制程审核表-五金
制造过程审核检查表

4
1、文件与工装、刀具、模具、检具其中任意 一项未符合最终版本各扣1分。
3
1、包装方案未按照和客户达成一致的包装方 案扣3分。
1、包装上未有客户标识扣1分。
4
2、包装上未有产品名称标识扣1分。 3、包装上未有产品零件号扣1分。
4、包装上未有产品数量标识扣1分。
3
1、无安全库存资料扣2分。 2、安全库存资料不完善扣1分。
1、物料未按要求区域划分待检区、合格区、
不合格区或划分不合理扣1分。
5
2、划分标识不明确扣1分。 3、每批次产品无编码标识扣1分。
4、每批次产品无厂家标识扣1分。
5、每批产品无炉批号扣1分。
第 1 页,共 4 页
文件编号: OK
检具精度能否满足要求,检具 3 得到了有效的验证,检测,
并有有效期标签
4
库存管理程序,来料的安全库 存
三: 生产工位 按照控制计划审核生产过
1 程,设备参数与文件一致
2 产出产品的追溯方案
3 RPN的改进
偶发事件的应急方案,人 4 员,设备,备用工装,检
具,刀具,模具 关键特性是否都在控制方式 5 之内
明确的产品状态及分析报
6
告,红盒子,黄盒子,绿盒 子及调机品,首末件,存储
2
1分。 2、控制计划版本与版本记录不相符不正确扣
1分
1、无工装夹具扣2分。
8
2、工装夹具与清单不相符扣2分。 3、过程责任者不明确扣2分。
4、过程责任者未经培训考核就上岗扣2分
1、未采用SPC统计过程控制扣2分。
5
2、未采用防错过程控制扣2分.
3、未采用全检的控制方式扣1分
5
1、来料未按要求进行检验扣3分。 2、未有检验报告扣2分。
【最全】五金行业QPA供应商评审表
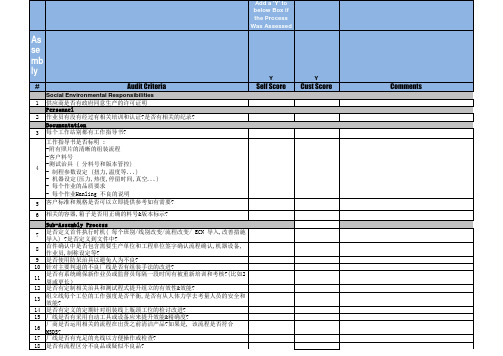
20 每班开工和收工时,是否确认验证关键制程参数是和文件一致的
21
是否用限度样品(剥离后的产品)来定义表面最小点胶量(包括点胶速度和 胶的高度)
22
点胶后,是否剥离首末件,与限度样品的点胶量做比对,来验证关键部位的 点胶量是足够的
23 首末件是否做拉拔力测试,来验证点胶制程符合产品规格要求
24
如果需要把点胶重点管控参数(包括治具变化)调整到管控范围外,是否按 PCR流程执行
10 针对主要判退的不良厂线是否有组装手法的改进?
11
是否有系统确保新作业员或监督员每隔一段时间有被重新培训和考核?(比如2 周或更长)
12 是否有定制相关治具和测试程式提升组立的有效性&效能?
13
组立线每个工位的工作强度是否平衡,是否有从人体力学去考量人员的安全和 效能?
14 是否有定义的定期针对组装线上瓶颈工位的检讨改进?
29 首末件是否做拉拔力测试,来验证点胶制程符合产品规格要求
30
在量产前是否用足够多的样品 (至少10个)做拉拔力测试,来认可热熔制程 参数和治具
31
如果需要把热熔重点管控参数(包括治具变化)调整到管控范围外,是否按 PCR流程执行
ESD Compliance (if applicable)
32 如果组立过程中接触到ESD的敏感零件作业人员是否有正确佩戴静电环?
45
厂商是否有100% ,加严,正常,减量的抽样标准.从一个标准转化至另一个标准 是否有明确定义
46 GR &R 是否用于机器人员 , 量具治具的承认
47 统计应用是否用于管控PMP 中定义的特性/制程参数
48 仪器是否有执行校验 , 频率是否定义到相关文件中 OBE Station
五金制品制程巡检报告表

客户订单编号品名规格原材料规格机器编号操作员模穴日期8:00-10:0010:00-12:0012:00-14:0014:00-16:0016:00-18:0018:00-20:0020:00-22:0022:00-0:0000:00-02:0002:00-04:0004:00-06:0006:00-08:00备注1
外观2结构形状
检 具:说明:1、以1H为基本单位,其中8:00-19:00为白班,20:00-07:00为夜班.2、按照相应的零件检查标准书规定的项目,进行检查作业,外观OK时在相应的栏内画“√”,NG时画"×".3、尺寸检验NG时需记录全部不良真实数据,OK时只需记录最大值及最小值。
4、检查员必须在白/夜班处签名。
NO
检验项目检验标准参样五金制品制程巡检报告
巡回检验时间段/次数判 定
白班检验员: 夜班检验员: 审核/日期:
(1)目视 (2)卡尺 (3)千分尺 (4)高度计 (5)塞规 (6)显微镜 (7)二次元 (8)推拉力计 (9)其他。
制程审核清单A0版

生效日期: ____________制定 :____________ 複核: ____________ 審批: ____________序號審核項目1通用審核重點2ESD检查1. 檢查操作員在作業時是否戴靜電帶或靜電帶未接地.2. 用靜電測試儀檢查靜電帶壞.3. 用萬用表檢查地線及靜電席是否接地不良或未接地.4. 檢查操作員所用的測試靜電帶是否做記錄或做假記錄.5. 檢查操作員在存入半成品或PCBA時是否使用非防靜電膠袋/泡泡袋/膠盆防靜電措施做得不好, 靜電容易損壞元件或影響產品可靠性.3A面枚状切割4A面枚状檢查(IQC全檢)1.核对作业票記錄信息是否 清晰完整,下拉到本工位良品数需与作业票上一工序所记录良品数是否一致。
2.双手对角拿取并放置产品。
放置时要留意,避免资材与夹具碰撞摩擦,避免造成划伤折痕。
3.检查产品时,双手拿稳治具,避免资材掉落。
4.产品与灯管的间距为3~5cm,眼睛与产品的间距为20~30cm,产品不可接触到灯管边缘,防止划伤不良。
5.资材如有粘着性异物等付着现像,是否清洁干净。
6.需水平放置检查产品表面不平。
7.是否優先參考使用限度樣品對產品進行判定。
8. 银线异物/绝缘边异物:是否安裝WI要求,未连接两根银线,电性OK 的话为良品,進行判定。
9.相關記錄表單是否記錄完整清晰,有無有關責任人員的簽名、確認、審核.10.檢驗作業環境是否符合相關要求。
1.所有檢驗項目均需要按照檢驗WI要求進行操作判定,防止產品漏判,誤判,不良流出。
2..相關記錄表單的完整記錄和保存便於即時監控檢驗情況。
5A面枚状阻抗檢查(IQC全檢)1.作业前檢查員是否先戴好软胶手套,将离子风机风速调到刻度位置,并打开台灯或荧光灯。
2.檢驗使用萬用表是否在有效期內使用。
3.檢驗員工是否有崗位資格證,相關檢驗作業內容是否清楚熟悉?4.測試電路圖及測試數據要求是否正確確認。
確保作業過程中對資材的保護,按檢驗WI正確操作,防止產品漏測,誤測,不良流出。
五金行业制程检验记录表样板

完成日期: 其它 □
产品名称 订单号
检验项目 抽样水准
尺寸
5PCS
尺寸
5PCS
尺寸
5PCS
尺寸
5PCS
尺寸
5PCS
尺寸
5PCS
尺寸
5PCS
尺寸
5PCS
尺寸
5PCS
外观
5PCS
检验项目 抽样水准
尺寸
5PCS
尺寸
5PCS
尺寸
5PCS
尺寸
5PCS
尺寸
5PCS
尺寸
5PCS
尺寸
5PCS尺寸5Fra bibliotekCS平面度
5PCS
外观
5PCS
判定:
合格 □ 不合格□ 数量:
规格 机台
时刻表
时刻表
不良原 因:
巡检 员:
制程检验记录表
产品料号 模具编号
结果
数量 生产日期 检验数据及结果 时刻表
结果
表单编号:
首检 □
巡检 □
检验日期
时刻表
结果
结果
检验数据及结果 时刻表
结果
时刻表
结果
处理结果: 改善措施:
报废□
调机 □ 主管:
返工□ 修模 □
工艺变更 □
五金制品制程检验标准

感 官 游标卡尺
5.下架时:颜色按订单,对照色板.同一产品的零组件颜色一致,颜色对卡允许≤半个 色差. 工件无密集型针孔,气泡,砂粒,不得有少粉、少油、粉堆、流挂。露底,桔皮 等现象, 6.防护:按规定要求数量用报纸或胶管分类包扎存放,严禁磕碰划伤和酸、
性能
7.性能:a:附着力,划格法,掉漆≤5%合格.B:耐水性:24小时,常温无气泡,裂 纹,起皱,生锈氧化及明显失光,涂层软化.C:耐蚀性:24小时NSS盐雾试验6级以上: 无腐蚀生成物,掉漆,气泡及涂层软化;
检验工具
14
装配
特性 5.拧螺丝:首检螺丝的螺纹质量合格,螺丝硬度、外观(镀锌、镀镍)质量合格;工件
拧入螺丝后,垂直、端正、不斜、螺丝头不刺手. 6.打胶塞:胶脚各塑料配件颜色一致,材质合格,打入后无烂边、飞边、毛边、不破裂 等情形,并与管口紧贴、无离缝. 7.包五金配件:配件袋必须按照产品明细表的规格,型号和数量,计数准确,不得多数 、少数或漏件,袋口必须封好,装配性配件必须首检试装合格后才能使用. 8.产品组装后,装配顺畅,四脚平稳.
1
开料
外观
刃口;管类的截面平直管口无螺旋印,管缝圆滑,无裂口.特别注意电镀氧化管材表面外 观质量合格. 2.拉杆内管,衣架系列伸缩管为了避免批锋磨损,须加倒角工序;注意板料表面保护膜 磕碰划伤及氧化铝管等材料表面的保护;开料时特别注意辨识镜光、砂光材料的区 分,根据产品要求排版砂光纹路方向. 尺寸按图纸,直线偏差≤0.2MM,沉孔和平孔的方向正确,具有对称组装性能的孔位正确定 位,通孔批锋高度≤0.2MM,装配螺丝能顺利穿过单边孔并无阻塞孔径现象. 工件无裂口、碰凹、刮花等现象,U型工件冲孔方向根据要求(垂直或平行). R位尺寸、定位尺寸、限位、上下宽度、高度等尺寸和工艺按图纸要求检验 铁管弯制长度适中,管材(板材)表面无起皱、拉伤、夹伤,刮伤等痕迹,管缝方向正 确,铁管、板材表面无明显压伤、失圆、刮印等现象. 工艺设备,缩口长度,直径按图纸要求,缩管长度公差为±1~0MM,缩口直径公差为 ±0.1MM. 入螺母胶塞位的缩口大小适中,缩口部位无裂痕、严重拉伤、管材弯曲变形等观象. 压型尺寸按图纸要求,定位,限位准确,工件压型一般按照模具的使用要求,U型状的 两侧高度相等对称,允许高低相差≤0.5MM. 工件表面无压痕,擦花和明显的拉伸条纹等现象. 卷边尺寸按照图纸要求确保卷边成型规格的半径、直径和形状.成形后产品符合图纸公 差要求. 不得有变形,凹凸起皱等情形. 成型尺寸按图纸要求. 产品外观无模具压痕,擦伤,明显折痕,定位准确.操作合理, 产品高度,接合缝紧 密,缝隙公差为0.01MM. 按图纸要求该工序加工的方向,螺纹的公制或英制,有效螺纹牙长度按要求,注意螺 纹质量同螺栓螺纹相符,表面无螺旋状印痕.
制造过程审核清单

问题工序详细说明
2
审核员:
日期:
制造过程审核检查表
部门:
陪同人员:
评分标准:10---完全符合要求;8---绝大部分符合要求,有少量偏差;6---部分符合要求,有较大偏差; 4----少部分符合要求,偏差严重;0---完全不符合要求; 对每一大项全部满分(10),或每一小项6分以下,要陈述情况,并说明证据;
审核项目
生产线
1 人员/素质
1.1 提问生产员工,对本岗位的生产质量要求是否清楚
1.2 提问生产员工,本岗位设备保养、点检有那些要求,如何做。
1.3
员工是否了解本岗位的质量风险及其对顾客(包括内部顾客)的影 响?
1.4
员工是否了解作业标准,对照作业指导书,员工是否了解特殊特性、 关键特性符号及意义?
审核项目
生产线
6.3 作业员\检查员是否按规定频率和样本数量使用指定工具检查?
6.4 测量记录完整,准确、有效?
6.5 关键控制点,是否按要求进行了测量,并制定了控制图表
7 车间综合管理
7.1 车间制定了月度、周生产计划;
情况描述
打 分
7.2 对每周、月生产情况、质量情况进行统计和分析
7.3 每天工作计划安排清晰,各生产岗位数量与安排一致;
8.7 对不合格进行了专门的记录,并进行了处理; 8.8 对维修、返工的产品进行了重新检验,并能提供记录; 8.9 能提供每月质量检验和趋势的分析资料 8.10 每月对质量问题分析的异常情况进行了原因分析,并采取了措施
8.11 对各纠正实施的情况进行了验证,并提供实施和验证的记录
问题工序详细说明
7
审核员:
审核员:
日期:
制造过程审核检查表
五金车间制程检验作业流程管理卡

五金车间制程检验作业流程管理卡一、制程检验作业流程管理卡的设计要点1.标题:设计卡片的标题,以清晰明确的方式表达卡片的用途和功能,例如“五金车间制程检验作业流程管理卡”。
2.作业流程图:绘制制程检验作业的流程图,包括每个环节的操作步骤和顺序,以便操作人员清楚了解整个作业流程。
3.关键环节标识:在流程图上标注出关键环节,以便操作人员在执行作业时,特别重视和把握这些环节。
4.操作规范:针对每个操作环节,详细描述操作方法和注意事项,以确保操作人员按照规定的操作流程进行作业。
5.质量要求:在操作规范的基础上,标明每个操作环节对产品质量的要求,以便操作人员在作业过程中加强质量控制。
6.考核评价:制定考核评价标准,对操作人员的作业质量进行评估和考核,以激励操作人员严格按照作业规范进行作业。
二、制程检验作业流程管理卡的使用方法1.提前准备:在作业开始之前,检查并准备好所需的检验仪器、工具和材料,确保能够顺利进行作业。
2.按照作业流程图进行作业:根据制程检验作业流程管理卡上的流程图,按照操作规范依次执行每个操作环节,确保作业的准确性和规范性。
3.加强质量控制:在每个操作环节中,严格按照质量要求进行作业,确保产品质量的稳定性和一致性。
4.记录和汇报:在每个操作环节完成后,及时记录相关数据和结果,并向上级主管汇报作业情况,以便及时调整和改进作业流程。
5.考核和评价:根据制定的考核评价标准,对操作人员的作业质量进行评估和考核,及时给予奖惩措施,以确保作业质量的提高。
6.持续改进:定期对作业流程进行评估和改进,及时调整和完善制程检验作业流程管理卡,以适应工作需求的变化和提高管理效能。
通过使用制程检验作业流程管理卡,可以规范五金车间制程检验作业流程,提高作业效率和产品质量。
同时,可以加强质量控制,及时纠正错误和问题。
制程检验作业流程管理卡还可以作为培训和考核的基础,帮助操作人员提高作业技能和质量意识。
最终,通过持续改进和优化作业流程,实现工作效能和质量的提升。
五金加工PFMEA标准表格模版

FMEA 编号Number:页码Page:准备人Prepared By:关键日期Key Date:车型年/车辆类潜在的失效模式及效应分析表POTENTIAL FAILURE MODE AND EFFECTS ANALYSIS(过程PROCESS FMEA)过程责任部门Process Responsibility: 质量部 QA Dept.项目名称 Item:工程FMEA 编号Number:页码Page:准备人Prepared By:关键日期Key Date:车型年/车辆类潜在的失效模式及效应分析表POTENTIAL FAILURE MODE AND EFFECTS ANALYSIS(过程PROCESS FMEA)过程责任部门Process Responsibility: 质量部 QA Dept.项目名称 Item:工程FMEA 编号Number:页码Page:准备人Prepared By:关键日期Key Date:车型年/车辆类潜在的失效模式及效应分析表POTENTIAL FAILURE MODE AND EFFECTS ANALYSIS(过程PROCESS FMEA)过程责任部门Process Responsibility: 质量部 QA Dept.项目名称 Item:工程FMEA 编号Number:页码Page:准备人Prepared By:关键日期Key Date:车型年/车辆类潜在的失效模式及效应分析表POTENTIAL FAILURE MODE AND EFFECTS ANALYSIS(过程PROCESS FMEA)过程责任部门Process Responsibility: 质量部 QA Dept.项目名称 Item:工程FMEA 编号Number:页码Page:准备人Prepared By:关键日期Key Date:车型年/车辆类潜在的失效模式及效应分析表POTENTIAL FAILURE MODE AND EFFECTS ANALYSIS(过程PROCESS FMEA)过程责任部门Process Responsibility: 质量部 QA Dept.项目名称 Item:工程machiningFMEA 编号Number:页码Page:准备人Prepared By:关键日期Key Date:车型年/车辆类潜在的失效模式及效应分析表POTENTIAL FAILURE MODE AND EFFECTS ANALYSIS(过程PROCESS FMEA)过程责任部门Process Responsibility: 质量部 QA Dept.项目名称 Item:工程FMEA 编号Number:页码Page:准备人Prepared By:关键日期Key Date:车型年/车辆类潜在的失效模式及效应分析表POTENTIAL FAILURE MODE AND EFFECTS ANALYSIS(过程PROCESS FMEA)过程责任部门Process Responsibility: 质量部 QA Dept.项目名称 Item:工程FMEA 编号Number:页码Page:准备人Prepared By:关键日期Key Date:车型年/车辆类潜在的失效模式及效应分析表POTENTIAL FAILURE MODE AND EFFECTS ANALYSIS(过程PROCESS FMEA)过程责任部门Process Responsibility: 质量部 QA Dept.项目名称 Item:工程FMEA 编号Number:页码Page:准备人Prepared By:关键日期Key Date:车型年/车辆类潜在的失效模式及效应分析表POTENTIAL FAILURE MODE AND EFFECTS ANALYSIS(过程PROCESS FMEA)过程责任部门Process Responsibility: 质量部 QA Dept.项目名称 Item:工程FMEA 编号Number:页码Page:准备人Prepared By:Sev Occ Det R.P.N.. 关键日期Key Date:车型年/车辆类潜在的失效模式及效应分析表POTENTIAL FAILURE MODE AND EFFECTS ANALYSIS(过程PROCESS FMEA)过程责任部门Process Responsibility: 质量部 QA Dept.项目名称 Item:Completion工程版本Rev.A0A1批准Approval by日期 Date准备人Prepared by变更内容Comment审核Checked by0.2 Aout of spec.。
五金机构件类制程管制审查表

1.3.7 模具使用是否有记录?首件確認次數?
1.3.8
作業員有無做自檢?检验内容是什么?作业指导是否清晰简明的描述了检验标 准。
1.3.9 IPQC巡檢內容?
1.4 電鍍 :
1.4.1 電鍍前有無處理要求及作業方式(超聲水洗、電解脫脂)?
1.4.2 電鍍過程是否有加溫?
1.4.3 藥水更換時間要求及記錄?
1.1.13 工治具、設備、機器等有無環保(HSF)標識並有相關檢測記錄證據?
1.1.14 製程中是否有預防非環境(HSF)管理物質混入,洩露及污染?
1.1.15
作業員有無做自檢?檢驗内容是什么?作业指导書是否清晰简明的描述了检验 标准。
1.2 毛邊處理:
1.2.1 設備是否有每班檢查?用什么方式检查及檢查內容?
1.4.4 電鍍厚度如何管控?如何確保鍍層厚度一控制?是否有做測試? 1.4.6 電鍍電壓、時間的正確性如何控制? 1.4.7 電鍍附著力測試方法及判定標準? 1.4.8 電鍍符合品質要求的判定標準及依據? 1.4.9 水洗使用水質如何保證?如何確保工件水洗后可完全烤干? 1.4.10 電鍍廢液處理方式?
1.1.3 首件記錄內容是否完善、并經通確認?
1.1.4
是否有作業指導書?作業型號是否正確?作業方式是否依作業指導書要求執 行?
1.1.5 作業員上網前是否有培訓,并取得上網證?
1.1.6 模具溫度、料管溫度與成型時間是否正確?
1.1.7 模具、設備是否定期点檢、保養、运作是否正常?
1.1.8 如何監控過程中設備是否正常?參數有無SPC控制?
1.1.9 模仁是否有做清洗?有無作業指導書。
self Score
score
Yes=1 No=0 NA=X
五金车间制程检验流程图

部门
输 入
制程检验工作流程图
部门
输 出
技术
1、提供《检验指导书》
或《加工工艺文件》;
12
巡
N
Y
Y
N
检
N
Y
Y
检验
3、五金带班师傅(组长)对报检首件进行检验,根据检验结果填写《首检记录》;
4、根据实际情况判断该批次质量问题是否能进行现场处理,对能够现场处理的质量问题进行现场处理;
5、对不能现场处理的质量问题所对应的不合格品进行标识,并通知仓库隔离摆放;
6、厂长临时组织相关人员成立技术小组,开展不合格原因分析工作;
7、对能够现场处理的质量问题进行现场处理,并形成记录;
10、检验员进行转工序检验,对转工序不合格品转到步骤4执行,对转工序合格转到步骤11执行;
11、对加工未结束的半成品继续进行下一工序首件报检;对加工完成的成品转到步骤13进行成检;
12、巡检负责本车间所有工序检验,在巡检记录表上填报与首检表核对签字确认;有权对生产过程中发现的操作工违反工艺指导书操作的现象予以制止,造成损失的要及时向车间主管或厂长汇报。
14、成品检验员对产成品进行检验,并将结果填写《产成品检验记录》;对不合格成品按照步骤4执行
15、成品检验员对检验合格的成品开具合格证明,并通知仓库办理登记入库;
16、每月对产品加工过程中出现的不合格记录进行统计与分析并上报厂长。
生产
2、操作者首件报检;
8、操作者首件加工检验合格后方可进行工序内批量生产;
9、操作者本工序加工完成后提出转工序检验:
13、 操作者提出产品完工报检;
五金厂产品订单评审表
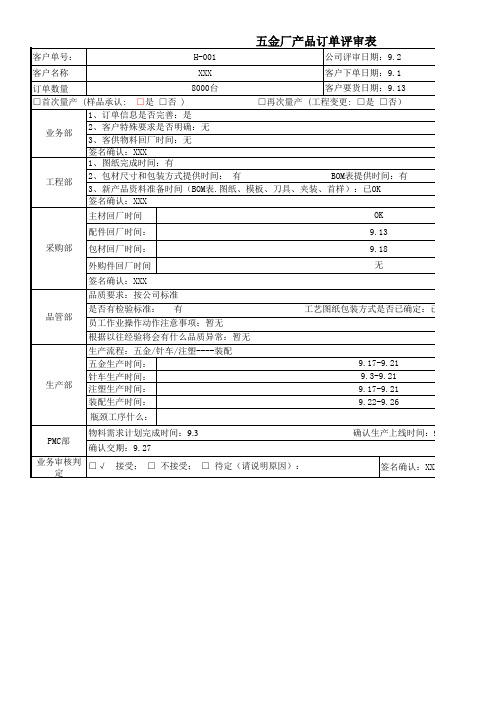
客户单号:
H-001
公司评审日期:9.2
客户名称
XXX
客户下单日期:9.1
订单数量
8000台
客户要货日期:9.13
□首次量产 (样品承认: □是 □否 )
□再次量产 (工程变更: □是 □否)
业务部
1、订单信息是否完善:是 2、客户特殊要求是否明确:无
3、客供物料回厂时间:无 签名确认:XXX 1、图纸完成时间:有
工程部
2、包材尺寸和包装方式提供时间: 有
BOM表提供时间:有
3、新产品资料准备时间(BOM表.图纸、模板、刀具、夹装、首样):已OK
签名确认:XXX
主材回厂时间
OK
配件回厂时间:
9.13
采购部 包材回厂时间:
9.18外购件回厂时间来自无品管部 生产部
签名确认:XXX 品质要求:按公司标准 是否有检验标准: 有 员工作业操作动作注意事项:暂无 根据以往经验将会有什么品质异常:暂无 生产流程:五金/针车/注塑----装配 五金生产时间: 针车生产时间: 注塑生产时间: 装配生产时间:
线时间:9.3 确认:XXX
工艺图纸包装方式是否已确定:已确定
9.17-9.21 9.3-9.21 9.17-9.21 9.22-9.26
瓶颈工序什么:
PMC部
物料需求计划完成时间:9.3 确认交期:9.27
业务审核判 定
□√
接受; □ 不接受; □ 待定(请说明原因):
确认生产上线时间:9.3 签名确认:XXX
3 ) 有
确定:已确定
铁芯类制程管制审查表 范本

1.1.12 有無首件檢查,檢查內容是否充分、明確?
Remarks self
1.1.13 製程中是否有預防非環境(HSF)管理物質混入,洩露及污染?
1.1.14
作業員有無做自檢?检验内容是什么?作业指导是否清晰简明的描述了检验标 准。
1.1.15 IPQC是否定期巡检?是否有不合格品的追溯机制?有無IPQC巡查記錄。
1.3.6 倒角后是否有清洗?作业指导書是否清晰简明的描述。
1.3.7
作業員有無做自檢?检验内容是什么?作业指导書是否清晰简明的描述了检验 标准。
1.3.8 IPQC是否定期巡检?是否有不合格品的追溯机制?有無IPQC巡查記錄。
1.4 燒結: 1.4.1 排氣作業方式為何?如何控制爐內氧含量? 1.4.2 燒結各階段升溫速度、時間是否有明確定義?作業過程如何控制? 1.4.3 在最高溫度階段是否有做溫度?時間是否有定義? 1.4.4 如何防止鐵芯粘連?爐內氣壓如何控制確認一致? 1.4.5 如何確保尺寸、電性能的一致?
1.5.6 噴涂作業要求為何?有無作业指導書?要求是否清晰、明確?
1.5.7 對涂層材料是否有明確選用要求?
1.5.8 如何管制涂層厚度的一致性?是否有對涂層厚度做測試?
1.5.9 不同鐵芯是否有不同噴涂要求?有無文件明確定義?
1.5.10
作業員有無做自檢?检验内容是什么?作业指导書是否清晰简明的描述了检验 标准。
1.4.6
根据不同客戶和产品的不同要求,是否有規范工艺,实行定窑、定温、定气氛 、定摆坯方式和定期疏通排胶管道的标准化作业模式?
1.4.7
作業員有無做自檢?检验内容是什么?作业指导書是否清晰简明的描述了检验 标准。
1.4.8 IPQC是否定期巡检?是否有不合格品的追溯机制?有無IPQC巡查記錄。
五金行业管理部评审管理年度内审计划表单样板

S2 内部沟通
S3 人力资源管理
S4 基础设施和工作环境管理
S5 采购管理
S6 产品标识与追溯
S7 顾客财产管理与产品防护
S8 监视和测量设备管理
S9 产品及过程监视和测量
S10 不合格品控制
备注:
1、▲代表在此段时间内进行审核; 2、如因各种审核结果导致需要增加内部审核时,将更新此计划; 3、每次审核函盖ISO/TS16949标准的所有要素。
2016年度内审计划
类别
以往审核发现不符合条
重要性
款
1
2
3
4
5
6
7
内审 第二方 第三方
产品审核
▲
过程审核
过程↓
Hale Waihona Puke M1 质量管理体系策划M2 管理评审
M3 内部审核
M4 数据分析
M5 改进
C1 销售与合同评审过程
C2 产品设计和开发及变更
C3 产品生产
TS质量 C4 产品交付 体系审 C5 客户反馈
核 S1 文件与记录管理
Form Rev:A0
制定:
批准:
8 9 10 11 12
▲
7-8日 ↓
▲ ▲ ▲ ▲ ▲ ▲ ▲ ▲ ▲ ▲ ▲ ▲ ▲ ▲ ▲ ▲ ▲ ▲ ▲ ▲
日期:
- 1、下载文档前请自行甄别文档内容的完整性,平台不提供额外的编辑、内容补充、找答案等附加服务。
- 2、"仅部分预览"的文档,不可在线预览部分如存在完整性等问题,可反馈申请退款(可完整预览的文档不适用该条件!)。
- 3、如文档侵犯您的权益,请联系客服反馈,我们会尽快为您处理(人工客服工作时间:9:00-18:30)。
进料检验是否有客人或权威部门签署的标准样品,限度样品或 A3 颜色样品等供应参考?是否有一份明确的管理清单,并适时维 各类样品保存完好,有效签名,有管理清单,并及时更新 护? A4 A5 是否有要求供应商提供来料之检测数据、ROHS测试报告、成分 有效的供应商的ROHS测试报告、成分表COC,MSDS,出货检 表COC等证明资料并统一管理? 验报告,并有一管控清单 当来料不合格时的处理程序是否明确,是否有要求供方提供防 不合格品控制程序,供应商纠正/预防措施要求表清单及8D 止再发的原因对策? 内容,让步接受的相关定都有 编制了UAI让步接受的相关定,且按规定执行,有真实的记 录作为证据 入库的原料应有IQC检验合格的标识(章或标签),如为免 检物料则要求相应规定 ★
A6 是否有紧急放行的规定? A7 检验合格后入库是否有明确标识可以识别此批物料的检验状 态,以便追溯?
B
#
模具管理
审核要点 审核内容与基准
实际审核得分: 0.00 重点 得分
实际审核得分: 审核结果
备注
完整的模具清单(包括模具编号,数量,寿命,模穴数,客 户,当前状态等) 模具保养计划/维护(包括保养周期,保养项目,保养人 B2 是否有详细的模具保养/维护计划,并按计划切实执行? 等),并保存有保养/维护记录 以时间或是模具生产数量为标准,在对模具进行保养或维护 B3 对模具的维护如检查,清洁及保养,是否有适当的监控方法? 有数据支持 看是否有多件或少件的问题发生,及生产后模具是否涂有防 B4 每次上模生产前或下模后对否对模具进行点检与适当的保养? 锈油 B1 是否有一份最新的模具清单(包含所有模具)? 模具变更是否有书面的资料通知修改部门或人员,资料是否经 变更通知单 权威人士或工程经理签名确认? 新模或变更后的模具是否经评审,如何确认符合客人要求的? 新模制作/模具变更确认指导,试模记录,尺寸测试报告, B6 是否需客人评估? 样品 模具维修通知/记录表,要求通知到品管/生产/工模,且有 B7 模具的维修是否有相应的规范及记录? 三个部门相关人员签名,QC确认维修结果 B5 B8 B9 B10 模具是否有明确的标识,正常的防护,适当的存储,便捷的存 有模具编号,刷有油漆防锈,温/湿度控制,区域划分与摆 取? 放等 模具寿命如何监控,对于超过寿命的模具如何处理,品质如何 模具生产数量记录,过期模具处理流程等 保证? 工厂是否有能力维修,制造苏泊尔产品的模具?模具精度是否 模具制造能力(线切割,火花机,精密铣床等),工程人数 能达到苏泊尔的要求?
第1页共5页
供应商评估·审核·监察清单(五金)
C
# C1
设备与仪器管理
审核要点 审核内容与基准
实际审核得分: 0.00 重点 得分 审核结果 备注
是否有程序文件或作业指导定义设备与仪器的购置,安装,调 程序文件或作业指导书 试,编号等管理流程? 是否有最新的生产设备&工装夹具清单,及测量仪器清单(包 完整的生产设备及工装夹具清单及测量仪器清单(包括设备 C2 含所有的生产设备与测量仪器)? 编号,规格/型号,数量,当前状态等) 每台生产设备或测量仪器是否有操作规程/指引,指导作业员 查生产设备和测量仪器操作规程 正确的使用? 是否有详细的生产设备&仪器保养/维护计划,并按计划切实执 生产设备&测量仪器保养计划/维护(包括保养周期,保养项 C4 行? 目,保养人等),并保存有保养/维护记录 仪器校验计划(包括仪器编号,规格/型号,数量,所属部 C5 是否有一份测量仪器校验计划?并可视化管理? 门,内/外校,上次校验时间,下次校验时间等) 是否有内校人员?此人是否有资格从事内部测量仪器或设备的 C6 校验活动?是否有内校作业指导书?外校机构是否有资质或是 内校员资格证书,外校机构资格证,内校作业指导书 国家认可的机构? C3 C7 是否按校验计划准时或提前对量具及测试/检验设备进行校 验,并保存校验证书或记录? 查校验报告/证书 校验标签要贴在仪器上,无破损,清晰可辩 文件应规定有限用或禁用的条件,了解实际执行情况 就是查校验失效的解决方案流程 ★
F9
IPQC/OQC在检验中发现批量性不良,是否开出了纠正和预防措 纠正和预防措施要求表跟踪单,监控所有发出的CAR关闭状 F10 施要求表?并对生产分析的原因与采取的行动进行监控和验 况;对于重复发生的问题要重新分析与改善 证? IPQC/OQC检验合格的产品与不良品是否都有明确的标识可以区 F11 别与其它产品?对于紧急放行的物料,是否有一清晰的流程, 合格/不合格/让步接受章或标签,特采程序及相应记录 并在紧急放行物料时执行? F12 F13 IPQC/OQC是否都经过相应的培训后上岗的,培训与考核的内容 培训教材,考核记录(应包括看图纸,测量工具应用,QC7 是否保留? 大手法,品质标准,客户特殊要求,可靠性测试等内容) 在过程检验与出货检验中是否使用了不良监控的系统?如: SPC,防呆,目视管理或其它更先进的方面 SPC、CPK、防呆、目视管理等在过程中应用 样品清册应包括:客户、名称/规格,数量、类型(标准样 品或限度样品或颜色样品)签署日期,保存年限等
对于苏泊尔产品,量大的五金产品是否有固定机台/固定参数/ 从生产日报表中获取相关信息 固定人员以减少过程中的变异因素? 生产现场是否有首件或标准样品或限度样品作为参考,指导作 E6 业员正确地执行自检?若生产条件变异,作业员发现会如何处 现场审核 理? 生产员工是否按作业指导生产/加工/自检/包装产品?是否将 E7 不良品现象/数量记录入生产日报,并将不良品放入标识清晰 现场审核,查生产日报表及看不良分类 的指定的不良品箱/盒/袋/筐里? E8 调机品是如何管控的?过程中再次调机,如何管理? E9 E10 E11 E12 E13 E14 E15 E16 E17 E18 看相关文件与现场
C8 对校验后的仪器如何进行区分与标识? C9 对校验失效或损坏的仪器设备如何管理? C10 是否有适当的管控以确保针对校验失效采取相应的措施? C11
对所用的测量仪器或设备是否都做测量系统分析(重复性与再 看GR&R记录 现性分析GR&R),并保存有记录?
D
#
标识/可追溯性
审核要点
是否有批次管理的规定,每一批号的产品是否能识别到,识别 的标记是否能体现所需追溯的内容?供应商ຫໍສະໝຸດ 估·审核·监察清单(五金)A
#
进料检验
审核要点 审核内容与基准
实际审核得分: 0.00 重点 得分 审核结果 备注
进料检验程序文件(包含检验流程,抽样计划,操作步骤, 及所用表单等) 按规定项目并进行检查, 记录检查结果并保存相应记录
A1 是否有文件化的进料检验规定? A2 是否有进料检验基准书,且规定了检测项目及检测工具?
以前检验未覆盖到的,在发生的重大品质异常后或客户投诉后 品质控制计划/检验指导书更新版本,更新的原因与执行情 F4 是否及时更新了控制计划或检验指导,以便在过程中控制,防 况 止再次发生? 首件检验是否有执行?是否按检验标准上要求的内容逐项检测 带签名的首件、首检报告(客户要求检测的所有关键尺寸, F5 并规范地记录?检验合格后IPQC是否在首件上面签名标记(不 可靠性测试) 论有多少个穴号)? F6 F7 F8 首件是否在正式生产前放在相应的机台上,并对作业员进行重 现场审核 点强调及自检培训? IPQC在生产过程中是否对生产的重要参数进行监控并在相应的 参数点检表 点检或监控表上签名? IPQC/OQC是否按检验指导书定时/定量进行检验,并将检验结 果记录下来? IPQC/OQC检验的数据是否进行分析,作为后续持续改善的依 据?生产、过程及出货检验的DPPM是否有统计,走势如何? 检验记录按要规范,与要求内容一致,数据真实 品质周报/月报,CIP计划 ★ ★
不良品返工或报废是否有相应记录?返工是否有相应的流程? 返工/报废单,返工流程/方案,重检记录 返工后的产品是否交IPQC进行再次检验? 生产过程中出现批量性的品质不良时,生产是否对不良批进行 内部纠正和预防措施要求表清单 原因分析,并采取有效的纠正和预防措施? 是否对纠正和预防措施的有效性进行确认与验证?如确实有 效,是否加入作业指导书形成标准化? 改善后数据收集,分析,更新后的作业指导书 ★
实际审核得分: 0.00 审核内容与基准
标识/可追溯性控制程序的相关规定 查看是按批次还是按订单号管理,可追溯性有效程度。
重点 得分
审核结果
备注
D1 是否有产品识别的管理规定(含环保产品的识别))? D2
仓库,IQC,车间是否有存储区,周转区,不良品区,待检 D3 区,合格品区,半成品区,成品区之分并标识?所有物料按区 现场区域划分,标识与摆放的规范,有序 域摆放? 从进料、在库、生产、组装、包装、交付每一过程产品是否能 物料/产品标识卡(有料号,名称,规格,数量,生产部门/ D4 保证能被识别或不被漏掉 工序,生产日期,班组,检验状态等) D5 是否有一个实时的信息控制系统(ERP或其它)? D6 当客户要求时,是否记录和保持了可追溯性? D7 是否标识在库和在制原材料,以便按先进先出的次序使用物 料? 信息化,自动化 追溯的方法与记录 颜色管理,其它有效的管理方案
第3页共5页
供应商评估·审核·监察清单(五金)
F
# F1 F2 F3
过程/出货检验与测试
审核要点 审核内容与基准
实际审核得分: 0.00 重点 得分 审核结果 备注
对于每一款产品,IPQC/OQC是否都有最新版本的图纸,检验指 从机台上随机抽一款产品查相应资料(核对客户图纸) 导书? 检验指导书是否内容齐全,有图片标识,简单易懂,且有品管 应包括:外观/尺寸/装配/功能/可靠性等相关测试内容,检 权威人签署? 验与测试方法/工具,抽样水准,抽检频率/数量等 是否依照工艺流程制订有品质控制计划,且将所有过程中需要 品质控制计划 控制的重点及标准都进行了评估与明确? ★
第2页共5页
供应商评估·审核·监察清单(五金)
E