第三章 机械加工检验规程
机械加工检验规程修订稿

机械加工检验规程 Document number【AA80KGB-AA98YT-AAT8CB-2A6UT-A18GG】机械加工检验规程1?总则检验人员必须具有一定的专业知识和实际工作经验,且能满足现行产品对检验工作的各项要求。
检验人员所用的计量器具必须是经计量部门校验合格并在规定周期内。
检验人员验收产品前应熟读相关图样和技术文件,了解零件的关键尺寸及装配关系要点。
检验人员必须严格按照图样和技术文件所规定的要求对零件进行判定。
检验人员应对车间在制品按规定进行标识。
检验人员必须定期(6个月最长1年)参加专业知识培训,学习和接受先进的检测方法,以提高自身的业务水平。
2目的和范围通过严格执行三检,“首件检验”、“巡回检验”、“完工检验”将检验工件与工序控制紧密结合,对每一工序的质量问题或可能出现的质量问题不放过,剔除不合格品,使其不能投入下序或出厂,从而达到工序控制目的。
3检验依据:过程检验的检测依据按检验工艺卡执行。
4检验类别首件检验:在下述情况下,必须首件检验后,才能开始加工:工作班开始加工的第一个工件;调换操作者后加工的第一个工件;更换(调整)工艺装备或更换模具后加工的第一个工件;更换材料批(炉)号后加工的第一个工件;代用材料后加工的第一个工件。
首件检验的依据:a)工艺图纸或工艺卡片;b)作业指导书(工艺控制点)。
检验内容:根据检验工艺规程的要求,核对首件产品的质量特性值是否真正符合要求;对首件检验合格,批准生产加工,首件检验不合格,进行不合格品的处理,同时分析不合格原因,采取改进措施后生产,产品继续首件检验,直至合格为止。
检验要求:对首件,根据加工工艺要求,核实首件产品或工件(毛坯)产品的质量特性是否符合要求。
对首批检查的工件(毛坯),操作者必须做好自检和标识,在操作者缺乏检测手段时,也应对工件外观质量自检,合格后送检验员检查。
无论在任何情况下,首件检验未经检验合格,不得进行批量生产或继续加工作业。
机械加工检验制度

机械加工检验制度宁波市日丰机械制造有限公司机械加工检验制度一. 首件三检:是防止工序生产产品过程中出现成批超差、返修、报废的预先控制措施,属强制性的工作要求。
检验员对生产现场有监督指导的职责。
1、首件必须实行自检、互检、检验员检,应如实填写实际尺寸,签字盖章。
三检合格后,首件应做标记。
2、生产现场的工艺流程单、生产图纸必须是有效版本。
生产图纸必须加盖生产许可印章。
3、投料单与图纸、工艺流程单相符,上道工序签字盖章后,方可进行下道工序。
4、现场不准使用无标识的白图。
临时工艺必须由主管领导确认签字。
5、不执行三检、违反工艺纪律,检验员有权停止其工作,并追究个人责任。
二、过程检验1、三检合格后,工人应及时自检,检验员应主动进行流动检验,加强抽检,抽检过程中,零件工序检验抽检率应不低于30%。
成品检验率100%。
2、生产过程中出现废品,及时隔离,并在报(料)废单上如实填写废品数量,一式三份,仓库、统计室、品保部各留一份。
三、成品检验1、零、组件应装入零件箱内或有相应的防护措施。
2、检查零(组)件的外观,应清洗干净、无锈蚀、碰伤、划伤、毛刺等缺陷。
3、按照成品检验工艺对零件进行100%检验,将检验结论准确填写在“成品检验记录”上并加盖检验员印章。
4、成品检验员发现不合格时,按不合格品审理程序进行。
四、技术质量部对该文件的执行情况进行考核,考核结果纳入质量奖惩中编制/日期: 批准/日期:大件全检工序检(质量,数量)必须签字确认,当班完成,异常汇报。
异常单及时确认数量开单,责任确认入库。
每天入库的数量,物料报废及时放入报废区(开单) 产品返工返修,需确认出哪个部门,上报各部门主管,及时跟踪处理至入库。
(机械制造行业)第三章机械加工工艺规程的制定

第三章机械加工工艺规程的制定§3-1基本概念一.生产过程与工艺过程(一)生产过程从原材料到机械产品出厂的全部劳动过程。
包括:1)生产技术准备过程2)毛坯的制造3)零件的机械加工及热处理4)产品的装配、检验、试车、油漆、包装等。
5)产品的辅助劳动过程直接生产过程被加工对象的尺寸、形状或性能、位置产生一定的变化。
如:零件的机械加工、热处理、装配等。
间接生产过程:不使加工对象产生直接变化。
如:工装夹具的制造、工件的运输、设备的维护等。
(二)机械加工工艺过程是生产过程的一部分,是对零件采用各种加工方法,直接用于改变毛坯的形状、尺寸、表面粗糙度以及力学物理性能,使之成为合格零件的全部劳动过程。
工艺:使各种原材料、半成品成为成品的方法和过程工艺过程:在生产过程中,凡是改变生产对象的形状、尺寸、相对位置和性质等,使其成为成品和半成品的过程。
二.机械加工工艺过程的组成1.工序一个或一组工人,在一台机床或一个工作地点对一个或同时对几个工件所连续完成的那一部分工艺过程。
划分工序的主要依据:工作地点是否改变和加工是否连续完成。
同一零件,同样的加工内容可以有不同的工序安排。
如图所示的阶梯轴的加工:加工内容:1.加工小端面 2.小端面钻中心孔3.加工大端面 4.大端面钻中心孔5.车大端外圆 6.对大端倒角7.车小端外圆8.对小端倒角9.精车外圆10.铣键槽11.去毛刺工序1:加工内容1到9——车床工序2:加工内容10、11——铣床(手工去毛刺)工序1:加工内容1、2、7、8—加工小端工序2:加工内容3、4、5、6—加工大端工序3:加工内容9工序4:加工内容10、11 第三种工序安排:工序1:加工内容:1、2、3、4—铣两端面打中心孔工序2:加工内容:5、6、7、8—仿形车外圆、倒角工序3:加工内容:9—精车外圆工序4:加工内容:1—铣键槽工序5:加工内容:11—去毛刺2、安装如果在一个工序中要对工件进行几次装夹,则每次装夹下完成的那部分加工内容称为一个安装。
机械加工检验规范

测量或试验
处 理
比
较
记录反馈
1.1.1名词诠释
• 1.明确标准:熟悉和掌握质量标准、检验方法,并将其 作为测量和试验、比较和判定的依据; • 2.测量和试验:采用一定的检测器具或设备,按规定的 方法,对产品的特性进行测量,得出一具体的数据或结果; • 3.比较:把检测的结果与规定的标准要求进行比较; • 4.判定:根据比较的结果,判定产品是否合格; • 5.处理:将合格的接收(通过),不合格的重新处理 (报废或返修等); • 6.记录反馈:把测量或试验的数据做好记录、整理、统 计、计算和分析,按一定的程序和方法,向领导和部门反 馈质量信息,作今后改进质量,提高质量制订措施的依据。
机械加工检验规范
1 目的和范围
• 通过严格执行三检,“首件检验”、“巡回检验”、“终 检”将检验工作与工序控制紧密结合,对每一工序的质量 问题或可能出现的质量问题不放过,剔除不合格品,使其 不能投入下工序或出厂,从而达到工序控制的目的。 • 本检验程序适用于本厂所有自制产品零部件的由检验人员在生产现场,进行日常工艺纪律巡回监督检查, 重点监控工序质量和工艺纪律,并做好记录。 • a)根据检验工艺规程和作业指导书的要求、检验、 核对巡检产品的质量特性值是否真正符合要求。 • b)若巡检时某质量特性值不合格,应按《不合格品 控制程序》处理,同时,立即对本次巡检与上次巡检(或 首检)间隔中生产的产品的不合格质量特性值逐件100% 检查,剔除不合格品--追溯。 • c)对巡检中剔除的不合格品按《不合格品的控制程 序》进行处理。 • d)对投入批量生产的工件某尺寸在机加工过程中有 争议时,应立即报告技术部门进行分析性检查、仲裁性检 测,必要时核实工艺装备或工艺卡,严禁不合格工艺装备 或工艺卡继续生产和现场毛坯流入下道工序。
机械加工检验规定

机械加工检验规定1 目的和范围:通过严格执行三检,“首件检验”、“巡回检验”、“完工检验”将检验工作与工序控制紧密结合,对每一工序的质量问题或可能出现的质量问题不放过,剔除不合格品,使其不能投入下序或出厂,从而达到工序控制的目的。
本检验程序适用于本厂所有自制产品零部件和分、总成在冷加工过程中的检验和试验。
2 检测依据:过程检验的检测依据及技术支持和标准:按图纸、工艺要求、技术要求执行。
3 检验类别、内容和要求:3.1首件检验:3.1.1在下述情况下,必须首件检验确认后,才能开始加工;a)工作班开始加工的第一个工件;b)调换操作者后加工的第一个工件;c)更换(调整)工艺装备或更换模具后加工的第一个工件;d)代用材料后加工的第一个工件。
3.1.2首件检验的依据:a)生产图纸或工艺图纸或工艺卡片;b)作业指导书(工序控制点)3.1.3检验内容:根据检验工艺规程的要求,核对首件产品的质量特性值是否真正符合要求:对首件检验合格,批准生产加工。
首件检验不合格,进行不合格品的处理,同时分析不合格原因,采取改进措施后生产,产品继续首件检验,直至合格为止。
3.1.4检验要求:a)对首件,根据加工工艺要求,核实首件产品或工件(毛坯)产品的质量特性是否符合要求。
对首批检查的工件(毛坯),操作者必须做好自检和标识,在操作者缺乏检测手段时,也应对工件的外观质量自检,合格后送检验员检查。
无论在任何情况下,首件检验未经检验合格,不得进行批量生产或继续加工作业。
对首件不报检查的,检验员有权拒绝该批零件的检查。
b)作好首检检验记录,要求按工件种类分类填写首检记录,以便于追溯。
c)检验状态分为:合格、不合格、待检、检后待定;产品标识要求填具“工件名称、规格、数量、尺寸、首检合格”要素,并放在料块的最顶端。
3.2巡回检验:由检验人员在生产现场,进行日常工艺纪律巡回监督检查,重点监控工序质量和工艺纪律,原则上每班抽检三次,并做好记录。
机械加工检验规程

机械加工检验规程??1?总则?1.1?检验人员必须具有一定的专业知识和实际工作经验,且能满足现行产品对检验工作的各项要求。
?1.2?检验人员所用的计量器具必须是经计量部门校验合格并在规定周期内。
?1.3?检验人员验收产品前应熟读相关图样和技术文件,了解零件的关键尺寸及装配关系要点。
?1.4?检验人员必须严格按照图样和技术文件所规定的要求对零件进行判定。
?1.5?检验人员应对车间在制品按规定进行标识。
?1.6?检验人员必须定期(6个月最长1年)参加专业知识培训,学习和接受先进的检测方法,以提2??3?检验依据:?4?检验类别4.1?????4.2?要求。
?对投入批量生产的工件某尺寸在机加工过程中有争议时,应立即报告生产技术部进行分析性检查、仲裁性检测,必要时核实模具或工艺卡片,严禁不合格模具或工艺卡继续生产和现场毛坯流入下道工序。
?4.3?完工检验(终检)?的工序是否全部完成,有无漏序、跳序的现象存在,并分析原因,采取措施。
?货验收技术条件及标准。
??完工批抽样以该批总数量的10%,但不低于5件,如果检测样件全部检测项目(质量特性)均合格,则判定该完工批为合格批。
??如果检测样件的一个(或一个以上)检测项目(质量特性)不符合,则应对整个完工批产品该检测项目(质量特性)全数(100%)的检验,剔除所有不合格品,剔除不合格品后的完工批判定为合格批,并在检验卡上记录。
??检验加工后的几何尺寸;??检验形状和位置误差;??检验外观,对零件的倒角、毛刺、磕碰、划伤应予以特别关注;??检查应有的标识是否齐全、正确,有无漏序、跳序的现象存在,在批量完工件中有无尚未完工或不同规格的零件混入,并分析产生的原因,采取纠正措施,必要时提出防止再发生的措施建议。
?5?检验方法?5.1?外径的测量?角应在605.2?线交角应在5.3?5.4???采用粗糙度样块比较法进行比较判断。
?应采用打表法检测,即平板上放置三个可调支撑,将零件测量面朝上放置于支撑点上,调整支撑点,使三点等高(千分表在三点上的读数均为零),打表所测得峰谷值即为该平面的平面度。
机加工检验规范
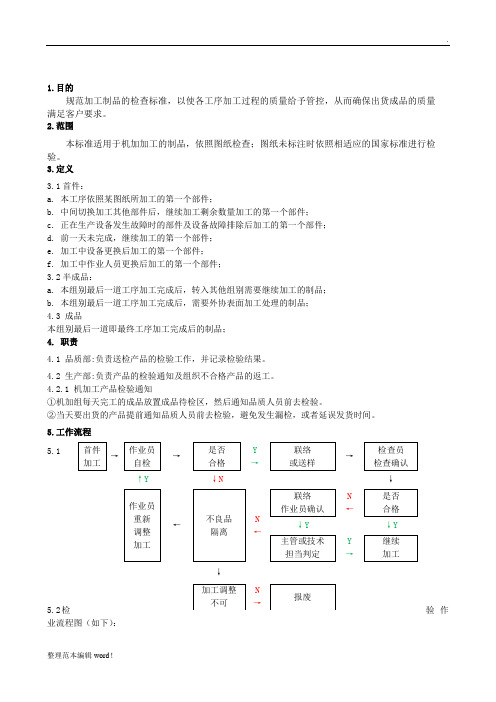
1.目的规范加工制品的检查标准,以使各工序加工过程的质量给予管控,从而确保出货成品的质量满足客户要求。
2.范围本标准适用于机加加工的制品,依照图纸检查;图纸未标注时依照相适应的国家标准进行检验。
3.定义3.1首件:a. 本工序依照某图纸所加工的第一个部件;b. 中间切换加工其他部件后,继续加工剩余数量加工的第一个部件;c. 正在生产设备发生故障时的部件及设备故障排除后加工的第一个部件;d. 前一天未完成,继续加工的第一个部件;e. 加工中设备更换后加工的第一个部件;f. 加工中作业人员更换后加工的第一个部件; 3.2半成品:a. 本组别最后一道工序加工完成后,转入其他组别需要继续加工的制品;b. 本组别最后一道工序加工完成后,需要外协表面加工处理的制品; 4.3 成品本组别最后一道即最终工序加工完成后的制品; 4. 职责4.1 品质部:负责送检产品的检验工作,并记录检验结果。
4.2 生产部:负责产品的检验通知及组织不合格产品的返工。
4.2.1 机加工产品检验通知①机加组每天完工的成品放置成品待检区,然后通知品质人员前去检验。
②当天要出货的产品提前通知品质人员前去检验,避免发生漏检,或者延误发货时间。
5.工作流程 5.15.2检验作业流程图(如下):→→Y →→ ↑Y↓N↓←N←N ←↓Y ↓Y Y →↓N →6.相关文件根据ISO 2768-m 标准进行判定是否合格抽检方式以AQL 标准进行抽检材质、数量 确认Y → 抽样 → 尺寸 检查 ↑Y ╲N ↘ ╱ ↙ N ↓Y 接收待检品及图纸→ 待检品与图纸一致确认N → 联络 作业员 确认 N ← 手动试 装配确认 ↑Y ↓Y ╱ ↙ N ↖ N ╲返工 全检 ← 全数 退回 ↓Y 外观 检查 ↖ N ╲ ↓N 主管或技术 担当判定↓Y ╲Y ↘ 报废 半成品 继续流动 检查表单 记录←成品 入库7.检验要求及方法7.1被测品与其对应图纸比对确认其各加工工序是否全部完成,有无漏序;7.2 材质、数量确认依照图纸标注确认;7.3尺寸确认:a.被测品本体长、宽(高)、厚是否一致;b.图纸标注公差要求的先行检查;其次检查一般公差尺寸。
机械加工过程检验规程

机械加工过程检验规程Q/YHZ益和电气集团股份有限公司作业指导书YH/ZD 21-2007-2013益和电气集团股份有限公司企业标准代替YH/ZD 21-2007-2012益和电气集团股份有限公司企业标准机械加工检验规程2013-07-25发布 2013-08-01实施发布益和电气集团股份有限公司YH/ZD 21-2008-2013目次目次 ..................................................................... ............ I 前言 ..................................................................... ............ II 机械加工检验规程 ..................................................................... . (1)1 目的 ..................................................................... . (1).................................................................... ........... 1 2 范围3 引用标准 ..................................................................... (1)4 检验类别、内容和要求: (1)5 记录 ..................................................................... .......... 2 附录A ...................................................................... .......... 3 附录B ...................................................................... . (6)IYH/ZD 21-2008-2013前言本标准按GB/T 1.1-2009给出的规则起草。
机械加工检验规程

机械加工件检验规程1、范围本检验规程适用本厂机械加工产品的检验。
2、检验依据2.1 国家标准、行业标准2.2 质量计划/检验计划2.3 产品图纸及加工工艺2.4 Q/DTGQ39-2004《产品最终检验和试验控制程序》3 测量设备的选择选用机加工工艺卡所规定的测量进行产品过程检验。
4 检验4.1 尺寸的检验4.1.1 基本原则所用验收方法应接收位于规定尺寸极限之内的工件.4.1.2 尺寸检验方法4.1.2.1 用标准量规检验,其判断准则是:如果通规通过,止规不能通过,则该工件为合格品。
4.1.2.2 通用量具检验法4.1.2.2.1 常用通用量具a.钢直尺(钢板尺)b.钢卷尺(盒尺)c.塞尺(厚薄规)d.游标卡尺e.高度游标卡尺f.深度游标卡尺g.外径千分尺h.内径千分尺i.内径量表j.量块4.1.2.2.2 对于公差等级高于IT10的用内外径千分尺或内外径量表检测;标准公差等级等于或低于IT10的游标类量具或其他通用量具检测。
4.1.2.2.3 对于特型结构尺寸的检验,采用专用样板、试规或通用量具。
4.2 形位误差的检验执行《形状和位置公差检测规定》5 检验方案5.1 过程首件产品,按图纸和加工过程卡要求对产品相应过程实施全参数检验。
5.2 出车间(完工)的产品,按照《产品最终检验和试验控制程序》的抽检比例进行全尺寸的检验。
6 质量记录检验员在产品机械加工检验的各相应过程作好过程首件合格证和产品质量跟单相应栏目的填写,按规定时间(每月5日前)将过程首件合格证交质管分部统计归档。
7 产品质量状态标识按Q/DTGQ26—2004《产品标识和可追溯性管理控制程序》的相关规定执行。
机械加工检验规范
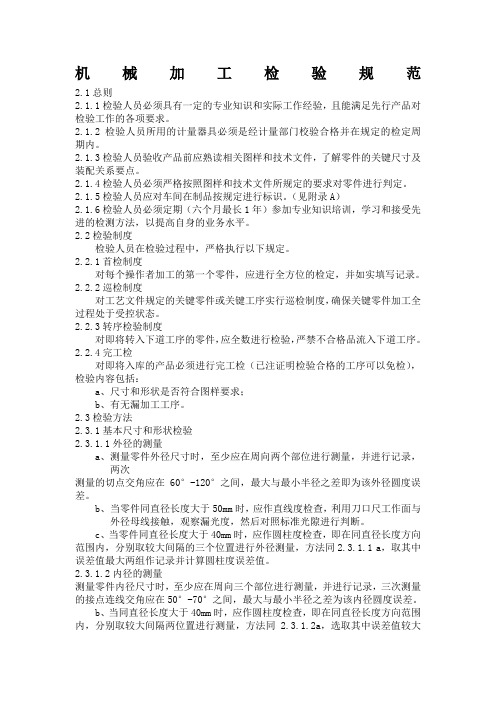
机械加工检验规范2.1总则2.1.1检验人员必须具有一定的专业知识和实际工作经验,且能满足先行产品对检验工作的各项要求。
2.1.2检验人员所用的计量器具必须是经计量部门校验合格并在规定的检定周期内。
2.1.3检验人员验收产品前应熟读相关图样和技术文件,了解零件的关键尺寸及装配关系要点。
2.1.4检验人员必须严格按照图样和技术文件所规定的要求对零件进行判定。
2.1.5检验人员应对车间在制品按规定进行标识。
(见附录A)2.1.6检验人员必须定期(六个月最长1年)参加专业知识培训,学习和接受先进的检测方法,以提高自身的业务水平。
2.2检验制度检验人员在检验过程中,严格执行以下规定。
2.2.1首检制度对每个操作者加工的第一个零件,应进行全方位的检定,并如实填写记录。
2.2.2巡检制度对工艺文件规定的关键零件或关键工序实行巡检制度,确保关键零件加工全过程处于受控状态。
2.2.3转序检验制度对即将转入下道工序的零件,应全数进行检验,严禁不合格品流入下道工序。
2.2.4完工检对即将入库的产品必须进行完工检(已注证明检验合格的工序可以免检),检验内容包括:a、尺寸和形状是否符合图样要求;b、有无漏加工工序。
2.3检验方法2.3.1基本尺寸和形状检验2.3.1.1外径的测量a、测量零件外径尺寸时,至少应在周向两个部位进行测量,并进行记录,两次测量的切点交角应在60°-120°之间,最大与最小半径之差即为该外径圆度误差。
b、当零件同直径长度大于50mm时,应作直线度检查,利用刀口尺工作面与外径母线接触,观察漏光度,然后对照标准光隙进行判断。
c、当零件同直径长度大于40mm时,应作圆柱度检查,即在同直径长度方向范围内,分别取较大间隔的三个位置进行外径测量,方法同2.3.1.1 a,取其中误差值最大两组作记录并计算圆柱度误差值。
2.3.1.2内径的测量测量零件内径尺寸时,至少应在周向三个部位进行测量,并进行记录,三次测量的接点连线交角应在50°-70°之间,最大与最小半径之差为该内径圆度误差。
机械加工检验规范
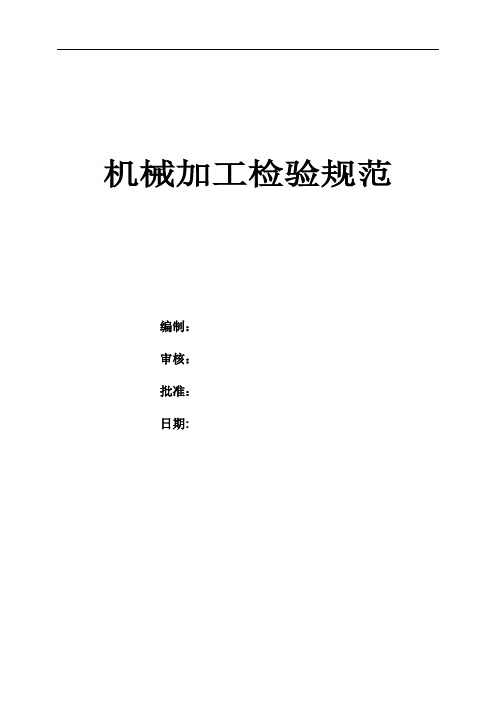
机械加工检验规范编制:审核:批准:日期:1、范围本检验规程适用本公司机械加工产品的检验。
2、检验依据国家标准、行业标准、API标准、图纸工艺等技术文件、质量计划等3、检验内容3.1 尺寸的检验3.1.1 基本原则所用验收方法应只接收位于规定尺寸极限之内的工件。
3.1.2常用量具钢直尺(钢板尺)、钢卷尺(盒尺)、塞尺(厚薄规)、游标卡尺、高度游标卡尺、深度游标卡尺、外径千分尺、内径千分尺、内径量表、量块3.1.3量具的选择3.1.3.1量具的选择原则A、保证测量精确度;B、保证测量的经济性,从计量器具成本、耐磨性、检验时间方便性等来考虑合理性;3.1.3.2量具具体选择A、根据零件的公差选用,取测量精度系数为二分之一到五分之一;B、根据计量器具的不确定度允许值选用;C、根据零件的大小选用;D、根据零件的表面质量选用;E、根据零件的批量来选用;3.1.3.3量具精度选择原则A、根据本公司的实际情况及以上的原则确定以下量具精度具体的选用原则;B、公司现有量具精度表3.1.4尺寸检测方法①轴径——中低精度轴径的实际尺寸通常用卡尺、千分尺、专用量表等普通计量器具进行检测。
②孔径——通常用卡尺、内径千分尺、内径规、内径摇表、内测卡规等普通量具、通用量仪;高精度深孔和精密孔等的测量常用内径百分表(千分表)或卧式测长仪(也叫万能测长仪)测量,用小孔内视镜、反射内视镜等检测小孔径。
③长度、厚度——长度尺寸一般用卡尺、千分尺、专用量表、测长仪、比测仪、高度仪、气动量仪等;厚度尺寸一般用塞尺、间隙片结合卡尺、千分尺、高度尺、量规;壁厚尺寸可使用超声波测厚仪或壁厚千分尺来检测管类、薄壁件等的厚度,用膜厚计、涂层测厚计检测刀片或其他零件涂镀层的厚度;用螺距规检测螺距尺寸值。
④表面粗糙度——a.目测检查:工件表面粗糙度比规定的粗糙度明显地好,不需用更精确的方法检验时,可用目测法检验判定;工件表面粗糙度比规定的粗糙度明显不好时,不需用更精确的方法检验时,可用目测法检验判定;工件表面存在明显影响表面功能的表面缺陷,选择目视法检验判定。
机械加工检验规程 (2)
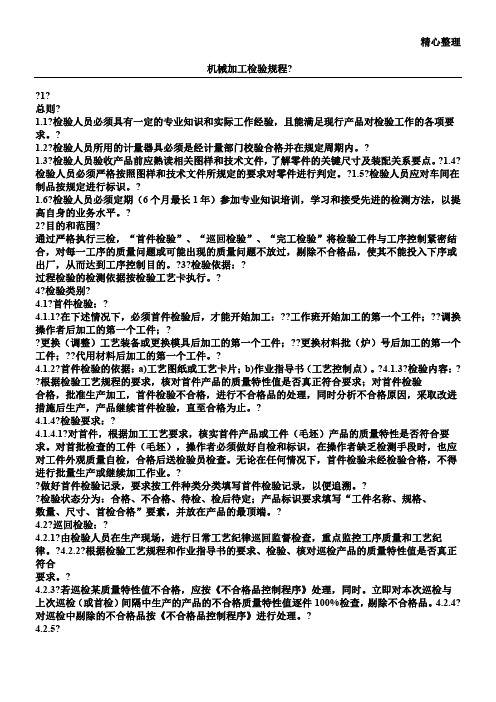
精心整理机械加工检验规程??1?总则?1.1?检验人员必须具有一定的专业知识和实际工作经验,且能满足现行产品对检验工作的各项要求。
?1.2?检验人员所用的计量器具必须是经计量部门校验合格并在规定周期内。
?1.3?检验人员验收产品前应熟读相关图样和技术文件,了解零件的关键尺寸及装配关系要点。
?1.4?检验人员必须严格按照图样和技术文件所规定的要求对零件进行判定。
?1.5?检验人员应对车间在制品按规定进行标识。
?1.6?2?4?4.1?4.1.1???调换?工件;4.1.2?? ?4.1.4?4.1.4.1???4.2?巡回检验:?4.2.1?由检验人员在生产现场,进行日常工艺纪律巡回监督检查,重点监控工序质量和工艺纪律。
?4.2.2?根据检验工艺规程和作业指导书的要求、检验、核对巡检产品的质量特性值是否真正符合要求。
?4.2.3?若巡检某质量特性值不合格,应按《不合格品控制程序》处理,同时。
立即对本次巡检与上次巡检(或首检)间隔中生产的产品的不合格质量特性值逐件100%检查,剔除不合格品。
4.2.4?对巡检中剔除的不合格品按《不合格品控制程序》进行处理。
?4.2.5?对投入批量生产的工件某尺寸在机加工过程中有争议时,应立即报告生产技术部进行分析性检查、仲裁性检测,必要时核实模具或工艺卡片,严禁不合格模具或工艺卡继续生产和现场毛坯流入下道工序。
?4.3?完工检验(终检)?4.3.1?全部加工活动结束后,对半成品或完工的产品、零件进行综合性的核对工作,核对加工件的工序是否全部完成,有无漏序、跳序的现象存在,并分析原因,采取措施。
?4.3.2?完工检验依据:a)工艺卡(图)或零件图;b)产品设计图样及作业指导书;c)合同规定或交货验收技术条件及标准。
?4.3.3?完工检验的抽样规定:??完工批抽样以该批总数量的10%,但不低于5件,如果检测样件全部检测项目(质量特性)均合格,则判定该完工批为合格批。
??4.3.4????5?5.1?5.1.1?角应在5.1.2?5.1.3?值。
03机械加工工艺与检验规范
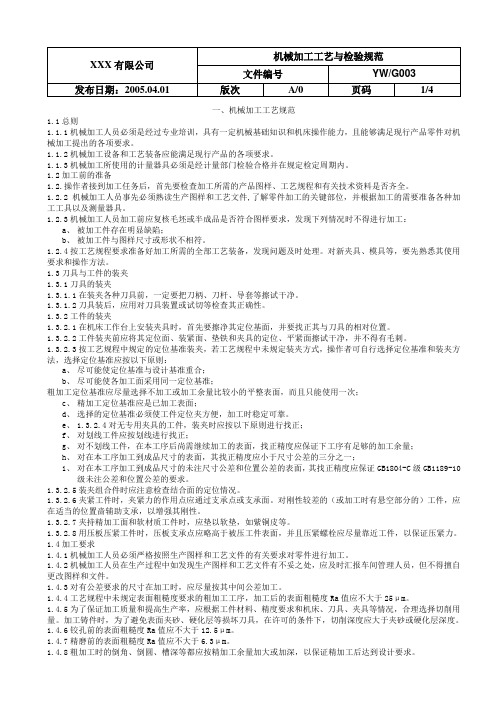
一、机械加工工艺规范1.1总则1.1.1机械加工人员必须是经过专业培训,具有一定机械基础知识和机床操作能力,且能够满足现行产品零件对机械加工提出的各项要求。
1.1.2机械加工设备和工艺装备应能满足现行产品的各项要求。
1.1.3机械加工所使用的计量器具必须是经计量部门检验合格并在规定检定周期内。
1.2加工前的准备1.2.操作者接到加工任务后,首先要检查加工所需的产品图样、工艺规程和有关技术资料是否齐全。
1.2.2机械加工人员事先必须熟读生产图样和工艺文件,了解零件加工的关键部位,并根据加工的需要准备各种加工工具以及测量器具。
1.2.3机械加工人员加工前应复核毛坯或半成品是否符合图样要求,发现下列情况时不得进行加工:a、被加工件存在明显缺陷;b、被加工件与图样尺寸或形状不相符。
1.2.4按工艺规程要求准备好加工所需的全部工艺装备,发现问题及时处理。
对新夹具、模具等,要先熟悉其使用要求和操作方法。
1.3刀具与工件的装夹1.3.1刀具的装夹1.3.1.1在装夹各种刀具前,一定要把刀柄、刀杆、导套等擦试干净。
1.3.1.2刀具装后,应用对刀具装置或试切等检查其正确性。
1.3.2工件的装夹1.3.2.1在机床工作台上安装夹具时,首先要擦净其定位基面,并要找正其与刀具的相对位置。
1.3.2.2工件装夹前应将其定位面、装紧面、垫铁和夹具的定位、平紧面擦试干净,并不得有毛刺。
1.3.2.3按工艺规程中规定的定位基准装夹,若工艺规程中未规定装夹方式,操作者可自行选择定位基准和装夹方法,选择定位基准应按以下原则:a、尽可能使定位基准与设计基准重合;b、尽可能使各加工面采用同一定位基准;粗加工定位基准应尽量选择不加工或加工余量比较小的平整表面,而且只能使用一次;c、精加工定位基准应是已加工表面;d、选择的定位基准必须使工件定位夹方便,加工时稳定可靠。
e、1.3.2.4对无专用夹具的工件,装夹时应按以下原则进行找正;f、对划线工件应按划线进行找正;g、对不划线工件,在本工序后尚需继续加工的表面,找正精度应保证下工序有足够的加工余量;h、对在本工序加工到成品尺寸的表面,其找正精度应小于尺寸公差的三分之一;i、对在本工序加工到成品尺寸的未注尺寸公差和位置公差的表面,其找正精度应保证GB1804-C级GB1189-10级未注公差和位置公差的要求。
机加工检验规范

1.目的规范加工制品的检查标准,以使各工序加工过程的质量给予管控,从而确保出货成品的质量满足客户要求。
2.范围本标准适用于机加加工的制品,依照图纸检查;图纸未标注时依照相适应的国家标准进行检验。
3.定义3.1首件:a. 本工序依照某图纸所加工的第一个部件;b. 中间切换加工其他部件后,继续加工剩余数量加工的第一个部件;c. 正在生产设备发生故障时的部件及设备故障排除后加工的第一个部件;d. 前一天未完成,继续加工的第一个部件;e. 加工中设备更换后加工的第一个部件;f. 加工中作业人员更换后加工的第一个部件; 3.2半成品:a. 本组别最后一道工序加工完成后,转入其他组别需要继续加工的制品;b. 本组别最后一道工序加工完成后,需要外协表面加工处理的制品; 4.3 成品本组别最后一道即最终工序加工完成后的制品; 4. 职责4.1 品质部:负责送检产品的检验工作,并记录检验结果。
4.2 生产部:负责产品的检验通知及组织不合格产品的返工。
4.2.1 机加工产品检验通知①机加组每天完工的成品放置成品待检区,然后通知品质人员前去检验。
②当天要出货的产品提前通知品质人员前去检验,避免发生漏检,或者延误发货时间。
5.工作流程 5.1 5.2检验作业流程图(如下):首件 加工 →作业员自检→是否 合格 Y → 联络 或送样 →检查员 检查确认↑Y ↓N↓ 作业员重新 调整 加工←不良品 隔离N ←联络 作业员确认N ← 是否 合格 ↓Y ↓Y 主管或技术 担当判定Y → 继续 加工↓加工调整 不可N →报废6.相关文件根据ISO 2768-m 标准进行判定是否合格 抽检方式以AQL 标准进行抽检 7.检验要求及方法7.1 被测品与其对应图纸比对确认其各加工工序是否全部完成,有无漏序; 7.2 材质、数量确认依照图纸标注确认; 7.3尺寸确认:a. 被测品本体长、宽(高)、厚是否一致;b. 图纸标注公差要求的先行检查;其次检查一般公差尺寸。
机械加工制程检验规程

机械加工制程检验规程一、目的:根据公司在机械加工中批量生产的特点特制定此检验规程。
二、范围:适用于本公司自制零件各工序的检验。
三、具体检验项目如下:1、落料(数控冲,数控剪,冲床,俗称展开图):⑴确认其材质、板厚是否与图相符,我公司所使用的板材主要有冷轧钢板、镀锌钢板、不锈钢板、热轧钢板、镀锌花纹板、铜板、以及铝板应注意其表面要求是雾面,镜面还是拉丝面,不可搞错。
⑵外观1)有无毛边毛刺,锐角,划碰伤,接刀痕,锈蚀;2)面板类,板材在去除毛边时,要特别注意不可被打磨成斜面(四角);3)如果此产品下道工序须作拉丝处理那么板材表面的划碰伤及毛刺只要不是很明显的手感即可接收,如为镀锌、镀铬等不需喷塑的需保护;4)在下料时还应注意其板材是否平直,不可有明显的波浪状及滚辊印痕。
⑶尺寸检验必须将其四周及孔的毛边毛刺,接刀痕去除于净,并且要产品校平后才能进行测量,否则会影响对产品尺寸的测量及判断。
⑷摆放及保护是否合理此方面主要依据作业指导书上的要求执行检验,要求贴膜保护,用隔板隔离的一定要遵照执行,如果工件摆放过高,四角要用透明打包胶带包好,以免在运输过程中发生倒塌及碰撞,损坏工件表面。
⑸现场有无作自检记录,记录是否真实,写的是否规范等。
⑹上述检验项目不可漏掉任何一项,当全部合格时方可下转。
2、数控折弯,冲床成型。
⑴确认其材质,板厚是否与图相符;⑵外观:表面有无明显之折痕,变形,折斜,划碰伤,接模痕等不良;⑶角度:每一刀的角度依图面清楚进行检测,对于折弯角度较复杂要求较高的工件,可做检具加以控制;⑷方向:在看折弯方向时先弄清楚图面要求的是什么视图方法(第一角,第三角还是机械视图)当发生折弯成型后毛边在正面一定要对折弯方向重新进行确认是否折反。
⑸尺寸:1)依图量测所有折弯尺寸;2)重点尺寸(图纸提示,有特殊标注或标有公差的尺寸)应予以重点控制,特别是那些不易测量,客户有投诉过的重点尺寸一定要设计检具进行控制;3)对不重要的尺寸如加强筋,工艺加强尺寸只要与图纸无太大的差别即可。
- 1、下载文档前请自行甄别文档内容的完整性,平台不提供额外的编辑、内容补充、找答案等附加服务。
- 2、"仅部分预览"的文档,不可在线预览部分如存在完整性等问题,可反馈申请退款(可完整预览的文档不适用该条件!)。
- 3、如文档侵犯您的权益,请联系客服反馈,我们会尽快为您处理(人工客服工作时间:9:00-18:30)。
第三章机械加工检验规程
1 目的和范围:
通过严格执行三检,“首件检验”、“巡回检验”、“完工检验”将检验工作与工序控制紧密结合,对每一工序的质量问题或可能出现的质量问题不放过,剔除不合格品,使其不能投入下序或出厂,从而达到工序控制的目的。
本检验程序适用于本厂所有自制产品零部件和分、总成在冷加工过程中的检验和试验。
2 检测依据:
过程检验的检测依据,按检验工艺卡执行。
3 检验类别、内容和要求:
3.1首件检验:
3.1.1在下述情况下,必须首件检验确认后,才能开始加工;
a)工作班开始加工的第一个工件;
b)调换操作者后加工的第一个工件;
c)更换(调整)工艺装备或更换模具后加工的第一个工件;
d)更换材料批(炉)号后加工的第一个工件;
e)代用材料后加工的第一个工件。
3.1.2首件检验的依据:a)工艺图纸或工艺卡片; b)作业指导书(工序控制点)
3.1.3检验内容:
根据检验工艺规程的要求,核对首件产品的质量特性值是否真正符合要求:对首件检验合格,批准生产加工。
首件检验不合格,进行不合格品的处理,同时分析不合格原因,采取改进措施后生产,产品继续首件检验,直至合格为止。
3.1.4检验要求:
a)对首件,根据加工工艺要求,核实首件产品或工件(毛坯)产品的质量特性是否符合要求。
对首批检查的工件(毛坯),操作者必须做好自检和标识,在操作者缺乏检测手段时,也应对工件的外观质量自检,合格后送检验员检查。
无论在任何情况下,首件检验未经检验合格,不得进行批量生产或继续加工作业。
b)作好首检检验记录,要求按工件种类分类填写首检记录,以便于追溯。
c)检验状态分为:合格、不合格、待检、检后待定;产品标识要求填具“工件名称、规格、数量、尺寸、首检合格”要素,并放在料块的最顶端。
3.2巡回检验:
由检验人员在生产现场,进行日常工艺纪律巡回监督检查,重点监控工序质量和工艺纪律。
a)根据检验工艺规程和作业指导书的要求、检验、核对巡检产品的质量特性值是否真正符合要求。
b)若巡检件某质量特性值不合格,应按《不合格控制程序》处理,同时,立即对本次巡检与上次巡检(或首检)间隔中生产的产品的不合格质量特性值逐件100%检查,剔除不合格品。
c)对巡检中剔除的不合格品按《不合格品的控制程序》进行处理。
d)对投入批量生产的工件某尺寸在机加工过程中有争议时,应立即报告技术部门进行分析性检查、仲裁性检测,必要时核实模具或工艺卡,严禁不合格模具或工艺卡继续生产和现场毛坯流入下道工序。
3.3完工检验(终检):
全部加工活动结束后,对半成品或完工的产品、零件进行综合性的核对工作,核对加工件的工序是否全部完成,有无漏序、跳序的现象存在,并分析原因,采取措施。
3.3.1完工检验依据:a)工艺卡(图)或零件图; b)产品设计图样及作业指导书; c)合同规定或交货验收技术条件及标准。
3.3.2完工检验的抽样规定:
a)完工批抽样以该批次总数量的10%、但不低于5件。
如果检测样件全部检测项目(质量特性)均合格,则判定该完工批为合格批。
b)如果检测样件的一个(或一个以上)检测项目(质量特性)不符合。
则应对整个完工批产品该检测项目(质量特性)全数(100%)的检验,剔除所有不合格品,剔除不合格品后的完工批判定为合格批,并在检验卡上记录。
4.3.3 完工检验内容和项目
a) 检验加工后的几何尺寸;
b)检验形状和位置误差;
c)检验加工面的粗糙度;
d)检验外观,对零件的倒角、毛刺、磕碰、划伤应予以特别注意。
e)检查应有的标识是否齐全、正确,有无漏序、跳序的现象存在,在批量的完工件中,有无尚未完工或不同规格的零件混入,并分析产生的原因,采取纠正措施,必要时提出防止再发生的措施建议。