无取向硅钢连续退火炉炉压控制方法介绍
硅钢连续退火操作
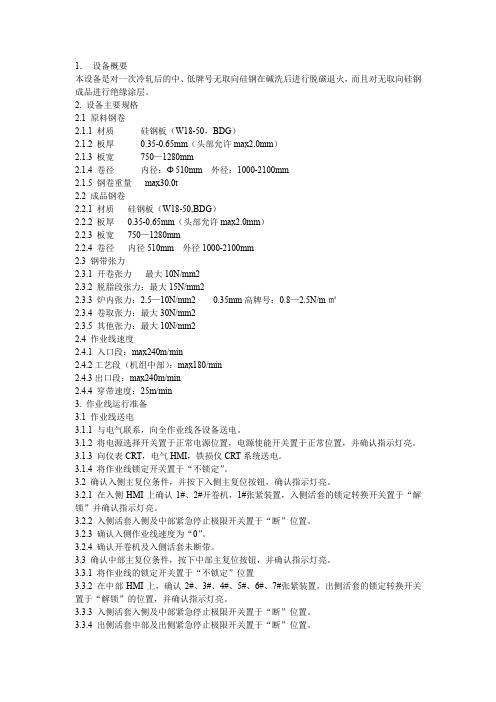
1.设备概要本设备是对一次冷轧后的中、低牌号无取向硅钢在碱洗后进行脱碳退火,而且对无取向硅钢成品进行绝缘涂层。
2. 设备主要规格2.1 原料钢卷2.1.1 材质硅钢板(W18-50,BDG)2.1.2 板厚0.35-0.65mm(头部允许max2.0mm)2.1.3 板宽750—1280mm2.1.4 卷径内径:Φ510mm 外径:1000-2100mm2.1.5 钢卷重量max30.0t2.2 成品钢卷2.2.1 材质硅钢板(W18-50,BDG)2.2.2 板厚0.35-0.65mm(头部允许max2.0mm)2.2.3 板宽750—1280mm2.2.4 卷径内径510mm 外径1000-2100mm2.3 钢带张力2.3.1 开卷张力最大10N/mm22.3.2 脱脂段张力:最大15N/mm22.3.3 炉内张力:2.5—10N/mm2 0.35mm高牌号:0.8—2.5N/m㎡2.3.4 卷取张力:最大30N/mm22.3.5 其他张力:最大10N/mm22.4 作业线速度2.4.1 入口段:max240m/min2.4.2工艺段(机组中部):max180/min2.4.3出口段:max240m/min2.4.4 穿带速度:25m/min3. 作业线运行准备3.1 作业线送电3.1.1 与电气联系,向全作业线各设备送电。
3.1.2 将电源选择开关置于正常电源位置,电源使能开关置于正常位置,并确认指示灯亮。
3.1.3 向仪表CRT,电气HMI,铁损仪CRT系统送电。
3.1.4 将作业线锁定开关置于“不锁定”。
3.2 确认入侧主复位条件,并按下入侧主复位按钮,确认指示灯亮。
3.2.1 在入侧HMI上确认1#、2#开卷机,1#张紧装置,入侧活套的锁定转换开关置于“解锁”并确认指示灯亮。
3.2.2 入侧活套入侧及中部紧急停止极限开关置于“断”位置。
3.2.3 确认入侧作业线速度为“0”。
3.2.4 确认开卷机及入侧活套未断带。
无取向电工钢(硅钢)生产流程[S]、[C]、[N]的控制剖析
![无取向电工钢(硅钢)生产流程[S]、[C]、[N]的控制剖析](https://img.taocdn.com/s3/m/8c62ca6ae45c3b3567ec8b28.png)
高炉顺行; 高温; 高锰; 高硅。
NERC-CCT
四、转炉工序[C]、[S]、 [N]的控制
4.1
4.2
4.3
转炉冶炼工序脱[C] 转炉冶炼工序脱[N] 转炉冶炼工序控[S]
NERC-CCT
4.1 转炉冶炼工序脱[C]
—— 转炉终点碳、氧的控制:
根据RH真空脱碳原理,要求处理前初始钢水的 [C]和[O]应达到一定的范围,以求最佳脱碳效果。
—— 改进真空脱碳效果的措施
1)提高抽气速度,实行真空快速降压,提高脱碳速度; 2)尽可能加大插入管直径,加大驱动气体流量,增大钢水循环量,提高脱碳 速度; 300 3)强制(吹氧)脱碳。 改进前 250
[C](ppm)
强制(吹氧)脱碳的特点: 可提高初始[C],达到0.04~0.06%; 可降低初始[O],降至250~ 400ppm。 脱碳速度比传统RH脱碳快。
NERC-CCT
2)影响转炉“回硫”的因素分析
——铁水脱[S]扒渣对回硫的影响 ——入炉铁水[S]对回硫的影响 ——废钢种类对回硫的影响 ——石灰中[S]对回硫的影响
12 10 8
Δ [S]*10-5
Al钢废钢方式对Δ [S] 的影响
11
7.3
7.6
6 4 2 0 1 3.2
4.8
2
3 废钢方式
4
[C],ppm
240 220 200 180 160 140 120 100 80 60 40 20 0 0 5 10 15 550mm 650mm 750mm
20
脱碳时间 ,min
不同浸渍管径下脱碳比较
300 250
650mm内径,供气流量90Nm3/h
[C](ppm)
无取向硅钢退火作用

无取向硅钢退火作用无取向硅钢退火是一种常见的金属加工工艺,主要用于改善硅钢的磁性能和机械性能。
在无取向硅钢的制造过程中,经过冷轧和热轧后,需要进行退火处理,以消除内应力、改善晶粒结构和磁性能。
本文将重点介绍无取向硅钢退火的作用及其工艺过程。
无取向硅钢是一种特殊的电工钢,由于其低磁滞损耗、高磁导率和良好的磁饱和磁感应强度等特性,广泛应用于电力工业、电子工业和交通工业等领域。
无取向硅钢的性能取决于其微观结构和晶粒取向,而退火过程正是对这些因素进行调控的重要工艺。
无取向硅钢退火的主要目的是改善材料的磁性能和机械性能。
在冷轧和热轧过程中,硅钢中的晶粒会发生拉伸和变形,形成了一定的内应力,导致磁导率下降。
通过退火处理,可以消除这些内应力,使晶粒恢复正常的形态和取向,提高磁导率和磁饱和磁感应强度。
无取向硅钢退火的工艺过程一般包括加热、保温和冷却三个阶段。
首先,将硅钢样品加热到适当的温度,一般在800-950摄氏度之间。
然后,保温一段时间,使晶粒得到充分的生长和再结晶,消除内应力。
最后,通过适当的冷却速度,固定晶粒的取向和结构,使其达到最佳的磁性能。
无取向硅钢退火过程中的温度和时间是影响退火效果的关键因素。
温度过高或时间过长会导致晶粒长大过大,从而降低磁导率和磁饱和磁感应强度。
而温度过低或时间过短则无法充分消除内应力和改善晶粒结构。
因此,在实际生产中,需要根据具体的硅钢材料和要求,进行合理的温度和时间控制。
除了温度和时间,退火过程中的冷却速度也是影响退火效果的重要因素。
过快的冷却速度会导致晶粒无法充分长大,从而影响磁性能的提高。
因此,在退火过程中,需要选择合适的冷却速度,使晶粒得到适当的长大和固定。
无取向硅钢退火是一种重要的金属加工工艺,通过合理的温度、时间和冷却速度控制,可以改善硅钢的磁性能和机械性能。
在实际生产中,需要根据具体的要求和材料特性,进行合理的退火工艺设计和参数控制,以获得最佳的退火效果。
这将有助于提高无取向硅钢的应用性能,推动相关领域的发展和进步。
无取向电工钢(硅钢)生产流程[S]、[C]、[N]的控制教材
![无取向电工钢(硅钢)生产流程[S]、[C]、[N]的控制教材](https://img.taocdn.com/s3/m/73071f07a300a6c30c229f8f.png)
NERC-CCT
—— 电工钢中[S]对磁性能的影响
钢中[S]含量增加,铁损增加,存在铁损急剧增加的[S]含 量,由此,电工钢中[S]控制成分为小于50ppm。
NERC-CCT
—— 电工钢中[N]对磁性能的影响
[N]含量在25ppm以上时,铁损急剧增加,由此,钢中[N] 含量控制应以25ppm为极限。
NERC-CCT
二、转炉流程生产无取向电工钢的关键工序
关键工序与任务: 铁水预处理工序,脱[S]、控制[N]; 转炉冶炼工序,脱[C]、脱[N]、控[S]; RH 精炼工序,脱[C]、脱[S]、控[N]; 连铸工序,控[C]、控[N]、控[S]。
NERC-CCT
—— 转炉流程脱硫工序的选择
1)铁水脱硫的优点:
—— 铁水中碳、硅含量高,提高了硫的反应能力, 从而有利于脱硫; —— 铁水中氧含量低,提高了渣-铁之间的硫分配 比,脱硫效率高; —— 铁水脱硫因其较好的动力学条件,脱硫剂利用 率高,而且脱硫速度快; —— 铁水脱硫费用低,如高炉、转炉、炉外精炼每 脱除1kg硫,其费用分别约为铁水脱硫的2.5倍、16 倍和6倍。
氮在α-Fe、γ –Fe、 δ –Fe、液态铁中的溶解度
氮在铁液中的溶解度
氮在铁中的溶解度
NERC-CCT
② 合金元素含量对氮在铁液中溶解度的影响
连退机组退火炉炉压控制研究

连退机组退火炉炉压控制研究摘要:文章介绍了连续退火炉炉内氛围主要组成成分,阐述了氢气含量配比控制和炉内正常生产时的压力控制以及造成炉压炉波动的相关因素,分析了炉压波动的主要常见原因,并提供了具体问题的解决措施,在实际生产中,特别适用于特殊钢材的生产操作炉内氛围要求,使得退火炉炉内氛围得到有效控制,保证了带钢退火生产工艺稳定,满足各类带钢退火要求,提高产品质量。
关键词:连退机组;退火炉;炉压控制前言攀钢西昌钢钒冷轧厂连续退火炉是进口立式退火炉。
炉内氛围为氮气和氢气按照一定比例混合构成的氛围,炉内压力保持微正压保证带钢在炉内不被氧化,同时还可以去除带钢表面残留的氧化物,提高带钢的表面质量。
1保护气体注入控制攀钢连退线按照区段划分保护气体注入分8个主控制管路。
炉内氛围控制完全基于西门子公司的PCS 7软件,以Win CC作为人机界面,实现过程参数的在线检测、显示和调节,实现数据采集、报警和趋势记录,保证设备的控制精度和生产稳定运行。
为了防止空气进入炉内,加热炉在生产中常保持一定的正压,炉压是由大量保护气体注入形成的,保护气通过位于炉底的注入点流进炉内,在各注入支路的流量控制阀和炉顶的放散阀共同调节下,保证炉内一定的压力和炉内气氛再生,炉内压力的设定以保证加热炉安全性为主,防止带钢氧化来决定,因为退火炉内的气氛压力直接影响着带钢的质量和退火炉的安全,炉压低无法有效保证还原反应效果,炉压过高容易出现事故和浪费气体。
1.1保护气注入模式根据加热炉生产状态,保护气注入一共存在六种模式可供选择,各个模式间的切换遵循顺序,模式的启停完全由顺控完成,保证切换过程平稳性。
其中快冷段高氢模式HNx+RCH2和模式N2+RCH2间的切换需要经历HNx模式和N2模式,此过程也是由顺控自动完成的,不需要操作工进行干预。
1.2保护气注入流量修正1.2.1炉压控制及修正保护气体注入炉内后,按照工艺设定的炉压大小由炉压控制器采用PI控制,其比例系数取2,积分时间取200s。
浅析连续退火炉生产硅钢的原理与工艺解读

首钢工学院毕业设计(论文)题目:浅析连续退火炉生产硅钢的原理与工艺系别:建筑与环保工程系专业:冶金技术(高端金属材料)班级:高端材料131姓名:指导教师:张红文老师2016年5 月3 日摘要本篇论文通过自己查阅的相关资料。
比较详细的介绍了硅钢生产中连续退火炉的工艺和技术。
论文主要分为三个部分。
第一部分介绍了硅钢及硅钢生产中连续退火的重要性并简单的介绍了连续退火的原理和设备情况,第二部分则介绍了硅钢生产中连续退火炉的工艺技术,其中重点介绍了在硅钢生产中退火炉的气体的操作技术;最后介绍了硅钢生产中退火炉的现状与发展前景。
关键词:冷轧;硅钢;退火炉工艺;发展目录摘要 (1)目录 (2)前言 (3)1.硅钢生产中退火炉的现状与前景 (4)1.1硅钢生产中退火炉的现状 (4)1.1.1国外退火炉的现状 (4)1.1.2国内退火炉的现状 (4)1.2未来发展前景 (5)2.硅钢生产中连续退火炉的重要性及工作原理 (6)2.1退火炉在硅钢生产中的重要性 (6)2.2退火炉的工作原理 (6)2.3退火炉设备 (7)3.硅钢生产中退火炉的工艺技术 (8)3.1退火炉点火升温 (8)3.1.1点火升温的条件 (8)3.1.2 点火升温注意事项 (8)3.2连续脱碳退火 (9)3.2.1脱碳原理: (9)3.3退火炉降温 (10)3.4退火炉抽穿带注意事项 (10)3.4.1退火炉穿带 (10)3.4.2退火炉抽带 (11)3.5退火炉气体操作 (11)3.5.1 NH混合气的使用 (11)3.5.2 N2的使用 (11)3.5.3 H2的使用 (13)3.5.4异常时的处理方法 (13)结论 (15)参考文献 (17)致谢......................................................................................................................................错误!未定义书签。
无取向电工钢(硅钢)生产流程[S]、[C]、[N]的控制
![无取向电工钢(硅钢)生产流程[S]、[C]、[N]的控制](https://img.taocdn.com/s3/m/73be60e9c8d376eeaeaa319a.png)
高炉顺行; 高温; 高锰; 高硅。
NERC-CCT
四、转炉工序[C]、[S]、 [N]的控制
4.1
4.2
4.3
转炉冶炼工序脱[C] 转炉冶炼工序脱[N] 转炉冶炼工序控[S]
NERC-CCT
4.1 转炉冶炼工序脱[C]
—— 转炉终点碳、氧的控制:
根据RH真空脱碳原理,要求处理前初始钢水的 [C]和[O]应达到一定的范围,以求最佳脱碳效果。
氮在α-Fe、γ –Fe、 δ –Fe、液态铁中的溶解度
氮在铁液中的溶解度
氮在铁中的溶解度
NERC-CCT
② 合金元素含量对氮在铁液中溶解度的影响
C、Si:降低溶解度;
Nb、V、Cr、Mn、Zr、Ti、Al:增加溶解度; Mo、Ni、Co :影响不大。
NERC-CCT
③ 低氮铁水的获得
铁水[N]含量:30~40ppm 低氮铁水的措施:
NERC-CCT
二、转炉流程生产无取向电工钢的关键工序
关键工序与任务: 铁水预处理工序,脱[S]、控制[N]; 转炉冶炼工序,脱[C]、脱[N]、控[S]; RH 精炼工序,脱[C]、脱[S]、控[N]; 连铸工序,控[C]、控[N]、控[S]。
NERC-CCT
—— 转炉流程脱硫工序的选择
铁水脱硫
无取向硅钢片退火工艺2

无取向硅钢片退火工艺1、退火温度温度不宜选得过高,以能够恢复到原磁性水平为限。
退火温度偏高,固然可以进一步改善磁性,但相应会影响绝缘涂层或使叠片粘结。
冷轧取向电工钢带(取向硅钢片)一般选用800±10℃。
冷轧无取向电工钢片(无取向硅钢片)选用680-750℃,退火温度高于750℃,应严格控制炉内保护气氛为无氧化气氛。
2、退火时间指炉内温度达到设定退火温度后的保温时间。
实际退火时间是根据退火方式、退火炉型、装炉量、装炉方式以及铁芯尺寸等因素而定。
为了防止在加热和冷却过程中,由于热应力导致铁芯冲片变形,必须适当控制加热速度和冷却速度。
加热方式最好选用从铁芯冲片侧面加热,以实现均匀快速加热。
冷却速度视装炉量而定,应低于30℃/时,装炉量更大时,还应该更低些。
3、退火气氛选用以铁芯冲片不氧化、不渗碳和电工钢带片(硅钢片)表面绝缘涂层无明显恶化为原则。
最好选用含氢2-10%的氢氮混合气体。
加入少量的氢可确保铁芯冲片不氧化。
保护气体中的露点一般应在0℃以下。
4、严防渗碳和氧化冷轧电工钢带片(冷轧硅钢片)含碳量一般小于0.003%,因此在消除应力退火时,必须严防渗碳,以免恶化磁性。
炉用材料,如炉罩、底版应选用低碳钢材,冲片表面的残余油脂,应在退火前清除,防止冲片氧化是消除应力退火效果的重要措施。
除合理选用退火气体外,在实际操作时,首先要确认炉膛密封是否完好。
同时,在送电升温前,先通入保护气体进行炉内清扫。
这个也可以参考下,根据实际情况设计.一、将待退火硅钢片装入铁盒(按硅钢片尺寸大小,注意装箱最好不要超过三层),装架,每箱硅钢片上覆盖一张略小于铁盒的盖板(最好用硅钢片材料做),吊至炉膛内,锁好炉盖.二、将大华表的三只热电偶安装在炉体上,装上烟囱,打开排气阀门.三、检查电气柜的电压、电流、仪表是否正常,装上大华表的记录纸,检查记录纸的正常走纸(首先打开电源开关).四、将温控表的初始温度设定为400℃,检查功率表的各项电流是否一致,在确保调整一致后,打开加热开关进行加热.五、检查电房仪表的正常与否,进行煺火炉的功率调整.六、接好氮气,检查是否漏气,并检查循环水的正常供给.七、在温度升至400℃时,打开氮氮气阀门,注入100-200ml的氮气,此时将循环水的阀门打开.八、温度确定升至400℃时,进行恒温,恒温1小时左右,并确定大华表温度也在400℃左右(此时废气不是很多).九、保温完毕后,将温控表设定为500℃,进行加热,此间注意电流表的状况是否一致,有问题及时处理.十、温度升至500℃时进行恒温45分钟左右,此时看炉体有无变化,是否有漏气现象,循环水供给是否正常.十一、恒温完毕后,将温控表设定为600℃,进行加温.将氮气调压阀调大,注入200-400 ml 的氮气,此时废气较多.十二、温度升至600℃时,恒温45分钟左右,此时看一看电压是否正常.十三、最后将温控表设定为680℃-750℃(根据硅钢片材质而定,冷轧无取向硅钢片低牌号国产B50A600、50W600、50AW600、50WW540以下一般退火温度在680℃左右,进口同等材质可适当+20℃,无取向高牌号一般退火温度在750℃左右.冷轧取向硅钢片一般退火温度为820℃左右).氮气可以开大一些,或保持400 ml的氮气,此时废气较多.十四、温度升至设定温度后,恒温时间不可少于2小时,大华表也应在设定温度上下,此时可将排气阀门关小一些.十五、结束后,将排气阀门关小(不关闭即可),氮气注入在100-200ml,循环水阀门可关闭(出水阀门一直是打开的),关闭加热开关、电源开关.十六、检查无误后,该炉硅钢片去应力退火过程进入自然冷却状态,当炉内温度降至380℃以下(最好是350℃)方可出炉.。
轧无取向硅钢连续退火线干燥炉设计

冷轧无取向硅钢连续退火线干燥炉设计龚彦兵摘要:以理论与实践经验为基础,详细阐述了用于冷轧无取向硅钢片绝缘涂层的干燥炉的设计及生产工艺、结构特点等全部要素的设计方法,同时简单地介绍了漂浮器这一新设备。
关键词:冷轧无取向硅钢干燥炉设计DESIGN OF DRYING FURNACE IN CONTINUOUS ANNEALINGLINE FORCOLD ROLLED NON—ORIENTED SILICON STRIPGong Yanbing(Wuhan Iron & Steel Design And Research Institute)Abstract:On the base of theoretical and practical experiences the present article described in detail the design method about the drying furnace used for treatment of the insulation coating on the surface of the silicon steel, including design task, heating process and structure features.In addition a new equipment floater was briefly introduced.Keywords:cold rolled non oriented silicon strip drying furnace design1 前言在近年的国内无取向硅钢生产中,实践已经严峻地证明了干燥炉在连续退火线(APL)上的价值和地位。
它在让人们品尝顺利生产的喜悦的同时,也在扮演着制约生产的“瓶颈”的角色。
然而科技毕竟是无可质疑的,只要严格遵从先进的设计方法,“自顶向下,逐步求精”,和系统论原则,“整体等于部分之和”,不遗漏、不忽视任一设计要素,干燥炉一定是切实可靠的。
- 1、下载文档前请自行甄别文档内容的完整性,平台不提供额外的编辑、内容补充、找答案等附加服务。
- 2、"仅部分预览"的文档,不可在线预览部分如存在完整性等问题,可反馈申请退款(可完整预览的文档不适用该条件!)。
- 3、如文档侵犯您的权益,请联系客服反馈,我们会尽快为您处理(人工客服工作时间:9:00-18:30)。
在无取向硅钢连续退火机组中,为了将带钢的含碳量降到一定的范围,需要在炉内通入湿的保护气体,保护气体中的
H 2O 可以与C 发生反映:
H 2O+C=H 2+CO,完成脱碳过程。
在脱碳过程中,因为H 2O 与Fe 也会发生反应:H 2O+Fe=FeO+H 2[1],所以保护气体中需要加入一定浓度的氢气,用来还原被氧化的带钢。
因为氢气属于易燃易爆气体,所以在使用过程中需要格外的注意安全的问题。
为了控制炉内的氢气分布,需要精确控制各处的炉压值,使炉内的氢气可以按照设计好的路线流动,最终从温度较高的炉子入口处溢出,直接在空气中烧掉。
要防止氢气流向低温炉段,因为氢气在低温炉段聚集会有爆炸的危险。
为了实现上述目的,需要将炉内压力分布情况控制为从入口到出口程逐步递增的趋势。
如图一所示,无取向硅钢脱碳退火炉由入口密封、加热段、均热段、冷却段、出口密封组成。
硅钢在进行脱碳退火时,退火炉内通有氢气含量为25%左右的保护气体,氢气作为还原剂用来防止带钢在脱碳过程中被氧化。
为了安全利用炉内的氢
气,在硅钢连退机组设计过程中有着非常
周到的考虑,其中就包括对炉内压力的严格控制。
为了控制退火炉内的炉压,在冷却段和加热段入口处设有炉压控制点,包括炉压检测装置、泄压装置和连续氮气通入孔;冷却段炉压最高,此处炉压检测点S1的正常值为60Pa ;入口密封炉压最低,炉压检测点S3的正常值为30Pa ;在均热段设有氮氢混合气通入孔,此处布置炉压检测点S2,炉压值约为45Pa。
所以,通入的氮氢混合气体会流向压力比较低的方向,最终从入口密封处溢出退火炉。
因退火炉内的气体温度高达900℃,溢出的氢气会在空气中自动燃烧,从而保证了溢出气体的安全。
如果炉内的压力值波动幅度过大,会使氢气在炉内流向不稳定,从而导致安全隐患,所以在炉内压力控制功能设计上需要做如下考虑:
1.冷却段检测点S1处设置高压氮气通入孔,当此处压力低于设定值下限
(50Pa)时,由工业计算机自动开启高压氮气控制阀,给冷却段通入高压氮气。
在通入高压氮气的过程中,炉压检测设备实时将炉压值传回到工业计算机,直到此处炉压达到炉压设定值上限(70Pa)时,工业计算机自动切断高压氮气控制阀,完成一次炉压调整的过程。
2.加热段检测点S3处设置有泄压阀,通过计算机中心自动控制。
当S3检
测到的炉压值高于设定的上限值(40Pa)时,计算机自动开启泄压阀K。
炉
内泄出的高温氢气在泄压阀外自燃,同时
加热段的炉压开始降低,直到此处压力降到炉压设定值下限(20Pa),泄压阀才会被自动关闭,完成加热段自动调整炉压的过程。
3、工业计算机将S2与S1处的炉压值实时的进行比较。
当炉内压力波动导致S2>S1时,工业计算机也要自动开启高压氮气通入阀,给冷却段增压,直到S1>S2为止。
综上所述,在连续退火炉内控制压力时,首先要为各个炉段设置恰当的压力值。
因为压力值过高,会导致保护气体消耗量过大,生产成本过高;压力值过小时,会增加炉外空气进入炉内的风险,导致控制炉内气氛难度增大。
不同带钢种类和炉子密封形式对应的炉压设定值也会不尽相同。
其次,为保证各处炉压设定值,需要制定科学有效的应对方法,比如泄压或增加等手段。
最后,采用自动化控制系统,可以更有效地保证各处的炉压。
只有将各处炉压控制在一定的范围内,才能保证炉内氢气不会流向危险区域,为安全生产提供最有效的保障。
结论
炉压控制方法有很多种,不同的炉子结构都有各自最适合的控制方法。
在需要使用氢气做保护气体的连续退火炉内,不但要能够清楚的理解炉子结构,根据各炉区的特点制定相应的氢气应对措施,还要根据生产工艺要求,不同的炉内气氛,对炉压的要求程度也是不同的。
另外,在生产过程中,严格执行操作规程也是至关重要的,因为无论多么完善的控制方法,如果不能得到严格的执行,其危害都是不可估量的。
无取向硅钢连续退火炉炉压控制方法介绍
许庆绍 张振甲 天津项明武工程技术有限公司 100070
图一
无取向硅钢连续退火炉炉压控制方法介绍
作者:许庆绍, 张振甲
作者单位:天津项明武工程技术有限公司 100070
刊名:
电子制作
英文刊名:Practical Electronics
年,卷(期):2012(8)
1.王秉铨工业炉设计手册-2版 1996
本文链接:/Periodical_dzzz201208156.aspx。