降低铝电解氟盐消耗的有效途径
降低铝电解槽电能消耗措施的探讨
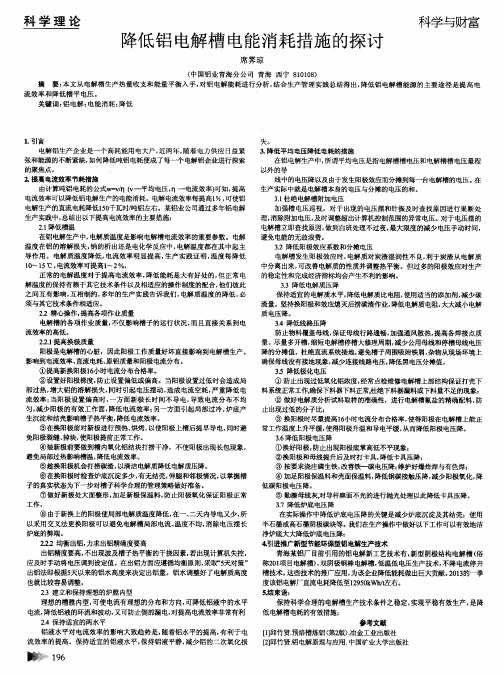
1 . 引言
失电大户 , 近两年 , 随着 电力供应 日益紧 3 . 降 低 平均 电压 降 低 电耗 的 措施 张和能源的不断紧缺, 如何 降低吨铝 电耗便成了每一个电解铝企业进行探索 在铝 电解生产中, 所谓平均 电压是指电解槽槽 电压和电解槽槽电压量程 的聚焦 点 。 以外 的 导 Z提高电流效率节耗措施 线中的电压降以及 由于发生阳极效应而分摊到每一台电解槽 的电压 。 在 由计算吨铝 电耗的公式w = v / q( v —平均 电压, n一 电流效率) 可知 , 提高 生产实际中就是电解槽本身的电压与分摊的电压的和。 电流效率可以降低铝电解生产 的电能消耗。电解电流效率每提高l %, 可使铝 3 . 1 杜绝 电解槽附加 电压 电解生产 的直流 电耗降低 1 5 0 千瓦时/ 吨铝左右。某铝业公司通过多年铝 电解 加强槽 电压巡视,对于出现的 电压摆和针振及时查找原因进行果断处 生产实践中, 总结 出以下提高电流效率 的主要措施: 理, 消除附加 电压, 及时调整超出计算机控制范围的异常 电 压。 对于电压摆的 2 . 1 降低槽温 电解槽立即查找原因, 做到 白班处理不过夜, 最大限度 的减少电压手动时间, 在铝电解生产中, 电解质温度是影响电解槽电流效率的重要参数。电解 避免电能的无故浪费。 温度在铝的溶解损失, 钠 的析 出还是电化 学反应 中, 电解温度都在其 中起主 3 . 2降低阳极效应系数和分摊 电压 导作 用。电解 质温度 降低 , 电流效率 明显提高 , 生产实践证明 , 温度每 降低 电解槽发生阳极效应时, 电解质对炭渣湿润性不良, 利于炭渣 从电解 质 l 0 ~1 5 ℃, 电 流效率可提高l ~2 %。 中分离出来, 可改善 电解质 的性质并调整热平衡 。但过多的阳极效应对生产 正常的电解温度对于提高电流效率, 降低 能耗是大有好处的, 但 正常 电 的稳定性和完成经济指标均会产生不利的影响。 解温度 的保持有赖于其它技术条件 以及相适应 的操作制度的配合, 他们彼此 3 . 3降低 电解质压降 之间互有影 响, 互相制约, 多年 的生产实践告诉我们 , 电解质温 度的降低 , 必 保持适宜的电解质水平, 降低电解质 比电阻, 使用适当的添加剂, 减少碳 须与其它技术条件相适应。 渣量。坚持换阳极和效应熄灭后捞碳渣作业, 降低电解质电阻, 大大减小电解 2 . 2精心操作, 提高各项作业质量 质 电压降。 电解槽的各项作业质量 , 不仅 影响槽子的运行状况 , 而且直接关系到电 3 . 4降低线路压降 流效率的高低 。 防止物料覆盖母线 , 保证母线行路通 畅, 加强通风散热, 提高各焊接点质 2 . 2 . 1 提高换极质量 量。尽量多开槽, 缩短电解槽停槽大修理周期, 减少公用母线和停槽母线电压 阳极是电解槽的心脏,因此阳极工作质量好坏直接影响到 电 解槽生产。 降的分摊值 。 杜绝直流系统接地 , 避免槽子周围吸附铁屑, 杂物从现场环境上 影响到电流效率 、 直流电耗、 原铝质量和阳极 电流分布。 确保母线没有接地现象, 减少连接线路电压, 降低黑电压分摊值。 ①提高新换阳极 l 6 小时电流分布合格率。 3 . 5降低极化 电压 ②设置好 阳极梯度 , 防止设置偏低或偏高。当阳极设置过低时会造成局 ① 防止出现过低氧化铝浓度, 经常点检维修 电解槽上部结构保证打壳下 部过热 , 增大铝的溶解损 失, 同时引起 电压摆动, 造成电流空耗 , 严重降低 电 料系统正常工作确 保下料器下料正常魁 绝下料器漏料或下料量不足的现象; 流效 率; 当阳极 设置偏 高时, 一方面新极长 时间不 导电, 导致电流分布不均 ② 做好电解质分析试料取样的准确性,进行电解槽氟盐的精确配料, 防 匀, 减少 阳极的有效工作面 , 降低 电流效率 ; 另一方面引起局部过冷 , 炉底产 止出现过低的分子比; 生沉淀和结壳影响槽子热平衡, 降低电流效率。 ③ 换阳极时尽量提高1 6 d x 时电流分布合格率, 使得阳极在电解槽上能正 ③在换阳极前对新极进行预热 、 烘烤, 以使阳极上槽后提早导电, 同时避 常工作温度上升平缓, 使得阳极升温和导电平缓, 从而降低阳极 电压降。 免阳极裂缝 、 掉块, 使阳极提前正常工作 。 3 . 6降低 阳极电压降 ④装新极前要做到槽 内氧化铝结块打捞干净 ,不使阳极出现长包现象 , ①换好 阳极, 防止出现阳极底掌高低不平现象; 避免局部过热影响槽温 , 降低电流效率。 ②换阳极和母线提升后及时打卡具, 降低卡具压降: ⑤趁换阳极机会打捞碳渣 , 以清洁电解质降低电解质压 降。 ③ 按要求浇注磷生铁 , 改善铁一碳 电压降: 维护好爆炸焊与有色焊; ⑥在换阳极时检查炉底沉淀多少, 有无结壳 , 伸腿和邻极情况, 以掌握槽 ④ 加足阳极保温料和壳面保温料, 降低钢碳接触压降, 减少阳极氧化 , 降 子的真 实状态为下一步对槽子科学合理的管理策略做好准备。 低碳阳极电压降。 ⑦做好新极处大面整形 , 加足新极保温料, 防止阳极氧化保证阳极正常 ⑤ 勤擦母线灰, 对导杆麻面不光的进行抛光处理以此 氐 卡具压 降。 工作。 3 . 7降低炉底 电压 降 ⑧ 由于新换上的阳极使局部 电解质温度降低, 在一、 二天 内导电又少 , 所 在实际操作中降低炉底电压 降的关键是减少炉底沉淀及其结壳;使用 以采用交叉法更换阳极可 以避免电解槽局部 电流、 温度 不均 , 消除 电压摆长 半石墨或高石墨阴极碳块等 。 我们在生产操作 中做好 以下工作可以有效地洁 炉底的弊端 。 净炉底大大 降低炉底 电压降: 2 . 2 . 2均衡出铝 , 力求出铝精确度要高 引进推广新型节能环保型铝电解生产技术
铝电解槽的氟平衡及降低氟排放的措施分析

预焙 阳极 电解 槽 的 氟 收入 主要 有 四项 :新 加 入 的氟 化盐 ,铝 电解烟 气净 化 回收 ,焙 烧炉 烟气 净 化 回收 ,电解质 、抬包 清理 及铸 造 除渣 回收 。 电解 槽 的 吨铝排 氟量 与氟 盐 的 加 入量 、烟 气 净化 的 回收 量 和 电解 槽槽 况 密切 相 关 ,根 据 国 内几 家铝 厂 的检 测 数 据 ,吨铝 排氟 一般 介 于 20~31kg之 间 ;氟 化 铝 加 入 量 一 般 介 于 15~22kg,下 面 以 电解 槽 吨 铝 排 氟 27kg,氟化铝加入量 17kg进行分析(所有数据的单
An fluorine equilibrium of alum inum reduction pot
and m easures of reducing fluorine em ission
Wd Magnesium Engineering and Research Institute Co., ,Shenyang 1 10001,China)
预焙 阳极 电解 槽 集 气效 率 可 达 98.5% 一99% , 而干 法 净 化 系 统 的 氟 净 化 效 率 高 达 99.4% 一 99.8% ,因此 电解 槽 烟气 中 的氟 约有 98% ~98.8% 通过 电解 烟气 净化 回收 并 返 回电解 槽 ,实现 电解 槽 氟 化 物 的循 环利 用 。
2018年 第 5期
· 铝 冶 炼 ·
轻 金 属
·21·
铝 电解 槽 的氟 平衡 及 降低 氟 排 放 的措 施 分 析
汪 林
(沈 阳铝镁 设 计研 究 院有 限公 司 ,辽 宁 沈 阳 110001)
摘 要 :本文对预焙槽生产 系统中氟的收入 和支 出进行 了详 细的分析 。根据 氟的收入和 支出得到 了氟平衡 图表 ,并对 氟排放的各项数值 进行 了对比分析 ,结果显示氟排放主要 集中在 电解槽 内衬 吸收及 电解 车间天窗排放 。随着环保要 求越来越严格 ,必须提 高电解槽的集气效率和烟气净化 效率才能满足 日益严格 的环保标准。 关键词 :氟平衡 ;氟化盐消耗 ;净化 效率;天窗排放 中 图 分 类 号 :TF821 文 献 标 识 码 :A 文 章 编 号 :1002—1752(2018)05—0021—05 DOI:10.13662/j.cnki.qjs.2018.05.006
降低铝电解槽电能消耗措施的探讨

降低铝电解槽电能消耗措施的探讨摘要:本文从电解槽生产热量收支和能量平衡入手,对铝电解能耗进行分析,结合生产管理实践总结得出,降低铝电解槽能源的主要途径是提高电流效率和降低槽平电压。
关键词:铝电解;电能消耗;降低1. 引言电解铝生产企业是一个高耗能用电大户,近两年,随着电力供应日益紧张和能源的不断紧缺,如何降低吨铝电耗便成了每一个电解铝企业进行探索的聚焦点。
2. 提高电流效率节耗措施由计算吨铝电耗的公式w=v/η(v —平均电压,η—电流效率)可知,提高电流效率可以降低铝电解生产的电能消耗。
电解电流效率每提高1%,可使铝电解生产的直流电耗降低150千瓦时/吨铝左右。
某铝业公司通过多年铝电解生产实践中,总结出以下提高电流效率的主要措施:2.1 降低槽温在铝电解生产中,电解质温度是影响电解槽电流效率的重要参数。
电解温度在铝的溶解损失,钠的析出还是电化学反应中,电解温度都在其中起主导作用。
电解质温度降低,电流效率明显提高,生产实践证明,温度每降低10~15 ℃,电流效率可提高1~2 %。
正常的电解温度对于提高电流效率,降低能耗是大有好处的,但正常电解温度的保持有赖于其它技术条件以及相适应的操作制度的配合,他们彼此之间互有影响,互相制约,多年的生产实践告诉我们,电解质温度的降低,必须与其它技术条件相适应。
2.2 精心操作,提高各项作业质量电解槽的各项作业质量,不仅影响槽子的运行状况,而且直接关系到电流效率的高低。
2.2.1 提高换极质量阳极是电解槽的心脏,因此阳极工作质量好坏直接影响到电解槽生产。
影响到电流效率、直流电耗、原铝质量和阳极电流分布。
①提高新换阳极16小时电流分布合格率。
②设置好阳极梯度,防止设置偏低或偏高。
当阳极设置过低时会造成局部过热,增大铝的溶解损失,同时引起电压摆动,造成电流空耗,严重降低电流效率;当阳极设置偏高时,一方面新极长时间不导电,导致电流分布不均匀,减少阳极的有效工作面,降低电流效率;另一方面引起局部过冷,炉底产生沉淀和结壳影响槽子热平衡,降低电流效率。
浅析电解铝生产节能降耗措施
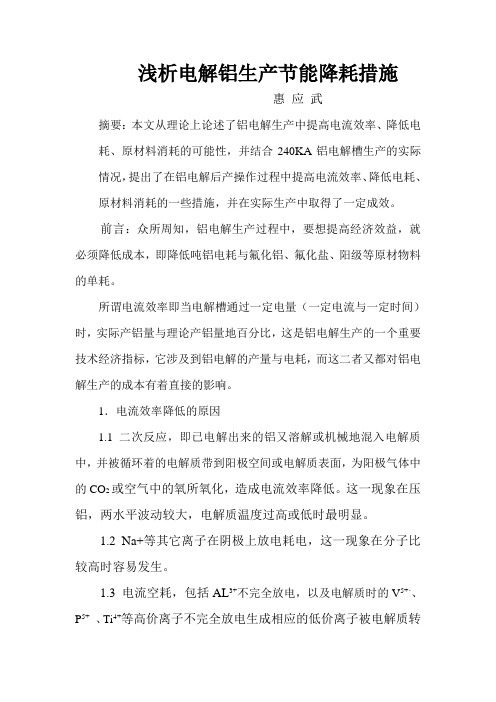
浅析电解铝生产节能降耗措施惠应武摘要:本文从理论上论述了铝电解生产中提高电流效率、降低电耗、原材料消耗的可能性,并结合240KA铝电解槽生产的实际情况,提出了在铝电解后产操作过程中提高电流效率、降低电耗、原材料消耗的一些措施,并在实际生产中取得了一定成效。
前言:众所周知,铝电解生产过程中,要想提高经济效益,就必须降低成本,即降低吨铝电耗与氟化铝、氟化盐、阳级等原材物料的单耗。
所谓电流效率即当电解槽通过一定电量(一定电流与一定时间)时,实际产铝量与理论产铝量地百分比,这是铝电解生产的一个重要技术经济指标,它涉及到铝电解的产量与电耗,而这二者又都对铝电解生产的成本有着直接的影响。
1.电流效率降低的原因1.1 二次反应,即已电解出来的铝又溶解或机械地混入电解质中,并被循环着的电解质带到阳极空间或电解质表面,为阳极气体中的CO2或空气中的氧所氧化,造成电流效率降低。
这一现象在压铝,两水平波动较大,电解质温度过高或低时最明显。
1.2 Na+等其它离子在阴极上放电耗电,这一现象在分子比较高时容易发生。
1.3 电流空耗,包括AL3+不完全放电,以及电解质时的V5+、、P5+、Ti4+等高价离子不完全放电生成相应的低价离子被电解质转移到阳级空间后,又再氧化成高价离子,即:A L3+ + 2e = A L+(阴极上)A L+ —2e = A L3+ (阳极上)如此循环,造成电流空耗。
这种现象在阴极表面的电子密度(即电流密度)较小时,如AE过多,炉温过高、化炉膛时,或整流所突然限电时比较明显。
1.3.2漏电通常是炉帮结壳熔化,并且电解质面上有大量炭渣时发生,即电流有可能连接槽壳与格子板之间,及铁渣箱体与槽壳接触等均可造成漏电损失。
在上述这些造成电流效率降低的原因当中原铝二次反应是电流效率降低的主要原因。
2.提高电流效率的措施既然电流效率降低的主要原因是熔解铝的再氧化(二次反应)损失,那么提高电流效率的措施可以从控制铝损失过程中探索。
浅谈降低铝电解氟化铝消耗的有效对策

2018年05月浅谈降低铝电解氟化铝消耗的有效对策王锦(重庆旗能电铝有限公司,重庆綦江410420)摘要:氟化铝是铝电解生产重要辅助原料,主要作用是调整分子比,有效控制氟化铝消耗不但确保槽运行稳定高效,而且影响生产成本。
结合实际情况,分析氟化铝消耗控制对策。
关键词:氟化铝;铝电解槽;分子比;对策铝电解槽生产过程中,氟化铝消耗是一项重技术指标,氟化铝是添加剂类辅助材料,主要作用调整电解槽的分子比,达到降低电解质初晶温度,本文就旗能电铝2016年和2017年氟化铝实际消耗情况,分析主要影响氟化铝消耗以及控制氟化铝消耗的对策。
1近两年氟化铝消耗情况经统计,2016年至2017年氟化铝单耗情况:(单位:kg/t-Al)月份2016年2017年1月17.321.72月33.116.23月30.320.24月15.720.75月24.525.16月25.623.37月24.721.88月22.919.09月19.119.810月20.423.711月24.731.812月28.920.5年度23.921.9从上表可看出,2016年和2017年氟化铝单耗完成分别为23.91kg/t-Al 和21.17kg/t-Al ,2017年单耗略有降低,均高于生产计划20kg/t-Al 。
同时,每月单耗高低不一,相对不均匀。
2影响氟化铝消耗的分析2.1与电解槽工艺参数的关系2.1.1氟化铝消耗与工作电压的关系经统计,2016年度电解槽平均电压为4.006V ,氟化铝单耗为23.9kg/t-Al ;2017年度电解槽平均电压为4.001V ,氟化铝单耗为21.9kg/t-Al 。
由此可见,氟化铝消耗与电解槽工作电压成反比关系。
当槽工作电压增加时,根据电解槽能量平衡关系,应适当降低分子比,保持电解槽能量平衡。
2.1.2氟化铝消耗与分子比的关系经统计,2016年度分子比平均2.33左右,氟化铝单耗为23.9kg/t-Al ;2017年度分子比平均2.37左右,单耗为21.9kg/t-Al 。
350kA电解系列降低氟化铝消耗的实践
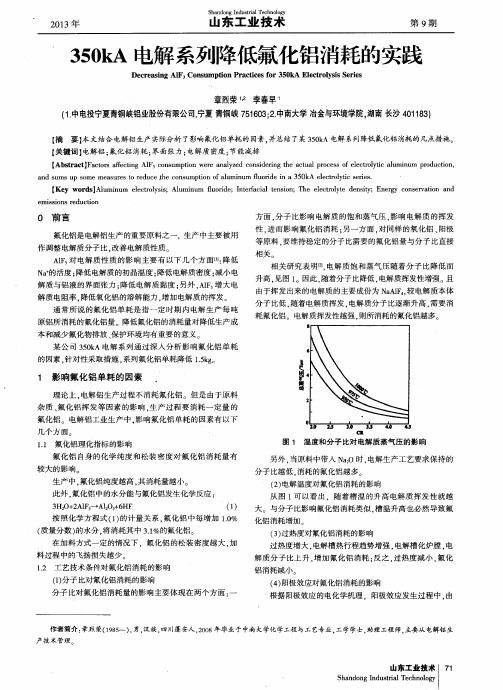
【 Ke y w o r d s ] A l u mi n u m e l e c t r o l y s i s ; A l u m i n u m l f u o i r d e ;I n t e r f a c i a l t e n s i o n ; T h e e l e c r t o l y t e d e n s i  ̄ ;E n e r g y c o n s e r v a t i o n a n d
【 关键词 】 电解铝 ; 氟化铝 消耗 ; 界 面张力; 电解质密度 ; 节能减排
【 Ab s t r a c t ] F a c t o r s a f e c t i n g A 1 F 3 c o n s u mp t i o n w e r e a n a l y z e d c o n s i d e i r n g t h e a c t u a l p r o c e s s o f e l e c t r o l y t i c a l u m i n u m p r o d u c t i o n ,
生产 中 。 氟化铝纯度越高 , 其消耗量越小 。 此外 , 氟化铝中的水 分能与氟化铝发生 化学反应 :
3 H 2 0 + 2 A 1 _ + A 1 2 O 3 + 6 H F ( 1 )
大 与分子 比影 响氟化铝消耗类 似 . 槽温升高 也必 然导致氟
化 铝 消 耗 增 加
按照化 学方程式 ( 1 ) 的计量关 系 . 氟化铝 中每增加 1 . 0 % ( 质量分数 ) 的水分 . 将 消耗其 中 3 . 1 %的氟化铝 。 在加料方式一定 的情 况下 .氟化铝 的松装密度越 大 . 加
料 过程 中的 飞 扬 损 失 越 少
降低铝电解氟盐消耗的有效途径

降低铝电解氟盐消耗的有效途径[摘要]铝电解槽氟盐消耗是电解铝生产的主要技术经济指标,不但关系到电解生产辅助原料的消耗、影响原铝生产成本,而且,作为辅助材料添加到电解槽中的氟化盐,对改善电解质成份和性能,提高生产指标有很重要作用。
本文从多年铝电解生产实践出发,总结降低氟盐消耗的有效途径,望能给大家一些参考。
[关键词]铝电解;氟盐消耗;降低;途径中图分类号:tf111.5文献标识码:a文章编号:1009-914x(2013)21-0000-01氟化盐作为添加剂加入电解槽中,是铝电解生产原料中一项重要的辅助原料,主要包括冰晶石和氟化铝。
氟化铝应用于铝电解生产,是用来改善电解质成份、降低电解质的熔化温度和提高导电率。
氟化铝在电解槽中的消耗速度较大,一部分随电解槽挥发烟气等物质,主要以naalf4形式挥发损失掉;另一部分与水份发生以下反应而消耗掉:2alf3+3h2o=al2o3+6hf冰晶石也是作为溶剂添加到电解槽中,它是电解质的主要成份,理论上只损失不消耗,但电解槽焙烧启动开槽时,冰晶石主主要的装炉料,用量在7吨以上。
所以,降低氟盐消耗是铝电解生产管理中一项重要而以艰巨的任务。
1 铝电解生产的氟平衡[1]铝电解的氟平衡有氟支出和氟收入,正常生产中电解槽除了人们熟知的物料平衡和能量平衡外,还有更重要的氟平衡。
铝电解槽的氟支出包括:铝电解槽内衬吸收;残极吸收和带走;电解质水解、挥发和飞扬而进入烟气和机械损失。
铝电解槽的氟收入有三项:铝电解烟气净化回收;阳极焙烧炉烟气净化回收;新补充氟。
当前较为通用的预焙阳极电解槽的烟气净化效率为98%,全氟净化效率为99%。
结合铝电解烟气净化工艺及电解槽的氟收、支平衡关系,可以绘制图1所示氟平衡图。
2 降低氟盐消耗的途径2.1 强化管理,减少氟盐浪费损失2.1.1 加强氟化盐添加使用过程中的现场管理,要求在氟化盐添加的各环节上严禁“跑、冒、滴、漏”等浪费现象的发生;氟化盐是一种易挥发的物质,为减少挥发,要求将氟化盐与粘性较大的冰晶石混合后添加,降低其挥发损失。
电解铝生产中含氟烟气的治理技术

云南 冶 金
YUNNAN METAL LUR GY
0c . 2 0 t 01
第3 9卷第 5期 ( 总第 24期 ) 2
V 13 . N . ( u 2 4) o 9 . o5 S m 2
电解 铝 生 产 中含 氟 烟气 的治 理 技 术
李振 宇
( 中国铝业 抚顺 铝业有 限公 司 ,辽 宁
i he Elc r l tc Al m i u o c i n n t e t o y i u n m Pr du to i
L e y IZh n- u
( hn l uh nAu nu o ,Ld ,F su ,Lann 0 1 hn ) C iac F s u lmii C . t. uh n i ig13 0 ,C ia o m o 1
K EY ORD S: ee t l i u n m ; F me Flo de d rc s u f ain W lcr y c a miu ot l u ; u r ; r po esp ri t i y i c o
工 业生 本 。无组 织排 放也将 造成 电解 车间 内及周边 地 区
关 键 词 :电解 铝 ;烟 气 ;氟 化 物 ;干 法净 化
中图 分 类 号 :X 5 文 献 标 识 码 :A 文章 编 号 :1 0 - 3 8 ( o o 5 0 7 - 5 78 0 6 0 0 2 l )0 - 0 3 0
Tr a m e t Te h l g fFl o i e-c n a n n m e e t n c no o y o u r n o t i i g Fu
摘
抚顺
13 0 ) 10 1
要 :介绍了铝 电解含氟污染物的产生 与危 害 ,重点从生产工 艺角度探讨 了治 理铝 电解 阳极 烟气 的方法 。
电解铝业氟污染特点和防治策略

电解铝业氟污染特点和防治策略
1.污染范围广:电解铝工艺中产生的氟污染不仅仅局限于生产场所的
周围环境,还会通过大气、水体和土壤等途径传播,影响周边的生态环境。
2.污染浓度高:电解铝工艺中所使用的氟化铝和氟离子含量较高,进
入生态环境后会积累和富集,造成污染程度较为严重。
3.毒性强:氟化物对人体和动植物具有较强的毒性,会对骨骼、牙齿
和神经系统等造成损害,长期暴露会引发氟中毒症状。
针对电解铝业氟污染问题,可以采取以下防治策略:
1.技术改进:通过改进电解工艺和采用先进的氟处理技术,减少和控
制氟化铝和氟离子的排放。
例如,可采用气体收集和气体洗涤等技术,降
低氟化铝气体在生产过程中的释放。
2.氟污染治理:对于电解铝工艺中产生的废水、废气和废渣,采取合
理的治理措施,如使用水处理技术和气体净化设备进行氟离子的去除。
同时,对电解泥和废渣进行合理的处理和处置,避免其对环境的二次污染。
3.监测和控制:建立完善的氟污染监测体系,实时监测氟化铝、氟离
子和二氧化碳等污染物的排放情况,及时采取控制措施,确保污染物排放
达标。
4.环境保护意识提高:加强员工的环境保护意识教育,提高其对氟污
染的认识和风险意识,增强环境保护意识和责任感。
5.加强监管:加强对电解铝生产企业的监管力度,加强对污染治理设
施的竣工验收和日常巡查监测,对于违反环保法规和标准的企业,依法进
行处罚,确保企业合规运行。
总之,电解铝业氟污染是一个环境保护和人体健康的重要问题,需要通过技术改进、污染治理、监测控制、环境保护意识提高和加强监管等措施来减少和防治氟污染,保护环境和人民的健康。
除尘器过滤面积对铝电解生产中氟化盐单耗的影响

除尘器过滤面积对铝电解生产中氟化盐单耗的影响除尘器过滤面积对铝电解生产中氟化盐单耗有着较大的影响,改善除尘器过滤面积能够有效改善铝电解生产过程中的氟化盐单耗量,这一措施值得在生产中进行推广。
标签:除尘器过滤面积铝电解氟化盐影响铝电解生产的原料是炭阳极、氧化铝以及氟化盐,其主要的添加剂就是氟化铝,氟化铝能够起到控制电解质分子比的作用,可以有效降低反应的温度。
在实际生产的过程中,电解槽生产的固氟与气氟通过净化系统处理之后可以进行二次利用,这样就能够优先提升原材料的利用率。
有关研究显示,除尘器过滤面积对铝电解生产中氟化盐单耗有着较大的影响,下面就针对这一问题进行深入的分析。
1 电解烟气净化方式就现阶段来看,铝电解主要使用干法净化原理进行生产,该种生产方式可以有效提升氟化物回收率,干法净化工艺涉及的流程较多,包括电解槽集气、吸附反应、气固分离反应、氧化铝的输送以及机械排风几个流程。
电解槽中的烟气有着扩散与无组织的特征,如果想要有效控制好烟气污染率,就需要将电解槽适当的密闭起来,并采取适宜的措施将收集的烟气汇集到电解厂房的排烟总管中,收集完成之后,再将其进行集中处理。
在进行反应时,需要将氧化铝粉与烟气进行结合,使其充分与烟气中的HF进行结合,完成吸附之后的氧化铝会变成载氟氧化铝,这一流程完成后,就需要将烟气与载氟氧化铝进行分离,这里分离需要采用袋式除尘器来进行,分离完成的载氟氧化铝部分能够作为氧化铝参与到后续的吸附反应中,而另外一部分则可以供电解来使用。
输送氧化铝的主要目的是为了解决原料的返回问题,新的氧化铝能够经过风动溜槽进入到其他的反应器之中,并作为原材料参与到新的电解反应中。
2 铝电解生产过程中的常见问题在铝电解的反应过程中,机械排风系统一直都起着十分重要的作用,机械排风系统也是整个反应系统的动力源,其主要的设备是引风机,在净化系统之中,除尘器、输送器以及烟气输送系统都是在负压状态下进行操作的,并不会对周围的环境造成污染。
提高阳极质量减少过量消耗的途径与措施
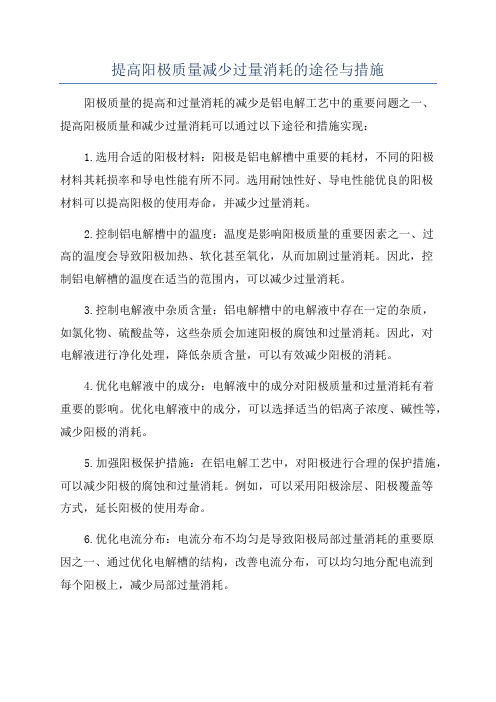
提高阳极质量减少过量消耗的途径与措施阳极质量的提高和过量消耗的减少是铝电解工艺中的重要问题之一、提高阳极质量和减少过量消耗可以通过以下途径和措施实现:1.选用合适的阳极材料:阳极是铝电解槽中重要的耗材,不同的阳极材料其耗损率和导电性能有所不同。
选用耐蚀性好、导电性能优良的阳极材料可以提高阳极的使用寿命,并减少过量消耗。
2.控制铝电解槽中的温度:温度是影响阳极质量的重要因素之一、过高的温度会导致阳极加热、软化甚至氧化,从而加剧过量消耗。
因此,控制铝电解槽的温度在适当的范围内,可以减少过量消耗。
3.控制电解液中杂质含量:铝电解槽中的电解液中存在一定的杂质,如氯化物、硫酸盐等,这些杂质会加速阳极的腐蚀和过量消耗。
因此,对电解液进行净化处理,降低杂质含量,可以有效减少阳极的消耗。
4.优化电解液中的成分:电解液中的成分对阳极质量和过量消耗有着重要的影响。
优化电解液中的成分,可以选择适当的铝离子浓度、碱性等,减少阳极的消耗。
5.加强阳极保护措施:在铝电解工艺中,对阳极进行合理的保护措施,可以减少阳极的腐蚀和过量消耗。
例如,可以采用阳极涂层、阳极覆盖等方式,延长阳极的使用寿命。
6.优化电流分布:电流分布不均匀是导致阳极局部过量消耗的重要原因之一、通过优化电解槽的结构,改善电流分布,可以均匀地分配电流到每个阳极上,减少局部过量消耗。
7.精确控制电解过程:借助先进的自动化控制系统,对铝电解过程进行精确控制,可以减少操作误差,提高电解过程的稳定性,从而减少过量消耗。
8.加强监测与维护:定期对铝电解槽进行检查,提前发现可能影响阳极质量和过量消耗的问题,并及时进行维护和修复,可以保证阳极的正常工作,延长使用寿命。
综上所述,提高阳极质量和减少过量消耗需要综合考虑材料、温度、电解液成分、电流分布等多个因素,并通过优化工艺控制、加强保护措施和监测维护等手段进行实施。
只有全面考虑和采取相应的措施,才能有效地提高阳极质量,减少过量消耗。
如何降低电解铝烟气氟化物排放浓度
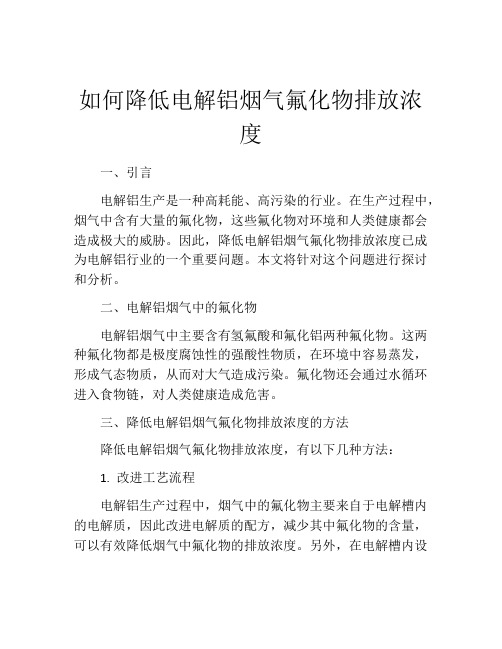
如何降低电解铝烟气氟化物排放浓度一、引言电解铝生产是一种高耗能、高污染的行业。
在生产过程中,烟气中含有大量的氟化物,这些氟化物对环境和人类健康都会造成极大的威胁。
因此,降低电解铝烟气氟化物排放浓度已成为电解铝行业的一个重要问题。
本文将针对这个问题进行探讨和分析。
二、电解铝烟气中的氟化物电解铝烟气中主要含有氢氟酸和氟化铝两种氟化物。
这两种氟化物都是极度腐蚀性的强酸性物质,在环境中容易蒸发,形成气态物质,从而对大气造成污染。
氟化物还会通过水循环进入食物链,对人类健康造成危害。
三、降低电解铝烟气氟化物排放浓度的方法降低电解铝烟气氟化物排放浓度,有以下几种方法:1. 改进工艺流程电解铝生产过程中,烟气中的氟化物主要来自于电解槽内的电解质,因此改进电解质的配方,减少其中氟化物的含量,可以有效降低烟气中氟化物的排放浓度。
另外,在电解槽内设置氧化槽,可以将一部分氟化物转化为氧化物,减少其在烟气中的含量。
2. 安装烟气净化设备烟气净化设备是现代电解铝企业中广泛采用的降低烟气氟化物排放浓度的方法。
常见的烟气净化设备包括湿式电除尘器、干式电除尘器和喷淋吸收塔等。
其中,湿式电除尘器和喷淋吸收塔能够同时减少氟化物和颗粒物的排放,效果更为显著。
3. 加强监管和管理强化对电解铝企业的监管和管理,对不符合排放标准的企业进行处罚和限制生产,同时加强对电解铝生产中所使用的原材料、燃料和助剂等的管理,可以减少烟气中的氟化物。
4. 推广清洁能源电解铝生产过程中的能源主要来自煤炭和天然气等传统能源,燃烧这些能源会产生大量的二氧化碳、氮氧化物和硫化物等有害物质。
因此,推广清洁能源,如太阳能、风能和水能等,可以避免传统能源带来的环境问题,减少烟气中的氟化物排放。
四、结论降低电解铝烟气氟化物排放浓度,是电解铝企业必须要面对的问题。
通过改进工艺流程、安装烟气净化设备、加强监管和管理,以及推广清洁能源等手段,可以有效地降低烟气中的氟化物排放量,保护环境、维护人类健康。
电解铝生产过程氟化物总量排放控制措施

电解铝生产过程氟化物总量排放控制措施摘要:电解铝生产技术作为有色金属工业领域一项重点技术,近些年来,取得了许多创新性技术突破,多项经济技术指标已经达到世界领先水平。
但在电解铝生产作业中,产生氟化物的问题始终存在,在此以提高电解槽集气效率和烟气净化效率为目标,探究电解铝生产中氟化物总量排放控制措施。
关键词:电解铝生产;氟化物;排放量;净化;控制措施引言:随着现代化技术发展,绿色、节能、环保理念成为发展重点,电解铝生产过程中产生的烟气治理得到进一步关注,其中高效率、高稳定性成为主要方向。
且2010年发布的《铝工业污染物排放标准》(GB25465-2010),明确就氟化物排放量提出要求。
在相关法律法规、技术规范指引下,我国电解铝生产中氟化物排放总量得到有效控制,相关控制技术得到进一步发展,为理想指标达成提供支持,在此从氟化物排放量控制措施方面入手展开研究具有实际意义。
1研究案例阐述为了更为全面、科学探究电解铝生产中氟化物排放总量控制措施,在此以xx 省内的XSL企业为研究对象展开分析。
1.1控制氟化物总量排放可行思路氟化物支出主要路径如下:电解槽内衬吸收、抬包清理、铸造除渣和电解质及残极损失、天窗以及净化系统排放。
上述路径中前三种路径可以通过科学管控降低氟化物排放量。
但最后一种路径:天窗及净化系统排放,由于结构特殊性,是电解铝生产中氟化物排量主要路径,也是造成氟损失的主要渠道,基于此,从此方面入手,提出控制策略有积极作用[1]。
主要可从以下两个方向进行思考:第一,提高集气效率。
电解铝生产时氟化物这一污染物主要产生路径包括两方面,其一是净化系统净化后的有组织排放,其二是天窗处的无组织排放。
基于此,从电解槽的烟气捕集效率方面入手是可行思路。
第二,提高净化效率。
先进的净化技术是降低污染物产生的关键,因此,从净化效率角度入手,提升烟气净化设备工艺和应用科学技术,降低氟化物产生率,也可以达到降低排放总量的目标。
降低铝电解生产电能消耗的途径
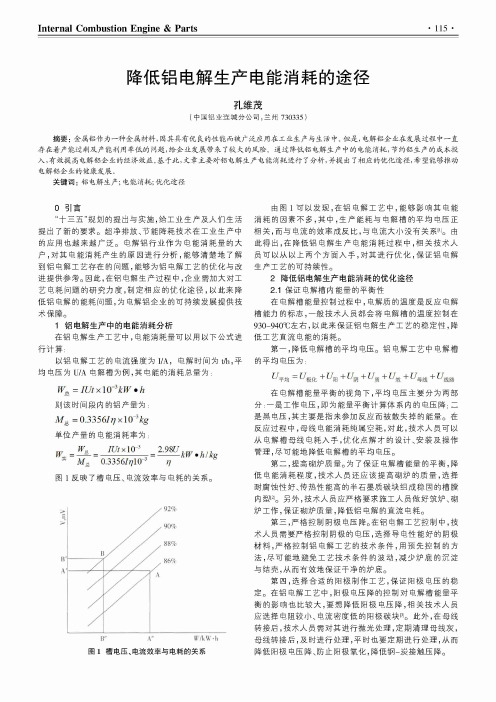
Internal Combustion Engine & Parts•115 •降低铝电解生产电能消耗的途径孔维茂(中国铝业连城分公司,兰州730335)摘要:金属铝作为一种金属材料,因其具有优良的性能而被广泛应用在工业生产与生活中。
但是,电解铝企业在发展过程中一直 存在着产能过剩及产能利用率低的问题,给企业发展带来了较大的风险。
通过降低铝电解生产中的电能消耗,节约铝生产的成本投 入,有效提高电解铝企业的经济效益。
基于此,文章主要对铝电解生产电能消耗进行了分析,并提出了相应的优化途径,希望能够推动 电解铝企业的健康发展。
关键词:铝电解生产;电能消耗;优化途径0引言“十三五”规划的提出与实施,给工业生产及人们生活 提出了新的要求。
超净排放、节能降耗技术在工业生产中 的应用也越来越广泛。
电解铝行业作为电能消耗量的大 户,对其电能消耗产生的原因进行分析,能够清楚地了解 到铝电解工艺存在的问题,能够为铝电解工艺的优化与改 进提供参考。
因此,在铝电解生产过程中,企业需加大对工 艺电耗问题的研究力度,制定相应的优化途径,以此来降 低铝电解的能耗问题,为电解铝企业的可持续发展提供技 术保障。
1铝电解生产中的电能消耗分析在铝电解生产工艺中,电能消耗量可以用以下公式进 行计算:以铝电解工艺的电流强度为I/A,电解时间为t/h,平均电压为U/A电解槽为例,其电能的消耗总量为:W& =I U t x l O~3k W»h则该时间段内的铝产量为:M总=0.3356切父10-%单位产量的电能消耗率为:l U^O-2M U k W m h/买M总0.3356/^103ij图1反映了槽电压、电流效率与电耗的关系。
由图1可以发现,在铝电解工艺中,能够影响其电能 消耗的因素不多,其中,生产能耗与电解槽的平均电压正 相关,而与电流的效率成反比,与电流大小没有关系[1]。
由此得出,在降低铝电解生产电能消耗过程中,相关技术人 员可以从以上两个方面入手,对其进行优化,保证铝电解 生产工艺的可持续性。
电解铝节能降耗措施探究
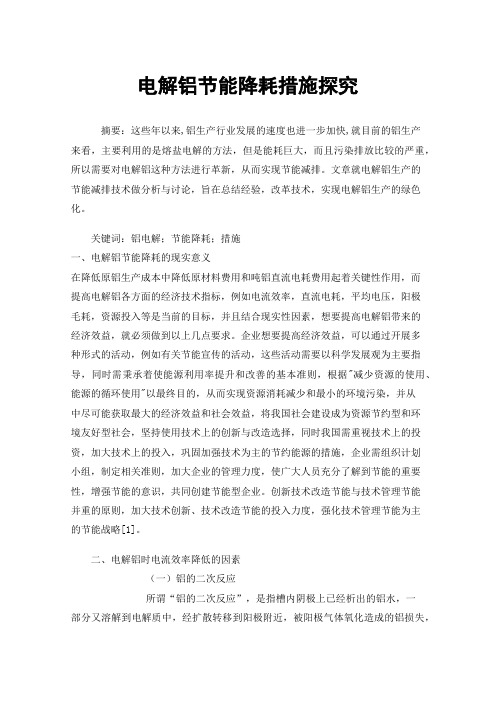
电解铝节能降耗措施探究摘要:这些年以来,铝生产行业发展的速度也进一步加快,就目前的铝生产来看,主要利用的是熔盐电解的方法,但是能耗巨大,而且污染排放比较的严重,所以需要对电解铝这种方法进行革新,从而实现节能减排。
文章就电解铝生产的节能减排技术做分析与讨论,旨在总结经验,改革技术,实现电解铝生产的绿色化。
关键词:铝电解;节能降耗;措施一、电解铝节能降耗的现实意义在降低原铝生产成本中降低原材料费用和吨铝直流电耗费用起着关键性作用,而提高电解铝各方面的经济技术指标,例如电流效率,直流电耗,平均电压,阳极毛耗,资源投入等是当前的目标,并且结合现实性因素,想要提高电解铝带来的经济效益,就必须做到以上几点要求。
企业想要提高经济效益,可以通过开展多种形式的活动,例如有关节能宣传的活动,这些活动需要以科学发展观为主要指导,同时需秉承着使能源利用率提升和改善的基本准则,根据"减少资源的使用、能源的循环使用"以最终目的,从而实现资源消耗减少和最小的环境污染,并从中尽可能获取最大的经济效益和社会效益,将我国社会建设成为资源节约型和环境友好型社会,坚持使用技术上的创新与改造选择,同时我国需重视技术上的投资,加大技术上的投入,巩固加强技术为主的节约能源的措施,企业需组织计划小组,制定相关准则,加大企业的管理力度,使广大人员充分了解到节能的重要性,增强节能的意识,共同创建节能型企业。
创新技术改造节能与技术管理节能并重的原则,加大技术创新、技术改造节能的投入力度,强化技术管理节能为主的节能战略[1]。
二、电解铝时电流效率降低的因素(一)铝的二次反应所谓“铝的二次反应”,是指槽内阴极上已经析出的铝水,一部分又溶解到电解质中,经扩散转移到阳极附近,被阳极气体氧化造成的铝损失,称为铝的溶解与损失,即“铝的二次反应”,这就是电流效率降低的本质和主要原因。
其反应式:2AL(溶解的)+3CO2(气)=AL2O3(溶解的)+3CO(气)。
铝电解企业降低氟盐消耗调研分析
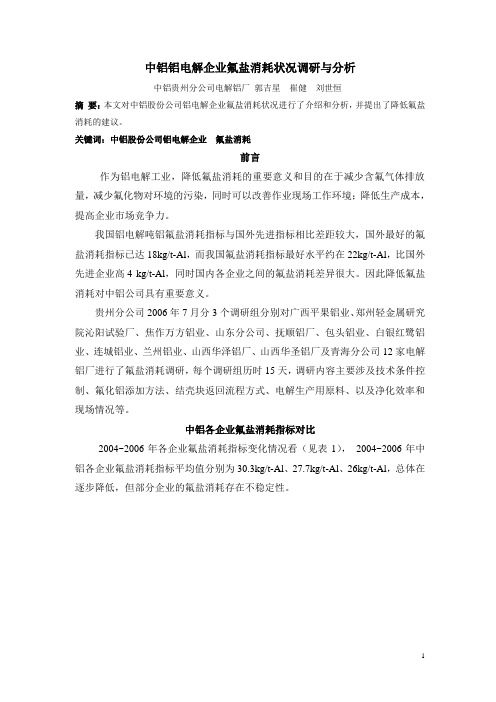
中铝铝电解企业氟盐消耗状况调研与分析中铝贵州分公司电解铝厂郭吉星崔健刘世恒摘要:本文对中铝股份公司铝电解企业氟盐消耗状况进行了介绍和分析,并提出了降低氟盐消耗的建议。
关键词:中铝股份公司铝电解企业氟盐消耗前言作为铝电解工业,降低氟盐消耗的重要意义和目的在于减少含氟气体排放量,减少氟化物对环境的污染,同时可以改善作业现场工作环境;降低生产成本,提高企业市场竞争力。
我国铝电解吨铝氟盐消耗指标与国外先进指标相比差距较大,国外最好的氟盐消耗指标已达18kg/t-Al,而我国氟盐消耗指标最好水平约在22kg/t-Al,比国外先进企业高4 kg/t-Al,同时国内各企业之间的氟盐消耗差异很大。
因此降低氟盐消耗对中铝公司具有重要意义。
贵州分公司2006年7月分3个调研组分别对广西平果铝业、郑州轻金属研究院沁阳试验厂、焦作万方铝业、山东分公司、抚顺铝厂、包头铝业、白银红鹭铝业、连城铝业、兰州铝业、山西华泽铝厂、山西华圣铝厂及青海分公司12家电解铝厂进行了氟盐消耗调研,每个调研组历时15天,调研内容主要涉及技术条件控制、氟化铝添加方法、结壳块返回流程方式、电解生产用原料、以及净化效率和现场情况等。
中铝各企业氟盐消耗指标对比2004~2006年各企业氟盐消耗指标变化情况看(见表1),2004~2006年中铝各企业氟盐消耗指标平均值分别为30.3kg/t-Al、27.7kg/t-Al、26kg/t-Al,总体在逐步降低,但部分企业的氟盐消耗存在不稳定性。
表1 2004~2006年各电解系列氟盐消耗指标统计不同槽容量电解系列氟盐消耗对比分析1、300KA 级图一 300KA级电解系列氟盐消耗指标对比51015202530354045广西320郑院300焦作280华泽300电解系列氟盐消耗指标(k g /t -A l )300KA 级电解系列2004~2006年各电解系列氟盐消耗指标总体呈下降趋势,2006年上半年平均值比2004年降低了2.8 kg/t-Al 。
电解铝业氟污染特点和防治策略

CATALOGUE 目录•电解铝业氟污染特点•电解铝业氟污染防治策略•电解铝业氟污染防治技术•电解铝业氟污染防治管理政策建议•电解铝业氟污染防治案例分析01矿石冶炼过程电解槽排放生产废水030201氟污染来源排放量大排放形式多样毒性危害氟污染特点分析对环境的影响对人类的影响氟污染对环境和人类的影响021 2 3研发和推广新型低氟生产工艺提高能源利用效率合理规划电解铝产业布局预防措施强化环境监管和管理实施清洁能源政策严格环保法规和标准03开展区域性综合治理01开发和应用高效治理技术02加强企业自备治理设施建设03新型电解质体系低氟原铝含氟废气高效收集系统自动化控制采用先进的自动化控制系统,精确控制电解过程,减少氟的挥发和排放。
节能减排技术通过优化生产工艺、提高能源利用效率,减少氟的排放。
在线监测与报警系统建立在线监测与报警系统,实时监控生产过程中氟的排放情况,及时发现并处理异常情况。
高效吸附剂采用湿法净化技术,通过化学反应将氟转化为低氟化合物,降低废气中氟的含量。
湿法净化技术再生循环利用末端治理技术04完善政策法规体系制定严格的氟排放标准完善环保法规建立环保评价制度加强行业自律管理成立行业协会01建立企业联盟02加强企业环保意识培训03研发新的清洁生产技术推广成熟的技术和设备实施节能减排措施推行清洁生产技术05案例一某大型电解铝厂。
该厂采用先进的工艺和设备,对氟污染进行有效的控制。
在生产过程中,采用封闭式的电解槽,减少氟化物对外部环境的排放。
同时,配备高效的烟气净化系统,对排放的烟气进行深度处理,确保达标排放。
案例二某地区电解铝产业集群。
该地区注重整体规划,合理布局电解铝企业,避免相互之间的污染影响。
同时,建立完善的污染物处理设施,对产生的各类污染物进行集中处理,确保达标排放。
国内成功案例介绍国际成功案例介绍案例一某发达国家电解铝厂。
该厂采用先进的生产工艺和设备,对氟污染进行有效的控制。
在生产过程中,注重资源节约和环境保护,采用清洁能源和高效的生产线,减少对环境的影响。
铝电解节能降耗的措施
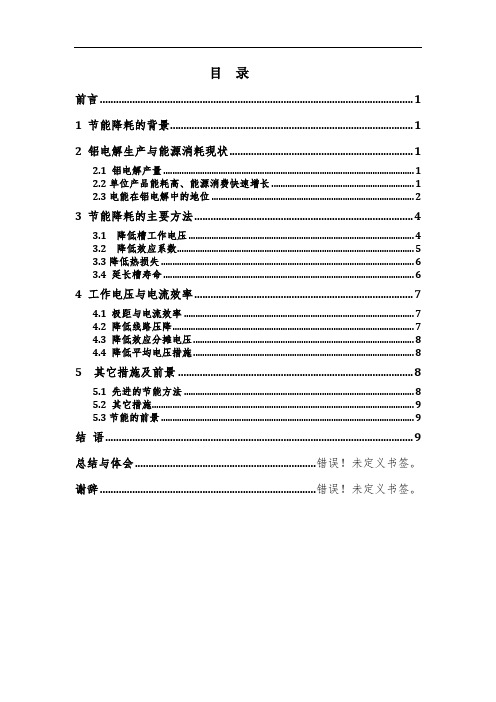
目录前言 (1)1 节能降耗的背景 (1)2 铝电解生产与能源消耗现状 (1)2.1 铝电解产量 (1)2.2单位产品能耗高、能源消费快速增长 (1)2.3电能在铝电解中的地位 (2)3 节能降耗的主要方法 (4)3.1 降低槽工作电压 (4)3.2 降低效应系数 (5)3.3降低热损失 (6)3.4 延长槽寿命 (6)4 工作电压与电流效率 (7)4.1 极距与电流效率 (7)4.2 降低线路压降 (7)4.3 降低效应分摊电压 (8)4.4 降低平均电压措施 (8)5 其它措施及前景 (8)5.1 先进的节能方法 (8)5.2 其它措施 (9)5.3节能的前景 (9)结语 (9)总结与体会 ................................................................... 错误!未定义书签。
谢辞 ................................................................................ 错误!未定义书签。
前言电解铝是用电大户, 电耗占吨铝成本的 40 %左右,做好电解工艺和动力用电方面的节能降耗工作,降低吨铝综合交流电耗可有效提高铝电解的经济效益。
我们应该开展多种形式的节能宣传活动, 以科学发展观为指导,以提高和优化能源利用率为目标,按照减量化、再利用、资源化的原则, 实现以尽可能少的能源消耗和尽可能小的环境代价,获取尽可能大的经济和社会效益, 建设资源节约型和环境友好型社会, 坚持技术创新、技术改造节能与技术管理节能并重的原则,加大技术创新、技术改造节能的投入力度,强化技术管理节能为主的节能战略.铝电解槽的电耗,只与电解槽的平均电压和电流效率两个因素有关,若要降低吨铝直流电耗,必须降低电解槽工作电压或者提高电解槽电流效率,在两者之间取个平衡点,在尽量不降低电流效率的情况下,电压最低,能耗最小。
- 1、下载文档前请自行甄别文档内容的完整性,平台不提供额外的编辑、内容补充、找答案等附加服务。
- 2、"仅部分预览"的文档,不可在线预览部分如存在完整性等问题,可反馈申请退款(可完整预览的文档不适用该条件!)。
- 3、如文档侵犯您的权益,请联系客服反馈,我们会尽快为您处理(人工客服工作时间:9:00-18:30)。
降低铝电解氟盐消耗的有效途径
作者:王有银
来源:《中国科技博览》2013年第21期
[摘要]铝电解槽氟盐消耗是电解铝生产的主要技术经济指标,不但关系到电解生产辅助原料的消耗、影响原铝生产成本,而且,作为辅助材料添加到电解槽中的氟化盐,对改善电解质成份和性能,提高生产指标有很重要作用。
本文从多年铝电解生产实践出发,总结降低氟盐消耗的有效途径,望能给大家一些参考。
[关键词]铝电解;氟盐消耗;降低;途径
中图分类号:TF111.5文献标识码:A文章编号:1009-914X(2013)21-0000-01
氟化盐作为添加剂加入电解槽中,是铝电解生产原料中一项重要的辅助原料,主要包括冰晶石和氟化铝。
氟化铝应用于铝电解生产,是用来改善电解质成份、降低电解质的熔化温度和提高导电率。
氟化铝在电解槽中的消耗速度较大,一部分随电解槽挥发烟气等物质,主要以NaAlF4形式挥发损失掉;另一部分与水份发生以下反应而消耗掉:
2AlF3+3H2O=Al2O3+6HF
冰晶石也是作为溶剂添加到电解槽中,它是电解质的主要成份,理论上只损失不消耗,但电解槽焙烧启动开槽时,冰晶石主主要的装炉料,用量在7吨以上。
所以,降低氟盐消耗是铝电解生产管理中一项重要而以艰巨的任务。
1 铝电解生产的氟平衡[1]
铝电解的氟平衡有氟支出和氟收入,正常生产中电解槽除了人们熟知的物料平衡和能量平衡外,还有更重要的氟平衡。
铝电解槽的氟支出包括:铝电解槽内衬吸收;残极吸收和带走;电解质水解、挥发和飞扬而进入烟气和机械损失。
铝电解槽的氟收入有三项:铝电解烟气净化回收;阳极焙烧炉烟气净化回收;新补充氟。
当前较为通用的预焙阳极电解槽的烟气净化效率为98%,全氟净化效率为99%。
结合铝电解烟气净化工艺及电解槽的氟收、支平衡关系,可以绘制图1所示氟平衡图。
2 降低氟盐消耗的途径
2.1 强化管理,减少氟盐浪费损失
2.1.1 加强氟化盐添加使用过程中的现场管理,要求在氟化盐添加的各环节上严禁“跑、冒、滴、漏”等浪费现象的发生;氟化盐是一种易挥发的物质,为减少挥发,要求将氟化盐与粘性较大的冰晶石混合后添加,降低其挥发损失。
2.1.2 提高操作质量,电解车间做到严禁将氟化盐洒到槽下、向槽下扫料、风管吹地等现象,杜绝飞扬损失。
2.1.3 由于添加到槽内的一部分氟化盐会被电解质、氧化铝块、阳极吸收,因此在平时的打捞炭渣、出铝、换极等日常工作中尽量避免电解质、氧化铝块的损失,并及时清理槽下料,将洒漏的物料回收到电解槽内重新利用;换出的残极块上的氧化铝块经粉碎处理后全部重新返回到电解槽内,减少氟化盐、氧化铝等物料损失。
2.1.4 氟盐添加时务必使用盐料箱进行添加,杜绝飞扬、洒落等浪费现象。
2.2 改进生产工艺技术
2.2.1 控制好电解槽工艺技术条件,保持电解槽的平稳生产,保持槽温和分子比的稳定控制,精确计算单槽的氟化盐添加量,对氟盐下料量进行称量,调整好加料间隔,保证氟化盐添加量稳定,减少因槽温和分子比发生大的波动而造成的氟化盐的增加。
2.2.2 改进新开槽装炉工艺,主要有以下技术创新点。
一是电解槽装炉时,中缝不装冰晶石,形成空腔,有利于槽膛内热空气循环,避免了电解槽阴极局部过热,有利于电解槽顺利启动;二是阳极上不再添加冰晶石,而是用破碎电解质块代替冰晶石,这样达到节约氟化盐目的,每台新开槽可节约冰晶石3吨,同时,在新开槽启动时,灌入足量的电解质。
2.2.3 加强对炉底的关注和处理,往往炉底的急剧变化会导致分子比和氟盐(氟化铝)添加量的急剧变化。
因此,在日常管理中,根据炉底状况变化及时调整技术条件和相关技术参数,确保炉底状况稳定。
2.2.4 坚持电解槽日评判制度。
每天坚持日评判,严格按照电解槽“控制分析评判会”技术参数调整要求,查找出不符合技术规范的电解槽,进一步合理匹配技术条件,使其向技术规范靠拢,促进电解槽更加平稳高效运行。
电解工区要保证槽温、分子比的真实性,给电解槽氟盐的投放量提供可靠的参考依据。
2.3 对电解槽进行综合分析合理使用氟盐
2.3.1 氟盐投放量与分子比、槽温变化不相符合时,工区一定要检查称量氟盐的每次下料量,来合理设定氟盐投放量。
2.3.2 对于长期分子比走低、槽温较低的槽子,要检查氟盐有没有漏料的情况;对于分子比偏高、槽温较高的槽子,要及时检查保证第一点火眼的开口率。
总之,要坚决避免氟盐的浪费。
2.3.3 分子比与槽温难以对应,长期投放氟盐效果不佳的电解槽,要综合分析电解槽各项技术条件是否合理,及时查找出原因后采取有效措施进行合理调整、控制。
2.4 加强设备管理降低盐消耗
2.4.1 加强对电解槽的密封处理,比如对电解槽槽盖板加装密封毡(炉门和三角盖板);对打壳锤杆周围进行密封改造;对氟化盐料箱盖子四周加密封毡或及时调整风量,杜绝料箱冒料现象;提高集气效率和净化效率,减少了氟化盐的排放损失。
采取以上措施后,从净化回收的载氟料重新打到电解车间,可在一定程度上降低氟化盐添加量。
2.4.2 加强电解槽打壳——下料系统的维修管理力度,进一步降低效应系数,减少电解槽在效应时造成氟盐的大量挥发损失。
认真处理和解决壳头包的问题,保持打壳下料系统平稳畅通,确保了氧化铝、氟化铝下料量的准确性。
对电解槽下料系统、计算机控制系统控制参数及电解槽技术条件进行优化改进,延长电解槽效应等待周期,将效应等待周期延长至720h以上,并通过提高电解操作工人效应熄灭质量,杜绝长重效应的发生,使效应持续时间向120s 以内靠拢。
2.4.3 合理开启多叶阀开启角度,提高烟气净化效率,提高电解烟气中氟的净化回收。
净化车间安排每班深入现场,及时了解供料及烟气净化情况,及时合理调整排烟机的开启。
2.4.4加强净化黑白料的配比,确保载氟料和新鲜氧化铝的均匀配料,对出现的供料问题,做到及时调整。
净化车间做好电解槽载氟氧化铝供料的均衡性和含氟量,为电解工区降低氟盐单耗打好基础力争使氧化铝供料含氟量的均衡性。
3 结束语
3.1 强化生产、技术、作业管理,提高设备正常运转,是降低铝电解生产氟盐消耗的有效途径。
3.2 确保电解生产技术条件、操作质量和槽况稳定是有效减少吨铝氟盐消耗的最有力途径。
3.3通过采取有效措施,某电解分厂吨铝氟盐消耗逐月降低,目前,2012年比2011吨铝氟盐消耗降低2.2多公斤。
参考文献
[1] 劼刘业翔,李.现化铝电解[M].北京.冶金工业出版社.2008.
[2] 邱竹贤.预焙槽炼铝北京[M].冶金工业出版社.2005.
[3] 田应甫.大型预焙铝电解槽生产实践[M].中南工业大学出版社.2003.。