原料预处理装置标定方案
第二章原料预处理
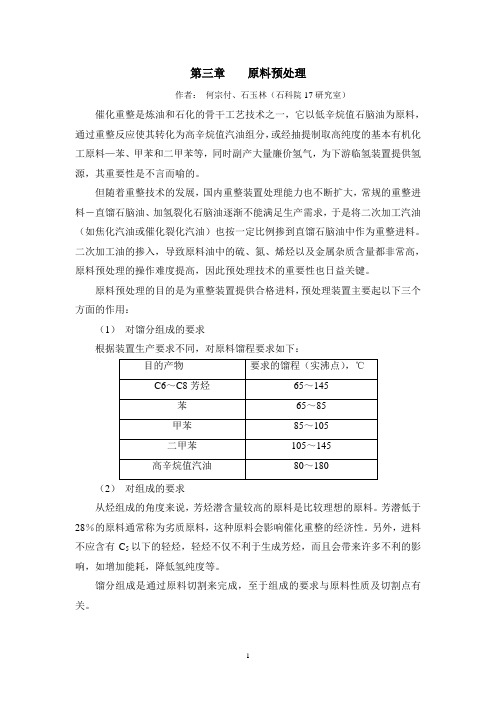
第三章原料预处理作者:何宗付、石玉林(石科院17研究室)催化重整是炼油和石化的骨干工艺技术之一,它以低辛烷值石脑油为原料,通过重整反应使其转化为高辛烷值汽油组分,或经抽提制取高纯度的基本有机化工原料—苯、甲苯和二甲苯等,同时副产大量廉价氢气,为下游临氢装置提供氢源,其重要性是不言而喻的。
但随着重整技术的发展,国内重整装置处理能力也不断扩大,常规的重整进料-直馏石脑油、加氢裂化石脑油逐渐不能满足生产需求,于是将二次加工汽油(如焦化汽油或催化裂化汽油)也按一定比例掺到直馏石脑油中作为重整进料。
二次加工油的掺入,导致原料油中的硫、氮、烯烃以及金属杂质含量都非常高,原料预处理的操作难度提高,因此预处理技术的重要性也日益关键。
原料预处理的目的是为重整装置提供合格进料,预处理装置主要起以下三个方面的作用:(1)对馏分组成的要求根据装置生产要求不同,对原料馏程要求如下:(2)对组成的要求从烃组成的角度来说,芳烃潜含量较高的原料是比较理想的原料。
芳潜低于28%的原料通常称为劣质原料,这种原料会影响催化重整的经济性。
另外,进料不应含有C5以下的轻烃,轻烃不仅不利于生成芳烃,而且会带来许多不利的影响,如增加能耗,降低氢纯度等。
馏分组成是通过原料切割来完成,至于组成的要求与原料性质及切割点有关。
(3)对杂质含量的要求杂质含量要求一般为:硫含量<0.5ppm、氮含量<0.5ppm、砷含量<1ppb、铅含量<10ppb、铜含量<10ppb、水含量<5ppm、氯含量<0.5ppm。
针对原料中的杂质,在预处理部分是通过加氢脱砷、加氢精制、原料脱氯以及蒸发脱水来实现。
在本章中,将针对这重整装置对原料要求这三个方面,一一叙述重整预处理技术。
第一节原料油的切割重整预分馏的目的,是在重整原料进入反应系统之前,首先将原料中过轻、过重组分分馏出去。
分馏出去的轻组分通常叫“拔头油”,切割出的过重组分称为“切尾油”。
预分馏过程的基本原理是利用原料混合物中的各种组分的沸点不同,将其切割成不同沸点范围的馏分。
聚丙烯装置标定方案

聚丙烯装置标定方案
一、标定目的
为了精确装置原料消耗量,确保生产的正常进行,所以对聚丙烯装置进行原料单耗的标定。
二、标定条件
1、装置已具备开车条件或已开车,已经向A罐输送过一次原
料(为了确保罐区送料和装置收料一致性)
2、各部门人员就位
三、标定步骤
1、准备工作
◆检查100m³原料罐A罐出料线阀门是否关闭
◆记录粗丙烯球罐、100m³原料罐ABC罐、高压丙烯回收罐、气柜、气柜回流罐的原始液位
◆检查ABC罐气相线是否断开
2、罐区向聚丙烯送料
当把100m³A罐打满后,关闭球罐出料线阀门和A罐进料线阀门,记录此时球罐和A罐的液位(流程简图见后页)
3、装置开车
A罐向原料精制单元送料,关闭出料阀门,记录液位
4、装置停车
◆记录BC罐、高压丙烯回收罐、气柜、气柜回流罐液位
◆记录聚丙烯产量
5、数据计算
◆用料量=进料量-(BC罐、高压丙烯回收罐、气柜、回流罐
剩余量)
◆产品单耗=用料量÷聚丙烯产量
四、表格记录
聚丙烯原料单耗标定记录表
罐区送料前液位送料后液位液位差值核定物料吨数100m³A罐
100m³B罐
100m³C罐
高压丙烯回收罐
气柜
回流罐
◆液位差值=送料前液位-送料后液位
◆核定物料吨数为查液位与吨数表所得。
某装置标定方案
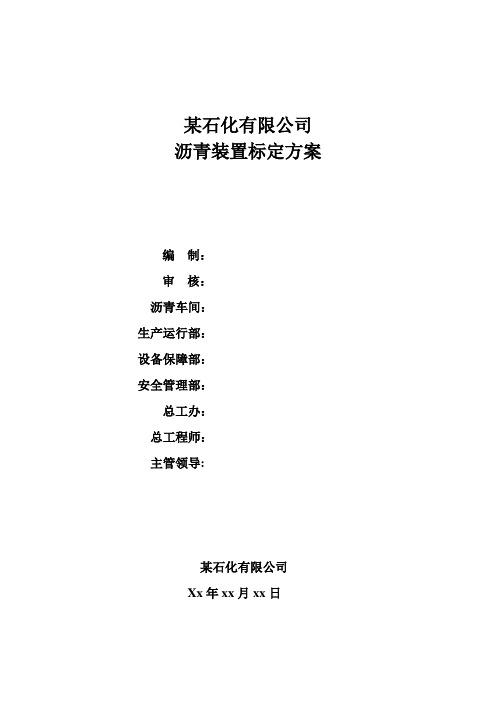
某石化有限公司沥青装置标定方案编制:审核:沥青车间:生产运行部:设备保障部:安全管理部:总工办:总工程师:主管领导:某石化有限公司Xx年xx月xx日某石化有限公司沥青装置标定方案一、装置概况本装置是由某化学工程有限公司设计,年加工原油1000万吨的燃料油型常减压蒸馏装置。
全装置共有设备232台,占地面积17100m2,2008年10月破土动工,于2009年11月竣工,2010年3月投产。
本装置由以下几部分组成:电脱盐系统、闪蒸和常压分馏系统、汽柴油电精制系统、减压分馏系统、蒸汽发生系统、加热炉烟气余热回收系统。
本装置有以下特点(1) 本装置主要设计要求是能生产出优质的燃料油。
(2) 本装置还可利用特定的原油生产出优质的道路沥青。
(3) 本装置为催化裂化装置提供原料,对装置产品的含盐量有一定限制,因此装置设有电脱盐系统。
(4) 本装置为可生产腐蚀、酸碱度等指标合格的直馏汽油和柴油,因而设计了汽柴油的电精制系统。
(5) 本装置采用集散型控制系统(DCS),以提高装置的管理水平并实现过程的部分优化控制,提高轻质油收率,降低能耗,确保产品质量,提高经济效益。
(6) 废水排放:排放的含硫含酸污水进缓冲罐预处理合格后输送到含油污水场。
(7) 废气排放:本装置正常生产时排放的低压瓦斯,常顶气和减顶气分别引到加热炉烧掉,因此本装置正常生产时,不向大气排放有污染性的废气。
塔和容器顶部油气的安全阀放空设有放空总管,引到装置外火炬系统烧掉;本装置的大气污染源主要是燃料在加热炉燃烧后排放的烟气,其中含有SO2,NOX的排放量低于国家排放标准。
(8) 噪声:针对装置中产生的噪音,采用隔音等措施,保证装置内其他各类地点的噪声检测达到了GBJ87-85《工业企业噪声控制设计规范》中有关标准。
(9) 装置为降低能耗,采用了一系列先进技术控制装置能耗本装置主要产品及付产品(1) 主要产品:汽油、常一线油、常二线油、常三线油、常底渣油、减顶瓦斯油、减一线蜡油、减二线蜡油、减三线蜡油、减四线蜡油、减底渣油(沥青)。
溶剂油厂原料预处理装置工艺管线水压施工技术方案

1.工程概况项目名称:溶剂油厂加氢装置原料预处理系统增设脱芳措施建设单位:茂名实华东成化工有限公司设计单位:广西工联工业工程咨询设计有限公司监理单位:广州宏达工程顾问有限公司施工单位:中石化第十建设有限公司溶剂油厂加氢装置原料预处理系统增设脱芳措施装置工艺管线约有4400米,包括抽余油、氢气、循环氢、混氢物料、反应产物、高分油、石油醚、溶剂油系列产品及瓦斯气、氮气、蒸汽、循环水、新鲜水和净化风等管线,为保证管线试压工作有序、保质保量、安全高效地完成,特编制本方案。
2. 编制依据2.1《工业金属管道工程施工及验收规范》GB50235-20102.2《工业金属管道工程施工质量验收规范》GB50184-20112.3《现场设备、工业管道焊接工程施工规范》GB50236-20112.4《工业安装工程施工质量验收统一标准》GB50252-20102.5《石油化工管道支吊架设计规范》SH/T3073-20042.6《石油化工有毒、可燃介质管道工程施工及验收规范》SH3501-20112.7《阀门的检验与管理规程》SH3518-20002.8《石油化工工程建设交工技术规定》SH/T3503-20072.9《石油化工建设工程项目施工过程技术文件规定》SH/T3543-20072.10《压力管道安装工艺标准》QJ/SH 132524.00—20052.11《石油化工建设工程施工安全技术规范》GB50484-20082.12广西工联工业工程咨询设计有限公司提供的相关管道图2.13茂名实华东成化工有限公司相关管理规定3. 试压要求与程序3.1 试压要求3.1.1管线试压时所有不能参与试压的设备、管线须做好系统隔离,无法隔离的设备须经设计和建设单位认可同意后方可参加系统试压。
3.1.2试验压力应以相同等级系统中设计压力最高的管线试验压力为整个系统的试验压力,且不同压力等级的管线不得串联在一起试验。
3.1.3当管道与设备作为一个系统进行试验时,应征得建设/监理和设计单位同意,并符合下列规定:a)管道的试验压力小于或等于设备的试验压力时,按管道的试验压力进行试验;b)管道试验压力大于设备的试验压力,且设备无法隔离,设备的试验压力大于或等于管道试验压力的77%时,按设备的试验压力进行试验。
重整原料的预处理

工艺流程说明一、重整原料的预处理工艺图1-预分馏塔2-预加氢加热炉3、4-预加氢反应器5-脱水塔1、预分馏工艺流程根据重整产物的要求切取适宜馏程的馏分作为重整原料。
在预分馏塔中,切去<80℃或<60℃的轻馏分,同时也脱去原料油中的部分水分。
2、预加氢工艺流程脱除原料油中对催化剂有害的杂质,使杂质含量达到限制要求,使烯烃饱和以减少催化剂的积炭,从而延长运转周期。
从预脱砷反应器出来的原料油进入预加氢精制反应器。
预加氢精制后生成油经换热器、冷却后进入高压油气分离器,分离出的富氢气体出装置可用在加氢精制等用氢装置。
分出的液体油因溶解有少量水、氨等,需送至蒸馏脱水塔除去以上溶解物,经脱水后的塔底油便可作为重整原料。
二、麦格纳重整工艺流程麦格纳重整属于固定床反应器半再生式过程,该工艺将循环氢分为两路,一路从第一反应器进入,另一路从第三反应器进入。
在第一、二反应器采用高空速、较低反应温度及较低氢油比,这样有利于环烷烃的脱氢反应,同时抑制加氢裂化反应。
后面的1个或2个反应器采用低空速、高反应温度及高氢油比,这样有利于烷烃脱氢环化反应。
三、芳烃抽提工艺流程1、抽提部分:原料油从抽提塔的中部进入,溶剂从塔的顶部进入与原料进入逆流接触抽提。
从塔底出来的是提取液,再送去溶剂回收部分的气提塔以分离溶剂和芳烃。
2、溶剂回收部分:从提取液中分离芳烃,回收溶剂并循环利用3、溶剂再生部分:从气提塔底抽出的贫溶剂中引出部分溶剂去再生。
四、芳烃精馏工艺流程1、芳烃混合物经加热到90℃左右后,进入苯塔中部,塔底物料在重沸器用热载体加热到130℃-135℃,塔顶产物经冷凝冷却器冷却至40℃左右进入回流灌,经沉降脱水后,打至苯塔顶作回流,苯产品是从塔侧线抽出,经换热冷却后进入成品罐。
2、苯塔底芳烃用泵抽出打至甲苯塔中部,塔底物料由重沸器用热载体加热至155℃左右,甲苯塔顶馏出的甲苯经冷凝冷却后进入甲苯回流罐。
一部分作甲苯塔顶回流,另一部分去甲苯成品罐。
原料预处理装置停工方案

原料预处理装置停工方案编制:原料预处理装置停工领导小组停工统筹1。
停工准备编制好停工方案经公司有关部门确认、会签。
操作人员熟练掌握开工方案.停工方案、工艺卡片上墙;编制好停工阶段临时组织体系,明确分工。
详见附图1《停工阶段班组运行方式和组织结构图》。
1。
1 停工要求(1)装置停工要达到安全、平稳、文明、卫生的要求,做到统一指挥,各岗位要密切配合,有条不紊,忙而不乱;(2)参加停工的所有人员,必须严格按方案工作,工作认真细致,每项工作都预先考虑好、联系好、准备好。
要保证做到:不冒罐、不串油、不超压、不超温、不损坏设备、不着火、不爆炸、不伤人、不跑油、不出次品;(3)将需检修的300℃以上法兰、人孔的螺栓用油点浸,以便于拆卸;(4)退油时,各塔和容器内存油尽量送往罐区,严禁大量排入污油井.各种油品出装置线必须保持畅通;(5)电缆沟、仪表引线沟不得进油,沟内有油时,要用水或风赶走,若需动火则要作气体分析;(6)瓦斯放空一定要在加热炉熄火以后进行,并伴以蒸汽掩护;液化气不许放入污油井,应放入低压瓦斯管线;(7)要处理的设备管线一律要吹扫干净,符合动火要求,动火要加的盲板一定要挂牌并作表登记,动火结束后拆除;塔人孔要自上而下打开;详见附表4原料预处理装置停工盲板一览表(8)检修中清除出的硫化亚铁要及时送往指定地点,统一集中处理;(9)停工扫线期间,装置内严禁动火;(10)装置停工要求做到:停得稳、放得空、扫得净,一次分析合格达到动火检修条件;(11)停工过程中要注意控制好降量的速度,注意控制好产品质量,按“宁轻勿重”的原则调节产品质量,做到少出污油;(12)降量降温熄嘴时,要求每熄灭一个吹扫一个,加热炉完全熄火后要注意不能向炉膛吹扫,应断开软管吹扫;(13)破真空过程中要注意严防空气倒窜入减压塔;(14)在停工过程中要注意控好各塔顶油水分液罐的液位,防止罐满跑油;(15)扫线时应按扫线流程走,严防油串入蒸汽中;(16)扫线时应先扫回流线,后扫外送线;先扫重油线,后扫轻油线;重油管线要防止凝线;(17)执行HSE有关规定,扫线中不乱排乱放;(18)对外要加强联系,对内要加强配合。
FCC装置技术标定
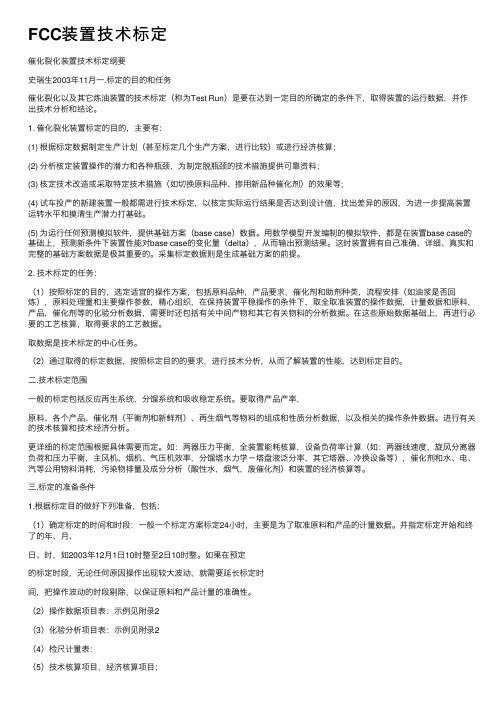
FCC装置技术标定催化裂化装置技术标定纲要史瑞⽣2003年11⽉⼀.标定的⽬的和任务催化裂化以及其它炼油装置的技术标定(称为Test Run)是要在达到⼀定⽬的所确定的条件下,取得装置的运⾏数据,并作出技术分析和结论。
1. 催化裂化装置标定的⽬的,主要有:(1) 根据标定数据制定⽣产计划(甚⾄标定⼏个⽣产⽅案,进⾏⽐较)或进⾏经济核算;(2) 分析核定装置操作的潜⼒和各种瓶颈,为制定脱瓶颈的技术措施提供可靠资料;(3) 核定技术改造或采取特定技术措施(如切换原料品种、掺⽤新品种催化剂)的效果等;(4) 试车投产的新建装置⼀般都需进⾏技术标定,以核定实际运⾏结果是否达到设计值,找出差异的原因,为进⼀步提⾼装置运转⽔平和摸清⽣产潜⼒打基础。
(5) 为运⾏任何预测模拟软件,提供基础⽅案(base case)数据。
⽤数学模型开发编制的模拟软件,都是在装置base case的基础上,预测新条件下装置性能对base case的变化量(delta),从⽽输出预测结果。
这时装置拥有⾃⼰准确、详细、真实和完整的基础⽅案数据是极其重要的。
采集标定数据则是⽣成基础⽅案的前提。
2. 技术标定的任务:(1)按照标定的⽬的,选定适宜的操作⽅案,包括原料品种,产品要求,催化剂和助剂种类,流程安排(如油浆是否回炼),原料处理量和主要操作参数,精⼼组织,在保持装置平稳操作的条件下,取全取准装置的操作数据,计量数据和原料,产品,催化剂等的化验分析数据,需要时还包括有关中间产物和其它有关物料的分析数据。
在这些原始数据基础上,再进⾏必要的⼯艺核算,取得要求的⼯艺数据。
取数据是技术标定的中⼼任务。
(2)通过取得的标定数据,按照标定⽬的的要求,进⾏技术分析,从⽽了解装置的性能,达到标定⽬的。
⼆.技术标定范围⼀般的标定包括反应再⽣系统,分馏系统和吸收稳定系统。
要取得产品产率,原料、各个产品、催化剂(平衡剂和新鲜剂)、再⽣烟⽓等物料的组成和性质分析数据,以及相关的操作条件数据。
常减压原料预处理装置操作指南

表1-1 几种典型原油的物理性质
性质
胜利原油
沙特原油
大庆原油
阿曼原油
密度 kg/m3
粘度(50℃)mm2/s
凝点℃
在常温下,甲烷至丁烷的正构烷呈气态;戊烷至十五烷的正构烷呈液态;十六烷以上的正构烷呈蜡状固态(是石蜡的主要成分)。 由于烷烃是一种饱和烃,故在常温下,其化学安定性较好。烷烃的密度最小,粘温性最好,是燃料与润滑油的良好组分。
环烷烃
环烷烃的化学结构与烷烃有相同之处,只是其碳原子相互连接成环状,故称为环烷烃。由于环烷烃分子中所有碳价都己饱和,因而它也是饱和烃。环烷烃的分子通式为CnH2n。 环烷烃具有良好的化学安定性,与烷烃近似但不如芳香烃。其密度较大,自燃点较高,辛烷值居中。它的燃烧性较好、凝点低、润滑性好,故是汽油、润滑油的良好组分。环烷烃有单环烷烃与多环烷烃之分。润滑油中含单环烷烃多则粘温性能好,含多环烷烃多则粘温性能差。
3、原油中的非烃化合物:
硫化物
硫在原油中主要是以元素硫(S)、硫化氢(H2S)、硫醇(RSH)、硫醚、二硫化物、噻吩的形态存在。其中元素硫、硫化氢、硫醇称为活性硫化物,它们的化学性质较活跃,容易与铁发生反应生成硫化亚铁,使工艺管线和设备器壁减薄,穿孔,发生泄漏事故;硫醚、二硫化物、噻吩等属于非活性硫化物,它们对金属的腐蚀性较弱,但是,非活性硫化物受热后可以分解成活性硫化物。硫的腐蚀性在后面专门说明。
还有一种烃类,叫作不饱和烃,如烯烃、炔烃。原油一般不存在不饱和烃,因为这些不饱和烃不稳定,容易氧化生成胶质。举例来说,汽油存放时间长了,颜色慢慢变深,就是里面的烯烃氧化了。但是烯烃的辛烷值较高,凝点较低,是汽油的良好组分。不饱和烃主要存在于二次加工产物里。
原料预处理原则范文

原料预处理原则范文原料预处理是食品加工的重要环节,它包括了清洗、去皮、去骨、切割等操作。
通过预处理可以去除原料上的污垢、不符合卫生要求的部分,使原料更加干净、卫生,同时也为后续的加工工序提供便利。
下面我将介绍原料预处理的原则。
一、确保卫生安全二、保持原料的天然特性在进行原料预处理时,尽量保持原料的天然特性,避免对原料产生过多的破坏。
例如,在清洗原料时,可以选择用清水轻轻冲洗,尽量避免使用化学清洁剂,以免对原料产生残留。
在切割原料时,也要尽量保持原料的形状和结构,避免过分剥离或切割,以保持原料的营养价值和口感。
三、根据使用需求进行处理原料预处理的方式和程度应该根据具体的使用需求进行决定。
例如,对于水果,可以选择将皮去掉或者留下,根据使用的食谱和个人喜好进行处理。
对于肉类,可以根据不同的菜品需求选择去骨或者保留骨头,以增加食品的口感和风味。
四、提高加工效率原料预处理的目的之一就是提高后续加工工序的效率。
因此,在进行原料预处理时,可以采取一些方法来提高效率。
例如,在切割蔬菜时,可以使用适当的切割工具,如刨丝机、切丁机等,以提高切割的速度和效果。
在处理大量原料时,可以采用批量处理的方式,以节省时间和人力成本。
五、减少营养流失在原料预处理过程中,尽量减少营养流失是一个重要的原则。
一方面,可以选择合适的处理方式和工具,以减少营养成分的流失。
例如,在切割蔬菜时,可以选择快速切割或者冷冻切割的方式,减少与空气接触的时间,从而减少维生素C等易氧化的成分的流失。
另一方面,可以将原料预处理的剩余部分进行合理利用,如用果皮制作果酱、用鱼骨熬制鱼汤等,以保持营养的完整性。
六、符合食品安全标准在进行原料预处理时,要根据食品安全标准进行操作,确保原料的安全性和卫生性。
例如,在处理肉类时,要确保充分煮熟,避免食品中携带病原微生物。
在处理海鲜时,要选择新鲜的原料,避免食品中存在大量的有害物质。
总之,原料预处理是食品加工过程中的重要一环,它能够为后续加工提供干净、卫生、合适的原料,并且可以尽量保持原料的天然特性和营养成分。
装置标定方案

2.5标定步骤及内容
具体阐述工艺控制、分析安排、计量标准及其它过程等。
2.6标定风险评价 编写危害识别、危害、风险评价、削减措施等内容。
2.7标定记录表 根据要求设计表格,以便收集数据。
2.5.7机电运行情况标定
2.5.8三废治理效果标定
2.6标定风险评价
2.7标定记录表
2007年**月**日XX厂(部)XX装置标定方案
第2页
2.7.1装置标定综合评价
2.7.2标定记录表
2007年**月**日XX厂(部)XX装置标定方案
第3页
(
1.1编制依据
252装置消耗标定253主要工艺指标考核254主要经济指标考核255成品质量标定256仪表运行情况标定257机电运行情况标定258三废治理效果标定26标定风险评价27标定记录表2007xx厂部xx装置标定方案兰州石化分公司装置标定方案271装置标定综合评价272标定记录表2007xx厂部xx装置标定方案兰州石化分公司装置标定方案本方案特点及要求11编制依据12本次作业简介标定方案21标定目的标定工作的意义
1.2本次作业简介
2标定方案
2.1标定目的
标定工作的意义;标定深度、范围;达到的目标。
2.2标定时间
根据标定计划的有关要求及生产安排,初步确定标定时间。
2.3标定领导小组及职责
生产厂成立以主管厂长或副总工程师为组长的标定领导小组;合理安排各有关部门 和单位分工和责任。
2.4标定应具备的条件
(1) 内部条件:经二级单位各部门协调,达到完成标定的条件。
***************
(体系编号,编制单位受控章)
XX
原料预处理原则

1原料预处理系统操作原则严格执行原料预处理岗位的工艺操作指南,并保证离心机、过滤系统、减压进料炉F1101、减压塔T1101的正常生产与操作,负责本岗位的开停工及事故处理;同时负责原料预处理系统所有的换热器,水冷却器和机泵的正常运转;做好本岗位工艺设备及相关的工艺管线的巡检和日常维护工作,做好交接班和原始记录;保证整个装置的安全平稳运行,为下游装置的平稳生产创造条件,完成车间下达的有关指令和任务。
原料预处理岗位负责离心机、过滤器、减压进料炉、减压塔及所属机、泵的开、停车操作,做好日常机泵的运行操作和维护保养,确保机泵的平稳运行,保证整个装置的安全平稳运行。
原料预处理的目的是通过原料系统的处理,使原料煤焦油达到反应进料的指标,为反应系统的平稳运行打下坚实的基础。
原料预处理系统是整个煤焦油加氢装置的前分馏系统,主要是把煤焦油组分切割出能适应加氢的馏分,把其余的焦炭残渣、沥青质等重组分分离出来。
原料系统的减压分馏段的操作方要把握三条原则:物料平衡、气液平衡和热量平衡的原则,定性参数轻易不要改变,利用定量参数来调节的原则。
减压系统稳定操作的原则:在稳定物料平衡的基础上,调节塔的热量供给和热量分布,确保产品的合格,在操作中重要区别什么是定性参数(P、T),什么是定量参数(F),尽量保持定性参数不变,通过调节定量参数来调节产品质量。
即在正常操作中应稳定塔顶压力、塔顶温度、塔底液面及各塔顶回流量,以侧线抽出量来调整产品质量。
温度:温度是系统热平衡和物料平衡的关键因素,要想保持系统的平稳操作,就要严格控制好各点的温度。
分馏各点温度的高低主要视进料性质而定,温度是随着进料变化程度进行增加或降低的,所以在正常操作中,应随进料性质变化及时调整各点温度。
压力:压力控制的平稳与否直接影响产品质量、系统的热平衡和物料平衡,甚至威胁到装置的安全生产。
在对塔压力进行调节时要进行全面分析,尽力找出影响塔压的主要因素(一般情况下主要有:进料、回流带水、轻组分量变化),进行准确而合理的调整使操作平稳下来。
装置技术标定工作要求
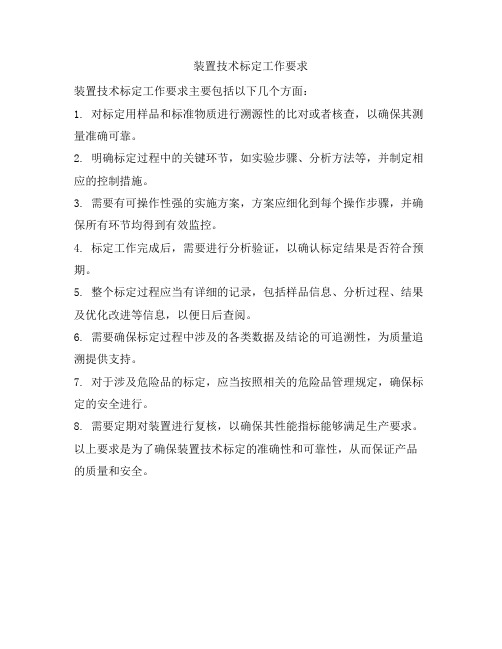
装置技术标定工作要求
装置技术标定工作要求主要包括以下几个方面:
1. 对标定用样品和标准物质进行溯源性的比对或者核查,以确保其测量准确可靠。
2. 明确标定过程中的关键环节,如实验步骤、分析方法等,并制定相应的控制措施。
3. 需要有可操作性强的实施方案,方案应细化到每个操作步骤,并确保所有环节均得到有效监控。
4. 标定工作完成后,需要进行分析验证,以确认标定结果是否符合预期。
5. 整个标定过程应当有详细的记录,包括样品信息、分析过程、结果及优化改进等信息,以便日后查阅。
6. 需要确保标定过程中涉及的各类数据及结论的可追溯性,为质量追溯提供支持。
7. 对于涉及危险品的标定,应当按照相关的危险品管理规定,确保标定的安全进行。
8. 需要定期对装置进行复核,以确保其性能指标能够满足生产要求。
以上要求是为了确保装置技术标定的准确性和可靠性,从而保证产品的质量和安全。
催化重整装置重整原料的预处理
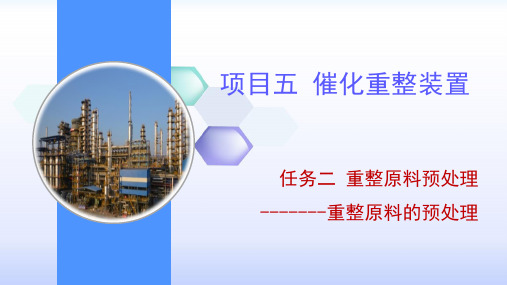
提出问题
催化重整过程为什么要进行原料的预处 理,如果不进行原料的预处理会发生什 么?预处理的方法有哪些?
一、工作原理与流程
根据催化重整的基本原理,一套完整的重整工业装置 大都包括原料预处理和催化重整两部分。以生产芳烃 为目的的重整装置还包括芳烃抽提和芳烃精馏两部分。
➢ 通常原料油含砷量在100~200ppb时,经预加氢后砷含量可 降至1~2ppb以下。若含砷量过高,则必须先经过预脱砷。
(4)重整原料的脱水(dehydration)及脱硫 (desulfurization )
➢ 从预加氢过程得到的生成油中尚溶解有H2S、NH3和H20等, 为了保护重整催化剂,必须除去这些杂质。
➢ 例如,生产芳烃时,切除<60℃的馏分;生产高辛烷 值汽油时,切除<80℃的馏分。
(3)预加氢 prehydrogenation
➢ 目的:脱除原料油中的杂质。 ➢ 将预分馏所得的原料,经钼酸镍(或钼酸钴)催化剂,在压
力1.5~1.8MPa,温度280~360℃,氢油比70~150nm3/m3, 体积空速2~4h-1条件下加氢精制,烯烃被饱和,硫化物、 氮化物、氧化物等转变成易于除掉的气体、硫化氢、氨和水; 原料中的砷、铅、铜、汞、铁等金属毒物被催化剂吸附除掉, 满足重整催化剂对原料油中杂质含量的严格要求。
➢ 汽提塔底设重沸器作为汽提塔的热源。
➢ 脱除硫化物、氮化物和水分的塔底物料(即精制油),与该塔进料换热 后作为重整反应部分的进料。
能力提升
能力提升
Description of the coபைடு நூலகம்tents
复习预习 1.完成平台课后测验 2.观看平台催化重整原料预处理相关视频
原料预处理操作规程
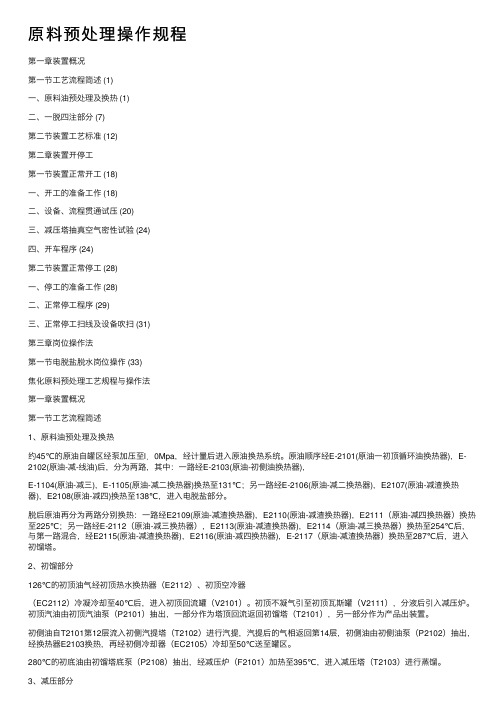
原料预处理操作规程第⼀章装置概况第⼀节⼯艺流程简述 (1)⼀、原料油预处理及换热 (1)⼆、⼀脱四注部分 (7)第⼆节装置⼯艺标准 (12)第⼆章装置开停⼯第⼀节装置正常开⼯ (18)⼀、开⼯的准备⼯作 (18)⼆、设备、流程贯通试压 (20)三、减压塔抽真空⽓密性试验 (24)四、开车程序 (24)第⼆节装置正常停⼯ (28)⼀、停⼯的准备⼯作 (28)⼆、正常停⼯程序 (29)三、正常停⼯扫线及设备吹扫 (31)第三章岗位操作法第⼀节电脱盐脱⽔岗位操作 (33)焦化原料预处理⼯艺规程与操作法第⼀章装置概况第⼀节⼯艺流程简述1、原料油预处理及换热约45℃的原油⾃罐区经泵加压⾄l.0Mpa,经计量后进⼊原油换热系统。
原油顺序经E-2101(原油⼀初顶循环油换热器),E-2102(原油-减-线油)后,分为两路,其中:⼀路经E-2103(原油-初侧油换热器),E-1104(原油-减三),E-1105(原油-减⼆换热器)换热⾄131℃;另⼀路经E-2106(原油-减⼆换热器),E2107(原油-减渣换热器),E2108(原油-减四)换热⾄138℃,进⼊电脱盐部分。
脱后原油再分为两路分别换热:⼀路经E2109(原油-减渣换热器),E2110(原油-减渣换热器),E2111(原油-减四换热器)换热⾄225℃;另⼀路经E-2112(原油-减三换热器),E2113(原油-减渣换热器),E2114(原油-减三换热器)换热⾄254℃后,与第⼀路混合,经E2115(原油-减渣换热器),E2116(原油-减四换热器),E-2117(原油-减渣换热器)换热⾄287℃后,进⼊初馏塔。
2、初馏部分126℃的初顶油⽓经初顶热⽔换热器(E2112)、初顶空冷器(EC2112)冷凝冷却⾄40℃后,进⼊初顶回流罐(V2101)。
初顶不凝⽓引⾄初顶⽡斯罐(V2111),分液后引⼊减压炉。
初顶汽油由初顶汽油泵(P2101)抽出,⼀部分作为塔顶回流返回初馏塔(T2101),另⼀部分作为产品出装置。
标定方案

国望高科聚酯装置容器标定方案编制人:俞卫华李华编制时间: 2011.11121-TA01标定一、标定目的为了使操作更加准确,确保生产的正常进行必须充分了解设备的各种参数及设备容量与液位指示之间的关系,所以对各种容器、反应器进行标定,并记录相应的标定曲线。
二、先决条件1、软化水供应系统处于正常工作状态,并已到达各使用点;2、DCS系统已经投用,待标定设备已经由安装单位安装完毕,并验收合格;3、要求标定的设备的液位传送系统已经由仪表部门校正合格,并交付使用;4、仪表风供应系统已经处于正常运转状态,并已到达各使用点;5、操作人员能熟练使用标定用水表,水表的零点已经校正完毕;6、确保所标定的设备是空罐,液位指示为零;7、打开人孔,关闭所有与容器相连的物料及公用工程管线上的阀门;8、准备好纸、笔及标定表格。
9、随时与控制室保持畅通的联系。
三、标定步骤1、准备♦标杆若干米(也可将卷尺平贴在均匀的木板条上做成标杆)♦带短接的透明软管一根(软管长度根据待标定设备确定)♦水表若干♦胶管若干♦短接若干♦铁丝若干♦钳子、螺丝刀2、静态标定1)拆去人孔盖,用带水表的胶管接软水伸入人孔内;2)用透明胶管从底部与设备连通,把标杆垂直立于地面,立于待标定设备旁,把胶管平直地绑于标杆上;3)向待标定容器加软水,当液位接近液位计时,加水要缓慢进行,当DCS的液位显示刚一发生变化时,停止加水,在记录表中记录此时标尺的液位高度、水表读数、现场液位计读数及DCS的显示液位;4)以每次5%液位的速度继续标定直至100%液位或至罐满,在记录表中记录相应的标尺液位高度、水表读数、现场液位计读数及DCS的显示液位;5)标定过程中还必需记录水位刚没过搅拌桨叶、蒸汽盘管、取样口及到达满罐时的标尺液位高度、水表读数、现场液位计读数及DCS的显示液位。
并把这些特殊点数据记录在标定表格的备注中。
6)做出标定曲线,如果有多个点偏离标定曲线较远或标定曲线与理论曲线差距较大,或者液位计需要校正,重新进行标定。
重整原料的预处理

工艺流程说明一、重整原料的预处理工艺图1-预分馏塔2-预加氢加热炉3、4-预加氢反应器5-脱水塔1、预分馏工艺流程根据重整产物的要求切取适宜馏程的馏分作为重整原料。
在预分馏塔中,切去<80℃或<60℃的轻馏分,同时也脱去原料油中的部分水分。
2、预加氢工艺流程脱除原料油中对催化剂有害的杂质,使杂质含量达到限制要求,使烯烃饱和以减少催化剂的积炭,从而延长运转周期。
从预脱砷反应器出来的原料油进入预加氢精制反应器。
预加氢精制后生成油经换热器、冷却后进入高压油气分离器,分离出的富氢气体出装置可用在加氢精制等用氢装置。
分出的液体油因溶解有少量水、氨等,需送至蒸馏脱水塔除去以上溶解物,经脱水后的塔底油便可作为重整原料。
二、麦格纳重整工艺流程麦格纳重整属于固定床反应器半再生式过程,该工艺将循环氢分为两路,一路从第一反应器进入,另一路从第三反应器进入。
在第一、二反应器采用高空速、较低反应温度及较低氢油比,这样有利于环烷烃的脱氢反应,同时抑制加氢裂化反应。
后面的1个或2个反应器采用低空速、高反应温度及高氢油比,这样有利于烷烃脱氢环化反应。
三、芳烃抽提工艺流程1、抽提部分:原料油从抽提塔的中部进入,溶剂从塔的顶部进入与原料进入逆流接触抽提。
从塔底出来的是提取液,再送去溶剂回收部分的气提塔以分离溶剂和芳烃。
2、溶剂回收部分:从提取液中分离芳烃,回收溶剂并循环利用3、溶剂再生部分:从气提塔底抽出的贫溶剂中引出部分溶剂去再生。
四、芳烃精馏工艺流程1、芳烃混合物经加热到90℃左右后,进入苯塔中部,塔底物料在重沸器用热载体加热到130℃-135℃,塔顶产物经冷凝冷却器冷却至40℃左右进入回流灌,经沉降脱水后,打至苯塔顶作回流,苯产品是从塔侧线抽出,经换热冷却后进入成品罐。
2、苯塔底芳烃用泵抽出打至甲苯塔中部,塔底物料由重沸器用热载体加热至155℃左右,甲苯塔顶馏出的甲苯经冷凝冷却后进入甲苯回流罐。
一部分作甲苯塔顶回流,另一部分去甲苯成品罐。
1#炼油装置标定方案
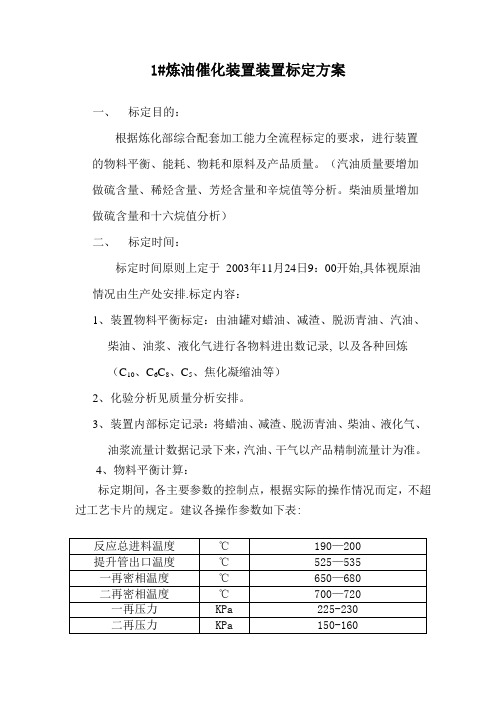
1#炼油催化装置装置标定方案一、标定目的:根据炼化部综合配套加工能力全流程标定的要求,进行装置的物料平衡、能耗、物耗和原料及产品质量。
(汽油质量要增加做硫含量、稀烃含量、芳烃含量和辛烷值等分析。
柴油质量增加做硫含量和十六烷值分析)二、标定时间:标定时间原则上定于2003年11月24日9:00开始,具体视原油情况由生产处安排.标定内容:1、装置物料平衡标定:由油罐对蜡油、减渣、脱沥青油、汽油、柴油、油浆、液化气进行各物料进出数记录, 以及各种回炼(C10、C6C8、C5、焦化凝缩油等)2、化验分析见质量分析安排。
3、装置内部标定记录:将蜡油、减渣、脱沥青油、柴油、液化气、油浆流量计数据记录下来,汽油、干气以产品精制流量计为准。
4、物料平衡计算:标定期间,各主要参数的控制点,根据实际的操作情况而定,不超过工艺卡片的规定。
建议各操作参数如下表:附表:装置物料平衡标定注:*各种回炼由于无计量累积表,所以最好由生产处安排停掉,如不能停,那计量由发出方记录。
能耗标定记录注:*这些项目都是整个装置的总量,催化装置无分表。
1#炼油气体分馏装置标定方案1、标定内容根据炼油厂综合配套加工能力全流程标定的要求,进行装置的物料平衡、能耗、物耗和原料及产品质量。
2、标定条件:气分原料进料:按催化液化气产量,其他工艺条件均按现行工艺卡片。
3、原料与产品质量见分析安排。
4、标定方法装置在上述标定方案情况下,调整操作至产品合格维持4小时后开始标定,标定所需数据所附表格的要求进行填写。
物料记录消耗情况记录注:以上项目单元装置均无分表。
1#炼油产品精制装置标定方案1、标定内容根据炼油厂综合配套加工能力全流程标定的要求,进行装置的物料平衡、能耗、物耗和原料及产品质量。
2、标定条件:原料进料:汽油、液化气、干气按催化产量,其他工艺条件均按现行工艺卡片。
3、原料与产品质量见分析安排。
4、标定方法装置在上述标定方案情况下,调整操作至产品合格维持4小时后开始标定,标定所需数据所附表格的要求进行填写。
加氢裂化装置标定方案(初稿)
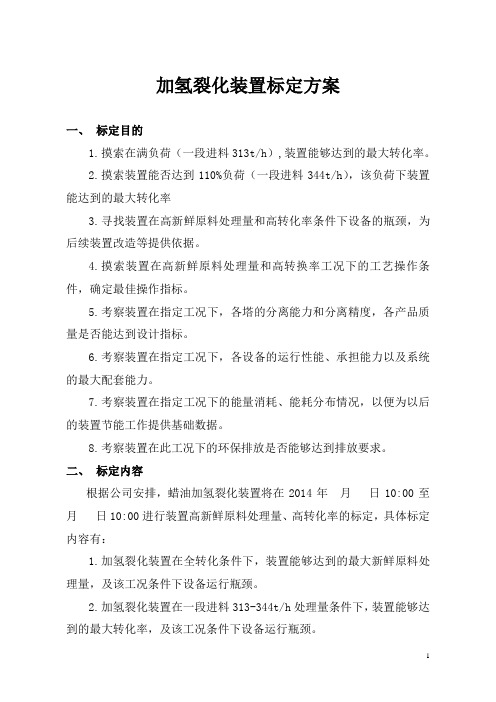
加氢裂化装置标定方案一、标定目的1.摸索在满负荷(一段进料313t/h),装置能够达到的最大转化率。
2.摸索装置能否达到110%负荷(一段进料344t/h),该负荷下装置能达到的最大转化率3.寻找装置在高新鲜原料处理量和高转化率条件下设备的瓶颈,为后续装置改造等提供依据。
4.摸索装置在高新鲜原料处理量和高转换率工况下的工艺操作条件,确定最佳操作指标。
5.考察装置在指定工况下,各塔的分离能力和分离精度,各产品质量是否能达到设计指标。
6.考察装置在指定工况下,各设备的运行性能、承担能力以及系统的最大配套能力。
7.考察装置在指定工况下的能量消耗、能耗分布情况,以便为以后的装置节能工作提供基础数据。
8.考察装置在此工况下的环保排放是否能够达到排放要求。
二、标定内容根据公司安排,蜡油加氢裂化装置将在2014年月日10:00至月日10:00进行装置高新鲜原料处理量、高转化率的标定,具体标定内容有:1.加氢裂化装置在全转化条件下,装置能够达到的最大新鲜原料处理量,及该工况条件下设备运行瓶颈。
2.加氢裂化装置在一段进料313-344t/h处理量条件下,装置能够达到的最大转化率,及该工况条件下设备运行瓶颈。
3.加氢裂化装置产品收率与设计对比。
4.加氢裂化装置产品质量控制与设计对比。
5.加氢裂化装置能耗与设计对比。
三、标定条件1.全转化率条件下,装置能够达到的最大新鲜原料处理量的标定。
装置在标定期间按照两段全循环生产方案运行,以5t/h速度提高反应总进料(反应进料每提高5t后稳定4小时),在提处理量过程中,逐步提高反应温度控制尾油外送为10t/h以下。
装置进料以常减压装置供料为主,直供料不足时罐区补充。
工艺条件均按现行工艺指标执行,过程控制参照原设计参数。
2.300~313t/h新鲜原料处理量条件下,装置能够达到的最大转换率的标定。
装置在标定期间按照一次通过生产方案运行,在标定方案一结束后以5t/h速度继续提高处理量至313t/h,在提量过程中尾油量首先按比例增加,处理量提至313t/h稳定6小时后,逐步提高反应温度至装置能够达到最大转换率。
- 1、下载文档前请自行甄别文档内容的完整性,平台不提供额外的编辑、内容补充、找答案等附加服务。
- 2、"仅部分预览"的文档,不可在线预览部分如存在完整性等问题,可反馈申请退款(可完整预览的文档不适用该条件!)。
- 3、如文档侵犯您的权益,请联系客服反馈,我们会尽快为您处理(人工客服工作时间:9:00-18:30)。
原料预处理装置标定方案一、标定目的为全面了解装置技改后的生产状态,考察装置经过改造后的各项经济技术指标情况,对装置进行标定,通过本次标定,为公司下一步的优化物料平衡、公用工程的平衡及全面完成各项任务指标提供参考依据。
二、装置标定领导小组为了本次标定工作开展顺利进行,原料预处理二车间特此成立装置标定领导小组组长:**副组长:**成员:**和各工艺班长三、标定依据原料预处理装置是由**设计院设计,本装置设计加工原料为**,加工量**万吨/年,年加工时间8400小时。
原油进装置(35℃、2.7MPa、596430kg) 分为两路进行换热。
两路原油换热汇合后(140℃),进电脱盐进行脱盐处理,脱后原油(135℃) 去换热。
脱后原油(135℃)分两路换热,两路原油汇合后换热至240℃进初馏塔。
初馏塔底油经初底泵P–103A/B抽出升压后分为两路换热,换热至300℃后进入常压炉F–101,经常压炉加热至363℃后进入常压塔T–102进行分离。
四、主要标定内容1.本次标定以(**油)为原料,由原料罐区提供,按设计的工艺条件或现有的工艺条件,标定装置的物料平衡情况、加工量能否达到设计水平及装置的总能耗。
2.对装置中的相关计量表进行标定。
3.考察各机泵等主要设备在设计或现有条件下的运转情况。
4.考察在设计或现有条件下产品的质量情况、收率情况。
5.考察原油换热终温是否达到设计水平。
6.考察换后温度,油品出装置温度能否达到要求。
7.考察加热炉出口温度、炉膛温度、加热炉热效率是否在设计范围之内。
8.电脱盐效果是否达到要求。
五、标定的准备工作和要求a)联系调度,安排标定用原料**吨左右。
要求在标定期间原料油油种、组成稳定。
b)联系调度处、技术处和罐区准备好标定专用的原料油罐和产品油罐,并配合进行原料油罐和产品油罐的标尺和记录,要求每8小时一次。
标定期间所有的油罐专罐专用。
c)联系设备处、维修公司对计量表(尤其是进出装置的计量表)进行检查和校验,确保标定期间正常运行。
并做好标定的其它配合工作。
d)联系电修车间做好标定的用电计量等配合工作,要求所有机泵和空冷等设备电功率和装置总电功率每天测试1次,做好记录。
e)联系化验车间按标定方案要求的分析项目作好分析化验的准备工作。
标定期间化验车间要做好加样分析,并在规定时间内完成分析。
f)联系动力车间、电修车间、供水车间保证装置水、电、汽、风等的正常供应。
g)联系生产调度处、质检中心做好环境检测,标定期间污水排放每天检测1次。
h)对装置的工艺和设备作全面的检查,确保标定顺利进行。
i)原料预处理二车间安排好标定取数项目的记录,由工艺员牵头负责好标定期间的工艺数据管理。
j)标定前一天,按照标定的工艺条件调整各操作参数。
六、标定工艺条件k)进装置原料量温度50±5℃l)F-101常压炉炉出口温度:360±3℃左右m)F-102减压炉炉出口温度: 370±3℃左右n)初馏塔顶温:135±10℃,顶压:0.27-0.35Mpa,塔底液面:30-70% o)常压塔顶:125℃±10℃,顶压:≯150Kpap)常一线馏出:180±5℃q)常二线馏出:220±5℃,r)常三线馏出:320-345℃,s)塔底液面:40-80%。
t)减压塔顶温≯150℃,u)减顶残压:≯7Kpa七、标定方法v)装置在标定开始和结束时各塔、容器的液面应基本在相同位置上,并做好记录。
w)标定时间为9月28、29、30日连续3天。
装置按标定要求达到工艺条件。
x)油品罐区储备足量原油且性质稳定,并处理达到付装置要求;各项产品及蜡油,原油要具备单收单付条件,罐区检尺每8小时一次,以便于精确计量。
y)在加工卡斯蒂拉、凯莎杰克拉夫、卢拉+萨宾奥混合油的工况下,要求不掺炼任何污油,加工量取为620t/h。
z)化验室做好安排,每4小时采样分析产品馏程、密度、闪点、凝点等数据,原油分析每4小时一次。
电脱盐脱水含盐每班2次,初、常、减顶酸性水PH值和铁离子含量每天分析一次。
aa)装置操作人员确保操作平稳,给装置标定创造最佳条件,按要求真实填写各项信息,准确记录各温度、流量、压力及化验室、油品报予的数据。
八、标定取样项目1、进出物料:原油、减压渣油、蜡油、石脑油、柴油等产品由生产调度部最好安排专罐储存。
⑴装置内计量项目8:00 16:00 24:00 8:00 16:00 24:00 8:00 去向原油石脑油柴油蜡油渣油燃料油液化气(2)计量原则计量数据以罐区量为准;由于柴油直接付加氢,在柴油计量表经校验后,以计量表为准,报告中对各计量表准确程序做出结论。
2、操作条件与分析2.2.1 电脱盐系统电脱盐系统标定操作条件见表2.2-1表2.2-1 电脱盐系统操作条件项目设计值月日数据月日数据月日数据原油入电脱盐温度℃原油出电脱盐温度℃注水量 t/h脱后原油含盐量mgNaCl/l脱后原油含水量%(wt)排水含油量ppm2.2.2 塔系统表2.2-2 主要操作条件汇总表项目单位设计数据月日月日月日初馏塔T101塔顶压力MPa T 101塔顶温度℃T 101进料温度℃T 101塔底温度℃常压塔T 102塔顶压力MPa T 102塔顶温度℃常一线馏出温度℃常二线馏出温度℃常三线出馏温度℃常顶循抽出温度℃常顶循返塔温度℃常一中抽出温度℃常一中返塔温度℃常二中抽出温度℃常二中返塔温度℃提馏段℃塔底℃常压炉出口℃减压塔T104塔顶残压(A) KPa T104塔顶温度℃减一线馏出温度℃减二线馏出温度℃减三线馏出温度℃减四线馏出温度℃减顶循返塔温度℃减一中返塔温度℃减二中返塔温度℃提馏段温度℃提馏段压力(A) KPa 塔底℃减压炉出口℃2.2.3 换热网络表2.2-3 换热网络标定结果项目单位年月日标定数据年月日标定数据年月日标定数据换热终温℃2.2.4加热炉2.2.4.1常压炉设计工况与标定工况数据对比项目设计值实际值对比部位辐射段入口辐射段出口辐射段入口辐射段出口温度℃流量kg/h热负荷kw表面热强度kw/m2部位对流段入口对流段出口对流段入口对流段出口温度℃流量kg/h热负荷MW (油品总的热负荷)表面热强度kw/m2部位过热蒸汽段入口过热蒸汽段出口过热蒸汽段入口过热蒸汽段出口温度℃流量kg/h热负荷MW表面热强度kw/m2炉膛体积热强度kw/m3冷油流速m/s最大流速m/s压降Mpa燃料消耗kg/h燃料总发热MW排烟温度℃过剩空气系数散热损失kw排烟损失Kw热效率%辐射室氧含量% 备注2.2.4.2减压炉设计工况与标定工况数据对比项目设计值实际值对比部位辐射段入口辐射段出口辐射段入口辐射段出口温度℃流量kg/h热负荷MW表面热强度kw/m2部位对流段入口对流段出口对流段入口对流段出口温度℃流量kg/h热负荷MW表面热强度kw/m2部位过热蒸汽段入口过热蒸汽段出口过热蒸汽段入口过热蒸汽段出口温度℃流量kg/h热负荷kw表面热强度kw/m2炉膛体积热强度kw/m3冷油流速m/s最大流速m/s压降Mpa燃料消耗kg/h燃料总发热MW排烟温度℃过剩空气系数散热损失kw排烟损失Kw热效率%辐射室氧含量%备注2.2.4.3 余热回收设计工况与标定工况数据对比1) 设计工况空气预热器型式:复合式空气预热器单位空气侧烟气侧备注流量Kg/s介质温度复合式空气预热器入口℃出口℃热负荷复合式空气预热器MW流动阻力Pa2) 操作工况:空气预热器型式:复合式空气预热器单位空气侧烟气侧备注流量Kg/s介质温度复合式空气预热器入口℃大气温度出口℃热负荷热管式空气预热器MW流动阻力Pa2.2.5、化工辅料项目单8:00 16:00 24:00 8:00 16:00 24:00 8:00 位破乳剂用量Kg/t缓蚀剂用量Kg/t中和剂用量Kg/t氯转移剂用量Kg/t2.2.6、装置能耗项目单位8:00 16:00 24:00 8:00 16:00 24:00 8:00循环水t/t1.0MPa蒸汽t/t净化水t/t除盐水t/t新鲜水t/t电kw.h2.2.7、产品质量附1:常压产品质量分析数据序号样品名称分析项目分析时间单位1 常顶密度kg/m3 初馏点℃10% ℃50% ℃90% ℃终馏点℃硫含量%(m/m) 酸值mgKOH/g)2 常一密度kg/m3 初馏点℃10% ℃50% ℃90% ℃终馏点℃闪点℃硫含量%(m/m)酸值mgKOH/g)3 常二密度kg/m3 初馏点℃10% ℃50% ℃90% ℃终馏点℃闪点℃硫含量%(m/m) 酸值mgKOH/g4 常三密度kg/m3 初馏点℃5% ℃10% ℃20% ℃50% ℃90% ℃95% ℃终馏点℃凝点℃闪点℃硫含量%(m/m) 酸值mgKOH/g 氮含量μg/g 油品颜色号5 常底密度kg/m3 初馏点℃5% ℃10% ℃20% ℃30% ℃40% ℃50% ℃60% ℃350℃回收体积% 500℃回收体积% 100℃粘度mm2/S 硫含量%(m/m) 残炭%(m/m) 酸值mgKOH/g 铁含量mg/Kg 钠含量mg/Kg 镍含量mg/Kg 钒含量mg/Kg 氮含量μg/g6 混合柴油密度kg/m3 初馏点℃5% ℃10% ℃20% ℃50% ℃90% ℃95% ℃终馏点℃凝点℃闪点℃硫含量%(m/m)酸值mgKOH/g 油品颜色号十六烷值附2:减压塔产品质量分析表序号样品名称分析项目分析时间单位1 减顶密度kg/m3 初馏点℃5% ℃10% ℃20% ℃50% ℃90% ℃95% ℃终馏点℃硫含量%(m/m) 酸值mgKOH/g 油品颜色号2 减一密度kg/m3 初馏点℃5% ℃10% ℃20% ℃50% ℃90% ℃95% ℃终馏点℃凝点℃闪点℃硫含量%(m/m) 酸值mg KOH/g 铁含量mg/Kg3 减二密度kg/m3 初馏点℃5% ℃10% ℃20% ℃50% ℃90% ℃95% ℃终馏点℃40℃粘度mm2/S 硫含量%(m/m) 残炭%(m/m)酸值mg KOH/g 铁含量mg/Kg 镍含量mg/Kg 钒含量mg/Kg 氮含量μg/g4 减三密度kg/m3 初馏点℃5% ℃10% ℃20% ℃50% ℃90% ℃95% ℃终馏点℃40℃粘度mm2/S 100℃粘度mm2/S 硫含量%(m/m) 残炭%(m/m) 酸值mg KOH/g 铁含量mg/Kg 镍含量mg/Kg 钒含量mg/Kg 氮含量μg/g5 减渣密度kg/m3 初馏点℃5% ℃10% ℃20% ℃500℃回收体积%(v/v) 100℃粘度mm2/S 硫含量%(m/m) 残炭%(m/m) 灰分%(m/m) 酸值mg KOH/g 铁含量mg/Kg 镍含量mg/Kg 钒含量mg/Kg 氮含量μg/g附3:原油性质记录原油实沸点蒸馏数据:时间序号沸点范围收率%密度2.2.8、装置防腐8.1 低温部位防腐情况表6-1 常减压低温部位防腐情况对比初顶罐切水常顶罐切水减顶罐切水Fe离子mg/LCl-mg/LPHFe离子mg/LCl-mg/LPHFe离子mg/LCl-mg/LPH8.2 高温部分防腐情况表8-1 高温部分油品防腐效果分析数据项目月日数据月日数据月日数据酸值mgKOH/100LFe(ppm) Ni(ppm)酸值mgKOH/100LFe(ppm) Ni(ppm)酸值mgKOH/100LFe(ppm) Ni(ppm)常二常三减二减三减渣2.2.9、环保项目原料预处理装置废水分析数据采样点分析项目单位初顶罐切水油mg/L 硫化物mg/L 氯化物mg/L FePH氨氮mg/L常顶罐切水油mg/L 硫化物mg/L 氯化物mg/L FePH氨氮mg/L减顶罐切水油mg/L 硫化物mg/L 氯化物mg/LFePH氨氮mg/LV101A电脱盐切水油mg/L 硫化物mg/L Fe备注:具体标定时间听调度处通知。