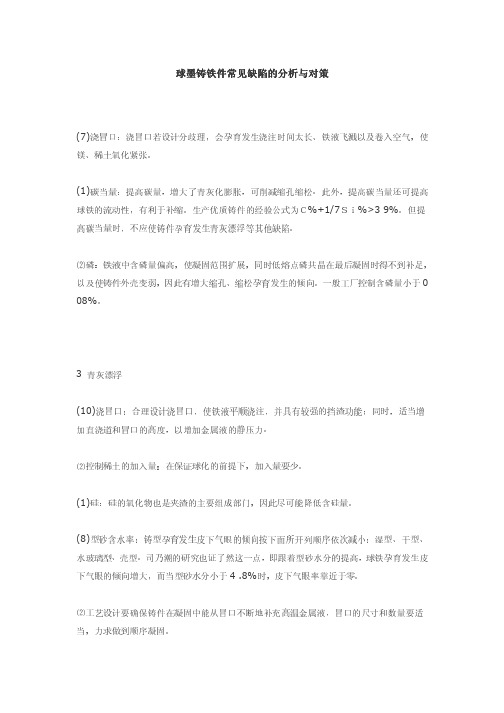
球墨铸铁件常见缺陷的分析与对策(7)浇冒口:浇冒口若设计分歧理,会孕育发生浇注时间太长、铁液飞溅以及卷入空气,使镁、稀土氧化紧张。
(1)碳当量:提高碳量,增大了青灰化膨胀,可削减缩孔缩松。
此外,提高碳当量还可提高球铁的流动性,有利于补缩。
生产优质铸件的经验公式为C%+1/7Si%>3 9%。
但提高碳当量时,不应使铸件孕育发生青灰漂浮等其他缺陷。
⑵磷:铁液中含磷量偏高,使凝固范围扩展,同时低熔点磷共晶在最后凝固时得不到补足,以及使铸件外壳变弱,因此有增大缩孔、缩松孕育发生的倾向。
一般工厂控制含磷量小于0 08%。
3 青灰漂浮(10)浇冒口:合理设计浇冒口,使铁液平顺浇注,并具有较强的挡渣功能;同时,适当增加直浇道和冒口的高度,以增加金属液的静压力。
⑵控制稀土的加入量:在保证球化的前提下,加入量要少。
(1)硅:硅的氧化物也是夹渣的主要组成部门,因此尽可能降低含硅量。
(8)型砂含水率:铸型孕育发生皮下气眼的倾向按下面所开列顺序依次减小:湿型、干型、水玻璃型、壳型。
司乃潮的研究也证了然这一点,即跟着型砂水分的提高,球铁孕育发生皮下气眼的倾向增大,而当型砂水分小于4 .8%时,皮下气眼率靠近于零。
⑵工艺设计要确保铸件在凝固中能从冒口不断地补充高温金属液,冒口的尺寸和数量要适当,力求做到顺序凝固。
(4)注意处理温度。
出炉温度应低于1460℃,以防球化剂紧张烧损;要防止高温下的氧化征象,盖好覆盖球化剂的铁板(厚度应>3mm);铁液扒渣后应用草木灰等盖好;当铁液温度>1350℃出现球化不良及衰退时,可补加球化剂;而当<1350℃时就不能补加球化剂,也不得浇注球铁件,只能补加其它铁液浇注不重要的灰铸铁件或芯骨等。
⑵硅:在碳当量不变的条件下,适当降低含硅量,有助于降低孕育发生青灰漂浮的倾向。
(4)浇注温度:浇注温度过低时,金属液内的金属氧化物等因金属液的粘度过高,不容易上浮至表面而残留在金属液内;温度过高时,金属液表面的熔渣变得太淡薄,不容易自液体表面去除,往往随金属液流入型内。
球墨铸铁件生产中若干问题的探讨

球墨铸铁件生产中若干问题的探讨一、引言球墨铸铁件是一种重要的工程材料,在机械制造、汽车制造等领域得到广泛应用。
然而,在球墨铸铁件生产过程中,存在着一些问题,如热处理质量不稳定、缺陷率高等。
因此,本文将从材料选择、生产工艺、热处理等方面探讨球墨铸铁件生产中若干问题,并提出相应的解决方案。
二、材料选择1.球墨铸铁原材料的选择球墨铸铁原材料主要包括:生铁、钢锭、废钢和回收球团等。
其中,生铁是最常用的原材料之一,但其含碳量和硫、磷等元素含量对球墨铸铁品质有很大影响。
因此,在选用生铁时,需要考虑其化学成分是否符合要求。
2.莫氏硬度试验莫氏硬度试验是检测球墨铸铁硬度的一种方法。
在进行试验时,需要注意控制试验环境的温度和湿度,并按照标准操作流程进行测试。
三、生产工艺1.砂型制作砂型制作是球墨铸铁生产中的重要工艺环节。
在制作砂型时,需要注意砂型的密实度和表面光滑度,以保证铸件质量。
2.浇注工艺浇注工艺是球墨铸铁生产中最关键的环节之一。
在进行浇注时,需要控制浇注速度、温度和压力等参数,并采用适当的浇注系统设计,以保证铸件质量。
3.冷却控制冷却控制是球墨铸铁生产中另一个重要的环节。
在进行冷却时,需要控制冷却速率和温度梯度等参数,并采用适当的冷却方式,以避免出现缺陷。
四、热处理1.淬火处理淬火处理是球墨铸铁生产中常用的一种热处理方法。
在进行淬火处理时,需要控制加热温度和保温时间等参数,并采用适当的淬火介质,以保证淬火效果。
2.回火处理回火处理是球墨铸铁生产中另一种常用的热处理方法。
在进行回火处理时,需要控制加热温度和保温时间等参数,并采用适当的回火方式,以保证回火效果。
五、结论球墨铸铁件生产中存在着一些问题,如材料选择、生产工艺和热处理等方面。
为了解决这些问题,需要采取相应的措施,如选用合适的原材料、控制浇注速度和温度等参数、采用适当的热处理方法等。
只有这样,才能保证球墨铸铁件的质量和性能。
球墨铸铁件生产中若干问题的探讨
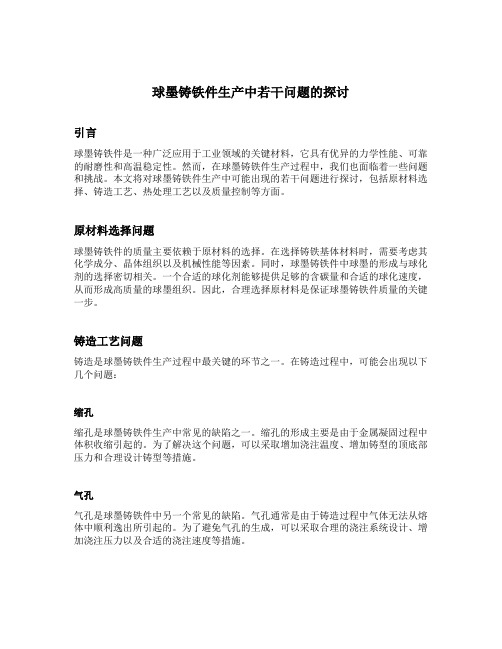
球墨铸铁件生产中若干问题的探讨引言球墨铸铁件是一种广泛应用于工业领域的关键材料,它具有优异的力学性能、可靠的耐磨性和高温稳定性。
然而,在球墨铸铁件生产过程中,我们也面临着一些问题和挑战。
本文将对球墨铸铁件生产中可能出现的若干问题进行探讨,包括原材料选择、铸造工艺、热处理工艺以及质量控制等方面。
原材料选择问题球墨铸铁件的质量主要依赖于原材料的选择。
在选择铸铁基体材料时,需要考虑其化学成分、晶体组织以及机械性能等因素。
同时,球墨铸铁件中球墨的形成与球化剂的选择密切相关。
一个合适的球化剂能够提供足够的含碳量和合适的球化速度,从而形成高质量的球墨组织。
因此,合理选择原材料是保证球墨铸铁件质量的关键一步。
铸造工艺问题铸造是球墨铸铁件生产过程中最关键的环节之一。
在铸造过程中,可能会出现以下几个问题:缩孔缩孔是球墨铸铁件生产中常见的缺陷之一。
缩孔的形成主要是由于金属凝固过程中体积收缩引起的。
为了解决这个问题,可以采取增加浇注温度、增加铸型的顶底部压力和合理设计铸型等措施。
气孔气孔是球墨铸铁件中另一个常见的缺陷。
气孔通常是由于铸造过程中气体无法从熔体中顺利逸出所引起的。
为了避免气孔的生成,可以采取合理的浇注系统设计、增加浇注压力以及合适的浇注速度等措施。
夹杂物是球墨铸铁件中可能出现的另一个问题。
它主要指的是非金属夹杂物,如氧化物、硫化物等。
夹杂物的生成往往与熔体中的气体和杂质有关。
为了减少夹杂物的产生,需要采取适当的熔炼和净化措施,以提高熔体的纯净度。
热处理工艺问题热处理是球墨铸铁件生产过程中不可或缺的一部分,它能够改善球墨铸铁件的力学性能和组织结构。
然而,在热处理过程中也可能出现以下一些问题:马氏体组织不均匀球墨铸铁在热处理过程中需要通过控制冷却速度形成良好的马氏体组织。
然而,由于铸铁件的不均匀性,很容易引起马氏体组织的不均匀分布。
为了解决这个问题,可以通过合理的工艺控制和提高冷却速度的方法来改善马氏体组织的均匀性。
高强度灰铸铁生产中不可忽视的技术问题完整
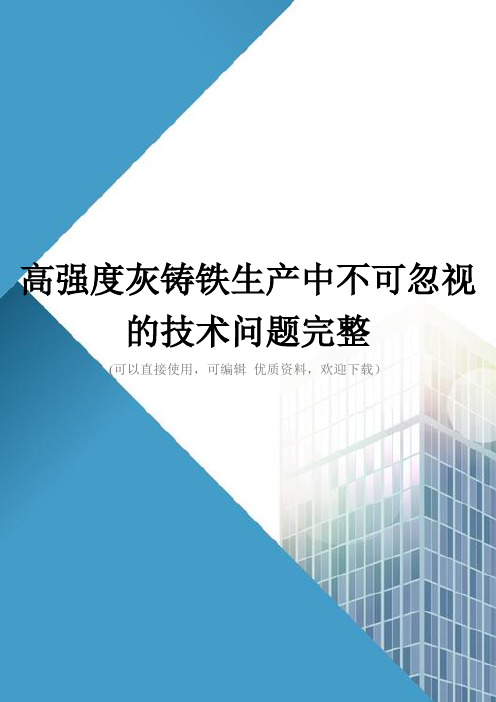
高强度灰铸铁生产中不可忽视的技术问题完整(可以直接使用,可编辑优质资料,欢迎下载)高强度灰铸铁生产中不可忽视的技术问题1、摘要:灰铸铁是“面大量广”的常用金属结构材料。
本文主要论述了合金元素硫、锰含量及其比例,微量元素钛和氮的控制,以及孕育剂加入量对灰铸铁组织和性能的影响。
据统计,2007年我国铸件产量达到了3000万多吨,其中,灰铸铁占60-70%。
由于灰铸铁具有独特的性能特点,它在机械、机床、冶金、汽车等行业的应用中占有非常重要的位置。
改革开放30年来,我国的灰铸铁生产技术水平获得了很大提高。
但与国外先进国家相比,还存在着较大差距。
在高强度灰铸铁生产过程中,我国大多数工厂比较注重五大元素、合金元素、熔炼温度、铸造工艺等因素的控制,这些因素的控制对提高灰铸铁的内在质量和外在质量是至关重要的。
但是,还有一些其他因素没有引起人们足够的重视,这些同样对灰铸铁的质量有着重要影响,譬如,元素硫与锰的含量与比例,微量元素钛、氮的控制以及孕育剂加入量等细节的掌握。
本文就这些因素对灰铸铁组织和性能的影响进行讨论,抛砖引玉,以期引起人们的注意。
1硫、锰的控制(1)硫过去,由于我国的灰铸铁和球墨铸铁大部分利用冲天炉熔炼,铁液的增硫比较严重,导致原铁液的含硫量较高,使得铸铁的铸造性能、力学性能降低,球化效果不好,所以,在人们的记忆中硫是一个有害元素。
随着电炉熔炼工艺的发展,可以容易获得含硫量低的铁液,这对处理球墨铸铁非常有利。
但是,有些工厂在灰铸铁生产中发现,电炉灰铸铁的材质性能还不如冲天炉好。
因此,硫不能被简单的被认为是一个有害元素。
在灰铸铁生产中发现,硫量控制在一定范围内,随着硫量的增加,片状石墨长度变短,石墨形态变得弯曲,而且石墨的头部变得钝化,并细化共晶团,提高强度。
为什么硫在一定范围内,促进石墨化,改善石墨形态?硫在铁水中的溶解度很低,对Fe-C 系平衡相图的影响不是很大。
但硫降低碳在铁水中的溶解度,理应是一个促进石墨化的元素,实际上它对石墨化的影响比较复杂。
铸铁件消失模铸造对铁液的要求分析

铸铁件消失模铸造对铁液的一些要求铁水质量对消失模铸铁件的影响较大,从浇注温度不当对消失模铸铁件缺陷产生的影响,以及不同材质铸铁件对铁水质量的要求,分析了防止出现铸造缺陷的措施和调整方法。
消失模铸造由于泡塑模(白模)气化要消耗铁液热量,要求提高铁液浇注温度,为此必须对铁液熔炼进行适当调整,以便得到与砂型浇注一样或更优的铸件组织。
1 提高浇注温度铁液浇入型腔后,首先要使带有浇注系统的铸件白模(EPS,STMMA)气化、分解、裂解掉,为此浇注温度一般比砂型铸造提高30~50℃,对簿壁球铁件甚至提高至80 ℃。
球铁浇注温度范围为: 1380~1480℃,灰铸铁为1 360~1 420℃,合金铸铁(铬系白口铁)为1 380~1 450℃。
提高浇注温度增加的热量应恰好消耗于烧掉白模,之后铁液温度应降低到砂型铸件的浇注温度,才得保证获得合格铸件,因此在实际生产过程中必须依据本单位工艺,工艺设备等条件找出适合的浇注温度。
1.1 浇注温度过高容易引起的缺陷1.1.1 粘砂过高的铁液温度易引发化学粘砂和机械粘砂。
化学粘砂:砂型中干砂含有细小砂粒、灰尘、尤其是石英砂,极易与铁液起物化矿化反应而产生化学粘砂,极难清理;机械粘砂:过高的铁液温度造成白模涂料层脱落、开裂、软化破裂,铁液通过破裂、隙缝裂纹,加上浇注速度又快,铁液渗入的温度高,粘砂程度也愈严重。
最易发生部位是铸件底部或侧面及热节区,型砂不易紧实地方,特别是转角处,组串铸件浇注系统连接处,容易形成铁液与型砂机械混合的机械粘砂。
1.1.2 反喷气化模EPS(或STMMA)模样浇注时在过高的浇注温度铁液的作用下产生激烈的热解相应反应。
(1)75~164℃:热变形,高弹态软化状,白模开始变软玻璃状并膨胀变形,泡孔内的空气和发泡剂开始逸散,体积收缩,泡孔消失产生粘流状聚苯乙稀液体;(2)164~316℃:熔融,粘流态其分子量不变;(3)316~576℃:解聚,气化状态,在重量开始变化的同时长链状高分子聚合物断裂成短链状低分子聚合物,气化反应开始,产生聚乙稀单体和它的小分子量衍生物组成蒸汽状产物;(4)567~700℃:裂解,气化燃烧,析出气体显著增加,低分子聚合物裂解成少量氢(0.6%),CO2,CO的小分子量的饱和、不饱和的碳氢化合物;(5)700~1 350℃:极度裂解,气化燃烧,低分子聚合物裂解逐步完全,在生产大量小分子碳氢化合物的同时,开始分解出氢和固态的碳;在1 350℃析出氢的含量达32%;在有氧的条件下伴随着燃烧有游离碳和火焰的出现;(6)1 350~1 550℃:急剧裂解,燃烧气化,低分子聚合物迅速裂解,析出氢达到48%;同时燃烧过程更加剧烈,并析出大量的游离碳和由挥发性气体产生的火焰。
铸铁件生产过程铁水特性若干问题的探讨(1)
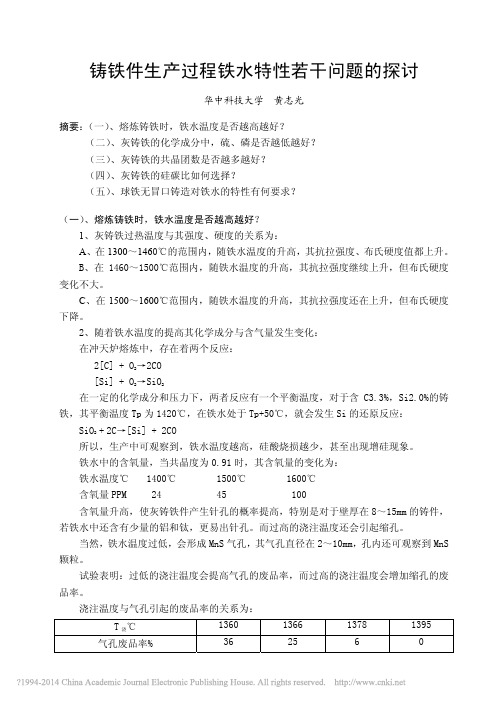
华中科技大学 黄志光
摘要:(一)、熔炼铸铁时,铁水温度是否越高越好? (二)、灰铸铁的化学成分中,硫、磷是否越低越好? (三)、灰铸铁的共晶团数是否越多越好? (四)、灰铸铁的硅碳比如何选择? (五)、球铁无冒口铸造对铁水的特性有何要求?
(一)、熔炼铸铁时,铁水温度是否越高越好?
1、灰铸铁过热温度与其强度、硬度的关系为:
而可使铸件表面光洁。生产实践表明,当磷含量在 0.02-0.04$时,铸件出现粘砂,而将含
磷量增加至 0.09-0.12%时,铸件粘砂就消失,并且铸件清砂时间可以减少 35%。
磷为什么有减少铸件粘砂的作用?铸件粘砂主要产生在热节处,尤其是内腔的热节
处,而不是发生在铁水静压力最大的位置即铸件的下部。粘砂是发生在铸件的凝固过程,
铁水中的含氧量,当共晶度为 0.91 时,其含氧量的变化为:
铁水温度℃ 1400℃
1500℃
1600℃
含氧量 PPM 24
45
100
含氧量升高,使灰铸铁件产生针孔的概率提高,特别是对于壁厚在 8~15mm 的铸件,
若铁水中还含有少量的铝和钛,更易出针孔。而过高的浇注温度还会引起缩孔。
当然,铁水温度过低,会形成 MnS 气孔,其气孔直径在 2~10mm,孔内还可观察到 MnS
在冲天炉熔炼中,存在着两个反应:
2[C] + O2→2CO [Si] + O2→SiO2 在一定的化学成分和压力下,两者反应有一个平衡温度,对于含 C3.3%,Si2.0%的铸
铁,其平衡温度 Tp 为 1420℃,在铁水处于 Tp+50℃,就会发生 Si 的还原反应:
SiO2 + 2C→[Si] + 2CO 所以,生产中可观察到,铁水温度越高,硅酸烧损越少,甚至出现增硅现象。
铸钢件常见质量问题及主要影响因素汇总

2.防止缩孔缩松的措施 (1)合适的冒口位置和尺寸 冒口放在铸件厚大部位,最好是上部; 冒口的尺寸要足够大,使得它凝固时间长,铸件全部凝固了,冒口中心 部分还要处于液态; 冒口有足够的液体钢水补充铸件体积收缩的需要。 (2)冒口的补缩距离 钢水在凝固过程中凝固层出现固液共存,影响钢水的流动,补缩受阻, 因此冒口的补缩距离(范围)受到限制。 (3)冒口颈和冒口补贴 冒口与铸件之间的连接部分称冒口颈(边冒口)和冒口补贴(顶冒口), 目的是让冒口中的钢水始终有通道进入铸件,满足铸件的需要,是就要 求冒口颈和冒口补贴有一定的形状尺寸。
(1)铸件设计和工艺上采取措施改变和减少局部热节;
(2)工艺上采取防裂纹,冷铁; (3)提高钢水质量,减少夹杂物; (4)气割、碳刨、焊补采用预热、后热去应力措施。 -20-
人有了知识,就会具备各种分析能力, 明辨是非的能力。 所以我们要勤恳读书,广泛阅读, 古人说“书中自有黄金屋。 ”通过阅读科技书籍,我们能丰富知识, 培养逻辑思维能力; 通过阅读文学作品,我们能提高文学鉴赏水平, 培养文学情趣; 通过阅读报刊,我们能增长见识,扩大自己的知识面。 有许多书籍还能培养我们的道德情操, 给我们巨大的精神力量, 鼓舞我们前进。
-2-
C.炉内的化学成分变化
已化验合格的钢水长时间放在炉内,成分会变化。 D.出钢时钢水成分的变化,某些元素如:Si,Mn, Cr会烧损
E.钢水包对钢水成分的影响
前一包中残余钢水会污染下一包的钢水成分,特别是产生含碳量低的不 锈钢时很明显,碳容易上升,要求浇注后钢水包一定要用氧气吹干净,
不能结包底,结包壁,也不要留有残渣,钢包一定要烘烤好(800℃以
3.防止方法
外来夹渣:一是减少夹杂物的来源,二是浇注前镇静。包
废钢铸造生产中常见缺陷铸件案例与出现原因分析!

废钢铸造生产中常见缺陷铸件案例与出现原因分析!用废钢+回炉料+生铁+增碳剂来生产铸铁,工艺控制不当的话,总会出现这样那样的问题。
接下来,我们了解一下废钢生产中的常见问题。
首先,我们来看原材料。
原材料使用不当,是造成废钢铸造废品率居高不下的原因之一。
废钢原料,杂而不齐,各种各样的钢、铁、合金都有可能进入废钢堆中。
这就增加而了原材料的不稳定性。
一、下面这种料,质量相对稳定,杂质少,但价格也非常高。
用这种料,成本是铸造厂要考虑的问题。
压块,压块价格便宜,稳定性差。
里面的夹杂物多角钢、管类废钢,杂、乱,尤其是管类,生产中容易喷火,烧伤炉前工作人员。
冷轧板压块,这类压块体积较大,较小的炉子用不了。
价格中等偏上。
废钢铸造生产,有其特有缺陷问题。
这类问题需要技术人员熟记于心,并掌握其规律。
一、使用废钢进行铸造生产,铁水容易发生因自我补缩不足而造成缩孔、冷隔,浇不足,铁水流动性差等问题。
使用废钢熔炼出来的铁水与冲天炉相比,流动性差,这是为什么呢?原因一,钢材生产对硫磷的控制非常严苛。
其含量也非常低。
硫和磷虽然是铸铁有害元素,但是过低的硫、磷会使铁水流动性变差。
原因二,由于废钢收集过程中,会夹杂进来合金,有些合金是铸铁硬化元素,有些合金会使铁水流动性变差。
如果不能掌握各种金属元素对铸铁的化学反应,在生产中就难以避免因金属元素裹入造成的铁水流动差的问题。
铁水流动差,随之而来就造成冷隔、缺肉、白口,铸件过硬等问题。
二、化学成分配比不当造成的加工不动缺陷废钢铸造生产中,铸件硬,加工困难,加工不动是常见的,也是异常让铸造厂头疼的问题。
一旦解决不好这个问题,将会迫使铸造厂放弃废钢铸造技术。
造成铸件加工不动的原因,也是多种多样,归纳起来,不外乎这几大类,一,化学成分配比不正确,二铁水中裹入了硬化相元素。
三,浇注系统设计有缺陷,造成铁水流速低。
怎样解决这种种的问题呢,今天咱们建一个群,大家进来,一起探讨,群的二维码在文章结尾,具体问题,具体讨论。
铸造件问题原因及措施

铸件缺陷铸件表面的砂孔和渣孔通常合称为“砂眼”。
翻砂过程中,气体或杂质在铸件内部或表面形成的小孔,是铸件的一种缺陷。
例:铸件外轮廓精加工后,不得有气孔等铸造缺陷。
砂(渣)眼在铸件表面上出现分布不均匀的小空洞,通常呈现不规整,深浅不一且内部较不光洁,无冷口现象。
它主要是由于铁水不干净,浇注时夹渣混入,滤渣片下放时铲砂。
铸型中残余小砂粒随铁水冲入型腔。
合模时,铸型之间或铸型与砂芯之间挤压造成砂粒脱落。
铸型砂性能不良(如:水分低,强度低等)方案设计时入水太快易造成冲砂。
铸造砂眼产生的原因主要原因:1:型腔内沙粒没清净。
2:浇注前从浇道或冒口等开放处侵入了沙粒。
3:砂型强度不够,受外力作用引起脱落。
4:浇注不连续或浇注速度太慢导致型腔内沙粒不能顺利漂浮到冒口上,而滞留在温度较低的地方。
5:温度太高、浇注速度太快冲刷浇道卷入沙粒。
砂型铸造中为什么会出现多肉或缺肉1、当型腔中某一部位的型砂由于各种原因而脱落时,便会留下一个凹坑,当金属液充满型腔时,凹坑就变成了一块凸出的多肉。
砂眼与多肉是一对相辅相成的缺陷。
当铸型掉砂时,掉砂的地方便形成多肉,掉下的砂则形成砂眼或缺肉。
2、多肉的另一种可能是涨箱;砂眼与掉下的砂没有明确关系铸造黑皮在钢铁铸件外表面形成的一层氧化皮,俗称黑皮。
可以采用喷砂的方法去除,当然也可以用机加工手段去除,不方便的地方可以用酸洗的方法去除。
有这层氧化皮后,由于这层氧化皮可能脱落,外观变得不好看,不易采取油漆电镀等防腐措施,如果浸在液体中使液体出现杂质。
应该讲没有多少正面作用。
1、提高浇铸温度,采用保温冐口,铁水防氧化保护。
适当增加加工余量2、有可能是加工时刀具磨损过度导致刀具和零件产生摩擦产生的。
请检查更换刀具。
3、适当增加加工余量常见的铸造缺陷有哪些?形成的原因及解决办法?一、气孔形成原因:1. 液体金属浇注时被卷入的气体在合金液凝固后以气孔的形式存在于铸件中2. 金属与铸型反应后在铸件表皮下生成的皮下气孔3. 合金液中的夹渣或氧化皮上附着的气体被混入合金液后形成气孔解决方法及修补1. 浇注时防止空气卷入2. 合金液在进入型腔前先经过滤网以去除合金液中的夹渣、氧化皮和气泡3. 更换铸型材料或加涂料层防止合金液与铸型发生反应4. 在允许补焊部位将缺陷清理干净后进行补焊二、疏松形成原因1. 合金液除气不干净形成疏松2. 最后凝固部位不缩不足3. 铸型局部过热、水分过多、排气不良解决方法及修补1. 保持合理的凝固顺序和补缩2. 炉料静洁3. 在疏松部位放置冷铁4. 在允许补焊的部位可将缺陷部位清理干净后补焊三、夹杂形成原因1. 外来物混入液体合金并浇注人铸型2. 精炼效果不良3. 铸型内腔表面的外来物或造型材料剥落解决方法及修补1. 仔细精炼并注意扒查2. 熔炼工具涂料层应附着牢固3. 浇注系统及型腔应清理干净4. 炉料应保持清洁5. 表面夹杂可打磨去除,必要时可进行补焊四、夹渣形成原因1. 精炼变质处理后除渣不干净2. 精炼变质后静置时间不够3. 浇注系统不合理,二次氧化皮卷入合金液中4. 精炼后合金液搅动或被污染解决方法及修补1. 严格执行精炼变质浇注工艺要求2. 浇注时应使金属液平稳地注入铸型3. 炉料应保持清洁,回炉料处理及使用应严格遵守工艺规程五、裂纹形成原因1. 铸件各部分冷却不均匀2. 铸件凝固和冷却过程受到外界阻力而不能自由收缩,内应力超过合金强度而产生裂纹解决方法及修补1.尽可能保持顺序凝固或同时凝固,减少内应力2.细化合金组织3.选择适宜的浇注温度4.增加铸型的退让性六、偏析形成原因合金凝固时析出相与液相所含溶质浓度不同,多数情况液相溶质富集而又来不及扩散而使先后凝固部分的化学成分不均匀解决方法1.熔炼过程中加强搅拌并适当的静置2.适当增加凝固冷却速度七、成分超差形成原因1. 中间合金或预制合金成分不均匀或成分分析误差过大2. 炉料计算或配料称量错误3. 熔炼操作失当,易氧化元素烧损过大4. 熔炼搅拌不均匀、易偏析元素分布不均匀解决方法1. 炉前分析成分不合格时可适当进行调整2. 最终检验不合格时可会同设计使用部门协商处理八、针孔形成原因合金在液体状态下溶解的气体(主要为氢),在合金凝固过程中自合金中析出而形成的均布形成的孔洞解决方法及修补1. 合金液体状态下彻底精炼除气2. 在凝固过程中加大凝固速度防止溶解的气体自合金中析出3. 铸件在压力下凝固,防止合金溶解的气体析出4. 炉料、辅助材料及工具应干燥。
铸铁的几个关键技术问题的探讨
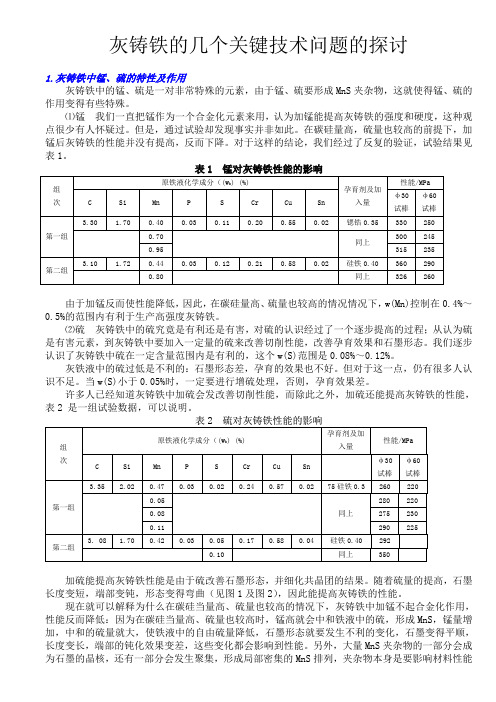
灰铸铁的几个关键技术问题的探讨1.灰铸铁中锰、硫的特性及作用灰铸铁中的锰、硫是一对非常特殊的元素,由于锰、硫要形成MnS夹杂物,这就使得锰、硫的作用变得有些特殊。
⑴锰我们一直把锰作为一个合金化元素来用,认为加锰能提高灰铸铁的强度和硬度,这种观点很少有人怀疑过。
但是,通过试验却发现事实并非如此。
在碳硅量高,硫量也较高的前提下,加锰后灰铸铁的性能并没有提高,反而下降。
对于这样的结论,我们经过了反复的验证,试验结果见表1。
由于加锰反而使性能降低,因此,在碳硅量高、硫量也较高的情况情况下,w(Mn)控制在0.4%~0.5%的范围内有利于生产高强度灰铸铁。
⑵硫灰铸铁中的硫究竟是有利还是有害,对硫的认识经过了一个逐步提高的过程;从认为硫是有害元素,到灰铸铁中要加入一定量的硫来改善切削性能,改善孕育效果和石墨形态。
我们逐步认识了灰铸铁中硫在一定含量范围内是有利的,这个w(S)范围是0.08%~0.12%。
灰铁液中的硫过低是不利的:石墨形态差,孕育的效果也不好。
但对于这一点,仍有很多人认识不足。
当w(S)小于0.05%时,一定要进行增硫处理,否则,孕育效果差。
许多人已经知道灰铸铁中加硫会发改善切削性能,而除此之外,加硫还能提高灰铸铁的性能,表2 是一组试验数据,可以说明。
加硫能提高灰铸铁性能是由于硫改善石墨形态,并细化共晶团的结果。
随着硫量的提高,石墨长度变短,端部变钝,形态变得弯曲(见图1及图2),因此能提高灰铸铁的性能。
现在就可以解释为什么在碳硅当量高、硫量也较高的情况下,灰铸铁中加锰不起合金化作用,性能反而降低:因为在碳硅当量高、硫量也较高时,锰高就会中和铁液中的硫,形成MnS,锰量增加,中和的硫量就大,使铁液中的自由硫量降低,石墨形态就要发生不利的变化,石墨变得平顺,长度变长,端部的钝化效果变差,这些变化都会影响到性能。
另外,大量MnS夹杂物的一部分会成为石墨的晶核,还有一部分会发生聚集,形成局部密集的MnS排列,夹杂物本身是要影响材料性能的这就是加锰反而使灰铸铁性能降低的原因。
- 1、下载文档前请自行甄别文档内容的完整性,平台不提供额外的编辑、内容补充、找答案等附加服务。
- 2、"仅部分预览"的文档,不可在线预览部分如存在完整性等问题,可反馈申请退款(可完整预览的文档不适用该条件!)。
- 3、如文档侵犯您的权益,请联系客服反馈,我们会尽快为您处理(人工客服工作时间:9:00-18:30)。
A、含硫量对灰铸铁共晶团的影响:
由于硫化物可以作为共晶石墨形核的基底,同时又能抑制共晶团的长大,但是,硫又
是促进铸铁形成白口的元素,所以,适当的硫量是有利的。
铸铁的化学成分为:C 3.19% Si 2.1% Mn 0.75% P 0.04%时,硫量的变化为 S 0.016%,0.014%,0.4%时,壁厚变化从 5/8 英寸至 3 英寸时,对铸件的白口宽度和共 晶团个数的关系为:(一英寸=25.4mm)
HT300
3.48
15~30 ﹥30
15~30
HT350
3.30
﹥30~50
﹥50
铁水适宜温度℃ 1430 1420 1450 1440 1430 1460 1450 1470 1460 1480 1470 1460
值得指出:牌号越高,虽然温度要求越高,但是其过热度不但没升高,反而下降。如 对于同时壁厚为 15mm,其牌号与过热度的关系为:
若铁水中还含有少量的铝和钛,更易出针孔。而过高的浇注温度还会引起缩孔。
当然,铁水温度过低,会形成 MnS 气孔,其气孔直径在 2~10mm,孔内还可观察到 MnS
颗粒。
试验表明:过低的浇注温度会提高气孔的废品率,而过高的浇注温度会增加缩孔的废
品率。
浇注温度与气孔引起的废品率的关系为:
T 浇℃ 气孔废品率%
而可使铸件表面光洁。生产实践表明,当磷含量在 0.02-0.04$时,铸件出现粘砂,而将含
磷量增加至 0.09-0.12%时,铸件粘砂就消失,并且铸件清砂时间可以减少 35%。
磷为什么有减少铸件粘砂的作用?铸件粘砂主要产生在热节处,尤其是内腔的热节
处,而不是发生在铁水静压力最大的位置即铸件的下部。粘砂是发生在铸件的凝固过程,
面形成一些六角形的组织如下图,从而恶化了铸件的抗加工性能。
1000×
2000×
铸件表面硬化层的扫描电镜观察
(2)磷用于改善铸件的耐磨性和流动性
对于要求耐磨性较高的铸件如机床导轨、活塞环、缸套等,往往采用含磷的合金铸铁,
如 P-Cu-Ti 铸铁,含 P 量也在 0.35-0.65%;加磷的目的在于利用磷共晶的耐磨性达到减磨
1、灰铸铁过热温度与其强度、硬度的关系为:
A、在 1300~1460℃的范围内,随铁水温度的升高,其抗拉强度、布氏硬度值都上升。
B、在 1460~1500℃范围内,随铁水温度的升高,其抗拉强度继续上升,但布氏硬度
变化不大。
C、在 1500~1600℃范围内,随铁水温度的升高,其抗拉强度还在上升,但布氏硬度
三角试片炉前检测铁水质量应注意事项:
A、三角试片尺寸的选择:根据所留测量的白口密度可以选取下列四种型号:
A
型号
1
2
3
4
Amm 6
12
20
32
B
Bmm 25
32
38
50
长度 126mm
B、三角试片最好用铝合金制造,尖角有 Φ0.8mm 圆角。 C、在一个铸型上浇注几个三角试片时,为了防止三角试片在冷却过程传热的相互干 扰,三角试片铸型的距离至少是三角试片铸型宽度的 2.5 倍以上。 D、三角试片需冷却至墨紫色后取出,然后浸水冷却,先将三角试片平直底部着水冷 却。试片冷却到从水中取水时不沾水为宜。 应避免因操作不当产生的误码判: A、浸水过早,在三角试片红热状态浸水,这样会导致白口宽度增大。而且,有时还 会出现反白口,即试片中心处白口。 B、未经充分水冷的三角试片就过早打断,可能出现试片断口表面氧化,造成白口宽 度测量引起误差。 C、应从三角试片的二分之一长度处打断,注意不要将试片的端部打断,以免无法检 测白口宽度。 D、规范白口宽度的测量位置:一种是以白口区域出现第一个灰点处,另一种是测量 麻口区的二分之一处。每个工厂可按自己的条件决定。
较高,显然是在炉料中加入磷铁和硫化铁。
两者对比如下:
种类 好加工
化学成份
机械性能
C Si Mn P
S
Sb
Sn бbMPa
HB
3.27 2.15 0.43 0.065 0.083 0.002 0.035 250 187~215
不好加工 3.31 2.7 0.66 0.03 0.014 0.004 0.035 250 207~241
牌号 HT 铁水适宜温度℃ 铁水过热度℃
150 1430 262
200 1450 246
250 1460 236
300 1470 235
350 1480 225
所以,在生产中可观察到:尽管高牌号铸件的浇注温度较高,但其铁水的流动能力不 如浇注温度较低的低牌号铸件的流动能力,其原因在于:后者的过热度较前者高。
1MP=145 磅/英寸 2; HR
布氏硬度值(HB) 100+0.44 бb(MPa)
试验表明:无论孕育或非孕育铸铁,当 S≤0.04%时,其布氏硬度随硫量的增加而迅速 提高;当 S>0.04%后,硬度的增加趋缓,含硫量在 0.006%时,基体中有 40%珠光体,而在 含硫 0.04%时,珠光体含量为 100%,无论对于孕育或非孕育灰铸铁,其抗拉强度在 S0.04-0.06%之间达到最大值,而且相对硬度达最低值。
的目的。对于一些薄壁铸件和艺术铸件,为了使铸件轮廓清晰,表面光洁,通常都会加入
适量的磷,如缝纫机铸件含 P 为 0.3%,暖气片含 P 为 0.4-0.5%,一些艺术铸件含 P 量甚至
达 1.5%。
(三)三角试片如何炉前检测铁水质量
三角试片常用于炉前铁水质量的检测。铸铁是一种含有一定量的 Mn、Si、P、S 的铁
20
92
92
132
450
对 于 薄 壁 的 冰 箱 压 缩 抗 铸 件 , 虽 然 其 化 学 成 分 规 定 C3.3-3.7% , Si1.8-2.7% ,
Mn0.3-0.7%,而 P.S≤0.1%;由于是用合成铸铁,其 P.S 可以非常低。但是,观察到一批
铸件比另一批铸件的加工性优越,对两者进行分析表明:加工性能好的铸件,其 S.P 都比
SiO2 + 2C→[Si] + 2CO 所以,生产中可观察到,铁水温度越高,硅酸烧损越少,甚至出现增硅现象。
铁水中的含氧量,当共晶度为 0.91 时,其含氧量的变化为:
铁水温度℃ 1400℃
1500℃
1600℃
含氧量 PPM 24
45
100
含氧量升高,使灰铸铁件产生针孔的概率提高,特别是对于壁厚在 8~15mm 的铸件,
评估孕育效果。
碳硅总量—碳当量—白口宽度的关系:
(C+Si)%总量
5.87
5.06
4.79
4.81
4.59
碳当量 CE%
4.40
4.02
3.82
3.59
3.35
白口宽度 mm
无
~2
4~5
~6
~8
各种牌号灰铸铁,其适宜的白口宽度为:
牌号 HT
100
150
200
250
300
白口宽度 mm
0~2
2.5~4
下降。
2、随着铁水温度的提高其化学成分与含气量发生变化:
在冲天炉熔炼中,存在着两个反应:
2[C] + O2→2CO [Si] + O2→SiO2 在一定的化学成分和压力下,两者反应有一个平衡温度,对于含 C3.3%,Si2.0%的铸
铁,其平衡温度 Tp 为 1420℃,在铁水处于 Tp+50℃,就会发生 Si 的还原反应:
3
5
3500
2260
1700
0.041
2
3
1975
1600
975
0.40
8
14
1700
1421
1025
可见,从减少白口的角度考虑,含硫量在 0.041%时,白口宽度最小,无论孕育与否都
一样,但从共晶团数则处于中间状态。
B、硫对灰铸铁机械性能的影响
对非孕育与孕育灰铸铁抗拉强度和相对硬度的影响为:
布氏硬度值(HB) HR 100+3.03×抗拉强度(磅/英寸 2)
它是由铸铁共晶转变产生石墨化膨胀引起的。
对于铁水中磷含量与铁水渗入深度的测量表明:含磷量越高,铁水渗入砂粒之间的深
度越小。另外,铸件粘砂严惩必导致强化抛丸,进一步造成铸件表面硬化,恶化加工性能。
铸铁含 P 量%
0.068
0.102
0.172
0.191
0.26
渗入深度 mm
12
8
4
1
无
由于粘砂导致强化清丸,造成铸件表面硬化,对此层进行扫描电镜观察,可观察到表
4、铁水温度如何判断:有时,铁水表面呈耀眼的亮白色,给人以“铁水温度很高” 的印象,并且,可观察到其相应的炉渣呈泡沫状。此时,若采用热电偶温度计测量其铁水 温度并不高。
有些工厂据此现象,作为判断炉内元素的烧损和铁水氧化程度的依据:将用接触式(如
热电偶)和非接触式(如光学、红外测温仪)同时测量铁水的温度,用其差值来判断铁水
两者的共晶团与树枝晶的对比如下图:加工性能好的铸件,共晶团比较粗,树枝晶间
距也较宽,而加工性能欠缺的铸件,则树枝晶很细,共晶团也很密。虽然都是用含 Sr 硅铁
孕育,但 S 低于 0.04%时,孕育作用受到限制。
共晶团
树枝晶
加工性能欠缺的铸件的共晶团与树枝晶
共晶团
树枝晶
加工性能良好的铸件的共晶团与树枝晶
3.5~6
4.5~7
6~8
对于铸件而言,根据主要壁厚和要求,选择适当的白口宽度,设 f 为白口宽度与铸件
壁厚之比,则:
要求最好的切削性能
f=15~20%
要求最佳的强度