基于机械加工的深孔加工技术探析
机械加工过程中的深孔加工技术分析

机械 - r . 过程中的深孔加工技术分析
粱 俊
( 合肥 力威 汽车油泵有 限公 司,安徽合肥
2 3 0 0 4 1 )
摘 要 : 机械加 工行 业是保 证我 国工业化进程顺利 实施 的关键 。随着机械加 工业的发展 ,其各项工 艺技 术也得 到 了快速的 演 变。同时,在机械k _ T - 过程 中,深孔加 工技 术是 整个机械加 工的关键 所在。下面,就一起跟随本 文对机械加 工过程 中的深孔 加 工技术进行一个 简单的分析与探讨 。
关键词 : 机械加工 ; 深 孔加 工 ; 技 术 中图分类号 : T U7 文献标识码 : A
文章编号 : 1 6 7 1 . 5 5 8 6( 2 0 1 5 )1 0 . 0 0 0 8 - 0 1
在机械加 工过程 中,深孔加工是一项十分复杂的工序 ,同 交错齿 内排 削深 孔加 工技 术是 目前 应用较为 广泛 的一种深 它主要应用于钢件 的深孔加工技术 中。一般来说 , 时也是出现问题较 多的一道工序 。因此,为保证机械加 工过程 孔加工技术 , 中的各项工序顺 利实施,就必须要对深 孔加工技术进 行优 化, 在钢件上进行深孔加工远 比在 铸件 上进 行加 工要难得 多,所产 这也是 目前机械加工行业所最为重要的任务之一。 生 的铁屑也较多 。因此,必须采用像交错齿钻具这种 刀片排列 1什么是深孔 加工技术 顺序为错开式的刀具 。由于交错齿钻具的刀片的特殊 构造 ,从 所谓 的深孔 加工主 要是指在 机械 加工过程 中孔 的长度 与 而可 以使切 削通过 刀具 的两个 孔排入 到刀具 自身 的空心 刀杆 孔 的直径之 比大于 1 O 的孔。深 孔加 工技术在我 国的起步较早 , 中,切 削再 由空心刀杆 中排 出,从而实现 了排 出切削 的整个过 目前 各项技 术均 已相对较为 成熟 。 目前就 一般机械加 工企 业 程 。另外 ,刀片是在刀具 的两侧 内呈交错排列方式 的,这种排 来看 ,深孔加工时深孔与直径 的比值一般为 L / d 1 0 0 。例如 : 列方式可 以起着很好 的分屑作用 ,同时还能够使钻具两侧刀片 油箱孔、各种轴的轴向孔、空心主轴孔等 。 的受力度里平衡状态 ,即不会对刀片造成损害 ,又保证 了钻孔 2 深子 L 加工技术 的难点 的直线 性。另外 ,在 刀片 前加 工断屑槽 ,就会使钻孔 的切 削形 深孔加工 中由于对质量及其他方面 的要求均较高 ,因此在 成一种小 c形 的状态 ,从 而保证 了钻具 在高压 切削状 态下切 技术加工上有着诸多的难点 : 首先,由于机械加工过程 中深孔 削分较 容易被冲 走排 向外面 。同时,由于刀 具的钻 头沿径 向上 加工时速度不能太快 ,因此一般作业 效率均不高 ,其次在深孔 的切削在各 点的速度均不 同,例如 : 钻孔外 围部分的切削速度 加工时工作人员无法观察到设备切削时的情况 ,而 只能通过设 相 对较快,因此可采用耐磨性能较强 的 YT类硬材质 的合 金材 备切割 时所发 出的声音来判断深孔加工是否达 到一 定的标准要 料。而靠近刀具钻头中心的切 削速度 由较慢,在切削相互挤压 求 ,这种方 式在一定程度上是很容易出现误差 的。再次 ,一般 的过程 中刀片容 易受到损伤 ,因此必须采用 Y A类 型的硬质合 而 言,深孔加工 的长径距离是较大的,因此用 于切 削深孔 的刀 金 。 具等设备就相对较长较细 。但 由于刀具较长较 细的特 点,导致 另外 ,在深 孔加 工时 ,如果深 孔 的直径 大 于 6 . 5 厘 米 时, 钻 具 自身的钢性 强度较差 ,同时 由于该设备刀具刃 口偏差等 问 则可采用机械夹固式不重磨深孔加工技术,它的结构与施工方 题 ,从而在 工作 时产生较大 的振动 ,很容易在作业过程 中使钻 式与交错齿深孔加工技术基本相 同。它在作业时刀片 的内部会 孔因受到的振动较大等原 因而发生偏离设计的现象。针对这 一 出现一个阶 台,并用螺丝固定在刀头部分 ,以上刀片做为断屑 点难点 , 就必须要求工作人员在深孔加工时, 首先要 间断切削 , 板 ,并将导 向板作为半 圆形状 ,从而使导 向块与孔壁形成一个 并且要 同时不断提升 刀具 ,要具备较强的判断力来对深 孔加 工 很好 的接触点 。而后再采用 4 0 C的金属制成 的钻头体将空心钻 中切削的长度及 形状进行判断 。最后 ,一般在深孔加工时会 产 杆 与 其 连 接 在 一 起 。 生较大 的热量,而这些热量受一些 因素 的影响无法在深孔加工 3 . 3喷 吸钻深子 L 加工技术 过程 中快速释放 出来, 再加之深孔加工钻具排削条件较为恶劣 。 使用该方法进行深孔加工时 ,必须要 同时配备 一套相应 的 因此在深孔加工 中必须采用冷 却法对刀具设备进行冷却, 以保 设备 ,并将管夹头 安装于车床板 的夹具 中,同时利用大拖板 的 证深孔加工质量的有效性 。深孔加工 中一定要有较好的钻具冷 自动进给使物件钻 出深度 ,另外 ,为 了防止钻 头刚钻人 工件 时 却方法 以及 良好的排削系统,因此 目前机械加工企业均采用 内 发生扭 断,要在工件前 安装一个 导向设备 ,从而使 喷吸钻 的高 排 削深钻孔机械来对大直径深孔进行加工 。 压深孔钻工作时获得一个很好的结果。 3机械加工过程 中深F U J O 工技术 例如 : 在使用 喷吸式刀 具和高压式 刀具进行深 孔加工 时, 3 . 1单刀深孔钻加工技术 切削 的液 流量需在达 到每分钟 1 5 0 L以上 ,压力 要控制在每 立 所谓 的单刀钻具的主要特 点在于它 的刀片和导 向的部位均 方厘米 3 5 公斤 以上。在这 种大流 量和压 力下 ,传 统的车床 冷 是采用材质较为坚硬的金属合 金材料构成 ,并且单刀 的刀尖部 却系统是无法满足大热量冷却需求的 ,因此必须同时配备一系 分偏离整个钻具 的中心点约 3 毫米的距离,从而使刀具在深孔 列大流量 的冷却系统支持 ,从而达到喷吸刀具 比高压刀具 内所 加 工切 削过程 中形成 了一种定心尖状态 ,因此该钻具可 以在切 排 出的切 削液压力低 的 目的 。这种方法下 的冷却系统 的功率消 削过程 中分担一部分 的径 向切割力。另 外,单刀深钻孔钻具 的 耗及钻具 的损害程度都会降低 ,因此在深孔加工时 ,要尽时 多 主 削刀在工作 中形成一种阶台型的结构 ,从而 能够很好地起到 采用喷吸式刀具进行深孔加工 。 分 削的 目的,因此在操作过程 中可以根据深孔直径 的大小要求 4 结语 来设置 单刀的使用数量 ,以此来保证排削的有效性。 综上所述 ,机械加 工过程 中深孔加工 技术 直接 关系着整个 另外,在深孔加工整个过程中 ,单刀钻 具中各刀削部分的 机械加工 的质 量,因此 ,在深孔加工 中必须针对 不同的深孔加 应 面与被加 工的深孔之 间形成一种错开的孔径距 离,从而防范 工要 求采 用不 同的加工技术措施 ,最大限度保 证深 孔加工的质 了刀具在加 工过程 中对深孔表面可能会造成的损伤。 同时,单 量 安 全 。 刀刀具 的导 向部分 的尺 寸距离 要 比单 刀尖部 的直径 尺寸距 离 参考文献 小0 . 1 毫米 ,以防止刀具钻孔时出现偏 离直线距 离的状况 发生。 [ 1 ] 王峻 . 现代深 孔加工技 术 [ M] . 哈尔滨 : 哈 尔滨工 业大学 出 最后,在使用单 刀刀 具进行深孔加工时 ,该刀具导 向垫 的倒角 版社 ,2 0 0 5 . 角度应 设计为 1 8 度 角,这种角 度更有利 于将物件 切 削排 除 出 【 2 】 邓文英 . 机械加 工过程 中深孔加工技术探讨 [ J ] . 2 0 1 3( 0 8 ) : 去。 目前该种 刀具深孔加工方法广泛应用于种类实心 的铸件油 1 4 . 1 5 . 箱上,并在 其中起着较好 的应 用效 果。 [ 3 】 李伟光 . 机械 制造 中深孔加工技术 【 J 】 . 机械 工业论坛 ,2 0 1 4 3 . 2交错齿内排 削深 孔加工技术 ( 】 7) .
基于机械加工的深孔加工技术探析
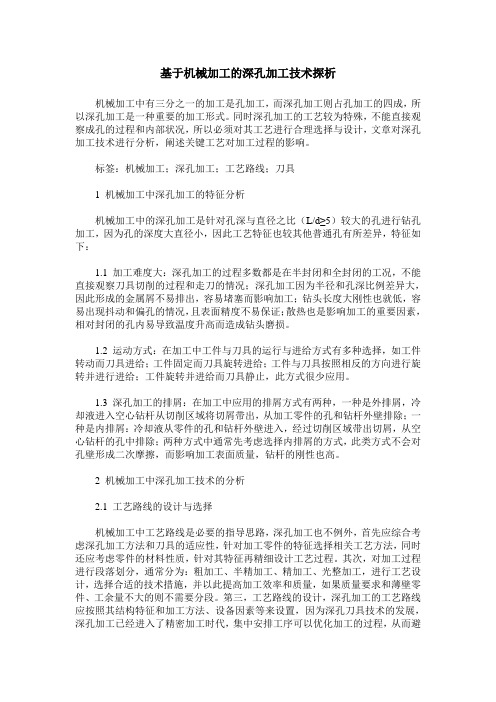
基于机械加工的深孔加工技术探析机械加工中有三分之一的加工是孔加工,而深孔加工则占孔加工的四成,所以深孔加工是一种重要的加工形式。
同时深孔加工的工艺较为特殊,不能直接观察成孔的过程和内部状况,所以必须对其工艺进行合理选择与设计,文章对深孔加工技术进行分析,阐述关键工艺对加工过程的影响。
标签:机械加工;深孔加工;工艺路线;刀具1 机械加工中深孔加工的特征分析机械加工中的深孔加工是针对孔深与直径之比(L/d≥5)较大的孔进行钻孔加工,因为孔的深度大直径小,因此工艺特征也较其他普通孔有所差异,特征如下:1.1 加工难度大:深孔加工的过程多数都是在半封闭和全封闭的工况,不能直接观察刀具切削的过程和走刀的情况;深孔加工因为半径和孔深比例差异大,因此形成的金属屑不易排出,容易堵塞而影响加工;钻头长度大刚性也就低,容易出现抖动和偏孔的情况,且表面精度不易保证;散热也是影响加工的重要因素,相对封闭的孔内易导致温度升高而造成钻头磨损。
1.2 运动方式:在加工中工件与刀具的运行与进给方式有多种选择,如工件转动而刀具进给;工件固定而刀具旋转进给;工件与刀具按照相反的方向进行旋转并进行进给;工件旋转并进给而刀具静止,此方式很少应用。
1.3 深孔加工的排屑:在加工中应用的排屑方式有两种,一种是外排屑,冷却液进入空心钻杆从切削区域将切屑带出,从加工零件的孔和钻杆外壁排除;一种是内排屑:冷却液从零件的孔和钻杆外壁进入,经过切削区域带出切屑,从空心钻杆的孔中排除;两种方式中通常先考虑选择内排屑的方式,此类方式不会对孔壁形成二次摩擦,而影响加工表面质量,钻杆的刚性也高。
2 机械加工中深孔加工技术的分析2.1 工艺路线的设计与选择机械加工中工艺路线是必要的指导思路,深孔加工也不例外,首先应综合考虑深孔加工方法和刀具的适应性,针对加工零件的特征选择相关工艺方法,同时还应考虑零件的材料性质,针对其特征再精细设计工艺过程。
其次,对加工过程进行段落划分,通常分为:粗加工、半精加工、精加工、光整加工,进行工艺设计,选择合适的技术措施,并以此提高加工效率和质量,如果质量要求和薄壁零件、工余量不大的则不需要分段。
基于机械加工的深孔加工技术探析

基于机械加工的深孔加工技术探析深孔加工是一种用于加工长孔或深孔的技术,通常用于制造汽车零部件、航空航天零部件、模具以及军事装备等领域。
这种加工技术广泛应用于工业生产中,而基于机械加工的深孔加工技术是其中的一个重要分支。
本文将从机械加工的角度,探析深孔加工技术的发展历程、优势及影响因素,以期为深孔加工技术的研究和应用提供参考。
一、深孔加工技术的发展历程深孔加工技术起源于18世纪,当时主要用于加工火炮管和火枪管。
随着工业化的进程和科学技术的进步,深孔加工技术得到了不断的发展。
在20世纪初期,传统的深孔加工方式主要是采用钻孔、铰削和扩孔等手工操作,效率低、精度差,且不能适应大批量生产的需要。
随着机械加工技术的不断进步,出现了很多新的深孔加工技术和设备。
目前,深孔加工技术已经广泛应用于机械制造、汽车工业、模具制造、航空航天等领域,成为现代制造业不可或缺的重要工艺之一。
随着工件的结构越来越复杂、生产效率的要求越来越高,深孔加工技术的要求也越来越高,传统的深孔加工方式已经不能满足工业生产的需要。
基于机械加工的深孔加工技术相对于传统的手工操作方式,有着诸多优势。
机械加工可以提高加工效率,保证产品的质量和精度。
机械加工设备可以进行自动化加工,减少了人工干预,提高了生产效率。
机械加工可以提高工作环境,减少对操作人员的要求。
传统的手工操作方式存在安全风险,而机械加工可以减少了这些风险。
机械加工可以减少生产成本,提高企业的竞争力。
自动化机械设备可以减少劳动力成本,提高生产效率,降低生产成本。
深孔加工技术的加工精度、表面光洁度、加工速度等方面受到很多因素的影响。
材料的选择对深孔加工的影响很大。
不同种类的材料对深孔加工的难度和要求不同,需要根据具体的材料特性来选择合适的机械加工设备和工艺。
深孔加工设备对加工效果也有很大的影响。
不同的设备有着不同的加工原理和加工精度,需要根据加工要求来选择合适的设备和工艺。
操作人员的技术水平也对深孔加工的影响不容忽视。
基于机械加工的深孔加工技术探析

基于机械加工的深孔加工技术探析一、引言深孔加工是一种特殊的加工方式,其对工件质量和加工精度要求非常高。
针对深孔加工技术,传统的机械加工方法在加工效率和加工质量方面都存在一定的局限性。
如何基于机械加工技术进行深孔加工是一个重要的课题。
本文将探索基于机械加工的深孔加工技术,分析其优势和不足,并对未来的发展方向进行展望。
二、传统机械加工中的深孔加工技术1. 深孔加工的难点及其解决方法深孔加工过程中的难点主要包括切削阻力大、刀具寿命短、加工精度难以控制等问题。
针对这些难点,传统的机械加工技术采用了一系列工艺改进和刀具优化措施,如采用特殊的刀具材料、提高刀具的刚性和韧性、优化刀具结构等方法。
这些改进措施在一定程度上提高了深孔加工的加工效率和加工质量,但仍然存在一定的局限性。
2. 传统机械加工的优势和不足传统机械加工方法在深孔加工中有其独特的优势,如设备成本低、加工精度高、加工表面质量好等。
但传统机械加工方法在面对深孔加工时,由于工件材料和加工尺寸的限制,存在加工效率低、加工精度难以控制等问题。
1. 刀具技术的发展随着刀具制造技术的不断进步,新型刀具材料和刀具涂层技术的应用,保障了刀具的寿命和性能。
新一代的刀具结构设计也在提高切削效率的降低了切削温度和切削力,有利于深孔加工过程中的稳定加工。
2. 设备技术的改进基于机械加工的深孔加工技术中,设备的改进也是一个重要的方向。
随着数控技术的发展,深孔加工设备的自动化程度不断提高,加工精度和稳定性得到了显著提升。
一些新型的深孔加工设备在结构上也有所突破,如多轴切削、自动化刀具更换等技术的应用,进一步提高了深孔加工设备的灵活性和效率。
3. 加工工艺的优化在基于机械加工的深孔加工技术中,加工工艺的优化也是一个重要的方向。
通过优化切削参数、采用新型的切削液和切削方式等措施,可以提高深孔加工的效率和精度。
基于数字化加工的优化方法也在不断发展,通过建立数学模型和仿真分析,提高深孔加工的过程控制和优化效果。
基于机械加工的深孔加工技术探析
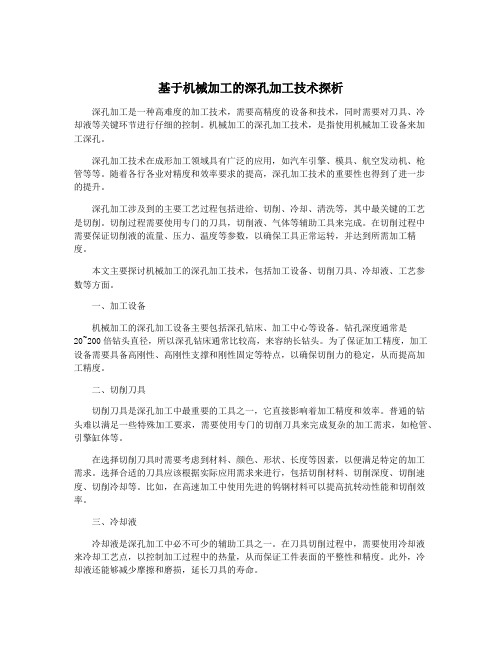
基于机械加工的深孔加工技术探析深孔加工是一种高难度的加工技术,需要高精度的设备和技术,同时需要对刀具、冷却液等关键环节进行仔细的控制。
机械加工的深孔加工技术,是指使用机械加工设备来加工深孔。
深孔加工技术在成形加工领域具有广泛的应用,如汽车引擎、模具、航空发动机、枪管等等。
随着各行各业对精度和效率要求的提高,深孔加工技术的重要性也得到了进一步的提升。
深孔加工涉及到的主要工艺过程包括进给、切削、冷却、清洗等,其中最关键的工艺是切削。
切削过程需要使用专门的刀具,切削液、气体等辅助工具来完成。
在切削过程中需要保证切削液的流量、压力、温度等参数,以确保工具正常运转,并达到所需加工精度。
本文主要探讨机械加工的深孔加工技术,包括加工设备、切削刀具、冷却液、工艺参数等方面。
一、加工设备机械加工的深孔加工设备主要包括深孔钻床、加工中心等设备。
钻孔深度通常是20~200倍钻头直径,所以深孔钻床通常比较高,来容纳长钻头。
为了保证加工精度,加工设备需要具备高刚性、高刚性支撑和刚性固定等特点,以确保切削力的稳定,从而提高加工精度。
二、切削刀具切削刀具是深孔加工中最重要的工具之一,它直接影响着加工精度和效率。
普通的钻头难以满足一些特殊加工要求,需要使用专门的切削刀具来完成复杂的加工需求,如枪管、引擎缸体等。
在选择切削刀具时需要考虑到材料、颜色、形状、长度等因素,以便满足特定的加工需求。
选择合适的刀具应该根据实际应用需求来进行,包括切削材料、切削深度、切削速度、切削冷却等。
比如,在高速加工中使用先进的钨钢材料可以提高抗转动性能和切削效率。
三、冷却液冷却液是深孔加工中必不可少的辅助工具之一。
在刀具切削过程中,需要使用冷却液来冷却工艺点,以控制加工过程中的热量,从而保证工件表面的平整性和精度。
此外,冷却液还能够减少摩擦和磨损,延长刀具的寿命。
在选择冷却液时需要考虑到加工材料、刀具材料、加工深度等因素。
一般来说,深孔加工需要使用专门的冷却液,可以根据加工工艺的不同而调整冷却液的化學成分和流量,以达到最佳的效果。
机械加工深孔加工技术研究论文

机械加工深孔加工技术研究论文机械加工深孔加工技术研究论文一、研究背景深孔加工是目前机械加工领域的一个热门技术,适用于制作特制的精密孔和精密轴。
特别是在一些外国企业的高精密加工领域和国防军工等领域,深孔加工都被广泛应用。
深孔加工在航天、军工、锅炉和化工等高端制造领域有着重要的地位。
然而,由于深孔加工的特殊性,其难度和风险相对较高。
长时间的孔加工过程和复杂的孔形结构都会给孔加工带来较大的不确定性和变异性等风险。
因此,在深孔加工领域,深入研究其加工技术和优化方法,提高深孔加工的加工质量和效率,对于提升我国制造业的技术水平和产品质量有着重要的意义。
二、研究内容和方法本论文通过对深孔加工的研究和实际应用,系统地分析了深孔加工技术的相关原理、特点和应用方法。
并在此基础上,提出了一种优化深孔加工的方法。
该方法主要涉及到以下几个方面:1. 工艺参数优化,在保证加工质量、安全性和效率的基础上,寻求合适的加工参数组合。
这里所指的工艺参数包括加工切削速度、进给速度、切削深度和加工精度等。
2. 加工设备优化,根据加工孔的形状和材料特性,合理选择深孔加工机床和刀具。
对于不同的孔型,采用不同类型的刀具和工艺流程,以保证加工的效率和质量。
3. 加工过程监控,在加工过程中通过监控切削力、温度和位移等参数,实时反馈并控制加工过程。
通过数据分析和处理,优化加工过程控制,提高加工质量。
4. 刀具润滑改进,在切削过程中应选用合适的刀具润滑方式,以降低切削力和工具磨损程度,提高加工效率和质量。
本论文的实验内容主要包括了深孔加工试样制作、加工参数优化和加工质量评估等。
通过分析加工过程中的各项参数,对加工效率和质量进行了比较和分析。
三、研究结论通过本研究的实验和分析,可以得出以下结论:1. 在深孔加工中,加工参数的选择和优化是关键。
不同的参数组合会直接影响加工效率和加工质量。
因此,应选用适合的参数组合以保证加工效果。
2. 加工设备对于深孔加工的影响较大。
机械加工中深孔加工技术的研究

机械加工中深孔加工技术的研究摘要:在机械工程行业壮大发展的背景下,机械化工艺水平,深加工技术在现实生产活动中得到了广泛应用,该项技术虽然能创造出较好的效益,但是客观上讲技术应用中还滞留着一些问题。
本文简单分析了深孔加工技术应用的重点与难点,包括技术操作难度较高、钻孔操作有应局限性、碎屑外排环节有问题等,简单分析以上状况的成因,以促进深加工技术有效应用为目标,总结技术要点及应用策略,希望能给同行实践过程带来些许帮助。
关键词:机械化加工;深加工;难点分析;技术应用引言机械加工制造是我国的传统行业之一,其直接关系着国民经济的整体发展水平。
机械化加工生产中可供选择的技术方法有很多,深加工就是其一,其在促进我国机械加工水平全面提升方面表现出良好效能。
深孔通常是孔长度和直径比大于5~10的孔。
通常而言,在机械化加工生产中,深孔的实际加工数量在总量内占比约50%。
综合以上数据,能够认识到做好深孔加工工作的必要性。
为了能全面提升深孔加工效率与质量,应积极研发适宜且高效化的深孔加工技术,并结合实际情况持续完善技术应用过程,彰显新技术的优势,促进我国机械行业获得更大的发展进步。
1深孔加工技术的重点和难点1.1技术应用难度较高主要体现在如下几个方面[1]:一是基本上是孔径小,孔深大的条件下进行生产,受限于设备或刀具因素的制约,加工时出口位置容易产生偏差。
二是由于孔深大,切削过程中切屑不能及时有效地排出孔,以致加工时容易发生金属屑堵塞造成孔壁局部的不良状况,甚至刀具断裂的情况。
三是配备的钻头及定位夹具均会对深孔加工技术应用效果产生较大的影响。
长时间进行深孔加工作业会导致定位导向件发生不同程度的磨损问题,以致深孔半径、深度等指标和设计要求之间出现很大的出入,不仅影响加工的精准度,还弱化深孔加工技术的价值。
四是造成钻头及加工夹具发生磨损情况的因素不唯一,而加工部位的冷却效果差、温度较高等被认定是引起磨损问题的两大主因。
1.2深孔钻加工有一定局限性钻孔作业过程中,加工零件的材质可切削性,被加工的孔深与孔径比例也局限于加工条件,钻孔的刀具刚性和排屑效果也会限制深孔的加工质量。
基于机械加工的深孔加工技术探析

基于机械加工的深孔加工技术探析
深孔加工技术是现代制造业中非常重要的加工技术之一,其能够满足高精度、高效率、高成品率的制造要求,被广泛应用于机械零部件、航空航天、船舶、汽车、轨道交通等领域。
深孔加工技术常常被用于制造一些形状特殊、长度细长的工件,如轴类、齿轮、导杆、液压系统体、汽车发动机等系统。
随着工业的进步和科技技术的提升,深孔加工技术也在
不断地发展和完善,其中基于机械加工的深孔加工技术是目前应用最广泛的一种。
机械加工的深孔加工技术包括铰孔、钻孔、加拉棒等多种方法,其核心原理是将加工
工件安装在机床上,在工件的轴线上加工出一定深度的孔。
机械加工的深孔加工技术的加
工精度和形状精度较高,加工效率也相对较高,更适合加工要求不高的普通深孔。
机械加
工的深孔加工技术具有结构简单、生产效率较高、精度控制容易等特点,因此在一些场合
中仍然扮演着重要的角色。
但机械加工的深孔加工技术也存在一些缺点,其中最主要的就是加工效率较低、操作
繁琐。
虽然加速主轴转速、节省起动时间等措施可以提高机械加工深孔加工技术的效率,
但这些措施会加剧工具磨损、缩短机床的寿命等问题,同时对机床的要求也更高。
为了克服机械加工深孔加工技术的缺点,现在科学家们正在不断研究新的深孔加工技术,如激光深孔加工、电化学深孔加工、微细加工等。
在这些新技术的引领下,深孔加工
技术必将得到更好的应用和推广,进一步推动着制造业的发展。
机械加工深孔加工技术研究的论文

机械加工深孔加工技术研究的论文摘要:随着工业的不断发展,对于深孔加工技术的需求也越来越大。
深孔加工是指在工件中加工出较大长度宽径比的孔。
本文通过分析机械加工深孔加工技术的研究现状和存在的问题,提出了一种改进的深孔加工技术,并进行了实验验证。
实验结果表明,改进的深孔加工技术能够提高加工效率和质量,具有较好的应用前景。
关键词:机械加工;深孔加工;技术;研究1.引言深孔加工技术作为一种重要的加工工艺,在航空航天、汽车制造、兵器制造等领域中有着广泛的应用。
随着工业的快速发展,对于深孔加工技术的需求也越来越大。
然而,由于深孔加工存在加工难度大、加工效率低以及加工质量不稳定等问题,限制了其进一步的应用和发展。
2.研究现状深孔加工技术的研究主要集中在以下几个方面:材料选型、切削力分析、润滑冷却技术、切削参数优化等。
其中,材料选型是深孔加工中一个重要的环节,需要选择适合的刀具和工件材料组合,以提高加工效果和延长刀具寿命。
切削力分析能够帮助工程师更好地理解深孔加工过程中力的变化规律,从而指导实际生产中的操作。
润滑冷却技术是深孔加工中的一个关键技术,可以降低加工温度、减少刀具磨损和延长刀具寿命。
切削参数优化能够通过分析加工条件和材料特性,提高加工效率和质量。
3.存在问题虽然深孔加工技术已经有了一定的研究成果,但仍然存在一些问题。
首先,深孔加工过程中的切削力和切削温度较大,容易导致刀具的磨损和加工质量的下降。
其次,传统的润滑冷却技术对于深孔加工来说效果不佳,需要进一步改进。
最后,深孔加工技术的加工效率较低,需要采取一些措施来提高效率。
4.改进技术针对深孔加工技术存在的问题,本文提出了一种改进的深孔加工技术。
首先,在材料选型方面,选择了适合的刀具和工件材料组合,以提高加工效果和延长刀具寿命。
其次,在切削力和切削温度方面,采用了刀具涂层和冷却剂的方式来降低切削力和切削温度,减少刀具磨损和提高加工质量。
最后,在加工效率方面,通过优化切削参数,提高加工效率和质量。
机械加工中的深孔加工技术研究

机械加工中的深孔加工技术研究发布时间:2021-09-06T05:47:43.076Z 来源:《时代建筑》2021年10期5月下作者:厉恩贵[导读] 目前,我国机械制造业蓬勃发展,特别是在各类机械产品需求稳步增长的今天,机械制造业的发展进程加快。
临海伟星新型建材有限公司厉恩贵 317000摘要:目前,我国机械制造业蓬勃发展,特别是在各类机械产品需求稳步增长的今天,机械制造业的发展进程加快。
因此,为了更好地应对机械制造的创新,需要相应地开发一些新技术,其中深孔加工技术是最好的技术之一。
该技术可有效地应用于机械加工中的钻削环节,能直观地探索孔的内部情况,从而获得最佳的施工效率。
因此,本文对机械加工中深孔加工的加工工艺进行了探讨,以期为相关加工工作者提供参考。
关键词:机械加工;技术;深孔加工;特征 1深孔加工简介深孔加工主要针对孔深l与孔直径D之比。
当L/D比大于5时,该类型加工为深孔加工,反之为浅孔加工。
例如,油缸孔和轴向油孔属于深孔加工的范畴。
由于不同机械设备对孔的加工精度不同,在深孔加工过程中,必须根据加工精度要求进行相应的质量控制。
深孔加工技术在切削过程中,刀杆受孔径因子的限制,在切削过程中容易产生振动,导致深孔表面粗糙度达不到加工要求。
此外,在深孔加工过程中,也很难去除切屑。
在加工过程中,必须采用科学的处理手段,避免堵塞等现象。
2机械加工中深孔加工的特点2.1处理非常困难在深孔加工过程中,通常采用半封闭或全封闭的方式进行加工。
因此,加工过程中不能直接看到刀具切削或走刀的场景,由于孔深的深度半径和深孔的比重之间的深度差非常大。
在加工过程中,其产生的一些金属碎屑通常难以排出,容易造成堵塞,影响产品加工。
此外,加工过程中使用的圆形钻头很长。
由于使用时间长,其机械刚度大大降低,很容易直接产生温度抖动和孔刚度偏差,难以有效保证产品表面处理精度。
2.2操作模式非常复杂在进行深孔加工时,由于工件和刀具的活动和进给方式多种多样,其活动通常非常繁琐,必须根据加工的实际情况进行选择。
基于机械加工的深孔加工技术探析

在发展现状方面,深孔加工技术逐渐向高效、自动化、数字化方向发展。一些先进的数控深孔加工设备逐渐取代传统的手动操作,实现了加工过程的自动化和智能化。一些新型工具材料的应用也为深孔加工技术的进步提供了重要支持。超硬合金钻头、刀具等,不仅能够提高加工效率,还能够有效延长工具的使用寿命。
针对深孔加工技术的关键问题,基于机械加工的深孔加工技术探索正在不断进行。通过优化加工工艺、改进加工设备等手段,可以提高深孔加工的效率和精度,使其更加符合工件加工的要求。
基于机械加工的深孔加工技术探索是当前深孔加工领域的热点研究之一。通过不断探索和创新,相信深孔加工技术将会实现更大的突破和发展,为工件加工领域带来更多的机遇和挑战。
2. 深孔加工技术的发展不仅可以推动机械加工行业的技术进步,还可以促进相关工业领域的发展。研究基于机械加工的深孔加工技术,有助于完善该技术的应用范围,提高加工精度和加工质量,推动工业制造的数字化、智能化发展。
3. 深孔加工技术的研究还可以促进我国在机械加工领域的自主创新能力提升。通过深入研究基于机械加工的深孔加工技术,可以提高我国机械加工领域的核心技术水平,推动国内相关产业的发展,实现从"Made in China"向"Created in China"的转变。
深孔加工技术在提升工件加工质量、提高生产效率、节约成本等方面都有着显著的贡献。机械加工作为深孔加工的主要手段,通过不断创新和发展,为深孔加工技术的进步提供了强有力的支持。
在实际应用中,仍然存在一些问题和挑战,如加工精度的提高、加工效率的进一步提升、设备性能的改进等。需要不断的研究和探索,进一步完善技术,以满足不断增长的市场需求。
【关键词】
深孔加工、机械加工、技术探析、发展现状、关键问题、未来发展、研究展望
基于机械加工的深孔加工技术探析

基于机械加工的深孔加工技术探析1. 引言1.1 研究背景深孔加工是一种在工件中加工深孔的高精度加工技术,广泛应用于航空航天、汽车、机械制造等领域。
随着工件结构和材料的不断创新,深孔加工技术也在不断发展和完善。
基于机械加工的深孔加工技术是深孔加工技术中的一种重要方法,它采用机械设备和工具来实现对工件深孔的加工,具有工艺简单、成本低廉等优点。
目前基于机械加工的深孔加工技术还存在一些问题和挑战,如加工精度难以保障、加工效率低下等。
开展对基于机械加工的深孔加工技术的研究和探索具有重要意义。
本文旨在对基于机械加工的深孔加工技术进行深入分析与探讨,为进一步提高深孔加工技术的加工精度和效率提供参考和借鉴。
1.2 研究目的研究目的是为了深入探讨基于机械加工的深孔加工技术,分析其在工业生产中的应用情况及优缺点。
通过对深孔加工技术的概述和基于机械加工的深孔加工技术的详细介绍,我们旨在揭示其在现代制造业中的重要性和价值。
我们希望通过工艺流程的分析和对技术优缺点的对比,为工程技术人员提供更加全面和深入的了解,以便在实际生产中更好地选择和应用相应的加工技术。
通过探讨深孔加工技术在不同应用领域中的具体应用情况,我们可以更好地了解其适用范围和潜在发展方向,从而为未来深孔加工技术的研究和应用提供有效的参考依据。
通过本次研究,我们旨在为深孔加工技术的发展和工业生产的进步做出积极的贡献。
1.3 意义深孔加工技术在现代制造业中扮演着重要角色,其在航空航天、汽车制造、模具加工等领域都有着广泛的应用。
通过深孔加工,可以实现对工件内部复杂结构的加工,提高工件的精度和表面质量,满足高精度加工的需求。
深孔加工技术的研究和应用具有重要的意义。
深孔加工技术的发展可以促进制造业技术的进步。
随着制造业的发展和对产品精度要求的不断提高,深孔加工技术的研究将推动相关加工设备和工艺的创新,提高产品质量和生产效率。
深孔加工技术的应用还可以提高产品的性能和可靠性。
基于机械加工的深孔加工技术探析

基于机械加工的深孔加工技术探析深孔加工技术在现代工业生产中被广泛应用,尤其在航空航天、汽车、军工等领域有着重要的地位。
而机械加工是深孔加工技术中最主要的方式。
本文将从机床结构、刀具选择、液压系统等方面对基于机械加工的深孔加工技术进行探析。
一、机床结构深孔加工对机床的精度、刚度、稳定性等有着较高的要求,因此机床结构的设计是深孔加工技术成功的关键。
首先,机床刚度需要足够高,以保证切削力的传递和加工精度的保持。
其次,机床必须保持稳定,以减小振动对加工质量的影响。
最后,机床必须具有足够的重复精度和位置精度。
二、刀具选择在深孔加工中,刀具的选择对加工效果有着至关重要的作用。
刀具应具有足够的硬度、耐磨性和刚度,以抵消切削力和切削热对刀具的影响。
常见的深孔加工刀具有极长锥度钻、深孔钻、铰孔钻、钻孔刀、拓孔钻等。
三、液压系统在深孔加工过程中,液压系统的设计和运用同样是非常重要的。
液压系统主要用于冷却和润滑,以及对工件和刀具施加足够的切削力。
液压系统的设计要求具有足够的流量和压力,以保证冷却和润滑过程的有效性,同时也要保证切削力的平衡和精度的保持。
四、加工参数在深孔加工中,加工参数的选择对加工质量和效率有着决定性的作用。
常见的加工参数包括切削速度、进给量、切削深度等。
切削速度应根据刀具材质、加工材料等因素进行综合考虑,以保证刀具的寿命和加工效率。
进给量应根据不同加工情况进行选择,一般来说,进给量越小,加工精度越高,但加工时间也会相应增加。
切削深度应根据刀具和材料性质等综合考虑,以保证加工效率和加工表面质量。
综上所述,机械加工是深孔加工技术中最主要的方式,机床结构的设计、刀具选择、液压系统和加工参数的选择对于加工质量和效率有着至关重要的作用。
深孔加工技术的不断发展和改进将会有着广泛的应用前景。
基于机械加工的深孔加工技术探析

基于机械加工的深孔加工技术探析深孔加工技术是指在工件中加工直径远大于加工长度的孔,一般来说,当加工孔径与加工长度之比大于10时,即可称为深孔加工。
机械加工是指利用机械化设备进行金属材料加工的过程。
基于机械加工的深孔加工技术是指利用机械加工设备进行深孔加工的方法和技术。
本文将对基于机械加工的深孔加工技术进行探析。
基于机械加工的深孔加工技术的主要挑战之一是如何保持加工稳定性。
由于深孔加工时钻头与工件之间的接触面积较小,切削力相对较大,容易引起刀具振动和共振。
为了保持加工的稳定性,可以采用以下几种方法:1. 使用刚性刀具:选择合适的材质和加工精度高的刀具,提高加工的稳定性。
2. 采用合适的切削参数:根据工件材料和加工条件,选择合适的切削速度、进给速度和切削深度,减小切削力,降低振动。
3. 使用刀具防护套管:在深孔加工时,可以添加刀具防护套管,增加刚性,减少振动。
基于机械加工的深孔加工技术还需要考虑如何提高加工精度。
深孔加工对加工精度要求较高,需要考虑以下几个方面:1. 刀具选择:选择适合加工需要的刀具,如深孔钻头、刀柄等,刀具的刚性和精度对加工精度有重要影响。
2. 加工稳定性:如前所述,保持加工的稳定性可以有效提高加工精度。
3. 冷却润滑:深孔加工时容易产生高温,使用合适的切削液冷却,并提供足够的润滑,可以减少热变形,提高加工精度。
1. 刀具进给系统:采用高速进给刀具系统,提高切削速度和进给速度,减少加工时间。
2. 自动化控制:采用自动化控制系统,如数控机床,可以实现自动换刀、自动切削控制,提高生产效率。
3. 刀具润滑系统:采用高效的切削液供给系统,保持切削液的稳定喷射,减少切削液的浪费,提高加工效率。
基于机械加工的深孔加工技术是一种可靠和高效的加工方法。
通过合理选择刀具、优化切削参数和采用自动化控制等手段,可以提高加工的稳定性、精度和效率,满足工业生产的需求。
机械加工中的深孔加工技术分析

误差 ,将各道加工环节效果做到最好 ,进而提高整体加工质量 。
2 . 3 加 工 刀 具 的 选 择
1 深孔加工技术的特点
1 . 1 从深孔加工技术方面 而言 。难度较 高
如何 判断其切削情况极 为复杂 , 在机 械进 行深孔加工过程 中大部 分都采 用半封闭式或者全封 闭模 式 , 其 中不可直观查看 刀具 的切削状 况 ,而要 通过 听加工过程 中的声音 、检查 切削效果 以及观测仪 表等 人 工方式判 断,这也是 这种技术 方法 的一大难 点。由于深孔的长度问题 , 使用 的深 孔钻刀具过于纤细 ,导致 其刚性降低 ,易受外界 因素 影响出 现钻孔走偏现象 。
工 业 技 术
柬工案 捉术
1 8
机械 加工 中的深 孔加工 技术分析
王 子 山
( 济 宁职 业技 术学院 , 山东 济宁 2 7 2 0 0 0)
摘 要 :随着现 代工艺的不断进步 ,各类 器械原件加 工要 求更加精 密 , 对 机械加工 的深孔技术有 了更高要 求 机械加 工中孔加 工作 业 占 据 了大 约 3 0 N的工作 量,而深孔加 工又是孔加工作业的重要部分 ,对加 工技 术有 着更 高要求。鉴 于深孔加工 不能直接观察成孔过程和 了解 内部状 况的 特殊情 况, 必须对深孔加工工艺进行科学合理的设计 , 解决加工中 出现的 问题 , 以此提 高深 孔加 工的效果和质量 。 本文对深孔加工技术进行探讨 , 希望对深孔加 工质量 的提 高提供 帮助 。
一
刀具是加工机床的关键部分 , 同时也是深孔加工的直接作业工具 , 因此 ,加工刀具 的选择 对深 孔加工效果而言尤为重要 。深孔加工 因不 同加工需求可采 用扁钻、枪钻、麻花钻 、复合刀具等刀具 ,具有较强 的专业性 。因此深 孔加工时 ,针对不 同工作需要 ,合理选择相应加工 刀具 ,才能确保加工刀具能够达到理想的加工效果 。 2 . 4 加工定位的精准性 深孔加工是一项精 密的机械加工工序 ,其每个深孔定位的准确性 直接决定 了该深 孔加工的质量 。深孔加工定位方式有许多种 ,其 中锥 面定位是最为常 见和 有效的定位方式 ,通常应用在 回转体 、中小直径 孔 、管坯镗孔加 工定 位中 ,在定位操作 中,需特别注意保证直线度和 余量 ,处理好深 孔加 工前的端面处理 内外锥面 。另外 ,在 中等直径 的 内排切削 加工 中主要 应用 内锥面定位方式 。而大孔 径的深孔加工 一般 采用 圆定位方 式 , 这 种定位方式是利用 同心 圆定理 ,将外 圆面上加工 的安装面 、定 位面和 找正面确定为 同心 圆,进而保证深孔加工定位 的 准确性 。无论 哪种定 位方法 ,都是为提高深孔加工质量而服务 的,应 重点关注深孔加工的定位操作 。
基于机械加工的深孔加工技术探析

基于机械加工的深孔加工技术探析发表时间:2019-09-06T09:49:12.727Z 来源:《防护工程》2019年12期作者:隋少玲[导读] 并对其中的关键工艺和过程进行分析,指出深孔加工技术中应当注意的技术要点。
费斯托气动有限公司山东省济南市 250100摘要:在机械加工中超 30%的部分需要进行孔加工,其中深孔加工占据孔加工比例的 40%,因此深孔加工是机械加工的重要形式之一。
深孔加工工艺特殊,无法直接观察到孔内部的情况,因此必须合理选择和设计孔加工的技术和工艺。
文章对深孔加工技术相关内容进行简述,并对其中的关键工艺和过程进行分析,指出深孔加工技术中应当注意的技术要点。
关键词:机械加工;深孔;加工技术1深孔加工技术的技术特点1.1深孔加工技术难度大首先,绝大部分的深孔加工在半封闭或者是全封闭的环境下实施,因此,加工切削以及走刀等问题工作人员无法直接的进行观察;其次,通常来说,深孔的半径与孔深两者之间的比值比较大,正因如此,容易出现金属屑难以排出堵塞孔洞的情况;最后,过长的钻头所导致的问题是会大幅度的降低钻头的刚性,以至于出现偏孔或者是抖动等方面的问题,也就难以有效的保障深孔加工的精度;此外,孔洞加工散热问题的影响,封闭环境下孔洞内温度上升会导致钻头的磨损。
1.2运动方式本身具有特殊性在深孔整个加工过程之中,工件以及刀具两者之间可以采用多种相互运行的方式,其中,就包括工件转动同时刀具进给;工件固定同时刀具进给以及二者以相反方向运行进给等,如何选择不同的运动方式是深孔加工技术使用的重点问题之一。
1.3深孔加工排屑问题深孔加工中排屑问题也是应当重点关注的问题之一,排屑方式主要分为两种,第一种是外排屑,在孔心钻杆处倒入冷却液,将切屑从切削区清理出;第二种是内排屑,在孔和钻杆外壁处倒入冷却液,将切屑从切削区域带出。
在实际加工过程中一般优先考虑内排屑加工方式,因为该方式不会造成孔壁二次摩擦,钻杆刚性较高更不会影响孔洞的表面质量。
基于机械加工的深孔加工技术探析

基于机械加工的深孔加工技术探析摘要:深孔加工是重要的加工形式之一,因为在加工过程中必须加工30%以上的孔,而深孔加工占孔加工率的40%。
深孔加工技术很特殊,不能直接观察孔的内部,因此必须合理选择和设计孔加工技术和工艺。
本文简要介绍了深孔加工技术的相关内容,分析了主要工序和工艺,并指出了深孔加工技术中应注意的技术要点。
关键字:机械加工;深孔;加工技术1深孔处理技术的技术特征1.1深孔加工技术很困难首先,大多数深孔加工是在半封闭或完全封闭的环境中进行的,因此无法直接观察到诸如加工,切削和切削之类的操作人员。
因为孔的半径与深度之间的比率较大,所以它会排干金属屑并使孔难以堵塞。
毕竟,如果钻头太长,则会出现严重降低钻头刚性的问题。
由于孔偏移或抖动等问题,难以有效地保证深孔加工的精度,并且由于孔加工的散热问题,在封闭环境下,由于孔的温度升高,钻头可能会磨损。
1.2锻炼方法本身很特殊在深孔加工的整个过程中,可以通过多种方式来操作工件和刀具,其中工件旋转并且刀具同时进给。
固定工件并同时进给刀具。
选择多种运动方法,例如定向进给,是使用深孔加工技术的主要挑战之一。
1.3深孔加工中的排屑问题深孔加工中的排屑问题是要重点解决的问题之一,排屑方法主要分为两种。
首先是外部排屑。
将冷却液倒入岩心钻杆中以清除切屑。
切割区域已清洁。
第二个是去除内部切屑,将其倒入钻杆的孔和外壁中以从切削区域去除切屑。
在实际的加工过程中,内部排屑处理方法通常是优选的,因为该方法不会引起孔壁的二次摩擦,并且钻杆的高刚度不会影响孔的表面质量。
2深孔加工中冷却润滑液的作用在深孔加工中,冷却润滑剂不仅可以快速消除钻孔过程中产生的热量,润滑工具和工件,还可以减少两者之间的摩擦,并需要使用更重要的压力和流动冷却剂。
冲洗切屑以达到去除切屑的目的。
切屑很容易堵塞切屑疏散通道并影响工具的正常使用。
当切屑堵塞在切屑出口中时,刀片会被挤压,发生切屑并影响切削过程。
当热量积聚在孔中时,钻头会变干,形成一个内置边缘,该边缘会使刀片变钝,“刮擦”工件,破坏钻头并破坏边缘。
基于机械加工的深孔加工技术研究
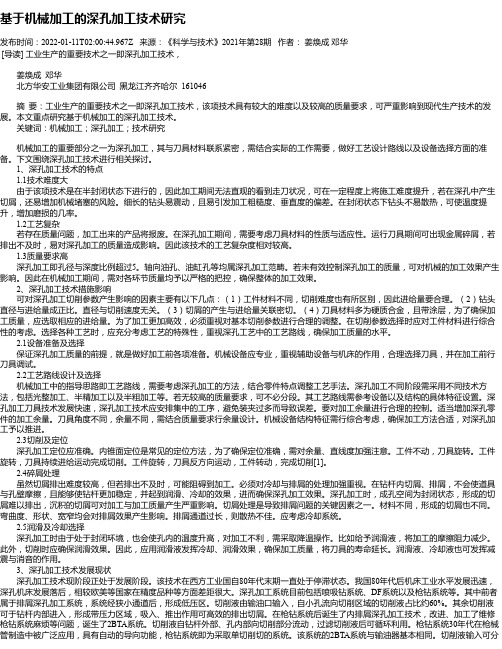
基于机械加工的深孔加工技术研究发布时间:2022-01-11T02:00:44.967Z 来源:《科学与技术》2021年第28期作者:姜焕成邓华[导读] 工业生产的重要技术之一即深孔加工技术,姜焕成邓华北方华安工业集团有限公司黑龙江齐齐哈尔 161046摘要:工业生产的重要技术之一即深孔加工技术,该项技术具有较大的难度以及较高的质量要求,可严重影响到现代生产技术的发展。
本文重点研究基于机械加工的深孔加工技术。
关键词:机械加工;深孔加工;技术研究机械加工的重要部分之一为深孔加工,其与刀具材料联系紧密,需结合实际的工作需要,做好工艺设计路线以及设备选择方面的准备。
下文围绕深孔加工技术进行相关探讨。
1、深孔加工技术的特点1.1技术难度大由于该项技术是在半封闭状态下进行的,因此加工期间无法直观的看到走刀状况,可在一定程度上将施工难度提升,若在深孔中产生切屑,还易增加机械堵塞的风险。
细长的钻头易震动,且易引发加工粗糙度、垂直度的偏差。
在封闭状态下钻头不易散热,可使温度提升,增加磨损的几率。
1.2工艺复杂若存在质量问题,加工出来的产品将报废。
在深孔加工期间,需要考虑刀具材料的性质与适应性。
运行刀具期间可出现金属碎屑,若排出不及时,易对深孔加工的质量造成影响。
因此该技术的工艺复杂度相对较高。
1.3质量要求高深孔加工即孔径与深度比例超过5。
轴向油孔、油缸孔等均属深孔加工范畴。
若未有效控制深孔加工的质量,可对机械的加工效果产生影响。
因此在机械加工期间,需对各环节质量均予以严格的把控,确保整体的加工效果。
2、深孔加工技术措施影响可对深孔加工切削参数产生影响的因素主要有以下几点:(1)工件材料不同,切削难度也有所区别,因此进给量要合理。
(2)钻头直径与进给量成正比。
直径与切削速度无关。
(3)切屑的产生与进给量关联密切。
(4)刀具材料多为硬质合金,且带涂层,为了确保加工质量,应选取相应的进给量。
为了加工更加高效,必须重视对基本切削参数进行合理的调整。
- 1、下载文档前请自行甄别文档内容的完整性,平台不提供额外的编辑、内容补充、找答案等附加服务。
- 2、"仅部分预览"的文档,不可在线预览部分如存在完整性等问题,可反馈申请退款(可完整预览的文档不适用该条件!)。
- 3、如文档侵犯您的权益,请联系客服反馈,我们会尽快为您处理(人工客服工作时间:9:00-18:30)。
基于机械加工的深孔加工技术探析作者:李恒扬来源:《科技创新与应用》2014年第02期摘要:机械加工中有三分之一的加工是孔加工,而深孔加工则占孔加工的四成,所以深孔加工是一种重要的加工形式。
同时深孔加工的工艺较为特殊,不能直接观察成孔的过程和内部状况,所以必须对其工艺进行合理选择与设计,文章对深孔加工技术进行分析,阐述关键工艺对加工过程的影响。
关键词:机械加工;深孔加工;工艺路线;刀具1 机械加工中深孔加工的特征分析机械加工中的深孔加工是针对孔深与直径之比(L/d≥5)较大的孔进行钻孔加工,因为孔的深度大直径小,因此工艺特征也较其他普通孔有所差异,特征如下:1.1 加工难度大:深孔加工的过程多数都是在半封闭和全封闭的工况,不能直接观察刀具切削的过程和走刀的情况;深孔加工因为半径和孔深比例差异大,因此形成的金属屑不易排出,容易堵塞而影响加工;钻头长度大刚性也就低,容易出现抖动和偏孔的情况,且表面精度不易保证;散热也是影响加工的重要因素,相对封闭的孔内易导致温度升高而造成钻头磨损。
1.2 运动方式:在加工中工件与刀具的运行与进给方式有多种选择,如工件转动而刀具进给;工件固定而刀具旋转进给;工件与刀具按照相反的方向进行旋转并进行进给;工件旋转并进给而刀具静止,此方式很少应用。
1.3 深孔加工的排屑:在加工中应用的排屑方式有两种,一种是外排屑,冷却液进入空心钻杆从切削区域将切屑带出,从加工零件的孔和钻杆外壁排除;一种是内排屑:冷却液从零件的孔和钻杆外壁进入,经过切削区域带出切屑,从空心钻杆的孔中排除;两种方式中通常先考虑选择内排屑的方式,此类方式不会对孔壁形成二次摩擦,而影响加工表面质量,钻杆的刚性也高。
2 机械加工中深孔加工技术的分析2.1 工艺路线的设计与选择机械加工中工艺路线是必要的指导思路,深孔加工也不例外,首先应综合考虑深孔加工方法和刀具的适应性,针对加工零件的特征选择相关工艺方法,同时还应考虑零件的材料性质,针对其特征再精细设计工艺过程。
其次,对加工过程进行段落划分,通常分为:粗加工、半精加工、精加工、光整加工,进行工艺设计,选择合适的技术措施,并以此提高加工效率和质量,如果质量要求和薄壁零件、工余量不大的则不需要分段。
第三,工艺路线的设计,深孔加工的工艺路线应按照其结构特征和加工方法、设备因素等来设置,因为深孔刀具技术的发展,深孔加工已经进入了精密加工时代,集中安排工序可以优化加工的过程,从而避免多次装夹而出现误差。
最后,合理控制加工余量,深孔零件的加工余量与其他孔不同,余量应增加,不同刀具和刀具角度余量也不同,如单刃铰刀比多刃铰刀余量大,偏角大的比偏角小的余量大等,所以在加工中必须按照相应的工艺和质量要求来设计余量。
2.2 深孔加工的刀具选择按照不同的深孔表面要求,选择适应的刀具也十分重要。
在加工中常见的刀具有:扁钻、麻花钻、外排屑深孔钻、内排屑深孔钻、喷吸钻、枪钻、复合刀具等。
具体应用情况如下:(1)扁钻:从结构上分为整体扁钻和装配扁钻,整体扁钻结构相对简单,生产与加工容易,对硬度高的铸件和锻件适用。
装配式扁钻刀杆的刚性大,刀片则是高速钢或者合金,可实现快速更换,且可以打磨成各种形状,切削液容易导入,加工范围广,适用于自动化加工。
(2)麻花钻:该刀具应用广泛,通常在粗加工阶段应用。
(3)外排屑深孔钻:通常是单双刃深孔钻,原理是高压油进入到钻杆孔,经过腰孔进入到切削区域,迫使碎屑随着切削液从V型的导槽和工件壁之间排出。
这种深孔钻刀面为0°,方便加工。
没有横刃,钻尖与轴线形成一个角度,钻孔中钻尖形成小圆锥,可以让切屑断裂,容易排出。
切削部分形状对孔的公差、切屑成型、切削液压力、刀具寿命、偏离角度等都会对其成孔过程产生影响。
(4)内排屑钻头:钻头和钻杆之间有螺纹连接,工作时高压切削液从钻杆外圆和工件壁之间注入,切削同时产生的切屑从钻杆的中心排出。
(5)喷吸钻:主要是利用切削液产生的喷射效应来排出切屑,通常该钻有内外两根管,其中三分之二的切削液从内外管的空隙和钻头前部流入到切削区域,起到导向和冷却、润滑的效果,并可以将切屑从孔内排出,另外的三分之一,切削液从内管后部喷射,产生快速的喷射流,形成一个低压区域由此与前端配合形成压差,起到一个喷吸效果,提高了钻削的效率。
2.3 定位选择深孔加工与其他成孔加工一样都需要保证定位基准,在实践中锥面定位是常见的方式,主要应用在回转体、中小直径孔、管坯镗孔等;也可采用内锥面定位,是应用在中等直径的内排切削加工方式;而小孔直径的外排切削加工或枪钻加工则可以利用外锥面定位。
如果采用锥面定位必须注意对直线度和余量的保证,必须在钻孔、镗孔前的端面进行内外锥面的处理。
对于大直径深孔则利用外圆进行定位。
如果采用圆定位,应在外圆上加工安装面、定位面、找正面,并保证三者之间是同心圆,对于非回转体则应利用安装面作为定位基准。
2.4 冷却润滑的保证深孔加工中因为孔内在加工中相对封闭,因此容易造成温度急剧升高,因此必须进行降温处理,同时还应保证切削过程中润滑效果。
所以必须利用润滑液来起到冷却与润滑作用。
冷却液、润滑液必须进行合理的配合,使得工件在加工中保证质量并保证刀具寿命延长。
另外,冷却液和润滑液在深孔加工中还可以起到冲刷、减震、消音等作用。
钻削中因为孔径小且深度大,就会在加工中产生较大的抗力和阻力,克服这些阻力而顺利完成加工则会消耗较多的能量,同时切向和径向的力同时作用在导向块上,此时孔壁和刀具就会产生摩擦,摩擦能量就会产生热量和温度升高。
这些热量只能借助于冷却措施来降低。
同时冷却液的存在可以让导向块和孔壁之间形成一种液压支撑系统,以此有效降低导向块摩擦,也可降低摩擦力对功率的消耗,在节能方面也可以起到一定的作用。
再有,润滑液和冷却液可以通过压力和流量来帮助清理切屑。
利用冷却液将工作区域的切屑冲刷到加工区以外,实现清理排屑的效果,保证成孔过程的顺利进行。
因为在工作区域和钻杆内部、外部充满了油性的液体,从而减少了切削过程中的摩擦、震动等,降低了噪声。
2.5 排屑处理深孔加工中因为成孔的空间相对封闭,因此形成的切屑很难排除,沉积切屑会影响加工的过程和质量。
尤其是内排屑钻的过程中,排屑受到空间和环境的影响,只有有限的空间可以利用进行排屑,所以排屑工作难度大不易开展。
从切削的角度看,深孔成孔排屑的问题集中在切屑的处理上,如分屑、断屑、排屑三个连续过程。
针对不同的材料会形成不同特征的切屑,形状、宽窄、弯曲程度、尺寸等都会影响排屑的效果。
所以在深孔加工中排屑问题是重要的工艺指标。
然而深孔加工中排屑通道过长,工作中属于半封闭的状态,切削热量大散热难度也大。
所以在深孔成孔工艺中必须考虑冷却与排屑两个系统,以内排屑深孔钻工艺为例,该工艺具备较为明显的优势,最主要的是具有外冷内排屑和自身导向,能够加工直径6-80mm深孔。
在成孔过程中,工件首先进行旋转,钻头借助螺纹与钻杆进行连接,封油头在刀架的带动下开始成孔,使得导向装置进入到工件中。
内排屑深孔钻进的过程中,切屑在钻杆内实现排屑,不会在孔壁和刀具之间发生摩擦,这样可以最大限度地保证加工表面的质量和精度。
该技术采用的钻杆外径要大于外排屑装置,因此刚性得到了提高,且增加了供给量,成孔的效率也得到了大幅提高。
内排的原理就是在切削液的压力作用下,从孔壁和钻杆外表面寻觅空隙,进入到切削区域的冷却和润滑部位,将前端的切屑冲入到钻杆内,然后从钻杆后部排除。
此类排除切屑的方式容易实现,且兼具冷却和润滑的效果。
同时也可保证钻杆的稳定,但是因为需要独立设置内排屑供液系统,加工造价稍高。
3 深孔加工中应用的设备深孔加工中往往利用专业的设备来完成工件加工,主要按照运动模式进行选择,通常是工件旋转辅助刀具进行轴向进给,使得加工工艺可以顺利完成。
其中最为重要的设备就是机床的选择。
机床是整个加工工艺的基础,主要由主轴箱、进给箱、刀具夹装设备、机床主体、中心架、移动辅助装置共同构成。
主轴箱是支撑主轴,控制旋转和移动不同级的转变,卡盘和拨盘等附属部件通常安装在主轴的右端,转轴多为空心,内部有锥孔,这样可以为夹装细长的刀具提供设置环境。
进给箱是利用丝杆将电机产生的动能传递到刀具上,推动刀具完成直线运动。
夹装装置主要夹装钻杆,利用螺母相互连接,在丝杠的带动下,钻杆可以沿着轴向完成加工进给。
机床床身是基本结构,可以将多个部件组合起来,除了保证各个部件都处在正确的位置,还能协调各个部分的工作状况。
床身上设置刀架和支架导轨等,床身下有支撑支架等,保证其固定在基础上,稳定整个加工系统。
当然在深孔加工中,工件的情况不同也就不能一概而论,在设备选择上如果不能完全采用深孔加工设备,则可以采用卧式的车床来取代成孔设备。
如以卧式机床加工油缸缸套深孔为例,通常采用的是一夹一支的装夹方式,一端则利用四爪单动或者其他类型的卡盘来进行夹紧,另一端则利用中心架完成对轴向的支撑。
深孔刀具的夹装则需要配置专用的刀具架。
专用的刀具架安装在滑板上保证进给。
车削过程中,车床主轴带动刀具完成旋转,滑板则带动刀具完成加工的进给。
还有输油器,该设备也是深孔加工的重要辅助装置,主要的功能就是保证切削液进入到指定的区域,使得切屑能够在液压的推动下完成排屑的过程,主要设置在工件和钻头相互接触的位置上。
同时内排屑的方法中,钻孔的冷却液容易出现渗漏的情况,应重视这个问题,这就要求输油器的密封达到一定的标准,加工中需要调整保证其状态。
输油器和导向架之间应利用密封垫来完成连接,这样就是要控制漏油的问题。
同时输油器和钻杆的接触面、支承架工件端面之间也应利用密封圈进行控制,由此提高防漏的效果。
4 结束语综合来看,机械加工中深度和孔径之间的比例大于5的时候,就属于深孔加工工艺,这一类加工成孔困难且复杂,孔深大则会导致加工工艺特征的改变,如刀杆细长刚性低,钻削容易抖动且容易产生偏移等。
因此在加工的过程中需要考虑工艺的特殊性来选择各种工艺措施,对于深孔工艺而言,技术水平和实施方法必须重视从工艺路线到排屑方式等细节,这样才能在加工中获得较好的工艺效果,保证深孔加工的质量。
参考文献[1]贾玉菊,张真超.机械加工中深孔加工的方法探讨[J].煤矿机械,2012,(6):139-140.[2]都启军.浅谈深孔加工技术[J].装备制造技术,2013,(3):72-74.。