模具动静态检测表
冲压模具检查记录表范例
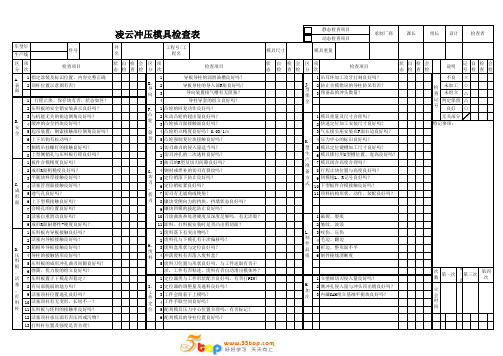
3 预备品的冲头数量?
全
1 模具重量及尺寸合理吗?
2 快速定位加工安装尺寸良好吗?
3 气压接头座安装在F面右边良好吗?
K. 4 压力中心的标识良好吗? 型 5 模具定位键槽加工尺寸良好吗?
生 6 模具锁付用U型槽位置、宽高良好吗?
产 准
7 模具闭合高度合理吗?
备 8 行程止块位置与高度良好吗?
方 9 闭模钮L、R记号良好吗? 式 10 下型板件合模接触良好吗?
12 活塞顶杆承压面有否压凹或污物?
13 打料杆位置及强度是否合理?
1 E. 2 导 向3
4
导板导柱的润滑油槽良好吗? 导板导柱的导入部R角良好吗?
导向装置排气槽有无阻塞? 导柱导套的组立良好吗?
F. 1 凸轮的回复动作良好吗?
凸 2 从动凸轮的超出量良好吗?
轮 、
3 凸轮插刀面接触面良好吗?
斜 4 凸轮组立精度良好吗?0.03/1m
凌云冲压模具检查表
静态检查项目 动态检查项目
承制厂商
课长
组长 设计
检查者
车型年 生产线
件号
件 名
工程号/工 程名
模具尺寸
模具重量
区项 分次
检查项目
状自检会 区项 态检查检 分次
检查项目
状 自 检会 区项 态 检 查检 分次
检查项目
状自检会 态检查检
说明
记自检会 号检查检
A. 1 指定涂装及标识位置、内容完整正确 表 2 顶杆位置示意图有否? 面
11 顶料机构形状、动作、装配良好吗?
1 破裂、裂痕
2 皱纹、波浪
L. 3 咬伤、压伤 制 4 毛边、翻边 件 品 5 折边、整形面不平 质 6 制件棱线清晰度
模具动静态检验标准

镶
材质是否与图纸
17 块 刃口吃入量
积料不超过 3 片。刃口吃入量 3-5mm。
18 与 接刀缝
间隙规测量 0.05mm 以下
19 刀 镶块补焊
补焊光顺,横向裂纹无,纵向裂纹 100 mm 内允许 3 条
20 口 镶块与安装底面
自由状态,贴合间隙小于 0.02mm/与基体或背托贴合率大于 90%
21 冲 标准异形冲头
凹模套在斜面上要有防转措施,小于等于¢8 的冲头采用快换冲头 材质、编号与实物一一对应;字体工整,醒目,内容齐全
15kg 以上或难于取出的镶块应有起吊螺纹孔,并有标示
检查时看导柱、导板间隙;如果是钢板变形量大,涂红丹看导柱间隙。
除压(托)料面,其他地方都要倒角
压(托)料板与刃口配合间隙 0.5-0.8mm 单边至少有两处定位,进料方向有导入角,并且刚性良好。 压料板上要有导正销,导正销突出压料板时要有退料销 活动部分必须有安全护板。 沉孔深度一致,正反面要倒角。螺钉拧入直径 2 倍以上。 工作时不起作用,但位置分布要合理,孔四周用黄漆标注 与沉孔一致,正反面倒角,螺钉紧入量是螺钉直径的 2 倍
8
上、下模型面 R 角光顺,棱线清晰,油石抛光
上
9
压边圈
下
压料面油石抛光;拉延筋(槽)圆顺光滑。
10 模 排气孔
钻孔¢6 应在凹处不影响制件外观
11
防尘管
紧固可靠,通畅
12
材质与硬度 材质依技术协议及图纸,硬度不低于 HRC50
13
拉延成型标记 标记深度 0.3mm,左右件用“L、R”代替, 压印不得留在 A 表上
型 型面及压料面
14 面 空研
上下模空研。平面着色
模具动静态检查表

零件图号 操作者
检查方法
目视
验收 123
9 修边口粗糙度
※ Ra<0.8,240#以上油石推光
粗糙度样块
10 修边口无咬合、擦黑、刮痕等现象
※ 空车4-5次
目视
11 修边口及刃口的状态
※
锋利、无缺口,崩刃,啃刃等现象,刃口垂 直,无倒椎
目视,直角尺
12
焊接刃口不能有气孔、夹渣及平行于刃口的 裂纹
※
允许垂直于刃口的微裂纹应控制在100mm≤3条 (长<2mm,宽<0.02mm,深度≤1mm)
目视
※ 筋内侧100%,外侧85%,均匀 ※ 板厚+0.25mm以上
红丹粉 红丹粉
7 型面、侧壁的间隙 8 拉延面、型面、棱线及圆角,拉延筋粗糙度 9 其它加工面精糙度
※ 板厚±0 Ra≤0.8,320#以上油石推光,圆角、筋细砂
※布 推光
※ Ra≤1.6
10
凸模凹模、压料圈等工作部位,凸圆角淬火 硬度
直角尺 厚薄规
5 上下模导向面中心
※ 应无错位现象
目视
6 导板导柱的导入圆角
※ R8-R10
R规
7 导滑面、导入圆角粗糙度
※ ≤0.8,平整顺滑,240#油石推光
粗糙度样块
导 8 导板、导柱配合使用时
※ 导板应先于导住导向
目视
向 9 导板止退台宽度
10 导板与止退台安装面配合 装
11 导柱与导套配合间隙 置
※
无划伤、裂纹、波纹、磕碰伤、气孔、砂眼、 塌角、凹陷等,缺陷<0.05mm以内
目视
※
必须按基准制作,不准随意打磨,修改,要保 产品图,工艺
证产品尺寸要求
模具验收检查表(动态)

全 5 压料圈的限位螺钉要对角固定(限位螺钉保证2个以上、起重孔应保证4个)
部
份
6
施压时聚胺脂缓冲器变形后不能与模具本体发生干涉,并且安装面面积应大 于变形后聚胺脂面积
7 聚胺脂安装螺钉要紧固
产品名称
2 判定 标记
合格 不合格 未装配 未确认
○
×
序号
△
——
检查时间
检查员
备注
无此项 /
1 拉延筋部位的间隙取(板厚+0.15mm以上)
车型
令号
模具图号
分类 NO
检查项目
1 导板及Ф60以上衬套应用铜基自润结构,不允许拉毛
2 导板导向间隙<0.12mm,间隙均匀
模 3 导滑面研合率的确认(红丹粉研合70%以上)
具 导
4 导板的垂直度要求应在0.03/150mm以内
向 5 上下模导向面中心有无错位 部
位 6 凸模和压边圈的导向间隙单边<0.12以下,两边保持均匀
7 导柱的导向间隙<0.03mm
模具检查专用表——模具动态(拉延序用)
模具名称
自 检
1
2
分 类
NO
1
检查项目 压料圈上升时,应与上底板无干涉(与上模应有50mm)
自检 1
2 气垫防护板要稳定,可靠(防护板高度=气垫行程+20mm)
3 到下死点时,聚胺脂防护板应有2-5mm间隙
安4
压料圈限位螺钉长度要比其它安装面长23-30mm
2 定位板有效导向部位高度应合适(导向高度=板料厚度+30mm)
定 位
3
定位板与安装面空开处间隙要满足使用要求,防止间隙过大使板 料变形或起皱
模具检查表(新型)(XLS)

模具检查表(新型)
最终检查日: 检查员: 模具番号: 模具品名: 厂家验收 顾客验收 设计担当
分 类
嵌和有无问题 有无防转销 是否打字码 (考虑保养) 是否有火(HRC58~60确认品质)
检 查 项 目 (径 杆 顶管冷却有无问题 顶管高度有无问题 时间差顶杆动作有无问题 (动作量) 孔内径是否用铰刀加工 是否使用了特殊型号(扁形 极细 阶梯 其他) 有无干涉 (径. 间距) 回 导柱是否使用沾火料 程 杆 回程杆的碰面是否良好 回程杆的头部是否倒角 推板上是否有冷却 厚度是否够. 是否会弯 推 分型面是否设计缓冲块或勒聚胺脂块 板 回位弹簧和导柱的位置设计有无问题(因弯曲而动作不良) 在表面按回位弹簧时要在背面把螺丝 角落的镶块要注意斜度的设定和推杆孔的间隙 顶 环式镶块要却认是否有冷却 出 环式镶块的有配管型. 动作时要确认是否有干涉 镶 块 环式镶块顶出时是否会因重量发生平衡不良(支点确认) 动作部位是否使用了无油导套和轴承 顶板和芯子和顶杆导柱位置有无错位 设定的行程能否顺畅动作 是否使用了中荷重的弹簧 早回位弹簧是否能顺畅回位(0面) 100T以上的自动落下无问题否 150T以上自动取出无问题否 有无顶杆回位确认限位(防止滑块和顶杆相互干涉) 有无强制回位的装置(防止滑块和顶杆相互干涉) 顶出有无白化 是否多肉 有无拉着 (顶杆. 导柱) 顶杆眼加工间距是否良好(有无紧) 离型的行程有无问题 动作时使用油缸的时候.构造和轴承是否无问题 是否使用特殊构造(轴承.2段顶出.斜向凸轮) 固定板上是否安装了顶杆孔用的垫片 出荷前顶杆是否清扫好(润滑油.研磨膏) 是否确认了备品的种类荷数量
排气导套是否有台肩或横向顶丝固定侧是否有保护锁块pl面上有突形吊物是否平衡各顶板的螺丝孔处理基准面是否有标记螺丝有无弯曲和龟裂确认部品350t的时候要使其能采取一点吊爱丽思的特别式样吊的平衡是否好挂上钢丝绳时有无干涉物对突出物品的保护是否到位固定板和对各个板上的水嘴的保护热流道模具在换色时型板是否能分离确认为防止各型板丢失是否进行了丝锥处理支脚4的粗细平衡性螺丝是否够深根据模具的重量选择的型号是否合适是否安全周围有无干涉物装卸有无问题有有有ok是否有标牌模具尺寸
模具验收通过判定标准

3)顶杆端部固定台阶为标准尺寸,
不允许有打磨痕,顶杆台阶下部不允
许安装垫圈
顶杆及孔
17
4)顶杆尾部的防转销按标准制作
检查
5)顶杆及顶杆固定板的对应编号规
范、清晰、不混淆
6)顶杆与型腔固定孔的配合长度在 30mm~50mm 之间
7)型腔顶杆固定孔与顶杆的配合尺 寸保证设计要求,保证成型时不漏塑 料
1)导柱、导套同心
4
内滑块检查
利取件
2)内滑块不转动和上下摆动
导柱、导套
5
保证生产过程中导柱、导套不单边和拉伤
检查
冷却水和抽
6
工作时不漏水、不漏油
芯油检查
模具喷嘴检
7
保证成型时不漏塑料
查
脱模性好、不用脱模剂,顶出时制品不自由
8
脱模性检查
下坠
5 件连续成
9
成型正常、不发生异常
型检查
30 件连续成
10
成型正常、不发生异常
25
检查
中不变形
1)使用规定材质,并出具材质报告
模具材质
26 检查
2)模具型腔、型芯必须进行探伤,并
出具探伤报告
标准件检
符合技术要求规定的标准件种类、数
27
查
量
综合判定:
甲方:
乙方:
签字: 日期:
签字: 日期:
2、模具动态验收标准见表 2
工装模具验收报告书 (动态检查)
类别:模具
名称:
序 检查项目
号
2)皮纹无锈蚀、无针眼
芯表观
要求,保证制品脱模时皮纹不拉伤
质量检查
4)无皮纹模具型腔表面粗糙度在 0.2
[过程验收]模具静检标准表
![[过程验收]模具静检标准表](https://img.taocdn.com/s3/m/b5f4183af111f18583d05a5f.png)
1 压料板缓冲的滑动行程良好吗? 2 压料板和切刀,曲刃的间隙良好吗? 3 弹簧,优力胶的装配良好吗? 4 5 6 7 压料板吊挂螺丝孔位置良好吗? 压料板与下模接触率是否良好? 模具有局部脆弱部位吗? 缓冲的逃孔良好吗?
H 切 刀 曲 刃 冲 8 冲孔衬套防止转良好吗? 孔 9 快换凸凹模的锁紧可靠,拆卸方便. 10 刃口无咬合、崩刃. 11 1 I 2 3 刃口镶块接合面间隙是否良好? 废料长度在指定尺寸以内吗? 废料滑槽的长、宽、高、度适当吗? 废料滑槽的倾斜角度有利于废料滑出?
K 钣 件 品 质
1 破裂,裂痕 2 重叠,皱纹 3 咬伤,刮伤 4 毛边,翻边 5 模具的接触率
模具合格证
发运 返工 × √
与机能无关的尖角是否有倒角? 安全防护板的安装.(气垫行程+20) 模具翻转处设置翻转R角?(保护起吊钢丝) 吊耳或吊棒大小合适?铸入吊柄紧固? 吊耳周围无铸造缺陷.
废 4 周围落料、切边废料排出是否良好? 料 5 废料落下孔与废料盒位置是否良好? 落 6 废料滑槽的安装与肋的逃隙良好吗?制品形状的配合好吗? 投 2 定位器的调整量及逃隙好吗? 入 3 制品会附着在上模或下模吗? 取 4 定位器类的固定良好吗? 出 5 制品手取空间良好吗? 1 模具重量及尺寸适当吗? 2 模具定位用快速定位块的安装良好吗? 3 模具定位键槽良好吗?
不良 × 检未装配,未加工 ◇ 查 判定保存 △ 记 良好 ○ 号 无关部分 检查日期: 年月
日
特记事项:
7 上模/下模/压料芯具有翻转孔? 8 起吊棒必须自锁. 9 模具导向有防反? 1 2 C 3 型 面 4 5 6 D 压 料 与 缓 冲 制品与下模基准面的接触率良好吗?(85%) 模具的基准面钣厚确认? 制品与压料板接触好吗? 透油,透气良好吗?(防尘管) 上下模平衡块、墩靠块是否贴合? 模具型面的表面粗糙度良好吗?
冲压模具验收动静态检查表

A
√
/
/
87
安全护板
厚度22∙Omm,操作安全
C
√
/
/
88
销钉
松紧合适,上下各销•半,安装防脱落装置
C
√
√
√
√
89
侧销孔
船销直径+0∙2mm=侧销孔宜径,无兄动
A
/
√
√
Z
90
侧销固定长度
原则上固定25mm根据直径大小现场判定
A
/
√
√
/
91
侧销锁板销钉
锁板按要求安装摞钉孔不允许人工打磨或加工
65
翻边整形刃口面
顺滑,无凸凹不平等缺陷
B
/
/
/
√
66
翻边整形块安装
间隙W0.05mm,无台阶,圆角顺滑一致
B
/
/\
/
√
67
翻边顶出器顶杆
螺钉孔与顶杆壁厚保证3-5M
B
/
/
/
√
冲压模具静态验收检查表
项目
CN200
零件名称
螺母片
备注:符合要求填写,不符合要求填写“X”,不适用填写
*7”具体问题填入“模具问题记录表”
目视
B
/
7
4
/
102
防护板涂黄色
目视
C
√
Z
/
Z
103
取出压料芯前需要先拆除的镶块涂红色
目视
A
/
√
/
/
104
模具存放块外周边涂红色.
目视
A
√
√
模具验收静检查表附录7

18
表面粗糙度(压料面)
未精加工处无残留突起,镶块研磨。
修边切口、翻边刃口
19
刃口(上刃、下刃)
刃口不能有啃坏、堆塌、擦痕。接合面间隙∠0.05mm。修边
侧销、固定销、安全销
锁板是否满足要求。圆孔与销的配合是否符合要求。压板螺钉是否满足要求。确认锁止状态是否可靠。行程限位销尾部端面“H”标识,安全销尾部端面“S”标识。
36
12
型面研配(用制件)
研配精度良好。DCH和CH销使用时的符贴程度(S面全部符贴)。销与制件及模具不存在松动现象。
13
补焊(重要形状及重要部位不得补焊处理)
不得有气孔、塌角、毛刺、不平、沙眼。焊接宽度合理。修整后外观质量良好。
14
模具强度
铸件毛胚不允许存在缺损现象。镶块加强部位保证强度足够。有侧向力的部位,加强筋的强度和布局要合理,C15或R。
从后方向看,左前和右后两个位置。安全区底部有加强筋(有足够的承受强度)□150mm,周边用15mm宽黄色线表示。
33
安全(退料板螺钉、防护板)
安全长度:行程+L。安全板(参照安全线)全部白色。螺钉头或螺钉沉孔处、入口处涂白色。
34
工作行程限制板(固定螺钉、板)
长度,行程。板调质后安装(D/W安装)。螺钉头或螺钉沉孔处、入口处涂红色。
30
起重螺孔(起重、翻转)
起吊时的平衡。螺纹直径、深度(直径的1.5倍)是否满足起吊要求。倾斜处要加工窝座。起重孔的边缘距边的最小尺寸(螺径/3)。
31
安全保管装置(套管、橡胶)
链条位置和长度是否合理。存放限制器的键槽方向是否正确。稳定性。安全防护盖、红色。安全装置无变形。
模具试模前检查表(塑胶模具)

序号备注1234567891011121314151617181920日 期:日 期:日 期:模具试模前检查表进胶口按图纸开通OK □ NG □OK □ NG □检查结果及处理意见:钳 工:品 质:品质课长:模具运水/油路/气路刻印相关字码,如“IN” “OUT” OK □ NG □OK □ NG □试模前按图面装上限位开关OK □ NG □OK □ NG □滑动部位加润滑油OK □ NG □OK □ NG □按照修改模资料中的内容修改模具OK □ NG □OK □ NG □模仁排气按设计要求加工OK □ NG □OK □ NG □试模前装上锁模片OK □ NG □OK □ NG □后模顶棍孔直径符合图纸OK □ NG □OK □ NG □导套底部开排气OK □ NG □OK □ NG □模仁镶件/镶针/日期章等零件无漏装OK □ NG □OK □ NG □胶塞孔内光滑,口部做R过渡OK □ NG □OK □ NG □模仁省模省到位OK □ NG □OK □ NG □模仁按客户要求蚀纹/蚀字OK □ NG □OK □ NG □流道光滑OK □ NG □OK □ NG □唧嘴球R符合图纸要求OK □ NG □OK □ NG □顶针/斜顶动作顺畅OK □ NG □OK □ NG □行位动作顺畅OK □ NG □OK □ NG □通过20PSI 水压测试不漏水(时限3分钟)OK □ NG □OK □ NG □三板模水口板滑动顺利,水口板易拉开OK □ NG □OK □ NG □检 查 内 容钳工自检QC判 定fit模红丹fit到位OK □ NG □OK □ NG □产品名称穴 数 □修改模客户名称试模次数第 次 □其它(塑胶模具)表格编号:模具编号制模组别 □新 模。
模具动静态检查表--

目视
2 导柱与导套配合间隙 向 3 导板面配合间隙 装 4 滑动导板接触面接合率
▲ 无单边接触,无损伤 大型<0.1,中型<0.08,反侧导板≤
▲
0.01 ▲ ≥85%,分布均匀
5 斜楔机构运动导滑面
▲ 间隙<0.03mm
置
6
各种斜楔机构运动灵活,扒钩间隙合 理
扒钩间隙侧冲0.5~1mm, ▲ 吊冲<0.03mm
目视 目视 目视
5 起吊孔的螺纹规格 检 6 压板槽位置、尺寸及数量
● 按用户和图纸要求 ▲ 按图纸尺寸
目视 直尺
查 7 模具定位键或定位孔 8 空气管接头座及电气安装位置
▲ 按图纸尺寸 ▲ 按图纸尺寸,不能超出模体
直尺 目视
9 闭合高度检查
▲ 按图纸尺寸
卷尺
导 1 导向面粗糙度
●
工作面和导入圆角粗糙度0.8,支承面 粗糙度1.6
︶ 部
11
10°~30°斜面冲裁时,冲孔及修边凸 模处理
工作刃口提前切入深度按2个料厚处 ▲ 理,冲头是否防转
直尺 目视
分 12 刃口切入量
▲ 按图纸规定
直尺
13
退料板与凸模,压料板与凹模的导正 间隙
▲ 间隙0.3~0.5mm
成 1 镶块接缝间隙 形 ︵ 2 工作面粗糙度
拉 延 3 工作表面无缺陷 、
● ≤0.01mm
成 7 凸凹模镶块材料牌号及件号标记
● 打印清晰,无凸起
形 8 上模销孔加丝堵
● 是否防止上模销子松动脱落
、 9 拉延模到底标记
整 形
10
卸料板型面与工件接触面
高于型面 ▲ 0.3mm,工件表 ▲ 是否产生压痕
模具动静态检验标准

上模销孔有防落措施,销不过紧过松,同一直径长度一致打入模座 1/2
深度一致,倒角 3×45 角,弹簧与面接触平稳、可靠,力量足够。
导
31
导柱、导套及间隙 向
32
废料处理
操
33 作 废料
34 性 废料装置
35
制件操作性与定位
36
防呆
37 安 安全护板
38 全 加垫
39
防反
40 41 外
观 42
43 44 其 45 他 试模次
8
上、下模型面 R 角光顺,棱线清晰,油石抛光
上
9
压边圈
下
压料面油石抛光;拉延筋(槽)圆顺光滑。
10 模 排气孔
钻孔¢6 应在凹处不影响制件外观
11
防尘管
紧固可靠,通畅
12
材质与硬度 材质依技术协议及图纸,硬度不低于 HRC50
13
拉延成型标记 标记深度 0.3mm,左右件用“L、R”代替, 压印不得留在 A 表上
5
检 中心键、快速 与(所选压机)图纸一致,机床精加工。中心槽为通槽(双动模除外) 查 定位
6
三销刻印
准确、齐全、工整、清晰
7
铸件外观
无夹砂、裂痕、变形和大的铸造缺陷、所有非工作面棱角倒角
承制 厂商 NO1 NO2
8
模具的标识 对于零件号、车型号、模具名称、工序号、模具号、模具铭牌、F、其他技术要求标识等
体
4 检 U 槽位置、数量
与图纸一致;L≥1500mm 6-8 个,L<1500 mm4-6 个
36 观 位颜色
客户指定颜色
37
铭牌、顶杆图 内容填写齐全、准确、清晰,顶杆顶出高度与图纸相符
福锐静动态验收表 (2)
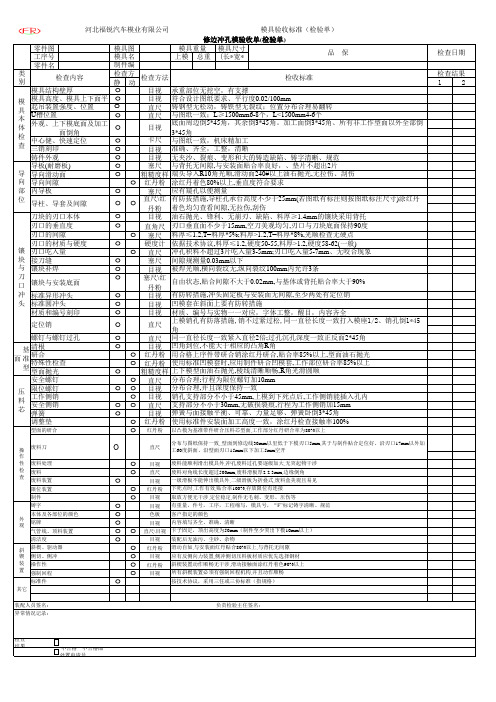
零件图模具尺寸工序号上模总重(长*宽*零件名静动12目视目视直尺直尺卡尺目视目视塞尺粗糙度样红丹粉塞尺目视直角尺塞尺硬度计直尺塞尺目视塞尺\红丹粉目视目视目视直尺目视红丹粉红丹粉粗糙度样直尺目视目视直尺目视红丹粉红丹粉目视直尺目视红丹粉目视目视色板目视直尺\目视目视红丹粉目视红丹粉目视检查结果 不合格 不合格品处置申请号废料刀直尺制件编检查方铸钢型无松动,铸铁型无裂纹;位置分布合理易翻转与图纸一致;L ≥1500mm6-8个,L<1500mm4-6个检收标准定位销上模销孔有防落措施,销不过紧过松,同一直径长度一致打入模座1/2、销孔倒1*45角直尺导板(耐磨板)与背托无间隙,与安装面贴合率良好,、垫片不超出2片三销刻印检查结果检查内容检查方法目视U 槽位置起吊装置强度、位置用合格上序件带研合销涂红丹研合,贴合率85%以上,型面油石抛光有防拔措施,导柱孔承台高度不少于25mm(若图纸有标注则按图纸标注尺寸)涂红丹着色均匀查看间隙,无拉伤,刮伤刀块的刃口本体油石抛光、锋利、无崩刃、缺陷、料厚≥1.4mm 的镶块采用背托刃口的垂直度刃口垂直面不少于15mm,空刀美观均匀,刃口与刀块底面保持90度刃口的间隙镶块与安装底面料厚≤1.2,T=料厚*5%;料厚>1.2,T=料厚*8%,光顺检查无硬点分布与图纸保持一致,,型面到修边线30mm 以里低于下模刃口5mm,其于与制件贴合定位好、沿刃口17mm 以外加工60度斜面、沿型面刃口15mm 以下加工5mm 空开自由状态,贴合间隙不大于0.02mm,与基体或背托贴合率大于90%标准异形冲头有防转措施,冲头固定板与安装面无间隙,至少两处有定位销凹模套在斜面上要有防转措施螺钉与螺钉过孔同一直径长度一致紧入直径2倍;过孔沉孔深度一致正反面2*45角清根凹角到位,不能大于相应的凸角R 角研合使用标准凹模套时,应用制件研合凹模套,工作部位研合率85%以上型面抛光上下模型面油石抛光,棱线清晰顺畅,R 角光滑圆顺型面的研合以凸模为基准带件研合压料芯型面,工作部分红丹研合率为80%以上特殊性检查废料装置一级滑板不能伸出模具外,二级滑板为折叠式,废料盒美观且易见限位装置下死点时,工作有效,贴合率100%,存放限位有连接废料处理废料能顺利滑出模具外,冲孔废料过孔要逐级加大,无突起物干涉废料制件取放方便无干涉,定位稳定,制件无毛刺、变形、压伤等斜楔、驱动器侧切、侧冲操作性强制回程模具名内容填写齐全、准确、清晰清洁度装配后无油污、尘砂、杂物标准件按技术协议,采用三住或三协标准(指规格)滑动自如,与安装面红丹贴合80%以上,与背托无间隙材质、编号与实物一一对应,字体工整,醒目,内容齐全河北福锐汽车模业有限公司模具验收标准(检验单)修边冲孔模验收单(检验单)模具图模具重量品 保检查日期承重部位无挖空,有支撑准确、齐全,工整,清晰铸件外观无夹沙、裂痕、变形和大的铸造缺陷、铸字清晰、规范与图纸一致,机床精加工外观、上下模底面及加工面倒角类别底面周边倒5*45角,其余倒3*45角。
静态检查表
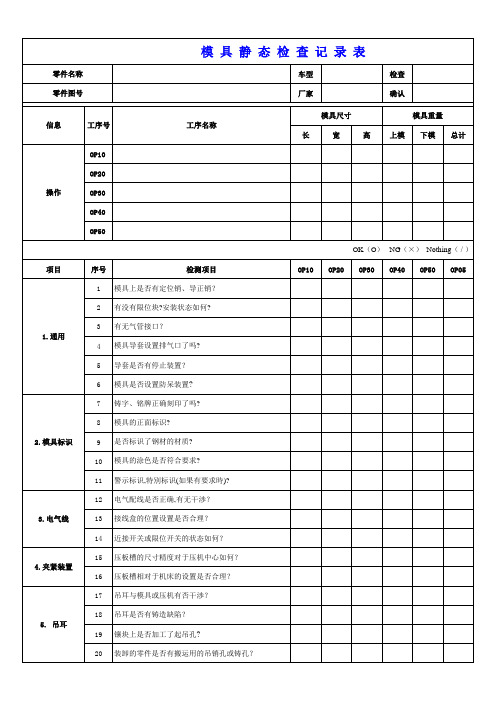
模具静态检查记录表
零件名称 零件图号
车型 厂家
检查 确认
信息 操作
工序号
OP10 OP20 OP30 OP40 OP50
工序名称
项目 1.通用
2.模具标识 3.电气线
4.夹紧装置 5. 吊耳
序号
检测项目
1 模具上是否有定位销、导正销?
2 有没有限位块?安装状态如何?
3 有无气管接口?
4 模具导套设置排气口了吗?
5 导套是否有停止装置?
6 模具是否设置防呆装置?
7 铸字、铭牌正确刻印了吗?
8 模具的正面标识?
9 是否标识了钢材的材质?
41 衬套的周围有充分保证强度的壁厚吗?
10.切边冲孔模 42 切刀是否取了剪切角度?
43 刃口的状态好吗?
44 堆焊后的刃口有没有横裂口竖裂口堆焊部有否针孔?
11. 翻边整形模
45 模具有无到底标识? 46 翻边、整形后模腔表面是否有凹痕?
47 斜契块彻底返回情况如何?
12. 斜契块
48 飞转斜契的强制返回如何?
31 模具是否有排气管,空气流通状态如何?
32 模具有无到底标识?
33 模具是否有顶料装置?
34 压边圈是否有拉紧螺栓?
9. 拉延模
35 加强筋,压边圈,凹凸的成形部表面状态如何?
36 与产品接触的表面状态如何?
37 圆角半径处的光顺情况?
38 平衡块正确地安装了吗?
39 平衡块下是否设置了竖筋?
模具的维护保养

模具的维护保养知识模具的一级保养模具的一级保养指的是在生产中操作人员对模具进行和日常保养,主要内容为清擦、润滑和检查。
一、装模时的保养1、装模前要对模具的上下表面进行清擦,保证模具安装面和压机工作台面不受压伤及模具在生产中上下安装面的平行度。
2、模具装好后将模具打开,将模具各部分清擦干净,特别是导向机构,对于表面件模具,其型面清擦干净,以保证制件的质量。
3、对模具各滑动部份进行润滑,涂润滑脂。
模具各部份的检查,特别是安全件。
如:安全侧销、安全螺钉、侧护板、冲孔废料道等。
二、生产中的保养1、生产中定期对模具的相应部分进行涂油。
如:拉延模的压料圈、圆角;修边模的刀口部位;翻边刀块部分等。
2、定期对修边冲孔模的小孔废料道进行废料的清理。
三、生产后的保养1、生产结束后要对模具进行全面的检查。
2、模具进行全面的清擦,保证模具的清洁度。
3、将模具内的废料清理干净,保证废料盒中无废料。
4、将模具的使用状态和使用后的情况如实地反馈到模具传票上。
模具的二级保养模具的二级保养指的是根据模具的技术状态和复杂程度而制定的对模具进行的定期系统的保养。
此项保养工作由模修人员完成,并根据保养情况作好记录。
以下就不同的零件叙述其二保的要求和方法。
拉延模凸模、凹模:拉延模的凸、凹模主要出现的问题是拉毛及型面的压坑,保养时主要对模具的圆角拉毛部位进行抛光。
如果出现压坑要对模具进行补焊,再进行修顺。
导向零件(导柱、导套及导板等):模具在工作中会出现拉痕等现象。
产生和主要原因有润滑油脏及导向间隙偏等。
导零件产生拉痕采取用油石推顺后抛光的办法进行消除。
修边刀口:模具在使用过程中刀口部分易出现崩刃和刃口塌陷现象。
此时要对模具损坏的刀口进行补焊修配。
(具体方法后详细介绍)弹簧等弹性零件:在使用过程中,弹簧是模具最易损坏的零件之一,通常出现断裂和变形现象。
采取的办法就是更换,但是更换过程中一定要注意弹簧的规格和型号,弹簧的规格型号通过颜色、外径和长度三项确定,只有在此三项都相同的情况下才可以更换。
工装模具日常点检记录表

123456789101112131415161718192021222324252627282930311
确定工装模具是否与过程控制卡要求相符2
外观(脏、损伤、配件缺失)3工装各部位紧固螺栓是
否松动4各定位基点,是否磨损
5防,放错功能检查
6导柱、滑块、润滑检查
操作工:班组长:
日期
记录符号:正常 √ 异常 × 已修好ⓧ 非故障停机 空白
1、模具是否能保证产品的尺寸精度要求,暂通过对产品首件检验,以及生产过程中的自检、巡检、完工检等检验手段进行确定!如有发现产品不良,在排除因模 具因素造成不良之前,所用模具不得再投入生产。
2、本记录由操作工填写,班组长、工装管理员监督;发现异常现像应速与班组长或工装管理员联系。
3、不同产品以及不同夹具名称的夹具点检不能填写在同一张点检记录上。
NO 项目
工装模具日常点检记录
年 月
班组名称:模具名称:模具编号:。
14 模具动静检查表

★
123
斜楔必须设置背托或底部镶键,滑动自如,与背托无间隙
重量15kg以上或难于取出的斜楔应有起吊螺纹孔,起重孔统一设置
124
M20、M16;
125
废料滑板的安装位置不得影响螺栓以及废料刀的拆卸与安装
★
126
侧冲必须有观察孔,排废料孔。
D
127
废料必须100%能滑落到模具以外(自动化模具必须100%滑出工作 台)
118
斜楔和驱动导向接触时上、下模导向在50mm以上
D
斜楔
119
机构 斜楔滑动前必须保证斜楔驱动装置先接触接触面的40%,其工作时斜 楔驱动装置之间至少80%充分接触
D
120
斜楔压料芯必须是上模压料板压住后才开始工作
D
121
斜楔滑动体在下模时,必须保证斜楔不得与送件、取件动作干涉
D
122
大型斜楔在上模时,必须考虑其安全性
94
多状态模具的切换工具需要运动自如,操作方便,并有相应操作说 D ★
95
氮明气缸相对应压料芯底部必须设置垫块
96
模具要考虑防反措施,对称零件要考虑定位的防反;
D★
97
模具安全平台尺寸符合要求
D
98
拉延工序的压边圈安全限位的A≥10mm,模座上的限位平台必须等 D
安高全限位螺钉分布合理,过孔支撑不小于30mm,深度为限位螺钉行
★
40
侧冲孔时,冲头需采用带顶针的结构,同时,有废料防堵塞装置
所有拼块,镶块都有销钉,且有防反,防错设计,销钉吃入其长度
41
的1/2,销钉的松紧程度通过拔销器来测定
易折断的凸模或使用球锁止凸模时,冲孔凸模周围的压料装置采用
钢板模具动静态检查表
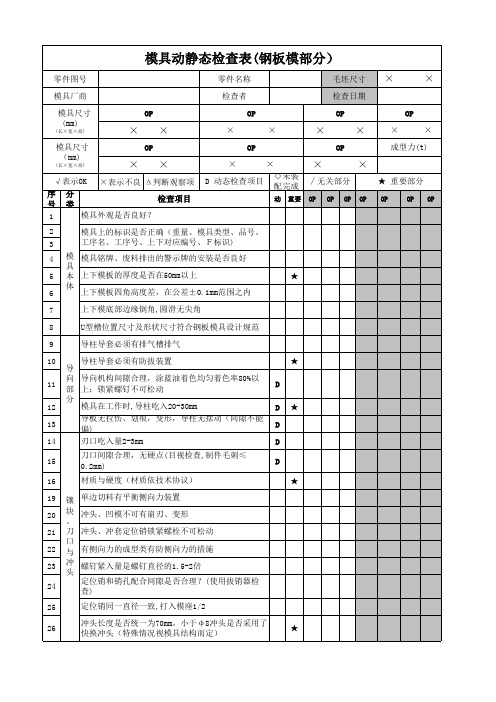
D D
D D
★ ★
64 65 66 67 68
标准件全部按协议要求使用 模柄需采用法兰式模柄 其 到底标记深度0.3mm,不易辨别左右件用L、R代替 它 制件无起皱、压伤、隐裂、棱线清晰,符合数模 制件毛刺≤0.2mm
★
D D
验收结论
ห้องสมุดไป่ตู้
确认人
动 重要 OP OP OP OP
★ 重要部分
OP OP OP
1 2 3 4 5 6 7 8 9 10 11 12 13 14 15 16 19 20 21 22 23 24 25 26 镶 块 、 刀 口 与 冲 头
模具外观是否良好? 模具上的标识是否正确(重量、模具类型、品号、 工序名、工序号、上下对应编号、F标识) 模 模具铭牌、废料排出的警示牌的安装是否良好 具 本 上下模板的厚度是否在50mm以上 体 上下模板四角高度差,在公差±0.1mm范围之内 上下模底部边缘倒角,圆滑无尖角 U型槽位置尺寸及形状尺寸符合钢板模具设计规范 导柱导套必须有排气槽排气 导柱导套必须有防拔装置 导 向 导向机构间隙合理,涂蓝油着色均匀着色率80%以 部 上;锁紧螺钉不可松动 分 模具在工作时,导柱吃入20-30mm 导板无拉伤、划痕,变形,导柱无摆动(间隙不能 偏) 刃口吃入量2-3mm 刀口间隙合理,无硬点(目视检查,制件毛刺≤ 0.2mm) 材质与硬度(材质依技术协议) 单边切料有平衡侧向力装置 冲头、凹模不可有崩刃、变形 冲头、冲套定位销锁紧螺栓不可松动 有侧向力的成型类有防侧向力的措施 螺钉紧入量是螺钉直径的1.5-2倍 定位销和销孔配合间隙是否合理?(使用拔销器检 查) 定位销同一直径一致,打入模座1/2 冲头长度是否统一为70mm,小于φ 8冲头是否采用了 快换冲头(特殊情况视模具结构而定) ★ ★ D D D D D ★ ★
模具状况及成形状况检查表
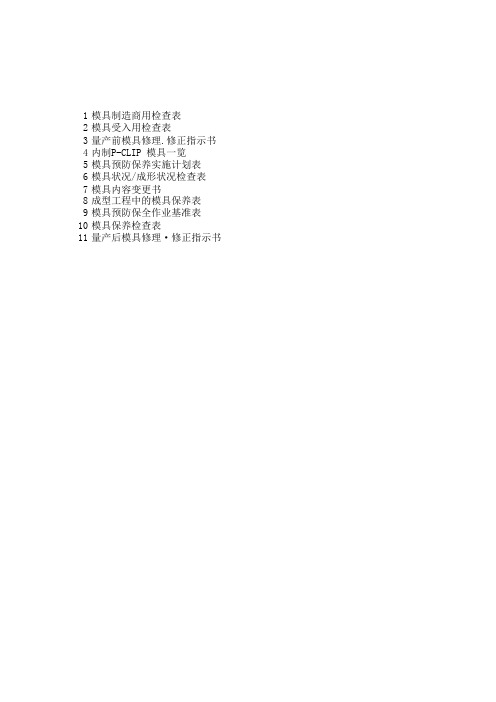
顶出导销的,导销套的清扫
弹簧,支撑块的清扫
一般分型面的清扫
用无尘布擦拭一般分型面 产 流道部的清扫 品 及 镶块部的清扫
滑 定位块的清扫 块 部 侧芯滑块的清扫
滑块导轨的清扫
确认带有球形活塞的模具的运作
确认吊眼螺丝的变形
确认吊眼螺丝的插入状况
其 确认定位环上的是否有严重的划伤等 它 确认模具联结器的变形,损伤
给品保5模以上样品
品担 质当 确
认承 认
流程:成型课—技术课—模具制造商—技术课-成型课-品质保证课(最终承认)-技术课(保管)
量产后模具修理·修正指示书
NO.
不具合内容
对策指示内容
费用明细(模具制造商记录栏)
工程
时间
及
零件
单价
金额
合计
修理内容(模具制造商记录)
模具制造商确认 印
模具接收日 STPS 制造商
1 有否确认模具图纸?
2 顶针孔是否呈三点式?
3 安装板是否是指定厚度?
4 吊环螺栓是否如指示?
5 是否是2点平行悬吊状或在定模上?
6 有否安装铭牌?
7 冷却水的IN、OUT是否在操作侧的反面?
8 是否安装指示?
10 模具是否能简单闭拢?滑块是否能用手轻易拨动?
Ⅳ
制定,改订 制定 改订
0~1万模/月
年月日 2004-8-2
—01 —02 —03 —04
作成
根据模具预防保养作业基 准书实施
确认
承认
备注
模具状况/成形状况检查表
Mold Condition Check List
质量记录编号: 品名:
日期
品号:
/ (星 / (星 / (星 / (星 / (星 / (星 / (星