压铸资料
压铸知识培训资料
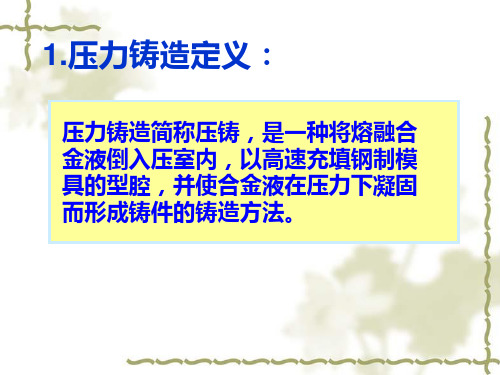
5.压铸机、压铸金属及压铸模具是组成压 铸工艺的3个要素。
卧式压铸机
立式压铸机
6.压铸机分类:
压铸机一般分为热压室压铸机和冷压室压铸机两大类。 冷压室压铸机按其压室结构和布置方式分为卧式压铸机 和立式压铸机(包括全立式压铸机)两种。 热压室压铸机(简称热空压铸机)压室浸在保温溶化坩 埚的液态金属中,压射部件不直接与机座连接,而是装 在坩埚上面。这种压铸机的优点是生产工序简单,效率 高;金属消耗少,工艺稳定。但压室,压射冲头长期浸 在液体金属中,影响使用寿命。并易增加合金的含铁量。 热压室压铸机目前大多用于压铸锌合金等低熔点合金铸 件,但也有用于压铸小型铝、镁合金压铸件。 冷室压铸机的压室与保温炉是分开的。压铸时,从保温 炉中取出液体金属浇入压室后进行压铸。
4.压力铸造适用材料及浇铸温度:
铝合金 铝硅系 610-650℃ 640-680℃ 600-620℃ 610650℃ 铝铜系 630-660℃ 660-700℃ 600-640℃ 630-660℃ 铝镁系 640-680℃ 660-700℃ 640-670℃ 650-690℃ 铝锌系 590-620℃ 620-660℃ 580-620℃ 600-650℃ 锌合金 420-440℃ 430-450℃ 400-420℃ 420-440℃ 镁合金 640-680℃ 660-700℃ 640-670℃ 650-690℃ 铜合金 普通黄铜 910-930℃ 940-980℃ 900-930℃ 900950℃ 硅黄铜 900-920℃ 930-970℃ 910-940℃ 910-940℃
7.压铸模具:
8.压铸工艺知识:
8-1、压力和速度的选择:按铸件结构确定。
8-2、浇注温度:从压定进入型腔时液态金属的平均温度。 8-3、压铸型的温度:在压铸前应进行预热。
压铸培训资料

根据企业实际情况制定相应的质量检测标准,确保产品质量符合 客户需求。
05
安全与环保
压铸安全操作规程
80%
操作前检查
在开始压铸前,应检查压铸机是 否正常,模具、工具和设备是否 完好,确保没有安全隐患。
100%
操作中注意事项
在压铸过程中,应保持稳定的速 度,避免过快或过慢,同时要密 切关注模具和设备的状态,如有 异常应立即停止操作。
通过改进模具设计,降低出现气孔、缩孔 、裂纹和变形等缺陷的风险。
控制压铸工艺参数
质量检测与控制
通过调整金属填充速度、模具温度和压力 等工艺参数,保证压铸件的质量。
对压铸件进行质量检测,及时发现并处理 缺陷,确保产品质量符合要求。
质量检测标准
国家标准
遵循国家相关标准,如GB/T 13821-2009《铝合金压铸件》等。
06
实际应用与案例分析
压铸在汽车制造业的应用
汽车发动机和底盘部件
高效生产
压铸技术广泛应用于汽车发动机和底 盘部件的制造,如气缸盖、油底壳等 。
压铸工艺可以实现大规模、高效的生 产,降低生产成本,提高汽车制造业 的竞争力。
轻量化需求
压铸技术能够生产出重量轻、强度高 的零部件,满足汽车轻量化需求,提 高燃油经济性和排放性能。
压铸培训资料
汇报人:任老师
2023-12-29
目
CONTENCT
录
• 压铸基础知识 • 压铸材料与模具 • 压铸设备与操作 • 压铸缺陷与质量控制 • 安全与环保 • 实际应用与案例分析
01
压铸基础知识
压铸定义
压铸是一种金属铸造工艺,利用高压将液态金属快速充填到模具 型腔内,并在压力下结晶凝固成铸件。
压铸知识培训资料
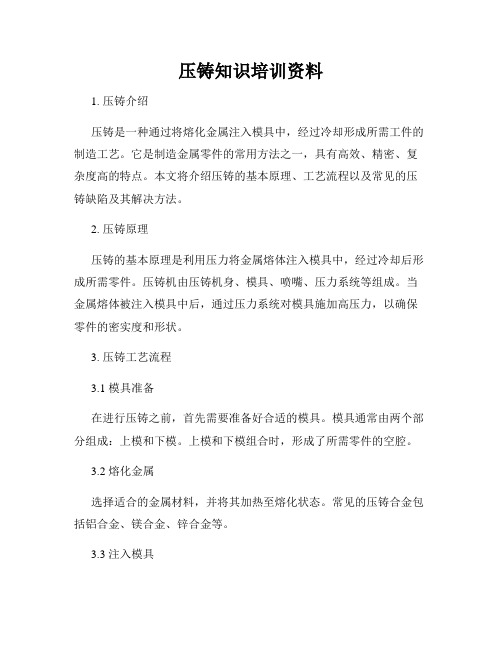
压铸知识培训资料1. 压铸介绍压铸是一种通过将熔化金属注入模具中,经过冷却形成所需工件的制造工艺。
它是制造金属零件的常用方法之一,具有高效、精密、复杂度高的特点。
本文将介绍压铸的基本原理、工艺流程以及常见的压铸缺陷及其解决方法。
2. 压铸原理压铸的基本原理是利用压力将金属熔体注入模具中,经过冷却后形成所需零件。
压铸机由压铸机身、模具、喷嘴、压力系统等组成。
当金属熔体被注入模具中后,通过压力系统对模具施加高压力,以确保零件的密实度和形状。
3. 压铸工艺流程3.1 模具准备在进行压铸之前,首先需要准备好合适的模具。
模具通常由两个部分组成:上模和下模。
上模和下模组合时,形成了所需零件的空腔。
3.2 熔化金属选择适合的金属材料,并将其加热至熔化状态。
常见的压铸合金包括铝合金、镁合金、锌合金等。
3.3 注入模具熔化的金属通过喷嘴注入模具中。
注入时需要保持恰当的温度和压力,以确保金属熔体充分填充模具空腔,并达到所需的形状、尺寸和表面质量。
3.4 冷却固化经过一段时间的冷却,金属熔体会逐渐固化成所需零件。
冷却时间取决于所使用的金属材料和零件的复杂度。
3.5 模具开启冷却固化后,模具会被打开,将成型的零件取出。
此时,零件通常还需经过后续的去毛刺、清洗和表面处理等工艺。
4. 常见压铸缺陷及其解决方法4.1 气孔气孔是指於压铸过程中形成的气体在金属熔体固化时被困住而产生的孔洞。
气孔会影响零件的密实度和强度。
解决方法:- 优化压铸过程中的通风系统,以消除气体积聚的机会。
- 使用合适的压力和注入速度,以确保金属熔体充分填充模具空腔,减少气体残留。
4.2 闪痕闪痕是指在模具接缝处形成的短裂纹或凹陷区域。
闪痕可能会导致零件的密封性能和外观质量下降。
解决方法:- 检查和调整模具的结构,尽可能减少接缝处的压力集中。
- 调整注入速度和压力,以避免压力过高造成闪痕现象。
4.3 密实度不良密实度不良是指零件内部存在过多的空洞或孔隙,导致零件不够坚固。
压铸工艺流程图示资料

一、压铸(BODY)工艺流程图示1,压铸机调试2,压铸模安装4,模具预热、涂料7,合型(合模)10浇注压射11,保压12,开模、抽芯取件14,清理(整修)17,终检验3,压铸模设计与制造5,涂料配制6,模具清理8,合金熔炼保温9,嵌件准备13,表面质量检查15,时效处理16,铸件浸渗、喷丸处理二、压射压力P3 P4压力P2P1 P2P1T1 t2 t3 t4 保压时间升压充填增压注:t1 金属液在压室中未承受压力的时间;P1为一级(慢速)t2 金属液于压室中在压射冲头的作用下,通过内浇口充填型腔的时间;P2为二级(快速)t3 充填刚刚结束时的舜间;P3为三级(增压)t4 最终静压力;P4为补充压实铸件4P yP b=Лd2式中:P b 比压(Mpa); Py 机器的压射力(N);(压射力=压射缸直径×蓄压器压射时间最小压力)d 压室(冲头)直径(MM)选择比压考虑的的主要因素上海旭东压铸技术咨询培训资料压铸工艺参数比压因素选择条件高低壁厚薄壁厚壁压铸件结构形状复杂简单工艺性差些好些结晶温度范围大小压铸合金特性流动性差好密度大小比强度大小阻力大小浇注系统散热速度快慢公布合理不太合理排溢系统截面积大小内浇口速度快慢温度合金与压铸模具温度大小压铸各种合金常用比压表(Mpa)铸件壁厚≤3(mm) 铸件壁厚>3(mm)合金结构简单结构复杂结构简单结构复杂锌合金20-30 30-40 40-50 50-60 铝硅、铝铜合金25-35 35-45 45-60 60-70铝、镁合金30-40 40-50 50-65 65-75 镁合金30-40 40-50 50-65 65-80铜合金40-50 50-60 60-70 70-80 压力损失折算系数K直浇道导入口截面F1,K值与内浇铸口截面F2之比>1 =1 <1立式冷室压铸机0.66-0.70 0.72-0.74 0.76-0.78卧式冷室压铸机0.88压射速度浇注金属液量占压室容积百分数(%) 压射速度(cm/s)≤30 30-4030-60 20-30>60 10-20高压速度计算公式:VVh= ×[1+(n-1)×0.1]1/4Лd2T式中:Vh 高速压射速度(CM/S);V 型腔容积(CM3);N 型腔数;D 冲头直径(CM);T 适当的充填时间。
压铸工艺复习资料
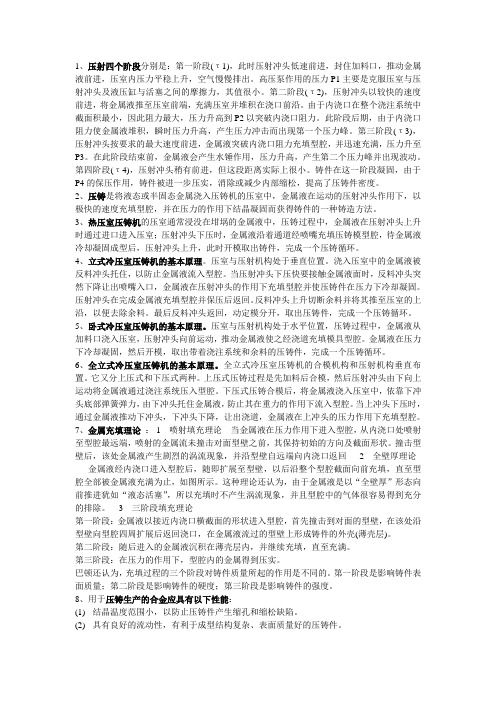
1、压射四个阶段分别是:第一阶段(τ1),此时压射冲头低速前进,封住加料口,推动金属液前进,压室内压力平稳上升,空气慢慢排出。
高压泵作用的压力P1主要是克服压室与压射冲头及液压缸与活塞之间的摩擦力,其值很小。
第二阶段(τ2),压射冲头以较快的速度前进,将金属液推至压室前端,充满压室并堆积在浇口前沿。
由于内浇口在整个浇注系统中截面积最小,因此阻力最大,压力升高到P2以突破内浇口阻力。
此阶段后期,由于内浇口阻力使金属液堆积,瞬时压力升高,产生压力冲击而出现第一个压力峰。
第三阶段(τ3),压射冲头按要求的最大速度前进,金属液突破内浇口阻力充填型腔,并迅速充满,压力升至P3。
在此阶段结束前,金属液会产生水锤作用,压力升高,产生第二个压力峰并出现波动。
第四阶段(τ4),压射冲头稍有前进,但这段距离实际上很小。
铸件在这一阶段凝固,由于P4的保压作用,铸件被进一步压实,消除或减少内部缩松,提高了压铸件密度。
2、压铸是将液态或半固态金属浇入压铸机的压室中,金属液在运动的压射冲头作用下,以极快的速度充填型腔,并在压力的作用下结晶凝固而获得铸件的一种铸造方法。
3、热压室压铸机的压室通常浸没在坩埚的金属液中,压铸过程中,金属液在压射冲头上升时通过进口进入压室;压射冲头下压时,金属液沿着通道经喷嘴充填压铸模型腔,待金属液冷却凝固成型后,压射冲头上升,此时开模取出铸件,完成一个压铸循环。
4、立式冷压室压铸机的基本原理。
压室与压射机构处于垂直位置。
浇入压室中的金属液被反料冲头托住,以防止金属液流入型腔。
当压射冲头下压快要接触金属液面时,反料冲头突然下降让出喷嘴入口,金属液在压射冲头的作用下充填型腔并使压铸件在压力下冷却凝固。
压射冲头在完成金属液充填型腔并保压后返回。
反料冲头上升切断余料并将其推至压室的上沿,以便去除余料。
最后反料冲头返回,动定模分开,取出压铸件,完成一个压铸循环。
5、卧式冷压室压铸机的基本原理。
压室与压射机构处于水平位置,压铸过程中,金属液从加料口浇入压室,压射冲头向前运动,推动金属液使之经浇道充填模具型腔。
压铸培训

52108853AA
异常曲线生产的产品
52108853AA
正常曲线及产品
G-BOX
产品探伤有气孔
G-BOX
检查产品,有冷隔缺陷
G-BOX
怀疑料温不够或模温不够,经调整料温、减少开模延 时,无明显改善;后将抽芯冷却水关掉,再生产OK。
G-BOX
怀疑料温不够或模温不够,经调整料温、减少开模延 时,无明显改善;后将抽芯冷却水关掉,再生产OK。
Home
5213606AB
浇口部位气孔:当靠近浇口部位有气孔,且敲掉浇口后,断 口部位能看出明显气孔时,基本上就是浇口套或料筒里进水, 这时需检查浇口套或压射头是否有漏水。检查浇口套时,需 将进水打开,回水关掉,等10分钟左右再观察浇口套是否漏 水。
5213606AB
52108853AA
异常曲线
压铸培训
一、压铸理论知识 1、压铸填充原理 2、压射机构工作原理 3、压射填充过程 二、压铸生产过程 1、压铸工序记录注意事项 2、模具冷却水检查 3、喷涂 三、压铸安全操作规程 四、压铸机工艺参数的调整 五、喷雾机、取件机的调整
压铸填充原理
• 压力铸造(简称压铸) 是将熔化的金属,在 高压作用下,以高速 填充至模具型腔内, 并使金属在此压力下 凝固而形成铸件的一 种方法。高压、高速 是压铸法与其他铸造 方法的根本区别,也 是最重要的特点。
压铸生产过程
• 以8G13为例
Home
模具冷却水检查
在装模具冷却水及接班时,不光 要检查冷却水管有无漏水,还要 检查模芯、模芯与模框之间、浇 口套、浇口套与模框之间有无漏 水,如发现有漏水,应及时上报;
Home
喷涂
• 喷涂后吹气
现车间有很多员工认为:模具温度这么高,喷的脱模剂到模具上 很快就蒸发掉了,不用吹气了,其实这种观点是不对的,喷涂后 吹气目的,是减少多余的脱模剂留在模具型腔内,也就减少模具 型腔内脱模剂挥发而产生的气体。
压力铸造培训资料之了解认识压铸
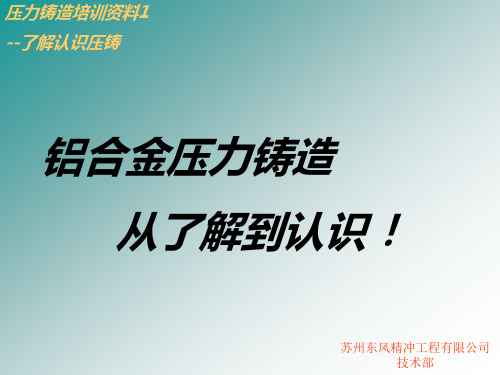
功能作用 存储油压能量为快速压射、 增压提供瞬间能量 挤压压射缸内的液压油,放 大其压力
推动压射杆前进进行压射动作
冲头
压射杆
压射油缸 增压油缸
压射机构
连接压射缸及冲头 推动铝液充填模具型腔 承装铝液
2.2 压铸机
2.2.3 液压系统示意图
2.3 压铸模具
2.3.1 压铸模具的作用
压铸模具是压铸生产过程的重要工装,他对生产节拍,压铸件质量起着极为重要 的作用,它与压铸工艺、生产操作即相互影响有相互制约,关系极为密切。压铸行业 内有个说法是“模具占60%、工艺占30%、人为操作占10%”,由此而知压铸的效益好 坏,关键在于模具质素的高低。 模具的重要作用是: (1)决定了压铸件的形状及尺寸公差等级。 (2)浇注系统决定了铝液在模具的填充状态。 (3)控制和调节压铸过程的热平衡。 (4)模具的强度及技术参数限定了压射比压的最大值。 (5)影响着压铸的生产效率。
高速 将熔杯内堆积到浇口 处的铝液压入模具型 腔。
高速的速度(冲头速度)一 般为2.5m/s~4.5m/s,速度 太慢了容易产生冷隔、产品 发黑等外观不良,速度太快 容易将模具型腔内的空气卷 入产品同时铝液对模具冲刷 严重。
增压 使铝液在高压力下凝固。
增压力(铝液承受压力)一般为 40Mpa—120Mpa,压力太高对设 备、模具冲击大,压力太小产品 内部组织不致密。
1.1 压铸的特点
1.1.3 铝压铸产品特点
铝压铸产品优点
可直接成型薄壁复杂的产品。
铝压铸产品 有什么特色 呢?
1.产品质量好:压铸件尺寸精度高;表面光洁度好;强度和硬度较高;尺寸稳定,互换性好;
2.生产效率高:机器生产效率高,卧室冷室压铸机(2000ton)铝合金汽车变速箱一天可生产
压铸培训资料

压铸培训资料xx年xx月xx日•压铸基础•压铸材料•压铸模具目录•压铸工艺•压铸缺陷及排除•压铸生产安全01压铸基础压铸是一种精密金属铸造方法,主要利用金属模具在高压下将熔融合金液倒入模具中,快速凝固成型。
压铸适用于大批量生产各种形状复杂、精密的金属零件,广泛应用于汽车、机械、电器、航空、仪器等领域。
压铸过程中,高压注射入金属模具内的熔融合金液在高压作用下快速充型并凝固,形成所需形状和尺寸的金属零件。
高压注射能够使熔融合金液在很短的时间内填满模具的各个角落,提高生产效率,降低废品率,生产出质量更好的产品。
压铸机的基本结构压铸机主要分为合模装置、注射装置、模具安装装置和液压系统等部分。
合模装置用于锁紧和开启模具,注射装置用于将熔融合金液注入模具,模具安装装置用于安装和固定模具,液压系统则提供动力。
各部分相互配合,协同工作,实现压铸过程的自动化和连续化。
02压铸材料铝合金流动性好,收缩率小,易于形成完整的铸件。
铸造性能优良强度和硬度较高广泛应用环保节能具有较好的力学性能,可满足各类压铸需求。
在汽车、航空航天、电子产品等领域得到广泛应用。
可回收再利用,符合绿色制造发展趋势。
易于进行熔炼、浇注、压铸等工艺操作。
良好的加工性能具有较好的力学性能,可满足各类压铸需求。
高强度和硬度成本较低,可降低生产成本。
经济实用在建筑、装饰、家具等领域得到广泛应用。
广泛应用强度和硬度较高具有较好的力学性能,可满足各类压铸需求。
重量轻密度较低,是铝合金的一半。
良好的铸造性能流动性好,易于形成完整的铸件。
广泛应用在汽车、航空航天、电子产品等领域得到广泛应用。
经济实用成本较低,可降低生产成本。
03压铸模具浇道是连接压铸机喷嘴和模具型腔之间的通道,其结构直接影响金属液的填充和成型效果。
模具结构浇道型腔是模具中直接成型工件的部分,通常由多块镶件组合而成,需要具有足够的强度和耐磨性。
型腔成型零件包括型芯、型腔和镶件等,直接影响工件的形状、尺寸和表面质量。
压铸安全培训资料
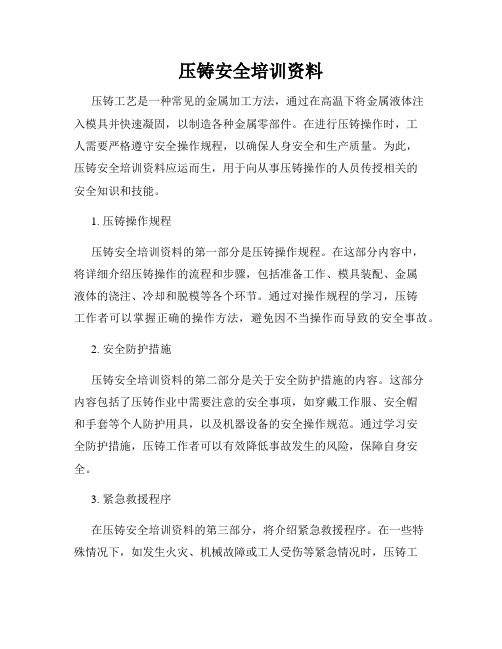
压铸安全培训资料压铸工艺是一种常见的金属加工方法,通过在高温下将金属液体注入模具并快速凝固,以制造各种金属零部件。
在进行压铸操作时,工人需要严格遵守安全操作规程,以确保人身安全和生产质量。
为此,压铸安全培训资料应运而生,用于向从事压铸操作的人员传授相关的安全知识和技能。
1. 压铸操作规程压铸安全培训资料的第一部分是压铸操作规程。
在这部分内容中,将详细介绍压铸操作的流程和步骤,包括准备工作、模具装配、金属液体的浇注、冷却和脱模等各个环节。
通过对操作规程的学习,压铸工作者可以掌握正确的操作方法,避免因不当操作而导致的安全事故。
2. 安全防护措施压铸安全培训资料的第二部分是关于安全防护措施的内容。
这部分内容包括了压铸作业中需要注意的安全事项,如穿戴工作服、安全帽和手套等个人防护用具,以及机器设备的安全操作规范。
通过学习安全防护措施,压铸工作者可以有效降低事故发生的风险,保障自身安全。
3. 紧急救援程序在压铸安全培训资料的第三部分,将介绍紧急救援程序。
在一些特殊情况下,如发生火灾、机械故障或工人受伤等紧急情况时,压铸工作者需要迅速采取应对措施,减少损失。
通过学习紧急救援程序,工作者可以在关键时刻做出正确的决策,确保人身安全。
4. 安全知识考核最后一部分是关于安全知识考核的内容。
在接受完压铸安全培训后,工作者需要进行安全知识考核,以检验其对安全规程和操作要求的掌握程度。
通过考核结果,可以评估工作者的安全水平,并及时提出改进意见和培训计划,以进一步提升工作人员的安全意识。
总结压铸安全培训资料对于保障压铸工作者的安全和生产质量具有重要作用。
通过学习相关的安全知识和技能,工作者可以避免事故的发生,提高工作效率,保障生产和人身安全。
希望所有从事压铸操作的人员能够严格遵守安全规程,不断提升安全意识,共同营造一个安全的工作环境。
铝合金压铸培训资料

铝合金压铸培训资料铝合金压铸是一种常见的金属成型工艺,广泛应用于汽车、航空航天、电子等领域。
本文将介绍铝合金压铸的基本原理、工艺流程以及注意事项。
一、铝合金压铸基本原理铝合金压铸是指将熔化的铝合金注入压铸机的模具中,在高压下冷却固化成型的工艺。
其基本原理是利用压铸机的合模装置将熔化的铝合金注入模具中,通过高压力将铝液充满整个模腔,并在冷却过程中产生固化缩胀,最终得到所需的铝合金零件。
二、铝合金压铸工艺流程1. 模具准备:选择合适的压铸机和模具,根据产品设计要求制作模具,并进行必要的模具调试。
2. 材料准备:选择适合的铝合金材料,并按照配比准备好所需的铝合金料。
同时,将冷却水和切削液配置好。
3. 熔炼铝合金:将铝合金料加热熔化,控制好熔化温度和熔化时间,确保熔化的铝合金质量符合要求。
4. 注铸:将熔化的铝合金通过喷杆注入模具中,控制注铸时间和注铸速度,使得铝液充分填充整个模腔。
5. 冷却固化:铝液在注铸过程中受到冷却水的冷却,逐渐固化成型。
冷却固化时间根据具体工艺要求进行控制。
6. 脱模:经过冷却固化后的铝合金零件从模具中取出,注意避免零件变形或损坏。
7. 修整:对脱模后的铝合金零件进行去毛刺、抛光、修整等工艺处理,使其达到产品要求的表面粗糙度和尺寸精度。
8. 检验:对修整后的铝合金零件进行质量检验,包括外观检查、尺寸测量、力学性能测试等项目。
9. 表面处理:根据产品要求进行表面处理,如喷涂、氧化、电泳等工艺,提高零件的耐腐蚀性和美观度。
10. 包装出货:对完成质量检验合格的铝合金零件进行包装,并按照客户要求进行出货。
三、铝合金压铸注意事项1. 模具选择:根据产品设计要求选择合适的模具材料和结构,确保模具的强度和寿命。
2. 材料选择:根据产品性能要求选择合适的铝合金材料,避免因材料不合适导致的缺陷和失效。
3. 工艺参数控制:控制好注铸温度、注铸速度、冷却水温度等工艺参数,确保铝液充分填充模腔并冷却固化。
压铸工艺流程学习培训资料

压铸工艺流程学习培训资料压铸工艺是利用压力将熔化的金属注入到模具中,并在模具内冷却、固化后取出铸件的一种制造工艺。
下面将介绍压铸工艺流程的学习培训资料。
一、压铸工艺流程概述1.材料准备:选择适合的铸造材料,一般选择具有良好流动性和机械性能的合金材料。
2.模具设计与制作:根据铸件的形状、尺寸和要求设计模具,并制作模具。
3.熔炼金属:根据所选材料的配方,将原料熔炼成铸造合金。
4.模具装配与预热:将熔炼好的铸造合金注入模具,并在高温条件下预热模具。
5.压力注射:将预热好的模具放入压铸机中,通过压力将熔化的金属注入到模具中。
6.冷却固化:待金属快速冷却后,取出铸件,进行冷却固化处理。
7.修磨、表面处理:对铸件进行修磨、抛光等处理,以达到所需的外观要求。
8.检验与包装:对铸件进行质量检验,并进行包装。
二、压铸工艺流程中的关键环节1.材料准备:合理选择材料,包括铸造合金的成分、配比、物理性能等。
2.模具设计与制作:模具的设计应考虑到铸件的形状、尺寸和结构要求,制作时应保证模具的精度和寿命。
3.熔炼金属:熔炼金属时应控制好熔炼温度、时间和炉内气氛,确保金属的成分和纯度。
4.模具装配与预热:模具的装配应严密,预热时应注意温度和时间的控制,避免模具变形和热裂纹。
5.压力注射:压铸机的操作要熟练,注射压力和速度要适当,保证铸件的密实度和表面质量。
6.冷却固化:冷却固化时间应根据材料的特性和铸件的尺寸来确定,确保铸件的冷却充分。
7.修磨、表面处理:修磨和表面处理要注意控制切削量和保持铸件的形状和尺寸。
8.检验与包装:对铸件进行质量检验,包括外观质量、尺寸精度、机械性能等,确保符合要求后进行包装。
三、压铸工艺流程中的常见问题与解决方法1.模具寿命不长:可以增加模具材料的硬度、改善冷却系统、调整注射参数等方法来延长模具寿命。
2.铸件表面质量差:可以调整注射压力和速度、改善冷却系统、加强模具维护等方法来改善铸件表面质量。
3.铸件尺寸偏差大:可以优化模具结构、改变注射和固化工艺、加强模具维护等方法来控制铸件尺寸。
压铸工艺及压铸新技术资料

3 压铸工艺及压铸新技术3.1 压铸合金要生产优质的压铸件,除了要有合理的铸件结构、设计和制造完善的压铸模以及工艺性能优越的压铸机外,还需要有性能良好的压铸材料。
除了制造电动机转子是用纯铝环绕叠片进行压铸外,其他压铸件都是用合金制成的。
与纯金属(单金属)相比,合金的强度要高一些。
3.1.1 对压铸合金的要求为了满足压铸件的使用要求,保证压铸件的质量,压铸合金应符合如下要求:(1)密度小,导电和导热性好。
(2) 强度和硬度高,塑性好。
(3) 性能稳定,耐磨和抗腐蚀性好。
(4) 熔点低,不易吸气和氧化。
(5) 收缩率小,产生热裂、冷裂和变形的倾向小。
(6) 流动性好,结晶温度范围小,产生气孔、缩松的倾向小。
一种合金是否适合于压铸,取决于它的熔点和流动性。
对任何合金系列而言,都是以共晶合金或者结晶温度范围小的合金具有最好的流动性,而结晶温度范围大的合金压铸性能差。
熔点高的合金都难于压铸。
3.1.2 常用压铸合金及其主要特性压铸用合金的分类见表3-l。
表3-l 压铸用合金分类目前最常用的压铸合金有铝合金、锌合金、镁合金、铜合金,其主要特性见表3仑。
我国常用压铸合金的化学成分、力学性能及应用范围见表35~表3l。
表3-2 常用压铸合全的主要特性3.1.3 压铸合金的选用合理地选择压铸合金是压铸件设计工作中的重要环节之一。
不同种类的压铸合金,其性能各有差异。
设计人员在选择压铸合金时,不仅要考虑所要求的使用性能,而且对压铸合金的工艺性能也要给予足够的重视,在满足使用性能的前提下,尽可能多考虑工艺性能优良的压铸合金。
压铸合金的性能包括使用性能和工艺性能两方面厂其项目与内容见表3-11.选择压铸合金应考虑的因素见表3-12。
3.2 压铸件的结构设计压铸件的设计是压铸生产技术中首先遇到的工作。
合理的压铸件结构不仅能简化压铸模的结构,降低制造成本,同时也能改善压铸件质量。
3.2.1 压铸工艺对压铸件结构设计的要求压铸生产技术上所遇到的种种问题,如分型面的选择、浇口的开设、顶出的布置、收缩规律的掌握、精度的保证、缺陷的种类及其程度等,都是以所压铸的零件本身的工艺性的优劣为前提的。
压铸机培训资料

压铸机培训资料压铸机培训资料(一)压铸机是一种应用广泛的加工设备,主要用于将液态金属注入模具中,经过加压和冷却后形成所需的铸件。
压铸机的操作需要掌握一定的技术和知识,下面我们将介绍一些压铸机的基本原理和操作技巧,以供大家参考。
一、压铸机的基本原理压铸机是利用液态金属在高压下通过注射装置进入模腔,经过冷却和固化后形成铸件的工艺过程。
其基本原理可分为以下几个环节:1. 模具装配:首先需要将压铸模具装配好,包括模具座和上下模板等部件。
确保模具装配准确、紧固可靠。
2. 铸料注入:将熔融的金属注入到注射装置中,通过加压将金属推入模腔中。
注入过程需要控制注射速度和注射压力,以确保铸件的质量。
3. 冷却固化:注入模腔中的金属将在模具中迅速冷却和固化,形成所需的铸件。
冷却时间和温度的控制非常重要,过长或过短的冷却时间都会影响铸件的质量。
4. 压力释放:当铸件冷却固化后,需要释放注射装置的压力,打开模具,取出铸件。
释放压力的过程需要谨慎,避免因压力过大而对模具或铸件造成损坏。
二、压铸机的操作技巧压铸机的操作需要掌握一定的技巧,下面我们介绍几点操作要点:1. 安全操作:压铸机是一种涉及高温和高压的设备,操作时务必注意安全。
使用必须严格按照操作规程进行,避免发生意外。
2. 模具装配:在装配模具时,要保证模腔的准确配合,确保上下模板垂直、紧固可靠。
可以在装配前使用轻微的润滑油,以提高模具的使用寿命和降低摩擦。
3. 注塑条件:注射装置的注塑条件需根据不同的铸件材料和形状进行调整。
应注意控制注射速度、注射压力和温度,以确保注塑过程的质量。
4. 冷却控制:冷却时间和温度对铸件的质量有重要影响。
应根据不同材料和形状的铸件调整冷却时间和温度,确保铸件冷却完全、固化良好。
5. 压力释放:在释放注射装置的压力时,要避免过快或过慢,以免产生冲击或卡死的情况。
应注意逐渐释放压力,并确保模具和铸件的安全。
以上是关于压铸机的基本原理和操作技巧的介绍,希望能对大家有所帮助。
压铸工艺参数表

压铸工艺参数表
摘要:
1.压铸工艺参数表的概述
2.压铸工艺参数表的分类
3.压铸工艺参数表的具体内容
4.压铸工艺参数表的应用领域
5.压铸工艺参数表的意义和作用
正文:
压铸工艺参数表是对压铸工艺过程中各项参数进行详细记录和整理的表格,对于保证压铸件质量和提高生产效率具有重要意义。
压铸工艺参数表主要分为以下几类:首先是模具参数,包括模具的尺寸、形状、材料等;其次是压铸机参数,包括压铸机的型号、吨位、压力等;再次是熔炼参数,包括熔炼炉的类型、温度、时间等;此外还有其他辅助参数,如喷涂、冷却、检测等。
具体的压铸工艺参数表内容可能因不同的压铸件和生产工艺而有所差异,但大体上都包含以上几类参数。
压铸工艺参数表广泛应用于压铸生产的各个环节,从模具设计、压铸机选型,到熔炼、压铸、后处理等,都需要参考和依据压铸工艺参数表来进行。
压铸安全培训资料

压铸安全培训资料压铸是一种常用的金属加工技术,广泛应用于汽车、航空、电子等领域。
然而,由于压铸过程中可能涉及高温、高压以及有害气体等安全风险,因此对于压铸操作人员来说,安全意识和知识的培训至关重要。
本文将介绍一些关键的压铸安全知识和培训内容,以确保压铸操作的安全性和可靠性。
一、压铸安全背景在进行压铸操作之前,了解一些相关的压铸安全背景是非常重要的。
首先,压铸过程可能会产生高温和高压,因此操作人员应该做好防护措施,避免烫伤或受压伤。
其次,压铸过程中可能会有金属溅射或飞溅的风险,因此戴上护目镜和防护面罩也是必要的。
此外,一些有害气体和废弃物也需要正确处理,以确保工作环境的安全和卫生。
二、压铸安全培训内容1. 压铸设备操作培训首先,操作人员应该接受基本的压铸设备操作培训。
这包括了解压铸设备的功能、控制面板和操作流程。
操作人员需要熟悉如何启动和关闭设备、调整参数以及处理常见故障。
此外,他们还应该了解设备的安全装置和紧急停机按钮的使用方法。
2. 安全防护措施培训操作人员在进行压铸作业时应该始终佩戴适当的个人防护装备。
这包括穿戴耐高温服、戴上安全帽、护目镜、防护手套和防护鞋。
培训中应重点强调正确佩戴和使用这些防护装备的方法,以确保安全性和舒适度。
3. 紧急情况处理培训在培训中,操作人员应该学习如何应对可能发生的紧急情况,例如设备故障、金属飞溅、火灾等。
他们需要熟悉紧急停机按钮的位置和使用方法,以及逃生通道和灭火器的位置。
通过模拟演练和案例分析,操作人员将能够更好地应对压铸作业中的紧急情况。
4. 有害物质处理培训在压铸过程中,可能会产生一些有害物质和废弃物,如有害气体和废水。
操作人员需要了解有关这些物质的性质、处理方法和安全要求。
培训应包括正确使用通风系统、处理废弃物和进行个人清洁卫生的方法。
三、培训评估和持续改进进行压铸安全培训后,评估培训成果的效果至关重要。
通过答题、模拟演练和现场观察等方式,可以对操作人员的知识和技能进行评估。
压铸车间培训资料

改变内浇口厚度与铸件厚度之比,除了影响填充的速度和时间外,也
影响金属液在型腔内的流态。
3.2内浇口开在型腔一侧的流态
金属液沿侧壁填充向前,到达顶端后包围,聚集,向反方向填充,聚
集处有旋涡包气。
3.3薄壁型腔填充流态
金属流的厚度接近型腔的厚度,金属流入是的飘动,与型腔一侧或两侧
相接触。
压铸车间培训资料
举例: JI213型--------表示250KN的自动热室卧式压铸机
JI25B型--------表示为2500KN第二次改型的卧式冷室压铸机
压铸车间培训资料
4.3压铸造的参数规格 部标JB2590-75规定,热室压铸机有9种规格,合于是力从100KN到10000KN,冷
室卧式压铸机有11种规格,合型力从250KN到35000KN,压铸机的基本参数有:合型 力、压射力、压型厚度(最小、最大)动型板行程、拉杠内间距水平×垂直、顶出 力、顶出行程、压射位置,一次金属浇入量、压室直径、空循环周期。 4.4热室内压铸机与冷室压铸机比较
2、金属填充型腔的流态 介绍三种填充理论 2.1喷射填充 填充分二个阶段:冲击阶段和涡流阶段 冲击阶段:在速度,压力保持不变的前提下,金属液 进入内浇口后,仍保持 着内浇口的截面形状,冲击到正对面的型壁处. 涡流阶段:向着内浇口反向填充 这种理论比较适用于薄壁内浇口,高速填充的长方形铸件 2.2全壁厚填充理论 由德国学者在1937年提出,内浇口厚度值取0.5~2mm, 内浇口与铸件的厚度 比值为f/F在0.1~0.6范围内. 这种理论认: 金属液通过内浇口进入型腔后,即扩张到型壁,然后沿着整 个型腔截面向前填充,直到整个型腔充满为止.
入到镁液中去。目前普遍采用气体保护方式保护容了。保护气体以SF6 +N2 的混合气
压铸QC培训资料汇总

• 五、压铸机的检查:和样办比较是否有变形、 缺料、花纹大、气孔、合金泡、油泡等现象 孔径的量度 试装 整理批锋 抛光 洗水 整形打配套 出货之下 工序
人有了知识,就会具备各种分析能力, 明辨是非的能力。 所以我们要勤恳读书,广泛阅读, 古人说“书中自有黄金屋。 ”通过阅读科技书籍,我们能丰富知识, 培养逻辑思维能力; 通过阅读文学作品,我们能提高文学鉴赏水平, 培养文学情趣; 通过阅读报刊,我们能增长见识,扩大自己的知识面。 有许多书籍还能培养我们的道德情操, 给我们巨大的精神力量, 鼓舞我们前进。
压铸QC培训资料
一、金属压铸的原理 • 1、金属压铸是将熔融的液态金属注入压铸的 压室,通过压射冲头的运动,使液态金属在高 压作用下,高速能过模具浇注系统型腔,在压 力下结晶并迅速冷凝固形铸件: • 2、压铸过程环图: • 清理模具 关门 锁模 扣前 一速打料 二速打料 回锤 离咀 开模 顶针出 冲头下 喷雾
• • • •
③压铸成型效果好; ④啤件表面可镀金属; ⑤啤件易老化,抗腐拙性能差. 4、在合金原料中加入水口料可以降低成品, 在一定程度上降低了产品质量,如:水口料中 的杂质较多,导致啤件产生花纹和汽泡等手工 缺点,水口料中的铝铁等成份减少,锌合金的 一理化性能变坏,产品质量下降。
三、压铸机
• 1、压铸机的分类: • ①按压室浇注方式可分为:冷室压铸机和热室 压铸机; • ②按压室的结构布量方式可分为:卧式压室压 铸机和立式压室压铸机; • ③按功率可分:小型、中型、大型压铸机; • ④按自动化程度铸机的后室与熔炉 紧密的连成一个整体,压室浸在保坩埚的液体 金属中,而热室压铸机的后室和熔炉是分开的, 采用热室压铸机能缩短循环时间、提高设备生 产效率,容易实现自动化,减少金属消耗等。 • 四、影响压铸件质量的要求: • 1、压铸机的功能及其可靠性; • 2、压铸模的质量及其结构的合理性; • 3、合金材料的合金含量的超近质及其熔料温 度的稳妥性; • 4、压铸机的操作技术。
- 1、下载文档前请自行甄别文档内容的完整性,平台不提供额外的编辑、内容补充、找答案等附加服务。
- 2、"仅部分预览"的文档,不可在线预览部分如存在完整性等问题,可反馈申请退款(可完整预览的文档不适用该条件!)。
- 3、如文档侵犯您的权益,请联系客服反馈,我们会尽快为您处理(人工客服工作时间:9:00-18:30)。
低速速度压射的速度的第一阶段采用低速的目的是;让套筒内金属液不起浪,能顺畅地填充到套
筒内,同时将套筒内及浇道内的气体通过排气槽顺利排出。
关于压铸件含气量,有数据表明;好的铸造条
件下生产出来的产品;10_30cc/100g A1 不好的铸造条件下生产出来的产品;100-200
CC/100G A1 100GA1相当于37CC,气体被100%地封在成形部位也不过是37CC。
因此100-200CC就意味着套筒内的空气,套筒润滑剂的燃烧气体,水溶性脱模剂的蒸发气体站了含气量的大部分。
为了将这些气体有效排出要尽可能慢的速度静静地填充金属液。
但是在实际操作中,如果速度过慢会导致套筒内的金属液温度大幅下降,导致金属液流淌不畅。
如果速度过快,排气口的背压变大,排气困难另外套筒内金属液起浪,氧化物卷入,一部分从浇口喷出,造成次品。
为了避免金属液起浪,如何开启低速和加速也很重要。
另外套筒和冲头的配合状态非常重要。
综合这些因素,低速速度一般设定在0.1-0.3M/S
压射的第二阶段用高速的目的是可以获得表面光洁且内部缺陷少的优质产品,一最恰当的时间确保金属液注入到成形部位的每个角落。
因此以产品的壁厚为基础,有形成产品所需的最低高速速度。
这个速度可以参照表5-5-1的公式计算出。
实际操作时,在批量试验的阶段,以该值为基础,边确认产品的外观,边,尝试用更快的速度【1.5倍以内】,找出最佳速度作为大规模生产的条件。
高速速度如果过高会导致对模具的烧蚀,会大量出现飞边,过慢不但会造成金属液流淌不畅,影响外
观而且会增加内部缺陷。
大规模生产时一定要将批量试验时得出的最佳条件写入作业标准书严格,严格遵守
高速切换位置【高速距离】
高速切换位置是指将柱塞冲头从低速速度转换到高速速度的位置。
为了确定这个位置要计算保持高速速度的距离,即高速距离。
高速距离的计算公式在刚才的表5-5-1里。
考虑高速切换位置的思路是,先以低速速度将金属液填满至浇口处,将套筒内的空气等有效排出,然后再切换成高速制作出好的产品来。
作业标准书中的高速切换位置是指,为了压射结束位置开始高速距离段前为了启动高速切换阀门而设定的限位开关的位置。
如果想在现场确认高速位置是否正确,可以在压射结束时,测量限位开关的启动点到限位开关头部之间的距离就知道了。
准确的位置可以通过压射波形监视器确认。
用刚才的公式取-0﹢10㎜是考虑了浇注量的不一致及铸造方案的修改而设的一个余量。
批量试验的时候,边确认产品的美观程度和内部空洞的状况来确定最佳条件。
特殊情况下用比计算出的高速距离短的多的距离进行铸造反而能生产出缺陷较少的产品,这叫低速填充铸造。
但是应该采用高速距离的百分之几来进行低速填充没有理论依据,只能看现场的情况。
另外质量不稳定,原侧上不使用。
从切换到高速到达必要的高速速度之间的上升曲线是非常重要的因素,还很少有能够自由设定这种上升曲线的压铸机。
使用能够自由设定上升曲线的设备时,要用监视器确认达到必要的高速速度后到压射完成之间的压射波是否平坦,并加以调整。
参照5-6-1.。
增压是指在压射结束后,在极短的时间内{MS设定条件}对稿速压射的终压力施以约2倍的高压【500-1500㎏∕㎝】。
因此不是指压力值在多少以上而是指通过什么装置有效地将压力增加到比高速终压还高,起到增压的效果。
最终铸造压力是指不管有无增压,压射完成后大约0.3秒以后的压力。
一般有效增压提高最终铸造压力的目的是金属液将填充成形部位后快凝固的凝固收缩部分的金属液强行挤入以防止,所谓的凹陷,同时将成形部位没有排除干净的残留的气孔及销孔用高压进行缩压使其变小。
为了达到这两个目的,最终压力越高效果越好,但是最终压力越高能铸造的投影面积就越小。
因此需要更大的铸造机和强度更大的模具,带来经济上的问题,所以500-800㎏∕㎝的范围就足够了。
为了充分利用增压效果,高速填充完成后上升到最终压力的时间即增压上升时间非常重要。
理论上从凝固开始到凝固结束都要保持增压状态。
如果过早会出现飞边喷溅,如果太晚浇口凝固,就无法给成形部位的金属液补给和增压。
现实生产中压铸机一般将增压上升时间定在10-30MS的程度为好。
增压装置因压铸机厂家而异。
东芝和东洋的机器只要读压射缸的压力计就能看出增压有效和无效时压力的差别,但是宇部的机器增压无效的情况下液压油供给侧的压力和吐出侧的压力一样,这个吐出侧的压力叫背压,背压为0时就是100%增压,吐出侧的压力在0以上,供给侧在压力以下时就是增压有效的百分比。
终压达到多少看机器的使用说明书就明白。
在铸造现场偶尔会看到每次压射都有飞边喷出的情况,这是因为铸造面积过大。
飞边喷出时要立即确认铸造面积,用以下的公式计算允许的压力值
允许压力值㎏∕C㎡=锁模力㎏×0。
9∕铸造面积C㎡
计算值小于机器使用说明书上计算出的终压力时要将机器调整到计算以下的终压。
反过来计算值大于机器使用说明书的上计算出的终压力,却有飞边喷出。
一般是模具有问题,要再次确认合模情况。
林红军2010-3-20。