培训资料(胶印常见故障)
第六章 印刷工艺常见故障分析

解决方法
目前解决印刷品背面粘脏,一般采用下面的措施: (1) 使用快干油墨,对于卷筒纸胶印机来说采用红外干燥器。 (2)使用预防背面粘脏的喷粉。 (3)采用隔凉架,减少堆纸层高度。 (4)对粗糙的纸张采用加大印压减少墨量的方法印刷。 (5)控制润湿液的PH值及用量,防止油墨乳化。 (6)调节车间温、湿度并对印刷色序重新安排。 (7)图文的实地面积过大,印后加强通风。 (8)调整干燥剂用量。 (9)采用防粘脏剂或加粘衬纸的方法。
解决方法
1) 加入新墨或在油墨 中加入亮光连结料。2) 换用高光泽的油墨或 用吸收性差的纸张。 3) 适当加些干燥剂。 4) 对已印成的印刷品,可用罩光油处理。 5)印刷品“泛白”的处理:调整好印刷油墨 所用的溶剂,减少挥发快的溶剂用量,控制车 间空气中相对温度在65%以下。
六、褪色
在印刷过程中油墨的颜色褪掉,或印刷品 在堆放中(在干燥过程中)油墨的颜色褪掉, 其原因是: (1)纸堆中由于油墨的氧化作用而产生 热,这个热量会使油墨颜色褪掉。 (2)油墨中使用的干燥剂含钴太多。 (3)颜料不耐热或油墨中颜料含量太少。 (4)配浅色时,白色油墨选用不合适。
三、油墨因素引起的花版
(1)油墨粘度过大,使版面产生花版。油墨粘度过大,除了 使印迹转印困难外,还会破坏墨层中间断裂的条件,使版面剩余 墨层不足,因图文部分裸露受磨损造成花版。 处理方法:适量加一些撤粘剂,降低油墨粘性,但不要让油 墨流动性增加太多。 (2)油墨粘度过小,使印版糊版,粘度小的油墨易乳化,造 成浮脏,油墨不能正常地转移,使墨辊、印版和橡皮布上逐渐堆 积颜料颗粒。当颜料颗粒在印版上堆积到一定厚度时,就会引起 糊版,有时因版面剩余墨层不足造成花版。 处理方法:适当加进一些0号调墨油。 (3)油墨流动性过大会使网点扩大变形 油墨流动性不足使 印版产生花版,油墨流动性过大,则墨层易铺展,使印迹几何尺 寸扩大,网点不能正确复制,油墨流动性不足往往传布不匀,造 成印版着墨不足而花版。 处理方法:根据油墨流动性可选用不同的调墨油。
典型胶印故障分析与排除—印刷条杠故障分析与排除
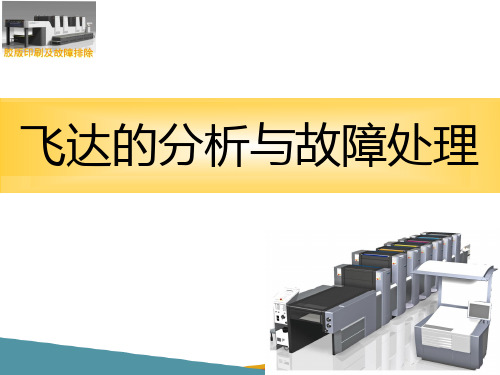
3.齐纸机构
纸堆前沿应低于 齐纸板4~6mm
4.传送带装置
•工作要求: ⑴ 要保证传送带辊与接纸辊同步运行,即传送带上的纸速 与接纸滚上的纸速应该相同。 ⑵ 保证4~6根线带厚薄需均匀,对称分布,张紧程度一致 ⑶ 为避免线带和带辊打滑,主动带辊表面应滚花处理
传送带装置主要包括主动带辊、从动带辊、传送带和张紧轮。
2.输纸部分常用部件及其作用
分纸吸嘴
吸嘴按其工作原理不同有两种类型,即直动型和差动型。 • a.直动型:接通吸气气路后,在弹簧力的作用下活塞移到下部
位置准备吸取纸张。 • b.差动型:当未接通吸气气路时,在弹簧力的作用下,活塞达
上部位置。
2.输纸部分常用部件及其作用
压纸吹嘴机构
当纸堆表面平整,纸堆面与 前齐纸板、分纸吸嘴的距离误 差相同时,通过调节螺母9, 在压纸吹嘴机件5伸长时,纸 堆面就降低一点,缩短可使纸 堆面升高。
飞达各部件之间的关系
•分纸吸嘴吸起纸张时,压脚开始下压。 •分纸吸嘴把吸起的纸张交给递纸吸嘴。这部分运动可分为三个阶段: a.分纸吸嘴吸起纸张后,递纸吸嘴开始吸纸; b.分纸吸嘴和递纸吸嘴共同持纸一段时间; c.分纸吸嘴放纸,递纸吸嘴持纸向前运动。 •递纸吸嘴把传过来的纸张交给接纸辊,接纸辊上的压轮压住纸张后, 两者共持一段时间纸,递纸吸嘴放纸。 •分纸吸嘴吸第二张纸时,压脚应提前离开纸堆。
尽可能做到不停机补充纸张。 • (6)在输纸过程中,不能损伤纸张,对已印刷的表面,不能产生蹭脏
现象。 • (7)当出现双张、纸张歪斜或残纸等故障时,要有可靠的自动停机安
全装置。 • (8)机构简单,操作方便,占地面积小。在机器运转过程中,能进行
必要的调整。
2、自动给纸机的组成
印刷故障集合

印刷故障集合(转)(一)套印不准1、轴向(来去)不准(拉纸不准a、拉不到和拉过头。
b、推不到和推过头。
2、周向(上下)不准(前规不准)a、走不到。
b、走过头。
3、局部不准4、正反面套印不准5、间隔性套印不准套印不准有多种情况,其原因也十分复杂,比较简捷的方法是通过树状图(鱼刺图)来醒目地提示我们,这是比较通常的做法。
(二)糊版由于目前有水平版印刷几乎都用PS 版,因此这里所指的印版均指PS版(如果没有特别指明的话)。
1、瞎眼字字号小、而笔画又多的字,其笔画多的空白处容易糊并且分不清笔画,被称为瞎眼字。
它分为:A、新版一上墨就有的瞎眼字,这种脏版有两种可能性:a、新版上字号小、而笔画又多的字,笔画之间有残留的亲油的感光胶膜,造成新版一上墨就有瞎眼字,这一般通过修版笔来修正或者重新晒版来解决。
B、新版空白部分没问题,只是新版上墨时,笔划之间没有润湿液来保护,造成新版一上墨就有的瞎眼字(字糊并了)。
这要及时用润湿液、阿拉伯树胶液或PS版洁版膏处理之。
b、新版印刷一段时间后才有的瞎眼字,一般是该处给水过多少或者油墨过于稀薄造成笔画多的地方成为瞎眼字。
这要及时调整供水量和印刷油墨的流动性,并用PS版洁版膏处理该处。
2、脏版又称为油腻、起脏、油脏、挂脏、龌龊等,即印版空白部分着了墨,这可以是局部脏版、也可以是全面脏版。
根据脏版在印刷过程中发生的时段可分为:A、新版一上墨就有的脏(版)。
这种脏版有两种可能:a、新版空白部分有残留的亲油的感光胶膜,造成新版一上墨就有的脏。
这要用专用的PS版修版膏或PS 版修版笔来清除之,但是使用时务必注意,千万不能把它涂在图文感光膜层有很强的清除作用。
B、新版空白部分本身并没问题,一般是该处给水过少或者润湿液来保护,造成新版式一上墨就有的脏。
因此新版上墨时,空白部分应有适度的润湿液来保护之。
b、新版印刷一段时间后才有的脏版,一般是该处给水过少或者润湿液组合分不妥或者该处的砂目已基本磨损所致。
胶印常见故障

a.滚筒齿轮或轴承轴颈使用年久磨损。
b.滚筒轴颈与滚筒壳体不同心。
c.靠版辊与印版压力过重,而产生跳动
(2)墨辊部分
a.使用年久墨辊表面老化
b.墨辊长期没能得到清洗,表面积墨,造成不能上墨
ห้องสมุดไป่ตู้
c.油墨粘度太大
(2)纸张
a.纸张裁切精度不高;
b.印刷时水量过大,纸张有伸缩。
(3)其它
a.印版或原稿本身有问题;
b.卡纸堆的过高或压纸块压的过重而导致卡纸走斜。
左右套位不准:
a.左右挡板过紧或左右挡板螺丝是否固定;
a.印版本身质量不高(版基不好或再生版);
b.晒版时曝光时间不足、显影液浓度太低;
c.印版版面的保护胶未清洗干净;
d.印版的空白部分被氧化;
(2)印刷机
a.靠版压力过轻;
b.水辊间的压力太轻;
c.油墨粘度过低;
(2)靠版辊与印版压力过轻,应重新调节其压力(2.5-3mm);
(3)靠版辊与印版压力过重,应减少其压力;
(4)润版水酸性太强,应适当降低润版水的酸性;
(5)油墨过稀,应在油墨中加“0#“调墨油;
(6)墨量太大,应减少供墨量;
(7)油墨中干燥剂加放过量,应清洗墨辊,减少油墨中干燥剂的用量;
(7)纸张粗糙,表面强度差。应勤洗橡皮布,并在油墨中加入6#调墨油以降低油墨的黏度,减轻纸张脱粉、掉毛的程度
十四、水杠产生原因及消除
水杠指的是在印刷平网或实地印件时,印版版面及印件上出现轴向的一条条明显的浅条痕,俗称“白条杠”或“白条头”。水杠一般是由输水部分引起的,产生的原因及解决办法是:
(3)齿轮间嵌有纸毛、墨皮等污物。应清除齿轮间各种污物,加入新的齿轮润滑油,加强对机器的清洁保养工作;
常见印刷故障分析及解决对策

常见印刷故障分析及解决对策刮刀线痕(刀丝、刀线)1.1刮刀线痕产生的原因①无油墨的线痕。
主要是油墨中混入了坚硬的无机杂质,如沙子等。
②较粗的有油墨的连续刮刀线痕。
是由于一些软性粒子顶起了刮墨刀,或刃口损伤而产生。
③“流星”状的刮刀线痕。
这类刮刀线痕一般在印刷版辊的网点很浅或未雕刻网点部分出现,时隐时现,危害大也较复杂。
涉及到油墨.制版很多因素。
主要原理是:版与刮刀产生的铬离子和油墨中的“活性粒子”结合并吸附在版辊上所导致的。
④细丝状的连续性刮刀线痕。
这类刮刀线痕细小,像头发丝一样。
其产生的原因很复杂。
总的来说,大概有如下几个方面。
a.辊筒表面镀铬层硬度不够光洁度不好。
b.油墨细度不够。
c.车间内空气的温度、湿度和洁净也会影响,特别是温度和湿度的突然变化。
d.静电方面。
e.刮刀方面。
硬的刮刀比软的刮刀产生的线痕要多。
1.2处理对策第一类的无油墨的刮刀线痕,处理时将刮刀稍微松开,用竹刀轻按刀身或轻擦,或升高压辊,将刮刀完全松开,让油墨将硬粒子带走。
处理时注意不能太用力,以防弄伤版辊。
第二类刮刀线痕是最简单的,只要用竹刀擦去即可,如果是刮刀损伤的,则要换刀。
第三类刀线痕(流星式或循环性刮刀痕)。
这类刮线的处理较难,需综合进行。
方法为:①过滤油墨。
②加入活性减缓剂消除印刷过程中产生的活性基团。
③横扫磨版。
用50目的金相砂纸对印刷版辊进行横扫式磨版。
④刮刀也应作适度的研磨及调整。
第四类刮刀线痕(细丝状刮刀线痕)。
这种线痕的处理最复杂,必须认真分析清楚产生原因。
基本的处理方法为:①用50目金相砂纸轻轻贴在线痕处磨版。
注意磨的时候砂纸能轻轻贴住。
另外,印刷速度太慢也不能使用此方法。
②过滤油墨或用另一桶油墨,甚至换另一类型油墨。
③使用印刷辅助剂也有一定作用,但加入助剂后必须保证油墨完全循环过滤。
在磨完版后先用助剂洗版,再添加于油墨中效果更好。
④轻度刀线时使用快干溶剂。
⑤改善印刷机的消除静电功能及在油墨中加入一定的抗静电剂。
胶印各种不良原因
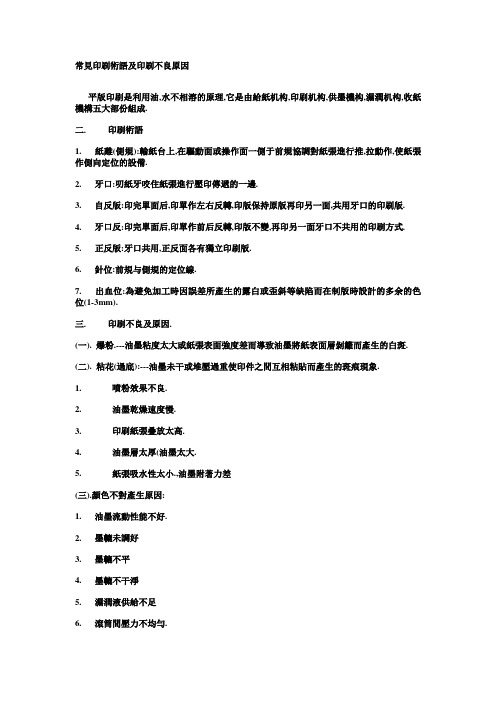
常見印刷術語及印刷不良原因平版印刷是利用油,水不相溶的原理,它是由給紙机构,印刷机构,供墨機构,濕潤机构,收紙機構五大部份組成.二. 印刷術語1. 紙雞(側規):輸紙台上,在驅動面或操作面一側于前規協調對紙張進行推,拉動作,使紙張作側向定位的設備.2. 牙口:叨紙牙咬住紙張進行壓印傳遞的一邊.3. 自反版:印完單面后,印單作左右反轉,印版保持原版再印另一面,共用牙口的印刷版.4. 牙口反:印完單面后,印單作前后反轉,印版不變,再印另一面牙口不共用的印刷方式.5. 正反版:牙口共用,正反面各有獨立印刷版.6. 針位:前規与側規的定位線.7. 出血位:為避免加工時因誤差所產生的露白或歪斜等缺陷而在制版時設計的多余的色位(1-3mm).三. 印刷不良及原因.(一). 爆粉.---油墨粘度太大或紙張表面強度差而導致油墨將紙表面層剝籬而產生的白斑.(二). 粘花(過底):---油墨未干或堆壓過重使印件之間互相粘貼而產生的斑痕現象.1. 噴粉效果不良.2. 油墨乾燥速度慢.3. 印刷紙張疊放太高.4. 油墨層太厚(油墨太大.5. 紙張吸水性太小.,油墨附著力差(三).顏色不對產生原因:1. 油墨流動性能不好.2. 墨轆未調好3. 墨轆不平4. 墨轆不干淨5. 濕潤液供給不足6. 滾筒間壓力不均勻.7. 紙張厚薄不均.8. 紙張上墨不良9. 油墨調色不均勻(2).顏色跟不上色稿1. 印墨厚薄未調好2. 油墨顏色偏差3. 紙張顏色偏差4. 晒版時間偏差5. 色序不當6. 套印不準7. 网點不同8. 潤濕液調節不當9. 壓力未調好10. 色稿有問題(雙勾).(3).色差(一批產品中出現多種)1. 機器老化(雙鉤)2. 洗膠布后行頭紙未抹干淨3. 紙張起波浪4. 調墨不勻5. 機器性能不穩定6. 生產過程中調機7. 水干,水大8. 紙張顏色偏差(四).墨屎,紙毛.---因墨皮或紙毛堆積使油墨不能正常轉移到紙上而產生斑塊,小白圈現象.產生原因:1. 紙張掉粉,掉毛.2. 裁切邊的紙張割裂粉沬.3. 在印机墨轆上兩端的干印墨.4. 在印机水轆上兩端的干印墨5. 印墨已在墨缸或木桶上面結皮,印墨轉移印机之前,所有結皮未除去.6. 舊印墨結皮后處理不當混入.7. 印墨中雜質.8. 濕潤液中雜塊.(五). 凹膠布.---因膠布襯墊不均勻,某處凹陷,使壓印時沒有足夠的壓力致使橡皮上的油墨不能完全轉移到紙上圖文不清晰.(六). 粘膠布.---由于紙質強度不夠,易破(撕)裂,在運轉過程中被粘在膠布上,而產生的大塊圖像不著墨或墨層太厚.1. 由于油墨粘度太大,紙与墨的分離小于墨的粘度易使紙張被撕裂而產生粘膠布.2. 機器咬紙不穩定,使走紙不暢順,導致粘膠布.(七).水干.---水量調控不當,產生水小不足以潤濕印版,致使印版模糊導致印件臟污.產生原因:1. 水轆未落.2. 水轆可能變形.3. 沒印刷水.4. 水轆調節不當.5. 印刷時水量過小.(八). 水大.---水量調不當,產生水大,使得某處墨色不鮮艷發白現象.(九).雙勾.---因紙張伸縮變形或機械精密度原因使印跡產生重影或顏色偏.(十).鬼影.---墨位較大的實地版或网版,由于部份地方是空白的部份,墨轆上的墨沒有轉移而當其轉移到圖文部份時,其上墨量較大,而其他地方上墨均勻,則形成鬼影..(十一). 套印不正.1. 拼版不正.2. 叼紙牙磨損.3. 紙張的吸水性能不穩定,吸水后伸長不一.4. 機器性能不穩定.5. 擺動牙位置不當.6. 套印機械調節不當.7. 滾筒包襯不符合要求.8. 紙張含水量不勻,四邊起波浪或緊邊造成紙張伸縮或皺折.9. 印版供水量過大,使紙張伸長.10. 紙張絲綹不符合印刷要求.11. 環境,溫度的改變,造成紙張伸縮.(十二). 重影.1. 滾筒襯墊沒墊好..2. 因紙張伸長不一,導致套印不正而產生.3. 紙起波浪.4. 機器故障.5. 紙張厚薄不勻.(十三).擦花,打花.1. 由于收紙部件調校不當或因紙輕薄使紙張印件在收紙過程中紙于紙相互磨擦造成擦花.2. 工人拿紙過程中,拿紙方法不當產生.3. 排骨位打花.4. 紙張吸鳳摯未調好.5. 紙張太細,太硬所致.6. 印反面時炮打花.7. 印刷紙机位擦花.8. 收紙時兩張間擦花.9. 刮墨屎時打花.10. 抽紙不當擦花.(十四).噴粉大.1. 噴粉嘴故障,導致噴粉不勻,堆積.2. 因排風扇調節不當吹風不勻,導致噴粉擴散不勻,產生噴粉大.3. 噴粉劑量大.(十五).爆粉,紙毛.1. 因紙施膠度不夠,紙質疏松不平滑,印刷時易起毛,爆粉,粘于印版或膠布上,進而轉移到印件上形成紙毛.2. 因紙張表面強度不夠,易使紙起毛,粘結到印版或膠布上,進而轉移到印件上形成紙毛.(十六).滴粉.---由于机頭噴粉堆積未清理乾凈,而掉于印件產生.(十七).陰陽色.1. 晒版時因晒版机吸气不均勻造成菲林于印版接触不均勻,使得网點密度有變.2. 顯影時顯影液攪拌不勻,導致顯影液濃度不勻,使得印版顯影效果不一致.3. 印刷時因多處水墨量調控不勻,引起供墨量不同.(十八).版臟.1. 晒版時菲林(原版)未清洗乾凈留有污漬.2. 晒版机玻璃未清洗乾凈,留有污漬,雜質.3. 印刷時因雜質紙毛等粘貼于印版上.(十九).字崩.1. 植字時因針頭靈敏度不穩定,導致字斷線引起.2. 晒版時因灰塵等雜質落于菲林(在字上).3. 修版時不小心涂掉某處,使字斷線.4. 紙毛(片)粘於印版上某處使不能正常轉移導致.5. 膠布被壓坏,凹進去導致油墨轉移不到.(二十).版花.1. 复制菲林時刮花,晒版時未注意印版版花.2. 不停机打墨屎或擦印版時因鋒利器刮花印版而致.(二十一).缺字.1. 因電腦植字時漏植.2. 顯影后,修版時不小心涂掉.3. 膠布被壓坏.(二十二).墨杠.(墨轆痕)1. 因機器性能穩定,水輥于印版壓力調節當(不均衡)影響某處供水量;2. 因機器性能不穩定,墨輥于印版壓力調節當(不均衡)影響某處供墨量. (二十三).滴水.1. 水路調控不當;2. 水量大.3. 水斗空間形成的水蒸汽溶解,增加水量形成.(二十四). 墨杠.1. 水轆污臟.2. 橡皮布及水膠絨老化.3. 滾筒襯墊不當.4. 印刷壓力過大.5. 滾筒間壓力不均勻.6. 打墨屎所致.。
胶印常见问题分析与解决

第一节胶印常见问题分析及解决一、胶印故障的形成胶印故障大致分为机械故障、印刷工艺技术故障、材料引起的故障、操作环境和维护保养造成的故障及电器故障等内容。
(一)、机械故障因素印刷机械产生的故障最多。
即使是新的胶印机,由于设计装配和安装调试中的某些缺陷,在工作中也会出现故障.一台胶印机由上万个零部件组成,各部件的制造加工精度极为重要,国产胶印机由于加工机件的工作母机及操作技术的条件限制,一些零件达不到先进水平,也是造成机械故障的一个因素。
有的胶印机如主机中的齿轮、滚筒加工质量较好,但配套件技术性能差,也会给正常印刷带来麻烦.例如有的胶印机水斗加水配置的真空水箱,达不到真空要求,自动加水经常失灵,导致水斗和版面缺水,操作者稍不注意,就会发生印品上脏糊版故障。
胶印机的安装和调试工作也很重要。
许多工厂安装机器前做地脚基础时,忽略了地面强度和硬度问题。
现在中、高速的胶印机对机器底座的水平要求极高:纵向允许水平误差不能超过0.08/1000,横向水平误差不能超过0。
04/1000,用机器底座下校正水平的底脚螺丝调节。
如J2108型机底座下有8只校正螺丝,螺丝的触地点垫8cm方铁,校正水平后,用螺帽扣紧底座,以防底脚螺丝自行走动,问题在于:现在机器的底座不着地,而靠8只底脚螺丝支撑,因为下面要放油盘,不可能再用水泥填封,故要求地基表面强度较高,而说明书上注明用200 号水泥,实际改用400号水泥较好,并在地基上层轧钢筋,否则地脚螺丝触地点受震动后,水泥容易损坏或开裂,机器失去水平。
特别是滚筒轴颈、轴套磨损快,就会造成重影、杠子等印刷故障。
机器使用到一定年限以后,由于机件逐渐磨损,精度下降,就会出现各种故障.机件磨损的快慢,除了保养不善的因素外,还同机件使用的材质及加工制造工艺有关。
例如胶木制做的进纸压球,容易磨损成椭圆形,造成输纸歪斜故障。
又如,受力不匀的万向轴转球和叉节,磨损后会产生输纸停顿故障。
压印咬牙轴摆杆和滚球,会由于受力大而不均,使推拔销松动、断裂、滚球轴承破碎,造成套印不准或设备事故。
胶版印刷过程的常见印刷故障及解决方法

胶版印刷过程的常见印刷故障及解决方法胶版印刷是一种常用的印刷方法,但在实际操作中可能会遇到一些印刷故障。
下面是一些常见的胶版印刷故障及其解决方法:1.印版表面出现光点或颗粒状物质:出现这种情况可能是由于油墨中含有固体颗粒,或者是印版表面有污染物。
解决方法是检查油墨并进行筛网处理,清洗印版表面。
2.网点锐化不良:出现这种情况可能是由于调和油低,网点过细或者油墨流动性差。
解决方法是调整调和油的含量,适当增加油墨的流动性,调整网点大小。
3.印刷品出现横纹或挤出现象:出现这种情况可能是由于过量的油墨,印刷压力过大或速度过快。
解决方法是控制油墨的用量,适当降低印刷压力或减慢印刷速度。
4.印刷品颜色不均匀:出现这种情况可能是由于油墨颜料分散不均匀,或者是印刷压力不均匀。
解决方法是调整油墨的均匀性,调整印刷压力,确保颜色均匀。
5.印刷品出现脱色或褪色现象:出现这种情况可能是由于油墨中颜料含量不足,或者是油墨质量低。
解决方法是增加油墨中颜料的含量,选择质量较好的油墨。
6.印刷品出现模糊不清的字迹:出现这种情况可能是由于印刷压力过小,油墨流动性差或印刷速度过快。
解决方法是增加印刷压力,调整油墨的流动性,适当减慢印刷速度。
7.印刷品出现纸张翘曲或皱纹:出现这种情况可能是由于纸张湿度不均匀,或者是印版表面湿度不足。
解决方法是调整纸张湿度,确保印版表面有足够的湿度。
8.印刷品出现网点粘连或铺展:出现这种情况可能是由于油墨粘度过高,过量的油墨或印版表面过湿。
解决方法是调整油墨粘度,控制油墨的用量,适当调整印版表面的湿度。
9.印刷品出现印痕或抖动现象:出现这种情况可能是由于印刷机构调整不良,或者是松紧带传动松动。
解决方法是调整印刷机构,确保印刷机正常工作,检查并紧固松紧带。
10.印刷品出现水墨分离现象:出现这种情况可能是由于水和油墨没有完全混合,或者是油墨品质较差。
解决方法是调整水和油墨的混合比例,选择质量较好的油墨。
胶印常见故障的分析与处理

方案。囤
作 者 地 址 : 湖 北省 老 河 口市 北 京路 树 脂 厂 院 内
发 生 ,一定要 事先 向油墨 的供应 者提 出 包 装 印 刷 油 墨 的 具 体 要 求——适 应 范
装印 刷工序相协调 ,才能取得 良好 的包
责 任 编 辑 /继 红 余
一
4 4一
一
广 东印刷 2 0 . - 0 85
由于油墨的颜料性 能不好 ,采 用了劣质 的有机颜料 ,或者
异质颜料 混入使用 ,以致 发生了化 学反应导致 色变 。这种 油墨 不适 宜用于彩色印刷 。
0
印 技 刷术
瓣 獭 麟 粼辅醴 蓬嚣 端 簧 黼 妻
一
— 一
一 技术 专栏
造成墨色不均匀和糊 版故障 。这 主要是 由于油墨 中燥 油用量过
度 ,以及空气湿度过 分干燥 引起 的 。对 上述 原因造成 的油墨在 墨辊上结皮 ,可加入 适量 的止干 油 ,以达 到抑制其干燥 速度 的
使之 与纸张的特性相匹配 。
二 、油墨 不 良引起 的故 障
1 油 墨 干 燥 不 良 .
当纸 张的表面 强度差 ,印刷 时纸 毛 ( 植物纤维)就 容易被
当油墨干燥过 陕会 造成墨层早期结 膜现 象 ,印刷 时就 容易
此认识 到 油墨快 速 图文成 膜 的重 要性 。 如果我们 不能很快地使 包装 印刷墨膜 干
刷油墨 的配方设计 和制造 工艺 、健 全的 油墨 印刷 的成 品质量标准 ……只有 与包
个包 装 印刷操 作工如在 临 上机前
才调墨将会 浪费很 多时间 ,用刚 调的 油
导致这样 或那样 的印刷故 障 的最佳 解决
墨 上机 试印 , 品也会 给企 业资金 上带 废
常见的印刷故障及解决办法

受各种因素的影响,印刷过程中难免发生各种故障,影响印刷品质量,这就要求印刷操作工人必须具备对印品故障的判别能力,并能根据故障进行相应印刷参数调节。
1.印品破损故障分析与解决印品破损主要指纸张叼口部分破损,造成破损的原因及调节方法如下。
(1)递纸牙和滚筒叼牙不准确。
调节方法:对输纸器进行正确调节,或对前规高低进行一定调整。
(2)胶印机收纸部分叼牙排的各个叼牙调节不当。
纠正方法:将收纸牙排各个牙垫重新调节,使其平直、高低一致,再仔细调节一下叼牙的叼力,使其均衡。
2.印品褶皱故障分析与解决(1)纸张出现“荷叶边”或“紧边”等现象,使纸张不能在平整状态下进行印刷。
调节方法:对印刷车间进行调湿处理,保持车间温湿度恒定,一般要求温度23℃±3℃,湿度50%±5%;建立与印刷环境温湿度相同或相差不大的纸库,保持纸张含水量稳定。
(2)滚筒压力不一致。
叼纸牙叼住纸张进入滚筒时纸面会有气流产生,若滚压瞬间不能均匀辗赶气流使纸张均匀受压,就会产生褶皱。
调节方法:校准滚筒压力。
按照设备规定的标准包衬和压力进行调整,并进行多次测量与计算,使滚筒压力均匀一致;及时更换橡皮布,以防因其老化失去弹性而造成印品褶皱。
北京科雷阳光印刷技术有限公司(3)叼纸牙叼力不同或叼纸牙交接时间不一致,造成纸张整体位移或变形量不一致。
调节方法:检查叼纸牙。
重点对叼纸牙牙垫平整度、牙片齐整度、叼力均匀度、牙套配合间隙、叼纸牙撑簧弹性等方面进行检查,还要检查相关的螺丝和销轴是否松动、断裂等,以保证纸张平稳交接。
(4)滚筒表面堆积脏物,使滚筒表面不平整,纸张受压不匀,产生褶皱。
调节方法:及时清理滚筒表面和滚枕上的脏物,并保持清洁。
3.印品斑点故障分析与解决(1)纸张表面不规则,即纸张平滑度低,导致纸张表面受墨不匀而出现斑点。
调节方法:更换纸张,适当增加印刷压力等。
(2)油墨乳化严重。
对于透明度好的油墨来说,油墨乳化太快,会使油墨黏性降低,施加较大的印刷压力时,纸张表面凸出部分油墨很容易被挤掉,油墨落在印版实地等部位时就会产生斑点。
胶印常见的问题与解决方法
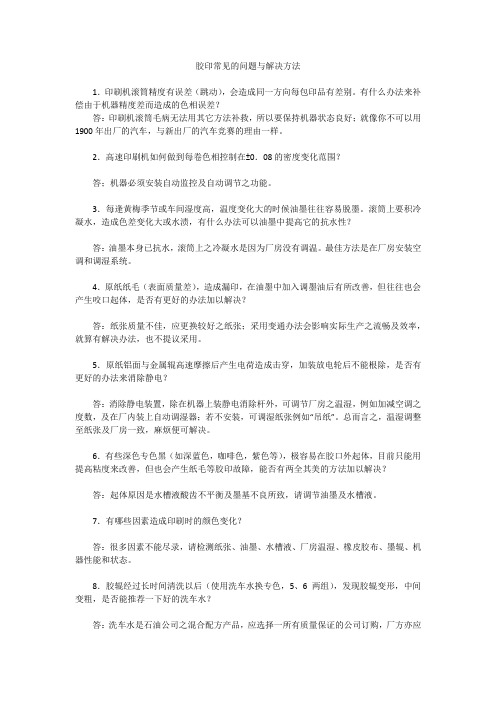
胶印常见的问题与解决方法1.印刷机滚筒精度有误差(跳动),会造成同一方向每包印品有差别。
有什么办法来补偿由于机器精度差而造成的色相误差?答:印刷机滚筒毛病无法用其它方法补救,所以要保持机器状态良好;就像你不可以用1900年出厂的汽车,与新出厂的汽车竞赛的理由一样。
2.高速印刷机如何做到每卷色相控制在±0.08的密度变化范围?答;机器必须安装自动监控及自动调节之功能。
3.每逢黄梅季节或车间湿度高,温度变化大的时候油墨往往容易脱墨。
滚筒上要积冷凝水,造成色差变化大或水渍,有什么办法可以油墨中提高它的抗水性?答:油墨本身已抗水,滚筒上之冷凝水是因为厂房没有调温。
最佳方法是在厂房安装空调和调湿系统。
4.原纸纸毛(表面质量差),造成漏印,在油墨中加入调墨油后有所改善,但往往也会产生咬口起体,是否有更好的办法加以解决?答:纸张质量不佳,应更换较好之纸张;采用变通办法会影响实际生产之流畅及效率,就算有解决办法,也不提议采用。
5.原纸铝面与金属辊高速摩擦后产生电荷造成击穿,加装放电轮后不能根除,是否有更好的办法来消除静电?答:消除静电装置,除在机器上装静电消除杆外,可调节厂房之温湿,例如加减空调之度数,及在厂内装上自动调湿器;若不安装,可调湿纸张例如“吊纸”。
总而言之,温湿调整至纸张及厂房一致,麻烦便可解决。
6.有些深色专色黑(如深蓝色,咖啡色,紫色等),极容易在胶口外起体,目前只能用提高粘度来改善,但也会产生纸毛等胶印故障,能否有两全其美的方法加以解决?答:起体原因是水槽液酸齿不平衡及墨基不良所致,请调节油墨及水槽液。
7.有哪些因素造成印刷时的颜色变化?答:很多因素不能尽录,请检测纸张、油墨、水槽液、厂房温湿、橡皮胶布、墨辊、机器性能和状态。
8.胶辊经过长时间清洗以后(使用洗车水换专色,5、6两组),发现胶辊变形,中间变粗,是否能推荐一下好的洗车水?答:洗车水是石油公司之混合配方产品,应选择一所有质量保证的公司订购,厂方亦应自行试验哪一种洗车水适合应用;采用进口洗车水太昂贵,不直推荐。
印刷过程中常见胶印故障原因及处理方法
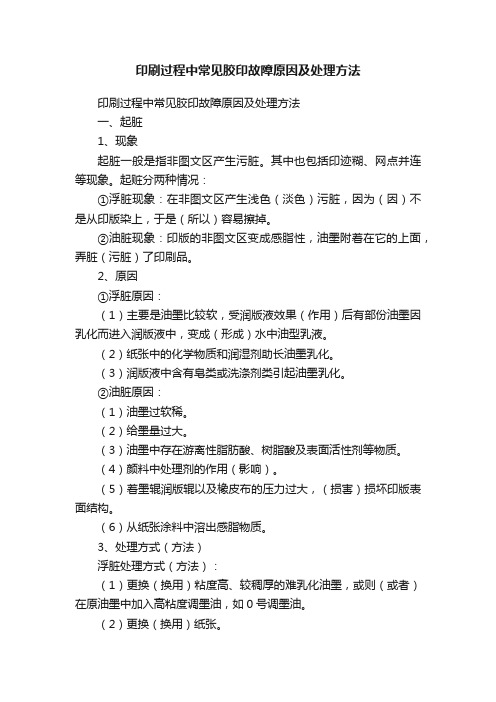
印刷过程中常见胶印故障原因及处理方法印刷过程中常见胶印故障原因及处理方法一、起脏1、现象起脏一般是指非图文区产生污脏。
其中也包括印迹糊、网点并连等现象。
起赃分两种情况:①浮脏现象:在非图文区产生浅色(淡色)污脏,因为(因)不是从印版染上,于是(所以)容易擦掉。
②油脏现象:印版的非图文区变成感脂性,油墨附着在它的上面,弄脏(污脏)了印刷品。
2、原因①浮脏原因:(1)主要是油墨比较软,受润版液效果(作用)后有部份油墨因乳化而进入润版液中,变成(形成)水中油型乳液。
(2)纸张中的化学物质和润湿剂助长油墨乳化。
(3)润版液中含有皂类或洗涤剂类引起油墨乳化。
②油脏原因:(1)油墨过软稀。
(2)给墨量过大。
(3)油墨中存在游离性脂肪酸、树脂酸及表面活性剂等物质。
(4)颜料中处理剂的作用(影响)。
(5)着墨辊润版辊以及橡皮布的压力过大,(损害)损坏印版表面结构。
(6)从纸张涂料中溶出感脂物质。
3、处理方式(方法)浮脏处理方式(方法):(1)更换(换用)粘度高、较稠厚的难乳化油墨,或则(或者)在原油墨中加入高粘度调墨油,如0号调墨油。
(2)更换(换用)纸张。
(3)调整(调节)润版液组成成分(组份)和pH值。
(4)调整水量和墨量。
油脏处理方式(方法):(1)更换油墨或者在原墨中加入高粘度树脂油或0号调墨油,使油墨具有粘性和弹性。
(2)调节(调整)供墨量。
(3)调节(调整)润版液适当用量。
(4)使用表面张力较低的润版液。
(5)将压力调适宜(适当)。
(6)换用(更换)纸张。
二、套印不良1、现象湿对湿套印时后面印刷的油墨,不能顺利地粘着(附着)在先印刷的油墨上。
2、原因(1) 与先印的油墨相比后印的油墨粘性过高。
(2) 先印的油墨固着慢而且墨量大。
(3) 四色油墨的颜色强度平衡不合适(适当)。
3、处理方式(方法)选用(采用)粘性高的油墨先印刷,粘性低的油墨后印刷,比较合意(理想)的粘性要求是应该(应当)按套印颜色的顺序陆续下降(降低)。
15种最常见的胶印机故障及解决方法

15种最常见的胶印故障及解决方法一、墨斗脱墨。
现象:油墨不能够从墨斗转移到墨辊上,供墨减少或中断,印品颜色变浅。
原因:油墨流动性差,墨性太短(如黄油状),油墨粘度小,触变性大,不搅动时形成胶体。
解决方法:经常搅动墨斗中的油墨,加入粘度高,流动性好的油墨。
加入高粘度树脂油以改善油墨的流动性。
二、堆橡皮。
现象:油墨堆积在橡皮布上,不能转移到纸上。
原因:油墨粘度小,抗水性差,油墨中颜料和填充料太多,细度不够,纸粉剥落混入油墨中使油墨变短,防粘脏剂和撤粘剂的加入量太大。
解决方法:尽量减少润版液的含量,加入粘度大,抗水性好的油墨,减少防粘脏剂和撤胶剂的用量,更换纸张。
三、堆墨辊。
现象:墨辊上的油墨传递不下去。
原因:油墨的抗水性差或印刷药水用量过大导致油墨乳化,油墨墨性太短,粘度小,流动性差。
解决方法:减少给水量或药水中加入异丙醇来提高润湿性,增加挥发性,加入粘度大,流动性好的油墨。
四、飞墨。
现象:在墨辊之间形成雾状的油墨微滴散落在机器周围。
原因:印刷速度过快,给墨量太大,墨辊上墨层太厚。
油墨偏粘,丝头长,墨辊安装不合适或磨损。
解决方法:降低印刷速度,换用颜色浓度高的油墨,减少给墨量,用撤粘剂降低油墨粘度,调整墨辊压力,使其墨膜厚薄均匀,调节棘轮加大墨辊的轴向运动来增加串墨量,更换损坏的墨辊。
五、匀墨不好。
现象:印品墨色不均匀,图案不清晰。
原因:油墨太稠太粘,油墨在印版,墨辊上干燥,印版滚筒衬垫,橡皮滚筒衬垫不合适。
解决方法:用调墨油降低油墨的粘稠度,如干燥过快适当加入525防结皮剂1%~3%;重新调整印版和橡皮布衬垫。
六、拉纸毛。
现象:印刷时有小部分纸毛纤维从纸面上拨下来,堆积在橡皮布的图文上。
原因:油墨粘性大,纸张表面强度低,印刷速度太快,压力太大。
解决方法:降低印刷速度,在油墨中加入撤粘剂降低油墨粘性,更换表面强度高的纸张。
七、环状白斑。
现象:印品图文部分出现环状白色的斑点。
原因:油墨中墨皮混进油墨中附着在印版橡皮布上,纸屑,灰尘等其他异物混入油墨中。
胶印机印刷常见故障及原因
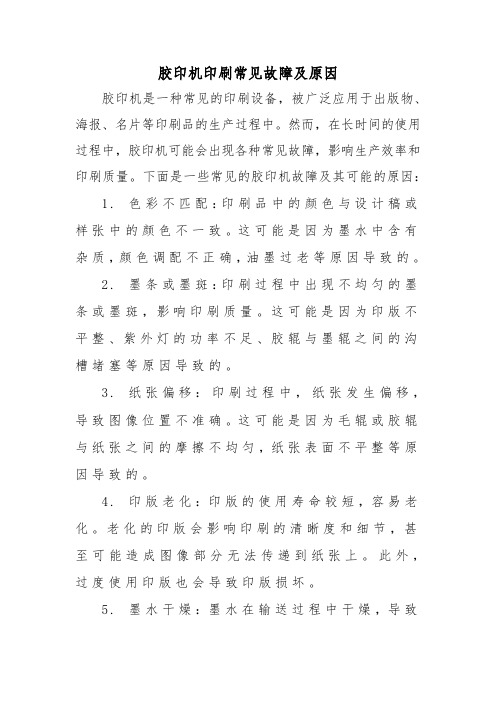
胶印机印刷常见故障及原因胶印机是一种常见的印刷设备,被广泛应用于出版物、海报、名片等印刷品的生产过程中。
然而,在长时间的使用过程中,胶印机可能会出现各种常见故障,影响生产效率和印刷质量。
下面是一些常见的胶印机故障及其可能的原因:1.色彩不匹配:印刷品中的颜色与设计稿或样张中的颜色不一致。
这可能是因为墨水中含有杂质,颜色调配不正确,油墨过老等原因导致的。
2.墨条或墨斑:印刷过程中出现不均匀的墨条或墨斑,影响印刷质量。
这可能是因为印版不平整、紫外灯的功率不足、胶辊与墨辊之间的沟槽堵塞等原因导致的。
3.纸张偏移:印刷过程中,纸张发生偏移,导致图像位置不准确。
这可能是因为毛辊或胶辊与纸张之间的摩擦不均匀,纸张表面不平整等原因导致的。
4.印版老化:印版的使用寿命较短,容易老化。
老化的印版会影响印刷的清晰度和细节,甚至可能造成图像部分无法传递到纸张上。
此外,过度使用印版也会导致印版损坏。
5.墨水干燥:墨水在输送过程中干燥,导致无法正常传递到纸张上,影响印刷质量。
这可能是因为环境湿度过低、墨水中溶剂含量不足等原因导致的。
6.印品起蜡:印品表面出现起蜡现象,导致图像模糊不清。
这可能是因为墨水中的油墨成分过多,纸张表面处理不当等原因导致的。
7.胶辊或墨辊损坏:胶印机的胶辊和墨辊在长时间使用后可能会磨损,影响印刷质量。
损坏的胶辊和墨辊可能需要更换或修复。
8.油墨污染:墨水在印刷过程中可能会污染印刷机的其他部件,影响印刷质量。
这可能是因为墨水泄漏、墨水箱堵塞、墨辊表面不洁净等原因导致的。
9.电气故障:印刷机的电气部件可能会出现故障,导致无法正常运行。
这可能是因为电源故障、控制柜内部线路故障等原因导致的。
10.机械故障:印刷机的机械部件可能会出现故障,影响印刷效果和生产效率。
这可能是因为传动带断裂、轴承磨损等原因导致的。
为了避免以上故障的发生,需要定期对胶印机进行维护和保养,包括清洁胶印机各部件、更换旧的印版和墨水、调整机器的各项参数等。
胶印故障分析及解决方案

S t andar d椽灌胶印故障分析及解决方案印刷过程中出现的各种故障,一般来说很少由单一因素所致,多因油墨、纸张、印刷药水以及印刷环境条件不协调、相互影响所致。
本文将研究各个印刷要素与印刷故障之间的关系,主要从油墨、印刷药水、纸张、环境温湿度等几个方面人手。
一、油墨涉及油墨方面的印刷故障很多,这里重点讨论与油墨墨性、光泽、抗水性能相关的印刷故障:1.印品背面蹭脏在铜版纸上印刷大面积实地印时极易发生油墨沾脏的现象,对印刷品质量的影响很大。
产生的原因:油墨档次偏低或调配油墨时的疏忽,造成油墨过稀,油墨干燥不好,或因印刷时油墨色相淡薄人为加大墨量,印刷后的产品背面出现蹭脏现象。
解决方法:(1)最根本的措施是采用快固亮光、快固着油墨印刷并采用喷粉,调整控制喷粉量,如可在油墨中加入5%的玉米粉搅匀后印刷,就可克服粘脏。
(2)在不影响印刷效果的f青况下可以减少墨量,(3)给油墨中加入适量的干燥剂及防粘剂,以调整和改善油墨的特性。
38印刷质量与标准化20r4.2文/周乾于蒙蒙(4)油墨调得太稀薄沾脏印品背面,应调换新墨或者调入部分新墨,以增加油墨的粘度。
2.糊版产生的原因:(1)由于油墨中颜料的耐水性差,油墨配方调整不当,去粘剂、低粘度调墨油用量过多。
(2)油墨调得太稀薄,粘度小。
(3)油墨颜料颗粒太粗,使得连结料对它的传递性能降低,使其沉积在版面上从而了阻塞网点。
(4)油墨油重,使版面的空白部分感脂产生糊版。
(5)油墨中加入的辅料太多,降低了油墨的粘度、墨质变松,使得油墨的油性变大从而造成糊版。
(6)油墨的软化点低或PH值偏低。
解决方法:(1)选用抗水性好的油墨。
(2)适当加进一些黏度大的调墨油。
(3)调整各种印刷助剂的用量,可在水斗中适当加些阿拉伯树胶,也可用915维利油和05—93亮光浆进行冲淡。
(4)多数因油墨调得太稀而造成油墨过于稀薄而产生的糊版,可以适当加些浓调墨油,有助于克服蹭脏现象。
(5)调还软化点较高的油墨或者选择PH值接近中性的油墨。
胶版印刷过程的常见印刷故障及解决方法

一般情况下,是油墨的抗水性不良,易乳化时常出现此现象。可以加适量高粘度树脂调墨油、亮光浆或印刷型罩光油,提高油墨的粘性、传递性和抗水性,同时增大印刷药水的PH值,减少给水量,减少给墨量,可改善或克服此故障。
3、蹭脏
蹲脏,亦称“沾脏”、“沾后背”,印刷速度太快,印在纸张上的油墨固着时间不够或纸堆压力过大时,墨层尚未干燥,发生油墨再转移现象称为蹭脏。
油墨和印刷工作者都十分清楚,不会有万能的油墨,可以适应各种印机、纸张、印刷环境以及不同的印刷需求,因此印刷时应根据不同情况,对油墨进行调配是必不可少的,也是非常重要的,调配得当,可以减少不少的印刷故障,以上仅供各位同行参考,望指正!
7、不下墨
不下墨也称墨脱辊,是指印刷品出现条痕,色相也比较淡的现象。
此现象主要是油墨的墨性不好、屈服值太高,油墨中的颜料含量过高、油墨丝头过短而成乳酪状、油墨已胶化或水进入了油墨导致部分絮凝所引起,使印机墨槽内的油墨和墨辊脱离,不能很好传递,遇到此问题首先要从油墨设计上改善墨性和油墨的流动性。其次,印刷时,适当调配粘度大的调墨油,改善油墨的流动性,能有助于克服触变性较大而粘度、流动度尚可的油墨,经常以墨刀搅动墨槽中的油墨或直接在墨槽中装一个搅拌器,也可以克服此弊。
10、网点扩大
网点扩大,主要表现在版上的网点,不能忠实的再现,结果造成网点变形或相连,反差不足,影响印品质量。
此现象多由油墨调配不当、油墨过稀过软,浓度不足造成,油墨调配时应加适量去粘剂,不用较稀的调墨油去粘,或采用浓度较高的油墨,减少给墨量,此现象可以克服、其次印机墨辊的硬度不适合,辊压过大,橡皮布松弛,辊筒排列不良也是造成此问题的重要原因,亦因检查调整。
糊版现象的出现,一般是由于油墨中颜料的耐水性差,油墨配方调整不当,去粘剂、低粘度调墨油用量过多,油墨调配得过软、过稀而造成糊版。要解决此问题,一是选用抗水性好的油墨,二是调整各种印刷助剂的用量,保证油墨的抗水性、水墨平衡性。
胶版印刷过程的常见印刷故障及解决方法

胶版印刷过程的常见印刷故障及解决方法
一、胶版印刷过程常见故障
1、印刷图案不清晰
①硬度不足:印板表面硬度不足,印版与胶版之间摩擦力减小,印版
与胶版容易“停滞”的现象发生,造成胶版上的油墨受外力影响而不能清
晰地转移到印刷品上,图案模糊不清。
解决方法:①增加胶版的硬度;②检查印刷机的运转方向,及时调整;
③检查印版的安装,是否松动,需及时拧紧松动的部分;④保持印刷设备
清洁,及时清洁印刷机上的积油,毛毡等脏物。
2、油墨分布不均匀
①墨刷不均匀:墨刷不均匀,会出现油墨分布不均匀的现象,影响图
案质量。
解决方法:①检查墨刷的头部,更换磨损的墨刷;②检查墨刷的头部
是否完整,若不完整,请及时补充;③调整墨刷的压力,尽量达到墨刷与
胶版间贴合度最大的状态;④检查墨刷是否松动,若是,请及时拧紧墨刷
的螺钉。
3、胶板残留
①不均匀的清洗:胶版表面不均匀清洁,残留的胶水在印刷时会粘附
在胶版上,用于清洁的液体也可能留在胶版上,使其失去弹性,影响图案
质量。
胶印制版中的常见异常现象及处理方法

胶印制版中的常见异常现象及处理方法作为一名胶印制版人员,会不时遇到各种异常情况,根据不同情况,要采取不同的处理方法。
一、原版密度不够硫酸纸密度不够是很常见的,特别是大字和实地块。
一般先用增密剂(增黑剂)涂抹(注意涂抹时所蘸增密剂不可太多),待干燥后才能在同一个地方涂抹第二次,全干后才能晒版。
但有时只涂抹增密剂密度仍然不够,这时还有两种处理方法。
(1)涂墨汁或用黑纸遮盖涂墨汁适用于大字和较复杂的图案,用黑纸遮盖适用于实地条块。
也可将两种方法相结合,即先用墨汁涂边沿和较细窄的地方,再用黑纸遮盖余下的大块实地。
注意用墨不可太多,否则硫酸纸会发皱,影响晒版质量。
(2)反复拷贝法用反复拷贝的方法可得到密度足够的胶片原版。
首先用较少的曝光时间和显影时间(一般为正常时间的50%~70%)拷贝得到阴图,将阴图中空白部分因密度不够而被显出来的银颗粒刮去,再将此阴图用较多的时间(一般为正常时间的120%~150%)拷贝第二次,这时一般可得到密度足够的胶片。
如果仍不够,可再翻拷一次即可。
二、胶片有灰雾胶片上灰雾大可用增加曝光时间或显影时间、增加显影液浓度等方法来处理,但必须保证图文质量。
如果无法保证图文质量或灰雾太重,也只好重出胶片。
三、文字笔画粗细不均匀这种情况常见于硫酸纸,是因为激光打印机故障或硫酸纸本身质量不好造成的。
也可用涂抹增密剂的办法来改善最粗笔画和最细笔画之间的差距,但不能完全消除粗细不均匀现象。
这时,应维修打印机或更换硫酸纸后重发硫酸纸。
四、版心发生几何变形或大小不等几何变形常是因为打印机调整不当而造成的,但也有偶然发生的。
变形常发生在硫酸纸上,多是平行四边形变形,即版心的行、列不是垂直关系。
当变形或大小不等现象严重时只能重新出硫酸纸,不严重时在征得客户同意的情况下可不重发硫酸纸,这样,需在拼版时左右以版心靠切口一侧为基准、上下以页码为基准进行拼版。
因为以版心靠切口一侧为基准,行套印不准现象就不是很严重,但如果以行为基准,列套印不准现象就会很严重,而且当以版心切口一侧为基准时,书脊侧没对齐不易被发现。
胶印常见故障分析

胶印常见故障分析近年来,印刷行业的市场竞争日益加剧,利润率逐渐降低,为了在激烈的竞争中得以生存,采取薄利多销、提高印刷速度、降低能耗等手段已成为印刷企业的首选,其中,印刷设备的运行状态、故障的准确判断和及时处理便成为重中之重。
下面,笔者以三菱胶印机为例,对单张纸胶印机的给纸部(飞达部分)、套准部(前规部分)、印刷部、收纸部这4个主要单元的常见故障进行分析,希望对业内人士有所帮助。
第一单元:输纸部输纸部主要由飞达头总成、传纸离合器、挡纸板机构、输纸轮、双张检测机构、输纸过桥及其他传动机构组成。
在输纸部的作用下,纸张通过飞达机构的分纸吸嘴、送纸吸嘴被送入输纸过桥,之后再进入套准部,便完成了输纸过程。
在输纸过程中,较为常见故障有双张、纸张歪斜、断张、给张不到位(超前或滞后)等。
1.双张引起双张故障的原因较多,其中最为普遍的是纸张自身的质量问题,如新纸静电较大、纸张较为潮湿等,这些问题容易导致输纸过程中纸张不易分离,从而造成双张故障。
另外,机械故障也是引起双张的主要因素之一,由于飞达头总成空间较为狭窄,各连接构件尺寸细小,在粉尘(纸粉、纸毛)等恶劣的生产环境下长期高速运行,一些机构容易发生磨损,主要表现在以下几个方面。
(1)压纸脚及连接机构发生磨损长期高速运转之后,压纸脚与纸张接触的平面容易发生局部凹陷,该凹陷面与原平面之间会形成过渡圆弧角,当压纸脚向下踩纸时便会形成一个与走纸方向相同的分力,使纸张不能被压缩空气有效分离,从而造成双张故障。
此外,压纸脚连接机构(销轴)发生磨损也会使压纸脚发生晃动,出现踩纸不稳、搓纸等问题,从而出现双张纸进入输纸轮的现象。
(2)挡纸板零部件发生磨损纸张在送纸吸嘴的作用下被送入输纸轮的瞬间,挡纸板打开以保证纸张顺利通过,随后立即恢复垂直状态,从而有效阻止后一张纸的进入。
当挡纸板的轴、套及连杆轴套等零部件发生严重磨损时,便无法保证挡纸板保持垂直状态,在12000张/小时以上的高速印刷速度下,松纸吹气系统基本为连续吹气,这样就很容易造成双张或多张纸通过挡纸板的现象。
常见的几种胶印故障
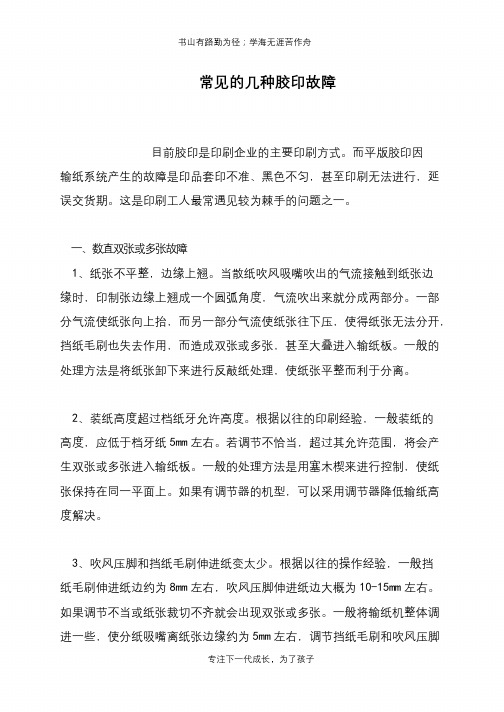
书山有路勤为径;学海无涯苦作舟
常见的几种胶印故障
目前胶印是印刷企业的主要印刷方式。
而平版胶印因
输纸系统产生的故障是印品套印不准、黑色不匀,甚至印刷无法进行,延
误交货期。
这是印刷工人最常遇见较为棘手的问题之一。
一、数直双张或多张故障
1、纸张不平整,边缘上翘。
当散纸吹风吸嘴吹出的气流接触到纸张边
缘时,印制张边缘上翘成一个圆弧角度,气流吹出来就分成两部分。
一部
分气流使纸张向上抬,而另一部分气流使纸张往下压,使得纸张无法分开,挡纸毛刷也失去作用,而造成双张或多张,甚至大叠进入输纸板。
一般的
处理方法是将纸张卸下来进行反敲纸处理,使纸张平整而利于分离。
2、装纸高度超过档纸牙允许高度。
根据以往的印刷经验,一般装纸的
高度,应低于档牙纸5mm左右。
若调节不恰当,超过其允许范围,将会产生双张或多张进入输纸板。
一般的处理方法是用塞木楔来进行控制,使纸
张保持在同一平面上。
如果有调节器的机型,可以采用调节器降低输纸高
度解决。
3、吹风压脚和挡纸毛刷伸进纸变太少。
根据以往的操作经验,一般挡
纸毛刷伸进纸边约为8mm左右,吹风压脚伸进纸边大概为10-15mm左右。
如果调节不当或纸张裁切不齐就会出现双张或多张。
一般将输纸机整体调
进一些,使分纸吸嘴离纸张边缘约为5mm左右,调节挡纸毛刷和吹风压脚
专注下一代成长,为了孩子。
- 1、下载文档前请自行甄别文档内容的完整性,平台不提供额外的编辑、内容补充、找答案等附加服务。
- 2、"仅部分预览"的文档,不可在线预览部分如存在完整性等问题,可反馈申请退款(可完整预览的文档不适用该条件!)。
- 3、如文档侵犯您的权益,请联系客服反馈,我们会尽快为您处理(人工客服工作时间:9:00-18:30)。
胶印常见故障(一)印刷过程中纸张常见故障一、纸张的伸缩通常在印刷厂里,纸张的丝缕是以纸张纤维与滚筒轴线的方向为基准而确定的。
纤维排列方向与滚筒轴线平行的纸张,称为纵丝缕纸张;而纤维排列方向与滚筒轴线相垂直的纸张,称为横丝缕纸张。
在胶印中应采用丝缕纸张进行印刷。
这是因为:从输纸方面来看,纵丝缕纸张在来去(轴向)方向比较挺硬,沿径向不易撕口,便于吹松和输送;从套印方面来看,一根干燥后的纤维完全润湿后,其直径可能增加30%,而长度方向增加1%~2%。
所以,横丝缕纸张比纵丝缕纸张在来去(轴向)方向伸长较多,直接影响套印精度。
虽然纵丝缕纸张上下(径向)伸长较多,但通过调整包衬或其他方法可保证套印准确。
二、纸张的甩角甩角又称纸尾散形,是指经印刷后的纸张拖梢部分一边出现套印不准的现象。
近年来,大多数甩角故障多发生在多色胶印。
其主要原因是:(1)前规不在一平行直线上,致使纸张到达前规后,一边叼纸少。
(2)纸张厚度差异较大;纸张叼口成波浪状。
(3)各色组压力呈递增趋势。
(4)橡皮布滚筒包衬不平。
(5)压印滚筒叼牙两边松紧有差异。
(6)压印滚筒叼牙两边个别牙垫光滑或太低。
(7)由于印版后部两侧空白区域较大,在此区域内润湿液用量较大,致使纸张沾附较多润湿液,引起拖梢部分伸缩,形成甩角。
(8)印版两侧空白区域用液量大小不同,也会使一边形成甩角。
在单色胶印机中也有类似故障发生。
三、纸张的掉毛、掉粉纸张的掉毛主要是两方面的原因造成的。
首先是纸张的质量,其次是印刷条件。
纸张的质量是指纸张的表面强度。
纸张的表面强度是度量纸张表面的纤维、填料、胶料间结合力大小的物理量,一般是指单位纸面上垂直于纸面的抗水层、抗撕裂的能力。
表面强度大的纸张在印刷中掉毛少。
所以,在实际应用中,纸张的表面强度也叫做纸张的掉毛抗阻,它反映了纸张在印刷过程中抗掉毛的能力。
印刷条件包括的内容较多,有润湿液的供给量、油墨的黏性、黏度、印刷速度等等。
(1)纸张掉毛与堆墨纸张的掉毛一般分为干掉毛和湿掉毛。
在单色胶印中,纸张的掉毛为干掉毛,是在纤维或颜料之间的结合力小于油墨的黏着力时发生的,而湿掉毛是在这一条件下再加上水的参与发生的。
多色机印刷过程中,除了第一色油墨外,其余几个色组的油墨都要印在已经印过的油墨或白纸表面,而这个表面是经过润湿液润湿的。
纸张在润湿后,其表面强度必然下降,显然,最后一色若在白纸部分进行印刷,白纸表面强度最弱。
从纸张上脱落的纤维与涂料粒子堆积在橡皮布上,便发生橡皮布堆墨的故障。
多色胶印机根据印刷图文的不同,堆墨的程度也有所不同。
一般来讲,第一色组橡皮布滚筒上不容易发生堆墨,往往是在第二色或以后各色组上发生,这是因为此时纸张产生堆墨是由于油墨残余黏性所引起的涂料粒子脱落和润湿液的润湿引起的湿掉毛。
因此,越是靠后面的滚筒,越容易发生堆墨。
堆墨开始形成时,首先使图像变得粗糙。
这是由于脱落的纤维、涂料粒子随同油墨一起剥落,并在橡皮布上堆墨,使凸起部分的油墨转移不良,致使印版发生花、糊、掉版。
(2)纸张掉毛及堆墨的处理方法减少纸张掉毛的最根本的方法是选择高表面强度的纸张。
然而,实际中未必都使用这类纸张,那么从工艺角度考虑,首先润湿液应控制在最少量的范围,其次降低印刷速度,以便降低油墨在印刷过程中的黏性,缓冲纸张的掉毛。
对于掉毛较严重的纸张,为了保证印品质量,在正式印刷前,应先压一遍清水,或印刷精细产品前先套印一次白油或多次清洗橡皮布。
四、纸张静电纸张带静电会影响输纸和印刷过程,纸张静电形成一是上机前纸张就有静电,二是纸张印刷之前静电并不明显,压印后静电骤然加重,致使收纸不齐。
胶印过程因有水参与,一般经过印刷后静电增加者并不多见。
消除静电常用的方法有:利用加湿器增加吊晾纸张的室内和车间的相对湿度,以提高纸张的含水量;担前将纸张放到机器旁,以适应印刷车间的温、湿度。
若输纸机输纸尚可,但印出的产品却在收纸部位不齐,此时略微加大版面水分是有一定效果的。
另外,还可采用静电消除器或抗静电剂来消除纸张带静电的现象。
五、纸张弓皱在印刷过程中,纸张弓皱(起褶子)是最常见的故障之一,经济损失比较大,产生这类故障的原因主要有两个方面:一是纸张本身所造成的(大多出现在非涂料纸张上),二是机器调节使用不当。
下面按其形状来进一步分析其原因及处理方法。
1.小散发形褶子产生这类褶子的原因:(1)纸张吸潮后产生的“荷叶边”(纸张本身含水量不匀或车间相对湿度较高,纸张含水量较低)。
(2)两面印刷的印件背面墨迹“堆滚筒”(压印滚筒表面堆积油墨太厚,致使局部压力发生变化)。
处理方法:重新吊晾纸张。
如果是两面印刷的印件,一定要注意经常清洗压印滚筒。
2.不出头的细直形褶子(褶子在纸张中间)产生这类褶子的主要原因是纸张四周变形(紧边)。
处理方法:重新吊晾纸张,如果有的印刷厂没有吊晾纸张的设备,可以将要印刷的未裁切的纸张提前一周抖风,放在印刷车间以适应作业环境的温、湿度,印刷时再裁切上机。
3.大歪形褶子产生这类褶子的原因:(1)水大纸边角翘起来了,叼纸牙不好。
(2)叼纸牙在纸张的一边叼力太轻。
(3)纸角飘起来。
(4)侧规定位不当,纸角碰递纸叼牙缺口。
处理方法:纸张反敲处理后上机印刷;对于较松的叼纸牙需重新调节,纸角飘起来主要是叼牙叼不住纸张。
4.大散发开褶子产生这类褶子的原因:(1)压印滚筒叼纸牙在一处有两只或两只以上太松,甚至叼不住纸张。
(2)递纸牙牙垫高低不平,致使叼口纸边不成一直线面成为波浪形曲线,压印滚筒叼纸牙叼住纸张压印时,缩短了纸张的长度,从叼口开始产生大散发开褶子。
处理方法:检查压印滚筒叼纸牙的叼力。
(二)印刷过程中油墨常见故障在印刷过程中,由某种单一的材料引起的单一故障是很少见的,大多故障都是由多种因素引起,只不过某种因素是产生故障的主要原因。
由油墨引起的故障在胶印中所占的比例相对较大,主要表现在以下几个方面:一、粘脏及背面蹭脏由于油墨干燥太慢、油墨太软、太稀,而且给墨量太大,造成印好的一张印刷品上的油墨粘脏了上面一张纸的背面。
这种现象大多发生在印刷品上油墨较大的实地(或暗调)部分。
粘页、粘贴、成块(俗称贴成一块)是粘背的最严重现象,这是指印好的一堆印刷品粘连在一起的情况。
粘脏及背面蹭脏是胶印中最常见的故障之一,这种故障主要由以下因素引起:(1)印刷表面粗糙的纸张,需用墨量大。
(2)印刷双面光滑的纸张。
(3)印刷实地或密度较大的网点处,墨量较大。
(4)在吸收性差的纸张上以氧化干燥型油墨印刷时。
(5)油墨干燥剂的用量过多,易在纸堆中氧化生热,导致油墨发黏而使纸张粘在一起。
(6)油墨乳化导致粘脏。
目前,解决印刷品背面粘脏一般采用下面的措施:(1)使用快干油墨,对于卷筒纸胶印机来说采用红外干燥器。
(2)使用预防背面粘脏的喷粉。
(3)采用隔晾架,减少堆纸层高度。
(4)对粗糙的纸张采用加大印压减少墨量的方法印刷。
(5)控制润湿液的pH值及用量,防止油墨乳化。
(6)调节时间温、湿度,并对印刷色序重新安排。
(7)图文的实地面积过大时,印后加强通风。
(8)调整干燥剂用量。
(9)采用防粘脏剂或加粘衬纸的方法。
二、油墨晶化所谓“油墨晶化”,是指两色油墨的印刷间隔控制不当,先印的油墨已经干固才叠印后一色油墨。
由于干固的墨层黏性和被油墨润湿的性能都很低,因而下一色油墨很难附着在上面。
这种现象一般发生在单色胶印机的油墨叠印中,为了不发生油墨晶化故障,先印的油墨层必有具备以下条件:(1)保持一定的润湿性,能被后印的油墨润湿而附着。
(2)保持一定的黏性,其与后印的油墨所产生的黏附力要大于后印油墨的内聚力。
(3)控制干燥剂(燥油)的使用量。
如果出现了“油墨晶化”故障,可用细纱布摩擦印品油墨表面,使墨膜表面粗糙,增加毛细吸附力来提高油墨叠印效果。
对于印刷幅面较大、批量大的“油墨晶化”印品,最好先在油墨表面叠印黏度高的调墨油,利用它的强烈附作用附着在干固的墨层上,然后以它为媒介,使后印油墨很好地附着。
三、油墨因素引起的花版(1)油墨黏度过大,使版面产生花版。
油墨黏度过大除了使印迹转印困难外,还会破坏墨层中间断裂的条件,使版面剩余墨层不足,因图文部分裸露受磨损而造成花版。
处理方法:适量加一些撤黏剂,降低油墨黏性,但不要让油墨流动性增加太多。
(2)油墨黏度过小,使印版糊版。
黏度小的油墨易乳化造成浮脏,油墨不能正常地转移,使墨辊、印版和橡皮布上逐渐堆积颜料颗粒。
当颜料颗粒在印版上堆积到一定厚度时,就会引起糊版,有时因版面剩余墨层不足造成花版。
处理方法:适当加进一些0号调墨油。
(3)油墨流动性过大会使墨层易铺展,使印迹几何尺寸扩大,网点不能正确复制;油墨流动性不足往往传递不匀,易造成印版着墨不足而花版。
处理方法:根据油墨流动性可选用不同的调墨油。
四、堆墨由油墨引起的堆墨故障就是指油墨堆积在墨辊、印版或橡皮布上,油墨转移性差。
产生堆墨除纸张原因外,便是油墨、印压和版压了。
油墨在橡皮布上堆积,颜料呈分离状态的粉末,网点糊死,印品看起来颜色不一致,这是由于:(1)油墨分散不良,油墨中采用了相对密度太大的粗颗无机颜料。
(2)油墨膜太。
(3)油墨冲淡过度,连结料太稀。
(4)印刷压力不实,辊子传墨性能不良。
处理方法:(1)检查印刷压力、墨辊性能以及衬垫。
(2)给墨量要适宜,如果油墨太软,可采用稠一些的油墨。
(3)换用新墨。
五、印品光泽差、不鲜艳印品光泽差、不鲜艳,除纸张因素外,主要由于油墨稀释过度,树脂析出而失去连结作用,油墨的干性慢或者纸张的吸收性太强,造成油墨吸入张而使印刷品暗淡无光。
处理方法:(1)加入新墨或在油墨中加入亮光连结料。
(2)换用高光泽的油墨或用吸收性差的纸张。
(3)适当加些干燥剂。
(4)对已印成的印刷品可用罩光油处理。
六、褪色在印刷过程中油墨的颜色褪掉,或印刷品在堆放中(在干燥过程中)油墨的颜色褪掉,其原因是:(1)纸堆中由于油墨的氧化作用而产生热,这个热量会使油墨颜色褪掉。
(2)油墨中使用的干燥剂含钴太多。
(3)颜料不耐热或油墨中颜料含量太少。
(4)配浅色时,白色油墨选用不合适。
处理方法:(1)减少干燥剂的用量,采用快干(或快固)型的油墨。
(2)油墨中采用耐热、耐光的稳定型颜料。
(3)换用白色油墨。
七、输墨不畅输墨不畅的主要原因是油墨的流变特性太差,如果油墨的触变性、屈服值太大,黏性太小,丝头太短等这些流变特性的因素综合在一起,必然使油墨的流动性差,从而导致供墨系统输墨不畅或根本不下墨。
另外,纸张脱粉、掉毛也易使输墨不畅。
为了使胶印生产正常进行,得到质量上乘的印刷品,一方面要选择流变特性适合于印刷的油墨,另一方面要结合生产现场的工艺条件来使用印刷材料。
同时,还可以在油墨中加入适量的辅助剂,对油墨的流变特性进行调节。
八、油墨粉化(剥落)印刷品上的油墨干燥后可以像干粉一样被擦去,其原因是:(1)油墨中的连结料大量渗入纸张,使油墨失去黏性作用,另外,颜料的颗粒太粗。