化学蚀刻二层板操作流程
蚀刻生产的流程与工艺
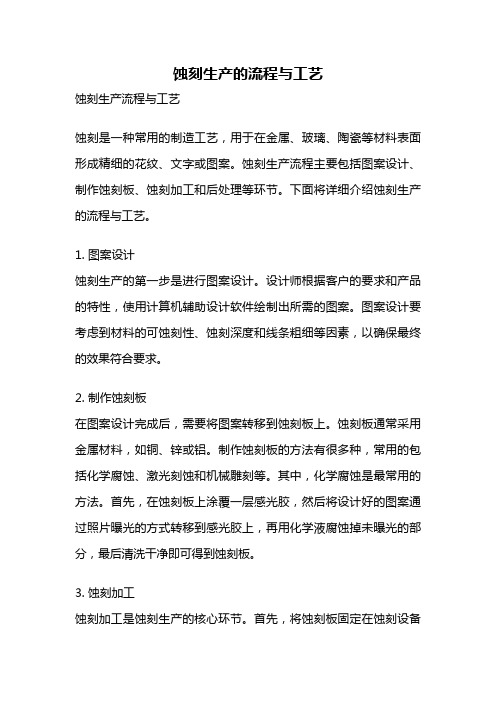
蚀刻生产的流程与工艺蚀刻生产流程与工艺蚀刻是一种常用的制造工艺,用于在金属、玻璃、陶瓷等材料表面形成精细的花纹、文字或图案。
蚀刻生产流程主要包括图案设计、制作蚀刻板、蚀刻加工和后处理等环节。
下面将详细介绍蚀刻生产的流程与工艺。
1. 图案设计蚀刻生产的第一步是进行图案设计。
设计师根据客户的要求和产品的特性,使用计算机辅助设计软件绘制出所需的图案。
图案设计要考虑到材料的可蚀刻性、蚀刻深度和线条粗细等因素,以确保最终的效果符合要求。
2. 制作蚀刻板在图案设计完成后,需要将图案转移到蚀刻板上。
蚀刻板通常采用金属材料,如铜、锌或铝。
制作蚀刻板的方法有很多种,常用的包括化学腐蚀、激光刻蚀和机械雕刻等。
其中,化学腐蚀是最常用的方法。
首先,在蚀刻板上涂覆一层感光胶,然后将设计好的图案通过照片曝光的方式转移到感光胶上,再用化学液腐蚀掉未曝光的部分,最后清洗干净即可得到蚀刻板。
3. 蚀刻加工蚀刻加工是蚀刻生产的核心环节。
首先,将蚀刻板固定在蚀刻设备上,并调整好刀具的位置和深度。
然后,将工件放置在蚀刻设备的工作台上,并固定好。
接下来,通过控制蚀刻设备的移动和刀具的进给,使刀具按照预定的路径在工件表面进行切削,形成所需的图案。
蚀刻加工时间的长短取决于蚀刻深度和图案的复杂程度。
4. 后处理蚀刻加工完成后,需要进行后处理以提高产品的质量和美观度。
后处理的方法有很多种,常用的包括去除蚀刻残渣、打磨、抛光和防锈等。
首先,使用化学溶液或机械方法去除蚀刻残渣,使产品表面平整光滑。
然后,对产品进行打磨和抛光,以提高光泽度和触感。
最后,对产品进行防锈处理,延长其使用寿命。
总结起来,蚀刻生产流程与工艺主要包括图案设计、制作蚀刻板、蚀刻加工和后处理等环节。
通过精细的设计和加工,蚀刻生产可以在各种材料上实现精美的图案和文字,广泛应用于工艺品、装饰品和标识等领域。
随着科技的进步,蚀刻技术也在不断发展,使得蚀刻生产更加高效、精确和多样化,满足了人们对个性化和独特性的需求。
玻璃表面化学深蚀刻的工艺原理与操作方案
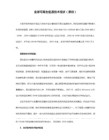
解决方案: a: 试加10%络合剂 b: 试加8%氧化剂 c: 试加30%络合剂及18%氧化剂。
5: 深度和冰棱都理想,就是凹面不亮?
解决方案: 对全量加入12%—25%缓冲剂并适量延长蚀刻时间约30—50min即可。
6: 环境气味太重可添加FC129, 对全量加入0.03—0.05%。
6: 冬天化学蒙砂的反应速度太慢的解决方案是在池液中适量添加55%HF与氧化剂即可大大提快蒙砂速度,平置琳砂法的解决方案是在平池上端安装数个浴霸红外线灯泡,使被淋砂物质有温度提升,导至蒙砂时间提速, 提高产效.
7: 夏天蒙砂后的玻璃板面易出现象泪痕似的花道, 解决方案例如改变蒙砂粉配比结构, 不用H2SO4而选用31%HCL, 这个原理是可大大减缓蒙砂速度, 导至不易产生二次水道性再蚀刻。
事隔月把,我为所里试制出第一桶丝网型可剥离拷贝油墨,为此全所上下还开了个茶杯表彰会,会上我快活地龇牙咧嘴一个劲嘿嘿嘿……也许是受神经质感染,大伙会也都呵呵呵……嘿嘿嘿……嘿嘿喷了水的刘好被揪着耳朵乱嚼妈呀哎呀…….闭会后财会老杨给了我一个信封,里头妈哎齐唰唰三张崭新一百的…呵呵呵……有意思……倒赚150…
说巧成书就此将黄金凹蒙加工技术献给<<艺术玻璃>>的读者您:
具体操程序如下:
1. 准备材料如下:a凹蒙玻璃,b空白丝网c丝网网刮d较宽幅单面胶带e空气喷枪f玻璃色漆g 拷贝油墨
2. 用空白丝网将拷贝油墨印刷在凹蒙玻璃背面上,
3. 自然干燥大约30---50分钟,
4. 用空气喷枪将有色的玻璃漆均匀喷涂到干燥的拷贝油墨面上,
1:无论平置淋砂法或垂直浸泡法,在蒙砂之前必须将玻璃制品进行彻底脱脂清洗,并视工艺状态,决定是否用水喷枪对已脱脂的玻璃表面再度冲淋, 方向可由上至下往复操作,
化学蚀刻技术课件

无误。
穿戴防护用品
02
操作人员必须穿戴防护眼镜、实验服、化学防护手套等防护用
品,防止化学试剂溅到身上。
保持通风
03
在操作过程中,要保持实验室通风良好,避免有害气体在室内
积聚。
废液处理与环保要求
废液分类处理
根据废液的性质和成分,将其进行分类存放和处理,避免混合后 产生有毒有害气体或发生危险。
废液回收利用
蚀刻处理
选择合适的蚀刻液
根据基材的特性和工艺要 求选择合适的蚀刻液,确 保其具有较高的蚀刻速率 和选择性。
控制蚀刻条件
控制蚀刻液的浓度、温度、 PH值等条件,以确保蚀刻 过程的稳定性和精度。
蚀刻方式
采用浸泡、喷淋、刷涂等 方式进行蚀刻处理,确保 基材表面被均匀蚀刻。
去胶与清洗
去胶
去除抗蚀剂掩膜,将其彻底清洗干净,以便后续处理。
化学蚀刻技术课件
• 化学蚀刻技术概述 • 化学蚀刻技术的基本原理 • 化学蚀刻技术的工艺流程 • 化学蚀刻技术的材料选择 • 化学蚀刻技术的质量控制 • 化学蚀刻技术的安全与环保
01
化学蚀刻技术概述
定义与特点
定义
化学蚀刻技术是一种利 用化学反应将材料进行 选择性溶解或去除的工
艺过程。
高精度
能够实现高精度的图形 转移,满足微细加工的
总结词:性能测试
详细描述:在化学蚀刻过程中,抗蚀 剂的性能至关重要。通过性能测试, 如耐酸性、耐碱性、耐温度性等,可 以评估抗蚀剂的适用性和稳定性。
抗蚀剂的性能检测与控制
总结词:成分分析
VS
详细描述:对抗蚀剂进行成分分析, 了解其化学成分和浓度,有助于优化 配方和工艺参数。同时,成分分析还 可以及时发现潜在的问题和失效模式。
FPC生产流程(全流程)

1、简述 pcb 双面板和多层板生产流程。

【主题】:PCB双面板和多层板生产流程一、引言PCB(Printed Circuit Board,印刷电路板)是现代电子产品中不可或缺的一部分,它承载着电子元器件并提供电气连接。
在不同的电子产品中,我们经常会听到双面板和多层板的概念。
那么,它们的生产流程究竟是怎样的呢?二、双面板生产流程1. 设计与布局:双面板的生产流程首先要进行电路设计和布局,包括元件布局和线路走向的设计。
2. 制作内层板:将玻璃纤维布浸渍树脂,然后在铜箔上覆盖光敏胶,通过曝光、显影、蚀刻等步骤形成线路和铜箔残留的区域。
3. 复板:将内层板与预制好的介质层板及铜箔层板复合,并通过热压技术将其加以固化。
4. 外层图形化:在外层板铜箔表面上覆盖一层光敏胶,然后按照设计图形进行曝光、显影、蚀刻,形成外层线路及铜箔残留的区域。
5. 孔位铆合:利用机械或激光技术在板面上打孔(冲压孔位)。
6. 表面化学镀镍金:对板面进行化学镍金处理,以增强其与焊盘的附着力。
7. 色素沉积:在板面上形成阻焊油墨或者焊盘油墨图形。
8. 表面喷镘:将表面喷上喷锡层,构成铅(锡)粘接的表面。
三、多层板生产流程1. 设计与布局:多层板的设计和布局要比双面板更为复杂,需要考虑多层板间的互连关系和信号传输。
2. 制作内层板:多层板同样需要制作内层板,但在此之前需要将设计好的电路图分层布局,并使用铜箔、介质等材料进行层压。
3. 复合与预压:通过预压机将内层板与预制好的介质层板及铜箔层板复合,并进行热压处理。
4. 钻孔:利用高精度数控钻孔机对多层板进行钻孔处理,确保孔位的精确性。
5. 表面处理:在板面进行化学镀铜处理,以增强其导电性。
6. 外层图形化:进行外层线路的图形化处理,包括曝光、显影、蚀刻等步骤。
7. 色素沉积:形成阻焊油墨或者焊盘油墨图形。
8. 表面处理:喷镘或者喷锡等表面处理工艺,以增强焊盘的焊接性能。
四、总结从以上的生产流程可以看出,双面板和多层板的生产流程都是需要经过多道工艺步骤的复杂过程。
pcb蚀刻工艺流程
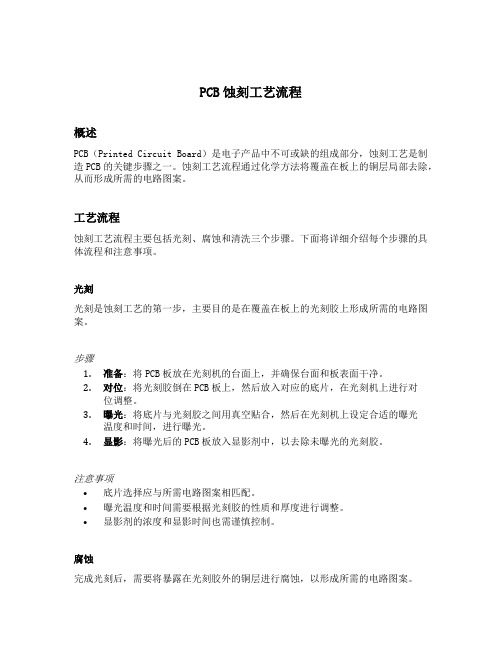
PCB蚀刻工艺流程概述PCB(Printed Circuit Board)是电子产品中不可或缺的组成部分,蚀刻工艺是制造PCB的关键步骤之一。
蚀刻工艺流程通过化学方法将覆盖在板上的铜层局部去除,从而形成所需的电路图案。
工艺流程蚀刻工艺流程主要包括光刻、腐蚀和清洗三个步骤。
下面将详细介绍每个步骤的具体流程和注意事项。
光刻光刻是蚀刻工艺的第一步,主要目的是在覆盖在板上的光刻胶上形成所需的电路图案。
步骤1.准备:将PCB板放在光刻机的台面上,并确保台面和板表面干净。
2.对位:将光刻胶倒在PCB板上,然后放入对应的底片,在光刻机上进行对位调整。
3.曝光:将底片与光刻胶之间用真空贴合,然后在光刻机上设定合适的曝光温度和时间,进行曝光。
4.显影:将曝光后的PCB板放入显影剂中,以去除未曝光的光刻胶。
注意事项•底片选择应与所需电路图案相匹配。
•曝光温度和时间需要根据光刻胶的性质和厚度进行调整。
•显影剂的浓度和显影时间也需谨慎控制。
腐蚀完成光刻后,需要将暴露在光刻胶外的铜层进行腐蚀,以形成所需的电路图案。
步骤1.准备:将光刻胶去除,并确保PCB板表面干净。
2.腐蚀:将PCB板放入腐蚀槽中,并注入蚀刻剂,观察腐蚀过程。
3.停止腐蚀:当所需电路图案的铜层已被完全腐蚀后,及时将PCB板从腐蚀槽中取出并进行下一步处理。
注意事项•腐蚀剂的选择应根据所需腐蚀速度和安全性进行合理选取。
•腐蚀时间的控制需要根据腐蚀剂的性质和腐蚀速度进行调整。
•腐蚀过程中需保持腐蚀剂的温度恒定。
清洗蚀刻后,PCB板上可能残留有光刻胶、腐蚀剂等污染物,因此需要进行清洗以确保电路质量和可靠性。
步骤1.去除光刻胶:将PCB板放入光刻胶去胶剂中,浸泡一段时间后,用刷子轻轻刷洗,直至光刻胶完全去除。
2.清洗腐蚀剂:将PCB板放入清洗槽中,注入清洗液,进行循环清洗。
3.漂洗和烘干:用纯净水对PCB板进行漂洗,然后将其放入烘干机中进行烘干。
注意事项•清洗剂的选择应兼顾去除能力和安全性。
蚀刻操作注意事项

蚀刻操作注意事项
1.安全防护:蚀刻操作涉及到化学物质,应穿戴化学防护服、口罩和手套等防护用品。
2.作业环境:蚀刻操作应在通风良好的环境下进行,以尽量减少对人体健康的影响。
3.化学品的储存:蚀刻操作需要使用各种化学品,化学品应当储存在专用的化学品柜中,以防止引起烟雾或泄漏。
4.调配蚀刻液:蚀刻液是根据具体的需要调配,应用量不宜过量,否则会导致化学反应过于剧烈,产生不良影响。
5.处理废液:蚀刻过程中会产生废液,应按照规定处理,避免废液污染环境。
6.设备维护:蚀刻设备需要定期保养和保洁,以维护设备的稳定性和使用寿命。
PCB电路板蚀刻工艺及过程控制 - 电子技术

PCB电路板蚀刻工艺及过程控制 - 电子技术印刷线路板从光板到显出线路图形的过程是一个比较复杂的物理和化学反应的过程,本文就对其最后的一步--蚀刻进行解析。
目前,印刷电路板(PCB)加工的典型工艺采用"图形电镀法"。
即先在板子外层需保留的铜箔部分上,也就是电路的图形部分上预镀一层铅锡抗蚀层,然后用化学方式将其余的铜箔腐蚀掉,称为蚀刻。
一.蚀刻的种类要注意的是,蚀刻时的板子上面有两层铜。
在外层蚀刻工艺中仅仅有一层铜是必须被全部蚀刻掉的,其余的将形成最终所需要的电路。
这种类型的图形电镀,其特点是镀铜层仅存在于铅锡抗蚀层的下面。
另外一种工艺方法是整个板子上都镀铜,感光膜以外的部分仅仅是锡或铅锡抗蚀层。
这种工艺称为“全板镀铜工艺“。
与图形电镀相比,全板镀铜的最大缺点是板面各处都要镀两次铜而且蚀刻时还必须都把它们腐蚀掉。
因此当导线线宽十分精细时将会产生一系列的问题。
同时,侧腐蚀会严重影响线条的均匀性。
在印制板外层电路的加工工艺中,还有另外一种方法,就是用感光膜代替金属镀层做抗蚀层。
这种方法非常近似于内层蚀刻工艺,可以参阅内层制作工艺中的蚀刻。
目前,锡或铅锡是最常用的抗蚀层,用在氨性蚀刻剂的蚀刻工艺中.氨性蚀刻剂是普遍使用的化工药液,与锡或铅锡不发生任何化学反应。
氨性蚀刻剂主要是指氨水/氯化氨蚀刻液。
此外,在市场上还可以买到氨水/硫酸氨蚀刻药液。
以硫酸盐为基的蚀刻药液,使用后,其中的铜可以用电解的方法分离出来,因此能够重复使用。
由于它的腐蚀速率较低,一般在实际生产中不多见,但有望用在无氯蚀刻中。
有人试验用硫酸-双氧水做蚀刻剂来腐蚀外层图形。
由于包括经济和废液处理方面等许多原因,这种工艺尚未在商用的意义上被大量采用.更进一步说,硫酸-双氧水,不能用于铅锡抗蚀层的蚀刻,而这种工艺不是PCB外层制作中的主要方法,故决大多数人很少问津。
二.蚀刻质量及先期存在的问题对蚀刻质量的基本要求就是能够将除抗蚀层下面以外的所有铜层完全去除干净,止此而已。
金属蚀刻工艺流程

2
3
硝酸(HN03,65%)/(mL/L)
盐酸(HCl,37%)/(9/L)
溶液温度/C
处理时间
(三)工艺操作条件的影响
蚀刻是金属板模图纹装饰过程中的关键,要想得到条纹清晰、装饰性很强的图纹制品,必须注意控制好蚀刻工艺的条件。主要是蚀刻溶液的温度和蚀刻时间。溶液温度稍高,可以提高金属溶解的速度,也就是蚀刻的速度,缩短蚀刻所需要的时间,但是蚀刻溶液一般都是强酸液,强酸液在温度高的情况下腐蚀性强,容易使防护的涂层或耐蚀油墨软化甚至溶解,使金属非蚀刻部位的耐蚀层附着力下降,导致在蚀刻和非蚀刻交界处的耐蚀涂层脱落或溶化,使蚀刻图纹模糊走样,影响图纹的美观真实和装饰效果,因此温度不宜超过45℃。同样,如果蚀刻的时间太长,特别是蚀刻液温度较高的情况下,耐蚀油墨或防护涂层浸渍时间过长,也同样起到上述的副作用和不良后果,因此时间控制上也要适当,不能浸得太久,一般不宜超过20~25min。
本着色溶液在着色过程中,工艺条件对颜色有较大影响。首先是硫酸对铬酐的浓度比例对颜色的影响,铬酐浓度高时,为金黄色,浓度再高,则变成紫红色。温度对着色的影响为:温度升高,色泽逐渐加深。着色时间的影响为:5min便开始着色,随着时间的增加,颜色加深,20min后色泽基本稳定。电流密度对着色的影响为:/dm2时,为玫瑰色,/din2时,则为l8K金色。
(4)蚀刻后除墨蚀刻后必须除去保护的碱溶性耐酸油墨。方法是浸入40~60g/LNaOH碱液中,温度控制在60~70℃,浸泡3~5min,以除干净油墨为准。然后用水冲表面的碱液至中性。(5)蚀刻后处理经蚀刻后的图纹不锈钢板经过除油墨及清洗干净后,可以根据用户的不同需要作如下附加装饰处理。
①对要求保留不锈钢原色及光泽的,经除油墨及清洗干净后,放进50%HN03(体积分数)和50%H20的溶液中浸泡l0~20min,作钝化处理,使不锈钢蚀刻图纹板获得新的保护膜,即可得装饰制品。
金属蚀刻工艺流程

(一)金属蚀刻工艺流程
金属的种类不同,其蚀刻的工艺流程也不同,但大致的工序如下:金属蚀刻板→除油→水洗→浸蚀→水洗→干燥→丝网印刷→千燥→水浸2~3min→蚀刻图案文字→水洗→除墨→水洗→酸洗→水洗→电解抛光→水洗→染色或电镀→水洗→热水洗→干燥→软布抛(擦光)光→喷涂透明漆→干燥→检验→成品包装。
600~800
80~120
20~30
80~100
10~45
15~20不锈钢
600~650
90~100
8~12
15~50
10~15
铜合金
450~550
200~300
10~20
20~40
10~20
铸铝
表6-5金属铜化学蚀刻溶液配方及工艺条件
溶液成分及工艺条件
1
2
3
4
硝酸(HN03)/(mL/L)
硫酸(HzS04)/(mL/L)
2.工艺流程
不锈钢板→除油→水洗→干燥→丝网印刷→干燥→水浸→蚀刻图纹叶(片)水洗→除墨→水洗→抛光→水洗→着色→水洗叶(片)硬化处理→封闭处理→清洗叶(片)干燥→检验→产品。
3.具体操作及注意事项
(1)除油除油是为了使丝印油墨与板材有良好的附着力,所以金属板在印前必须彻底把油除干净。除油的方法很多,可以根据情况及需要选择,例如采用常规的化学除油、表面活性剂除油,甚至电解除油、超声除油等,也可以选用商品的专用除油剂。彻底清洗干净后,经干燥再转入丝网印刷。
(2)丝网印刷选用l50目不锈钢、聚酯或尼龙单丝维网,用绷网机固定在网框上,再用上浆器刮涂DH重氮型感光胶,涂覆2~3次,涂膜干燥后,将拍摄好的图纹黑白胶片附着在涂膜丝网上,经曝光、显影后,即制得丝印模板,然后再将不锈钢板、图纹模板固定在丝网印刷机对应位置上,采用碱溶性的耐酸油墨,印上所需要的图纹,自然干燥(或烘干)。如果烘烤,则温度不宜过高及时间不宜过长,否则油墨的碱溶性降低,到除油墨时,不易清除干净。一般情况下,自然干燥1h。烘干为55~60℃,4~5min。
蚀刻工艺流程

蚀刻工艺的重要性及发展趋势
蚀刻工艺的重要性
• 广泛应用于各种行业 • 对产品的质量和性能起着关键作用
蚀刻工艺的发展趋势
• 蚀刻工艺不断精细化和环保化 • 未来蚀刻工艺的研究将更加注重绿色生产和可持续发展
02
蚀刻工艺的种类与特点
化学蚀刻与电解蚀刻的区别与特点
化学蚀刻
• 通过化学反应使材料溶解 • 蚀刻速度较快,成本低 • 对设备的腐蚀性较大
影响蚀刻效果的因素
• 蚀刻液或蚀刻气的浓度 • 蚀刻温度和时间 • 材料的种类和性质
蚀刻后的处理与质量控制
蚀刻后的处理
• 清洁表面,去除杂质 • 检查蚀刻效果
质量控制
• 对蚀刻后的产品进行检测 • 确保产品符合要求
04
蚀刻设备与材料的选择
蚀刻设备的选择与维护
蚀刻设备的选择
• 根据蚀刻工艺和材料选择合适的设备 • 考虑设备的性能、精度和成本
蚀刻工艺过程中的问题
• 蚀刻不均匀 • 蚀刻速度慢 • 设备腐蚀严重
解决策略
• 优化蚀刻工艺和参数 • 使用高性能的设备 • 采用环保的蚀刻方法和材料
蚀刻工艺的未来发展方向
• 未来发展方向 • 绿色生产 • 精细化蚀刻 • 高精度蚀刻
06
蚀刻工艺的安全与环保问题
蚀刻过程中的安全与 防护措施
• 安全与防护措施 • 佩戴防护装备 • 遵守安全操作规程 • 妥善处理蚀刻废液和废气
蚀刻设备的维护
• 定期检查设备的运行状态 • 及时处理设备故障
蚀刻液与蚀刻气的选择与应用
蚀刻液的选择
• 根据蚀刻材料和工艺选择合适的蚀刻液 • 考虑蚀刻液的浓度、温度和腐蚀性
蚀刻气的选择
• 根据蚀刻材料和工艺选择合适的蚀刻气 • 考虑蚀刻气的浓度、温度和腐蚀性
电子厂蚀刻部具体工作流程
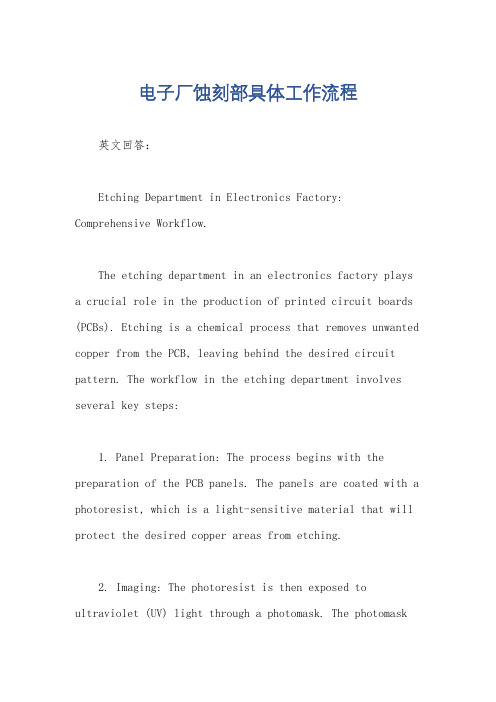
电子厂蚀刻部具体工作流程英文回答:Etching Department in Electronics Factory: Comprehensive Workflow.The etching department in an electronics factory plays a crucial role in the production of printed circuit boards (PCBs). Etching is a chemical process that removes unwanted copper from the PCB, leaving behind the desired circuit pattern. The workflow in the etching department involves several key steps:1. Panel Preparation: The process begins with the preparation of the PCB panels. The panels are coated with a photoresist, which is a light-sensitive material that will protect the desired copper areas from etching.2. Imaging: The photoresist is then exposed to ultraviolet (UV) light through a photomask. The photomaskdefines the circuit pattern that will be etched. The exposed areas of the photoresist will harden, while the unexposed areas will remain soft.3. Development: The exposed photoresist is then removed using a developer solution. This leaves behind the desired circuit pattern on the PCB panel.4. Etching: The PCB panel is then immersed in an etching solution, which removes the unprotected copper. The etching solution is usually composed of a strong acid, such as hydrochloric acid or ferric chloride.5. Stripping: After etching, the remaining photoresist is removed using a stripping solution. This leaves behind the finished PCB with the desired circuit pattern.6. Inspection: The etched PCBs are then inspected to ensure that they meet the specifications. This involves visual inspection as well as electrical testing.7. Storage: The finished PCBs are stored in acontrolled environment to prevent contamination or damage.中文回答:电子厂蚀刻部详细工作流程。
蚀刻工艺流程说明

蚀刻工艺流程说明蚀刻工艺是一种利用化学反应将某些部分材料从工件表面腐蚀掉的制造方法。
它广泛应用于电子、半导体、光电子和微电子等领域的制造工艺中。
以下是蚀刻工艺的基本流程说明:1. 设计图纸和图案:根据产品的设计需求,绘制出要在工件表面上蚀刻的图案和尺寸要求,通常使用计算机辅助设计(CAD)软件进行设计。
2. 制备工件:选择合适的材料作为工件,通常使用金属、玻璃或半导体材料,根据设计要求切割成适当的尺寸和形状。
3. 清洗工件:将工件放入清洁溶液中进行清洗,以去除表面的杂质和污染物,使工件表面干净和光滑。
4. 杯型孔洗:将工件放入酸蚀溶液中,这个过程是为了去除可能影响蚀刻图案的杂质。
5. 蚀刻涂膜:使用特殊的蚀刻涂膜材料涂覆在工件表面,涂覆薄膜的部分将作为保护层,不被蚀刻液所腐蚀。
6. 曝光:将工件放入曝光机中,通过曝光来固化蚀刻涂膜,通常使用紫外线的照射来启动固化反应。
7. 蚀刻:将工件放入蚀刻槽中,含有特定蚀刻液的槽中,蚀刻液中的化学物质会与蚀刻涂膜中未固化的部分发生反应,使其腐蚀掉。
8. 清洗和去膜:将工件从蚀刻槽中取出后,在清洁溶液中进行彻底的清洗,以去除蚀刻液和残留的蚀刻涂膜。
9. 检验和质量控制:对蚀刻后的工件进行检验,确保蚀刻的尺寸、形状和表面质量符合设计要求。
10. 后处理和包装:根据产品的要求,对蚀刻后的工件进行后处理(如电镀、热处理等),最终将其包装成成品。
需要注意的是,蚀刻工艺的具体流程和步骤可能会根据材料和产品的不同而有所差异,上述流程仅为一般情况下的示意。
除了以上介绍的基本流程,蚀刻工艺中还有一些进一步的细分和改进流程,以满足不同产品的要求和技术需求。
其中,有两种常用的蚀刻方法:湿法蚀刻和干法蚀刻。
湿法蚀刻是最常见的蚀刻方法,它使用蚀刻液(如酸、碱等)与工件表面进行化学反应,将部分材料腐蚀掉。
具体的蚀刻速度和蚀刻深度可以通过调整蚀刻液的成分和浓度来控制。
湿法蚀刻适用于各种材料,如金属、半导体和玻璃等,但在执行过程中需要注意对环境和工人的安全性。
金属蚀刻工艺流程

金属蚀刻工艺流程(总3页)--本页仅作为文档封面,使用时请直接删除即可----内页可以根据需求调整合适字体及大小--金属蚀刻工艺流程(一)金属蚀刻工艺流程金属的种类不同,其蚀刻的工艺流程也不同,但大致的工序如下:金属蚀刻板→除油→水洗→浸蚀→水洗→干燥→丝网印刷→千燥→水浸2~3min→蚀刻图案文字→水洗→除墨→水洗→酸洗→水洗→电解抛光→水洗→染色或电镀→水洗→热水洗→干燥→软布抛(擦光)光→喷涂透明漆→干燥→检验→成品包装。
1.蚀刻前处理在金属蚀刻之前的工序都是前处理,它是保证丝印油墨与金属面具有良好附着力的关键工序,因此必须要彻底清除金属蚀刻表面的油污及氧化膜。
除油应根据工件的油污情况定出方案,最好在丝印前进行电解除油,保证除油的效果。
除氧化膜也要根据金属的种类及膜厚的情况选用最好的浸蚀液,保证表面清洗干净。
在丝网印刷前要干燥,如果有水分,也会影响油墨的附着力,而且影响后续图纹蚀刻的效果甚至走样,影响装饰效果。
2.丝网印刷丝网印刷要根据印刷的需要制作标准图纹丝印网版。
图纹装饰工序中,丝印主要起保护作用,涂感光胶时次数要多些,以便制得较厚的丝网模版,这样才使得遮盖性能好,蚀刻出的图纹清晰度高。
丝网版的胶膜在光的作用下,产生光化学反应,使得光照部分交联成不溶于水的胶膜,而未被光照部分被水溶解而露出丝网空格,从而在涂有胶膜丝网版上光刻出符合黑白正阳片图案的漏网图纹。
把带有图纹的丝印网版固定在丝网印刷机上,采用碱溶性耐酸油墨,在金属板上印制出所需要的图纹,经干燥后即可进行蚀刻。
3.蚀刻后处理蚀刻后必须除去丝印油墨。
一般的耐酸油墨易溶于碱中。
将蚀刻板浸入40~60g/L的氢氧化钠溶液中,温度50~80℃,浸渍数分钟即可退去油墨。
退除后,如果要求光亮度高,可进行抛光,然后进行染色,染色后为了防止变色及增加耐磨、耐蚀性,可以喷涂透明光漆。
对于一些金属本身是耐蚀性能好而且不染色的,也可以不涂透明漆,要根据实际需要而定。
多层印制板的凹蚀与负凹蚀

多层印制板的凹蚀与负凹蚀Metallization&Plating■多层印制板的凹蚀与负凹蚀四州是学化工学院n1㈨j)马忠艾摘要多层板孔金属化包括击钻污处理扣化学;兄铜,去钻污过程是时孔壁非导电材料的蚀一1.而沉铜前处理中的微蚀是对内层导电铜箔的性剖.当前者的量走于后者时为凹蚀,当后者走于前者时为角凹蚀本文通过对凹蚀与负凹性的形成过程进行分析,提供了两种蚀剖量的测定方法,对航天标准.国军标以及IP(I标堆中关于凹蚀与负凹蚀的规定进行时}匕阆达T如何控制凹蚀与负凹蚀的深度.防止产生过度的凹蚀与套凹毫暑,而保-b~_:IL金属化的质量关键词多层板凹蚀负凹蚀EtchbackandNegativeEtchbackinMLBMaZhongyiAbslractPTHofMLBitic】tidesdesme;-ffandelectrolesscoppenDesIll~2aretchingtheinsulatedmaterial?nthehole. butelectrolesscopperisforetchingthecopperofJnnerlayerWhenthefo rmerisgreaterthanthelater,”isca Iledetchback otherwiseitiscallednegativeetchbackThroughanalyzinghowetchbackandnegativeetchbackforms,t hispaperoffersthetestingmethodsabou【twoetchingspeedscarriesthroughcontrastsbetweenQJ83】A-98andGJB362A一96andIPC一6f~)Faboutetchbackandnegativeetcbback,expatiateshowtOcontrolthedepthofMLB’***************************** Oas”,avoidexcessiveetchbackornegativeetchbackandaSSLll~itsI’TH’quality KeywordsMLBetchbackhogativeetchback】凹蚀与负凹蚀的定义多层板在钻孔过程中.由于钻头的高速运转产生摩擦.而产生高热使孔壁环氧树脂熔化粘附到孔壁以及内层铜箔上.如果不将其去除.后续L壁金属化铜层就会与内层失去电气互连.此.多层板沉铜前都要进行去钻污处理去钻污(desmear)就是指去除孔壁上的熔融讨脂和钻屑的过程:多层板沉铜典型的工艺流程为:上板一溶胀一高锰酸钾一中和一玻璃蚀刻一清洁调整一微蚀一预浸一胶体钯一解胶一沉铜.其中带下划线部分为去钻污流程去钻污过程是针对孔壁非导电材料的蚀到,而后续沉铜过程中的微蚀是针对内层导电铜箔的蚀刻,当前者蚀刻量大于后者时.为凹蚀(etc-hback)(如图I).凹蚀过程也叫正凹蚀(positiveetchback);当后者速率大于前者时,为负凹蚀(negativeecchback)(如图2图2负凹蚀孔化与电镀PrintedCircuitInformation印制电路信息2004No.7..…...33一■!一孔化与电镀_:Metallizatioiq&Plating根据IECf1l】Iq4《印制板殳汁,制造与组姨一术浯与定义的定义.凹蚀是指”为了去障甜脂钻污硬充分暴露内层导电表而而有控制地除去孔哇非金腻材料规定深度的化学过程”,负【L『I蚀是指“内层的导电材丰=}捐对于J围蘩材【缩的蚀”2:种蚀刻量的测定及控制21去钻污时L壁非金属材料蚀刻量的测定取lI)cmx…cm半固化片一片(1¨(I或H均可).顶部钻_一个小孔.授以下步骤试验:(L)l2I)℃~¨(1℃烘1小时称重(g1:(2)按工艺流程进行去钻污处理(高锰酸钾处理时IhJ为f分钟).水洗,l2I)一144)℃烘i小时.称重(E】;f3)以毫克每分([132,miI】】ir的蚀刻逑率的计算:忙1…)I】x(一)/r以毫克每平方厘米(mg/cm1计的诎刻量的计算:.1I)x(.一.).一般如果数值在2II~nIlmg/min或1—2mg/cill之H】,Jl!lj速率比较正常.容易得到负蚀22内层导电铜箔蚀刻量的测定取一块】I)cm×10cm覆铜板f基材厚度可选16mm,铜箔旱度可选luI1]).顶部钻一个小孔.按以F步骤试验:(Ij按工艺流程进行清l吉酬整处理.水洗.12()~¨I】℃烘I小时,称重WI(g):(2)按工艺流程进行微蚀处理水洗.121I~l4I)℃烘l小时.称重(g);(1{j以微米(mnl}I十蚀刻量的’十算:d=Il2xf一1一股如果蚀刻量在llira~:pm之.则比较正常23凹蚀与负凹蚀深度的控制多层板化学沉铜过程中控制了以上两种蚀刻量,也就控制了凹绌或负凹蚀的深度.控制去钻污时L壁非金属材料蚀划速牢.使其蚀刻深度为l5um~20m.将内层导电铜箔蚀刻深度控制在jm~141um左右.这样可以得到比较理想的凹蚀深度:控制去钻污时孔壁非金属材料蚀刻速率刚好将内层焊盘上环氧钻污去掉,再将后续内层导电铜箔蚀刻深度控制在5lira~IlIm左右,这样就得到了比较理想的负凹蚀深度值得注意的是多层板在化学沉铜的返工过程中,由于一般都不再经过去钻污流程而直接将不台格的沉铜层徽.….…PrintedCircu.缺点是如果负凹蚀过度,孔壁与内层连接凹处容易存留气泡和污物.且捌角处容易产生应力集中,日_制板在后续实验或使过程中可能引起内层与孔壁产生断裂和分离(如3).凹蚀的优点是它使镀覆孔的铜层与内层铡箔之间产生三维界面的结合.三维连接比一个界而连接更加可靠但缺点是凹蚀姿造成L壁粗糙【如图4),容易产生超过规定的芯吸作用(wicking)+并且使镀覆孔的镀铜层可能产生裂纹过度的凹蚀也会导致可能引起内层锏蒲破裂的应力.■图4凹蚀使多层板孔结构粗糙不平4各标隹对凹蚀与负凹蚀的验收条件总的来兑.各标准对手凹蚀与负凹蚀的验收条件基本相同规定凹蚀时.不允许有负凹蚀,最佳凹蚀深度都规定为13m;不同的一点是航天标准与国军标规定负凹蚀深度最大为13lim.而IP~标准规定理想的负凹蚀深度为2Slim.接受状况3级为小于13岬.接受状况],2级为小于25um. 以下是三个标准关于凹蚀与负蚀的具体规定.…………………………………………………………Metallization&Plating……4.1航天标准QJ831A-98原中国航天工业总公司于98年发布的QJ831A一98《航天用多层印制电路板通用规范》属于航天工业行业强制性标准,其3.6.3.2.1”凹蚀与去钻污”对多层板的金属化孔质量作出了如下规定:“3.5.3.2.1.1凹蚀当布设总图有规定时,在孔化前应进行凹蚀.凹蚀深度最小应为0.005mm,最大应为0.080mm,优选0.0l3mm.当规定凹蚀时,不允许有负凹蚀.3.6.3.2.1.2去钻污当布设总图未规定凹蚀时,孔应是清洁的,无树脂钻污,从孔壁径向除去的材料应不大于0.030mm.允许的负凹蚀最大为0.0l3mm.”4.2国军标GJB362A一96中华人民共和国国家军用标准GssJB362A一96 《刚性印制板总规范》是l996年由国防科学技术工业委员会批准发布的.其对凹蚀以及去钻污的规定为”3.6.2.1.5凹蚀或去钻污”,具体规定如下: “3.6.2.1.s.1凹蚀(当规定时)当布设总图有规定时,在镀孔前应进行凹蚀,从印制板内层导体侧面除去树脂和玻璃纤维.当在内层铜箔接触区伸出头测量时,凹蚀深度最小为0.005mE,最大为().080mE,优选的凹蚀深度应为0.0l3mm.玻璃纤维渗铜可伸入0.080mE,但不得使两相邻孔壁的导体间距小于布设总图规定的最小值.凹蚀至少应对每个内层导体的上下两表面发生作用.当凹蚀时,不允许有负凹蚀.3.6.2.1.s.2去钻污(洗孔)3.62.1.5.2.1交收态当布设总图未规定凹蚀时,镀覆孔应当是清洁的,无树脂钻污,从孔壁径向除去的材料应不大于0.03ram.3.6.2.1.5.2.2负凹蚀当布设总图未规定凹蚀时,若提供的印制板试样满足3.6.2.4的要求,允许的负凹蚀最大为0.013mm.”4.3lPC—A-6OOFIPC(美国连接电子业协会)于l999年修订的IPC—A一600F《印制板的验收条件》,其中”凹蚀”作为”内部可观察特性”在标准的”3.1.5凹蚀”中进行了规定.具体规定如下:“3.1.5.1凹蚀理想状况——l,2,3级均匀地凹蚀到最佳的深度0.0l3mm【0.000512in】接收状况——l,2,3级凹蚀深度介于0.005mm【0.00020in1和0.08mm【0.003lin]之间.在每个连接盘的一侧上允许有凹蚀阴影.拒收状况——l,2,3级凹蚀深度小于0.005mm【0.00020in】或大于0.08ram【0.003lin】.任一连接盘的两侧面上均有凹蚀阴影.3.1.s.2负凹蚀理想状况——l,2,3级铜箔上为均匀的负凹蚀深度为0.0025mm(0.0000984in】接收状况——l级负凹蚀小于0.013mm[0.00512in】.接收状况——l,2级负凹蚀小于().025mm[0.000084in1.拒收状况——l,2,3级缺陷超过上述规定.5结论不管是凹蚀或负凹蚀,只要控制其深度都能得到合乎要求的多层印制板产品.通过控制化学沉铜过程中两种蚀刻流程的蚀刻速率,可以得到规定要求的凹蚀或负凹蚀深度由于凹蚀过程对多层板孔壁结构的完整性有一定的破坏性.笔者建议倾向于得到负凹蚀.采用负凹蚀的工艺必须注意多层板返工过程的控制,以免产生过度的负凹蚀.参考文献【l1IEc60]94fll~1]板设计,制造与组装术语与定义,中国印制电路行业协会【2】马忠义.多层板热应力产生断裂的原因分析,第一届全国青年委员会学术年会论文集IPC—A一600F印制板的验收条件,中国印制电路行业协会【41QJ831A一98航天用多层印制电路板通用规范[5]GJB362A一96刚性印制板总规范PrintedCircuitInformation印制电路信息2004No.7.…….35:孔化与电镀。
玻璃的表面化学深蚀刻的工艺原理与其操作方案
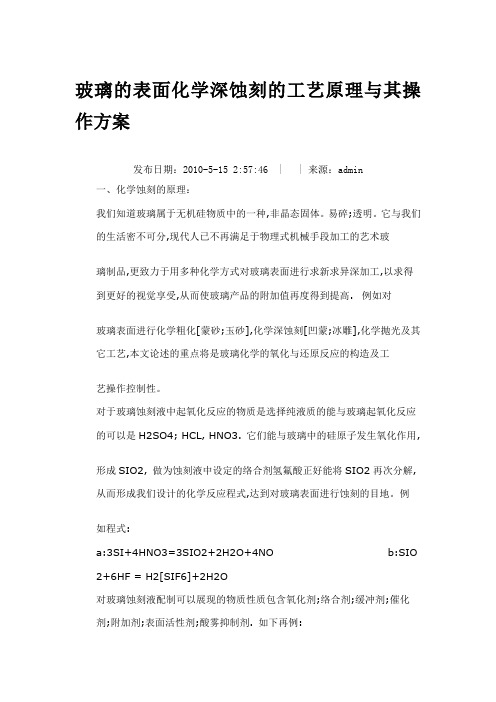
玻璃的表面化学深蚀刻的工艺原理与其操作方案发布日期:2010-5-15 2:57:46 | | 来源:admin一、化学蚀刻的原理:我们知道玻璃属于无机硅物质中的一种,非晶态固体。
易碎;透明。
它与我们的生活密不可分,现代人已不再满足于物理式机械手段加工的艺术玻璃制品,更致力于用多种化学方式对玻璃表面进行求新求异深加工,以求得到更好的视觉享受,从而使玻璃产品的附加值再度得到提高. 例如对玻璃表面进行化学粗化[蒙砂;玉砂],化学深蚀刻[凹蒙;冰雕],化学抛光及其它工艺,本文论述的重点将是玻璃化学的氧化与还原反应的构造及工艺操作控制性。
对于玻璃蚀刻液中起氧化反应的物质是选择纯液质的能与玻璃起氧化反应的可以是H2SO4; HCL, HNO3. 它们能与玻璃中的硅原子发生氧化作用,形成SIO2, 做为蚀刻液中设定的络合剂氢氟酸正好能将SIO2再次分解, 从而形成我们设计的化学反应程式,达到对玻璃表面进行蚀刻的目地。
例如程式:a:3SI+4HNO3=3SIO2+2H2O+4NO b:SIO 2+6HF = H2[SIF6]+2H2O对玻璃蚀刻液配制可以展现的物质性质包含氧化剂;络合剂;缓冲剂;催化剂;附加剂;表面活性剂;酸雾抑制剂. 如下再例:氧化剂:H2SO4 ; HCL ; HNO3;还原剂:HF缓冲剂:H2O; CH3COOH;催化剂:NH4NO3; CuSO4; NaNO2; AgNO3;附加剂:Br2酸雾抑制剂:FC-129; FC-4; FT248TM 湿润活性剂; 长直链烷基TH系; 烷基酚聚氧乙烯醚按重量百分比配制玻璃蚀刻液可以视深蚀刻、浅蚀刻及抛光要求对蚀刻液中各物质百分比投料进行调整. 如下续例:缓冲剂--------------------------------------- 40----67%氧化剂--------------------------------------- 15----38%络合剂--------------------------------------- 27----45%催化剂--------------------------------------- 0.03---0.06附加剂--------------------------------------- 0.05---0.1--------------------------- 0.04酸雾抑制剂----------------------------------0.003重度蚀刻液中氧化剂控制在20%左右; 值得提醒的是被蚀刻的玻璃凹面呈抛光状态的控制是将缓冲剂的量放在60%左右. 若冰棱小可适量提高络合剂比例上升4%—8%左右.对于玻璃表面化学抛光方案另再续实例如下:1: 100g五倍子酸+ 305ml乙醇胺+ 140ml水+ 1.3g吡嗪+ 0.24mlFC1292: 60ml49%HF +30mlHNO3[69%] +30ml/5ml/LCrO3+2gCu[NO3]+ 60ml CH3COOH + H2O 60ml3: 100gH2O+ 40% HF36g + 68%HNO3 + NaNO2 0.03g +0.24mlFC--3或0.02gFT2484: 50g HNO3[68%] + 30gHF {55%} + CH3 COOH 30 g+0.6gBr2对于以上各种化学配比希望操作人再次调试以获得良好结构比,满足工艺要求!二、关于对玻璃表面蚀刻的冰棱大小及深度的调整方案∶1: 蚀刻深度较理想,但冰棱较小或没有?解决方案: 对全量加入5%—16%络合剂适量调整。
金属蚀刻工艺流程

金属蚀刻工艺流程(一 )金属蚀刻工艺流程金属的种类不一样,其蚀刻的工艺流程也不一样,但大概的工序以下:金属蚀刻板→ 除油→水洗→ 浸蚀→水洗→ 干燥→丝网印刷→ 千燥→水浸 2~3min→蚀刻图案文字→水洗→除墨→水洗→酸洗→水洗→电解抛光→水洗→染色或电镀→水洗→热水洗→干燥→软布抛 (擦光 )光→喷涂透明漆→ 干燥→查验→ 成品包装。
1.蚀刻前办理在金属蚀刻以前的工序都是前办理,它是保证丝印油墨与金属面拥有优秀附着力的重点工序,所以一定要完全消除金属蚀刻表面的油污及氧化膜。
除油应依据工件的油污状况定出方案,最幸亏丝印行进行电排除油,保证除油的成效。
除氧化膜也要依据金属的种类及膜厚的状况采纳最好的浸蚀液,保证表面冲洗洁净。
在丝网印刷前要干燥,假如有水分,也会影响油墨的附着力,并且影响后续图纹蚀刻的成效甚至走样,影响装修成效。
2.丝网印刷丝网印刷要依据印刷的需要制作标准图纹丝印网版。
图纹装修工序中,丝印主要起保护作用,涂感光胶时次数要多些,以便制得较厚的丝网模版,这样才使得掩盖性能好,蚀刻出的图纹清楚度高。
丝网版的胶膜在光的作用下,产生光化学反响,使得光照部分交联成不溶于水的胶膜,而未被光照部分被水溶解而露出丝网空格,进而在涂有胶膜丝网版上光刻出切合黑白正阳片图案的漏网图纹。
把带有图纹的丝印网版固定在丝网印刷机上,采纳碱溶性耐酸油墨,在金属板上印制出所需要的图纹,经干燥后即可进行蚀刻。
3.蚀刻后办理蚀刻后一定除掉丝印油墨。
一般的耐酸油墨易溶于碱中。
将蚀刻板浸入40 ~60g /L 的氢氧化钠溶液中,温度50 ~ 80 ℃,浸渍数分钟即可退去油墨。
退除后,假如要求光明度高,可进行抛光,而后进行染色,染色后为了防备变色及增添耐磨、耐蚀性,能够喷涂透明光漆。
关于一些金属自己是耐蚀性能好并且不染色的,也能够不涂透明漆,要依据实质需要而定。
( 二)化学蚀刻溶液配方及工艺条件蚀刻不一样的金属要采纳不一样的溶液配方及工艺条件,常用金属资料的蚀刻溶液配方及工艺条件见表6―4~表 6-6。
- 1、下载文档前请自行甄别文档内容的完整性,平台不提供额外的编辑、内容补充、找答案等附加服务。
- 2、"仅部分预览"的文档,不可在线预览部分如存在完整性等问题,可反馈申请退款(可完整预览的文档不适用该条件!)。
- 3、如文档侵犯您的权益,请联系客服反馈,我们会尽快为您处理(人工客服工作时间:9:00-18:30)。
化学蚀刻制作二层电路板流程
主要流程:PCB文件的导出(GERBER文件)——GERBER文件的导入——打靶标、打孔——刷板——孔金属化——刷板——覆干膜——曝光——显影——蚀刻——去膜——阻焊——字符——助焊
具体如下:
1.将要用到的机器设备打开预热。
2.PCB电路图设计完成后,在protel99软件下点击File菜单下的
CAM manager栏生成相关印制电路板信息的gerber文件,然后导出。
3.打孔
(1)打开LPKF CircuitPro软件,file-new-2layer_GalvanicTHP.cbf- OK,导入生成的二层板gerber文件,计算好雕刻时的信息,配好打孔时需要的刀。
(2)打卡位孔将选好的双面板放入雕刻机内,粘好胶带,选好打孔需要的3mm刀,点击home点,X方向115mm,Y方向295mm,X 方向+1mm,-2mm位置打孔。
(3)打靶标和孔将打好卡位孔的双面板放在刻制机内,并粘好胶带,然后进行打孔操作。
打孔完成后,将印制电路板取出进行下一步刷板操作。
3.刷板
刷板前可先用气泵枪处理掉遗留在电路板上的板屑。
刷板时,先打开热风烘干按钮和水阀开关,进板后控制好进板速度和刷板的压
力,刷板压力适中,以免刷坏覆铜面。
刷板速度为0.3-0.4m/min,摆动40-60次/min。
刷板目的是为了去除打孔后双面板表面的毛刺。
烘干时也可以使用吹风机吹干。
然后进行孔金属化操作。
4.孔金属化
将打好孔的四层板先进行刷板,去除表面毛刺。
观察通孔是否打好,用气枪或小钻头处理被板屑堵住的孔。
然后开始孔金属化。
①去油污
碱性药液达到预热温度50℃后,放入板子,设定时间为15min。
夹板时注意观察药液是否可以将所有孔浸入,打开控制摆动的开关,其作用是更好地去除板面的油污,为电镀做好准备。
去油污完成后时间按钮复位。
关闭摆动,取板时板子尽量平放,避免药液滴落地面,然后进行水洗。
②微蚀
微蚀作用主要是除去板面的氧化物,粗化板面,保证后续沉铜层与基材底铜之间良好的结合力。
设定时间为5min,微蚀后一定要用去离子水清洗,烘干,主要是为了防止影响C溶胶的浓度。
③沉碳
沉碳时间设定为15min,打开电机电源开关。
打孔后的孔壁不导电,沉碳主要是为了给孔壁附着碳粒,使之活化可以导电,便于镀铜。
沉碳完成后,用刮板刮掉表面的碳黑,烘干,用柔软的棉布将板面的碳尽量擦拭干净,烘干。
观察是否有堵孔,如有用气泵枪吹通。
④电镀
时间设定为60min,电流为10A左右,用专用的电镀夹板夹好板子,打开电镀开关,开始电镀。
电镀完成后注意观察板面是否平整光滑,孔是否通透。
表面不光滑时可以用砂纸轻轻打磨。
刷板后烘干,准备覆膜。
注:每次都打开摆动开关,完成后关闭。
5.刷板
操作同3。
6.覆干膜
覆膜机需要预热至100℃,预热时间大约30min左右。
达到预热温度后,先用废板将可能被氧化的膜用掉,再将刷板后烘干的双面板放至滚轴上,选好放板的位置,尽量节约的前提下,小心操作,摁下RUN按钮,速度调至0.3-0.4m/min,干膜加好后,割掉多余的部分。
7.出菲林
通过光绘机将需要的菲林片绘出,注意负片和镜像的问题,外层负片,顶层水平镜像;并注意区分药膜面。
光绘完成后,将菲林片放置微电脑自动冲片机进行冲片。
工作环境为绿光暗室房。
8.曝光
根据定位孔信息进行菲林定位(药膜面朝向铜面),并用胶带粘好,胶带尽量小。
曝光机使用时,打开操作台,将贴好菲林的双面板小心放入曝光机内。
合上操作台,将操作台完全推进后抽真空。
抽真空目的是防止菲林片和干膜之间的气泡散射影响曝光效果。
选择双面板模式,曝光时间40S。
9.显影
将曝好光的双面板取出后,揭下菲林片,将菲林片保护好以方便多次使用。
撕掉覆在双面板上的干膜的外层保护膜,撕的时候注意不要让干膜残屑掉到板面上。
将板子固定在夹具上,放入和拿出时应掌握技巧,选择最好最有效的方式。
待到显影液温度达到40℃后,进行显影操作,传送速度调至8-9mm/s。
操作之前为防止药液沉淀将空卡槽放入走一遍,以使药液混合均匀。
显影后,拿出卡槽时尽量不要让药液滴到地面,用水冲洗板子,防止污染下一步操作使用的药液。
下一步进行蚀刻操作。
8.蚀刻
操作类似7,预热40℃左右,速度8-9 mm/s。
蚀刻完毕后,再次水洗,下一步进行去膜操作。
9.去膜
操作类似7和8,预热40℃左右,速度8-9 mm/s。
去膜后水洗,刷板并烘干。
下一步进行层压。
10.阻焊
阻焊油墨:固化剂=1:3,调好助焊油墨后用滚刷将油墨均匀涂布在板子上,用烘箱预固化(80℃,15-20min),贴菲林片曝光60s,将焊盘以外的线路保护起来,显影液配置时水温最好40°—50°之间,显影液蚀刻掉阻焊油墨将焊盘暴露出来,用烘箱固化(160℃,30min)。
11.字符
字符油墨:固化剂=1:3,调好油墨后用滚刷将油墨均匀涂布在板子上,用烘箱预固化(80℃,15-20min),贴菲林片曝光400s,显影
液将字符留下来,蚀刻掉其它的油墨,再用烘箱固化(160℃,30min)。
12.助焊
将板子放入孔金属化仪器8槽内预浸,通过有机助焊剂预浸15min。
13.裁板
将板子放入雕刻机内,选择对应流程自动裁板。