60t转炉初步设计
炼钢主要设备及其工艺参数

主要设备及其工艺参数混铁炉设备主要工艺参数公称容量: G 600t炉容铁量:G 526t熔池最大深度: h 3.122m炉体外形尺寸: L×B×H9545㎜×7897㎜×7520㎜炉壳重量: 113.475 t炉衬重量: 349t最大操作角度: +24.5°炉体向前倾动极限角度: + 47°炉体向后倾动极限角度:-5°炉顶燃烧温度: 1200℃铁水出炉温度: 1250℃转炉设备主要工艺参数:2.1 转炉炉体转炉公称容量: 60t炉体总高: 7000㎜炉壳高度: 6800㎜炉壳外径: 4700㎜炉壳内径: 4610㎜炉壳壁厚: 45㎜炉壳高度/炉壳外径: H/D=6800/4700=1.45炉膛内高/炉膛直径: H/D=6652/3480=1.91有效容积: 47 m3炉容比: V/t=0.78熔池深度: 900㎜炉口直径:Ф1440㎜出钢口直径:Ф125㎜出钢口与水平夹角: 10°炉衬厚度: 500㎜炉壳总重: 71000㎏炉衬总重: 153t(包括135.7t镁碳砖,17.3烧镁砖) 转炉净环冷却水:总给水量:70t/h 水压p≥0.3MPa T≤60℃2.2 托圈及倾动部分托圈结构:水冷箱型;托圈与炉壳间隙:100㎜,耳轴部位50㎜电机: 45KW×4台最大操作力矩:~1000N·m倾动转速: 0.1-1.22r/min倾动角度: ±360 °倾动减速机比:一次:98.821 二次:8.1176额定制动力矩: 1000N·m×42.3 氧枪系统a. 氧枪系统:氧枪总长度: 17.730m喷头:四孔拉瓦尔型枪直径Ф219㎜喉口Ф30.5㎜出口Ф39.5㎜马赫数 M=1.95 α= 11°50´~12°三层同心套管:内:Ф133㎜×5㎜中:Ф180㎜×5㎜外:Ф219㎜×7㎜供水压力>1.2MPa,进水温度≤35℃,出水温度≤50℃,供水量≥100t/h供氧压力: 0.7~0.9MPa氧枪总重: 2030㎏(包括枪内水量480㎏)b.提升机构提升能力: 55KW升降速度: V快=40m/min V慢=3.5m/min升降行程:工作行程:13900㎜c.横移装置:横移速度: 4m/min横移行程: 2500㎜连铸机设备主要设备工艺参数连铸机台数: 3台机型:2#机:四机四流R8m全弧形方坯连铸机3#机:五机五流R7m矩坯连铸机4#机:三机三流R6.5m直弧形板坯连铸机铸机流间距: 1.25m、 1.4m、 3.2m铸流断面: 2#机: 150×180 150×2203#机: 150×260 150×320 150×3304#机: 150×(330~650)中间包容量: 2#机: 18t 3#机:20t 4#机:25t引锭杆型式: 2#、3#机:钢性引锭杆 4#机:柔性引锭杆钢包转台:a) 钢包最大(单臂)承重:2#连铸机100t,3#连铸机90t,4#连铸机100tb) 钢包转台中心回转半径: 3.5 mc) 钢包回转速度: 1转/分中间包车:a) 行走速度: 2.9~13 m/minb)中间包车轨矩: 2#、3# 5670㎜ 4#6300㎜c)车长: 2#7600 ㎜、3#9200㎜、4#9800㎜结晶器振动装置:a) 型式:四连杆仿弧b) 振幅: 4~8㎜c)振动频率: 0~200次/min拉矫机:a) 型式: 2#、3#机双驱动五辊拉矫机4#机 7组拉矫机,4点矫直b) 辊子开口度: 2#、3#机最小106㎜,最大480㎜4#机 150㎜切割机:a) 型式:火焰切割b) 工作行程: 2#、3#机 2.1m,4#机4.65mc)切割速度: 0.3~0.4m/min4、 60t钢包尺寸包壳:上口2640㎜,下口2300㎜,全高3350㎜打结好钢包:上口2200㎜,下口1880㎜,内高2850㎜常用原材料基本技术要求(一)基本检测1、原材料计量入炉铁水必须经吊车电子秤称量。
伊钢转炉单机试车方案概况

伊钢炼钢60t转炉系统工程设备单体试车方案中国五冶2011年6月目录1、工程概况 (2)2、方案编制依据 (3)3、设备单体试运转通用规定 (3)4、主要设备单体试运转 (5)5、设备单体试运转注意事项 (21)6、设备单体试运转检查调整项目 (22)7、试运转的安全措施 (22)8、试运转用工机具及材料 (22)9、试运转外部条件 (23)10、试车组织体系 (23)1.工程概况1.1伊钢炼钢60T转炉系统工程项目由中冶赛迪工程技术股份有限公司总承包建设,中国五冶施工。
本系统工程主要试车项目包括转炉本体设备、副原料系统设备、车辆设备、除尘风机、水处理设备、起重设备、其他辅助设备。
为了保证设备单体试运转工作顺利进行并达到单体试运转目的,以考验设备的机械性能,特编制本设备单体试运转方案。
1.2 主要试运转设备2. 方案编制依据1、《机械设备安装工程施工及验收》通用规范GB50231-98。
2、《冶金机械液压润滑和气动设备工程安装验收规范》GB50387-2006。
3、《压缩机、风机、泵安装工程施工及验收规范》 GB50275-984、《炼钢机械设备工程安装验收规范》GB50403-20075、《起重设备安装工程施工及验收规范》GB50278-20106、施工图纸及技术文件的要求。
6、设备使用说明书。
3.设备单体试运转通用规定3.1设备单体试运转前应具备下列条件:(1)设备及其附属装置安装完毕,经检查合格,安装质量记录及资料齐全。
(2)液压润滑系统油冲洗合格,正式用油并送至设备用户。
集中润滑系统润滑点按要求应填充润滑油和润滑脂。
(3)冷却水、压缩空气、天然气、氮气、电源等应满足设备单体试运转要求。
(4)试运转所用的材料、工机具、检测仪器、安全防护设施应准备齐全。
(5)危险部位和易燃部位应设置安全防护和灭火设施。
(6)设备周围环境应清扫干净,设备附近不得有干扰试运转的因素。
(7)建立设备单体试运转组织机构,确保统一领导,统一指挥。
脱磷转炉本体(包括氧枪)操作规程

脱磷转炉本体(包括氧枪)操作规程目录1总则1.1使用范围1.2结构简述1.3设备性能2安装、试车技术要求2.1安装要求2.2试车要求3自动控制4操作程序5开新炉操作5.1开新炉前检查5.2开新炉6安全检查6.1运行中6.2运行中紧急停车7设备点检交接班制度1总则1.1适用范围本规程使用于泰山不锈钢厂脱磷转炉维护和检修, GOR转炉本体与此相同,亦可参照使用。
1.2结构简述泰山不锈钢厂60t转炉为锥球形,其溶池由倒圆锥台体和球缺体组合而成,既炉身与炉底分离式。
其转炉本体主要包括:炉壳装配、托圈装配、倾动装置、游动端轴承、驱动端轴承、炉体支撑装置及驱动端轴承润滑配管、游动端轴承润滑配管、炉体底吹气配管等部分。
1.2.1炉壳装配炉壳装配主要由炉体、铸造炉口、挡渣板、吊座、斜楔等组成。
转炉炉体由炉底、炉身、及炉帽三部分组成,转炉炉底为可拆卸式活炉底,炉底与炉身由T 型销钉固定,炉帽与炉身的外壳为一个整体,炉体为球面三点支撑,炉体主要采材质为16MnR。
炉帽上设有出钢口,为保护炉帽减小变形,在炉帽外壳钢板上焊有环形散状挡渣板,可避免喷溅物直接粘附在炉帽外壳钢板上,同时也可保护炉体和托圈。
1.2.2托圈与耳轴托圈与耳轴用于支撑转炉炉体和传递倾动力矩。
托圈断面为矩形箱体结构,托圈中部辅之以钢管,既增加了托圈的强度,又有利于冷热气体的流通交换,降低热应力。
托圈与耳轴为过盈配合,轴向销加法兰联结,托圈主要材质为16Mn,耳轴主要材质42CrMo。
由于耳轴受热会产生轴向伸长和翘起变形,因此驱动侧、游动端耳轴轴承选用调心圆柱滚子轴承,且游动端轴承座为铰接连接。
耳轴轴承采用干油润滑,润滑脂为中极压锂基润滑脂。
1.2.3倾动装置倾动装置主要由右侧驱动、左侧驱动、一二次减速机、扭力杆装置、主令控制器装配、润滑系统等组成。
倾动装置能够旋转±360°,以满足兑铁水、加废钢、取样、测温、出钢、倒渣、喷补炉等工作,并与炉下钢包车、烟罩等设备有连锁装置。
出钢量为60t转炉设计

转炉设计冶金工程课程设计任务书1 设计题目:转炉设计2已知条件:炉子平均出钢量为60t,钢水收得率取94%,最大废钢比取18%,采用废钢矿石法冷却:铁水采用P08低磷生铁[ω(Si)≦0.85%]ω(P)≦0.2%ω(S)≦0.05%],氧枪采用四孔拉瓦尔喷头,设计氧压为1.0MPa。
3设计内容及要求:(1)确定炉型和炉容比(2)计算熔池尺寸、炉帽尺寸、炉身尺寸、出钢口尺寸、炉衬厚度及炉壳厚度(3)绘制转炉炉型图(4)其它要求:①在课程设计期间要努力工作,勤于思考,仔细检索文献和分析设计过程的问题。
②设计说明书必须认真编写,字迹清楚、图表规范、符合制图要求。
3 设计工作量:设计说明书1份;转炉炉型图1份;参考文献列表1份1.1转炉炉型设计1.1.1转炉炉型设计概述(1)公称容量及其表示方法公称容量(T),对转炉容量大小的称谓。
即平时所说的转炉的吨位。
(2)炉型的定义转炉炉型是指转炉炉膛的几何形状,亦即指由耐火材料切成的炉衬内形。
炉型设计内容包括:炉型种类的选择;炉型主要参数的确定;炉型尺寸设计计算;炉衬和炉壳厚度的确定;顶底复吹转炉设计。
1.1.2炉型种类及其选择(1)炉型种类根据熔池(容纳金属液的那部分容积)的形状不同来区分,炉帽、炉身部位都相同,大体上归纳为以下三种炉型:筒球形、锥球形和截锥形。
①筒球形炉型:该炉型的熔池由一个圆筒体和一个球冠体两部分组成,炉帽为截锥体,炉身为圆筒形。
其特点是形状简单,砌砖简便,炉壳容易制造。
在相同的熔池直径D和熔池深度h的情况下,与其他两种炉型相比,这种炉型熔池的容积大,金属装入量大,其形状接近于金属液的循环运动轨迹,适用于大型转炉。
②锥球形炉型(国外又叫橄榄形):该炉型的熔池由一个倒置截锥体和一个球冠体两部分组成,炉帽和炉身与圆筒形形炉相同。
其特点是,与同容量的其他炉膛相比,在相同熔池深度h下,其反应面积大,有利于钢、渣之间的反应,适用于吹炼高磷铁水。
③截锥体炉型:该炉型的熔池有一个倒置的截锥体组成。
一、 工艺布置 - 凤宝股份

炼钢厂60tLF精炼炉初步设计方案一、概述炼钢系统现有1座600t混铁炉,两座40吨转炉(平均出钢量40吨),3座LF精炼炉(其中两座LF炉功率8MV A,一座LF炉6MV A),年平均产能120万吨。
2017年年产钢量111.4万吨。
但随着品种钢增多,精炼问题凸显,精炼能力严重不足,导致经常出现精炼周期不够,连铸空包时有发生,质量得不到有效保证。
精炼能力不足,已成为制约凤宝特钢品种结构调整的瓶颈,严重威胁到凤宝特钢的生存和发展。
为更好地适应公司品种钢开发的需求,我厂拟建一座60tLF精炼炉。
现特邀贵设计院对新建60tLF精炼炉进行设计。
二、设计原则1、尽量采用已有的成熟技术,注重技术的适用性、可靠性、经济性和先进性;设备选型尽量考虑能与现有系统设备互换;2、方案设计中尽量做到总体布局、物流和运输尽可能合理,并有利于公司今后的发展;3、尽量利用现有设施,节省工程投资;同时在制定工艺方案和技术措施时要充分考虑减少改造工程对现有生产运行的影响,尽可能缩短现有生产设施的停产时间;4、本工程中的环境保护、安全、工业卫生、消防设施严格按照有关的国家标准、规范执行,与主体工程同时设计、同时施工、同时投产。
三、设计范围(一)、工艺布置⑴新建60tLF精炼炉工艺布置60tLF精炼炉暂时考虑布置在钢水浇铸跨18~21号柱间(原2期连铸位置),双钢包车平行于转炉主厂房横向(东西方向)布置,设置单加热位(双喂丝工位)及单加料系统。
LF炉用变压器室、液压室、操作室、合金加料系统均布置在过渡跨18~21号柱间。
(2)工艺流程LF钢包精炼炉工艺流程LF钢包精炼炉工艺流程见图:LF钢包精炼炉工艺流程图(二)、主要设备选型及技术参数要求1、LF钢包精炼炉(1)60tLF炉技术参数如下:LF精炼炉公称容量:60t;LF精炼炉座数:1座;平均钢水处理量:60t/炉(远期65t/炉);最大钢水处理量:65t/炉;现钢水处理量:45 t/炉;平均冶炼周期:38min/炉;年处理钢水量:~70万t/a;(2)变压器额定功率为:12MV A(设计院核定)。
日照钢铁60t转炉倾动力矩的计算与分析

Ca c a i n a d na y i f t e tli o qu f Ri h o S e l6 o e t r lul to n a l ss o h i ng t r e o z a t e 0 tc nv r e t
S NG L i C N Hu , JAO Ho gwe O e , HE i I n — i
问的出 题 提
日照钢铁 有 限公 司第一 炼 钢 厂有 6 转炉 4 0t 座 ,均 由 4 转 炉 扩 容 而 成 ,是 生 产 的关 键 设 5t 备 。 因曾经 发生 过 倾 动 电机 带不 动转 炉 的 问题 , 所 以必须 对 6 转 炉 的安全 性 能进行 核算 。 0t 转炉倾 动 时作 用在 耳轴 上 的静力 矩被 称 为倾 动力 矩 。它倾 动力 矩是 转炉 的基 本载 荷参 数 ,由
炉液力矩和摩擦力矩进行计算 ,得出倾 动总力矩的极值 ,以此校核倾动 电机 的力 矩 ,得 出了转炉倾动
设备能力偏小 的结论 ,但是通过采取必要 的应对措施 ,可以保证 电机安全运行 。 关键词 :倾动 ;力矩 ;质心 ;电机力矩 ;校核 中图分类号 :T 7 1 F 2 文献标识码 :A 文章编 号 :10 —16 2 1 )2— 0 5— 4 0 1 9 X(0 0 0 0 3 0
tr T e c n et rt i g e u p n a o o a a i o . h o v r h n q ime t s at ol w c p ct b tte s f p rto ft emoo a e a he e e i h y, u ae o e ain o t rc n b c iv d h h b d p i g n c s ay me s r s y a o t e e s r a u e . n Ke r s i ig;t r u y wo d :t t ln o q e;c n r i moo o q e; c e k e t d; o trt r u h c
260吨转炉本体检修方案

目录1工程概况 (3)1.1转炉本体设备简介 (3)1.2 设备基本参数 (3)1.3 设备功能 (2)1.4 设备检修缺陷 (5)2施工内容 (6)2.1 施工组织、安全体系 (6)2.3施工工程量 (7)2.4 施工方案 (7)2.5施工前的准备工作 (15)2.6对施工单位的要求 (15)3 安全确认办理流程 (15)3.1安全确认流程 (15)3.2安全确认方式 (16)3.3安全确认内容 (16)3.4安全确认要求 (16)3.5填写要求 (17)3.6作业票填写流程 (18)4文明施工 (18)5安全事故预案 (18)5.1目的 (18)5.2组织机构及职责 (18)5.3 安全事故应急措施 (19)5.4注意事项 (19)1工程概况:1.1转炉本体设备简介转炉本体是由炉体、托圈、炉体下悬挂装置、驱动侧旋转接头、游动侧旋转接头、水冷炉口、水冷炉帽、滑板挡渣油缸及机构、底吹枪、驱动端轴承座、游动端轴承座、炉体挡渣板、托圈隔热防护板等设备组成。
在冶炼过程中主要用于承载钢水,并通过转炉倾动机构实现铁水、废钢的入炉以及钢水的出炉。
1.2 设备基本参数1.2.1 炉体主要参数1、公称出钢量:240 t ;平均出钢量:260 t2、炉壳外径:Φ8480mm ;炉壳内径:Φ8300 mm3、转炉全高:10975 mm ;内高:11200 mm4、炉壳内全高/炉壳内径 1.35 ;炉壳容积:495.5m35、砌砖后容积:256m3 ;V/t=0.985 m3/t (1.1)6、转炉炉口直径:Φ3600 (6块耐热球磨铸铁(QT40-17),内埋蛇形管冷却的散形段拼接而成)7、水冷炉口直径:Φ51008、出钢口角度:10°9、直径:Φ17010、熔池直径:Φ630011、转炉炉体冷却水(软化水):工作压力:0.5~0.9Mpa总流量:≥216 m3/h主动耳轴流量:≥3m3/h被动耳轴流量:≥3m3/h托圈流量:≥80 m3/h炉口流量:≥50 m3/h炉帽流量:≥80m3/h出水温度:<65 ℃12、炉壳重:233吨13、炉壳钢板:材料:Q345R炉口钢板厚:150mm 炉壳上部圆锥段板厚:80mm炉身圆柱段板厚:80mm 炉底部分板厚:80mm托圈与炉壳之间的间隙:250mm1.2.2 支撑装置主要参数1、托圈:箱形焊钢结构、水冷。
设计一座年产150万吨良坯氧气转炉炼钢车间毕业设计说明书
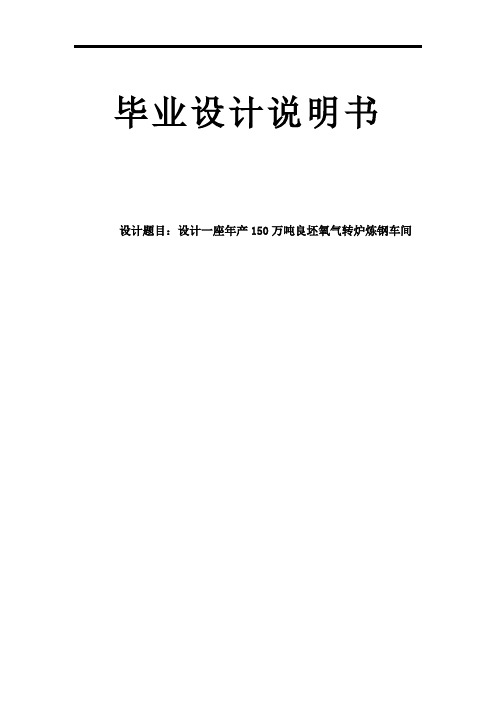
毕业设计说明书设计题目:设计一座年产150万吨良坯氧气转炉炼钢车间毕业设计(论文)原创性声明和使用授权说明原创性声明本人郑重承诺:所呈交的毕业设计(论文),是我个人在指导教师的指导下进行的研究工作及取得的成果。
尽我所知,除文中特别加以标注和致谢的地方外,不包含其他人或组织已经发表或公布过的研究成果,也不包含我为获得及其它教育机构的学位或学历而使用过的材料。
对本研究提供过帮助和做出过贡献的个人或集体,均已在文中作了明确的说明并表示了谢意。
作者签名:日期:指导教师签名:日期:使用授权说明本人完全了解大学关于收集、保存、使用毕业设计(论文)的规定,即:按照学校要求提交毕业设计(论文)的印刷本和电子版本;学校有权保存毕业设计(论文)的印刷本和电子版,并提供目录检索与阅览服务;学校可以采用影印、缩印、数字化或其它复制手段保存论文;在不以赢利为目的前提下,学校可以公布论文的部分或全部内容。
作者签名:日期:学位论文原创性声明本人郑重声明:所呈交的论文是本人在导师的指导下独立进行研究所取得的研究成果。
除了文中特别加以标注引用的内容外,本论文不包含任何其他个人或集体已经发表或撰写的成果作品。
对本文的研究做出重要贡献的个人和集体,均已在文中以明确方式标明。
本人完全意识到本声明的法律后果由本人承担。
作者签名:日期:年月日学位论文版权使用授权书本学位论文作者完全了解学校有关保留、使用学位论文的规定,同意学校保留并向国家有关部门或机构送交论文的复印件和电子版,允许论文被查阅和借阅。
本人授权大学可以将本学位论文的全部或部分内容编入有关数据库进行检索,可以采用影印、缩印或扫描等复制手段保存和汇编本学位论文。
涉密论文按学校规定处理。
作者签名:日期:年月日导师签名:日期:年月日注意事项1.设计(论文)的内容包括:1)封面(按教务处制定的标准封面格式制作)2)原创性声明3)中文摘要(300字左右)、关键词4)外文摘要、关键词5)目次页(附件不统一编入)6)论文主体部分:引言(或绪论)、正文、结论7)参考文献8)致谢9)附录(对论文支持必要时)2.论文字数要求:理工类设计(论文)正文字数不少于1万字(不包括图纸、程序清单等),文科类论文正文字数不少于1.2万字。
LF-60t钢包精炼炉工程技术协议资料

山西建邦特钢有限公司LF-60t钢包精炼炉工程技术协议甲方:山西建邦特钢有限公司乙方:西安桃园冶金设务工程有限公司二〇〇六年十一月目录1.主要工艺条件2.设备技术规格说明3.设计交接点和设备清单及设计联络4.资料的提交及进度5.运行保证值6.设备制造的监制和验收7.人员培训及技术服务8.安装调试9.其它山西建邦特钢有限公司——————以下简称甲方西安桃园冶金设备工程有限公司——————以下简称乙方为满足生产发展需要及适应调整产品结构、扩大产量及产口品种,提高质量,达到节能、降耗、降低成本;同时协调转炉与连铸之间的生产需要,保证转炉、连铸匹配生产实现多炉连浇,山西建邦集团特钢有限公司转炉炼钢车间拟新建一台LF-60t钢包精炼炉。
LF炉主要与新建的转炉和连铸机匹配。
新建的LF炉设备必须是完整的、技术的先进的、运行是可靠的;保证钢包炉的产品具有较强的国际市场竞争力。
工程范围包括LF精炼炉设备及其设备土建的设计、设备供货、运输、安装和调试。
1.主要工艺条件1.1工艺布置a.LF钢包精炼炉采用离线布置。
b.LF钢包精炉采用钢包回转台工作。
c.单炉处理量:最大70t,平均60t。
d.处理周期:300min。
1.2冶炼条件转炉座数1座(新建)转炉公称容量60t转炉平均出钢量60t转炉最大出钢量70t转炉平均冶炼周期300min1.3LF-60t精炼炉电极条件考虑电极的合理载流能力,LF-60t钢包精炼炉电极及接头选用Ф350mm的UHP电极较合理。
1.4设备结构形式LF-60t钢包精炼炉采用还原气氛及微正压条件下的电弧加热,电极升降采用三相电极分别调节,结构形式为三相三臂加热基架式。
1.5设备功能LF钢包精炼炉可以取代初炼炉进行还原期操作,对钢液进行升温、脱氧、脱硫、脱气、合金化、吹氩搅拌,使钢液成份和温度均匀,提高钢液质量,增加产量。
设备具有以下功能:1)对钢水的成分进行调及精确控制;2)确保炉内气氛的可控性强,可实现在强还原气氛下精炼;3)可精确调整钢水温度,为连铸机提供准确的浇钢温度;4)采用钢包底吹氩搅拌,均匀钢水成分和温度;5)通过氩气搅拌(配合渣精炼进行脱硫)及喂丝改变夹杂物形态,去除夹杂,提高钢水的纯净度和质量;6)作为转炉、连铸机之间的缓冲设备,保证转炉、连铸匹配生产,实现多炉连铸。
探析60t转炉炉底上涨原因及处理措施

探析60t转炉炉底上涨原因及处理措施0.引言在钢铁冶炼生产过程中,60t的转炉常会出现炉底上涨的状况,特别是炼钢冶炼过程中广泛地采用溅渣护炉技术,炉底上涨的情况变得越来越严重。
这给冶炼生产带来了极大的不便,造成能源材料的大量损失,增加了企业的生产成本。
因此,企业要全面分析转炉炉底上涨的各方面原因,采取合理有效地措施,控制炉底上涨,从而达到降低企业生产成本的作用。
1. 60t转炉炉底上涨的原因分析1.1溅渣护炉技术的应用,碱度过高造成炉底上涨溅渣护炉主要是在转炉产出钢铁后,将熔渣中的MgO含量调整到一定的饱和程度,在利用N2吹溅使其附着在转炉的炉衬,形成一种氧化脱碳的溅渣层,以保护炉衬,提高60t转炉的使用时间。
但是,由于溅渣的碱性过高,MgO的饱和值达到一定程度,倒炉出钢后的转炉内温度迅速降低MgO就会产生一定的结晶,高熔点的C2S、C3S也会同时析出。
同时熔渣不能完全附着于炉衬,余下部分的熔渣留在了炉底,与MgO的结晶以及C2S、C3S一起引起炉底的上涨[1]。
某钢铁企业在钢铁冶炼过程中,由于生铁的装入量过大,60t转炉冶炼前期温度过低,倒炉出钢时温度过高,熔渣的碱度也特别高,过程化化渣很难控制[1]。
在连续的钢铁冶炼过程中,随着溅渣护炉技术的应用,余留在炉底的炉渣温度相对较低,碱性也比较高,很容易凝固并析出高熔点的矿物质,对炉衬进行保护。
另外,在冶炼中添加废钢和兑铁水时,由于机械的冲刷,物理的溶解容易对转炉的炉底产生一定的损耗,一旦炉底结渣的速度快于炉底的损耗速度,炉底就很容易产生上涨。
1.2氧气射流冲击的深度不够导致炉底上涨在氧气气流冲击的过程中,氧气以高速射流的形式对熔池进行搅拌,促使炉内的金属实现循环,达到供氧与化渣的目的。
但是,由于氧枪喷头还存在缺陷,大量的氧枪参数较为落后,致使氧气射流对熔池的搅拌力度减小,冲击的深度不够,达不到准确的供养效果,致使转炉的炉底上涨。
例如,某企业在去年9—10月的氧压变化就十分明显。
60吨转炉设计
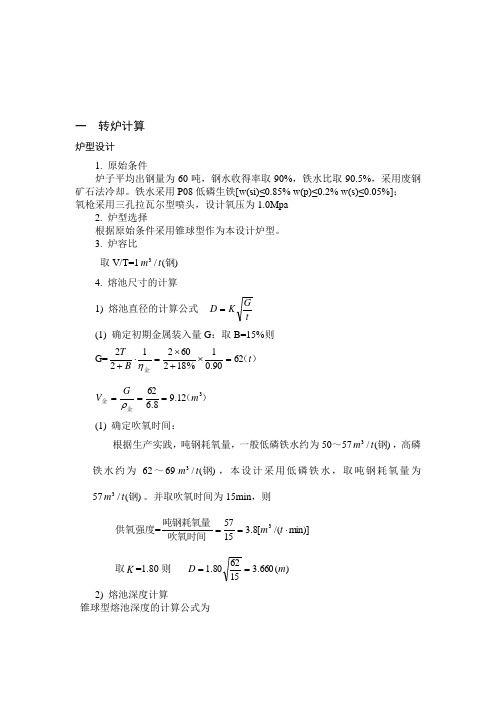
一 转炉计算炉型设计1. 原始条件炉子平均出钢量为60吨,钢水收得率取90%,铁水比取90.5%,采用废钢矿石法冷却。
铁水采用P08低磷生铁[w(si)≤0.85% w(p)≤0.2% w(s)≤0.05%]; 氧枪采用三孔拉瓦尔型喷头,设计氧压为1.0Mpa2. 炉型选择根据原始条件采用锥球型作为本设计炉型。
3. 炉容比取V/T=1)(/3钢t m 4. 熔池尺寸的计算1) 熔池直径的计算公式 tG KD = (1) 确定初期金属装入量G :取B=15%则 G=)(金t B T 6290.01%182602122=⨯+⨯=⋅+η )(金金312.98.662m G V ===ρ (1) 确定吹氧时间:根据生产实践,吨钢耗氧量,一般低磷铁水约为50~57)(/3钢t m ,高磷铁水约为62~69)(/3钢t m ,本设计采用低磷铁水,取吨钢耗氧量为57)(/3钢t m 。
并取吹氧时间为15min ,则 供氧强度=m in)]/([8.315573⋅==t m 吹氧时间吨钢耗氧量取K =1.80则 )(660.3156280.1m D == 2) 熔池深度计算锥球型熔池深度的计算公式为)(162.166.37.066.30363.01.970.00363.02323m D D V h =⨯⨯+=+=金 确定D =3.66m, h =1.162m3) 熔池其他尺寸确定 (1) 球冠的弓形高度:)(3294.066.309.009.01m D h =⨯==(2) 炉底球冠曲率半径:)(026.466.31.11.1m D R =⨯==(3) m D h 3294.09.01== 5. 炉帽尺寸的确定 1) 炉口直径 0d :()m D d 90.166.352.052.00=⨯==2) 炉帽倾角θ:取067=θ3) 炉帽高度帽H)(07.267tan )9.166.3(21tan 2100m d D H =-=-=θ)(锥取mm H 380=口,则整个炉帽高度为:)(口锥帽m H H H 45.238.007.2=+=+=在炉口处设置水箱式水冷炉口炉帽部分容积为:口锥帽)(H d d Dd D H V 202002412ππ+++=)06.1438.09.14)9.19.166.366.3(07.2123222m =⨯⨯++⨯+⨯⨯=ππ6. 炉身尺寸确定1) 炉膛直径D D =膛=3.66m (无加厚段) 2) 根据选定的炉容比为1,可求出炉子总容积为)(容360601m V =⨯= )(帽池总身382.3606.1412.960m V V V V =--=--=3) 炉身高度)(50.366.3482.36422m D V H =⨯=⨯=ππ身身4) 炉型内高)(身帽内m H H h H 112.750.345.2162.1=++=++=由97.166.3112.7H ==膛内H 知符合2.2—1.85范围 7. 出钢口尺寸的确定1) 出钢口直径)(13.0)(136075.16375.163m cm T d T =≈⨯+=+= 2) 出钢口衬砖外径)(78.013.066m d d T ST =⨯== 3) 出钢口长度)(91.013.077m d L T T =⨯== 4) 出钢口倾角β:取015=β8. 炉衬厚度确定炉身工作层选600mm,永久层115mm,填充层90mm,总厚度为600+115+90=805(mm )炉壳内径为27.52805.066.3=⨯+=壳内D炉帽工作层500mm ,炉底工作层选550mm,炉帽永久层为150mm,炉底永久层用标准镁砖立砌一层230mm 粘土砖,平砌三层65×3=195(mm ),则炉底衬砖总厚度为550+230+195=975(mm ),故炉壳内形高度为)087.8975.112.7m H (壳内=+=,工作层材质全部采用镁碳砖。
60t固定式电加热熔炼保温炉结构浅析

60t固定式电加热熔炼保温炉构造浅析熔炼炉和保温炉用来为半连续液压铸造机提供铝液。
一般来说熔炼炉用以承接来自电解槽的铝液并能处理固体铝锭和厂内废料,按化学成分添加所需数量的合金元素,然后转炉至保温炉,经过保温等处理后再把铝液经过流槽平稳转至半连续液压铸造机。
下面介绍的设备即做熔化炉又可做保温炉用。
1.熔炼保温炉工序描述加料由以下动作完成:电解铝液可通过浇包、坩锅或其他专业设备经过熔炼保温炉的专用受铝口加料参加炉内,固体铝锭和厂内废料可通过叉车经过炉门参加熔炼保温炉。
此种加料法同样平安、快捷且高效。
1.1熔化及保温固体铝锭和厂内废料的熔化以及电解铝液的保温是由完全自动的PLC控制系统来完成的。
特殊设计以满足生产要求的宽阔炉膛和炉门加上合理的加热元件系统,可以确保加料简便以及生产所需的熔化率、保温功能和最小的金属烧损。
1.2合金调整,扒渣和搅拌合金调整,扒渣和搅拌是通过一个大炉门来完成的。
炉膛面向炉门的斜坡一般要设计成小于或等于30°,以便于扒渣。
熔炼保温炉的铝水经流口砖排出,流口砖位于炉底,因此可以完全排干炉内的铝水。
流口砖选用氮化碳化硅材质,并采用整体式构造,经过实践检验,此流口砖构造平安系数高,使用寿命长。
2.设备概述60吨固定式电加热熔炼保温炉采用电辐射管加热,设备具有铝液升温速度快,操作方便、平安等特点,可确保铸造工艺对铝液的要求。
60吨固定式电加热熔炼保温炉用于电解铝液铸造前的调质保温及熔化局部铝块冷料及中间合金冷料。
本设备由炉体(炉体钢构造、耐火炉衬)、炉门及炉门升降装置、加热元件装置、炉门除尘装置、测温装置(炉气及铝液测温)、控制系统、前炉及虹吸系统等部件组成。
3.设备系统说明60吨固定式电加热熔炼保温炉的方案设计是根据用户所提供的技术根本条件,总结我们设计、制造熔铝、保温炉的多年技术经历而设计的。
该炉用于电解铝液铸造前的调质保温及熔化局部铝块冷料及中间合金冷料。
熔体成份和温度适宜的铝液,调温后铝液温度符合铸造工艺参数要求,通过铸造流口流经溜槽到铸造机参与铸造。
60t转炉用含铬铁水冶炼HRB400钢的工艺实践
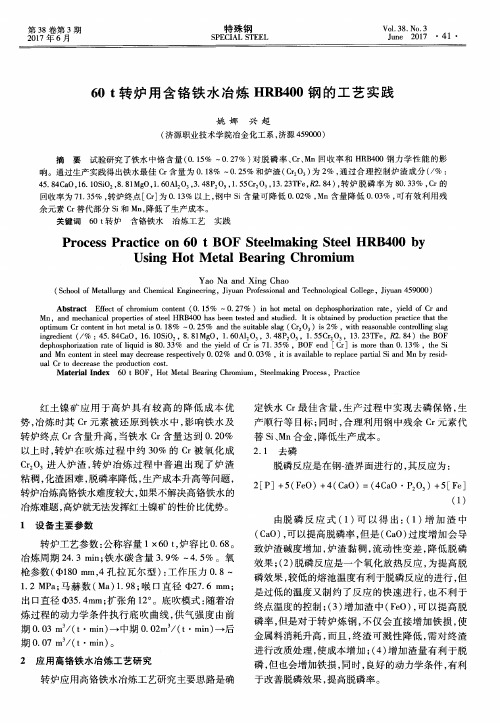
由脱 磷 反 应 式 ( 1 ) 可 以得 出: ( 1 ) 增 加 渣 中 ( C a O) , 可 以提高 脱磷 率 , 但是( C a O) 过 度增 加会 导 致 炉渣 碱度增 加 , 炉渣黏稠, 流 动性 变 差 , 降 低脱 磷 效果 ; ( 2 ) 脱磷 反应 是一 个 氧 化放 热 反应 , 为提 高脱 磷 效果 , 较低 的熔 池温 度有利 于脱 磷反应 的进 行 , 但
( 1 )
粘稠 , 化 渣 困难 , 脱 磷率 降 低 , 生产成 本 升高等 问题 , 转炉 冶炼高铬铁水难 度较大 , 如果 不解决 高铬 铁水 的
冶炼 难题 , 高炉就无法 发挥红 土镍 矿的性价 比优 势 。 1 设 备主 要参数 转 炉 工艺参 数 : 公 称容 量 1 X6 0 t , 炉容比0 . 6 8 。 冶炼周 期 2 4 . 3 mi n ; 铁 水 碳含 量 3 . 9 % ~ 4 . 5 % 。氧
红 土镍 矿应 用 于 高 炉 具 有 较 高 的 降低 成 本 优
势, 冶炼 时其 C r 元 素被 还原 到 铁 水 中 , 影 响铁 水 及 转 炉终 点 C r 含 量 升高 , 当铁 水 C r 含量达到 0 . 2 0 % 以上 时 , 转 炉在 吹炼 过 程 中 约 3 0 %的 C r 被 氧 化 成 C r : O 进 人 炉 渣 , 转 炉 冶 炼 过 程 中普 遍 出 现 了炉 渣
Ya o Na a n d Xi n g Cha o
( S c h o o l o f Me t a l l u r g y a n d C h e m i c a l E n g i n e e i r n g , J i y u a n P r o f e s s i o n a l a n d T e c h n o l o g i c a l C o l l e g e , J i y u a n 4 5 9 0 0 0 ) A b s t r a c t E f f e c t o f c h r o m i u m c o n t e n t( 0 . 1 5 % ~ O . 2 7 % )i n h o t m e t a l o n d e p h o s p h 0 r i z a t i o n r a t e , y i e l d o f C r a n d
转炉设备安装施工方案

镔鑫炼钢60T转炉设备安装施工方案受控标记:(红色印章)受控编号:施工单位:河北冶建三公司日期:200年月日编制: 审核:批准:建设单位意见:1。
工程概况由我公司承建的镔鑫特钢1#转炉设备安装工程,位于镔鑫钢厂新建60T炼钢主厂房内。
主要包括60T转炉系统,烟道系统,氧枪系统,上料系统,投料系统,炉下系统,废钢系统及其他.此项工程的特点为工期紧,任务重,交叉工种多,吊装难度大.2。
主要安装实物量2。
1 转炉系统安装主要包括60T转炉炉体110000千克,60T转炉炉体支撑装置11900千克,60T转炉托圈131000千克,轴承配套装置48250千克,倾动机装置80100千克,转炉润滑配管3180千克,非传动侧旋转接头1730千克,转炉倾角指示盘200千克,挡渣板和防热罩11530千克,传动侧旋转接头595千克。
其中转炉公称容量60吨,炉子最大装容量76吨,炉体外径5500mm,炉口直径2520mm,炉体总高8050mm,耳轴轴承为双列向心球面滚子轴承,托圈结构为整体焊接水冷结构,冷却方式有水冷炉口,水冷托圈,水泠炉帽.转炉托圈为焊接形式,托圈外径7200mm,内径5700mm,长度11505mm,高度为1900mm.被动端耳轴轴承内圈直径为900mm,外圈直径为1270mm。
倾动装置为四点啮合全悬挂扭力杆式,最大工作倾动力矩200吨。
米,最大事故倾动力矩500吨。
米,倾动速度0.21-0.8r/min,总传动比1190.78,一次减速机四台,二次减速机一台。
主动端耳轴轴承内圈直径为900mm,外圈直径为1270mm。
2。
2 烟道系统安装主要包括活动罩裙8027千克,固定烟道17165千克,尾部烟道6297千克,烟道I段11748千克,罩裙提升装置13524千克,烟道II段8510千克。
其中活动罩裙本体的工作压力为2。
45MPa,试验压力为3.675 Mpa。
烟道I段冷却用蒸汽设计压力2。
63MPa,进水温度35°C,汽化后蒸汽温度210°C,进气管管径2-φ159*10,除气管管径2-φ219*14,烟道公称直径φ200mm。
转炉基础设计方案

转炉基础设计方案转炉是一种用于炼钢的重要设备,其基础设计方案的合理性和可靠性直接关系到整个冶金过程的正常进行和生产效益的提高。
下面给出一份转炉基础设计方案的700字示例:一、设计目标:该转炉设计旨在提高钢水质量和生产效率,并减少能源消耗和环境污染。
主要目标包括提高炉后合格品质率、降低转炉喷吹时间、增加钢水温度的恒定性和提高炉后脱氧效果。
二、转炉型号选择:根据生产工艺和产能需求,选用50吨中倾转炉作为目标型号。
该型号具有适中的产能和灵活的操作性能,能够满足生产需求。
三、结构设计:转炉底本身使用整体浇铸,底部设计防爆口,以应对突发情况。
炉身采用钢筋混凝土结构,增加了稳定性和耐磨性。
炉盖采用活动式结构,方便装卸料和维护。
四、吹氧系统设计:吹氧系统采用双面吹氧,以提高氧气利用率和搅拌效果。
吹风系统要求高压、大流量、稳定性好,并配备过滤装置,防止炉衬堵塞。
同时,安装可调节喷嘴,以便根据不同炼钢工艺的需要进行调整。
五、钢渣处理系统设计:为了提高钢渣处理效率,设计采用双辊倾转混渣机,以提高钢渣的处理速度和均匀度。
同时增加钢渣铺垫泥石圈,以提高钢渣的液流性和隔热性,减少热损失。
六、自动化控制系统设计:为了提高生产效率和产品质量,设计采用现代化的自动化控制系统。
通过温度传感器、压力传感器和氧气含量传感器等监控设备,及时获取各个指标的数据,并通过计算机控制中心进行集中处理,实现转炉的自动化操作。
七、安全防护措施设计:为了保障生产人员的安全,设计要求安装爆炸防护装置,实时监测转炉内部的温度和压力,并在超过设定值时及时报警。
此外,还要配备火焰探测器和自动灭火系统,以应对火灾和爆炸等紧急情况。
这是一份转炉基础设计方案的示例,能够满足提高钢水质量和生产效率的要求,并符合安全防护标准。
当然,实际设计还需根据具体情况进行细化和优化。
菜钢60tLF炉渣系工艺研究

】5 3 O . .
≤3 O
力不够强 , 不利于开发高端 H型钢产品。因此开展
渣系工艺研究 , 缩短成渣时间 , 合理分 配 L 不 同时 F 间段的精炼任务非常重要。本文主要介绍 了通过优
3 确定合理 的精炼渣 系
3 1 白泡 沫渣 的重 要性 .
化L F精炼渣 系 目标 , 制定二次快速造 白泡沫渣操 作标准 , 确定合理渣量等以提高精炼渣的综合冶金性 能, 充分吸附夹杂物 , 进一步净化钢水。
0 前言
炼钢厂 4 转炉_4 L - F炉_ 4连铸 机主要 配套 _ 中 型 H 型 钢 生 产 线 , 要 生 产 Q 4C Q 4D 主 35 、 35 、 Q 4E 35 L等一系列抗低温 冲击优质 H型钢。4 转炉 冶炼及 4连铸 机浇注周期较 短 ( 平均 2 i) L 5mn ,F 精炼时间紧迫 。生产中常因工序衔接紧张,F快速 L 造 白渣 困难 , 夹杂物上浮时间难以保证 , 质量控制能
沫渣埋弧操作可提高热效率, 减少耐火材料侵蚀。 3 2 合理 目标 渣 系选择 . 炉渣的精炼能力决定于炉渣的化学性质和物理 性质 , 为确保渣尽快形成, 具有 良好 的流动性 、 发泡 埋弧作用 、 脱硫及吸附夹杂物的能力 , 要综合考虑各 组分对造渣的影响。 1 炉渣硫容量 从脱硫角度考虑 , ) 可选择的精 炼渣 系主 要有 C O—C F 渣 系 、 a a a2 C O—C F 一A2 3 a2 10 渣系、 a A2 3 S 2 C O— I 一 i 渣系 , C O—CF 渣系 0 O 而 a a2 具有最高的脱硫能力 。单从脱硫角度考虑, a CF 含 量 4 %左右为最佳组成 , 0 此时硫 的分配 比约为 10 7 10 但含 c F 量越 高, 8, a2 钢包 耐材侵蚀速度越快。
转炉设计 (2)

1 转炉炉型选型设计及相关参数计算1转炉炉型设计1.1.1 炉型选择氧气顶底复吹转炉是20世纪70年代中、后期,开始研究的一项新炼钢工艺。
其优越性在于炉子的高宽比略小于顶吹转炉却又大于底吹转炉,略呈矮胖型;炉底一般为平底,以便设置底部喷口。
综合以上特点选用转炉炉型为锥球型(适用于中小型转炉见图1-1)。
图1-1 常见转炉炉型(a)筒球型;(b)锥球型;(c)截锥型1.1.2 主要参数的确定本设计选用氧气顶吹转炉(公称容量50t)。
(1) 炉容比炉容比系指转炉有效容积与公称容量之比值。
转炉炉容比主要与供氧强度有关,与炉容量关系不大。
从目前实际情况来看,转炉炉容比一般取0.9~1.05m3/t。
本设计取炉容比为1.05m3/t。
(2) 高径比转炉高径比,通常取1.35~1.65。
小炉子取上限,大炉子取下限。
本设计取高径比:1.40。
(3) 熔池直径D 可按以下经验公式确定:tG KD = (1-1)式中 D ——熔池直径,m ;G ——新炉金属装入量,t ,可取公称容量; K ——系数,参见表1-1;t ——平均每炉钢纯吹氧时间,min ,参见表1-2。
表1-1 系数K 的推荐值注:括号内数系吹氧时间参考值。
设计中转炉的公称容量为50t ,取K 为1.85,t 取15min 。
可得:38.3155085.1==D m(4) 熔池深度h锥球型熔池倒锥度一般为12°~30°,当球缺体半径R=1.1D 时,球缺体高h1=0.09D 的设计较多。
熔池体积和熔池直径D 及熔池深度h 有如下的关系:23665.0033.0DD V h +=池 (1-2)由池V G 1ρ=可得:09.705.7501===ρGV 池(m 3)将池V 代入式(7-2)得:98.038.3665.038.3033.009.7665.0033.02323=⨯⨯+=+=DD V h 池(m)(5) 炉身高度身H转炉炉帽以下,熔池面以上的圆柱体部分称为炉身。
九江萍钢60t转炉投弹式副枪应用生产实践

冶金信息导刊生产实践Production Practice九江萍钢60 t转炉投弹式副枪应用生产实践贾建磊 袁仕兵 古 琪(九江萍钢钢铁有限公司 九江 332500)摘 要:简要叙述了投弹式副枪技术的投弹方式、数据采集及数据输出原理。
详细介绍了该技术在九江萍钢炼钢厂60 t转炉的应用情况与具体的使用效果;投弹式副枪使用后,转炉的生产效率得到明显提高,降低了劳动强度,炉钢周期缩短约2 min,有效提高了一倒出钢率,为转炉的自动化控制打下了良好基础。
关键词:转炉;投弹式副枪;终点控制;自动化炼钢THE APPLICATION OF BOMBRELEASE TYPE SUBLANCE IN THE 60 TON CONVERTER OF JIUJIANGSTEELJia Jianlei Yuan Shibin Gu Qi(Jiujiang Pinggang Iron and Steel Co., Ltd. Jiujiang 332500,China)Abstract: This paper briefly describes the method of dropping bombs, data acquisition and data output of the sub-guntechnology. The application of this technology in the 60 ton converter of Jiujiang Steelmaking Plant and its applicationeffect are introduced in detail. After the use of the sub-gun, the production efficiency of the converter is obviouslyimproved, the labor intensity is reduced, the furnace steel cycle is shortened by about 2 minutes, the rate of pouring outsteel is effectively increased, which lays a good foundation for the automatic control of the converter.Key words: converter; Sub-projectiles; Terminal control; Automatic steelmaking第一作者:贾建磊,男,37岁,助理工程师收稿日期:2021-03-19使用成本相对较低。
- 1、下载文档前请自行甄别文档内容的完整性,平台不提供额外的编辑、内容补充、找答案等附加服务。
- 2、"仅部分预览"的文档,不可在线预览部分如存在完整性等问题,可反馈申请退款(可完整预览的文档不适用该条件!)。
- 3、如文档侵犯您的权益,请联系客服反馈,我们会尽快为您处理(人工客服工作时间:9:00-18:30)。
2.1 生产规模和产品方案
脱碳净化炉的平均出钢量为 54 t/炉,最大出钢量为 60t/炉,平均冶炼周期 32 min/炉,日 出钢炉数为 42 炉,平均日产钢水 Q1=2268t/d,年作业率为 90.4%,年作业天数 330 天,设计 年产钢水达到 Q2=748440 t/a。
2.2 炼钢车间工艺布置
(4)散状原料
脱碳净化炉用散状料包括:活性石灰、轻烧白云石、调渣剂、镁球、铁皮等。
其成份、块度及需要量见表 2-3
表 2-3 散状料成份、块度及需要量
序号 品种
成分%
块度
吨钢耗 年需要
量
量
CaO MgO Al2O3 Fe SiO2 P
S (mm) kg/t (万 t)
活性石
1
≥90 ≤5
灰
≤2.5 ≤0.02 ≤0.1 10-50 95
设计所需生产、生活、消防给水由厂区生产、生活给水管网供给。软水由自备软水站供 给。厂区内的生活、生产等排水采用分流制的排水系统;生活中的粪便污水经化粪池处理后 排入排水系统,其它生产废水,溢流水等直接排入排水系统,经厂区排水总管收集后排入厂 区总排水管网。
1.7.2 除尘系统
脱碳净化炉一次烟气净化采用“二文三脱”湿法除尘工艺(OG 法),两台一次除尘风机, 一用一备。
1
总论 ........................................................................................................................... 3
2
炼钢工艺.................................................................................................................... 7
4)脱碳净化炉系统的上料、加料、脱碳净化炉倾动,吹氧管升降、连铸机均实现计算机 控制。
5)在设备选型上遵循先进、实用、土建设计合理的条件下,尽量减少投资。 6)总图布置、车间工艺布置要求简洁、紧凑、实用。
1.5 建设规模及产品方案
建设规模:金属铁深加工车间生产规模为年产 65 万吨连铸方坯。金属铁深加工车间总体
5
消防 ......................................................................................................................... 32
6
劳动安全机构设置 .................................................................................................. 34
脱碳净化炉烟气二次除尘采用干法布袋除尘工艺。 另外分别在地面建设地下散装料仓除尘器,在散装料平台建设卸料小车除尘器,均可以 单独控制;
刘亚辉(15830983066)
5 / 35
1.7.3 供配电设施
65 万吨连铸工程初步设计
工程总用电负荷为:装机容量 2983.35W,工作容量 2194.6kW。
刘亚辉(15830983066)
8 / 35
65 万吨连铸工程初步设计
设计废钢单耗为 150kg/t 钢水,平均日需废钢~340t/a,年需废钢量约 11.23×104t/a,除自 产废钢返回外,不足部分由公司内调配或外购解决。
合格废钢用汽车运至加料跨东端废钢配料区装槽。 各类废钢入炉前需进行清理切割。入炉废钢要求见表 2-2:
表 2-1 主厂房各跨间基本尺寸及起重机配置
跨间 名称 翻渣跨
长度 跨度 轨面标
(m) (m) 高(m)
84
24
12
起重机配置 (吨位×台) 50/10t×1 吊钩桥式起重机 16/3.2t×1 电磁桥式起重机
备注
加料跨
96
27
脱碳净化炉除 96
尘跨
42
21
18.66 100/30t×1 铸造桥式起重机
9.67
16+16t×1 吊钩桥式起重机
13.5 42
5t×1 单梁悬挂起重机
钢水接受跨
96
24
18.66 100/32t×1 铸造桥式起重机
刘亚辉(15830983066)
7 / 35
跨间 名称
浇铸跨 出坯跨
长度
65 万吨连铸工程初步设计
跨度 轨面标
起重机配置
(m) (m) 高(m)
(吨位×台)
3
环境保护及综合利用 .............................................................................................. 23
4
安全与工业卫生 ...................................................................................................... 27
2.2.1 车间组成及公辅设施
脱碳净化炉炼钢车间包括主厂房和公用辅助设施。 主厂房包括:翻渣跨、加料跨、脱碳净化炉除尘跨、钢水接受跨、浇铸跨、出坯跨,共 6 个跨间组成。 公用辅助设施包括制氧站、水泵站、空压站、配电室、一次除尘风机房、二次除尘、散 装料除尘等。 主厂房主要参数及起重机配置情况见下表;
1.7.4 氧、氮、煤气供应
炼钢用的氧气、氮气由制氧站供应,煤气采用高炉煤气; 工程氮气、氧气的消耗量: 氧气平均用量:6615 Nm3/h; 氮气平均用量:3000 Nm3/h。 煤气平均用量:6000 Nm3/h
刘亚辉(15830983066)
6 / 35
65 万吨连铸工程初步设计
2 炼钢工艺
1.7 公辅设施
1.7.1 给排水设施
65 万吨连铸工程,增建一座 50t 脱碳净化炉及配套公辅设施。主要给排水设施包括脱碳 净化炉车间内净环、浊环、软水、生产水、排水等管道系统。
设计生产总用水量 1415m3/h,其中净环水量 370m3/h,浊循环水 470m3/h,新水用量 81m3/h, 软水 30m3/h,生产用水 10m3/h,生活水 5m3/h,循环水循环率:96%
1.4 基本设计原则
1)本工程设计本着工艺先进、可靠、经济、实用的原则,技术装备水平满足产品大纲品 种质量的要求。
2)总平面布置及工艺布置结合现场实际情况,统一考虑“脱碳净化炉—〉连铸一体化工 艺流程,优化工艺布置及总图运输。
3)认真贯彻国家有关环保、安全、卫生、防火的有关规定和标准,采用行之有效地措施, 同时设计、同时施工、同时投产,争创最佳环境效益和社会效益。
表 2-2 入炉废钢理化要求Βιβλιοθήκη 项目SP渣量
单重
长度
指标
<0.1%
<0.1%
≤1.0%
≤0.3t
~0.70m
若外购废钢,严禁武器、弹药、有色金属及密闭容器混入。
(3) 铁合金
硅铁、锰铁、硅锰合金、金属铝等,各种铁合金单耗合计约 25kg/t,年需总重约 1.87×104t/a。
铁合金均需外购解决。铁合金成份应符合国家标准,粒度 30mm~80mm。
车间产品大纲见表 1-1
表 1-1 车间产品大纲表
钢种
一般碳素结构钢 低合金结构钢
合计
代表钢号
HPB235、Q195、Q275 HRB400、HRB335
产能 (万吨/年)
35 30 65
1.6 工艺及总图布置
1.6.1 工艺流程
采用“高炉炼铁—脱碳净化炉炼钢—连铸”工艺流程。 炼钢用的铁水由炼铁厂供应,用 65t 铁水罐车沿着厂内铁路,运到炼钢厂加料跨的折罐 区,将铁水倒入铁水包,脱碳净化炉需要铁水时,用 100/32t 铸造起重机吊起兑入脱碳净化炉; 炼钢用的废钢,先运至加料跨的废钢区,需要时,用 16+16t 桥式起重机将废钢加入脱碳 净化炉,进行冶炼。 炼钢用的散装料由汽车运至车间内散装料间,通过波纹挡边皮带机运至散装料平台,通 过卸料皮带机卸入高位料仓,脱碳净化炉吹炼时,散装料通过震动给料机从高位料仓加到称 量斗,再加入到汇总斗,通过溜槽加入到脱碳净化炉炉内; 炼钢用的合金,由汽车运至脱碳净化炉除尘跨铁合金区,卸至铁合金吊篮,然后通过 10/3.2t 桥式起重机吊运至合金料仓储存,铁合金称量后装入翻斗车或有轨小车备用; 炼钢用的氧气和氮气由制氧站供应,水、电、压缩空气均由相关配套设施供应; 脱碳净化炉要出钢时,由炉下钢水包车操作箱控制开动钢水包车,运至脱碳净化炉下方 等待出钢。出钢时钢水包车改为由炉后操作室操作。当钢水包车到达预定位置后,脱碳净化 炉向炉后方向倾动 70~115°,将钢水倒入钢水包车上的 60 吨钢水包内,并由布置在炉后的铁 合金旋转溜槽将铁合金加入钢水包内。 出钢后,根据炉役情况溅渣护炉,然后脱碳净化炉前倾出渣;钢水经炉后吹氩处理后, 由炉下钢水包车运至钢水接受跨,由 100/32t 铸造起重机吊运至连铸机大包回转台进行浇铸。
工艺配置为:1×50t 脱碳净化炉(平均出钢量 55t)、一台四机四流方坯连铸机以及钢渣处理
等工艺设施、一座相应的制氧系统等配套设施。
产品方案:投产初期产品钢种为普碳钢和低合金钢。
刘亚辉(15830983066)
3 / 35
65 万吨连铸工程初步设计
连铸坯断面尺寸为 150mm×150mm,铸坯定尺 8~12m。
2) 脱碳净化炉修砌采用炉底下修工艺; 3) 在脱碳净化炉出钢线上设钢包在线快速升温装置,实现红包出钢,降低出钢温度,
提高炉衬和包衬寿命,降低耐材消耗。在线快速烘烤器和其它烘烤器均采用高效蓄 热燃烧系统,以节约能源; 4) 脱碳净化炉一次烟气冷却采用汽化冷却,回收蒸汽。烟气净化采用湿法除尘并回收 煤气; 5) 脱碳净化炉采用二次除尘,脱碳净化炉散状料上料、加料系统的散尘点也设除尘设 施; 6) 脱碳净化炉采用溅渣护炉技术,提高脱碳净化炉寿命; 7) 挡渣出钢; 8) 脱碳净化炉炼钢车间采用 PLC 控制系统;